Форма литьевая на деталь Крышка




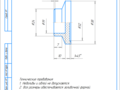
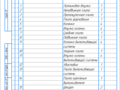
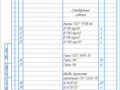
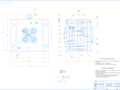
- Добавлен: 25.01.2023
- Размер: 278 KB
- Закачек: 0
Описание
Форма литьевая на деталь Крышка
Состав проекта
![]() |
![]() |
![]() ![]() ![]() |
![]() ![]() ![]() ![]() |
![]() ![]() ![]() |
![]() ![]() ![]() ![]() |
![]() ![]() ![]() |
![]() |
![]() ![]() ![]() |
![]() ![]() ![]() |
![]() ![]() ![]() |
![]() ![]() ![]() ![]() |
![]() ![]() ![]() |
![]() |
![]() ![]() ![]() |
![]() ![]() ![]() |
![]() ![]() ![]() ![]() |
Дополнительная информация
ZAKLYuChENIE.doc
Для установки формы выбрана литьевая машина "KuASY 10025" с объемом впрыска 40 мл.
Kryshka.cdw

Недоливы и облой не допускаются.
Все размеры обеспечиваются заливочной формой.
Полиэтилен низкого давления
VVEDENIE.doc
В данной работе представлен расчет литьевой формы для производства детали "Крышка". Материал изделия – полиэтилен низкого давления Гнездность формы 4.
Forma_kryshka.cdw

Форма для литья под давлением полиэтилена низкого давления
Литниковая система - холдноканальная.
Форма четырехгнездная
Технические требования
Форма спроектирована на термопластавтомат FT-90
производства фирмы "Шенда".
Трущиеся поверхности смазать кремнийорганическим вазелином
типа КВ-3 ГОСТ 15975-70.
Каналы охлаждения испытать гидравлическим давлением 1
Литниковые каналы доработать после испытания формы.
Расчетный коэффициент усадки 2
Prilozhenie_3.doc
Размеры и технические характеристики:
Давление масла (5 ед.)
Readme.doc
Чертежи формы (со спецификацией) и эскиза а также рамки пояснительной записки выполнены в системе КОМПАС 5.11.
Рекомендую ознакомиться с содержимым пояснительной записки особое внимание уделив при этом описанию работы формы.
Обратить внимание на наличие туннельного литника посредством которого происходит срезание литника с изделия (на сборке разрез Б-Б).
Рекомендую изучить чертеж знать назначение каждого элемента формы и смысл обозначений (напр. О – повернуто или – шероховатость поверхностей с максимальной высотой неровностей 160 мкм).
Некоторые детали формы могут быть знакомы Юрию Терентьевичу по предыдущим курсовикам; в случае если он обратит на это внимание можно сослаться на то что элементы сборочного чертежа (колонки втулки стандартные изделия) были заимствованы из архива чертежей КОМПАСА.
1_-_TEKhNOLOGIChESKAYa_ChAST.doc
1. Основные стадии процесса литья под давлением
Процесс литья под давлением является циклическим. Цикл состоит из следующих стадий загрузка сырья в пластикационный цилиндр литьевой машины и подготовка расплава (пластикация) смыкание формы заполнение формы расплавом выдержка под давлением в форме выдержка без давления в форме раскрытие формы и извлечение изделия.
Загрузка сырья проводится через загрузочный бункер и окно в цилиндре литьевой машины. В пластикационном цилиндре проводятся нагрев материала до перехода в вязкотекучее состояние уплотнение и гомогенизация расплава. Под гомогенизацией понимается перемешивание приводящее к равномерному распределению температуры по массе что обеспечивает равномерную плотность и вязкость расплава. Условия пластикации не должны приводить к заметной деструкции материала.
Необходимая температура расплава создается за счет двух источников тепла внешнего обогрева цилиндра и перехода в тепло работы сил трения возникающих при деформировании материала вращающимся шнеком. Температура расплава должна обеспечивать необходимую вязкость для заполнения формы но при этом не должна протекать деструкция материала. Обычно вязкость расплава необходимая для литья под давлением достигается у аморфных полимеров при температуре на 100—150° С выше температуры стеклования а у кристаллических полимеров как правило при температурах на несколько градусов превышающих температуру плавления. Максимально возможной является температура расплава на 30—40° С ниже чем температура деструкции. Чем выше вязкость расплава материала тем больше разница между температурой деструкции и предельной температурой расплава так как процесс пластикации вызывает дополнительный прогрев.
Нагнетаемый шнеком расплав при закрытом сопле накапливается в зоне дозирования и за счет развивающегося в материале давления шнек перемещается назад Скорость отхода шнека регулируется путем создания в гидроцилиндре узла впрыска противодавления. Чем больше противодавление тем выше плотность расплава и более однородна его температура. Кроме того с ростом противодавления увеличивается нагрев материала в зоне дозирования за счет сдвиговых деформаций. Однако с ростом противодавления уменьшается пластикационная производительность литьевой машины т. е. уменьшается количество материала переводимого в расплав в единицу времени.
Если пластикационная производительность литьевой машины невелика то за счет увеличения времени подготовки новой дозы расплава приходится увеличивать время пребывания отливки в форме что снижает производительность оборудования.
Заполнение формы расплавом (впрыск) начинается после подготовки необходимой дозы расплава и смыкания формы. Под действием усилия развивающегося в гидроцилиндре узла впрыска шнек движется вперед и через сопло и литниковую систему подает расплав в формующую полость Создаваемое наконечником шнека давление затрачивается на вязкое течение расплава и входовые эффекты обусловленные вязкоупругими свойствами расплавов полимеров Поэтому давление в форме существенно ниже чем давление развиваемое шнеком.
На рис. 1 приведена зависимость давления на входе в сопло Рспл (1) давления на входе в форму ф (2) и объемной скорости течения Q (3) от времени. Первоначально расплав течет с постоянной объемной скоростью (кривая 3) при этом давление на входе в сопло и в форму растет что соответствует первому режиму (участок I). По достижении в сопле максимального давления Рсплmax определяемого величиной Рл объемная скорость течения начинает уменьшаться так как увеличивается длина течения при постоянном перепаде давлений наступает второй режим — режим постоянного давления на входе в сопло и убывающей скорости течения (участок II). В этом режиме давление на входе в форму постоянно растет за счет снижения потерь давления в сопле и в литниковой системе так как скорость течения в них уменьшается. В режиме Q=const заполнение формы идет за счет перепада давлений по длине формы. Расплав заполняет свободную часть формы.
Рис. 1. Зависимость давления на входе в сопло Pспл (1) давления на входе в форму ф (2) объемной скорости течения Q (3) и длины затекания расплава в форму L (4) от времени: I — режим постоянной объемной скорости течения; II — режим постоянного давления на входе в сопло
Движение расплава термопласта в полости формы сопровождается охлаждением расплава при соприкосновении со стенкой так как температура его выше чем температура формы. На стенках формы образуется канал с толщиной стенок из высоковязкого неподвижного материала. Внутри этого канала течет расплав. По мере заполнения толщина пристенного слоя в ранее заполненной части формы постоянно возрастает. В режиме P=const неподвижный слой имеет большую толщину чем при заполнении в режиме Q=const но в обоих случаях вблизи литника толщина пристенного слоя мало меняется по мере поступления расплава так как температура расплава на входе в форму высокая. Характер движения расплава по формующей полости связан с конструкцией формы. При литье плоских изделий с постоянной толщиной через литник лежащий в плоскости формы заполнение идет последовательным движением расплава по уровням равноудаленным от литника. При заполнении формы поток перемещается последовательным растягиванием фронтальной пленки и продвижением новых порций вдоль неподвижных слоев уже застывшего полимера на стенке формы. Скорость частиц в центре потока полимера выше чем скорость его фронта. Частицы полимера входят в форму с большей скоростью чем движется фронт потока. При приближении к фронту потока скорость частиц движущихся параллельно общему направлению течения постепенно снижается а при достижении фронта становится равной его скорости. Частица смещается по линии фронта к стенке формы; соприкасаясь с ней затормаживается и некоторое время скользит вдоль стенки увлекаемая движением вышележащих слоев. По-видимому этот эффект и приводит к ориентации пристенного слоя в направлении заполнения формы расплавом. Продвижение фронта потока по форме сопровождается нарастанием давления на тех участках формы которые поток прошел что приводит к разглаживанию волн образовавшихся на поверхности. Если скорость заполнения формы мала то поверхностные слои могут охладиться до того как волны разгладятся и на поверхности изделия останутся их следы.
Если толщина впуска литникового канала намного меньше толщины изделия (точечные впуски) то процесс заполнения идет с высокой скоростью и расплав полимера поступает в полость формы в виде отдельной непрерывной струи которая хаотически пульсируя продвигается вперед. Поверхность струи похожа на поверхность экструдата выдавливаемого из капиллярного вискозиметра при высоких скоростях сдвига. Струйное заполнение формы отражается на качестве поверхности изделия и на его свойствах: плохая свариваемость струи с последующим потоком расплава приводит к образованию поверхностных дефектов и непрочных мест в изделии. Струйный эффект снижается при увеличении температуры расплава или формы.
Масса материала поступившая в формующую полость формы с начала цикла до завершения выдержки под давлением не меняется после затвердевания литника. Поэтому плотность и объем готового изделия определяются средней температурой и давлением в полости формы к моменту завершения выдержки под давлением. Соотношение между плотностью (удельная объемом) температурой и давлением для расплава полимера описывается уравнением состояния расплава Спенсера—Джилмора являющегося видоизмененным уравнением Ван-дер-Ваальса:
где n — удельный объем полимера при T и P м3кг; —давление МПа; T — температура. К; R — универсальная газовая постоянная [R=829 кДж(моль·К)] M — молекулярная масса структурного звена полимера кгмоль; — объем занимаемый собственно молекулами полимера м3кг p — внутреннее давление МПа.
Выдержка под давлением. Время выдержки под давлением (включающее в себя и время заполнения формы) для цилиндрического впускного литника можно рассчитать по формуле
для прямоугольного впускного литника — по формуле
и для центрального впускного литника с радиусом большим чем половина толщины изделия — по формуле
где r A S — размеры впускных литников м (м2); TТ — температура текучести (или плавления). К; Тф — температура формы. К; Кл — коэффициент учитывающий течение расплава во время подпитки: Кл=DVIVл [здесь DV — объем расплава нагнетаемый в форму при выдержке под давлением м3; Vл — объем впускного литника м3; — коэффициент формы для литника (для цилиндрического =2 для щелевого и кольцевого =1.5)].
Охлаждение без давления завершает процесс формирования структуры изделия в форме. На этой стадии скорость охлаждения выше чем в период выдержки под давлением. Причем чем длительнее выдержка под давлением тем меньше разница в скорости охлаждения на последней стадии.
Продолжительность охлаждения изделия в форме связана с толщиной изделия и его формой температуропроводностью полимерного расплава перепадом температур Tр и Tф а также с температурой в центре изделия в момент его извлечения из формы Tи.
Полная продолжительность охлаждения изделия в форме tохл представляет собой сумму времени охлаждения под давлением (т. е. времени выдержки под давлением tв) и охлаждения без давления и может быть рассчитана с учетом ряда допущений по формуле
где Т0 Tф ТИ — температуры расплава формы и изделия соответственно в момент съема К — толщина охлаждаемого изделия м (для плоского изделия =h для цилиндрического =r) А и С — коэффициенты определяемые формой изделия (для плоского изделия A=127 и С=p2 для цилиндра A=16 и С=576).
Продолжительность охлаждения без давления определяет уровень остаточного давления в форме Рост. Если величина Рост превышает прочность материала в момент съема изделия с температурой ТИ то при раскрытии формы может произойти деформация (и даже поломка) изделия.
2. Классификация литьевых форм
Формы для литья под давлением изделий из полимерных материалов относятся к самым распространенным сейчас и весьма перспективным в будущем. В этих формах устанавливаемых на универсальных или специализированных литьевых машинах-автоматах получают изделия практически из всех термопластов а также из многих марок порошкообразных и гранулированных реактопластов резиновых смесей. В формах для литья под давлением получают разнообразные изделия - от простейших до особо сложных и высокоточных.
Формы для литья под давлением разделяют на стационарные полустационарные и ручные.
В стационарных формах весь цикл литья изделий и их удаление из формы осуществляется непосредственно на литьевой машине-автомате. Форма не снимается с машины до окончания изготовления заданной программы выпуска изделий (или до ее ремонта - в случае необходимости).
Полустационарные формы имеют съемные оформляющие кассеты которые после каждого цикла литья извлекают из формы и разбирают вне рабочей зоны машины-автомата.
Ручные формы целиком извлекают из зоны формования после каждого цикла литья.
Применяют также стационарные и полустационарные формы устанавливаемые на универсальных блоках. В комплект формы устанавливаемой на универсальном блоке входят лишь основные оформляющие детали (матрицы знаки и др.) а вспомогательные детали (передние и задние плиты обоймы и т. д.) включены в универсальный блок.
Стационарные формы для литья под давлением в том числе устанавливаемые на универсальных блоках разделяют на полуавтоматические и автоматические обеспечивающие отделение и сепарацию литников от изделий при размыкании формы; на управляемые (т. е. снабженные датчиками регистрирующими состояние расплава в течение всего цикла литья под давлением) и неуправляемые (фактически непригодны к работе в системе АСУТП).
Все формы независимо от характера их связи с литьевой машиной-автоматом и системой управления ее работой по количеству одновременно отливаемых изделий разделяются на одно- и многогнездные а по интенсивности заполнения гнезд - на одно- и многовпускные (в одно гнездо).
Все формы для литья под давлением по важному признаку - направлению их размыкания (разъема) относительно горизонтальной оси литьевой машины-автомата - разделяют на следующие: с одной вертикальной плоскостью с одной вертикальной плоскостью и раздвижными полуматрицами с комбинированными разъемами (с одной основной и вспомогательными; с основной вспомогательной и дополнительной плоскостями и т. д.) в которых оформляющие детали раскрываются параллельно и перпендикулярно оси машины. Формы с комбинированным разъемом применяются для деталей с поднутрениями боковыми отверстиями и тому подобными элементами. Конструктивно они выполняются в виде клиновых или шиберных форм.
Дополнительные классификационные признаки форм для литья под давлением термопластов связаны с конструктивными особенностями функциональных систем форм. Например литниковые системы по состоянию материала в них в них в момент окончания заполнения внутренней полости формы разделяют на холодноканальные (затвердевающие) горячеканальные (незатвердевающие) и комбинирован-ные. Формы разделяют также на термостатируемые (с различными вариантами конструктивного оформления системы - канальным полостным комбинированным) и нетермостатируемые. Классификация стационарных форм предусматривает разделение их по способу извлечения изделий из формы: стержневыыми или трубчатыми выталкивателями; плитой съема; комбинированным (ступенчатым) выталкиванием.
Формы с выталкивателями применяются случаях когда изделия достаточно жестки и прочны и на них допускаются следы выталкивателей причем формы со стержневыми выталкивателями используются для изделий имеющих достаточную поверхность для контактов с выталкивателями - для изделий типа втулок.
Форма с плитой съема рекомендуется для тонкостенных изделий исключающих возможность использования стержневых выталкивателей.
В формах со ступенчатым выталкиванием изделие сначала снимается со знака плитой съема а затем выталкивается из этой плиты стержневыми выталкивателями (при этом используется механизм шариковой защелки).
3_-_RASChETNAYa_ChAST.doc
Литьевую машину выбираем по расчетному объему впрыска:
Где ρ - плотность расплава полимера (095 гсм3);
К- коэффициент учитывающий сжатие и утечки расплава при его впрыске в форму (к=12);
N - гнездность формы;
Н - навеска материала необходимая для отливки одной детали:
Где к1 - коэффициент безвозвратных потерь 0004.
К2 - коэффициент возвратных потерь 005.
Н=7(1+0004+005)=74 г.
V=1 2·74·4095= 374 см3.
Выбираем литьевую машину FT-90 (производитель фирма "Шенда" КНР) с объемом впрыска 138 см3 номинальное усилие запирания 900 кН.
Проверим подойдет ли данная машина по усилию запирания формы:
Рзап=Руд·к·b·F=18 кгсм2·05·11·113 см2·= 119 кН.
Давление литья для полиэтилена низкого давления составляет 140 МПа. Давление литьевой машины 180 МПа. Максимальный ход подвижной плиты термопластавтомата 320 мм.
Данная литьевая машина подходит.
2.Расчет центрирующих элементов
К центрирующим элементам относят фланцы крепежных плит направляющие колонки и втулки.
Ориентировочно диаметры колонок можно определить по эмпирической формуле:
Где D - диаметр направляющей части колонки мм;
Д - диаметр формы мм.
D=4+006·176=1456 мм.
По таблице выбираем колонку направляющую по ГОСТ 17385-72
3.Расчет и выбор системы выталкивания
Толкатели - подвижные элементы системы выталкивания обеспечивающие прямым воздействием на отливку её извлечение из пресс-формы. Дважды за цикл литья толкатели перемещаются в соответствующих отверстиях формообразующих деталей - при извлечении отливки и при возврате системы выталкивания в исходное положение. Зазор между толкателем и стенкой отверстия исключающий затекание туда расплава должен быть менее для полиэтилена 003 мм.
Согласно ГОСТ на пресс-формы твердость формообразующих деталей колеблется в диапазоне 36-64HRCэ.
Конструктивно толкатель состоит из стержня d (длиной l) обеспечивающего извлечение отливки из пресс-формы и головки D (высотой k) - для закрепления толкателя в плитах системы выталкивания. Анализ каталогов нормализованных деталей пресс-форм позволяет выделить пять основных типов толкателей:
толкатели с цилиндрическим гладким стержнем и цилиндрической головкой (обыкновенные толкатели); ejector p
толкатели с цилиндрическим гладким стержнем и конической головкой ejector p
толкатели с цилиндрическим ступенчатым стержнем (ступенчатые толкатели); shouldered ejector p
толкатели с цилиндрической несущей ступенью и прямоугольным сечением рабочей ступени (ножевые или плоские толкатели); flat ejector p
толкатели с цилиндрическим гладким стержнем трубчатого сечения (трубчатые толкатели); ejector sleeve DIN 16756.
Выпускаемые специализированными фирмами нормализованные толкатели обеспечивают оптимальное соотношение качествоцена повышают надёжность работы пресс-формы и её ремонтопригодность.
Для изготовления толкатели применяются инструментальные стали двух типов: WS- alloyed cold work steel- легированная сталь для холодной обработки и WAS- hot work steel- легированная сталь для горячей обработки. Стали типа WS после закалки имеют твердость 64HRC.
Все толкатели из стали типа WS отвечают следующим техническим требованиям:
Твердость: стержень d: 58-64HRC сквозная закалка; головка D: 40-50HRC.
Шероховатость поверхности: стержень d: головка D: торцевые поверхности головки Rz16.
Точность изготовления: стержень d: диаметр головки D: (-02); высота головки k:(-005); длина толкателя радиус галтели r:(+02).
Температура эксплуатации: 200-250° С.
Стержень d(g6) толкателя ходит в калиброванном направляющем отверстии D(H7) по посадке H7g6 что и обеспечивает при литье отсутствие облоя вокруг толкателя. Длина для d> 3мм: l=2d+5. Для d = 5 мм:
Итак по каталогу толкателей фирмы D-M-E (Германия) выбираем обыкновенный (цилиндрический) толкатель с цилиндрической головкой АН 5-70 DIN 1530 длиной 70 мм и диаметром 5 мм.
Spetsifikatsia_list1.cdw

soderzhanie.doc
1. Основные стадии процесса литья под давлением
2. Классификация литьевых форм
ОБОСНОВАНИЕ КОНСТРУКЦИИ ФОРМЫ
2.Положение изделия в форме
3.Выбор выталкивающей системы
4.Общие характеристики формы
5. Описание работы формы
1. Выбор литьевой машины для установки формы
2. Расчет центрирующих элементов
3. Расчет и выбор системы выталкивания
СПИСОК ИСПОЛЬЗОВАННЫХ ИСТОЧНИКОВ
Приложение 1. Литьевая форма на деталь "Колпачок". Спецификация
Приложение 2. Деталь "Колпачок". Эскиз
Приложение 3. Описание термопластавтомата FT-90
2_-_OBOSNOVANIE.doc
Согласно заданию на курсовое проектирование целью данного курсового проекта является разработка четырехгнездной формы для производства детали "крышка" (см. приложение 1) методом литья под давлением. Материал изделия – полиэтилен низкого давления. Габариты детали 15х38х38. детали 7 г. Объем изделия 74 см3.
Форма проектируется с учетом установки и эксплуатации ее на выбранной литьевой машине.
Основными параметрами термопластавтоматов являются:
Давление впрыска Мпа;
Усилие смыкания формы кН;
Пластикационная производительность кгч.
Важными являются также паспортные характеристики:
Объемная скорость впрыска см3с;
Наименьшее время запирания и раскрытия формы с;
Наибольшее расстояние между плитами мм;
Наименьшая и наибольшая высота формы мм.
2. Положение изделия в форме
Положение изделия в форме определяет всю конструкцию последней (степень механизации и автоматизации тип выталкивающей системы габариты формы и т. д.).
Положение изделий в проектируемой форме будет следующим:
Изделия в форме расположены симметрично центру формы;
Изделие в гнезде расположено так что наибольшая поверхность параллельна линии разъема (для облегчения извлечения детали из формы);
Подвод литников осуществляется к кромкам детали.
3. Выбор выталкивающей системы
Выбор того или иного типа выталкивающей системы определяется формой изделия конструктивными особенностями формы и требованиями к поверхности изделия.
Данная форма оснащена выталкивателями изделий (4 шт) и выталкивателем литника. Отделение литника от изделий происходит за счет системы туннельных литников.
4. Общие характеристики формы
Для изготовления детали была разработана автоматическая четырехгнездная форма.
Форма спроектирована на машину FT-90 фирмы "Шенда" (Китай). Расчетный вес формы – 65 кг. Форма холодноканальная. Система охлаждения формы – водяная. Плита системы охлаждения изготовлена из сплава с высоким значением теплопроводности. Для установки и перемещения формы используется рым-болт положение которого рассчитано в соответствии с массово-центровочными характеристиками формы.
5. Описание работы формы
На первом этапе расплав полимера из сопла литьевой машины поступает через литьевую втулку 1 откуда через систему литников впрыскивается в формующую полость.
После выдержки под давлением и охлаждения наступает второй этап: форма раскрывается по линии разъема. Подвижная часть формы отводится при этом изделие за счет усадки остается на охватываемой поверхности формующей втулки. Следует отметить что обратная конусность литниковой системы препятствует забиванию втулки литника остывшим материалом.
Литьевая форма раскрывается до тех пор пока хвостовик не упирается в заднюю стенку термопластавтомата и за счет этого выталкиватели толкают сформованные изделия и литник. Наличие туннельного литника способствует срезанию литника с изделия.
Изделия и литник падают форма смыкается литьевой цикл повторяется заново.
spisok.doc
Методические указания к выполнению курсовой работы по курсу "Расчет и конструирование изделий и форм". Панов Ю. Т. Уткин А. В. Владимир 1998. 28 с.
Басов Н. И. и др. Расчет и конструирование формующего инструмента для изготовления изделий из полимерных материалов. М.: Химия. 1991.
Калинчев Э. Л. Соковцева М. Б. Выбор пластмасс для изготовления и эксплуатации изделий: Справ. Изд. Л.: Химия 1987. 416 с.
Spetsifikatsia_list2.cdw

Рекомендуемые чертежи
Свободное скачивание на сегодня
- 29.08.2014
- 24.01.2023