Электролитическое рафинирование алюминия


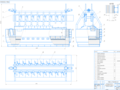
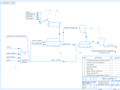
- Добавлен: 25.01.2023
- Размер: 2 MB
- Закачек: 0
Узнать, как скачать этот материал
Подписаться на ежедневные обновления каталога:
Описание
Электролитическое рафинирование алюминия
Состав проекта
![]() |
![]() ![]() ![]() |
![]() ![]() ![]() ![]() |
![]() ![]() ![]() ![]() |
![]() ![]() |
Дополнительная информация
Контент чертежей
Технологическая схема электролитического рафинирования алюминия.cdw

Электролизер в сборе.cdw

Рекомендуемые чертежи
Свободное скачивание на сегодня
Обновление через: 4 часа 48 минут
- 22.08.2014
- 29.08.2014