Экскаватор роторный





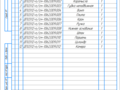
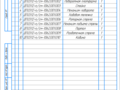
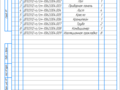
- Добавлен: 24.01.2023
- Размер: 2 MB
- Закачек: 0
Описание
Состав проекта
![]() |
![]() |
![]() |
![]() ![]() ![]() |
![]() ![]() ![]() ![]() |
![]() ![]() ![]() ![]() |
![]() ![]() ![]() |
![]() ![]() ![]() |
![]() ![]() ![]() ![]() |
![]() ![]() ![]() |
![]() |
![]() ![]() ![]() ![]() |
![]() |
![]() |
![]() |
![]() |
![]() |
![]() |
![]() |
![]() |
![]() ![]() ![]() ![]() |
![]() ![]() ![]() ![]() |
![]() ![]() ![]() ![]() |
![]() ![]() ![]() ![]() |
![]() ![]() ![]() ![]() |
![]() ![]() ![]() ![]() |
![]() ![]() ![]() ![]() |
![]() ![]() ![]() ![]() |
![]() ![]() |
![]() ![]() ![]() ![]() |
![]() |
![]() ![]() ![]() |
![]() ![]() ![]() |
![]() ![]() ![]() |
![]() ![]() ![]() |
![]() ![]() ![]() |
![]() ![]() ![]() |
![]() ![]() ![]() |
![]() ![]() ![]() |
![]() ![]() ![]() |
![]() ![]() ![]() |
Дополнительная информация
5. Технол 2.cdw

ДП.0312-псм-1062.009.000.СБ
ДП.0312-псм-1062.009.001
ДП.0312-псм-1062.009.002
ДП.0312-псм-1062.009.003
ДП.0312-псм-1062.009.004
ДП.0312-псм-1062.009.005
ДП.0312-псм-1062.009.006
ДП.0312-псм-1062.009.007
ДП.0312-псм-1062.009.008
ДП.0312-псм-1062.009.009
ДП.0312-псм-1062.009.010
ДП.0312-псм-1062.009.011
ДП.0312-псм-1062.009.012
2.1. Ходовая тележка.cdw

Каток поддерживающий
Подшипник скольжения
ДП.0312-псм-1062.002.000.СБ
ДП.0312-псм-1062.002.001
ДП.0312-псм-1062.002.002
ДП.0312-псм-1062.002.003
ДП.0312-псм-1062.002.004
ДП.0312-псм-1062.002.005
ДП.0312-псм-1062.002.006
ДП.0312-псм-1062.002.007
ДП.0312-псм-1062.002.008
ДП.0312-псм-1062.002.009
ДП.0312-псм-1062.002.010
ДП.0312-псм-1062.002.011
ДП.0312-псм-1062.002.012
2.3. Кабина.cdw

Изоляционная прокладка
ДП.0312-псм-1062.004.000.СБ
ДП.0312-псм-1062.004.001
ДП.0312-псм-1062.004.002
ДП.0312-псм-1062.004.003
ДП.0312-псм-1062.004.004
ДП.0312-псм-1062.004.005
ДП.0312-псм-1062.004.006
ДП.0312-псм-1062.004.007
ДП.0312-псм-1062.004.008
ДП.0312-псм-1062.004.009
2.4. Ковш.cdw

ДП.0312-псм-1062.005.000.СБ
ДП.0312-псм-1062.005.001
ДП.0312-псм-1062.005.002
ДП.0312-псм-1062.005.003
ДП.0312-псм-1062.005.004
2.2. Стрела ротора.cdw

ДП.0312-псм-1062.003.000.СБ
ДП.0312-псм-1062.003.001
ДП.0312-псм-1062.003.002
ДП.0312-псм-1062.003.003
ДП.0312-псм-1062.003.004
ДП.0312-псм-1062.003.005
ДП.0312-псм-1062.003.006
ДП.0312-псм-1062.003.007
ДП.0312-псм-1062.003.008
1. Общий вид.cdw

Механизм подъема стрелы
ДП.0312-псм-1062.001.001
ДП.0312-псм-1062.001.002
ДП.0312-псм-1062.001.003
ДП.0312-псм-1062.001.004
ДП.0312-псм-1062.001.005
ДП.0312-псм-1062.001.006
ДП.0312-псм-1062.001.007
ДП.0312-псм-1062.001.008
ДП.0312-псм-1062.001.009
ДП.0312-псм-1062.001.010
4. Привод ротора.cdw

ДП.0312-псм-1062.006.000.СБ
ДП.0312-псм-1062.006.001
ДП.0312-псм-1062.006.002
ДП.0312-псм-1062.006.003
ДП.0312-псм-1062.006.004
ДП.0312-псм-1062.006.005
ДП.0312-псм-1062.006.006
ДП.0312-псм-1062.006.007
5.1. Технол1.cdw

Фрезерный широко универсальный 6P81
Операция 060 Фрезерная
Вертикально-фрезерный 6Т104
Операция 065 Фрезерная
Станок токарно-винторезный 16К50П
Операция 070 сверлильная
Вертикально-сверлильный 2Г175М
Операция 075 Резьбонарезная
Операция 080 Шлифовальная
кругло шлифовальный станок ЗУ12УА
2.2.Стрела ротора.cdw

ГОСТ12806-80-Т3-Рн3- 5
ГОСТ12806-80-У1-Рн3- 3
ГОСТ12806-80-Н1-Рн3- 5
5.1. Технол1 (передел).cdw

Операция 050 Фрезерная
Фрезерный широко универсальный 6P81
Операция 060 Фрезерная
Вертикально-фрезерный 6Т104
Операция 065 Фрезерная
Операция 075 Резьбонарезная
Вертикально-сверлильный 2Г175М
Операция 080 Шлифовальная
кругло шлифовальный станок ЗУ12УА
Операция 070 сверлильная
2.1.Ходовая тележка новая.cdw

5.2. Технол2.cdw

Максимальное усилие зажима - 15030Н
Рабочую полость пневмокамеры испытать давлением 0
Пневматический ход губки - 4 мм
Тиски пневматические
ДП.0312-псм-1062.009.000.
2.3.Кабина.cdw

2.4.Ковш.cdw

2.1.Ходовая тележка.cdw

4. Привод ротора.cdw

Частота вращения ротора n
Частота вращения вала электроматора n
Передаточное число U=4
3.Электросхема.cdw

Распредилительный пункт
Контакторы переменного тока
Двигатели приводов экскаватора
универсальный переключатель
Концевой выключатель
Кнопка управления аварийная
4.Конструкторская часть.doc
1. Рабочее оборудование
Рабочим органом экскаватора является бескамерный ротор с боковой гравитационной разгрузкой грунта на вращающийся конус с неподвижным сектором.
Диаметр ротора определяется по формуле:
где Q — производительность (м3час) = 315 м3час
Ковши ротора имеют цепное днище 1 литой пояс 2 и зубья 3. Ковш крепится к роторному колесу при помощи сварки.
Рис.1. Ковш с двумя зубьями
Роторная стрела состоит из металлоконструкции и конвейера с приводом. Несущий элемент стрелы выполнен из трубы диаметром 720 мм.
На щековинах вилки головной части размещен кронштейн 7 под установку редуктора и электродвигателя бункер 8 контейнера 9 а также проушины подвески роторной стрелы. В хвостовой части стрела оканчивается вилкой 10 с проушинами для навески стрелы на цапфы портала.
Вдоль стрелы к трубе с помощью кронштейнов и планок приварена рама конвейера основной несущий элемент которой – швеллерные балки с установленными на них роликами рабочей и холостой ветви. Конвейерная лента рабочей ветвью опирается на трехроликовые опоры. Угол наклона крайних роликов к горизонтам составляет 30°. Этим ленте придается желобчатая форма уменьшается просыпание увеличивается производительность конвейера.
В месте перегрузки грунта из ковша на конвейер на металлоконструкции стрелы установлен приемный бункер.
Для предотвращения просыпания транспортируемого материала предусмотрены щитки и фартуки. С левой стороны стрелы находится площадка с барьером для обслуживания конвейера и ротора с приводом.
Для компенсации вытяжки ленты в процессе эксплуатации натяжной барабан сконструирован с подвижными в горизонтальной плоскости опорами которые перемещаются натяжным устройством винтового типа с ручным приводом. Особенностью натяжного устройства является расчётность конструкции. Это позволяет снимать натяжной барабан не разрезая ленту. К оси барабана шарнирно крепится скребок очищающий ленту от налипшего грунта.
Ролики конвейера выполнены на сквозных осях. Ролики поддерживающие рабочую ветвь ленты имеют унифицированную конструкцию подшипниковых узлов. Подшипники заполняются густой смазкой и закрываются волокнитовой крышкой с лабиринтным уплотнением. Стаканы подшипниковых узлов витого ролика соединены трубкой на которой симметрично навиты две спирали - левая и правая. Спирали выполняют роль центрирующего элемента.
где Кр =15 —коэффициент разрыхления грунта;
Q =315 м3час — производительность экскаватора;
d =Зм — диаметр ротора;
Z =8 — число ковшей ротора;
Vp =15 — окружная скорость ротора;
где q — емкость ковша =013м3
Расчет козырька ковша с цепным днищем
Определение геометрических характеристик сечений
Рис.2 Поперечное сечение козырька ковша с указанием размеров центральных осей осей X и Y и главных осей инверсии площади сечения.
На рис. 3 изображена условная продольная ось рамы на которой обозначены наименования сечении. Определим геометрические характеристике для этих сечений. Считаем что момент инерции между обозначенными сечениями изменяется по закону прямой (это достаточно справедливо для моментов инерции вокруг оси X и условно для моментов инерция вокруг оси Y .
Запишем вычисление момента инерции Jx используя формулы параллельного переноса и поворота осей:
Рис.3. Расчетная схема козырька ковша
α расстояние от центра тяжести отдельной части сечения до оси X;
Jxα Jуα собственные моменты инерции относительно повернутых угол а осей.
Разбивка сечения на отдельные части показана на рис.
Аналогично находим для сечения А - А моменты инерции
Геометрическую характеристику Jd находим по формуле тонкостенного открытого профиля:
Подставляя в формулу значение l = 12.5 и = 2 Получим Jd = 33 см4
Угол наклона главных осей инерции сечения определяем по формуле
Подставим значения Jx = 50 Jy = 250 Jxy = 92 в формулу выполнив соответствующие преобразования получим:
Главные моменты инерции определяем во формулам:
Подставляя значения Jx Jy Jxy tgαo в данные уравнения получим:
Моменты сопротивления сечения А - А относительно осей max и min - Wmax и Wmin получим деление соответствующих моментов инерции на расстояния от оси до наиболее удаленной точки. Геометрическая характеристика определяемся по формуле:
Окончательно находим
Результаты вычисления геометрических характеристик для расчетных сечений полученные так как это частично показано для сечения А — А сведены в таблицу:
Расчет рамы из плоскости
При загружении рамы силами направленными перпендикулярно к ее плоскости деформация будет пространственной. Она характеризуется изгибом рамы из ее плоскости и кручением. На рис.58 показан закон изменения по контуру рамы момента инерции сечений рамы при изгибе из плоскости Jx и момента инерции при кручений Jy на основании которого получены соотношения моментов инерции между отдельными элементами рамы.
А. Резание грунта острыми зубьями.
Рис.4 Эпюры моментов инерции сечений рамы вокруг осей Y и моментов
инерции сечений при кручении.
Ординаты эпюры крутящих моментов:
МКЕ =285·0879·Р = 2506·Р
Мкд =(285+337) ·0879·Р = 546·Р
МКА =[(285+337) ·05-34-965] ·Р = -1255·Р
Формула для определения ik имеет вид:
В рассматриваемой раме изгибная жесткость стержней EJy значительно превышает жесткость на кручение GJk. Так например для горизонтального ригеля отношение:
Следовательно при определении перемещений можно пренебречь изгибными деформациями и сохранить в формуле только второй член.
Составляем систему канонических уравнений. В связи с симметрией рамы эта система распалась на одно уравнение с одним неизвестным X1 и систему двух уравнений с двумя неизвестными Х2 и Х3:
Из первого уравнения найдем :
Систему двух уравнений решим по Гауссу:
Б. Резание грунта изношенными зубьями
Нагрузочные коэффициенты:
Запишем первое уравнение:
Два других уравнения:
47Х2 + 3394Х3 +39Р = 0;
94Х2 + 18760Х3 11357Р=0.
Х2 = (-730715 - 084)Р = -606 Р
Определение расчетных напряжений в опасных сечениях рамы по третьей теории прочности
Расчетная формула третьей теории прочности:
здесь и - главные напряжения; [] - допускаемое напряжение.
При наличии изгибающих моментов продольных сил и крутящих моментов формулы для главных напряжений запишутся так:
Подставляя эти выражения получим:
где - касательное напряжение вызванное крутящим моментом и перерезывающими силами;
Формулы для изгибающих моментов относительно главных осей как было указано выше
Здесь Мmax и Mmin считаются положительными в том случае если они сжимают положительное направление осей. Поэтому напряжения от изгиба записаны со знаком "минус".
Касательные напряжения от кручения на длинной стороне сечения (не у самых углов) определяются по формуле
Напряжения от продольных сил N и напряжения от поперечных сил и получаются значительно меньше чем от Мu и Mv и от Мкр поэтому их можно не учитывать.
Наименование сечений для правой половины рамы будем обозначать так же как и для левой но со знаком "штрих".
Из эпюр моментов при резании острыми зубьями находим:
Полагая для удобства записи Р = 1т =1000 кг= 10 кН получим:
Нормальные напряжения в точке 1 и 2 (рис. 2) соответственно будут равны:
Касательные напряжения от кручения на длинной стороне
Расчетное напряжение вблизи точки 1 с некоторым запасом
При резании тупыми зубьями в этом же сечении:
Усилия получились значительно меньше чем при резании острыми зубьями поэтому напряжения определять нет необходимости.
Сечение А'-А' (правая часть рамы). Резание острыми зубьям:
Максимальное касательное напряжение от кручения:
Расчетное напряжение возле точки 1:
В точке 3 (рис.47) соответственно:
Рассмотрим сечение Б - Б (правая часть рамы). Резание острыми зубьями:
Для точки соответствующей точке 3 (рис. 2) получим:
Сечение Г - Г (левая половина рамы). Резание острыми зубьями:
Сечение Е - Е (левая половина раны).
Резание острыми зубьями:
В угловой точке прямоугольного сечения Е-Е с размерами сторон 2 х 30 см подучим
Наибольшие касательные напряжения от кручения:
С некоторым запасом прочности
3. Расчет стрелы ротора.
Допускаемое напряжение:
m1 = 08 - учитывает условия работы;
m2 = 09 - учитывает погрешность расчета;
m3 = 03 02 - учитывает ответственности конструкции
где у предел текучести
n запас прочности по СНИП = 5
Поскольку на стрелу будет действовать крутящий момент Т от двигателя и от редуктора равный:
Т = F В = 50 кН 05 = 25 кН
то касательное напряжение будет равно:
Тогда эквивалентное напряжение по гипотезе касательного напряжения
где А* площадь фигуры;
Для того чтобы выполнялось условие прочности необходимо диаметр трубы был не менее 630 мм.
4. Расчет усилия резания
Усилие резания определяется по формуле:
Fi - соответствующая площадь срезаемая i-м ковшом.
P = 14 кН или 1400 кг
Окружное усилие резания:
Рокр =Ррез +Рразгр +Рзапол +Рбок
Ррез усилие резания;
Рразгр усилие разгрузки = 006 Ррез = 006 14 = 840 Н
Рзапол усилие заполнения ковшей = 0
Рбок боковое усилие резания
Рбок = 03 Ррез = 013 14 = 42 КН
Рокруж = Ррез + Рзап + Рбок = 14 + 42 + 084 = 1904 кН
Тип хода - гусеничный гусениц - две. Ходовая часть экскаватора состоит из рамы с опорно-поворотным устройством и ходового механизма с приводами.
5.1. Ходовой механизм с приводами
Ходовая тележка включает две продольные балки с опорными катками (по пять катков с каждой стороны) левую и правую приводные звездочки 8 натяжные катки 9 поддерживающие катки 10 гусеничные цепи 11 механизмы натяжения гусеничных цепей и приводы.
Два параллельных ряда шарнирно соединенных между собой траков гусеничной цепи образуют дорожки качения опорных катков. Одновременно с помощью приводной звездочки гусеничная цепь передает тяговое усилие. Опорные и поддерживающие катки на бронзовых втулка вращаются на неподвижных осях закрепленных на балке. Натяжение катки на бронзовых втулка посажены на хвостовиках общей оси которая может перемещаться по направляющим балкам.
Приводные звездочки посажены на ведущих полуосях. После натяжения гусеничной цепи ось фиксируется распорной трубой и набором прокладок относительно специального упора расположенного внутри балки.
В целя повышения маневренности машины каждая ветвь гусеничной цепи снабжена отдельным приводом.
Каждый привод цепи включает редуктор типа РМ-650 с приводным электродвигателем 13 (марки 4А250М4УЗ мощностью - 90 кВт) и две зубчатые пары 15 16 (выходная пара сдвоенная). Электродвигатель тормоз и зубчатые пары закрываются кожухами. Электродвигатель с редуктором соединяются посредством кулачковой муфты. В приводе применен тормоз ТКТ-300.
Общее передаточное число трансмиссии гусеничного привода составляет 36225.
5.2. Тяговый расчет механизма передвижения экскаватора
Условие передвижения экскаватора:
где Тс max максимальная сила тяги
Wn сопротивление передвижению
где G сила тяжести = 150т =1500 кН
Vx = 5 м мин - скорость экскаватора = 008 мс
tр = 4с время разгона
Wпод - сопротивление подъему
где α = 5° угол подъема
Wk сопротивление качению по грунту
где к = 15 коэффициент конструкции гусеницы
п = 2 число гусениц;
b = 1 м ширина гусеницы
L = 35 длина гусеницы
Рф фактическое давление на грунт
h глубина продавливания грунта гусеницами
Ро коэффициент сопротивления грунта =13
D = 096 м диаметр колеса
Тяговое условие выполняется.
Максимальная мощность привода хода:
Для обеспечения мощности выбираем 2 двигателя марки 4А250М4УЗ
6. Пересчет мощностных характеристик привода роторного колеса поворота платформы приемного и отвального конвейеров
6.1. Мощность привода роторного колеса
где γ плотность грунта в ковше = 178 тм
nk = число ковшей = 8;
Рок = окружное усилие = 1905 кН
Vk =15 мс окружная скорость ротора
q = емкость ковша = 013 м3
Выбираем двигатель марки 4А250М4УЗ
6.2. Мощность привода поворота платформы
Lб 122 длина стрелы ротора
r = 15 радиус ротора
f = 05 эксцентриситет
6.3. Мощность привода приемного и отвального конвейеров
P1 = 22 кВт; (см. расчет ленточного конвейера отвального транспортера)
6.4. Суммарная установочная мощность
P = P1 + P2+ Р3+ Р4+ Р5= 90 + 90 + 90+90 + 44 = 404 кВт
7. Расчет ленточного конвейера отвального транспортера
Транспортируемый груз огнеупорное сырье.
Требуемая производительность конвейера 315 м3ч = 630 тч
Длина конвейера 14 м.
Крупность частиц груза а= 160мм.
Угол наклона конвейера 20°.
Насыпная плотность 2 тм3
Угол внутреннего трения φ =40°
Угол наклона боковых роликов α =30°
Скорость движения ленты 3мс.
Определение ширины ленты
Проверяем ленту по гранулометрическому составу для рядовых грузов получаем:
В соответствии со стандартом лента должна иметь ширину 800 мм так как меньшее значение приведен к перегрузке ленты. Выбираем В=1000 мм. Существенное увеличение ширины ленты по сравнению с первоначальной расчетной требует пересчета скорости:
Снижение скорости благоприятно повлияет на увеличение срока службы ленты.
Определение параметров роликовых опор
Шаг роликовых опор выбран постоянным: для верхней ветви Lр= 13 м для нижней Lp1 = 3 м. Для обеих ветвей принимаем ролики среднего типа Др =133 мм.
Массы вращающихся частей трехроликовых mp и однороликовой m’p:
Расчет распределенных масс
Распределенные массы транспортируемого груза:
Вращающихся частей опор верхней ветви:
Вращающихся частей опор нижней ветви:
Определение по формуле:
где 1 = 6 мм - толщина рабочей обкладки (см.стр.96[3]).
= 2 мм - толщина перерабатывающей обкладки.
П = 11 мм - толщина прокладки с резиновой прослойкой из полиамидных нитей (см.табл.21[3]).
IН = 5 — число прокладок (взято максимально возможное значение из рекомендуемого ряда (стр.95 [3])).
Распределенная масса ленты:
Выбор коэффициентов и определение местных сил сопротивления движению ленты
При эксплуатации в средних условиях коэффициенты сопротивления на рядовых роликовых опорах: для верхней ветви Wp =0025 для нижней Wx =0022. Соответственно на натяжном барабане с углом поворота 180° Wпз =006.
Сила сопротивления в пункте загрузки:
где fл=063 fб=05 коэффициенты внешнего трения груза по резиновой ленте и по стальным бортам.
V1 — проекция составляющей средней скорости струн материала на направлении ленты.
КБ — коэффициент бокового давления груза на бортовые направляющие.
Коэффициент бокового давления определяют по формуле:
Определение точек с наименьшим натяжением ленты
Необходимость этого определения связана с характером настоящего расчета (проектного) предусматривающего выявление значения тягового коэффициента и схемы привода.
Наименьшее натяжение ленты может быть только в точка 1 и 5
При выполнении условия ограничения стрелы провеса для нижней ветви:
Натяжение S4 является наибольшим необходимым для определения числа прокладок РТКЛ.
где Сп = 9 коэффициент запаса прочности
Кр = 100 Нмин — предел прочности для ткани из комбинированных нитей ТА-100 с толщиной прокладки Бп = 11мм
Запас прочности ленты:
Определение тягового коэффициента мощности двигателя
При m =04 и где L - угол обхвата где L угол обхвата приводного барабана.
Необходимая мощность привода:
где К3=11 коэффициент запаса мощности
γо =03 КПД передач привода γб =094 - КПД барабана.
Принимаем электродвигатель серии 4А - 4А 600М4УЗ номинальная мощность - 22 кВт число оборотов - 1000 обмин.
8.Конструкция кабины
Основное назначение кабины для членов экипажа роторного экскаватора - защита людей от внешней Среды и создание для членов экипажа микроклимата благоприятного для работы под внешней средой подразумевается температура воздуха отличающаяся от нормальной для человека (18-22 С) ветер осадки пыль.
Лучше всего отвечают основным требованиям кабины полностью изолированные от внешней Среды с аппаратурой для создания микроклимата (кондиционерами) и с надлежащей звуко- и виброизоляцией. Разумеется создание таких кабин обусловлено повышенными экономическими расходами и созданием специального оборудования. Заимствование кабин у других машин например автомобилей или тракторов не дает ожидаемого эффекта так как работа экипажа экскаватора отличается своей спецификой. Внешние очертания кабины обусловлены использованием максимальных удобств экономии материала и композиции конструкции.
Создание микроклимата в кабине при минимальных энергетических и экономически затратах достигается:
Эффективной виброизоляцией кабины от металлоконструкций при помощи резиновых амортизаторов.
Эффективной тепло и звукоизоляцией стен кабины с применением вспененного полистирола (пенопласт поропласта) или синтетического волокна.
Эффективной защитой от солнечны лучей при помощи козырьков-навесов над окнами кабины и двойной крыши с вентиляцией.
Системой принудительной и естественной вентиляции кабины.
Системой обогрева электрическими излучателями.
Создание внутри кабины микроклимата не допускающего сквозняков предусматривающего вентиляцию в летнее и обогрев в зимнее время достигается путем соответствующего исполнения стен двери крыши и пола. Внешние габариты и очертания помещения кабины обуславливаются размерами свободного пространства имеющегося на экскаваторе. Учитывая необходимость создания для машиниста экскаватора условий позволяющих ему максимально сосредоточиться и исключающих присутствие посторонних лиц которые могут отвлекать его в процессе работы рабочее помещение кабины разделено на две части:
- одноместная кабина управления 1 для машиниста экскаватора (кабина машиниста) в которой расположены панель управления 3 и сидение машиниста 4 панель 5 вспомогательных приборов которые не используются при непосредственном управлении работой экскаватора расположена сзади машиниста;
- вспомогательная кабина 6 в которой расположены вспомогательный агрегаты и приборы а также могут находиться другие члены экипажа.
Кабина машиниста 1 расположена на вспомогательной кабине 2 которая с целью виброизоляции от металлоконструкции экскаватора крепится на резиновых амортизаторах 3.
Конструкция нижней кабины приспособлена для вспомогательного обслуживания машины. Здесь располагается установка наддува кабин и фильтром 4 и обогревателем 5 печь для разогрева обедов шкафы для рабочей одежды стол для приема пищи слесарный верстак и ящики для инструментов. При необходимости здесь же устанавливается второй пульт управления экскаватором для стажировки машинистов стенд для ведения исследовательских работ.
Стены кабин выполнены двойными с улучшенной отражательной способностью снаружи. Крыша выполнена двойной полой с большим напуском со всех сторон для защиты внутрикабинного пространства от солнечных лучей двойная крыша способствует удержанию тепла в зимнее время. В летнее время открываются люки чем создается конвенционный поток воздуха охлаждающий крышу.
Двери выполняются задвижными с целью экономии площади на экскаваторе. Дверь должна обладать минимальной массой и управляться электроприводом с возможностью ручного управления. Это вызвано тем что при разворотах или переездах не исключены наклоны экскаватора затрудняющие открывать или закрывать массивную дверь.
Переднее стекло должно иметь наклон верхней части вперед благодаря чему оно меньше будет подвержено загрязнению от пыли и осадков. Стекла окон уплотнены с помощью резины что исключает создание сквозняков.
Важное значение в создании оптимальны санитарно-гигиенических условий труда имеют чистота хорошая освещенность правильный воздухообмен и температурно-влажностной режим допустимые уровни шумов и вибраций.
9.ЭЛЕКТРООБОРУДОВАНИЕ
Экскаватор Эр-315 получает питание от передвижной трансформаторной подстанции с трехфазным напряжением 380 В которое по кабелю подается через центровую цапфу непосредственно в распределительное устройство 04 кВт на вводе зажимы общего автоматического выключателя на 600А.
С этих же зажимов получают питание сварочный трансформатор трансформатор общего освещения и трансформатор котельного освещения. Сюда же подключается вольтметр контроля напряжения со шкалой 0 - 460В и автомат цепи управления.
Расположение электрооборудования.
Аппараты управления приводами экскаватора скомплектованы на четырех панелях которые установлены по продольной оси кабины электрооборудования с целью двустороннего обслуживания. Здесь же у торцевой стенки кабины размещены сопротивления 2-х двигателей хода и трансформатор освещения.
Электропривод роторного колеса и конвейеров.
Для привода роторного колеса применен короткозамкнутый двигатель типа МА-36-72-6 90 кВт 1000 обмин имеющий жесткую механическую характеристику. Выбор двигателя серии МА оправдан повышенной влажностью или запыленностью среды в которой работает экскаватор круглый год.
Отвальный и приемный конвейеры оборудованы двигателями 4А250М4УЗ 22 кВт 1000 обмин. Защищенного исполнения с самовентиляцией.
Блокировка от завалов грунтом перегрузочных мест осуществляется пуском конвейеров последовательно навстречу грузопотоку (вначале отвальный конвейер а затем приемный и роторное колесо).
Исходное положение схемы:
Автоматы 2А 5А и 6А включены на клеммы 3-4 цепи управления подано напряжение. Переключатель ЗУП находится во втором положении. При нажатии на кнопку «ПУСК» (ЗК) включается контактор О происходит запуск отвального конвейера. Блок контактами (6-4) он подготавливает цепь для включения контактора премного конвейера последний включается кнопкой 4К и в свою очередь блок-контактами (7-6) создает цепь контактора Р привода ротора. Последний запускается кнопкой 5К и транспортная линия экскаватора готова к приему грунта. Остановка всей линии осуществляется общей кнопкой «СТОП» (2К).
На случай ремонта опробования или наладки в схеме предусмотрено снятие блокировки универсальным переключателем ЗУП установленным на пульте управления. Максимальная и тепловая защита двигателей осуществлена комбинированным расцепителем встроенным в автоматические выключатели.
Электропривод хода экскаватора.
Гусеничный ходовой механизм экскаватора оборудован двумя асинхронными двигателями 4А250М4УЗ мощностью 90 кВТ 1000 обмин служащим для независимого привода левой и правой гусениц.
Выбор направления движения осуществляется двумя универсальными переключателями 1УП 2УП которые коммутируют цепи катушек статорных контакторов 1ВХ; 1НХ; 2ВХ; 2НХ. Запуск двигателей двухступенчатый с помощью педального командоаппарата 1КА в функции времени. Выдержка времени создается машинистом в зависимости от условий проходимости в забое.
Индивидуальный привод каждой гусеницы обеспечивает высокую' маневренность машины необходимую при селективной выемке. Остановка экскаватора осуществляется отпусканием педали командоаппарата 1КА которая возвращается в нулевой положение и разрывает цепь катушек статорных и роторных контакторов после чего включаются тормоза IT и 2Т. Педальный командоаппарат удобен в работе и позволяет перемещаться с различными скоростями что особенно важно при установочных операциях. Защита двигателей осуществлена автоматическими выключателями.
Проверка выбора электродвигателей приводов механизмов передвижения и поворота по обеспечению запаса по сцеплению и максимальному ускорению.
Электропривод механизмов передвижения необходимо проверить по запасу сцепления при пуске и торможении для наиболее неблагоприятных условий работы.
При этом должны удовлетворяться следующее условие:
Ксцеп = (Fприв(0+fmin))(Wn+FД)>1.1÷1.2
Fприв=008 МПа-давление на грунт
= 10 – коэффициент сцепления колеса с гусеницей.
Wn= 406кН - сопротивление передвижению.
Ксцеп =(0.08(1+0))40.6=1.97
Ксцеп =1.97>1.2 условие выполняется.
Мощность привода поворота платформы
Привод приемного и отвального конвейеров.
Проверка по перегреву.
По условиям тепловой нагрузки время пуска короткозамкнутых двигателей не должно превышать 3с.
Рр=[(G+Qn)·Vном(103Кn·мех·γn)]*[(α'·Vном3)+m)]
Для механизмов передвижения экскаваторов m=0 т.к. он взрывобезопасен.
Проводим проверку выбранного двигателя по потерям в роторе путем определения допустимого числа включений.
–потери в роторе двигателя допустимые статические и динамические.
Кз=1.15-1.25 рб=0.05
8. Заключение.doc
Список литературы.doc
Владимиров. Москва «машиностроение» 1967.
Совершенствование экскаваторных работ на карьерах. Ю.И. Беляков
В.М.Владимиров. Москва «Недра» 1974.
Исследование гидропривода рабочего оборудования роторного
экскаватора. Отчет по научно исследовательской работе.
Исследование объемного гидропривода роторного экскаватора
ШРС — 160. Отчет по научно исследовательской работе.
Анализ работы роторного экскаватора на добычи сырья огнеупорной промышленности. В.И. Сероштан. Украина Н.И.И.Н.Т.И. Киев 1970г.
Инструкция роторного экскаватора РЭ-120. Донецк. 1970г.
Технический проект ЭРГ-250. Чсов-Яр. 1969г.
Строительные машины. П.С. Гренкевич. Москва. «Машиностроение» 1975г.
Машины непрерывного действия. Р.Я. Зенков И. И.Иванов. Москва.
«Машиностроение» 1987г.
Определение линейных параметров роторного экскаватора.
В.И.Сероштан. ЦНИИТЭИ «Огнеупоруд». 1965г.
.Справочник технолога машиностроителя. А.Г.Косиловой Р.К.Мещерикова. Т-1 Т-2. Москва. «Машиностроение» 1986г. 12.Справочник молодого электросварщика. Э.К.Карамазов. Москва.
«Высшая школа » 1992г.
Механизация и автоматизация ПТРС работ. А.И. Головин. Методические указания. Калуга. «КФ МГТУ» 1981г.
Анализ влияния различных факторов на производительность роторных экскаваторов. В.И. Сероштан. Украина «ДонНИГРИ» 1970г.
5 Технологическая часть.doc
Назначение детали в узле.
Валы применяются для поддержания вращающихся деталей а главное для передачи крутящего момента.
В нашем случае вал используется в приводе отвального конвейера роторного экскаватора.
Определение годового объема выпуска.
Объем выпуска - это число изделий определенного наименования изготовляемых за планируемый промежуток времени.
Одно из основных характеристик является коэффициент Кзо (закрепленных операций) показывающий сколько операций выполняется за одном рабочем месте.
где Q =15 - количество операций;
Р =12 - количество рабочих мест.
Согласно ГОСТ 31108-74 производство будет относиться к крупносерийному.
Разработка маршрута механической обработки.
Эта задача так же как и проектирование маршрута для отдельной поверхности является многовариантной. Маршрут обработки детали представляет собой определенную последовательность выполнения операций. При установление общей последовательности выполнения операций необходимо:
Определить подготовительные базы.
Установить поверхности в последовательности обрабатываемой их точности.
Последняя обрабатывается наиболее точная поверхность.
Не совмещать черновые и чистовые переходы.
Если деталь подвергается термообработки то маршрут разбивается на 2 части: до термообработки и после так как возможны деформации.
Для деталей массового производства необходимо чтобы длительность операций была равна или кратна такту выпуска.
Выбранный маршрут подвергают экономическим расчетам.
При разработки операций решаются две основные задачи.
Обеспечение точности и качества обрабатываемой поверхности. 2.Получение высокой производительности (за счет уменьшения штучного времени)
Маршрут обработки вала.
0. Заготовительная (заготовку получить).
0. Фрезерно-центровальная (отрезать в размер сверлить центровочные
0. Токарная (точить поверхности 12).
5. Токарная (точить поверхности 12).
0. Термическая (термообработать до твердости 285 НБ).
0. Токарная (точить поверхности 123).
5. Токарная (точить поверхности 123).
0. Фрезерная ( отрезать в размер).
5. Токарная (нарезать фаски 12).
0. Фрезерная (нарезать шпоночный паз).
5.Фрезерная (нарезка шлицов).
0. Сверлильная ( сверлить 3 отверстия).
5. Резьбонарезная (нарезать резьбу в трех отверстиях).
Расчет операционных припусков и межоперационных размеров
рассчетно — аналитическим методом.
Этот метод заключается в том что промежуточный припуск на каждом технологическом переходе должен быть таким чтобы при его снятие устранялись погрешности обработки и дефекты поверхностного слоя полученные на предшествующих переходах а также для исключения погрешности установки заготовки.
Определение минимального припуска для поверхности вращения.
Rzi-1 высота неровностей профиля на предыдущем переходе.
hi-1 глубина дефектного слоя возникающего на предшествующем
- суммарное отклонение расположения поверхности на
предшествующем переходе рассчитывается по формуле
где к- отклонение оси детали от прямолинейности.
- длина заготовки до зажима.
Х - длина обрабатываемой части заготовки.
Максимальный припуск на обработку поверхности вала рассчитывается по формуле
Z max =2Zmin+Tdi-1+Tdi
Tdi-1 - допуск размеров на предшествующем переходе
Tdi - допуск размеров на выполнимом переходе.
Минимальный диаметр с учетом припуска рассчитывается по формуле:
- минимальный диаметр полученный на выполняемом переходе.
Максимальный диаметр с учетом припуска рассчитывается по
Расчет режимов резания выбор оборудования и режущего
Операция 020 токарная (черновая).
Скорость резания [м мин] при наружном продольном точение рассчитываем по эмпирической формуле:
Т = 45 [мин] - среднее значение стойкости инструмента (том 2 стр. 268).
t = 85 [мм] - глубина резания
s = 05 [мм] - подача (том 2 стр. 268 т - 13)
Cv = 350 - коэффициент скорости (том 2 стр. 269 т - 17)
m = 055 - показатель степени (том 2 стр. 269 т - 17)
х = 015 - показатель степени (том 2 стр. 269 т - 17)
у = 02 - показатель степени (том 2 стр. 269 т - 17)
kv- поправочный коэффициент рассчитывается по формуле:
Kv = KmvКт Kuv = 13109 = 117.
Kmv = 13 - коэффициент учитывающий влияние материала заготовки (том 2 стр. 263
Kuv =1 - коэффициент учитывающий влияние материала инструмента (том 2 стр.
Knv = 09 - коэффициент состояния поверхности (том 2 стр. 263 т - 5)
Частота вращения n[обмин] заготовки определяется по формуле:
D = 925 [мм] - диаметр заготовки
V = 896 [ммин] - скорость резания.
Стандартное значение nст=315[обмин]
Фактическая скорость резания.
Силу резания принято раскладывать на составляющие силы направленные по осям координат станка: тангенсальную Pz радиальную Ру осевую Рх. При наружном продольном точение эти силы рассчитываются по формуле:
Постоянная Ср и показатели степени для конкретных условий обработки для каждой из составляющих сил резания берем из (том 2 стр. 273 т-22).
Кр- поправочный коэффициент рассчитывается по формуле:
Kp=KmpKфрКурКλрКrp=111111
Кm = 11 - коэффициент учитывающий качество обрабатываемого материала заготовки (том 2 стр. 264).
Поправочные коэффициенты учитывающие влияние геометрические параметры режущей части инструмента на составляющие сил резания берем из ( том 2 стр. 275 т - 23) для углов φ° = 45° γ0 =0° λ° = 0° г = 2 [мм].
Pz = 10 300 851 03075 89601511 = 572248[Н]
Pr = 10243 8509 0306896-0311 = 233733[Н]
Px =103398510305896-0411 = 233733[Н]
Станок: токарно-винторезный 16К50П
Операция 040 токарная (чистовая).
где: T = 45 [мин] - среднее значение стойкости инструмента (том 2 стр. 268).
t = 25 [мм] - глубина резания
s = 03 [мм] - подача (том 2 стр. 268 т - 13)
Cv = 420 - коэффициент скорости (том 2 стр. 269 т - 17)
m = 02 - показатель степени (том 2 стр. 269 т - 17)
Kv- поправочный коэффициент рассчитывается по формуле:
Ky=Kmv-Knv-Kuv = 13 -1-09 = 117.
Kmv = 13 - коэффициент учитывающий влияние материала заготовки
(том 2 стр. 263 т - 1)
Kuv =1 - коэффициент учитывающий влияние материала
инструмента ( том 2 стр. 263 т - 6)
Knv = 09 - коэффициент состояния поверхности ( том 2 стр. 263 т -5)
Частота вращения n [обмин] заготовки определяется по формуле:
D = 908 [мм] - диаметр заготовки
Стандартное значение nст=800 [обмин].
Kp=KmpKфрКурКλрКrp=11111
Kmp = 11 - коэффициент учитывающий качество обрабатываемого материала заготовки (том 2 стр. 264).
Поправочные коэффициенты учитывающие влияние геометрические параметры режущей части инструмента на составляющие сил резания берем из ( том 2 стр. 275 т - 23) для углов
φ° = 45° γ° =0° λ0 = 0° г = 2 [мм].
Pz =103008.510.30.7589.6-0.151.1=5722.48[H]
Ру = 102438.50.90.30.689.6-0.31.1=2337.33[H]
Рх =103398.510.30.589.6-0.41.1=2337.33[H]
Станок: токарный 16К50П
Операция фрезерная 050 (отрезная).
Для отрезания заготовки в размер выбираем отрезную фрезу ГОСТ 2679 -73.
Скорость резания. Рассчитывается по формуле:
В = 5[мм] - ширина фрезирования
D = 315[мм] - диаметр фрезы
t = 20[мм] - глубина резания
Sz= 0028 [ммоб] - подача на 1 зуб фрезы
Т = 150[мин] - период стойкости инструмента (11 том 2 стр. 290
Су= 53 - скоростной коэффициент (11 том 2 стр. 287 т - 39)
q = 043 - показатель степени (11 том 2 стр. 287 т-39)
х = 03 - показатель степени (11 том 2 стр. 287 т - 39)
у = 02 - показатель степени (11 том 2 стр. 287 т - 39)
u= 02 - показатель степени (11 том 2 стр. 287 т - 39)
р = 01 - показатель степени (11 том 2 стр. 287 т - 39)
m = 02 - показатель степени (11 том 2 стр. 287 т - 39)
kv - поправочный коэффициент рассчитывается по формуле:
kmv=l3 - коэффициент учитывающий влияние материала заготовки
knv=09 - коэффициент учитывающий состояния поверхности
kuv=l - коэффициент учитывающий влияние материала инструмента.
Частота вращения фрезы.
V = 979 [ммин] — скорость резания
D = 315 [мм] - диаметр фрезы.
Стандартное значение числа оборотов принимаем nc=100[обмин]
Фактическая скорость.
Расчет силы резания.
Главным составляющим силы резания при фрезеровании - окружная сила которая рассчитывается по формуле:
В = 5 [мм] - ширина фрезерования
D = 315 [мм] - диаметр фрезы
п = 100 [обмин] - частота вращения фрезы
sz = 0028 [ммоб] - подача на 1 зуб фрезы
t = 20 [мм] - глубина резания
z=160 - количество зубьев фрезы
Cv= 261 - коэффициент резания (11 том 2 стр. 287 т - 41)
х = 09 - показатель степени (11 том 2 стр. 287 т - 41)
у = 08 - показатель степени (11 том 2 стр. 287 т - 41)
u= 11 - показатель степени (11 том 2 стр. 287 т - 41)
q = 11 - показатель степени (11 том 2 стр. 287 т - 41)
w= 01 - показатель степени (11 том 2 стр. 287 т - 41)
кр= 11 - поправочный коэффициент.
Крутящий момент шпинделя.
Фрезерный широко универсальный 6Р81.
Операция фрезерная 060 (нарезка шпоночного паза 2штуки.)
Для нарезания шпоночного паза выбираем шпоночную фрезу ГОСТ 9140-78.
В = 24 [мм] - ширина фрезирования
D = 24 [мм] - диаметр фрезы
t = 8 [мм] - глубина резания
Sz= 036 [ммоб] - подача на 1 зуб фрезы
Т = 90 [мин] - период стойкости инструмента (11 том 2 стр. 290
Cv=12 - скоростной коэффициент (11 том 2 стр. 287 т - 39)
q = 03 - показатель степени (11 том 2 стр. 287 т - 39)
у = 025 - показатель степени (11 том 2 стр. 287 т - 39)
u=0 - показатель степени (11 том 2 стр. 287 т - 39)
р = 0 - показатель степени (11 том 2 стр. 287 т - 39)
m = 026 - показатель степени (11 том 2 стр. 287 т - 39)
kv=kmvknvkuv=1.30.91=1.17
V = 137 [ммин] - скорость резания
D= 24 [мм] - диаметр фрезы. Стандартное значение частоты вращения принимаем nc=200[обмин].
В = 24 [мм] - ширина фрезерования
n = 200 [обмин] - частота вращения фрезы
sz = 0036 [ммоб] - подача на 1 зуб фрезы
z = 2 - количество зубьев фрезы
Cv= 125 - коэффициент резания (11 том 2 стр. 287 т - 41)
х = 085 - показатель степени (11 том 2 стр. 287 т - 41)
у = 075 - показатель степени (11 том 2 стр. 287 т - 41)
q = 073 - показатель степени (11 том 2 стр. 287 т - 41)
w= -013 - показатель степени (11 том 2 стр. 287 т - 41)
Вертикально-фрезерный 6Т104
Операция 065 (фрезерная).
Нарезка шлицов дисковой фасонной фрезой марки Р6М5..
В = 24[мм] - ширина фрезерования
D = 28[мм] - диаметр фрезы
t = 10[мм] - глубина резания
Sz= 0037 [ммоб] - подача на 1 зуб фрезы
Cv=53 - скоростной коэффициент (11 том 2 стр. 287 т — 39)
q = 045 - показатель степени (11 том 2 стр. 287 т - 39)
х = 03 - показатель степени (11 том 2 стр. 287 т - 39)
u = 01 - показатель степени (11 том 2 стр. 287 т - 39)
m = 033 - показатель степени (11 том 2 стр. 287 т - 39)
V = 112 [ммин] - скорость резания
D= 28 [мм] - диаметр фрезы.
Стандартное значение частоты вращения принимаем nc=160[обмин].
D = 28[мм] - - диаметр фрезы
п=160 [обмин] - частота вращения фрезы
sz = 0037 [ммоб] - подача на 1 зуб фрезы
t=10[мм] - глубина резания
Сv= 47 - коэффициент резания (11 том 2 стр. 287 т - 41)
х = 086 - показатель степени (11 том 2 стр. 287 т - 41)
у = 072 - показатель степени (11 том 2 стр. 287 т - 41)
u = 01 - показатель степени (11 том 2 стр. 287 т - 41)
q = 086 - показатель степени (11 том 2 стр. 287 т - 41)
w= 0 - показатель степени (11 том 2 стр. 287 т - 41)
Вертикально-фрезерный 6Т104.
Операция 070 (сверлильная).
При сверлении выбираем сверло (Р6М5) ГОСТ 2092 — 77.
D = 14[мм] - диаметр сверла.
где: S = 023 [ммоб] - подача сверла (11 том 2 стр. 277 т - 25)
Т = 45 [мин] — период стойкости инструмента (11 том 2 стр. 279
Cv=98 - скоростной коэффициент (11 том 2 стр. 279 т - 28)
q = 04 - показатель степени (11 том 2 стр. 279 т - 28)
у = 05 - показатель степени (11 том 2 стр. 279 т - 28)
m = 02 - показатель степени (11 том 2 стр. 279 т - 28)
kv_- поправочный коэффициент рассчитывается по формуле:
kmv= 13 - коэффициент учитывающий влияние материала заготовки (11 том 2 стр. 278 т - 3)
кnv= 09 - коэффициент учитывающий состояния поверхности (11 том 2 стр. 263 т - 6)
kuv= 1 - коэффициент учитывающий влияние материал инструмента (11 том 2 стр. 280 т - 31)
Частота вращения n [oбмин] заготовки определяется по формуле:
D = 14 [мм] - диаметр сверла
V = 356 [ммин] - скорость резания.
Стандартное значение nст=800 [обмин].
Крутящий момент который рассчитывается по формуле:
D=14 [мм] - диаметр сверла
n = 800 [обмин] -частота вращения сверла
s = 023 [ммоб] - подача на сверла
См= 00345 - коэффициент резания (11 том 2 стр. 281 т-32)
у = 075 - показатель степени (11 том 2 стр. 281 т — 32)
q = 073 - показатель степени (11 том 2 стр. 281 т - 32)
кр= 11 - поправочный коэффициент (11 том 2 стр. 264т-9)
Осевая сила рассчитывается по формуле:
Р = 10 Ср Dq sY kp = 10 68 141 0230.7 11 = 374317[H].
D = 14 [мм] - диаметр сверла s = 023 [ммоб]- подача на сверла
Ср= 68 - коэффициент резания (11 том 2 стр. 281 т - 32)
у = 07 - показатель степени (11 том 2 стр. 281 т - 32)
q = 1 - показатель степени (11 том 2 стр. 281 т - 32)
Вертикально-сверлильный 2Г175М.
Операция 075 (резьбонарезная).
Для нарезания резьбы выбираем метчик (Р6М5) ГОСТ 3266-81.
D= 16 [мм] - диаметр нарезаемой резьбы
S = 023 [ммоб] - подача сверла (11 том 2 стр. 277 т - 25)
Т = 90 [мин] - период стойкости инструмента (11 том 2 стр.279т - 28)
Cv= 410 - скоростной коэффициент (11 том 2 стр. 279 т - 28)
q = 12 - показатель степени (11 том 2 стр. 279 т - 28)
m = 09 - показатель степени (11 том 2 стр. 279 т — 28)
kv=kmvknvkuv=0911=09
kmv = 09 - коэффициент учитывающий влияние материала заготовки (11 том 2 стр. 278 т - 3)
knv= 1 - коэффициент учитывающий состояния поверхности (11 том 2 стр. 263 т - 6)
D = 16 [мм] - диаметр метчика
V = 35(6 [ммин] - скорость резания.
Стандартное значение nст=630 [обмин].
МКР =CmDqsr kp =0027161.4 З1'.511 = 104.77[Нм].
D=16 [мм] - диаметр нарезаемой резьбы
См= 0027 - коэффициент резания (11 том 2 стр. 296 т-51)
у = 14 - показатель степени (11 том 2 стр. 296 т - 51)
q = 15 - показатель степени (11 том 2 стр. 296 т - 51)
кр= 11 - поправочный коэффициент (11 том 2 стр. 264т-9).
Операция 080 (шлифовальная).
Для обработки заготовки выбираем шлифовальный круг типа ПП с Н - 50 [мм] ширина профиля так как шлифование врезное то подача s будет радиальной.
Мощность при врезном шлифовании рассчитывается по формуле:
N = CNVзrsxpdqbz = 014 3508 00030810002501 = 29[кВт].
d = 100 [мм] - диаметр заготовки
V3 = 35 [ммин] - скорость вращения заготовки (11 то2стр.301)
s = 0003 [ммоб] - радиальная подача
Cn= 014 - коэффициент резания (11 том 2 стр. 301)
х = 08 - показатель степени с
q = 02 - показатель степени (11 том 2 стр. 301)
z = 1 - показатель степени (11 том 2 стр. 301).
Кругло шлифовальный станок ЗУ12УА.
Расчет станочного приспособления
При фрезеровании принимаем усилие зажима равным 4000Н. Определяем необходимое давление в цилиндре.
где QШТ=400 Н осевая сила на штоке;
Ду= 130 мм. диаметр пневмоцилиндра;
γ =085÷090 - кПд пневмоцилиндра.
Вследствие того что в магистрали давление воздуха 4-5 атм. то перед приспособлением должен быть понижающий редуктор.
Конструкция станочного приспособления.
При разработке технологического процесса необходимо правильно выбрать приспособление которое должно способствовать повышению производительности точности обработки улучшению условий труда.
В отверстие неподвижной оси 8 тисков встроен пневмоцилиндр 11 с которым винтами соединен полый поворотный корпус 12. К корпусу прикреплен распределительный кран 6 с рукояткой 7 для переключения золотника при поочередном выпуске сжатого воздуха в верхнюю или нижнюю полость пневмоцилиндра 11 и выпуска воздуха в атмосферу. На верней части поворотного корпуса 12 закреплена плита 5.
Сжатый воздух поступает в верхнюю полость пневмоцилиндра 11 и перемещает поршень 10 со штоком вниз при этом длинное плечо рычага 2 находящееся в пазу штока опускается а короткое перемещает подвитую губку вправо и деталь зажимается.
Во время поворота рукояти 7 завиток крана 6 пропускает воздух в нижнюю полость пневмоцилиндра 11. Сжатый воздух действуя на поршень 10 перемещает его со штоком 9 вверх. При этом длинное плечо рычага 2 поднимается вверх а короткое отводит губку 1 влево и деталь разжимается.
Сила зажима 392 кН давление 039 МПа.
3.Исследовательская часть.doc
Стенды для исследования рабочего процесса роторных экскаваторов
Работа роторных экскаваторов на отечественных карьерах характеризуется разнообразием горно-геологических условий. При экскавации рыхлых и липки пород существенное влияние на работу ротора оказывает процесс разгрузки. При разработке вязких крупнотрещиноватых и крепких углей и пород работа осложняется появлением повышенной кусковатости и значительными колебаниями нагрузок действующих на рабочее оборудование. В этих условиях необходимая эффективность роторных экскаваторов может быть достигнута только в результате оптимизации конструктивно-кинематических и силовых параметров ротора а также конструктивных решений его элементов.
Совершенствование методов расчета параметров и определение действующих нагрузок требует не только теоретических разработок но и широких экспериментальных исследований. При этом обоснование рабочих гипотез принятых при построении расчетных схем рабочего процесса возможно как правило при помощи экспериментальных исследований выполняемых на строгих методических. Выполнение экспериментальных работ подобного рода на действующем оборудовании затруднено рядом обстоятельств: разнообразием грунтовых условий ограниченными возможностями изменения конструктивно-кинематических параметров оборудования сложными условиями фиксации ряда факторов характеризующих рабочий процесс экскаватора и др.
В связи с этим особое место занимают исследования рабочего процесса роторных экскаваторов на специальных экспериментальных стендах. Такие стенды позволят исследовать следующие основные вопросы рабочего процесса и выбора оптимальных конструктивных решений рабочего оборудования роторных экскаваторов.
Спроектированы и изготовлены два роторных стенда:
Стенд для исследования процесса
Диаметр по режущим кромкам м
Диаметр внутреннего обода м.
Ёмкость одного коша м3
Общее передаточное число привода
Пределы регулирования скорости вращения обмин
Диапазон изменения угла установки кромки запорного сектора град
Максимальная подача ротора на забой без передвижки пути м
Двигатель привода ротора
Номинальная мощность кВт
Номинальное число оборотов обмин.
Механизм передвижения
Номинальная мощность двигателя кВт
Номинальное число оборотов двигателя обмин
Передаточное число редуктора
Пределы регулирования скорости передвижения ммин
Ширина рельсовой колей м
Максимальная производительность по конвейеру м3ч
Общий вес роторного стенда кН
Первый стенд предназначен для исследования вопросов связанных с выбором конструктивно-кинематических параметров ротора и конструкции ковшей. Поэтому при его создании была предусмотрена возможность широкого регулирования скорости ротора и его боковой подачи изменения углов установки кромки запорного сектора и конструкции днища ковшей. При исследовании предусматривалась возможность киносъёмки процесса разгрузки как в плоскости вращения ротора со стороны конвейера так и в контуре ковша с применением специального устройства перемещающего киноаппарат синхронно с применением спец-устройства перемещающего киноаппарат синхронно ковшу от момента заполнения последнего до полного опорожнения.
Конструкция стенда включает в себя ротор с приводом конвейер верхнюю и нижнюю рамы. Бескамерный ротор с боковой гравитационной разгрузкой установлен на верхней раме на неподвижной оси и приводится во вращение от двигателя через редуктор и венцовое зубчатое колесо. Привод ротора выполнен по системе Г-Д. Редуктор привода ротора со стороны электродвигателя опирается на пружинную подставку а со стороны выходного вала подвешен на кронштейнах. При работе ротора верхняя рама жёстко соединяется с нижней посредством стопорных болтов. Нижняя рама опирается на две двухосные тележки перемещающиеся вдоль забоя по рельсовому пути.
Передвижение стенда вдоль забоя (боковая подача ротора) осуществляется механизмом передвижения который находится на отдельной тележке присоединённой к нижней раме стенда с правой стороны. Механизм передвижения - канатного типа включает в себя систему Г-Д редуктор и приводной барабан с тросом концы которого жестко закреплены на противоположных концах рельсового пути.
Управление электроприводами стенда сосредоточено в электрошкафах а приборы управления и контроля установлены на общем пульте в кабине. Электропитание подводится кабелем подвешенным к тросу который натянут между стойками установленными по концам рельсового пути.
Рельсовый путь состоит из трех участков два из которых общей протяженностью 25 м. расположены по фронту забоя и являются рабочими а третий вынесен за пределы забоя и через катки опирается на поперечную колею по которой он вместе со стендом может подаваться на забой при помощи специальных стяжек Участки пути во время работы стенда соединены между собой обычными рельсовыми скреплениями.
Разрабатываемый забой представлен песчаноглинистым грунтом с естественной влажностью 9—13%. Выполненные исследования позволили детально изучить процесс разгрузки роторного рабочего органа обосновать расчетную схему процесса для грунтов различного типа и рекомендовать рациональную конструкцию ковшей при экскавации пород склонных к налипанию.
На втором стенде исследуются величины и характер внешних нагрузок на рабочем оборудовании роторного экскаватора в зависимости от совокупности действующих факторов. Принципиальной особенностью этого стенда является возможность замера суммарных составляющих усилия копания с помощью подвески вала ротора на тензометрических опорах. Кроме того ковши крепятся к ротору специальными мерными устройствами выполненными в виде промежуточных тензометрических рамок. В этом случае замена ковшей или установка каких-либо дополнительных режущих устройств не потребует перемонтажа измерительных элементов и исключает возникающие при этом дополнительные ошибки измерения. Установка ковшей позволяет фиксировать нагрузки на всех ковшах находящихся одновременно в контакте с забоем. Металлоконструкция ротора выполнена таким образом что благодаря сменным разъемным обечайкам возможно изменение числа ковшей без демонтажа установки ротора. Принципиальная схема компоновки стенда аналогична предыдущей.
Механизм привода ротора смонтирован на специальной раме и установлен по статически определимой схеме. Один конец через подшипники опирается на вал ротора другой через упругую подвеску и мерный элемент — на верхнюю раму. Верхняя подвижная рама опирается на нижнюю через катки на которых осуществляется подача ротора на забой. Привод подачи как и в разгрузочном стенде ручной. В период работы верхняя рама при помощи четырех аутригеров и тяг жестко связывается с рамой ходового устройства включающего в себя нижнюю раму опирающуюся на ходовые колеса и привод аналогичный приводу хода разгрузочного стенда. Рельсовый путь имеет колею шириной 27 м. что в комплексе с балластным пригрузом установленным на верхней и нижней рамах обуславливает необходимую устойчивость всего агрегата. Перемещение всего стенда на забой осуществляется так же как и перемещение роторного разгрузочного стенда.
Исследование на стенде производится в специальном забое (см. рис) представляющем собой бетонное ложе с опорной стенкой которое заполняется боками из углецементной массы. Общая длина рабочей части забоя 40 м глубина блоков-6 м а высота может достигать 5 м. Варьируя процентным содержанием угля и цемента можно создавать забой состоящий по фронту из 10 блоков различной крепости.
Необходимые исследования можно поводить также на блоках включающих пропластки разной толщины а также подверженных трещеноватости. Последняя создаётся при заливке блоков посредством введения полихлорированных прокладок между очередной массой углецемента.
Регулировать интенсивность трещеноватости и коэффициент структурного ослабления блока можно установкой на различном расстоянии друг от друга прокладок а также изменением площади отверстия в прокладках через которые схватываются два очередных слоя. При заливке первых углецементных блоков использован уголь марки АРШ и цемент марок 200-400.
Проведение широких исследований на созданных стендах будет способствовать дальнейшему совершенствованию конструкций и методов расчета ротор экскаваторов.
Схема работы в углецементном забое (размеры в метрах): 1 - рельсовый путь; 2 - роторный стенд; 3 - устройство для подачи стенда на забой; 4 - углецементный блок; 5 - опорная стенка.
7. Экономический раздел.doc
Общая характеристика и назначение объекта
Роторный экскаватор - машина непрерывного действия предназначенная для добычи огнеупорного сырья. Экскаватор работает в карьере круглогодично.
Технико-экономические характеристики объекта
Производительность - 315 м3час
Технико-экономические характеристики базового варианта:
Расчёт капитальных затрат.
Капитальные затраты на внедрение новой техники - это единовременные затраты связанные с осуществлением технического решения. В зависимости от характера этих решений состав капитальных затрат может быть различным.
К=Кэкскаватора+Ксопутствующие
Кэкскаватора - капитальные затраты по экскаватору
Ксопутствующие – сопутствующие затраты.
Кэкскаватора = Ц+Км+Ктр+Кзч
Ц – цена единицы оборудования
Км- затраты на монтаж
Ктр- затраты на транспортировку
Кзч- затраты на запчасти.
Капитальные затраты на модернизацию экскаватора ЭРГ-250 до производительности 315 м3час
Расчет себестоимости модернизированной машины.
Себестоимости модернизированной машины определяется по формуле:
Sмодернизированной =Sбаз.-Sэл.баз.+Sэл.модерн.
Sмодернизированной =Sбаз.-Sэл.баз.+Sэл.модерн = 6000000-1500000 – 10000 – 600000 – 70000+ 1560000 + 11600 + 800000 +90000 + 500000+100000 =6881600 руб.
Стоимость базовых элементов:
Sбаз=6000000 – себестоимость экскаватора ЭРГ-250
SМеталлоконструкция = 1500000 руб.
SЭлектродвигатель = 600000 руб.
SТормоза = 70000 руб.
Расчет эксплуатационных затрат.
При расчёте экономической эффективности транспортных средств и средств механизации под эксплуатационными затратами понимаются удельные издержки связанные с эксплуатационным обслуживанием экскаватора.
Определяем технологическую себестоимость.
Стех=Сз+Сэл.эн+Ср+Са+Свсп.
Сз = К1К2Fэф. rтар. Nсп.
Fэф- эффективный годовой фонд рабочего времени.
rтар – тарифная ставка.
Nсп. – численность рабочих.
Сзбаз =1.1511412228810=360000 руб.
Сзмод=11511412305110=480000 руб.
Затраты на электроэнергию
Сэл = Цэл Ny Fд А 12где
Fд - действительный фонд работы машины в год
Цэл - цена за 1 кВт эл.энергии = 07 руб. т.к. привод экскаватора питается энергией от трансформатора который в свою очередь работает на дизельном топливе.
- коэффициенты использование Э.Д. по мощности и времени.
Ny - установочная мощность двигателей (суммарная) = 360 кВт и 320 кВт
Сбэл =07 320 3456 4025= 774144 тыс.руб
Смэл = 07 360 3456 4025=870912 тыс.руб
Транспортные расходы
Отчисления на амортизацию
где ЦП – первоначальная стоимость машин (базового и модернизированного варианта соответственно)
Но - 26% - норма амортизации
где -коэффициент учитывающий ремонты
Общие эксплуатационные затраты базового и модернизированного вариантов
Затраты на единицу производительности
где - эксплуатационные затраты
Р – производительность.
Расчет показателей экономической эффективности
Годовая экономия на единицу производительности:
Годовая экономия при производительности 315 м3ч:
Интегральная экономия:
где - срок службы экскаватора.
Экономический эффект:
где - капитальные затраты на модернизацию.
Сравнительная таблица
Технические показатели
Производительность м3час
Экономические показатели
Цена металлоконструкции руб.
Цена электродвигателя руб.
Стоимость монтажа руб.
Расчеты показывают что применение нового модернизированного экскаватора приводит к экономии средств при закупке материалов а также к экономии эксплуатационных затрат на протяжении всего периода эксплуатации тем самым обеспечивая экономический эффект 149035 тыс. руб. при сроке окупаемости 3717 года.
1.Введение.doc
В металлургии важное место занимает производство огнеупорных изделий (своды печей огнеупорный кирпич и т.п.). Для их изготовления требуется огнеупорное сырье. Месторождение огнеупорного сырья представляет собой сложно структурный пласт. Эффективная разработка такого пласта достигается только с применением роторных экскаваторов.
В связи с этим возникает актуальная проблема модернизации роторных экскаваторов
2.Аналитический обзор.doc
Экскаваторы – один из основных механизмов для выполнения строительных работ. Существует много разных видов экскаваторов: с малой вместимостью ковша экскаваторов на автошасси гидравлических 3-й размерной группы гусеничные экскаваторы и другие. Современный экскаватор - это не просто землеройная машина а многофункциональный комплекс способный выполнять очень широкий спектр общестроительных и дорожных работ а также мелиоративных металло- и лесозаготовительных мусороперерабатывающих сельскохозяйственных и т.д. Гусеничные экскаваторы успешно работают на сносе зданий и при аварийно-спасательных работах.
Роторные экскаваторы относятся к экскаваторным машинам непрерывного действия. Рабочим органом такого экскаватора является роторный ковш то есть непрерывно вращающийся барабан с размещенными на нем ковшами которые в одной точке цикла вращения зачерпывают сыпучие породы а в противоположные выгружают их на транспортерную ленту по которой породы перемешаются к отгрузочному сектору.
Диаметры роторных барабанов могут колебаться от двух до восемнадцати метров. Большинство роторных экскаваторов оснащаются гусеничным ходом а особенно крупные экскаваторы имеют железнодорожный ход.
Производительность роторного экскаватора может достирать пятнадцати тысяч кубометров в час. Роторные экскаваторы в большинстве случаев работают в карьерах для добычи рыхлых пород и пород средней крепости. Роторные экскаваторы предназначенные для карьерной добычи угля способны создавать большое усилие резания.
Условия залегания глин и каолинов определяют специфику работы добычных роторных экскаваторов и особые требования к их конструкции. Должна быть обеспечена полнота выемки сортовых слоев марок огнеупорных глин и каолинов с минимальным засорением разубоживанием и технологическими потерями особенно на контактах с почвой и кровлей а также при удалении прослоек песка и некондиционных слоев.
Предлагается следующая классификация основных месторождений огнеупорного сырья:
Сложное строение пласта с 4-6 и более литологическими разновидностями сложным напластованием и переменной мощностью слоя.
Менее сложное строение пласта с 2-4 литологическими разновидностями.
Простое строение пласта полезного ископаемого с одним или двумя литологическими разновидностями выдержанной мощности и преимущественным распространением одного сорта.
Селективная разработка пласта огнеупорного сырья с применением роторных экскаваторов в зависимости от сложности строения продуктивной толщи может осуществляться горизонтальными стружками вертикальными однорядными стружками вертикальными многорядными стружками.
На месторождениях первых двух типов разработку забоя ведут роторными экскаваторами горизонтальными стружками так как этот способ является наиболее приемлемым для раздельной разработки маломощных пластов. Третий тип месторождений разрабатывают одноковшовыми экскаваторами.
Разработка забоя горизонтальными стружками заключается в том что исполнительным органом в забое пласта последовательно вынимаются горизонтальные стружки. Основные достоинства этого способа - низкий процент смешивания сортов сырья и меньшая длина суммарного пути перемещений ротора. К недостаткам этого способа следует отнести уменьшение обрабатываемой высоты уступа то есть максимальная высота подъема стрелы используется более эффективно при разработке вертикальными стружками.
Многолетний опыт подтверждает что наиболее эффективными выемочно-погрузочными машинами на карьерах огнеупорных глин и каолинов являются роторные экскаваторы. Решающими преимуществами роторных экскаваторов перед одноковшовыми а также перед другими механизмами (бульдозеры скреперы и пр.) являются следующие: высокая производительность относительно небольшая металлоемкость возможность селективной разработки пластов сложного строения приспособленность рабочего оборудования к частым изменениям мощности пласта и отдельных его слоев возможность применения в непрерывно-поточных технологических схемах позволяющих автоматизировать процесс производства.
Отечественной промышленностью выпускаются роторные экскаваторы на базе дизель-электрических одноковшовых экскаваторов четвертой и шестой размерных групп для разработки грунта выше уровня стоянки до 75 м. и ниже этого уровня до 35 м. при радиусе копания до 115 м и технической производительности в грунтах I категории до 550 м3ч. По удельной энергоемкости эти машины находятся на уровне лучших экскаваторов непрерывного действия (022 024 кВт-чм3) но уступают им по удельной материалоемкости (100 140 кгч).
От базовых одноковшовых экскаваторов в конструкциях роторных стреловых экскаваторов сохраняются ходовые и опорно-поворотные устройства частично или полностью платформу на которой располагают силовую дизель-генераторную установку (обычно в хвостовой части платформы с целью ее уравновешивания) насосную станцию механизмы поворота кабину с органами управления и две стойки-пилоны. В верхней части пилонов шарнирно закрепляют стрелу с ротором на конце и приемным ленточным конвейером расположенным вдоль стрелы. Для работы на уступах различных уровней стрела может поворачиваться относительно шарнира на пилоне в вертикальной плоскости посредством гидроцилиндра. Ротор с ковшами и тарельчатым питателем приводится во вращение от электродвигателя через систему карданных валов и зубчатых передач а приемный конвейер — мотор-барабаном. Последний представляет собой барабан со встроенным в него электродвигателем и зубчатым редуктором. Отвальный конвейер опирается на центрально установленный подпятник с индивидуальным электрическим приводом обеспечивающим конвейеру независимый поворот в плане относительно поворотной платформы. Вертикальное положение отвального конвейера в зависимости от высоты разгрузки регулируют гидроцилиндром шарнирно закрепленным на кронштейнах стоек-пилонов с возможностью соосного вращения с отвальным конвейером. Привод отвального конвейера осуществляется мотор-барабаном на его дальнем конце.
Дли работы верхним копанием (выше уровня стоянки экскаватора) машину располагают перед забоем на расстоянии вылета стрелы. Отвальный конвейер устанавливают по высоте и в плане в положение разгрузки. Вертикальными перемещениями стрелы при вращающемся роторе последний заглубляют в грунт на высоту уступа. Фиксируя в этом вертикальном положении стрелу одновременным поворотом платформы и вращением ротора при движении ковшей снизу вверх разрабатывают грунт отделяя его от массива вынося ковшами вверх и разгружая на тарельчатый питатель выполненный в виде наклонного вращающегося диска.
С помощью скребка грунт ссыпается с тарельчатого питателя на приемный ленточный конвейер транспортируется им и перегружается в центральной части поворотной платформы на отвальный конвейер которым выносится и разгружается в транспортное средство или в отвал. При разгрузке в транспортные средства положение отвального конвейера в плане неизменно а при разгрузке в отвал конвейер может находиться в одном положении или поворачиваться для распределения отсыпанного грунта ровным слоем в пределах отведенной полосы. В конце поворотного перемещения платформы ограниченного шириной захватки забоя ротор со стрелой опускают до уровня следующего уступа и реверсивным движением поворотной платформы при прежнем направлении вращения ротора повторяют экскавацию грунта. После разработки последнего уступа чаше всего соответствующего уровню стоянки экскаватора машину переметают в направлении к забою на новую стоянку и повторяют землеройный процесс.
Для работы нижним копанием ковши на роторе переставляют поворачивая их на 180о для возможности разработки грунта вращением ротора в направлении обратном прежнему направлению. Опустив стрелу экскавацию грунта осуществляют по описанной выше схеме для верхнего копания. Для надежного транспортирования грунта круто наклоненным приемным конвейером используют прижимной конвейер который устанавливают над приемным конвейером. Грунт перемешается между лентами двух конвейеров движущимися в одном направлении.
Для добычи полезных ископаемых открытым способом а также для вскрышных работ применяют мощные роторные комплексы производительностью до 5000 м3ч в составе роторного экскаватора и накопительно-перегрузочных устройств с железнодорожными или автомобильными транспортными средствами на карьерно-добычных работах или транспортного отвального оборудования непрерывного действия на вскрышных работах. По своей структуре эти экскаваторы сходны с описанными выше строительными экскаваторами но отличаются от них размерами и конструктивными решениями отдельных узлов. Фактическая эксплуатационная производительность этих комплексов в значительной мере зависит от типа транспортных средств которыми в основном определяются размеры вынужденных простоев экскаватора меньшие для отвального оборудования непрерывного действия и большие для железнодорожного транспорта особенно одноколейного.
6. Техника безопасности и охрана труда.doc
Основные задачи охраны труда при производстве и эксплуатации роторного экскаватора направлены на снижение производственного травматизма и профессиональной заболеваемости сокращение доли ручного труда и рабочих мест с неблагоприятными для здоровья производственными факторами.
Роторный экскаватор является устройством повышенной опасности. Безопасное состояние роторного экскаватора должно удовлетворять двум условиям: исключение аварийной ситуации при проведении добычи огнеупорного сырья и исключение воздействия на рабочих и обслуживающий персонал опасных и вредных производственных факторов возникающих при изготовлении роторного экскаватора.
Общая характеристика источников опасных и вредных факторов при производстве роторного экскаватора
Выбор технических средств обеспечения безопасности при изготовлении эксплуатации и ремонте роторного экскаватора должен осуществляться на основе выявления опасных и вредных факторов характерных для соответствующих технологических процессов.
Классификация опасных и вредных производственных факторов
г)психофизиологические
) Физическим опасные и вредные производственные факторы:
- движущиеся части машин и механизмы;
- незащищённые подвижные элементы производственного оборудования;
- передвигающиеся изделия заготовки материалы;
- острые кромки заусенцы режущие органы;
- повышенная запылённость и загазованность воздушной рабочей зоны;
- повышенная или пониженной температура рабочей зоны;
- повышенная или пониженная температура поверхности оборудования и материалов
- повышенный уровень шума на рабочем месте;
- повышенный уровень вибрации;
- повышенная или пониженная влажность воздуха;
- повышенная или пониженная подвижность воздуха;
- опасный уровень напряжения в электрической цепи;
- замыкание в цепи которое может произойти через человека;
- недостаточная освещенность рабочей зоны
) Химические опасные и вредные производственные факторы классифицируются по пути проникновения в организм человека на проникающие:
- через дыхательную систему;
- через систему пищеварения.
) Психофизиологические вредные и опасные производственные факторы
а) Статические перегрузки
б) Динамические перегрузки
в) Нервно-психологические перегрузки: эмоциональные умственные информационные монотонный труд.
г) Перенапряжение зрительных анализаторов.
В соответствии с ГОСТ 12.4.011-75 различают средства коллективной и индивидуальной защиты от воздействия опасных и вредных производственных факторов.
К основным средствам коллективной защиты при производстве малогабаритного башенного крана относятся: оградительные и предохранительные устройства тормозные устройства блокировки сигнализаторы об опасности дистанционное управление специальные средства безопасности.
К основным средствам индивидуальной защиты при эксплуатации малогабаритного башенного крана можно отнести специальную одежду обувь средства защиты для рук (рукавицы) средства защиты головы (каска) средства защиты от падения с высоты (предохранительные пояса).
Общие требования безопасности к производственным процессам при производстве роторного экскаватора регламентирует ГОСТ 12.3.002-80; основные требования безопасности при проведении выемочных работ с использованием роторного экскаватора - ГОСТ 12.3.009-76; требования безопасности к процессам перемещения грузов при помощи забойного и отвального конвейеров - ГОСТ 12.3.020-80; требования безопасности к грузоподъемному оборудованию роторного экскаватора — стандарты на общие технические требования к соответствующим типам машин (ГОСТ 24378-80 Е ГОСТ 12.2.053-83 ГОСТ 12.2 065-81 ГОСТ 12.2.071-82 и другие).
Реальные условия производства металлоконструкции роторного экскаватора типа характеризуется отсутствием биологических химических и опасных психофизиологических и вредных производственных факторов. Следовательно далее рассматриваются только опасные физические и вредные производственные факторы и методы их устранения или ослабления их влияния на человека. Защита от повышенного уровня вибрации при работе на экскаваторе заключается в уменьшении уровня вибрации в источнике ее возникновения например установка противовибрационных прокладок под двигатель.
Общие технические требования при вибрации должны соответствовать требованиям ГОСТа 12.1.012-90.
Оценка освещенности рабочей зоны в цеху
Вредность этого производственного фактора заключается в притуплении остроты зрения появления головных болей нагрузка на нервную систему. Достаточная освещенность достигается применением на рабочем месте естественного или искусственного освещения. Естественное освещение при ремонте экскаватора осуществляется через окна в стенах а также через световые проемы в местах перепадов высот смежных пролетов зданий. Если естественного света не хватает или он отсутствует то прибегают к искусственному освещению. В качестве искусственного освещения целесообразно применять лампы дневного света.
Освещение регламентировано нормами СНиП 11-4-79.
Оценка температуры воздуха рабочей зоны
При высокой температуре повышается температура тела учащается пульс и дыхание появляется головокружение. Отдача тепла испарением пота зависит от относительной влажности и скорости движения воздуха. Повышенная влажность затрудняет терморегуляцию вследствие снижения испарения пота а слишком низкая влажность вызывает пересыхание слизистой оболочки дыхательных путей. В жаркое время движение воздуха способствует увеличению отдачи тепла и улучшает состояние воздуха но оказывает неблагоприятное воздействие при низкой температуре в холодное время.
Нормальная температура обеспечивается:
защитой от источников теплового излучения;
устройством вентиляции и отопления;
применение технологических процессов и оборудования исключающих
Оценка запылённости загазованности воздуха рабочей зоны
При ремонте и эксплуатации роторного экскаватора наиболее вредными являются для человека и окружающей среды сварочные операции. Вредные вещества проникают в организм человека через дыхательные пути а так же через кожу и с пищей вызывая при этом отравление нарушая процесс пищеварения и дыхания а также зрения.
Снижение запыленности и загазованности воздуха рабочей зоны обеспечивается:
образование вредных веществ;
применением отточной вентиляции;
применением защитных средств (респираторов спец. одежды);
применением дистанционного управления производственными процессами в процессе которых выделяются вредные вещества.
В экскаваторе шум создается движущимися частями и механизмами. Шум создаваемый движущимися частями составляет:
Движение роторного экскаватора
Производственный шум оказывает раздражающее действие на нервную систему ускоряет процесс утомления снижает трудоспособность внимание к опасностям и может привести к постепенному развитию глухоты. Длительное воздействие громкого шума на человека ведет к снижению производительности труда на 10 - 40 %.
Для снижения уровня шума применяют:
облицовку кабины звукопоглощающими материалами;
уменьшение шума в источнике;
изменение направленности излучения шума.
Нормы допустимых уровней шумов должны соответствовать требованиям ГОСТа 12.1.003-83.
Движущиеся части машин и механизмы
Движущиеся механизмы экскаватора (роторная стрела ротор отвальная стрела поворотная платформа) составляют опасную зону экскаватора. Движущиеся механизмы могут привести к травматизму и гибели человека.
Средствами защиты препятствующими попаданию человека в опасную зону являются оградительные устройства в соответствии с ГОСТ 13.54.8-83 и ОСТ24.006.01 -83.
Оценка возможности обеспечения электробезопасности для роторного экскаватора
Персонал обслуживающий электроустановки должен предварительно пройти обучение безопасным методам работы на рабочем месте и сдать экзамен квалификационной комиссии. В соответствии с «Правилами технической эксплуатации и безопасного обслуживания электроустановок промышленных предприятий» установлено пять квалификационных групп. Группу устанавливает квалификационная комиссия сроком на один год.
При работе на экскаваторе механик подвергается повышенному значению напряжения в электрической цепи замыкание которого может произойти через тело человека.
Электрический ток оказывает на человека термическое электролитическое и биологическое воздействие. Выделяют два вида поражения:
электрические травмы - ожоги нейтрализация кожи механические
повреждения и сокращение мышц
электрические удары различной степени поражения приводящие к
остановке дыхания потере сознания нарушении сердечной деятельности.
Цепь которая питает кабину управления имеет пониженное значение тока и напряжения что в свою очередь делает их безопасными для человека. С целью устранения опасности поражения людей электрическим током используется заземление экскаватора а также используют в силовой цепи двойную изоляцию. Средства защиты от поражения электрическим током установлены ГОСТом 12.4.011-75.
Обеспечение электробезопасности при работе и обслуживании роторного экскаватора
Для устранения опасности поражения людей электрическим током при появлении напряжения на конструктивных частях электрооборудования и самой металлоконструкции применяются заземляющие устройства. Защитное заземление - это преднамеренное соединение нетоковедущих металлических частей оборудования с землей для предотвращения поражения работающих людей электрическим током при пробое на корпус или появлении потенциала на оборудовании.
Принцип действия защитного заземления основан на снижении до безопасных значений напряжений соприкосновения и шага за счет снижения потенциала или его выравнивания с заземленным оборудованием.
Для обеспечения электробезопастности при проведении работ необходимо периодически измерять электрическое сопротивление заземления и при превышении им допустимого уровня необходимо производить его ремонт.