Блюменталь Э.С., Лысенко В.Г. Детали приборов. Курсовое проектирование




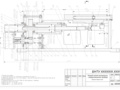
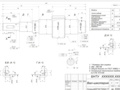
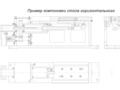

- Добавлен: 24.01.2023
- Размер: 2 MB
- Закачек: 0
Описание
Состав проекта
![]() |
![]() |
![]() ![]() ![]() |
![]() |
![]() ![]() ![]() |
![]() ![]() ![]() ![]() |
![]() ![]() ![]() ![]() |
![]() ![]() ![]() ![]() |
![]() ![]() ![]() ![]() |
![]() ![]() ![]() ![]() |
![]() ![]() ![]() ![]() |
![]() ![]() ![]() ![]() |
![]() ![]() ![]() ![]() |
![]() ![]() ![]() ![]() |
![]() ![]() ![]() ![]() |
Дополнительная информация
Детали приборов Курсовое проектирование Блюменталь.doc
Белорусский национальный технический университет
Кафедра «Стандартизация метрология
и информационные системы»
Э.С. Блюменталь В.Г. Лысенко П.А. Петрусенко Б.В.Цитович
КУРСОВОЕ ПРОЕКТИРОВАНИЕ
Учебно-методическое пособие для студентов приборостроительных специальностей
Рекомендовано УМО вузов РБ по образованию в области обеспечения качества
Д.Г.Девойно к.т.н. доцент кафедры механики Военной академии РБ;
Г.А.Есьман к.т.н. доцент кафедры КИПП БНТУ
Детали приборов. Курсовое проектирование. Учебно-методическое пособие для студентов приборостроительных специальностей
Э.С. Блюменталь. – Мн.: БНТУ 2007. – с.
Учебно-методическое пособие предназначено для использования в высших учебных заведениях при подготовке инженеров по приборостроительным специальностям.
Пособие включает общие положения цели и задачи курсового проекта исходные данные для проектирования справочные данные и формулы для расчетов представляет структуру проекта и порядок его выполнения включая требования к оформлению.
Издание может быть полезно инженерно-техническим работникам занимающимся проектированием средств измерений и точных механических устройств.
1 Цель и задачи курсового проектирования4
3 Этапы курсового проектирования6
4 Назначение и содержание расчетов7
ВЫБОР ДВИГАТЕЛЯ И КИНЕМАТИЧЕСКИЙ РАСЧЕТ9
1 Рекомендации по выбору электродвигателя9
2 Кинематический расчет привода12
ПРОЕКТИРОВАНИЕ И РАСЧЕТ ЗУБЧАТЫХ ПЕРЕДАЧ15
1 Разработка конструкции передачи и необходимые расчеты15
2 Крепление колес на валах23
3 Выбор норм точности зубчатых колес и передач24
4 Пример конструирования прямозубой передачи24
5 Расчеты подтверждающие работоспособность передачи25
1 Предварительный расчет валов33
2 Проверочный расчет валов на прочность33
3 Расчёт валов на выносливость (усталостную прочность)36
4 Расчет на жесткость37
ПОДШИПНИКИ СМАЗКА УПЛОТНИТЕЛИ42
1 Опоры на стандартных подшипниках качения. Конструирование и расчет42
1.1 Конструкции и обозначения42
1.2 Типы и условное обозначение подшипников42
2 Схемы установки опор конструктивные элементы смазывание уплотнение47
3 Порядок проектирования опор50
4 Требуемая долговечность работы подшипника LN54
5 Пример расчёта работоспособности подшипников качения60
ПЕРЕДАЧА ВИНТ-ГАЙКА63
1 Кинематика и КПД передачи63
2 Проверка на износостойкость передачи винт-гайка65
3 Проверка винта на устойчивость65
1 Трение в направляющих68
2 Выбор и расчет пружин73
3 Материалы пружин и используемые покрытия76
4 Изображение пружин на общем виде и требования к ним77
5 Общие требования примеры рабочих чертежей пружин правила изображения78
6 Обозначение на чертежах материала покрытия требований связанных с термообработкой79
7 Допуски размеров пружин79
8 Последовательность простановки технических требований на рабочих чертежах80
ШПОНКИ. ШПОНОЧНЫЕ СОЕДИНЕНИЯ81
ШТИФТОВЫЕ СОЕДИНЕНИЯ И КОРПУСНЫЕ ДЕТАЛИ87
1 Штифтовые соединения87
ОБЩИЕ ТРЕБОВАНИЯ К ОФОРМЛЕНИЮ ПОЯСНИТЕЛЬНОЙ ЗАПИСКИ95
1 Оформление графических документов97
2 Выполнение и защита курсовых проектов97
Настоящее учебно-методическое пособие разработано для выполнения курсового проекта по дисциплине «Детали приборов» для студентов приборостроительных специальностей. Материалы изложенные в пособии содержат сведения теоретического и справочного характера и предназначены для студентов дневной и заочной форм обучения.
Объём справочного материала приведенного в пособии соответствует тематике заданий на курсовой проект принятой на кафедре «Стандартизация метрология и информационные системы» и помогает студентам в освоении опыта проектирования накопленного в промышленности и отражённого в Технических нормативных правовых актах (ТНПА). Вместе с тем надо отметить что дополнительный справочный материал а также более подробное изложение вопросов касающихся проектирования и расчётов приводятся в литературе список которой дан в конце пособия.
Знания и опыт приобретённые студентом в процессе проектирования являются основой для дальнейшей конструкторской работы а также для выполнения курсовых проектов по специальным дисциплинам и дипломного проекта.
Материал в пособии изложен в той последовательности которая методически соответствует порядку работы над курсовым проектом.
1 Цель и задачи курсового проектирования
Курсовой проект по деталям приборов является первой конструкторской работой студента при выполнении которой студент приобретает навыки проектирования расчета и конструирования деталей и механизмов приборов на базе знаний полученных при изучении общетехнических и специальных дисциплин.
Основная цель курсового проектирования состоит в приобретении опыта проектирования объектов приборостроения. Дополнительной целью является выполнение и защита курсового проекта по соответствующей дисциплине.
Основные задачи курсового проектирования:
– изучение и анализ конструкций аналогичных устройств и механизмов;
– анализ научно-технической литературы по теме задания;
– освоение методик проектирования деталей и механизмов приборов;
– приобретение навыков использования справочников каталогов стандартов и других ТНПА;
– развитие навыков выполнения чертежей общего вида рабочих чертежей выполнения и оформления пояснительной записки.
По ГОСТ 15.001-88 «Разработка и постановка продукции на производство. Основные положения» Разработка продукции осуществляется по договору с заказчиком или по инициативе разработчика. Функции заказчика предусмотренные настоящим стандартом может выполнять государственная кооперативная или общественная организация (предприятие). Основанием для проектирования изделия в данном проекте является Задание на проектирование выданное кафедрой студенту.
Разработка и постановка продукции на производство в общем случае предусматривает:
) разработку технического задания;
) разработку технической и нормативно-технической документации;
) изготовление и испытания образцов продукции;
) приемку результатов разработки;
) подготовку и освоение производства.
Отдельные из указанных работ можно совмещать а также изменять их последовательность и дополнять другими работами в зависимости от специфики продукции и организации ее производства.
Техническое задание является исходным документом для разработки конструкторской документации и как правило составляется разработчиком с участием заказчика.
ТЗ содержит наименование и область применения изделия цель назначение и источники разработки технические требования к изделию и требования к его экономическим показателям перечень стадий и этапов разработки и состава разрабатываемой документации и т.п.
Стадии разработки проектной и рабочей конструкторской документации установлены стандартами ЕСКД.
В техническом предложении в соответствии с требованиями ГОСТ 2.118-73 дают технико-экономическое обоснование целесообразности разработки изделия и уточняют требования к изделию разработанные на основании анализа технического задания и проработки вариантов возможных технических решений изделия с учетом его конструктивных и эксплуатационных особенностей а также анализа патентных материалов. Результаты технического предложения являются основанием для выполнения эскизного проекта.
Эскизный проект (ГОСТ 2.119-73) включает конструкторские документы содержащие принципиальные решения которые дают общее представление об устройстве и принципе работы изделия а также данные определяющие его основные параметры и габаритные размеры. Эскизный проект разрабатывают обычно в нескольких вариантах с расчетами на основании чего выбирают наиболее подходящий вариант для последующей разработки в техническом проекте.
На стадии эскизного проектирования для тех элементов которые несущественно влияют на основные показатели конструкции выполняют приближенные расчеты. Отдельные элементы конструкции могут быть взяты без расчета например по результатам практического применения аналогичных образцов.
Технический проект (ТП) по ГОСТ 2.120-73 предусматривает подробную конструкторскую разработку всех элементов выбранного варианта. Конструкторская документация ТП содержит окончательное техническое решение конструкции изделия и исходные данные для разработки рабочей документации. При техническом проектировании разрабатывают чертежи общих видов габаритные чертежи и схемы уточняют конструкцию деталей выполняют все необходимые проверочные расчеты элементов объекта и составляют полный перечень элементов конструкции.
Рабочую документацию (документацию рабочего проекта) разрабатывают на заключительной стадии проектирования. На этом этапе в некоторых случаях изготавливают уточненные чертежи общих видов согласованные с ними чертежи деталей спецификации сборочные чертежи.
Таким образом документация рабочего проекта содержит все то что необходимо для воплощения в материальную форму технического задания.
В ходе курсового проектирования студент выполняет основные работы предусмотренные ЕСКД включая упрощенное представление ТЗ чертежи общего вида проверочные расчеты и примеры рабочей документации.
Упрощенное техническое задание студент разрабатывает на основании задания на курсовое проектирование. Затем исполнитель выполняет эскизное проектирование (как правило в черновых вариантах) выбирает окончательный вариант разрабатывает технический проект и примеры чертежей деталей которые он представляет на защиту.
3 Этапы курсового проектирования
Процесс выполнения студентом курсового проекта можно разделить на следующие основные этапы объем и содержание которых могут изменяться в зависимости от новизны и сложности разрабатываемого изделия.
Анализ задания на курсовой проект.
Изучение материалов по теме проекта.
Выполнение проектировочных расчетов и выбор элементов конструкции.
Эскизное проектирование.
Выполнение расчетов подтверждающих работоспособность конструкции.
Разработка материалов технического проекта изделия и чертежей деталей.
В ходе анализа задания студент должен понять поставленную задачу проектирования и разработать упрощенный вариант ТЗ на проектирование данного объекта.
Изучение материалов по теме проекта предусматривает поиск и анализ технической литературы и других источников информации включающих описание физических принципов которые могут быть положены в основу конструкции проектируемого прибора.изучает схемы и конструкции ранее разработанных аналогичных изделий оценивает их достоинства и недостатки а также степень их соответствия требованиям задания. Затем исполнитель выбирает один или несколько подходящих прототипов и представляет их руководителю проекта.
Проектировочные расчеты изделия часто включают выбор двигателя муфты ориентировочные расчеты габаритов зубчатых передач диаметров валов и др. Проектировочные расчеты не входят в документацию технического проекта но являются обязательным элементом курсового проектирования. Эти расчеты как правило включают в пояснительную записку курсового проекта в виде приложений.
Затем на основании результатов проектировочных расчетов выполняют эскизный чертеж проектируемого привода и при необходимости уточняют проектировочные расчеты (определяют все размеры основных деталей: зубчатых колес валов муфт передачи винт-гайка и т.д.).
Эскизный чертеж дает возможность выполнить проверочные расчеты подтверждающие работоспособность конструкции так как известны основные размеры элементов.
Разработка материалов технического проекта изделия [1] включает выполнение чертежей общего вида окончательного варианта с выбранными конструктивными решениями. На базе чертежей общего вида выполняют рабочие чертежи типовых деталей в соответствии с Заданием на курсовое проектирование и указаниями руководителя. Затем оформляют пояснительную записку проекта со всеми необходимыми расчетами схемами и приложениями.
Перечень этапов проектирования с указанием сроков выполнения каждого этапа приведен в задании на курсовое проектирование (приложение 3).
4 Назначение и содержание расчетов
В ходе курсового проектирования выполняют расчеты двух видов:
проектировочные расчеты;
проверочные расчеты.
Геометрический кинематический и силовой расчеты на стадии технического предложения рассматриваются как проектировочные расчеты и проводятся по данным определенным заданием на курсовой проект. Эти расчеты как правило носят ориентировочный характер и их включают в пояснительную записку курсового проекта в виде приложений.
По результатам проектирования выполняют проверочные расчеты необходимые для подтверждения работоспособности конструкции. Эти расчеты являются необходимым элементом проектирования.
Расчеты в общем случае должны содержать:
схему рассчитываемого изделия;
задачу расчета (с указанием что требуется определить);
исходные данные для расчета;
условия положенные в основу расчета;
расчет (расчетные зависимости с необходимыми данными и результаты расчета);
заключение по результатам расчета.
ВЫБОР ДВИГАТЕЛЯ И КИНЕМАТИЧЕСКИЙ РАСЧЕТ
1 Рекомендации по выбору электродвигателя
В проектируемом изделии может требоваться постоянное или переменное значение частоты вращения вала двигателя. В первом случае применяют синхронные и асинхронные двигатели переменного тока или двигатели постоянного тока с регуляторами скорости. Для регулируемых приводов обычно выбирают двигатели постоянного тока шаговые двигатели двигатели переменного тока с частотным управлением.
Для проектируемых в рамках данного курсового проекта приводов общего назначения рекомендуются асинхронные короткозамкнутые двигатели серии 4А. Эти двигатели наиболее универсальны причем могут при необходимости обеспечивать реверсивность.
Асинхронные двигатели переменного тока имеют угловую скорость установившегося движения отличающуюся от номинальной на (5 20) %.
Рисунок 2.1 - Конструкции двигателей
Размеры двигателей асинхронных серий 4А
Для определения требуемой мощности электродвигателя (Таблицы 2.2 2.3) следует использовать значения приведенных моментов сил сопротивления на выходном валу редуктора Tc и номинальной угловой скорости этого вала с; или же тяговой силы стола F и скорости перемещения стола прибора V.
Технические характеристики двигателей асинхронных трехфазных серии 4ААМ
Двухполюсные синхронная частота вращения 3000 обмин
Четырёхполюсные синхронная частота вращения 1500 обмин
Примечания – Fr Fa – предельные радиальная и осевая (при предельной радиальной) нагрузках на конец вала Io – момент инерции ротора
В скобках даны значения кратности моментов и токов для двигателей с пусковым конденсатором (исполнения У и УТ)
Моменты инерции ротора и предельные нагрузки на конец вала смотрите для соответствующего габарита по
Следует иметь в виду что на потребляемую мощность влияют не только полезная нагрузка но и потери в механизме его динамические характеристики строгие значения которых можно определить только в процессе конструирования.
Требуемую мощность P электродвигателя при вращательном движении рабочего элемента определяют из зависимости:
где P – мощность электродвигателя Вт;
Tc – момент сил сопротивления на выходном валу редуктора Нм;
с – номинальная угловая скорость выходного вала радс;
Kдин – коэффициент запаса учитывающий необходимость преодоления динамических нагрузок в момент разгона. Если в задании не оговорено время переходного процесса обычно принимают Kдин = 105 110.
– коэффициент полезного действия привода равный произведению частных КПД передач входящих в кинематическую схему.
Требуемую мощность P электродвигателя при поступательном движении рабочего элемента определяют из зависимости:
Где F – тяговая сила стола Н;
V – скорость перемещения стола прибора мс;
Значения КПД на этой стадии проектирования задают исходя из предполагаемого вида передач от двигателя к рабочему звену. Мощность электродвигателя для проектируемого привода должна быть не ниже той которая определена по формулам (2.1) (2.2). Каждому значению номинальной мощности Pном соответствует обычно не один а несколько типов асинхронных двигателей с различными частотами вращения близкими к номинальным значениям 3000 1500 1000 750 обмин.
При выборе двигателя надо учитывать что тихоходные электродвигатели с синхронной частотой вращения 750 обмин и менее применяют в технически обоснованных случаях т.к. они дороже быстроходных и имеют большие габариты.
После проектирования редуктора необходимо определить действительные значения КПД и произвести проверочный расчет двигателя. Момент на валу выбранного двигателя должен быть не менее приведенного расчетного момента.
2 Кинематический расчет привода
Исходные данные на курсовое проектирование содержат частоту вращения стола прибора nст или скорость перемещения V стола прибора.
При заданной частоте вращения стола прибора общее передаточное отношение привода определяют по формуле:
При заданной скорости линейного перемещения стола угловая скорость и частота вращения n ведущего звена (винта или гайки) связаны со скоростью V ведомого звена движущегося поступательно зависимостями:
где – угловая скорость радс;
V –скорость движущегося поступательно ведомого звена ммс;
np – число заходов резьбы;
n – частота вращения ведущего звена (винта или гайки) 1мин.
Рекомендуется применять стандартную трапецеидальную резьбу с шагом p не менее 2 мм.
Передаточное отношение привода:
Пример 1. Выбрать двигатель привода стола контрольно-измерительного прибора; определить общее передаточное число привода и произвести его разбивку. Схема 1 (см. Приложение 4)
Исходные данные: тяговая сила стола F = 600 Н скорость перемещения стола в установившемся режиме V = 40 ммс = 004 мс.
Определяем КПД привода
зубчатой пары з = 098;
одной пары подшипников каченияп = 099;
передачи винт-гайкав-г = 035;
Требуемая мощность электродвигателя по формуле 2.2
В Пояснительной записке для каждой из формул приводят расшифровку всех элементов с указанием единиц.
По таблице [2] выбираем двигатель серии 4А с номинальной мощностью Pном = 80 Вт и n = 1380 обмин.
Определим частоту вращения винта в передаче винт гайка по формуле (2.5)
Примем шаг резьбы винта p = 4 мм тогда
Передаточное отношение зубчатой передачи
Для данного передаточного отношения выбираем одноступенчатую зубчатую передачу.
Пример 2. Выбрать двигатель привода вращающегося стола контрольно- измерительного прибора; определить общее передаточное число привода и произвести его распределение по ступеням. Схема 6 (см. Приложение 4)
Исходные данные: момент сопротивления вращению стола Т = 15 Нм частота вращения стола wст = 628 радс.
зубчатой цилиндрической парызц = 098
зубчатой конической пары зк = 097
пары подшипников каченияп = 099
Требуемая мощность электродвигателя по формуле 2.1:
По таблице [2] выбираем двигатель серии 4А с номинальной мощностью Pном = 120 Вт и n = 1380 обмин тогда частота вращения двигателя равна: радс.
Передаточное отношение зубчатой передачи:
Округленное значение передаточного отношения – 23 необходимо использовать двухступенчатую зубчатую передачу. Производим приближенное распределение передаточного отношения по ступеням в соответствии с [3]
Для конической передачи Uпк = 4
Для цилиндрической передачи Uпц = 56
Расчетное передаточное отношение:
Относительная погрешность заданной скорости не должна превышать 5 %:
Проверим правильность наших расчетов:
ПРОЕКТИРОВАНИЕ И РАСЧЕТ ЗУБЧАТЫХ ПЕРЕДАЧ
1 Разработка конструкции передачи и необходимые расчеты
Определение основных размеров передачи
Из условия прочности [45] можно вычислить приблизительное значение диаметра меньшего колеса (шестерни):
гдеd1 – делительный диаметра меньшего колеса (шестерни) мм;
С – коэффициент учитывающий геометрию передачи и свойства материалов: 28 – для стальных незакаленных колес; 20 – для стальных закаленных;
Т1 – крутящий момент на валу меньшего колеса Нмм;
U12 –передаточное отношение пары зубчатых колес;
Модуль m в миллиметрах определяется из следующей зависимости:
где z1 – число зубьев шестерни (определяется по рекомендации справочной литературы [34] в зависимости от необходимой плавности работы скорости вращения или заданного межосевого расстояния).
Модули эвольвентного зацепления цилиндрических колес регламентированы ГОСТ 9563-60. Стандартизован нормальный модуль mn . Стандарт предусматривает два ряда предпочтения. В первом ряду предусмотрены модули от 005 до 100 мм [2]. Второй ряд предусматривает промежуточные значения в единичном производстве его применение нежелательно.
Изготовление колес c модулем менее 10 мм затруднительно.
Определение числа зубьев колеса z2 осуществляется по формуле:
Межосевое расстояние аw в миллиметрах:
где d1 – делительный диаметр шестерни мм;
d2 – делительный диаметр колеса() мм;
Диаметры вершин зубьев:
где y bd– коэффициент ширины зубчатого венца (y bd=04 0.6)
Силовой расчет передачи
Целью силового расчета является определение сил и моментов действующих на звенья передачи.
Исходные данные для расчета силовых параметров передачи
Наименование параметра
Подводимая (потребляемая) мощность
Угловая скорость колеса
а. Линейная скорость рейки
а. Диаметр колеса (сектора)
б. Угол наклона зуба
г. Угол зацепления в торцовой плоскости
Передаточное отношение
Коэффициент внешней динамической нагрузки
Коэффициент перегрузки
Коэффициент трения в зацеплении зубьев
Расчет силовых параметров передачи
Определяемая величина
а. То же при перегрузке
Окружная сила в зубчатой передаче
Радиальная сила на колесе
Осевая сила на колесе
Нормальная сила на рабочей поверхности зубьев
Коэффициент нагруженности контакта
Коэффициент полезного действия цилиндрической передачи
Момент на ведомом валу
В расчетных формулах учтены потери непосредственно в зацеплении
Потери в опорах муфтах и др. элементах механизма учитываются за счет коэффициентов запаса по нагрузке
Коррекция зубчатого зацепления
Коррекция зубчатого зацепления необходима для:
– повышения эксплуатационных характеристик передачи (в том числе устранение подрезания профилей);
– получения заданного межосевого расстояния.
Коррекция смещением профиля позволяет решить обе задачи и не требует никаких дополнительных затрат.
Коррекция смещением профиля заключается в формировании поверхности зуба путем обкатки делительной окружности колеса по прямой параллельной делительной прямой инструмента.
где x – коэффициент смещения контура при нарезании колеса (может быть как положительным так и отрицательным).
Так как параметры контура остаются неизменными форма эвольвентных поверхностей сохраняется но для получения рабочей поверхности зуба используются иные участки эвольвенты полученной с той же основной окружности. Вследствие этого изменяется положение полюса зацепления на эвольвентах изменяются угол зацепления и радиусы кривизны эвольвент в полюсе зацепления скорости взаимного скольжения толщина зуба у основания.
Особенностью этого вида коррекции является возможность изменения межосевого расстояния без изменения параметров и .
При применении коррекции смещением профиля достигается:
– устранение явления подрезания что позволяет использование колес с малым числом зубцов;
– повышение изгибной или контактной прочности зубцов хотя при этом уменьшается коэффициент перекрытия т.е. повышение прочности происходит за счет снижения плавности передачи;
– повышение плавности передачи увеличение коэффициента перекрытия но за счет снижения прочностных показателей;
– повышение износостойкости путем уравнивания скоростей скольжения профилей.
Эти цели достигаются рациональным выбором сочетания смещений пары колес. Ограничением значения смещения у каждого колеса данной пары являются условия обеспечения достаточности коэффициента перекрытия опасность возникновения явления подрезания или же интерференции зубцов заострение вершин зубцов. Границы возможной коррекции можно определить используя блокирующие контуры приведенные в приложениях к ГОСТ 16532-70 и [236].
Коэффициенты смещения рекомендуемые для обеспечения максимальной контактной прочности при износостойкости даны в таблице 3.3.
Интерполяцией находим для передачи
Обычно рекомендуемые коэффициенты смещения даны в пределах блокирующих контуров.
Рекомендуемые значения коэффициентов смещения
Кн – повышение контактной прочности;
Из – повышение износостойкости
Выбор материалов зубчатой передачи
Виды материалов деталей передачи могут быть назначены еще при разработке технического предложения – сталь цветной металл чугун пластмасса. Однако такие данные пригодны только для ориентировочных расчетов на этапе эскизного проектирования. Для окончательных расчетов требуется указание марки материала и при необходимости его свойств с учетом термообработки.
Для колес получаемых резанием чаще всего применяют стали марок 45 и 40Х в нормализованном или улучшенном состоянии.
Для литых колес обычно применяют чугуны типа СЧ30 ВЧ65 и др. чаще всего с дополнительной обработкой резанием. Применение литейных сталей например типа сталь 40Л позволяет уменьшить габариты передачи. Для повышения работоспособности колес применяется термообработка например улучшение или закалка.
Из цветных металлов сравнительно часто применяются бронзы типа БрАЖ 9-4 или высокопрочные алюминиевые сплавы например типа В95. Литые колеса рационально изготавливать из бронз типа БрА9Мц2 алюминиевых сплавов типа АЛ8 или магниевых типа МЛ6. Повышенная стоимость материалов может окупиться их более высокой технологичностью и эффективностью работы.
Следует заметить что цветные металлы и пластмассы как правило применяют в качестве материала колеса сопряженного со стальным или чугунным колесом.
В литературе [2347] содержатся сведения о материалах зубчатых колес и реек. Механические свойства некоторых наиболее распространенных материалов применяемых в приборостроении даны в таблице 3.4.
Механические свойства распространенных материалов
Марка материала и термообработка
Модуль упругости E МПа
Коэффициент Пуассона
Допустимое напряжение
Сталь 45 ГОСТ 1050-74
Сталь У10А ГОСТ 1435-74
Сталь 40ХЕ ГОСТ 1414-75
Сталь 40Х ГОСТ 4543-75
Сталь 40Х13 ГОСТ 5632-72
Сталь 40Л-Ш ГОСТ 977-75
Окончание таблицы 3.4
Сплав В95 ГОСТ 4784-74
БрАЖ 9-4 ГОСТ 18175-78
Полиамид ПА610-1-101
Конструкции колес (примеры)
Конструктивно принято различать колеса (рисунок 3.1) дисковые без ступицы (пример А) колеса с симметричным расположением ступицы (пример Б) и с односторонним (пример В) расположением ступицы а также колеса дисковые со ступицей и отверстиями в диске (пример Г).
Для обработки резанием наиболее подходит по технологичности конструкции вариант конструктивного оформления колес А позволяющие производить обработку венца пакетом до 5-10 заготовок одновременно.
При необходимости увеличения посадочной поверхности применяют вариант конструктивного оформления Б.
Для литых колес ступицу рационально располагать несимметрично относительно зубчатого венца (пример В) хотя в этом случае увеличивается неравномерность распределения нагрузки по зубу. Несимметричная ступица применяется и в случае штифтового крепления колеса на валу или крепления установочным винтом а также и по другим конструктивным соображениям.
Рисунок 3.1 – Примеры конструктивного оформления зубчатых колес
При большом соотношении диаметров зубчатого венца и ступицы (пример конструктивного оформления Г) рационально предусмотреть отверстия в диске. Диаметр окружности центров отверстий рассчитывается по формуле:
где Dz – диаметр обода мм;
Dy1 – наружный диаметр ступицы мм;
Конструктивные размеры мелкомодульных колес – ширина венца диаметр и длина ступицы установлены ГОСТ 13733-77 (см. также [68]).
Расчетная ширина венца bw обычно задается еще при разработке эскизного проекта и уточняется затем при расчетах на прочность.
Длина ступицы конструктивно определяется шириной венца и размерами элементов крепления колеса на валу. Следует учесть что при наличии зазора в посадке устойчивость колеса тем выше чем длиннее ступица. Вместе с тем излишне длинные ступицы усложняют изготовление и сборку колес. Обычно длина ступицы
где Dy – диаметр вала мм.
2 Крепление колес на валах
Примеры крепления колес на валах показаны на рисунке 3.2.
Крепление с помощью сил трения может быть осуществлено применением посадок с натягом (вариант А). При нормальной длине и толщине ступицы и для сравнительно прочных материалов (сталь высокопрочный чугун деформируемые бронзы) возможно обеспечение надежной передачи значительного крутящего момента от ступицы к валу.
Рисунок 3.2 - Крепление колес на валах
Обеспечение натяга с одновременным упрощением сборки может быть достигнуто посадкой на конус. Значение конусности регламентировано стандартом
ГОСТ 8593-31.Достаточные силы трения могут быть созданы при креплении колеса с коническим отверстием при помощи гайки (вариант Б).
Крепление колеса штифтом (вариант В) цилиндрическим ГОСТ 3128-70 или коническим ГОСТ 3129-70 обеспечивает как передачу крутящего момента так и фиксацию колеса в осевом направлении даже при наличии осевых нагрузок. Рекомендации по методам предохранения штифтов от выпадения даны в [2] размеры штифтового соединения – в [8].
Применение шпоночного соединения (вариант Г) – призматическими шпонками
ГОСТ 23360-78 возможно при диаметрах валов от 6 мм сегментными шпонками ГОСТ 24071-80 – от 3 мм. Сегментные шпонки имеют ограниченную длину контактирующей со ступицей поверхности поэтому для ступиц из непрочных материалов – легких цветных сплавов пластмасс - их применение ограничено.
Сечения шпонок регламентированы стандартами в зависимости от диаметра вала. Равнопрочность шпоночного соединения и вала обеспечивается при рабочей длине шпонки:
где Ссм – коэффициент учитывающий прочность материала ступицы при работе на смятие для стальных втулок – Ссм = 08 для чугунных и бронзовых – 12 из алюминиевых и магниевых сплавов – 16 18.
Различные варианты крепления и фиксации втулок на валах приведены в литературе [9].
Сведения о размерах шпонок допусках и посадках шпоночных соединений а также о расчетах шпонок см. ниже в разделе - шпоночные соединения.
3 Выбор норм точности зубчатых колес и передач
Точность параметров зубчатых колес и передач нормирована следующими стандартами:
ГОСТ 1643-81 «Передачи зубчатые цилиндрические. Допуски» (для модулей зубчатых колес m = 1 55 мм);
ГОСТ 9587-81 «Передачи зубчатые цилиндрические мелкомодульные. Допуски» (для модулей зубчатых колес m = 01 09 мм).
ГОСТ 1643-81 устанавливает 12 степеней точности цилиндрических зубчатых колес и передач: 1 2 12 (в порядке убывания точности). В настоящее время степени 1 и 2 предусмотрены как перспективные.
Стандартизованы 6 классов точности отклонений межосевого расстояния обозначаемые римскими цифрами от I до VI (в порядке убывания точности).
При выборе норм точности изготовления зубчатых колес и сборки передач необходимо исходить из назначения передачи условий ее эксплуатации требований к ней т.е. учитывать окружную скорость колес передаваемую мощность продолжительность и режим работы требования к кинематической точности плавности бесшумности отсутствию вибраций надежности и т.д. [2310]
4 Пример конструирования прямозубой передачи
Требуется спроектировать прямозубую цилиндрическую зубчатую передачу в приводе стола прибора.
В соответствии с конкретным заданием к курсовому проекту известны нагрузки скорость стола и тип производства.
Например из расчетов выполненных на предыдущих стадиях получено:
- передаваемый крутящий момент Т1 = 50 Н.м
- передаточное отношение передачи U12=10.
Предварительно принимается ориентировочный диаметр меньшего колеса:
Максимальная угловая скорость радс. Число зубьев меньшего колеса (шестерни) =12.
Выбрана прямозубая зубчатая передача:
исходный контур ГОСТ 13755-81
коэффициенты смещения =065 =165 (выбраны для обеспечения требуемого межосевого расстояния) ширина венца =4 мм степень точности
-7-6 E ГОСТ I643-81.
Ведущее колесо – расположено на первичном валу редуктора ведомое – на вторичном валу симметрично между опорами материалы колес принимаем – сталь по бронзе смазывание периодическое.
Диаметр выступов меньшего колеса = 14 мм диаметр ступицы =(7 9) мм. Для пары сталь-бронза при требованиях износостойкости рекомендуется сталь типа 40Х закаленная или улучшенная [23].
Приняты материалы колес:
меньшего колеса Сталь 40Х ГОСТ 4543-71 улучшенная 270 290 НВ
большего колеса Бр A9Мц2 ГОСТ 493-79.
Ширина венца большего колеса =4 мм. Меньшее колесо рекомендуется делать шире +(02 2)=4+(02 2) = 42 6 мм. Принято: =6 мм. Так как вал двигателя гладкий крепление на нем ведущего колеса возможно установочным винтом шпонкой или штифтом.
Рекомендуемый штифт ГОСТ 3129-70 - 16x10 кольцо 05x8.
Диаметр ведомого вала из условия равнопрочности:
На ведомом валу может быть применена призматическая или сегментная шпонка.
По стандарту ГОСТ 24071-80 сегментная шпонка для диаметра вала 11 мм имеет размеры 3x5x13 [2] что в данном случае достаточно для обеспечения прочности. Принято: шпонка 3x5х13 ГОСТ 24071-80.
Выбор применения шпонки или штифта будет зависеть от условий сборки и от возможности предотвращения осевого смещения колеса. Для гладкой шейки консольного вала предпочтительнее применение штифта.
Толщина диска для колес при m = 1 = 3 мм. Так как диаметр впадин колеса = 1175 [8] то диаметр диска:
= 117.5-2.3=111.5 мм
По ряду Ra40 ГОСТ 6636-69 принято = 110 мм.
При имеющемся соотношении диаметров доска и ступицы рационально предусмотреть отверстия в диске. Диаметр окружности центров отверстий:
= (110 + 25)2 = 675 мм.
Если принять= 67 мм по ряду Ra40 [2] то диаметр отверстия:
= 67 - 25 - 4(04 06) - 4(09 14) = 34 37 мм.
По ряду Rа10 можно принять = 32 мм. Количество отверстий – 4.
В качестве параметра для контроля толщины зуба рационально принять размер по роликам М общепринятый для мелкомодульных передач.
5 Расчеты подтверждающие работоспособность передачи
Определение показателей и параметров передачи:
Запаса прочности по контактным напряжениям – KН.
Запаса прочности на изгиб при максимальной нагрузке – KFST.
Размер по роликам – M.
Исходные данные для расчета
Модуль упругости (для стали)
Твердость материалов
Межосевое расстояние
Диаметры окружностей вершин
Коэффициент перекрытия
Шероховатость рабочих поверхностей зубцов
Коэффициент динамичности внешней нагрузки
Максимальная окружная сила
Расчёт на контактную выносливость зуба в соответствии с ГОСТ 21354-87
Коэффициент свойств материалов
Коэффициент формы сопряженных поверхностей
Коэффициент суммарной длины контакта
Коэффициент наклона зуба
Коэффициент вида передачи
Коэффициент точности передачи
Удельная динамическая нагрузка
Коэффициент динамичности
Допуски направления зуба и взаимного перекоса осей передачи по ГОСТ 1643 (при согласии руководителя проекта можно сразу перейти к пункту №21 этого расчета)
Вероятный перекос линий контакта
Жесткость валов передачи
Перекос зубца при деформации вала:
для консольного колеса
для колеса между опорами
Суммарный перекос зубца
Продолжение таблицы 3.6
Коэффициент податливости поверхности
Удельная торцевая податливость контакта
Удельная торцевая податливость зубцов на изгиб
Суммарная удельная податливость
Наибольшая удельная нагрузка
Коэффициент приработки
Коэффициент прилегания зубца
Коэффициент неравномерности нагрузки по зубцу( можно получить его значение по диаграммам из литературы [45611].или из текста ГОСТ 21354-87)
Контактные напряжения
Предельные напряжения
Базовое число циклов
Коэффициент долговечности
Коэффициент безопасности
Коэффициент ответственности
Коэффициент шероховатости
Коэффициент скорости
Коэффициент смазывания
Допускаемые напряжения
Окончание таблицы 3.6
Запасы прочности по контактным напряжениям
Примечание: Допускается расчет зубьев на изгиб и контактную прочность выполнить в соответствии с методикой изложенной в следующих источниках [46711]
Расчёт зуба на изгиб в соответствии с ГОСТ 21354-87
Удельная динамическая сила
Коэффициент неравномерности нагрузки по длине зубца
Коэффициент формы зубца (можно получить его значение по диаграммам из литературы [45611].или из текста
Коэффициент наклона зубца
Коэффициент степени перекрытия
Расчетные напряжения изгиба
Коэффициент переходной поверхности
Коэффициент упрочнения
Коэффициент вероятности неразрушения
Коэффициент вида заготовки:
Коэффициент градиента напряжений
Запас прочности на изгиб при максимальной нагрузке
Определение размера по роликам [2]
Угол профиля в точке касания ролика
Диаметр окружности центров роликов
Наименьшее смещение контура
Допуск радиального биения
Допуск на смещение контура
Коэффициент угла контакта ролика
Отклонение размера по роликам верхнее
То же нижнее технологическое
Размер по роликам наименьший
Условия контролепригодности
В случае получения положительных результатов расчета выводы могут быть сформулированы в следующем виде:
Передача работоспособна.
Запас прочности по контактным напряжениям колеса – KH ≥1.
Запас прочности на изгиб при максимальной нагрузке – KFst =14.
Передача контролепригодна.
1 Предварительный расчет валов
Диаметры валов приближенно определяют в результате проектировочного расчёта по следующей формуле:
где d – диаметр вала мм;
Tкр – крутящий момент Н·м;
[t] – допускаемое напряжение материала вала(05 МПа) [3]
Также можно производить расчет по формулам из следующей литературы [411].
При наличии шпоночного паза в опасном сечении вала полученное значение необходимо увеличить на 5 – 10%.
Проверочный расчёт валов проводится на статическую и усталостную прочность а также на жёсткость. Основными изгибающими нагрузками на валы являются силы в зубчатых передачах. Влияние веса вала и насаженных деталей в передаче обычно не учитываются. Силы трения в подшипнике также не учитываются.
2 Проверочный расчет валов на прочность
Валы на прочность проверяются по формуле:
где – напряжение возникающее в теле вала МПа
Tкр – максимальный крутящий момент в опасном сечении Н·мм;
Ми – максимальный изгибающий момент в опасном сечении Н·мм:
где Ми.г и Ми.в – максимальные изгибающие моменты в опасном сечении действующие соответственно в горизонтальной и вертикальной плоскостях).
W – момент сопротивления в опасном сечении мм3;
[] – допускаемое напряжение МПа определяемое при динамическом расчете стальных валов по пределу усталости с учетом факторов вызывающих концентрацию напряжений и диаметру вала
Момент сопротивления в опасном сечении для круглого сплошного вала
Момент сопротивления в опасном сечении для круглого полого вала ( диаметр отверстия в валу-do):
Расчетную нагрузку определяют по моментам или силам (задаваемым обычно тоже на входе или выходе) передаточному отношению и КПД.
Расчетный крутящий момент на валу:
где – КПД участка кинематической цепи от двигателя до рассчитываемого вала;
TД – крутящий момент на валу двигателя Н·м;
U= w0 w – передаточное отношение от двигателя до выходного вала;
w – расчетная частота вращения вала радсек;
w0 – частота вращения вала двигателя радсек;
Рд – мощность на валу двигателя Вт.
Окружная сила на зубчатых колесах:
где d – делительный диаметр зубчатого колеса;
Ткр – крутящий момент на колесе. Н·мм.
Суммарная сила действующая на вал со стороны зубчатых колес (сумма окружной и радиальной сил):
где d – делительный диаметр зубчатого колеса или цепной звездочки мм;
Ткр – крутящий момент на колесе Н·мм.
Определение реакций в опорах и изгибающих моментов
В таблице 4.1 и на рисунке 4.1 приведены формулы для определения реакций опор и изгибающих моментов двухопорных валов с характерными случаями нагружения [3].
А=А1+А2+А3; В=В1+В2+В3 (алгебраическая сумма).
Если приложенная сила Qn имеет направление обратное указанному
на рисунке то реакции в опоре Аn и Bn меняют знак на обратный.
Qn =Аn+Bn (для проверки)
При расчете вал принимают за балку лежащую на шарнирных опорах. Эта расчетная схема точно соответствует действительному положению для валов на подшипниках качения. Для других опор такую расчетную схему можно применить как приближенную. При длинных несамоустанавливающихся подшипниках скольжения расположенных по концам вала равнодействующую реакции подшипника следует предполагать приложенной к точке отстоящей от его кромки со стороны пролета на 13-14 длины подшипника.
Рисунок 4.1 - Определение реакций опор и изгибающих моментов двухопорных валов с приведенными случаями нагружения
3 Расчёт валов на выносливость (усталостную прочность)
Условие прочности имеет вид:
где [S]=25 3 – требуемый коэффициент запаса прочности;
S S – коэффициенты запаса соответственно по нормальным и касательным напряжениям:
где -1 -1 – пределы выносливости материала стального вала при изгибе и кручении с симметричным знакопеременным циклом нагружения МПа;
а а и m=0 m=0 – амплитудные и средние напряжения циклов нормальных и касательных напряжений;
– коэффициенты учитывающие влияние постоянной составляющей цикла на усталость вала;
k k – эффективные коэффициенты компенсации напряжений при изгибе;
– масштабные факторы;
=04 28 – коэффициент поверхностного упрочнения.
то условие прочности выполняется.
4 Расчет на жесткость
Вал рассчитанный из условий динамической прочности может не обеспечить нормальной работы зубчатых колес и подшипников если под действием передаваемых усилий он будет чрезмерно деформироваться.
Расчет на жесткость сводится к определению прогибов и углов наклона оси вала и к сопоставлению их с допускаемыми. Допускаемый прогиб вала y не должен превышать 00001 – 00005 расстояния между опорами или 001 – 003 модуля под зубчатыми колесами. Углы наклона оси вала в опорах не должны превышать в радианах : 00025 – для цилиндрических роликоподшипников; 00016 – для конических роликоподшипников; 0005 – для однорядных шарикоподшипников; 005 – для сферических подшипников и быть не более 0001 под зубчатыми колесами.
Формулы углов наклона и прогибов двухопорных валов
Углы наклона и прогибы
Окончание таблицы 4.2
В заданиях на курсовое проектирование предусматривается не проектирование муфт для соединения валов а выбор муфты из числа стандартных конструкций с учетом особенностей эксплуатации прибора.
Типоразмер муфты выбираем по диаметру вала и по величине расчётного крутящего момента на данном валу:
где –- коэффициент учитывающий условия эксплуатации (=115 13);
Tном – номинальный крутящий момент Н·м;
[T] – предельный крутящий момент Н·м.
Если соосность валов в процессе монтажа и эксплуатации строго выдерживается (например двигатель крепится к корпусу стаканом имеющим центрирующие выступы) то допустимо устанавливать жёсткие муфты. В этом случае выбираем муфту втулочную по ГОСТ 24246-96. [23].
Рисунок 5.1 – Конструкция втулочной муфты
Если отклонение от соосности соединения валов больше 01 мм (двигатель установлен на плите на лапах) то нужно устанавливать дисковые плавающие или упругие муфты.
Эти муфты допускают у соединяемых валов небольшое отклонение от соосности или несовпадение геометрических осей смещение и перекос их на некоторый угол.
Дисковые муфты или муфты с поводком характеризуются тем что один из закрепляемых на концах осей дисков 1 и 2 или подобных им деталей (рисунок 5.2) имеет на окружности штифт палец или кулачок а другой – соответствующее отверстие или прорезь куда входит этот штифт или палец.
Рисунок 5.2 - Конструкция дисковой муфты
Рисунок 5.3 - Муфта упругая четырехпальцевая
На рисунке 5.3 показана упругая четырехпальцевая муфта имеющая среднюю часть изготовленную из резины. Такое устройство муфты допускает некоторую несоосность и перекос соединяемых валов за счет эластичности средней части муфты.
На рисунке 5.4 показана плавающая муфта состоящая из трех частей: двух одинаковых крайних 1 и 3 и средней части 2. Каждая из крайних частей муфты имеет прорезь в которую входят соответствующие выступы прямоугольного сечения средней части муфты. Выступы расположены перпендикулярно друг к другу. Это позволяет допускать значительное несовпадение осей соединяемых муфтой валов.
Рисунок 5.4 - Муфта плавающая
Конкретные размеры выбранной по диаметру вала и по величине расчётного крутящего момента муфты берут из справочной литературы [39].
ПОДШИПНИКИ СМАЗКА УПЛОТНИТЕЛИ
1 Опоры на стандартных подшипниках качения. Конструирование и расчет
1.1 Конструкции и обозначения
Как правило опорами для валов в данном курсовом проекте служат подшипники качения.
Опоры на стандартных подшипниках качения нашли самое широкое применение как в машиностроении так и в приборостроении и освещены в учебной литературе [241112].
Подшипники качения нормированы следующими стандартами:
ГОСТ 3189-89 «Подшипники шариковые и роликовые. Система условных обозначений»;
ГОСТ 3395-89 «Подшипники шариковые и роликовые. Типы и конструктивные разновидности»;
ГОСТ 520-2002 «Подшипники качения. Общие технические условия»;
ГОСТ 3325-85 «Подшипники качения. Поля допусков и технические требования к посадочным поверхностям валов и корпусов. Посадки»;
ГОСТ 20226-82 «Подшипники качения. Заплечики для установки подшипников качения. Размеры».
1.2 Типы и условное обозначение подшипников
Условное обозначение подшипника состоит из семи цифр (справа налево) (рисунок 6.1).
Рисунок 6.1 Условное обозначение подшипника
В обозначении подшипника первые две цифры (1 и 2) определяют внутренний диаметр подшипника следующим образом:
внутренние диаметры подшипников от 20 мм и более обозначают частным от деления значения этого диаметра на 5 ((например подшипник 305 внутренний диаметр подшипника 25 мм);
внутренние диаметры подшипников от 10 мм до 17 мм определяются из таблицы 6.1 (например подшипник 102);
подшипники с внутренними диаметрами до 9 мм серия диаметров располагается на 2-м месте а на 3-м месте стоит цифра «0». В этом случае внутренний диаметр подшипника определяется цифрой на 1-м месте (например подшипник 1000096).
Внутренние диаметры подшипников
Внутренний диаметр подшипника мм
Серия диаметров может быть: сверхлегкая особо легкая легкая средняя тяжелая.
Тип подшипника определяется (таблица 6.2):
направлением воспринимаемой нагрузки (радиальный – воспринимает нагрузку перпендикулярную оси вращения подшипника; радиально-упорный - воспринимает комбинированную нагрузку; упорный - воспринимает осевую нагрузку);
формой тел качения (шариковый роликовый).
Шариковый радиальный
Шариковый радиальный сферический
Роликовый радиальный с короткими цилиндрическими роликами
Роликовый радиальный со сферическими роликами
Роликовый радиальный с длинными цилиндрическими или игольчатыми роликами
Роликовый радиальный с витыми роликами
Шариковый радиально-упорный
Роликовый конический
Шариковый упорный шариковый упорно-радиальный
Роликовый упорный роликовый упорно-радиальный
Конструктивная разновидность подшипника состоит из двух цифр от 00 до 99.
Серия ширин может быть: узкая особо узкая нормальная широкая особо широкая.
1.3 Классы точности подшипников качения
ГОСТ 520-2002 устанавливает следующие классы точности подшипников качения: нормальный 6 5 4 Т 2. Установлены дополнительные классы точности (7 8) для применения по заказу потребителей в неответственных узлах. Нормальный класс точности для шариковых и роликовых радиальных и шариковых радиально-упорных подшипников обозначается «0» для роликовых конических подшипников – «N».
Классы точности подшипников характеризуются значениями предельных отклонений размеров формы расположения и шероховатости поверхностей подшипников. Числовые значения данных параметров определяются номинальными размерами и классом точности подшипника.
1.4 Поля допусков и посадки подшипников качения
ГОСТ 3325-85 распространяется на подшипниковые узлы машин механизмов и приборов посадочные поверхности которых предназначены для монтажа подшипников качения с номинальным диаметром отверстий до 2500 мм при выполнении следующих условий:
валы сплошные или полые толстостенные ( где d – диаметр внутреннего кольца подшипника D – диаметр отверстия вала);
корпуса толстостенные;
материал валов и корпусов – сталь или чугун;
нагрев подшипников при работе до 100 С0.
Общее обозначение полей допусков подшипников:
для среднего диаметра внутреннего кольца подшипника –
для среднего диаметра наружного кольца подшипника - lD m.
Поля допусков колец подшипника обозначаются буквами L или l по классам точности например L0 L6 l5 l4 .
Диаметры наружного кольца и внутреннего кольца подшипника приняты соответственно за диаметры основного вала и основного отверстия. Однако поле допуска внутреннего кольца располагается вниз от номинального размера (перевернуто относительно нулевой линии). Такое расположение поля допуска позволяет получать посадки внутреннего кольца подшипника с валами с небольшим натягом без применения дополнительных полей допусков валов используя основные отклонения n m k js .
Схемы расположения полей допусков при посадках подшипников на валы и в отверстия корпусов представлены на рисунке 6.2.
Выбор посадок внутреннего кольца подшипника на вал и наружного кольца подшипника в отверстие корпуса зависит от:
вида нагружения кольца подшипника;
режима работы подшипника;
соотношения эквивалентной нагрузки Р и динамической грузоподъемности С;
типа размера и класса точности подшипника.
Различают следующие виды нагружения колец подшипника;
Рисунок 6.2 Схемы расположения полей допусков при посадках подшипников
При местном нагружении действующая на подшипник результирующая радиальная нагрузка воспринимается одним и тем же ограниченным участком дорожки качения кольца и передается соответствующему участку посадочной поверхности вала или корпуса.
При циркуляционном нагружении действующая на подшипник результирующая радиальная нагрузка воспринимается и передается последовательно в процессе вращения всей дорожке качения а следовательно и всей посадочной поверхности вала или корпуса.
При колебательном нагружении неподвижное кольцо подшипника подвергается одновременному воздействию радиальных нагрузок: постоянной по направлению и вращающейся но меньшей или равной по величине первой нагрузке. Равнодействующая этих нагрузок совершает периодическое колебательное движение которое передается ограниченному участку посадочной поверхности.
Между режимами работы подшипника и соотношениями РС установлена следующая зависимость (таблица 6.3):
Режимы работы подшипника
Режим работы подшипника
Отношение нагрузки к динамической
Некоторые конструкции стандартных подшипников качения показаны на рисунке 6.3.
Рисунок 6.3 - Основные типы подшипников качения
Радиальные шариковые подшипники (тип 0. см. таблицу 6.2) – наиболее распространенный тип подшипников. Они предназначены для восприятия радиальных нагрузок но могут воспринимать и осевые. Вследствие точечного контакта тел качения они имеют меньшие потери на трение.
Радиальные роликовые (тип 2) и игольчатые (тип 4) подшипники дают экономию по размерам обеспечивают более высокую жесткость опор но не способны воспринимать осевые нагрузки.
Упорные подшипники (тип 8) способны воспринимать только осевые нагрузки. В опорах они устанавливаются совместно с радиальными обычно в случаях когда те неспособны нести осевую нагрузку или когда осевая нагрузка является превалирующей.
Сферические подшипники (типы 1 и 3) допускают значительные перекосы вала в опорах и применяются либо при невозможности добиться нужной соосности посадочных мест (опоры установленные в раздельных корпусах) либо при длинных нежестких валах имеющих большие перекосы сечений на опорах.
Радиально-упорные шариковые (тип 6) и роликовые конические (тип 7) подшипники предназначены для восприятия комбинированных нагрузок но пригодны для чисто радиальных и чисто осевых. Особенностью этих типов является необходимость обеспечения регулировки зазора по дорожкам качения что усложняет конструкцию. Одновременно это делает рациональным их применение в опорах требующих минимальных регулируемых зазоров или даже натягов.
Габаритные размеры подшипников стандартизованы ГОСТ 3478-79 «Подшипники качения. Основные размеры».
2 Схемы установки опор конструктивные элементы смазывание уплотнение
Различают две принципиальные схемы установки опор – с одной фиксированной опорой и другой «плавающей» (схема Ф рисунок 6.4) и с подпертыми опорами «враспор» или «врастяжку» (схема Р рисунок 6.4) каждая – с двумя вариантами крепления колец подшипников.
Рисунок 6.4 - Примеры конструкции опор с различными схемами установки
В схеме Ф осевые нагрузки воспринимает фиксированная опора А; наличие плавающей опоры необходимо для компенсации неточности продольных размеров и деформаций.
Фиксированной обычно назначают ту опору которая ближе к функциональному элементу требующему точного осевого расположения или же из соображений прочности опор (осевая нагрузка добавляется туда где радиальная меньше если это не противоречит принятой схеме или условиям сборки).
В схеме Р опоры имеют одинаковую осевую фиксацию колец. Осевую нагрузку воспринимает та из них в сторону которой эта нагрузка направлена при переменной по направлению нагрузке – обе опоры. Конструктивно вариант Р проще чем вариант Ф. Неточности продольных размеров и деформации требуют осевого компенсационного зазора или регулировки полученного зазора. Для радиально-упорных подшипников схема Р – единственно возможная.
Фиксация положения колец на валу и в отверстии может осуществляться с помощью заплечиков. Размеры заплечиков стандартизованы ГОСТ 20226-82 «Заплечики для установки подшипников качения. Размеры» [2312].
Галтели фаски и канавки на валу и в отверстии назначаются в зависимости от координат округлений колец подшипников. Их размеры можно найти в справочной литературе [2312].
Смазывание подшипников качения обычно осуществляется той же смазкой что и передач. В ответственных случаях предусматривается специальный подвод смазки с помощью смазочных устройств.
Данные о свойствах стандартных марок масел и рекомендации по их выбору смотри литературу [312].
Рекомендации по выбору способа смазывания содержатся в литературе [3912 ]. Там же даны и конструктивные решения узлов с различными системами смазывания.
В сравнительно быстроходных узлах при скоростном показателе
(dn) = (20 40)104 ммобмин рекомендуется применять капельную или фитильную систему смазывания При очень высоких скоростях
(dn) = (150 200)104 ммобмин рекомендуется подача масляного тумана.
При невысоких скоростях (dn) = (2 5)104 ммобмин применяется смазывание окунанием (уровень масла – до середины тел качения) или разбрызгиванием (наиболее распространенный способ).
Пластичные смазки рационально вносить в полость узла при сборке в расчете на периодическую замену при профилактическом уходе за изделием. Более совершенна система направленного продавливания: свежая смазка подаваемая в полость подшипника под давлением вытесняет через зазоры в уплотнении отработанную. При конструировании таких систем необходимо предусматривать направление подачи и выхода смазки исключающее образование застойных зон.
В ответственных опорах применяется автоматическая подача смазки от централизованной системы.
Конструктивные решения узлов с применением консистентных смазок содержатся в литературе [31213].
Конструкции смазочных устройств – масленок насосов маслораспределителей и др. – смотри в литературе [381213].
При конструировании подшипниковых узлов особое внимание уделяется их уплотнению т.к. необходимо обеспечить отсутствие вытекания смазки из полости подшипника и предохранение от попадания влаги и пыли что часто бывает причиной потери работоспособности опоры.
В настоящем курсовом рекомендуется чаще всего применять манжетные уплотнения.
Манжета представляет собой выполненное из мягкого упругого материала кольцо с воротником охватывающим вал. Под действием давления в уплотняемой полости воротник манжеты плотно охватывает вал с силой пропорциональной давлению. Для обеспечения постоянного натяга воротник стягивают на валу кольцевой пружиной.
Манжеты ранее изготовляли из кожи. В настоящее время манжеты чаще всего изготовляют из пластиков типа поливинилхлоридов и фторопластов превосходящих кожу по упругости и износостойкости. Полихлорвиниловые манжеты выдерживают температуру до 80 °С. Фторопластовые манжеты могут работать при температурах до 300 °С.
Широко применяют в машиностроении армированные манжеты для валов (рисунок 6.5). Эти уплотнения представляют собой самостоятельную конструкцию целиком устанавливаемую в корпус; манжету изготовляют из синтетических материалов что позволяет придать ей любую форму; воротник манжеты стягивается на валу кольцевой витой цилиндрической пружиной (браслетной пружиной) строгого регламентированной силой.
Рисунок 6.5 - Конструкции армированных манжет
Манжеты изготовляют прессованием или пресс-литьем (с опрессовкой внутренних металлических элементов) из эластичных износостойких масло- и химически стойких пластиков и резины. Браслетные пружины изготовляют из пружинной проволоки диаметром 02-05 мм и подвергают закалке и среднему отпуску защищают кадмированием цинкованием или делают их из бронзы.
Способы установки манжетных уплотнений в корпусах показаны на рисунке 6.6. При способе установки показанном на рисунке 6.6 I соединение с корпусом достигается за счет упругого радиального сжатия манжеты при вводе в корпус; однако соединение получается ненадежное. В конструкции на рисунке 6.6 II уплотнение предварительно сжатое вводят в выточку в корпусе; высота буртика у входа в канавку не должна превышать допустимого упругого сжатия манжеты.
Рисунок 6.6 - Способы установки манжет
Поверхности по которым работают манжеты должны обладать твердостью не менее 45 HRC и иметь шероховатость не более Ra = 016 ÷ 032 мкм.
На рисунке 6.7 I-III показаны три случая установки манжет. Во втором и третьем случаях необходимо предупредить возможность просачивания масла по зазору между валом и втулкой (или ступицей насадной детали). Это достигается обработкой торцов а до шероховатости Ra = 063 ÷ 125 мкм и соблюдением строгой перпендикулярности торцов относительно оси отверстия. Для обеспечения полной герметичности рекомендуется покрывать торцы герметизирующими мазями или устанавливать на торцах уплотнительные прокладки.
Рисунок 6.7 - Основные случаи установки манжетных уплотнений:
I – на вал; II – на промежуточную втулку; III – на ступицу насадной детали
На валах на которые надевают манжету при сборке должны быть предусмотрены пологие фаски. Это избавляет от необходимости применять специальные монтажные приспособления например монтажную втулку.
Более подробно конструкции уплотнений их сравнительный анализ методика выбора и расчета подробно изложены в литературе [381213].
3 Порядок проектирования опор
. Из технического задания а также по мере принятия решений определяются основные требования к проектируемым опорам.
Сразу из задания можно определить рабочие температуры вид и характер нагрузки нормируемый ресурс (срок службы). В ходе разработки эскизного проекта после выбора двигателя и оценки сил полезного сопротивления можно оценить и предварительно определить значение нагрузок.
. Определяются возможные варианты опор из которых выбирается оптимальный по конструктивным и экономическим (тип производства цена подшипника и т.п.) соображениям. На данном этапе определяют:
-схему установки опор;
-систему смазки и уплотнения;
-обеспечение прочности (при необходимости).
Поскольку в любом проектировании одним из основных критериев является стоимость изделия в первую очередь необходимо проанализировать возможность применения сравнительно дешевых радиальных шариковых подшипников а затем учитывая возможность максимального удовлетворения предъявляемых требований остановить свой выбор на конкретном типе подшипника.
Выбор серии связан с требуемой статической грузоподъемностью или долговечностью и заданными или считающимися рациональными диаметрами вала и отверстия.
Часто задается диаметр вала – например для первого вала передачи он принимается равным диаметру вала двигателя для других валов определяется из условия прочности или же по принципу унификации принимается для всех валов одинаковым. Так как при всех прочих достаточных показателях легкие серии имеют меньшие габариты и меньшую стоимость в первую очередь следует анализировать возможность применения подшипников легких серий и только при установлении их непригодности (недостаточной прочности или долговечности) переходить к подшипникам более тяжелых серий.
При проектировании опор на радиально-упорных подшипниках возникает вопрос о выборе угла контакта.
Различные углы контакта предусмотрены для различных соотношений осевой и радиальной нагрузок.
Класс точности подшипника выбирается в зависимости от наличия дополнительных требований к точности вращения вала. В отсчетных передачах он находится предварительным расчетом схемы на точность или принимается по аналогии с имеющимся прототипом. Повышенная точность может оправдать себя также при высоких скоростях вращения – 10 20 тыс. обмин. При выборе подшипников высоких классов точности следует иметь в виду их резко возрастающую с повышением класса точности стоимость.
В силовых механизмах общего назначения – зубчатых фрикционных или других передачах в мальтийских и кулачковых механизмах – обычно бывает достаточным класс точности 0.
При выборе схемы установки опор часто критерием является точность осевого положения вала. При требованиях повышенной точности принимается либо схема с фиксированной опорой либо установка подшипников предусматривающая регулировку зазора. При этом необходимо учесть что при большой длине вала и значительных температурных деформациях а также при переменных осевых нагрузках рационален только первый вариант. В случаях когда сочетается требование высокой точности с большой длиной вала возможна установка в одной опоре сдвоенного радиально-упорного или двух (в том числе и радиальных) подшипников с осевой регулировкой зазора. Схемы с регулировкой зазора необходимы также при требованиях высокой точности радиального положения вала.
). Предварительный расчет производится для определения приемлемости выбранного варианта опор. В данном курсовом проекте чаще всего размеры валов модули зубчатых колес габаритные размеры соответственно и размеры подшипника выбирают из конструктивных и экономических соображений. Поэтому в большинстве случаев предварительный расчет опор показывает очень большие коэффициенты запаса. В таком случае в пояснительной записке к курсовому проекту приводится только окончательный (проверочный) расчет опор который включает расчет на долговечность и на прочность (при необходимости).
Подбор подшипников шариковых и радиальных с цилиндрическими роликами при действии на них только радиальных нагрузок ведут в таком порядке:
а) выполняют эскизную компоновку узла и приближенно намечают расстояние между подшипниками;
б) определяют реакции опор;
в) определяют эквивалентные нагрузки подшипников;
г) задавшись долговечностью наиболее нагруженного подшипника вычисляют требуемую динамическую грузоподъемность его ;
д) подбирают по диаметру посадочного места номер подшипника начиная с легких серий находят его динамическую грузоподъемность и проверяют выполнение условия:
где - значение динамической грузоподъемности по каталогу.
Если это условие не выполнено то переходят от легкой серии к средней или тяжелой (при том же диаметре цапфы ).
Если подшипник по своим габаритам применить в данном узле нет возможности то следует перейти к другому типу подшипника например от шариковых к роликовым или к другой схеме расположения их на валу. При осложнениях в выборе радиально-упорных подшипников (при наличии больших осевых нагрузок и др.) рекомендуется переходить на подшипники с большим углом контакта - . В некоторых случаях может оказаться что все эти меры не дадут желаемого эффекта тогда следует увеличить диаметр посадочного места и проверить подшипник большего номера.
Если значительно выше даже при применении подшипника легкой серии что часто имеет место для тихоходных валов редукторов с цилиндрическими прямозубыми колесами и для валов колес червячных редукторов то диаметр цапфы вала уменьшать ни в коем случае не следует так как он определен из расчета на прочность. Расчетная долговечность подшипника будет намного больше регламентированной.
Выбор радиально-упорных шариковых и конических роликовых подшипников ведут в другой последовательности:
а) учитывая условия эксплуатации конструкцию узла диаметр цапфы намечают типоразмер подшипника;
б) выполняют эскизную компоновку узла определяют точки приложения радиальных реакций (размер а который зависит от )
в) определяют суммарные реакции опор;
г) вычисляют эквивалентные нагрузки подшипников (коэффициенты и зависят от величины для нахождения которой необходимо знать типоразмер подшипника);
д) по таблицам приложения или по каталогу определяют динамическую грузоподъемность намеченного подшипника;
е) по эквивалентной нагрузке и динамической грузоподъемности вычисляют теоретическую долговечность подшипника которая не должна быть меньше требуемой. Если это условие не обеспечивается то выбирают подшипники других серий и типов увеличивают диаметр цапфы вала.
Если предварительный расчет показал что коэффициент запаса по долговечности не более 11 то необходимо заменить выбранный подшипник на более долговечный (прочный) либо привести для обоснования выбора расчет на статическую грузоподъемность.
Окончательный выбор опор.
На этом этапе необходимо определить:
1. Типоразмеры подшипников при необходимости измененные по результатам предварительного расчета.
2. Посадки внутренних и наружных колец подшипников особенности их крепления.
Выбор посадок колец подшипников зависит от ряда факторов важнейшие из которых следующие:
–вид нагружения кольца – местное циркуляционное или колебательное а также чувствительность подшипника к нему;
–относительная нагруженность подшипника определяемая как отношение нагрузки к грузоподъемности подшипника;
–требуемые зазоры или натяги по дорожкам качения определяемые скоростью вращения заданными точностью положения оси и жесткостью опоры;
–податливость сопрягаемых деталей – вала и корпуса;
–условия сборки и регулирования в том числе при ремонтах.
Для колец циркуляционно или колебательно нагруженных рекомендуются посадки с натягом для местно нагруженных – с зазором позволяющим постоянное смещение наиболее нагруженного участка кольца в процессе работы.
Чем выше относительная нагруженность подшипника и больше податливость сопрягаемых деталей тем туже берутся посадки по обоим кольцам так как вызванные нагрузкой деформации могут привести к появлению нежелательных зазоров в посадках.
Чем выше требования к точности положения оси и жесткости опоры тем меньше как допустимые зазоры в посадках колец так и зазоры зависящие от деформации колец при натягах а также зазоры по дорожкам качения. При повышенных скоростях наоборот требуются увеличенные зазоры по дорожкам качения. Наконец большие натяги усложняют сборку а для регулируемых колец натяги недопустимы.
3. Конструкцию смазочных и уплотнительных мест и деталей.
Расчеты подтверждающие работоспособность.
Основные критерии работоспособности подшипника качения - его динамическая и статическая грузоподъемность.
Динамическую грузоподъемность и долговечность рассчитывают согласно ГОСТ 18855-94.
Метод подбора подшипников по динамической грузоподъемности применяют в тех случаях когда частота вращения кольца обмин. При обмин в расчетах следует принимать обмин.
Статическую грузоподъемность Co (при необходимости) рассчитывают согласно ГОСТ 18854-94. Подбор подшипников по статической грузоподъемности в данном методическом пособии не рассматривается.
4 Требуемая долговечность работы подшипника LN
Номинальная долговечность (ресурс) подшипника в миллионах оборотов:
где С – динамическая грузоподъемность по каталогу;
Р – эквивалентная нагрузка;
– показатель степени:
для шарикоподшипников
для роликоподшипников .
Номинальная долговечность в часах:
L – долговечность подшипника час;
n – скорость вращения об. мин.
При расчетах следует строго следить за тем чтобы в формулах С и Р были выражены в одних и тех же единицах. Для однорядных и двухрядных сферических радиальных шарикоподшипников однорядных радиально-упорных шарикоподшипников и роликоподшипников эквивалентная нагрузка:
где V – коэффициент вращения кольца; при вращении внутреннего кольца V = 1 при вращении наружного – V = 1.3;
– радиальная нагрузка Н;
– осевая нагрузка Н.
Значения X и Y см. в таблице 6.5. Значения Кб – в таблице 6.4; значения КТ – в таблице 6.6.
Значение коэффициента Кб
Нагрузка на подшипник
Примеры использования
Спокойная без толчков
Ролики ленточных конвейеров
Легкие толчки кратковременные перегрузки до 125 % номинальной (расчетной) нагрузки
Прецизионные зубчатые передачи металлорежущие станки (кроме строгальных и долбежных) блоки электродвигатели малой и средней
мощности легкие вентиляторы и воздуходувки
Умеренные толчки вибрационная нагрузка кратковременная перегрузка до 150% номинальной (расчетной) нагрузки
Буксы рельсового подвижного состава зубчатые передачи 7-й и 8-й степеней точности редукторы всех конструкций винтовые конвейеры
То же в условиях повышенной надежности
Центрифуги мощные электрические машины энергетическое оборудование
Нагрузки со значительными толчками и вибрацией кратковременные перегрузки до 200% номинальной (расчетной) нагрузки
Зубчатые передачи 9-й степени точности дробилки и копры кривошипно-шатунные механизмы валки прокатных станов мощные вентиляторы и эксгаустеры
Нагрузки c сильными ударами кратковременные перегрузки до 300% номинальной× (расчетной) нагрузки
Тяжелые ковочные машины лесопильные рамы рабочие рольганги у крупносортных станов блюмингов и слябингов
Значения X и V для подшипников
Радиальные однорядные и двухрядные
Радиалъно-упорные конические и радиальные самоустанавливающиеся роликоподшипники
Радиально-упорные шарикоподшипники
Продолжение таблицы 6.5
Значение коэффициента Кт
Рабочая температура подшипника °С
Эквивалентная нагрузка для однорядных и двухрядных подшипников с короткими цилиндрическими роликами (без бортов на наружном или внутреннем кольцах):
Эквивалентная нагрузка для упорных подшипников (шариковых и роликовых):
Для радиально-упорных шарикоподшипников с номинальным углом контакта и конических роликоподшипников коэффициенты радиальной (X) и осевой (Y) нагрузки выбирают в зависимости от отношения коэффициента осевого нагружения и угла контакта . Величины X и Y для радиальных и радиально-упорных шарикоподшипников с углом выбирают по величине отношения осевой нагрузки к его статической грузоподъемности: . При выборе Y следует применять линейную интерполяцию.
При подборе радиальных и радиально-упорных шарикоподшипников а также конических роликовых подшипников необходимо учитывать что осевая нагрузка не оказывает влияния на величину эквивалентной нагрузки до тех пор пока значение не превысит определенной величины (значение выбирают по таблицам или формулам).
Учитывая указанное выше в формуле для определения эквивалентной нагрузки при следует принимать Y = 0.
Для шариковых радиально-упорных подшипников с углом контакта величину определяют по формуле:
Для тех же подшипников с углом контакта :
Для подшипников с углами контакта величину e можно определить из графика (рисунок 6.9).
Рисунок 6.9 - График для определения в зависимости от и
При подборе двухрядных радиально-упорных шариковых или конических роликовых подшипников надо иметь в виду что даже небольшие осевые силы влияют на величину эквивалентной нагрузки.
Следует учитывать что при расчете динамической грузоподъемности и эквивалентной динамической нагрузки узла состоящего из сдвоенных радиально-упорных подшипников установленных узкими или широкими торцами наружных колец друг к другу пару одинаковых подшипников рассматривают как один двухрядный радиально-упорный подшипник.
Сдвоенные радиально-упорные шариковые или конические роликовые подшипники при отношении рассчитывают как двухрядные. Если то в двухрядных подшипниках будет работать только один ряд тел качения и величину динамической грузоподъемности следует принимать такой же как для однорядного подшипника.
В радиально-упорных подшипниках при действии на них радиальных нагрузок возникают осевые составляющие определяемые по формулам:
– для конических роликоподшипников; (6.9)
– для радиально-упорных шарикоподшипников (6.10)
Рисунок 6.10 - Схема действия сил в радиально-упорных подшипниках установленных:
а - в распор б — врастяжку
Осевые нагрузки действующие па радиально-упорные конические подшипники определяют с учетом схемы действия внешних сил в зависимости от относительного расположения подшипников должны быть учтены осевые составляющие от радиальных нагрузок действующие на каждый подшипник (рисунок 6.10)
Если радиально-упорные подшипники установлены по концам вала в распор или врастяжку то результирующие осевые нагрузки каждого подшипника определяют с учетом действия внешней осевой нагрузки (осевая сила червяка осевые силы косозубых или конических зубчатых колес и пр.);
Результирующие осевые нагрузки подшипников определяют по таблице 6.7.
Ориентировочные рекомендации по выбору подшипников даны в таблице 6.8.
Все данные для расчета берутся из технического задания и чертежа общего вида.
Формулы для расчета осевых нагрузок
Рекомендации по выбору радиально-упорных шарикорикоподшипников
Конструктивное обозначение и угол контакта
Осевая составляющая радиальной нагрузки в долях от
Допустимо использование особо легкой и сверхлегкой серий
При весьма высоких скоростях легкая серия предпочтительнее
Для высоких скоростей подшипник с данным углом контакта непригоден.
Примечание: применяют однорядные радиальные шариковые подшипники
5 Пример расчёта работоспособности подшипников качения
требуемая долговечность работы подшипника:
крутящий момент T1 = 1.1 Н м
делительный диаметрзубчатого колеса d1=36 мм
Рассчитаем эквивалентную нагрузку Р:
– коэффициент учитывающий какое кольцо вращается (для внутреннего 1);
Fr – радиальная нагрузка на подшипник Н;
y – коэффициент осевой нагрузки;
Fa – осевая нагрузка на подшипник с учётом осевой составляющей от действия радиальной нагрузки Н;
kT – коэффициент учитывающий температуру подшипника (при t100ºC kT=1);
k – коэффициент безопасности (нагрузка с лёгкими толчками и кратковременными перегрузками до 125% номинальной нагрузки k=11).
Рисунок 4.3 Схема действия сил
Определение реакций опор и осевой силы
Горизонтальная плоскость
Вертикальная плоскость
Рассчитаем осевые составляющие:
где e=057 – вспомогательный коэффициент ( y=100).
Таким образом имеем:
– результирующая осевая нагрузка: Н;
– эквивалентная динамическая нагрузка: Н;
– динамическая грузоподъёмность: С= 695 Н (табличное значение по каталогу для данного подшипника)
– долговечность подшипника: 31432часов;
– запас долговечности:;
Можно сделать следующий вывод: срок службы подшипников достаточен.
Передача винт-гайка представляет собой кинематическую винтовую пару которую используют для преобразования с большой плавностью и точностью хода вращательного движения в поступательное. Ведущим звеном совершающим вращательное движение может быть как винт (рисунок 7. 1) так и гайка. В силовых механизмах большее распространение получила трапецеидальная резьба
(ГОСТ 9484-81). В механизмах приборов для получения точных перемещений используют метрическую резьбу.
Рисунок 7.1 - Передача винт-гайка
Поскольку основным видом разрушения в передачах винт-гайка является изнашивание сопряженных винтовых поверхностей средний диаметр резьбы обычно выбирают исходя из критерия работоспособности для совпадающих поверхностей зависящем от межвиткового давления и допускаемого давления: p [р].
Допускаемые давления выбирают исходя из условий работы и материалов винта и гайки которые должны составлять износостойкую антифрикционную пару.
1 Кинематика и КПД передачи
Скорость поступательного перемещения V гайки или винта мс
где z – число заходов винта;
n – частота вращения гайки или винта 1мин.
При определении КПД пренебрегают потерями в опорах и его определяют приближенно как отношение работ на завинчивание винта без учета сил трения
( =0 и ρ=0) и с учетом сил трения ( 0 и ρ0). Тогда используя зависимость между моментом сопротивления в резьбе и осевой силой получим:
где - угол подъема резьбы град
- приведенный угол трения в резьбе град.
Из этой формулы видно что КПД передачи возрастает с увеличением угла подъема и уменьшением коэффициента трения в резьбе (уменьшением ρ).
Для увеличения угла подъема в механизмах применяют многозаходные винты. Ход резьбы в этом случае (P и z – шаг и число заходов резьбы). Однако винты с углом >25° на практике не применяют так как дальнейшее увеличение не дает существенного повышения КПД а передаточное отношение при этом снижается. Обычно ≤ 07.
Для повышения КПД механизмов стремятся уменьшить коэффициент трения в резьбе путем изготовления гаек из антифрикционных материалов (бронзы латуни и др.) смазывания и тщательной обработки контактирующих поверхностей.
Средний диаметр винта по условию износостойкости:
где yr – коэффициент высоты гайки ;( Н1 – высота гайки)
– осевая нагрузка Н;
[p] – допустимое давление в резьбе для материала винтовой пары сталь-бронза [r]=8 10 МПа.
Потребное число рабочих витков определяющих высоту гайки находят по формуле:
где – осевая нагрузка Н;
d2– средний диаметр резьбы мм;
h – рабочая высота профиля мм;
[р] – допустимое давление в резьбе МПа.
Высота гайки определяется по следующей формуле:
где р – шаг резьбы мм.
Ходовые винты изготовляют из высокоуглеродистых сталей 40 45 50 40ХН 50ХГ 65Г и др. с закалкой до твердости 40 50 HRC. Гайки изготовляют из оловянистых бронз БрО10Ф1 БрО6Ц6СЗ и др. для высоких окружных скоростей (01—025 мс) а для малых окружных скоростей используют антифрикционные чугуны марок АВЧ-1 АВЧ-2 АКЧ-1 АКЧ-2 или серые чугуны марок СЧ 15 СЧ 20.
2 Проверка на износостойкость передачи винт-гайка
Работоспособность передачи по износу оценивается условно по среднему контактному давлению на рабочих поверхностях витков
где d2 – средний диаметр резьбы мм
h – рабочая высота профиля резьбы мм;
[р] – допустимое межвитковое давление в резьбе МПа.
Значения допускаемых давлений [р] для пар винт-гайка из закаленной стали и бронзы составляют 10-13 МПа; незакаленной стали и бронзы 8-10 МПа; незакаленной стали и антифрикционного чугуна 6-7 МПа; незакаленной стали и серого чугуна 4-5 МПа. Для механизмов точных перемещений (делительных др.) значения [р] принимают в 2-З раза меньше чем для механизмов общего назначения.
3 Проверка винта на устойчивость
Проверка винта на устойчивость осуществляется исходя из неравенства:
Fкр – критическая сила определяемая по формуле:
где Jпр – приведенный момент инерции сечения винта определяемый по формуле:
d – наружный диаметр винта мм;
d1 – внутренний диаметр резьбы винта мм;
E – модуль упругости МПа;
m – коэффициент закрепления концов винта (m =15 если винт закреплен по концам шарнирно и m=10 если винт закреплен консольно).
Коэффициент запаса устойчивости:
На рисунке 7.2 показаны варианты конструктивных решений установки невращающейся гайки в корпус.
В механизмах к которым предъявляются жесткие требования компенсации износа с целью уменьшения «мертвого» хода (зазора между витками винта и гайки) применяют разрезные гайки (рисунок 7.3) или специальные устройства (например пружинные) обеспечивающие радиальную или осевую выборку зазора [389].
Рисунок 7.2 - Невращающаяся гайка установленная в корпус
Рисунок 7.3 - Разрезная гайка обеспечивающая осевую выборку зазора
Различают направляющие для прямолинейного перемещения с трением скольжения и с трением качения. Конструктивно их выполняют открытыми или закрытыми [2389].
Направляющие с трением скольжения бывают: с плоскими поверхностями и с цилиндрическими поверхностями.
На рисунке 8.1 приведены различные примеры конструктивного решения направляющих с плоскими поверхностями.
Рисунок 8.1 - Направляющие:
а – призматические с регулируемой планкой; б – типа «ласточкин хвост».
В цилиндрических направляющих роль направляющего элемента выполняет цилиндрическая поверхность деталей.
Рисунок 8.2 - Цилиндрические направляющие с устройством для предотвращения проворачивания
1 Трение в направляющих
В направляющих изображенных на рисунке 8.1 сила трения определяется зависимостью :
где Q – нагрузка на каретку( поперечная сила) Н;
– коэффициент трения.
В призматических направляющих (рисунок 8.3) реакции R и R определяются из зависимости:
Рисунок 8.3 Призматические направляющие
При движении каретки возникают силы трения F и F определяемые по формуле
где – коэффициент трения;
Q – нагрузка на каретку Н.
При работе направляющих иногда происходит так называемое силовое заклинивание или резкое увеличение в направляющих сил трения в результате значительного смещения точки приложения внешних нагрузок.
При конструировании направляющих необходимо устранить возможность заклинивания. Условия заклинивания зависят от длины направляющей L плеча приложения внешней силы l и коэффициента трения (рисунок 8.4).
Рисунок 8.4 - Схема к расчету зависимости L и l
Для призматических направляющих обычного типа зависимость выражается следующим соотношением:
L – длина направляющей мм;
l – плечо приложения внешней силы мм.
Значения величин коэффициентов трения скольжения см. таблицы 8.1 и 8.2.
Значения коэффициентов трения
Материал трущихся поверхностей
По стали марки У8 незакаленной
По стали марки У8 закаленной
Заклинивание системы может быть вызвано большим перепадом температур (температурное заклинивание). Для предохранения от температурных заклиниваний материалы трущихся деталей должны по возможности иметь одинаковые коэффициенты температурного расширения или между ними должен быть оставлен гарантированный зазор величина которого компенсировала бы величины линейных расширений сопрягаемых деталей.
Для проверки правильности выбранной посадки для сопрягаемых деталей в направляющих необходимо производить проверочный расчет для минимальной и максимальной температур по формуле:
где – минимальный зазор при данной температуре мм;
D – наименьший диаметр или линейный размер охватывающей детали при данной посадке мм;
D1 – наибольший диаметр или линейный размер охватываемой детали мм;
t0 – начальная и t – конечная температура °С;
и – коэффициенты линейного расширения материалов сопрягаемых деталей.
Для обеспечения долговечности направляющих выполняется проверка условия прочности масляного слоя:
где [p]=5 10 МПа – допустимое давление для масляного слоя;
F – поперечная сила действующая на направляющие Н;
S – площадь соприкосновения направляющих и каретки мм2.
2 Выбор материалов направляющих
Основными критериями при выборе материалов для деталей направляющих поступательного движения с трением скольжения служат требуемая долговечность механизма и характеристика трения. Для уменьшения износа и сил трения желательно применить различные материалы для ползуна и направляющих планок. Находят применение комбинации материалов сталь-бронза сталь-латунь сталь-чугун и т.д. однако для неответственных направляющих возможно и применение одноименных материалов для трущихся поверхностей при этом желателен перепад твердости т.е. одна из деталей делается закаленной другая незакаленной.
Наиболее часто встречается сочетание сталь-бронза. При невысоких требованиях к износостойкости выбор марки бронзы и стали а так же термообработка стальных деталей не имеет существенного значения. На первый план выступают стоимость и дефицитность бронзы той или другой марки сталь же применяется со средним содержанием углерода (например стали 30 40 или 45 ГОСТ 1050-60).
3 Пример расчёта направляющих скольжения.
где L=115 мм – длина направляющей или расстояние между опорами;
=0.15 – коэффициент трения (сталь по стали);
Условие незаклинивания:
По результатам расчетов можно утверждать что заклинивания не произойдёт.
Выполним проверку направляющих на прочность:
F = 500 Н– – поперечная сила действующая на направляющие;
S = 600 мм2– площадь опорных поверхностей направляющих.
Условие прочности масляного слоя выполняется.
4 Направляющие качения
В направляющих качения предусматривают планки с дорожками заполняемыми телами качения: шариками роликами или иглами. При перемещениях деталей по этим направляющим тела качения катятся по дорожкам. Тела качения выбирают из применяемых тел в подшипниках качения.
Основными достоинствами направляющих качения являются малые силы сопротивления движению (меньшие до 20 раз чем в направляющих скольжения) малая их зависимость от скорости перемещения и незначительная разница между силами трения покоя и движения. В связи с этим на направляющих качения могут быть достигнуты как быстрые так и весьма медленные равномерные перемещения и установочные перемещения высокой точности.
К недостаткам направляющих качения относят большую сложность изготовления чем направляющих скольжения необходимость термической обработки дорожек качения до высокой твердости повышенные требования к защите от загрязнений.
Направляющие качения применяют если необходимо:
) уменьшить силы сопротивления движению для перемещения деталей вручную и для перемещения тяжелых деталей;
) медленно и равномерно перемещать или точно устанавливать детали;
) перемещать детали с высокой скоростью.
По форме тел качения направляющие разделяют на:
– шариковые применяемые при малых нагрузках;
– роликовые применяемые при значительных нагрузках;
– игольчатые применяемые при ограниченных по высоте габаритах и средних нагрузках;
– роликовые на осях применяемые при малых нагрузках больших ходах и нестесненных габаритах (обычно в качестве вспомогательных).
По направлению воспринимаемых нагрузок направляющие разделяют на: разомкнутые плоские и угловые (рисунок 8.5а); замкнутые в одной плоскости; замкнутые в двух плоскостях (рисунок 8.5б-г); цилиндрические.
Несущая способность роликовых направляющих больше чем шариковых (с плоскими гранями) имеющих те же габаритные размеры; жесткость больше в 25-35 раза.
При перемещении деталей по направляющим качения со скоростью движение тел качения сводится к поступательному перемещению (вместе с сепаратором) со скоростью и к вращению вокруг собственной оси.
Рисунок 8.5 Направляющие качения примеры конструкций
Материалы тел качения - подшипниковые стали типа ШХ 15.
Оптимальные материалы направляющих – закаленные до высокой твердости (HRC 58-63) сталь ШХ15 хромистые и другие легированные стали цементированные на достаточную глубину.
Расчеты направляющих качения производят по формулам Герца. Наибольшее контактное напряжение в роликовых направляющих
в шариковых направляющих с плоскими рабочими гранями
где Q – сила на наиболее нагруженный ролик или шарик;
E – приведенный модуль упругости материала; МПа.
r – радиус ролика или шарика мм;
Конструкцию и типоразмеры направляющих выбирают по справочной литературе [23].
В настоящем курсовом проекте заданием предусмотрено применение только пружин сжатия с неконтролируемыми силовыми параметрами. Поэтому описание проектирования и изображения пружин на чертежах дано в кратком виде.
Основы конструирования и расчета пружин даются в методической и справочной литературе [31415]. В специальной литературе изложены свойства технология и контроль пружин [1516].
Стандартизация винтовых пружин растяжения и сжатия из стали круглого сечения касается классификации (ГОСТ 13764-86) и методов расчета размеров (ГОСТ 13765-86). Для этих пружин стандарты нормируют виток по размерам силовым параметрам и деформациям (ГОСТ 13766-86 – ГОСТ 13777-86). Стандартизация охватывает пружины диаметром от 1 до 300 мм под нагрузку от 1 Н до 100 кН что практически исчерпывает потребности любой отрасли производства.
Общие правила выполнения чертежей деталей содержатся в ГОСТ 2.109-73 «ЕСКД. Основные требования к чертежам». Чертежи пружин кроме этого регламентированы дополнительно ГОСТ 2.401-68 «ЕСКД. Правила выполнения чертежей пружин».
Расчет и подбор пружины нужно проводить когда в целом сделан эскизный проект предварительно определены расположение размеры и вес столика направляющих габаритные размеры всего устройства.
В данном механизме пружина сжимается при движении стола в одну сторону и возвращает стол в обратную сторону. То есть пружина должна преодолеть силу трения в направляющих стола а ее рабочая деформация должна обеспечить максимальный ход стола. При этом пружина не должна быть необоснованно жесткой а по размерам органично вписываться в конструкцию всего устройства.
2 Выбор и расчет пружин
Первый шаг при проектировочном расчете – это определение силы трения в направляющих стола – Pтр. После этого назначается сила предварительного сжатия пружины в крайнем положении Р1 (при установочном сжатии – Н1 мм). Рекомендуется для того чтобы преодолеть силу инерции в момент начала движения стола. Затем необходимо назначить рабочее сжатие пружины(рабочий ход) – Fмм которое обычно равно максимальному ходу стола.
Теперь можно переходить к выбору пружины и расчету ее параметров. Необходимо назначить установочное сжатие пружины Н1 обеспечивающее требуемую силу – Р1. Для этого нужно исходя из эскизного проекта обозначить границы выбираемых параметров пружины а затем назначать их уже из обозначенных границ.
Установочный размер свободная высота и деформация пружин растяжения-сжатия связаны зависимостями:
где H0 – высота свободной пружины мм (для пружин растяжения H0` – размер между зацепами в свободном состоянии);
H1 и H2 – установочные размеры в начале и в конце рабочего хода мм
F1 F2 и F – соответствующие им деформации и рабочий ход мм.
В формулах для пружин сжатия «-» для пружин растяжения «+».
Высоту свободной пружины сжатия в свободном состоянии при проектировочном расчете приблизительно можно определить:
где n – общее число витков.
d- диаметр проволоки мм.
Установочные размеры H1 и H2 определяются по размерным цепочкам на чертеже общего вида.
где f3 - наибольший прогиб одного витка (предельная деформация) мм.
где n – число витков z1 - жесткость витка Нмм.
Значение диаметра пружины и диаметра проволоки стандартной пружины или пружины со стандартизованным витком содержится в соответствующем стандарте. Например указано:
Пружина 84 ГОСТ 13771-68 n = 6.
По стандарту такая пружина имеет диаметр проволоки d=04 мм и наружный диаметр пружины D = 5 мм.
Стандарт устанавливает также жесткость одного витка z1 и наибольший прогиб одного витка f3(предельную деформацию). Числовые значения жесткости лежат в пределах 0102 Нмм (пружина 79 класса 1 разряда 1) до 1837 Нмм (пружина 232 класса 3 разряда 2 ГОСТ 13775-86). Весь диапазон предельных деформаций лежит в пределах от 0065мм до 57030мм.
Таким образом из стандарта можно подобрать несколько значений жесткости одного витка z1 и наибольшего прогиба одного витка f3(предельную деформацию) которым будут соответствовать разные значения диаметра проволоки d и наружного диаметра пружины D .
Число витков пружины в данном курсовом проекте назначается в зависимости от рабочей деформации всей пружины F2 например с учетом ее возможной предельной деформации:
где F3—предельная деформация всей пружины мм;
f3—то же одного витка мм.
В данном курсовом проекте нам важна установочная деформация а не рабочая поэтому желательно выбирать пружину не очень жесткой но и достаточно ограниченной размерами столика. Для пружин сжатия рациональное количество витков при котором не требуется направляющей такое которое дает высоту пружины n=4 12.
Затем по формулам 9.1 9.8 проводится проектировочный расчет параметров нескольких пружин и подбирается та параметры которой более всего соответствуют эскизному проекту.
Для нестандартных пружин диаметр пружины указывается в перечне деталей а диаметр проволоки находится из указания материала или также указывается в перечне например:
Пружина D = 32 n = 408. Проволока 1-02 ГОСТ 9389-75 т.е. диаметр пружины D = 32 мм диаметр проволоки d = 02 мм или указано:
Пружина D = 12 d = 05 n = 65 БрКМц 3-1 т.е. диаметр пружины D = 12 мм диаметр проволоки d = 05 мм.
Для нестандартных пружин растяжения-сжатия жесткость витка-z1 Нмм:
где G – модуль сдвига МПа
f1 – деформация витка мм;
D – диаметр пружины мм;
d – диаметр проволоки мм;
Для нестандартных пружин максимальная допустимая деформация витка f3 мм:
где. G – модуль сдвига МПа
- (допустимое) напряжение МПа принимаются в зависимости от прочности материала
K – коэффициент учитывающий наличие других напряжений кроме расчетных:
где c – индекс пружины:
где D – диаметр пружины мм;
Предельные значения сил:
После окончания проектировочного расчета пружины необходимо выполнить проверочный расчет который и приводится затем в пояснительной записке. В проверочном расчете и в рабочих чертежах необходимо указывать дополнительные и уточненные параметры пружин.
Значение зазора между поджатыми и предыдущими витками задается по зависимости
значение коэффициента Kλ = 010 по ГОСТ 16118-70 для пружин точности 1. группы 2 – 015 группы 3 – 020.
Для пружин с витком поджатым на оборота Kλ может быть увеличено до 025.
Для более ответственных пружин с диаметром проволоки не менее 05 (обычно не менее 16) с целью получения более надежной опорной поверхности крайние витки могут быть сошлифованы. Толщина сошлифованного опорного витка:
где kB – доля сошлифованного витка (обычно но не менее).
Высота пружины в свободном состоянии:
где nB – число прижатых витков
3 Материалы пружин и используемые покрытия
Данные о материалах пружин имеются в литературе [16].
Основным материалом пружин является проволока стальная пружинная углеродистая по ГОСТ 9389-75. Выпускается она диаметром 014 8 мм нормальной и повышенной (П) точности классов прочности I II IIA III. Имеет высокую прочность. Проволока класса IIA с пониженным содержанием серы и фосфора отличается несколько повышенной пластичностью. Мелкие неответственные пружины из проволоки по ГОСТ 9389-75 могут не подвергаться термообработке. Крупные ответственные пружины а также пружины из термообработанной проволоки по ГОСТ 1071-81 с целью снятия наклепа который значительно снижает усталостную прочность как правило подвергаются отпуску.
Вид термообработки на чертежах как правило не указывается (в том числе ТВЧ т.к. пружины прокаливаются насквозь). Указание твердости после термообработки – достаточная гарантия обеспечения требуемых свойств.
Покрытия у пружин применяются как для защиты от коррозии так и в декоративных целях. Покрытие влияет также на механические свойства проволоки. Для пружин наиболее часто применяются следующие виды покрытий.
Для мелких пружин и пружин из цветных металлов применяется пассивирование – нанесение тонкой пленки снижающей химическую активность поверхностного слоя металла.
Цинковое покрытие сравнительно дешево но при пониженных температурах вследствие хрупкости покрытие недостаточно надежно. Последующее пассивирование несколько повышает его химическую стойкость и прочность.
Кадмирование находит применение когда такому покрытию подвергаются другие детали этого изделия. При покрытии кадмием повышаются упругие и прочностные свойства за счет некоторого снижения пластичности.
Фосфатирование – сравнительно дешевый и надежный способ предохранения от коррозии в том числе для мелких пружин. Прочность и упругость как и при применении большинства видов покрытий пружин повышаются однако вследствие малой толщины фосфатной пленки ее влияние на механические свойства незначительно.
Окисные покрытия - широко применяются для других деталей находят применение и для пружин но вследствие хрупкости окисного слоя снижается динамическая прочность пружин. Последующее промасливание или пропитка лаком улучшают свойства этих покрытий.
4 Изображение пружин на общем виде и требования к ним
На чертеже общего вида помещаются:
-изображение пружины как правило упрощенное а в перечне деталей указывается:
-обозначение пружины (для стандартных пружин)
-параметры и размеры пружины и допуски на них если их соблюдение при разработке рабочего чертежа обязательно
-указание на материал пружины (при необходимости)
-дополнительные требования или ссылка на пояснительную записку где они содержатся.
При наличии открытой пружины в конструкции необходимо исходя из условия безопасности оператора по возможности закрывать ее от доступа к ней легкими и простыми в изготовлении деталями типа чехла кожуха экрана.
Наличие пружины чаще всего предполагает что в одну сторону стол перемещается винтовым валом не закрепленным с ним. При этом желательно усиливать места контакта вала и стола. Например в торец вала может быть вставлен закаленный шарик а в место контакта в столе запрессована твердосплавная втулка.
5 Общие требования примеры рабочих чертежей пружин правила изображения
При разработке рабочей документации все данные которые внесены в чертеж общего вида переносятся в рабочую документацию без каких-либо изменений остальные же назначаются разработчиком рабочего чертежа самостоятельно или по расчету с учетом действующих норм и условий конкретного производства.
Номер чертежа пружины выбирается на основе классификационной характеристики по ГОСТ 2.201-68 которая устанавливается в зависимости от формы пружины.
Правила изображения пружин на рабочих чертежах установлены ГОСТ 2.401-68. Изображения пружин и обозначения проставляемых на них размеров показаны на рисунке 9.2.
Рисунок 9.2 Общий вид пружины и обозначение размеров; : А – без поджатых витков Б – поджат один виток; В – поджато два витка; Г – виток поджат и ошлифован; Д – виток ошлифован.
Так как пружины как правило изготавливаются путем гибки из проволоки или ленты размеры и форма сечения содержатся в указании материала поэтому в случае необходимости их показывают только как справочные.
Изображения пружин на рабочих чертежах располагаются горизонтально навивка пружин на изображении – правая кроме тех случаев когда форма зацепов у пружин кручения зависит от направления моментов. Витки пружины изображаются прямыми линиями. При наличии нескольких прижатых опорных витков на чертеже показывают только по одному с каждого конца пружины количество их определяется указанием полного числа витков в технических требованиях. У пружин с числом витков более четырех с каждого конца показывают один-два витка остальные не изображаются центровые линии сечений витков и ось пружины не прерываются.
6 Обозначение на чертежах материала покрытия требований связанных с термообработкой
Материалы стандартных пружин и пружин I разряда со стандартным витком по ГОСТ 13766-68 ГОСТ 13770-68 и ГОСТ 13774-86 могут быть однозначно определены по стандарту. Например если в перечне указано:
Пружина 95 ГОСТ 13766-68 n=225. Материал пружины: Проволока I –045 ГОСТ 9389-75.
Обозначение проволоки вносится в соответствующую графу основной надписи рабочего чертежа.
При необходимости применения пружин стандартных размеров из материала не предусмотренного стандартом перечень содержит указание по типу:
Пружина 452 ГОСТ 13766-68 n=10 P=100 Н 12Х18Н9.
Такое указание обозначает что в данном случае материал пружины – не проволока по ГОСТ 9389-75 как это предусмотрено стандартом а проволока из стали 12Х18Н9 по ГОСТ 18149-72.
Указание материала на чертеже общего вида может содержаться в технических требованиях например по типу:
« 2. Материал поз – Проволока 12Х18Н9 В-П-ХН 35 ГОСТ 18149-72».
В перечне в таком случае должно содержаться указание на пункт технических требований:
Пружина 452 ГОСТ 13766-68 n = 10 P =100 Н.
Покрытия обозначаются по ГОСТ 9.073-77.
Примеры обозначений:
«Покрытие Ц 3 фос» – цинковое 3 мкм фосфатированное
«Покрытие Ц 5 пас» – цинковое 5 мкм пассивированное
«Покрытие Кд 10 хр» – кадмиевое 10 мкм хроматированное
«Покрытие Хим. фос» – фосфатное толщина не оговорена.
7 Допуски размеров пружин
Допуски размеров пружин растяжения-сжатия установлены ГОСТ 16118-70. Их значения даны в зависимости от принятой группы точности по силовым параметрам. Допускается возможность комбинирования групп точности по силовым и размерным параметрам. Допуски диаметров проволоки установлены стандартами на пружинную проволоку и на чертеже не проставляются так как ссылка на стандарт полностью их определяет.
В случае когда на чертеже общего вида материал не обозначен разработчику необходимо задать определенную точность диаметра проволоки. При выборе необходимо руководствоваться требуемым соотношением допуска диаметра и принятой группы точности пружины что установлено ГОСТ 16118-70.
8 Последовательность простановки технических требований на рабочих чертежах
По ГОСТ 2.401-68 основные технические требования на чертеже пружины рекомендуется приводить в следующей последовательности.
G = МПа 3 = МПа или Е = МПа 3 = МПа.
Значения модулей G и Е а также максимальных напряжений при кручении и изгибе 3 и 3 даются как справочные. Для пружин стандартной конструкции их значения не указываются. При этом в технических требованиях должна быть ссылка на стандарт.
Направление навивки пружины
Направление навивки (левое или правое) указывается всегда независимо от того с какой навивкой изображена пружина.
Левая навивка указывается на чертеже общего вида. При отсутствии указаний – навивка правая.
Дается расчетная длина развернутой пружины. Допуски длины устанавливаются технологом и в чертеж не вносятся.
Указывается номинальное число рабочих витков. У пружин без поджатых или отогнутых витков – с допусками если допуски раcположения зацепов этих отклонений не задают.
Указывается полное число витков с отклонениями. В число витков включаются поджатые витки пружин сжатия и отогнутые или нерабочие витки пружин растяжения. В число витков не включаются витки разогнутые для образования зацепов. У пружин без поджатых и отогнутых витков n = n1 указание n1 исключается.
Твердость пружин назначается только в том случае когда пружина подвергается закалке после навивки. Для крупных пружин контроль твердости может производиться на самой пружине. В таком случае требование дополняется указанием места контроля.
Покрытие также указывается только в том случае когда оно наносится на пружину после навивки. При применении проволоки с покрытием такое указание должно содержаться в обозначении проволоки.
Прочие требования например требование к отклонениям шага заневоливанию дробеструйной обработке и др. Требования могут быть указаны ссылкой на нормативный документ и т.п.
Указание на справочные размеры и параметры.
ШПОНКИ. ШПОНОЧНЫЕ СОЕДИНЕНИЯ
Шпоночное соединение предназначено для передачи крутящего момента без предъявления особых требований к точности центрирования деталей.
В настоящем курсовом проекте применяются шпоночные соединение между валами и такими конструктивными элементами как соединительные муфты зубчатые колеса втулки и плиты.
По форме шпонки делятся на:
призматические (ГОСТ 23360-78 «Соединения шпоночные с призматическими шпонками. Размеры шпонок и сечений пазов. Допуски и посадки»);
сегментные (ГОСТ 24071-97 «Соединения шпоночные с сегментными шпонками. Размеры шпонок и сечений пазов. Допуски и посадки»);
клиновые (ГОСТ 24068-80 «Соединения шпоночные с клиновыми шпонками. Размеры шпонок и сечений пазов. Допуски и посадки»);
тангенциальные (ГОСТ 24069-97 «Соединения шпоночные с тангенциальными нормальными шпонками. Размеры шпонок и сечений пазов. Допуски и посадки»).
При использовании призматических шпонок получают как подвижные так и неподвижные соединения; соединения сегментной и клиновой шпонками служат для образования только неподвижных соединений.
1 Призматические шпонки
Основными размерами призматической шпонки являются ширина b высота h и длина шпонки l (рисунок 10.1). Размеры ширины и высоты шпонки а также глубина паза вала t1 и глубина паза втулки t2 зависят от диаметра вала d. Длина шпонки выбирается из ряда: 6 8 10 12 14 16 18 20 22 25 28 32 40 45 50 56 63 70 80 90 100 110 125 140 160 и далее до 500 мм.
Рисунок 10.1 Соединение с призматической шпонкой
Стандарт устанавливает следующие поля допусков размеров призматических шпонок и шпоночных пазов:
высота h – h9 если h > 6 –
длина паза вала L –
глубина паза вала t1 и глубина паза втулки t2 – ЕI = 0; ES = +01 +03 мм.
Призматические шпонки бывают трех исполнений (рисунок 10.2):
Исполнение 1 Исполнение 2 Исполнение 3
Рисунок 10.2 Призматические шпонки
Основным посадочным размером шпоночного соединения является ширина шпонки. По этому размеру установлены следующие типы шпоночных соединений: свободное нормальное и плотное.
В зависимости от характера (типа) шпоночного соединения нормированы следующие поля допусков по ширине паза вала и втулки (таблица 10.1):
Типы шпоночных соединений
шпоночного соединения
Условное обозначение призматической шпонки включает:
обозначение исполнения (исполнение 1 не указывается);
обозначение стандарта.
Пример - Шпонка 2 – 4 ×4 × 12 ГОСТ 23360-78.
Сегментные шпонки применяют для передачи небольших крутящих моментов. Размеры сегментных шпонок и шпоночных пазов выбираются в зависимости от диаметра вала d (рисунок 10.3).
Рисунок 10.3 Соединение с сегментной шпонкой
Стандарт устанавливает следующие поля допусков размеров сегментных шпонок и их пазов:
Сегментные шпонки изготавливают двух исполнений (рисунок 10.4).
Рисунок 10.4 Сегментные шпонки]
Для сегментных шпонок используют следующие виды шпоночных соединений (таблица 10.2).
Виды шпоночных соединений
Примечание - Для термообработанных деталей допускается ширину паза вала изготавливать по H11 ширину паза втулки - по D10.
Условное обозначение сегментной шпонки включает:
Пример - Шпонка 2 – 4 × 65 ГОСТ 24071-97.
3 Расчет шпоночных соединений на прочность
Призматические шпонки применяемые в проектируемых редукторах (приводах) проверяют на смятие (и в некоторых ответственных случаях на срез). Проверке подлежат шпонки под зубчатые колёса на быстроходном и тихоходном валах и под полумуфтой или элементом открытой передачи.
Условие прочности на смятие:
где Ft окружная сила H; (Ft=2Тd)
Aсм=(h-t1) b h t1 стандартные размеры призматической шпонки.
[см] допускаемое напряжение на смятие Hмм2. При стальной ступице и спокойной нагрузке [см] = 110 190 Hмм2; при колебаниях нагрузки [см] следует снижать на 20 25%; при ударной нагрузке снижать на 40 50%; при чугунной ступице приведенные значения [см]снижать вдвое.
Если при проверке шпонки см окажется значительно меньше [см] то можно взять шпонку меньшего сечения но обязательно проверить её на смятие. Если см>[см] то рациональнее перейти на посадку вала с натягом. При этом рекомендуются посадки:
для цилиндрических прямозубых колёс H7 p6 (H7 r6);
для цилиндрических косозубых и червячных колёс H7 r6 (H7s7);
для конических колёс H7s7 (H7t6).
Так как размеры шпонки выбирают по диаметру вала обычно расчет прочности на срез не производится. В необходимых случаях расчет на срез производится по следующей формуле:
где [ср] – допустимое напряжение на срез МПа.
4 Расчёт шпоночных соединений.
Шпонка 4×4×12 ГОСТ 23360-78.
Призматическая шпонка рассчитывается на смятие и на срез.
Из условия прочности на смятие рассчитывается часть шпонки выступающая из вала:
где [см]=30..50 МПа – допустимое напряжение смятия;
T – крутящий момент на валу;
мм – рабочая длина шпонки мм
h -- высота шпонки мм.
t1 -глубина паза вала мм.
Так как см[см] то прочность на смятие обеспечена.
Условие прочности на срез:
Прочность шпонки на срез обеспечена.
4 Обозначение требований к точности шпоночного паза на чертежах
К шпоночным пазам вала и втулки на чертежах предъявляются следующие требования к точности расположения и шероховатости поверхностей:
допуски параллельности и симметричности шпоночного паза определяются по формулам
где Тпарал. – допуск параллельности мкм;
Тсим. – допуск симметричности мкм
Тшп. – допуск шпонки по ширине мкм.
Полученные числовые значения округляются до стандартных значений по
шероховатость поверхностей шпоночного паза зависит от полей допусков размеров шпоночного соединения (Rа не более 32 мкм или 63 мкм).
ШТИФТОВЫЕ СОЕДИНЕНИЯ И КОРПУСНЫЕ ДЕТАЛИ
1 Штифтовые соединения
Штифтовые соединения применяют для крепления деталей (соединение вала со втулкой) или для взаимного ориентирования деталей которые крепят друг к другу винтами или болтами (соединение крышки и корпуса соединение стойки и основания и др.). Эскиз изделия со штифтовыми соединениями двух видов – вал-зубчатое колесо и крышка-корпус (соединение с применением двух штифтов) представлен на рисунке 11.1.
При ориентировании деталей относительно друг друга (соединение крышки и корпуса) обычно используют два штифта но для фиксации углового положения деталей ориентирование которых обеспечивается цилиндрическим сопряжением (например соединение круглой крышки с корпусом) достаточно одного фиксирующего штифта.
Рисунок 11.1 Применение штифтовых соединений
Штифтовые соединения вала со втулкой относятся к разъемным неподвижным соединениям в которых штифт как дополнительный конструктивный элемент обеспечивает взаимную неподвижность деталей. В этом соединении штифт фиксирует детали в осевом и тангенциальном направлениях (предотвращает как осевой сдвиг так и взаимный поворот). В отличие от неразъемных соединений вала и втулки с натягом штифтовые соединения позволяют осуществлять разборку и повторную сборку конструкции с обеспечением того же эффекта что и при первичной сборке. В штифтовом соединении вала с ответной деталью штифт обычно используется для передачи крутящего момента (в соединениях вращающегося вала с зубчатым колесом или со шкивом) но возможны и другие решения например – защита вала от проворота относительно неподвижного корпуса.
Штифтовое соединение крышки и корпуса образует две посадки: штифт-отверстие корпуса и штифт-отверстие крышки а в штифтовом соединении вала с зубчатым колесом следует различать центрирующее сопряжение вал-отверстие зубчатого колеса и две собственно штифтовые посадки: штифт-отверстия (два) во втулке зубчатого колеса и штифт-отверстие вала.
Точность центрирования деталей в штифтовом соединении вала с зубчатым колесом (шкивом ступицей рычага и др.) обеспечивается посадкой колеса на вал. Это обычное центрирующее гладкое цилиндрическое сопряжение для которого можно выбрать посадку с очень малыми зазорами или натягами следовательно предпочтительны переходные посадки.
Поскольку поле допуска на диаметр штифта одинаково по всей длине штифтовые посадки являются посадками в системе вала. Если выбрано основное отклонение поля допуска штифта h (например 4 h8) посадки реализуются в системе основного вала. А если выбрать иное стандартное основное отклонение поля допуска штифта (например m) штифтовые посадки реализуются в системе неосновного вала например 4 F8m6 и 4 K7m6.
Стандарты предусматривают ряд конструкций штифтов в том числе конические цилиндрические с гладкими поверхностями с лысками и насечками (для установки в глухие отверстия) трубчатые в том числе с продольными разрезами. Дополнительными конструктивными элементами штифтов могут быть резьбовые отверстия или резьбовые выступы для извлечения штифтов из глухих отверстий. Штифты обычно изготавливают из стали 45 хотя в некоторых случаях допускается изготовление из сталей А12 10кп и 20кп. Стандартами регламентируются номинальные размеры штифтов и поля допусков их основных размеров что позволяет назначать необходимые типовые посадки штифтов в отверстия корпусов крышек втулок и валов.
Гладкие цилиндрические штифты изготавливают с полями допусков на основную поверхность m6 h8 h9 h11 на длину штифта – по h14 на диаметр глухого отверстия – по Н13 на его глубину – по IT15. Поля допусков резьбовых отверстий штифтов – по 7Н. Конические штифты изготавливают с конусностью 1:50 с полями допусков на угловой размер ± АТ82 или ± АТ102 и с полем допуска на диаметр по h10 или по h11.
Типичный ряд длин штифтов в некотором ограниченном диапазоне мм: 4 5 6 8 10 12 14 16 20 25 30 35 40 45 50 отличается от рядов нормальных линейных размеров.
Условное обозначение штифта включает:
обозначение типа (тип 1 не указывают не указывают и другие если тип однозначно определяется стандартом);
размеры (диаметр d и длину L штифта при необходимости с указанием поля допуска диаметра);
Примеры обозначений штифтов:
Штифт 10 m6 × 60 ГОСТ 3128-70 – штифт диаметр 10 мм длина 60 мм.
Штифт 8 h11 × 45 Хим. Окс. прм. ГОСТ 10773-93 – штифт диаметр 8 мм и длина 45 мм с покрытием Хим. Окс. прм..
Штифтовые соединения крышки и корпуса представляют достаточно сложную задачу связанную с составлением и решением взаимосвязанных размерных цепей. Каждое штифтовое сопряжение включает в себя две простейшие размерные цепи (посадка штифта в отверстие корпуса и посадка штифта в отверстие крышки). Образовавшиеся замыкающие звенья-зазоры (натяги) – будут входить как составляющие звенья в размерные цепи определяющие межосевые размеры штифтового соединения а также их замыкающие звенья-зазоры (натяги) – между образующими штифтов и отверстием корпусной детали (крышки).
Рисунок 11.2 - Эскиз соединения крышка-корпус (ориентирование по двум штифтам)
Кроме намеченных линейных размерных цепей следует также составить и рассчитать еще и угловые размерные цепи поскольку отклонения осей штифтовых отверстий от перпендикулярности также существенно влияет на собираемость изделия.
В связи с тем что обеспечить точность замыкающих звеньев таких размерных цепей методами полной взаимозаменяемости бывает затруднительно достаточно часто прибегают к «технологической компенсации» – применяют совместную окончательную обработку штифтовых отверстий в сборе. Корпус и крышку с предварительно просверленными отверстиями собирают без штифтов и крепят друг к другу затем «совпадающие» отверстия обрабатывают разверткой чем обеспечивается их соосное расположение при фиксированном межосевом расстоянии. Такой технологический процесс можно рассматривать как применение технологии индивидуального производства поскольку каждая крышка подходит только к своему корпусу.
2 Допуски расположения осей отверстий под крепежные детали
Взаимное расположение деталей в узле механизма часто определяется размерами между осями отверстий которые предназначаются под крепежные детали (болты винты резьбовые шпильки установочные штифты) и валы с посаженными на них деталями. Отклонения от номинальных размеров определяющих взаимное расположение отверстий неизбежны но они не должны превосходить пределов определяемых служебным назначением соединения.
Соединения крепежными деталями могут быть двух типов (рисунок 11.3): А – с гарантированными зазорами в обеих соединяемых деталях и Б – с зазорами только в одной из соединяемых деталей в другой имеются резьбовые отверстия или отверстия обеспечивающие натяг.
Рисунок 11.3 - Типы соединений крепежными деталями
При параллельном расположении осей отверстия под крепежные детали располагаются на прямых линиях или на окружностях одной сборочной группы в которую могут входить и другие конструктивные элементы (центрирующие отверстия буртики привалочные плоскости и т.п.).
Диаметры сквозных отверстий соответствующие им гарантированные зазоры допуски расположения осей отверстий для соединений типов А и Б приведены в справочной литературе [10].
Допуски расположения осей отверстий при требованиях взаимозаменяемости устанавливаются исходя из расчетного зазора Sp который определяется по следующей формуле:
где – гарантированный диаметральный зазор под проход крепежной детали мкм;
Sрег – зазор между сквозным отверстием и стержнем крепежной детали который должен быть обеспечен для последующей регулировки взаимного расположения деталей или для облегчения сборки мкм;
Тпер – допуски перпендикулярности осей отверстий к опорной плоскости мкм;
Тс – допуск соосности ступеней крепежной детали мкм.
Если требования к деталям ограничиваются только собираемостью а другие отклонения расположения осей отсутствуют или ими можно пренебречь то принимают:
Допуски расположения осей отверстий под крепежные детали могут устанавливаться одним из двух способов: позиционными допусками (смещением от номинального расположения осей) и предельными отклонениями размеров координирующих оси отверстий. Нормирование позиционных допусков является более предпочтительным комплексно ограничивая отклонение осей от номинального расположения они наиболее полно обеспечивают требования взаимозаменяемости и облегчают оформление чертежей. Позиционные допуски рассчитываются на основе формул единых для всех видов расположения осей отверстий:
для соединений типа А
для соединений типа Б
где Т – позиционный допуск в диаметральном выражении мкм.
В наибольшей степени преимущества позиционных допусков проявляются в серийном и массовом производстве поскольку они упрощают расчет кондукторов и комплексных калибров. Нормирование предельных отклонений координирующих размеров необходимо в тех случаях (обычно для деталей единичного и мелкосерийного производства) когда отверстия получают обработкой по разметке или на координатно-расточных станках а измерение расположения осей производят универсальными средствами.
Например для осей четырех отверстий (рисунок 11.4) под болты М4-6h (тип соединения деталей А) по справочным данным [10]: диаметры сквозных отверстий 43Н12; Sm позиционный допуск в диаметральном выражении Т=Sр=03 мм; отклонения размеров между осями отверстий dL=± 05 Sр = ± 016мм.
Рисунок 11.4 - Допуски расположения осей отверстий соединения болтами М4:
а) исходное расположение; б) назначение позиционного допуска; в) указание предельных отклонений размеров координирующих оси отверстий
Допуски расположения осей отверстий определяют точность расположения элементов в пределах одной сборочной группы. Расположение сборочной группы в целом относительно других элементов детали (например боковых кромок) нормируют предельными отклонениями размеров координирующих группу непосредственно у размеров или оговаривают записью об общих допусках размеров (отклонения как правило назначают симметричными.
В тех случаях когда в сборочные группы входят центрирующие элементы (например отверстие или выступ – рисунок 11.5) по которым должно быть обеспечено совмещение при сборке их принимают в качестве баз при простановке размеров и допусков определяющих расположение осей отверстий под крепежные детали (рисунок 11.6).
Рисунок 11.5 Соединение с центрирующим элементом по посадке с зазором
Рисунок 11.6 Схема нормирования точности расположения отверстий при наличии центрирующего элемента
Материал и размеры элементов корпуса назначаются из условия его прочности жесткости и технологичности а также от программы выпуска (серийное или единичное производство). Для изготовления корпусных деталей используют чугуны стали и легкие сплавы [91718].
Для удобства сборки редуктора его корпус (см. рисунок 11.7) обычно выполняется разъемным (крышка и основание). Корпуса редукторов могут выполняться гладкими (без выступающих элементов) как с внутренней стороны (рисунок 11.7а) так и с внешней (рисунок 11.7б). В последнем случае выступающие элементы (бобышки подшипниковых гнезд соединительные фланцы ребра жесткости) расположены внутри корпуса фундаментные лапы отсутствуют а места крепления корпуса к фундаментной плите (раме) оформляют в виде ниш. Корпус в таком варианте более эстетичен удобен для обслуживания обладает большей жесткостью и объемом масляной ванны но имеет бльшую массу и усложненную литейную оснастку. Возможны и другие конструктивные решения формы корпусов редукторов.
Основной материал корпусов редукторов в случае серийного производства – серый чугун марки СЧ-15. Толщина стенки основания корпуса определяется по эмпирической зависимости:
гдеТ4 – вращающий момент на выходном валу Н·м.
Толщина стенки крышки корпуса и ребер жесткости:
Толщина фланцев и фундаментных лап принимается по рекомендациям приведенным на рисунке 11.7.
Для соединения крышки с основанием используют болты с наружной нормальной (или уменьшенной) шестигранной головкой или винты с цилиндрической головкой и внутренним шестигранником.
Номинальный диаметр фланцевых болтов определяют по формуле:
Рисунок 11.7 Размеры некоторых элементов корпуса
Номинальный диаметр фундаментных болтов (винтов) для крепления редуктора к фундаментной плите (раме): .
Ширина фланца корпуса и фундаментных лап назначается из условия свободного размещения головки болта (винта) или гайки и возможности поворота гаечного ключа на угол не менее 60.
Размеры некоторых элементов корпуса приводятся на рисунке 11.7.
В случае единичного производства корпус и крышку корпуса выполняют сборными или сварными из пластин изготовленных из малоуглеродистых сталей.
Примеры сборных и сварных конструкций даны в следующей литературе [39].
ОБЩИЕ ТРЕБОВАНИЯ К ОФОРМЛЕНИЮ ПОЯСНИТЕЛЬНОЙ ЗАПИСКИ
Пояснительные записки выполняют в соответствии с требованиями изложенными в ГОСТ 2.105-95 и ГОСТ 2.106-68. Они должны включать документы в указанной ниже последовательности:
обложка к курсовому проекту; (см. приложение 1)
титульный лист к пояснительной записки; (см. приложение 2)
задание на проектирование (см. приложение 3)
Содержание выполняют по форме 5 (ГОСТ 2.106-68) а основную часть и список литературы выполняют на последующих листах по форме 5А (ГОСТ 2.106-68). При этом дополнительные графы могут быть опущены а основные надписи выполняют в соответствии с требованиями ГОСТ 2.104-68 форма 2 и 2а.
Выполняют пояснительные записки рукописным способом на одной стороне листа белой бумаги формата А4 (210x297).
Объем пояснительных записок должен составлять не менее 25 листов.
Расстояние от рамки до границ текста рекомендуется оставлять:
в начале строк - не менее 5 мм;
в конце строк - не менее 3 мм.
Расстояние от верхней и нижней строк текста до верхнем и нижней линий рамки соответственно должно быть не менее 10 мм.
Рубрикация пояснительной записки. Основную часть пояснительной записки при необходимости разделяют на разделы и подразделы. Каждый раздел рекомендуется начинать с нового листа. Разделы должны быть пронумерованы арабскими цифрами. После номера раздела ставится точка.
Подразделы следует нумеровать арабскими цифрами в пределах каждого раздела. Номер подраздела должен состоять из номера раздела и номера подраздела разделенных точкой. В конце номера подраздела также ставят точку.
Наименование разделов должно быть кратким соответствовать содержанию и записываться в виде заголовка прописными (заглавными) буквами. Наименование подразделов записывают в виде заголовков строчными буквами (кроме первой прописной). В конце заголовка точку не ставят. Подчеркивать заголовки и переносить слова в заголовках не допускается.
Расстояние между заголовком и последующим текстом должно быть равно
мм. Расстояние между заголовком подраздела и последней строкой предыдущего текста должно быть равно 15 мм.
Нумерация страниц пояснительной записки должна быть сквозной. Первой страницей является титульный лист.
Формулы. В формулах в качестве символов следует применять обозначения установленные соответствующими стандартами или общепринятые в данном разделе науки.
Значения символов и численных коэффициентов входящих в формулу должны приводиться непосредственно под формулой в той последовательности в какой они даны в формуле. Значение каждого символа и числового коэффициента следует давать с новой строки. Первая строка расшифровки должна начинаться со слова "где" без двоеточия после него.
Формулы на которые имеются ссылки в тексте должны нумероваться в пределах раздела арабскими цифрами. Номер формулы должен состоять из номера раздела и порядкового номера формулы разделенных точкой. Номер формулы следует заключать в скобки и помещать на правой стороне листа на уровне нижней строки формулы к которой он относится.
При ссылке в тексте на формулу необходимо указывать ее полный номер в скобках например: "В формуле (2.1)".
Иллюстрации. Количество иллюстраций помещаемых в записке определяется ее содержанием и должно быть достаточным для пояснения излагаемого текста. Ссылки на графические документы курсовых проектов при описании схем или конструкций приборов не допускаются.
Иллюстрации должны размещаться сразу после ссылки на них в тексте либо на следующем листе.
Все иллюстрации (фотографии схемы чертежи и пр.) именуются рисунками. Рисунки нумеруются последовательно в пределах всей записки арабскими цифрами. На все рисунки в тексте должны быть ссылки при этом следует указывать его полный номер например: "(рисунок 2.)". Повторные ссылки на рисунки следует давать с сокращенным словом "смотри" например: "(см. рисунок 2)".
Каждый рисунок должен сопровождаться содержательной подписью.
Таблицы. Цифровой материал помещенный в записке допускается оформлять в виде таблиц.
Все таблицы если их несколько должны бить пронумерованы арабскими цифрами в пределах всей пояснительной записки. Надпись "Таблица" с указанием порядкового номера таблицы например "Таблица 2" помещается над правым верхним углом таблицы.
Если в пояснительной записке только одна таблица то номер ей не присваивают и слово "Таблица" не пишут.
Каждая таблица должна иметь содержательный заголовок который помещают после слова "Таблица ".
На все таблицы должны быть ссылки в тексте при этом слово "Таблица" в тексте пишут полностью например " в таблице 2". Повторные ссылки на таблицу следует давать с сокращенным словом "смотри" например: "(см.таблицу 2)".
Таблицу следует помещать после первого упоминания о ней в тексте.
При переносе таблицы на следующую страницу головку таблицы повторяют и под ней помещают слова "Продолжение таблицы" с указанием номера. Если головка таблицы громоздка допускается ее не повторять; в этом случае пронумеровывают графы и повторяют их нумерацию на следующей странице.
Список литературы. В список литературы включают все использованные источники которые следует располагать в порядке появления ссылок в тексте пояснительной записки.
Сведения о книгах должны включать: фамилию и инициалы автора заглавие книги место издания издательство и год издания объем в страницах.
Сведения о статье из периодического издания должны включать: фамилию и инициалы автора заглавие статьи наименование издания (журнала) наименование серии (если таковая имеется) год выпуска номер издания (журнала) страницы на которых помещена статья
Ссылки. При ссылке в тексте на источник документальной информации следует приводить порядковый номер по списку литературы заключенный в квадратные скобки.
Приложения оформляются как продолжение пояснительной записки на последующих ее страницах.
Каждое приложение начинают с новой страницы; в правом верхнем углу пишут слово “Приложение”. Каждое приложение должно иметь тематический заголовок.
Если в пояснительной записке имеется два или более приложении их нумеруют последовательно арабскими цифрами например: "Приложение 2".
1 Оформление графических документов
Графические документы курсовых проектов выполняется с соблюдением требований ГОСТов на листах формата А1.
Каждый чертеж должен иметь основную надпись соответствующую
Перечень выполняется на отдельных листах формата А4 которые по нумерации являются продолжением листа (листов) общего вида. Листы перечня должны быть скреплены с чертежом или пояснительной запиской. В некоторых случаях допускается составление перечня на листе общего вида.
Графическая часть проекта должна составлять 2 3 листа формата А1 по
ГОСТ 2.301-68 и содержать:
– чертеж общего вида привода состоящего например из двигателя муфты редуктора передачи винт-гайка направляющих рамы или плиты;
– рабочие чертежи деталей (корпус вал зубчатые колеса и т.д.).
2 Выполнение и защита курсовых проектов
Курсовые проекты должны выполняться в сроки установленные учебным планом.
Студент в течение пятнадцати дней после начала семестра должен получить у руководителя задание на очередной курсовой проект. При выдаче задания устанавливается план-график выполнения проекта с указанием сроков представления основных разделов а также сроков завершения и защиты курсового проекта.
В течение семестра студент обязан систематически бывать на консультациях и информировать преподавателя о ходе выполнения курсового проекта предоставлять ему уже сделанную работу. При этом уточняется ее содержание и направленность последовательность и сроки выполнения этапов курсового проекта.
Законченный курсовой проект удовлетворяющий предъявляемым требованиям подписывается руководителем и только после этого допускается к защите. Защита проводится перед специальной назначенной решением кафедры комиссией состоящей из 2-3-х преподавателей при обязательном непосредственном участии руководителя проекта. Не менее чем за 5 дней до начала работы комиссии студенты должны быть информированы о составе сроках и месте работы комиссии.
Защита включает краткий доклад (5-7 минут) студента о выполненном проекте и ответы на вопросы примерный список которых приведен в приложении Г. После успешной защиты курсового проекта в зачетную книжку студента проставляется положительная оценки за подписью руководителя проекта.
Студент не представивший в установленный срок курсового проекта и не защитивший его по неуважительной причине считается имеющим академическую задолженность.
Защищенные проекты сдаются руководителем под расписку в архив кафедры где хранятся в установленном порядке.
Соломахо В.Л. Томилин Р.И. Юдовин Л.Г Приборостроение. Дипломное проектирование. Учебное пособие для высших учебных заведений. Изд.2 стереотипное Минск. "Дизайн ПРО" 2002
Справочник конструктора-приборостроителя. Детали приборов В.Л.Соломахо Р.И.Томилин Б.В.Цитович Л.Г. Юдовин.-Мн.: Выш. Шк. 1990.- 440с.
Анурьев В.И Справочник конструктора-машиностроителя.- В 3-х т.- Т.I.- 3. – 6-е изд. перераб. и доп. – М: Машиностроение 1982.- 736с. 576с. 557с.
Решетов Д.Н. Детали машин: Учебник для студентов машиностр. и механич. спец. вузов.- Изд. 4-е перераб. и доп. – М.: Машиностроение 1989.- 496с.
Томилин Р.И. Цитович Б.В. Передачи зубчатые цилиндрические. Учебно-методическое пособие. Часть 2. Разработка эскизного и технического проекта – Мн.: БГПА 1993.- 95с.
Зубчатые передачи: Справочник Е.Г. Гинзбург Н.Ф.Голованов Н.Б. Фирун Н.Т. Халебский; Под общ. ред. Н.Г. Гинзбурга. – 2-е изд. Перераб. и доп. – М.: Машиностроение 1980. – 416с.
Скойбеда А. Т. Детали машин и основы конструирования. 2-е изд. перераб Вышэйшая школа 2006-560с.
Дунаев П.Ф. Леликов О.П. Конструирование узлов и деталей машин: Учеб. Пособие для машиностроительных вузов.- Изд. 4-е перераб.- М.Ж Высшая школа 1985.-368с.
Орлов. П.И. Основы конструирования: Справочно – методическое пособие в 2- х кн. – Кн.1 2. – М.: Машиностроение 1988. – 560с. 544с.
Допуски и посадки. Справочник. В 2-х ч.В.Д.Мягков М.А.Палей А.Б.Романов В.А.Брагинский. – Л.: Машиностроение 1983. – Ч.1. – 543с.].
Кудрявцев В.Н. Детали машин: Учебник для студентов машиностроительных специальностей вузов. – Л.: Машиностроение Ленингр. отд-ние 1980. – 464с.
Перель Л.Я. Подшипники качения. Расчет проектирование и обслуживание опор: Справочник. – М.: Машиностроение 1983. – 543с.
Комиссар А.Г. Уплотнительные устройства опор качения: Справочник. М.:Машиностроение 1979.- 702с.
Лариков Е.А. Вилевская Т.И. Узлы и детали механизмов приборов: Основы теории и расчета. – М. : Машиностроение 1974 - 328с.
Батанов М.В. Петров Н.В. Пружины: - М.: Машиностроение 1968. – 216с.
Андреева Л.Е. Упругие элементы приборов . – 2-е изд. перераб. и доп. – М.: Машиностроение 1981. – 392с.
Технологичность конструкции изделия: Справочник Ю.Д. Амиров Т.К. Алферова П.Н. Волков и др.; Под. Общ. Ред. Ю.Д. Амирова – 2-е изд. перераб. И доп. – М.: Машиностроение 1990. – 268с. (Б –ка констр.) .
Справочник конструктора-приборостроителя. Проектирование: Основные нормы В.Л. Соломахо Р.И. Томилин Б.В. Цитович Л.Г. Юдовин. – Мн.: Высш. шк. 1988. – 272с.
Белорусский Национальный Технический Университет
риборостроительный факультет
Кафедра «Стандартизация метрология и информационные системы»
КУРСОВОЙ ПРОЕКТ (РАБОТА)
по дисциплине «Детали приборов»
Исполнитель: студент (факультет курс группа)
(фамилия имя отчество)
(ученое звание ученая степень должность)
ПОЯСНИТЕЛЬНАЯ ЗАПИСКА
к курсовому проекту
по дисциплине «Детали приборов»
Белорусский национальный технический университет
Приборостроительный факультет
на курсовое проектирование по дисциплине «Детали приборов»
Тема проекта - Привод стола контрольно-измерительного прибора
Сроки сдачи студентом законченного проекта – 24.12.20__ г.
Исходные данные к проекту
Кинематическая схема
Тяговое усилие стола F Н
Скорость перемещения стола V ммс
Габаритные размеры стола ахв мм
Рабочий ход стола L мм
Момент сопротивления вращению стола Т Нм
Частота вращения стола n обмин
Тип направляющих вращения
Срок службы привода час.
Содержание расчетно-пояснительной записки (перечень подлежащих разработке вопросов)
1Описание объекта проектирования
2Расчеты подтверждающие работоспособность конструкции
2.1Кинематический и силовой расчеты
2.2Расчеты отдельных узлов и деталей (зубчатой передачи винтовой
передачи подшипников качения валов направляющих пружин и др.)
2.3Перечень использованной литературы
3.1Техническое задание
3.2Проектировочные расчеты
3.3Перечень деталей (при отсутствии его на чертеже общего вида)
Перечень графического материала
1. Кинематическая схема(А4)
2. Чертеж общего вида изделия (1 2 листа А1)
3. Рабочие чертежи деталей (5 6 типовых деталей формат А3А4)
Календарный график работы над проектом на весь период проектирования (с указанием сроков выполнения и трудоемкости отдельных этапов)
1.Проектировочный кинематический и силовой расчеты 30.09.20__
2.Выполнение кинематической схемы 07.10.20__
3.Проектировочные расчеты передач.
Выполнение эскизов передач 20.10.20__
4.Проектировочные расчеты опор и направляющих.
Выполнение эскизов опор и направляющих 05.11.20__
5.Компоновка изделия и выполнение эскизного проекта 20.11.20__
6.Выполнение и оформление расчетов
и пояснительной записки 10.12.20__
7.Выполнение чертежа общего вида изделия
и рабочих чертежей деталей 20.12.20__
8.Защита проекта . . 24.12.20__
Задания на курсовой проект
В пособии разработаны задания на проектирование реверсивных приводных устройств столов контрольно-измерительных приборов.
Приводные устройства включают одно или двухступенчатые редукторы различных типов передачу винт-гайка направляющие для вращательного и прямолинейного движения с трением скольжения и трением качения муфты и двигатели.
Каждое из заданий на курсовое проектирование включает кинематическую схему а также исходные данные для приводного устройства (Приложение 5).
Исходные данные для столов с горизонтальным и вертикальным перемещениями:
Тяговая сила стола F Н
Скорость перемещения стола в установившемся режиме V ммс
Габаритные размеры стола a × b мм
Срок службы привода час
Исходные данные для вращающихся столов:
Момент сопротивления вращению Т Нм
– редуктор цилиндрический
– редуктор конический
Общие вопросы по материаловедению нормированию точности и деталям приборов:
Какие материалы используются в машиностроении и приборостроении?
Чем отличается сталь от чугуна?
Какие существуют виды сталей и чугунов?
Какие существуют виды пластмасс?
Что такое углеродистая и легированная сталь?
Каковы особенности применения разных материалов?
Как назначаются нормы точности при проектировании различных сборочных соединений и деталей?
Что обозначают те или иные нормы точности на чертежах?
Какие Вы знаете графические обозначения норм точности?
10 Какие покрытия применяются при проектировании различных сборочных
соединений и деталей?
11 Что Вы знаете о назначении различных видов покрытий?
12 Как обозначаются различных виды покрытий на чертежах?
13 Какие смазочные материалы применяются при проектировании различных
сборочных соединений и деталей?
14 Каковы особенности назначения различных видов смазок?
15 Как обозначаются различные виды смазок на чертежах?
16 Какие существуют разъемные и неразъемные соединения?
17 Какие существуют штифтовые соединения как назначаются нормы точности?
18 Как обозначаются штифтовые соединения на чертежах?
19 Какие существуют шпоночные соединения как назначаются нормы точности?
20 Как обозначаются шпоночные соединения на чертежах?
21 Что Вы знаете о клеевых паяных и сварочных соединениях?
22 Какие существуют виды сварочного соединения каковы особенности их
23 Как обозначаются сварочные соединения на чертежах?
Общие вопросы по конструированию:
1 Каковы этапы курсового проектирования и последовательность действий?
2 Для чего разрабатывается и что включает техническое задание?
3 Как производится выбор двигателя при проектировании?
4 Какие существуют виды двигателей их достоинства и недостатки в разных случаях применения?
Какие существуют обозначения и конструктивные особенности крепления двигателей?
6 Как производится выбор муфты при проектировании?
7 Какие существуют виды муфт их конструктивные особенности достоинства и недостатки?
8 Как назначаются нормы точности при выборе муфт?
9 Какие существуют типы подшипников их достоинства и недостатки в разных случаях применения?
10 Какие существуют обозначения и конструктивные особенности подшипников?
11 Как производится выбор подшипника при проектировании?
12 Как назначаются нормы точности при проектировании опор?
13 Какие существуют виды зубчатых передач их достоинства и недостатки в разных случаях применения?
14 Какие встречаются конструкции зубчатых колес?
15 Что такое модуль зуба?
16 Какие материалы применяются для изготовления зубчатых колес?
17 Как назначаются нормы точности при проектировании зубчатых колес?
18 Каковы достоинства и недостатки передачи винт-гайка?
19 Какие встречаются конструкции передачи винт-гайка?
20 Какие материалы применяются для изготовления деталей передачи винт-гайка?
21 Как назначаются нормы точности при проектировании передачи винт-гайка?
22 Какие встречаются конструкции направляющих?
23 Какие материалы применяются для изготовления деталей направляющих?
24 Как назначаются нормы точности при проектировании направляющих?
25 Каковы особенности конструкций корпусных деталей?
26 Какие материалы применяются для изготовления корпусных деталей?
27 Как назначаются нормы точности при проектировании корпусных деталей?
Вопросы непосредственно по представленному курсовому проекту:
1 Каков состав курсового проекта (документы входящие в состав курсового проекта)?
2 Каковы назначение и принцип действия проектируемого изделия?
3 Каковы стадии проектирования конструкторской документации в соответствии с ГОСТ 2.103—68? К какой стадии относится данный курсовой проект?
4 Как проводились расчеты при проектировании?
5 Какие виды передач использованы в механизме?
6 Как проводился выбор муфты?
7 Как проводилось определение числа оборотов тихоходного вала?
8 Как проводилось определение диаметров валов?
9 Как проводилось определение радиальной и осевой составляющих сил действующих на подшипник?
10 Как определяется крутящий момент на каждом валу?
11 Как проводились расчёты зубчатых колёс?
12 Как проводились расчёты шпонок?
13 Как проводился расчёт передачи винт—гайка?
14 Как проводился расчёт направляющих на прочность?
15 Как проводился расчёт подшипников?
16 Как проводился выбор варианта конструкции и выбор сборочных единиц?
17 Как производится сборка-разборка спроектированного изделия?
18 Как и чем производится смазка. Как удаляется отработанная смазка?
19 Какие детали и сборочные единицы смазываются?
20 Предусмотрены ли смазочные уплотнения в конструкции?
21 Что обозначают технические требования на чертеже общего вида?
22 Чем чертеж общего вида отличается от сборочного чертежа?
23 Предусмотрена ли регулировка зазоров в конструкции и за счет чего она происходит?
24 Из каких материалов изготовлены детали? Почему?
25 Что значат конкретные обозначения материалов?
26 Какова твердость деталей? Почему?
27 Как обозначается твердость на рабочих чертежах?
28 Какие покрытия применены для конкретных деталей? Почему?
29 Как обозначаются различные виды покрытий на чертежах?
30 Как и почему назначены нормы точности для спроектированных деталей?
Примеры выполнения чертежей общего вида схем
и рабочих чертежей деталей
Правила выполнения рабочих чертежей цилиндрических зубчатых колес
Исходным документом для разработки рабочих чертежей зубчатых колес служит чертеж общего вида механизма.
Изображения деталей зубчатых передач регламентированы ГОСТ 2.402-68 «ЕСКД. Условные изображения зубчатых колес реек червяков и звездочек цепных передач».
Общие правила разработки рабочих чертежей детали определяет ГОСТ 2.403-75 «ЕСКД. Правила выполнения чертежей зубчатых колес». В соответствии с требованиями стандартов чертеж зубчатого колеса должен содержать сведения необходимые для его изготовления и контроля: изображение детали с необходимыми размерами допусками формы расположения и параметрами шероховатости поверхностей; таблицу параметров зубчатого колеса; технические требования указание материала детали.
На чертеже зубчатого колеса в правом верхнем углу помещают таблицу параметров зубчатого венца которая состоит из трех частей разделяемых основными линиями (рис. 16.3).
В первой части таблицы помещают основные данные для изготовления которые включают:
нормальный исходный контур (для нестандартного указывают необходимые для воспроизведения параметры стандартный задают ссылкой на стандарт);
нормальный исходный контур
степени точности по ГОСТ 1643-81 и другие данные.
Во второй части таблицы помещают данные для контроля взаимного положения разноименных профилей зубьев по одному из следующих вариантов:
постоянная хорда SC и высота до постоянной хорды hC (при этом указывают номинальное значение постоянной хорды до третьего знака после запятой а высоту до постоянной хорды приводят в виде номинального значения и двух отрицательных отклонений);
толщина по хорде и высота до постоянной хорды (в этом случае указывают номинальное значение высоты до хорды и контролируемое значение толщины с двумя отрицательными отклонениями);
торцовый размер по роликам М и диаметр ролика D (диаметр ролика указывают как номинальное значение размер по роликам – с двумя отрицательными отклонениями);
длина общей нормали W (номинальное значение с двумя отрицательными отклонениями).
В третьей части таблицы помещают справочные данные включающие делительный диаметр колеса число зубьев сектора или при необходимости прочие данные.
Рисунок 12.1 Таблица параметров зубчатого колеса
Рисунок 12.2 Простановка размеров и допусков на рабочем чертеже зубчатого колеса
На изображении зубчатого колеса указываются следующие параметры (рис.16.4):
При m ≥ 1 – ГОСТ 13755-81 при m 1 – ГОСТ 9587-81.
Возможна запись по одному из следующих вариантов:
постоянная хорда SC и высота до постоянной хорды
длина общей нормали W;
толщина по хорде и высота до постоянной хорды ;
торцовый размер по роликам М и диаметр ролика D.
Делительный диаметр вычисляется d = m z.
Диаметр вершин вычисляется da = d + 2 m. Если в п.2 задаются SC и hC или и то da изготавливают по h6 если в п. 2 задаются W или М и D то da – по h9 h12.
Допуск радиального биения зубчатого колеса определяется по формуле Трад.б. = 06 ×Fr где Fr (допуск радиального биения зубчатого венца) выбирается по табл. 6 ГОСТ 1643-81 и округляется до стандартного значения по ГОСТ 24643-81.
Допуск биения торцевых поверхностей зубчатого колеса определяется по формуле Тторц.б. = 05 (da×В) F где В – ширина зубчатого венца F (допуск на погрешность направления зуба) выбирается по табл 11 ГОСТ 1643-81 и округляется до стандартного значения по ГОСТ 24643-81.
Допуски круглости и профиля продольного сечения определяются исходя из уровней относительной геометрической точности А или В и вычисляются соответственно по формулам Ткр. (Тпрод.сеч.) = 03 ITD или Ткр. (Тпрод.сеч.) = 02 IT. Полученное значение округляется до стандартного значения по ГОСТ 24643-81.
Размер посадочного отверстия указывается комбинированным способом (буквенное обозначение поля допуска и числовые значения предельных отклонений).
Параметр шероховатости посадочной поверхности отверстия задается по уровням относительной геометрической точности А или В и вычисляются соответственно по формулам Ra ≤ 005 ITD или Ra ≤ 0025 ITD. Полученное значение округляется до стандартного значения по ГОСТ 2789-73.
Параметр шероховатости по делительному диаметру зубчатого колеса определяется по формуле Ra ≤ 01 ff где ff (допуск на погрешность профиля зуба) выбирается по табл. 8 ГОСТ 1643-81 и округляется до стандартного значения по ГОСТ 2789-73.
Параметр шероховатости торцевых поверхностей зубчатого колеса (ступицы) определяется по формуле Ra ≤ 01 Тторц.б. и округляется до стандартного значения по ГОСТ 2789-73.
Допуски параллельности и симметричности шпоночного паза определяются по формулам Тпар. = 06 Тшп. Тсим. = 40 Тшп. и округляются до стандартных значений по ГОСТ 24643-81.
Параметр шероховатости сторон шпоночного паза зависит от размеров посадочного отверстия и его полей допусков: при D ≤ 50 мм - Rа ≤ 32 ; при D > 50 мм - Rа ≤ 63.
Размер ширины шпоночного паза зубчатого колеса указывается комбинированным способом (буквенное обозначение поля допуска и числовые значения предельных отклонений).
Размер d + t2 с указанием предельных отклонений.
Указываются технические требования: по твердости материала общие допуски размеров (формы поверхностей) и другие данные.
Параметры шероховатости неуказанных поверхностей зубчатого колеса.
Правила выполнения рабочих чертежей валов с посадочными поверхностями под подшипники качения
На рабочем чертежах вала и корпуса обозначают допуски размеров допуски формы и расположения посадочных и опорных торцовых поверхностей заплечиков валов и отверстий корпусов а также шероховатость данных поверхностей (рисунок 12.3).
Рисунок12.3 Обозначение допусков на рабочем чертеже вала
ГОСТ 3325-85 устанавливает числовые значения допусков формы расположения и шероховатости поверхности в зависимости от номинального размера посадочной поверхности и класса точности подшипника:
шероховатость поверхности – таблица 3 ГОСТ;
допуски круглости и профиля продольного сечения – таблица 4 ГОСТ;
допуск торцового биения заплечиков валов – таблица 5 ГОСТ.
Допуски соосности посадочных поверхностей вала и корпуса указываются в Приложении 7 для различных типов подшипников при длине посадочного места
В = 10 мм. При другой длине посадочной поверхности ВП необходимо табличное значение умножить на ВП 10. Полученное значение округляется до стандартного значения по ГОСТ 24643-81.
Стандартом допускается на чертежах вместо допуска соосности указывать допуск радиального биения. Величина радиального биения определяется как сумма допуска соосности и допуска круглости. Числовое значение радиального биения округляется до стандартного значения по ГОСТ 24643-81.
Расчеты зубчатой передачи
Запас прочности по контактным напряжениям – KН.
Тоже на изгиб при максимальной нагрузке – KFST.
Обозначение и значение
2. Коэффициент Пуассона
3. Твердость материалов [6.1 c. 18 49]
5. Начальные диаметры
6. Межосевое расстояние
7. Диаметр окружностей вершин шестерни
8 Диаметр окружностей вершин колеса
9. Коэффициент перекрытия
10. Передаточное отношение
11. Точность передачи
12. Шероховатость рабочих поверхностей зубцов
13. Окружная скорость
15. Коэффициент динамичности внешней нагрузки
16. Максимальное окружное усилие
17. Нормируемый ресурс
19. Метод изготовления
Расчёт на контактную выносливость
Коэффициент свойств материала
E – модуль упругости;
–коэффициент Пуассона
Для прямозубых колес = 0
Для прямозубых передач при α=20° k=124
Для прямозубых колес
Допуски направления зуба и взаимного перекоса осей передачи
Перекос зубца при деформации вала
Для консольного колеса
Для колеса между опорами
Для прямозубых колес α=1
Коэффициент неравномерности нагрузки по зубцу
Для однородной структуры
Отказ без особых последствий
Для периодического смазывания
Расчёт зуба на изгиб
Коэффициент формы зубца
X2-коэффициенты смещения.
Для шлифованной поверхности
Коэффициент вида заготовки
Определение размера по роликам
Для четного числа зубцов
Выводы по результатам расчета
Передача работоспособна и контролепригодна.
Запас прочности по контактным напряжениям колеса – KH = 19.
То же на изгиб при максимальной нагрузке – KFST = 23.
Размер по роликам ;
Расчёт работоспособности вала
Расчёт на статическую прочность
Проводится в целях предупреждения пластических деформаций.
Определим окружные радиальные и осевые силы действующие на ведущий вал от зубчатой передачи (рисунок 13.1).
Цилиндрическая передача:
где Т1 – крутящий момент на валу(11 Нм);
d1 – диаметр колеса (36мм);
α – угол зацепления в нормальном сечении (20 град).
Горизонтальная плоскость:
Рисунок 13.1 Силы действующие на ведущий вал
Вертикальная плоскость:
Для построения эпюр произведем следующие расчеты (рисунок 13.2) :
Наибольшее значение суммарно изгибающего момента:
Эквивалентный момент:
Строим эпюры изгибающих и крутящих моментов:
Рисунок 13.2 Эпюры изгибающих и крутящих моментов
Определим допустимый диаметр вала:
где []=50 60 МПа – допустимое напряжение при изгибе.
Из конструктивных соображений был принят вал диаметр которого 12 мм.
>76 мм значит статическая прочность вала обеспечена.
Расчёт на усталостную прочность
S S – коэффициенты запаса соответственно по нормальным и касательным напряжениям;
где -1=200 МПа -1=320 МПа – пределы выносливости материала вала при изгибе и кручении с симметричным знакопеременным циклом нагружения;
а а и m=0 m=0 – амплитудные и средние напряжения циклов нормальных и касательных напряжений:
а=МИ01 d3=77901 123=45 МПа;
а=T02 d3=110002 123=32 МПа.
=01 =005 – коэффициенты учитывающие влияние постоянной составляющей цикла на усталость вала;
k=2 k=19 – эффективные коэффициенты компенсации напряжений при изгибе;
=087 – масштабные факторы;
Условие прочности выполняется.
Расчёт валов на жёсткость
Различают изгибную и крутильную жесткость.
Изгибная жёсткость обеспечивается при выполнении условий:
где [f]=002 мм допустимый прогиб вала.
Прогиб в месте воздействия силы:
[f]=002 > f =0004 следовательно жёсткость вала обеспечена.
4 Проверка работоспособности передачи винт-гайка
Допустимое давление в резьбе для пар трения закалённая сталь по бронзе:
Основным критерием работоспособности передачи является износостойкость которая оценивается по среднему давлению между витками резьбы винта и гайки:
где Fa – осевая нагрузка на передачу Н;
d2 – средний диаметр резьбы мм;
мм – рабочая высота профиля для трапецеидальной резьбы;
– число витков резьбы в гайке (НГ – высота гайки Р-ход резьбы).
Проверка работоспособности передачи винт-гайка
ВО 2 испр.dwg
Винт М6х16.48.016 ГОСТ 1491-70
Болт М5х14.48.016 ГОСТ 1491-70
Винт М4х16.48.016 ГОСТ 1491-70
Болт М6х18.48.016 ГОСТ 1491-70
Двигатель Т50В2 ГОСТ 19523-74
Подшипник 36206 ГОСТ 8338-75
Приспособление для контроля радиального биения Чертеж общего вида
Крышка испр.dwg

(Modell- oder Gesenk-Nr)
Сталь 40ХГОСТ4543-71
Общие допуски по ГОСТ 30893.1-m
Остальные технические требования
Пружина испр.dwg

Винт М6х16.48.016 ГОСТ 1491-70
Болт М5х14.48.016 ГОСТ 1491-70
Винт М4х16.48.016 ГОСТ 1491-70
Болт М6х18.48.016 ГОСТ 1491-70
Двигатель Т50В2 ГОСТ 19523-74
Подшипник 36206 ГОСТ 8338-75
Привод стола контрольно - измерительного прибора
Пружина 95 ГОСТ 13768-86 2. Направление навивки - правое 3. l*=3580 4. n=18 5. n4=20±1 6. 46 48 HRCэ
В - место контроля твёрдости 7. Покрытие Ан. окс. прм. 8. Материал-заменитель - Проволока 60С2 Б-ХН 6 ГОСТ 14963-78 9. Dc=49.55 h10 10. Dr=65.23H10 11. Остальные требования по гр. 2 ГОСТ 16118-70 12. * Размеры и параметры для справок
Проволока 51ХФА - Б-ХН 6 ГОСТ 14963-78
ЧОВ-1 испр.dwg

Винт М6х16.48.016 ГОСТ 1491-70
Болт М5х14.48.016 ГОСТ 1491-70
Винт М4х16.48.016 ГОСТ 1491-70
Болт М6х18.48.016 ГОСТ 1491-70
Двигатель Т50В2 ГОСТ 19523-74
Подшипник 36206 ГОСТ 8338-75
Привод стола контрольно - измерительного прибора
ЗК испр.dwg

(Modell- oder Gesenk-Nr)
Сталь 40ХГОСТ4543-71
Сталь 40 ГОСТ1050-88
Остальные технические
требования по СТБ 1014-95
ВО испр.dwg

Винт М6х16.48.016 ГОСТ 1491-70
Болт М5х14.48.016 ГОСТ 1491-70
Винт М4х16.48.016 ГОСТ 1491-70
Болт М6х18.48.016 ГОСТ 1491-70
Двигатель Т50В2 ГОСТ 19523-74
Подшипник 36206 ГОСТ 8338-75
Приспособление для контроля радиального биения Чертеж общего вида
Кинематическая схема испр.dwg

Двигатель 4АА63В4УЗ ГОСТ 19523-94 Р=370 Вт; n=1500 обмин; I=0
-14-1-УЗ ГОСТ 14084-93 3. Конические колеса. Нормальный исходный контур ГОСТ 13754-81 4. Зубчатые колеса. Нормальный исходный контур ГОСТ 13755-81 5. Направляющие качения РТМ-2 РОЗ-5-77
ЧОВ-2 испр.dwg

Винт М6х16.48.016 ГОСТ 1491-70
Болт М5х14.48.016 ГОСТ 1491-70
Винт М4х16.48.016 ГОСТ 1491-70
Болт М6х18.48.016 ГОСТ 1491-70
Двигатель Т50В2 ГОСТ 19523-74
Подшипник 36206 ГОСТ 8338-75
*Размеры для справок. 2. Смазка раб. пов. дет. поз. 7
ЦИАТИМ 201 ГОСТ 6267-74 3. Поверхности деталей поз. 2
покрыть - эмаль МЛ-152 синяя МРТУ 6-10-642-70.II.ж. Раб. пов. от покрытия предохранить. 4. Сопряжение шпонки поз. 6 по ГОСТ 23360-78 . Вид соединения - свободный 5. Детали поз. 20
Хим. Окс. 6. Сварной шов T3 5 по ГОСТ 14771-76. 7. Сварной шов T1 5 по ГОСТ 14771-76.
Привод стола контрольно - измерительного прибора
Вал-шестерня испр.dwg

Винт М6х16.48.016 ГОСТ 1491-70
Болт М5х14.48.016 ГОСТ 1491-70
Винт М4х16.48.016 ГОСТ 1491-70
Болт М6х18.48.016 ГОСТ 1491-70
Двигатель Т50В2 ГОСТ 19523-74
Подшипник 36206 ГОСТ 8338-75
Общие допуски по ГОСТ 30893.1-m
* Размеры для справок
Остальные технические требования
кин.схема испр(без момента ин).dwg

Двигатель 4АА63В4УЗ ГОСТ 19523-94 Р=370 Вт; n=1500 обмин; I=0
-14-1-УЗ ГОСТ 14084-93 3. Конические колеса. Нормальный исходный контур ГОСТ 13754-81 4. Зубчатые колеса. Нормальный исходный контур ГОСТ 13755-81 5. Направляющие качения РТМ-2 РОЗ-5-77
Компоновочный чертеж испр.dwg

Винт М6х16.48.016 ГОСТ 1491-70
Болт М5х14.48.016 ГОСТ 1491-70
Винт М4х16.48.016 ГОСТ 1491-70
Болт М6х18.48.016 ГОСТ 1491-70
Двигатель Т50В2 ГОСТ 19523-74
Подшипник 36206 ГОСТ 8338-75
*Размеры для справок. 2. Смазка раб. пов. дет. поз. 7
ЦИАТИМ 201 ГОСТ 6267-74 3. Поверхности деталей поз. 2
покрыть - эмаль МЛ-152 синяя МРТУ 6-10-642-70.II.ж. Раб. пов. от покрытия предохранить. 4. Сопряжение шпонки поз. 6 по ГОСТ 23360-78 . Вид соединения - свободный 5. Детали поз. 20
Хим. Окс. 6. Сварной шов T3 5 по ГОСТ 14771-76. 7. Сварной шов T1 5 по ГОСТ 14771-76.
Привод стола измерительного прибора Чертеж общего вида
Пример компоновки стола горизонтального