Автоматизированный участок прессового цеха по производству детали корпус инструментального ящика автомобиля ЗИЛ




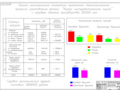
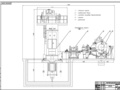
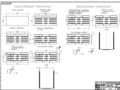
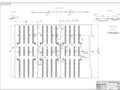
- Добавлен: 24.01.2023
- Размер: 6 MB
- Закачек: 1
Описание
Состав проекта
![]() |
![]() |
![]() |
![]() ![]() ![]() |
![]() ![]() ![]() ![]() |
![]() ![]() ![]() |
![]() ![]() ![]() ![]() |
![]() |
![]() |
![]() ![]() ![]() |
![]() ![]() ![]() ![]() |
![]() |
![]() |
![]() |
![]() |
![]() |
![]() |
![]() ![]() ![]() ![]() |
![]() |
![]() |
![]() ![]() ![]() |
![]() ![]() ![]() ![]() |
![]() ![]() ![]() |
![]() ![]() ![]() |
![]() ![]() ![]() |
![]() |
![]() |
![]() ![]() ![]() ![]() |
![]() |
![]() |
![]() |
![]() |
![]() ![]() ![]() ![]() |
![]() |
Дополнительная информация
Штамп.docx
Автоматизированный участок прессового цеха по производству детали «корпус инструментального ящика» для автомобиля ЗИЛ
последовательной штамповки
Сталь У10А; 59 63 HRC
Сталь У10А; 57 60 HRC
Сталь Х12М; 59 63 HRC
Сталь 5ХНМ; 51 55 HRC
Сталь 5ХНМ; 46 51 HRC
Сталь 5ХНМ; 52 56 HRC
Сталь У8А; 57 59 HRC
02 технологические переходы.dwg

Автоматизированный участок прессового цеха по производству детали "корпус инструментального ящика" автомобиля ЗИЛ
Кафедра КиОД Группа 10-МАК-2
1. Пояснительная зписка.docx
1 Описание существующего производства и задачи по его совершенствованию7
2 Предлагаемый технологический процесс . 9
3 Определение коэффициента использования материала .. . 13
4 Выбор оборудования . 17
Конструкторская часть 21
1 Выбор типа и технологической схемы штампа .. 21
2 Предлагаемая конструкция штампа . 22
3 Выбор материала и термообработки деталей штампа 26
4 Расчет исполнительных размеров разделительных пуансонов и матриц 28
5 Расчет основных деталей штампа на прочность и жесткость 29
6 Расчет стойкости штампа .. 31
7 Автоматизация участка . 32
7.1 Расчет разматывающего устройства . 32
7.2 Расчет правильного устройства . 34
7.3 Расчет валковой подачи . 35
8 Проектирование участка 37
9 Организация производства на участке 39
Организационно-экономическая часть 43
1 Описание экономической части производства 43
2 Организация ремонта транспорта и инструментального хозяйства цеха 44
3 Расчёт количества оборудования и коэффициента его загрузки . 46
4 Организация оплаты труда . 49
5 Расчет технико – экономических показателей участка цеха по базовой технологии 54
6 Расчет сметы косвенных (накладных) расходов 57
6.1 Статьи группы А связанные с работой оборудования 57
6.2 Статьи группы Б – общецеховые (участковые) расходы 61
6.3 Калькуляция себестоимости единицы продукции . .. 64
7 Расчет экономики по предлагаемому варианту 68
8 Расчет технико – экономических показателей участка цеха по базовой технологии 72
9 Расчет сметы косвенных (накладных) расходов .. .. 75
10 Расчет экономического эффекта .. .. 82
Безопасность труда . 84
1 Анализ вредных и опасных факторов листоштамповочных цехов .. 84
2 Расчет уровня шума на участке 87
3 Нормативы уровня шума .. 88
4 Мероприятия по снижению шума 90
1 Очистка промышленных выбросов в атмосферу от пыли туманов газов 95
Список использованных источников 106
Автомобильное производство характеризуется чрезвычайно широкой номенклатурой изделий получаемых листовой штамповкой. В этой номенклатуре подавляющее большинство составляют детали которые технологическими подразделениями ЗИЛа относятся к среднегабаритным.
Годовая программа выпуска современных автомобилей в нормальных условиях производства составляет как правило 100 000 и более машин в год. Соответственно годовая номенклатура каждого типоразмера изделия как минимум не менее этой цифры а в случае парных деталей существенно увеличивается. Соответственно данное производство можно отнести к крупносерийному.
Листовая штамповка является широко распространенной (практически монопольной) и весьма прогрессивной разновидностью технологии обработки листового материала (листа полосы ленты штучной заготовки). Листовая штамповка позволяет изготавливать самые разнообразные плоские и пространственные изделия в связи с чем находит применение во всех отраслях производства связанных с изготовлением металлических деталей.
Листовая штамповка имеет ряд преимуществ перед другими видами обработки металлов как в технологическом так и в экономическом отношении. В технологическом отношении листовая штамповка позволяет:
- получать детали весьма сложных форм изготовление которых другими методами обработки либо невозможно либо затруднительно;
- создавать прочные и жесткие но легкие по массе конструкции деталей при небольшом расходе материала;
- получать взаимозаменяемые детали с достаточно высокой точностью размеров преимущественно без последующей механической обработки. В экономическом отношении холодная штамповка обладает следующими преимуществами:
- экономным использованием материала и сравнительно небольшими отходами;
- высокой производительностью оборудования (несложная механизация и автоматизация производственных процессов);
- низкой стоимостью изготовляемых изделий и возможностью массового производства.
Наибольший эффект от применения листовой штамповки как правило достигается при комплексном решении технических вопросов на всех стадиях подготовки производства начиная с создания технологичных конструкций деталей допускающих их экономичное изготовление. Соответственно разработка технологических процессов холодной штамповки и проектирование штампов неразрывно связаны между собой хотя и могут выполняться разными лицами.
В настоящее время в массовом и крупносерийном производстве наблюдается тенденция преимущественного применения автоматизированных процессов штамповки либо в последовательных штампах либо на многопозиционных листовых автоматах. Преимущества таких процессов очевидны: человек управляет процессом с пульта управления и не попадает в рабочую зону повышается качество изделий (брак обнаруживающийся после конечной операции устраняется сразу количество бракованных изделий не превышает количества переходов) повышение производительности (80-100 деталей в минуту) [1].
Исходя из вышесказанного я хочу автоматизировать технологический процесс получения детали «Корпус инструментального ящика» применив автоматизированную линию штамповки и штамп последовательного действия использующий заготовку – ленту. Так же требуется рассчитать экономический эффект предлагаемой технологии повысить безопасность рабочих на производстве и уделить равное всему внимание экологии листоштамповочного производства.
Технологическая часть
1 Описание существующего производства и задачи по его совершенствованию
При существующем технологическом процессе рисунок 1.1 изготовление детали «корпус инструментального ящика» осуществляется штамповкой за семь технологических переходов:
Рисунок 1.1- Существующий технологический процесс
-На заготовительном участке из листа 1 × 1250 × 2500 мм нарезаются карточки размером 1 × 1250 × 600 мм.
-Затем транспортировщик доставляет их участок штамповки.
-Осуществляется формовка рёбер жёсткости на прессе под управлением и наблюдением оператора наладчика.
-Полученные заготовки доставляются транспортировщиком к следующему прессу.
-Осуществляется пробивка отверстий на прессе под управлением и наблюдением оператора наладчика.
-Следующий этап получение детали «корпус инструментального ящика» заключается в транспортировке к очередному прессу
-Осуществляется операция отрезка полуфабриката по шагу.
-Далее заготовки транспортируют на следующую операцию.
-Осуществляется гибка полок предварительная завивка двух петлей диаметром 4мм.
-Транспортировщик доставляет заготовки к следующему прессу.
-На прессе осуществляется окончательная завивка.
-Далее заготовка транспортируется на участок «Молдинги»
-Окончательная гибка боковых стенок ящика.
Закладка заготовок в штамп и удаление деталей из штампа осуществляется вручную. Это значительно увеличивает время на производство изделия и может привести к получению травмы рабочего обслуживающего данный технологический процесс.
Существующий технологический процесс имеет ряд недостатков:
-отсутствие автоматизации;
-использование малоэффективного ручного труда;
-низкая производительность;
-большая трудоемкость изготовления детали;
-затраты времени на наладку техпроцесса;
-затраты времени на транспортировку заготовок от пресса к прессу.
Подходя к вопросу о возможном совершенствовании технологического процесса следует отметить возможные варианты а именно:
-уменьшение количества и трудоемкости операций;
-выбор более технологичного материала;
-усовершенствование заготовки;
-изменение конструкции детали с целью повышения технологичности;
-использование более нового и производительного оборудования;
-применение средств автоматизации и механизации процесса;
-снижение различных видов расходов.
Самым приемлемым можно считать выбор более производительного оборудования и изменение техпроцесса а именно изготовление деталей на одном прессе – автомате путем совмещения всех операций в штампе последовательного действия применение средств автоматизации и механизации.
2 Предлагаемый технологический процесс
Деталь «корпус инструментального ящика» рисунок 1.2 имеет довольно сложную форму. Она относится к классу средних деталей. Наиболее оптимальным вариантом изготовления данной детали является последовательная штамповка которую целесообразно осуществлять на прессе – автомате. Известно что при штамповке на прессе – автомате применяют сложные штампы последовательного действия. [14]
Деталь изготавливается в три технологических перехода: 1 – обрезка по шагу пробивка формовка; 2 – надрезка ленты пробивка; 3 – отрезка (вырезка перемычки). Предлагаемый типовой технологический процесс представлен на рисунке 1.3.
Рисунок 1.2 – Корпус инструментального ящика
Рисунок 1.3 – Предлагаемый технологический процесс
Деталь «Корпус инструментального ящика» не является силовой к внешнему виду специальных требований не предъявляется она должна быть достаточно прочной.
Для штамповки применяется большое количество металлов а также неметаллических материалов. Материал применяемый для изготовления холодноштампованных деталей должен соответствовать не только назначению и условиям работы детали (обеспечивать эксплуатационные свойства изделия) он должен удовлетворять также технологическим требованиям и обеспечивать экономический эффект. Поэтому наибольшее применение в машиностроении имеет тонколистовая качественная низкоуглеродистая сталь. Это наиболее дешевый материал обладающий хорошими механическими и технологическими свойствами.
Основные механические свойства[5]:
Временное сопротивление разрыву
Относительное удлинение
Относительное сужение
Таблица 1.1 – Химический состав
Массовая доля элементов %
Массовая доля серы в стали должна быть не более 0040 % фосфора - не более 0035 %.
Остаточная массовая доля никеля в стали не должна превышать 030 % меди - 030 %.
В стали допускается массовая доля мышьяка не более 008%.
В прокате заготовках поковках и изделиях дальнейшего передела допускаются отклонения по химическому составу от норм приведенных в табл. 1.1 в соответствии с табл. 1.2. [11]
Таблица 1.2 – Отклонение по химическому составу
Наименование элемента
Допускаемые отклонения %
При изготовлении детали «Корпус инструментального ящика» применяется сталь 08кп – это низкоуглеродистая качественная конструкционная сталь общего назначения.
ГОСТ 9045 – 93 - на сталь;
ГОСТ 503 – 81 - на прокат.
Применяемый в листоштамповочном производстве материал по виду заготовки подразделяется на:
- штучные заготовки.
В крупносерийном производстве наиболее целесообразно применять непрерывный материал так как для каждого размера заготовки можно заказать ленту соответствующей ширины сокращая таким образом до минимума отходы. Кроме того лента дает возможность широко применять средства автоматизации которые значительно увеличивают производительность уменьшают затраты на рабочую силу и способствуют безопасности в работе. Для производства детали «Корпус инструментального ящика» выбираем холоднокатаную сталь в рулоне по ГОСТ 503 – 81.
Штамповка будет осуществляться без перемычек поскольку это даёт существенную экономию материала большую точность изготавливаемой детали.
При развертке на плоскость данная деталь дает заготовку с размерами 520 × 1206 мм следовательно выбираем ленту шириной 1250 мм (ближайшую по сортаменту). Шаг подачи равен 520 мм.
3 Определение коэффициента использования материала
Раскрой должен обеспечивать экономию металла высокое качество детали высокую производительность простоту штампа а также простоту и безопасность работы.
Существуют прямой наклонный встречный комбинированный многорядный и другие типы раскроя с отходами.
При наклонном типе раскроя будет очень большой отход. При встречном комбинированном многорядном усложняется конструкция штампа. Для данного типа детали удобнее применить цепочечный тип раскроя. Схема раскроя исходного материала представлена на листе А1 № 2.
Коэффициент использования материала для существующего технологического процесса определяется по формуле [2]:
КИМ = (МдНр.р) ×100% (1.1)
где Мд – масса детали кг.;
Нр.р. – норма расхода для рулона кг.
КИМ=(48005164) ×100%=93 %
КИМ = 93% для предлагаемого технологического процесса изготовления детали ''корпус инструментального ящика''.
Определение усилий и работ по переходам:
Требуется отформовать 8 рёбер жёсткости пробить 7 отверстий
×115мм 4 отверстия 8×16 мм и 2 технологических отверстия диаметром 15 мм отрезать полуфабрикат по шагу.
Усилие деформирования при формовке определяется по формуле [2]:
где L – длинна формуемого элемента мм.;
S – толщина материала мм.;
k – коэффициент зависящий от ширины рифта.
- предел прочности МПа
РФ. = 540×8×1×300×07 = 907200 (Н)
Работа пластической деформации при формовке определяется по формуле:
Ач. = λ Рч. h1000 (1.3)
где λ – коэффициент полноты диаграммы;
Рч. – усилие формовки Н;
h – ход формовки мм.
АФ. = 065×907200×31000 = 176904 (Дж)
Усилие деформирования при пробивке определяется по формуле:
Pпр. = К L S ср (1.4)
где К = 12 – коэффициент учитывающий неоднородность материала и притупление режущих кромок;
L – длина пробиваемого контура мм.;
S – толщина металла мм.;
ср – сопротивление срезу МПа.
Пробивка семи отверстий 8×115 мм.
Pпр.1 = 12×83×7×1×250 = 174300 (H)
Пробивка 4х отверстия 8×16 мм.
Pпр.2 = 12×48×4×1×250 = 57600 (H)
Пробивка 2х технологических отверстий диаметром 15 мм.
Pпр.3 = 12×47×2×1×250 = 28200 (H)
Полное усилие при пробивке определяется по формуле
Pпр.полное= Pпр.1+Pпр.2 +Pпр.3 (1.5)
Pпр.полное= 174300+57600+28200=260100 (Н)
Работа пластической деформации при пробивке определяется по формуле:
Апр. = λ Рпр. S1000 (1.6)
Рпр. – полное усилие пробивки Н
Апр. = 065×2601001000 = 169 (Дж)
Усилие деформирования при отрезке по шагу определяется по формуле:
Pотр. = К L S ср (1.7)
L – длина отрезаемого контура мм.;
Pотр. = 12×1206×1×250 = 361800 (H)
Работа пластической деформации при отрезке определяется по формуле:
Аотр. = λ · Ротр. · S1000 (1.8)
Ротр. – усилие отрезки Н.
Аотр. = 065×361800×11000 = 23517 (Дж)
Расчет усилия проталкивания производится по формуле:
Рпрот. = kпр. · Р · n (1.9)
где Р – суммарное усилие пробивки и обрезки Н;
kпр. – коэффициент равный 005 – 010 при вырубке на провал;
n – количество деталей находящихся в шейке матрицы.
Рпрот. = 005× (260100+361800) ×1 = 31095 (Н)
Работа пластической деформации при проталкивании определяется по формуле:
Апр. = λ Рпр. S1000 (1.10)
Рпр. – усилие проталкивания Н.
Апрот. = 065×31095×11000 = 202 (Дж)
Суммарное усилие штамповки определяется по формуле:
Рсум. = РФ. + Рпр.полное + Ротр.+ Рпрот. (1.11)
Рсум. = 907200+360100+361800+31095 = 1660195 (Н) = 166 (т.с.) [10]
Суммарная работа деформации определяется по формуле:
А =АФ.+Апр. +Аотр.+Апрот. (1. 12)
А = 176904+169+23517+202=219341 (Дж)
Согласно расчету суммарное усилие для выполнения технологических операций составляет 160 т. с. по этой величине выбирается листоштамповочное оборудование.
При выборе номинального усилия и габаритов штампового пространства пресса исходили из следующих соображений:
-Тип пресса и величина хода ползуна должны соответствовать технологической операции.
-Номинальное усилие пресса должно быть больше усилия требуемого для штамповки.
-Мощность пресса должна быть достаточной для выполнения работы необходимой для данной операции.
-Закрытая высота пресса должна соответствовать или быть больше закрытой высоты штампов.
-Габаритные размеры стола и ползуна пресса должны давать возможность установки и закрепления штампов.
-Число ходов пресса должно обеспечивать достаточную производительность штамповки.
-В зависимости от рода работы должно быть предусмотрено наличие специальных устройств и приспособлений (выталкивателей и подушек).
-Удобство и безопасность в обслуживании пресса должны соответствовать требованиям техники безопасности. [6]
Таблица 1.3 - Техническая характеристика пресса
Наименование параметра
Номинальное усилие т. с.
Регулировка закрытой высоты мм
Частота ходов ползуна мин-1
Закрытая высота пресса
Высота выдвижного стола
Регулируемость ползуна
Толщина подштамповой плиты мм
Мощность электродвигателя главного привода кВт
В данном случае максимальное усилие технологической операции составляет 160 т.с. Так как прессы изготовляют в определенном интервале по номинальному усилию то обычно при выборе пресса расчетное усилие не соответствует точно номинальному усилию. Поэтому пресс выбирается заведомо большего усилия чем требуется по расчету. Применение более сильного пресса обеспечивает более высокую жесткость и меньшую деформацию станины что позволяет получать более точные детали по высоте. С учетом того что при разделительных операциях усилие штамповки как правило не должно превышать 0.7 от номинального усилия пресса (кроме специальных прессов для разделительных операций) а также с учетом того что во всей номенклатуре деталей возможен разброс усилий выбираем усилие пресса равным 315 тс.
В качестве основного оборудования для производства вышеуказанной детали предлагается автоматизированная линия на базе листоштамповочного пресса усилием 315 тс общий вид линии представлен на рис. 1.5
Рисунок 1.5 – Общий вид листоштамповочной автоматизированной линии
Конструкторская часть
1 Выбор типа и технологической схемы штампа
Штампы для листовой штамповки классифицируются по трем признакам: технологическому (по роду и совмещенности операций) конструктивному (по способу направления) и эксплуатационному (по способу подачи заготовок и удалению деталей).
По технологическому признаку штампы разделяются на типовые группы по роду выполнения операций.
По совмещенности операций штампы разделяются на простые и комбинированные выполняющие одновременно несколько операций. Комбинированные штампы в свою очередь подразделяются по характеру совмещения операций во времени на:
-штампы последовательного действия в которых изготовление детали производится за несколько переходов под различными пуансонами при последовательном перемещении заготовки;
-штампы совмещенного действия в которых изготовление деталей производится за один ход пресса концентрированно расположенными пуансонами при неизменном положении заготовки;
-штампы последовательно – совмещенного действия в которых изготовление детали происходит путем сочетания последовательной и совмещенной штамповок.
По конструктивному признаку штампы разделяются на штампы без направления и штампы с направляющими устройствами. Штампы без направляющих более просты в изготовлении имеют малую массу и габаритные размеры но неудобны при установке небезопасны в эксплуатации и обладают невысокой стойкостью. Применяются только в мелкосерийном и опытном хозяйстве. Штампы с направляющими просты и надежны в эксплуатации удобны при установке обладают повышенной стойкостью но боле сложны в изготовлении. Применяются в серийном крупносерийном и массовом производстве. Наибольшее распространение получили штампы с направляющими колонками которые в большинстве случаев снабжаются неподвижным или подвижным съемником.
По эксплуатационному признаку определяемому приемами и способами работ штампы различаются: по способу подачи и установки заготовок; по способу удаления деталей; по способу удаления отходов.
По способу подачи и установки заготовок различают штампы с ручной подачей и штампы с автоматической подачей являющейся принадлежностью штампа или пресса. Штампы с ручной подачей отличаются один от другого лишь конструкцией применяемого упора или фиксатора а штампы с автоматической подачей различаются по типу подачи ленты или штучных заготовок.
По способу удаления деталей различают следующие типы штампов:
-с провалом через отверстие матрицы;
-с обратной вставкой в ленту и удалением вместе с ней;
-с обратным выталкиванием на поверхность штампа и ручным удалением;
-с обратным выталкиванием и автоматическим удалением.
Обратное удаление осуществляется от пружин выбрасывателя или выталкивателя от буфера или от пресса.
По совмещенности операций выбираем комбинированный штамп последовательного действия.
По конструктивному признаку выбираем штамп с направляющими колонками.
По эксплуатационному признаку выбираем штамп с автоматической валковой подачей и с автоматическим удалением деталей по склизу в кроватку. [7]
2 Предлагаемая конструкция штампа
Чертежи штампа представлены на рисунках 2.1 – 2.3 Верхняя часть штампа направляется и центруется относительно нижней части с помощью четырех направляющих колонок. Подача материала в штамп осуществляется валковой
Рисунок 2.1 - Штамп продольный разрез
Рисунок 2.2 - Штамп план верха
Рисунок 2.3 - Штамп план низа
подачей с приводом от вала пресса. Для повышения точности подачи в верхнюю плиту штампа встроены ловители.
Верхняя и нижняя плиты штампов крепятся непосредственно к прессу при помощи пневматических зажимов. На всякий случай в штампе предусмотрены пазы для крепления болтами и хвостовик для крепления за хвостовик верхней части штампа.
К верхней плите крепятся: пуансонодержатель пробивного пуансона и шаговых ножей а также непосредственно гибочные пунсоны. Последний гибочный пуансон также отрезает готовую деталь от ленты после чего она по склизу попадает на ленточный конвейер и транспортируется в тару для деталей. При вырубке осуществляется прижим заготовки пружинным съемником при окончательной гибке – выталкивателем. И тот и другой работают от пружин.
На входе ленты для ее точного направления установлен специальный кронштейн с направляющими планками предотвращающими боковые смещения ленты.
Удаление отходов от обрезки ленты шаговыми ножами происходит в специальный паз в нижней плите штампа откуда периодически сдуваются пневмосдувом.
3 Выбор материала и термообработки деталей штампа
Рабочие детали штампов подвергаются ударной нагрузке с сильной концентрацией напряжений на рабочих кромках или на рабочей поверхности. Поэтому к материалу пуансонов и матриц предъявляются требования высокой или повышенной твердости и износостойкости при наличии достаточной вязкости.
Материал должен хорошо сопротивляться износу от трения должен сохранять острые режущие кромки без разрушения и затупления в течение как можно большего времени. Материал должен быть дешевым и не дефицитным.
Выбор материала ведем с учетом локальной фактической нагрузки режущих кромок пуансонов и матриц в зависимости от отношения Sd 3. При вырубке до 5 мм можно деталей простой конфигурации из материала толщиной применять:
-углеродистые инструментальные стали небольшой прокаливаемости (диаметром до 25 мм) У8А У10А У8 У10;
-легированные стали повышенной прокаливаемости (диаметром до 45 мм) Х09 (ШХ9) 9Х 9ХС ХВГ 9ХВГ;
-высокохромистые стали (диаметром до 80 мм) Х12Ф1 Х12Ф Х12М Х12ТФ Х12М;
-легированные стали повышенной вязкости 4ХС 6ХС 5ХВ2С 5ХВГ.
Исходя из рекомендаций УГК-ТОС ЗИЛа выбираем следующие материалы для деталей штампа:
Пробивные матрицы - У10А HRCэ 57 61
Пробивные пуансоны - У10А HRCэ 57 61
Гибочная матрица - У10А HRCэ 57 61
Гибочный пуансон - У10А HRCэ 55 59
Шаговые ножи - У10А HRCэ 55 59
Направляющие колонки и втулки – Сталь 20 цементация на глубину 0.5 мм до твердости HRCэ 61 65.
Штампы для холодной листовой штамповки представляют собой сложную конструкцию состоящую из большого количества деталей разнообразного технологического и конструктивного назначения. Исходя из условий работы и различного характера сопряжения эти детали требуют различной точности изготовления.
Поверхности деталей не соприкасающихся с другими деталями а так же поверхность отверстий после сверления должны иметь шероховатость поверхности не ниже величины 6.3;
Опорные поверхности плит обычной твердости не каленых держателей пуансонов и матриц – шероховатость поверхности 1.6;
Рабочие поверхности гибочных и вытяжных пуансонов – не ниже 0.8;
Рабочие поверхности вырубных пробивных пуансонов рабочие поверхности вытяжных матриц направляющие поверхности колонок и отверстия направляющих втулок изготавливаются с шероховатостью поверхности не ниже 0.4. [3]
4 Расчет исполнительных размеров разделительных пуансонов и матриц
При определении исполнительных размеров пуансонов и матриц для разделительных операций необходимо предусмотреть правильный выбор зазоров и допусков на рабочие размеры инструмента. Величина вырубаемой детали определяется размером матрицы а величина пробиваемого отверстия определяется размером пуансона. При пробивке отверстий размеры пуансона и матрицы определяются зависимостями (2.1) [7]
где - номинальный размер детали;
- верхнее отклонение допуска на этот размер;
- величина одностороннего зазора;
- допуски на изготовление пуансона и матрицы соответственно.
При вырубке отверстий размеры пуансона и матрицы определяются зависимостями (2.2)
где - нижнее отклонение допуска на этот размер;
В данном случае расчету подвергаем размеры инструмента для пробивки отверстия диаметром 8.3 мм.
Допуски на размеры изделия заданы по 14-му квалитету ЕСДП составляют: диаметр 15+0.52. Величина одностороннего зазора для металла толщиной 1 мм из стали с составляет 0.030 мм [3]. Таким образом имеем следующие исполнительные размеры пуансонов и матриц:
dn=(15-2×0.030)-0.040=14.94-0.040
5 Расчет основных деталей штампа на прочность и жесткость
Матрица и пуансон определяют работоспособность надежность и долговечность штампа. Их расчет - важнейший этап разработки документации штампа.
Проверочному расчету на прочность подлежат обычно наиболее нагруженные пробивные пуансоны небольших размеров. При пробивке отверстий размеры которых сопоставимы с толщиной материала локальные удельные нагрузки на режущие кромки пуансона в два - три раза больше чем на режущие кромки матриц. В данном случае таких отверстий нет поэтому расчет удельных давлений на режущие кромки пуансонов проводить не обязательно.
Пуансон следует проверить на сжатие по наименьшему сечению. Условие удовлетворительной прочности на сжатие может быть выражено зависимостью (2.3):
где - усилие реза Н;
- площадь режущей кромки мм;
- допустимое напряжение сжатия для закаленной стали У10А.
сж=12×314×15×09×300×1314×7.52=864 (МПа)
При неточности изготовления штампа возникает некоторое смещение пуансона относительно матрицы. Из-за этого возникает изгибающий момент поэтому следует дополнительно проверить пуансон на смещение от изгиба. Принимаем величину смещения пуансона равной половине зазора между матрицей и пуансоном. В нашем случае присутствует поперечный изгиб стержня (пуансона) нагруженного с одного конца (жестко закрепленного) некоторым изгибающим моментом Ми. [7]
Условие изгибной прочности определяется по формуле (2.4):
где - изгибающий момент;
- момент сопротивления сечения мм3;
- допустимое напряжение изгиба для стали У10А.
u=1.2×3.14×15×0.9×300×10.1×153=452 (МПа)
Также необходимо проверить плиту штампа под опорной головкой пуансона на смятие. Условие допустимой прочности на смятие определяется формулой (2.19).
где - опорная поверхность головки пуансона мм2;
- допустимое напряжение смятия для плиты штампа из стали Ст.3 в которую упирается пуансон.
см=1.2×3.14×15×0.9×300×10.1×252=98
Поскольку то под головку пуансона можно не подкладывать стальную каленую пластину.
Также необходимо проверить пуансон на продольный изгиб согласно формуле (2.6):
где - модуль упругости первого рода для стали;
- момент инерции сечения пуансона м4;
- коэффициент запаса.
L=4.43× (200×0.05×0.01542.5×1.2×3.14×15×0.9×300×2.5)-12=16 мм
В нашем случае свободная длина пуансона составляет 16 мм.
Подвергнутый расчету пуансон удовлетворяет всем необходимым условиям прочности и жесткости.
6 Расчет стойкости штампа
Долговечность штампов измеряется количеством деталей отштампованных до полного износа рабочих частей определяемого невозможностью их восстановления и получением размерного брака штампуемых деталей.
Значительно раньше этого брака возникает брак по снижению качества штампуемых деталей (заусенцы при вырубке и пробивке задиры риски и царапины при вытяжке и гибке). Этот вид брака сравнительно легко устранить путем перешлифовки вырубных и пробивных штампов или зачистки наростов металла на поверхности вытяжных и гибочных штампов.
Таким образом следует различать долговечность или полную стойкость штампов и промежуточную стойкость или стойкость между двумя перешлифовками.
Полная стойкость штампов находится в прямой зависимости от качественной стойкости так как количество допустимых перешлифовок и зачисток ограничено полным использованием рабочих деталей штампов.
Стойкость штампов зависит от следующих факторов: сорта и механических свойств штампуемого материала; конфигурации детали; относительной толщины материала; конструкции штампа и типа производимой операции; величины зазора; материала и термообработки рабочих деталей штампа; состояния пресса; способа и типа смазки.
Стойкость штампов является условным понятием так как различные рабочие части изнашиваются по-разному.
Расчет стойкости штампа производится по разделительной операции пробивки.
Расчетная формула для определения стойкости пробивных штампов до перешлифовки имеет вид (2.7) [7]:
где - предел прочности штампуемого материала МПа;
К1 = 0.3 - коэффициент материала рабочих частей;
К2 = 0.55 - коэффициент толщины материала.
Указанная формула выведена для следующих производственно-технологических условий: штампуемый материал - Ст.3 Ст.4 Сталь 08кп 08пс; толщина материала 1 мм; материал пуансона и матрицы - Сталь У10А; критерий износа - образование заусенца высотой 0.2 мм.
N= K1×K2×16000((12×300×30012))13=70 тыс.дет.
7 Автоматизация участка
Для повышения производительности и улучшения условий труда при штамповке используются средства автоматизации. На данном пресс – автомате используются разматывающее устройство правильное устройство и валковая подача толкающего типа. Рассмотрим каждый механизм подробнее.
7.1 Расчет разматывающего устройства
Основными требованиями предъявляемыми к разматывающе-правильным устройствам являются их универсальность т.е. возможность использования с различными технологическими агрегатами и постоянство скорости подачи.
Тип разматывающих устройств рекомендуется выбирать в зависимости от массы рулона: до 100 кг применяются неприводные типа катушек; до 150 кг – приводные типа катушек; до 500 кг – приводные с установкой на катки; свыше 500 кг – приводные установки барабанного типа [4].
При выборе приводного разматывающего устройства типа катушки следует учитывать передаточное число редуктора исходя из того чтобы скорость разматывания была немного больше средней скорости подачи (произведение числа ходов в минуту на шаг подачи). При этом во время работы автоматизированной установки между подающим и разматывающим устройством будет образовываться компенсационная петля. Для поддержания длины петли в определенных заданных пределах обеспечивающих спокойную работу подачи разматывающее устройство снабжено командным щупом. При образовании большой петли щуп через конечные выключатели отключает электродвигатель привода. По мере расходования петли лента будет натягиваться и при достижении заданной длинны подаётся команда на включение электродвигателя привода.
Необходимое усилие для распрямления материала рассчитывается по формуле:
где Qз–усилие необходимое для передачи рабочего момента;
S – истинное напряжение которое в данном случае может быть принято равным пределу текучести;
s – толщина материала;
bпр – ширина материала;
- коэффициент трения; для металла по металлу со смазкой принимают = 008 ÷ 012;
z - число зажимных кулачков захватного органа обычно равно 3;
7.2 Расчет правильного устройства
Стабильная работа подающего устройства а так же получение качественных деталей из непрерывного материала в значительной степени зависят от правки материала. Для непрерывного материала правка желательна во всех случаях. Для этого правильные ролики расположены в шахматном порядке накладка их осуществляется исходя из того что каждый участок материала должен получить знакопеременные изгибающие напряжения превышающие предел текучести материала. В результате имеющиеся на материале выпуклости и другие неровности устраняются. Для улучшения качества материала возникающие при этом напряжения должны превышать предел текучести. [4]
В настоящее время правильные устройства компонуются вместе с разматывающим устройством реже с подающим. Специализированные правильные устройства устанавливаются очень редко в основном для широкорулонной стали.
Число правильных роликов зависит от толщины ленты в нашем случае число роликов принимаем равным 9.
где Qпр – суммарное усилие необходимое для продвижения непрерывного материала через zпр непрерывных валков;
zпр – число правильных валков
Мощность электродвигателя привода правильных устройств определяется исходя из расчетного крутящего момента Mр.п:
7.3 Расчет валковой подачи
В валковых подачах используется фрикционный захватный орган. В зависимости от числа кареток в которых устанавливаются валки захватного органа различаются односторонние обычно толкающего типа и двусторонние валковые подачи.
При применении валковых подач для автоматизированного кузнечно-штамповочного производства необходимо учитывать что они надежно работают при использовании материала толщиной 03 – 25 мм. При толщине менее 03 мм происходит неустойчивое захватывание материала вследствие его малой жесткости; при толщине большей 25 мм значительно повышаются инерционные нагрузки от материала которые так же приводят к неустойчивой работе захватного органа валковой подачи. [4]
В современных подачах шарниры преобразующего механизма выполняются на опорах качения; валки захватного органа – полыми и оснащенными постоянно замкнутыми тормозами; диаметры валков выбирают как можно меньшими а для увеличения угла поворота применяют зубчатую передачу.
Движение валки подачи получают от главного вала пресса при проходе ползуна вверх. При ходе ползуна вниз происходит выстаивание валков за счет срабатывания обгонной муфты.
Угол поворота валков φз обеспечивающий перемещение материала на заданный шаг подачи находим по формуле:
где 0 =102 – 103 – коэффициент учитывающий проскальзывание в захватном органе;
D – диаметр валков мм;
φ0 – угол необходимый для заклинивания обгонной муфты рад.
При подстановке числовых значений:
И средняя скорость подачи:
где hз – шаг подачи мм;
t – время перемещения материала на шаг сек;
при подстановке числовых значений:
Расчетное усилие развиваемое захватным органом:
где Рз – Усилие требуемое для оптимально захвата листового материала;
Zр – число приводных роликов;
ашт – ускорение рабочих частей пресса;
g – ускорение силы тяжести;
8 Проектирование участка
Согласно проведенным выше расчетам на участке необходимо разместить две автоматизированные линии. В проекте участка предлагается использовать объемную компоновку линии агрегатированной со складом штампов и рулонов.
Такая компоновка во-первых занимает мало производственных площадей а во-вторых что самое важное позволяет значительно сократить время переналадки пресса на новую деталь за счет практически полной автоматизации процесса смены штампов. [9]
Ширина пролета принята равной 24 метра высота пролета 12 метров. В пролете работает мостовой кран грузоподъемностью Q = 50 т и Q = 5 т. Колонны расположены друг от друга на расстоянии 6 метров (рис. 2.5). На участке так же предусмотрено расположение вспомогательных помещений в состав которых входят: склад деталей склад контрольных приспособлений ОТК склад технологической оснастки участок ремонта штампов и оборудования санузел рассчитанный на 25 человек контора мастера помещение отдыха рабочих.
Рисунок 2.5 – Поперечный разрез цеха
9 Организация производства на участке
Для осуществления технологического процесса необходимо доставить к рабочему месту исходную ленту и установить новый штамп. Это осуществляется следующим способом:
На складе штампов и монтажных плит производится винтовое крепление плит штампа к адаптерным плитам. Эта операция не отнимает машинное время поскольку производится вне пресса. Затем штамп вместе с плитами мостовым краном ставится на выдвижной стол пресса где производится центрирование штампа и крепление адаптерных плит к подштамповой плите восемью пневматическими зажимами. Затем плита пресса вдвигается в рабочую зону и верхняя часть штампа крепится к ползуну при помощи восьми гидравлических зажимов.
Доставка ленты к разматывающему устройству осуществляется с помощью электрокара со склада рулонного материала по проездам где он посредством “щек” центрируется по внутреннему диаметру а затем закрепляется.
Разматывающее устройство подает материал причем в качестве запаса для последующей подачи образуется компенсирующая петля ленты. Лента протягивается при помощи транспортных валков сквозь правильный аппарат. Правильное устройство обеспечивает правку протягиваемой ленты до ее поступления в последующую штамповку. Верхние валки правильного аппарата можно при каждом ходе автоматически приподнимать благодаря чему после каждого хода обеспечивается центрирование ленты по середине.
Использование электрических систем контролирующих положение деталей на рабочей позиции и в процессе перехода обеспечивает безаварийное обслуживание и работу пресса.
После установки нового рулона и оснастки линия готова к работе. В процессе штамповки в таре для готовых деталей накапливаются изделия.
После заполнения кроватка с деталями транспортируется электрокаром на участок хранения готовой продукции по соседству с которым находится участок ОТК и склад контрольных приспособлений. Детали проходят контроль и рассортировываются на годные и бракованные.
Мелкие и средние детали хранят в металлической таре унифицированной по своим размерам что позволяет размещать ее в несколько ярусов.
На рабочем месте в процессе штамповки образуется много отходов металла в среднем не меньше 15% от общего количества перерабатываемого на участке металла. Поэтому при проектировании цеха должно быть уделено большое влияние вопросом удаления частичного использования и придания отходам вида удобного для транспортировки и переплавки в металлургических печах.
Существуют несколько способов уборки и транспортировки отходов:
-отходы собирают в тару или напольные тележки расположенные возле прессов.
-отходы транспортируют тележками в подвальных помещениях под цехом куда они ссыпаются через люки в перекрытии подвала.
-отходы собирают и транспортируют ленточными транспортерами установленными в подвалах под цехом или в траншеях.
-отходы собирают и транспортируют комбинированным способом сочетая наземный и подземный сбор и удаления отходов.
Применительно к спроектированному участку предпочтительнее первый способ удаления отходов в связи с малыми габаритами отходов и непригодности их дальнейшего использовании.
На разработанном участке предусмотрены ремонтные службы осуществляющие работы по техническому уходу и малый ремонт. Остальные виды ремонта выполняются в ремонтно-механических и инструментальных цехах завода.
Участок ремонта штампов и приспособлений выполняет периодические осмотры и проверки штампов приспособлений: малый и средний ремонт. Капитальный ремонт штампов осуществляется в инструментальных цехах.
Общее число вспомогательного оборудования мастерских составляет 40 от числа основных станков но не менее трех. В состав вспомогательного оборудования входят: обдирочно-шлифовальные станки настольное точило настольно-сверлильные станки ручные прессы.
В состав участка ремонтных служб входят: площади размещения основного и вспомогательного оборудования; рабочих мест для слесарных работ; площади складов металла и запасных частей; площади кладовых инструмента приспособлений абразивов вспомогательных материалов.
В настоящей главе рассмотрена конструкция штампа последовательного действия для изготовления детали «Корпус инструментального ящика». Конструкция штампа позволяет обойтись без ручного труда при подаче заготовки (ленты) удалении готовых деталей и удалении отходов. Материал термообработка и шероховатость поверхностей основных частей штампа выбраны в соответствии с рекомендациями [7]. Проведенные расчеты наиболее нагруженного пуансона показали достаточный запас его жесткости и прочности. Расчетная стойкость вырубного инструмента составляет 70 000 деталей до перешлифовки.
Для точной центрации верхней и нижней плит штамп оснащен четырьмя направляющими колонками. Крепление штампа к прессу может осуществляться как быстродействующими зажимами что предусматривается в процессе эксплуатации так и традиционными болтами в случае отказа системы смены штампов. Верхняя плита штампа может быть закреплена за хвостовик.
Описанная компоновка линии обеспечивает во-первых существенную экономию производственных площадей за счет использования всего объема отводимого под нее пролета и во-вторых существенное упрощение конструкции как за счет ликвидации промежуточных магазинов роль которых берет на себя транспортно складская система расположенная непосредственно у модулей так и за счет отборочных транспортеров для готовых изделий и отходов роль которых берут на себя склизы металлоконструкции соединяющие прессы с тарой расположенной на нижнем ярусе.
Расположение линии под мостовыми кранами большой грузоподъемности способствует увеличению ее надежности ремонтопригодности и в конечном итоге производительности. При выходе из строя любого автономно установленного устройства в том числе пресса оно оперативно удаляется из линии мостовым краном затем заменяется исправленным устройством и линия продолжает функционировать. Ремонт неисправного устройства осуществляется вне линии на специально оборудовано площадке.
Организационно-экономическая часть
1 Описание экономической части производства
При существующем технологическом процессе изготовление детали «корпус инструментального ящика» осуществляется штамповкой на 7 прессах PKZZ111 315 – 5и PKZZ111 500 – 2 шт.
Работа подразделений данного участка заключается в:
)На заготовительном участке из листа 1 × 1250 × 2500 мм нарезаются карточки размером 600 × 600мм.
)Затем транспортировщик доставляет их участок штамповки.
)Осуществляется формовка рёбер жёсткости на прессе под управлением и наблюдением оператора наладчика.
)Полученные заготовки доставляются транспортировщиком к следующему прессу.
)Осуществляется пробивка отверстий на прессе под управлением и наблюдением оператора наладчика.
) Следующий этап получение детали «корпус инструментального ящика» заключается в транспортировке к очередному прессу
)Осуществляется операция отрезка полуфабриката по шагу.
)Далее заготовки транспортируют на следующую операцию.
)Осуществляется гибка полок предварительная завивка 2- х петлей 4мм.
) Транспортировщик доставляет заготовки к следующему прессу.
) На прессе осуществляется окончательная завивка.
) Далее заготовка транспортируется на участок “Молдинги”
) Окончательная гибка боковых стенок ящика.
К работе на данном участке цеха привлечены также контролер слесарь по штампам слесарь по ремонту оборудования и электромонтер. Все они входят в штат всего цеха холодной листовой штамповки и их подразделения находятся в цеху (в состав проектируемого участка занимаемые площади этими подразделениями не входят). Их скооперированость обеспечивается мастером данной линии цеха а скооперированость всех линий цеха в лице управляющих мастеров обеспечивается старшим мастером цеха. Мастера и старшие мастера так же ведут управление всей работой закрепленными за ними линиями цеха. Общее управление и учет работы всего цеха холодной листовой штамповки осуществляет начальник цеха.
2 Организация ремонта транспорта и инструментального хозяйства цеха
Организация обслуживания и ремонта производственного оборудования и инструмента является структурной единицей цеха так как все оборудование и инструмент применяется и находится только в данном цехе листовой штамповки. Такое решение обосновано тем что:
– были исключены затраты на перемещение ремонтного и обслуживающего оборудования из спец. ремонтных цехов в данный цех холодной листовой штамповки;
– сэкономлено время реагирования и обслуживания данной службы;
– есть возможность транспортировки рем. и обслуживания оборудования транспортными средствами данного цеха холодной листовой штамповки благодаря небольших габаритах а также относительно небольшом весе производственного оборудования и инструмента для мелкой листовой штамповки;
– сэкономлены средства на постройку содержание и обслуживание отдельного ремонтного цеха.
Организация транспорта предусматривает свободное и организованное перемещение различных грузов по цеху. Цех разбит на параллельно расположенные производственные линии. Расположение прессов на проектируемой линии двухрядное на траншейном фундаменте посередине между прессами расположен сквозной проезд вдоль всей линии. Центральных проезда 2 проходящих перпендикулярно производственным линиям.
Над каждой производственной линией расположен 1 рельсовый мостовой кран с возможностью перемещения вдоль всей линии с зоной охвата соответственных участков центральных проездов.
Перемещение заготовительного материала штампов и другого оборудования по линии осуществляется 1 краном. Перемещение тары по линии осуществляется 1 электрокаром. Перемещение грузов от линии к линии а так же межцеховые перемещения осуществляются специализированными электрокарами (не входят в штат проектируемого участка цеха).
Организация контроля произведенной продукции а так же промежуточных полуфабрикатов осуществляется службой контроля качества продукции являющейся структурной единицей всего цеха (не входит в состав проектируемого участка цеха).
Все затраты на услуги перечисленных раннее служб не входящих в состав проектируемого участка но являющимися структурными единицами всего цеха будут внесены в смету годовых затрат на производство как «прочие расходы»
Количество и стоимость оборудования при существующей технологии:
Годовой объём выпуска 300000Стоимость прессов:
– PKZZ111315 – 850 000 руб.
– PKZZ111500 – 1 000 000 руб.
3 Расчёт количества оборудования и коэффициента его загрузки
Таблица 3.1 – Расчет потребного количества оборудования
Годовой объем выпуска(Вr)
Пресс №1 PKZZ111500
Пресс №2 PKZZ111500
Пресс №3 PKZZ111315
Пресс №4 PKZZ111315
Окончательная завивка
Пресс № 5 PKZZ111315
Пресс № 6 PKZZ111315
Итого в нормо-минутах
Время на переналадку (7%)
Время станко-часов с учетом времени на переналадку
Фонд времени единицы оборудования в часах (Фэф)
Расчетное количество оборудования
Коэффициент загрузки
Фонд времени работы единицы оборудования Фэф в течение планового периода определяется по формуле:
где Фэф – эффективный фонд времени [час];
Фн=(250×2×8) – номинальный фонд времени определяемый умножением количества рабочих дней в плановом периоде на число рабочих смен в сутки – n и на продолжительность одной смены в часах [час];
Р – процент времени простоя оборудования в ремонте к номинальному фонду времени.
Коэффициент загрузки оборудования определяется по формуле:
где Ср = – расчетное количество оборудования;
Спр = 7 – принятое количество оборудования.
Ср – расчетное количество оборудования [шт.];
Спр – принятое количество оборудования [шт.].
Принятое количество оборудования определяется округлением дробного расчетного числа единиц оборудования до большего целого числа. Таким образом принятое количество оборудования равно единице.
Коэффициент загрузки по участку должен быть как правило в пределах от 075 до 086. Этот предел показывает недогруженность оборудования что влечет к выбору лучшего варианта загрузки а в случае перегрузки следует предусмотреть для оборудования трехсменную работу. [8]
Таблица 3.2 – Ведомость оборудования
Кол-во ед. оборудования
Мощность электродвигателя кВт
Амортизационные отчисления
С учетом времени работы 3333%:
- стоимость оборудования составляет (4250000+2000000)026 = 2083125 (руб.)
- амортизационные отчисления составляют (327250+154000) ×06109 = 25880 (руб.)
Ремонтная сложность пресса – PKZZ 315
Ремонтная сложность пресса – PKZZ 500
Площадь участка составляет (455) +(502) =325 (м2)
Определение численности и состава работающих на участке;
Для работы на данных видах оборудования требуется 7 операторов-наладчиков и 1 штамповщиков.
4 Организация оплаты труда
Форма оплаты труда для основных рабочих – повременно-премиальная. Это обосновано тем что данная форма оплаты труда применяется при следующих условиях:
- производственный процесс строго регламентирован и функции оператора-наладчика сводятся к наблюдению за технологическим процессом;
- премии являются стимулом для рабочих для производства большего количества деталей и повышения их качества.
Тарифный фонд зарплаты Фтар = Стар×Фэф×Кр×n
где Стар – тарифная ставка [руб. ×час];
Фэф – эффективный фонд времени рабочего [час]
Таблица 3.3 – Расчет потребного числа основных рабочих
Тарифный фонд зарплаты Фтар руб.
Дополнительная зарплата Дз руб.
Годовой фонд зарплаты руб.
С учетом ЕСН (26%) = 96702606 026 = 25142677 (руб.)
Кр – коэффициент разряда.
Фтар =4028×3600×15×7 = 761292 (руб.)
П =03×761292= 2283876 (руб.)
Дополнительная зарплата Дз составляет 10% от суммы Фтар и П:
Дз =(761292 + 2283876) ×01 = 121806.72 (руб.)
где Стар – тарифная ставка
Фэф – эффективный фонд времени рабочего
Фтар =3578×3600×15×7 = 676242 (руб.)
П =03676242 = 202872.6 (руб.)
Дз =(202872.6+676242) ×01 = 8701146 (руб.)
Таблица 3.4 - Расчет потребного числа вспомогательных рабочих
Тарифный фонд зарплаты
Слесарь по ремонту оборудования
Итого по вспомогательным и основным рабочим
С учетом времени работы 3333%: 18055529×03333 = 7760841(руб.)
С учетом ЕСН (26%): 6560315 ×026 = 1705681 (руб.)
на 100 деталей на 6 операций следовательно принимаем
где n – норма на 1-го рабочего
Тарифный фонд зарплаты Фтар = Стар×Фэф×К ×n
Фтар =96×3600×13×006 = 134784 (руб.)
П =03×134784 = 40435 (руб.)
Дополнительная зарплата Дз составляет 10% от суммы Фтар и Д:
Дз = (40435+134784) ×01 = 17521 (руб.)
Слесарь по ремонту оборудования:
на 300 единиц оборудования к наибольшей рем. сложности оборудования следовательно принимаем
Фтар = Стар×Фэф×Кр×n.
Фтар= 2244×3600×15×0117 = 7088.8 (руб.)
П =04×7088.8= 283551 (руб.)
Дз =(7088.8+283551) ×01 = 992.43 (руб.)
на 40 единиц инструмента к наибольшей рем. сложности оборудования следовательно принимаем
Фтар = Стар×Фэф×Кр×n = 2536×3600×16×05 = 365184 (руб.)
Премии П = 04×Фтар = 04×365184 = 1460736 (руб.)
Дз = (П + Фтар) ×01 = (1460736+365184) ×01 = 511257 (руб.)
на 800 единиц оборудования к наибольшей рем. сложности оборудования следовательно принимаем
Фтар = Стар×Фэф×Кр×n = 1623×3600×14×00375 =153373 (руб.)
Премии П = 04×Фтар = 04×153373= 61349 (руб.)
Дз = (П + Фтар) ×01 = (61349+153373) ×01 = 21472 (руб.)
на 1 единицу оборудования к норме 1 следовательно принимаем
Тарифный фонд зарплаты Фтар = Стар×Фэф×Кр×n = 1152×3600×14×1 = 290304 (руб.)
Премии П = 04×Фтар = 04×290304 = 1161216 (руб.)
Дополнительная зарплата Дз составляет 10% от суммы Фтар и П:
Дз = (П + Фтар) ×01 = (11612+290304) ×01 = 406425 (руб.)
Тарифный фонд зарплаты Фтар = Стар×Фэф×Кр×n = 1713×3600×13×1 = 400842 (руб.)
Премии П = 04×Фтар = 04×400842 = 1603368 (руб.)
Дз = (П + Фтар) ×01 = (1603368+400842) ×01 = 5611788 (руб.)
на 2000 м2 к площади пола в цехе 375 следовательно принимаем
Фтар = Стар×Фэф×Кр×n
Фтар 536×3600×018 = 1736.64 (руб.)
П = 04×1736.64 = 694.65 (руб.)
Дз = (П + Фтар) ×01
Дз = (694.65+1736.64) ×01 = 24312 (руб.)
Таблица 3.5 - Расчет потребного числа руководящего персонала
Месячный фонд зарплаты руб.
С учетом времени работы 3333%: 244728×03333 = 81568 (руб.)
ЕСН составляет 26%: 81568×026 = 21208 (руб.)
на норму в 20 рабочих к 48745 рабочих по цеху следовательно принимаем
на норму в 5 мастеров к 0244 рабочих по цеху следовательно принимаем
на норму в 3 старших мастеров к 00488 старших мастеров по цеху следовательно принимаем
5 Расчет технико – экономических показателей участка цеха по базовой технологии
Определение стоимости основных фондов:
Стоимость основных фондов включает стоимость:
здания и сооружения;
рабочих машин и оборудования;
производственного и хозяйственного инвентаря.
Стоимость части здания определяется по площади занимаемой проектируемым участком. Расчёт производится укрупнено:
Кзд = S ×Сзд = 375 × 534 = 200250 (руб.)
где Кзд – капитальные вложения в здания (руб.)
S – площадь участка (м2);
Сзд – стоимость производственных площадей (руб.м2).
Стоимость оборудования (по форме 2) составляет 2083125 (руб.)
Стоимость штампа холодной листовой штамповки Цш определяется по формуле:
где Тп – плановая трудоемкость изготовления штампа [нормо-час] определяется в зависимости от типа штампа и его габаритов;
Сн – себестоимость одного нормо-часа без учета затрат на материалы штампа (руб.);
КQ – коэффициент учитывающий сложность заготовки и габариты штампа;
Цмш – стоимость материала штампа (руб.)
Стоимость материала штампа
Цмш =Vштамп×05×рмат.ла×стоимость 1кг материала
где Vштамп – объем штампа [м3];
рмат.ла – плотность материала штампа [кгм3].
Все инструменты используемые в данном производстве обладают стойкостью более года следовательно для них определяется доля амортизации в год.
В том случае если стойкость штампа больше годового выпуска детали определяется доля амортизации штампа в год Амортизационные отчисления устанавливаются в размере 30% от стоимости штампа.
Таблица 3.6 – Плановая трудоемкость изготовления штампов
Таблица 3.7 – Расчет амортизационных отчислений
Количество штампов шт.
Таблица 3.8 – Основные фонды
Группа основных фондов
Здания и сооружения м2
Рабочие машины и оборудование шт.
Производственный и хозяйственный инвентарь
Стоимость производственного и хозяйственного инвентаря принимается в размере 05-2% от общей стоимости машин и оборудования. Таким образом стоимость производственного и хозяйственного инвентаря составляет:
Синв = 0015(310360+2083125)= 359023 (руб.)
Таблица 3.9 - Потребность в основных материалах
Характеристика материала
Стоимость материала на одну шт.
Чистый вес одной детали
Количество отходов от одной детали
Цена отходов от одной детали
Программа деталей в год (Вr)
Потребность материала на год
Стоимость потребного на год материала
Количество отходов в год
Стоимость отходов за год
Сгод.отх=Мгод.отх×Ц1отх
Затраты на материал за вычетом отходов
6 Расчет сметы косвенных (накладных) расходов
6.1. Статьи группы А связанные с работой оборудования
Статья 1. Содержание оборудования и рабочих мест.
а) Стоимость смазочных обтирочных материалов мелких запасных частей для оборудования принимают в размере 14% от стоимости оборудования т.е. эти расходы составляют: 2083125×0014 = 29163.75 (руб.);
б) Годовой фонд зарплаты вспомогательных рабочих составляет 18055529 (руб.)
ЕСН (26%) составляет: 18055529×026 = 4694437 (руб.)
в) W =М××(В×tшт)К1 К2 =(6003 × 11500095×09) 2+ (55×03 11500095 × 09) × 5 =4842105+11096491=15938596 (кВтч)
где W – годовой расход силовой электроэнергии для оборудования с одинаковой мощностью [кВтч];
М – установленная мощность [кВт];
– коэффициент использования мощности:
– для средних прессов = 03;
– для малых прессов = 025;
Вtшт – суммарное количество нормо-часов по виду оборудования в течение года [нормо-час];
К1 – коэффициент учитывающий потерю тока в сети;
К2 – КПД электромоторов = 09.
г) Стоимость электроэнергии определяется по формуле:
Сэ =С W = 275 15938596 =43831139 (руб.)
где С – стоимость 1кВт-ч = 275 (руб.)
д) Расход воды для хозяйственных нужд Вх определяется из расчета на одну тонну изделий - 10 м3 . Стоимость воды за 1 м3 – 567 (руб.)
В Х = 112 т ×10 м3 × 567 руб. = 63504 (руб.)
Вся партия деталей: Вr×чистый вес детали = 300000× 0381= 114300 кг
е) Затраты на сжатый воздух Зв в цехах холодной штамповки –200 м3 на 1 тонну продукции.1м3 = 031 (руб.)
Зв = 200 м3 ×112 т × 031 руб. м3 = 6944 (руб.)
Статья 2. Текущий ремонт оборудования и штампов.
Стоимость ремонтируемых средств (т.е. прессов и штампов) составляет:
Затраты по статье 2 (запасные части услуги других цехов) принимаются в размере 1% от стоимости ремонтируемых средств и составляют:
- для прессов: 2083125× 001 = 2083125 (руб.)
- для штампов: 310360× 001 = 31036 (руб.)
Всего по статье 2: 2083125+ 31036 = 2393485 (руб.)
Статья 3. Содержание и расходы по эксплуатации транспорта.
Из всего комплекса затрат в данном дипломе определяется только зарплата и отчисления (ЕСН) рабочих занятых в данном виде работ.
Годовой фонд зарплаты рабочих составляет:
- крановщик: 4470681 (руб.)
- транспортировщик: 6172966 (руб.)
ЕСН (26%) составляет:
- крановщик: 4470681 × 026 = 1591562 (руб.)
- транспортировщик: 6172966 × 026 = 2197575 (руб.)
Затраты на оборудование можно принять в размере 150% от рассчитанной зарплаты: (44706+6172966) ×15 = 15965349 (руб.)
Статья 4. Амортизационные отчисления для оборудования.
Для штампов норма амортизации составляет 30%: 310360×03 = 93108 (руб.)
Для прессов – 77%: 0077×2083125 = 16040062 (руб.)
Всего расходов по статье 3: 65520 +16938306 = 25350862 (руб.)
Статья 5. Затраты на малоценный и быстроизнашивающийся инструмент.
Данная статья не учитывается так как весь инструмент обладает стойкостью более года.
Статья 6. Прочие расходы.
Прочие расходы не предусмотренные в предыдущих статьях принимаются в размере 2% от суммы расходов по статьям 1-5 и составляют:
(29163.75+18055529+4694437+43831139 +63504 +6944+2393485 +15965349 +25350862) ×002 = 101803.37 (руб.)
6.2 Статьи группы Б – общецеховые (участковые) расходы
Статья 7. Основная зарплата руководящего персонала
Годовой фонд зарплаты руководящего персонала составляет 244728 (руб.)
ЕСН (26%) составляет: 244728×026 = 6363 (руб.)
Статья 8. Содержание зданий и сооружений.
Эти затраты включают:
а) Стоимость материалов на хозяйственные нужды составляет 03% от стоимости зданий и сооружений: 0003200250 = 60075 (руб.)
б) Расходы на электроэнергию для освещения определяемые по формуле:
Э осв =15×П ×1300×105 1000 ×Ц = 15 ×375 ×1300×1051000 × 275 = 279204 (руб.)
где 15 – средний расход электроэнергии площади участка на 1м2 [кВт×чм2];
П – внутренняя площадь [м2];
00 – число часов освещения в год при односменной работе;
5 – коэффициент учитывающий дежурное освещение;
Ц – цена за 1 кВт-ч = 275 (руб.)
в) Затраты на пар для отопления подсчитываются по формуле:
Пот =Р× Ф от × П × h 500 × 1000 Цn =25×4000× 375 × 15 500 × 1000 × 3173 = 354554 (руб.) где Р – средний расход тепла на 1м3 объема отапливаемого помещения (25 калчас);
Фот – число часов отопительного сезона (4000 часов);
h – высота потолков в помещении [м];
0 – теплоотдача 1 кг пара в калориях;
00 – пересчет кг в тонны;
Цп – цена тонны пара (3173 руб.);
г) Расход воды для хозяйственных нужд Вх определяется из расчета на одного работающего в год 8 м3 для холодных цехов. Стоимость воды за 1 м3 = (399 руб.)
Вх = 133267 × 8 × 399 = (425388 руб.)
Статья 9. Текущий ремонт зданий и сооружений.
В эту статью включается стоимость ремонтно-строительных материалов услуг ремонтных цехов и т.п. Затраты составляют 3% от стоимости зданий и сооружений: 003 × 200250 = 60075 (руб.)
Статья 10. Амортизация зданий и сооружений.
Принимается в размере 12% от стоимости зданий и сооружений и составляет: 0012×200250 = 2403 (руб.)
Статья 11. Отчисления на социальное страхование основных рабочих.
С учетом ЕСН 26% составляет: (11114858 + 96702606) ×026 = 54041322 (руб.)
Статья 12. Дополнительная зарплата основных рабочих.
1806.72+ 8701146 = 20881818 (руб.)
Статья 13. Расходы по охране труда.
Принимаются в размере 1200 (руб.)
Составляют: 1200×133267 = 1599204 (руб.)
Статья 14. Прочие расходы.
Составляют 2% от суммы по статьям общецеховых (участковых) расходов (244728 + 6363 + 60075 + 279204 + 354554 + 425388 + 60075+ 2403+ +54041322+ 20881818 + 1599204 ) 002 = 163839 (руб.)
Статьи затрат входящие в состав калькуляции подразделяются на простые и сложные. Простые состоят из одного экономического элемента (заработная плата). Комплексные статьи включают в себя несколько элементов затрат и могут быть разложены на простые составляющие (общепроизводственные общехозяйственные расходы).
Учет затрат необходим для определения финансовых затрат предприятия.
Из затрат на материальные ресурсы включаемых в себестоимость продукции исключается стоимость реализуемых отходов [12].
Таблица 3.10 – Смета цеховых (накладных) расходов
Содержание оборудования и рабочих мест
Текущий ремонт оборудования и штампов
Содержание и расходы по эксплуатации транспорта
Амортизационные отчисления для оборудования
Затраты на малоценный и быстроизнашивающийся инструмент
Основная зарплата руководящего персонала
Содержание зданий и сооружений
Текущий ремонт зданий и сооружений
Амортизация зданий и сооружений
Отчисления на социальное страхование основных рабочих
Дополнительная зарплата основных рабочих
Расходы по охране труда
Всего цеховых расходов
Таблица 3.11 - Составление сметы годовых затрат на производство
По экономическим элементам затрат
По статьям калькуляции
Основные материалы за вычетом отходов
Энергия технологическая
Зарплата основных рабочих с доплатами
в т.ч. на инструмент
Вспомогательные материалы
Амортизация основных средств
6.3 Калькуляция себестоимости единицы продукции
способ. Себестоимость одной детали С определяется по статьям калькуляции:
где М – стоимость основных материалов на деталь;
М = С1шт-Цотх = 1177–0013 = 11757 (руб.)
Н – величина накладных расходов приходящихся на деталь определяется по формуле:
Н = Всего цеховых расходов Вr = 5840752.1300000 = 1947 (руб.)
ЗО - основная зарплата за деталь
ЗО = Зарплата_ основных_ рабочих число деталей =1013512300000 = 338 (руб.)
С = 11757 + 1947 + 338 = (3562 руб.)
способ. Себестоимость одной детали С определяется по смете годовых затрат на производство:
С = Итого в смете годовых затрат Вr = 10688091 300000 = (3562 руб.)
Процедура калькуляции себестоимости по операциям включает в себя следующие моменты: определения основных видов деятельности предприятия определения факторов себестоимости по конкретным видам деятельности создание центров ответственности по каждому виду деятельности процесс перемены затрат с видов деятельности на созданные продукты. Данная методика в основном сосредоточена на косвенных элементах себестоимости продукции большая часть которых рассматриваются как постоянные. Использование информации о различных методах калькуляции для принятия определенных управленческих решений с учетом финансовой перспективы в значительной степени зависит от возможности прогнозирования и регистрации будущего потока денежных средств. Если постоянные затраты принятые в расчет но не влияют на изменения денежных потока ( или результаты незначительны ) тогда выгоды от прекращения находят отражения в данных о полной себестоимости единицы продукции которые представляются руководству для принятия решения. [12]
7 Расчет экономики предлагаемого варианта
Таблица 3.12 – Расчет потребного количества оборудования
Фн (25028) – номинальный фонд времени определяемый умножением количества рабочих дней в плановом периоде на число рабочих смен в сутки – n и на продолжительность одной смены в часах [час];
где Ср =182328 3600 =05 – расчетное количество оборудования;
Спр = 1 – принятое количество оборудования.
- стоимость оборудования составляет (850000)03333 = 283305 (руб.)
- амортизационные отчисления составляют (65450)06109 = 399834 (руб.)
Таблица 3.13 – Ведомость оборудования
Двух- кривошипный пресс
Площадь участка составляет 300 (м2)
Определение численности и состава работающих на участке:
Для работы на данных видах оборудования требуется 1 оператор-наладчик и 1 штамповщик.
Организация оплаты труда:
- производственный процесс строго регламентирован и функции оператор-наладчика сводятся к наблюдению за технологическим процессом;
Таблица 3.14 – Расчет потребного количества основных рабочих
С учетом ЕСН (26%) = 30366838 × 026 = 7895377 (руб.)
Фэф – эффективный фонд времени рабочего [час];
Фтар =4028×3600×15×1 = 108756 (руб.)
П =03×108756= 326268 (руб.)
Дз =(326268 + 108756) ×01 = 1413828 (руб.)
Фтар =3578×3600×15×1 = 96606 (руб.)
П =03×96606 = 289818 (руб.)
Дз =(2898186+196606) ×01 = 2255878 (руб.)
Таблица 3.15 – Расчет потребного количества вспомогательных рабочих
Продолжение таблицы 3.15
С учетом времени работы 3333%: 18055529×03333 = 7760841 (руб.)
С учетом ЕСН (26%): 6560315 × 026 = 1705681 (руб.)
Тарифный фонд зарплаты Фтар = Стар×Фэф×К×n
П =03134784 = 40435 (руб.)
Дз = (40435+134784)01 = 17521 (руб.)
Фтар = Стар×Фэф×Кр×n = 2536×3600×16×05 = 365184 (руб.)
Дз = (П + Фтар) ×01 = (61349+153373)01 = 21472 (руб.)
Тарифный фонд зарплаты Фтар = СтарФэфКрn = 11523600141 = 290304 (руб.)
на 2000 м2 к площади пола в цехе 300 следовательно принимаем
Дз = (694.65+1736.64)01 = 24312 (руб.)
Таблица 3.16 – Расчет потребного количества руководящего персонала
8 Расчет технико – экономических показателей участка цеха по базовой технологии
Кзд = S Сзд = 300 534 = 160200 (руб.)
где Кзд – капитальные вложения в здания (руб.):
S – площадь участка [м2];
Сзд – стоимость производственных площадей [рубм2].
Стоимость оборудования (по форме 2) составляет 283305 (руб.)
Сн – себестоимость одного нормо-часа без учета затрат на материалы штампа [руб.];
Цмш – стоимость материала штампа [руб.]
Таблица 3.17 – Плановая трудоемкость изготовления штампа
Цмш =Vштамп05рмат.ластоимость 1кг материала
Таблица 3.18 – Расчет амортизационных отчислений
Амортиза-ционные отчисления
Синв = 0015×5739878 = 860981 руб.
Таблица 3.19 – Основные фонды
Таблица 3.20 - Потребность в основных материалах
9 Расчет сметы косвенных (накладных) расходов
Статьи группы А связанные с работой оборудования:
а) Стоимость смазочных обтирочных материалов мелких запасных частей
для оборудования принимают в размере 14% от стоимости оборудования т.е.
эти расходы составляют: 283305×0014 = 396627 (руб.);
в) W =М(Вt)К 1 × К 2 = (5503 ×1704095 × 09) =3288421 (кВтч)
Сэ =С W = 275 × 3288421=9043157 (руб.)
где С – стоимость 1кВтч = 275 (руб.)
В Х = 114 т ×10 м3 × 567 руб. = 63504 (руб.)
Вся партия деталей: Вrчистый вес детали = 300000 × 0381= 114300 (кг)
Зв = 200 м3 × 114 т × 031 руб. м3 = 6944 (руб.)
- для прессов: 283305× 001 = 283305 (руб.)
- для штампов: 2906828× 001 = 290682 (руб.)
Всего по статье 2: 283305×290682 = 573987 (руб.)
- транспортировщик: 6172966 026 = 2197575 (руб.)
Для штампов норма амортизации составляет 30%: 290682×03 = 872046 (руб.)
Для прессов – 77%: 0077×283305 = 2181448 (руб.)
Всего расходов по статье 4: 872046 +2181448= 25350862 (руб.)
(396627 +18055529+9043157+4694437+63504+6944+573987+15965349 +25350862)002 = 1508187 (руб.)
Статьи группы Б – общецеховые (участковые) расходы:
а) Стоимость материалов на хозяйственные нужды составляет 03% от стоимости зданий и сооружений: 0003×160200 = 4806 (руб.)
Э осв =15 П × 1300× 105 1000 ×Ц = 15×375 × 1300× 1051000 ×275 = =279204 (руб.)
П от =Р Ф от × П × h 500 × 1000 Цn =25×4000×300×15 500 × 1000 × 3173= -=354554 (руб.)
где Р – средний расход тепла на 1м3 объема отапливаемого помещения (25 калчас);
Цп – цена тонны пара 3173 (руб.).
г) Расход воды для хозяйственных нужд Вх определяется из расчета на одного работающего в год 8 м3 для холодных цехов. Стоимость воды за 1 м3 = 399 (руб.)
Вх = 133267 × 8 × 399 = 425388 (руб.)
В эту статью включается стоимость ремонтно-строительных материалов услуг ремонтных цехов и т.п. Затраты составляют 3% от стоимости зданий и сооружений: 003 × 160200 = 4806 (руб.)
Принимается в размере 12% от стоимости зданий и сооружений и составляет: 0012×160200 = 19224 (руб.)
С учетом ЕСН 26% составляет: 30366838×026 = 7895377 (руб.)
Статья 12. Дополнительная зарплата основных рабочих = 36697.06 (руб.)
Составляют: 1200133267 = 1599204 (руб.)
Статья 14. Прочие расходы
Составляют 2% от суммы по статьям общецеховых (участковых) расходов (244728 +363+4806+279204+354554+425388+4806+19224+7895377+36697.06 + +1599204) × 002 = 366342 (руб.)
Таблица 3.21 – смета цеховых (накладных) расходов
Продолжение таблицы 3.21
Составление сметы годовых затрат на производство:
Таблица 3.22 – Смета затрат на производство
Калькуляция себестоимости единицы продукции:
Н = Всего_ цеховых_расходов Вr = 97601064300000 = (325 руб.)
ЗО = Зарплата_ основных_ рабочих число деталей =30366838300000 = 101 (руб.)
С = Итого в смете годовых затрат Вr = 590262514 300000 = 196 (руб
10 Расчет экономического эффекта
Э = (С1+нК1) - (С2+нК2) (руб.)
где С1 – себестоимость годового выпуска по базовому варианту;
С2 – себестоимость годового выпуска по проекту;
К1 = 616231300000 = 205 (руб.) – капитальные вложения на деталь по действующей технологии;
К2 = 605631300000 = 201 (руб.) – капитальные вложения по предлагаемой технологии;
н – нормативный коэффициент эффективности = 02.
Себестоимость единицы изделия по базовому варианту: С1=3562 (руб.)
Себестоимость единицы изделия по новому варианту: С2=196 (руб.)
Э = ((3562 + 02·205) - (196+ 02·201))300000 = 4808400 (руб.)
Усовершенствование технологии получения детали «корпус инструментального ящика» заключается в том что после модернизации процесса изготовления данной детали сведено количество оборудования от семи единиц к одной следовательно количество штампов так же уменьшается с семи единиц до одной.
Уменьшение количества рабочих площади занимаемого оборудования затрат на электроэнергию и прочих денежных расходов способствуют в перспективе использование рациональной выгоды для наращивания мощи прессового корпуса как части завода так и способствовать переходу завода на новые серийные выпуски новых автомобилей европейских стандартов.
1 Анализ вредных и опасных факторов листоштамповочных цехов
В цехах холодной листовой штамповки могут возникать следующие опасные и вредные факторы для здоровья людей:
-производственный шум и вибрация;
-опасность поражения электрическим током;
-загрязнения техническими жидкостями;
-опасность возникновения пожара;
-недостаточная освещенность;
-возможность травматизма;
-неблагоприятный климат.
Прессовые цеха относятся к тому типу производства где уровни шума довольно высоки. В листоштамповочном производстве основными источниками шума прессов и механизмов являются зубчатые передачи подшипники соударяющиеся металлорежущие предметы и т.д. Так же шумовые эффекты на участке создает сам процесс резания металла т.е. вклинивание режущих кромок штампа в металл.
Шум оказывает вредное влияние на весь организм и в первую очередь на центральную нервную систему сердечно-сосудистую систему и органы слуха человека. Длительное его воздействие может привести к ухудшению слуха а в отдельных случаях и к глухоте. [15]
Шум на производстве неблагоприятно воздействуют на работающего: ослабляет внимание человека увеличивает расход энергии при одинаковой нагрузке замедляет скорость психических реакций снижает производительность труда.
Защита рабочих от шума может осуществляться как коллективными средствами и методами так и индивидуальными средствами. Борьба с шумом в производственном помещении направлена на его снижение до нормативного уровня.
Снижение шума в помещении на рабочем месте ведется по 3-м направлениям; уменьшение шума в источнике; использование средств звукоизоляции; использование средств индивидуальной защиты.
В первую очередь надо использовать коллективные средства снижающие шум на пути его распространения от источника до защищаемого объекта. Наиболее эффективны мероприятия ведущие к снижению шума в источнике его возникновения. Для этого рабочее пространство пресса закрывается специальным кожухом. Пол цеха холодной листовой штамповки имеет звукопоглощающее покрытие уменьшающее его звукопроводность. На клапанах пневмосистемы производящей сброс сжатого воздуха установлены глушители. Воздуховоды вентиляционных систем звукоизолированы. Для снижения вибрации возникающей при работе пресс устанавливается на фундамент с вибродемпфирующими прокладками. В приводах вспомогательных устройств также предусмотрены виброгасящие элементы. Документом нормирующим параметры шума на рабочих местах является ГОСТ 12.1.003-83 а параметры вибрации - ГОСТ 12.1.012-78.
Загрязнения техническими жидкостями (смазка и т.д.) в предлагаемом технологическом процессе холодной листовой штамповки сведено к минимуму. В предлагаемом к применению относительно современном прессе система смазки организованна так что масло не попадает в окружающую среду. Отработанное масло легко заменяется на новое без каких-либо выбросов. Смазка заготовок перед штамповкой осуществляется в рабочей зоне пресса автоматически и в минимально необходимой мере. Готовые детали укладываются в специальную тару не допуская таким образом загрязнения смазкой рабочего места и соответственно цеха в целом.
Необходимая освещенность рабочих мест обеспечивается естественным и искусственным освещением. Освещение организовано в соответствии со СНиП 11-4-79 и периодически проверяется сотрудниками заводской лаборатории. Проводится плановая очистка и замена светильников и стекол.
Микроклимат в листоштамповочном цехе то есть допустимую температуру относительную влажность скорость движения воздуха и его чистоту обеспечивает система отопления и система вентиляции. Основным нормирующим микроклимат документом является ГОСТ 12.1.005-76 «ССБТ. Воздух рабочей зоны. Общие санитарно-гигиенические требования». Для работы средней тяжести которой и представлен данный технологический процесс допустимые параметры воздушной среды в рабочей зоне производственного цеха (участка линии и т.д.) представлены в таблице 4.
Таблица 4.1 - Оптимальные нормы микроклимата
Относительная влажность %
Скорость движения (воздуха не более) мс
Холодный и переходный
На проектируемом участке холодной листовой штамповки установлено несколько потребителей электроэнергии. Электрооборудование этих потребителей с целью недопущения поражения человека электрическим током должно соответствовать «Правилам установки электроустановок» действующим ГОСТам а его эксплуатация «правилам технической эксплуатации электроустановок потребителей». Кроме этого необходимо выполнять указания по эксплуатации соответствующих установок имеющихся в инструкциях заводов-изготовителей. Подсоединение и отсоединение от электрической цепи а также наблюдение за состоянием электроустановок в процессе их эксплуатации должно проводиться электротехническим персоналом цеха. Включение оборудования в сеть должно производиться только при заземлении корпуса. Изоляция всех проводов должна быть защищена от механических повреждений. Для быстрой остановки всех механизмов на пульте управления необходимо предусмотреть соответствующие кнопки управления в легко доступном месте.
2 Расчет уровня шума на участке
В прессовых цехах шум создается за счет работы электродвигателей выброса в атмосферу сжатого воздуха из пневмосистем муфт и тормозов а также из-за наличия зазоров в исполнительных механизмах прессов что приводит к характерному металлическому стуку в момент соударения рабочих частей штампа.
Для устранения шума от зазоров необходимо выбрать зазоры в исполнительном механизме к моменту начала деформации заготовки. Для этого во всех прессах устанавливаются уравновешиватели ползуна которые к тому же играют еще одну существенную роль в обеспечении безопасности труда: удерживают ползун пресса в крайнем верхнем положении и не дают ему упасть при любом возможном отказе (отказе системы управления и размыкании тормоза поломке шатуна и т.д.).
Для устранения шума от выпуска сжатого воздуха на большинстве современных прессов устанавливается глушитель клапаны распределителя. При штамповке в режиме непрерывных ходов муфта постоянно включена и перепуска воздуха в клапанах не происходит как следствие нет шума от выпуска сжатого воздуха.
Таким образом основным источником шума в кузнечно-прессовых цехах остается гул электродвигателей.
Для оценки соответствия шума предельно допустимым нормам необходимо провести расчет уровня звукового давления на рабочем месте. Для этой цели используем выражение (4.1):
где - уровень звукового давления на рабочем месте;
- уровень звуковой мощности одного источника дБ;
- площадь занимаемая оборудованием м2;
- приведенный к единице площади коэффициент звукопоглащения.
Уровень звуковой мощности одного источника определяется зависимостью (4.2):
где - излучаемая звуковая мощность кВт. [16]
Звуковая мощность прессов составляет 0.001% от номинальной установочной мощности электродвигателя [13]. Общая установленная мощность электродвигателей на участке включая подъемно - транспортное оборудование и станочное оборудование равняется 140 кВт. Площадь участка составляет 620 м2. Приведенный к единице коэффициент звукопоглощения равен 0.3. В этом случае:
3 Нормативы уровня шума
Интенсивный шум приводит к профессиональным заболеваниям органов слуха. Наиболее неблагоприятным для органов слуха является высокочастотный шум (1000 - 4000Гц). Шум особенно прерывистый импульсивный ухудшает точность выполнения операций затрудняет мышление человека.
Нормирование шума ведется в двух направлениях: гигиеническое нормирование и нормирование шумовых характеристик машин ГОСТ 8.055-73 . Действующие нормы шума на рабочих местах регламентируются ГОСТ 12.1.003-83 “ССБТ. Шум. Общие требования безопасности”. Для постоянных шумов нормирование ведется по предельному спектру шума.
Предельным спектром шума – называется совокупность нормативных уровней звукового давления в восьми октавных полосах частот: 63; 155; 250; 500; 1000; 2000; 4000; 8000 Гц.
Для ориентировочной оценки ГОСТ допускает за характеристику постоянного шума на рабочем месте принимать уровень звука в дБА измеряемый по шкале “А” шумометра и определяемый по формуле (4.3):
где - среднеквадратическое звуковое давление с учетом коррекции шумометра Па;
- среднеквадратическое звуковое давление.
В производстве часто шум имеет не постоянный характер. Здесь наиболее удобно пользоваться средней величиной называемой эквивалентным уровнем (по энергии) звука и характеризующей среднее значение энергии звука в дБА (см. табл. 4.2)
Следует заметить что нормы устанавливают предельные значения параметров шума в различных производственных помещениях в зависимости от характера труда в них а не от видов оборудования.
Зоны с уровнем звука выше 85 дБ следует обозначать знаками безопасности. Работающих в этой зоне людей администрация обязана снабжать средствами индивидуальной защиты.
В зонах с октавными уровнями звукового давления свыше 135 дБ в любой октавной полосе даже кратковременное пребывание работающих запрещается.
“Шумным“ технологическим оборудованием считается оборудование на рабочих местах которого уровни шума превышают допустимые по действующим нормам на 10 дБ. [16]
Таблица 4.2 - Допустимые уровни звукового давления (дБ) и уровня звука (дБА) на постоянных рабочих местах
Среднегеометрические значения частот основных полос
Уровни звука и эквивалент уровня звука дБА
Уровни звукового давления
КБ лаборатории медпункты.
Управления (рабочие комнаты)
Помещения и участки точной сборки
Постоянные рабочие места и рабочие зоны на территории предприятия
4 Мероприятия по снижению шума
Защита от шума может осуществляться коллективными и индивидуальными средствами. На рис. 36 представлена общая классификация методов и средств коллективной защиты от шума в зависимости от способа реализации.
Уменьшение шума в источнике т.е. выбор средств снижения шума в источнике его возникновения зависит от происхождения шума. В данном случае для снижения шума от подшипников и зубчатых передач пригодны такие мероприятия как:
-повышение точности обработки и сборки зубчатых передач;
-размещение зубчатых зацеплений в масляных ваннах;
-применение принудительной смазки в сочленениях;
-применение прокладочных материалов и упругих вставок в соединениях для уменьшения колебаний;
-уменьшение интенсивности вибраций поверхностей создающих шум путем повышения жесткости их крепления;
-применение в подшипниках смазок и присадок.
Вместе с тем одним из наиболее эффективных методов снижения шума является использование звукоизоляции. С помощью звукоизолирующих преград легко снизить уровень шума на 30 40 дБ. Метод основан на отражении звуковой волны падающей на ограждение поскольку большая часть падающей на ограждение звуковой энергии отражается и лишь ее небольшая доля (около 1100 и менее) проникает через ограждение (рисунок 4.4). Т.о. можно сказать что звуковая энергия проникает за преграду только за счет колебаний самой преграды. Следовательно чем тяжелее массивнее преграда тем труднее привести ее в состояние колебаний и тем она эффективнее изолирует от проникновения звука. Поскольку сопротивление преграды определяется ее инертностью то звуковые колебания высокой частоты изолируются лучше чем колебания низкой частоты поэтому необходимо учитывать характер шума источника. [15]
В дипломном проекте предлагается оградить все имеющиеся в цеху электродвигатели защитными кожухами в этом случае уровень шума в цеху можно рассчитать по формуле (4.4):
где дБ - уровень звукового давления в помещении;
- площадь перегородки м2;
- расстояние от источника шума м;
- постоянная помещения.
- коэффициент звукопоглощения для однородной перегородки где
- масса 1 м2 ограждения кг;
- частота звуковых колебаний Гц;
Расчет проводим для наиболее опасной частоты 8000Гц.
Таким образом в результате установки звукоизоляционных кожухов уровень шума на участке снижается до 88 дБ и спроектированный участок полностью отвечает санитарным нормам по уровню шума. Поскольку наибольший эффект в борьбе с шумом достигается при комплексных мерах защиты то рекомендуется по возможности использовать все доступные меры для снижения шума в помещении.
Рис. 4.1 - Схема отражения звуковой волны от преграды
Несмотря на соответствие уровня шума после проведенных мероприятий допустимым нормам целесообразно покрывать стены здания пористой штукатуркой у которой коэффициент звукопоглощения находится в пределах 0.20.8.
При таком коэффициенте степень поглощения шума будет определятся по формуле (4.5):
где: - коэффициенты звукопоглощения до и после обработки.
В данном случае применение этого метода не вызвано необходимостью однако дополнительное снижение уровня шума не является лишнем.
Целесообразно также применение средств индивидуальной защиты органов слуха работающих. Средства индивидуальной защиты органов слуха работающих установлены ГОСТ 12.4.011–75. Это противошумовые шлемы наушники заглушки вкладыши. Они эффективно защищают организм от раздражающего действия шума предупреждая возникновение различных функциональных нарушений и расстройств если правильно подобраны и систематически используются. Однако они должны использоваться только в качестве дополнительных средств защиты.
Вкладыши – наиболее простое дешевое и удобное защитное средство. Они вставляются в слуховой канал. Вкладыши могут быть жесткими изготовленными в виде конуса из резины пластмассы и мягкими. Мягкие вкладыши изготавливают из хлопчатобумажной ваты и других материалов. Вкладыши не мешают носить головной убор и очки. К недостаткам их надо отнести возможность раздражения слухового канала особенно при повышенной температуре воздуха.
Наушники плотно облегают ушную раковину и удерживаются дугообразной пружиной тесьмой или шлемом. Они удобны имеют небольшую массу активно ослабляют шум особенно высокочастотной части спектра который наиболее неблагоприятно действует на организм.
При высоких уровнях шумов превышающих 120 дБ вкладыши и наушники всех типов не пригодны поскольку шум воздействуя на черепную коробку проникает непосредственно в мозг. Объясняется это тем что шум такого уровня вызывает вибрацию костей черепа которая воздействует на слуховые нервы и оказывает влияние на мозг. В этих случаях используют шлемофон герметично закрывающий всю околоушную область.
Средства индивидуальной защиты позволяют снизить уровень воспринимаемого звука на 10 - 45 дБ причем наиболее значительное глушение шума наблюдается в области высоких частот которые наиболее опасны для человека. [15]
Рассмотрены основные вредные и опасные факторы возникающие в листоштамповочных цехах. Такими факторами являются: производственный шум и вибрация; опасность поражения электрическим током; загрязнения техническими жидкостями; опасность возникновения пожара; недостаточная освещенность; возможность травматизма; неблагоприятный климат.
Наиболее распространенным вредным фактором прессовых цехов является шум. На сегодняшний день ни один из существующих в стране прессов не соответствует нормативам по уровню шума поэтому в первую очередь следует направлять усилия на борьбу с шумом. В нашем случае это подтверждается проведенным расчетом.
1 Очистка промышленных выбросов в атмосферу от пыли туманов газов
Основное направление работ по удалению загрязнений предполагает создание местных отсосов в зоне их образования что позволяет более эффективно очищать воздух при меньших энергозатратах. Удаляемый от источников загрязнения воздух обычно проходит двухступенчатую очистку в сухих и мокрых пылегазоочистителях.
Из аппаратов сухой инерционной очистки воздуха и газов от пыли наибольшее распространение получили циклоны. Этому способствовала простота конструкции несложность изготовления простота обслуживания компактность установки и надежность работы.
Общим принципом циклонной очистки газов и воздуха от пыли является вращательное или вихреобразное движение двухфазного потока в аппарате круглого сечения благодаря чему центробежная сила отбрасывает более тяжелые частицы пыли к стенкам аппарата а более легкая газовая фракция удаляется через нейтральное газоотводное отверстие.
В поисках наиболее рациональной конструкции была создана большая группа различных типов циклонов - более 20 разновидностей все они основаны на одном и том же принципе.
Циклоны могут применяться как в одиночном так и в групповом исполнении при этом они компонуются в два ряда или вкруговую в количествах 2 4 6 8 10 12 и т.п. штук.
Эффективность работы циклонов колеблется в широких пределах от 33 до 98%. Это объясняется тем что циклон эффективно работает только при расчетных скоростях воздуха или газа а при пониженных - эффективность резко снижается. Учитывая это в последние годы стали применять двухступенчатую очистку газов. Грубая очистка в циклоне а в качестве второй ступени используют мокрые аппараты с воздухоочистительными каналами и внутренней циркуляцией воды - "ротоклоны" или "омикроны" которые обеспечивают высокую степень очистки. Однако эти аппараты очень чувствительны к изменениям воздушной нагрузки и требуют тщательного изготовления и установки импеллера строго по уровню.
Учитывая эти особенности работы ротоклонов в последние года все большее распространение находят гидродинамические аппараты с упрощенной формой воздухоочистительного канала типа ПВМ и ГШ-2М. Эти аппарата хорошо зарекомендовали себя поэтому их следует использовать для очистки воздуха.
Второй тип ротоклонов - барбатажно-вихревой пылеуловитель типа БВПК который по сравнению с другими аппаратами мокрой очистки отличается высокой эффективностью в нем степень улавливания пыли доходит до 98-99% размеры частиц которой крупнее 5-10 мкм незначительным расходом воды и компактностью установки. В этом основные преимущества данного аппарата. В зависимости от конфигурации пылеочистительного канала сопротивление системы может составлять от 500 до 2000 Па. Принцип работы пылеуловителя следующий: запыленный воздух или газ двигаясь вниз огибает импульсары касается жидкости считается от пыли и поворачивается на 180° после чего выбрасывается в атмосферу. При уровне жидкости "0" когда она касается нижней кромки верхнего импульсора начинается режим эжекции жидкости газом диспергация капель жидкости смачивание частиц пыли водой и их улавливание в пылеочистительном канале и в каплеуловителе. При повышении уровня жидкости выше 100 мм сопротивление резко возрастает начинается чистое барботирование газа через жидкость и при подъеме уровня жидкости до 200 мм или даже до 250 мм наблюдается "захлебывание" и запирание аппарата.
Основным недостатком конструкции данного типа аппаратов является то что уровень жидкости в нем должен быть строго выдержан на высоте 75 мм с пределами отклонения 25 мм что трудно выполнимо в условиях производства.
Шлам сливается через задвижку в нижней части его днища в транспортируемую металлическую емкость. Слив производят не реже одного раза в сутки.
Аппаратура применяемая для очистки газов нагретых до высоких температур имеет определенные особенности.
Для осаждения наиболее крупных частиц пыли (более 40 мкм) обычно применяют сухие или мокрые инерционные пылеосадители и скрубберы различных конструкций. Наибольшее распространение нашли циклоны и мультициклоны которые при температурах газов выше 400°С футеруются. В тех цехах где имеется гидрошламоудаление применяются для предварительной очистки газов мокрые пылеотделители.
Особенно плохо очищается пыль имеющая на поверхности частиц пленки органических веществ. Наиболее широко для тонкой очистки пыли используют турбулентные скоростные мокрые пылеуловители тканевые рукавные пылеуловители дезинтеграторы а также сухие и мокрые электрофильтры.
Скоростные мокрые пылеуловители с трубами Вентури имеющие к.п.д. 97-98% и остаточную концентрацию пыли П = 01-006 Гм3 состоят из коагулятора мелких частиц пыли каплеосадителя и газодувки (дымососа). Вода подается в горловину трубы Вентури. Газовый поток движущийся со скоростью 80-200 мс дробит воду на мелкие капли обеспечивает хорошее перемешивание газов с каплями воды и осаждение на каплях мельчайших частиц пыли. Пыль скоагулировавшаяся на каплях воды улавливается в каплеосадителях инерционного типа (циклоны скрубберы и т.п.). Высокая степень очистки достигается при скорости газового потока в горловине равной 150-200 мс; при этом гидравлическое сопротивление пылеуловителя преодолеваемое за счет газодувки составляет 1500 - 2000 мм рт.ст).
Преимущества этих пылеуловителей: простота эксплуатации небольшие габаритные размеры низкая стоимость сооружения. Недостатки: большие затраты электроэнергии польщенная трудоемкость и малая надежность работы газодувки опасность образования хлопков и взрывов в системе газоочистки из-за подсоса воздуха.
Мокрые пылеуловители с эжекторными трубами Вентури имевшие к.п.д. 80%~97% и Пост. = 015-010 Гм3 состоят из коагулятора мелких частиц пыли каплеосадителя и водных насосов высокого давления. Газы проходят через горловину трубы Вентури с невысокой скоростью (10-15 мс) в направлении перемещения газов. Подаются вода с большой скоростью (40-150 мс). За счет разности скоростей воды и газов обеспечивается коагуляция пыли на каплях воды и эжекция газового потока. Преимущества этого пылеуловителя: высокая надежность простота эксплуатации отсутствие разряжения в системе газоочистки. Недостатки: ограниченные возможности из-за преодоления значительного гидравлического сопротивления устройств обеспечивающих дожигание и утилизацию тепла газов.
Тканиевые фильтры имеющие к.п.д. = 99% и П ост.= 005-007 Гм3
состоят из пучка матерчатых труб или мешков размещенных в герметичном металлическом каркасе имеющем в нижней части бункер для сбора пыли. Запыленные газы через бункерную часть каркаса проходят внутрь труб или мешков фильтруются через ткань и выходят из фильтра через клапан чистого газа. Ткань очищается от пыли за счет периодического встряхивания или обратной продувки воздухом. При температурах газов 100-300% применятют синтетические волокна или стекло-ткань. Преимущества тканиевых фильтров: высокая степень очистки низкий расход электроэнергии низкое гидравлическое сопротивление. Недостатки: большие капитальные затраты и габариты; температура очищаемых газов ограничена 70-300°С
Дезинтеграторы имеющие к.п.д. = 85-98% и П ост. = 05-005 Гм3 состоят из улиткообразного корпуса ротора с разбрызгивателем и лопатками шламоотстойника и каплеосадителя. Газы подаются в центральную часть корпуса за счет вращения ротора с лопатками и неподвижных прутьев укрепленных в корпусе перемешиваются с водой подаваемой через разбрызгиватель. Центробежной силой капли воды насыщенные пылью отбрасываются на стенки корпуса и по ним стекают в шламоотстойник. Окончательное осаждение пыли производится в каплеотстойнике инерционного типа. Преимущества этих пылеуловителей: небольшие габаритные размеры совмещение в одном аппарате коагулятора пыли и дымососа возможность регулирования степени очистки за счет изменения мощности двигателя. Недостатки: сложность и высокая точность изготовления и ремонта высокое разряжение создаваемое в системе газоочистки и связанная с этим опасность подсоса воздуха вызывающего хлопки и взрывы.
Электрофильтры имеющие к.п.д. = 99% и П. ост. = 003-005 Гм3 представляют собой каналы стенки которых соединены с положительным полюсом высокого напряжения. Внутри каналов располагаются электроды соединенные с отрицательным полюсом. Частицы пыли проходя по каналам ионизируются приобретают электрический заряд и под его влиянием оседают на электродах. Для очистки газов применяют как сухие так и мокрые электрофильтры. Преимущества электрофильтров: очень высокая степень очистки низкий расход электроэнергии и низкое гидравлическое сопротивление. Недостатки: большие габариты и высокая Стоимость сооружения опасность возникновения хлопков и взрывов при очистке газов содержащих окись углерода. [13]
Циклоны – устройства для отделения твердых частиц от газа; центробежные пылеуловители конструктивные элементы которых обеспечивают вращательно - поступательное движение газового потока.
Принципиально циклоны работает по следующей схеме (рисунок 5.1). Обеспыливаемый газ поступает в образующую кольцевое пространство аппарата цилиндрическая часть где движется по спирали с возрастающей скоростью от периферии к центру спускается по наружной спирали затем поднимается по внутренней спирали и выходит через выхлопную трубу. Под действием центробежной силы частицы пыли отбрасываются к стенке циклоны и вместе с частью газа попадают в бункер. Часть освободившегося от пыли газа возвращается из бункера в циклоны через центр пылеотводящего отверстия давая начало внутреннему вихрю.
Отделение частиц от попавшего в бункер газа происходит при перемене направления их движения на 180° под действием сил инерции. По мере движения данной части газа в сторону выхлопной трубы к ним присоединяются порции газа не попавшего в бункер. Это не вызывает существ. увеличения выноса пыли в трубу т. к. распределенное на довольно большом отрезке длины циклоны перетекание газа происходит со скоростью недостаточной для противодействия движению частиц к периферии аппарата. Значительно большее влияние на полноту пылеулавливания оказывает движение газа в области пылеотводящего отверстия периферии аппарата.
4 - входной и отводящий патрубки; 2 - корпус; 3 - пылевой бункер.
Рисунок 5.1- Схема течения газовых потоков в циклоне
Значительно большее влияние на полноту пылеулавливания оказывает движение газа в области пылеотводящего отверстия. Поэтому частицы чрезвычайно чувствительны к подсосам газа через бункер из-за увеличения объема потока движущегося навстречу улавливаемой пыли. Отсюда видна важная роль бункера при осаждении частиц пыли в циклоны; использование таких аппаратов без бункеров или с бункерами уменьшенных размеров приводит к снижению эффективности пылеулавливания.
Конструкции циклоны весьма разнообразны. На рисунке 5.2 представлены основные виды циклонных пылеуловителей циклоны различаются по способу подвода газа который может быть спиральным (рисунок 5.2а) тангенциальным или обычным (рисунок 5.2б) винтообразным (рисунок 5.2в) и осевым; циклоны с осевым (розеточным) подводом газа работает как с возвратом газа вверх в часть аппарата (рисунок 5.2г) так и без него (рисунок 5.2д). Аппараты последнего типа отличаются низким гидравлическим сопротивлением и меньшей по сравнению с циклонами иных типов эффективностью пылеулавливания. Простота конструкции прямоточных циклоны облегчает нанесение на них футеровки что позволяет применять эти аппараты для осаждения крупных абразивных частиц пыли.
а - спиральный; б - тангенциальный; в -винтообразный; г - розеточный с возвратом газа; д - розеточный прямоточный.
Рисунок 5.2 - Основные виды циклонов
Групповые циклоны при больших расходах очищаемого газа применяют групповую компоновку аппаратов. Это позволяет не увеличивать диаметр циклонов и повышать эффективность пылеулавливания. Группа циклонов составленная обычно из цилиндрических аппаратов имеет общие коллектор загрязненного газа сборник очищенного газа и пылевой бункер. Отвод обеспыленного газа от циклонной группы осуществляют либо через специальные устройства (улитки) устанавливаемые на каждом аппарате и объединяемые общим коллектором либо непосредственно через него. Использование улиток уменьшает общую высоту группы. При равной производительности цилиндрические и конические аппараты отличаются большими габаритами и поэтому в групповом исполнении не применяются.
Батарейные циклоны (рисунок 5.3). Из выражения следует что эффективность очистки газа в циклонах можно повысить путем увеличения скорости газа или уменьшения диаметра аппарата. Однако возрастание скорости связано со значительным увеличением гидравлического сопротивления. Поэтому для повышения эффективности работы циклонов желательны уменьшение их диаметра и замена одного аппарата несколькими малого диаметра. Такой принцип положен в основу устройства батарейного циклона (рис. 5.3а). Последний состоит из многих (несколько десятков) параллельно работающих элементов (рис. 5.3б) - циклоны небольшого диаметра смонтированных в общем корпусе. Поступая в него запыленный газ входит в газораспределительную камеру ограниченную трубными решетками в которыхр герметично укреплены циклонные элементы. Обеспыленный газ удаляется через выхлопные трубы элементов в общую камеру а пыль собирается в коническое днище (пылесборнике).
Однако эффективность очистки в батарейном циклоне как правило на 20-25% меньше той которая может быть достигнута в эквивалентном по диаметру обычном циклоне. Это объясняется перетоком газа из элементов с большим гидравлическим сопротивлением в элементы с меньшим сопротивлением.
Поэтому а также из-за возможности образования отложений циклонные элементы должны иметь диаметр не менее 03 м. Каждый элемент отличается от обычного циклона преимущественно способом ввода запыленного газа который поступает в элемент не по касательной а сверху через кольцевое пространство между корпусом и выхлопной трубой. В этом пространстве на входе газа в каждый элемент установлен направляющий аппарат (винт или розетка с наклонными лопатками) сообщающий потоку газа вращательное движение. В отличие от обычных батарейные циклоны сложнее в изготовлении но имеют значительно меньшие габариты.
Благодаря невысокой стоимости простоте устройства и обслуживания сравнительно небольшому гидравлическому сопротивлению и высокой производительности циклоны являются наиболее распространенным типом сухих мехеханических пылеуловителей. [13]
- корпус; 2 4 - камеры газораспределительные и для обеспыленного газа; 3 - циклонные элементы; 5 - пылесборник.
Рисунок 5.3 - Батарейный циклон (а) и его элемент (б)
Конечно же понятие «безотходное производство» имеет несколько условный характер; это идеальная модель производства так как в реальных условиях нельзя полностью ликвидировать отходы и избавиться от влияния производства на окружающую среду. Точнее следует называть такие системы малоотходными дающими минимальные выбросы при которых ущерб природным экосистемам будет минимален.
В настоящее время определилось несколько основных направлений охраны биосферы которые в конечном счете ведут к созданию безотходных технологий:
) разработка и внедрение принципиально новых технологических процессов и систем работающих по замкнутому циклу позволяющих исключить образование основного количества отходов;
) создание бессточных технологических систем и водооборотных циклов на базе наиболее эффективных методов очистки сточных вод;
) переработка отходов производства и потребления в качестве вторичного сырья;
) создание территориально-промышленных комплексов с замкнутой структурой материльных потоков сырья и отходов внутри комплекса.
Разработка и внедрение принципиально новых технологических процессов и систем работающих по замкнутому циклу позволяющих исключить образование основного количества отходов является основным направлением технического прогресса.
Подводя итоги хочется ещё раз подчеркнуть проблемы получившие современное решение в данном дипломном проекте после подробного анализа неблагоприятных факторов которые в силу стечения обстоятельств сложились на АМО «ЗИЛ».
Нерациональность использования оборудования устаревшие технологические подходы к анализу производства а так же беспечно оставленная без внимания проблема экологии и уж совсем на мой взгляд забытая тема безопасности жизни и здоровья должны быть исключены.
В данном дипломе мною были разработаны: рациональный технологический процесс изготовления детали «корпус инструментального ящика» состоящий из автоматизированной линии подачи заготовки – ленты штампа последовательного действия и агрегативной малогабаритной компоновкой данного оборудования на производственной площади. Были учтены нежелательные для здоровья факторы имеющие место в листоштамповочном цехе а в частности подсчитан допустимый уровень шума рассмотрены методы борьбы с ним как в коллективном так и в индивидуальном исполнении. Так же приведен обзор аппаратов для качественной очистки от пыли и других загрязняющих воздух веществ широко распространенных на рынках и уже не раз примененных на отечественных и зарубежных производствах.
Список используемых источников
Катков В.Ф. Оборудование и средства автоматизации и механизации штамповочных цехов: учеб. пособие – М.: Машиностроение 1985. – 384 с. ил.
Романовский В.П. Справочник по холодной штамповке: учеб. пособие – М. Машиностроение 1971. – 782 с.
Корсаков В.Д. Справочник мастера по штампам: учеб. пособие – М.: Машиностроение 1972. – 192 с. ил.
Норицын И.А. Власов В.И. Автоматизация и механизация технологических процессов ковки и штамповки: учеб. пособие – М.: Машиностроение 1967. – 388 с. ил.
Пейсахов А.М. Кучер А.М. Материаловедение и технология конструкционных материалов: 3-е изд. учеб. пособие – СПБ.: Михайлова В.А. 2005. – 416 с.
Банкетов А.Н. Бочаров Ю.А. Добринский Н.С. Ланской Е.Н Трофимов И.Д. Кузнечно-штамповочное оборудование: 2-е изд. перераб. и доп. – М.: Машиностроение 1982. – 576 с. ил.
Скворцов Г.Д. Основы конструирования штампов для холодной листовой штамповки: подготовительные работы: 2-е изд. перераб. и доп. – М.: Машиностроение 1970. – 318с. ил.
Оськин Ю.Ф. Буйлова З.Ф. Методические указания к выполнению курсовой работы по дисциплине «Организация производства» для студентов специальности 1204 «Машины и обработка металлов давлением»: М.: МГТУ «МАМИ» 1997. – 40 с.
Норицын И.А. Шехтер В.Я. Проектирование кузнечных и холодноштамповочных цехов и заводов: учеб. пособие – М.: Высшая школа 1977. – 379 с. ил.
Барон Н.М. Квят Э.И. Подгорная Е. А. Пономарёва А.М. Равдель А А. Тимофеева З.Н. Краткий справочник химико-физических величин: 4-ое изд. перераб. и доп. – М.: Химия 1965. – 159 с.
Шатерина М.А. Технология конструкционных материалов: учеб. пособие для вузов – СПБ.: Политехника 2005. – 597 с. ил.
Дыбаль С.В. Финансовый анализ: теория и практика: Учеб. пособие – СПБ.: «Бизнес-пресса» 2004. – 304 с.
Русанова А.А. Очистка промышленных газов от пыли: 2-ое изд. – М.: Высшая школа 1981. – 376 с.
Мошнин Е.Н. Технология штамповки крупногабаритных деталей: учеб. пособие – М.: Машиностроение 1973. – 240 с.
Резчиков Е.А. Носов В.Б. Пышкина Э.П. Щербак Е.Г. Безопастность жизнедеятельности: учеб. пособие – М.: МГИУ 1998. – 374с.
Айрбабамян С.А. Графкина М.В. Иванов К.С. Методические указания к лаб. раб. №2 «Измерение шума на рабочих местах» - М.: МГТУ «МАМИ» 2006.
12 Экономика.dwg

+ экономия - перерасход
- на производственную площадь
Текущий ремонт и содержание производственной площади
Текущий ремонт и обслудивание оборудования
- на технол. энергию
- на cоц. страхование
- на заработную плату
Амортизационные отчисления:
Капитальные вложения
- на силовую энергию
Себестоимость одного
Годовой экономический эффект составил: 4808400 рублей.
Технико-экономические показатели проектного технологического процесса
Автоматизированный участок прессового цеха по производству детали "корпус инструментального ящика" автомобиля ЗИЛ
Кафедра КиОД Группа 10-МАК-2
05 план верха.dwg
Автоматизированный участок прессового цеха по производству детали "корпус инструментального ящика" автомобиля ЗИЛ
Кафедра КиОД Группа 10-МАК-2
01 Вид детали.dwg

Корпус инструментального ящика
Автоматизированный участок прессового цеха по производству детали "корпус инструментального ящика" автомобиля ЗИЛ
Кафедра КиОД Группа 10-МАК-2
03 Технологии.dwg

Окончательная завивка
Комбинированная штамповка
формование ребер жесткости
Существующая технология
Предлагаемая технология
Переходы штамповок в старом и новом технологическом процессе
Автоматизированный участок прессового цеха по производству детали "корпус инструментального ящика" автомобиля ЗИЛ
Кафедра КиОД Группа 10-МАК-2
04 План низа.dwg
Окончательная завивка
Комбинированная штамповка
формование ребер жесткости
Существующая технология
Предлагаемая технология
технологическом процессе
с разработкой технологии
Корпус инструментального ящика
Участок цеха листовой штамповки
средних деталей автомобиля ЗиЛ
Изм.Лист N докум. Дата
Штамп последовательного действия План низа
Автоматизированный участок прессового цеха по производству детали "корпус инструментального ящика" автомобиля ЗИЛ
Кафедра КиОД Группа 10-МАК-2
09 Циклограмма.dwg

Автоматизированный участок прессового цеха по производству детали "корпус инструментального ящика" автомобиля ЗИЛ
Кафедра КиОД Группа 10-МАК-2
11 поперечный разрез цеха.dwg
Автоматизированный участок прессового цеха по производству детали "корпус инструментального ящика" автомобиля ЗИЛ
Кафедра КиОД Группа 10-МАК-2
07 продольный разрез.dwg
Автоматизированный участок прессового цеха по производству детали "корпус инструментального ящика" автомобиля ЗИЛ
Кафедра КиОД Группа 10-МАК-2
06 рахрезы.dwg
Кафедра КиОД Группа 10-МАК-2
Разрезы Штампа последовательного действия
10 Циклограмма автоматизации.dwg

Механизм подъема валков
Подъем верхнего валка
Угол поворота главного вала
I- ход рейки II - ход ползуна
Циклограмма работы кривошипного пресса с валковой подачей в совмещенном цикле
Автоматизированный участок прессового цеха по производству детали "корпус инструментального ящика" автомобиля ЗИЛ
Кафедра КиОД Группа 10-МАК-2
08 Автоматизация.dwg

Автоматизированная линия штамповки
Автоматизированный участок прессового цеха по производству детали "корпус инструментального ящика" автомобиля ЗИЛ
Кафедра КиОД Группа 10-МАК-2
Рекомендуемые чертежи
- 24.01.2023
- 27.11.2021