АСУТП электротермической линии ЭЛТА 8/45



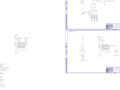
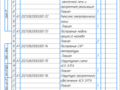
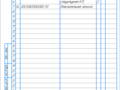
- Добавлен: 24.01.2023
- Размер: 4 MB
- Закачек: 0
Описание
АСУТП электротермической линии ЭЛТА 8/45
Состав проекта
![]() |
![]() |
![]() |
![]() |
![]() ![]() ![]() ![]() |
![]() |
![]() |
![]() ![]() ![]() |
![]() |
![]() |
![]() ![]() ![]() ![]() |
![]() |
![]() ![]() |
![]() |
![]() |
![]() |
![]() ![]() ![]() |
![]() ![]() ![]() ![]() |
Дополнительная информация
Ведомость OSS1.cdw

электротермической линии
Схема электрическая
Пояснительная записка
Готовый диплом.doc
2.1 Назначение системы ..
2.2 Цели создания системы .
3 Характеристики объекта автоматизации
3.1 Общие сведения об объекте автоматизации
3.2 Сведения об условиях эксплуатации
4 Требования к системе
4.1 Требования к структуре и функционированию системы ..
4.2 Требования к функциям системы ..
4.3 Требования к видам обеспечения ..
Техническое предложение
1 Выбор методов управления .
2 Выбор технического обеспечения ..
3 Выбор программного обеспечения и структуры программного обеспечения проекта
4 Разработка структурных схем КТС
5 Визуализация технологического процесса
Разработка математической модели синтез и программная реализация алгоритмов работы закалочной печи
1 Исследование тепловых процессов в закалочной печи .
1.1 Построение модели нагрева закалочной печи .
1.2 Модель нагревателя закалочной печи ..
1.3 Построение САР температуры для зоны нагрева ..
1.4 Определение коэффициентов передаточных функций модели нагрева закалочной печи и модели нагревателя .
1.5 Определение передаточной функции датчика температуры ..
1.6 Передаточная функция преобразователя ..
2 Программирование алгоритмов работы устройств ЭЛТА 845
Технико-экономическое обоснование внедрения АСУ ЭЛТА
1 Исходные данные для расчета .
2 Расчет экономической эффективности
2.1 Расчет временных затрат на разработку системы
2.2 Расчет затрат на разработку и ввод в эксплуатацию системы
2.3 Расчет затрат на внедрение системы .
2.4 Расчет ожидаемой экономии по основным технико-экономическим показателям
2.5 Расчет ожидаемого годового экономического эффекта .
2.6 Расчет коэффициента экономической эффективности и срока окупаемости системы .. ..
Безопасность труда в термическом цехе
1 Опасные факторы возникающие в процессе термической обработки
2 Обеспечение безопасной работы в условиях термического цеха
3 Методы расчета местной вентиляции в термическом цехе ..
4 Расчет вентиляции цеха
Приложение А Справка об анализе патентной литературы
Приложение Б Технические характеристики частотных преобразователей
В данной работе разработана система автоматического управления электротермической линии ЭЛТА 845 и проанализированы процессы нагрева протекающие в электрических печах. Внедрение данное системы позволит повысить качество продукции обрабатываемой на электротермической линии облегчит эксплуатацию электротермической линии.
Целью данной работы является анализ процесса нагрева как процесса управления моделирование процесса нагрева на ЭВМ. Построение системы автоматического поддержания постоянства температур в печах. Синтез алгоритмов управления устройствами электротермической линии. Программная реализация алгоритмов работы устройств входящих в состав ЭЛТА 845.
В конце прошлого века на российском рынке в огромных количествах появились автомобили произведенные за рубежом во многом превосходящие производимые в России. Для успешной конкурентной борьбы отечественной автопромышленности требовалось повышать качество автомобилей произве-денных внутри страны и прежде всего увеличить надежность двигателей. Соответственно выросли требования к конструктивным элементам двигателя.
В связи с повышением технических требований качеству металлических деталей производимых для автомобильной промышленности увеличился процент изделий не удовлетворяющих данным требования и следовательно относимым к браку. В технологическом процессе их изготовления можно отметить что наибольшее количество брака появляется на завершающей стадии технологической операции а именно в процессе закалки. Чтобы определить причины порождающие данное явление для этого необходимо рассмотреть технологический процесс. Процесс закалки состоит из следующих стадий: закалка мойка и сушка отпуск. Для того чтобы обеспечить высокое качество продукции требуется тщательное соблюдение технологического процесса. Время и температура нагрева должны выдерживаться с точностью до долей процента также требуется тщательно отслеживать состояние технических средств на которых производиться термическая обработка. Однако большинство применяемых сегодня систем не способны обеспечивать заданную точность. Кроме того качество обрабатываемой продукции зависит от человеческого фактора. Оператор контролирующий выполнение технологического процесса не может отслеживать все множество параметров от которых зависит процесс ввиду того что занимаясь длительной и монотонной работой быстро становится невнимательным.
Другая проблема быстрое устранение неисправностей возникающих в процессе работы технических средств и длительная переналадка оборудования при необходимости внести изменения в процесс.
Тем не менее на сегодняшний день уже созданы технический средства при помощи которых возможно решить указанные проблемы.
Применение АСУ (Автоматизированной Системы Управления) может
обеспечить нормальный ход непрерывно протекающих процессов в системе управления процессом термообработки освободит оператора от непосредственного выполнения функций управления процессом за счет передачи этих функций автоматическим устройствам. Сегодня системы автоматизации строятся преимущественно на базе промышленных контроллеров. Это обусловлено их высокой надежностью и возможностью организовать систему визуализации техпроцесса что в свою очередь позволяет тщательно контролировать процесс быстро обнаруживать и устранять неисправности возникающие в процессе работы. Таким образом внедрив систему автоматизации на основе программируемого логического контроллера можно решить задачу поддержания постоянства параметров техпроцесса снизить роль человеческого фактора в процессе термообработки сократить время требуемое для устранения неисправностей возникающих в процессе работы системы.
1.1 Полное наименование системы управления
Автоматизированная система управления электротермической линией ЭЛТА 845 (Далее АСУ ЭЛТА).
2 Назначение и цели создания системы
2.1 Назначение системы
Назначением автоматизированной системы управления электротермической линией ЭЛТА 845 является:
–обеспечение контроля состояния оборудования;
–автоматическое управление и защита технологического оборудования в процессе его работы;
–автоматическое поддержание стабильности заданных значений следующих параметров:
время нахождения деталей в закалочной печи (ЗП);
время нахождения деталей в отпускной печи (ОП);
температура в закалочной печи по зонам;
температура в отпускной печи по зонам;
температура масла в закалочном баке;
температуры моющего раствора в моечной машине;
температуры обезжиривающего раствора в моечной машине;
температуры в зоне сушки моечной машины;
уровня масла в закалочном баке;
уровня обезжиривающего раствора в моечной машине;
уровня моющего раствора в моечной машине;
веса порций загружаемых деталей;
–контроль параметров технологического процесса (ТП);
–визуализация ТП на автоматизированном рабочем месте (АРМ) оператора;
–светозвуковая сигнализация и выдача сообщений об аварийных ситуациях на АРМ оператора;
2.2 Цели создания системы
Целями создания АСУ ЭЛТА является:
–автоматизация управления технологическими процессами отделения термообработки;
–повышение надежности работы оборудования;
–повышение качества продукции;
–автоматизация сбора и хранения информации о работе линии термообработки;
–снижение влияния ошибок эксплуатационного персонала на процесс работы линии и качество продукции;
3 Характеристика объекта автоматизации
3.1 Общие сведения об объекте автоматизации
Объектом автоматизации является электротермическая линия ЭЛТА 845 предназначенная для термической обработки металлических крепежных изделий.
– устройство дозированной загрузки (загрузочное устройство);
– электропечь сопротивления закалочная;
– бак масляный закалочный;
–машина моечная конвейерная;
–электропечь сопротивления отпускная;
Загрузочное устройство подает детали дозированными порциями из металлического контейнера на конвейер закалочной печи через загрузочный шлюз. В закалочной печи должны поддерживаться заданная технологической программой температура в каждой из трех зон нагрева а также скорость движения конвейера. Детали перемещаются конвейером через закалочную печь (в закалочной печи производится нагрев изделий до температуры аустенизации и выдержка изделий в печи в течении заданного времени) и подаются сквозь масляную завесу в закалочный бак где происходит процесс закаливания и охлаждения. Масляная завеса создается для предотвращения попадания газов образующихся при закалке деталей в атмосферу закалочной печи.
Далее конвейером закалочного бака детали перемещаются в моечную машину где подвергаются обезжириванию мойке и сушке. В моечной машине контролируется и поддерживается постоянство температуры обезжиривающего и промывочного растворов температуры воздушного потока для сушки изделий создаваемого калорифером. Затем изделия загрузочным устройством подаются на конвейер отпускной печи. В отпускной печи необходимо поддерживать постоянную температуру в каждой из трех зон нагрева в соответствии с выбранной технологической программой. Из отпускной печи изделия подаются в бак охлаждения. Охлажденные детали выгружаются конвейером в тару готовой продукции для дальнейшей транспортировки.
Технические средства расположенные в помещении цеха и операторной должны иметь эксплуатационные характеристики соответствующие следующим условиям:
–температура +15÷45ºС;
–относительная влажность не более 90%;
–атмосферное давление 084÷107 кгссм2;
–содержание пыли до 1 мгм3;
–режим эксплуатации – круглосуточный.
4.1 Требования к структуре и функционированию системы
4.1.1 Структура системы
В соответствии с назначением в АСУ ЭЛТА должны входить следующие подсистемы:
I.Подсистема управления линией термообработки;
II.Подсистема управления загрузкой;
III.Подсистема управления закалочной печью;
IV.Подсистема управления закалочным баком;
V.Подсистема управления моечной машиной;
VI.Подсистема управления отпускной печью;
VII.Подсистема управления баком охлаждения;
VIII.Подсистема отображения технологических процессов (АРМ оператора).
Подсистемы II - VII предназначены для преобразования сигналов от подсистемы управления линией термообработки в непосредственное воздействие на исполнительные механизмы и выдачи в подсистему управления линией термообработки информации о состоянии оборудования.
Подсистема управления линией термообработки должна включать в себя:
–программируемый логический контроллер (ПЛК) с модулями ввода-вывода и коммуникационными модулями управляющий остальными подсистемами в соответствии с загруженной в него программой;
–средства гальванической развязки цепей контроллера от силовых цепей;
–источник бесперебойного питания;
–автоматические выключатели;
–промежуточные реле;
–- источники питания 24VDC и т.д.
Подсистемы управления закалочной и отпускной печами должны включать в себя:
–вторичные преобразователи датчиков технологических параметров относящихся к печам;
–астотные преобразователи (ЧП) управления двигателями конвейеров печей;
–блоки управления силовыми ключами нагревателей;
–коммутационную и защитную аппаратуру всех электрических исполнительных механизмов относящихся к данным печам.
Подсистемы управления загрузкой управления закалочным баком управления моечной машины охлаждающим баком должны включать в себя:
–вторичные преобразователи датчиков технологических параметров
установленных иили относящихся к этим подсистемам;
–частотные преобразователи управления двигателями конвейеров;
–блоки управления силовыми ключами вибропитателей и нагревателей;
–коммутационную и защитную аппаратуру всех агрегатов и
исполнительных механизмов относящихся к данным подсистемам.
Подсистема отображения технологических процессов должна включать в себя автоматизированное рабочее место (АРМ) оператора состоящее из панельного компьютера с установленным на него программным обеспечением выполняющим функции HMI (human-machine interface – человеко-машинный интерфейс).
Структура АСУ ЭЛТА представлена на рисунке 1.
Рисунок 1- Структура АСУ ЭЛТА
4.1.2 Требования к способам и средствам связи для информационного обмена между компонентами системы
Информационный обмен между частотными преобразователями (ЧП) и ПЛК необходимо осуществлять по шине ProfiBus.
Для выдачи аварийных сигналов на останов приводов и получения сигналов состояния привода необходимо использовать дискретные цифровые входывыходы ЧП.
Информационный обмен между ПЛК и АРМ оператора должен осуществляться по промышленной сети на основе протоколов семейства Simatic S7 PROTOCOL SUITE.
4.1.3 Требования к режимам функционирования системы
АСУ ТП электротермической линии должна функционировать в непрерывном круглосуточном режиме. Должно быть обеспечено управление линией и отдельными агрегатами в следующих режимах:
Режим работы «Автоматический»: электротермическая линия должна работать автоматически по заданной программе поддерживаться заданные температурные режимы скорости конвейеров производиться автоматическая загрузка деталей.
Режим работы «Наладочный» предназначен для проверки работоспособ-ности настройки и регулировки исполнительных механизмов. В режиме работы «Наладочный» необходимо предусмотреть возможность включения и выключения отдельных элементов (электродвигателей нагревателей насосов вентиляторов и пр.) по командам оператора.
Режим работы «Дежурный» предназначен для поддержания электротерми-ческой линии при минимально допустимой температуре в печах с целью экономии энергозатрат при длительном отсутствии полезной загрузки. В данный режим линия может быть переведена оператором. Параметры режима могут быть заданы (изменены) технологом.
Режим работы «Сушка» предназначен для подготовки печей к работе по заданным режимам нагрева после ремонта или длительного простоя с выключением нагревателей. В данный режим работы линия может быть переведена оператором. Параметры режима могут быть заданы (изменены) технологом.
4.1.4 Требования по диагностированию системы
Система должна обеспечивать бесперебойное функционирование с высокой степенью надежности. В случае сбоя или отказа восстановление системы должно обеспечиваться за короткий срок. Для этого система должна обеспечивать следующие возможности:
–оперативную диагностику технических средств (для диагностирования должны использоваться стандартные средства диагностики оборудования подсистем автоматического управления технологическими процессами и передачи данных);
–наличие встроенной диагностики аппаратных средств.
4.1.5 Требования к показателям назначения
АСУ ЭЛТА должна обеспечивать следующие показатели назначения:
–получение информации о состоянии оборудования и параметрах ТП от датчиков системы с интервалом не более 1 с;
–должна обеспечиваться автономная работа подсистемы управления электротермической линией от источника бесперебойного питания в течение не менее 15 минут после отключения питающего напряжения;
– отклонение массы деталей одной порции деталей загружаемой в
закалочную печь от заданной не должно превышать -05÷+2 кг;
–отклонения температур не должны превышать ± 5 ºС от заданных значений;
– отклонение скоростей конвейеров управляемых частотными преобразователями не должны превышать ± 05% от заданного значения;
–период опроса и обновления технологических данных ТП на экране АРМ оператора – не более 3 секунд;
–включение аварийной и предупредительной сигнализации и выдачу текстового сообщения содержащего описание события в случае возникновения аварийной ситуации или о наступлении события о котором необходимо предупредить оператора;
–глубина архива системы должна быть не менее 3-х месяцев.
4.1.6 Показатели надежности
Для системы АСУ ТП должны быть установлены следующие показатели надежности (в соответствии с ГОСТ 27.002-89 и ГОСТ 27.003-90):
–средняя наработка на отказ часов;
4.1.7 Требования к показателям надежности
Система АСУ должна иметь следующие значения показателей надежности:
–средняя наработка на отказ – не менее 10 000 часов;
–срок службы при условии выполнения регламентных работ и замены комплектующих устройств не менее 10 лет.
4.1.8 Требования по безопасности
Технические средства АСУ ЭЛТА должны удовлетворять требованиям ГОСТ 12.1.030-81 «Межотраслевым правилам по охране труда при эксплуатации электроустановок» и «Правилами устройства электроустановок» (ПУЭ-2002). Оборудование АСУ ТП должно быть подключено к отдельному контуру заземления (СНиП 3.05.07-00).
4.1.9 Требования к защите информации от несанкционированного доступа
Для обеспечения нормального функционирования системы предотвращения нарушения информации от случайных воздействий со стороны эксплутационного и обслуживающего персонала не имеющего доступа к отдельным функциям системы должна быть предусмотрена защита информации от несанкционированного доступа. Это должно быть достигнуто идентификацией личности пользователя при помощи пароля.
Должна быть предусмотрена следующая градация по уровню доступа:
–администратор системы (инженер-программист).
4.1.10 Требования к стандартизации и унификации
Система должна отвечать общим принципам стандартизации и унификации:
–открытость и способность к наращиванию;
–модульный принцип построения технических и программных средств;
–использование стандартных протоколов обмена информации;
–возможность наращивания аппаратных и программных средств при изменении количества и масштабов используемых подсистем;
–применение стандартных средств разработки приложений.
Для отображения информации должны быть использованы стандартные символьные обозначения. При этом условные обозначения используемые в системе должны быть приближены к терминам и понятиям применяемым персоналом Заказчика и не должны вызывать трудностей при их восприятии.
При разработке должны быть проанализированы и использованы прогрессивные технические решения аналогичных систем.
4.2 Требования к функциям системы
4.2.1 Требования к функциям подсистемы управления линией термообработки
Подсистема должна выполнять следующие функции:
–сбор значений температуры закалочной среды в электропечах температуры масла в закалочном баке и обезжиривающего раствора в моечной машине;
–сбор значений давления и расхода эндогаза и азота;
–получение сигналов о состоянии загрузочного устройства и сигналов с пульта управления загрузочным устройством;
–выработка сигналов управления клапанами регулирующими подачу газов вентиляторами и электронагревателями в печах;
–выработка сигналов управления приводами конвейеров;
–включение аварийной звуковой и световой сигнализации;
Сигналы контроля и управления должны поступать в ПЛК. Обработку входных сигналов от датчиков и от технологического оборудования выработку управляющих воздействий на оборудование а также защитное отключение оборудования и закрытие регулирующих клапанов необходимо осуществлять в соответствии с описанием технологического процесса.
Значения диапазонов измерения датчиков порогов срабатывания аварийной и предупредительной сигнализации а также перечень аварийных защит и отключений должны быть предоставлены Заказчиком в виде «Карты технологических уставок» до начала пусконаладочных работ. Для организации обмена данными между АРМ оператора и ПЛК должны использоваться стандартные протоколы семейства Simatic S7 PROTOCOL SUITE.
4.2.2 Требования к функциям подсистемы управления загрузкой
Подсистема управления устройством загрузки должна выполнять следующие функции:
–обеспечивать исполнение сигналов управления от подсистемы управления линией термообработки;
–формировать сигналы для ПЛК о состоянии оборудования;
–дозировать загрузку деталей в закалочную печь.
4.2.3 Требования к функциям подсистемы управления закалочной печью
Подсистема управления закалочной печью должна выполнять следующие функции:
–обеспечивать получение и исполнение сигналов управления от подсистемы управления линией термообработки;
–формировать сигналы о состоянии оборудования;
–поддерживать заданные температуры в закалочной печи по зонам нагрева;
–поддерживать заданную скорость конвейера;
–поддерживать равномерность температуры между зонами.
4.2.4 Требования к функциям подсистемы управления закалочным баком
Подсистема управления закалочным баком должна выполнять следующие функции:
–поддерживать заданную температуру масла;
–поддерживать уровень масла;
–поддерживать заданную скорость конвейера.
4.2.5 Требования к функциям подсистемы управления моечной машиной
Подсистема управления моечной машиной должна выполнять следующие функции:
–формировать сигналы о состоянии оборудования;
–поддерживать заданные температуры обезжиривающего и моющего растворов воздушного потока сушки;
–поддерживать уровень моющего и обезжиривающего растворов;
4.2.6 Требования к функциям подсистемы управления отпускной печью
Подсистема управления отпускной печью должна выполнять следующие функции:
–поддерживать равномерность температур между зонами.
4.2.7 Требования к функциям подсистемы управления баком охлаждения
Подсистема управления баком охлаждения должна выполнять следующие функции:
–поддерживать заданную температуру раствора;
–поддерживать уровень раствора;
–поддерживать заданную скорость конвейера.
4.2.8Требования к функциям подсистемы отображения технологических процессов
АРМ оператора должна выполнять следующие функции:
–обеспечивать оконный интерфейс управления;
–обеспечивать выбор режима работы при помощи меню;
– обеспечивать ввод технологических процессов для различных деталей;
–обеспечивать выбор технологических процессов и типа обрабатываемых деталей из сформированной библиотеки;
– квитирования оператором предаварийных и аварийных сообщений.
4.3 Требования к видам обеспечения
4.3.1 Требования к математическому обеспечению
Математическое обеспечение системы должно обеспечивать реализацию функций системы и содержать алгоритмы разработанные на основе описания технологического процесса.
Должны быть разработаны следующие алгоритмы:
–алгоритмы управления работой загрузочного устройства;
–алгоритмы управления работой нагревательных элементов в закалочной и отпускной печах;
–алгоритмы управления работой приводов конвейеров;
–алгоритмы управления работой насосов масляной завесы циркуляции масла водяной завесы циркуляции охлаждающего раствора;
–алгоритмы управления работой клапанов подачи воды на охлаждение подпитки обезжиривающего и моющего растворов в моечной машине подачи эндогаза и азота.
4.3.2 Требования к информационному обеспечению
В системе должна использоваться единая система классификации и кодирования. В то же время должна обеспечиваться поддержка существующих у заказчика классификаторов в целях совместимости с принятой у него нормативно-справочной базой и комплексирования с существующими смежными системами.
Информационное обеспечение системы должно включать описание следующих массивов данных:
–перечень наблюдаемых системой АСУ ЭЛТА технологических данных и состояний оборудования;
–перечень управляющих воздействий;
–перечень используемых в приложениях текстовых и графических окон;
–перечень сообщений;
4.3.3 Требования к лингвистическому обеспечению
К лингвистическому обеспечению системы АСУ ЭЛТА (согласно ГОСТ 24.104-85) предъявляются следующие требования:
–стандартизация обозначений переменных применяемых в АСУ ЭЛТА;
–удобство и однозначность общения пользователей со средствами АСУ ЭЛТА;
–использование стандартных языков программирования а именно:
перечень отчетов для программирования контроллеров должны использоваться языки совместимые со стандартом IEC 6113-03 входящие в состав S
для программирования приложений АРМ оператора должны быть использованы стандартные языки программирования входящие в состав WinCC 6.0.
4.3.4 Требования к программному обеспечению
Программирование ПЛК должно осуществляться на основе программного пакета Simatic Step7.
АРМ оператора должно программироваться с использованием SCADA –пакета WinCC v6.0.
На АРМ оператора должна быть установлена операционная система MS Windows XP.
4.3.5 Требования к техническому обеспечению
В состав оборудования АСУ ЭЛТА должны входить:
–программируемый логический контроллер нормализаторы аналоговых сигналов промежуточные реле источник бесперебойного питания клеммные соединители лотки;
–блоки управления силовыми ключами нагревателей ОП и ЗП;
–частотные преобразователи и коммутационная аппаратура приводов клапанов и вентиляторов нагревателей;
–панельные компьютеры промышленного исполнения имеющих клавиатуру манипулятор (Track Ba
–средства аварийной сигнализации.
Для обеспечения связи между АРМ оператора и ПЛК по промышленной шине должны быть предусмотрены специальные коммуникационные модули. Оборудование комплекса технических средств АСУ ЭЛТА должно быть смонтировано в электротехнические шкафы. В шкафах должны быть предусмотрены системы контроля температуры и вентиляция.
Прокладка кабелей и проводов внутри шкафов должна осуществляться в пластиковых кабель-каналах. Провода цепей управления 24VDC и 220380 VAC должны прокладываться раздельно.
Частотные преобразователи (ЧП) должны комплектоваться базовой панелью оператора (BOP-Basis Operator Panel) и коммуникационными модулями ProfiBus устанавливаемыми непосредственно на ЧП.
Должна быть предусмотрена гальваническая развязка между силовыми цепями и цепями контроллера.
1 Выбор методов управления
Процесс термической обработки зависит от целой группы различных по своему физическому смыслу но взаимосвязанных параметров влияющих на качество изготавливаемой продукции.
Как объект управления электротермическая линия распадается на множество меньших объектов каждый из которых связан с остальными.
Электротермическую линию сложно однозначно отнести к дискретным или непрерывным системам так как в электротермической линии протекают как дискретные процессы так и непрерывные. Отметим что непрерывными процессами в системе являются только процессы связанные с изменением температур и скоростей то есть работа двигателей конвейеров и нагревателей в печах. Все остальные процессы (открытиезакрытие клапанов заслонок закалочной печи включениеотключение любых устройств электротермической линии) являются дискретными.
Большинство процессов протекающих в устройствах электротермической линии являются дискретными. Очевидно что для управления устройствами линии следует применить дискретно-логическое управление поскольку для любого устройства электротермической линии есть группа дискретных состояний в которых оно может находиться а переходы между состояниями происходят по условиям которые можно представить только как дискретные сигналы.
В зависимости от решаемой задачи для синтеза логического аппарата можно применить следующие методы логического синтеза: метод синтеза дискретно-логических систем управления на основе циклограмм работы механизмов и метод ориентированных графов[617]. Будем применять как основной - метод ориентированных графов и теорию конечных автоматов [20] так как при
синтезе логического аппарата на основе циклограмм невозможно учесть аварийные состояния объекта и следовательно получить полные алгоритмы работы устройств для любых ситуаций возможных в работе.
Система логического управления представима с помощью двух взаимодействующих моделей: модели управляемой системы (в нашем случае устройств электротермической линии) модели системы управления (АСУ ЭЛТА). Алгоритм логического управления синтезируется по модели поведения объекта управления. Можно использовать следующую последовательность синтеза алгоритма управления:
–моделирование поведения объекта управления;
–описание связи переменных модели поведения объекта и устройства управления;
–синтез алгоритма логического управления как модели поведения устройства управления.
Выберем в качестве аппарата моделирования поведения ОУ теорию конечных автоматов в которой конечный автомат представляется кортежем множеств:
XSY fперех fвых>; (2.1)
где Х – множество входных переменных;
S – множество внутренних переменных состояния;
Y – множество выходных переменных;
Fперех – функция переходов;
Fвых – функция выходов.
Таким образом моделирование поведения объекта управления сведётся к перечислению множеств X Y S и определению функций переходов и выходов.
Состояния элементов электротермической линии зависят от внутренних состояний устройств и входных переменных для описания таких объектов применяется конечный автомат четвертого рода – автомат Милли.
Структура автомата Милли представлена на рисунке 2.1.
Рисунок 2.1 – Автомат Милли
Используем понятия «состояние» «подсостояние» и «наблюдаемость» при составлении алгоритмов для того чтобы наглядно представлять поведение управляющих автоматов и композиций из них. В работе будем рассматривать два вида состояний:
–желаемые то есть состояния связанные с нормальной работой системы;
–аварийные связанные с нарушением алгоритмов нормальной работы электротермической линии.
Наиболее важной задачей при проектировании системы автоматизации электротермической линией является управление температурой так как качество обрабатываемой продукции непосредственно связанно с точность поддержания температуры в закалочной и отпускной печах. Для того чтобы определить характер процессов нагрева протекающих в печах и оценить их качество необходимо построить математическую модель нагрева.
Для построения модели рассмотрим закалочную печь как объект управления. Закалочная печь состоит из трех зон нагрева в каждой из которых должна поддерживать постоянная температура. В каждой из зон нагрева располагается нагреватель чьи спирали располагаются на стенах печи. Через все зоны печи движется конвейер. Каждая из зон нагрева закалочной печи можно представить как тепловую систему состоящую из нагревателя атмосферы зоны стенок печи. Поскольку зоны нагрева закалочной печи почти идентичны достаточно построить модель одной зоны закалочной печи.
Из курсов физики и математического моделирования систем [12] известно что основными физическими свойствами технических объектов любой физической природы являются – инерционные упругие и диссипативные. Они отображаются в динамических моделях соответственно инерционными упругими и диссипативными элементами. Однако тепловая система которую мы рассматриваем не обладает инерционными свойствами это следует из того что падение температуры вдоль дискретного элемента не зависят от скорости изменения теплового потока а зависит лишь от его абсолютной величины. Следовательно модель зоны нагрева электрической печи можно представить группой взаимосвязанных простых элементов: упругих и диссипативных. Состояние простого элемента характеризуется одной переменной типа потока и одной переменной типа потенциала. Для тепловой системы переменной типа поток является Ф - тепловой поток а переменной типа потенциал Т –температура. Зависимость между этими переменными называют компонентным уравнением. Компонентное уравнение упругого элемента для тепловой системы в общем случае выглядит следующим образом:
где СТ - удельная теплоемкость вещества в котором распространяется тепловой поток ;
Фи – тепловой поток расходуемый на нагрев вещества Джс.
Компонентное уравнение диссипативного элемента для тепловой системы в общем случае выглядит следующим образом:
где Тд – разница между температурой нагреваемого тела и температурой среды
в которую рассеивается тепловая энергия ºС;
Т – коэффициент конвективного теплообмена ;
Фд – тепловой поток рассеиваемый нагретым телом Джс.
На поверхностях контакта твердого тела с жидкостной или газовой средой осуществляется конвективный теплообмен. Для конвективного теплообмена коэффициент теплового сопротивления определяется по формуле:
где - коэффициент конвективного теплообмена ;
- площадь контакта твердого тела с газом или жидкостью м2.
Для получения полной математической модели технической системы необходимо объединить все компонентные уравнения элементов в общую систему уравнений. Объединение осуществляется на основе физических законов выражающих условия равновесия и непрерывности физических переменных. Уравнения этих законов называют топологическими уравнениями. Они описывают характер взаимодействия между простыми элементами устанавливая соотношения между однотипными переменными.
Условия равновесия записываются для фазовой переменной типа потенциала (в рассматриваемой системе температура):
Условия непрерывности – для переменных типа потока (для рассматриваемой системы тепловой поток):
Для построения модели воспользуемся методом электроаналогий [1216]. Метод электроаналогии – это один из методов имитационного моделирования опирающийся на единообразие физических законов. Поскольку именно электрические схемы обладают наибольшей наглядностью и изученностью то благодаря единству формы уравнений математического представления объектов различной физической природы исследование явлений в неэлектрической системе может быть заменено исследованием процессов в электрической цепи. Сравнивая компонентные и топологические уравнения
можно отметить очевидность динамических аналогий между тепловой и электрической системами. Для топологических уравнений тепловой системы аналогами являются законы Кирхгофа. Для компонентных уравнений тепловой системы - закон Ома и уравнение конденсатора:
В результате моделирования были получены графики переходного процесса протекающего в замкнутом контуре регулирования температуры в зоне нагрева закалочной печи при нагреве от температуры цеха до минимальной рабочей (810 ºС). График переходного процесса в системе при нагреве представлен на рисунке 2.2.
Рисунок 2.2- График переходного процесса в зоне нагрева закалочной печи.
Из графика можно определить что время нагрева печи от начальной температуры (температура атмосферы цеха) до минимальной рабочей температуры составляет около двух с половиной часов. Перерегулирование отсутствует.
Рассмотрим также переходные процессы протекающие в системе при появлении возмущающих воздействий. В качестве возмущающих воздействий выступают снижение температуры в печи связанные с потерей тепла при открытии заслонок шлюзования с целью загрузки деталей в печь. Потери тепла при однократном открытии заслонок шлюзования малы но так как открытие заслонок шлюзования происходит многократно то следует удостоверится в том что температура в печи не выйдет за допустимые пределы (± 5ºС от установившегося значения). Процессы протекающие в системе при подаче таковых возмущений представлены на рисунке 2.3.
Рисунок 2.3 – Переходной процесс протекающий в системе при
появлении возмущающих воздействий.
Отметим что при появлении серии скачкообразных возмущений температура в печи не вышла за пределы допустимых значений (± 5ºС от установившегося значения).
Опираясь на полученные характеристики можно сделать вывод что система не нуждается в применении дополнительного регулятора так как показатели качества процесса вполне удовлетворяют требованиям указанным в техническом задании [14].
Для управления температурой целесообразно будет применить широтно-импульсное регулирование так как широтно-импульсное регулирование позволяет обеспечить высокую плавность регулирования [1].
Импульсные методы регулирования основаны на изменении количества энергии подводимой к объекту управления (в нашем случае к нагревателю). В этом случае к нагревателю подводится последовательность импульсов неизменного напряжения (U) и работа нагревателя состоит из периодов Т (нагрев - охлаждение). Требуемый нагрев должен соответствовать среднему значению за период Т и будет определяться относительной продолжительностью включения (скважностью) импульсов γ:
где tИ - длительность импульса;
tП - длительность паузы.
Импульсное регулирование нагрева может быть осуществлено при помощи различных преобразователей: широтно-импульсных частотно-импульсных и широтно-частотно-импульсных.
При импульсном управлении мгновенное значение теплового потока будет непрерывно колебаться в определенных пределах. При этом размах колебаний будет тем меньше чем больше теплоемкости к периоду следования импульсов. Следовательно с ростом частоты управляющих импульсов размах колебаний теплового потока уменьшается. Отметим что среднее значение теплового при этом остается неизменным что наиболее важно с точки зрения поддержания
температуры в печи. Оно может быть изменено только путем изменения скважности импульсов g за счет изменения их длительности (2.7). С ростом скважности импульсов подаваемых на нагреватель среднее значение температуры в печи также растет.
В техническом задании поставлена задача регулирования скоростей двигателей конвейеров электротермической линии. В электротермической линии применяются асинхронные двигатели это обусловлено рядом преимуществ асинхронных двигателей таких как высокая надежность низкая стоимость простота изготовления и эксплуатации [1].
Из теории электропривода известно что скорость вращения вала асинхронного двигателя зависит от конструктивных параметров электродвигателя момента нагрузки и частоты напряжения питающей сети это следует из уравнений механической характеристики асинхронного двигателя (3.1) и формулы (3.2):
где 0 – синхронная угловая скорость (скорость холостого хода) радс;
Uф – первичное фазное напряжение В;
X1 – первичное приведенное реактивное сопротивление Ом;
– вторичное приведенное реактивное сопротивление Ом;
R1 – первичное приведенное активное сопротивление Ом;
– вторичное приведенное активное сопротивление Ом;
p – число пар полюсов асинхронного двигателя;
f – частота питающей сети Гц.
Очевидно для получения качественного регулирования необходимо изменять последний параметр т. е. частоту питания. Для этой цели применяются преобразователи частоты. Преобразователь частоты – это устройство преобразующее электрическую энергию с параметрами U1 f1(в нашем случае 380 В 50 Гц) в электрическую энергию с параметрами U2 f2. Частотные преобразователи можно разделить на преобразователи частоты со скалярным и векторным управлением. Такое деление обусловлено необходимостью управлять не только частотой на выходе преобразователя но и напряжением. Алгоритм вычисления значения напряжения и определяет способ управления. В преобразователях частоты со скалярным управлением значение напряжения определяется из зависимости U(f) которая как правило рассчитывается методом линейной интерполяции по нескольким базовым точкам. Имеется возможность изменять значение этих точек.
В преобразователях частоты с векторным управлением значение напряжения рассчитывается методом моделирования процессов проходящих в асинхронном двигателе. В этом случае пользователю необходимо задать параметры двигателя. Очевидно что второй способ управления позволяет осуществлять более качественной управление электродвигателем. Однако настройка такого преобразователя частоты требует довольно глубоких познаний в области электропривода и электрических машин. Скалярный же способ управления обеспечивает достаточно хорошее качество регулирования даже с использованием заводских настроек частотного преобразователя. Использование векторного управления электроприводами конвейеров вряд ли даст существенный выигрыш в сравнении со скалярным. Следовательно применение векторного управления в нашем случае является нецелесообразным. Для управления скоростями конвейеров будем использовать скалярное управление.
Рассмотрим более подробно структурную схему преобразователя частоты со звеном постоянного тока. Структурная схема преобразователя частоты представлена на рисунке 2.2. Основу преобразователя составляет трехфазный инвертор напряжения (АИН) с широтно-импульсной модуляцией (ШИМ). Система управления преобразователя выполнена на базе программируемого микропроцессорного контроллера (МК). В АИН преобразование постоянного напряжения в трехфазное переменное осуществляется в мостовом транзисторном инверторе собранном на трех транзисторно-диодных модулях. Каждый модуль содержит два IGBT-транзистора с шунтирующими обратными диодами. IGBT-транзисторы переключаются многократно в течение периода выходной частоты в соответствии с ШИМ-алгоритмом МК.
Алгоритм ШИМ-управления поддерживает требуемое регулирование частоты и действующего значения основной гармоники выходного напряжения обеспечивая при этом синусоидальность формы тока нагрузки.
Рисунок 2.3 – Структурная схема преобразователя частоты
Современные преобразователи частоты являются интеллектуальными устройствами использующими микроконтроллеры достаточно высокой производительности в современных преобразователях имеется ряд дополнительных опций и расширений позволяющих создавать несложные системы автоматического управления без использования контроллеров.
Рассмотрим подробнее ряд таких расширений которые есть практически во всех современных преобразователях частоты.
Аналоговые выходы - позволяют наглядно представить значение какого-нибудь параметра. Однако использования их в системах автоматизации нецелесообразно так как они как правило имеют малую мощность и неудовлетворительное качество.
Аналоговые входы - позволяют подавать сигналы от датчиков напрямую в преобразователь частоты без использования каких-либо дополнительных устройств. Как правило используются унифицированные типы сигналов (0 – 5 В 0 – 10 В 4 – 20 мА) так что согласующие устройства не требуются. Кроме того имеется возможность использования внутреннего питания преобразователя для подключения потенциометра например для задания частоты вращения.
Дискретные входы - позволяют управлять преобразователем частоты с кнопок установленных на лицевой панели шкафа или с поста управления.
Дискретные выходы - используются для сигнализации режимов работы преобразователя.
В современных преобразователях предусмотрена возможность подключения его в промышленную сеть. Обычно используется протокол RS-485. Соединение преобразователей в сеть позволяет построить более сложную систему автоматического управления технологическими процессами с использованием контроллеров и промышленных компьютеров.
К достоинствам современных частотных преобразователей можно отнести ниже перечисленные факторы.
Плавное регулирование скорости вращения электродвигателя позволяет в большинстве случаев отказаться от использования редукторов вариаторов дросселей и другой регулирующей аппаратуры что значительно упрощает управляемую механическую (технологическую) систему повышает ее надежность и снижает эксплуатационные расходы.
Частотный пуск управляемого двигателя обеспечивает его плавный без повышенных пусковых токов и механических ударов разгон что снижает нагрузку на двигатель и связанные с ним передаточные механизмы увеличивает срок их эксплуатации. При этом появляется возможность по условиям пуска снижения мощности приводных двигателей нагруженных механизмов.
Встроенный микропроцессорный ПИД-регулятор позволяет реализовать системы регулирования скорости управляемых двигателей и связанных с ним технологических процессов.
Применение обратной связи системы с частотным преобразователем обеспечивает качественное поддержание скорости двигателя или регулируемого технологического параметра при переменных нагрузках и других возмущающих воздействиях.
Частотный преобразователь в комплекте с асинхронным электродвигателем может применяться для замены приводов постоянного тока.
Частотный преобразователь в комплекте с программируемым микропроцессорным контроллером может применяться для создания многофункциональных систем управления электроприводами в том числе с резервированием механических агрегатов. Таким образом возможно добиться точного поддержания скорости двигателя используя только возможности микропроцессорного частотного преобразователя.
Устройства электротермической линии работают в соответствии с представленными ниже алгоритмами.
Алгоритм блока управления клапаном.
Блок предназначен для:
–управления клапаном;
–формирования слова состояния клапана.
На рисунке 2.4 представлена модель блока управления клапаном типа «черный ящик».
Рисунок. 2.4 – Модель блока управления клапаном типа «черный ящик»
Входной информацией для данного блока являются переменные представленные в таблице 2.1.
Таблица 2.1 – Входные данные блока управления клапаном
Команда «Открыть» от алгоритма верхнего уровня
«Клапан открыт» сигнал с концевого выключателя клапана
Время отводимое на открытиезакрытие
Выходной информацией являются переменные представленные в таблице 2.2.
Таблица 2.2 – Выходные данные блока управления клапаном
Переменная состояния – «клапан открыт по ошибке» передача в алгоритм более высокого уровня
Переменная состояния – «клапан не закрылся» передача в алгоритм более высокого уровня
«Открыть клапан» команда на пускатель
Формирование слова состояния и управление клапаном производится в соответствии с графом его состояний представленном на рисунке 2.5.
Рисунок 2.5 – Граф алгоритм работы блока управления клапаном
Граф формирует возможные состояния клапана. Описание состояний приводится в таблице 2.3.
Таблица 2.3 – Состояния клапана
- состояние активно
- состояние неактивно
Авария клапан – закрыт.
Клапан открылся по неизвестной причине
Закрывается из-за ошибки
Алгоритм блока управления конвейером.
–управления конвейером;
–формирования слова состояния конвейера.
На рисунке 2.6 представлена модель блока управления конвейером типа «Черный ящик».
Рисунок. 2.6 – Модель блока управления конвейером типа «черный ящик»
Входной информацией для данного блока являются переменные представленные в таблице 2.4.
Таблица 2.4 – Входные данные блока управления конвейером
«конвейер включен» сигнал с концевого выключателя клапана
Время отводимое на включение отключение конвейера
Готовность конвейера к работе
Выходной информацией являются переменные представленные в таблице 2.5
Таблица 2.5 – Выходные данные блока управления конвейером
Переменная состояния – «конвейер включился по неизвестной причине» передача в алгоритм более высокого уровня
Переменная состояния – «конвейер не отключился» передача в алгоритм более высокого уровня
«Включит конвейер» команда на пускатель
Блокировать конвейер
Переменная состояния - «Конвейер не включился» передача в блок обработки аварий
Формирование слова состояния и управление конвейером производится в соответствии с графом его состояний представленном на рисунке 2.7.
Рисунок 2.7 – Граф алгоритм работы блока управления конвейером
Граф формирует возможные состояния конвейера. Описание состояний приводится в таблице 2.6.
Таблица 2.6 – Состояния конвейера
Конвейер готов к пуску
Авария конвейер – отключен.
Конвейер включен – норма
Конвейер отключается
Отключается по аварии
Конвейер включен – авария
Таблица 2.6 – продолжение
Конвейер не отключился
Конвейер включился по неизвестной причине
Алгоритм блока управления вентилятором.
–управления вентилятором;
–формирования слова состояния вентилятора.
На рисунке 2.8 представлена модель блока управления вентилятором типа «Черный ящик».
Рисунок. 2.8 – Модель блока управления вентилятором типа «черный ящик»
Входной информацией для данного блока являются переменные представленные в таблице 2.7.
Таблица 2.7 – Входные данные блока управления вентилятором
Команда «Включить» от алгоритма верхнего уровня
«Вентилятор включен» сигнал с концевого выключателя клапана
Время отводимое на включение отключение
Выходной информацией являются переменные представленные в таблице 2.8.
Таблица 2.8 – Выходные данные блока управления клапаном
Переменная состояния – «вентилятор включился по неизвестной причине» передача в алгоритм более высокого уровня
Переменная состояния – «вентилятор не отключился» передача в алгоритм более высокого уровня
«Включит вентилятор» команда на пускатель
Переменная состояния - «Вентилятор не включился» передача в блок обработки аварий
Формирование слова состояния и управление вентилятором производится в соответствии с графом его состояний представленном на рисунке 2.9.
Рисунок 2.9 – Граф алгоритм работы блока управления вентилятором
Граф формирует возможные состояния вентилятора. Описание состояний приводится в таблице 2.9.
Таблица 2.9 – Состояния вентилятора
Авария вентилятор – отключен
Вентилятор включился по неизвестной причине
Таблица 2.9 – продолжение
Вентилятор не отключился
Вентилятор включается
Вентилятор отключается
Вентилятор отключается по аварии
Алгоритм блока широтно-импульсной модуляции.
Блок ШИМ предназначен для генерирования последовательности импульсов заданной продолжительности в соответствии с заданием.
На рисунке 2.10 представлена модель блока управления ШИМ типа «Черный ящик».
Рисунок 2.10 – модель блока ШИМ типа «черный ящик»
Входной информацией для данного блока являются переменные представленные в таблице 2.10.
Таблица 2.10 – Входные данные блока управления клапаном
Команда «Включить» сформированная в алгоритме нагревателя
«Трансформатор тока включен» сигнал с трансформатора
Значение времени в данный момент считываемое с таймера
Продолжительность импульса
Выходной информацией являются переменные представленные в таблице 2.11.
Таблица 2.11 – Выходные данные блока управления клапаном
Блок ШИМ функционирует в соответствии с графом его состояний представленным на рисунке 2.
Рисунок 2.11 – Граф алгоритм работы блока управления широтно-импульсной модуляцией.
Граф формирует возможные состояния блока ШИМ. Описание состояний приводится в таблице 2.12.
Таблица 2.12 – Состояния ШИМ
Выдача импульсов остановлена
Ожидание завершения периода
2 Выбор технического обеспечения
В настоящее время автоматизация любых производственных процессов выполняется на базе универсальных микропроцессорных контроллерных средств [5]. Это обусловлено следующими факторами:
–использование готовых технических средств устранит необходимость их проектирования;
–микропроцессорные системы отличаются высокой надежностью;
–сокращается время проектирования системы;
–унифицируется элементная база систем управления
Существуют следующие варианты технических решений при построении системы управления на базе микропроцессорной техники:
–система управления на базе персонального компьютера;
–система управления на базе локального контроллера PLC (programmable log
–сетевой комплекс контроллеров (PLC Network);
–полномасштабные распределенные системы управления (DCS Full Scale).
Для построения системы управления электротермической линией целесообразно использовать система управления на базе локального контроллера PLC это связанно с тем что система управления на базе персонального компьютера не обладает достаточными возможностями для управления электротермической линией сетевой комплекс и распределенная система управления напротив применяются для более сложных объектов и слишком дороги.
Поскольку система будет располагаться в термическом цехе контроллеры должны быть пригодны для работы при температуре до 45 ºС. Так как для управления температурой решено применить широтно-импульсное управление необходимо чтобы на базе применяемого контроллера возможно было организовать управлямый широтно-импульсный модулятор.
Можно отметить что российский рынок на сегодняшний день предлагает достаточно широкий диапазон контроллерных средств среди них можно назвать контроллеры компаний Siemens и Advantech Mitsubishi.
Для построения системы управления целесообразно применить контроллеры Siemens [18]. Это обусловлено их высокой надежностью простотой программирования приемлемой стоимостью и доступностью. Для наших целей применимы контроллеры серий S-300 и S-400.
Для объектов автоматизации средней сложности к которым относится и ЭЛТА 845 можно выбрать один из контроллеров серии S-300 контроллеры серии S-400 стоят дороже и применяются в основном для сложных объектов (объектов с большим количеством сигналов) в нашем случае их применение было бы необоснованным. Контроллеры S-300 имеют модульное построение и могут включать в свой состав следующие компоненты:
–стойки (RACK) служащие для размещения модулей и соединения их между собой;
–блок электропитания (Power Supp
–центральное процессорное устройство (Central Process
–сигнальные модули (S
–функциональные модули (Funct
–коммуникационные процессоры (Communication Processor CP)
устанавливает соединение с вспомогательными сетями (подсетями);
– подсети (Subnets).
Раннее указанным требованиям к контроллеру (работоспособность при температуре до 45 ºС возможность программной реализации блока ШИМ) удовлетворяет контроллер Siemens S-317 2DP.
Для регулирования скоростей конвейеров в проекте применены частотные преобразователи серии MicroMaster (представлены на рисунке 2.12) производимые компанией Siemens (технические характеристики преобразователей MicroMaster представлены в приложении Б). Это связано с тем что это привода удовлетворяющие требованиям технического задания легко интегрируются в любые современные системы позволяют управлять ими по промышленным вычислительным сетям (PROFIBUS).
Рисунок 2.12 Преобразователи серии MicroMaster (слева направо MicroMaster 410 MicroMaster 420 MicroMaster 440).
Применим частотные преобразователи M возможность изменения оператором вольт-частотной характеристики что облегчает его переналадку.
Подсистему визуализации (АРМ оператора) возможно реализовать с помощью следующих технических средств:
–встраиваемая панель оператора;
–панельный компьютер промышленного исполнения;
–настольный компьютер.
Для технической реализации подсистемы визуализации технологического процесса применим панельный компьютер промышленного исполнения. Это обусловлено тем что ни одна из существующих моделей встраиваемых панелей оператора не способна обеспечить выполнение всех функции указанных в техническом задании а настольный компьютер занимает слишком много места и его невозможно разместить в цехе.
3. Выбор программного обеспечения и структуры программного обеспечения проекта
Для обеспечения нормального функционирования системы необходимо чтобы программное обеспечение решало две задачи:
–формирование управляющих сигналов для электротермической линией в соответствии с алгоритмами её работы;
–представление информацию о состоянии системы в форме понятной оператору и обеспечение взаимодействия между оператором и объектом управления возможность управлять процессом.
Программное обеспечение решающее указанные задачи состоит из программного обеспечения HMI (Human-Machine Interface – человеко-машинного интерфейса) и программного обеспечения контроллера интерфейса связи между АРМ и ПЛК а так же интерфейса связи между контроллером и объектом управления.
Так как в качестве оборудования системы был выбран контроллер Siemens то очевидно что наиболее целесообразным будет использовать программное обеспечение также разработанное компанией Siemens и приспособленное для наиболее полного и эффективного взаимодействия с контроллерами того же производителя.
Для организации человеко-машинного интерфейса изберем систему исполнения SCADA WinCC 6.0. Фактически управление осуществляется контроллером.
WinCC позволяет осуществлять обмен информацией между оператором и контроллером [19].
Разработку проекта будем осуществлять используя стандартные средства
WinCC6.0 в том числе:
–графическую систему редактор для создания кадров (Graph
–система сообщений редактор для конфигурирования сообщений (Alarm Log
–система архивирования редактор для определения архивируемых данных (Tag Logg
–система отчетов редактор для создания шаблонов отчетов (Report Des
–библиотека программных модулей используемых в проекте (Scr
–система администрирования.
Для создания программного обеспечения контроллера воспользуемся программным пакетом SIMATIC STEP7 [2]. Данный пакет позволяет так же сконфигурировать применяемое оборудование. STEP7 позволяет объединить все подсистемы используемые в решении задач автоматизации от полевого уровня до уровня управления процессом – в рамках однородной системной архитектуры в гомогенное целое. В SIMATIC STEP7 в соответствии со стандартом IEC 1131-3 предоставляются следующие языки программирования:
–STL (список инструкций);
–SCL (структурированный текст);
–LAD (язык контактных элементов);
–FBD (язык диаграмм функциональной логики).
В состав программного обеспечения контроллера входят:
–система конфигурирования оборудования;
–организационные блоки;
–функциональные блоки;
Для организации интерфейса обмена данными между контроллером и автоматизированным рабочим местом воспользуемся стандартным протоколом семейства Simatic S7 PROTOCOL SUITE.
В качестве операционной системы на АРМ оператора применим Windows XP.
Структура программного обеспечения представлена на рисунке 2.13.
Рисунок 2.14 – Структура программного обеспечения АСУ ЭЛТА
4 Разработка структурных схем КТС
Структурная схема представлена на чертеже 2021.082.000001.С1 включает в себя следующие элементы:
A 1.0 – модуль ввода дискретных сигналов в контроллер;
A 2.0 – модуль вывода дискретных сигналов контроллера;
B 1 – оптосемистор выполняет функции гальванической развязки между цепью контроллера и цепью нагревателя;
EK1 EK3 – нагревательные элементы;
KM 1- катушка контактора выполняет функцию коммутации цепи нагревателя;
KM 1:1 4 – контакты контактора KM 1;
K 1– катушка реле предназначена для гальванической развязки силовых цепей и цепей управления;
K 1:1 – контакт реле K 1 при замыкании данного контакта на дискретный вход поступает сигнал;
QF 1 – автоматический выключатель выполняет функцию защиты цепи нагревателя;
TA 1 TA 3 – измерительные трансформаторы тока;
TV 1 – понижающий трансформатор напряжения 38042 В;
X 1:1 – X 2:6 – клеммные контакты;
VS 1 – VS 3 – семисторы предназначены для управления нагревателями.
Структурная схема 2021.082.000002.С1 включает в себя следующие элементы:
A 3.0 – модуль ввода аналоговых сигналов в контроллер;
A 4.0 – модуль вывода аналоговых сигналов из контроллера;
A 5.0 – блок управления семисторами и тиристорами;
R 2 – резистор предназначен для преобразования сигнала на входе в БУСТ;
SF 1 – автоматический выключатель вибратора выполняет функцию защиты
X 2:1 X 6:2 – клеммные контакты;
Y 1- катушка электромагнита вибратора 3;
VS 4 – семистор управления вибратором;
UA 1 – нормализатор сигнала преобразует сигнал 0÷5 А во входную величину модуля аналоговых входов 4÷20 мА.
5 Визуализации технологического процесса
Визуализация технологического процесса позволит отобразить о работе устройств системы в удобной для оператора наглядной форме. Для этого применимы мнемосхемы линии с изображением основных устройств входящих в ЭЛТА 845. На экране панели оператора целесообразно отображать текущие значения параметров системы: скорости конвейеров в печах температуры и уровни жидкостей в закалочном баке и баке охлаждения время до завершения обработки партии дату и информацию об операторе.
На рисунке 2.14 представлена мнемосхема электротермической линии реализованная в скада-пакете WinCC 6.0.
Рисунок 2.14 – Мнемосхема электротермической линии.
Разработка математической модели синтез и программная реализация алгоритмов работы устройства управления закалочной печи.
1 Исследование тепловых процессов в закалочной печи
1.1 Построение модели нагрева закалочной печи
Как уже отмечалось зоны нагрева в печах организованны идентично поэтому нет необходимости рассматривать каждую зону достаточно рассмотреть одну из зон нагрева.
Представим модель зоны нагрева в виде «черного ящика» представленную на рисунке 3.1. На входе черного ящика тепловой поток Ф1 на выходе температура в закалочной печи. Возмущением является ΔQ – относительно малые потери тепловой энергии при открывании заслонок шлюзования закалочной печи. Отметим что заслонки шлюзования являются часть шлюзовой камеры закалочной печи которая предназначена для минимизации тепловых потерь при загрузке. Это осуществляется за счет того что одна из заслонок камеры шлюзования всегда закрыта и следовательно отсутствует непосредственный контакт между атмосферой печи и атмосферой цеха.
Рисунок 3.1 – Модель зоны нагрева в виде «черного ящика»
Температура в зоне нагрева зависит от следующих параметров: теплового поток от нагревателя зоны нагрева потери тепла через стенки печи которые в свою очередь определяются тепловым потоком между внешними стенками печи и атмосферой цеха и тепловым потоком идущим на нагрев стенок печи теплоемкостью атмосферы печи теплоемкостью материала из которого изготовлена печь. Распределения теплового потока от нагревателей представлено схематично на рисунке 3.2.
– вентилятор зоны нагрева печи;
– секции нагревателя;
– внутреннее пространство печи;
Рисунок 3.2 – Схема распределения тепла в зоне нагрева закалочной печи.
На рисунке Ф1– тепловой потоки от нагревателя Ф12 – тепловой поток из рабочего пространства закалочной печи в её корпус Ф2 – тепловой поток от стенок печи в атмосферу цеха Ф1С – тепловой поток идущий на нагрев атмосферы печи Ф2С – тепловой поток идущий на нагрев стенок печи.
При построении модели приняты следующие допущения:
–утечка тепла из печи через заслонки отсутствует;
–распределение температуры в зоне нагрева равномерно за счет вентилятора;
–температура во всех зонах печи одинакова;
–теплообмен между соседними зонами нагрева пренебрежимо мал;
–процессы протекающие в симисторах скоротечны по сравнению с процессом нагрева поэтому для модели можно принять что преобразование сигнала задания в величину входного тока нагревателя происходит по линейному закону.
Исходные данные для построения математической модели зоны нагрева закалочной печи представлены в таблице 3.1.
Таблица 3.1 - Исходные данные для построения модели зоны нагрева закалочной печи
Наименование параметра
Обозначение параметра
Удельная теплоёмкость эндогаза
Таблица 3.1 - продолжение
Коэффициент теплопередачи между материалом (шамотный кирпичпеношамот) и атмосферой печи
Удельная теплоёмкость пеношамота
Плотность пеношамота
Применяя метод электроаналогий [16] распределение тепла в зоне нагрева печи можно представить электрической схемой представленной на рисунке 3.3.
Рисунок 3.3 – Эквивалентная электрическая схема зоны нагрева закалочной печи
Для данной электрической схемы можно записать следующую систему топологических уравнений:
где – температура нагревателя в зоне нагрева ºС;
– температура в зоне нагрева печи ºС;
– температура материала печи ºС;
– температура воздуха в цехе в котором располагается печь ºС;
– разница между температурой нагревателя и температурой атмосферы печи ºС;
– разница между температурами атмосферы печи и температуры материала корпуса печи ºС;
– разница между температурой материала корпуса печи и температурой воздуха в цехе ºС.
На основании системы уравнений (3.1) построим алгебраизированный граф связей между топологическими уравнениями системы.
Граф связей между топологическими уравнениями системы представлен на рисунке 3.4.
Рисунок 3.4 – Алгебраизированный граф связей между топологическими уравнениями системы
Компонентные уравнения и соответствующие им передаточные функции представленные в таблице 3.2 определяют количественные взаимосвязи физических величин.
Таблица 3.2 – Физические уравнения и передаточные функции тепловой системы
Физические зависимости
Передаточные функции
где А1 – площадь нагревателя зоны закалочной печи м2;
А2 – площадь внутренней поверхности печи м2;
А3 – площадь внешней поверхности печи м2;
α1 – коэффициент теплопередачи между воздухом и материалом
α2 – коэффициент теплопередачи между материалом нагревателя и
С1 – теплоёмкость атмосферы одной зоны печи ;
С2 – теплоёмкость материала печи одной зоны нагрева .
На основе таблицы можно построить структурную схему зоны нагрева закалочной печи (рисунок 3.5).
1.2 Модель нагревателя закалочной печи
Исходные данные для построения математической модели нагревателя в зоне нагрева закалочной печи представлены в таблице 3.3.
Таблица 3.3 - Исходные данные для построения математической модели нагревателя
Длина нагреваемого проводника нагревателя в зоне нагрева
Диаметр нагреваемого проводника нагревателя
Удельная теплоемкость материала нагревателя (нихром)
Удельное сопротивление нихрома
Номинальный ток нагревателя
Температурный коэффициент сопротивления нихрома
Коэффициент теплопередачи между материалом нагревателя и атмосферой печи
Нагреватель представляет собой устройство преобразующее электрическую энергию в тепловую [11]. Для секции нагревателя можно записать уравнения электрической мощности:
где I – ток нагревателя А;
Rнаг – сопротивление секции нагревателя Ом;
– коэффициент полезного действия.
Мощность выделяемая секцией нагревателя не является постоянной величиной так как при изменении температуры нагревателя изменяется его сопротивление. Это изменение описывается следующим выражением:
где R0 – сопротивление секции нагревателя при температуре 20ºС Ом;
- температурный коэффициент сопротивления материала
ΔТнаг – изменение температуры нагревателя ºС.
Сопротивление проводника нагревателя можно определить из формулы:
где – удельное сопротивление материала нагревателя ;
S – площадь поперечного сечения нагревателя м2.
Мощность выделяемую в нагревателе можно представить как тепловой поток поступающий в нагреватель.
Если проинтегрировать уравнение по времени то можно получить количество энергии выделившееся в нагревателе:
Энергия выделившаяся в нагревателе расходуется на нагрев нагревателя и на нагрев атмосферы печи.
Для энергии расходуемой на нагрев материала нагревателя можно записать следующую формулу:
где – энергия расходуемая на нагрев нагревателя Дж
с – удельная теплоемкость вещества нагревателя ;
– изменение температуры материала нагревателя при передаче ему
m – масса секции нагревателя кг.
Энергия выделяемая нагревателем в атмосферу печи можно определить по формуле:
где Q1 – энергия выделившаяся в атмосферу печи.
Исходя из выше рассмотренного можно составить структурную схему нагревателя. Структурная схема нагревателя представлена на рисунке 3.6.
Рисунок 3.6 – Структурная схема нагревателя
Применяя формулы (3.6) и (3.7) можно записать выражение для передаточной функций нагревателя:
где с – удельная теплоемкость материала нагревателя;
m – масса нагревателя кг.
1.3 Построение САР температуры для зоны нагрева
Структурная схема САР температуры для зоны нагрева представлена на рисунке 3.7.
Wз.п. – передаточная функция зоны нагрева закалочной печи;
Wнаг. – передаточная функция нагревателя;
WШИМ – передаточная функция широтно-импульсного модулятора;
Wрег. – передаточная функция регулятора температуры;
УУзад. – устройство управления выдающее сигнал задания;
Wдат.тем. – передаточная функция датчика температуры.
Устройство управления ШИМ и регулятор температуры реализованы в схеме на базе программируемого логического контроллера.
1.4 Определение коэффициентов передаточных функций модели нагрева закалочной печи и модели нагревателя
Площадь поверхности нагревателя определяется по формуле:
где – длина нагревателя в зоне нагрева м;
D – диаметр проводника нагревателя м;
–площадь нагревателя м2.
Подставляя в формулу значения из таблицы 3.3 получим:
Площадь внутренней поверхности зоны нагрева печи можно определить следующим образом:
где – длина зоны нагрева м;
– ширина зоны нагрева м;
– высота зоны нагрева м;
– площадь внутренней поверхности зоны нагрева м2.
Подставляя значения из таблицы 3.1 получим:
Площадь внешней поверхности зоны нагрева печи можно определить следующим образом:
– длина нагревателя в зоне нагрева м.
Подставляя значения из таблицы 3.1 определим площадь внешней поверхности:
Определим теплоемкость атмосферы зоны закалочной печи для этого воспользуемся следующей формулой:
где V1 – объем зоны нагрева печи ;
с1 – удельная теплоемкость эндогаза ;
– плотность эндогаза ;
С1 – теплоемкость атмосферы печи .
Объем можно определить из геометрических размеров зоны печи указанных в таблице 3.1:
– высота зоны нагрева м.
Подставляя значения из таблицы 3.1 в формулы (3.12 3.13) рассчитаем значение теплоемкости атмосферы в зоне нагрева печи:
тогда теплоёмкость атмосферы зоны печи:
Аналогично можно определить теплоёмкость части корпуса которая расположена вокруг зоны нагрева печи:
где V2 – объем занимаемый материала корпуса печи в зоне нагрева.
с2 – удельная теплоемкость материала печи ;
– плотность материала печи ;
С2 – теплоемкость стенок печи граничащих с зоной нагрева .
Объем можно определить из геометрических размеров зоны печи
указанных в таблице 3.1:
– длина зоны нагрева м;
Подставляя значения из таблицы 3.1 в формулe (3.15) определим теплоемкость материала корпуса печи в зоне нагрева:
тогда теплоемкость корпуса по (3.14):
При подстановке значений из таблицы 3.1 и выше рассчитанных значений в математические выражения передаточных функций указанные в таблице 3.2 передаточные функции примут вид:
W1=0.0018 · 14=0.0504;
Передаточная функция нагревателя при подстановке в формулу (3.8) данных из таблицы 3.3 примет вид:
1.5 Определение передаточной функций датчика температуры
Устройство измеряющее температуру в печи представляет собой термопару. На выходе датчика формируется сигнал в виде унифицированного сигнала 4÷20 мА.
Диапазон измерения датчика (DТизм) 0 ÷ 1000 ºС.
Сигнал с датчика поступает в программируемый логический контроллер на входе которого находится аналого-цифровой преобразователь (АЦП). АЦП преобразует сигнал датчика из аналогового значения в значение температуры (Тк) в диапазоне 0 ÷ 1000 ºС. Поэтому если рассматривать термопару совместно с АЦП как единый датчик получим передаточную функцию датчика
где Тк – максимальное значение температуры определяемое контроллером ºС;
Tизм.макс – максимальное значение температуры измеряемое датчиком ºС.
Подставляя в формулу (3.16) получим:
1.6 Передаточная функция преобразователя
Целесообразным будет рассматривать блок-ШИМ (широтно-импульсный модулятор) реализованных на базе контроллера и симисторный преобразователь как единое устройство далее именуемое «Преобразователь».
ШИМ выдает последовательность импульсов продолжительность которых зависит от величины ошибки на входе преобразователя. Ток подаваемый на нагреватель пропорционален скважности импульсов. Запишем выражение для скважности импульса:
где tимп – продолжительность импульса с;
Т – период импульса с.
Симисторный преобразователь преобразует продолжительность импульса во входной ток нагревателя.
Таким образом передаточная функция преобразователя выглядит следующим образом:
где Iн – номинальный ток нагревателя А;
Тзад.макс – максимальная величина задания температуры.
Подставляя значения номинального тока (таблица 3.3) и диапазона задания температуры получим:
2 Программирование алгоритмов работы устройств ЭЛТА 845
Программную реализацию алгоритмов работы устройств электротермической линии представим на примере клапана и широтно-импульсного модулятора алгоритмы котрых приведены в разделе техническое предложение.
Программа составляется на языке SCL встроенном в программный пакет Simatic Step 7:
OPd: клапан открылся (с пускателя)
Acknow: квитированно
To_OP: команда открыть от верхнего алгоритма
Breake_L сигнал наступления аварии
OPtoVa открыть клапан (команда на пускатель)
Dont_OP: клапан не открылся
ErNotC клапан не закрылся
ErOp:BOOL клапан открылся по неизвестной причине
C клапан закрыт и в аварии
OPd_Er: клапан открыт ошибка
Norma клапан открыт и в норме
Norma клапан закрыт и в норме
Cl_ клапан открывается
Op_ клапан закрывается
Cl_ сигнал задания снимается по ошибке
re_val:=READ_CLK(CDT :=cur_t
interval:=SB_DT_DT(DT1 :=cur_time
IF interval>T#5s THEN
IF NOT To_OP AND NOT OPd AND NOT Closed_Error AND NOT OPd_ER THEN
IF To_OP AND (NormalCL OR Closed_Error) THEN
IF OPtoValve AND OP_ing THEN
IF Op_ing AND OPd THEN
IF Op_ing AND NOT OPd AND timer1 THEN
IF NormalOP AND NOT To_OP THEN
IF NOT OPtoValve AND Cl_ing THEN
IF (Cl_ing AND OPd AND timer1) THEN
IF NormaCl AND OPd THEN
IF ErOp OR ErNotCl THEN
IF OPd_Er AND NOT OPd AND Acknow THEN
IF (Cl_ing_ErR AND NOT OPd THEN
IF Closed_Error AND NOT Breake_List AND Acknow THEN
TR_swтрансформатор включен
Turn_ON: команда включить от алгоритма нагревателя
timer2:BOOL ожидать разрешения на следующий импульс
t переменная запуска таймера 1
t переменная запуска таймера 2
t переменные разрешения работы таймеров
стандартные переменные функций таймера
IF intervaltime1 THEN
interval1:=SB_DT_DT(DT1 :=cur_time
IF TR_swithing_ON AND Turn_ON AND NOT timer2 THEN
ORGANIZATION_BLOCK OB1
Info: ARRAY[0..19] OF
END_ORGANIZATION_BLOCK
Технико - экономическое обоснование внедрения АСУ ЭЛТА
Автоматизация производства и производственных процессов как правило сопряжена со значительными финансовыми затратами в том числе на разра-ботку проекта приобретение технических средств на проведение подготови-тельных работ и подготовку персонала. Поэтому для того чтобы избежать необоснованных затрат и финансовых потерь ещё до внедрения систем автоматизации должно быть произведено экономическое обоснование целесообразности внедрения системы. Исходя из вышесказанного необходимо произвести расчет эффективности применения системы автоматизации.
Основными показателями определяющими экономическую целесообраз-ность затрат являются: ожидаемый годовой экономический эффект эконо-мическая эффективность капитальных вложений срок окупаемости капи-тальных вложений.
В данном проекте будет оценена экономическая эффективность проекта по внедрению системы автоматизации процесса термообработки для электро-термической линии ЭЛТА 845. Электротермическая линия предназначена для термической обработки металлических деталей используемых в автомобильной промышленности.
Целью внедрения данной системы является снижение экономических потерь связанных с браком а так же сокращение расходов на энергоресурсы.
Ожидаемые результаты внедрения:
–уменьшение влияния человеческого фактора на технологический процесс;
–сокращение количества продукции отправляемой в брак;
–повышение отказоустойчивости системы;
–исключение длительной перенастройки при необходимости внести изменения в параметры процесса термической обработки.
Факторы обуславливающие повышение эффективности системы:
–самостоятельная остановка работы электротермической линии при возникновении нештатной либо аварийной ситуации;
–возможность задания параметров техпроцесса с АРМ оператора;
–совершенная система самодиагностирования;
–более точное поддержание параметров процесса.
За базу для сравнения при расчете экономической эффективности примем процесс термообработки на существующем аналоге СКЗА 6-30 на котором отсутствует система автоматизации.
Основные источники данных для расчета:
–задание на проектирование системы АСУ ЭЛТА;
–результаты предпроектного обследования объекта автоматизации.
1 Исходные данные для расчета
В качестве исходных данных для расчета принимаются данные о затратах на разработку и внедрение системы данные о сроках разработки системы данные о функционировании разрабатываемой системы указанные в таблице 4.1.
Таблица 4.1 – Исходные данные для расчета затрат на разработку и внедрение системы
Условное обозначение
Оклад иниженера-программиста
Оклад главного инженера проекта
Оклад инженера пусконаладочных работ
Паспортная мощность рабочих станций в совокупности
Стоимость одного кВтч электроэнергии
Отчисления во внебюджетные фонды
Фонд социального страхования
Фонд обязательного медицинского страхования
Фонд страхования от несчастных случаев на производстве и профессио-нальных заболеваний
Число рабочих дней в месяце
Число рабочих дней в году
Продолжительность рабочего дня
Затраты на материалы
% от бал. Ст-ти оборудования
Расходы на транспортировку и установку оборудования
Таблица 4.1 - продолжение
Амортизация оборудования
Затраты на текущий ремонт оборудования
Балансная стоимость оборудования применяемого на этапе проектирования системы
Региональный коэффициент
Коэффициент готовности оборудования
Количество единиц вычислительной техники необходимых для разработки
Базовая стоимость комплекта оборудования необходимого для внедрения системы
Данные о сроках отводимых на разработку и внедрение системы приведены в таблице 4.2
Таблица 4.2 – Сроки на разработку и внедрение системы
Фонд рабочего времени отводимый на стадию
В том числе машин-ное время
сотруд-ников занятых на этапе
Предпроектный анализ
Разработка техни-ческого задания
Разработка техни-ческого обеспечения
Разработка программно-математического обеспечения
Пусконаладочные работы и сдача в эксплуатацию
Данные для расчета экономической эффективности приведены в таблице 4.3
Таблица 4.3 – Данные для расчета экономической эффективности.
Стоимость продукции обрабатываемой линией за год
% от стоимости обрабатываемой продукции
Расходы на обслуживание линии
Нормативный Коэффициент эффективности кап. вложений
2 Расчет экономической эффективности
2.1 Расчет временных затрат на разработку системы.
В течение срока работы над системой затраты времени инженера-программиста составили [4]:
Временные затраты главного инженера проекта на разработку проекта:
Временные затраты главного инженера проекта на внедрение проекта:
Временные затраты инженера ПНР на разработку системы:
Временные затраты инженера ПНР на внедрение системы:
где Танализ – время необходимое для анализа и изучения объекта
ТТЗ – время на разработку технического задания;
ТРТО – время необходимое для разработки технического обеспечения;
ТПО – время на разработку программно-математического обеспечения;
ТМО – время необходимое для монтажа оборудования;
ТПНР – время отводимое на пусконаладочные работы.
Таким образом подставив в формулы (4.1 – 4.5) значения из таблицы 4.2 получим:
2.2 Расчет затрат на разработку и ввод в эксплуатацию системы
Затраты на разработку системы можно определить из следующей формулы [4]:
где ЗЗПразраб – затраты на оплату труда;
Овнбф – отчисления во внебюджетные фонды;
Знакл – накладные расходы;
Зэвм – затраты на эксплуатацию ЭВМ.
В пункте 4.2.1 были определены временные затраты сотрудников проекта: главного инженера проекта инженера-программиста инженера пусконаладочных работ; используем полученные данные для расчета фонда заработной платы.
Расходы на заработную плату можно рассчитать по формуле:
где ОКЛпрогр – оклад инженера-программиста;
ОКЛПНР – оклад инженера ПНР;
Крег – региональный коэффициент;
СР прогр – срок работы инженера-программиста над проектом (мес.);
СРПНР – срок работы инженера ПНР над проектом (мес.);
Подставив исходные данные из таблицы 4.1 в формулу (4.7) определим расходы на заработную плату:
Отчисления во внебюджетные фонды рассчитаем по формуле:
где ОПФ – отчисления в пенсионный фонд;
Осоц – отчисления в фонд социального страхования;
Омед – отчисления в фонд обязательного медицинского страхования;
Онсп – отчисления в фонд страхования от несчастных случаев на производстве и профессиональных заболеваний.
Рассчитаем накладные расходы:
Затраты на эксплуатацию ЭВМ можно определить по следующей формуле:
где Смашч – себестоимость машино-часа;
ТЭВМ – машинное время необходимое для разработки проекта.
Машинное время необходимое для разработки системы определим по формуле: (4.10)
где – время работ на ЭВМ на стадии технического задания (дней);
– число сотрудников разрабатывавших техническое задание;
– время работ на ЭВМ на стадии разработки технического
– число сотрудников разрабатывавших техническое
– время работ на ЭВМ на стадии разработки ПО;
– количество сотрудников участвовавших в разработке ПО;
Праб.дн – продолжительность рабочего дня.
Себестоимость одного машино-часа определяется по формуле:
где Зобор – суммарные затраты за год связанные с содержанием и
эксплуатацией оборудования;
Fп – годовой фонд полезного времени;
Кгот – коэффициент готовности оборудования.
Для определения годового фонда полезного рабочего времени воспользуемся формулой:
где РДгод – число рабочих дней в году.
Таким образом годовой фонд полезного рабочего времени составит:
Суммарные затраты связанные с содержанием и эксплуатацией оборудования рассчитаем по следующей формуле:
где Змат – затраты на расходные материалы;
Аоборуд – величина амортизационных отчислений;
Зремонт – затраты на текущий ремонт;
Зээ – затраты на электроэнергию;
Зпрочие – затраты прочие.
Для определения затрат потребуется балансовая стоимость оборудования
Сбаланс – используемого для разработки которая определяется как сумма стоимости оборудования и затрат на его транспортировку и установку.
Из таблицы 6.1: Сбаланс= 214000 руб. Тогда затраты на эксплуатацию составят:
где М – суммарная мощность всего оборудования;
- стоимость одного кВтч электроэнергии;
Подставив имеющиеся данные (таблица 4.1) получим:
Подставляя полученные значения в формулу (4.13) получим годовые затраты связанные с содержанием и ремонтом оборудования:
Теперь стало возможным рассчитать стоимость одного машино-часа подставив полученные значения в формулу (4.11):
Величина себестоимости машино-часа при разработке АСУ ЭЛТА составит 43.8 руб.
Рассчитаем фонд машинного времени для разработки проекта:
Таким образом затраты на эксплуатацию ЭВМ составят:
Соответственно затраты на разработку системы составят:
2.3 Расчет затрат на внедрение системы
Затраты на внедрение систем определяются по формуле [4]:
где ФОТвн – фонд оплаты труда за период внедрения системы;
Овнбф.вн – отчисления во внебюджетные фонды за период внедрения;
Знакл.вн – накладные расходы при внедрении системы;
– стоимость базового комплекта оборудования необходимого для
В ходе внедрения затраты на применение ЭВМ пренебрежимо малы.
Для расчета ФОТвн – воспользуемся формулой:
Подставив табличные значения получим заработную плату сотрудников на внедрение:
Отчисления во внебюджетные фонды за период внедрения можно определить следующим образом:
Подставив данные из таблицы 6.1 в формулу получим:
Определим накладные затраты на внедрение системы:
Стоимость базового комплекта оборудования указана в таблице 4.1
Подставив полученные данные в формулу (4.22)
2.4 Расчет ожидаемой экономии по основным технико-экономическим показателям.
Условная годовая экономия за счет сокращения расходов на эксплуатацию определяется по формуле [4]:
где С1 – расходы на эксплуатацию по базовому варианту (таблица 4.3);
С2 – расходы на эксплуатацию по внедряемому варианту (таблица 4.3);
Таким образом получим:
Ожидаемая годовая экономия за счет сокращения потерь на брак:
где – стоимость продукции обрабатываемой электротермической
– коэффициент потерь на брак по базовому варианту;
– коэффициент потерь на брак по внедряемому варианту.
Подставив в формулу (4.24) данные из таблицы 4.3 получим:
Таким образом сложив экономию за счет сокращения расходов на эксплуатацию с экономией за счет сокращения брака получим суммарную годовую экономию:
2.5 Рассчет ожидаемого годового экономического эффекта
Ожидаемый годовой экономический эффект рассчитывается по формуле:
где Ен – нормативный коэффициент экономической эффективности:
К – величина капитальных вложений (затраты на создание и внедрение
Подставляя рассчитанные данные получаем:
Согласно формуле (4.25) получим:
2.6 Расчет коэффициента экономической эффективности и срока окупаемости
Коэффициент экономической эффективности Ер капитальных вложений на создание системы рассчитывается по формуле [4]:
Подставив в формулу имеющиеся данные получим:
Срок окупаемости капитальных вложений Т определяется по формуле:
Подсчитаем срок окупаемости капитальных вложений:
Таким образом срок окупаемости капитальных вложений составляет 2.2 года.
Сведем результаты экономической эффективности в таблицу 4.4.
Таблица 4.4 – Результаты расчетов экономической эффективности
Затраты на создание системы
Затраты на внедрение системы
Ожидаемый годовой экономический эффект
Расчетный коэффициент экономической эффективности
Расчетный срок окупаемости капитальных вложений
Расчетный показатель экономической эффективности должен быть выше нормативного коэффициента эффективности капитальных вложений [4].
Таким образом Ер больше Ен (0.44>0.2) Тр ниже Тн (2.25)
Сравнив расчетные и нормативные коэффициенты экономической эффективности и сроки окупаемости можно сделать вывод что внедрение АСУ ЭЛТА является целесообразным.
Современное машиностроение невозможно представить без операции термической обработки таких как отжиг закалка; химико-термических (азотирование науглероживание и т.д.); деформационно-термических (высокотемпературная прокатка). Однако цех в котором производятся операции термообработки является зоной повышенного риска.
Проектируемая в проекте АСУ предназначена для управления электротермической линией на которой выполняются операции термической обработки металлических крепёжных изделий. Электротермическая линия состоит из двух электрических печей (закалочной и отпускной) бака закаливания и бака охлаждения загрузочного устройства и конвейеров.
Очевидно что данный комплекс является источником множества вредных и опасных факторов способных негативно повлиять на здоровье работников цеха либо стать причиной несчастного случая. Поэтому обеспечения безопасных условий труда в термическом цехе является наиболее важным аспектом при организации цеха.
–обеспечение безопасных условий труда в термическом цехе.
–определение тепловыделения в термическом цехе;
–определение необходимого воздухообмена и способов его организации в помещениях термического цеха;
–расчет местной приточной и вытяжной вентиляции в термическом цехе.
1 Опасные факторы возникающие в процессе термической обработки.
Опасные и вредные факторы возникающие при термической обработке изделий обусловлены её видом применяемым оборудованием и рабочими средствами. Оборудование применяемое при термической обработке является мощным источником энергии (инфракрасного излучения) [3]. Интенсивность излучения энергии различными устройствами термообработки представлено в таблице 5.1
Таблица 5.1. – Интенсивность излучения энергии устройствами термического цеха
Рабочее место операция
Закалочно-отпускной агрегат загрузка
Закалочно-отпускной агрегат выгрузка
Ванные с электронно-соляным подогревом (T=1550 К)
Шахтные цементационные электропечи печи ванны с электродно-соляным подогревом (T=1120-1170 К) тигельные печи-ванные с газовым подогревом
Вертикальная закалочная печь подъем деталей
Маслянные закалочные ванные селитровые и щелочные ванные с газовым подогревом шахтные отпускные электропечи камерные газовые печи с выдвижным подом
В процессе химико-термической обработки возможно образование ядовитых соединений (например цианистых соединений аммиака нитробензола паров свинца) что может нанести вред здоровью персонала выполняющего работу в цехе.
В термическом цехе может существовать опасность возникновения пожара или взрыва при применении масел при работе с контролируемыми
атмосферами с соляными щелочными печами и ванными. Особую опасность представляет система масло-кислород (воздух) когда масло при перегреве подвергается термическому разложению и образуются углеродные фракции [13].
Сведения характеризующие свойства закалочных масел представлены в таблице 5.2.
Таблица 5.2. – Свойства закалочных масел.
Плотность при температуре
Так же источником взрывоопасности являются водоохлаждаемые узлы так как при неисправностях герметичность их нарушается и вода попадает в рабочее пространство печи; под действием высокой температуры она интенсивно испаряется поэтому в результате повышения давления в печи может произойти взрыв; иногда вода разлагается а при попадании воздуха в печи может образоваться гремучая смесь.
2 Обеспечение безопасной работы в условиях термического цеха
Меры безопасности при работе в термическом цехе регламентируются ГОСТ 12.3.004-75 «Термическая обработка металлов. Общие требования безопасности» [13].
Согласно данному стандарту в термическом цехе участки травления металлов цианирования жидкостного азотирования и свинцовых печей-ванн а так же участки подготовки твердого карбюризатора диффузной металлизации и борирования должны быть отделены от других участков цеха термической обработки металлов.
При термической и химико-термической обработке должны применятся масла кислоты щелочи и другие химические вещества на которые утверждена нормативно-техническая документация.
Ядовитые соли для термической обработки должны использоваться в гранулированном виде. Кислоты и щелочи легко воспламеняющиеся и горючие жидкости используемые в количестве более 400 кг в рабочую смену должны подаваться к рабочим местам по трубопроводам. Погрузка изделий и деталей массой свыше 20 кг и разгрузка их должны осуществляться погрузочно-разгрузочным устройством.
Помещения термических цехов термическое оборудование и коммуникации должны быть оснащены контрольно-измерительными приборами для контроля уровня опасных и вредных производственных факторов возникающих при данном процессе.
В местах возможной локализации действия опасных и вредных производственных факторов (участки на газопроводах на линиях сжатого воздуха) должны быть установлены быстродействующие отсекающие устройства.
Предельно допустимая напряженность электромагнитных полей (ЭМП) на рабочих местах и в местах возможного нахождения персонала связанного с применением ВЧ-энергии для промышленной термообработки не должна превышать в течение рабочего дня по электрической составляющей Вм: 50–
для частот от 60 кГц до 3 МГц 20 -– для частот от 3 до 30 МГц 10 – для частот от 30 до 50 МГц 5 – для частот от 50 до 300 МГц; по магнитной составляющей Ам: 5 – для частот от 60 кГц до 15 МГц 03 – для частот от 30 до 50 МГц.
При обслуживании установок для высокочастотного нагрева металла (ламповые и машинные генераторы) необходимы мероприятия по электробезопасности и защите от длинноволнового излучения. Экранировку источников излучения следует проводить при помощи замкнутых камер из листового железа или мелкой металлической сетки.
Санитарно-эпидемиологические станции и лаборатории чистоты воздух при отделе технической безопасности предприятия должны регулярно проводить анализы воздуха на содержание в нем цианистых соединений щёлочи свинца СО углеводородов масляного аэрозоля и др.
Для предотвращения образования взрывоопасных смесей на печах с периодически открываемыми проемами применяются пламенные завесы. Если это нецелесообразно (большие размеры проемов большая тяга) то необходимо предусмотреть установку запальных горелок обеспечивающих воспламенение контролируемой атмосферы.
Для защиты замкнутых объёмов от разрушения давлением при его возрастании необходимо применять взрывные (предохранительные) клапаны.
Предупреждение пожаро и взрывоопасных ситуаций при работе с закалочными маслами достигается в результате правильного выбора марки масла и режима работы. Эффективным средством тушения пожара вызванного возгоранием масла могут быть кислотные огнетушители) и не загрязняют закалочное масло). На больших масляных ваннах целесообразно создавать «углекислотный душ».
Эффективны автоматические противопожарные устройства и системы подавления взрывов.
Наиболее важным при организации безопасной работы в термическом цехе является правильная организация вентиляции. Вентиляция – это
организованный воздухообмен заключающийся в удалении из рабочего
помещения загрязненного воздуха и подача вместо него свежего наружного или очищенного воздуха. Кроме того вентиляция выполняет функцию удаления избытка выделяемой нагретыми поверхностями энергии.
В ряде случаев необходимо использовать различные экраны защищающие рабочего от прямого воздействия лучистой энергии и воздушные души.
Существенным фактором улучшения условий труда является организация специальных зон отдыха имеющих благоприятный микроклимат и систему радиационного охлаждения.
Для обеспечения требуемых метеорологических условий в помещениях термических цехов предусматривается местная и общеобменная вентиляция.
Вентиляция – это организованный воздухообмен заключающийся в удалении из рабочего помещения загрязненного воздуха и подача вместо него свежего наружного или очищенного воздуха.
Различают следующие виды местной вентиляции:
–отсасывающие панели;
Схемы вентиляции рекомендуемые для применения в термическом цех указаны в таблице 5.3.
Необходимый воздухообмен в помещениях термических цехов рассчитывается из условий ассимиляции тепла для трех периодов года.
Достаточность воздухообмена для зимнего времени года рекомендуется проверять по разбавлению поступающих в цех вредных веществ исходя из их содержания в воздушной среде цеха и эффективности применяемых средств защиты.
Таблица 5.3 – Схемы вентиляции применяемые в термическом цехе
Отделение цеха оборудование
Основные вредные факторы
Приточная вентиляция
Тепло продукты сгорания топлива пары углеводородов
Местные отсосы и вытяжная вентиляция
Естественная Естественная
Воздушное душирование на рабочих местах
камерные щелевые печи
Скорость воздуха в откры-том проеме не менее 0.7 мс;
расход воздуха 3000 на 1 м пода печи
Нагревательные камерные печи
Скорость воздуха в откры-том проеме не менее 0.8 мс;
расход воздуха 4000÷5000 на 1 м пода печи
Загрузки и выхода деталей
Скорость отсасываемого воздуха не менее 3 мс; расход воздуха 2680
3 Методы расчета местной вентиляции в термическом цехе
Расчет необходимого количества воздуха для помещений с тепловыделением производится по избыткам явного тепла; для помещений с тепло и влаговыделениями – по избыткам явного тепла влаги и скрытного тепловыделения; для помещений с газовыделением – по количеству выделяющихся вредных веществ (из условия обеспечения концентраций ниже предельно допустимых) [13].
Тепловыделение от электрических печей и ванн определяют по формуле:
значение коэффициента следует принимать 03 для электрованн для печей камерных с подвижным подом – 0.45; с неподвижным подом – 0.5; для щелевых и шахтных печей – 0.4; для электрических печей 0.7. При оборудовании печей местными вытяжными устройствами тепловыделение в помещении должно составлять 30% от рассчитанных по формулам.
Расчет необходимого количества воздуха производится по следующим зависимостям:
при расчете по избыткам явного тепла
где – количество воздуха удаляемого из рабочей или обслуживаемой зоны
помещения местными отсосами который затрачивается на
технологические и иные нужды;
– избыток явного тепла в помещении;
массовая удельная теплоёмкость воздуха равная 1 ;
– плотность поступающего воздуха равная 1.2 ;
– температура воздуха удаляемого из рабочей или обслуживаемой
зоны помещения местными отсосами который используется на
технологические и другие нужды;
– температура воздуха подаваемого в помещение;
– температура воздуха удаляемого из помещения за пределы рабочей
или обслуживаемой зоны;
при расчете по избыткам полного тепла
где – теплосодержание воздуха удаляемого из рабочей или обслуживаемой
технологические или другие нужды ;
– теплосодержание воздуха подаваемого в помещение и удаляемого
из него за пределы рабочей или обслуживаемой зоны ;
при расчете по избыткам влаги
где – избыток влаги в помещении ;
– влагосодержание воздуха удаляемого из рабочей или
обслуживаемой зоны помещения местными отсосами который
затрачивается на технологические и другие нужды ;
– влагосодержание воздуха подаваемого в помещение ;
– влагосодержание воздуха удаляемого за пределы рабочей или
обслуживаемой зоны ;
при расчете по количеству выделяющихся вредных веществ
где – количество вредных веществ поступающих в воздух помещения
– концентрация вредных веществ в воздухе удаляемом из рабочей
или обслуживаемой зоны местными отсосами который используется
на технологические и иные нужды ;
– концентрация вредных веществ в воздухе удаляемом из
помещения за пределы рабочей или обслуживаемой зоны ;
– концентрация вредных веществ в воздухе подаваемом в
Параметры воздуха поступающего в приемные отверстия и проемы местных отсосов технологических и других устройств которые расположены в рабочей и обслуживаемой зоне помещения следует принимать в соответствии с ГОСТ 12.1.005-76 [3].
Для обеспечения воздухообмена помещения термического цеха согласно схеме из таблицы 5.3 используем: воздушные души зонты - козырьки.
Для расчета воздушного душирования используют следующие правила [13]:
)ПО СН 245-71 определяют допустимую скорость и температуру воздуха на рабочем месте.
)Определяют скорость выхода воздуха из насадка по формуле:
где и – скорость воздуха в рабочей зоне и на выходе из душирующего
и – температура воздуха в помещении рабочей зоне и
приточного воздуха соответственно.
)Используя расчетные зависимости для осесимметричной струи определяют диаметр душирующего патрубка и его площадь:
где – средняя скорость воздуха на расстоянии S мс;
– расстояние от насадка до рабочего места;
– диаметр душирующего патрубка;
- коэффициент турбулентной структуры струи его значение принимается в пределах 006 - 012 (в зависимости от конструктивных особенностей душирующего патрубка).
) Определяются размеры душирующего факела в зоне рабочего места по формуле:
где – диаметр душирующего факела на расстоянии S от насадка .
) Определяется количество воздуха на выходе из душирующего патрубка по формуле:
где – площадь сечения на выходе из душирующего патрубка .
) Вычисляется расход воздуха в душирующем факеле на заданном от
душирующего патрубка расстоянии по формуле:
где и – расход воздуха на выходе из насадка и на расстоянии S от него.
) Количество эжектируемого струей воздуха вычисляется по формуле:
) Составляется уравнение теплового равновесия:
Из уравнения (5.11) определяют и сравнивают его с заданным. Сравниваемые значение не должны сильно отличатся друг от друга что и свидетельствует о верности вычислений.
Расчет вытяжных зонтов производится следующим образом:
Для эффективной работы зонта количество воздуха удаляемого через него
должно превышать количество воздуха переносимое конвективной струей которая образуется над источником тепла на уровне расположения зонта. В соответствии с рекомендацией количество воздуха подтекающее к зонту с конвективной струей которая возникает над тепловым источником прямоугольной или круглой формы при отношении сторон источника плане
может быть определена по формуле:
где – количество тепла выделяемого источником путем конвекции ;
z – расстояние от нагретой поверхности до воздухоприемного сечения
F – площадь источника .
Значение Q определяют следующим образом:
где – коэффициент конвективной теплоотдачи;
и – температура поверхности источника и температура окружающего
воздуха соответственно ºС.
Коэффициент конвективной теплоотдачи определим из следующей формуле:
Расход воздуха удаляемого зонтом определяется по формуле:
где – площадь сечения зонта;
– площадь входного сечения зонта определяемая из условия .
У загрузочных отверстий печей сушил и другого оборудования для улавливания продуктов сгорания устанавливаются зонты в виде козырьков.
Расход воздуха поступающего из открытого проема печи под зонт козырек может быть рассчитан по формуле:
где – коэффициент расхода принимаемый обычно равным 0.65;
F – площадь проема ;
Δρ – избыточное давление под влиянием которого газы выходят из печи
ρ – плотность газовой среды в печи .
Вылет зонта следует принимать равным примерно удвоенной высоте проема печи а ширину зонта – равной ширине проема плюс по 0.1 с каждой его стороны.
Среднее избыточное давление определяется следующим образом:
где ρв – плотность воздуха в помещении ;
h – высота проема печи м;
g – ширина проема печи м.
4 Расчет вентиляции цеха.
В цехе располагается 25 электротермических линии. На каждую линию потребуется два воздушных зонта (для загрузочных проемов печей) и воздушный душ для рабочего места оператора.
Произведем расчет для одной линии.
Энергия выделяемая одной линией вычислим по формуле (5.1):
Расчет будем производить для летнего периода. Рассчитаем необходимое количество воздуха по избыткам явного тепла применим формулу (5.2):
Рассчитаем необходимое количество воздуха по выделению вредных веществ (формула 5.5):
Для дальнейших расчетов выберем большее значение то есть L1.
Определим скорость воздуха на выходе из душирующего патрубка
используем для этого формулу (5.6):
Из формулы (5.7) определи диаметр душирующего патрубка:
тогда площадь сечения на выходе:
Расход воздуха на выходе из патрубка согласно (5.9):
Расход воздуха в душирующем факеле в рабочей зоне (формула 5.10):
Количество эжектируемого струей воздуха:
Составим уравнение теплового баланса душирующего факела и из него:
что близко к заданному значению 24ºС следовательно расчет произведен верно.
Произведем расчет для зонтов линии:
Примем вылет зонта равным 1.4 м а ширину 1.2 м. Из формул (5.17 и 5.18) определим :
для закалочной печи:
Таким образом в данном разделе дипломного проекта автором рассмотрены вопросы безопасности труда в термическом цехе основные опасные и вредные факторы возникающие в процессе производства и методы борьбы с ними.
При анализе производства с точки зрения безопасности жизнедеятельности особо опасной является химико-термическая обработка. В ходе процессов выделяются вредные вещества: аэрозоли кислот аэрозоли щелочей цианистые соединения а так же пары масла. Для их улавливания используется местная вентиляция.
В результате работы над разделом:
–была рассмотрена схема вентиляции термического цеха;
–определено тепловыделение в рассматриваемом цехе;
–произведен расчет местной приточной и вытяжной вентиляции (воздушные души и зонты).
В дипломном проекте разработана АСУ электротермической линии ЭЛТА 845 предназначенная для управления процессом закалки металических изделий автомобильной промышленности.
В проекте произведен анализ проблемной ситуации анализ технологического процесса как объекта управления разработана структура АСУ и составлено техническое задание. Были проанализированы тепловые процессы протекающие в печах электротермической линии. В разделе техническое предложение были выбраны принципы управления устройствами электротермической линии управления температурой в печах и управления скоростями конвейеров электротермической линии а также техническое и программное обеспечение для их реализации. Произведен синтез алгоритмов логического управления устройствами линии реализована система визуализации технологического процесса в SCADA WinCC 6.0. Результаты разработки системы соответствуют требованиям ТЗ.
В разделе технико-экономическое обоснование внедрения АСУ ЭЛТА сравниваются экономические показатели эксплуатации электротермической линии ЭЛТА 845 на которой применена АСУ ЭЛТА и её аналога термоагрегата СКЗА 6-30. Определен коэффициент экономической эффективности внедрения АСУ ЭЛТА.
В ходе работы над разделом безопасность и экологичность проекта произведен анализ вредных и опасных факторов термического цеха рассчитаны необходимый воздухообмен в термическом цехе и параметры местной вентиляции требуемые для обеспечения безопасных условий труда в термическом цехе.
В работе использованы следующие программные пакеты: MicroSoft Word MicroSoft Excel AutoCad 2004 MatLab 7.03 Simatic Step 7 Scada WinCC 6.0. Для технической реализации применено оборудование производства компании
Siemens. Результаты проекта применены в проекте АСУ ЭЛТА 425270.003 разрабатываемом в инженерно-производственной фирме «АСУПРОМ».
Справка об анализе патентной литературы
по теме дипломного проектирования
Технические данные частотных преобразователей MicroMaster
Основные особенности
–простой пуск в эксплуатацию;
–бесшумная работа двигателя благодаря высокой частоте импульсов;
–полная защита двигателя и преобразователя;
–фильтры EMC в том числе для использования в жилых зданиях;
–дроссели коммутации сети;
–базовая панель оператора Bas
–комфортная панель оператора Advanced Operator Pane
–модуль коммуникаций PROFIBUS-DP.
–высококачественное векторное управление в том числе с использованием импульсного датчика скорости;
–регулирование прямым током (FCC) для наилучших динамических характеристик и оптимального управления двигателем
–Uf-управление линейное квадратичное параметрируемое;
–управление моментом;
–режим низкого потребления энергии;
–"подхват на ходу" – замена вышедшего из строя преобразователя другим включенным параллельно без остановки двигателя;
–компенсация скольжения;
–автоматический повторный запуск при пропадании сети или нарушениях режима работы;
–высококачественный PID контроллер (с авто- настройкой) для простого управления производственными процессами;
–параметрируемое время разгона и торможения в пределах 0 650 секунд;
–быстродействующее токоограничение (FCL) для безаварийной работы;
–точный ввод заданного значения благодаря 10-битному аналоговому входу;
–комбинированный тормоз для контролируемого быстрого останова;
–4 частоты пропускания.
Преобразователь MicroMaster 410 выпускается на однофазное напряжение 220 В и трехфазное 200 380 500В. Отличается большим диапазоном сетевого напряжения.
Основные технические характеристики:
–Напряжение питания: 1АС 200 В 240 10 % 1АС 100 В 120В 10 %;
–Частота сети 47 Гц 63 Гц M
–Выходная частота 0 Гц 650 Гц;
Диапазон мощностей 012 кВт 075 кВт 1АС 200 В 240 10 % 012 кВт 055 кВт 1АС 100 В 120В 10 %;
Преобразователь MicroMaster 420 выпускается на однофазное напряжение 220 В и трехфазное 200 и 380 В. Отличается высокой производительностью и удобством использования. Пульт управления и модули PROFIBUS могут быть заменены без применения какого либо инструмента.
–напряжение питания: 1АС 200 В 240 10 % 3АС 200 В 240 В 10 % 3АС 380 480 В 10%;
–частота сети 47 Гц 63 Гц MICROMASTER 410;
–Диапазон мощностей 012 кВт 3 кВт 1АС 200 В 240 10 % 012 кВт 55 кВт 3АС 200 В 240 В 10 % 037 кВт 11 кВт 3АС 380 480 В 10%;
параметрируемые потенциально развязанные переключаемые PNPNPN
для задания или вход PI(0 10 В Масштабируемый или используемый в качестве 4-го цифрового входа)
параметрируемый(0 20мА)
программируемый DC 30 V5 А (омическая нагрузка)АС 250 V2 A(индуктивная нагрузка)
Преобразователь MicroMaster 440 выпускается на однофазное напряжение 220 В и трехфазное 200 380 500В . Отличается большим диапазоном сетевого напряжения.
Основные технические характеристики:
–сетевое напряжение и диапазон мощностей:
АС 200 240В10 %012 кВт 3 кВт -
АС 200 240 В10 %012 кВт 45 кВт 55 кВт 45 кВт
АС 380 480 В 10%037 кВт 200 кВт 75 кВт 250 кВт
АС 500 600 В10% 075 кВт 75 кВт 15 кВт 90 кВт;
–частота сети: 47 Гц 63 Гц;
–выходная частота: 0 Гц 650 Гц;
–цифровые входы: 6 параметрируемые потенциально развязанные переключаемые
–аналоговый вход: 2 вход 0 10 В 0 20мА и -10 В +10 В вход 0 10 В и 0 20 мА;
–аналоговый выход: 1 параметрируемый (0 20мА);
–релейный выход: 1 программируемый DC 30 V5 А (омическая нагрузка) АС 250 V2 A(индуктивная нагрузка).
Башарин А.В. Новиков В.А. Соколовский Г.Г. Управление электроприводами: Учебное пособие для вузов. – Л.: Энергоиздат. Ленингр. Отд-ние 1982.-392 с.
Бергер Г. Автоматизация посредством Step 7 с применением SCL и STL и программируемых контроллеров Siemens – 2001г.- 421 c.
Безопасность жизнедеятельности: Учебник для средних специальных учебных заведений. Под общей редакцией С.В. Белова. – 3-е издание исправленное и дополненное – М.: Высшая школа 2003. – 357 с.
Геворкян - Карасева Г.Д. Экономика и организация производства в дипломных проектах на технических специальностях – М.: Высшая школа 1997.-328 с.
Ицкевич Э. Трапезников В.А Как выбирать контроллерные средства ТСА
Крючков В.Г. Построение информационных портретов объектов программного управления Автоматизированные технологические и мехатронные системы в машиностроении. . Сб. науч. трудов УГАТУ. Уфа 1997 78 c.
Методические указания по выполнению выпускной квалификационной работы специалиста для студентов специальности 210200 «Автоматизация технологических процессов и производств». Требования к составу и содержанию выпускной квалификационной работы. Правила оформления пояснительной записки Уфимск. Гос. Авиац. Техн. Ун-т; Сост Крючков В.Г. Никин А.Д. Чугунова О.И. 2000. – 25 с.
Методические указания по выполнению выпускной квалификационной работы специалиста для студентов специальности 210200 «Автоматизация технологических процессов и производств». Организация выполнения и защиты выпускной квалификационной работы Уфимск. Гос. Авиац. Техн. Ун-т; Сост Крючков В.Г. Никин А.Д. Чугунова О.И. 2000. – 33 с.
Методические указания по оформлению графической части курсовых и дипломных проектов для студентов специальности 210200 «Автоматизация технологических процессов и производств». Уфимск. Гос. Авиац. Техн. Ун-т; Сост Крючков В.Г. Никин А.Д. Чугунова О.И. 2000. – 31 с.
Михайлов О.П. Стоколов В.Е. Электрические аппараты и средства автоматизации. Учебник для вузов. – М.: Машиностроение 1982. – 183 с.
Родштейн Л.Л. Электрические аппараты: Учебник для техникумов –четвертое издание переработанное и дополненное. Л. Энергоатомиздат 1989.- 304 с.
Советов Б.Я. Яковлев С.А. Моделирование систем – М. Высшая школа 1985. – 372 с.
Справочная книга по охране труда в машиностроении. Под ред. Русакова О.Н. – Л.: Машиностроение 1989. – 541 с.
Теория автоматического управления. Под ред. Нетушила А.В.. Изд.2-е. - М. Высшая школа 1976. – 486 с.
Усатенко С.Т. Каченюк Т.К. Терехова М.В.. Выполнение электрических схем по ЕСКД – М. Издательство стандартов 1992. – 172 с.
Чикуров Н.Г.. Курс лекций по дисциплине «Моделирование систем управления» - учебное пособие. Уфа. УГАТУ 2001- 146 с.
Чикуров Н.Г. Логический синтез дискретных систем управления – учебное пособие. Уфа. УГАТУ2003 –132 с.
Simatic. Комплексная автоматизация производства. – М.: Каталог Siemens 2005. – 436 с.
Simatic HMI. WinCC 6.0 Начало работы: Руководство пользователя 2005.- 108 с.
Harel D. Statechart: A VISUAL FORMALISM FOR COMPLEX SISTEMS
Ведомость OSS._5cdw.cdw

силовым режимом процесса механической
обработки на станках с ЧПУ
Ведомость дипломной работы
Алгоритмы работы устроиств
программная реализация
Мнемосхема электротермической
Структура программного
обеспечения АСУ ЭЛТА
Внесенные изменения.doc
В связи с повышением технических требований качеству металлических деталей производимых для автомобильной промышленности увеличился процент изделий не удовлетворяющих данным требования и следовательно относимым к браку. В технологическом процессе их изготовления можно отметить что наибольшее количество брака появляется на завершающей стадии технологической операции а именно в процессе закалки. Чтобы определить причины порождающие данное явление для этого необходимо рассмотреть технологический процесс. Процесс закалки состоит из следующих стадий: закалка мойка и сушка отпуск. Для того чтобы обеспечить высокое качество продукции требуется тщательное соблюдение технологического процесса. Время и температура нагрева должны выдерживаться с точностью до долей процента также требуется тщательно отслеживать состояние технических средств на которых производиться термическая обработка. Однако большинство применяемых сегодня систем не способны обеспечивать заданную точность. Кроме того качество обрабатываемой продукции зависит от человеческого фактора. Оператор контролирующий выполнение технологического процесса не может отслеживать все множество параметров от которых зависит процесс ввиду того что занимаясь длительной и монотонной работой быстро становится невнимательным.
Другая проблема быстрое устранение неисправностей возникающих в процессе работы технических средств и длительная переналадка оборудования при необходимости внести изменения в процесс.
Тем не менее на сегодняшний день уже созданы технический средства при помощи которых возможно решить указанные проблемы.
Применение АСУ (Автоматизированной Системы Управления) может
обеспечить нормальный ход непрерывно протекающих процессов в системе управления процессом термообработки освободит оператора от непосредственного выполнения функций управления процессом за счет передачи этих функций автоматическим устройствам. Сегодня системы автоматизации строятся преимущественно на базе промышленных контроллеров. Это обусловлено их высокой надежностью и возможностью организовать систему визуализации техпроцесса что в свою очередь позволяет тщательно контролировать процесс быстро обнаруживать и устранять неисправности возникающие в процессе работы. Таким образом внедрив систему автоматизации на основе программируемого логического контроллера можно решить задачу поддержания постоянства параметров техпроцесса снизить роль человеческого фактора в процессе термообработки сократить время требуемое для устранения неисправностей возникающих в процессе работы системы.
В данной работе разработана система автоматического управления электротермической линии ЭЛТА 845 и проанализированы процессы нагрева протекающие в электрических печах. Внедрение данное системы позволит повысить качество продукции обрабатываемой на электротермической линии облегчит эксплуатацию электротермической линии.
Целью данной работы является анализ процесса нагрева как процесса управления моделирование процесса нагрева на ЭВМ. Построение системы автоматического поддержания постоянства температур в печах. Синтез алгоритмов управления устройствами электротермической линии. Программная реализация алгоритмов работы устройств входящих в состав ЭЛТА 845.
2 Назначение и цели создания системы .
2.1 Назначение системы ..
2.2 Цели создания системы .
3 Характеристики объекта автоматизации
3.1 Общие сведения об объекте автоматизации
3.2 Сведения об условиях эксплуатации
4 Требования к системе
4.1 Требования к структуре и функционированию системы ..
4.2 Требования к функциям системы ..
4.3 Требования к видам обеспечения ..
Техническое предложение
1 Выбор методов управления .
2 Выбор технического обеспечения ..
3 Выбор программного обеспечения и структуры программного обеспечения проекта
4 Разработка структурных схем КТС
5 Визуализация технологического процесса
Разработка математической модели синтез и программная реализация алгоритмов работы закалочной печи
1 Исследование тепловых процессов в закалочной печи .
1.1 Построение модели нагрева закалочной печи .
Современные преобразователи частоты являются интеллектуальными устройствами использующими микроконтроллеры достаточно высокой производительности в современных преобразователях имеется ряд дополнительных опций и расширений позволяющих создавать несложные системы автоматического управления без использования контроллеров.
Рассмотрим подробнее ряд таких расширений которые есть практически во всех современных преобразователях частоты.
Аналоговые выходы - позволяют наглядно представить значение какого-нибудь параметра. Однако использования их в системах автоматизации нецелесообразно так как они как правило имеют малую мощность и неудовлетворительное качество.
Аналоговые входы - позволяют подавать сигналы от датчиков напрямую в преобразователь частоты без использования каких-либо дополнительных устройств. Как правило используются унифицированные типы сигналов (0 – 5 В 0 – 10 В 4 – 20 мА) так что согласующие устройства не требуются. Кроме того имеется возможность использования внутреннего питания преобразователя для подключения потенциометра например для задания частоты вращения.
Дискретные входы - позволяют управлять преобразователем частоты с кнопок установленных на лицевой панели шкафа или с поста управления.
Дискретные выходы - используются для сигнализации режимов работы преобразователя.
В современных преобразователях предусмотрена возможность подключения его в промышленную сеть. Обычно используется протокол RS-485. Соединение преобразователей в сеть позволяет построить более сложную систему автоматического управления технологическими процессами с использованием контроллеров и промышленных компьютеров.
К достоинствам современных частотных преобразователей можно отнести ниже перечисленные факторы.
Плавное регулирование скорости вращения электродвигателя позволяет в большинстве случаев отказаться от использования редукторов вариаторов дросселей и другой регулирующей аппаратуры что значительно упрощает управляемую механическую (технологическую) систему повышает ее надежность и снижает эксплуатационные расходы.
Частотный пуск управляемого двигателя обеспечивает его плавный без повышенных пусковых токов и механических ударов разгон что снижает нагрузку на двигатель и связанные с ним передаточные механизмы увеличивает срок их эксплуатации. При этом появляется возможность по условиям пуска снижения мощности приводных двигателей нагруженных механизмов.
Встроенный микропроцессорный ПИД-регулятор позволяет реализовать системы регулирования скорости управляемых двигателей и связанных с ним технологических процессов.
Применение обратной связи системы с частотным преобразователем обеспечивает качественное поддержание скорости двигателя или регулируемого технологического параметра при переменных нагрузках и других возмущающих воздействиях.
Частотный преобразователь в комплекте с асинхронным электрическим двигателем может применяться для замены приводов постоянного тока.
Частотный преобразователь в комплекте с программируемым микропроцессорным контроллером может применяться для создания многофункциональных систем управления электроприводами в том числе с резервированием механических агрегатов. Таким образом возможно добиться точного поддержания скорости двигателя используя только возможности микропроцессорного частотного преобразователя.
2 Выбор технического обеспечения
В настоящее время автоматизация любых производственных процессов выполняется на базе универсальных микропроцессорных контроллерных средств [5]. Это обусловлено следующими факторами:
–использование готовых технических средств устранит необходимость их проектирования;
–микропроцессорные системы отличаются высокой надежностью;
–сокращается время проектирования системы;
–унифицируется элементная база систем управления
Существуют следующие варианты технических решений при построении системы управления на базе микропроцессорной техники:
–система управления на базе персонального компьютера;
–система управления на базе локального контроллера PLC (programmable log
–сетевой комплекс контроллеров (PLC Network);
–полномасштабные распределенные системы управления (DCS Full Scale).
Для построения системы управления электротермической линией целесообразно использовать система управления на базе локального контроллера PLC это связанно с тем что система управления на базе персонального компьютера не обладает достаточными возможностями для управления электротермической линией сетевой комплекс и распределенная система управления напротив применяются для более сложных объектов и слишком дороги.
Поскольку система будет располагаться в термическом цехе контроллеры должны быть пригодны для работы при температуре до 45 ºС. Так как для управления температурой решено применить широтно-импульсное управление необходимо чтобы на базе применяемого контроллера возможно было организовать управляемый широтно-импульсный модулятор.
Можно отметить что российский рынок на сегодняшний день предлагает достаточно широкий диапазон контроллерных средств среди них можно назвать контроллеры компаний Siemens и Advantech Mitsubishi.
Для построения системы управления целесообразно применить контроллеры Siemens [18]. Это обусловлено их высокой надежностью простотой программирования приемлемой стоимостью и доступностью. Для наших целей применимы контроллеры серий S-300 и S-400.
Для объектов автоматизации средней сложности к которым относится и ЭЛТА 845 можно выбрать один из контроллеров серии S-300 контроллеры серии S-400 стоят дороже и применяются в основном для сложных объектов (объектов с большим количеством сигналов) в нашем случае их применение было бы необоснованным. Контроллеры S-300 имеют модульное построение и могут включать в свой состав следующие компоненты:
–стойки (RACK) служащие для размещения модулей и соединения их между собой;
–блок электропитания (Power Supp
–центральное процессорное устройство (Central Process
–сигнальные модули (S
–функциональные модули (Funct
–коммуникационные процессоры (Communication Processor CP)
устанавливает соединение с вспомогательными сетями (подсетями);
–подсети (Subnets).
Для организации интерфейса обмена данными между контроллером и автоматизированным рабочим местом воспользуемся стандартным протоколом семейства Simatic S7 PROTOCOL SUITE.
В качестве операционной системы на АРМ оператора применим Windows XP.
Структура программного обеспечения представлена на рисунке 2.13.
Рисунок 2.14 – Структура программного обеспечения АСУ ЭЛТА
4 Разработка структурных схем КТС
Структурная схема представлена на чертеже 2021.082.000001.С1 включает в себя следующие элементы:
A 1.0 – модуль ввода дискретных сигналов в контроллер;
A 2.0 – модуль вывода дискретных сигналов контроллера;
B 1 – оптосемистор выполняет функции гальванической развязки между цепью контроллера и цепью нагревателя;
EK1 EK3 – нагревательные элементы;
KM 1- катушка контактора выполняет функцию коммутации цепи нагревателя;
KM 1:1 4 – контакты контактора KM 1;
K 1– катушка реле предназначена для гальванической развязки силовых цепей и цепей управления;
K 1:1 – контакт реле K 1 при замыкании данного контакта на дискретный вход поступает сигнал;
QF 1 – автоматический выключатель выполняет функцию защиты цепи нагревателя;
TA 1 TA 3 – измерительные трансформаторы тока;
TV 1 – понижающий трансформатор напряжения 38042 В;
X 1:1 – X 2:6 – клеммные контакты;
VS 1 – VS 3 – семисторы предназначены для управления нагревателями.
Структурная схема 2021.082.000002.С1 включает в себя следующие элементы:
A 3.0 – модуль ввода аналоговых сигналов в контроллер;
A 4.0 – модуль вывода аналоговых сигналов из контроллера;
A 5.0 – блок управления семисторами и тиристорами;
R 2 – резистор предназначен для преобразования сигнала на входе в БУСТ;
SF 1 – автоматический выключатель вибратора выполняет функцию защиты
X 2:1 X 6:2 – клеммные контакты;
Y 1- катушка электромагнита вибратора 3;
VS 4 – семистор управления вибратором;
UA 1 – нормализатор сигнала преобразует сигнал 0÷5 А во входную величину модуля аналоговых входов 4÷20 мА.
5 Визуализации технологического процесса
Визуализация технологического процесса позволит отобразить о работе устройств системы в удобной для оператора наглядной форме. Для этого применимы мнемосхемы линии с изображением основных устройств входящих в ЭЛТА 845. На экране панели оператора целесообразно отображать текущие значения параметров системы: скорости конвейеров в печах температуры и уровни жидкостей в закалочном баке и баке охлаждения время до завершения обработки партии дату и информацию об операторе.
На рисунке 2.14 представлена мнемосхема электротермической линии реализованная в SCADA WinCC 6.0.
Рисунок 2.14 – Мнемосхема электротермической линии.
Разработка математической модели синтез и программная реализация алгоритмов работы устройства управления закалочной печи.
1 Исследование тепловых процессов в закалочной печи
1.1 Построение модели нагрева закалочной печи
Как уже отмечалось зоны нагрева в печах организованны идентично поэтому нет необходимости рассматривать каждую зону достаточно рассмотреть одну из зон нагрева.
Представим модель зоны нагрева в виде «черного ящика» представленную на рисунке 3.1. На входе черного ящика тепловой поток Ф1 на выходе температура в закалочной печи. Возмущением является ΔQ – относительно малые потери тепловой энергии при открывании заслонок шлюзования закалочной печи. Отметим что заслонки шлюзования являются часть шлюзовой камеры закалочной печи которая предназначена для минимизации тепловых потерь при загрузке. Это осуществляется за счет того что одна из заслонок камеры шлюзования всегда закрыта и следовательно отсутствует непосредственный контакт между атмосферой печи и атмосферой цеха.
Рисунок 3.1 – Модель зоны нагрева в виде «черного ящика»
В дипломном проекте разработана АСУ электротермической линии ЭЛТА 845 предназначенная для управления процессом закалки металических изделий автомобильной промышленности.
В проекте произведен анализ проблемной ситуации анализ технологического процесса как объекта управления разработана структура АСУ и составлено техническое задание. Были проанализированы тепловые процессы протекающие в печах электротермической линии. В разделе техническое предложение были выбраны принципы управления устройствами электротермической линии управления температурой в печах и управления скоростями конвейеров электротермической линии а также техническое и программное обеспечение для их реализации. Произведен синтез алгоритмов логического управления устройствами линии реализована система визуализации технологического процесса в SCADA WinCC 6.0. Результаты разработки системы соответствуют требованиям ТЗ.
В разделе технико-экономическое обоснование внедрения АСУ ЭЛТА сравниваются экономические показатели эксплуатации электротермической линии ЭЛТА 845 на которой применена АСУ ЭЛТА и её аналога термоагрегата СКЗА 6-30. Определен коэффициент экономической эффективности внедрения АСУ ЭЛТА.
В ходе работы над разделом безопасность и экологичность проекта произведен анализ вредных и опасных факторов термического цеха рассчитаны необходимый воздухообмен в термическом цехе и параметры местной вентиляции требуемые для обеспечения безопасных условий труда в термическом цехе.
В работе использованы следующие программные пакеты: MicroSoft Word MicroSoft Excel AutoCad 2004 MatLab 7.03 Simatic Step 7 Scada WinCC 6.0.
Для технической реализации применено оборудование производства компанииSiemens. Результаты проекта применены в проекте АСУ ЭЛТА 425270.003 разрабатываемом в инженерно-производственной фирме «АСУПРОМ».
Технико - экономическое обоснование внедрения АСУ ЭЛТА
Автоматизация производства и производственных процессов как правило сопряжена со значительными финансовыми затратами в том числе на разра-ботку проекта приобретение технических средств на проведение подготови-тельных работ и подготовку персонала. Поэтому для того чтобы избежать необоснованных затрат и финансовых потерь ещё до внедрения систем автоматизации должно быть произведено экономическое обоснование целесообразности внедрения системы. Исходя из вышесказанного необходимо произвести расчет эффективности применения системы автоматизации.
Основными показателями определяющими экономическую целесообраз-ность затрат являются: ожидаемый годовой экономический эффект эконо-мическая эффективность капитальных вложений срок окупаемости капи-тальных вложений.
В данном проекте будет оценена экономическая эффективность проекта по внедрению системы автоматизации процесса термообработки для электро-термической линии ЭЛТА 845. Электротермическая линия предназначена для термической обработки металлических деталей используемых в автомобильной промышленности.
Целью внедрения данной системы является снижение экономических потерь связанных с браком а так же сокращение расходов на энергоресурсы.
Ожидаемые результаты внедрения:
–уменьшение влияния человеческого фактора на технологический процесс;
–сокращение количества продукции отправляемой в брак;
–повышение отказоустойчивости системы;
–исключение длительной перенастройки при необходимости внести изменения в параметры процесса термической обработки.
Факторы обуславливающие повышение эффективности системы:
Безопасность труда в термическом цехе
Современное машиностроение невозможно представить без операции термической обработки таких как отжиг закалка; химико-термических (азотирование науглероживание и т.д.); деформационно-термических (высокотемпературная прокатка). Однако цех в котором производятся операции термообработки является зоной повышенного риска.
Проектируемая в проекте АСУ предназначена для управления электротермической линией на которой выполняются операции термической обработки металлических крепёжных изделий. Электротермическая линия состоит из двух электрических печей (закалочной и отпускной) бака закаливания и бака охлаждения загрузочного устройства и конвейеров.
Очевидно что данный комплекс является источником множества вредных и опасных факторов способных негативно повлиять на здоровье работников цеха либо стать причиной несчастного случая. Поэтому обеспечения безопасных условий труда в термическом цехе является наиболее важным аспектом при организации цеха.
–обеспечение безопасных условий труда в термическом цехе.
–определение тепловыделения в термическом цехе;
–определение необходимого воздухообмена и способов его организации в помещениях термического цеха;
–расчет местной приточной и вытяжной вентиляции в термическом цехе.
Схема.п.4.dwg

Схема структурная КТС
Состояние автоматического выключателя трансформатора 1 ЗП
Контактор трансформатора 1 ЗП включен
Питание контактора трансформатора 1 ЗП
Управление нагревателями
зоны 1 закалочной печи
фазы А группы 1 зоны 1
Модуль ввода аналоговых сигналов SM 331
Модуль вывода дискретных сигналов SM 322
Модуль ввода дискретных сигналов SM 321
Состояние автомата вибратора 3
Питание вибратора 3
Задание скорости вибратора 3
Модуль вывода аналоговых сигналов SM 332
Ток катушки вибратора