Разработка АСУТП производства лакокрасочных изделий




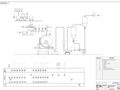
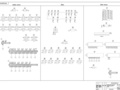
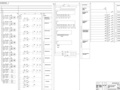
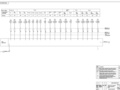
- Добавлен: 25.10.2022
- Размер: 1 MB
- Закачек: 8
Описание
Состав проекта
![]() |
![]() |
![]() ![]() ![]() ![]() |
![]() ![]() ![]() ![]() |
![]() ![]() ![]() ![]() |
![]() ![]() ![]() ![]() |
![]() ![]() ![]() ![]() |
![]() ![]() ![]() ![]() |
![]() |
![]() ![]() ![]() |
Дополнительная информация
ФСА.dwg

Подача выс. отв из камеры в мультициклон
ЭДВ3 сушильного аппарата
ЭДВ11дозировочно- смесительная станция
Обогреваемый сборник
Работа ЭДВ1 насоса подачи хлебного экстракта в сборник I
Работа ЭДВ2 насоса подачи хлебного экстракта из сборника I в сборник II
Работа ЭДВ3 насоса подачи разведенного хлебного сусла из сборника II в бродильный чан III
Работа ЭДВ4 насоса подачи закваски в бродильный чан III из сборника для закваски IV
Работа ЭДВ5 насоса подачи сахарного сиропа
Работа ЭДВ6 насоса подачи сусла из бродильного чана III в холодильник VI
Работа ЭДВ7 насоса подачи охлажденного сусла из холодильника VI в чан VII
Работа ЭДВ8 насоса подачи готового кваса на розлив
Подача горячей воды в сборник для разведенного экстракта
Подача рассола в рубашку бродильного чана
Подача сахарного сиропа в бродильный чан
Подача сахарного сиропа в чан для купажирования
Подачи рассола в рубашку для холодильного аппарата
ГУ им. Шакарима кафедра "Автоматики и электротехники" гр. АУ-210
Схема функциональная
Разработка АСУТП производства порошковых лакокрасочных изделий
Бункеры дозаторы для исходного сырья
Готовая краска на упаковку
Краска на дополнительное дробление
ВО.dwg

Подача выс. отв из камеры в мультициклон
ЭДВ3 сушильного аппарата
ЭДВ11дозировочно- смесительная станция
Обогреваемый сборник
Электромагнитный исполнительный механизм 15-2 подачи горячей воды в рубашку первого смесителя I
ЭДВ12 затвора букера
Кабель аллюминевый резиновй с поливинилхлоридной оболочкой
Кабель медный резиновй с поливинилхлоридной оболочкой
Стальная защитная труба
Мерный бак для молочно-кислой закваски
Тестомесильная машина
Емкость для кратковременного брожжения
Молочно-кислая закваска
СГУ имени Шакарима кафедра "А и У" гр. М-524
Разработка АСУТП порционного замеса теста
Надписи на табло и в рамках
Проверка сигнализации
Работа ЭДВ1 мешалки мерного бака
Работа ЭДВ3 тестомесильной машины
Работа ЭДВ4 тестомесильной машины
Работа ЭДВ5 тестомесильной машины
Работа ЭДВ6 питающего шнека
Работа ЭДВ7 силоса для муки
Работа ЭДВ8 дозатора для муки
Работа ЭДВ9 дозатора для муки
Насоса подачи закваски
Подача пара рубашку мерного бака
Подача раствора соли в дозатор
Подачи закваски в дозатор
Подача закваски в дозатор
Подача закваски в мерный бак
Подача дрожжевого молока в дозатор
Подача воды в дозатор
Подача раствора сахара в дозатор
Подача смеси в тестомесильную машину
Подача воды в тестомесильную машину
ГУ им. Шакарима кафедра "Автоматики и электротехники" гр. АУ-210
* размер для справок
Сигнальная лампа MT22 LED
Переключатель типа МТВ2-ED5
Переключатель типа МТВ2-ED3
Кнопочный пост МТВ2-EL83
Рамка для надписей РПМ-66
ЭДВ3 привода экструдера
ЭДВ9привода вибросито
Разработка АСУТП производства порошковых лакокрасочных изделий
ИМ 13-1 подачи охлаждающего воздуха
Выбор режима управления
ЭДВ4 привода барабана
Щит шкафной ЩШ-М3 (800х600)
СМ.dwg

Разработка АСУТП приготовления кваса
СГУ имени Шакарима кафедра "А и У" гр. ДАП-12
СГУ имени Шакарима гр. АУ-924
Разработка АСУТП производства порошковых лакокрасочных изделий
ГУ им. Шакарима кафедра "Автоматики и электротехники" гр. АУ-210
ВП.dwg

ГУ им. Шакарима кафедра "Автоматики и электротехники" гр. АУ-210
ВС.dwg

Подача выс. отв из камеры в мультициклон
ЭДВ3 сушильного аппарата
ЭДВ11дозировочно- смесительная станция
Обогреваемый сборник
Работа ЭДВ1 насоса подачи хлебного экстракта в сборник I
Работа ЭДВ2 насоса подачи хлебного экстракта из сборника I в сборник II
Работа ЭДВ3 насоса подачи разведенного хлебного сусла из сборника II в бродильный чан III
Работа ЭДВ4 насоса подачи закваски в бродильный чан III из сборника для закваски IV
Работа ЭДВ5 насоса подачи сахарного сиропа
Работа ЭДВ6 насоса подачи сусла из бродильного чана III в холодильник VI
Работа ЭДВ7 насоса подачи охлажденного сусла из холодильника VI в чан VII
Работа ЭДВ8 насоса подачи готового кваса на розлив
Подача горячей воды в сборник для разведенного экстракта
Подача рассола в рубашку бродильного чана
Подача сахарного сиропа в бродильный чан
Подача сахарного сиропа в чан для купажирования
Подачи рассола в рубашку для холодильного аппарата
изоляция и оболочка из поливинилхлоридного пластиката
с резиновой изолцией
Витая пара UTP (экранированный)
ЭДВ привода вентилятора
Схема внешних соединений
ЭДВ привода вибросито
ЭДВ привода дробилки
Пластиковая защитная труба
ГУ им. Шакарима кафедра "Автоматики и электротехники" гр. АУ-210
Разработка АСУТП производства порошковых лакокрасочных изделий
ЭДВ привода барабана
в пластиковой трубе
Кабель с медной жилой
изоляция и оболочкой поливинилхлоридного пластиката
Кабель с алюминиевой жилой
изоляция и оболочка из поливинихлоридного пластиката
с резиновой изоляцией
Кабель для интерфейса RS-485 с изоляцией из полиэтилена
в оболочке из поливинилхлоридного пластиката
ПСА.dwg

Подача выс. отв из камеры в мультициклон
ЭДВ3 сушильного аппарата
ЭДВ11дозировочно- смесительная станция
Обогреваемый сборник
Работа ЭДВ1 насоса подачи хлебного экстракта в сборник I
Работа ЭДВ2 насоса подачи хлебного экстракта из сборника I в сборник II
Работа ЭДВ3 насоса подачи разведенного хлебного сусла из сборника II в бродильный чан III
Работа ЭДВ4 насоса подачи закваски в бродильный чан III из сборника для закваски IV
Работа ЭДВ5 насоса подачи сахарного сиропа
Работа ЭДВ6 насоса подачи сусла из бродильного чана III в холодильник VI
Работа ЭДВ7 насоса подачи охлажденного сусла из холодильника VI в чан VII
Работа ЭДВ8 насоса подачи готового кваса на розлив
Подача горячей воды в сборник для разведенного экстракта
Подача рассола в рубашку бродильного чана
Подача сахарного сиропа в бродильный чан
Подача сахарного сиропа в чан для купажирования
Подачи рассола в рубашку для холодильного аппарата
Работа ЭДВ рецептурного смесителя
СГУ имени Шакарима гр. АУ-924
Разработка АСУТП производства порошковых лакокрасочных изделий
Схема принципиальная электрическая
Ц е п и у п р а в л е н и я
ИМ12-1 подачи охлаждающего воздуха в барабан
Блок питания БП30 Б-Д
Распределительная система ADAM-6000
Шестиканальный релейный выходной модуль ADAM-6060
Семиканальныйканальный модуль для подключения термометров сопротивления ADAM-6015
Восьмиканальный модуль аналогового ввода ADAM 6017
Проверка сигнализации
Ц е п и с и г н а л и з а ц и и
Работа ЭДВ смесителя
Работа ЭДВ нагревающего ТЭНа
Работа ЭДВ вентиляции
ТЭН первой секции экструдера
ТЭН второй секции экструдера
ТЭН третйй секции экструдера
ГУ им. Шакарима кафедра "Автоматики и электротехники" гр. АУ-210
Розетка Питание щита
ЭДВ1 привода смесителя
ЭДВ3 привода экструдера
ЭДВ4 привода барабана
ЭДВ5 привода дробилки
ЭДВ6 привода фильтра
ЭДВ7 привода фильтра
ЭДВ8 привода вентилятора
ЭДВ 9 привода вибросито
канальный релейный выходной модуль ADAM-6051
Семиканальный модуль для подключения термометров сопротивления ADAM-6015
ИМ13-1 подачи охлаждающего воздуха в барабан
Курсовая М2.doc
1.Описание технологического процесса5
3.Выбор приборов и средств автоматизации14
4.Схема принципиальная электрическая20
5.Щит автоматизации22
7.Схема внешних соединений26
Список использованных источников .28
Автоматизация производства – это процесс при котором функции управления и контроля ранее выполнявшиеся человеком передаются приборам и автоматическим устройством. Главная цель автоматизации производства заключается в повышении производительности труда улучшении качества выпускаемой продукции создании условий для оптимального использования всех ресурсов производства.
Большое внимание должно уделяться изучению проектирования систем управления. В процессе проектирования осуществляемого на основе государственных стандартов и другой нормативно – технической документации создается комплексная техническая документация необходимая для обоснования оценки комплектации строительства монтажа наладки и эксплуатации объекта. Объектом проектирования могут быть жилые здания промышленные предприятия ирригационные системы АСУ и т.п. Проект должен не только дать ясное представление о характере форме и технической сущности проектируемого объекта но и содержать убедительное доказательство того что данные в проектах решения являются наиболее рациональными отвечают современному уровню науки и техники и обеспечивают высокие технико – экономические показатели.
Знание проектирования систем автоматизации технологических процессов помогает в решении основных этапов построения систем автоматического и автоматизированного управления в составлении основной документации сопутствующей каждому из этапов проектирования. При одностадийном проектировании документация проекта выполняется в двух видах: графическая и текстовая. В графический материал входят:
Структурные схемы управления автоматизированными производствами;
Схемы автоматизации технологических процессов;
Принципиальные схемы контроля управления технологической сигнализации и питания технических средств системы;
Документация на щиты и пульты включая чертежи общих видов щитов таблицы соединений и подключений спецификации щитов и пультов;
Схемы соединения и подключения внешних проводок;
Чертежи расположения проводки оборудования;
Чертежи установки вспомогательной аппаратуры устройств щитов и пультов при отсутствии соответствующих нормалей.
Автоматизация является одним из основных факторов современной научно – технической революции. В основе автоматизации производства лежит подход к анализу и синтезу объектов управления а также к построению и использованию комплекса технических средств автоматического управления регулирования и контроля. Эффективная автоматизация машин приборов и технологического оборудования основана на широком применении средств микропроцессорной техники (МТ). Автоматизация с использованием микропроцессоров (МП) и микроконтроллеров (МК) быстро распространяется в самых разнообразных отраслях народного хозяйства охватывает новые сферы.
Как известно МТ состоит из двух специфических частей: аппаратурных средств (АС) и прикладного программного обеспечения (ППО). При этом рассматривая общий процесс проектирования МТ можно отметить что в большинстве случаев доля общей трудоемкости разработки ППО значительно превосходит трудоемкость разработки АС. Указанное обстоятельство объясняется тем что разработка аппаратурной части МТ на базе типовых микропроцессорных БИС сводится (чаще всего) к выполнению стандартных операций в соответствии с рекомендациями изложенными в технической документации на используемые БИС.
Развитие микроэлектроники и широкое применение в промышленном производстве в устройствах и системах управления самыми разнообразными объектами и процессами является в настоящее время одним из основных направлений научно технического прогресса.
Использование микроэлектронных средств в изделиях промышленного и культурно-бытового назначения не только приводит к повышению технико-экономических показателей изделий (стоимости надежности потребляемой мощности габаритных размеров) и позволяет многократно сократить сроки разработки и отодвинуть строки "морального старения" изделий но и придет им принципиально новые потребительские качества (расширенные функциональные возможности модифицируемость адаптивность и т.д.).
Экономические преимущества использования автоматических систем в производстве вытекают из их технических преимуществ. К экономическим преимуществам автоматизации можно отнести: возможность значительного повышения производительности труда; более экономичное использование физического труда материалов и энергии.
Разработка АСУТП производства лакокрасочных изделий
1.Описание технологического процесса
Порошковая окраска – это безотходная и экологически чистая технология получения полимерных покрытий с высокими защитными и декоративными свойствами. Технология порошковой окраски была разработана и начала применяться в 50-60 х годах прошлого столетия. В настоящее время порошковыми красками обрабатывается примерно 15% окрашиваемых изделий в мире. Основное различие между технологией нанесения традиционных жидких и порошковых материалов заключается в том что порошковые краски не содержат в своем составе органических растворителей жидкого пленкообразователя и изначально находятся в твердом агрегатном состоянии. Порошковые краски представляют собой смеси пигментов наполнителей и сухих олигомерных или полимерных органических пленкообразователей образующих при расплаве сплошные пленочные покрытия. В состав порошковых материалов входят следующие компоненты:
пленкообразователи – термопластичные полимеры или термореактивные олигомеры; пигменты и наполнители;
структурирующие вещества.
В зависимости от типа пленкообразователя входящего в состав порошковых лакокрасочных материалов последние подразделяются на эпоксидные эпоксиполиэфирные полиэфирные полиуретановые полиакриловые полиэтиленовые полиамидные и др. Каждый из перечисленных материалов имеет свои преимущества недостатки и специфические области применения. Частицы пигмента должны быть в несколько раз меньше зерен полимеров быть инертными и не увеличивать температуру текучести и вязкость расплавов а также не тормозить пленкообразование. Для пигментирования используют высокодисперсные укрывистые и термостойкие пигменты: диоксид титана оксид хрома железооксидные пигменты технический углерод фталоцианиновые пигменты; а также наполнители – тальк барит аэросил. Независимо от состава порошковые материалы представляют собой однородный нерасслаивающийся сыпучий порошок с размерами зерен от 10 до 100 мкм.
Для получения порошковых красок применяют три разных способа:
сухое смешение дисперсных компонентов;
смешение в расплаве с последующим измельчением плава;
диспергирование пигментов в растворе пленкообразователей с последующей отгонкой растворителя из жидкого материала.
Сухое смешение применяется при пигментировании предварительно измельченных термопластичных полимеров. При использовании этого способа нерасслаивающиеся стабильные композиции получаются только в том случае если при смешении происходит дезагрегация зерен исходных материалов и образование новых смешанных агрегатов с большой контактной поверхностью между разнородными частицами. При сухом смешивании без измельчения зерен полимеров частицы пигментов и наполнителей только "опудривают" поверхность зерен полимеров снаружи. Полярные полимеры (поливинилбутираль полиамиды эфиры целлюлозы и др.) имеют хорошую адгезию к дисперсным пигментам и наполнителям. Неполярные полимеры (полиолефины фторопласты и др.) значительно труднее смешиваются с наполнителями. Жидкие компоненты – пластификаторы отвердители модификаторы как правило предварительно перетирают с пигментами и наполнителями а затем смешивают с полимерами в шаровых вибрационных и др. мельницах. Сухое смешение – наиболее простой способ осуществляемый в различных смесителях но получаемый при этом конечный продукт имеет недостаточно равномерное распределение пигментов. Смешение в расплавах (Рис. 1) производится при температуре несколько выше температуры текучести пленкообразователя. При этом пигментные частицы смачиваются и проникают внутрь частиц пленкообразователя создавая более однородные макро- и микроструктуры еще до стадии пленкообразования. Смешение компонентов в расплавах возможно для любых пленкообразователей но наибольшее применение находит для эпоксидных полиэфирных акрилатных уретановых олигомеров низкомолекулярного поливонилхлорида и др.
Рис. 1 Технологическая схема производства порошковых красок
Процесс изготовления включает пять операций:
дробление исходных компонентов до зерен размером 1 – 3 мкм;
расплавление полимера или олигомера и смешение компонентов в расплаве;
охлаждение расплава;
измельчение расплава;
сухой просев или сепарация порошка.
Дробление пигментов при производстве порошковых материалов производится практически только в экструдерах (червячных смесителях). Попытки использования других видов оборудования не оправдали себя.
Рис. 2. Схема одношнекового экструдера:
-полость для циркуляции воды;
- формующая головка с адаптером.
Главной частью экструдера является шнек вращающийся в цилиндрическом корпусе (Рис. 2). Червяк захватывает сухую смесь "пленкообразователь – пигмент – наполнитель" из питающего бункера и пропускает ее через цилиндрический корпус расплавляя и смешивая (перетирая) ее по мере продвижения. В промышленности порошковых красок используются два конкурирующих типа экструдеров: первый является двухшнековым экструдером с двумя совмещенными шнеками вращающимися в одном направлении второй – одношнековый экструдер в котором шнек периодически двигается назад - вперед (т.н. смеситель co - compounder ).
Червяки двухшнекового экструдера дополнительно оснащены перемешивающими дисками. В одношнековом экструдере смешение происходит из-за сложной формы и характера движения шнека в сочетании со специальными выступами расположенными на внутренней стенке цилиндра.
Основная операция – горячее смешение компонентов проводится при температуре 90 – 110 о С вязкости 10 3 – 10 5 Пас в течение 05 – 50 минут в аппаратах непрерывного действия – экструдерах двухчервячных шнековых смесителях с четко регулируемой системой обогрева. Наилучшие результаты достигаются при предварительном диспергировании пигментов в небольшом количестве расплава пленкообразователя и пластификатора затем такие пигментные концентраты вводят в основную массу расплава пленкообразователя с остальными компонентами. Максимальная температура расплава должна быть на 20 о С ниже температуры отверждения порошкового материала среднее время пребывания не должно превышать время необходимое для диспергирования и распределение времени пребывания должно быть как можно более узким (как правило не более 15 секунд).
На эффективность работы экструдера влияют:
эффект сдвига (скорость момент);
среднее время пребывания смеси в аппарате;
производительность аппарата;
Данный способ производства порошковых материалов позволяет резко улучшить дисперсность сократить время смешивания и уменьшить опасность преждевременного отверждения порошка. Дисперсность частиц пигмента составляет от 1 до 20 мкм. При таком способе производства энергозатраты на смешение в расплаве и последующее измельчение более высокие но они оправдываются высоким качеством покрытий и меньшей их толщиной по сравнению с сухим способом. Недостатком данного способа производства порошковых красок является трудность точной подгонки цвета и необходимость зачистки оборудования при переходе с цвета на цвет. Порошковые краски получаемые испарением органических растворителей из жидких красок наиболее дисперсны и имеют частицы округленной формы размером 20 – 40 мкм. Они отличаются более высокой красящей способностью и пониженной температурой отверждения. Их изготовление включает стадии обычного производства органорастворимых лакокрасочных материалов а также отгонки растворителя в сушилках распылительного типа и улавливания конденсата отогнанного растворителя с возвращением его в производственный цикл. Недостатком этого способа является его чрезвычайная взрывоопасность поэтому в качестве теплоносителя для сушки используется азот. Появление порошковых материалов – закономерный результат эволюции лакокрасочной индустрии. Лакокрасочные материалы с высокой долей нелетучих веществ во-первых более экономичны в плане нанесения а во-вторых их широкое использование позволяет если не оздоровить то хотя бы улучшить экологическую обстановку.
Будучи лакокрасочными материалами со стопроцентным сухим остатком порошковые краски находят все большее и большее применение. Однако их использование ограничивается формой и габаритами окрашиваемых изделий а также чувствительностью подложки к повышенной температуре. Основными преимуществами порошковых красок по сравнению с традиционными органоразбавляемыми материалами являются:
отсутствие органических растворителей;
значительно меньшее количество отходов (менее 005% от массы мате - риала);
высокая скорость отверждения;
возможность нанесения материала за один слой;
широкий диапазон легко достигаемых специальных эффектов (муар апельсиновая корка и др.);
возможность регулирования толщины слоя покрытия;
практически полное отсутствие вредных выбросов;
низкая пожароопасность производства;
меньше затраты на получение покрытия.
Все порошковые краски могут быть разделены на две большие группы: термопластичные и термореактивные. Технология порошковой окраски термопластичными порошковыми красками основывается на формировании покрытия без химических реакций лишь за счет сплавления частиц при нагревании. Образующиеся из них покрытия термопластичны обратимы. Их используют преимущественно для получения покрытий функционального назначения – химически стойких противокоррозионных антифрикционных электроизоляционных. Покрытия обычно наносят толстыми слоями – 250 мкм и более. Типичные области их применения – это защита проволоки труб корзин посудомоечных машин морозильных камер шлицевых валов и узлов трения переключателей и других изделий. Существуют различные технологии и методы нанесения порошковых материалов. Электростатический и трибостатический методы напыления являются наиболее популярными и распространенными.
Технология порошковой окраски электростатическим напылением. Популярность нанесения порошковой краски электростатическим напылением обусловлена следующими факторами: высокая эффективность зарядки почти всех порошковых красок высокая производительность при порошковом окрашивании больших поверхностей относительно низкая чувствительность к влажности окружающего воздуха подходит для нанесения различных порошковых материалов со специальными эффектами (металлик шагрень муар и т.д.). Основное оборудование для порошковой окраски – электростатический пистолет-распылитель.
Наряду с достоинствами электростатическое напыление имеет ряд недостатков которые обусловлены сильным электрическим полем между пистолетом-распылителем и деталью которое может затруднить нанесение порошкового покрытия в углах и в местах глубоких выемок (Рис. 4). Это явление носит название эффекта клетки Фарадея. Данный дефект является результатом воздействия электростатических и аэродинамических сил.
Рис. 3 Эффект клетки Фарадея
На Рис. 3 показано что при нанесении порошкового покрытия на участки в которых действует эффект клетки Фарадея электрическое поле создаваемое распылителем имеет максимальную напряженность по краям выемки. Силовые линии всегда идут к самой близкой заземленной точке и скорее всего концентрируется по краям выемки и выступающим участками а не проникают дальше внутрь. Это сильное поле ускоряет оседание частик образуя в этих местах порошковое покрытие слишком большой толщины. Эффект клетки Фарадея наблюдается в тех случаях когда наносят порошковую краску на металлоизделия сложной конфигурации куда внешнее электрическое поле не проникает поэтому нанесение ровного покрытия на детали затруднено и в некоторых случаях даже невозможно.
Кроме эффекта клетки Фарадея при нанесении порошковых красок в электрополе иногда встречается и другая проблема – неправильный выбор электростатических параметров распылителя и расстояния от распылителя до детали может вызвать обратную ионизацию и ухудшить качество полимерного порошкового покрытия (Рис. 4).
Рис. 4 Обратная ионизация
Обратная ионизация вызывается излишним током свободных ионов от зарядных электродов распылителя. Когда свободные ионы попадают на покрытую порошковой краской поверхность детали они прибавляют свой заряд к заряду накопившемуся в слое порошка. На поверхности детали накапливается слишком большой заряд. В некоторых точках величина заряда превышается настолько что в толще порошка проскакивают микро-искры образующие кратеры на поверхности что приводит к ухудшению качества покрытия и нарушению его функциональных свойств. Обратная ионизация также способствует образованию дефекта "апельсиновой корки" снижению эффективности работы распылителей и ограничению толщины получаемых покрытий.
Для уменьшения эффекта клетки Фарадея и обратной ионизации было разработано специальное оборудование сокращающее количество ионов в ионизированном воздухе когда заряженные частицы порошка притягиваются поверхностью. Свободные отрицательные ионы отводятся в сторону благодаря заземлению самого распылителя что значительно снижает проявление вышеупомянутых негативных эффектов. Увеличив расстояние между распылителем и поверхностью детали можно уменьшить ток пистолета распылителя и замедлить процесс обратной ионизации.
Технология порошковой окраски трибостатическим напылением. В отличие от электростатического напыления в данной системе нет генератора высокого напряжения для распылителя. Порошок заряжается в процессе трения. Главная задача в данном процессе – увеличение числа и силы столкновений между частицами порошка и заряжающими поверхностями пистолета распылителя.
Одним из лучших акцепторов в трибоэлектрическом ряду является политетрафторэтилен (тефлон) он обеспечивает хорошую зарядку большинства порошковых красок имеет относительно высокую износоустойчивость и устойчив к налипанию частиц под действием ударов.
Трибостатическое напыление имеет ряд существенных преимуществ:
В распылителях с трибостатической зарядкой не создается ни сильного электрического поля ни ионного тока поэтому отсутствует эффект клетки Фарадея и обратной ионизации. Заряженные частицы могут проникать в глубокие скрытые проемы и равномерно прокрашивать изделия сложной конфигурации.
Рис. 5 Отсутствие эффекта клетки Фарадея
Возможно нанесение нескольких слоев краски для получения толстых порошковых покрытий.
Распылители с использованием трибостатической зарядки конструктивно более надежны чем пистолеты распылители с зарядкой в поле коронного разряда поскольку они не имеют элементов преобразующих высокое напряжение. За исключением провода заземления эти распылители являются полностью механическими чувствительными только к естественному износу.
Технология порошковой окраски в кипящем слое и струйным распылением Технология порошковой окраски термореактивными порошковыми красками основывается на том что покрытие в отличие от термопластичных материалов формируется посредством химических реакций при нагревании. Такие покрытия имеют трехмерное строение они неплавкие и нерастворимы т. е. необратимы. Термореактивные краски служат для получения как функциональных покрытий так и защитно-декоративных. Для получения покрытий функционального назначения наиболее широко применяют эпоксидные составы. Их наносят слоями 100-150 мкм на предварительно нагретую до 50-60 о С поверхность изделия в аппаратах кипящего слоя (многократно чередуя нагрев и погружение в порошок) или струйным распылением. Толщина покрытия нанесенного таким способом как правило колеблется в пределах 300-500 мкм. Поэтому данный метод применяют для окраски изделий имеющих небольшую площадь и сложную конфигурацию поверхности – роторов и статоров электродвигателей труб (изнутри и снаружи) металлической арматуры проволоки сетки катушек и т.д.
Порошковое покрытие формируется одним из вышеперечисленных способов затем идет тепловая обработка в течение 10-20 минут при температуре 160-200 о С во время которой порошковая краска плавится растекаясь по поверхности изделия и образуя тонкую прочную пленку – полимерное покрытие толщиной 60-80 мкм.
В последние годы все шире внедряются различные способы низкотемпературного (при температуре 120-130 о С) отверждения применяемые для окраски изделий чувствительных к повышенным температурам. Однако низкотемпературное отверждение применимо только для эпоксидных материалов. Отверждение покрытия посредством ИК-излучения позволяет быстро нагреть изделие до нужной температуры при этом технологический процесс значительно сокращается и уменьшаются габариты оборудования но данный способ отверждения подходит только для изделий простой формы не отбрасывающей тень на саму себя. Одним из перспективных способов отверждения покрытия порошковых материалов является УФ-отверждение. Однако и оно не лишено недостатков. Во-первых данным способом нельзя получать матовые покрытия. Вторым недостатком является невозможность отверждения порошковых материалов желтого цвета связанная со способностью желтых пигментов поглощать свет как в УФ- так и в видимой области спектра. Порошковые материалы используются главным образом для нанесения покрытий на металлы. Однако новые технологии и оборудование для порошковой окраски позволяют окрашивать и другие материалы например стекло керамику МДФ-плиты (древесноволокнистая плита средней плотности).
Хотя технология порошковой окраски имеет много преимуществ имеются некоторые ограничения в производстве тонких и гладких декоративных покрытий. Текстура и свойства поверхности зависят от типа порошковых красок и настройки технологического оборудования для порошковой окраски. Для получения качественного порошкового покрытия очень важно соблюдать технологию нанесения и температурные режимы. Многие производители предпочитают наносить порошковое покрытие с эффектом "апельсиновой корки" т.к. он позволяет скрыть дефекты металла появляющиеся в ходе производства. Порошковая окраска также имеет значительное преимущество в том что не осевшая краска может быть собрана и повторно использована. Однако если в цикле окраски используется несколько цветов это накладывает определенные ограничения на вторичное использование материала. Такую порошковую краску соответствующую всем требованиям нормативной документации исключая показатель "цвет краски" называют «вторичкой». Как правило она используется для окраски деталей декоративные свойства которых не имеют принципиального значения. Использование порошковых лакокрасочных материалов предполагает получение долговечного покрытия. Однако если возникает необходимость удалить порошковую краску для этого есть специальные средства. Технология порошковой окраски не сложна однако требует практических навыков и опыта работы.
2.Функциональная схема автоматизации.
Функциональная схема автоматизации является основным техническим документом определяющим объем автоматизации технологических установок и отдельных агрегатов автоматизированного объекта.
Функциональная схема автоматизации представляет собой чертеж на котором схематически условными изображениями изображены технологическое оборудование коммуникации органы управления и средства автоматизации с указанием связи между ними.
Функциональная схема автоматизации разработана на основании описания технологического оборудования производства порошковой краски. Она включает в себя:
а) автоматизацию работы электродвигателей:
) электродвигатель привода смесителя (ЭДВ1);
) электродвигатель привода шнека (ЭДВ2);
) электродвигатель привода экструдера (ЭДВ3);
) электродвигатель привода барабана (ЭДВ4);
) электродвигатель привода дробилки (ЭДВ5);
) электродвигатель привода фильтра (ЭДВ6);
) электродвигатель привода фильтра (ЭДВ7);
) электродвигатель привода вентилятора (ЭДВ8);
) электродвигатель привода вибросито (ЭДВ9);
) термоэлектрический нагреватель первой секции;
) термоэлектрический нагреватель второй секции;
) термоэлектрический нагреватель третий секции;
б) автоматизация работы исполнительных механизмов;
) подачи охлаждающегося воздуха в барабан (13-1);
) подачи питания на щит управления (HL1);
) работы электродвигателя привода смесителя (HL2);
) работы электродвигателя привода шнека (HL3);
) работы электродвигателя привода нагревающего ТЭНа (HL4);
) работы электродвигателя привода барабана (HL5);
) работы электродвигателя привода дробилки (HL6);
) работы электродвигателя привода фильтра (HL7);
) работы электродвигателя привода фильтра (HL8);
) работы электродвигателя привода шнека (HL9);
) работы электродвигателя привода вентиляции (HL10);
) термоэлектрический нагреватель первой секции (HL11);
) термоэлектрический нагреватель второй секции (HL12);
) термоэлектрический нагреватель третий секции (HL13);
г) контроль и регулирование:
) масса смесителя (датчик 19-1);
) температура секции ТЭНа (датчики14-115-116-117-1);
) температура охлаждающего барабана (датчик 18-1).
Система работает следующим образом: при помощи автоматического выключателя SF1 типа PL4-B 252 оператор подает питание на щит управления затем при помощи переключателя «Выбор режима» SA1 типа MTB2-ED3 выбирается режим работы системы: операторный (ручной) или автоматический.
Система работает в автоматическом режиме а ручной режим предусмотрен для отключения всех электродвигателей и клапанов в аварийном режиме и при пуско–наладочных работах.
Автоматический режим представлен распределительной системой ADAM-6000. Это компактные интеллектуальные устройства обработки сигналов датчиков для применения в промышленности. Встроенные МП позволяют осуществлять нормализацию сигналов аналоговый и дискретный вводвывод отображение данных и их передачу по интерфейсу RS-485.
Все модули имеют гальваническую развязку по цепям питания и интерфейса RS-485 программную установку параметров командный протокол ASCII и сторожевой таймер.
Контроллер имеет открытую архитектуру и может программироваться как с помощью традиционных языков программирования так и с помощью языков логического программирования в соответствии со стандартом МЭК-1131.
Распределительная система ADAM-6000 имеет 4 модулей: Р1 – восьмиканальный релейный выходной модуль ADAM-6015 который необходим для управления электродвигателями ЭДВ1..ЭДВ6 Р2 – восьмиканальный релейный выходной модуль ADAM-6051 который необходим для управления электродвигателями ЭДВ7..ЭДВ9 и термоэлектрическими нагревателями ТЭН1 ТЭН3 и исполнительным механизмамом 13-1 Р3 – семиканальный модуль для подключения термометров сопративления ADAM-6015 Р4 – восьмиканальный модуль аналогового ввода ADAM-6017 для подключения датчиков уровня давления и масса известкого молочка. При помощи модулей Р3 Р4происходит сбор информации с датчиков уровня давлениямассы и температуры а при помощи модулей Р1..Р2 происходит управление соответствующими электродвигателями и исполнительными механизмами.
После операции горячего смешения смеси компонентов в экструдере происходит измерение температуры датчиком ТЕ-18-1 термопреобразователь сопротивления медный ТСМ Метран-203 после чего сигнал поступает модуль Р3 далле идет на распределительную систему ADAM-6000 затем на модуль Р2 после сигнал поступает на исполнительный механизм подачи охлаждающегося воздуха в барабан (13-1).
3. Выбор приборов и средств автоматизации
Датчик термометр сопротивления
Основные характеристики
Диапазон измеряемой температуры °С
Термопреобразователи сопротивления медные ТСМ Метран-203 предназначены для измерения температуры жидких и газообразных химически неагрессивных сред а также агрессивных не разрушающих материал защитной арматуры.
Рисунок 3.1 – Датчик ТСМ Метран-203
Тензодатчик Т4(Рис 3.2) используется в платформенных бункерных весах дозаторах а также для взвешивания небольших баков и других емкостей. Консольное крепление датчика позволяет создавать сило- и весоизмерительные системы минимальной высоты.
Упругий элемент датчика выполнен из нержавеющей стали и состоит из двух балок изгиба образующих параллелограмм. В конструкции датчика удачно сочетаются небольшие размеры и высокая точность. Датчик герметизирован металлическим однослойным сильфоном. Крепление сильфона к упругому элементу осуществляется при помощи лазерной сварки. Герметичность датчика проверяется с помощью плазменного течеискателя. Датчик надежно работает во влажных и частично агрессивных средах. Степень защиты оболочкой по ГОСТ 14254 IP68.
Датчик используется в платформенных весах ВПН монорельсовых весах ВМ бункерных весах и тензометрических весоизмерительных электронных устройствах (ТВЭУ).
Рисунок 3.2 – Т4 датчик тензорезисторный
Устройство распределенного сбора данных и управления ADAM 6000
Модули серии ADAM-6000 предназначены для построения интеллектуальных распределенных систем сбора данных и управления на основе интерфейса Ethernet который позволяет легко интегрировать системы на основе модулей ADAM-6000 в сети Интернетинтранет. Web-доступ к данным модулей в реальном времени организуется благодаря встроенному в каждый модуль сбора данных Web-серверу. Для настройки встроенной в модули Web-страницы предусмотрена возможность удалённой загрузки JAVA-аплетов. Поддержка P2P-соединения позволяет легко настроить систему вводавывода без использования управляющего устройства и сложного программирования. Благодаря функции GCL (Graphic Condition Logic) модули вводавывода могут работать в качестве управляющих устройств осуществляя локальный или удаленный вводвывод а также простейшую обработку данных.
Программная поддержка
Для организации взаимодействия со SCADA-системами верхнего уровня в модулях реализована поддержка протокола Modbus ТСР и обмен данными происходит через ОРС-сервер. Кроме того с модулями поставляются соответствующие DLL-драйверы и ActiveX-компоненты а также утилита ADAM.NET для конфигурирования модулей и настройки функций P2P-содинения и GCL.
Общие параметр модуля ADAM-6060
входных каналов с гальванической изоляцией и поддержкой цепей с «сухим» контактом
Напряжение изоляции 2000 В
реле с контактом на замыкание: 120 В05 A перем. тока 30 В1 A пост. тока
Рисунок 3.3 – Микроконтроллер ADAM-6060
Общие параметр модуля ADAM-6051
выходных канала типа открытый коллектор (до 30 В02 А)
Два 32-разрядных счетчика с функциями подсчета событий (частота до 5 кГц) измерения частоты (от 03 до 1000 Гц)
Напряжение изоляции 2000 В пост. Тока
Рисунок 3.4 – Микроконтроллер ADAM-6051
Общие параметр модуля ADAM-6015
Эффективное разрешение АЦП 16 разрядов
Количество каналов: 7 дифференциальных
Типы поддерживаемых термометров сопротивления: Pt 100 Pt 1000 Balco 500 Ni 50
Схема подключения: 2- и 3-проводная
Рисунок 3.5 – Микроконтроллер ADAM-6015
Общие параметр модуля ADAM-6017
Количество каналов: 8 дифференциальных
Программная настройка типа и диапазона входного сигнала (мВ В мА) индивидуальная для каждого канала
дискретных выхода (30 В100 мА)
Рисунок 3.6 – Микроконтроллер ADAM-6017
Компактный промышленный компьютер iROBO-3000ITX-ATOM –с двумя ядрами и поддержкой памяти DDR3.
Обновленные модели iROBO-3000ITX-ATOM и iROBO-3000ITX-ATOM-PCI поддерживают более производительные энергоэффективные процессоры Intel Atom D425 (1.8ГГц). Новая платформа поддерживает оперативную память DDR3. Таким образом обновленная платформа отличается повышенным быстродействием и не уступает в энергоэффективности предыдущему поколению систем. Промышленные компьютеры серии iROBO-3000 могут с успехом применяться в условиях ограниченного пространства для создания рабочих мест повышенной надежности в офисах и на производстве.
4.Схема принципиальная электрическая
Принципиальная схема – это схема каждый элемент которой выполняя определенную функцию не может быть разделен на части имеющие самостоятельное функциональное назначение.
На основании принципиальных схем определяющих полный состав элементов и связей между ними разрабатываются остальные материалы проекта общие виды щитов их монтажные схемы схемы внешних соединений.
Принципиальная схема разрабатывается на основании функциональной схемы автоматизации «Разработка АСУТП производства лакокрасочных изделий».
Условно можно разделить принципиальную схему на схему управления сигнализации и питания.
Силовые питающие цепи (трехфазные) А В С показываем горизонтальными сплошными линиями нулевую линию изображаем также горизонтальной но пунктирной линией.
На схеме питания изображаем питание электродвигателей М1..М8.
Цепи питания для электродвигателя представлены тремя фазами А В С пакетным автоматическим выключателем QF1 типа ПВЕ-25 магнитным пускателем КМ1 типа ПМЕ- ПМ 12-100-250 и тепловыми реле КK1 и КK2.
Цепи питания для остальных электродвигателей аналогичны вышеизложенным.
Для облегчения чтения электрических схем особенно когда эти схемы сложны целесообразно маркировать цепи путем последовательной их нумерации а также указывать адреса контактов этой аппаратуры. При горизонтальном изображении цепей схемы цепи и их ответвления нумеруются сверху вниз а при вертикальном слева направо.
Маркировка цепей производится следующим образом: цепи питания и силовые – 800 и выше цепи сигнализации – 400 и выше цепи управления - 1 и выше.
Цепи питания ЭДВ (силовые цепи) маркируем буквами обозначающими фазы и последовательными цифрами А1 А2 и т.д.
Провод приходящий с фазы С имеет нумерацию 800 а с провода N нумерацию 801. Провод 800 разделен автоматом SF2 типа PL4-B 252 поэтому это считается разными участками и ему уже соответствует нумерация 802.
Цепи управления условно можно разделить на цепи управления электродвигателями цепи управления исполнительными механизмами и цепи управления двумя распределительными системами с модулями.
Питающие участки цепей управления располагаем с правой стороны силовых цепей они представлены двумя сплошными вертикальными линиями фаза и ноль. К питающим участкам подсоединяем приборы и аппаратуру управления регулирования и сигнализации причем цепи управления и сигнализации располагают горизонтально в порядке вертикальной последовательности их действия при чтении схемы сверху вниз.
В верхней части цепей управления располагаем автомат SF1 типа PL4-B 252 для подачи питания на розетку а также автомат SF2 типа PL4-B 252 для подачи питания на щит управления.
Схемы управления в зависимости от степени участия оператора могут работать в автоматическом автоматизированном и ручном режимах. Данная система поддерживает два режима: автоматический и ручной. Причем работа процесса происходит только в автоматическом режиме а ручной режим необходим для проверки работоспособности клапанов и электродвигателей и при аварийном отключении всей системы.
Реализует работу в двух режимах переключатель SA1 «Выбор режима работы» при помощи которого оператор выбирает необходимый режим.
Далее располагаем цепи управления электродвигателей. Цепи управления ЭДВ1 в ручном режиме представлены кнопочным постом с двумя кнопками «Стоп» SB1.2 и “Пуск” SB1.1 типа MTB2-EL83 аварийной кнопкой “Стоп” расположенной по месту а также магнитным пускателем КМ1 типа ПМЕ- ПМ 12-100-250 с тепловыми реле КК1 и КК2. В автоматическом режиме управление осуществляется от контакта К1.1 реле работающего от Р1- шестиканального модуля вывода ADAM-6060. Работа электродвигателей ЭДВ2 ЭДВ9 аналогична вышеизложенному двигателю с тем отличием что управление в автоматическом режиме поддерживается контактами последующих реле. Так для ЭДВ2 – это контакт K2.1 реле напряжения K2 типа РП-53 работающего от модуля Р1. Для ЭДВ3 – это контакт K3.1 реле K3 того же модуля. Для ЭДВ4 – это контакт 4.1 реле K4 типа РП-53 модуля Р1. Для ЭДВ5 – это контакт K5.1 реле K5 модуля Р1. Для ЭДВ6 – это контакт K6.1 реле K6 для ЭДВ7 – это контакт K7.1 реле K7 модуля Р2 для ЭДВ8 – это контакт K8.1 реле K8 модуля Р2 для ЭДВ9 – это контакт K9.1 реле K9 модуля Р2. Исполнительный механизмы включаются с помощью промежуточных реле модуля Р2 для ИМ 13-1 – это контакт K13.1 реле K13 для ИМ 13-1 это контакт реле К14.1 реле К14. Распределенная система ADAM-6000 имеет питание 30 V поэтому используем блок питания БП провода от которого подводим к распределительным системам.
В ручном режиме цепи управления электромагнитными исполнительным механизмам осуществляется за счет переключателей SA2 типа MTB2-ED2 в автоматическом режиме за счет контактов K13.1.. K14.1 реле K13 ..K14 типа РПУ РП-53 модуля Р2 распределительной системы ADAM-6000.
Схема сигнализации содержит 13 сигнальных ламп. Лампа HL1 типа MT22 LED загорается при подачи питания на щит. Лампы HL2.. HL13 типа MT22 LED при срабатывании контактов магнитных пускателей КМ1..КМ12 типа ПМ-12-100-250.
Маркировку цепей сигнализации начинаем с 400.
Щит предназначен для размещения приборов и аппаратуры автоматического контроля управления и сигнализации на пунктах управления и состоят из корпуса аппаратурой электрической и трубной проводкой подготовленного к подключению внешних цепей.
Выбор типа и конструкции щитов определяем в первую очередь их эксплуатационным назначением. На стадии выбора конструкции и размеров щитов должны быть испытаны такие данные как общая структура системы управления но также объем и характеристики комплекса технических средств распределения функций между оператором и автоматическим управляющим устройством.
Основанием для проектирования щита управления является функциональная схема автоматизации «Разработка АСУТП производства лакокрасочных изделий».
Для локальных пунктов управления используем малогабаритный щит управления причем так как щит устанавливаем в производственном помещении то он должен быть шкафным (защищенным).
Габариты щитов выбираем в зависимости от числа и размеров приборов и средств автоматизации удобства монтажа и обслуживания размеров помещения и условий окружающей среды а также правил техники безопасности.
Проектом предлагается шкафной щит с задней дверью односекционный шириной –600 мм глубиной – 350 мм и высотой 800 мм. Тип выбранного щита ЩШ-М-800*600 УХЛ-IР30 ГОСТ36.17-76.
Расстояние от двери до противоположной стенки равно 600 мм то есть данный щит считается обслуживаемым извне. Щит имеет климатическое исполнение У категории размещения 4- по ГОСТу 15150-69.
Степень защиты данного щита от прикосновения к токоведущим частям попадания посторонних тел и проникновения воды должна соответствовать ГОСТ 14254-80 [2] то есть для щитов шкафных IР00.
Эксплуатация данного типа щита осуществляется при следующих условиях:
- температура окружающего воздуха 1-35ºС
- относительная влажность воздуха 65% при температуре 20ºС и не более 80% при температуре 25ºС
- высота над уровнем моря не более 1000м.
В практике проектирования щитов существует несколько приемов размещения аппаратуры контроля и управления. Это функциональный принцип принцип значимости и частоты и последовательности.
Проектом предлагается разместить аппаратуру в соответствии с принципом последовательности то есть предполагается размещение приборов на панели строго по схеме их последовательного использования.
Приборы и аппаратуру в пределах одной секции размещаем симметрично. Применительно к условиям наилучшего восприятия информации оператором и манипулирования органами управления в практике проектирования щитов существуют оптимальные зоны размещения аппаратуры.
В чертеж общего вида единичного щита входят вид спереди на фронтальную плоскость щита таблица надписей на табло и в рамках перечень составных частей.
Чертежи общих видов щитов изображают в масштабе 1:5. Все приборы и средства автоматизации показывают упрощенно в виде внешних очертаний. Всем шкафам рамкам приборам и средствам автоматизации устанавливаемым на фасадах щитов и внутри них присваиваем номера позиций начиная с цифры 1 в порядке записи их в перечень составных частей. Номера позиции наносим на полки линий – выносок.
Проектом предлагается следующее размещение приборов:
С первого по второй ряд размещаем сигнальные лампы в следующем порядке. В первом ряду HL1– это лампа сигнализирующая о подачи питания на щит управления HL2 HL8 лампы сигнализирующие о работе ЭДВ1..ЭДВ7.
Во втором ряду с лампы сигнализирующие о работе ЭДВ8..ЭДВ9 и работе термоэлектрический нагреватель ТЭН10 ТЭН12
В третьем ряду располагаем переключатель «Выбор режима» и кнопку проверки сигнализации.
В четвертом ряду кнопочные переключатели для включения исполнительных механизмов.
В пятом и шестом рядах расположены кнопочные посты для управления двигателями.
Все приборы и сигнальная аппаратура располагаются соответственно с указанием их горизонтальных и вертикальных осей.
Общий вида щита содержит таблицу надписей на табло и в рамках. Она снабжается тематическим заголовком «Надписи на табло и в рамках». Каждой надписи присваивается номер и проставляется внутри контура табло или рамки слева направо сверху вниз. В таблицу также вначале включает надписи на табло затем в рамках при этом в графе «Наименование» указывают наименование и тип рамки. Надписи в рамках и на сигнальных табло должны быть лаконичными полностью определяющими значение элемента и не допускающими неоднозначного толкования.
Перечень составных частей щита состоит из двух разделов «Стандартные изделия» и «Прочие изделия». В раздел «Стандартные изделия» входят щитовые конструкции (то есть сам шкафной щит).
Раздел «Прочие изделия» содержит приборы аппаратуру и монтажные изделия по группам:
- электроаппаратура по функциональным группам
- аппаратура управления (ключи переключатели кнопки)
- сигнальная аппаратура выключатели
- монтажные изделия и рамки для надписей.
Внутри шкафного щита предусматриваются штепсельная розетка для присоединения переносной лампы и электрифицированного инструмента во время ремонтных работ. Включатель в цепях и штепсельная розетка размещается на боковых стенках щита.
При разработке вида на внутренние плоскости щита было разработана размещение электрических аппаратов не показанных на общем виде щита на левой стенке расположено: Диодная платаблок питанияраспределительная система ADAM-6000 модули ADAM (P1P2P3P4) клемная сборка (XT4) а также розетка(XS1).
На правой стенке расположено автоматические выключатели PL4-B 252 (SF1SF2)клемные сборки(XT1-XT3)а также промежуточные реле РП-53(K1-K14).
Для защиты от случайного опасного одновременного прикосновения к заземленному щиту и неизолированной токоведущей части приборов и аппаратов должны соблюдаться следующие требования:
- проходы обслуживания внутри щита имеющие открытые токоведущие части с напряжением на них выше 36В – ограничение не имеют.
- проходы обслуживания перед шкафным щитом – не менее 800мм и сзади них (не менее 800 мм) устанавливаемых в производственных помещениях.
На чертежах монтажных схем щитов контроля и управления в общем случае показывают:
Монтажную сторону щита;
Компоновку аппаратуры устанавливаемой внутри щита;
Спецификации монтажных изделий и перечень аппаратуры устанавливаемой внутри щита;
Исходными материалами для разработки монтажных схем являются:
– функциональная схема автоматизации;
– принципиальные схемы питания средств автоматизации;
– схемы электрических и трубных проводок.
Монтажная схема выполнена на основании принципиальной схемы и общего вида щита. Она выполнялась параллельно со схемой внешних соединений. Существует три метода выполнения монтажной схемы – это графический адресный или табличный.
Монтажная схема построена табличным способом.
Монтажная схема представляет собой вид на внутренней плоскости щита. На плоскости чертежа мы показываем: «Правая боковая панель» «Дверь» «Левая боковая панель».
На двери располагаем приборы которые изображены на фронтальной плоскости щита. Размеры приборов соблюдать не обязательно но должно быть выдержано соотношение приборов.
Для всех приборов указываем позиционные обозначения которые наносим над прибором в верхней части окружности. Позиционные обозначения проставляем слева направо сверху вниз. Для приборов и аппаратуры изображенных и не изображенных на фронтальной плоскости щита показываем позиции по принципиальной схеме или по перечню составных частей его показываем в нижней части окружности. Для блоков зажимов обозначение К и порядковый номер присвоенный блоку на данном чертеже.
Всем приборам и средствам автоматики присвоены номера а так же указаны позиции в соответствии со схемой электрической принципиальной. Нумерация производится по порядку справа налево на передней панели и 2 секциях сверху вниз соответственно на каждой стенке и панели щита.
Для блоков зажимов обозначение К и порядковый номер присвоенный блоку на данном чертеже.
После того как проставили маркировку переходим к адресации проводов. Адресация проставляем возле промаркированных проводов и указываем откуда пришел данный проводи и куда уходит.
Изображение таких приборов как автоматический выключатель SF1 SF2 кнопочные посты управления переключатели SA1.. SA2 контакты и реле напряжения розетка и диодная плата выполняется по ГОСТу принципиальной схемы.
Каждый прибор аппарат и средство автоматизации имеет маркировку соответствующую принципиальной схеме. Так сигнальные лампы расположенные на «Двери» имеют один общий 801 провод и второй провод приходящий с диодной платы. Например для лампы HL2 – это 401 для лампы HL3 – 402 провод.
На «Правой боковой панели» сверху вниз показана два автоматических выключателя SF1и SF2 второй для подачи питания на щит управления для подачи питания на розетку а первый для выбора режима работы. На переключатель SF1 приходит 800 провод а уходит провод с нумерацией 1 на SF2 приходит 800 а уходит 802. Под автоматическими выключателями располагаем промежуточные реле напряжения К1-К14. Реле напряжения K1..K14 имеют три контакта и катушку реле. Для всех реле задействован один контакт. В нижней монтажной части щита управления на схеме показаны соединения клеммных сборок К1-К3.
На «Двери» расположены сигнальные лампы HL1 HL13 переключатель SA1 кнопка SB13 переключатель SA2 кнопочные посты SB2 SB12 . Переключатель «Выбор режима» имеет три провода питания 802 ручное управление – провод 2 и автоматическое управление – провод с нумерацией 3. Далее располагаем переключатели для исполнительных механизмов: причем переключатель SA2 имеют два провода. Нумерацию проставляем по принципиальной схеме.
Кнопочные посты представляют собой связанные между собой кнопку «Пуск» и кнопку «Стоп». Рассмотрим метод адресации на примере кнопочного поста SB1 который имеет позиционное обозначение 42. В соответствии с принципиальной схемой автоматизации SB1 имеет три провода 2 4 5 которые идут на управление ЭДВ1. Провод 2 – это провод питания который тянется по всему щиту и является общим для всей аппаратуры ручного управления. Так для кнопочного поста SB1 провод 2 пришел с прибора 41 и ушел на прибор 36. Провод 4 непосредственно уходит на клеммную сборку 2К а провод 5 соединен с контактом K1.1 промежуточного реле K1 то есть уходит на промежуточное реле с адресом 3 и на управление магнитным пускателем КМ1 электродвигателя М1. Адресация остальных кнопочных постов аналогична вышеизложенной.
В верхней части “Левой стенки “ располагаем диодную плату с адресом 45 которая состоит из 12 диодов далле блок питания с позицией 45. Рассмотрим адресацию на диодной плате: провод 400 приходит с кнопки проверки сигнализации с позиционным обозначением 31. Все провода начиная с 401 и заканчивая 412 приходят с соответствующей сигнальной лампы. Например для провода 401- это сигнальная лампа HL2 с позиционным обозначением 23 и уходит на клеммную сборку 2К.
К блоку питания подходят два провода питания 801 и 802 и уходят 28 и 29 с питанием 30 V для распределительной системы ADAM с адресом 47. Модуль А1 имеет два провода на питания – это 2829 а также провода для подключения модулей Р1 Р2 Р3 Р4 – эти провода не имеют нумерации так как модуль может быть подключен в любой слот распределительной системы А1. В нижней монтажной части щита управления располагаем розеткук которой приходит провод 801 и уходит 1 позиционное обозначение которой 52 и показываем соединение клеммной сборок К4.
7.Схема внешних соединений
Схема внешних соединений проводок представляет собой комбинированную схему на которой показаны электрические и трубные связи между приборами и средствами автоматизации установленными на технологическом оборудовании вне щитов и на щитах а также подключение проводок к приборам и щитам.
Схема соединения внешних проводок выполняется без масштаба и является чисто монтажной. Она содержит собственно схему перечень монтажных материалов и изделий примечание с перечнем относящихся чертежей.
В верхней и нижней частях схемы у поясняющих и в принятом условном изображении применяемом при выполнении функциональной схемы автоматизации показываем отборные устройства чувствительные элементы исполнительные механизмы и другие элементы систем автоматизации которые на функциональной схеме автоматизации наносят непосредственно на коммуникации или оборудования технологической схемы.
Над ними располагаем поясняющую таблицу указывающую наименование технологического агрегата или аппарата контролируемого или регулируемого параметра среды а также место установки позицию по спецификации или обозначение по схемам приборов и средств автоматизации.
Каждому из этих процессов соответствуют свои чувствительные элементы исполнительные механизмы и магнитные пускатели. Так для процесса происходящего в отделении подготовка сырья– это двигатель ЭДВ1 и датчик массы. В графе «Позиция» проставляем позиционные обозначения приборов по функциональной схеме автоматизации для датчиков уровня – для ЭДВ1 и – КМ1.
После этого переходим к маркировке проводов которая соответствует принципиальной схеме автоматизации. Так для отделения подготовки сырья провода для подключения магнитного пускателя КМ1 имеют номера 4 5 802 401 801.
Графические изображения магнитных пускателей датчиков и исполнительных механизмов соответствуют функциональной схеме автоматизации.
Изображение последующих процессов на схеме внешних соединении аналогична вышеизложенным.
В средней части схемы в виде прямоугольника изображаем щит управления.
Электрические проводки между перечисленными приборами и устройствами систем автоматизации чертят на схеме сплошными линиями. Около каждой линии соответствующей электрической проводки указывают марку кабеля (провода) число жил их сечение и кроме того длину кабеля или провода в метрах. Кабель и провод прокладываем в защищенной трубе поэтому необходимо указать тип трубопровода его диаметр и длину. Перечисленные данные располагаем по линии изображающей проводку.
Электрической проводкой для исполнительного механизма является кабель с алюминиевой жилой АКВВГ 4х25 изоляция и оболочка из поливинихлоридного пластиката количество жил 4 с сечением 25мм.
Электрической проводкой для магнитных пускателей является алюминиевый кабель АКВВГ 7*25 резиновый гибкий с поливинилхлоридной оболочкой 7 жильный с сечением 25мм.
Электрической проводкой для датчиков влажности температуры является кабель КВВГ 4*1 то есть кабель с поливинилхлоридный жилой с поливинилхлоридной оболочкой гибкий четырехжильный с сечением 1 мм.
Для подачи питания на щит управления предусмотрена электрическая проводка 20 тип провода АПРТО 3*4 то есть провод с алюминиевой жилой резиновой оболочкой сечение жилы 4 мм.
Способ прокладки вышеописанных проводов – это труба пластиковая диаметром 40мм.
В курсовом проекте в соответствии с требованиями задания разработан проект лакокрасочных изделий с использованием современных решений в области автоматизации в частности с применением микроконтроллерной вычислительной техники.
В процессе разработке проекта особое внимание уделялось вопросам эффективного взаимодействия микроконтроллера с периферийными устройствами практической и экономической целесообразности предлагаемого решения а также вопросам охраны труда и техники безопасности. Разработаны функциональная принципиальная электрическая схемы схема общего вида щита управления монтажная схема щита и схема внешних соединений.
Внедрение АСУТП способствует увеличению производительности труда на предприятии улучшению качества вырабатываемой продукции повышению технической культуры производства. Успешное внедрение АСУТП возможно при наличии надежного безотказно работающего технологического оборудования и квалифицированного обслуживающего персонала.
Список использованных источников
А.В. Соколов «Автоматизация технологических процессов пищевой промышленности»: учебное пособие для студентов вузов – М.: Агропромиздат 1991.- 445с.: ил.
Петров И.К. Курсовое и дипломное проектирование по автоматизации производственных процессовМ. Высшая школа1986 г.-350 с.
А.С. Клюев Б.В. Глазов А.Х. Дубровский А.А. Клюев «Проектирование систем автоматизации технологических процессов»: Справочное пособие Под ред. А.С. Клюева. – 2-е изд. перераб. И доп. – М.: Энергоатомиздат 1990. – 464с.: ил.
Каталог продукции «Контрольно – измерительные приборы промышленных предприятий» - М.: 2004. – 152с.
А.И. Емельянов О.В. Капник «Проектирование систем автоматизации технологических процессов: Справочное пособие по содержанию и оформлению проектов» - 3-е изд. перераб. и доп. – М.: Энергоатомиздат 1983. – 400 с. ил.
Каталог ОВЕН 2014г. Оборудование для Автоматизации
Рекомендуемые чертежи
- 18.03.2021
- 09.06.2024