Ремонт и установка коленвала ВАЗ - 2112


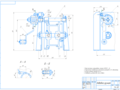
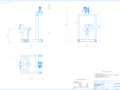
- Добавлен: 04.11.2022
- Размер: 13 MB
- Закачек: 1
Подписаться на ежедневные обновления каталога:
Описание
Курсовой проект - Ремонт и установка коленвала ВАЗ - 2112
Состав проекта
![]() |
![]() |
![]() |
![]() ![]() ![]() ![]() |
![]() ![]() ![]() |
![]() ![]() ![]() |
Дополнительная информация
Контент чертежей
Лебедка.cdw

Неуказанные предельные отклонения размеров по 14 квалитету
Усилие затяжки болтов 10 Н
Проверить устройство после сборки
КР Марусина готовое.docx
Принципиальные основы планово-предупредительной системы технического обслуживания и ремонта автомобилей установлены действующим Положением о техническом обслуживании и ремонте подвижного состава автомобильного транспорта.
Техническое обслуживание включает следующие виды работ: уборочно-моечные контрольно-диагностические крепежные смазочные заправочные регулировочные электротехническое и другие работы выполняемые как правило без разборки агрегатов и снятия с автомобиля отдельных узлов и механизмов. Если при техническом обслуживании нельзя убедиться в полной исправности отдельных узлов то их следует снимать с автомобиля для контроля на специальных стендах и приборах.
По периодичности перечню и трудоемкости выполняемых работ техническое об-служивание согласно действующему Положению подразделяется на следующие виды: ежедневное (ЕО) первое (ТО-1) второе (ТО-2) и сезонное (СО) технические обслуживания.
Положением предусматривается два вида ремонта автомобилей и его агрегатов: текущий ремонт (ТР) выполняемый в автотранспортных предприятиях и капитальный ремонт (КР) выполняемый на специализированных предприятиях.
В области материально-технического снабжения происходят революционные процессы. Брошен вызов традиционному поиску товара по минимальной цене и все больше внимания уделяется снижению общих затрат. Под общими затратами понимается закупочная цена плюс все фирменные издержки необходимые для превращения конкретного материала или услуги в конечный продукт готовый для использования. Внутрифирменные издержки включают затраты связанные с доставкой товара входящим контролем проверкой и испытаниями хранением производством предоставлением гарантий обслуживанием возвратами и потерями при реализации. В общие издержки входят также любые расходы связанные с неисправностью или плохой работой конечного изделия у потребителя причиной которой может быть дефект в закупленном материале.
Чтобы обеспечить снижение общих затрат работники отдела снабжения должны постоянно думать о качестве обслуживании технологическом процессе и приобретении нужного материала или услуги. Нередко для этого требуется организовать рабочую группу в состав которой входят представители проектно-конструкторского производственного транспортного отделов ОТК и подразделения по обслуживанию клиентов.
В то же время сотрудники отдела снабжения обязаны работать с каждым внутренним клиентом пытаясь выяснить что же в действительности они ожидают от поставщика. Снабженцы должны быть кроме всего прочего и хорошими продавцами для того чтобы убеждать своих "клиентов" подающих заявку в необходимости испробовать иные менее дорогостоящие методы для удовлетворения своих потребностей. Работнику отдела снабжения часто приходится доказывать что отдаваемое предпочтение какой-то марке и стоимости никак не связаны.
Объектами материально-технического снабжения комплексного АТП являются подвижной состав инструменты гаражное и ремонтное оборудование автомобильное топливо смазочные и прочие эксплуатационные материалы автомобильные шины запасные части материалы для ремонта автомобилей хозяйственное и технологическое топливо электроэнергия и т.д.
Задачами службы материально-технического снабжения являются:
- определение потребности в материальных и технических ресурсах изыскание возможности удовлетворения этой потребности;
- организация получения хранения и выдача материалов топлива оборудования автомобилей и других средств;
- контроль за использованием этих ресурсов.
Рис.1. Классификация факторов определяющих потребность в запасных частях и материалах
Служебное назначение и анализ конструкции
Коленчатый вал— деталь (или узел деталей в случае составного вала) сложной формы имеющая шейки для крепления шатунов от которых воспринимает усилия и преобразует их в крутящий момент. Составная часть кривошипно-шатунного механизма (КШМ).
Основные элементы коленчатого вала:
Коренная шейка— опора вала лежащая в коренном подшипнике размещённом в картере двигателя.
Шатунная шейка— опора при помощи которой вал связывается с шатунами (для смазки шатунных подшипников имеются масляные каналы).
Щёки— связывают коренные и шатунные шейки.
Передняя выходная часть вала (носок)— часть вала на которой крепится зубчатое колесо или шкив отбора мощности для привода газораспределительного механизма (ГРМ) и различных вспомогательных узлов систем и агрегатов.
Задняя выходная часть вала (хвостовик)— часть вала соединяющаяся с маховиком или массивной шестернёй отбора основной части мощности.
Противовесы— обеспечивают разгрузку коренных подшипников от центробежных сил инерции первого порядка неуравновешенных масс кривошипа и нижней части шатуна.
Коленчатый вал — пятиопорный отлит из чугуна. Поверхности шеек вала закалены токами высокой частоты на глубину 2-3 мм. В заднем конце коленчатого вала выполнено гнездо под передний подшипник ведущего вала коробки передач по наружному диаметру которого центрируется маховик.
Шатунные и коренные шейки коленчатого вала соединяются каналами по которым подводится масло для смазки шатунных подшипников. Технологические выходы каналов закрыты колпачковыми заглушками которые запрессованы и для надежности зачеканены в трех точках.
Рис.2. Коленчатый вал с маховиком.
Для продления срока службы коленчатого вала предусмотрена возможность перешлифовки шеек коленчатого вала при износе или повреждении их поверхностей. Шлифованием диаметры шеек уменьшаются на 025; 05; 075 и 100 мм.
Вкладыши коренных и шатунных подшипников -сталеалюминиевые. Верхние вкладыши 1- 2- 4- и 5-го коренных подшипников имеют канавку на внутренней поверхности а нижние без канавки (до 1987 г. нижние вкладыши этих подшипников устанавливались с канавкой). Вкладыши центрального (3-го) коренного подшипника отличаются от остальных большей шириной и отсутствием канавки на внутренней поверхности. Все вкладыши шатунных подшипников без канавок одинаковые и взаимозаменяемые.
Маховик отливается из чугуна и снабжен стальным зубчатым венцом для пуска двигателя стартером. Маховик устанавливается на коленчатый вал так чтобы метка (конусообразная лунка около зубчатого венца) — находилась против шатунной шейки 4-го цилиндра. Метка служит для определения ВМТ в первом и четвертом цилиндре.
Очистка каналов системы смазки
Для очистки удалите заглушки каналов. Затем прогоните гнезда заглушек зенкером А.9401610 надетым на шпиндель А.94016 тщательно промойте каналы бензином и продуйте сжатым воздухом.
Оправкой А.86010 запрессуйте новые заглушки и для большей надежности зачеканьте каждую заглушку в 3-х точках кернером.
Коренные и шатунные шейки
Проверка. Установите коленчатый вал крайними коренными шейками на две призмы и проверьте индикатором:
биение коренных шеек (максимально допустимое 003 мм);
биение посадочных поверхностей под звездочку и подшипник ведущего вала коробки передач (максимально допустимое 004 мм);
смещение осей шатунных шеек от плоскости проходящей через оси шатунных и коренных шеек (максимально допустимое ±035 мм).
неперпендикулярность по отношению к оси коленчатого вала торцевой поверхности фланца. При проворачивании вала индикатор установленный сбоку на расстоянии 34 мм от оси вала не должен показывать биения более 0025 мм.
На коренных шатунных шейках и на щеках коленчатого вала трещины не допускаются. Если они обнаружены замените вал.
На поверхностях коленчатого вала сопрягаемых с рабочими кромками сальников не допускаются царапины забоины и риски.
Измерьте диаметры коренных и шатунных шеек. Шейки следует шлифовать если их износ больше 003 мм или овальность шеек более 003 мм а также если на шейках есть задиры и риски.
Рис.3. Предельные размеры коренных и шатунных шеек вала.
Рис.4.Максимально-допустимый износ коренных и шатунных шеек вала.
Вкладыши коренных подшипников.
На вкладышах нельзя производить никаких подгоночных операций. При задирах рисках или отслоениях антифрикционного слоя замените вкладыши новыми.
Проверьте зазор между вкладышами и шейками коленчатого вала:
Расположите отрезок калиброванной пластмассовой проволоки на проверяемой шейке;
Установите крышки с коренными вкладышами и затяните крепежные болты крышек моментом 804 Н-м (82 кгс-м).
Снимите крышки и по величине сплющивания проволоки по шкале упаковки определите величину зазора.
Зазор между шейками коленчатого вала и вкладышами можно определить расчетом измерив диаметры коренных шеек постелей под вкладыши и толщину вкладышей.
Номинальный расчетный зазор составляет 0050— 0095 мм. Если он меньше предельного (015 мм) то можно снова использовать эти вкладыши. При зазоре большем предельного замените на этих шейках вкладыши новыми.
Рис.5. Толщина вкладышей шатунных подшипников
Если шейки коленчатого вала изношены и шлифуются до ремонтного размера то вкладыши замените ремонтными (увеличенной толщины).
Признаком правильности сборки и сопряжения шеек с вкладышами является свободное вращение коленчатого вала.
Проверьте состояние зубчатого обода и в случае повреждения зубьев замените маховик. Поверхности маховика сопрягаемые с коленчатым валом и с ведомым диском сцепления должны быть без царапин задиров и быть совершенно плоскими. Если на рабочей поверхности маховика под ведомый диск сцепления имеются царапины проточите эту поверхность снимая слой металла толщиной не более 1 мм. Затем проточите поверхность крепления сцепления выдерживая размер (05±01) мм. При проточке необходимо обеспечить параллельность поверхностей крепления сцепления и опорную поверхность ведомого диска сцепления относительно поверхности крепления к фланцу коленчатого вала. Допуск не параллельности составляет 01 мм.
Установите маховик на оправку центрируя его по посадочному отверстию с упором на поверхность крепления к фланцу коленчатого вала и проверьте биение плоскостей поверхности крепления сцепления и поверхности ведомого диска сцепления. В крайних точках индикатор не должен показывать биений превышающих 01 мм.
Проверка осевого зазора коленчатого вала.
Осевое перемещение коленчатого вала ограничено двумя упорными полукольцами установленными по обе стороны заднего коренного подшипника. С передней стороны подшипника устанавливается сталеалюминевое полукольцо а с задней стороны — металлокерамическое (желтого цвета). Полукольца изготавливаются нормальной толщины (2310—2360 мм) и увеличенной (2437—2487 мм). Осевой зазор между упорными полукольцами и упорными поверхностями коленчатого вала проверяется так:
установите индикатор на магнитной подставке и вставьте концы двух отверток;
переместите вал отвертками и проверьте по индикатору осевой зазор который должен быть в пределах 006-026 мм.
Если зазор превышает максимально допустимый 035 мм замените упорные полукольца другими увеличенными на 0127 мм. Осевой зазор коленчатого вала можно проверять также на двигателе установленном на автомобиле с помощью приспособления 67.8701.9510. При этом осевое перемещение коленчатого вала создается нажатием и отпусканием педали сцепления а величина осевого зазора определяется по перемещению переднего конца коленчатого вала.
Материал специальный высокопрочный чугун ВЧ-45. Твердость 250-350 HВ.
Возможные дефекты коленчатого вала
Допустимый без ремонта
Трещины на коренных шатунных шейках.
Износ коренных шеек в пределах ремонтных размеров
Измерьте диаметры коренных шеек микрометрами .
Шейки следует шлифовать ближайшего ремонтного размера если их износ больше 003 мм или овальность шеек больше 003 мм а также если на шейках есть задиры и риски.
Износ шатунных шеек в пределах ремонтных размеров
Измерьте диаметры шатунных шеек микрометрами .
Шейки следует шлифовать ближайшего ремонтного размера если их износ больше 003 мм или овальность шеек больше 003 мм.
Износ коренных шеек за пределами ремонтных размеров
Шейки следует восстановить наплавкой гальвано-покрытиями или другими способами.
Износ шатунных за пределами ремонтных размеров
Биение коренных шеек
Установите коленчатый вал на две призмы и проверьте индикатором
биение коренных шеек (максимально допустимое 003 мм). При превышении править.
Биение посадочных поверхностей под звездочку и подшипник первичного вала коробки передач
При превышении править.
Смещение осей шатунных шеек от плоскости проходящей через оси шатунных и коренных шеек
При превышении править
Неперпендику-лярность по отношению к оси коленчатого вала торцевой поверхности фланца.
Установите коленчатый вал на две призмы и проверьте индикатором. При проворачивании вала индикатор установленный сбоку на расстоянии 34 мм от оси вала не должен показывать биения более 0025 мм.
Разработка технологического процесса восстановления детали
Особенности конструкции детали
-Материал: высокопрочный чугун ВЧ-60-2
-Шероховатость ремонтных поверхностей и точность их обработки:
а) 5027 мм Ra =025 мкм
а) Для восстановления 5027мм будет служить 4975мм
-Класс детали: круглые стержни.
Условия работы детали при эксплуатации
Нагруженность детали
Вид трения изнашивание
Ударные вибрационные знакопеременные нагрузки. Скручивание изгиб.
Моторное масло масляная ванная.
Трение скольжения и каченя
Воздействие ГСМ картерных газов
Механические свойства материала детали химический состав
Высокопрочный чугун ВЧ 60-2.
Временное сопротивление разрыву – 40 - 60 кГмм²
Условный предел текучести при растяжении – 42 кГмм²
Относительное удлинение 2%
Высокопрочный чугун получается из серого чугуна путем присадки 03 – 12% магния.
Магний способствует выделению графита в виде шаровидных включений а также уменьшает количество серы и газов в металле очищает и улучшает чугун.
- Наименование: коленвал двиг-ля ВАЗ-2112
-Термообработка: закалка шеек ТВЧ НRС 50-60
- Материал: высокопрочный чугун ВЧ-60-2 НВ-197-269
а) Круглошлифовальный станок 3М131
б) Ванна для хромирования
в) Установка электроконтактной наплавки «Ремдеталь» 011-1-02 и ОКС-12296-ГОСНИТИ-для шеек валов.
- Требуемая точность:
а) Коренных шеек – 5027мм(2рем)
шероховатость Rа=025мкм
а) Круг шлифовальный ПВД 24
б) Проволка для наплавки Нп-30ХГСА
в) Полировочная паста ГОИ
г)Микрометр МК-0-300; 001 ГОСТ 6507-71
Определение припусков на обработку
Шлифовальная: шлифовать коренные шейки с последующей полировкой. Поверхность в размер5027-152
Расчет режимов обработки и норм времени
Поперечная подача на один оборот детали
Скорость вращения обрабатываемой детали
Vd = (С · D) (Тм · tх · у)
t = 003 мм – глубина шлифования и 0015 для чистового.
Vd =( 027 · 517903)( 1005 · 151 · 0551) =476 ммин и 35 для чернового.
n = (1000 · Vd) ( П · D) = (1000 · 47.6 ) (314 · 5179) = 374обмин
Мощность двигателя станка
Мощность на шпинделе Nшп = 6 кВт
То = (2 n · S ) · · К
= число проходов = в t = 025001 = 25
К = 17 – корректирующий коэффициент.
То = (2 · 49 374 · 35) · 25 · 17 = 03мин
Вспомогательное время
Топ = То + Твс = 03 + 042 = 072мин
Подготовительно – заключительное время
Тпз = Тпз1 + Тпз2 = 10 + 6 = 16мин
Тпз1 = 10мин – установка в самоцентрирующемся патроне
Тпз2 = 6мин - замена круга
Время на обслуживание рабочего места
Торм = Топ · Аобс100 = 072 · 006 = 004мин Аобс = 6%
Тшт = Топ + Торм = 072 + 004 = 076мин
Зачистка покрывающих поверхностей наждачной бумагой
Смонтировать деталь на подвеску
Изоляция поверхностей не подвергающихся покрытию
То = (Б · у · 1000 · 60) ( ДК · С · гте)
Б – толщина слоя – 03мм=003см
у – плотность покрытия – 69гсм3
С – электрохимический эквивалент – 0324гАч
ДК – плотность тока – 50-75
гте – выход металла по току – 15%
То = (003 · 69 · 1000 · 60 )( 75 · 0324 · 15%) = 34мин
Тв = 445мин – вспомогательное время
Топ = То + ТВ = 34 + 445 = 3845МИН
Дополнительное время
Тдоп = 3845 · 05% 100% = 019мин
Предварительно-заключительное время.
Тш = (То + Тв) · К Пд · К4
К4 – коэффициент использования ванн – 08
Пд – количество деталей – 1
К – коэффициент подготовки закл. Работ – 116
Тш = (34 + 445) · 116 1 · 08 = 558мин
Скорость подачи (S). S = 24 ммоб
Частота вращения детали (n)
N =1000 · Vн ПD =61 обмин.
D =5179 мм – диаметр детали после наплавки
Vн – скорость наплавки
Vн = (0785 · d2 · Vпр · к · а)(t · S) = 1ммин.
D = 2мм – диаметр проволоки Нп-30ХГСА
S = 24 подача проволоки на 1 оборот детали.
T =25мм – толщина наплавочного слоя.
к = 09 – коэффициент нанесения металла на поверхность
а = 099 – коэффициент неполноты наплавочного слоя.
Vпр = 204ммин – скорость подачи проволоки.
Qрм – объем расплавления металла
Qрм = Gрм 64см3мин = 85грсм2
Gрм – масса расплавленного металла
I = 0785 · d2 · Да = 2512А.
Да = 80Амм2 – плотность тока
d – диаметр проволоки.
Вспомогательное время (Тв).Тв = 1мин.
Основное время (Тосн)
Тосн =L · n · S = 133 200 · 242 = 002
Оперативное время(Топ). Топ = 002 + 1 = 102мин.
Дополнительное время (Тдоп). Тдоп = (Топ · 15%) 100 =015мин
Подготовительно-заключительное время(Тпз)
Тш = Тосн +Тв (ТпзП) = 2.31мин
Организация рабочих мест и техника безопасности
Рабочие места при восстановлении деталей должны быть оснащены:
- слесарными тисками;
- контрольной и правочной плитой;
- устройствами для хранения и размещения технологической документации и мерительного инструмента;
- в ящиках верстака в фиксированных местах весь слесарный необходимый инструмент;
Рабочее место станочника должно иметь:
- стеллаж или контейнер для деталей;
- грузоподъемные устройства;
- планшет или подставка для технической документации;
- местный светильник.
Техника безопасности при использовании электроинструмента:
- должна быть обеспечена исправность инструмента;
- выполнение работ с электроприборами осуществлять на резиновом коврике или деревянном трапе;
- для предупреждения поражения электрическим током все оборудование должно быть заземлено;
- электроустановки электрооборудование и проводку разрешается ремонтировать только после отключения от сети.
- останавливать деталь руками;
- придерживать обрабатываемую деталь руками;
- работать без ограждений;
- выполнять операции с приводными ремнями на ходу;
- оставлять ключ в патроне;
- работать без рукавиц и головного убора;
- без защитных очков;
- работать в одежде с широкими рукавами;
- оставлять обтирочный материал вблизи электроприборов;
- убирать стружку руками.
Требования к гальваническим участкам: помещения должны быть отделены от остальных цехов сплошными стенами или перегородками доведенными до перекрытия здания; высота помещения – не меньше 5 м; пол должен быть покрыт метлахской плиткой по асфальту или кослотно упорному цементу с уклоном 1 : 150 в сторону канализационного трапа; стены должны быть высотой 15 2 м и облицованы керамической плиткой или окрашивают масляной краской; наличие естественного и искусственного освещения; температура воздуха в зимнее время 17 22ºС влажность – не более 75%
Для удаления паров газов пыли и создания нормальных условий труда необходимо оборудовать участки мощной приточно-вытяжной вентиляцией. Приточно-вытяжная вентиляция должна быть исправной ее разрешается включать не позже чем за 15мин до начала работы а выключать не раньше чем через 15мин после окончания смены.
Ванны выделяющие вредные вещества по окончании работы следует закрывать крышками.
Штанги подвески и аноды следует чистить только мокрым способом смачивая металлические щетки или шлифовальное полотно водой так как пыль цветных металлов ядовита и вдыхание ее может вызвать отравление.
Подъемно-транспортное оборудование с механическим приводом обязательно регистрируется в инспекции Гостехнадзора которая проводит его техническое освидетельствование.
Стенд для разборки и сборки двигателей
Устройство и принцип работы модернизируемого стенда для разборки и сборки двигателей
Стенд (Рис.6.) предназначен для разборки и сборки двигателей.
Рис.6. – Стенд для разборки-сборки двигателей:
- рама 2 – колесо 3 – червячный редуктор 4 – рукоятка 5 – плита крепления двигателя 6 – домкрат гидравлический 7 – стоика лебедки 8 – лебедка ручная.
Стенд имеет рамную сварную конструкцию. К платформе 1 приварена стойка 7. Ремонтируемый двигатель крепят к плите 5 в которой имеются отверстия. Поворот двигателя на нужный угол осуществляют с помощью червячного редуктора 3. Привод вращения – ручной при помощи рукоятки 4.
В конструкции стенда присутствует гидравлический домкрат 6 с помощью которого производится изменение положения оси вращения ремонтируемого двигателя по вертикали.
В зависимости от типа ремонтируемого двигателя к установочной плите 5 крепятся различные сменные кронштейны с отверстиями.
На стойках 7 в верхней части смонтирована ручная лебедка 8 с помощью которой осуществляется подъем ремонтируемого двигателя для закрепления его на установочной плите.
На раме стенда установлены колеса причем задние колеса являются поворотными что позволяет транспортировать стенд к ремонтируемому двигателю для дальнейшего его закрепления.
Разработанный стенд отвечает выдвинутым требованиям: имеется ручная лебедка для подъема двигателей обеспечена универсальность. Универсальность стенда обеспечивается применением сменных кронштейнов для крепления двигателей различных марок.
Редуктор червячный РК-450 с ручным приводом
Редуктор цилиндрический двухступенчатый (специальный крановой) горизонтальный.
Редукторы специальные крановые типов РК-450 предназначены для использования в подъемно-транспортном оборудовании а также в качестве привода общего назначения.
Редукторы применяются при работе в повторно-кратковременном режиме т.е. при переменных нагрузках с периодическими остановками;
Допускается их длительная работа с постоянной нагрузкой;
Работа при нагрузке одного направления и реверсивная;
Вращение валов в любую сторону;
Частота вращения входного вала не более 1500 обмин;
Атмосфера типов I и II по ГОСТ 15150-69 при запыленности воздуха не более 10 мгм3;
Внешняя среда – неагрессивная невзрывоопасная;
Расчет устойчивости стенда
Во время работы грузоподъемные машины (ГПМ) подвергаются действию различных сил которые стремятся изменить их нормальное рабочее положение. К таким силам относятся: масса консольно-расположенных частей ветровая нагрузка масса поднимаемого груза динамические нагрузки возникающие при резком пуске и торможении механизмов и при движении ГПМ по неровному пути и др.
Устойчивость рассчитывается для следующих случаев: при действии груза (Рис.7.) при отсутствии груза при внезапном снятии нагрузки на крюке при монтаже или демонтаже ГПМ.
Рис.7. – Схема определения грузовой устойчивости стенда
В соответствии с ГОСТ 13994-81 проверяется устойчивость:
где Мо Мнwр Мнwн – опрокидывающие моменты относительно ребра опрокидывания соответственно от массы груза динамических нагрузок и от ветровой нагрузки рабочего и нерабочего состояния Н·м;
Муд – удерживающий момент относительно ребра опрокидывания от силы тяжести ГПМ Н·м;
Fg – нормативная составляющая массы груза Fg = 7200 Н;
bFg – расстояние от точки подвеса груза до вертикальной плоскости проходящей через ребро опрокидывания м;
Go – нормативная составляющая массы ГПМ кг;
bк – расстояние от центра масс частей ГПМ до вертикальной плоскости проходящей через ребро опрокидывания м.
где то – масса стенда то = 150 кг;
g – ускорение свободного падения g = 981 мс2.
Go = 150 · 981 = 14715 Н
Так как эксплуатация стенда предполагается внутри производственного помещения то опрокидывающими моментами относительно ребра опрокидывания от ветровой нагрузки рабочего Мнwр и нерабочего Мнwн состояния можно пренебречь.
Мо = 7200 · 0066 = 4752 Н·м.
Опрокидывающий момент от массы поднимаемого ГПМ груза тем больше чем больше масса груза и вылет крюка от ребра опрокидывания. Под ребром опрокидывания р-р понимается грань опорного контура относительно которой силы стремятся опрокинуть ГПМ.
Коэффициент устойчивости К представляет собой отношение удерживающего момента к опрокидывающему:
Условие устойчивости выполняется.
Расчет ручной лебедки
В качестве рабочего тягового органа лебедки применяется стальной канат выбираемый исходя из условия:
Fp – разрывное усилие каната Н;
s – запас прочности каната.
Согласно Правилам Госгортехнадзора стальные канаты рассчитывают на растяжение при запасе прочности s = 4 6 принимаем s = 5.
Нагрузка на одну ветвь каната определится как суммарная сила тяжести действующая на поднимаемый двигатель
Суммарная сила тяжести определяется из выражения
где m – масса поднимаемого двигателя m = 800 кг.
Fg = 981 · 800 = 7200 Н.
Fр = 5 ·7848 = 39240 Н.
Выбираем стальной канат типа ЛК-РО 6×36 (1+7+77+14)+1 о.с.
ГОСТ 7668-80 dк = 81 мм при = 1770 МПа с разрушающим усилием
Чтобы ограничить напряжения изгиба и достичь определенной долговечности каната рекомендуется наименьшие диаметры барабана и блока определять по формуле:
где е – коэффициент зависящий от типа грузоподъемника и режима эксплуатации e = 25:
Dб = (25 – 1) 81 = 1944 мм
Рабочая поверхность барабана выполняется с винтовой канавкой для направленной навивки стального каната. Многослойная навивка допустима только на гладкие барабаны но она приводит к повышенному износу каната.
Основные размеры барабана круглого полого сечения. Различают номинальный (расчетный) Dб определяемый по формуле наружный D и внутренний Dв диаметры.
Наружный диаметр измеряемый по дну канавок:
D = Dб – dк = 1944 – 81 = 1863 мм
Внутренний диаметр барабана:
где – толщина стенки барабана мм.
= 002 · Dб + (6 10) = 002 · 1944 + 6 = 99
Dв = 1863 – 2 · 99 = 1665 мм
Рис.8. – Эскиз барабана
Длина каната при однослойном наматывании на один барабан:
где Н – высота подъема или длина перемещения груза Н = 2000 мм;
z – число ветвей подвеса или тяги;
zн – число ветвей наматываемых на барабан.
Lо = 2000 1 1= 2000 мм
Число рабочих витков на барабане:
где 15 2 – запасные витки рекомендуемые Правилами Госгортехнадзора для разгрузки крепления каната на барабане.
zв – число рабочих витков;
l1 – длина концевой части барабана l1 = 14 мм.
Расчет стопорного устройства
Стопорные устройства или остановы применяют в механизмах с ручным приводом работающих с небольшими скоростями. В качестве такого устройства нами используется храповой останов. Остановы данной конструкции надежны в работе и более распространены. Их чаще всего монтируют на валу рукоятки (привода) получая менее громоздкую конструкцию. Храповые колеса изготавливают из стали реже из чугуна с внешним или внутренним зацеплением.
Основные размеры профиля зуба и храповика 1 (Рис.9.) принимают в зависимости от модуля m = 6 30 мм и числа зубьев z = 10 30:
DK = m z; р = т; h = (075 08) m; а = 155 m; b1 = b + (2 3) мм;
kb = b m так для стали 45 – kb = 1 2; для стали 35Л – kb = 15 4; для СЧ-15 – kb = 2 6.
Исходя из данных условий выбираем храповое колесо из стали 35Л с числом зубьев z = 10 и модулем m = 10.
DK = 10 10 = 100 мм; р = 314 10 = 314 мм; h = (075 08) 10 = 8 мм;
а = 155 10 = 155 мм; b = 25 · 10 = 25 мм; b1 = 25 + 2 3 = 28 мм;
Рис.9. – Останов храповой
– храповик; 2 - защелка; 3 – пружина
Из расчета зуба на изгиб определим необходимое значение модуля по выражению:
где Tс – статический момент на валу барабана
у – коэффициент формы зуба для внешнего зацепления у = 0375;
[]и – допускаемое напряжение изгиба для зуба для стали
Статический момент на валу барабана определится по формуле:
Тс = 05 · g · mo · Dб Нм
где mо = m + mг – общая масса груза и грузозахватного органа;
Dб – диаметр барабана м.
Тс = 05 · 981 · 800 · 1944 · 10–3 = 7628 Н·м.
При проверке кромки зуба на смятие линейная нагрузка:
где [р] – допускаемая нагрузка на единицу ширины кромки зуба с учетом динамического характера нагружения [р] = 300 400 Нмм.
Линейная нагрузка р = 3158 Нмм укладывается в интервал допускаемой нагрузки – [р] = 300 400 Нмм таким образом условие прочности выполняется.
Расчет на прочность барабана лебедки сводится к определению напряжений сжатия изгиба и кручения действующих на барабан.
Для проверки барабана на прочность должно выполняться условие:
где [] – допускаемое напряжение для барабана [] = 230 МПа (для материала барабана).
Условие прочности выполняется.
Приспособление для контроля отклонений от параллельности шеек коленчатого вала.
На (Рис.10.) изображено съемное приспособление для контроля отклонения от параллельности шатунной шейки относительно коренных шеек коленчатого вала. Корпус устройства выполнен в виде скобы усиленной ребрами жесткости и облегченной по массе
рядом высверленных отверстий. Базирование приспособления на контролируемом валу осуществляется на призмы; две верхние ИГ 1 и 2 закрепленные винтами указывают величину перекоса в плоскости расположения осей шеек а упор 3 и ИГ 4 - в плоскости перпендикулярной к осям шеек. Настройку ИГ приспособления осуществляют по эталонной детали.
Рис.10. Приспособление для контроля отклонений от параллельности шеек коленчатого вала:
- ИГ 3 - упор4 - ИГ.
Б.А.Малышев. Справочник технолога авторемонтного производства.М; Транспорт 1982-431с
С.И.Румянцев. Ремонт автомобилей и двигателей.М; Транспорт 1988-327с.
В.Е. Канорчук. Восстановление автомобильных двигателей: Технология и оборудование.М: Транспорт 1985-303с.
А.Г. Косилова. Справочник технолога-машиностроителя в 2-х томах. М: Машиностроение 1986-496с.280с
В.А. Аршинов. Резание металлов и режущий инструмент М; Машиностроение 1968-500с.
А.К. Горошкин. Приспособления для металлорежущих станков.М; Машиностроение 1979-303с
И.Е. Дюмин Г.Г. Трегуб Ремонт автомобилей. Транспорт 1999-280с.
А.А. Панов Справочник технолога.М; Машиностроение 1988-736с
В.С. Стародубцева Сборник задач по техническим нормам в машиностроении.М; Машиностроение.1974-272с.
Министерство образования и науки Российской Федерации
Федеральное Агентство по Образованию
Государственное Образовательное Учреждение Высшего
Профессионального Образования
Новосибирский Государственный Технический Университет
Расчетно-графическая работа
«Ремонт и установка коленвала ВАЗ»
марусина стенд.cdw
Максимальная грузоподъемность лебедки
Технические требования
* Размер для справок
Неуказанные предельные отклонения размеров по 14 квалитету
Усилие затяжки болтов 10 Н
Проверить устройство после сборки
Рекомендуемые чертежи
Свободное скачивание на сегодня
Обновление через: 12 часов 9 минут