Рекуперативный кожухотрубный парожидкостной теплообменный аппарат




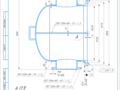
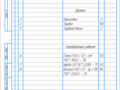
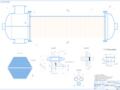
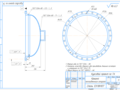
- Добавлен: 04.11.2022
- Размер: 652 KB
- Закачек: 2
Описание
Состав проекта
![]() |
![]() ![]() ![]() ![]() |
![]() ![]() ![]() ![]() |
![]() ![]() ![]() |
![]() ![]() ![]() |
![]() ![]() ![]() |
![]() ![]() ![]() |
![]() ![]() ![]() ![]() |
![]() ![]() ![]() |
Дополнительная информация
1 лист.cdw

Температура на выходе холодного теплоносителя T
Давление на входе горячего теплоносителя P
Расход холодного теплоносителя G
Суммарные потери давления
Схема движения теплоносителей - противоток
Длина матрицы ТА l = 2 м
Диаметр матрицы ТА D = 0
Объем матрицы ТА V = 0
Площадь поверхности ТО F = 84 м
Общее число трубок n
Скорость горячего теплоносителя w
Скорость холодного теплоносителя w
Зависимость площади ТО от скорости
холодного теплоносителя
Зависимость коэффициента теплопередачи от
скорости холодного теплоносителя
Зависимость количества трубок при однозаходном ТА
от скорости холодного теплоносителя
Зависимость длины матрицы ТА от
Зависимость скорости горячего теплоносителя
Курсовой проект по ТА
МГТУ им. Н. Э. Баумана
Определение скорости холодного теплоносителя
спецификация.spw

МГТУ им. Н. Э. Баумана
Распределительная камера
Шайба 20 ГОСТ 22355 - 77
2 лист.cdw
Обеспечить канализационный угол 2
для слива конденсата.;
Толщина слоя теплоизоляции - 20 мм
объем теплоизоляции - 0
Материал теплоизоляции - пенопласт ФРП-1.
Давление в трубках - 0
Давление в межтрубном пространстве - 0
Курсовой проект по ТА
Теплообменный аппарат
МГТУ им. Н. Э. Баумана
Схема расположения опорных поверхностей
4 лист (распределительная камера).cdw
ГОСТ 5264-80 - Т3 -
ГОСТ 5264-80 - С12 -
ГОСТ 5264-80 - Н2 -
ГОСТ 5264-80 - Н1 -
Сварные швы по ГОСТ 5264-80;
Контроль качества сварного шва производить внешним осмотром
и измерением по ГОСТ 3242-79;
Общие допуски по ГОСТ 30893.2 - тК.
Курсовой проект по ТА
Распределительная камера
теплообменного аппарата
МГТУ им. Н. Э. Баумана
4 лист (опора).cdw
Изготавливать в соответствии с требованиями стандарта ОСТ 26 - 291;
Дуговая сварка в защитном газе по ГОСТ 14771 - 76;
Контроль качества сварного шва производить внешним осмотром
и измерением по ГОСТ 3242 - 79;
Общие допуски по ГОСТ 30893.2 - тК.
Курсовой проект по ТА
теплообменного аппарата
МГТУ им. Н. Э. Баумана
4 лист (крышка).cdw
ГОСТ 5264-80 - Т1 -
Сварные швы по ГОСТ 5264 - 80;
Контроль качества сварного шва производить внешним осмотром
и измерением по ГОСТ 3242-79;
Общие допуски по ГОСТ 30893.2 - тК.
Курсовой проект по ТА
теплообменного аппарата
МГТУ им. Н. Э. Баумана
3 лист.cdw

Вальцовка по ГОСТ Р 55601-2013;
Момент затяжки резьбовых соединений 650 Н*м;
Контроль герметичности по ГОСТ 24054-80;
Общие допуски по ГОСТ 30893.2-тК;
Сварные швы по ГОСТ 5264-80.
Курсовой проект по ТА
МГТУ им. Н. Э.. Баумана
РПЗ.docx
Тепловой расчет .. .8
1. Составление теплового баланса ТА .8
2. Геометрические характеристики матрицы 8
3. Расчет коэффициента теплопередачи от греющего пара к наружной поверхности трубок .9
4. Расчет коэффициента теплоотдачи от внутренней поверхности трубок к нагреваемой воде .10
5. Расчет коэффициента теплопередачи .13
6. Определение площади поверхности ТО 13
Расчет проточной части трубного пространства .14
Поверочный расчет ТА ..17
Гидравлический расчет ..17
Расчет элементов конструкции ТА 18
1. Расчет корпуса и обечайки ..18
3. Расчет фланцев .20
4. Расчет трубной доски ..23
5. Расчет термических напряжений. .24
6. Расчет на устойчивость корпуса .25
Прочностной расчет ..26
2. Расчетные напряжения в элементах конструкции 30
3. Проверка прочности трубной решетки 35
4. Проверка прочности трубок ..35
5. Проверка трубок на устойчивость 36
6. Проверка жесткости трубок ..36
7. Проверка прочности крепления трубок в решетке .36
Расчет теплоизоляции 37
Закрепление трубок в трубных досках ..40
Элементы конструкции ТА 41
Пусконаладочные работы .42
Обслуживание и ремонт ТА .42
Список использованных источников .45
Разработать рекуперативный кожухотрубный парожидкостной теплообменный аппарат.
Температура на входе холодного теплоносителя Tв1 = 329 К.
Температура на выходе холодного теплоносителя Tв2 = 388 К.
Давление на входе горячего теплоносителя pп = 02 МПа.
Расход холодного теплоносителя Gв = 197 кгс.
Суммарные потери давления pΣ = 25%.
Теплообменные аппараты составляют большую часть оборудования теплогенерирующих и теплоиспользующих установок – элементы котлоагрегатов конденсаторы паровых турбин деаэраторы подогреватели систем регенеративного подогрева питательной воды котлов экономайзеры воздухоподогреватели подогреватели сетевой воды а также различные конденсационные и испарительные аппараты вентиляционные сушильные выпарные холодильные установки радиаторы калориферы и т.д.
Целью выполнения курсового проекта является проектирование рекуперативного кожухотрубного парожидкостного теплообменного аппарата.
Теплообменные аппараты представляют собой устройства для передачи теплоты от одного теплоносителя к другому. Теплоносителями или рабочими средами называют жидкие или газообразные вещества участвующие в процессах теплообмена. Теплоноситель имеющий большую температуру называют греющим (горячим) теплоноситель с меньшей температурой – нагреваемым (холодным).
Предназначены ТА для обеспечения технологических процессов в которых осуществляется нагрев или охлаждение теплоносителей повышения эффективности и надежности энергетического оборудования.
Теплообменные аппараты должны отвечать следующим основным требованиям:
)обеспечивать требуемые конечные температуры теплоносителей и передачу соответствующей теплоты;
)должны быть надежными в эксплуатации;
)материалы из которых они изготавливаются должны быть стойкими к химическим и термическим воздействиям со стороны теплоносителей;
)конструкция ТА должна быть проста в эксплуатации;
)металлоемкость конструкции должна быть оптимальной чтобы обеспечивать высокую экономическую эффективность.
В рекуперативных ТА оба теплоносителя находятся в аппарате одновременно и обмениваются теплотой через разделяющую стенку за счет теплопередачи. Большинство рекуперативных ТА работают в стационарном режиме. Рекуператорами являются парогенераторы подогреватели охладители конденсаторы и т.п.
В парожидкостных ТА греющим теплоносителем является пар нагреваемым – жидкость. Область применения их весьма широка: подогреватели питательной воды котельных агрегатов высокого и низкого давления конденсаторы паровых турбин подогреватели сетевой воды в системах отопления и горячего водоснабжения. Кроме того используются в химической пищевой целлюлозно – бумажной и других отраслях промышленности для подогрева различных рабочих жидкостей в технологических процессах производства.
Кожухотрубные аппараты выполняются в виде пучка трубок помещенных в общий корпус (кожух). Один из теплоносителей пропускается по трубкам второй проходит в межтрубном пространстве пучка.
1. Составление теплового баланса ТА
Находим по таблице насыщенных паров:
При pп = 200 кПа Тп = 39323 К – температура насыщенного пара.
i2 = 2706900 Джкг – энтальпия сухого насыщенного пара
Удельная теплота конденсации:
Средняя удельная теплоемкость воды:
Принимаем КПД ТА 98%.
Расход греющего пара:
Теплота поглощаемая нагреваемой водой:
2. Геометрические характеристики матрицы
Задаемся наружним и внутренним диаметрами трубок:
dн = 12 мм; dв = 10 мм
толщина стенки трубки:
коэффициент фронта пара:
коэффициент фронта воды:
коэффициент компактности пара:
коэффициент компактности воды:
эквивалентный диаметр пара:
3. Расчет коэффициента теплопередачи от греющего пара к наружной поверхности трубок
Средняя температура воды:
Температура поверхности трубок:
Средняя температура пленки конденсата:
Теплофизические свойства конденсата определяем по средней температуре пленки:
Приведенная длина трубки:
Коэффициент теплоотдачи пара:
4. Расчет коэффициента теплоотдачи от внутренней поверхности трубок к нагреваемой воде
Теплофизические свойства воды определяем по ее средней температуре:
Коэффициенты потерь на входе и выходе для воды:
Потери давления не зависящие от скорости:
Логарифмический температурный напор:
Средний диаметр трубок:
Приведенный диаметр:
Зависимость суммарных потерь давления от скорости воды:
Принимаем давление воды: pв = 200 кПа
Строим график относительных потерь:
Рис. 1. Определение скорости холодного теплоносителя
находим максимально допустимую скорость воды по потерям:
Принимаем скорость воды wв = 05 мс.
Коэффициент теплоотдачи воды:
5. Расчет коэффициента теплопередачи
Коэффициент теплопроводности стенки трубок:
Коэффициент теплопередачи:
Рис. 2. Зависимость коэффициента теплопередачи от скорости холодного теплоносителя
6. Определение площади поверхности ТО
Площадь поверхности ТО находится из уравнения теплопередачи:
Рис. 3. Зависимость площади поверхности ТО от скорости холодного теплоносителя
Расчет проточной части трубного пространства
Определение количества трубок при одном ходе:
Рис. 4. Зависимость количества трубок от скорости холодного теплоносителя
Определение расчетной длины трубки при одном ходе:
Рис. 5. Зависимость длины матрицы ТА от скорости холодного теплоносителя
Определение числа ходов:
Принимаем число ходов Z = 2.
Определение общего количества трубок с учетом принятого количества ходов:
Коэффициент заполнения трубной доски: при Z = 2.
Диаметр трубной доски:
Диаметр патрубка воды:
Диаметр патрубка пара:
Окончательные параметры: рабочая длина трубок 2 м;
общее число трубок 1102;
диаметр трубной доски 0678 м
Поверочный расчет ТА
Для выбранного ТА необходимо провести поверочный расчет с целью выяснения обеспечит ли этот аппарат требуемое значение температуры воды на выходе. Расчет проводится на основе уравнений теплового баланса и теплопередачи.
Расчетная площадь поверхности ТО:
Расчетная температура воды на выходе:
Расхождение заданного и расчетного значений температуры воды:
Гидравлический расчет
Коэффициент сопротивления трению:
Потери давления за счет сил трения:
Потери давления за счет местных сопротивлений:
коэффициент местного сопротивления для входной камеры;
коэффициент местного сопротивления для выходной камеры;
коэффициент местного сопротивления для входа в трубное пространство;
коэффициент местного сопротивления для выхода из трубного пространства;
коэффициент местного сопротивления для поворота между ходами.
Общее гидравлическое сопротивление:
Получившаяся величина меньше максимальных допустимых потерь давления.
Мощность нагнетателя:
Расчет элементов конструкции ТА
1. Расчет корпуса и обечайки
Материал – сталь Ст12Х18Н10Т.
Номинальная толщина стенки цилиндрической обечайки корпуса не ослабленной отверстиями:
p – расчетное давление МПа;
D – внутренний диаметр корпуса аппарата;
φр – расчетный коэффициент прочности продольного сварного шва;
[] – допускаемое напряжение МПа;
С – прибавка к толщине стенки м.
Коэффициент прочности обечайки ослабленной неукрепленным отверстием:
Расчетная толщина обечайки корпуса:
Толщина обечайки корпуса Sр = 8 мм.
Наибольший предельный диаметр неукрепленного отверстия:
Т. к. наибольший диаметр патрубка меньше наибольшего предельного диаметра неукрепленного отверстия то укрепления отверстия не требуется.
Форма днища – эллиптическая.
Длина цилиндрической части днища hц = 25 мм.
Принимаем h = 140 мм.
Радиус кривизны в верхней точке:
Минимальная толщина днища:
Принимаем толщину днища S = 8 мм.
D = 0678 м => шпилька М20 => d0ш = 20 мм
Материал шпильки – сталь 35Х.
Поправочный коэффициент:
Диаметр отверстия под шпильки d0 = 23 мм.
Прокладка: плоская неметаллическая (резиновая);
ширина прокладки b0 = 15 мм;
расстояние от внутренней кромки фланца u = 3 = 9 мм;
толщина прокладки = 3 мм.
Рис. 6. Размеры фланца
Наружный диаметр прокладки:
Диаметр болтовой окружности:
Шаг шпилек: p 25 МПа => 21d0 iш 5d0
Расчетное количество шпилек:
Принимаем количество шпилек Z = 28.
Проверка выполнения условия прочности для шпилек
Расчетный диаметр прокладки:
Эффективная ширина: b = b0 = 15 мм;
Удельное давление на прокладку в рабочих условиях:
Минимальное усилие на прокладку необходимое для сохранения плотности при рабочих условиях:
Растягивающее усилие в шпильках от рабочего давления:
Расчетное усилие воспринимаемое шпильками в рабочих условиях:
Напряжение в шпильках в рабочих условиях:
[] = 152 МПа => условие прочности шпилек выполнено.
Материал – сталь 20К
dш = 20 мм => d0 = 23 мм; e = 35 мм; a = 10 мм; 2a1 = 6 мм.
Наружный диаметр фланца:
Толщина тарелки фланца:
Принимаем hф = 23 мм.
Рис. 7. Расчетная схема фланца
Плечи моментов сил действующих на фланец:
Изгибающий момент от усилий действующих в рабочем состоянии:
Значение редуцированного диаметра отверстия под шпильки:
Момент сопротивления фланца:
Напряжение во фланце:
[] = 220МПа => прочность фланца обеспечена.
4. Расчет трубной доски
Материал – сталь 20К.
Коэффициент прочности трубной доски:
Толщина трубной доски без анкерных связей:
Расчетная толщина трубной доски:
Принимаем Sтр = 28 мм.
5. Расчет термических напряжений
Температура корпуса: tк = tп = 12023
Температура трубок: tт = tв = 115
Разность между рабочей температурой корпуса и температурой окружающей среды:
Разность между рабочей температурой трубок и температурой окружающей среды в момент изготовления аппарата:
Площадь поперечного сечения корпуса:
Площадь поперечного сечения трубок:
S – толщина стенки корпуса;
N – количество трубок в аппарате.
Осевая сила растягивающая корпус и трубки и возникающая под действием давления среды:
Модули упругости материала корпуса и трубок: Eк = Eт = 202*104 МПа
Сила взаимодействия между корпусом и трубками за счет температурных расширений:
αк = αт = 116*10-6 1 - коэффициенты линейного расширения трубок и корпуса аппарата.
Напряжения в корпусе:
Напряжения в трубках:
Т.к. к и т меньше [] = 130 МПа то компенсация температурных расширений не требуется.
6. Расчет на устойчивость корпуса
Средний диаметр оболочки корпуса:
Длина корпуса L = 2 м;
Предел текучести материала корпуса т = 220 МПа.
Критическая длина тонкостенной оболочки:
Критическое напряжение при 05Dc L Lкр:
Критическое давление:
Допустимое с точки зрения устойчивости наружное давление:
Т.к. pд > pатм = 01 МПа и L Lкр то можно считать корпус устойчивым и не требующим дополнительного ужесточения.
A – коэффициент для определения максимального изгибающего момента в перфорированной части трубной решетки;
a – внутренний радиус кожуха мм;
a1 – расстояние от оси кожуха до оси наиболее удаленной трубки мм;
b1 – ширина тарелки фланца кожуха мм;
b2 – ширина тарелки фланца камеры мм;
c – расчетная прибавка к толщине мм;
D – внутренний диаметр кожуха мм;
Dн – наружный диаметр фланца мм;
dт – наружный диаметр трубки мм;
Eр – модуль продольной упругости материала решетки МПа;
ED – модуль продольной упругости материала камеры МПа;
Eк – модуль продольной упругости материала кожуха МПа;
Eт – модуль продольной упругости материала трубок МПа;
E1 – модуль продольной упругости материала фланца кожуха МПа;
E2 – модуль продольной упругости материала фланца камеры МПа;
h1 – толщина тарелки фланца кожуха мм;
h2 – толщина тарелки фланца камеры мм;
Jт – момент инерции поперечного сечения трубки мм4;
Kq – коэффициент изменения жесткости системы трубки – кожух при действии осевой силы;
Kq* - отношение осевого перемещения компенсатора или расширителя при действии растягивающей силы к осевому перемещению краев корпуса межтрубного пространства без компенсатора и расширителя от действиятой же силы;
Kp – коэффициент изменения жесткости системы трубки – кожух при действии давления;
Kp* - отношение осевого перемещения компенсатора или расширителя при действии давления к осевому перемещению краев корпуса межтрубного пространства без компенсатора и расширителя от действия того же давления;
Ky – модуль упругости основания Нмм3;
Kф – коэффициент жесткости фланцевого соединения при изгибе Н*мм;
Kф1 – коэффициент жесткости фланца кожуха при изгибе Н*мм;
Kф2 – коэффициент жесткости фланца камеры при изгибе Н*мм;
K1 – коэффициент жесткости втулки фланца кожуха при изгибе Н*мм;
K2 – коэффициент жесткости втулки фланца камеры при изгибе Н*мм;
Kт – коэффициент условий работы при расчет труб на устойчивость;
Ma – изгибающий момент распределенный по периметру перфорированной части трубной решетки Н*мммм;
Mп – изгибающий момент распределенный по периметру трубной решетки Н*мммм;
Mт – изгибающий момент действующий на трубку Н*мм;
mA – коэффициент для определения максимального изгибающего момента в перфорированной части трубной решетки;
mср – коэффициент влияния давления на продольную деформацию трубок;
mn – относительная характеристика беструбного края трубной решетки;
m1 – коэффициент влияния давления на изгиб 1 – го фланца мм2;
m2 – коэффициент влияния давления на изгиб 2 – го фланца мм2;
Nт – осевая сила действующая на трубку Н;
pм – расчетное давление в межтрубном пространстве МПа;
pт – расчетное давление в трубном пространстве МПа;
p0 – приведенное давление на решетку МПа;
p1 – приведенное давление на фланцы МПа;
Qa – перерезывающая сила распределенная по периметру перфорированной зоны решетки Нмм;
Qп - перерезывающая сила распределенная по краю трубной решетки Нмм;
R1 – радиус центра тяжести тарелки фланца кожуха мм;
R2 – радиус центра тяжести тарелки фланца камеры мм;
sк – толщина стенки кожуха мм;
sр – толщина трубной решетки мм;
sт – толщина стенки трубы мм;
s1 – толщина стенки кожуха в месте соединения с трубной решеткой или фланцем мм;
s2 – толщина стенки камеры в месте соединения с трубной решеткой или с фланцем мм;
s1р – толщина решетки в зоне кольцевой канавки мм;
T1 T2 T3 – коэффициенты учитывающие влияние беструбного края и влияние труб;
tк – средняя температура стенки кожуха ;
tт – средняя температура стенок трубок ;
t0 – температура сборки аппарата ;
αк – коэффициент линейного расширения материала кожуха 1;
αт – коэффициент линейного расширения материала трубок 1;
– коэффициент системы решетка – трубки 1мм;
– коэффициент системы кожух – решетка 1мм;
– коэффициент системы обечайка – фланец камеры 1мм;
м т – коэффициенты влияния давления на трубную решетку со стороны межтрубного и трубного пространства соответственно;
ρ – приведенное отношение жесткости труб к жесткости кожуха;
ρ1 – приведенное отношение жесткости труб к жесткости фланцевого соединения;
р1 – изгибные напряжения в трубной решетке в месте соединения с кожухом МПа;
р2 – изгибные напряжения в перфорированной части трубной решетки МПа;
– суммарные напряжения в трубках в осевом направлении МПа;
т – мембранные напряжения в трубках в осевом направлении МПа;
т – мембранные напряжения в трубках в окружном направлении МПа;
р1 – касательные напряжения в трубной решетке в месте соединения с кожухом МПа;
р2 – касательные напряжения в перфорированной части трубной решетки;
Ф1 Ф2 Ф3 – коэффициенты учитывающие поддерживающее влияние трубок;
φр – коэффициент ослабления решеток трубчатых ТА с неподвижными трубными решетками;
φт – коэффициент уменьшения допускаемого напряжения при продольном изгибе;
– коэффициент жесткости перфорированной плиты;
– безразмерный параметр системы решетка – трубы.
2. Расчетные напряжения в элементах конструкции
Крепление трубной решетки к кожуху или фланцу
Рис. 8. Решетка приваренная втавр к обечайке корпуса
Изгибные напряжения в трубной решетке в месте соединения с кожухом
Коэффициент влияния давления на трубную решетку со стороны межтрубного пространства:
Коэффициент влияния давления на трубную решетку со стороны трубного пространства:
Модуль упругости основания:
Коэффициент системы решетка – трубки:
Безразмерный параметр системы решетка – трубки:
Относительная характеристика беструбного края трубной решетки:
Исходя из значений и mn определяем значения:
T1 = 483; T2 = 2238; T3=15.
Приведенное отношение жесткости трубок к жесткости кожуха:
Коэффициенты изменения жесткости системы трубки – кожух:
Коэффициент влияния давления на продольную деформацию труб:
Приведенное давление:
Приведенное отношение жесткости труб к жесткости фланцевого соединения:
Изгибные напряжения в трубной решетке в месте соединения с кожухом:
Перерезывающая сила:
Касательные напряжения в трубной решетке в месте соединения с кожухом:
Изгибающий момент в перфорированной зоне решетки:
Перерезывающая сила в перфорированной зоне решетки:
Максимальный расчетный изгибающий момент в перфорированной части трубной решетки:
Коэффициент ослабления решеток: φр = 048.
Изгибные напряжения в перфорированной части трубной решетки:
Касательные напряжения в перфорированной части трубной решетки:
Коэффициенты учитывающие поддерживающее влияние труб:
Ф1 = 13928; Ф2 = 96; Ф3 = 13648
Осевая сила действующая на трубку:
Мембранные напряжения в трубках в осевом направлении:
Изгибающий момент действующий на рубку:
Суммарные напряжения в трубках в осевом направлении:
Напряжения в трубках в окружном направлении:
3. Проверка прочности трубной решетки
Условие статической прочности:
Статическая прочность трубной решетки обеспечена.
4. Проверка прочности трубок
Условие статической прочности трубок:
Статическая прочность трубок обеспечена.
5. Проверка трубок на устойчивость
Условие устойчивости:
Коэффициент φт находится из зависимости от λ: φт = 01.
Устойчивость трубок обеспечена.
6. Проверка жесткости трубок
Проверку жесткости трубок проводят только при Nт 0.
В нашем случае Nт > 0 следовательно проверку проводить не надо.
7. Проверка прочности крепления трубок в решетке
Условие прочности крепления:
Прочность крепления трубок в решетке обеспечена.
Расчет теплоизоляции
Наружную поверхность ТА необходимо покрыть теплоизолирующим материалом с целью снижения тепловых потерь и обеспечения требований безопасности охраны труда при обслуживании установок.
Назначим температуру поверхности слоя теплоизоляции tиз = 35.
Тепловой поток от поверхности теплоизоляции:
α0 – коэффициент теплоотдачи в окружающую среду Втм2*К;
F – площадь поверхности ТА;
t0 – температура окружающей среды .
Тепловой поток в теплоизоляции:
λиз – коэффициент теплопроводности материала изоляции Втм*К;
из – толщина материала изоляции м;
tст – температура стенки ТА .
Принимаем материал изоляции – пенопласт ФРП - 1 λиз = 0033 Втм*К.
Необходимо определить коэффициент теплоотдачи во внешнюю среду.
D – наружный диаметр корпуса ТА м;
в = 1506*10-5 м2с – коэффициент кинематической вязкости воздуха.
Коэффициент объемного расширения воздуха:
Коэффициент теплоотдачи во внешнюю среду:
Необходимая толщина теплоизоляции 20мм.
Подбор опор выполняем по ОСТ 26 – 1265 – 75. Диаметр оболочки ТА больше 600 мм значит выбираем опору 2 типа. Одна из опор должна быть подвижной. Конструкция и размеры подвижной и неподвижной опор совпадают за исключением формы отверстия под фундаментные болты.
Конструктивное исполнение подвижной опоры приведено на рис. 9. Выбираем исполнение 1. По таблице приведенной в ОСТ назначаем размеры.
s2 = 15 мм;B = 250 мм;
R = 362 мм;B2 = 350 мм;
L = 630 мм;A = 480 мм.
Рис. 9. Седловая опора для горизонтальных аппаратов
В качестве материала для опор работающих при температуре рабочей среды от -40 до 350 назначаем сталь Ст3пс4 по ГОСТ 5520 технические требования по ГОСТ 14637.
К бетонному фундаменту опора крепится при помощи болта фундаментного М28 по ГОСТ 24379.0.
Подбираем стальные приварные фланцы по ГОСТ 12820 – 80. Для данного ТА необходимо подобрать фланцы с условным проходным диаметром 100 250 300 мм и с расчетным давлением 1 МПа.
Для фланца Dу = 100 мм:
D = 435 мм; D1 = 395 мм; D2 = 353 мм; Dв = 316 мм; d = 22 мм; n = 12; b = 20.
Для фланца Dу = 250 мм:
D = 370 мм; D1 = 335 мм; D2 = 297 мм; Dв = 266 мм; d = 18 мм; n = 12; b = 20.
D = 205 мм; D1 = 170 мм; D2 = 132 мм; Dв = 110 мм; d = 18 мм; n = 4; b = 20.
Рис. 10. Фланец стальной приварной
Закрепление трубок в трубных досках
Закрепление трубок в трубных досках проводится с помощью развальцовки их концов.
Развальцовка выполняется по ГОСТ Р 55601 – 2013.
Рис. 11. Вальцовочное соединение типа Р4
Элементы конструкции ТА
Распределительная камера
Шпилька М20 х 15 – 6g х 100
Корпус ТА устанавливают на двух седловых опорах: неподвижной и подвижной. Подвижная опора для температурной компенсации может скользить по фундаменту за счет овальной формы болтовых отверстий. К обечайке корпуса ТА опорный лист приваривается внахлестку прерывистым швом.
Торцы обечайки корпуса ТА вставляются в пазы в трубных досках. Обечайку корпуса и трубную доску фиксируют сварным тавровым швом.
При сборке прямые трубки вставляют в отверстия одной трубной доски и прогоняют по всей длине до другой трубной доски. Закрепление трубок в трубных досках реализуется за счет развальцовки их концов так как при этом способе закрепления можно заменить трубки в случае появления в них дефектов.
К фланцам трубных досок при помощи шпилечного соединения крепятся распределительная камера и крышка ТА. Шпильки в отверстиях устанавливаются с зазором.
После сборки теплообменный аппарат покрывают слоем теплоизоляции.
Пусконаладочные работы
При проведении пусконаладочных работ необходимо:
Установить соответствие смонтированного оборудования проекту и техническим требованиям;
Испытать на герметичность и прочность все смонтированные теплотехнические элементы оборудования;
Оформить необходимую техническую документацию по сдаче – приемке смонтированного оборудования;
Провести индивидуальное опробование смонтированного оборудования и определить пригодность его к последующей эксплуатации;
Опробовать совместную работу ТА и вспомогательного теплообменного оборудования при полной нагрузке.
Обслуживание и ремонт ТА
Типовая структурная схема технологического процесса характеризующая средний и капитальный ремонты теплообменного оборудования по наработке:
Рис. 12. Структурная схема процесса ремонта ТА
При ремонте ТА проводятся следующие работы:
Ремонт водяных камер каркаса трубного пучка;
Очистка трубных досок трубок межтрубного пространства;
Замена трубок включая их вырезку установку новых трубок закрепление трубок в трубных досках;
Проверка герметичности.
Снятие ремонт установка крышек водяных камер
Открепить и снять крышки ТА прокладки. Зачистить уплотнительную поверхность крышек и фланцев. Установить новые уплотняющие прокладки на фланец. Установить на место крышки. Затянуть гайки с последующей подтяжкой после гидроиспытания.
Очистка водяного пространства
Очистить трубные доски и водяные камеры от мусора и отложений. Провести очистку водяных камер и трубных досок. Промыть водой.
Проверка на герметичность
Установить жесткие опоры под ТА заполнить паровое пространство конденсатом. Осмотреть трубные доски обнаруженные протечки устранить подвальцовкой или отглушением поврежденных трубок. Слить конденсат заполнить водяное пространство ТА проверить герметичность фланцевых разъемов крышек устранить протечки и убрать жесткие опоры.
Выполнено проектирование рекуперативного кожухотрубного парожидкостного теплообменного аппарата.
Основные параметры ТА:
Схема движения теплоносителей – противоток.
Длина матрицы ТА l = 2 м.
Диаметр матрицы ТА D = 0678 м.
Объем матрицы ТА V = 0722 м3.
Площадь поверхности теплообмена F = 84 м2.
Общее число трубок n0 = 1102 шт.
Скорость горячего теплоносителя wп = 107 мс.
Скорость холодного теплоносителя wв = 05 мс.
Список использованных источников
Расчет рекуперативного парожидкостного теплообменного аппарата: методические указания сост.: И. Н. Дюкова [и др.]. – СПб.: СПбГЛТУ 2016. – 48 с.
Теплообменные аппараты и системы охлаждения газотурбинных и комбинированных установок: Учебник для вузов Иванов В. Л. Леонтьев А. И. Манушин Э. А. Осипов М. И.; Под ред. Леонтьева А. И. – М.: Изд – во МГТУ им. Н. Э. Баумана 2003. – 592 с.: ил.
Варгафтик Н. Б. – Справочник по теплофизическим свойствам газов и жидкостей.
Идельчик И. Е. – Справочник по теплогидравлическим сопротивлениям. М.: Машиностроение. 1992. 672 с.
Васильев Н. В. – Лекционный материал ТА.