Проектирование привода цепного конвеера (редуктор цилиндрический прямозубый)




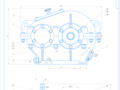
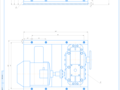
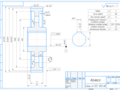
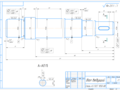
- Добавлен: 04.11.2022
- Размер: 404 KB
- Закачек: 2
Описание
Состав проекта
![]() |
![]() ![]() ![]() |
![]() ![]() ![]() |
![]() ![]() ![]() ![]() |
![]() ![]() ![]() |
![]() ![]() ![]() |
![]() ![]() ![]() |
Дополнительная информация
А3 колесо.cdw
Нормальнй исходный контур
Сталь 45 ГОСТ 1055-88
А1 Сборочный.cdw

Техническая характеристика
Редуктор с наружным расположением подшипниковых бобышек.
Боковые крышки выполнены накладными.
Число оборотов выходного вала nвых=302 обмин.
Передаточное число редуктора U=3
Крутящий момент на выходном валу Твых=117 Нм.
Объем масляной ванны - 2 л.
Технические требования
Поверхности соединения "корпус-крышка" перед сборкой покрыть уплотнительной пастой типа "Герметик".
Крышка ведущего вала сквозная
Крышка ведомого вала сквозная
Крышка ведомого вала глухая
Крышка ведущего вала глухая
Маслоотбойник ведомого вала
Маслоотбойник ведущего вала
Втулка ведущего вала
Втулка ведомого вала
Болт М8 х 20 ГОСТ 7798-70
Болт М10*42 ГОСТ 7798-70
Болт М14*105 ГОСТ 7798-70
Гайка М10 ГОСТ 15521-70
Гайка М14 ГОСТ 15521-70
Манжета 1-25*36-3 ГОСТ 8752-79
Манжета 1-36*45-3 ГОСТ 8752-79
ПОК 208 ГОСТ 27365-87
ПОК 306 ГОСТ 27365-87
Шпонка 6*6*18 ГОСТ 23360-79
Шпонка 10*8*32 ГОСТ 23360-79
Шпонка 10*8*40 ГОСТ 23360-79
Шпонка 14*9*36 ГОСТ 23360-79
Штифт 8*30 ГОСТ 3129-70
Уплотнение крышке ведомого вала
Уплотнение крышке ведущего вала
А1 Общий вид.cdw
Цепная передача условно не показана.
Техническая характеристика
Общее передаточное число привода 6
Мощность электродвигателя 4 кВт.
Частота вращения вала электродвигателя 950 обмин.
Платик электродвигателя
Болт М12 х 60 ГОСТ 7798-70
Болт М12-6gx200.58 (S18) ГОСТ 7798-70
Гайка М12 ГОСТ 5915-70
Гайка М12-6H.04(S18) ГОСТ 5915-70
МУВП 125-22-1.1-25-II2-УЗ ГОСТ 21424-93
Шайба 12 Н ГОСТ 6402-70
Шайба 12 ГОСТ 6402-70
Двигатель асинхронный АМ112МВ6УЗ
записка.doc
Федеральное государственное бюджетное образовательное учреждение
высшего профессионального образования
“Сибирский государственный аэрокосмический университет”
имени академика М. Ф. Решетнёва
по дисциплине: “Детали машин и основы конструирования”
студент гр. БТУ-15-01
Инженер-конструктор является творцом новой техники и уровнем его творческой работы в большей степени определяются темпы научно-технического прогресса. Деятельность конструктора принадлежит к числу наиболее сложных проявлений человеческого разума. Решающая роль успеха при создании новой техники определяется тем что заложено на чертеже конструктора. Широко используются сведения из курсов сопротивления материалов теоретической механики машиностроительного черчения и т. д. Все это способствует развитию самостоятельности и творческого подхода к поставленным проблемам.
При выборе типа редуктора для привода рабочего органа (устройства) необходимо учитывать множество факторов важнейшими из которых являются: значение и характер изменения нагрузки требуемая долговечность надежность КПД масса и габаритные размеры требования к уровню шума стоимость изделия эксплуатационные расходы.
Из всех видов передач зубчатые передачи имеют наименьшие габариты массу стоимость и потери на трение. Коэффициент потерь одной зубчатой пары при тщательном выполнении и надлежащей смазке не превышает обычно 001..
К недостаткам зубчатых передач могут быть отнесены требования высокой точности изготовления и шум при работе со значительными скоростями.
Одной из целей выполненного проекта является развитие инженерного мышления в том числе умение использовать предшествующий опыт моделировать используя аналоги.
Существуют различные типы механических передач: цилиндрические и конические с прямыми зубьями и косозубые гипоидные червячные глобоидные одно- и многопоточные и т. д.
При выборе типов передач вида зацепления механических характеристик материалов необходимо учитывать что затраты на материалы составляют значительную часть стоимости изделия: в редукторах общего назначения - 85% в дорожных машинах - 75% в автомобилях - 10% и т. д.
Поиск путей снижения массы проектируемых объектов является важнейшей предпосылкой дальнейшего прогресса необходимым условием сбережения природных ресурсов. Большая часть вырабатываемой в настоящее время энергии приходится на механические передачи поэтому их КПД в известной степени определяет эксплуатационные расходы.
Наиболее полно требования снижения массы и габаритных размеров удовлетворяет привод с использованием электродвигателя и редуктора с внешним зацеплением.
Мощность на ведомом валу привода РВЫХ = 3 кВт;
Частота вращения ведомого вала привода nВЫХ = 145 обмин;
Коэффициент годового использования Кгод = 07;
Коэффициент суточного использования Ксут = 09;
Срок службы Т = 6 лет.
Определение срока службы привода4
Кинематический расчет привода4
Проектирование и расчет передач редуктора7
1 Выбор материалов зубчатых колес и допускаемых напряжений7
2 Определение предварительных размеров зубчатых колес7
3 Определение усилий в зацеплении11
4 Предварительный расчет валов12
5 Выбор подшипников12
Проверочные расчеты передач редуктора13
Уточненный расчет валов15
1 Определение долговечности подшипников15
2 Проверка запаса прочности и выносливости21
Проектирование и расчет цепной29
1 Выбор основных геометрических параметров29
2 Усилия и направление в цепи31
Конструирование корпуса редуктора33
Расчет шпоночных соединений36
Выбор способа смазки и сорта масла37
Порядок сборки редуктора37
Библиографический список38
Определение срока службы привода
Принимаем сменность привода Lc = 2; длительность смены tc = 8. Ресурс привода определяем по формуле [2 стр. 36]:
Lh = 365 · Т · Кг · Кс · tc · Lc = 365 · 6 · 07 · 09 · 8 · 2 = 22075 ч(1)
Принимаем время простоя машинного агрегата 15% ресурса тогда срок общий ресурс привода Lh = 18764 ч.
Кинематический расчет привода
Определяем требуемую мощность рабочей машины [2 стр. 39]:
гдеобщ – коэффициент полезного действия привода равный произведению частных КПД [2 стр. 39]:
Частные КПД выбираем по таблице 2.2 [2 стр. 40]:
6 - КПД закрытой зубчатой цилиндрической передачи;
- КПД открытой передачи;
9 - КПД пары подшипников качения;
Полученные частные КПД подставим в формулу и получим общее КПД привода:
Принимаем по ГОСТ 19532-81 [2 стр. 384-386] или [1 стр. 390] электродвигатель серии 4АМ112МВ6УЗ мощностью Рдв = 4 кВт частотой вращения nДВ = 950 обмин.
Определяем передаточное число привода [2 стр. 41]:
Принимаем по СТ СЭВ 221-75 [2 стр. 43] передаточное число редуктора uр = 315 тогда передаточное число открытой передачи:
Полученное значение согласуется с рекомендованным [2 стр. 43].
Определяем силовые и кинематические параметры привода по формулам [2 стр. 45-46]:
n1 = nДВ = 950 обмин(7)
n2 = = = 302 обмин(8)
nРМ = = = 144 обмин(9)
T1 = Тдв · м · 40 · 099 · 099 = 39 Нм(14)
=39 · 315 · 096 · 099 = 117 Нм(15)
TРМ = T2 · uОП · ОП · ПО² · м (16)
TРМ = 117 · 21 · 09 · 099² · 099 = 215 Нм
Таблица 1 - Результаты кинематического расчета привода.
Передаточное число u
Угловая скорость радс
Частота вращения n обмин
Вращающий момент Т Нм
Проектирование и расчет передач редуктора
1 Выбор материалов зубчатых колес и допускаемых напряжений
Принимаем сталь 45 [2 стр. 53] со следующими характеристиками:
Таблица 2 – Характеристика механических свойств стали
Принимаем коэффициент долговечности для зубьев шестерни и колеса KHL= 1 [2 стр. 55].
По табл. 3.1 [2 стр. 52] и формуле [2 стр. 55] определяем допускаемые контактные напряжения:
[]H1 = KHL · 18 · 200 + 67 = 427 МПа(17)
[]H2 = KHL · 18 · 180 + 67 = 391 МПа(18)
Расчет для передач с прямыми и непрямыми зубьями при разности прочности НВ1–НВ2=20 50 ведется по наименьшему значению т.е. по []H2=391 МПа
Принимаем коэффициент долговечности для зубьев шестерни и колеса KFL = 1 [2 стр. 56].
По табл. 3.1 [2 стр. 52] и формуле [2 стр. 56] определяем допускаемые напряжения на изгибную прочность:
[]F1 = KFL · 103 · НВ1 = 1 · 103 · 200 = 206 МПа(19)
[]F2 = KFL · 103 · НВ2 = 1 · 103 · 180 = 185 МПа(20)
2 Определение предварительных размеров зубчатых колес
Определяем главный параметр - межосевое расстояние [2 стр. 61]:
гдеКа – вспомогательный коэффициент; Ка = 495 - для прямозубых передач [2 стр. 61];
KH – коэффициент неравномерности нагрузки по длине зуба. Принимаем для приработавшихся колес KH = 11 [2 стр. 61];
a – коэффициент ширины зубчатого венца принимаемый в пределах 028 036 для симметрично расположенных закрытых цилиндрических передач. Принимаем a = 028 [2 стр. 61].
Принимаем по табл. 4.1 aw = 140 мм [2 стр. 60].
Определяем модуль зацепления:
гдеKm – вспомогательный коэффициент равный 68 [2 стр. 62];
d2 – делительный диаметр колеса [2 стр. 61]:
d2 = = = 2125 мм(23)
b2 – ширина колеса [2 стр. 62]:
b2 = а · aw = 028 · 140 = 39 мм (24)
Принимаем по стандартному ряду m = 2 мм.
Определяем угол наклона зубьев [2 стр. 60]:
min = arcsin = arcsin = arcsin 01795 (25)
Принимаем угол наклона зубьев = 0° тогда cos = 1.
Определяем суммарное количество зубьев [2 стр. 60]:
Уточняем действительную величину наклона зубьев [2 стр. 60]:
= arccos = arccos = arccos 1000(27)
Окончательно принимаем угол наклона зубьев = 0° cos = 1.
Число зубьев шестерни определяем по формуле [2 стр. 60]:
Число зубьев колеса [2 стр. 60]:
Вычисляем фактическое передаточное отношение [2 стр. 60]:
Определяем отклонение от принятого [2 стр. 60]:
Проверяем фактическое межосевое расстояние:
Определяем основные геометрические параметры передачи [2 стр. 60-61]:
Диаметр вершин зубьев
Диаметр впадин зубьев
Ошибка! Закладка не определена. мм(36)
Рисунок 1 - Геометрические параметры типовой цилиндрической передачи.
3 Определение усилий в зацеплении
Определяем силы в полосе зацепления зубчатых колес [2 стр. 97]:
Ошибка! Закладка не определена.(40)
Рисунок 2 - Схема сил в зацеплении.
4 Предварительный расчет валов
Выбираем в качестве материала валов сталь 45. Принимаем допускаемое напряжение кручения []К в интервале 10 30 МПа.
Диаметр первой ступени вала определяем по формуле [2 стр. 108]:
Принимаем d1 = 22 мм
Принимаем d2 = 32 мм
Остальные диаметры и линейные размеры валов выбираем с учетом стандарта СТ СЭВ 514-77 исходя из эскизной компоновки редуктора.
Подшипники выбираем по таблицам К27 – К30 [2 стр. 410-417].
Ведущий вал - шарикоподшипник серии 306: d = 30 мм .
Ведомый вал - шарикоподшипник 208: d = 40 мм .
Проверочные расчеты передач редуктора
Проверяем межосевое расстояние [2 стр. 61]:
Определяем окружную скорость колеса [2 стр. 61]:
Принимаем по табл. 4.2 8 степень точности [2 стр. 62].
Проверяем условие по контактной прочности :
гдеК – вспомогательный коэффициент. Принимаем К = 436 для прямозубой передачи.
KHα – коэффициент учитывающий распределение нагрузки по зубьям. Принимаем для прямозубой передачи KHα = 1;
KHV – коэффициент динамической нагрузки зависящий от окружной скорости передачи V мс и степени точности передачи. Принимаем по табл. 4.3 [2 стр. 62] KHV = 12.
Вычисляем отклонение [2 стр. 62]:
Условие прочности выполняется т.к. отклонение нагрузки находится в допустимых пределах (-10 +5)%.
Проверяем выполнение изгибной прочности зубьев шестерни и колеса [2 стр. 63]:
гдеKFα – коэффициент учитывающий распределение нагрузки между зубьями. Принимаем методом интерполирования KFα = 091 [2 стр. 63];
KF – коэффициент неравномерности нагрузки по длине зуба. Принимаем KH = 1 для приработавшихся колес.
KFV – коэффициент динамической нагрузки. По таблице 4.3 [2 стр. 62] принимаем KFV = 167.
YF1 YF2 – коэффициенты формы зуба шестерни и колеса. По табл. 4.4 [2 стр. 64] принимаем для z1 = 34 - YF1 = 379; для z2 = 106 - YF2 = 36.
Y – коэффициент учитывающий наклон зуба [2 стр. 64]:
Y = 1 - = 1 - = 100(49)
Условия прочности выполняются.
Уточненный расчет валов
1 Определение долговечности подшипников
Определяем опорные реакции на ведущем валу. Принимаем из эскизной компоновки: lб = 120 мм lбк = 79 мм. Консольная сила на быстроходном валу от муфты Fбк = 312 Нм.
Вертикальная плоскость:
Ya = Yb = 05 · Fr = 05 · 401 = 201 Н
Горизонтальная плоскость
ΣMA = 0; Xb · lб – Ft · 05 · lб + Fбк · lбк = 0
ΣMВ = 0; -Xa · lб + Ft · 05 · lб + Fбк · (lб + lбк) = 0
ΣF Xb - Ft + Xa - Fбк = 0
5 - 1101 + 1068 - 312 = 0
Определяем суммарные радиальные реакции в опорах:
Определяем значения моментов
My2 = Xb · 05 · lб = 345 · 05 · 120 = 21 Нм
My3 = Xb · lб - Ft · 05 · lб = 345 · 120 - 1101 · 05 · 120 = -25 Нм
Горизонтальная плоскость
Mx2 = Yb · 05 · lб = 201 · 05 · 120 = 12 Нм
Крутящий момент Т = 39 Нм
Определяем реакции в опорах ведомого вала. Принимаем из эскизной компоновки lт = 120 мм lтк = 72 мм. Консольная сила от цепной передачи Fтк= 129 Нм.
Вертикальная плоскость
Yс = Yd = 05 · Fr = 05 · 401 = 201 Н
ΣMС = 0; Xd · lт - Ft · 05 · lт + Fтк · lтк = 0
ΣMD = 0; -Xc · lт + Ft · 05 · lт + Fтк · (lтк + lт) = 0
ΣF Xd - Ft + Xc - Fтк = 0
3 - 1101 + 757 - 129 = 0
My2 = Xd · 05 · lт = 473 · 05 · 120 = 28 Нм
My3 = Xd · lт - Ft · 05 · lт = 473 · 120 - 1101 · 05 · 120 = -9 Нм
Mx2 = Yd · 05 · lт = 201 · 05 · 120 = 12 Нм
Крутящий момент Т = 117 Нм
Рисунок 3 - Расчетная схема ведущего вала.
Рисунок 4 - Расчетная схема ведомого вала.
Подшипник пригоден при условии [2 стр. 128]:
Определяем расчетную динамическую грузоподъемность [2 стр. 128]:
гдеRe – эквивалентная динамическая нагрузка Н;
m – показатель степени. = 3 - для шариковых подшипников;
Эквивалентную динамическую нагрузку определяем согласно формулам приведенным в таблице 9.1 [2 стр. 129]:
Re = X · V · Rr · Кб · Кt (52)
гдеV – коэффициент вращения принимаем V = 1 т.к. вращается внутреннее кольцо подшипника;
Rr – радиальное усилие в наиболее нагруженной опоре;
Кб – коэффициент безопасности. По табл. 9.4 [2 стр. 133] в зависимости от характера нагрузки и вида машинного агрегата принимаем Кб = 11;
Кt – температурный коэффициент. При t ≤ 100º C принимаем по табл. 9.5 Кt =1 [2 стр. 135].
Re = 1 · 1087 · 11 · 1 = 1196 Н
Подшипник 306 пригоден.
Re = 1 · 783 · 11 · 1 = 861 Н
Подшипник 208 пригоден.
2 Проверка запаса прочности и выносливости
Ведущий вал. Опасные сечения: под зубчатым колесом (2-2) и под подшипниковой опорой (3-3) смежной с консольной нагрузкой.
Определяем суммарный изгибающий момент в опасном сечении:
Определяем осевой момент в сечении [2 стр. 256]:
Wнетто = = = 123019 мм³(54)
Определяем напряжение в опасном сечении [2 стр. 255]:
А = И = = = 1951 МПа(55)
Определяем полярный момент в сечении [2 стр. 256]:
Wρнетто = 02 · df³ = 02 · 63³ = 50009 мм³ (56)
Касательные напряжения [2 стр. 255]:
А = = = = 6180 МПа(57)
Определяем коэффициенты концентрации нормальных и касательных напряжений [2 стр. 256257]:
гдеК и К – эффективные коэффициенты концентрации напряжений [2 стр. 257];
Кd – коэффициент влияния абсолютных размеров поперечного сечения [2 стр. 258];
Кf – коэффициент влияния шероховатости [2 табл. 11.4];
Ку – коэффициент влияния поверхностного упрочнения [2 табл. 11.5].
Принимаем К = 16 К = 15 Kd = 077 Kf = 09 Ку = 16.
Определяем пределы выносливости в расчетном сечении [2 стр. 259]:
(-1)d = -1 Кd = 260 12 = 2600 МПа(60)
(-1)d = 058 · -1 Кd = 1508 12 = 126 МПа(61)
Определяем коэффициенты запаса прочности по нормальным и касательным напряжениям [2 стр. 259]:
Определяем общий коэффициент запаса прочности [2 стр. 259]:
Условие прочности выполняется т.к. S находится в допустимых пределах 15 3.
Wнетто = 01 · d³ = 01 · 30³ = 2700 мм³(66)
А = И = = = 926 МПа(67)
Wρнетто = 02 · d³ = 02 · 30³ = 5400 мм³(68)
А = = = = 7205 МПа(69)
Принимаем К = 16 К = 15 Kd = 090 Kf = 09 Ку = 16.
(-1)d = -1 Кd = 260 1 = 2600 МПа(72)
(-1)d = 058 · -1 Кd = 1508 1 = 151 МПа (73)
Ведомый вал. Опасные сечения: под зубчатым колесом (4-4) и под подшипниковой опорой (5-5) смежной с консольной нагрузкой.
Wнетто = 01 · d³ - (78)
Wнетто = 01 · 45³ - = 717843 мм³
А = И = = = 4179 МПа(79)
Wρнетто = 02 · d³ - (80)
Wρнетто = 02 · 45³ - = 726956 мм³
А = = = = 8047 МПа(81)
Принимаем К = 16 К = 15 Kd = 083 Kf = 09 Ку = 16.
(-1)d = -1 Кd = 260 11 = 2364 МПа(84)
(-1)d = 058 · -1 Кd = 1508 11 = 137 МПа(85)
Условие прочности выполняется т.к. коэффициент запаса прочности S больше минимально допустимого значения [S] = 15.
Wнетто = 01 · d³ = 01 · 40³ = 6400 мм³(90)
А = И = = = 1406 МПа(91)
Wρнетто = 02 · d³ = 02 · 40³ = 12800 мм³(92)
А = = = = 5754 МПа(93)
Принимаем К = 16 К = 15 Kd = 085 Kf = 09 Ку = 16.
(-1)d = -1 Кd = 260 11 = 2364 МПа(96)
(-1)d = 058 · -1 Кd = 1508 1 = 151 МПа(97)
Проектирование и расчет цепной передачи
1 Выбор основных геометрических параметров
Принимаем приводную роликовую цепь типа ПР. Определяем число зубьев меньшей звездочки цепной передачи [1 стр. 152]:
Определяем число зубьев ведомой звездочки [1 стр. 152]:
Условие соблюдается.
Определяем фактическое передаточное отношение цепной передачи:
Определяем отклонение фактического передаточного отношения от принятого:
Определяем коэффициент эксплуатации передачи [1 стр. 149]:
гдеКд = 1 - коэффициент учитывающий динамичность нагрузки [1 стр. 149];
Ка – коэффициент межосевого расстояния. Ка = 1 - для оптимального межосевого расстояния [1 стр. 150];
Кс – коэффициент способа смазывания. Принимаем Кс = 15 - при периодическом способе смазывания [1 стр. 150];
К – коэффициент наклона линии центров звездочек е горизонту. При угле наклона 60º принимаем К = 1 [1 стр. 150];
Креж – коэффициент режима работы. Принимаем Креж = 1 - при работе передачи в одну смену [1 стр. 150];
Кр – коэффициент способа регулирования натяжения цепи. Кр = 1 - при регулировании натяжения отжимными винтами [1 стр. 150].
Т.к. 3 то условия эксплуатации цепной передачи можно оставить без изменений.
Определяем шаг роликовой цепи по формуле 7.38 [1 стр. 149]:
гдеm – число рядов в цепи. Принимаем m = 1;
[pц] – допускаемое давление в шарнирах цепи. По таблице 7.18 [1 стр. 150] принимаем [pц] = 30.
По табл. 7.20 [1 стр. 156] принимаем цепь с шагом 1905 мм разрушающая нагрузка Q = 318 кН вес 1 метра цепи q = 19 кгм.
Определение геометрических параметров цепной передачи
Делительный диаметр ведущей звездочки
D1 = = = = 16408 мм(106)
Делительный диаметр ведомой звездочки
D2 = = = = 34586 мм(107)
Определяем ориентировочное межосевое расстояние по формуле [1 стр. 148]:
= 30 · 1905 = 572 мм(108)
Вычисляем длину замкнутой цепи выраженную в шагах t:
Принимаем четное значение lt = 100 мм.
Уточняем межосевое расстояние по формуле 7.37 [1 стр. 149]:
Подставив данные в формулу получаем а = 58918 мм.
Принимаем монтажное межосевое расстояние:
= 0998 · 58918 = 588 мм(111)
Окончательно принимаем цепь ПР-1905-166 ГОСТ 13568-75.
2 Усилия и направление в цепи
Скорость цепи [1 стр. 153]:
Определяем окружную силу на валу ведомой звездочки [1 стр. 153]:
Определяем центробежную силу [1 стр. 153]:
Fv = q · v² = 19 · 26² = 128 Н(114)
Определяем силу от провисания цепи [1 стр. 153]:
Ff = 981 · kf · q · a = 981 · 6 · 19 · 572 = 64 Н(115)
где kf – коэффициент учитывающий расположение цепи. При горизонтальном положении принимаем kf = 6 [1 стр. 151].
Расчетная нагрузка на валы [1 стр. 154]:
Fв = Ft + 2 · Ff = 1 +2 · 64 = 129 Н(116)
Проверяем коэффициент запаса прочности по формуле [1 стр. 154]:
По таблице 7.19 при n1 = 634 обмин и шаге t = 1905 мм нормативный коэффициент запас прочности [s] = 76. Т.к. s > [s] условие прочности выполняется.
Конструирование корпуса редуктора
Расчет ведем по формулам из табл. 10.2 [1 стр. 241].
Определяем толщину стенок корпуса и крышки редуктора:
= 0025 · aw + 1 ≥ 8 мм(118)
Принимаем толщину стенки
Определяем расстояние от внутренней стенки редуктора:
до боковой поверхности вращающейся части
= (10 12) · 8 = 8 10 мм (119)
до боковой поверхности подшипника качения
Определяем радиальный зазор от поверхности вершин зубьев до внутренней поверхности стенки редуктора:
= 12 · 8 = 10 мм (121)
Определяем расстояние от боковых поверхностей элементов вращающихся вместе с валом до неподвижных наружных частей редуктора:
Определяем ширину фланцев S соединяемых болтом диаметром :
Gри принимаем k = 28 мм.
Принимаем толщину фланца боковой крышки .
Принимаем высоту головки болта:
= 08 · 12 = 10 мм(125)
Принимаем толщину фланца втулки
Определяем расчетный момент [2 стр. 237]:
гдеКр – коэффициент режима нагрузки. Выбираем по табл. 10.26 Кр = 125 [2 стр. 237].
Тр = 125 · 39 = 49 Нм
Для вычисленного расчетного момента и диаметра вала 22 мм выбираем по табл. К21 [2 стр. 400] МУВП 125-22-1.1-25-II2-УЗ ГОСТ 21424-93.
Определяем консольную силу действующую на вал [2 стр. 98]:
Fм = 50 · = 312 Нм(127)
Рисунок 5 – Муфта упругая втулочно-пальцевая.
Расчет шпоночных соединений
Производим расчет шпонок на смятие по формуле 8.22 [1 стр. 170]:
Где h - высота сечения шпонки мм;
t1 - глубина паза вала мм;
b - ширина шпонки мм.
[см] - допускаемое напряжение на смятие [см] = 100 МПа - при стальной ступице.
Результаты расчета приведены в таблице 3.
Таблица 3 - Проверочный расчет шпоночных соединений.
Передаваемый момент Нм
Высота сечения шпонки мм
Напряжение на смятие МПа
Условие прочности для всех шпоночных соединений выполняется.
Выбор способа смазки и сорта масла
При окружной скорости колеса v = 34 мс и контактном напряжении Н=371МПа по табл. 10.2 [2 стр. 241] принимаем И-Г-А-46 – масло индустриальное для гидравлических систем без присадок.
Объем масла определяем по зависимости [2 стр. 241]:
V = (04 08) · Рдв = 16 32 л(129)
Принимаем объем масла V = 2 л.
Выбираем для подшипников качения консталин жировой УТ-1 ГОСТ 1957-73. Смазочный материал набивают в подшипники вручную при снятой крышке подшипникового узла. Смену смазки производят при ремонте.
Порядок сборки редуктора
Перед сборкой внутреннюю полость корпуса редуктора тщательно очищают и покрывают маслостойкой краской. Сборку производят в соответствии с чертежом общего вида редуктора начиная с узлов валов.
Кольца втулки колеса и подшипники нагревают в масле до температуры 100° С. В шпоночные пазы валов запрессовывают шпонки; устанавливают зубчатые колеса маслоотбойные кольца и подшипники на соответствующие участки валов.
Собранные узлы устанавливают в корпус. Фланцевые стыки покрывают герметиком. Одевают крышку корпуса центрируя ее штифтами. Затягивают болты. В подшипниковые камеры закладывают смазку ставят крышки подшипников с комплектом металлических прокладок регулируют тепловой зазор. Перед постановкой сквозных крышек в проточки закладывают манжеты.
Проверяют проворачиванием валов отсутствие заклинивания подшипников. Ввертывают сливную пробку с прокладкой. Заливают в корпус масло и закрывают смотровое отверстие крышкой с отдушиной закрепляют крышку болтами. Собранный редуктор обкатывают и подвергают испытанию на стенде по программе устанавливаемой техническими условиями.
Библиографический список
Курсовое проектирование деталей машин: учебное пособие для учащихся машиностроительных техникумов С.А. Чернавский К.Н. Боков И.М Чернин и др. – 2-е изд. переработанное и дополненное. – М.: Машиностроение 1988. – 416 с.: ил.
Шейнблит А.Е. Курсовое проектирование деталей машин: учебное пособие для техникумов. – М.: ВШ 1991. – 432 с.: ил.
Рекомендуемые чертежи
- 04.02.2024