Проектирование привода к ленточному конвейеру




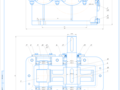
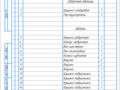
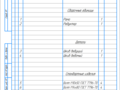
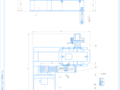
- Добавлен: 04.11.2022
- Размер: 1010 KB
- Закачек: 1
Описание
Курсовой проект - Проектирование привода к ленточному конвейеру
Состав проекта
![]() |
![]() ![]() ![]() ![]() |
![]() ![]() ![]() ![]() |
![]() ![]() ![]() ![]() |
![]() ![]() ![]() ![]() |
![]() ![]() ![]() ![]() |
![]() ![]() ![]() ![]() |
![]() ![]() ![]() |
![]() ![]() ![]() ![]() |
Дополнительная информация
Редуктор.cdw

Компоновка.cdw

Колесо зубчатое.cdw

Привод_спецификация.spw

Вал ведомый.cdw

Редуктор_спецификация.spw

Привод.cdw

Рекомендуемые чертежи
- 24.01.2023