Анализ и изготовление внутренних и наружных протяжек квадратного сечения




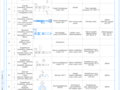
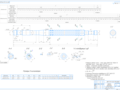
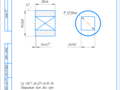
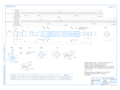
- Добавлен: 04.11.2022
- Размер: 7 MB
- Закачек: 1
Узнать, как скачать этот материал
Подписаться на ежедневные обновления каталога:
Описание
Курсовой проект - Анализ и изготовление внутренних и наружных протяжек квадратного сечения
Состав проекта
![]() |
![]() ![]() ![]() ![]() |
![]() ![]() ![]() ![]() |
![]() ![]() ![]() ![]() |
![]() ![]() ![]() |
![]() ![]() ![]() |
![]() ![]() ![]() |
Дополнительная информация
Контент чертежей
Маршруткаcdw2.cdw

2_14.cdw

1_14.cdw

Рекомендуемые чертежи
- 24.01.2023
- 20.08.2014
- 20.08.2014
- 20.08.2014
- 20.08.2014
- 20.08.2014
Свободное скачивание на сегодня
Обновление через: 9 часов 3 минуты