Дипломная работа - Автоматизация процесса контроля геометрии гребных винтов при их изготовлении и ремонте




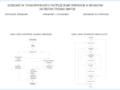
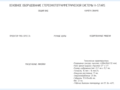
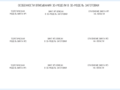
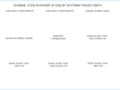
- Добавлен: 04.11.2022
- Размер: 32 MB
- Закачек: 2
Описание
Состав проекта
![]() |
![]() |
![]() |
![]() |
![]() ![]() ![]() |
![]() |
![]() |
![]() |
![]() |
![]() ![]() ![]() |
![]() |
![]() |
![]() |
![]() |
![]() ![]() |
![]() |
![]() |
![]() ![]() ![]() |
![]() |
![]() |
![]() |
![]() ![]() ![]() |
![]() ![]() ![]() |
![]() |
![]() |
![]() |
![]() |
![]() |
![]() |
![]() |
![]() |
![]() |
![]() |
![]() |
![]() |
![]() |
![]() ![]() ![]() |
![]() |
![]() |
![]() ![]() ![]() |
![]() |
![]() |
![]() |
![]() |
![]() ![]() ![]() |
![]() |
![]() |
![]() |
![]() |
![]() ![]() ![]() |
![]() |
![]() |
![]() |
![]() |
![]() |
![]() ![]() ![]() |
![]() |
![]() |
![]() |
![]() |
![]() |
![]() |
![]() |
![]() |
![]() |
![]() |
![]() |
![]() ![]() ![]() |
![]() |
![]() |
![]() |
![]() |
![]() |
![]() |
![]() |
![]() |
![]() |
![]() |
![]() |
![]() ![]() |
![]() |
![]() ![]() ![]() |
![]() |
![]() |
![]() |
![]() |
![]() |
![]() |
![]() |
![]() ![]() ![]() |
![]() |
![]() ![]() ![]() ![]() |
![]() |
![]() |
![]() |
![]() |
![]() |
![]() |
![]() |
![]() |
![]() |
![]() ![]() ![]() |
![]() |
![]() |
![]() |
![]() |
![]() |
![]() |
![]() ![]() ![]() |
![]() |
![]() |
![]() ![]() ![]() |
![]() |
![]() |
![]() |
![]() ![]() ![]() |
Дополнительная информация
Пл.№4 Основное оборудование ИИС V-STARS .docx
пл.№3.cdw
B - измерительная база;
f - фокусное расстояние видеокамер;
z - координаты на плоскости снимков
направляющие косинусы
ПРИНЦИП СТЕРЕОФОТОГРАММЕТРИИ
пл.№5.cdw
ОСНОВНЫЕ ЭТАПЫ ПОЛУЧЕНИЯ 3D-МОДЕЛИ ЗАГОТОВКИ ГРЕБНОГО ВИНТА
СОЗДАНИЕ ДРАЙВЕР-ФАЙЛА
ПОДГОТОВКА К ИЗМЕРЕНИЯМ №1
ОБРАБОТКА ДРАЙВЕР-ФАЙЛОВ
ПОДГОТОВКА К ИЗМЕРЕНИЯМ №2
shtamp4.cdw
AZIPOD -7104MP-427-504
Таблица теоретических катетов винта.
shtamp2.cdw
стереофотограмметрической системы
пл.№2.cdw
КОНТРОЛЬНО-ИЗМЕРИТЕЛЬНАЯ МАШИНА
ИЗМЕРИТЕЛЬНЫЕ РЕЙСМУСЫ
Пл.№2 Технологическое оборудованиедля контактных измерений.docx
пл.№6.cdw
ЗАГОВОТКИ ГРЕБНЫХ ВИНТОВ
НОРМАЛЬНОЕ ВПИСЫВАНИЕ
ВПИСЫВАНИЕ С ОТКЛОНЕНИЕМ
ВПИСЫВАНИЕ БЕЗ ПРИПУСКОВ
БЛОК-СХЕМА АЛГОРИТМА АНАЛИЗА ПРИПУСКОВ
БЛОК-СХЕМА АЛГОРИТМА РАБОТЫ АСУТП
Пл.№6 Особенности вписывания теорет. 3Д-модели .docx
shtamp1.cdw
принцип стереофотограмметрии
shtamp5.cdw
технологических операциях
пл.№4.cdw

пикселей: 4288х2848 (12 млн);
Поле зрения (ширина х высота): 67° х 47°;
Размер изображения (мм): 23
Точность: 16 мкм + 16 мкмм;
Фокусное расстояние: 17 мм;
Энергопотребление: 25 Вт;
Габариты: 157х154х86 мм;
Рабочий диапазон температур: от 0°С до +40°С.
ОСНОВНОЕ ОБОРУДОВАНИЕ СТЕРЕОФОТОГРАММЕТРИЧЕСКОЙ СИСТЕМЫ V-STARS
пл.№1.cdw
РAДИУС ВИНTA RB=2900.0
РАССТОЯНИЕ ОТ ТОРЦА ДО ОСИ ВИНТА 610.0
ТРЕХМЕРНЫЕ МОДЕЛИ ВИНТА И ЛОПАСТИ AZIPOD-7104MP-427-504
СОЗДАНИЕ МОДЕЛИ ВИНТА
пл.№7.cdw
ОТКЛОНЕНИЕ ВИНТА №1
ОТКЛОНЕНИЕ ВИНТА №2
ОТКЛОНЕНИЕ ВИНТА №3
ОСОБЕННОСТИ ВПИСЫВАНИЯ 3D-МОДЕЛИ В 3D-МОДЕЛЬ ЗАГОТОВКИ
Пл.№5 Основные этапы ТП получения3Д-модели заготовки .docx
Автоматизация процесса контроля геометрии гребных винтов при их изготовлении и ремонте на ОАО «ЦС» Звездочка»..docx
АНАЛИЗ ТЕХНОЛОГИЧЕСКОГО ПРОЦЕССА КОНТРОЛЯ ГЕОМЕТРИИ ГРЕБНЫХ ВИНТОВ ПРИ ИХ ИЗГОТОВЛЕНИИ9
1Анализ типового технологического процесса изготовления гребных винтов9
2Контрольно-измерительная аппаратура используемая в технологическом процессе12
3Основные разметочные операции и их особенности22
3.1Технология входного контроля заготовки лопасти гребного винта22
3.2Позиционирование заготовки станка FCW 150 (W 200H)23
3.3Разметочная операция выполнения расточной операции 090 на станке FCW 150 (W 200H) и после сборки фальшступицы23
4Современные требования к контрольно-измерительным системам24
АВТОМАТИЗАЦИЯ ПРОЦЕССА КОНТРОЛЯ ГЕОМЕТРИИ ГРЕБНЫХ ВИНТОВ ПРИ ИХ ИЗГОТОВЛЕНИИ26
1Бесконтактные методы контроля геометрии сложнопрофильных конструкций26
1.1Фотограмметрические методы27
1.2Лазерные системы31
2Фотограмметрическая система V-STARS31
3Лазерные сканеры трекеты и радары38
4Особенности автоматизации контрольно-измерительной и разметочной операций при изготовлении гребных винтов40
5Методика получения цифровой 3D-модели заготовки элементов гребного винта42
5.1Методика получения цифровой 3D-модели заготовки элементов гребного винта с помощью лазерных сканеров42
5.2Методика получения цифровой 3D-модели заготовки элементов гребного винта с помощью V-STARS44
6Особенности вписывания теоретической (исходящей) 3D-модели в 3D-модель заготовки47
7Особенности привязки виртуальных координат разметки к физическим (реальным) координатам заготовки48
8Особенности установки и ориентации на станке заготовки гребного винта на различных этапах изготовления50
9Формирование технического паспорта на гребной винт и сравнение 3D-модели «Как спроектировано» с 3D-моделью «Как построено53
ЭКСПЕРИМЕНТАЛЬНЫЕ ИССЛЕДОВАНИЯ КОНТРОЛЯ ГЕОМЕТРИИ ГРЕБНЫХ ВИНТОВ С ИСПОЛЬЗОВАНИЕМ СТЕРЕОФТОГРАММЕТРИЧЕСКОЙ СИСТЕМЫ V-STARS55
1Особенности подготовки заготовок гребного винта к контролю геометрии с использованием V-STARS55
2Варианты создания драйвер-файла перед измерением геометрии элементов гребного винта57
3Методика получения исходной цифровой 3D-модели заготовки гребного винта61
3.1Особенности получения цифровой 3D-модели 3-х лопастного гребного винта с 08 м61
3.2Особенности получения цифровой 3D-модели 4х-лопастного малого гребного винта с 12 м64
3.3Особенности получения цифровой 3D-модели 4-х лопастного гребного винта lk-7 с 35 м64
3.4Особенности получения цифровой 3D-модели одной лопасти для крупногабаритных гребных винтов65
4Особенности вписывания теоретической 3D-модели и определение припусков67
4.1Теоретические предпосылки вписывания67
4.2Управление технологическим процессом распределения припусков72
4.3Экспериментальные исследования использования стереофотограмметрической системы V-STARS78
5Оценка точности определения трехмерных координат поверхности стерефотограмметрической системой V-STARS86
5.1Экспериментальная оценка точности с использованием специального контрольного калибра (Check Master Mitytoyo Япония) 83011587
РАСЧЕТ ЗАТРАТ НА ВНЕДРЕНИЕ СТЕРЕОФОГРАММЕТРИЧЕСКОЙ СИСТЕМЫ V-STARS В ТЕХНОЛОГИЧЕСКОМ ПРОИЗВОДСТВЕ93
1Затрат на внедрение бесконтактного контроля геометрии гребных винтов93
2Расчет стоимости оборудования93
3Расчет заработной платы сотрудников95
4Расчет дополнительной заработной платы сотрудников96
5Расчет на социальные отчисления97
6Расчет накладных расходов97
ОХРАНА ТРУДА И ЗАЩИТА ОКРУЖАЮЩЕЙ СРЕДЫ99
1Техника безопасности при работе на персональной электронно-вычислительной машине99
1.1Требования безопасности при выполнении работ100
2Поражение электрическим током101
2.1Выделяются несколько пороговых значений тока102
3.1Комплекс упражнений для глаз и мышц тела103
4Техника пожарной безопасности104
5Защита окружающей среды105
СПИСОК ИСПОЛЬЗУЕМОЙ ЛИТЕРАТУРЫ108
ПЕРЕЧЕНЬ ПРИНЯТЫХ СОКРАЩЕНИЙ
В данной пояснительной записке применяются следующие определения обозначения и сокращения:
Фотограмметрия (ФГМ) – научная дисциплина и область техники предметом которой является получение геометрической информации об объектах фотограмметрической съемки [7] по их фотограмметрическим снимкам (используется одна камера).
Фотограмметрическая съемка – технологический процесс получения фотограмметрического снимка.
Фотограмметрический снимок – изображение объекта фотограмметрической съемки зафиксированное на материальном носителе в аналоговом или цифровом виде используемое для целей фотограмметрической обработки.
Объект фотограмметрической съемки – местность или предмет отображенные на фотограмметрическом снимке.
Стереофотограмметрия (СФГМ) – раздел фотограмметрии относящийся к одновременной обработке двух или более фотограмметрических снимков одного объекта фотограмметрической съемки полученных при разных положениях центра оптического проектирования съемочной системы (используется не менее 2 камер).
Стереопара – два перекрывающихся фотограмметрических снимка одного объекта фотограмметрической съемки полученных при различных положениях их центров оптического проектирования.
АСУТП – автоматизированная система управления технологическим процессом
БТК – бюро технологического контроля
КИМ – контрольно-измерительная машина
КИП – контрольно-измерительная плита
КТБ – контрольно-технологическое бюро
ОТК – отдел технологического контроля
ПО – программное обеспечение
ПЭВМ – персональная электронно-вычислительная машина
УЦИ – устройство цифровой индикации
В настоящее время в судостроении наблюдается тенденция к ужесточению требований к точности изготовления сложнопрофильных объемных судовых конструкций и к более широкому использованию современных информационных технологий.
Используемые средства не отвечают современным требованиям в связи с этим возникла острая необходимость внедрения в производство бесконтактных методов контроля геометрии ГВ и автоматизировать технологический процесс контрольно-измерительных операций и тем самым обеспечить оперативную корректировку технологического процесса изготовления винта.
В рамках дипломного проектирования были поставлены следующие задачи:
)Рассмотреть реальный технологический процесс выполнения контрольно-разметочных операций при изготовлении ГВ и их элементов;
)Произвести анализ существующих бесконтактных методов контроля геометрии сложнопрофильных конструкций и обособленно выбрать оборудование информационно-измерительной системы;
)Рассмотреть возможности автоматизации измерительно-разметочных операций;
)Систематизировать и выполнить предварительную обработку результатов экспериментальных исследований использования СФГМС V-STARS в специализированном винтообрабатывающем производстве «ЦС» Звездочка».
АНАЛИЗ ТЕХНОЛОГИЧЕСКОГО ПРОЦЕССА КОНТРОЛЯ ГЕОМЕТРИИ ГРЕБНЫХ ВИНТОВ ПРИ ИХ ИЗГОТОВЛЕНИИ
1Анализ типового технологического процесса изготовления гребных винтов
Процесс изготовление лопасти ГВ достаточно трудоемкая работа которая включает в себя большинство операций связанных с контролем геометрии и разметкой элементов ГВ на различных этапах изготовления (например первоначальная разметка восстановительно-разметочные операции протокол контроль геометрии лопасти восстановление разметки на отдельных операциях и т.д.). Для того чтобы рассмотреть все операции которые используются при изготовление лопасти необходимо получить модель заготовки с которой снимается металл и требуется точное позиционирование заготовки на станке. К основным операциям где требуется контроль геометрии и восстановление разметки на различных технологических операциях [9] относится:
0 – Первичная разметка заготовки. Выполняется в следующей последовательности:
Установить лопасть на разметочную плиту носовым торцом (1491) на призмы. Установить шагомер. Нанести меловой раствор. Выставить лопасть по уклону и шагу. Произвести разметку осевой линии. Разметить подрезку кормового (левого по сечению «Н-Н») торца на наружной поверхности фланца лопасти. Дать контрольные риски (углубление) на наружной поверхности фланца у скосов и на кромке лопасти для установки лопасти в горизонтальной плоскости. Нанести радиальные сечения 04R; 05R; 06R; 07R; 08R; 09R; 095R. Нанести на сечениях точки замера шага и толщин. Произвести замеры геометрических параметров лопасти: радиус лопасти длины сечений (вход выход) высоты точек замера относительно кормового торца толщины сечений катеты сечений откидку лопасти на сечениях 04R; 06R; 07R; 09R. Разметить центр отверстия 55Н9 в пере лопасти по сечению «V-V». Разметку углубить дать контрольную окружность. Данные заносятся в паспорт разметки винта.
0 – Разметочная-расточная операция выполняется на станке FCW 150 (W 200Н) после установки детали на планшайбу. Операция выполняется в следующей последовательности:
Произвести разметку подрезки скосов с обнижением 2 ± 05мм. Контроль по хордам на 1160. Произвести разметку центров: отверстия 80Н8 (смотри вид «G») 6 отверстий 107 (смотри виды «В-В» «С-С» «D-D» «E-E») и отверстия М110х4-6Н (смотри виды «F-F» и «L-L») нанести контрольные окружности. Точность разметки центров отверстий ± 05мм. Предъявить ОТК. Установку не сбивать лопасть не раскреплять.
0 – Расточная операция после разметочно-расточной операции 060.
Сверлить и расточить отверстие 80Н8(+0054) по узлу «G» на глубину 145 мм шероховатостью Ra 25. Точить фаску 05х45° по 80. Сверлить расточить 6 сквозных отверстий 107+087 по видам «J-J» и «K-K». Сверлить расточить 1 сквозное отверстие 1058+048 под резьбу М110х4-6Н по сечению «L-L». Расточить 7 колодцев 152+1 по видам «J-J» «K-K» и «L-L» с выполнением R5 выдерживая размеры 254 мм по виду «В-В» 218 мм по виду «С-С» 156 мм по виду «D-D» 100 мм по виду «Е-Е» и 95 мм по виду «L-L». Расфрезеровать 7 внутренних кольцевых канавок 166 шириной 14 мм (смотри вид «N») выдерживая размеры 70 мм по виду «J-J» и 50 мм по виду «L-L». Расточить 7 фасок 5х45° на 107 по видам «J-J» и «K-K». Точить 2 заходные фаски 116х120° фрезеровать резьбу М110х4-6Н. Фрезеровать скосы лопасти под 72 с обнижением 2 ± 05 мм. Фрезеровать на двух скосах канавки R3 по виду «R» и сечению «М – М» выдерживая размеры 265 мм 550 мм 130 мм и 650 мм.
5 – Разметочная операция после сборки фальшступицы выполняется на контрольно-измерительной плите в следующей последовательности:
Установить шагомер. Нанести меловой раствор. Произвести разметку осевой линии. Нанести радиальные сечения 04R; 05R; 06R; 07R; 08R; 09R; 095R. Нанести на сечениях точки замера шага и толщин. Произвести замеры геометрических параметров лопасти: радиус лопасти длины сечений (вход – выход) высоты точек замера относительно кормового торца толщины сечений катеты сечений откидку лопасти на сечениях 04R; 06R (или 07R); 09R. Заполнить паспорт. Копию паспорта передать мастеру механического участка оригинал в ОТК. Снять шагомер.
0 – Разметочная операция перед фрезерно-программной обработки нагнетательной поверхности.
Установить шагомер. Нанести меловой раствор. Произвести разметку осевой линии. Нанести радиальные сечения 04R; 05R; 06R; 07R; 08R; 09R; 095R. Нанести на сечениях точки замера. Произвести замеры геометрических параметров лопасти: радиус лопасти длины сечений (вход выход) высоты точек замера относительно кормового торца толщины сечений катеты сечений откидку лопасти на сечениях 04R; 06R; 07R; 09R. Заполнить паспорт. Копию паспорта передать мастеру механического участка оригинал в КТБ. Снять шагомер.
5 – Разметочная операция после предварительной фрезерной-программной обработки засасывающей поверхности.
Произвести замеры толщин по сечениям. Заполнить паспорт. Копию паспорта передать мастеру механического участка оригинал в ОТК.
5 – Разметочная операция после окончательной фрезерной-программной обработки нагнетательной поверхности.
5 – Разметочная операция после окончательной фрезерной-программной обработки засасывающей поверхности.
Установить шагомер. Восстановить осевую линию разметить сечения разметить точки замеров шага и толщин. Проверить геометрические параметры лопасти заполнить паспорт следующим образом: радиус лопасти; показания шагомера при замерах шага и местного шага сечений; длины сечений (вход – выход); толщины сечений; уклон лопасти. Разметить (углубить) контур лопастей. Копию паспорта передать мастеру обрубного участка оригинал в ОТК. Снять шагомер.
0 – Разметочная операция выполняется после цветной капиллярной дефектоскопии и устранений дефектов выполняется в следующей последовательности:
Установить шагомер. Восстановить осевую линию разметить сечения и точки замеров шага и толщин. Проверить геометрические параметры лопасти заполнить паспорт в следующем объёме: радиус лопасти; показания шагомера при замерах шага и местного шага сечений; длины сечений (вход – выход); толщины сечений; уклон лопасти. Копию паспорта передать мастеру обрубного участка оригинал в ОТК. Снять шагомер.
5 – Окончательная разметочная-контрольная операция выполняет окончательное устранение всех дефектов и обработку наплавленных участков осуществляется в следующей последовательности:
Установить шагомер. Нанести меловой раствор. Произвести разметку осевой линии. Нанести радиальные сечения 04R; 05R; 06R; 07R; 08R; 09R; 095R. Нанести на сечениях точки замера шага и толщин. Произвести замеры геометрических параметров лопасти: радиус лопасти длины сечений (вход выход) высоты точек замера относительно кормового торца толщины сечений катеты сечений откидку лопасти на сечениях 04R; 06R; 07R; 09R. Заполнить паспорт. Оригинал паспорта передать в БТК. Снять шагомер.
2Контрольно-измерительная аппаратура используемая в технологическом процессе
В последнее время в машиностроении и кораблестроении широко используются [8] КИМ различного типа. Они применяются для измерения размеров деталей в двух или трёх направлениях. Использование КИМ позволяет оперативно измерять геометрические параметры простых и сложных прецизионных деталей включая корпусные измерение которых традиционными способами требует дорогостоящей специальной оснастки или измерение которых невозможно вообще; сокращать время на наладку обрабатывающих станков центров и модулей за счет быстрого и достоверного контроля первых обработанных деталей из последующей партии; исключать брак используя постоянный контроль точности процесса обработки деталей и своевременно корректировать его.
Современные КИМ (рисунок 1.1) представляют собой высокоточные устройства обеспечивающие пять или более степеней свободы при ориентации измерительного щупа в пространстве.
Рисунок 1.1 Программно-управляемая КИМ
КИМ состоит из трёх взаимно перпендикулярных устройств для измерения линейных и угловых перемещений и чувствительного щупа (датчика контакта). На современных измерительных машинах в момент касания щупом поверхности детали автоматически фиксируются все координаты датчика. Перемещение датчика может осуществляться вручную или автоматически по заранее заданной программе. При этом результаты измерений обрабатываться специализированным программным обеспечением определяющим отклонение формы реальной поверхности детали.
Одним из основных достоинств КИМ является то что на ней концентрируются операции контроля которые выполняются за одну установку деталей со всех сторон. Это позволяет избежать ошибок базирования неизбежных при неоднократной установке изделия. Однако большинство КИМ являются атрибутом лабораторного кондиционированного помещения изолированного от основного производства так как точность и достоверность получения результатов существенно снижается в промышленных условиях. Кроме того КИМ не могут быть включены в систему автоматического управления станком.
Из большого многообразия приборов и устройств использующих контактные методы (смотри приложение Б) наибольшее использование получили КИМ а для контроля геометрии ГВ также широко используются шагомеры и толщиномеры [8].
Шагомер УРКГВ-7500 представляющего собой измерительное устройство обеспечивающее пять степеней свободы при ориентации измерительного щупа в пространстве. Прежде всего они ориентированы на измерение параметров поверхности изделий типовых геометрических объектов таких как плоскости тела вращения призмы и др.
Рисунок 1.2 – Шагомер
Контроль геометрических параметров ГВ при помощи шагомеров требует большого объёма одинаковых замеров при их высокой точности. Эта рутинная работа отнимает много времени у обслуживающего персонала с ростом времени работы падает и внимательность то есть точность получаемых результатов измерений.
Устройство цифровой индикации линейных перемещений предназначено для определения геометрических размеров ГВ по двум координатам X и Y и индикации результатов измерения на цифровом табло. Устройство используется вместо визуального лимбового измерителя линейных перемещений по осям X и Y.
2.1.1Использование шагомеров в изготовление гребных винтов
В соответствии с технологией изготовления ГВ контроль геометрических параметров производится периодически на различных этапах его изготовления и по результатам контроля вводится соответствующая коррекция технологического процесса изготовления винта.
Основными этапами являются:
)Входной контроль заготовки и оптимальное вписывание винта в эту заготовку;
)Замеры геометрических параметров после обработки наружной поверхности каждой лопасти винта;
)Контроль параметров заготовки после ее переустановки и поворота;
)Контроль геометрической поверхности каждой лопасти на соответствующих этапах обработки внутренней поверхности лопасти. На этих этапах контролируется не только геометрическая поверхность но и толщина лопасти в соответствующих сечениях. Причем информация о толщине является основной для корректировки технологического процесса фрезерования;
)Контроль толщины лопасти ГВ в процессе их доводки и шлифовки;
)Контроль геометрии и толщины лопастей в процессе окончательной доводки и шлифовки наружной поверхности лопасти после окантовки и установки. На этом этапе процесс контроля лопасти ГВ выполняется многократно по ходу обработки.
Окончательный контроль геометрии и толщины лопастей ГВ производится на специализированном стенде где винт устанавливается неподвижно с соответствующей ориентацией. Контроль производится с помощью специального шагомера путем замеров координат 8-10 точек в соответствующих сечениях винта при этом разметка контрольных точек на поверхности винта производится с помощью того же шагомера. Предварительно эти поверхности обмеливают. Замеры проводятся двумя операторами один из которых с помощью ручного привода перемещает шагомер вокруг вертикальной оси с требуемым шагом а второй управляет работой двух электроприводов по координатам X и Y с помощью которых устанавливается измерительный щуп в отмеченную точку заданного сечения. Измерение вертикальной координаты Y производится в момент касания щупа поверхности винта. При этом в качестве щупа используется микрометр. После установки щупа в заданную точку и момента касания снимаются показания со всех лимбов и заносятся в таблицу (вторым оператором). Точность измерений в соответствии с измерительными линейками составляет ± 02 мм. После разметки и замеров координат производятся измерения толщины лопасти ГВ во всех отмеченных сечениях на тех же точках в которых измерялись и координаты поверхности. Результаты окончательного контроля оформляются в виде таблиц и соответствующих протоколов и в дальнейшем вносятся в паспорт ГВ. По этим параметрам оценивается качество и производится приемка винта.
2.1.2Общие принципы обработки результатов измерений. Основы методов
Основой для определения отклонения от заданной формы является измеренный профиль в форме ветви кривых (линейной диаграммы) или точек Pi (Xi Yi) для i=1 n этого измеренного профиля. Координаты точек получают в зависимости от метода измерения непосредственно из измерений расстояний или косвенно из угловых измерений.
2.1.2.1Графическое определение результатов измерений
Координаты Xi Yi точек Pi профиля измеренного дискретными методами следует представить в соответствующем масштабе в прямоугольной системе координат X Y причем ось Х базовой прямой или базового направления соответствует измерению.направления Y необходимо выбрать всегда значительно больше масштаба в направлении X. Путем прямолинейного соединения представленного в системе координат точек Pi получают измеренный профиль в форме полигональной линии.
Измерение отклонения формы в заданном направлении координатно-измерительной машиной.
2.1.2.2Описание метода измерения
Измеряемую деталь устанавливают на стол координатно-измерительной машины и рассматриваемый профиль поверхности выравнивают с одной из осей координат измерительной машины. Ощупывают рассматриваемый профиль и измеряют координаты Xi Yi измеряемых точек Pi. Номинальный эталонный профиль содержится в памяти ПЭВМ в виде числового массива.
2.1.2.3Погрешность измерения
На погрешность методов измерения влияет особенно погрешность измерительного прибора определяемая измерительной линейкой совместно с лимбом. Она составляет ± 02 мм. Кроме этого существуют и менее значимые составляющие:
)Погрешность измерительного мостика;
)Погрешность обусловленная шаговым методом;
)Погрешность от ограниченного количества измеряемых точек;
)Погрешность от влияния внешней среды;
)Субъективная погрешность. Результаты снимаются визуально оператором и их точность зависит от его профессионализма и состояния. Эта погрешность может достигать ± (02-05) мм.
Характерным примером средства измерения является компьютерная лазерная интерференционная система фирмы Reniahaw.
Толщиномер предназначен для упрощения технологического процесса замеров толщины лопасти винта в контрольных точках а также для повышения точности этих измерений.
Рисунок 1.3 – Толщиномеры
)Контроль геометрической поверхности каждой лопасти на этапах обработки внутренней поверхности лопасти. На этапах контролируется геометрическая поверхность толщина лопасти в соответствующих сечениях. Причем информация о толщине является основной для корректировки технологического процесса фрезерования;
)Контроль геометрии и толщины лопастей в процессе окончательной доводки и шлифовки наружной поверхности лопасти после окантовки и установки. На этом этапе процесс контроля лопасти ГВ выполняется многократно по ходу обработки;
)Окончательный контроль геометрии и толщины лопастей ГВ производится на специализированном стенде где винт устанавливается неподвижно с соответствующей ориентацией. Контроль геометрии производится с помощью специального шагомера путем замеров координат 8-10 точек в соответствующих сечениях винта при этом разметка контрольных точек на поверхности винта производится с помощью того же шагомера. Предварительно эти поверхности обмеливают. После разметки и замеров координат производятся измерения толщины лопасти ГВ во всех отмеченных сечениях на тех же точках в которых измерялись и координаты поверхности. Результаты окончательного контроля оформляются в виде таблиц и соответствующих протоколов и в дальнейшем вносятся в паспорт винта. По этим параметрам оценивается качество и производится приемка винта.
2.2.1Метод измерения толщины лопасти гребного винта
Технологический процесс окончательного контроля толщины лопасти ГВ в соответствующих сечениях заключается в следующем:
)Винт устанавливается и соответствующим образом ориентируется на специальной контрольно-измерительной плите;
)Наружная поверхность винта покрывается мелованным раствором;
)Производится разметка с помощью шагомера сечений и точек измерения. Число сечений и точек измерения на каждой лопасти оговаривается требованием регистра Ллойда;
)В зависимости от типоразмеров ГВ выбирается необходимый кронциркуль таким образом чтобы с помощью этого кронциркуля можно было измерить любую точку лопасти вплоть до середины лопасти;
)Устанавливают верхний щуп кронциркуля в нужную контрольную точку а затем ориентируют его так чтобы плоскость кронциркуля совпадала с плоскостью сечения. Необходимо чтобы нижний и верхний щупы были перпендикулярны поверхности винта. При этом будет контролироваться минимальная толщина сечения;
)Осторожно не изменяя расстояния между щупами вынимают кронциркуль;
)Измеряют расстояние между щупами кронциркуля с помощью измерительной линейки или штангенциркуля;
)Измеренные расстояния заносятся в таблицу контроля в соответствующую графу;
)Вновь устанавливают кронциркуль в следующую точку сечения и повторяют операции под пунктами 5-8 для всех точек данного сечения и по всем сечениям в целом.
2.2.2Возможные методы контроля
На текущий момент существуют несколько методик контроля. В качестве возможных в использовании вариантов рассматривались лазерный способ измерения толщины лопасти ГВ ультразвуковой метод контроля метод обыкновенного кронциркуля но с блоком сопряжения его с оптоэлектронным датчиком угловых перемещений.
При использовании лазерного метода контроля точность измерения может быть намного больше чем у всех остальных методик. Недостаток данного метода заключается в том что винт имеет очень сложную геометрическую форму и не все точки геометрической поверхности могут быть промерены данным способом из-за того что не ко всем точкам поверхности может быть получен доступ при стационарном креплении лазеров. Поэтому от метода измерения толщины лопасти ГВ также пришлось отказаться.
Приемлемым оказался метод измерения толщины при использовании обычного толщиномера с модулем сопряжения с оптоэлектронным датчиком. В данном методе методика установки кронциркуля в контрольную точку осталась та же но результаты измерений сразу же выводится на индицирующее устройство. Поэтому при применении этого метода можно избежать субъективных ошибок вызванных неперпендикулярной установкой щупов. Это достигается тем что оператор располагая щупы перпендикулярно поверхности смотрит на показания прибора и выбирает положение кронциркуля так что показания прибора были минимальны. Очевидно что в этих точках и будет перпендикуляр т.к. наикратчайшее расстояние между двумя параллельными прямыми есть расстояние по перпендикуляру. На одном из этапов реализации прибора была утроена презентация заказчику прибора реализованная по данному типу и заказчика это метод контроля устроил.
3Основные разметочные операции и их особенности
3.1Технология входного контроля заготовки лопасти гребного винта
Технологический процесс входного контроля заготовок лопасти производится на специализированном КИС оборудованном системой установки шагомера и его перемещение вдоль измерительного стенда как по высоте так и по продольной высоте.
Входной контроль производится в следующей последовательности:
)Заготовка лопасти устанавливается на КИП наносится на контролируемую поверхность лопасти меловой раствор;
)С помощью шагомера измеряются трехмерные координаты опорных (контрольных) точек на поверхности лопасти и производится предварительная разметка осевых линий и радиальных сечений;
)По результатам предварительных замеров производится вписывание исходной теоретической лопасти в заготовку. Это наиболее трудоемкая операция от качества выполнения которой зависит качество и дальнейшая обработка лопасти.
Процесс вписывания производится путем установки заготовки лопасти по заданному уклону и шагу винта. С этой целью с помощью специальных клиньев производится изменение ориентации лопасти так чтобы добиться строго совпадения заданного шага и уклона лопасти. После чего производится уточнение и окончательная разметка осевых линий;
)Производится разметка подрезки кормового торца на наружной поверхности фланца лопасти. Нанести контрольные риски на кромке лопасти и наружной поверхности фланца у скосов для установки лопасти в горизонтальной плоскости;
)Наносятся радиальные сечения и в этих сечениях отмечаются точки замера шага и толщин лопасти;
)Производятся входные замеры геометрических параметров лопасти: лопасти длины и толщины сечений катеты сечений высоты точек замера относительно кормового торца откидку лопасти на сечениях. Данные занести в паспорт разметки заготовки лопасти ГВ.
3.2Позиционирование заготовки станка FCW 150 (W 200H)
Разметочно-расточная операция выполняется в следующей последовательности:
)Лопасть устанавливается на планшайбу станка ось вращения лопасти устанавливается в центр планшайбы а сама поверхность лопасти устанавливается в горизонтальное положение;
)Производится разметка скосов с обнижением 2 ± 05 мм. Выполнить разметку центров отверстия 80Н8 и отверстия М110х4 – 6. Наносятся контрольные окружности. Предъявить в ОТК. Установку и лопасти не раскреплять и не сбивать;
Все измерения выполняются с помощью штатной КИ системы станка. При этом точность разметки центра отверстий ± 05 мм;
)Составляется паспорт разметки и предъявляется в ОТК.
3.3Разметочная операция выполнения расточной операции 090 на станке FCW 150 (W 200H) и после сборки фальшступицы
Эта операция выполняется на КИП.
)Устанавливается шагомер и наносится меловой раствор;
)Производится разметка осевой линии;
)Наносятся радиальные сечения;
)Наносятся на сечениях точки замера шага и толщин;
)Производятся замеры геометрических параметров лопасти (радиус лопасти длины сечений высоты точек замера относительно кормового торца толщины сечений катеты сечений откидка лопасти на сечениях 04R; 06R; 09R);
)Заполняется паспорт копия паспорта отдается мастеру а оригинал в ОТК.
4Современные требования к контрольно-измерительным системам
В существующем технологическом процессе контроля геометрии ГВ и их элементов в основном используется измерительные системы использующие контактные методы точечного контроля поверхности (методы ощупывания). В частности широко используются толщиномеры и шагомеры которые были рассмотрены выше. Подобные измерительные системы не отвечают современным требованиям предъявляемые заказчиками.
К основным недостаткам таких контрольных систем относится:
)Используемые толщиномеры и шагомеры не позволяют получить заданную точность ± 05 мм у толщиномеров и ± 0005 мм у шагомеров. После модернизации автоматизации точность измерений увеличилась до 0005 мм (на порядок выше);
)Невозможность сопряжения подобных систем с современной цифровой и вычислительной техникой;
)Невозможность использования современных информационных технологий;
)Большая трудоемкость процесса технологии и из-за этого невозможность накоплений больших объемов координат трехмерного пространства (невозможность получения облака точек которое наиболее характеризует качество поверхности);
)Необходимость большого объема подготовительных работ для проведения контрольно-измерительных операций (в этом случаи для выполнения каждой операции необходимо демонтировать винт транспортировать на КИП подготовить рабочее место а потом все разобрать).
Анализируя указанные недостатки можно отметить что использование таких измерительных систем требует настоятельной замены и использование других современных систем. К таким системам должны предъявляться следующие требования:
)Точность измерения контроля трехмерных координат контролируемой поверхности должна быть не хуже 001 мм;
)Возможность получать и накапливать большие объемы измерительной информации (облако точек не менее 100000 на каждой поверхности области ГВ);
)По полученному исходному облаку точек обеспечить восстановление геометрии поверхности;
)Возможность хотя бы частичной автоматизации процессов контроля;
)Современные системы контроля должны использовать бесконтактные методы и обеспечивать контроль по дальности до 20 м;
)За счет автоматизации исключить из технологического процесса большое число промежуточных контрольно-измерительных и разметочных операций а также операций с дополнительной транспортировкой.
Анализируя предъявленные требования к современным системам можно отметить что наиболее подходящими системами контроля являются бесконтактные методы контроля геометрии сложнопрофильных конструкций.
АВТОМАТИЗАЦИЯ ПРОЦЕССА КОНТРОЛЯ ГЕОМЕТРИИ ГРЕБНЫХ ВИНТОВ ПРИ ИХ ИЗГОТОВЛЕНИИ
В настоящее время существует несколько методов контроля геометрии:
)контактный метод позволяющий с помощью специальных щупов получать координаты контролируемой поверхности;
)бесконтактный метод позволяющий определить с высокой точностью координаты множества точек форму и взаимное расположение всех элементов контролируемой конструкции.
Далее более подробно рассмотрим бесконтактный метод контроля геометрии.
1Бесконтактные методы контроля геометрии сложнопрофильных конструкций
Развитие фотограмметрии связано с использованием фотоснимков для измерительных целей. Однако в последнее время в связи с развитием науки и техники появились и другие средства для получения изображений обладающих измерительными свойствами (телевидение голография рентгеноскопия и т.д.). При этом во всех случаях общие принципы решения измерительных задач определяются классическими методами фотограмметрии и сводятся к установлению математической зависимости между координатами изображения точек на снимках и на реальном объекте съёмки а также к созданию методов обработки снимков в измерительных целях. В связи с этим понятие фотограмметрии стало более широким. Поэтому определение форм размеров и положения объектов по их фотографическому изображению [8] (измерительная фотография) несколько устарело и не раскрывает всех возможностей фотограмметрии как науки и технической дисциплины.
1.1Фотограмметрические методы
Такие методы позволяют при определённых способах съёмки найти абсолютное геометрическое описание объекта т.е. найти координаты Xi Yi Zi для любой точки полученной на изображении объекта в единой для него системе координат или решать частные задачи по определению координат отдельных деталей объекта взаимного их расположения и т.д.
ФГМС реализуются как в однокамерном так и двухкамерном вариантах СФГМС. В случае однокамерной ФГМС измеряемый объект фотографируется цифровой камерой с нескольких различных направлений. При этом 3D-координаты одноименных точек измеряемого объекта могут быть определены по их расположению на плоских изображениях (фотографиях) таких изображений требуется минимум два но для повышенной точности измерения следует получить намного больше фотографий. Таким образом однокамерные ФГС реализуют off-line технологию и 3D-координаты точек измеряемого объекта получаются в результате обработки всех полученных фотографий (смотри приложение В)
Рисунок 2.1 – Методы стереофотограмметрической съемки: а) нормальный случай съемки; б) общий случай съемки
Далее рассмотрим нормальный случай съемки который показан на рисунке 2.2 (а).
Получение пространственных координат точек объекта поясним на примере нахождения трех координат точки М принадлежащей контролируемой поверхности (рисунок 2.2). Пусть начало координат находится в левом центре проецирования S ось Y совпадает с направлением оптической оси левой камеры ось Х направлена вдоль базиса В а ось Z перпендикулярна плоскости рисунка.
Рисунок 2.2 – Нормальный случай съемки
Обозначим координаты точки m и m’ в плоскости снимков соответственно через и а пространственные координаты точки М – через (XYZ).
Если из правого центра проецирования провести прямую параллельную MS до пересечения в точки m1 лежащей в плоскости снимка р то получим подобные треугольники . Из подобия этих треугольников следует что
где – горизонтальный параллакс. Из (2.1) находим что
При рассмотрении другой пары подобных треугольников получаем что откуда с учетом (2.1) имеем:
Из подобия третей пары треугольников находим последнюю пространственную координату откуда
Точки и являются проекциями точки соответственно на плоскости и а точка – проекция точки в плоскости левого снимка. Для случая когда фокусные расстояния левой и правой видеокамер не равны уравнения (2.2) – (2.4) будут иметь вид:
где – координаты левого и правого снимка – фокусные расстояние левой и правой камеры.
Рассмотрим общий случай съёмки.
Стереоскопическая съемка в этом случае позволяет получить пару перекрывающихся снимков объекта. Основными трудностями этой съемки при вычислении пространственных координат являются определение параметров измерительной системы и угловых положений видеокамер.
В этом случае общее решение фотограмметрической задачи распадается на два этапа:
)Преобразование координат точек измеренных на реальных снимках и приведение их к воображаемому случаю нормальной съемки (взаимное ориентирование);
)Переход к пространственной системе координат SXYZ с учётом расчётных или известных углов ориентирования.
Для получения информации о размерах и форме исследуемых объектов необходимо чтобы полученное изображение было приведено к случаю съемки когда снимок и выбранная плоскость изображения параллельны.
Рассмотрим зависимость между координатами точки М на изображении стереопары и на реальной поверхности (рисунок 2.3).
Рисунок 2.3 – Общий случай съемки
Пусть координаты некоторой точки m в системе известны как . Требуется определить координаты этой же точки m в системе взаимного ориентирования т.е. . Так как матрица поворота системы относительно системы при совмещенных началах известна то необходимая связь координат может быть записана в виде [8]:
где – коэффициенты ортогональной матрицы которые являются направляющими косинусов системы относительно.
Для перехода к трансформированным координатам выражения для необходимо умножить на некоторый масштабный коэффициент чтобы координаты привести к первоначальному фокусному расстоянию снимков т.е.
где – измеренные координаты точек на наклонном снимке – трансформированные координаты сориентированных изображений.
Таким образом для определения пространственных координат при общем случае съёмки необходимо вначале определить углы ориентирования (направляющие косинусы) а затем по известным координатам изображения с учётом формул (2.7 – 2.9) определить координаты контролируемой поверхности.
Лазерные измерительные системы основанные на использовании трёхмерных лазерных сканеров трекеров лазерных тахеометров и т.д. Такие системы довольно широко используются в судостроительной промышленности и позволяют за одну установку получать координаты большого числа точек на удалении до 10-20 метров с точность порядка 1-2 мм. Затем по результатам измерений восстанавливать геометрию (вид или образ) контролируемого объекта в соответствующей системе координат.
2Фотограмметрическая система V-STARS
Фотограмметрические измерительные системы позволяющие сразу получать изображение объекта последующая цифровая обработка которого позволяет определить трёхмерные координаты большого числа точек с точностью менее 05 мм на приемлемом для судостроения удалении до 10-15 м. Эта группа методов противоположна первой т.к. здесь решается уже обратная задача – по реально полученной форме изделия (фотоснимкам) определяются координаты большого числа предварительно отмеченных точек и по ним получают абсолютное геометрическое описание объекта. Т.о. можно определить трёхмерные координаты для любой точки полученной на изображении объекта или решать частные задачи по определению размеров и координат отдельных деталей объекта взаимного их расположения и т.д.
Основные области применения системы V-STARS:
)Контроль и обратный инжиниринг как простых деталей так и сложных криволинейных поверхностей объектов различных размеров;
)Контроль изготовления и периодическая инспекция шаблонов кондукторов и калибров;
)Мониторинг деформаций и перемещений объектов и систем вызванных изменением температуры и нагрузки;
)Сборка элементов различных конструкций;
)Контроль партий деталей и проверка повторяемости размеров при сборке а также симметрии готовых изделий;
)Монтаж и контроль сборочных линий и конвейеров;
)Измерение трубопроводов.
Система V-STARS предназначена для контроля геометрических параметров крупногабаритных изделий и технологической оснастки в реальном масштабе времени. V-STARS это фотограмметрическая система высокого уровня обеспечивающая высокую универсальность скорость и точность измерений [8]. Главный элемент системы V-STARS – специальная цифровая камера DYNAMO разработанная для проведения высокоточных измерений в промышленности. Камера DYNAMO аккумулировала в себе все революционные решения технологии и продуманный дизайн предыдущих камер фирмы GSI. Эргономичный и прочный корпус камеры защищает её от возможного повреждения во время работы а система автоматической настройки экспозиции позволяет легко и быстро проводить измерения. Общий вид камеры с калиброванными щупами показан на рисунке 2.4. Система V-STARS работает с двумя камерами DYNAMO обеспечивая тем самым высокую динамику измерений.
Среди достоинств можно выделить функцию самокалибровки камеры. Изображения с камеры могут записываться на Flash-носитель или передаваться по Wi-Fi протоколу. V-STARS – это технология позволяющая определять трёхмерные координаты большого числа точек объекта из серии цифровых фотографий. При этом на каждом изображении программа находит общие точки. Достаточно нескольких снимков объекта чтобы получить облако точек. Полученные данные могут быть проанализированы в программном обеспечении V-STARS или экспортированы в другие программные пакеты для проведения контроля геометрических параметров изделия. Результатом измерений являются координаты X Y Z центров светоотражающих маркеров размещённых на объекте или светящихся точек спроектированных проектором Pro-SPOTA.
Стереофотограмметрическая система V-STASR производства фирмы Geodetic (США) состоит из следующих основных элементов определяющих её технические характеристики (смотри приложение Г):
)Две цифровые камеры DYNAMO-5 с ПЗС-матрицами с разрешением 5 мегапикселей с полем зрения 55°×48° и оснащённых объективами с фиксированным фокусом;
)Проектор Pro-SPOTA с калиброванной решёткой которая позволяет проектировать 22500 точек;
)ПО V-STARSM которое установлено на ноутбук обеспечивающее режимы фотограмметрических и стереофотограмметрических измерений;
)Масштабная линейка Sca
)Кодированные мишени разных размеров и рулоны самоклеящихся световозвращающих маркеров;
)Набор щупов различных конфигураций;
Рисунок 2.4 Цифровая камера DYNAMO с измерительным щупом
ФГМС V-STARS обеспечивает следующие характеристики:
)Рабочая зона до 100 м;
)Точность измерения в однокамерном режиме (S-Mode) 8 мкм + 8мкмм в двухкамерном режиме (M-Mode) 16 мкм + 16мкмм;
)Скорость съёмки в двухкамерном режиме до 10 кадровс.
Основными достоинствами системы V-STARS являются:
)Высокая точность измерений;
)Высокая степень автоматизации процесса измерений объективность их результатов;
)Большая производительность;
)Широкие возможности проведения измерений в полевых или цеховых условиях;
)Возможность дистанционных измерений в условиях
Фотограмметрическая система V-STARS может работать как в режиме on-line так и в режиме off-line. В режиме off-line изображения сохраняются на съёмном цифровом носителе. При этом используется быстрый и эффективный алгоритм сжатия изображений позволяющий сохранять сотни фотографий на одной карте Flash-памяти.
В on-line режиме изображения передаются по беспроводному протоколу на компьютер с программным обеспечением V-STARS. В этом режиме система может работать с несколькими камерами обеспечивая тем самым большую динамику измерений. DYNAMO позволяет учесть все условия и выполнить работу в кратчайшие сроки даже если задача требует кропотливых измерений с большого количества позиций при дистанционном проведении замеров а также быстрого получения результатов.
Для выполнения измерений на контролируемую поверхность вначале устанавливаются специальные кодированные мишени и светоотражающие маркеры различных размеров (рисунок 2.5).
Рисунок 2.5 Закодированные мишени и светоотражающие маркеры
Коды на закодированных мишенях по своей структуре уникальны и имеют идентификационный номер поэтому программа распознает их автоматически. Закодированные мишени являются связующим элементом на фотографиях сделанных с разных позиций. На фотографии таких мишеней должно быть видно минимум 4 штуки на каждом снимке. Также закодированные мишени позволяют программному обеспечению определить положение и ориентацию камеры в пространстве.
Чтобы определить размеры объекта в фотограмметрии применяются калиброванные масштабные линейки (рисунок 2.6) на которых фиксируется минимум 2 светоотражающих маркера на известном расстоянии. Расстояние между маркерами используется для масштабирования объекта т.к. без масштабной линейки можно определить только его форму.
Пример размещения маркеров на контролируемой поверхности и подготовки детали к измерениям показано на рисунке 2.7. После размещения маркеров и закодированных мишеней на объекте оператор с помощью камеры делает несколько снимков объекта с разных сторон и под разными углами. При использовании двух камер положения камеры в пространстве и относительно друг друга будет играть существенную роль при расчёте точности. Идеальным углом для измерений является угол 90° но положения камер под углами между 60° и 120° тоже допустимы. Слишком близкое расположение камер относительно друг друга при измерении ухудшает геометрию и оказывает негативное влияние на точность.
Рисунок 2.6 Масштабная линейка ScaleBar с базой 870 мм (одна половина) и 1840 мм (в сборе) в кейсе для переноски
Рисунок 2.7 Схема размещения ленточных маркеров кодированных мишеней и масштабной линейки
Альтернативным и более быстрым способом нанесения маркеров на объект является использование специального проектора Pro-SPOT (рисунок 2.8). Проектор Pro-SPOT направляет на объект мощный поток света проецирующий через специальные калиброванные решётки до 23 тысяч светящихся точек. Применение проектора Pro-SPOT позволяет измерять большой массив данных и получать результат в виде плотного облака точек которое можно наложить на CAD-модель с целью получения цветовой карты отклонений (рисунок 2.9). Использование проектора не исключает размещения на объекте закодированных мишеней но уже в меньшем количестве по сравнению с измерениями без проектора.
Рисунок 2.8 Проектор Pro-SPOT на треноге с камерами
Рисунок 2.9 – CAD-модель цветовой карты отклонений
3Лазерные сканеры трекеты и радары
Лазерные системы основаны на использовании трёхмерных лазерных сканеров трекеров лазерных тахеометров лазерных радаров и т.д. Такие системы широко используются в судостроительной промышленности и позволяют за одну установку получать координаты большого числа точек на удалении до 10-20 м с точность порядка 1-2 мм. Далее по измерительным результатам восстанавливают геометрию (вид или образ) контролируемого объекта в соответствующей системе координат.
Основой лазерных трекеров и радаров является измерительный блок состоящий из блока лазерного дальномера который с помощью электроприводов может поворачиваться вокруг двух взаимно перпендикулярных осей причём углы поворота контролируются угловыми датчиками с высокой точностью. Таким образом первичной информацией вырабатываемой трекером или радаром являются координаты измеряемой точки в сферической системе координат (рисунок 2.10) программное обеспечение позволяет выполнять пересчёт координат точек измеряемого объекта в любые требуемые системы отсчёта. Расстояние до измеряемого объекта может составлять 100 и более метров.
Принцип работы лазерного радара:
Рисунок 2.10 – Система координат измерительного блока лазерного трекера и радара
Измерительный блок (рисунок 2.11) может устанавливаться на специальном штативе или основании. Сервоприводы позволяют наводить и удерживать лазерный луч дальномера на измеряемом объекте даже в случае когда объект перемещается с достаточно большой скоростью (несколько градс). Трекерами измеряются координаты центра марки с уголковым отражателем (стальной шар с запрессованной в него трипельпризмой) или координаты наконечника специального щупа на котором также установлена трипельпризма вместо контактного наконечника. Кроме того на конец щупа может устанавливаться сканирующая головка превращающая трекер в лазерный сканер (скорость сканирования до 9000 точекс). Внешний вид марки-отражателя и щупа со сканирующей головкой показан на рисунке 2.12. Погрешность измерения расстояний (канал дальномера) в режиме абсолютного дальномера (измеряет реальное расстояние) использующего фазовый метод составляет не более 10 мкм ± 10 мкмм. Точность измерения расстояний может быть увеличена при использовании режима лазерного интерферометра (высокая точность) в этом случае погрешность не более 5 мкм ± 5 мкмм.
Рисунок 2.11 Внешний вид: лазерного трекера Radian50 фирмы API (а) и
лазерного радара MV200 фирмы Metris установленного на основание (б)
Лазерные радары не нуждаются в уголковых отражателях так как измеряют координаты точки высвечиваемой лучом лазера на поверхности измеряемого объекта или измеряют центры специальных мишеней (марок) установленных на объекте. Для измерения расстояний используется технология частотно-модулированного лазерного монохромного (постоянная длина волны) радара (рисунок 2.13) позволяющая получить точность сравнимую с лазерным интерферометром.
Рисунок 2.12 Внешний вид: а) стандартная марка-отражатель (диаметр шара 15 дюйма); б) беспроводной щуп Intell в) щуп IntelliProbe 360
со сканирующей головкой
Рисунок 2.13 Принцип измерения расстояний в лазерном радаре
4Особенности автоматизации контрольно-измерительной и разметочной операций при изготовлении гребных винтов
Существующий технологический процесс выполнение межоперационных и разметочных операций с использованием контактных методов и технических средств рассмотренных в главе 1 не отвечает современным требованиям и имеет целый ряд недостатков:
)Не обеспечивает требуемой точности. Показания измерения зачастую субъективны;
)Большая трудоемкость которая составляет 30 – 40% от технологического процесса;
)Как следствие подобных технических средств не позволяют автоматизировать технологический процесс межоперационного контроля геометрии и разметочных операций.
Предполагаемые бесконтактные методы контроля с использованием СФГМС V-STARS позволяет в более полной мере автоматизировать технологические операции связанные с контрольно-измерительными и разметочными операциями в частности:
)Процесс автоматизации характерен как на аппаратном так и на организационном уровнях. На аппаратном уровне используемое оборудование V-STARS хорошо сопрягается с вычислительными средствами и с информационными технологиями. Поэтому процесс автоматизации здесь возможен на стадии проектирования и изготовления винтов и их элементов. Т.е. можно ввести сравнение двух параметров «как спроектировано» и «как получено» на том или ином этапе изготовления следовательно вносить коррекцию в технологический процесс;
)При выполнении поэтапных измерительных операций возможен более быстрый обмен получаемой информации между технологическим и конструкторским отделами предприятия;
)Получение исходной цифровой 3D-модели заготовки и их сравнение (вписывание) теоретической 3D-модели позволяет произвести оптимальные распределение припусков с учетом возможных дефектов этой заготовки а следовательно своевременно вырабатывать заключение о запуске заготовки в технологический процесс или ее дефектации или предварительной наплавки;
)Важным процессом автоматизации при использовании СФГМС является автоматизация процесса позиционирования на техническом оборудовании при выполнении соответствий операций. В этом случае СФГМС позволяет визуально позиционировать (перемещать) обрабатываемую заготовку на том или ином станке без использования дополнительных разметок точек на КИП следовательно исключить дополнительно транспортировку и контовку;
)Использование СФГМС позволяет формировать окончательный технологический паспорт готового винта содержащий необходимые табличные данные требуемые регистром а также дополнительно окончательную цифровую 3D-модель готового винта (модель винта «как построено») и кроме того исходную 3D-модель «как спроектировано». Кроме того в технологическом паспорте в обязательном порядке должна приведена картина отклонения 3D-модели «как построено» с 3D-моделью «как спроектировано». По этой картине можно судить качество изготовления конкретного винта. Подобный технологический паспорт должен сопровождать винт на всех этапах его жизни (начиная от проектирования и кончая утилизацией). При этом можно автоматизировать процессы дефектации и ремонта ГВ на различных этапах его жизни.
5Методика получения цифровой 3D-модели заготовки элементов гребного винта
5.1Методика получения цифровой 3D-модели заготовки элементов гребного винта с помощью лазерных сканеров
Общие правила измерения:
)Обращайтесь со сканером системы и транспортируйте сканер с особой осторожностью. Избегайте ударов высокой тряски сенсора;
)Не изменяйте настройки диафрагмы проектора и объективов камер;
)Используйте транспортировочный кейс для перевозки сканера;
)Во время сканирования необходимо обеспечить неизменную освещенность объекта (как дневного освещения так и искусственного) и поддерживать постоянную температуру окружающей среды;
)При сканировании объекта не использовать внешнее неоновое освещение;
)Избегайте попадания прямых солнечных лучей;
)Перед сканированием объекта рекомендуется включить питание сенсора на 30 минут для прогрева его внутренних компонентов;
)По возможности сокращайте время работы лампы проектора (уменьшается внутренний нагрев компонентов и увеличивается срок службы лампы);
)Избегайте движения вблизи сканера во время сканирования (источники помех являются вибрации тени и т.д.).
Принцип действия системы сканера основан на проецирования структурированного света на сканируемый объект. Контрастное изображение спроецированное на объект искривляется что и дает возможность воссоздать его объемную форму. Получение полной объемной модели объекта заключается в проведении серии 3D-снимков (сканов) сделанных с разных сторон и их последующем объединении в единое целое. Предусмотрено несколько стратегий для осуществления «склейки» сканов – использование наклеенных маркеров использование характерных элементов геометрии объекта использование внешней фотограмметрической системы использование автоматизированных поворотных устройств.
Для поддержания постоянно высокой точности измерения система подвергается регулярной калибровке при помощи соответствующих для каждой зоны измерения калибровочных плит. Калибровочные плиты представляют собой плоские углепластиковые панели черного цвета в металлическом корпусе с нанесенными на них круглыми белыми метками координаты центров которых определены заводом-изготовителем и записаны в соответствующем файле. В процессе калибровки сканер замеряет калибровочную плиту в 9 различных положениях во всем объеме зоны измерения. Полученные сканером координаты центров меток сопоставляются с эталонными значениями из файла после чего рассчитываются новые геометрические характеристики сканера и параметры оптики (учет оптических искажений).
Весь процесс работы – управление сканером калибровка задание параметров сканирования обработка снимков получение трехмерных моделей и анализ их геометрии ведется через программное обеспечение OPTOCAT являющееся неотъемлемым компонентом системы измерения.
5.2Методика получения цифровой 3D-модели заготовки элементов гребного винта с помощью V-STARS
Требования к расположению измеряемого объекта:
)Измеряемый винт или лопасть располагается на ровной горизонтальной площадке – измерительной плите бетонном основании в устойчивом положении при необходимости раскрепляется;
)Винт располагается горизонтально (ось винта вертикально) лопасть желательно устанавливать на фланец чтобы перо ее было вертикально;
)Размеры площадки должны обеспечивать свободный доступ к измеряемому объекту со всех сторон свободное пространство вокруг измеряемого объекта не менее 15 метров;
)Должна быть предусмотрена возможность кантовки винта (лопасти) на другую сторону;
)Должна быть обеспечена возможность подключения СФГМ системы V-STARS к электросети 220В50Гц с заземлением и к цеховой сети сжатого воздуха.
5.2.1Развертывание стереофотограмметрической системы V-STARS и подготовка к измерениям
)Развертывание системы V-STARS для выполнения измерений объекта. Поблизости от измеряемого объекта располагается рабочее место оператора системы V-STARS - ноутбук с контроллером измерительных камер. При выборе положения рабочего места следует учитывать что длина соединительных кабелей измерительных камер DYNAMO-5 составляет 10 метров. Согласно руководству пользователя системы V-STARS выполняется подключение камер DYNAMO-5 к контроллеру и контроллера к ноутбуку. Включение контроллера производится только после подключения к нему камер и подключения контроллера к ноутбуку. Камеры подключаютсяотключаются только при выключенном контроллере. Питание системы осуществляется от сети 220 В50 Гц с заземляющим проводом.
В случае использования проектора он устанавливается на штатной треноге вместе со своим контроллеромблоком питания подключение проектора PROSPOTA к своему контроллеру и ноутбуку осуществляется согласно руководству пользователя системы V-STARS. Подключениеотключение проектора производится только при выключенном контроллереблоке питания. Питание проектора осуществляется от сети 220 В50 Гц с заземляющим проводом.
)Непосредственно на поверхности измеряемого винта (лопасти) создаются контрольные точки минимум 3 штуки. Контрольные точки должны быть промаркированы например К1 К2 К3.. . Контрольные точки задают вспомогательную систему координат используемую для геометрической связи (сшивки) поверхностей винта (лопасти) измеренных по отдельности. Контрольные точки не должны лежать на одной прямой и должны располагаться по возможности дальше друг от друга. Кроме того контрольные точки должны оставаться доступными для измерения после кантовки (лопасти) или при переходе к измерениям другой его стороны. Наиболее рациональным является положение контрольных точек на кромках лопастей винта (лопасти).
5.2.2Выполнение измерений
Измерение геометрии лопасти выполняется последовательно по этапам:
)На доступных для измерения поверхностях винта (лопасти) размещаются и фиксируются кодированные мишени и масштабная линейка ScaleBar. Выполняется процедура создания драйвер-файла после чего масштабная линейка ScaleBar убирается на хранение.
)Определяются с помощью ручного щупа определяются координаты всех контрольных точек в создаваемом файле геометрической информации контрольным точкам присваиваются имена соответствующие их маркировке.
)С помощью ручного щупа (или специальных инструментальных мишеней-меток) выполняется измерение точно обработанных поверхностей винта (лопасти) являющихся конструкторскими базами: цилиндрическая или коническая поверхность отверстия в ступице винта (фланца лопасти); торцевые плоскости ступицы винта (фланца лопасти); плоскости скосов фланца лопасти.
)Измерение геометрии сложных криволинейных поверхностей винта (лопасти) рекомендуется производить комбинированным способом:
1)Большая по площади часть поверхности лопасти имеет малую кривизну является самой ответственной и требует наибольшей плотности измеренных точек может быть измерена с помощью световых мишеней проецируемых проектором PRO-
2)Меньшая по площади часть поверхности (кромка лопасти и галтельные переходы) имеет большую кривизну она должна измеряться с помощью ручного щупа так как на такой поверхности мишени (метки) проецируемые PROSPOTA сильно искажаются и могут дать большую погрешность в измерении.
)Винт перекантовывается другой стороной вверх и повторяется этапы измерений с 1 по 4 описанные выше полученная геометрическая информация сохраняется в новом файле. В случае лопасти поставленной на фланец пером вверх кантовка лопасти не требуется просто переходим к измерениям другой стороны.
5.2.3Обработка результатов измерения и создание модели измеряемой лопасти гребного винта
Обработка осуществляется в ПО V-STARS состоит из следующих этапов:
)Осуществляется связывание (сшивка) измеренных по отдельности поверхностей винта (лопасти) для этого:
1)В каждом созданном файле с полученной геометрической информацией создается вспомогательная система координат по трем одинаковым контрольным точкам;
2)Выполняется преобразование координат всех измеренных точек в файле хранящихся в файле во вспомогательную систему координат таким образом вся полученная в результате измерений геометрическая информация приведена к одной системе координат;
3)Информация из всех файлов сводится в один.
)Создание (восстановление) конструкторской системы координат винта (лопасти):
1)По координатам точек измеренных на этапе 3 создаются модели поверхностей являющихся конструкторскими базами;
2)На основании указанных в предыдущем пункте поверхностей создается (восстанавливается) конструкторская система координат;
3)Координаты всех измеренных точек преобразуются в конструкторскую систему координат. Таким образом получаем 3D-модель винта (лопасти) в виде координат набора точек его поверхности.
)Построенная в точечная 3D-модель ГВ (лопасти) может непосредственно использоваться для контроля геометрии. Для этого теоретическая (конструкторская) твердотельная модель ГВ (лопасти) сравнивается с построенной точечной моделью в программе SpatialAnalyser. Результат сравнения в виде максимальных средних или иным образом взвешенных отклонений точечной модели от теоретической может быть использован для контроля геометрии винта (лопасти).
)Для получения паспорта винта в виде набора профилей расчетных (контрольных) сечений требуется:
1)По точечной 3D-модель ГВ (лопасти) создать поверхностную модель;
2)Выполнить сечение поверхностной модели цилиндрическими поверхностями расчетных радиусов получив таким образом профили расчетных сечений.
6Особенности вписывания теоретической (исходящей) 3D-модели в 3D-модель заготовки
Вписывание производится следующим образом:
)Наложение облака точек теоретической модели на облако точек модели заготовки. При этом смещая и ориентируя систему координат теоретической модели лопасти относительно системы координат заготовки добиваются чтобы как можно было равномернее (либо оптимально с учётом локальных дефектов) распределить припуски во всем объёме заготовки;
)После вписывания произвести совмещение системы координат модели заготовки с системой координат теоретической модели лопасти. Далее необходимо пересчитать координаты облака точек модели заготовки в систему координат теоретической модели лопасти X Y Z;
)Определить цветовую схему отклонений координат модели заготовки и координат теоретической 3D-модели лопасти (т.е. получить цветное 3D-изображение заготовки в которую вписано 3D-изображение теоретической лопасти). По величине полученных отклонений судят о равномерности распределения припусков во всем объёме заготовки. Если вписывание лопасти в заготовку неудачное то необходимо повторить пункты 2 и 3.
Операция вписывания лопасти в заготовку является ответственной так как от качества её выполнения зависит дальнейший технологический процесс обработки лопасти.
В результате вписывания координатные оси модели заготовки и координатные оси теоретической модели лопасти приводятся к основной системе координат XYZ которая и используется в дальнейшем технологическом процессе. На рисунке 2.14 показаны направление осей основной XYZ системы координат и некоторые вспомогательные системы X1Y1Z1 X2Y2Z2 X3Y3Z3 которые используются для удобства базирования заготовки на различных технологических операциях [8].
Рисунок 2.14 – Совмещение 3D-модели заготовки с теоретической 3D-моделью винта
7Особенности привязки виртуальных координат разметки к физическим (реальным) координатам заготовки
На заготовке которая установлена на разметочной плите (операция № 020) с помощью СФГС производятся замеры координат точек определяющих положение баз заготовки с использованием калибровочной линейки и щупа. Щуп устанавливается вблизи необходимой измеренной точки производится стереосъёмка и определяется отклонение между реально измеренной и виртуальной координатой. Далее по знаку и величине отклонения перемещают щуп выполняют повторный замер. Замеры выполняются до тех пор пока отклонения не будет превышать заданного допуска.
Рисунок 2.15 Результат вписывания теоретической модели лопасти в заготовку:
) Основная система координат лопасти XYZ (Z – ось винта Y ось лопасти X ось перпендикулярная плоскости ZY) в основной системе XYZ определяются координаты всех кодированных меток сохраняемых до получения физических баз L – след плоскости YZ на поверхности заготовки; 2) Для удобства базирования на технологических операциях определяются вспомогательные системы координат (координатные плоскости базовых поверхностей): X1Y1Z1 координатная система кормового торца фланца лопасти; X2Y2Z2 X3Y3Z3 координатные системы соответственно правого и левого скосов фланца лопасти
После чего в точке установке острия щупа производится углубление и по центру углубления (если это необходимо) устанавливается кодированная мишень или самоклеящийся маркер.
Аналогично производится привязка всех необходимых координат к реальным (физическим) координатам для всех заготовок. При этом число «отмеченных» опорных точек на поверхности заготовки должно быть достаточным для удобного базирования заготовки на станках при выполнении последующих технологических операций обработки лопасти.
По полученным физическим координатам опорных точек заготовки жёстко связанными с теоретическими координатами лопасти формируется разметочный паспорт по принятой форме который передаётся в бюро технического контроля. Таким образом полученные физические координаты опорных точек на всех заготовках лопастей должны сохраняться и периодически восстанавливаться по всему технологическому процессу [8].
8Особенности установки и ориентации на станке заготовки гребного винта на различных этапах изготовления
Точность размещения заготовки которая необходима для проведения технологических операций должна быть от 002 мм до 05 мм. Такую точность можно достичь с помощью СФГМС а также с помощью упрощения процесса определение станка и информацию (выводящую) об отклонениях.
Далее рассмотрим позиционирование заготовки ГВ на различных этапах изготовления:
)Получение трехмерной объемной модели заготовки. Операция 020 – первичная разметка заготовки;
Заготовка жестко устанавливается на разметочную плиту на деревянные брусья так чтобы перо лопасти стояло вертикально и просматривалась по нагнетательной и засасывающей поверхности (рисунок 2.16).
Рисунок 2.16 – Позиционирование лопасти при первой съемке. Вид на нагнетательную поверхность
)060 – Разметочно-расточная операция на расточном станке FCW 150 (W 200Н) после установки детали на планшайбу. 090 – Расточная операция. Последовательность выполнения описывается ниже;
Необходимо сделать так чтобы лопасть на рабочем столе станка была кормовым торцом фланца и ориентируясь так чтобы горизонтальная ось заготовки совпадала с осью шпинделя станка (рисунок 2.17). Установку лопасти можно произвести с помощью УЦИ станка и СФГМ контроля.
После установки боковая поверхность скоса фланца должна быть перпендикулярна плоскости стола с точностью до 002 мм а горизонтальная ось заготовки совпадать с осью шпинделя с точностью не хуже 05 мм.
Рисунок 2.17 – Позиционирование заготовки на станке FCW150(W200M)
)Разметка и установка лопасти на фрезерном станке TDP-70110. Разметочная операция 125 после сборки фальшступицы выполняется на контрольно-измерительной плите; операция 130 – Отладочная фрезерно-программная.
Установка лопасти на станок производится (рисунок 2.18) необходимо выполнять в следующей последовательности:
)В центр планшайбы необходимо установить заготовку ГВ с фальшступицей;
)С помощью СФГМ контроля выполнить на станке центровку ГВ с фальшступицей;
)Установить на фальшступицу кронштейн на которые будет крепиться траверса с проектором PRO-SPOTA и измерительными камерами для исполнения контроля геометрии заготовки;
Рисунок 2.18 – Установка лопасти на фрезерном станке TDP-70110
)Установка лопастей со фальшступицей на фрезерном станке TDP-70110. Операция 180 – разметочная операция после окончательной фрезерно-программной обработки нагнетательной поверхности;
Позиционирование лопастей производится с фальшступицей на которой установлены две (четыре) лопасти ГВ так чтобы засасывающая поверхность была сверху. Центровка и установка лопасти производится по аналогии с пунктом 6.
)Установка лопасти на контрольно-измерительную плиту. Операция 275 – окончательная разметочно-контрольная операция выполняет обработку наплавленных участков и устранение всех дефектов;
Необходимо закрепить две лопасти на фальшступицу и установить нагнетательной поверхностью (кормовым торцом) вверх на контрольно-измерительную плиту. Для установки камер СФГМС закрепится на фальшступицу кронштейн.
)На разметочную плиту установить лопасти для нахождения трехмерной модели.
На разметочную плиту на деревянные брусья устанавливается лопасть в вертикальное положение так чтобы выполнить необходимую съемку с двух сторон.
9Формирование технического паспорта на гребной винт и сравнение 3D-модели «Как спроектировано» с 3D-моделью «Как построено»
Конструктивный паспорт на ГВ должен содержать в себе:
)Общий вид лопасти ГВ со стороны нагнетательной и засасывающей поверхности (используются фотоснимки стереопар);
)Подробную цифровую 3D-модель лопасти вида «Как построено»;
)Подробную теоретическую исходную цифровую 3D-модель лопасти вида «Как спроектировано»;
)Технический паспорт содержащий необходимые параметры лопасти аналогичные штатной контрольной операции № 275 (радиус лопасти длины сечений высоты точек замера относительно кормового торца фланца лопасти толщины и катеты сечений откидку лопасти на сечениях и т.д.).
Ниже рассмотрим сравнение 3D-модели «Как спроектировано» с 3D моделью «Как построено».
После выполнения технологического процесса изготовления ГВ необходимо создать более подробную полную 3D-модель. Эту модель сравнить с исходной теоретической моделью. Сравнение моделей выполняется аналогично вписыванию теоретической модели в модель заготовки. По результатам вписывания определяют недочеты отклонения и качество выполнения процесса так же определяют брак и при возможности исправляют.
ЭКСПЕРИМЕНТАЛЬНЫЕ ИССЛЕДОВАНИЯ КОНТРОЛЯ ГЕОМЕТРИИ ГРЕБНЫХ ВИНТОВ С ИСПОЛЬЗОВАНИЕМ СТЕРЕОФТОГРАММЕТРИЧЕСКОЙ СИСТЕМЫ V-STARS
1Особенности подготовки заготовок гребного винта к контролю геометрии с использованием V-STARS
Заготовки ГВ и их элементы поступают в цех в виде отливок с соответствующей конфигурацией. При этом для получения 3D-модели в каждой такой заготовке требуется выполнить целый ряд подготовительных работ (смотри приложение А):
)Дробеметная очистка поверхности заготовки;
)Предварительная подготовка контролируемой поверхности:
1)При контроле малогабаритных заготовок (диаметр не более 1 – 2 м) измерения выполняются с помощью ручного щупа. При этом делается предварительная разметка основных сечений в которых нужно получить соответствующее число координат (точек) (рисунке 3.1).
Рисунок 3.1 – Подготовка лопасти к измерениям: а) 3-х лопастной винт;
б) 4-х лопастной винт
2)При измерениях крупногабаритных заготовок (диаметр более 2 м) измерения выполняются для получения координат большого числа точек целесообразно получать с помощью PRO-SPOT с помощью которого на контролируемую поверхность отмечается до 100000 светящихся точек. И в каждой из этих точек определяются координаты. В этом случае для получения хорошего качества проецируемых точек необходимо на всю контролируемую поверхность нанести однородный раствор (рисунок 3.2).
Рисунок 3.2 – Подготовка к измерениям: а) отдельная лопасть винта; б) винт lk-7
)После выполнения подготовительных работ заготовка устанавливается на КИП так чтобы был свободный доступ для установки камер (рисунок 3.3).
Рисунок 3.3 – Установка к подготовленной к измерениям лопасти на КИП
2Варианты создания драйвер-файла перед измерением геометрии элементов гребного винта
Перед измерениями необходимо в обязательном порядке выполнить юстировку самой системы V-STARS то есть знать точные параметры системы. Это довольно сложная задача. В системе V-STARS эта задача решается косвенно путем предварительного создания драйвер-файла по которому и происходит масштабирование всего измерительного пространства. То есть по драйвер-файлу определяются трехмерные координаты любой точки пространства охваченного этим драйвер-файлом.
При этом в это пространство поместить контролируемую деталь с помощью СФГМС можно легко определить любые координаты этой детали. Либо с помощью ручного щупа либо в точках спроецированных на контролируемую поверхность. И тем самым получить исходное облако точек для заготовки ГВ.
Принцип масштабирования основан на том что объем измеренного пространства помещается определенное число кодированных мишеней и калибровочная линейка. При этом координаты на мишенях и масштабной линейке известны с большой точностью. Поэтому получив снимки можно перейти от масштабов снимков к масштабам измерительного пространства. Этот драйвер-файл запоминается в программе V-STARS и в дальнейшем перед каждом измерением и обработкой результатов этих измерений используется для пересчетов от координат снимков к реальным координатам.
Получить исходный драйвер-файл можно получить несколькими способами.
2.1 Особенности получения стационарного драйвер-файла
Особенности получения стационарного драйвер-файла поясняется на рисунке 3.4. В этом случае на специальных стойках установленных так чтобы они охватывали все измерительное пространство для этих целей достаточно трех вертикальных стояк. На каждой такой стойке устанавливается соответствующее число мишеней. Кроме этого в это же пространство помещается калибровочная линейка.
Рисунок 3.4 – Получение стационарного драйвер-файла
Затем с помощью одной камеры с различных ракурсов производится 25-30 снимков (рисунок 3.5). Где видны координаты всех мишеней и координаты измерительной линейки.
Рисунок 3.5 – Результат обработки одного стереоснимка стационарного драйвер-файла
При этом на каждом снимке должно быть 3-5 кодированных мишеней. Для выполнения сшивки различных снимков.
После получения снимков производится обработка (рисунок 3.6) и в результате обработке получается исходный драйвер-файл в виде достоверных известных трехмерных координат всех кодированных мишеней. Пример стационарного драйвер-файла изображен на рисунке 3.7.
Рисунок 3.6 – Обработка стереоснимков
Рисунок 3.7 – Стационарный драйвер-файл
Далее контролируемая деталь помещается в измерительное пространство и с помощью СФГМС производится измерения координат этой поверхности.
Полученный таким образом стационарный драйвер-файл сохраняется в программе V-STARS и может многократно использоваться при различных измерений выполняемые в измерительном пространстве. Однако следует отметить что если расположенные кодированные мишени сдвинут то необходимо заново создавать драйвер-файл.
2.2Особенности получения временного драйвер-файла
Для получения временного драйвер-файла необходимо:
В объем расположения контролируемой детали разложить кодированные мишени как показано на рисунке 3.8. Причем кодированные мишени можно располагать как на основание так и на лопастях.
Рисунок 3.8 – Подготовка к снятию временного драйвер-файла перед измерениями: а) 3-х лопастной ГВ; б) 4-х лопастной ГВ
Как видно из этих рисунков распределение кодированных мишеней должно быть равномерным. Эти мишени должны располагаться так чтобы на каждой паре снимков было видно не менее 4-5 кодированных мишеней.
Перед получением драйвер-файла помимо кодированных мишеней нужно установить масштабную линейку. Затем уже с помощью СФГМС необходимо снять 25-30 снимков обработать их и получить окончательный вариант драйвер-файла (рисунок 3.9).
Рисунок 3.9 – Отображение драйвер-файла с системой координат в программе V-STARS
После получения драйвер-файла производятся измерения облака точек контролируемой поверхности. При этом расчете используются координаты полученного драйвер-файла.
После выполнения всех замеров кодированных мишени удаляются. При этом ранее полученный драйвер-файл использовать нельзя.
3Методика получения исходной цифровой 3D-модели заготовки гребного винта
Технологический процесс измерения цифровой 3D-модели заготовок рассмотрим на примере получения трех заготовок цельнолитых ГВ с различной конфигурацией и для крупногабаритных винтов на примере получения 3D-модели одной лопасти.
3.1Особенности получения цифровой 3D-модели 3-х лопастного гребного винта с 08 м
Технологический процесс измерения для получения 3D-модели происходит в следующем порядке (смотри приложение Д):
)Предварительно размеченный винт устанавливается и соответствующим образом ориентируется в объем масштабирования пространства (смотри пункты 3.1 и 3.2);
)С помощью специального измерительного щупа перед началом измерений оценивается расположение СФГМС (рисунок 3.10). При этом ручной щуп устанавливается в одну из точек ГВ и производится стереосъемка. По результатам обработки стереопары оценивается в процентах степень перекрытия контролируемого пространства. Если перекрытие превышает 25-50% с разбросом по камерам не более 20%. При этом на каждом снимке стереопары должны присутствовать не менее 4-5 одинаковых кодированных мишеней. Т.к. по координаты этих мишеней и осуществляется привязка к исходному драйвер-файлу а следовательно осуществляется привязка реальных координат ГВ к трехмерных координатам измерительного пространства;
Рисунок 3.10 – Измерения пространственных координат ГВ с помощью ручного щупа
)Включается режим точечного контроля с помощью ручного щупа и производятся измерения координат во всех ранее отмеченных точках сечения. Для чего щуп устанавливается в начальную точку заданного сечения и с помощью дистанционного пульта управления дает команду на стереосъемку. Затем щуп перемещается в другую точку сечения и вновь дается команда и т.д. производятся измерения в 20-30 точках каждого сечения.
Измерения производятся во всех отмеченных сечениях лопасти. При этом в каждом сечении необходимо измерить не менее 20-25 точек. После завершения измерений результаты обрабатываются и представляются в виде координат в каждом отмеченной лопасти (рисунок 3.11). Аналогично снимаются координаты кромки первой лопасти при этом щуп вертикально устанавливается по кромке и делаются стереоснимки так же выполняются измерения координат точки торца лопасти. Измеренные таким образом точки на кромке и торце показано на рисунке 3.12.
Рисунок 3.11 – Координаты в сечениях лопасти
Рисунок 3.12 – Координаты: а) в сечениях лопасти измеренного ручным щупом ;
б) кромки и торца лопасти №1
)Аналогично снимаются координаты поверхности и кромок в сечениях для лопастей №2 и №3;
)Переворачивают винт на 180° (кантуют) и производятся измерения точек поверхности во всех лопастях с другой стороны;
)С помощью программы V-STARS объединяют все ранее полученные файлы и строят полную цифровую 3D-модель заготовки. На рисунке 3.13 показан вид координаты кромок и торца винта и 3D-модель заготовки.
Рисунок 3.13 – Исходная 3D-модель заготовки 3-х лопастного ГВ: а) координаты кромки и торца; б) 3D-модель заготовки
3.2Особенности получения цифровой 3D-модели 4х-лопастного малого гребного винта с 12 м
Получение исходной 3D-модели заготовки 4х-лопастного ГВ аналогично пункту 3.3.1 за исключением того что в качестве исходного драйвер-файла используется стационарный драйвер-файл полученный с помощью трех вертикальных стояк на которых укрепляется соответствующее число кодированных мишеней (смотри пункт 3.2.1). Последовательность выполнения контрольно-измерительной операции для 4-х лопастного винта показано на рисунке 3.14.
Рисунок 3.14 – Исходная 3D-модель заготовки 4х-лопастного ГВ: а) координаты кромки и лопасти; б) 3D-модель заготовки
3.3Особенности получения цифровой 3D-модели 4-х лопастного гребного винта lk-7 с 35 м
Получение исходной 3D-модели заготовки 4-х лопастного ГВ аналогично пункту 3.3.1 с использованием временного драйвер-файла полученного перед измерениями (смотри пункт 3.2.2). Основные этапы измерения показаны на рисунках 3.15 и 3.16.
Рисунок 3.15 – Облако измеренных точек первой лопасти 4-х лопастного ГВ б) координаты засасывающей поверхности 1-ой лопасти
Рисунок 3.16 – Исходная 3D-модель заготовки ГВ lk-7
3.4Особенности получения цифровой 3D-модели одной лопасти для крупногабаритных гребных винтов
Технология и последовательность получения цифровой 3D-модели отдельных лопастей в целом аналогично пунктам 3.3.1 и 3.3.2 в зависимости от того как формируется исходный драйвер-файл. Последовательно выполнения измерений аналогично пункту 3.3.1 т.е. производится предварительная разметка произвольных сечений. Лопасть устанавливается в вертикальное положение так чтобы был свободный доступ для стереоизмерений с той и другой стороны. Затем снимается драйвер-файл после чего с помощью ручного щупа выполняется большое число точек измерений с обеих сторон лопастей а так же по кромке и по торцам лопасти.
Следует отметить что если у полученного драйвер-файла при съемке с одной стороны и с обратной стороны нет видимых 4-5 одинаковых кодированных мишеней то необходимо иметь два различных драйвер-файла. Эти драйвер-файлы с одной и с дрогой стороны снимаются автономно.
Однако для получения общего драйвер-файла и масштабирования всего измерительного объема необходимо иметь не менее 3-4 точек обеспечивающие сшивку драйвер-файлов с одной и с дрогой стороны. С этой целью на лопасти ГВ наносятся (кернятся) на кромки винта 3-4 контрольные точки которые измеряются с одной стороны. Затем координаты этих точек считаются одинаковыми.
Особенности получения цифровой 3D-модели одной лопасти поясняется на рисунках 3.17 и 3.18 где на рисунке 3.17 (а) показаны координаты измерений с нагнетательной стороны на поверхности лопасти торце и кромке 3.17 (б) координаты измерений с засасывающей поверхности лопасти.
Рисунок 3.17 – Координаты измеренных лопастей: а) нагнетательная поверхность лопасти на кромках и торце; б) засасывающая поверхность лопасти
Рисунок 3.18 – Исходная 3D-модель лопасти ГВ AZIPOD построенная с помощью ручного щупа
4Особенности вписывания теоретической 3D-модели и определение припусков
4.1Теоретические предпосылки вписывания
Распределение припусков так называемое автоматическое «вписывание» изделия в заготовку при механической обработке сложнопрофильных деталей с точечно-задаваемыми поверхностями в частности ГВ [8].
Разнообразие геометрических форм и размеров ГВ отсутствие каких-либо закономерностей в профилях отдельных сечений и методики расчётов и проектирования делает невозможным применение общепринятых способов базирования. Универсальное решение данной задачи подходящее ко всем типам и размерам ГВ может быть получено при решении математической задачи нахождения наилучшего способа вписывания теоретической исходной формы ГВ в имеющуюся заготовку. Это особенно актуально для такого мелкосерийного а зачастую и штучного производства как изготовление ГВ.
Совокупность трёхмерных координат точек принадлежащих некоторой поверхности с заданной степенью точности определяет 3D-модель рассматриваемого объекта. Однако информация о геометрии объекта выражена в неявной форме. Для того чтобы данный набор точек можно было сравнить с имеющейся теоретической 3D-моделью необходимо преобразовать совокупность точек в единую математическую модель аналогичную теоретической (эталонной).
В случае когда расположение контрольных точек заранее неизвестно а задана только плотность их распределения стандартные методы воссоздания поверхностей оказываются неэффективными. Графические методы при присущей им простоте и наглядности не позволяют провести качественного анализа взаимного расположения моделей. Аппроксимация при помощи сплайнов выдаёт в качестве результатов кусочно-линейные функции разбивающие поверхность объекта на множество подплоскостей пересекающихся в точках координаты которых заданы измерениями.
Сравнивать подобную «лоскутную» модель с эталонной возможно лишь при условии что сам эталон будет представлять собой множество подплоскостей причём точки разбиения подплоскостей эталона и полученной модели должны совпадать. Но подобное невозможно поскольку используемый метод получения координат точек поверхности позволяет предварительно определить плотность контрольных точек но не их расположение.
При сопоставлении эталонной модели и полученного набора точек мы сталкиваемся с проблемой несовпадения систем координат эталонной 3D-модели и измеренной 3D-моделью заготовки. Кроме того для анализа расхождения геометрических параметров необходимо решить задачу поиска ближайших точек в трёхмерном пространстве.
Для того чтобы полученную трёхмерную модель заготовки можно было сравнить с эталонной формой готового изделия то при её воссоздании необходимо использовать совокупность параметров общих как для имеющейся эталонной модели так и для получаемой трёхмерной формы заготовки. Эти параметры необходимы для приведения двух трёхмерных моделей к единой метрической системе координат.
Рассмотрим следующую задачу: массив точек поверхности заготовки задан их трёхмерными координатами. Требуется определить трёхмерную форму заготовки сравнить её с эталонной и выработать рекомендации по изменению положения заготовки с целью наилучшего вписывания.
Допустим что точкой которая будет основой воссоздания трёхмерной формы объекта то есть точкой начала координат будет геометрическое место центра точек расположенных на поверхности объекта. Тогда координаты центра рассчитываются как:
а координаты каждой точки изменяются на величины:
При этом полученная система координат по-прежнему является ортогональной поскольку смещение центра системы (т.е. параллельный перенос) является допустимой операцией. Направления осей системы также совпадают с исходными.
Для каждой из имеющихся точек найдём вектор из центра новой системы координат к этой точке. Переходя к полярной системе координат получаем угловые параметры и длину радиус-вектора. За положительное направление отсчёта угла принимаем направление против часовой стрелки.
В результате получается математическая модель измеренной заготовки где положение каждой точки поверхности описано тремя параметрами: углом по отношению к плоскости Ох углом по отношению к плоскости Оу и расстоянием r от геометрического центра точек поверхности заготовки.
Данная модель ориентирована произвольно – направления осей не привязаны к особенностям геометрии измеренного объекта. Однако для адекватного сопоставления модели измеренного объекта и эталонной модели необходима единообразная ориентация осей.
Выберем в качестве характерного признака определяющего ориентацию оси Оу осевую одной из лопастей винта. Номер выбранной лопасти не имеет значения так как винт – симметричная фигура. Тогда ось Ох будет направлена вдоль оси ступицы винта а ось Оz – перпендикулярно Ох и Оу.
Пусть действительное направление оси Оу задаётся специально проставленной реперной точкой (присвоим ей индекс k) местоположение которой определяется пересечением линии кромки лопасти с осевой лопасти. Тогда для данной точки
является углом поворота по оси Оу. Такой поворот будет производится в горизонтальной плоскости следовательно направление вертикальной оси Ох не изменится а ось Оz должна быть смещена в положение перпендикулярное новому положению Оу.
Как видно из рисунка 3.19 для сохранения перпендикулярности осей Оу Оz последняя ось также должна быть повёрнута на угол однако поскольку угол γ вектора данной точки с осью Оz является избыточной информацией уже содержащейся в значениях φ и перпендикулярности осей данные расчёты нет необходимости производить и приведение математической модели к правильной ориентации осуществляется при помощи простой формулы:
Рисунок 3.19 Изменение направления осей Ох Oz
Осуществим обратный переход от полярной к прямоугольной системе координат:
Данные для расчёта эталонной модели берутся из выходной документации на винт. Как правило выходному контролю подлежат такие точки ГВ как точки осевой лопасти точки линии наибольших толщин и 10-15 промежуточных точек на сечениях 01; 03; 05; 07 и 095 радиуса винта.
По имеющимся точкам рассчитываются координаты центра точек эталонного винта:
Переносим центр координат точечно-заданной фигуры в рассчитанный центр точек:
Перейдём к полярной системе координат присвоив каждой из точек фигуры значения и r [8]:
Полученное значение угла для точки пересечения линии кромки лопасти с осевой лопасти позволяет найти значение угла поворота по оси Оу
Тогда поворот оси Оу ориентирующий систему координат модели эталона рассчитывается по формуле:
В результате получается математическая модель эталона винта где положение каждой точки поверхности описано тремя параметрами: углом по отношению к плоскости Ох углом по отношению к плоскости Оу и расстоянием от геометрического места центра точек поверхности эталона r.
Полученная математическая модель заготовки сравнивается с эталонной моделью также представляющей собой совокупность векторов из центра точек фигуры.
Совмещением центров точек измеренной фигуры и эталонной модели накладываются друг на друга два массива точек (рисунок 3.20).
Рисунок 3.20 Совмещение измеренной и эталонной моделей
4.2Управление технологическим процессом распределения припусков
Задача распределения припуска на последующую обработку крупногабаритных сложнопрофильных изделий характерна для таких областей машиностроения как судостроение авиастроение производство турбин и т.п. т.е. для тех отраслей где от геометрической формы детали точности обработки и шероховатости поверхности зависят ходовые и акустические качества а также надёжность и долговечность работы изделия в целом (смотри приложение Е).
При изготовлении дорогостоящих деталей очень важно правильно распределить припуск на первой черновой операции когда решается вопрос о пригодности заготовки и целесообразности её последующей обработки. Не менее важным является и дальнейшее межоперационное распределение припусков.
Применение современных бесконтактных способов определения координат облака точек поверхности заготовки позволяет получить трёхмерные 3D-модели заготовки. При этом использование специализированных математических методик сравнения измеренной и эталонной моделей [16] позволяет рассчитать значения имеющегося припуска в каждой из контрольных точек.
Значения абсолютных и относительных величин имеющегося припуска являются входными данными для алгоритма распределения припуска. В первую очередь определяется количество и взаимное расположение точек (область) в которых имеющееся количество припуска меньше чем требуемое значение. Если распределение таких точек по поверхности заготовки таково что любое перемещение заготовки уменьшит и без того критически малое значение припуска в какой-нибудь из вышеупомянутых точек заготовка подлежит выбраковке либо предварительной наплавки металла в соответствующих областях.
Если же для всех имеющихся контрольных точек значение припуска не менее требуемого либо при наличии точек где припуск меньше требуемого значения но существует допустимое направление перемещения заготовки при котором увеличивается количество припуска в критических точках то рассчитывается вектор перемещения заготовки. При этом рациональное направление вектора перемещения – от точки с максимальным значением припуска к точке с минимальным значением припуска. Корректировка производится с учётом значений припусков в точках где относительное значение припуска по абсолютной величине больше 05. При этом учитывается требуемое горизонтальное смещение винта определяемое координатами геометрического центра точек поверхности заготовки.
Поскольку распределение припуска это нелинейная задача имеющая множество вероятных реализаций то окончательное решение принимается группой квалифицированных специалистов или лицом принимающим решение.
Рассмотрим следующий случай взаимного расположения заготовки и эталонной модели винта (рисунок 3.21).
– математическая модель измеренной заготовки;2 – отступ на припуск;
– математическая модель эталона
Рисунок 3.21 Смещённое расположение заготовки относительно эталонной модели винта
При данной установке заготовки имеется ряд точек для которых величина имеющегося припуска меньше чем требуемое значение то есть j 0. Кроме того имеются точки для которых j = 0. Однако анализ расположения точек для которых значение имеющегося припуска значительно превосходит нормативное значение показывает что возможно перемещение заготовки при котором для всех эталонных точек значение имеющегося припуска будет не менее требуемого. В данном случае вектор перемещения строго горизонтален.
Рассмотрим другой случай взаимного расположения заготовки и эталонной модели винта представленный на рисунке 3.22.
Рисунок 3.22 Смещённое расположение заготовки относительно эталонной модели винта
Здесь взаимное расположение точек таково что перемещение модели заготовки с целью увеличения припуска в точках где j 0 повлечёт за собой недопустимое уменьшение припуска в тех точках где в настоящий момент j = 0. Следовательно невозможно задать такой вектор перемещения заготовки при котором во всех контрольных точках эталонной математической модели будет достаточное количество припуска. Заготовка подлежит выбраковке.
При распределении припусков на заготовке возможна и ситуация подобная изображённой на рисунке 3.23.
Рисунок 3.23 Неравномерное расположение заготовки относительно эталонной
Здесь для большинства точек заготовки значение припуска близко к требуемому значению за исключением некоторой области в которой имеется излишек металла. Возможно переместив заготовку распределить излишек припуска равномерно между всеми обрабатываемыми поверхностями. Однако с точки зрения уменьшения трудоёмкости обработки оптимальным является удаление излишка металла за одну операцию (вертикальная пунктирная черта).
Таким образом алгоритм распределения припуска может быть представлен блок-схемой изображённой на рисунке 3.24.
Рисунок 3.24 Блок-схема алгоритма анализа припусков
Рассмотрим алгоритм работы системы управления технологическим процессом распределения припуска на заготовках ГВ – АСУТП “Оптима” [8]. Основа данной системы – разработанная методика распределения припусков которая в свою очередь базируется на математическом алгоритме преобразования трёхмерных координат точек поверхности объекта в величины отклонений геометрической формы измеряемой заготовки от точечно-заданной формы поверхности готового изделия. Блок-схема алгоритма АСУТП приведена на рисунке 3.25.
Рисунок 3.25 Блок-схема алгоритма работы АСУТП
Работа АСУТП начинается с анализа документации на изготовляемый ГВ. Если винты данного типа производились ранее в базе данных АСУТП имеется эталонная модель готового винта. В противном случае первым шагом работы системы является расчёт математической модели эталонного винта данного типа.
После того как заготовка пройдёт дефектоскопию она размещается на рабочей поверхности станка. Производится первая контрольная операция определения пригодности заготовки по геометрическим параметрам. Если заготовка признана годной выбирается оптимальное распределение существующих припусков. Информация об имеющихся припусках поступает в систему управления станка с ЧПУ. В случае когда количество припуска велико он делится на черновую и чистовую обработки. Быстродействие работы АСУТП позволяет производить операции распределения припусков после каждой черновой обработки причём время производственного процесса увеличивается незначительно.
По завершению операции обработки после чистовой расточки производится межоперационный контроль. Он необходим для большинства операций обработки винта (за исключением шлифования).
По завершению всех операций обработки винта производится выходной контроль заполняется паспорт винта.
4.3Экспериментальные исследования использования стереофотограмметрической системы V-STARS
Как отмечалось выше операция вписывания теоретическая 3D-модель винта в 3D-модель заготовки является наиболее ответственной операцией от качества выполнения которой зависит дальнейшая трудоемкость и качество обработки заготовки на технологических операциях. Основной задачей вписывания является оптимальное распределение припусков по всей поверхности заготовки с учетом возможных явно выраженных дефектов литья заготовки. После операции вписывания и совмещения теоретичеких координат с координатами 3D-модели заготовки выполняется виртуальная разметка заготовки ГВ. При этом должны быть отмечены: центр заготовки; направление осей; плоскости проходящие через оси каждой лопасти;горизонт проходящий через центр винта; основные радиальные сечения внутренний и внешний диаметр ступицы; подрезы торца лопасти; наиболее характерные точки облегчающие позиционирование заготовок на станках и т.д.
По полученной «виртуальной» разметки делается реальная (физическая) разметка уже непосредственно на заготовке ГВ. Ниже рассматриваются отдельные результаты экспериментальных исследований выпоненых на нескольких заготовок различных ГВ исходные 3D-модели которых рассмотрены в пункте 3.3.
4.3.1Особенности вписывания и распределение припусков для 3-х лопастного винта с 08 м
Теоретическая 3D-модель 3-х лопастного винта показан на рисунке 3.26 (а) а исходная 3D-модель заготовки этого винта показана на рисунке 3.26 (б).
Рисунок 3.26 – Исходные данные для выполнения операции вписывания:
а) теоретическая 3D-модель 3-х лопастного винта; б) полное измеренное облако точек 3-х лопастного винта
Процесс вписывания осуществляется с помощью программы Analyser и выполняется в ледующей последовательности (смотри приложение Ж):
)Запускается программа вписывания в нее загружаются все необходимые исходные данные: теоретическая 3D-модель винта; основные элементы 3D-модели заготовки; необходимые параметры вписывания; допуски на припуски и т.д.;
)Указываются взаимосвязи элементов теоретической и экспериментальной 3D-модели а так же основные поверхности по которым должно осуществляться совмещение.
Как показали экспериментальные исследования если совмещение производится по всей поверхности включая гольтеры ступицы подрезы то программа вписывания пакета Analyser пытается равномерно распределить на гольтерах и ступицах по всей поверхности винта что в конечном итоге ухудшает качество вписывания. При указании конкретных поверхностей которые должны быть совмещены программой (например: поверхности лопастей). Качество вписывания и распределение припусков получается намного лучше.
)В ручную производится совмещение теоретической и экспериментальной 3D-модели так чтобы теоретическая 3D-модель была правильно соеринтирована и примерно совмещелась с экспериментальной 3D-моделью;
)После чего запускается программа вписывания пакета Analyser и в автоматическом режиме производится оптимизация отклонений по методу наименьших квадратов. При этом используется интерактивный метод последовательных приближений число итеракций может достигать до 50 шагов. Пример вписывания и распределение припусков 3-х лопастного винта показан на рисенке 3.27.
Рисунок 3.27 – Вписывание 3-х лопастного винта
)Окончательный протокол вписывания представляется в виде таблицы вписывания и картины распределения по всей поверхности винта которая показана на рисунке 3.28.
Рисунок 3.28 – Отклонения 3-х лопастного винта: а) полная картина отклонений по всех поверхности заготовки; б) увеличенный фрагмент отклонений на лопасти №1
)Полученная таким образом картина отклонений и принимается решение о пригодности загготовки в дальнейший технологический процесс. Если отклонения велики или принимают отрицательные значения то заготовка отправляется на выполнение наплавки дополнительного металла в областях с отрицательными наклонениями или заготовка вообще выбраковывается;
)Если распределение припусков удовлетворительное и принято решение о ее запуске в технологический процесс то производится «виртуальная» разметка заготовки. Процесс выполнения «виртуальной» разметки не рассматривается.
4.3.2Особенности вписывания и распределение припусков для 4-х лопастного винта с 12 м
В экспериментальную полученную 3D-модель заготовки производится аналогично пункту 3.4.3.1.
Исходные данные для операции вписывания представлены на рисунке 3.29. Результаты окончательного вписывания 4-х лопастного винта показано на рисунке 3.30. Из которого видно что винт хорошо вписывается в данную заготовку.
Рисунок 3.29 – Исходные данные для выполнения операции вписывания:
а) теоретическая 3D-модель 4-х лопастного винта 12 м; б) полное измеренное облако точек 4-х лопастного винта 12 м
Рисунок 3.30 – Вписывание 4-х лопастного винта 12 м
Протокол окончательного вписывания и распределение припусков показан на рисунке 3.31.
Рисунок 3.31 – Отклонения 4-х лопастного винта 12 м: а) полная картина отклонений по всех поверхности заготовки; б) увеличенный фрагмент отклонений на лопасти №1
Как видно из полученных экспериментальных данных процесс вписывания выполнен довольно качественно припуски распределены равномерно по всей поверхности винта и не превышают 2-3 мм.
4.3.3Особенности вписывания и распределение припусков для 4-х лопастного винта lk-7 с 35 м
Отдельные результаты вписывания представлены на рисунках 3.32 – 3.34. На рисунке 3.32 представлены исходные данные на рисунке 3.33 изображена окончательная картина после вписывания винта а на рисунке 3.34 проиллюстрирован протокол окончательного вписывания и увеличенный фрагмент отклонений на поверхности лопасти №1.
Рисунок 3.32 – Исходные данные для выполнения операции вписывания:
а) теоретическая 3D-модель 4-х лопастного винта б) полное измеренное облако точек 4-х лопастного винтаlk-7 35 м
Рисунок 3.33 – Вписывание 4-х лопастного винта lk-7 35 м
Рисунок 3.34 – Отклонения 4-х лопастного винта б) увеличенный фрагмент отклонений на лопасти №1
Анализируя характер распределения припусков и величины отклонений можно сделать вывод что припуски распределены равномерно на всех лопастях припуски достигают 10-15 мм что вполне приемлемо для крупногабаритных винтов. Наиболее распределение припусков наблюдается в областях на гольтелях и на ступицах винта. В этих областях максимальные отклонения достигают до 30 мм. Такая заготовка может быть запущена в технологический процесс.
4.3.4Особенности вписывания теоретической 3D-модели в экспериментальную 3D-модель отдельных лопастей на различных этапах изготовления
Экспериментальные исследования по вписыванию и распределению припусков на различных лопастях представлено на рисунке 3.35. На рисунке 3.36 изображен результат вписывания лопасти и распределение припусков а на рисунке 3.37 показан характер распределения и цветовая гамма отклонений с той и с другой стороны.
Рисунок 3.35 – Теоретическая 3D-модель одной лопасти винта
Рисунок 3.36 – Результат вписывания и распределения припусков на лопасти AZIPOD: а) вписывание одной лопасти винта; б) определение отклонений
Рисунок 3.37 – Характер распределения и цветовая гамма отклонений на лопасти AZIPOD: а) нагнетательная сторона; б) засасывающая сторона
Как видно из полученных результатов характер распределения припусков не совсем равномерный и припуска достигают значительных отклонений до 25-30 мм. Области наибольших отклонений выходящих за допустимые отклонения наблюдаются как на нагнетательной так и на засасывающей поверхности. При этом синим цветом отмечена область с отрицательными отклонениями. В указанной области необходимо выполнить дополнительную наплавку металла с тем чтобы ее можно было запустить в технологический процесс.
На рисунке 3.38 (а) представлена теоретическая 3D-модель лопасти ГВ «Снежный Барс» а на рисунке 3.38 (б) изображено облако точек этой же лопасти. На рисунке 3.39 представлено результат вписывания твердотельной лопасти ГВ в заготовку (отливку) лопасти. При этом максимальные отклонения достигают 11-12 мм указаны только на отдельных районах поверхности лопасти остальные отклонения не достигают 10 мм.
Рисунок 3.38 Исходные данные для выполнения операции вписывания:
а) теоретическая 3D-модель лопасти; б) полное измеренное облако точек лопасти
Рисунок 3.39 Результат вписывания твердотельной лопасти ГВ в заготовку лопасти
Анализ результатов вписывания показывает характер распределения припусков вполне приемлемый.
5Оценка точности определения трехмерных координат поверхности стерефотограмметрической системой V-STARS
В измерительной СФГМС V-STARS используются две высокоскоростные видеокамеры DINAMO. Основные характеристики и параметры которые представлены в пункте 2.2. Из этих параметров видно что заявленная точность измерения для одной камеры (режим ФГМ который используется для создания драйвер-файла) составляет 8 мкм + 8 мкмм для СФГМС (с двумя видеокамерами) заявленная точность 16 мкм + 16 мкмм на удаление.
Следовательно заявленная точность измерений СФГМС на удаление до 3-5 м будет составлять порядка 100 мкм = 01 мм.
В реальных условиях измерения на точность измерений могут влиять самые разнообразные факторы:
)Точность определения координат на плоских снимках и идентификация светоотражающих или светящихся точек. При этом параметры идентификации измеряемых точек могут изменяться в программе V-STARS путем измерения соответствующих установок (в настоящее время нами используются установки по рекомендации изготовителя);
)Расстояние и условия стереосъемки а так же процент перекрытия снимков стереопары которые так же можно менять путем соответствия ориентации камер;
)Качество создания драйвер-файла с помощью которого и производится масштабирование измерительного пространства;
)Качество подготовки контролируемой поверхности заготовки и т.д.
С учетом указанных факторов точность измерения трехмерных координат от заявленной точности.
В связи с этим проведены экспериментальные исследования по оценке точности измерений. Исследования проводились двумя способами:
)С использованием специально-контрольного калибра 515-727 (длиной 1 м);
)С использованием высокоточной измерительной системы токарно-копировального станка.
5.1Экспериментальная оценка точности с использованием специального контрольного калибра (Check Master Mitytoyo Япония) 830115
Все измерения проводились в режиме СФГМ ручным щупом Board 173-3 на КИП. При этом вначале получен стационарный драйвер-файл с помощью кодированных мишеней равномерно распределенных по поверхности КИП в области установки контрольного калибра. Драйвер-файл с установленным калибром в горизонтальном и вертикальном положениях показано на рисунке 3.40.
Рисунок 3.40 – Общий вид драйвер-файла с установленным калибром:
а) в вертикальном положение; б) в горизонтальном положение
Различная ориентация контрольного калибра позволяет оценить точность измерения по координате y и z соответственно.
Качество создания драйвер-файла и точность определения координат в измерительном пространстве изображено на рисунке 3.41 экранные формы результатов формирования драйвер-файла. Из этого рисунка видно что точность определения координат в измерительном пространстве по оси y не превышает 11 мкм по оси z 12 мкм.
Рисунок 3.41 – Экранные формы результатов формирования драйвер-файла:
а) процент перекрытия измерительного пространства видеокамер; б) основные параметры драйвер-файла и точность определения координат в измерительном пространстве
После получения драйвер-файла в измерительное пространство помещался горизонтально контрольный калибр 515-725 затем устанавливались две видеокамеры на расстоянии не более 2 м от калибра и последовательно выполнялись ручным щупом стереосъемки через каждые 100 мм контрольного калибра (на каждом зубе калибра). При этом щуп устанавливался на грань каждого зубца и давалась команда на измерение. Каждая точка изменялась только один раз. Результаты измерений представлены в таблице 3.1 где указаны расстояния между каждым зубом калибра номинальные расстояния между зубьями калибра и отклонения измерения. Из таблицы 3.1 видно y что средняя погрешность измерений не превышает 18 мкм.
Таблица 3.1 – Каждая точка измерена 1 раз измеряемый калибр параллельно
Имена измеренных точек
Расстояния между измеренными точками мм
Номинальные расстояния между зубьями калибра мм
Отклонения (погрешность) мм
Продолжение таблицы 3.1 – Каждая точка измерена 1 раз измеряемый калибр параллельно
Усредненное значение
Аналогично проводились разовые измерения при вертикальной установке калибра. Результаты измерений представлены в таблице 3.2. Из которой видно что средняя погрешность вертикальной оси z более существенна и составляет 237 мкм.
Таблица 3.2 – Каждая точка измерена 1 раз измеряемый калибр перпендикулярно
Продолжение таблицы 3.2 – Каждая точка измерена 1 раз измеряемый калибр перпендикулярно
Аналогичные замеры усредненной погрешности и выполнялись путем десятикратного измерения в каждой точке. Полученные результаты по каждой точке усреднялись и представлены в таблицах 3.3 и 3.4. Из таблицы 3.3 видно что усредненная погрешность при десятикратных замерах в каждой точке составляет 21 мкм. Аналогично усредненная погрешность по составляет 19 мкм.
Таблица 3.3 – Каждая точка измерена 10 раз и ее координаты усреднены (Average) измеряемый калибр параллельно
Таблица 3.4 – Каждая точка измерена 10 раз и ее координаты осреднены (Average) измеряемый калибр перпендикулярно
Анализ полученных результатов позволяет сделать вывод что многократные замеры выполненные в одной и той же точке дают меньшую погрешность не превышающую 20-30 мкм что соответствует заявленной точности. Такой точности вполне достаточно для контроля геометрии ГВ на различных этапах их изготовления.
РАСЧЕТ ЗАТРАТ НА ВНЕДРЕНИЕ СТЕРЕОФОГРАММЕТРИЧЕСКОЙ СИСТЕМЫ V-STARS В ТЕХНОЛОГИЧЕСКОМ ПРОИЗВОДСТВЕ
В данном разделе необходимо рассчитать затраты на внедрение новой технологии в производство разработки ГВ на закупку нужного оборудования.
1Затрат на внедрение бесконтактного контроля геометрии гребных винтов
На разработку цифровой системы управления представляющая себестоимость использованных в технологическом процессе разработки покупных комплектующих материалов оплату труда сотрудников и др. Затраты на разработку определяются по формуле (4.1).
где – стоимость материалов руб.;
– основная заработная плата сотрудников технологического процесса на изготовление ГВ с учетом введения новой технологии руб.;
– дополнительная заработная плата сотрудников технологического процесса на изготовление ГВ с учетом введения новой технологии руб.;
– социальные отчисления руб.;
– накладные расходы руб.
2Расчет стоимости оборудования
Затраты включают стоимость необходимого оборудования на покупные комплектующие изделия представлены в таблицах 4.1 и 4.2.
Таблица 4.1 – Затраты на покупку основного оборудования
Наименование элемента
Цена за 1 штуку тыс. руб.
Комплект из двух камер Nikon D2X
Ноутбук с процессором Intel i5i7 2ого поколения с частотой ЦП не менее 2.7 ГГц
Программное обеспечение V-STARS включающее в себя модуль Graphical Solid Geometry Analys Package.
Комплект треног для камер DYNAMO.
Линейка масштабная Scale Bar 2м.
PRO-SPOTA проектор включая калиброванную решетку на 22500 точек.
Тренога для проектора PRO-SPOTA с поворотной головкой и кронштейном для 2х камер.
Набор щупов (калибровочная пластина 4 ручных щупа и кейс).
Таблица 4.2 – Затраты на покупку вспомогательного оборудования
Набор кодированных мишеней с 6 мм маркерами на магнитной основе (1-48) 48МСТ6.
Набор кодированных мишеней с 6 мм маркерами на магнитной основе (49-96) 48МСТ6.
Набор кодированных мишеней с 12 мм маркерами на магнитной основе (1-48) 48МСТ12.
Набор кодированных мишеней с 12 мм маркерами на магнитной основе (49-96) 48МСТ12.
Набор кодированных мишеней с 12 мм маркерами на магнитной основе (97-120) 24МСТ12.
Рулон самоклеющихся маркеров 45 метров TT6
Продолжение таблицы 4.2 – Затраты на покупку вспомогательного оборудования
Лист самоклеющихся 6 мм маркеров с метками для теодолита ITT6
Лист самоклеющихся 12 мм маркеров с метками для теодолита ITT12
Набор специальных магнитных мишеней «Центр окружности» диаметр 2-9мм
Набор специальных магнитных мишеней «Центр окружности» диаметр 8-14мм
Набор специальных магнитных мишеней «Угол» с 6 мм маркерами. TCR-6MM
Набор специальных магнитных мишеней «Цилиндр» с 6 мм маркерами. TIDM-6MM
3Расчет заработной платы сотрудников
В заработную плату включаются выплаты за выполненную работу в соответствии с тарифными ставками и окладами. В общем виде заработная плата сотрудников рассчитывается по формуле (4.3).
n – количество категорий сотрудников;
– трудоемкость проектных работ выполненных сотрудником час;
– почасовая тарифная ставка сотрудника руб.час.
В данной разработке принимали участие сотрудники двух категорий:
)Дипломный руководитель проекта;
Трудоемкость проектных работ выполняемых сотрудниками различных категорий определяется на каждом этапе разработки и по разработке в целом.
Суммарная трудоемкость работ инженера (студента) – 450 часов дипломного руководителя – 40 часов.
Почасовая тарифная ставка дипломного руководителя и студента (инженера) с учетом льгот крайнего севера:
где – месячный оклад разработчика -й категории руб.;
F - месячный фонд времени работы разработчика час.
Примем месячный фонд времени работы разработчика F равным 168 часам а месячные оклады разработчиков равными:
Таблица 4.3 – Расчет заработной платы сотрудников
Предпроектное формирование требований
Разработка технологической инструкции
Освоение принципов работы ФГМС
Построение 3D-моделей по чертежам
Написание текста и графический ввод
По результатам расчетов заработная плата сотрудников
4Расчет дополнительной заработной платы сотрудников
Дополнительной заработная плата рассчитывается по формуле (4.5).
5Расчет на социальные отчисления
Социальные отчисления рассчитываются по формуле (4.6).
где – взносы на страхование в ПФ РФ%.
6Расчет накладных расходов
В накладные расходы включаются такие затраты как на электроэнергию и освещение отопление и водоснабжение и прочие общехозяйственные расходы. Накладные расходы рассчитываются по формуле (4.7).
где – коэффициент накладных расходов .
На основании рассчитанных затрат составим смету затрат на внедрение ФГС. Расчеты затрат на разработку представлены в таблицу 4.4.
Таблица 4.4 – Смета затрат на разработку цифровой системы управления
Наименование статьи затрат
Затраты на покупку основного оборудования
Затраты на покупку вспомогательного оборудования
Продолжение таблицы 4.4 – Смета затрат на разработку цифровой системы управления
Заработная плата сотрудников
Дополнительная заработная плата сотрудников
Отчисления на социальные нужды
ОХРАНА ТРУДА И ЗАЩИТА ОКРУЖАЮЩЕЙ СРЕДЫ
1Техника безопасности при работе на персональной электронно-вычислительной машине
Техника безопасности – совокупность правил и мер по обеспечению достойного уровня безопасности труда защиты от производственных травм повышает производительность труда в целом.
Сотрудники работающие на электронно-вычислительной технике должны иметь 1 или 2 классы по гигиеническому условию труда; тяжесть и напряженность не должны превышать допустимых норм.
Первый класс является самым оптимальным для трудоспособности человека. В нем создаются такие условия труда при котором сохраняются высокий уровень работы и здоровье сотрудника.
Второй класс является допустимым для трудоспособности. Во втором классе трудоспособность человека зависит от трудового процесса и уровня факторов среды которые по гигиеническим нормам для рабочих мест не превышает допустимых величин такой класс называется допустимым. Во время отдыха организм в силах восстановиться к началу работы следующего дня. Последствий на организм человека никаких нет. Такие условия труда являются безопасными.
Продолжительность непрерывной работы с электронно-вычислительными машинами без регламентированного перерыва не должна быть больше 2 часов. Во время регламентированных перерывов с целью снижения утомления зрительного аппарата и предотвращения развития познотонического утомления необходимо выполнять комплексы физических упражнений.
Содержание вредных веществ в воздухе рабочей зоны не должно превышать предельно допустимых концентраций используемых при технологических процессов оборудования вентиляции для контроля за качеством производственной среды и профилактики неблагоприятного воздействия на здоровье работающих.
1.1Требования безопасности при выполнении работ
Во время работы необходимо соблюдать следующие правила:
)В течение рабочего дня содержать в чистоте рабочее место;
)Не закрывать вентиляционные отверстия электронно-вычислительной машины;
)Соблюдать требования настоящей инструкции и правила эксплуатации оборудования;
)При работе с программой выбирать наиболее подходящие параметры такие как контрастность яркость цвет и размер символов фон экрана и др.;
)Соблюдать установленные режимом рабочего времени перерывы в работе выполнять необходимые физические упражнения.
Во время работы запрещается:
)Закрывать оборудование посторонними предметами;
)Скапливать бумаги на рабочем месте;
)Производить отключение питания при выполнении активной задачи;
)Допускать попадание влаги на поверхности устройств;
)Производить самостоятельно ремонт оборудования;
)Производить заправку или вскрытие картриджей лазерных принтеров и копировальной техники;
)Прикасаться к нагретым элементам техники;
)Работать со снятыми кожухами оборудования являющегося источниками лазерного и ультрафиолетового излучения;
)Располагаться при работе на расстоянии менее 50 см от экрана монитора.
Все необходимые гигиенические требования и организация работы устанавливаются с соответствием СанПиН 2.2.2.542-96 [14].
2Поражение электрическим током
Самая распространенная опасность для сотрудников электронно-вычислительных машин связана с питанием сети. Переменный ток с частотой 50 – 60 Гц является опасным для человека.
Факторы которые влияют на поражения электрическим током человека разнообразны. Это род тока (постоянный или переменный) и сила тока время проникновения его через организм индивидуальные свойства каждого организма человека.
Чтобы снизить риск поражением тока требуется следить за исправностью электропроводки и правилами эксплуатации электрооборудования.
Требуется следить за правилами эксплуатации электрооборудования и за ее исправностью.
Предельно допустимые нормы напряжений и токов указаны в ГОСТе 12.1.038-82 [5].
Поражение электрическим током вызывается тем что человек не может обнаружить наличие напряжения без специальных средств. Поэтому следует уделять особое внимание защите от поражения током. Электрический ток проходящий через клетки организма человека вызывает электрическое (электрический удар) термические (ожоги) и биологическое воздействие.
Биологическое воздействие раздражает и возбуждает живых клеток организма. При этом возникают судорожные сокращения мышц которые могут привести к нарушению или полному прекращению работы органов дыхания и кровообращения.
Ожоги. Они появляются при прохождении электрического тока более 1 А через организм человека. В человеческих тканях через которые проходит ток выделяется некоторое количество тепла которое пропорционально приложенному напряжению и току. При большом токе полученного тепла достаточно для того чтобы получить термический ожог (нагрев тканей до 65 градусов).
Электрический удар наблюдать при малых токов (до нескольких сотен мА). При такой маленькой мощности выделение тепловой энергии очень мало и ожога возникнуть не может. Воздействие тока на организм человека может произойти паралич пораженных органов. Например паралич дыхательных органов или мышц сердца приводит к смертельному исходу из-за поражения электрическим током. Поэтому чем быстрее будет оказана первая помощь человеку тем больше вероятность его спасти. Характер воздействия электрическим током на организм человека зависит от состояния нервной системы от массы человека от его физического развития и от всего организма в целом.
2.1Выделяются несколько пороговых значений тока
)Первый порог ощущения от 05 мА до 1.5 мА – минимальное значение тока которое может ощутить человек;
)Второй порог не отпускающего тока от 15 мА до 100мА – наименьшее значение тока при котором человек уже не может самостоятельно освободиться от токоведущих частей;
)Третий порог самый смертельный ток от 100 мА и более.
Оказание первой медицинской помощи:
Пострадавшего нужно немедленно освободить от действия электрического тока. Самым лучшим является быстрое его выключение.
При поражении человека током сопровождающимся потерей сознания пострадавшему необходимо начать делать искусственное дыхание.
При искусственном дыхании нужно положить пострадавшего на ровное место освободить от стесняющей одежды. Положить на спину под лопатки подкладывая валик из свернутой одежды.
Оказывающий помощь статановится с левой стороны подводит под затылок свою левую руку и как можно больше запрокидывает голову назад.
В результате этого подбородок пострадавшего оказывается приподнятым и рот открывается. Сделав 2—3 глубоких вдоха оказывающий помощь вдувает через платок или марлю воздух из своего рта в рот или нос пострадавшего. При вдувании через рот оказывающий помощь должен закрыть пальцами нос пострадавшего а при вдувании через нос — рот.
Частота искусственного дыхания не должна превышать 12— 16 раз в минуту.
Правильная поза позволяет сберечь перенапряжение мышц которая способствует лучшему кровообращению. Необходимо сидеть прямо опираясь о спинку стула спиной чтобы не было утомления.
Нужно найти такое положение головы при котором мышцы шеи меньше напрягаются. Угол наклона головы до 20°.
За работой электронно-вычислительной машины необходимо чтобы руки были расслаблены предплечья должны быть параллельно полу кисти рук должны расположены на уровне локтей запястья - на опорной планке. Следовательно пальцы получают свободу передвижения и наименьшую напряженность.
Не следует класть ногу на ногу и скрещивать ноги так как нарушается циркуляция крови из-за сдавливания сосудов. Необходимо сохранять угол 90° в тазобедренных области локтевых голеностопных и коленных суставов.
Нельзя высоко поднимать выгибать запястья кисти - это может обойтись вам онемения пальцев и болью в руках.
3.1Комплекс упражнений для глаз и мышц тела
)Расслабьтесь выпрямите спину; закрытыми глазами смотрите только прямо перед собой – глаза не напрягая расфокусируйте; голову держите не напрягаясь не напрягая тело выполняйте легкие наклоны головы: к груди назад; по очереди к левому и правому плечу.
)Не открывая глаз делайте ими вращательные движения по и против часовой стрелки вниз и вверх.
)Закройте глаза и помассируйте пальцами делая легкие круговые поглаживающие движения. Затем посидите с закрытыми глазами 10-15 с.
)Посмотрите вдаль 2-3 с. затем переведите взгляд на кончик носа замрите на 2-3 с. Повторить 6-8 раз.
)Вытягивайте и разжимайте пальцы так чтобы почувствовать напряжение. Расслабьте а затем не торопясь сожмите пальцы.
)Чтобы расслабить плечи к верхнюю часть спины сплетите пальцы рук за головой и сдвигайте лопатки до тех пор пока не ощутите напряжение в верхней части спины. Оставайтесь в таком положении 10 с. Расслабьтесь. Повторите 5-10 раз.
)Сплетите за спиной пальцы рук с обращенными внутрь ладонями. Медленно поднять и выпрямить руки. Оставайтесь в таком положении 10 с. Повторить 5-10 раз.
4Техника пожарной безопасности
При организации работ необходимо руководствоваться ГОСТом 12.1.004 ССБТ. Пожарная безопасность. Общие требования [3].
Противопожарная безопасность – комплекс технических и организационных мероприятий направленных на защиту безопасности людей предотвращения пожара и быстрого его тушения.
Все электрооборудование и электрические сети которые эксплуатируются на объекте при их неправильной эксплуатации может являться причиной возникновения пожара. Поэтому сеть и электрооборудование должны находиться в исправном техническом состоянии.
Чтобы избежать пожара необходимо чтобы переходное сопротивление соединения ответвление жил кабелей и проводов производилось при помощи сварки пайки или специальных зажимов. Электротехнические установки должны быть защищены от короткого замыкания предохранительными устройствами.
Запрещается эксплуатация и устройство временных электросетей за исключением электропроводок и иллюминационных установок а также электросетей которые питаются от места проведения строительно-монтажных и ремонтных работ.
Неисправности в электротехническом оборудовании электросетях вызывающие искрение или короткое замыкание должны немедленно устраняться. Если неисправность устранить невозможно то необходимо отключить электросеть во избежание пожара.
Электротехнические установки и подступы к ним не разрешается загромождать. Необходимо проверять герметичность и уплотнительные прокладки взрывозащищенного электрооборудования особенно в производственных помещениях в которых могут быть выделения взрывоопасных паров.
Ограждающие и защитные устройства приспособления (кожуха щиты и т.п.) на электротехническом оборудовании должны быть изготовлены из несгораемых материалов исключающих возможность искрообразования. Все оборудование и электродвигатели должны быть заземлены.
Пусковая аппаратура (кнопки включатели и пускатели) на оборудовании светотехнических установках должны быть выполнены в водонепроницаемом исполнении с электропроводами имеющими изоляцию.
5Защита окружающей среды
Предельно-допустимую концентрацию вредных веществ в ГОСТе 12.1.005-88 [4] она не должна превышать единицы. Общие санитарно-гигиенические требования к воздуху рабочей зоны.
Организационная техника включает в свой состав: материалы на основе поливинилхлорида пластик различных видов набор металлов - эти компоненты не являются вредными в процессе эксплуатации. Но когда изделие попадает на полигон и взаимодействует с внешними условиями становится ядом.
Поэтому вся организационная техника утилизируется в соответствие с утвержденной методикой Государственным комитетом РФ по телекоммуникациям от 19 октября 1999 г. Благодаря утилизации организационной техники вред окружающей среде сводятся к минимуму неперерабатываемых отходов.
Процесс переработки происходит в несколько этапов: первый этап – удаление всех опасных компонентов. В экранах и аккумуляторах устаревших моделей ноутбуков имеется ртуть которая опасна для организма.
Затем удаляются крупные пластиковые части. После разборки оставшиеся части отправляют в большой измельчитель-шредер и все дальнейшие операции автоматизированы.
Измельченные остатки компьютеров подвергаются сортировке. Сначала с помощью магнитов извлекаются железные части. Затем выделяют цветные металлы которых в ПК множество. Алюминий добывают из лома посредством электролиза. В сухом остатке получается смесь меди и пластика. Медь выделяют способом флотации – гранулы помещают в специальную жидкость медь остается на дне а пластик всплывает.
В настоящее время существует большинство организаций и фирм которые оказывают услуги по утилизации организационной техники что снижает степень влияния на окружающую среду.
При соблюдении требований по охране труда можно избежать плохое влияние на организм человека при работе с организационной техникой.
В процессе выполнения дипломного проектирования получены следующие основные результаты:
)Рассмотрены бесконтактные методы контроля геометрии сложнопрофильных конструкций и выбрана наиболее оптимальная СФГМС V-STARS которая позволяет автоматизировать отдельные трудоемкие операции при изготовлении ГВ;
)Рассмотрены теоретические основы и методика получения цифровых 3D-моделей заготовок элементов ГВ на различных этапах изготовления а так же особенностей вписывания теоретической 3D-модели в 3D-модель заготовки;
)Выполнен и систематизирован объем экспериментальных исследований использования СФГМС V-STARS на начальных этапах технологического процесса изготовления ГВ. В частности: получены данные по цельнолитым ГВ трех разновидностей а так же экспериментальные данные по получению цифровых 3D-моделей лопастей крупногабаритных ГВ;
)По полученным результатам исследования установлено что наиболее целесообразным является получение стационарного драйвер-файла непосредственно на местах обработки заготовок. Это существенно сокращает продолжительность цикла изготовления ГВ;
)Выполнен большой объем исследования по наиболее ответственной операции вписывания теоретической 3D-модели винта в экспериментальную 3D-модель заготовки. А так же рассмотрены вопросы распределения припусков заготовок с целью принятия решений о запуске их в технологический процесс;
)Проведена экспериментальная оценка погрешности измерений с помощью СФГМС V-STARS. При этом получено что средняя погрешность на удаление от конструкции 3-4 м не превышает 01 мм; 02 мм что удовлетворяет современным требованиям к точности контрольно-измерительных приборов.
СПИСОК ИСПОЛЬЗУЕМОЙ ЛИТЕРАТУРЫ
Амромин П.Д. Прикладная фотограмметрия. Новосибирск 1981г. – 85с.
Б.В.Анисимов В.Д. Курганов В.К. Злобин. Распознавание и цифровая обработка изображений. Москва «Высшая школа» 1983г – 150с.
ГОСТ 12.1.004-91. ССБТ. Пожарная безопасность. Общие требования 1991г. – 64с.
ГОСТ 12.1.005-88. ССБТ. Общие санитарно-гигиенические требования к воздуху санитарной зоны 1988г. – 48с.
ГОСТ 12.1.038-82 ССБТ. Электробезопасность. Предельно допустимые значения напряжений прикосновения и токов 1982г. – 75с.
ГОСТ 8054-81 Винты гребные металлические. Общие технические условия 1981г. – 12с.
ГОСТ Р 51833-2001 Государственный стандарт российской федерации .Фотограмметрия термины и определения 2002г. – 12с.
Информатизация технологического оборудования судового машиностроения[М.А. Бызова и др.]; под общ. ред. В.И.Малыгина Архангельск 2014г. – 200с.
Комплект документов на технологический процесс изготовления лопасти гребного винта AZIPOD 7104MP-427-504 – 24с.
Лаптева Е.Н. Автоматизированная система управления технологическим процессом распределения припусков Е.Н. Лаптева В.А. Рогов Проблемы корабельного машиностроения Севмашвтуз вып.3 2004г. – 57с.
Лаптева Е.Н. Автоматизированная система управления технологическим процессом распределения припусков (на примере гребных винтов): дис. канд. техн. наук Е.Н. Лаптева 2004г. – 170с.
Проспект фирмы Geodetic Services (США) – 6с.
Путянин Е.П. Аверин С.А. Обработка изображений в робототехнике. М. Машиностроение 1990г. – 320с.
СанПиН 2.2.2.542-96 Гигиенические требования к видеодисплейным терминалам персональным электронно-вычислительным машинам и организации работы 1996г. – 45с.
Сердюков В.М. Фотограмметрия Москва «Высшая школа» 1983г. – 251с.
Сердюков В.М. Фотограмметрия в промышленности и в гражданском строительстве Москва «Недра» 1977г. – 245с.
Трехмерные модели винта и лопасти AZIPOD-7104МР-427-504
Технологическое оборудование для контроля геометрии ГВ
Принцип стереофотограмметрии
Основное оборудование СФГМС V-STARS
Основные этапы получения 3D-модели заготовки ГВ
Особенности технологического распределения припусков и обработки заготовки ГВ
Особенности вписывания 3D-модели в 3D-модель заготовки
Рекомендуемые чертежи
- 22.01.2023
- 24.01.2023
- 24.04.2014
- 23.08.2014
Свободное скачивание на сегодня
- 24.01.2023
Другие проекты
- 29.08.2014