Технология контроля конуса Морзе поводковой оправки





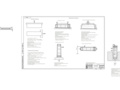
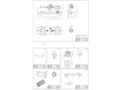
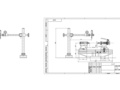
- Добавлен: 25.10.2022
- Размер: 1 MB
- Закачек: 1
Описание
Состав проекта
![]() |
![]() ![]() ![]() ![]() |
![]() ![]() ![]() ![]() |
![]() ![]() |
![]() ![]() ![]() ![]() |
![]() ![]() ![]() |
![]() ![]() ![]() ![]() |
Дополнительная информация
лист 1_Лист.dwg

Образцы шероховатости
с отсчетом по нониусу
Угол конуса Морзе №5
Курсовой проект по ТТК
МГТУ им. Н.Э.Баумана
* Размеры для справок
Общие допуски по ГОСТ 30893.1: Н12
поверхности (сравнения)
индикатор часового типа
Растачивание чистовое
Растачивание черновое
Растачивание отверстия
Протачивание поверхности
Обтачивание чистовое
Растачивание чистовое
Растачивание черновое
копирования на длину
Обтачивание чистовое
Обтачивание поверхности
Изготовление заготовки
Погрешность измерения
Контролтруемый параметр
Операционная технология
Шлифование чистовое конуса Морзе
Предварительное шлифование точных наружных поверхностей
Чистовая обработка наружных поверхностей
Черновая обработка наружных поверхностей
Чистовая обработка внутренних поверхностей
Черновая обработка внутренних поверхностей
Черновая обработка торцов
лист 2 сх_Лист.dwg

Контроль радиального биения
диаметр заготовки - 48мм
длина заготовки - 153мм
=80мкм)контролируется
длина детали 150мм (Т=0
резьбовыми калибрами
М36х3) контролируется
контролируется скобой индикаторной;
контролируются микрометром гладким;
наружные диаметры :
контролируется нутромером индикаторным;
контролируются гладкими калибрами-пробками
Операционный контроль:
Контроль угла конуса
Контролируемые параметры:
Погрешности средства измерения:
Диапазон измерения: 0-160мм
Предельная поргешность измерения: 100мкм
Метрологические харакиеристикм средства
Штангенциркуль ШЩII.
L=126мм (по ГОСТ 2848-75)
Диапазон измерения:
Предельная поргешность измерения: 0
Прибор с двумя отсчетными устройствами
Контролируемый параметр:
Предельная поргешность измерения: 1мкм
головка измерительная типа SIGNAL-HICATOR
отклонение от соосности 0
Контролируемый параметр:
Контроль круглости конуса
Погрешность средства измерения: 1мкм
отклонение от круглости 0
Контроль прямолинейности образующих
Прибор для контроля прямолинейности образующих
отклонение от прямолинейности образующих
Средства измерения по РД 50-98-86
Погрешности измерения по ГОСТ 8.051-81
лист 4-5.dwg

Приспособление для контроля радиального биения Сборочный чертеж
МГТУ им. Н.Э Баумана Группа МТ4-81
Совместная обрботка призм левой и правой бабки 2. Обеспечить отклонение от соосности центров не более 1.5 мкм
рпз.docx
Последовательность операций контроля при изготовлении конуса оправки 6
1 Технология изготовления .6
2 Входной контроль 8
3 Операционный контроль 9
4 Приемочный контроль. Анализ возможных схем измерения. .12
Проектирование контрольного приспособления .15
Список литературы 19
Технический контроль всегда являлся важнейшей и неотъемлемой частью производственного процесса на машиностроительных предприятиях. Его задача это предупреждение с заданной вероятностью пропуска дефектных заготовок деталей и сборочных единиц при последующем изготовлении изделий поэтому технический контроль должен охватывать весь технологический процесс. Кроме того операции технического контроля должны предусматривать получение информации для регулирования технологического процесса.
Контроль – это проверка соответствия норме которая устанавливается заранее а проверка соответствия ей заканчивается принятием решения: «соответствует – не соответствует» «годное изделие – брак » и т. п.
Естественно что сто процентный контроль после каждой операции может привести к неоправданному увеличению цены и с экономической точки зрения это должно быть учтено. С другой стороны пропустив дефект на одном этапе технологии возможны затраты на изготовление заведомо бракованного изделия. Разработка технологии контроля позволяет решить эти проблемы путем тщательного анализа. Установив где необходим сто процентный а где выборочный контроль.
В технический контроль помимо анализа входит разработка схемы контроля и ее реализация. В связи с тем что технический контроль проводиться в процессе производства он имеет ряд ограничений. Так контрольное приспособление должно отвечать следующим требованиям: не занимать много места; быть многофункциональным но при этом простым и удобным в эксплуатации. Поэтому выбору схемы контроля уделяется немаловажное внимание.
Метрологическая экспертиза конструкторской и технологической документации.
Для обеспечения качества и требуемой точности измерений параметров и характеристик изделия конструкторская и технологическая документация должна правильно отражать требования к измерениям физических величин. С этой целью проводится метрологическая экспертиза (МЭ) конструкторско-технологической документации которая является неотъемлемой частью метрологического обеспечения качества изделия и подготовки производства на всех стадиях изготовления изделия.
Под метрологической экспертизой понимается анализ и оценка технических решений по выбору параметров подлежащих измерению установлению норм точности измерений и обеспечению методами и средствами измерений процессов разработки изготовления испытания и применения продукции. Началом метрологической экспертизы должны быть более ранние стадии создания изделия тогда ошибки метрологического характера и их последствия могут быть устранены значительно легче. Исходя из этого МЭ проводится на стадиях подготовки и разработки технического задания проектирования изделия и разработки рабочей документации.
К задачам МЭ конструкторской и технологической документации относятся:
определение оптимальности номенклатуры измеряемых параметров при контроле с целью обеспечения эффективности и достоверности контроля качества и взаимозаменяемости
оценка обеспечения контролепригодности конструкции в процессе изготовления испытания эксплуатации и ремонта
установление соответствия показателей точности измерений требованиям эффективности и достоверности контроля обеспечения взаимозаменяемости оптимальных режимов технологических процессов
автоматизированных СИ обеспечивающих получение заданной точности измерений оценка правильности выбора СИ и МВИ а также выявление возможности преимущественного применения
оценка соответствия производительности СИ производительности технологического оборудования
установление правильности наименований и обозначений физических величин и их единиц
определение целесообразности результатов наблюдений на ЭВМ
установление правильности указаний по организации и проведению измерений для обеспечения безопасности труда и др.
Целью метрологической экспертизы чертежа детали является установление возможности контроля заложенных в чертеже норм точности.
Все контролируемые параметры можно разделить на 4 группы:
Параметры требующие неразрушающего контроля.
К такому виду контроля относится контроль заготовки (входной контроль).
Параметры имеющие невысокую точность и возможность контроля стандартными средствами измерения.
-размеры отверстий 28H7 38H9
Параметры требующие для контроля специальные средства измерения.
К этим параметрам относятся шероховатости поверхностей:
-Ra=5мкм проверить визуально путем сравнения с мерой либо органолептическим методом.
-Ra=125 мкм Ra=063 мкм обеспечиваются технологией (периодически контролируется выборочно с помощью профилографа).
Параметры имеющие повышенную точность при контроле.
- отклонение от прямолинейности образующей конуса 0.006 мм
- отклонение от круглости 001мм
- радиальное биение 001мм
Для контроля последней группы параметров типовых средств измерения нет. Ставим задачу разработки контрольного приспособления.
Последовательность операций контроля при изготовлении поводковой оправки.
1 Технология изготовления:
Операция 005: Заготовительная. Получить из прутка заготовку 48 мм.
Операция 010: Отрезная. Разрезать полученную на предыдущей операции заготовку на части на отрезном круглопильном автомате 8Г642 пильным диском. Наибольший размер разрезаемого материала - 160 мм длина отрезаемой заготовки по упору 20 1500 мм. После отрезания заготовка имеет длину 153 мм (IT14). Заготовку установить в призмы упереть в упор и прижать сверху силой.
Операция 015: Контрольная
Операция 020: Токарная. Заготовку базировать так же как и на предыдущей операции. Обработать торцы в размер 150 мм (IT12).
Операция 025: Контрольная.
Операция 030: Сверлильная. Сверлить отверстие заготовке: 20 мм (IT12) Оборудование – сверлильный станок 2Н18.
Операция 035: Токарная. Провести растачивание отверстия 25 мм (IТ12) на проход. Расточить отверстие 3275 мм на длину 25 мм – с правого торца отверстие 36 мм на длину 8 мм – с правого торца (IТ12). Расточить отверстие 29 мм на длину 45 мм – на расстоянии 52мм от правого торца (IТ12). Расточить канавку 31 шириной 3мм на расстоянии 15мм от левого торца и канавки 37 и 39 шириной 3мм и 2мм на расстоянии 22мм и 6 мм соответственно от правого торца. Шероховатость получаемая на этой операции равна Ra125. Деталь базировать в вертикальном положении в трехкулачковый патрон.
Операция 040: Контрольная.
Операция 045: Токарная. Провести получистовую обработку внутренней поверхности: зенкеровать диаметр 265 мм (IТ10) на проход. Провести нормальное развертывание отверстия 37 мм (IТ10) на длину 8мм от правого торца. Шероховатость поверхностей равна Ra63 и Ra 32. Оборудование и базирование то же что и на Операции 035.
Операция 050: Термическая. На предыдущих операциях в заготовке накопилось большое количество остаточных напряжений. Чтобы их устранить провести отжиг с последующей стабилизацией. Нагреть заготовку до температуры 540°С потом медленно охладить в печи до 240°С затем на воздухе. Оборудование - двухрядный автомат фирмы «Холкрофт».
Операция 055: Промывочная. Промыть заготовку после термической обработки.
Операция 060: Термическая. Провести закалку токами высокой частоты до твёрдости 395 495 НВ. Нагреть до температуры 1000°С и охладить в масле. Так как жёсткость получается больше требуемой провести средний отжиг. Оборудование - двухрядный автомат фирмы «Холкрофт».
Операция 065: Токарная. После термической обработки необходимо восстановить базы – наружную поверхность и торцы заготовки. Оборудование и базирование то же что и на Операции 035.
Операция 070: Токарная. Провести чистовую обработку внутренней поверхности: провести двукратное развертывание диаметра 28 мм (IТ7) на проход и точное развертывание отверстие 38 мм (IТ9) на глубину 8 мм. Шероховатость поверхностей равна Ra063и Ra125. Оборудование и базирование то же что и на Операции 035.
Операция 075: Контрольная.
Операция 080: Нарезание резьбы. Нарезание резьбы метрической резьбы со стороны левого торца М30 на глубину 18 мм и со стороны правого торца М36 на глубину 25 мм. И снятие фасок 2х45°. Оборудование и базирование то же что и на Операции 035.
Операция 085: Контрольная.
Операция 090: Токарная. Провести черновую обработку внешних поверхностей заготовки 38 мм (IТ12) на длину 6мм от левого торца и 47 мм (IТ12)на длину 12мм и конус проточить канавку 44 шириной 4мм на расстоянии 8мм от правого торца. Шероховатость на этой операции равна Ra125. Деталь базировать в центрах на оправке.
Операция 95: Токарная. Провести чистовую обработку внешних поверхностей заготовки: 45 мм (IТ12) и 35 мм (IТ12) и снять фаску 15×45°. Оборудование и базирование то же что и на Операции 090. Шероховатость поверхностей равна Ra5.
Операция 100: Контрольная.
Операция 105: Кругло-шлифовальная. Провести предварительное шлифование конуса Морзе. Шероховатость поверхностей – Ra125. Заготовку базировать на оправке с зажимной втулкой. Оборудование – кругло-шлифовальный полуавтомат ЗМ175.
Операция 110: Кругло-шлифовальная. Провести чистовое шлифование конуса Морзе. Шероховатость поверхностей – Ra063. Заготовку базировать на оправке с зажимной втулкой. Оборудование – кругло-шлифовальный полуавтомат ЗМ175
Операция 115: Контрольная.
Ему подвергают сырье исходные материалы комплектующие изделия техническую документацию и т.д. т. е. все то что используется при изготовлении ремонте или эксплуатации продукции. Необходимо применять статистические методы контроля: т.к. количество заготовок позволяет применять статистический метод (если параметры деталей и будут выходить за границы допуска то это мало повлияет).
Заготовка: пруток материал-сталь 20Х13
Контролируемый параметр: 153 мм ∅48 мм.
Риск поставщика: α=6%.
Риск потребителя: =8%.
Приемлемый уровень качества: qα=7%.
Браковочный уровень качества: q=20%.
Определяется план контроля. Т.к. то выбрана биноминальная модель распределения брака. Используя программу Project2 и выбранные выше значения строим оперативную характеристику. На основе этого считаем n и c. Получаем для биноминальной модели.
Оперативная характеристика:
Метод последовательного анализа.
На основании идей наибольшего подобия по значениям браковочного и приемочного уровня качества используя программу Metrology строятся две прямые: линия приемки и линия браковки.
Используем приемочные границы рассчитанные программой.
3 Операционный контроль.
Операционный контроль проводят с целью своевременного предотвращения отступлений от требований конструкторской и нормативно-технической документации при изготовлении деталей сборочных единиц а также для выявления характера и причин отклонений от технологических процессов в ходе производства и разработки мероприятий направленных на обеспечение стабильности качества выпускаемой продукции.
Контролируемые параметры:
выборочный т.к. деталь имеет хорошо налаженный и стабильный технологический процесс изготовления.
непосредственное измерение с допускаемой погрешностью измерения .
В соответствии с РД 50-98-86 выбираем средство измерения: штангенциркуль ШЦ II с отсчетом по нониусу 005 мм (Δ=100мкм).
Используя программу «Лена 10» получаем вероятность ошибок 1-го и 2-го рода:
m =6292 ; n =5149- для одной границы поля допуска
m1 =-014 ; n1 =1298 - для обеих границ поля допуска в %.
Для контроля данного параметра используем гладкий калибр (Δк50мкм).
m =6314 ; n =581- для одной границы поля допуска
m1 =-014 ; n1 =1162 - для обеих границ поля допуска в %.
m =5394 ; n =327- для одной границы поля допуска
m1 =-016 ; n1 =0654 - для обеих границ поля допуска в %.
В соответствии с РД 50-98-86 выбираем средство измерения: нутромер (Δ=5мкм).
m =6695 ; n =8149- для одной границы поля допуска
m1 =-013 ; n1 =163 - для обеих границ поля допуска в %.
Для контроля данного параметра используем гладкий калибр (Δк13мкм).
m =5897 ; n =5934- для одной границы поля допуска
m1 =-015 ; n1 =1187 - для обеих границ поля допуска в %.
непосредственное измерение -025с допускаемой погрешностью измерения .
В соответствии с РД 50-98-86 выбираем средство измерения: скоба индикаторная (Δ=15мкм)
m =5303 ; n =3219- для одной границы поля допуска
m1 =-016 ; n1 =0644 - для обеих границ поля допуска в %.
m =5108 ; n =3186- для одной границы поля допуска
m1 =-016 ; n1 =0637 - для обеих границ поля допуска в %.
m =5118 ; n =3231- для одной границы поля допуска
m1 =-016 ; n1 =0646 - для обеих границ поля допуска в %.
4 Приемочный контроль. Анализ возможных схем измерения.
Приемочный контроль проводит ОТК с целью определения функциональной пригодности и соответствия изделия.
Рассмотрим радиальное биение. РД 50-98-86 не предлагает готовых решений данной задачи контроля поэтому необходимо разработать контрольное приспособление.
Для разработки контрольного приспособления можно использовать следующие схемы измерения:
Базирование на конусе
Особенности: Деталь устанавливается в коническую втулку. Т.к. деталь является конусом Морзе то вращение детали внутри втулки невозможно. Необходимо вращение всего приспособления. Для этого втулка с деталью устанавливаются на вращающийся стол. Для измерения радиального биения применяется рычаг. Необходимо сконструировать съемное устройство для выбивания конуса Морзе. Недостаток: данное приспособление предназначено только для контроля биения совместный контроль радиального биения и угла конуса невозможен (т.к. длина конуса 130мм контроль угла конуса проводится на длине 126мм по ГОСТ 2848-75 что невозможно осуществить на данном приспособлении т.к. часть необходимой длины «уходит» во втулку).
Базирование в центрах
Особенности: Деталь устанавливается на оправку а затем в центра. Измерение происходит датчиком при вращении оправки с деталью. Преимущество схемы заключается в том что деталь базируется так же как и в процессе обработки (деталь установлена на оправку). При использовании второго датчика с помощью этой схемы можно проконтролировать угол конуса. Недостаток: сложность обеспечения точного центрирования.
При анализе схем измерения была выбрана схема 2.
Определение ошибок контроля для параметров приемочного контроля:
0% т.к. т.к. этот размер является функциональным.
непосредственное измерениес допускаемой погрешностью измерения .
В соответствии с РД 50-98-86 выбираем средство измерения: головки измерительные пружинные (Δ=04мкм)
m =1007 ; n =4267- для одной границы поля допуска
m1 =-006 ; n1 =0853 - для обеих границ поля допуска в %.
непосредственное измерение с допускаемой погрешностью измерения м.
В соответствии с РД 50-98-86 выбираем средство измерения: головки измерительные пружинные (Δ=07мкм).
m =2467 ; n =3248- для одной границы поля допуска
m1 =-012 ; n1 =0 65 - для обеих границ поля допуска в %.
Для контроля данного параметра используем кругломер (Δк05мкм).
m =6423 ; n =0013- для одной границы поля допуска
m1 =-014 ; n1 =2 62 - для обеих границ поля допуска в %.
Для контроля данного параметра разрабатывается приспособление (Δ4мкм).
m =6743 ; n =0019- для одной границы поля допуска
m1 =-013 ; n1 =3837 - для обеих границ поля допуска в %.
Проектирование контрольного приспособления.
Для данной детали возможно использовать сплошной контроль для функциональных размеров а остальные параметры контролировать выборочно.
Для контроля радиального биения рекомендуется разработать контрольное приспособление и применить его на этапе выходного контроля.
Главной задачей схем измерения является сокращение трёх составляющих погрешностей измерения то есть методической инструментальной и субъективной. Из перечисленных составляющих существенную роль играет субъективная и методическая составляющие которым в проекте уделено большее внимание.
Исходя из этого рассмотрим вопросы совершенствования возможных методов и средств измерений.
Выбор средств контроля основывается на обеспечении заданных показателей процесса технического контроля при условии минимальных затрат на его реализацию.
Процесс выбора включает следующие основные этапы:
- подготовка исходных данных контроля т. е. сбор исходных данных об операции объекте контроля и контролируемых параметрах (номинальное значение степень или квалитет точности);
- выбор средства контроля по виду контролируемого параметра по диапазону по способу точности измерения.
Допускаемые погрешности измерения отклонений формы и расположения определяют по ГОСТ 28187-89.
В связи с тем что одну и ту же метрологическую задачу можно решить посредством различных средств измерения которые имеют не только разную стоимость но и разные точность и другие метрологические характеристики дают неодинаковые результаты выбор точности средств контроля имеет первостепенное значение. Точность средств контроля должна быть примерно на порядок выше точности контролируемого параметра.
При проектировании контрольного приспособления необходимо решить следующие задачи:
обеспечение движения;
Деталь устанавливают на оправке с зажимными втулками а затем в центрах. Оправка обеспечивает точность центрирования 15 мкм. Точное базирование осуществляется при помощи установки центров на призмах (сверху центр тоже прижат призмой).
В задачу обеспечения движения входит обеспечение перемещения бабок и вращение детали.
Решением первой задачи является типовой механизм для перемещения вдоль направляющих (он состоит из болта гайки прокладки и рукоятки).
Вращение детали необходимо для съема датчиком информации по всему диаметру изделия поэтому для этого достаточно всего одного оборота а так же нет необходимости в больших скоростях вращения. Значит для решения второй подзадачи не нужно проектировать и использовать никакие дополнительные устройства. Вращение детали будет производиться вручную.
Для измерения значения радиального биения используем измерительную головку рычажно-зубчатую.
Выбираем измерительную головку фирмы Mitutoyo типа Signal-HICATOR. Она имеет корпус . Вставляется в кронштейн который в свою очередь крепится на штативе и закрепляется винтом. Измерительный стержень фактически не чувствителен к радиальным усилиям.
4. Расчет погрешности разработанного приспособления:
Погрешность находится по формуле:
где субъективная погрешность =05*ц.д.=0.0005мм .
Погрешность базирования детали зависит от несоосности центров и оправки:
Инструментальной погрешностью будем считать погрешность датчика. Погрешность выбранного датчика:
Расчет погрешности приспособления является трудоемким. Погрешности вносимые приспособлением можно разделить на систематические и случайные. Систематические погрешности можно исключить установкой датчиков с помощью эталонной детали.
Точность эталонной детали должна быть на порядок выше самой детали поэтому принимаем
Случайная погрешность приспособления сравнима с погрешность датчиков.
Тогда инструментальная погрешность:
Погрешность измерения на данном приспособлении:
Для радиального биения 10 мкм допускаемая погрешность измерений составляет мкм.
данное условие выполняется.
При выполнении курсовой работы была выполнена метрологическая экспертиза чертежа детали разработан Маршрутный технологический процесс изготовления детали произведен выбор параметров контроля на всех стадиях технологического процесса изготовления конуса разработана методика выполнения измерений этих параметров и на основании этих данных были спроектированы оправка с разжимными втулками и контрольно–измерительное приспособление.
Общий план контроля составлялся на основе маршрутного технологического процесса механической обработки детали и анализа установленных требований.
Выбранное расположение точек технологического процесса в которых проводился контроль должно было обеспечивать получение информации для оперативного регулирования технологических процессов.
Маршрут технологии контроля содержал следующие этапы:
- входной контроль заготовки;
- операционный контроль детали;
- приемочный контроль.
В целях уменьшения объема контрольных работ и повышения надежности контроля целесообразно было применить следующую последовательность контрольных операций:
- наружный осмотр на предмет проверки законченности всех предшествующих операций и переходов технологического процесса и отсутствия заусенцев или загрязненности;
- проверка качества поверхностей (шероховатость) визуальным сравнением с установленными образцами; выявление возможных видимых дефектов или механических повреждений;
- проверка качества материала специальным методом;
- проверка наиболее ответственных геометрических размеров;
- проверка отклонений формы и расположения поверхностей с помощью специальных контрольных приспособлений или приборов;
- проверка неответственных элементов детали имеющие сравнительно большие допуски.
Необходимо отметить что в первую очередь следует выполнять менее трудоемкие контрольные операции с тем чтобы не затрачивать лишнего времени на дальнейшую проверку заведомо дефектных деталей по другим параметрам.
Список использованной литературы
Лекции по курсу «Технология контроля» Ю.А.Шачнев
Лекции по курсу «Прикладная метрология» Н.Т. Крушняк
Справочник конструктора-машиностроителя В.И.Анурьев
Альбом контрольно-измерительных приспособлений Ю.А.Степанов
Справочник технолога-машиностроителя. Изд-е 5-ое в 2-х томах. М. 2003. (т.2)
РД 50-98-86 Методические указания. Выбор универсальных средств измерений линейных размеров до 500 мм (По применению ГОСТ 8.051-81).
лист 3_Лист.dwg

Рекомендуемые чертежи
- 24.01.2023