Сваебойный дизельный молот Вариант 2




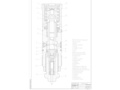
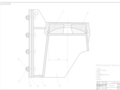
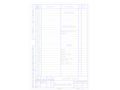
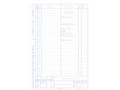
- Добавлен: 25.10.2022
- Размер: 6 MB
- Закачек: 0
Описание
Состав проекта
![]() |
![]() ![]() ![]() |
![]() |
![]() ![]() |
![]() |
![]() ![]() ![]() ![]() |
![]() ![]() ![]() ![]() |
![]() ![]() ![]() ![]() |
![]() ![]() ![]() ![]() |
![]() ![]() ![]() ![]() |
![]() ![]() ![]() ![]() |
![]() ![]() ![]() ![]() |
![]() ![]() |
![]() ![]() |
![]() ![]() |
![]() ![]() |
![]() ![]() |
![]() ![]() |
![]() ![]() |
![]() ![]() |
![]() ![]() |
![]() ![]() |
Дополнительная информация
Курсач мой 4.doc
Пермский национальный исследовательский политехнический университет.
Сваебойный дизельный молот.
Расчёт и проектирование
Руководитель проекта: Шардин В.П.
Задание на курсовой проект .. 3
Штанговые дизель-молоты .. .9
Исходные данные для расчёта . 12
Определение основных размеров молота 18
Определение параметров топливного насоса ..19
Расчет форсунки .. . . . 22
Определение массы ударной части молота (поршня) 23
Обеспечение требуемой частоты ударов молота . 25
Техника безопасности при сваебойных работах 27
Прочностные расчеты . . . . . . ..28
Расчетно-пояснительная записка
Сваебойное оборудование применяется для установки (наведения) сваи её ориентирования фиксации и погружения. Сваебойное оборудование применяется в мостостроении промышленном гидротехническом дорожном и других видах строительства.
Наиболее важным при сваебойных работах погружении шпунта или устройстве свайных фундаментов является квалификация специалистов и технические характеристики применяемого оборудования. Сваебойное оборудование должно отвечать следующим параметрам: повышенная производительность высокая экономичность эффективная работа с любым грунтом работа в любых условиях.
Сваебойное оборудование работает по ударному вибрационному или вдавливающему принципу. Для осуществления ударного действия обычно используют свайные молоты — паровоздушные (простого и двойного действия) и дизельные.
Рис 1 а — простого действия; б — двойного действия
Паровоздушные молоты простого действия имеют полуавтоматическое управление совершают 30—45 ударов в 1 мин такие молоты применяют для забивки в грунт железобетонных свай.
Молоты двойного действия производят 100—350 ударов в 1 мин они более производительны имеют закрытый корпус и могут работать под водой на глубине до 20 м.
Дизельные молоты энергетически автономны и представляют собой прямодействующий двигатель внутреннего сгорания. По типу конструкции ударного модуля дизельные молоты разделяются на:
) трубчатые (ударной частью служит подвижный груз-стержень а направляющей удара пустотелая труба -ствол молота камера сгорания данного молота по типу распыления горючего - ударное распыление). Применение трубчатого модуля для установки тяжёлых железобетонных и металлических свай в грунты средней и высокой плотности.
Рис. 2. Трубчатый дизель-молот
) штанговые (представляют собой массивный подвижный поршень перемещаемый по двум направляющим - штангам тип распыления топлива в камере сгорания - форсунчатое.) Конструктивная схема данного молота представляет собой подъёмно-сбрасывающий механизм состоящий из ударной части (блок - подвижный цилиндр) поршневого шарнирно-опорного блока штанговых направляющих захвата (подъёмное устройство ударной части молота) и механизма дизельной подачи топлива. Штанговые молоты имеют низкий КПД по сравнению с трубчатыми модулями и как следствие обладают малой энергией ударной силы. Область применения таких молотов : забивные деревянные сваи лёгкие железобетонные свай в лёгкие грунты.
По массе ударной части модули разделяются на 3 весовые группы:
) Лёгкие (до 500-600 кг)
) Средние (от 600 до 1800 кг)
) Тяжёлые (от 1800 до 2500 кг)
Рис. 3. Штанговый дизельный молот.
Сваебойное оборудование вибрационного действия подразделяется на вибропогружатели и вибромолоты. Погружатель вдавливающего действия представляет собой лебёдку на самоходном шасси. Разновидность этих погружателей — установки в которых наряду с лебёдкой используют вибропогружатель.
Рис. 4. Вибронагружатель ВП-1
а — общий вид; б — схема положения дебалансов за один оборот валов
Рис. 5. Гидравлический копер
Сваебойное оборудование работающее по принципу вдавливания свай называют копровой установкой. Наиболее эффективной областью применения технологии вдавливания является погружение железобетонных свай и шпунтов в условиях плотной застройки в исторических центрах городов вблизи ветхих и аварийных сооружений в оползневых зонах и в других местах где запрещено погружать сваи ударным методом и вибропогружением из-за недопустимости динамических вибрационных и шумовых воздействий.
Тип и мощность необходимого сваебойного оборудования устанавливают сообразно с местными условиями объемом свайных работ сроками их выполнения длины сваи особенностями предстоящих работ на данном строительстве.
Штанговые дизель-молоты
Штанговый дизель-молот (Рис. 6) состоит из следующих основных узлов: поршневого блока подвижного рабочего цилиндра (ударной части) двух направляющих штанг траверсы шарнирной опоры механизма подачи топлива и захвата-«кошки».
Рис. 6. Штанговый дизель-молот
Поршневой блок состоит из цилиндрического полого поршня с компрессионными кольцами и основания. В центре днища поршня укреплена распылительная форсунка соединенная топливопроводом с плунжерным топливным насосом высокого давления (до 50 МПа). Питание насоса осуществляется из топливного резервуара. Основание поршневого блока опирается на шарнирную опору состоящую из сферической пяты и наголовника. В теле основания закреплены нижние концы направляющих штанг верхние концы штанг соединены траверсой. По штангам перемещается массивный ударный цилиндр со сферической камерой сгорания в донной части. На внешней поверхности цилиндра укреплен штырь (выступающий стержень) приводящий в действие топливный насос при падении ударной части вниз. Подъем ударной части в верхнее крайнее положение перед запуском молота в работу осуществляется подвижным захватом-«кошкой» подвешенным к канату 8 лебедки копра.
При опускании «кошки» вниз крюк автоматически зацепляется за валик в углублении отливки цилиндра. «Кошку» и сцепленную с ней ударную часть поднимают лебедкой копра в крайнее верхнее положение. Затем воздействуя вручную (через канат) на рычаг сброса разъединяют «кошку» и ударный цилиндр последний под действием собственной массы падает вниз на неподвижный поршень. При надвижении цилиндра на поршень воздух находящийся во внутренней ролости цилиндра сжимается (в 25—28 раз) и температура его резко повышается (до 600°С). При нажатии штыря цилиндра на приводной рычаг топливного насоса дизельное топливо по топливопроводу подается к форсунке и распыляется в камере сгорания смешиваясь с горячим воздухом. При дальнейшем движении цилиндра вниз горячая смесь самовоспламеняется и в то же мгновение цилиндр наносит удар по шарнирной опоре наголовник которой надет на головку сваи. Расширяющиеся продукты сгорания смеси (газы) выталкивают ударную часть вверх и выходят в атмосферу. Поднимающийся рабочий цилиндр быстро теряет скорость под действием собственного веса начинает опять падать вниз и цикл повторяется. Дизель-молот работает автоматически до выключения топливного насоса.
Открытая конструкция штангового дизель-молота (поршень внутренняя полость и направляющие штанги открыты при работе) облегчает доступ абразивных частиц к трущимся поверхностям молота что способствует ускоренному их износу который усугубляется отсутствием системы смазки.
Обладая малой энергией удара (составляющей 25—35% потенциальной’энергии ударной части) штанговые дизель-молоты используют для забивки свай массой не более 2000—3000 кг в слабые и средней плотности грунты.
Во всех типах штанговых дизель-молотов имеется воздушное охлаждение позволяющее им работать без перерыва при температуре-наружного воздуха —25° С в течение 50—60 мин. Из-за перегрева дизель-молота могут выйти из строя поршневые кольца и цилиндр зависнет на поршне.
К недостаткам штангового дизель-молота относятся большая металлоемкость его (полезная масса конструкций составляет 54— 56% от общей массы) и высокая степень сжатия (—25~:-30) приводящая к потере части энергии удара на преодоление сил сжатия газовоздушной смеси.
ОСНОВНЫЕ ПРЕИМУЩЕСТВА ШТАНГОВЫХ МОЛОТОВ
Основным качеством штанговых дизельных молотов определившим их широкое применение на свайных работах является мягкость удара и то что штанговые дизельные молоты устойчиво работают при низких температурах и значительной величине осадки свай.
Отечественной промышленностью серийно выпускаются штанговые дизель-молоты с массой ударной части 240 и 2500 кг развивающие энергию удара соответственно 32 и 65 кДж при частоте ударов 50—55 в минуту. Штанговые дизель-молоты применяют в основном для забивки легких железобетонных и деревянных свай стальных труб и шпунта при сооружении защитных шпунтовых стенок траншей котлованов и каналов строительстве водоприемных сооружений и т. п
Технические характеристики дизельных молотов
Наименование показателей
Масса ударной части кг
Наибольшая энергия удара при работе молота в вертикальном положении кДж
Наибольшая допустимая высота подбрасывания ударной части мм
Число ударов в минуту
Масса забиваемых свай т
Средний расход топлива кгч
Высота (без наголовника) м
Масса молота (без заправки наголовника и подставок) кг
Исходные данные для расчёта.
Энергия удара 10 кДж
Частота ударов 100 удмин
Погружаемый элемент – стальная труба 219 мм масса 500 кг
Грунтовые условия – суглинок средней плотности и прочности
Направляющая копра – двутавровый профиль
Штанговый тип молота.
Принимаем для расчёта:
Теплота сгорания топлива
Отношение рабочего хода к диаметру
Давление в начале сжатия
Показатель политропы сжатия расширения
Степень повышения давления предварительного расширения
Коэффициент остаточных газов
Объём продувочного насоса
В качестве топлива выбираем дизельное с химическим составом по весу:
Определим теоритическое количество воздуха необходимое для сжигания 1 кг жидкого топлива:
3 – весовая доля кислорода в воздухе
- молекулярный вес воздуха
Находим действительное количество воздуха при
Состав продуктов сгорания на каждый кг топлива:
Всего продуктов сгорания кг
Состав продуктов сгорания в молях:
Всего продуктов сгорания моля
Вычисляем коэффициент молекулярного изменения (отношение числа молей продуктов сгорания к числу молей до сгорания):
Определим среднюю молекулярную теплоёмкость при постоянном давлении для продуктов сгорания:
где r – объёмные доли газов в смеси
- число молей смеси.
Теплоёмкость составляющих берём по данным М.П Вукаловича и В.А. Кириллина:
Находим среднюю молекулярную теплоёмкость продуктов сгорания при постоянном объёме:
Определяем параметры в конце такта сжатия
Параметры на впуске:
- давление в начале сжатия
- давление окружающего воздуха
- температура окружающего воздуха
Температура воздуха в начале сжатия с учётом теплообмена со стенками для двухтактного двигателя:
где - изменение температуры свежего заряда воздуха вследствие теплообмена со стенками.
Учитывая что при продувке через рабочий цилиндр поступает более атмосферного воздуха принимаем и температуру остаточных газов . Тогда
Коэффициент наполнения:
Давление газа где - показатель политропы сжатия.
Вычисляем параметры в конце процесса сгорания .
Степень повышения давления:
Для определения температуры конца сгорания коэффициент выделения тепла принимаем равным .
- находиться из уравнения сгорания
Подставив числовые значения получим:
Степень предварительного расширения
где – действительный коэффициент молекулярного изменения
Это значение весьма близко к величене принятой по экспериментальным данным. Принимаем .
Степень последующего расширения
Определяем параметры в конце расширения
Определим эффективные и индикаторные показатели работы двигателя.
Среднее индикаторное давление теоритической диаграммы определяется из уравнения:
Ввиду того что в дизель-молотах впуск и выпуск осуществляется через одни и те же окна цикл этих молотов следует рассчитывать в пределах полезного хода поршня поэтому коэффициент полноты индикаторной диаграммы для данного случая .
Среднее эффективное давление:
Индикаторный расход топлива
Эффективный расход топлива
Определение основных размеров молота.
На основе значений полученных в предыдущем расчёте:
где рабочий объём цилиндра
По условию степень сжатия
где - объём камеры сгорания.
Принимая условие получим
Принимаем диаметр рабочего цилиндра D=250мм
Объём продувочного насоса на основании экспериментальных данных
Рабочий ход продувочного насоса
Определение параметров топливного насоса.
Рис. 7. Принципиальная схема топливного насоса.
Расчет секции топливного насоса высокого давления
Расчет секции ТНВД заключается в определении диаметра и хода плунжера. Эти основные конструктивные параметры насоса находятся в зависимости от его цикловой подачи на режим номинальной мощности.
Цикловая подача т.е. расход топлива за цикл:
из (теплового расчета)
Теоретическая подача секции топливного насоса:
где н – коэффициент подачи насоса представляющий собой отношение объема цикловой подачи к объему описанному плунжером на геометрическом активном ходе и учитывающий сжатие топлива и утечки через неплотности а также деформации трубопроводов высокого давления.
Полная производительность секции ТНВД с учетом перепуска топлива перегрузки двигателя и обеспечения надежного пуска при низких температурах:
Определяем диаметр плунжера из соотношения:
где Sплdпл – изменяется в пределах 10 17. (принимаем 11)
Найденное значение приводим в соответствие с ГОСТ 15059-88 о Форсунках и топливных системах тракторных дизелей и их стандартных и прсоединительных размерах и принимаем dпл = 10 мм
Определяем ход плунжера (полный):
По ГОСТ 10578-74 принимаем Sпл = 10 мм
При выбранном диаметре плунжера его активный ход:
где fпл – площадь сечения плунжера.
По результатам теплового расчета и топливного насоса высокого давления определяем диаметр сопловых отверстий форсунки.
- действительное давление в конце сжатия: Р''с = 74 МПа;
- давление конуса сгорания: Рz = 82 МПа;
- цикловая подача топлива: Vц = 1644 мм3цикл
- плотность дизельного топлива: Pт = 842 кгм3
Время истечения топлива: примем (как у дизельного двигателя Т 130)
Среднее давление газов в цилиндре в период впрыска:
Среднее давление распыливания принимаем Рф = 150МПа. Принимаем данное значение давления тк при его уменьшения в дальнейшем получим слишком большой диаметр плунжера и форсунки.
Средняя скорость истечения топлива через сопловые отверстия:
Коэффициент расхода топлива принимаем = 072.
Площадь соплового отверстия:
Число сопловых отверстий принимаем равным m = 1.
Диаметр соплового отверстия:
Определение массы ударной части молота (поршня).
Рис. 8. Схема молота
Зная энергию удара 10 кДж и ход поршня 250 мм для воспламенения воздушно топливной смеси и рассчитаем требуемую массу поршня для обеспечения требуемой энергии удара.
Потенциальная энергия поршня в верхней мёртвой точке
Что сопоставимо с массами ударных частей молотов выпускаемых серийно. Но для обеспечения работы молота по сути являющегося двухтактным двигателем необходим значительно больший ход поршня приняв ход 250 мм за высоту подлёта поршня необходимую для обеспечения максимального использования энергии расширяющихся продуктов горения расположим продувочные патрубки на этой «высоте».
Рис. 9. Схема расположения продувочных патрубков
Для определения необходимого хода поршня для совершения процессов газораспределения высчитаем время истечения газов из рабочего цилиндра.
Примем следующие геометрические параметры продувочных патрубков: длина 250 мм 025 м диаметр 200 мм 005 м количество – 4 штуки.
Коэффициент истечения для одного патрубка:
Рассчитаем расход через один патрубок:
где Па – давление окружающей среды
Па – давление в цилиндре молота
Максимальный расход патрубка примем среднее значение истечения 25 м3с с учётом количества патрубков:
Из предыдущих расчётов известно какое количество воздуха необходимо для сгорания одной порции топлива так как за один так нужно и избавится от продуктов сгорания и впустить в цилиндр свежий заряд воздуха то примем объём воздуха для совершения одного такта:
Соответственно с учётом пропускной способности на один такт требуется 115 с.
Рассчитаем ход поршня с учётом времени С учётом закона сохранения энергии:
С учётом изменившегося хода поршня скорректируем его массу:
Обеспечение требуемой частоты ударов молота.
В стандартном исполнении дизельный трубчатый молот может обеспечить частоту ударов 50-60 в минуту. По техническому заданию молот должен выдавать частоту до 100 ударов в минуту. Для увеличения частоты рассмотрим процессы при работе молота. При рабочем ходе (вверх) поршень подлетает вверх толкаемый расширяющимися газами достаточно быстро а вот при движении вниз поршень набирает скорость достаточно медленно. За счёт ускорения поршня можно повысить частоту ударов молота.
Для повышения начальной скорости поршня при ходе вниз применим газовый амортизатор – в верхней части штанг устанавливается стакан с перепускным клапаном а на верхней части молота добавочный поршень тем самым создавая замкнутый объём газа над поршнем при ходе поршня вверх происходит сжатие газа и при уравновешивании энергий сжатый газ начинает толкать поршень вниз ускоряя его движения вниз. Так как при сжатии-расширении газа происходит выделение поглощение тепла объём газа над поршнем должен быть достаточен для гарантированного избегания перегрева.
Температура днища поршня и цилиндра в ходе работы постоянна при сжатии тепло выделяется при работе газа – расширении поглощается также тепло частично рассеивается через стенки цилиндра основываясь на выше сказанном можно принять объём газа над поршнем равным полному рабочему объёму молота соответственно длина штанг должна быть примерно равным 2.6 м примем 25 м.
Соответственно полная высота цилиндра:
Техника безопасности при сваебойных работах.
Перед тем как начать любые сваебойные работы с применением сваебойных молотов необходимо каждый раз проверять исправность копров надежность и целостность всех их соединений и элементов затяжку резьбовых соединений и т.д. В случае наличия неисправностей их нужно устранить.
Также необходимой является проверка:
- на отсутствие посторонних шумов и стуков
- на отсутствие заедания в работе шаровых кранов
- на герметичность трубопроводов и шлангов
- на степень износа элементов и соединений
- на наличие смазки на направляющих поверхностях.
Установку необходимо отключать для осуществления следующих мероприятий:
- проверка замеров отклонений от вертикали забиваемой сваи
- доливка рабочих жидкостей
- проведения регулировок
- подтягивание крепежных деталей
- надевание на блок соскочившего каната.
Во время работы сваебоя недопустимым является:
- подъем работающего молота;
- использование установки для выдергивания забитых свай;
- натягивание и перегиб шлангов и канатов.
Для того чтобы запланированные сваебойные работы проводились абсолютно безопасно необходимо следовать всем указаниям инструкций прилагаемых к установкам.
Прочностные расчеты.
Расчет крепления молота к копру.
Крепление должно быть разборным и поэтому принимаем болтовое соединение.
Основное нагрузка является статической и поперечно направленной к оси болтов поэтому соединение расчитываем на срез.
Примем следующие параметры соединения
Кол-во болтов = 8 (М 10)
Вес молота = 1400кг принимаем основываясь на весе ударной части. (см таб 5)
Рис..10. Работа элементов на срез
На основе сформулированных выше допущений получаем следующую расчетную формулу (условие прочности при расчете на срез):
где — рабочее (расчетное) напряжение среза возникающее в поперечном сечении рассчитываемой детали; — поперечная сила; при нескольких одинаковых соединительных деталях (— общая нагрузка соединения — число болтов заклепок и т. п.); — площадь среза одного болта (заклепки и т. п.); — допускаемое напряжение на срез зависящее от материала соединительных элементов и условий.
Принимая кофицент запаса прочности равным 4 а максимальное напряжение равным 220 Мпамм2 .
Что соответствует болтам М 10 из нержавеющей стали А-20-50 с пределом текучести 250 Мпамм2.
Расчет диаметра пальца.
Рассчитываем палец при поперечной нагрузке на срез.
Принимаем сталь А 20-50 с пределом текучести 200Мпамм2 .
Вес ударной части 600кг (см таб 5)
Коэфицент запаса прочности примем =4
из ряда стандартных размеров принимаем 20мм.
Расчет диаметра захвата.
При расчете данного элемента конструкций учтем что максимальные напряжения в узле будут возникать от изгибающих моментов. Поэтому расчет будет вестись по определению диаметра цилиндрической части захвата в зависимости максимальных изгибающих моментов.
P1=P2=300 кг (3000Н)
Ммах=P1*L*12=3000*015=450Нм
Эпюра изгибающих моментов
С учетом коэфицента запаса прочности Кзп =2 d=56мм принимаем 60мм
М.И Смородинов Л.В.Ерофеев :Сваебойное оборудование.1967-192с.
И.И. Косоруков Л.М. Пешковский Сваебойные работы 1974-392с.
Сарбаев В.И. Техническое обслуживание и ремонт автомобилей. Ростов нД: «Феникс» 2004.
Вахламов В.К. Техника автомобильного транспорта. М.: «Академия» 2004.
Барашков И.В. Бригадная организация технического обслуживания и ремонта автомобилей. – М.: Транспорт 1988г.
Алексеев И.В. Богданов С.Н. и др. Учебное пособие по курсовому проектированию двигателей внутреннего сгорания. В 3-х частях
Кошка доделал 1.dwg

диз молот 2 додел 4.dwg

ТНВД 1 диз молот додел 3.dwg

Уплотнительная шайба.
Уплотнительное кольцо.
Всасывающие отверстие.
Продольный паз плунжера.
Предохранительная пластинна.
Курсовой проект - Дизельный молот 1.dwg

Патрон додел 1.dwg

диз молот 1 додел 4.dwg

Масса ударнои части 364 кг.
Частота ударов 100удмин.
В Поршневом блоке использовать
Пресс-солидол синтетический Гост 4366-78.
Проверять наличие смазки
при каждой остановке молота.
Недопускать перегрева молота.
Техническая характеристика
Технические требования.
Курсовой проект - Крепление дизельного молота 2.dwg
