Ремонт силикатного пресса СМ-816



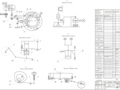

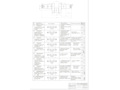
- Добавлен: 25.10.2022
- Размер: 1 MB
- Закачек: 2
Описание
Состав проекта
![]() |
![]() |
![]() |
![]() ![]() ![]() |
![]() ![]() ![]() |
![]() ![]() ![]() |
![]() ![]() ![]() |
![]() ![]() |
![]() ![]() |
![]() ![]() |
![]() |
![]() ![]() ![]() ![]() |
![]() |
![]() ![]() ![]() ![]() |
![]() |
![]() |
![]() ![]() ![]() ![]() |
Дополнительная информация
титулъ.doc
Белгородский государственный технологический
университет им. В. Г. Шухова
Кафедра Механического оборудования
по дисциплине: Эксплуатация и ремонт механического оборудования
на тему: «Ремонт силикатного пресса СМ-816»
Принял: к. т. н. доц. Ханин С. И.
Записка ремонт.doc
Оборудование цементных заводов в большинстве случаев работает в условиях интенсивного воздействия разрушающих факторов технологических процессов - абразивности больших удельных нагрузок высокой температуры влажности запыленности и агрессивности сред. В этих условиях ставится задача надежной работы каждого элемента технологической линии с высокопроизводительным и непрерывным выпуском готовой продукции.
Действие разрушающих факторов на детали и узлы оборудования при недостаточно эффективной системе технического обслуживания и ремонта оборудования а также при допускаемых нарушениях правил технической эксплуатации может привести к потере одного или нескольких свойств обеспечивающих надежность работы оборудования г-прочности жесткости износостойкости а это в конечном счете приведет к постепенным или внезапным (аварийным) отказам.
Большая и ответственная роль в повышении надежности оборудования отводится ремонтным службам. Увеличение объемов ремонтных работ при одновременном улучшении качества технического обслуживания требует постоянного совершенствования технологии ремонта повышения знаний ремонтного персонала. Качество ремонтных работ во многом зависит от уровня механизации труда централизации и специализации ремонтного производства совершенствования системы организации планирования выполнения и контроля проведения ремонтов .
Ремонт оборудования цементных заводов - сложное производство. Специфика его состоит в том что он в большинстве случаев выполняется на месте установки оборудования где не всегда есть стационарные ремонтные приспособления и грузоподъемные механизмы а требуются особые подъемно-монтажные устройства иногда грузоподъемностью 100 т и более переносное не стандартизированное металлорежущее прессовое оборудование и приспособления.
Назначение устройство и принцип действия пресса СМ-816
Для производства одинарного и полуторного силикатного кирпича применяют револьверный кривошипно-шатунный пресс с поворотным столом СМ-816. Он представляет собой трехпозиционный полуавтомат в одной из позиций происходит наполнение известково-песчаной массой двух форм во второй - прессование двух кирпичей в третьей - выталкивание их из форм.
Пресс состоит из следующих узлов (рисунок 1): литой станины поворотного стола с установленными на нем штампами механизма прессования механизма поворота стола механизма выталкивания кирпичей и питателя мешалки. В фундаментной плите 1 станины закреплена центральная колонна 23 служащая осью для вращения стола 18. В столе размещаются 16 радиально-расположенных пресс-форм 19 со вставленными в них штампами. В нижней части штампа имеется ролик 20. К плите прикреплено полукольцо из стальной полосы которое удерживает штампы после выталкивания спрессованного кирпича в необходимом положении по высоте. Стол охватывается кольцом. Кольцо может свободно перемещаться вокруг стола. Плита двумя стяжными болтами соединена с траверсой 14 закрепляя колонну. В подшипнике коробки установлен вал металлической щетки 16. На нижней поверхности траверсы клиньями укреплен контрштамп. В подшипниках скольжения фундаментной плиты установлен коленчатый вал 6 на шейке которого размещен шатун 5 являющийся дифференциальным рычагом. Другим концом рычаг 3 посажен на ось 2 и может на ней вращаться. Прессовый рычаг через колено 4 передает давление поршню.
Привод пресса состоит из электродвигателя 8 и редуктора 9 соединенных между собой муфтой. Редуктор через муфту соединяется с приводным валом. Привод мешалки состоит из электродвигателя и редуктора. На приводном валу 7 пресса жестко закреплена фрикционная муфта 10 и посажена шестерня 11. При включении муфты посредством рычага шестерня через зубчатые колеса и коленчатый вал приводит в действие механизм прессования.
Вращение столом пресса осуществляется от цилиндрического зубчатого колеса. Стол вращается периодически. На зубчатом колесе закреплен кривошипный палец который с помощью шатуна шарнирно соединен с кольцом охватывающим стол. В приливе кольца имеется палец прижатый пружиной сверху. Снизу стола в кольцевой проточке есть 8 вставок образующие в собранном виде храповик. При поступательном движении шатуна стол неподвижен. В этот период происходит заполнение форм смесью прессование и выталкивание кирпичей. При возвратном движении шатуна палец прижатый пружиной к храповику упирается в его выступ и поворачивает стол на 18 оборота. Фиксация каждого положения стола осуществляется тормозом.
Рисунок 1. Пресс СМ-816:
-фундаментная плита; 2-ось; 3-рычаг; 4-прессовое колено; 5-шатун; 6-коленчатый вал; 7-приводной вал; 8-электродвигатель; 9-редуктор; 10-фрикционная муфта; 11-зубчатая передача; 12-стойка; 13-плита; 14-траверса; 15- механизм зачистки стола; 16-щетка; 17-штемпель; 18-стол; 19-пресс-форма; 20-ролик; 21-шина; 22-поршень; 23-колонна. прессовой плитой.
Выталкивающий механизм пресса состоит из рычага поршня и кулачка посаженного на коленчатый вал. Когда 2 кирпича вытолкнуты штампы продолжают удерживаться полукольцом.
На прессе также установлен механизм зачистки 15 стола для очистки стола от налипания массы.
Пресса работают в тяжелых условиях так как на их рабочие и трущиеся части попадает песок и известковая пыль вызывающие повышенный износ деталей и как следствие этого выход пресса из строя. Поэтому к обслуживанию прессов предъявляют повышенные требования:
) пресса должны работать равномерно без толчков так как малейшие толчки вызывают разрушение свежесформованного сырца;
) необходимо чтобы механизм регулировки высоты
наполнения форм работал четко и надежно;
механизм выталкивания должен быть отрегулирован так чтобы выход сырца шел спокойно.
Возможные отказы в работе пресса.
Наиболее изнашивающимися деталями пресса являются штемпели (оси ролики пятки) боковые пластины форм штемпельные плиты прессового поршня зубчатые колеса вкладыши шатуна и коленчатого вала (таблица 1).
Таблица 1 Возможные отказы при эксплуатации пресса и методы их устранения.
Наименование отказа внешнее проявление и дополнительные признаки.
а) вкладышей подшипников шатуна коленчатого вала;
б) подшипников приводного и коленчатого валов;
в) двигателя и редуктора привода;
Недостаточное количество или загрязнение смазки.
Слишком плотное прилегание вкладышей к шейке коленвала или их перекос.
Перегруз двигателя вследствие чего возрастает сила тока.
Низкое напряжение в сети вследствие чего возрастает сила тока.
Неисправности двигателя и
Увеличить подачу смазки насосом пополнить смазкой масленки или заменить смазку.
Подогнать вкладыши устранить перекос.
Устранить перекос отрегулировать положение подшипников качения.
Проверить зазор тормозных колодок пневмотормоза и затяжку тормозных колодок стола.
Выяснить причины падения напряжения и устранить их.
См. инструкцию заводов-
Продолжение таблицы 1 Возможные отказы при эксплуатации пресса и методы их устранения.
штампа о пластину крышки прессующего поршня.
Несовпадение прессформ с пластиной прессующего поршня.
Резкий удар при повороте стола.
Износ щечек или держателей штампа.
а) разрегулировался тормоз;
б) износ накладки тормоза;
в) ослабли резьбовые соединения шатуна привода поворота стола и разрегулировалась его длина;
Увеличен зазор между щеколдой кольца поворота и упорами стола в результате расфиксации эксцентрика шатуна
Заменить щечки или держатели штампа.
Отрегулировать затяжку пружины тормоза.
Заменить накладки тормоза.
Отрегулировать длину шатуна и законтрить резьбовые соединения.
Отрегулировать и зафиксировать положение эксцентрика шатуна привода стола. Заменить изношенные упоры стола.
Повышенная высота кирпича сырца.
Уменьшенная высота кирпича-сырца.
а) износ вкладышей прессующей серьги;
б) износ механизма вкладышей прессования;
в) износ пластин крышки поршня;
г) износ пластин штампов;
д) износ упорных пластин на траверсе;
а) опускание стола вследствие износа фланца нижней втулки стола или опор стола;
Отрегулировать положение прессующего поршня путем установки прокладок.
Заменить пластины штампов.
Заменить пластины на траверсе.
Поднять уровень стола при капитальном ремонте втулки стола или до капитального ремонта уменьшить зазор между контр-
б) наличие слоя массы на “ножах” штампа или пластине крышке поршня;
а) не затянуты гайки оси стола и болтов станины;
б) наличие слоя массы на “ножах” штампа или пластине поршня;
в) неравномерный износ пластин крышки поршня и “низа” штампа;
г) износ облицовочных пластин штампа;
питой и столом до 1 мм уменьшить толщину пластин поршня.
Очистить крышку поршня и штампа от массы.
Произвести затяжку гаек.
Заменить пластины крышки поршня и реставрировать штампы.
Заменить пластины и штампы.
Продольные диагональные трещины а также “подрыв” сырца.
Разрушение кирпича сырца при съеме со стола захватами автомата.
Износ облицовочных пластин штампа.
Не отрегулированы захваты автомата-укладчика.
Зависание штампов в гнездах стола.
Завышенная влажность смеси (слабый сырец).
Недостаточное количество смеси попадающие в пресс-формы по причине:
-малое открытие шибера
-малое усилие подпрессовки
-неравномерная загрузка.
Заменить облицовочные пластины пресс-форм стола.
Отрегулировать автомат-укладчик.
Очистить штампы и гнезда стола.
Обеспечить подачу массы согласно утвержденному техпроцессу.
Увеличить давление воздуха.
Изменить высоту подрезного ножа.
Не поступает смазка.
Пневматическая фрикционная муфта буксует на ходу.
Высокая вязкость смазки марка и рецептура составления смазки не соответствует температуре в месте установки пресса.
Загрязнена смазка. После разборки насоса для заправки системы смазки был неверно установлен заправочный (обратный) клапан.
Падение давления в системе:
а) засорился фильтр.
б) разрегулировался напорный золотник.
Зажаты колодки тормоза.
Не перемещается шток пневмокамеры тормоза.
Износ ретинаксового вкладыша.
Подобрать надлежащую смазку или разбавить имеющуюся жидким маслом.
Промыть насос переустановить так чтобы он не пропускал смазку.
Отрегулировать золотник.
Отрегулировать тормоз.
Нет давления в пневмокамерах тормоза и муфты.
Не срабатывают конечные выключатели дверей общего ограждения пресса.
Штамп опустился ниже плоскости стола.
Зависание штампа в окне пресс-формы.
Сломан ролик конечного выключателя.
Неисправность электропроводки подключения к конечному выключателю.
Нарушение целостности провода.
Износ ролика износ оси ролика.
Коробление облицовочных пластин пресс-формы.
Появление заусениц на корпусе штампа вследствие работы на переувлажненной массе.
Заменить конечный выключатель исправным.
Снять крышку конечного выключателя и подключить к клеммам.
Устранить разрыв;при этом провода необходимо заизолировать.
Заменить изношенные ролики и оси.
Замена облицовочных пластин выемка штампа разборка чистка замена изношенных деталей снятие заусениц с корпуса регулировка влажности массы очистка прессующего поршня.
Раскалывание кирпича-сырца.
Низкая прочность сырца из-за нарушения технологии приготовления массы
(активность влажной массы).
Недостаточная засыпка массы.
Неравномерный износ пластин коробки стола.
Несоосное расположение пластин в траверсе и головной пластине.
Попадание в массу инородных включений
(камней гаек и др.).
Работа на переувлажненной массе.
Замена пластин коробки стола пресса регулировка глубины засыпки регулировка автомата-укладчика регулировка технологических параметров массы (активность влажность).
Ревизия замена траверсы устранение попадания инородных предметов снижение влажности массы до 5 6%.
Рисунок 2. Кинематическая схема пресса СМ-816:
Основные положения СТОИР
В процессе эксплуатации оборудование подвергается различным видам технического обслуживания и ремонтам. В нашей стране принята планово-предупредительная система технического обслуживания и ремонта машин ППР (СТОИР).
Система ППР – это комплекс организационно-технических мероприятий по содержанию и ремонту оборудования производимых в определенной последовательности через предусмотренные планом промежутки времени и направленных на обеспечение бесперебойной работы оборудования в заданном режиме при наивысшем коэффициенте использования и минимальных затратах на эксплуатацию и ремонт.
Система технического обслуживания и ремонта (СТОИР) технологического оборудования предприятий ПСМ выпуск 1 «Цементная промышленность» разработана взамен «Системы планово - предупредительного ремонта оборудования цементных заводов» (система ППР) введенной с 1.01.1980г.
СТОИР имеет следующие особенности и основные отличия от системы ППР:
СТОИР базируется на новых нормативных сроках службы оборудования;
в СТОИР учтена практика использования подотраслевых систем
ППР ПСМ системы ППР и СТОИР других отраслей народного хозяйства;
уделено важное место профилактическим мероприятиям: усилению роли технического обслуживания повышению требовательности к обслуживающему персоналу по соблюдению ПЭО эффективности работы средств диагностики и контроля эффективности работы по предотвращению и разбору аварий;
особое внимание уделено обеспечению качества технического
обслуживания и ремонта;
пересмотрены структуры ремонтных циклов и их продолжительность.
В соответствии с ГОСТ 18322-73 работы предусмотренные системой ППР подразделяются на техническое обслуживание и плановые ремонты.
Техническое обслуживание - это комплекс работ направленных на поддержание работоспособности машин при подготовке к использованию.
Техническое обслуживание предусматривает обязательный по плану периодический объем работ заранее установленный для данного типа и модели машины в определенных условиях эксплуатации.
Ремонт - это комплекс работ по восстановлению работоспособности машин. Объем работ по ремонту машин зависит от технического обслуживания и управления машиной условий эксплуатации и надежности конструкций поэтому объем ремонтных работ не регламентирован.
Ежедневное техническое обслуживание проводится в межсменное время и включает контрольно-осмотровые работы подрегулировку зазоров деталей узлов и их смазку проверку крепления деталей устранение мелких неисправностей а также работы связанные с внешним уходом за машиной.
Ежесменное техническое обслуживание осуществляется производственными рабочими в соответствии с правилами технической эксплуатации машин в течение рабочей смены и между сменами.
Периодическое техническое обслуживание включает все работы входящие в ежедневное техническое обслуживание и кроме того диагностические крепежные регулировочные и смазочные работы.
Учитывая тяжелые условия работы пресса его необходимо останавливать 3-4 раза в смену на 3-5 минут для очистки открытых деталей и узлов (крышки прессующего поршня пресс-форм стола).
Во время остановки проверяют наличие смазки во всех трущихся точках надежность работы централизованной системы густой смазки.
По объемам выполняемых работ различают: текущие средние и капитальные ремонты.
Текущий ремонт включает минимальный объем работ необходимый для поддержания оборудования в рабочем состоянии в период между ремонтами.
Во время текущего ремонта пресса заменяют вкладыши сменные пластины форм плиты контрштампов собачки пальцев и другие детали которые являются быстроизнашивающимися.
Средний ремонт включает восстановление точности мощности и производительности оборудования на срок до очередного планового среднего или капитального ремонта.
При среднем ремонте заменяют и ремонтируют ряд узлов и деталей: втулку прессового рычага прессовое кольцо втулку стола штемпели поршень выталкивателя прессовой рычаг верхние лицевые плиты стола вертикальный вал мешалки конические шестерни.
При капитальном ремонте машину полностью разбирают восстанавливают или заменяют все ее узлы и детали с целью достижения первоначальных качеств машины.
При проведении капитального ремонта пресса для его разборки на ремонтную площадку доставляют грузоподъемные механизмы - передвижной кран грузоподъемностью 2 тонны 2 реечных домкрата грузоподъемностью 75 тонн и другие приспособления необходимые для демонтажа и монтажа пресса.
Перед остановкой пресса для проведения капитального ремонта
сначала необходимо отключить подачу силикатной массы в бункер пресса затем выработать массу из бункера отключить подачу электропитания затем отключить подачу электропитания затем очистить от известково-песчаной массы.
Для ремонта пресс разбирают демонтируют все ограждения смеситель и аппарат наполнения форм разъединяют муфту привода демонтируют механизм поворота стола траверсы стол пресса и другие детали и узлы.
При демонтаже стола отсоединяют шатун поворота стола от пальца зубчатого колеса и от пальца поворота стола удаляют тормозное устройство пресса отворачивают нижнюю гайку стола и вытаскивают ось колонны. Демонтируют стол предварительно удалив пневмоподъемником штемпеля и траверсу с контрштампом. Далее демонтируют механизм регулирования наполнения форм выталкивающий механизм освобождая от крепления к раме стойку и цилиндр. После снятия крышки привода вынимают приводной вал и приступают к демонтажу коленчатого вала для чего отсоединяют шатун от коленчатого вала и демонтируют его в сборе.
Сняв крышку пресс-поршня отсоединяют прессующий поршень от прессового колена затем от прессового рычага отсоединяют шатун и вынимают прессовый рычаг.
Закончив демонтаж пресса по узлам приступают к дальнейшей разборке дефектовке и ремонту деталей.
Перед сборкой комплектуют детали и собирают узлы. Сборку пресса начинают с укладки коленчатого вала в подшипники выверки горизонтальности установки рамы пресса и согласования ее осей с осями редуктора и электродвигателя. Затем устанавливают прессовый рычаг с втулкой и соединяют с ним шатун. Перед установкой стола пресса в него предварительно запрессовывают втулку; на раму в месте прилегания стола укладывают стальные полукольца после этого монтируют центральные и стяжные колонны на центральную колонну устанавливают траверсу с контрштампом. Далее на фундаментной раме размещают выталкивающий механизм: цилиндр поршня поршень стойки выталкивающий рычаг левый конец которого заводят за копир. По окончании сборки пресса устанавливают наполняющий аппарат привод пресса и мешалки. Перед пуском пресса проверяют поступление смазки в смазываемые точки.
Работу полностью собранного пресса на холостом ходу проверяют не менее 2 часов после чего пресс пускают под нагрузкой. В случае прекращения работы пресса останавливают мешалку а затем пресс при пуске пресса - наоборот.
Во время работы пресса на холостом ходу и под нагрузкой проводят испытания работы пресса с целью соответствия рабочих и паспортных данных.
Для планирования и расчетов ремонта оборудования была введена нормативная единица ППР - ремонтосложность оборудования.
Численная величина ремонтосложности в условных единицах может быть определена из таблиц положений по ППР отдельно для механической и электрической частей.
Общая трудоемкость ремонта определяется по формуле:
Тобщ =Тмех + Тэл + Тподг.раб.
где Тмех- трудоемкость механической части;Тэл- трудоемкость электрической части;Тподг .раб- трудоемкость подготовительных работ .
Трудоемкость механической части определяется по формуле:
где Nмех- определяется из таблицы норм трудоемкости условной единицы ремонтосложности Nмех = 35 чел. -ч.;Rмех - определяется из справочника положений о ППР число условных единиц ремонтосложности Rмех= 42.
Трудоемкость электрической части определяется по формуле:
где Nэл - определяется из таблицы норм трудоемкости условной единицы ремонтосложности Nэл =15 чел. -ч.;Rэл - определяется из справочника положений о ППР число условных единиц ремонто- сложности Rэл = 12.
Трудоемкость подготовительных работ определяется по формуле:
Tподг.раб. = 03 . Tмех = 03 . Nмех . Rмех
тогда общая трудоемкость ремонта будет равна:
Tобщ = Nмех . Rмех + Nэл . Rэл + 03.Nмех . Rмех = 13 . Nмех . Rмех + Nэл . Rэл
Tобщ = 13 . 35 . 42 + 15 . 12 = 2091чел. –ч.
Время простоя определяется по формуле:
где Нпр - определяется по таблице норм простоя оборудования на одну условную единицу ремонтосложности в сутках Нпр = 04 тогда t = 04 . 42 = 168 (суток).
Расчет потребной рабочей силы. При работе в 3 смены:
Р3смен= Тобщ (21 . tпр) тогда
Р3смен = 2091 (21 . 168) = 6 чел.
При работе в 2 смены:
Р2смен = Тобщ (14 . tпр)
тогда Р2смен = 2091 (14 . 168) = 9 чел.
При работе в 1 смену:
Р1смен= Тобщ (7 . tпр)
Р1смен= 2091 (7 . 168) = 18 чел.
Для нормальной работы механизмов оборудования важно правильно выбрать смазочный материал. От смазочного материала зависит надежность деталей. Надежность определяется: способностью смазочных материалов защищать трущиеся поверхности от износа; обеспечивать необходимые характеристики трения; снижать потери на трение; отводить тепло. Смазочная эффективность материалов зависит от сочетания многочисленных факторов: от свойств материала в том числе от их изменений в процессе эксплуатации от состояния и свойств трущихся поверхностей от характера взаимодействия между компонентами смазочного материала трущимися поверхностями и покрывающими их окисными пленками; от скорости нагрузки температуры и других параметров режима трения.
Рассмотрим маршрут смазки пресса СМС-816. Маршрут смазки при нормальной работе: смазка поступает из резервуара насоса под нагнетательный плунжер. Затем смазка вытесняется через нагнетательный клапан в распределитель из него в питатель по трубопроводам к точкам смазки:
шатун шейки коленчатого вала;
вкладыш серьги верхней;
втулка прессующего поршня - правая сторона;
вкладыш серьги нижней;
втулка прессующего поршня - левая сторона;
ось прессующего рычага;
цилиндр механизма выталкивания;
ось роликов механизма выталкивания.
Маршрут смазки при блокировке: густая смазка поступает из насоса так как питатель заблокирован и давление возрастает то под действием указанного давления срабатывает индикатор давления и выдает сигнал о перегрузке (световой и звуковой).
В системе смазки пресса СМ-816 используют смазку ЦИАТИМ-203 и масло индустриальное. Для заправки резервуара насоса необходимо приготовить смесь состоящую из этих смазок.
Консистенция смеси должна обеспечить смазку втулок и подпятника стола и смазку цилиндров прессования и выталкивания.
Вместо смазки ЦИАТИМ-203 допускается использовать солидол-Ж вместо индустриального масла допускается использовать турбинное трансформаторное веретенное применяемые жидкие смазочные материалы должны иметь высокий класс чистоты.
Наличие комков не допускается. Подготовку смазки проводить с требованиями противопожарной безопасности.
Во время первоначального пуска или после длительного хранения пресса необходимо проверить работоспособность и параметры работы централизованной системы смазки. В состав централизованной системы смазки пресса СМ – 816 входят:
Станция смазочная одномагистральная Е.С.72001;
Фильтр 10 _ 250 _ 2 _УхА4 ГОСТ 6918-81;
Микропереключатель МП 2302;
Индикатор 9396 Н1 р = 36 МПА;
Манометр 06 мГц _ 1 _ 160 _ 100 _ 77;
Перекачной насос густой смазки НПГ_МУЗ;
Фильтр 10 _ 250 _ 2 _УхА4ГОСТ6918-81.
Рисунок 3. Технологическая карта смазки пресса СМ-816
Ремонт машин- производственный процесс состоящий из комплекса организационно- технических мероприятий и непосредственно технологического процесса ремонта машин.
Производственный процесс- совокупность мероприятий в результате которых восстанавливается годность отдельных деталей узлов агрегатов и машин в целом.
Организационные мероприятия- доставка оборудования к месту ремонта подготовка технической документации связанной с ремонтом снабжение материалом запасными деталями и узлами обеспечение грузоподъемным и транспортным оборудованием приспособлениями и инструментами комплектование производственного персонала и др.
Технологический процесс- совокупность технологических операций в результате которых происходит последовательная замена отдельных узлов и деталей новыми или отремонтированными узлами или деталями ремонтируемого объекта.
Для обеспечения качественного ремонта и проведения его в короткие сроки осуществляется конструкторская и технологическая подготовка к ремонту.
Конструкторская подготовка- обеспечение технической документацией- рабочими чертежами машины техническими условиями на ремонт машины и др.
Технологическая подготовка- разработка технологических карт (схем) разборки сборки узлов и машины в целом; технологических карт восстановления старых и изготовления новых деталей чертежей на приспособления и стенды для ремонта и др.
В виду громоздкости технологического оборудования как правило ремонт его производят на месте силами местного ремонтно- механического цеха или специализированными ремонтными предприятиями. В зависимости от имеющегося оборудования номенклатуры и конструктивных особенностей машин организации ремонтного производства условий и возможности ремонтных предприятий а также снабжения запасными деталями и узлами применяют различные методы ремонта оборудования: индивидуальный обезличенный смешанный.
Индивидуальный метод ремонта- все узлы и детали машины после ремонта устанавливают на те же машины с которых они были сняты.Этот метод ремонта может осуществляться как универсальными так и специализированными бригадами. В первом случае ремонтная бригада разбирает машину на узлы а затем на детали которые направляются для ремонта в соответствующие цеха. Универсальную ремонтную бригаду комплектуют из высококвалифицированных рабочих так как каждый член бригады должен уметь отремонтировать любой узел.
Специализированные бригады осуществляют индивидуальные ремонтные работы: разборочно- сборочные ремонт узлов или др. Они специализируются на ремонте определенных узлов или группы узлов близких по технологическим признакам. В этом случае ремонт осуществляется на определенных рабочих местах обеспеченных необходимыми приспособлениями и инструментом.
Организация ремонта специализированными бригадами более прогрессивна чем универсальными и имеет следующие преимущества: 1) повышенную производительность труда и лучшее качество ремонта; 2) меньшее время простоя машины в ремонте и стоимость ремонта.
Ремонт оборудования специализированными бригадами рекомендуется проводить в ремонтно- механических цехах крупных заводов имеющих большое количество однотипного оборудования. Универсальные бригады проводят ремонт в центральных ремонтных мастерских а также в небольших неспециализированных ремонтно- механических заводах.
Индивидуальный метод ремонта осуществляют для ремонта уникальных машин а также многомарочного парка оборудования завода стройиндустрии.
Основным недостатком этого метода является длительный простой машины в ремонте и трудность планирования загрузки ремонтного предприятия.
Обезличенный метод ремонта предусматривает ремонт узлов и машины в основном за счет сборки их из ранее отремонтированных деталей и узлов. При этом допускается взаимозаменяемость узлов и деталей а снятые с ремонтируемой машины узлы и детали поступают в ремонт обезличено. В результате пребывание машины в ремонте сокращается время затрачиваемое на ремонт и восстановление деталей и узлов. Кроме того механизация трудоемких процессов ремонта и применение необходимой технологической оснастки позволяют значительно снизить трудоемкость и стоимость ремонта повысить его качество и увеличить производительность труда. Этот метод ремонта является более прогрессивным но требует создания необходимого фонда оборотных узлов и деталей.
Обезличенный метод ремонта позволяет организовать ремонт машины и узлов на потоке. Этот метод имеет несколько разновидностей: агрегатно- узловой (узловой) периодической замены ремонтных комплектов (ПЗРК).
При агрегатно- узловом методе ремонта узлы обезличивают демонтируемые узлы ремонтируют и затем хранят как запасные; при этом снятые узлы агрегаты и детали можно ремонтировать любым методом. Базовую деталь (раму станину и др.) ремонтируют параллельно с ремонтом остальных узлов и агрегатов. Но ремонт последних не задерживает сборку машины так как узлы и детали поступают на линию сборки со склада или после ремонта непосредственно с участков и из отделений.
В практике ремонта оборудования промышленно- строительных материалов узлы крупных установок в большинстве случаев ремонтируют без обезличивания деталей.
Агрегатно- узловой метод ремонта широко применяют при ремонте однотипного оборудования или машин имеющихся в большом количестве. Данный метод по сравнению с индивидуальным способствует значительному сокращению времени нахождения машины в ремонте (до 50-60%) созданию условий для специализации рабочих по отдельным видам работ более равномерной загрузке ремонтно- механического цеха предприятий или ремонтного завода повышению качества ремонта и снижению его стоимости.
Важнейшим условием ремонта машин узловым методом- создание в необходимом количестве и сохранение оборотного фонда узлов и агрегатов.
Для снижения объема работ при разборке и сборке во время ремонта на месте установки машины узлы укрупняют в блоки или агрегаты которые ремонтируют в мастерских.
Метод периодической замены ремонтных комплексов (ПЗРК) является разновидностью агрегатно- узлового метода ремонта и состоит в том что узлы подлежащие ремонту заменяют по мере их износа в зависимости от срока службы последних и преимущественно в нерабочее время с использованием кратковременных плановых остановок на текущие ремонты непосредственно на месте работы машины.
1 Планирование ремонтов
В целях лучшего использования производственных мощностей на предприятиях промышленности строительных материалов необходимо обеспечить работу действующего оборудования с высоким коэффициентом его использования. Это достигается в частности за счет улучшения использования оборудования качественного и оперативного проведения ремонтно- восстановительных работ.
Ремонт оборудования следует проводить в сжатые сроки применяя совмещение максимальной механизации ремонтных работ с рациональным распределением людских и материальных ресурсов. Для решения этих задач широко внедрено в практику планирование и управление на основе передовых научных методов.
На предприятиях строительных материалов как и на большинстве предприятий страны планирование и управление ремонта и монтажа оборудования осуществляют с помощью линейных (ленточных) и сетевых графиков. В линейных графиках горизонтальными линиями отражается продолжительность и календарное расписание выполнения ремонтных работ. Графики характеризуют также распределение работ по видам и наименованиям. В линейных графиках используется один элемент- работа характеризующаяся продолжительностью и сроками начала и конца работы.
Линейные графики как правило содержат укрупненный перечень ремонтных работ что создает определенные трудности
при изображении последовательности работ и установлении связей между исполнителями.
Линейные графики не позволяют количественно оценить влияние отклонений в ходе ремонтных работ на общий срок ремонта оборудования что очень важно для принятия своевременного необходимого решения. Однако в процессе проведения ремонтных работ нередко возникает потребность их пересмотра в силу неучтенных производственных факторов. Это приводит к несоответствию плана с фактическим ходом ремонта или монтажа оборудования.
Метод сетевого планирования и управления (СПУ) полностью удовлетворяет эти требования и широко применяется во всех отраслях промышленности.
Сетевая модель представляет собой график отображающий объем решаемой задачи. Система СПУ дает возможность выяснить от каких видов работ и в какой степени зависят сроки достижения цели.
Организация работ по разработке и внедрению сетевого метода планирования и управления при ремонте оборудования включает подготовительный период этап исходного планирования и этап оперативного планирования и управления.
Подготовительный этап включает в себя определение вида ремонтных работ и ее технологический анализ с учетом возможностей предприятия.
Исходное планирование ремонта оборудования начинается с определения предполагаемого общего объема ремонтных работ. На основе технической и сметной документаций (дефектная ведомость сметы проект организации работ) определяют общую технологическую последовательность ремонта оборудования и закрепляют за исполнителем определенный объем работ.
Ответственные исполнители получив задание после детального изучения составляют технологию ремонта данного узла в виде частных сетевых графиков в которых должны наиболее полно отражаться последовательность и взаимосвязь между работами по ремонту отдельных узлов.
Основными элементами сетевого графика являются работа и событие. Работа- процесс требующий затраты времени и ресурсов. Событие- факт окончания одной или нескольких работ необходимый и достаточный для начала последующих работ. Само по себе оно не требует ни времени ни средств.
Основным в сетевом графике является последовательность выполнения работ не имеющая резерва времени называемая критическим путем. Поэтому во время производства работ уделяется большое внимание работам лежащим на критическом пути так как нарушение сроков их выполнения может привести к срыву графика. Наиболее целесообразно разрабатывать эти графики со степенью детализации до одной смены.
Описание событий помещенное рядом с сетевым графиком делает его более наглядным и доходчивым для исполнителей. На этом графике с помощью стрелок (характеризующих работу и зависимость) и кружков (характеризующих результат одной или нескольких работ) показывают последовательность и взаимосвязь работ по ремонту узла. На основе норм определяют продолжительность каждой работы и требуемое количество основных рабочих.
Отсутствие научно обоснованных технических норм на ремонтные операции заставляет сотрудников группы СПУ производить хронометраж ремонта.
По частным сетевым графикам составляют сводный сетевой график. При этом выясняется последовательность и взаимосвязь ремонта узлов и намечаются циклы работ. Степень детализации в этом случае наиболее целесообразно принимать равной 1 суткам.
Общая продолжительность ремонта определяется длиной критического пути который составляет работы имеющие нулевой резерв времени. Если расчетная продолжительность критического пути превышает нормативный срок ремонта то разрабатывают мероприятия по сокращению критического пути. В этом случае пересматривают и уточняют первоначальные временные оценки рассматривают возможности изменения технологии ремонта узлов с целью максимального совмещения работ т. е. перевода части работ с последовательного на параллельное исполнение привлекают дополнительную рабочую силу или перераспределяют имеющиеся людские ресурсы на более напряженные участки работ; переводят отдельные бригады на 2-3- сменную работу; повышают механовооруженность отдельных участков работы и т. д.
Как показал опыт сетевой график выполнения ремонтов позволяет из множества вариантов проведения производственного процесса выбрать наиболее рациональный и наглядно отразить все взаимосвязи между ремонтными операциями и их исполнителями. Кроме того здесь более четко определяются необходимые трудовые и материальные ресурсы а также их движение в процессе ремонта.
В результате расчета сетевого графика прежде всего определяют время начала работ позднее время начала работ резерв времени критический путь и работы критического пути общий срок ремонта оборудования.
Расчетную производительность критического пути по сетевому графику сопоставляют с нормативными сроками простоя оборудования.
Список использованной литературы.
Банит Ф.Г. Крижановский Г.С. Якубович Б.И. и др. Эксплуатация ремонт и монтаж оборудования промышленности строительных материалов М. 1971.
Силенок С.Г. Механическое оборудование предприятий строительной индустрии. Учебник для вузов.М.Стройиздат1973.-374с.
Дроздов Н.Е. Эксплуатация ремонт и испытание оборудования предприятий строительных материалов изделий и конструкций: Учебник для ВУЗов.-М.: Высшая школа 1979. – 312 с.ил.
Технический паспорт пресса СМ-816.
Система технического обслуживания и ремонта технологического оборудования предприятий ПСМ Выпуск 1 Часть 1-2. – М.: 1987.
Содержание рем(+).doc
Пояснительная записка
БГТУ им. В.Г.Шухова
Назначение конструкция и принцип действия 5
Основные положения СТОИ 17
Смазка оборудования 23
Организация ремонта 26
1 Планирование ремонтов 29
Список использованной литературы34
Вал коленчатый(+).dwg

Карта ремонта(+).dwg

Контроллер 4 разряда
Проверить соответствие чертежу всех размеров
Контрольный стол. 2. Штангенциркуль
Вал сдать ОТК или мастеру РМЦ.
Шлифовальщик 4 разряда
Круг Э-46-60 на керамической связке.
Режим резания: V=130 ммин. S=0.3 ммоб.
Круглошлифовальный станок с ø круга 400 мм.
Шлифовать рабочие места: ø224 ( ) до ø224 ( )мм.
Ток.-винт. станок16К20. 2.Проходной резец 25 25мм с пластиной Т15К6. 3.Щтангенциркуль 0-300мм.
Проточить по наружному диаметру ø229 до ø224( ) мм.
Точность проверки 0.1 мм.
Гидравлический пресс. 2.Приспособление для проверки биения.
Очистить вал от окалины
при необходимости выровнять.
После нагрева охладить на спокойном воздухе HB=260-280.
Газовая горелка. 2.Эл. таль 1 т.
Нормализация. Нагреть вал до t=800С и охладить на воздухе.
Электро- сварщик 4 разряда
Режим наплавки: Сила тока I=130А.
Сварочныцй аппарат. 2.Электроды УОНИ. 3.Молоток.
Наплавить: ø220 мм до ø229.
Ток.-винт. станок16К20. 2.Проходной резец 25 25мм. 3.Щтангенциркуль 0-300мм.
Проточить места под наплавку: ø224 мм до ø220 мм.
а) Шаблон для проверки центров отверстий. б) Точность центровки вала-0.1 мм по ø70мм.
Ток.-винт. станок16К20. 2. Центровое сверло. 3.Расточной резец 25 25мм. 4. Индикатор ЧТ.
Проверить и исправить центр отверстия.
Цена делния индикатора 0.01 мм.
Трехгранный шибер. 2. Штангенциркуль. 3. Индикатор ЧТ. 4. Приспособление для проверки валов с эл. талью 1 т.
зачис- тить центровые отверстия
проверить на биение и выровнять.
Скребок. 2. Металлическая щетка. 3. Ветошь. 4. Солярка.
Очистка вала от грязи
Наименование операции и работ
Технические указания
КАРТА РЕМОНТА КОЛЕНЧАТОГО ВАЛА
КПЭиР - 05 101 00 00 00
2 Карта ремонта коленчатого вала.
а) Шаблон для проверки центров отверстий. б) Точность центровки вала-0.1 мм.
БГТУ им. В. Г. Шухова
Технологическая карта ремонта
Карта смазки(+).dwg

Механизм выталкивания
Наименование и обоз- начение изделия (механизма) номера позиции на иллюстрированной карте смазки
Наименование смазочных материалов№ стандарта (технических условий на них для эксплуатации)
Коли- чество точек смазки
Способ подачи смазочных материалов
Периодич- ность смазки
Механизм прессования 1. Подшипник серьги нижней 2. Направляющая поршня 3. Направляющая поршня 4. Подшипник серьги верхней 5. Ось прессующего рычага Вал коленчатый 6. Шейка коленвала Механизм выталкивания 7. Ось рычага 8. Ось ролика рычага 9. Направляющая поршня Стол 10. Втулка и подпятник Выталкиватель штампов 11. Поршень 12. Шарниры кронштейна Привод 13. Муфта уравнительная Механизм выталкивания 14. Направляющая ролика Стол 15. Палец шатуна 16. Головка шатуна 17. Палец шарнира 18. Ролик штампа 19. Втулка щеколды 20. Кольцо поворота 21. Подшипник шатуна Привод пресса 22. Подшипник вала приводного Механизм прессования 23. Роликоподшипник прессующего шатуна Привод пресса 24. Зубчатая пара Вал коленчатый 25. Подшипник
Смесь циатим 203 ГОСТ 3773-73 25% и масла индустриаль- ного ИГОА ГОСТ 20799-75 75% Индустриальное ИГОЛ ГОСТ 20799-75 Солидол Ж ГОСТ 1033-79 Солидол Ж ГОСТ 1033-79 Масло индустриальное ЦЧО ГОСТ 20799-75 Солидол Ж ГОСТ 1033-79 Солидол Ж ГОСТ 1033-79 Солидол Ж ГОСТ 1033-79 Солидол Ж ГОСТ 1033-79 Солидол Ж ГОСТ 1033-79 Солидол Ж ГОСТ 1033-79 Солидол Ж ГОСТ 1033-79 Солидол Ж ГОСТ 1033-79 Солидол Ж ГОСТ 1033-79 Солидол Ж ГОСТ 1033-79 Солидол Ж ГОСТ 1033-79
Принудительно Поступает с воздухом Ручная набивка Ручная набивка Поливом Шприцем Шприцем Шприцем Шприцем Шприцем Шприцем Шприцем Шприцем Ручная набивка Ручная набивка Ручная набивка
Постоянно Постоянно 250 часов 8 часов 8 часов 8 часов 8 часов 8 часов 8 часов 8 часов 250 часов 500 часов Пти сборке и ремонте Замена через 500 часов Замена через 500 часов
Механизм поворота стола
БГТУ им. В. Г. Шухова
Рекомендуемые чертежи
- 04.11.2022
- 12.06.2014
- 18.02.2014