Редуктор коническо-цилиндрический




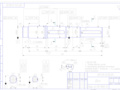
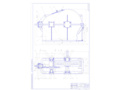
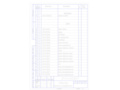
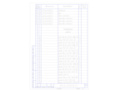
- Добавлен: 25.10.2022
- Размер: 995 KB
- Закачек: 0
Описание
Состав проекта
![]() |
![]() ![]() |
![]() ![]() |
![]() ![]() |
![]() |
![]() ![]() ![]() ![]() |
![]() ![]() ![]() ![]() |
![]() ![]() ![]() ![]() |
![]() ![]() ![]() ![]() |
![]() ![]() ![]() ![]() |
![]() ![]() ![]() ![]() |
![]() ![]() ![]() ![]() |
![]() ![]() ![]() ![]() |
![]() ![]() ![]() |
![]() ![]() |
![]() ![]() |
![]() ![]() |
![]() ![]() |
![]() ![]() |
Дополнительная информация
Крышка сквозная.dwg

Неуказанные предельные отклонения размеров поверхностей
точности; поверхностей
t2 грубого класса точности.
Вал.dwg

*Размер обеспеч. инстр.
Неуказанные предльные отклонения
Спецификация-2.dwg

Шайба 16 65Г ГОСТ 6402-70
Гайка М12 ГОСТ 2524-70
Шайба 12 65Г ГОСТ 6402-70
Шайба 8 65Г ГОСТ 6402-70
Шайба 10 65Г ГОСТ 6402-70
Шайба 36 ГОСТ 11872-80
Крышка глухая.dwg

Неуказанные радиусы 2мм max.
Неуказанные предельные отклоненя размеров поверхностей
точности; поверхностей
t2 грубого класса точности.
Колесо.dwg

Радиусы скруглений 1
Неуказанные предельные отклонения размеров: отверстий +t
Направление линии зуба
Нормальный исходный контур
Коэффициент смещения
Обозначение чертежа сопряжённого колеса
Спецификация-3.dwg

Подшипник 7210 ГОСТ 8338-57
Подшипник 7214 ГОСТ 8338-57
Редуктор.dwg

Спецификация-1.dwg

Колесо цилиндрическое
Крышка подшипника сквозная
Крышка подшипника глухая
Кольцо маслоотражательное
Курсовой (Детали машин ПЗ).doc
ГОУ ВПО Магнитогорский государственный технический университет
Кафедра ПМ Г ПТ и ТК
Комплект технической документации к курсовому
проекту по деталям машин
ПРИВОД ЛЕНТОЧНОГО КОНВЕЙЕРА
Пояснительная записка
Руководитель проектаКадошников В.И.
Магнитогорск 2006 г.
Выбор электродвигателя. Определение вращающих моментов и скоростей на валах редуктора4
1Выбор электродвигателя4
2Определение вращающих моментов и скоростей на валах редуктора4
Расчёт зубчатых колёс редуктора5
1Выбор материала и термической обработки. Допускаемые напряжения.5
2Расчёт зубчатой цилиндрической передачи5
2.2Расчёт сил в зацеплении6
2.3Проверочный расчёт передачи6
3Расчёт конической зубчатой передачи7
3.2Расчёт сил в зацеплении7
3.3Проверочный расчёт передачи8
Конструирование зубчатых колёс9
1Цилиндрическое колёсо9
Проектировка валов10
1.1Определение реакций опор в подшипниках11
1.2Построение эпюр изгибающих моментов и вызванных ими напряжений12
1.3Исследование опасных сечений13
1.4Проверка долговечности подшипников14
2Промежуточный вал14
2.1Определение реакций опор в подшипниках15
2.2Построение эпюр изгибающих моментов и вызванных ими напряжений16
2.3Исследование опасных сечений17
2.4Проверка долговечности подшипников17
3.1Определение реакций опор в подшипниках19
3.2Построение эпюр изгибающих моментов и вызванных ими напряжений20
3.3Исследование опасных сечений21
3.4Проверка долговечности подшипников21
4Проверка прочности шпоночных соединений21
Конструирование стаканов и крышек подшипников23
1Конструирование стакана23
2Конструирование крышек подшипников23
Конструирование корпусных деталей24
Смазывание зубчатых передач24
Спроектировать двухступенчатый горизонтальный коническо-цилиндрический редуктор общего назначения привода ленточного конвейера.
Рис. 1. – Кинематическая схема привода ленточного конвейера:
-двигатель; 2- ременная передача; 3- редуктор; 4- муфта; 5- барабан.
Окружная сила на барабанеР = 8 кН;
Скорость движения ленты транспортераV = 01 мс;
Выбор электродвигателя. Определение вращающих моментов и скоростей на валах редуктора
1Выбор электродвигателя
Требуемая мощность (Вт) электродвигателя:
где F – окружная сила на барабане V – скорость длины ленты транспортёра - общий КПД привода.
где - КПД ремённой передачи - КПД конической передачи - КПД цилиндрической передачи - КПД подшипников - КПД муфты.
Исходя из полученных данных выбираем электродвигатель со следующими техническими параметрами:
электродвигатель АИР 90 LB8 ТУ 16-525.564-84
Синхронная частота вращения n=715 обмин.
Частота вращения приводного вала рабочей машины (число оборотов на выходе):
обмин где - диаметр барабана.
Передаточное число привода:
2Определение вращающих моментов и скоростей на валах редуктора
Расчёт моментов на валах:
Расчёт зубчатых колёс редуктора
1Выбор материала и термической обработки. Допускаемые напряжения.
Так как в задании нет особых требований в отношении габаритов передачи выбираем материалы со средними механическими характеристиками. Для шестерен принимаем сталь 45 улучшенную с твердостью НВ 262; для колес сталь 45 улучшенную с твердостью НВ 235.
Твёрдость допускаемые контактные напряжения и напряжения изгиба:
Среднее допускаемое контактное напряжение:
2Расчёт зубчатой цилиндрической передачи
Коэффициент ширины зубчатого колеса при несимметричном расположении: . Коэффициент ширины в долях диаметра: .
Коэффициент неравномерности распределения нагрузки:
Межосевое расстояние:
Округлим до стандартного значения: .
Нормальный модуль зацепления: . Принимаем стандартный .
Минимальный угол наклона зубьев: .
Суммарное число зубьев: .
Действительное значение угла наклона зубьев: .
Количество зубьев шестерни: ; .
Количество зубьев колеса: .
Делительные диаметры шестерни и колеса:
Диаметры вершин зубьев:
Диаметры впадин зубьев: Рис. 2. – Схема зубьев.
Окружная скорость колёс:
. Степень точности передачи 9.
2.2Расчёт сил в зацеплении
Рис. 3. – Силы действующие в зацеплении.
2.3Проверочный расчёт передачи
Проверка зубьев по контактным напряжениям.
Значения коэффициентов ; ; .
Расчётное контактное напряжение:
Так как то условие прочности по контактным напряжениям выполнено.
Проверка зубьев по напряжениям изгиба.
Коэффициенты: ; ; ; ; ; .
Расчётное напряжение изгиба в зубьях колеса: что меньше .
Расчётное напряжение изгиба в зубьях шестерни: что меньше .
Таким образом прочность на изгиб зубьев колёс обеспечена.
3Расчёт конической зубчатой передачи
Диаметр внешней делительной окружности колеса при : принимаем .
Углы делительных косинусов конусное расстояние и ширина колёс. Угол делительного конуса колеса: ; .
Угол делительного конуса шестерни: ; .
Конусное расстояние: .
Ширина колёс: принимаем
Модуль передачи. Коэффициенты: ; .
Внешний торцевой модуль передачи: .
Число зубьев колёс: ; .
Фактическое передаточное число: . Отклонение: что меньше 4%.
Окончательные размеры колёс. Углы делительных косинусов колеса и шестерни: ; ; ; ; .
Делительные диаметры колёс: ; .
Коэффициенты смещения: ; .
Внешние диаметры колёс: ; .
3.2Расчёт сил в зацеплении
Окружная сила на среднем диаметре колеса: ; ; .
Осевая сила на шестерне: .
Радиальная сила на шестерни: .
Осевая сила на колесе: .
Радиальная сила на колесе: .
Рис. 4. – Силы действующие в зацеплении.
3.3Проверочный расчёт передачи
Проверка зубьев по напряжениям изгиба. Коэффициенты: ; ; ; ; ; .
Напряжения изгиба в зубьях колеса: .
Напряжения изгиба в зубьях шестерни: .
Расчётные напряжения в зубьях колеса и шестерни меньше допускаемых .
Проверка зубьев по контактным напряжениям. что меньше допускаемых напряжений .
Конструирование зубчатых колёс
1Цилиндрическое колёсо
Рис. 5 – Зубчатое цилиндрическое колесо.
Рис. 6 – Зубчатое коническое колесо.
Рис. 7 – Ведущий вал-шестерня.
Диаметр выходного конца вала рассчитывается по следующей формуле . Примем . Последующие диаметры вала больше предыдущих примерно в 11 раза: ; .
Диаметр подшипника является стандартным поэтому выбираем его из справочника соответственно . Внешний диаметр шестерни: .
Длины различных участков вала:
Н – ширина шлицевой гайки.
. Расстояние между подшипниками: . Ширина мазеудерживающего кольца: . .
1.1Определение реакций опор в подшипниках
Рис. 8 – Схема нагруженного ведущего вала.
Отрезки a b c d соответственно равны 48мм 96мм 29мм 30мм.
Для определения реакций в опорах и необходимо составить уравнения равновесия.
. Сила от ремённой передачи .
Аналогично находим и .
1.2Построение эпюр изгибающих моментов и вызванных ими напряжений
Рис. 9 – Эпюр изгибающих моментов и напряжений на валу.
1.3Исследование опасных сечений
Исследование сечения А-А. Напряжения в опасных сечениях .
Коэффициенты концентрации напряжений для данного сечения вала: ; .
Пределы выносливости вала в рассматриваемом сечении: ; .
Коэффициенты запаса по нормальным и касательным напряжениям: ; .
Коэффициент запаса прочности: что больше допускаемого значения.
Исследование сечения Б-Б. Напряжения в опасных сечениях .
Исследование сечения В-В. Напряжения в опасных сечениях .
1.4Проверка долговечности подшипников
Ведущий вал установлен на роликовых конических подшипниках лёгкой серии.
Рис.10. – Схема нагружения подшипников вала.
Определяем долговечность подшипника наиболее нагруженной опоры «1». Необходимые справочные данные: грузоподъёмность ; факторы нагрузки ; коэффициент .
Осевые нагрузки. Суммарная реакция . Осевая составляющая ; осевая сила .
Эквивалентная динамическая радиальная нагрузка: где - коэффициент вращения; - коэффициент безопасности; - температурный коэффициент.
Базовая долговечность подшипника: ; что соответствует допускаемой минимальной долговечности (ресурс работы подшипников принимают от 36000 ч до 10000 ч).
Рис. 11 – Промежуточный вал.
Диаметры различных участков вала. Диаметр на промежуточном валу должен быть на 25% больше чем на ведущем валу поэтому . Последующие диаметры больше предыдущих примерно в 11 раза: ; ; .
Расстояние между подшипниками .
2.1Определение реакций опор в подшипниках
Рис. 12 – Схема нагруженного промежуточного вала.
Отрезки a b c d e соответственно равны 20мм 105мм 85мм 77мм 20мм.
2.2Построение эпюр изгибающих моментов и вызванных ими напряжений
Рис. 13 – Эпюры изгибающих моментов и напряжений на валу.
2.3Исследование опасных сечений
2.4Проверка долговечности подшипников
Промежуточный вал установлен на роликовых конических подшипниках лёгкой серии.
Рис.14 – Схема нагружения подшипников вала.
Определяем долговечность подшипника наиболее нагруженной опоры «2». Необходимые справочные данные: грузоподъёмность ; факторы нагрузки ; коэффициент .
Эквивалентная динамическая радиальная нагрузка: где V=1 - коэффициент вращения; - коэффициент безопасности; - температурный коэффициент.
Рис. 15 – Ведомый вал.
Диаметры различных участков вала. Диаметр на промежуточном валу должен быть на 25% больше чем на промежуточном валу поэтому принимаем . Последующие диаметры больше предыдущих примерно в 11 раза: ; ; ; .
Длины различных участков вала:
3.1Определение реакций опор в подшипниках
Рис. 16 – Схема нагруженного ведомого вала.
Отрезки a b c d соответственно равны 22мм 194мм 77мм 140мм.
3.2Построение эпюр изгибающих моментов и вызванных ими напряжений
Рис. 17 – Эпюры изгибающих моментов и напряжений на валу.
3.3Исследование опасных сечений
3.4Проверка долговечности подшипников
Рис.18 – Схема нагружения вала.
4Проверка прочности шпоночных соединений
Материал шпонок - сталь 45 нормализованная.
Напряжения смятия и условие прочности: .
Напряжения среза и условие прочности: .
Допускаемые напряжения смятия при стальной ступице []см = 100 ÷ 120 при чугунной ступице []см = 50 ÷ 70 . При этом допускаемые напряжения среза .
Прочность обеспечена.
Проверим шпонку под зубчатым колесом.
Прочность не обеспечена поэтому необходимо поставить ещё одну шпонку.
Из двух шпонок более нагружена та которая на конце вала так как меньше диаметр вала и поэтому меньше размеры поперечного сечения шпонки.
Рис. 19 – Шпоночное соеденение.
Конструирование стаканов и крышек подшипников
1Конструирование стакана
Стакан выполнен литым из чугуна марки СЧ15. Диаметр под подшипник отсюда принимаем толщину стенки . Толщина фланца . Высота упорного буртика . Диаметр d принимаем равным 8мм а число винтов для крепления к корпусу равно 8. Принимая получаем минимальный размер фланца стакана.
2Конструирование крышек подшипников
Рис. 21 – а) крышка подшипника сквозная; б) крышка подшипника глухая.
Крышки подшипников изготовлены из чугуна марки СЧ21.
Размеры сквозной и глухой крышек на ведомом валу: ; ; ; количество винтов для крепления к корпусу ; ; толщина фланца ; ; .
Конструирование корпусных деталей
Рис. 22 – Корпус редуктора.
Корпус выполнен из чугуна марки СЧ15. Толщина стенки корпуса определяется по следующей формуле принимаем . Зазор между стенками корпуса и поверхностями колёс – ; . Диаметр фланца где – наружный диаметр крышки подшипника; ; .
Толщина фланцев поясов корпуса и крышки: ; нижний пояс корпуса: .
Толщина ребер основания корпуса: m = (085 ÷ 1) = 85 ÷ 10 мм; принимаем m = 9 мм.
Толщина ребер крышки:.
Фундаментных принимаем болты с резьбой М24;
крепящих крышку к корпусу у подшипников ; принимаем болты с резьбой М16;
соединяющих крышку с корпусом принимаем болты с резьбой М12.
Смазывание зубчатых передач
Учитывая рекомендуемую вязкость масла для смазывания зубчатых передач выбираем следующую марку масла: индустриальное И-30А. Оба колеса редуктора должны быть погружены в масло. Уровень погружения конического колеса в масло: .
Дунаев П.Ф. Леликов О.П. Конструирование узлов и деталей машин.
Дунаев П.Ф. Леликов О.П. Детали машин. Курсовое проектирование.
Чернавский С.А. Курсовое проектирование деталей машин.
Шейнблит А.Е. Курсовое проектирование деталей машин.
Курсовое проектирование деталей машин: методические указания по дисциплине «Детали машин».