Раздаточная коробка передач газ 66




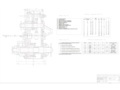
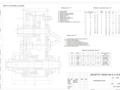
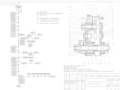
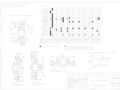
- Добавлен: 25.10.2022
- Размер: 6 MB
- Закачек: 2
Описание
Состав проекта
![]() |
![]() |
![]() ![]() ![]() ![]() |
![]() ![]() ![]() ![]() |
![]() ![]() ![]() ![]() |
![]() ![]() ![]() ![]() |
![]() |
![]() ![]() ![]() |
![]() ![]() ![]() |
![]() ![]() ![]() |
![]() ![]() ![]() |
Дополнительная информация
Схема сборки.dwg

КП-НГТУ-190201-06-А-3-81.004
Вал передних и задних колес в сборе
Крышка корпуса в сборе
К- Контроль ТО-Техническое обслуживание О- Обкатка
- резьбовое соединение
- соединение с натягом
- шлицевое соединение
- Свободное соединение
Затяжку деталей производить с Мкр Поз. 52
200 Нм Гайки Поз. 35
кернить после затяжки
Соединения с натягом производятся при помощи оправки.
Шлицевые соединения фланцев Поз. 30
смазать смазкой Литол-24 ГОСТ 21150-87
Раздатка газ 66.dwg

Таблица 1 решение цепи "A
Раздаточная коробка передач. Сборочный чертеж
КП-НГТУ-190201-02-А-2-45-2006
Схема обработки.dwg

- двойная опорная технологическая база (явная)
- вторая опорная технологическая база (скрытая)
- установочная технологическая база (явная)
Схема нумерации поверхностей
Граф конструкторских размеров в осевом сечении
КП-НГТУ-190201-06-А-3-81.002
Размерный анализ.dwg

Таблица 1 решение цепи "A
КП-НГТУ-190201-06-А-3-18.001
3. СБОРКА.doc
1.Анализ конструкции и классификация соединений изделия
Рисунок 3.1Сборочный чертеж раздаточной коробки
Раздаточная коробка показанная на рисунке 3.1 предназначена для распределения крутящего момента между осями автомобиля посредством включения пониженной и повышенной передачи а также использования планетарного дифференциала с возможностью блокировки.
Рисунок 3.2Укрупненная схема сборки
На основе укрупненной схемы сборки производится анализ соединений сборочных единиц.
Все соединения раздаточной коробки можно разбить на группы:
Гладкие цилиндрические с зазором;
Гладкие цилиндрические с натягом;
Гладкие цилиндрические соединения с натягом образованы шариковыми и роликовыми подшипниками которые устанавливаются на первичный вторичный и выходные валы. Сборка таких соединений производится на специальных стендах - прессах. Перед сборкой подшипник должен быть очищен от защитной смазки грязи и посторонних частиц. Для этого их тщательно промывают в 6%-ном растворе минерального масла в бензине или в горячих (70-75 С) антикоррозионных водных растворах. После промывки подшипник проверяют на легкость вращения. При внешнем осмотре не должно быть обнаружено на подшипниках качения и посадочных поверхностях корпусов и валов следов коррозии. На этих поверхностях не допускаются забоины задиры царапины. Для дополнительной фиксации подшипников используют закрепление посредством резьбового соединения гайкой и стопорением резьбы. После установки подшипника на вал проверяют фактическую величину радиального зазора в подшипнике.
Гладкие цилиндрические соединения с зазором образуются различными деталями такими как стаканы крышки и другие детали которые предусматривают частую разборку и сборку которая производится вручную.
К резьбовым соединениям предъявляют особые требования. Затяжка болтов раздаточной коробки производится в строго определенной последовательности крест накрест в три подхода с постепенным увеличением момента затяжки на треть от максимального значения. Затяжку этих болтов необходимо производить с Мкр от 200 до 250 Нм. Технические требования по затяжке по ОСТ 37.001.031 – 72.
Сборку шлицевых соединений производят методом полной взаимозаменяемости и методом подбора. Сборке предшествует тщательная очистка сопрягаемых деталей их контроль и внешний осмотр на предмет выявления дефектов поверхностей (забоин вмятин и др.). При сборке сборочной единицы дифференциала 16 ступицы выходных валов должны перемещаться по валу плавно без заеданий и приложения больших усилий. Контроль на биение производится индикатором в центровых бабках или на призмах. Остальные части раздаточной коробки которые устанавливаются по неподвижным шлицевым посадкам должны устанавливаться без приложения дополнительных усилий со стороны рабочего.
Сборку шпоночных соединений осуществляют с предварительной запрессовкой шпонок на валы с использованием пресса и оправки. После операции запрессовки следует контрольная операция расположения шпонки на валу с использованием соответствующих измерительных средств – калибров расположения.
На основании анализа сборочного чертежа механизма устанавливаем все типы соединений применяемых в сборочной единице. Результаты анализа представим в виде таблицы 3.1.
Таблица 3.1Классификация соединений сборочной единицы
Гладкое цилиндрическое
2.Образование сборочных соединений
Сборочные соединения формируются в процессе выполнения определенных действий направленных на формирование точности соединения и его надежности:
Установка подшипников на валы требует применения пресса для напрессовывания подшипника это сопровождается следующими действиями:
- промыть подшипник в керосине если подшипник без уплотнений;
- необходимо очистить сопрягаемые поверхности от грязи смазать маслом поверхности контакта для уменьшения трения;
- наживить подшипник выровняв его по заходной фаске вала;
- произвести прессование;
- проконтролировать радиальное и торцовое биение вала и положение подшипника на валу.
Установка шпонки 58 в вал 21: требуется запрессовка с контролем правильности запрессовки шаблоном.
Сборка подшипника на валу 8:
- нанести густую смазку на поверхность вала;
- распределить равномерно ролики в смазке;
- установить ступицу на подшипник.
Установка зубчатого колеса 4 на вал 2:
- очистить поверхности контакта;
- охладить вал в жидком азоте либо искусственном льде что приводит к уменьшению диаметра вала и в отличие от нагревания устанавливаемой шестерни не приводит к разупрочнению детали под воздействием нагрева.
Ввинчивание болтов и винтов:
- наживить крепежный элемент;
- окончательно затянуть использую ключи с контролем момента затяжки или гайковерты со встроенными муфтами.
3.Разработка последовательности сборки
Базовая деталь изделия – корпус 48
Вал выходной 20 в сборе;
Вал входной 1 в сборе;
Дифференциал 16 в сборе;
Вал промежуточный 2 в сборе.
Отдельные детали изделия: болты крышки зубчатые колеса прокладки.
Стандартные изделия: подшипники манжеты стопорные кольца болты.
Схема сборки раздаточной коробки представлена на отдельном чертеже.
При выполнении определенных операций в процессе сборки раздаточной коробки необходима некоторая подготовка сборочных единиц а также проведение дополнительных операций которые влияют на качество сборки:
Все детали раздаточной коробки должны быть смазаны толстым слоем солидола или консталина.
При сборке прокладки и крепежные болты необходимо смазать тонким слоем пасты «герметик».
Описание содержания контрольных операций:
Контроль подшипников. После установки подшипника на вал проверяют фактическую величину радиального зазора в подшипнике с помощью индикаторного приспособления.
Контроль затяжки болтовых соединений. Требуемая затяжка резьбовых соединений обеспечивается ограничением крутящего момента. При использовании механизированных инструментов (электрических или пневматических гайковертов) заданный момент затяжки обеспечивают муфтами тарирования реле тока самоостановкой двигателя в конце затяжки и другими способами.
Контроль биения венцов зубчатых колес. Контроль на биение производится индикатором в контрольном приспособлении.
После сборки всей раздаточной коробки необходимо провести его испытания на специальном испытательном стенде при этом:
Не должно быть шума при работе раздаточной коробки.
Герметичность раздаточной коробки то есть отсутствие течи масла из раздаточной коробки.
Рисунок 3.1Схема сборки раздаточной коробки
Таблица 3.2Описание сборочных операций раздаточной коробки
Контрольный инструмент
Напрессовать подшипник 51 на выходной вал 20
Установить втулку 49 на выходной вал 20
Напрессовать подшипник 50 на выходной вал 20
Установить стакан 52 на подшипники 50 и 51
Запрессовать манжету 54 в крышку 53
Установить крышку 53 в сборе на выходной вал 20
Напрессовать кольцо 56 на фланец 55
Установить фланец 55 в сборе на выходной вал 20
Установить муфту 19 на выходной вал 20
Запрессовать шпонку 58 в входной вал 1
Запрессовать зубчатое колесо 60 на входной вал 59
Установить зубчатое колесо 59 в сборе на входной вал 1
Напрессовать подшипник 25 на входной вал 1
Установить входной вал 1 в сборе в корпус 48
Установить вал промежуточный 2 в сборе в корпус 48
Установить дифференциал 16 в сборе в корпус 48
Завинтить пробку 63 в крышку 61
Муфта момента срабатывания
Установить крышку 63 в сборе в корпус 48
Запрессовать подшипник 23 в стакан 27
Запрессовать подшипник 43 в стакан 27
Запрессовать манжету 64 в крышку 26
Установить крышку 26 в сборе на стакан 27
Завинтить четыре болта 65 в корпус 48
4.Выбор оборудования и технологической оснастки
Перечень оборудования необходимого в процессе сборки зависит от типа производства и может быть представлено в следующем виде:
Сборочное оборудование:
- конвейер для перемещения собираемых узлов;
- пневматические гидравлические и электромеханические шуроповерты и гайковерты для закручивания гаек и болтов с требуемым моментом затяжки;
- пневматические гидравлические и электромеханические шпильковерты которые позволяют осуществлять как наживление шпилек так и их окончательное ввертывание при этом важно недопустить перекоса шпилек в процессе их ввинчивания что достигается использованием специальных самоустанавливающихся устройств в конструкции шпильковертов;
- прессы для напрессовывания и выпрессовывания различных деталей устанавливаемых по плотной посадке с натягом;
- печи для нагревания деталей для уменьшения силы запрессовки;
- холодильники для охлаждения деталей с той же целью (CO2).
Технологическая оснастка:
Контрольные приспособления:
- измерители уровня шума;
- эталонные узлы механизма для контроля зацеплений и щума;
- специализированные и специальные контрольные приспособления для контроля положения зубчатых колес друг относительно друга.
СПИСОК ИСПОЛЬЗОВАННОЙ ЛИТЕРАТУРЫ
В. Н. Тимофеев Методика расчета размерных цепей. Учебное пособие для студентов механического и машиностроительного факультетов. – Горький 1963 г.
Нормирование точности изделий машиностроения: Учеб. пособие В. Н. Кайнова Г. И. Лебедев С. Ф. Магницкая и др. Под ред. В. Н. Кайновой; НГТУ. Н.Новгород 2007. – 209 с.
Горбацевич А. Ф. Шкред В. А. Курсовое проектирование по технологии машиностроения: [Учеб. пособие для машиностроит. спец. вузов] – 4-е изд. перераб. и доп. – М: Высш. школа 1983 г.
Справочник технолога-машиностроителя. В 2-х томах. Т.1Под ред. А. Г. Косиловой и Р. К. Мещерякова – М: Машиностроение 1986.
Справочник технолога-машиностроителя. В 2-х томах. Т.2Под ред. А. Г. Косиловой и Р. К. Мещерякова – М: Машиностроение 1986.
Дипломное проектирование по технологии машиностроения: [Учеб. пособие для вузов В. В. Бабук П. А. Горезко К. П. Забродин и др.] Под общей ред. В. В. Бабука. – М: Высш. школа 1979 г.
2. Технологический процесс.doc
Требования к качеству обработанных поверхностей детали назначаются в зависимости от точности обработки этих поверхностей от условий эксплуатации сборочной единицы или механизма и от назначения поверхностей детали. Назначая технические требования к качеству обработки необходимо анализировать каждую обрабатываемую поверхность отдельно.
Рисунок 1.6Схема нумерации поверхностей
В первую очередь разрабатываются требования к качеству обработки тех поверхностей на которые будут устанавливаться отдельные стандартные детали или сборочные единицы (шпонки зубчатые колеса подшипники). Качество обработки этих поверхностей регламентировано соответствующими ГОСТами. Поэтому технические требования к качеству обработки этих поверхностей (шероховатость твердость и др.) определяем по стандартам.
Посадочная поверхность вала под подшипник – поверхности 4 (Ra=08);
Торцы вала для упора подшипника – поверхность 12 (Ra=16);
Поверхности прямобочных шлиц – поверхность 5 (наружный диаметр вала) (Ra=08);
Поверхности прямобочных шлиц – поверхность 5 (боковая поверхность шлиц) (Ra=16).
Затем назначают технические требования к качеству обработки поверхностей точность которых установлена расчетом размерных цепей:
- линейный размер мм;
- отклонение от соосности наружной цилиндрической поверхности (НЦП) шлиц относительно посадочной поверхности под подшипник (база А): 001 мм.
На остальные поверхности детали требование к качеству обработанной поверхности можно назначить конструктивно исходя из служебного назначения поверхности.
Параметры шероховатости конструктивно можно определить из следующих соотношений:
На основании проведенных расчетов составим таблицу 1.3.
Таблица 1.3Качество обработки поверхностей детали
Геометрическая форма и поле допуска
Параметры точности поверхности
Параметры качества обр. поверхности
Продолжение таблицы 1.3
Обозначения:— отклонения по ГОСТ 30893 Общие допуски;
НЦП – наружная цилиндрическая поверхность;
НТП – наружная торцовая поверхность;
НКП – наружная канавка;
ШП – шлицевая поверхность;
ВЦП – внутренняя цилиндрическая поверхность (отверстие);
РП – резьбовая поверхность.
ПРЕКТИРОВАНИЕ ТЕХНОЛОГИЧЕСКОГО ПРОЦЕССА МЕХАНИЧЕСКОЙ ОБРАБОТКИ ВЫХОДНОГО ВАЛА РАЗДАТОЧНОЙ КОРОБКИ
Чертеж детали (по результатам расчетов в разделе 1 курсового проекта);
Программа выпуска N=120000:
Тип производства – крупносерийный (mдет = 09 кг).
1.Анализ технологичности детали
Деталь – выходной вал коробки передач изготовлен из легированной стали 40Х ГОСТ 4543-71 и проходит термическую обработку. С точки зрения температурных деформаций возможных при нагревании и охлаждении детали вал является технологичной деталью так как возможные деформации не приведут к значительным нежелательным изменениям.
В отношении механической обработки вал можно считать также технологичным. Большинство поверхностей обрабатывается за одну установку в патроне с поджимом задним центром что говорит о возможности применения высокопроизводительных методов обработки и сборки тем самым обеспечить минимальную себестоимость.
Количественная оценка технологичности детали.
На основании анализа чертежа детали рассчитывают количественные показатели технологичности в соответствии с ГОСТ 18831-73.
) Уровень технологичности по точности обработки:
где - средний квалитет точности обрабатываемых поверхностей.
- квалитеты точности;
- число размеров соответствующего класса точности.
Так как коэффициент точности больше 08 то по данному показателю деталь является технологичной.
) Уровень технологичности по шероховатости поверхностей:
где - средняя шероховатость поверхностей прошедших механическую обработку;
- классы шероховатости;
- количество поверхностей соответствующего класса шероховатости.
Так как коэффициент шероховатости меньше 032 то по данному показателю деталь является технологичной.
Вывод: по количественным показателям выходной вал является технологичным изделием и значит к нему можно применить высокотехнологичные методы обработки (параллельная обработка нескольких поверхностей).
2.Выбор способа получения заготовки
Способ получения заготовки выбирается базируясь на типе производства технологичности детали и материале из которого делается деталь.
Существуют два основных способа получения заготовки для выходного вала:
С помощью горячей ковки;
Производством из сортового горячекатаного проката.
Конструкция заготовки является технологичной так как все поверхности имеют простую форму. Материал заготовки не играет большой роли при сравнении этих способов производства. Учитывая что производство детали крупносерийное основную роль играет минимальный объем механической обработки резанием. При получении заготовки с помощью горячей ковки припуски назначаются на все поверхности. В случае получения заготовки из сортового проката припуск назначается только на поверхность наибольшего диаметра и при дальнейшей механической обработке поверхностей меньшего диаметра мы будем иметь большое количество металла в отходах.
Критерием выбора способа получения заготовок в курсовом проекте может служить упрощенный коэффициент использования металла :
где - масса готовой детали;
Тогда после расчета масс заготовок получаем:
- для сортового проката;
В нашем случае заготовку экономичнее производить с помощью горячей ковки. Припуски и допуски на поковки из легированных сталей при ковке на молотах устанавливаются по ГОСТ 7829-70.
3.Проектирование технологического процесса механической обработки
3.1.Проектирование технологического процесса механической обработки
В соответствии с рисунком 1.6 поверхности подразделяются на следующие группы:
I группа – наружные цилиндрические поверхности: 1 2 3 4 5 6;
II группа – плоские поверхности (торцы): 9 10 11 12 13 14;
III группа – поверхность прямобочных шлиц: 5;
IV группа – внутренние цилиндрические поверхности: 16 17;
V группа – фаски: 7 8 18;
VI группа – резьбовая поверхность: 6.
3.2.Разработка планов механической обработки поверхностей детали
Планы механической обработки разрабатываются на основании проведенной классификации поверхностей детали с целью определения технологических методов которые необходимо применить для достижения заданного качества обработки (точности обработки и качества обработанной поверхности). Это определение носит предварительный характер и подлежит уточнению.
3.2.1.План обработки наружных цилиндрических поверхностей
Таблица 2.1Планы обработки наружных цилиндрических поверхностей
Технологический метод
Шлифование предварительное
Точение получистовое
Точение предварительное
3.2.2.План обработки плоских поверхностей (торцов)
Таблица 2.2Планы обработки плоских поверхностей
Торцевые поверхности 19 14 а также центровое отверстие 17 с фаской 8 обрабатываются на фрезерно-центровальной операции.
3.2.3.План обработки шлицевых поверхностей
Таблица 2.3План обработки шлицевых поверхностей
Фрезерование получистовое
Фрезерование черновое
Точение чистовое (см. пов. 5 в табл. 2.1)
Точение получистовое (пов. 5)
Точение предварительное (пов. 5)
3.2.4.План обработки внутренних цилиндрических поверхностей
Таблица 2.4План обработки внутренних цилиндрических поверхностей
Зенкерование получистовое
Сверление предварительное
3.2.5.План обработки резьбовых поверхностей
Таблица 2.5План обработки резьбовых поверхностей
3.3.Разработка основных схем базирования для обработки типовых поверхностей
Комплект технологических баз состоит из трех баз необходимых для полной ориентации заготовки в пространстве каждая из которых определяется как элементарная технологическая база.
Рисунок 2.1Схема базирования №1 на фрезерно-центровочной операции
При использовании такой схемы базирования обрабатываются торцовые поверхности 9 14 сверлится центровочное отверстие 17 и фаска 8. Схема базирования может реализовываться в виде двух сходящихся призм что обеспечивает центрирование заготовки в процессе подготовки технологических баз.
Комплект технологических баз:
2 3 4 – двойная направляющая технологическая база;
– опорная технологическая база;
– вторая опорная (неявная) технологическая база.
Рисунок 2.2Схема базирования №2 на токарных шлифовальных и фрезерных операциях с одной стороны
При использовании такой схемы базирования обрабатываются наружные цилиндрические поверхности 2 3 4 5 6 торцы 11 12 13 фаски 7 18 резьба 6 а также фрезеруются и шлифуются шлицы 5.
Рисунок 2.3Схема базирования №3 на токарных и шлифовальных операциях с другой стороны
При использовании такой схемы базирования обрабатываются наружная цилиндрическая поверхность 1 и торец 10.
Рисунок 2.4Схема базирования №4 на сверлильных операциях
При использовании такой схемы базирования обрабатываются отверстия 15 16.
– опорная (неявная) технологическая база.
На рисунках представлены схемы базирования заготовки для обработки на фрезерно-центровочном станке фрезерном сверлильном станке и на токарно-многорезцовом полуавтомате. На шлифовальных операциях применяется аналогичная схема базирования.
За основную технологическую базу принимаем ось центров.
3.4.Разработка содержания технологических операций
Под содержанием технологической операции понимается количество поверхностей и связанных с ними размеров которые могут быть получены на данной операции с применением соответствующего комплекта технологических баз.
Весь технологический процесс состоящий из чередующихся друг за другом операций делится в основном на три основные части: обработка на станках фрезерно-токарной группы термическую обработку и абразивную обработку.
Первая часть является предварительной и предназначена для образования геометрической формы и размеров.
Термообработка позволяет улучшить физико-механические свойства детали необходимые для эксплуатации.
Абразивная обработка является заключительным этапом механической обработки. На ней окончательно формируется точность обработки и качество обработанной поверхности.
Рисунок 2.4Схема последовательности обработки детали
Теперь рассмотрим каждую операцию более подробно.
Предварительная обработка
) Формирование основной технологической базы: подрезание торцов 9 14 сверление центрового отверстия 17 и фаски 8. Станок: фрезерно-центровочный полуавтомат 2Г942. Комплект технологических баз №1 (рис. 2.1).
) Черновое точение наружных цилиндрических поверхностей 2 4 5 6 продольным суппортом и канавки 3 торцов 11 12 13 поперечным суппортом. Станок: одношпиндельный токарно-многорезцовый полуавтомат 1716Ц. Комплект технологических баз №2 (рис. 2.2).
) Черновое точение наружной цилиндрической поверхности 1 продольным суппортом и торца 10 поперечным суппортом. Станок: одношпиндельный токарно-многорезцовый полуавтомат 1716Ц. Комплект технологических баз №3 (рис. 2.3).
Получистовая обработка
) Получистовое точение наружных цилиндрических поверхностей 2 4 5 6 продольным суппортом и канавки 3 фасок 7 18 торцов 11 12 13 поперечным суппортом. Станок: одношпиндельный токарно-многорезцовый полуавтомат 1716Ц. Комплект технологических баз №2 (рис. 2.2).
) Получистовое точение наружной цилиндрической поверхности 1 продольным суппортом и торца 10 поперечным суппортом. Станок: одношпиндельный токарно-многорезцовый полуавтомат 1716Ц. Комплект технологических баз №3 (рис. 2.3).
) Чистовое точение наружных цилиндрических поверхностей 4 5 продольным суппортом и торца 12 поперечным суппортом. Станок: одношпиндельный токарно-многорезцовый полуавтомат 1716Ц. Комплект технологических баз №2 (рис. 2.2).
) Чистовое точение наружной цилиндрической поверхности 1 продольным суппортом и торца 10 поперечным суппортом. Станок: одношпиндельный токарно-многорезцовый полуавтомат 1716Ц. Комплект технологических баз №3 (рис. 2.3).
Нарезание прямобочных шлиц
) Фрезерование черновое поверхности 5.
) Фрезерование получистовое поверхности 5.
Станок: фрезерный 5А252ПФ2. Комплект технологических баз №2 (рис. 2.2).
) Предварительное сверление трех отверстий 15 и центрального отверстия 16. Станок: вертикально-сверлильный станок 2Н135. Комплект технологических баз №4 (рис. 2.1).
) Получистовое зенкерование трех отверстий 15 и центрального отверстия 16. Станок: вертикально-сверлильный станок 2Н135. Комплект технологических баз №4 (рис. 2.1).
) Нарезание резьбы на поверхности 6. Станок: резьбонарезной полуавтомат 5993П. Комплект технологических баз №2 (рис. 2.2).
Закалка + высокий отпуск. Твердость 40 HRC.
Предварительное шлифование
) Предварительное шлифование наружных цилиндрических поверхностей 4 5 и торца 12. Станок: круглошлифовальный 3М153ДФ2. Комплект технологических баз №2 (рис. 2.2).
) Предварительное шлифование наружной цилиндрической поверхности 1 и торца 10. Станок: круглошлифовальный 3М153ДФ2. Комплект технологических баз №3 (рис. 2.3).
) Предварительное шлифование шлицевой поверхности 5. Станок: шлицешлифовальный 3В451ВФ20. Комплект технологических баз №2 (рис. 2.2).
) Чистовое шлифование наружных цилиндрических поверхностей 4 5. Станок: круглошлифовальный 3М153ДФ2. Комплект технологических баз №2 (рис. 2.2).
) Чистовое шлифование наружной цилиндрической поверхности 1. Станок: круглошлифовальный 3М153ДФ2. Комплект технологических баз №3 (рис. 2.3).
) Чистовое шлифование шлицевой поверхности 5. Станок: шлицешлифовальный 3В451ВФ20. Комплект технологических баз №2 (рис. 2.2).
3.5.Разработка последовательности обработки детали (маршрутного технологического процесса)
Маршрутный технологический процесс разрабатывается на основании установленной последовательности выполнения операций с подробным описанием содержания операций выбором технологического оборудования и технологической оснастки.
Технологическая схема обработки вала представлена на отдельном чертеже в приложении к пояснительной записке.
4.Расчет припусков на механическую обработку
Припуски на обработку и операционные размеры определяются для одной наиболее точно обрабатываемой поверхности. Такой поверхностью примем поверхность 4 – посадочная поверхность под подшипник. Выполним расчет для поверхности 4 - . На остальные обрабатываемые поверхности назначим припуски и допуски по таблицам ГОСТ 7829-70.
Заготовка – поковка полученная на молоте ковочном пневматическом. Класс точности – 1-ый.
Технологический маршрут обработки поверхности состоит из чернового получистового чистового точения и шлифования предварительного и чистового и записывается в расчетную таблицу 2.6.
Так как обработка поверхности ведется в центрах то погрешность установки в радиальном направлении равна нулю. В этом случае эта величина исключается из основной формулы для расчета минимального припуска.
Рисунок 2.5План обработки поверхности 4 выходного вала
Определяем суммарное отклонение расположения при обработке заготовок круглого сечения в центрах:
где - общее отклонение расположения заготовки мкм;
- отклонение расположения заготовки при зацентровке мкм;
- отклонение оси детали от прямолинейности мкм на 1мм (удельная кривизна заготовки);
- расстояние от сечения для которого определяем величину отклонения расположения до места крепления заготовки мм;
- общая длина заготовки мм.
- допуск на диаметральный размер базы заготовки использованной при центрировании мм.
Определяем величину остаточного отклонения расположения заготовки
для промежуточных этапов обработки:
где - коэффициент уточнения;
- суммарное отклонение расположения заготовки;
мкм – после чернового обтачивания;
мкм – после получистового обтачивания;
мкм – после чистового обтачивания;
мкм – после предварительного шлифования.
Расчет минимальных значений припусков при обработке наружных и внутренних цилиндрических поверхностей (двусторонний припуск) определяется по следующей формуле:
где - высота микронеровностей поверхности которая осталась после выполнения предшествующего перехода;
- глубина дефектного поверхностного слоя оставшегося при выполнении предшествующего перехода;
- суммарные отклонения расположения поверхности и отклонения формы возникающие при выполнении предшествующего перехода;
- погрешность при установке на выполняемом переходе.
так как обработка ведется в центрах.
Минимальный припуск на черновое точение:
Минимальный припуск на получистовое точение:
Минимальный припуск на чистовое точение:
Минимальный припуск на предварительное шлифование:
Минимальный припуск на чистовое шлифование:
Определяем значения максимальных припусков на каждом этапе обработке для случая двухстороннего припуска по следующей формуле:
где - допуски размеров на предшествующем переходе;
- допуски размеров на выполняемом переходе.
Максимальный припуск на черновое точение:
Максимальный припуск на получистовое точение:
Максимальный припуск на чистовое точение:
Максимальный припуск на предварительное шлифование:
Максимальный припуск на чистовое шлифование:
Определяем номинальные значения припусков по следующей формуле:
Номинальный припуск на черновое точение:
Номинальный припуск на получистовое точение:
Номинальный припуск на чистовое точение:
Номинальный припуск на предварительное шлифование:
Номинальный припуск на чистовое шлифование:
Определяем предельные межпереходные размеры и окончательные размеры заготовки по следующим формулам:
Максимальные размеры
Таблица 2.6Расчет припусков и предельных размеров по технологическим переходам на обработку поверхности 4 - входного вала редуктора
Параметры Zimin (мкм)
Номинальное значение размера с отклонениями
Предварительное точение
Получистовое точение
5.Расчет режимов резания
Расчет режимов резания и подсчет штучного времени обработки производим для двух операций. При назначении элементов режима резания учитывают характер обработки тип и размеры инструмента материал его режущей части материал и состояние заготовки тип и состояние оборудования.
5.1 Произведем расчет режимов резания на операцию предварительного точения для поверхности 4 .
Станок – одношпиндельный токарно-многорезцовый полуавтомат 1716Ц.
Поверхность должна быть обработана по 14–му квалитету.
Припуск на механическую обработку 222 мм.
Режущий инструмент: токарные проходные отогнутые резцы с пластинами из быстрорежущей стали (по ГОСТ 18868-73)
инструментальный материал – P6М5 (быстрорежущая сталь).
Определяем глубину резания:
При черновой обработке глубину резания назначают по возможности максимальную равную всему припуску на обработку или большей его части: t=22мм.
При черновой обработке выбирают максимально возможную подачу исходя из жесткости и прочности системы поэтому для t=22мм S=07 ммоб.
Определяем скорость резания:
Скорость резания рассчитывают по эмпирическим формулам установленным для каждого вида обработки которые имеют общий вид:
- поправочный коэффициент;
– коэффициент учитывающий влияние физико-механических свойств обрабатываемого материала (сталь 45);
где - коэффициент характеризующий группу стали по обрабатываемости;
- показатель степени;
- фактический параметр характеризующий обрабатываемый материал;
=08 – коэффициент учитывающий влияние состояния поверхности заготовки на скорость резания
=1 – коэффициент учитывающий влияние инструментального материала на скорость резания
=2 – коэффициент изменения стойкости в зависимости от числа одновременно работающих инструментов
где 08 – поправочный коэффициент обработки без охлаждения y=035; m=020;
T=30-60мин – среднее значение стойкости при одноинструментальной обработке.
Расчет частоты вращения шпинделя:
Принимаем 1600 обмин (для станка 1716Ц).
Расчет минутной подачи:
Определяем силу резания:
Сила резания раскладывается на составляющие направленные по осям координат станка.
тангенциальная составляющая
радиальная составляющая
осевая составляющая
– коэффициент учитывающий влияние качества обрабатываемого материала сплава на силовые зависимости
– коэффициенты учитывающие влияние геометрических параметров режущей части инструмента на составляющие силы резания
Определяем мощность резания:
(Для 1716Ц Nmax = 185 кВт)
Определяем основное машинное время обработки:
где – длина рабочего хода суппорта;
- дополнительная длина хода;
- подвод врезание и пробег инструмента;
при глубине резания - ; длина подвода и пробега - точение в упор
5.2 Обработка поверхности 4 на круглошлифовальном станке (чистовое шлифование)
Станок - круглошлифовальный 3М153ДФ2.
Заданная поверхность должна быть обработана по 6-му квалитету.
Шлифовальный материал - нормальный электрокорунд на керамической связке 14А. Тип круга ПП - прямого профиля. Диаметр круга ; толщина круга - ; шлифовальный материал - 9А зернистость 40 твердость СМ1-С1 [5стр.253]
Параметры резания при круглом наружном шлифовании [5стр.301]
Для окончательного шлифования с продольной подачей на каждый ход:
глубина шлифования - t=001мм
скорость заготовки -
продольная подача -
Характеристики круглошлифовального станка 3М153ДФ2
Частота вращения шпинделя шлифовального круга n=1900 обмин
Скорость врезной подачи шлифовальной бабки - 005 мммин
Определяем эффективную мощность
- диаметр шлифования
L=30 мм - длина рабочего хода с
1. Размерные цепи.doc
1.Анализ конструкции механизма его назначение и условия работы
Раздаточная коробка передач показанная на рисунке 1.1 служит для передачи и преобразования крутящего момента поступающего из коробки скоростей между передним и задним мостами а также обеспечивает отбор мощности при подключении соответствующего узла к входному валу раздаточной коробки.
Рисунок 1.1Раздаточная коробка передач
Устройство и принцип работы раздаточной коробки передач следующий: крутящий момент с входного вала 1 передается на промежуточный вал 2 посредством зубчатой передачи 3-4.
При сдвиге муфты 5 вправо происходит включение повышенной зубчатой передачи 2-6 при этом муфта 7 остается выключенной. Включение повышенной передачи приводит к блокированию свободного вращения зубчатого колеса 6 относительно левого вала 8 дифференциала посредством обоймы 9. С вала 8 крутящий момент распределяется между полуосями переднего 10 и заднего 11 мостов за счет двух зубчатых зацеплений. Зубчатое зацепление сателлитов 12 расположенных в валу 8 и зубчатого колеса 13соединенного с полуосью 10 передает крутящий момент на полуось переднего моста 10. Зубчатое зацепление сателлитов 12 с зубчатой обоймой закрепленной на полуоси 12 заднего моста обеспечивает передачу крутящего момента на задний мост.
При сдвиге муфты 7 влево происходит включение пониженной передачи 15-16 при этом муфта 5 должна быть выключена. Включение пониженной передачи происходит за счет блокирования муфтой 7 свободного вращения зубчатого колеса 15 относительно промежуточного вала 2. Крутящий момент с промежуточного вала 2 передается зубчатым колесом 15 на обойму 16 дифференциала закрепленную при помощи винтов 17 на валу 8. Далее крутящий момент с вала 8 распределяется между полуосями (описание см. выше).
При сдвиге муфты 18 вправо происходит блокирование дифференциала за счет блокирования относительного вращения вала 8 и полуоси 10.
При сдвиге муфты 19 влево происходит включение механизма отбора мощности за счет соединения входного вала 1 и вала 20.
Входной вал 1 промежуточный вал 2 вторичные валы 10 11 установлены на опоры представляющие собой три подшипника качения: шариковый радиальный однорядный подшипник (тип 0000 ГОСТ 8338) воспринимающих радиальную и осевую нагрузку в обе стороны; при этом могут работать под осевыми нагрузками до 70% от радиальной нагрузки; роликовый радиальный однорядный с однобортовым наружным кольцом (тип 12000 ГОСТ 8328); роликовый радиальный однорядный без бортов на наружном кольце (тип 2000 ГОСТ 8328).
Остальные узлы раздаточной коробки также устанавливаются на радиальные роликовые и шариковые подшипники.
Осевая фиксация подшипников осуществляется в основном за счет фиксирования внутренних колец гайками а наружных либо стопорными кольцами либо чаще за счет торцов крышек.
Смазка зацеплений и подшипников осуществляется пластичным смазочным материалом.
В рамках данного курсового проекта в соответствии с заданием рассмотрим более детально сборочную единицу вторичный вал 11 и детали сопряженные с ним.
В качестве задания на проектирование технологического процесса механической обработки принимаем вторичный вал 11.
Материал вторичного вала 11 – Сталь 40Х ГОСТ 4543-71.
1.1.Проанализируем конструкцию раздаточной коробки передач и выявим функции которые она должна выполнять:
преобразование крутящего момента (зубчатые передачи 3-4 4-6 15-16);
распределение крутящего момента в дифференциале (зубчатые передачи 12-13 и 12-14).
1.2.Рассмотрим сборочную единицу – вторичный вал 11 с сопрягаемыми деталями. Она выполняет функцию передачи момента. Для безотказной работы вала необходимо выполнить ряд условий:
прочность вала (диаметр вала больше минимально-допустимого);
отсутствие заклинивания в шариковом 30 и роликовом 29 подшипниках при повышении температуры (наличие зазоров между подшипниками и опорными торцами сопрягаемых деталей);
надежность соединений (точность сопрягаемых поверхностей);
наличие зазора между вторичным валом 11 и шестерней 13 вторичного вала 10 который препятствует контакту между этими деталями (линейная размерная цепь А);
зазоры между подвижными и неподвижными деталями.
1.3.В составе сборочной единицы вала 1 имеется несколько стандартных соединений:
соединение роликового подшипника 29 с валом 11 (посадка с натягом);
соединение роликового подшипника 29 с корпусом 28 (переходная посадка);
соединение ступицы 31 с валом 11 (шлицевое соединение);
соединение зубчатой обоймы 11 с вторичным валом 1 (посадка с натягом );
соединение гайки 34 и вторичного вала 11 (резьбовое соединение).
Для надежной работы узла и отсутствия заедания торца вторичного вала 11 о шестерню 13 зазор между вторичным валом 11 и шестерней 13 принимаем равным от 05 мм до 25 мм.
2.Разработка технических требований к точности обработки детали
Технические требования к точности обработки детали могут быть установлены:
Конструктивно устанавливаются требования к точности поверхностей на основании опыта эксплуатации подобного механизма позаимствованы из механизмов для которых были сделаны соответствующие расчеты установлены действующими ГОСТами или просто для рассматриваемой поверхности не предъявляются повышенные требования к точности обработки.
Выделим группу деталей смежных с вторичным валом 11 (рис. 1.1) и проставим размеры которые назначаются конструктивно (рис. 1.2). К таковым относятся габариты стандартных (п. 1.1.3) и не рассчитываемых соединений.
Рисунок 1.2Сборочная единица вторичного вала 11
Расчетом устанавливаются технические требования к точности наиболее ответственных поверхностей точность обработки которых оказывает существенное влияние на эксплуатационные характеристики не только сборочной единицы но и всего механизма в целом.
Расчетный метод позволяет установить наиболее обоснованные требования к точности поверхностей детали с учетом величин требуемых зазоров типа производства особенности конструкции механизма и других факторов.
На рисунке 1.3 изобразим замкнутую линейную размерную цепь обеспечивающую после сборки зазор между вторичным валом 11 и шестерней 13 в пределах не более 25 мм и не менее 05 мм.
Рисунок 1.3Линейная размерная цепь
На величину зазора влияют следующие размеры:
= мм – расстояние между торцами выходного вала;
= мм – ширина подшипника (ГОСТ 8338);
= мм – размер подшипника (ГОСТ 8338);
= 15 мм - ширина кольца;
= 205 мм - высота крышки;
= 110 мм - высота корпуса;
= 15 мм - ширина прокладки;
= 42 мм - высота крышки;
= 35 мм - ширина кольца;
= 20 мм - ширина дифференциала;
= 60 мм - расстояние между торцами вала;
= 225 мм - ширина шестерни.
Звенья являются уменьшающими а звенья - увеличивающими.
Схема размерной цепи показана на рисунке 1.4.
Рисунок 1.4Схема линейной размерной цепи
Проведем расчет размерной цепи :
Определяем номинальный размер замыкающего звена по следующей формуле [1 с.23]:
где - сумма увеличивающих звеньев;
- сумма уменьшающих звеньев.
Тогда замыкающее звено можно записать в виде:
Определяем класс точности размерной цепи по формуле [1с.59]
где = 20 мм – допуск замыкающего звена (зазор);
– средний коэффициент относительного рассеивания;
= 14 – количество размеров входящих в размерную цепь;
- коэффициент относительного рассеивания i-ого звена.
Полагаем в первом приближении:
- берется согласно ГОСТу в зависимости от размера [1 с.59 табл. 3];
Далее назначаем квалитеты на составные звенья размерной цепи.
Значение а=292 находится между а=250 (IT13) и а=400 (IT14). При этом допуск на ширину подшипников назначается по ГОСТ а=100 (IT11) и а=160 (IT12).
Если назначить на 3 звена точность по IT13 а на остальные по IT14 тогда расчетное значение будет равно:
Распределим все звенья размерной цепи на 3 класса: охватываемые для которых допуск задается «в минус» с отклонением h; охватывающие для которых допуск задается «в плюс» с отклонением H и симметричные – отклонения типа js.
Данные необходимые для расчета сводим в таблицу 1.1.
Размеры и допуски мм
Технологическая операция
Определяем коэффициент относительной асимметрии замыкающего звена по формуле:
где - передаточное отношение
- коэффициент относительной асимметрии
- допуск i-ого звена.
Определяем коэффициент относительного рассеивания замыкающего звена по формуле:
Определяем поле допуска замыкающего звена по формуле:
Таким образом расчетное значение больше допустимого по условиям задания:
- мало отличается от заданного.
Поэтому согласно методике [1 стр.60 табл. 4] процент сборок которые выйдут за пределы допуска замыкающего звена составит 038%. Полученное значение выхода за пределы очень низкое поэтому допустимо.
Определяем координату середины поля допуска замыкающего звена по формуле:
Получаем - требуется корректировка.
Сместим середину поля допуска звена таким образом чтобы
Предельные отклонения звена :
Окончательно звено должно быть изготовлено в размер:
Рассмотрим векторную размерную цепь сборочной единицы показанной на рисунке 1.5.
Искомым звеном будет являться величина зазора между зубчатыми колесами .
Рисунок 1.5Схема векторной размерной цепи
- зазор между зубьями зубчатых колес (замыкающее звено);
- межосевое расстояние сателлита и колеса;
- несоосность наружной цилиндрической поверхности (НЦП) и отверстием запрессованной втулки;
- зазор между отверстием втулки и НЦП-ти сателлита;
- несоосность НЦП-ти и зубчатой поверхностью сателлита;
- делительный радиус сателлита;
- делительный радиус зубатого колеса;
- несоосность зубчатой поверхности и посадочной поверхности под выходной вал зубчатого колеса;
- радиальное биение поверхности под зубчатое колесо относительно поверхности под подшипник выходного вала;
- радиальное биение подшипника;
- зазор между подшипником и стаканом;
- несоосность поверхностей стакана.
Звенья являются скалярными ошибками; звенья - зазорами; - вращающимися векторными ошибками.
Необходимые данные занесем в таблицу 1.2.
Таблица 1.2Расчетные параметры векторной размерной цепи
- приведенный коэффициент относительного рассеивания при рассеивании по закону Максвелла для векторных ошибок.
Рассеивание замыкающего звена (в квадрате) под действием скалярных ошибок:
Определим координату середины поля допуска замыкающего звена от скалярных ошибок:
Рассеивание замыкающего звена (в квадрате) под действием зазоров:
Определим координату середины поля допуска замыкающего звена от звеньев-зазоров полагая :
Результирующая координата середины поля допуска берется из условия выборки зазоров в одну сторону:
Рассеивание замыкающего звена (в квадрате) под действием вращающихся векторных ошибок:
Общее поле рассеивания замыкающего звена под действием векторных ошибок:
Предельные значения величины зазора между зубчатыми колесами:
где - результирующая координата середины поля рассеивания замыкающего звена.
Таким образом зазор между зубчатыми колесами будет составлять:
Тимофеев В.Н. Методика расчета размерных цепей 1963.
Маршрутная технологическая карта.DOC
ДЕТАЛЬ: ВЫХОДНОЙ ВАЛ
Наименование операций
Собираемые детали и материал
Оборудование и инструм.
Технологический режим и присадочные материалы
Мощность и № чертежа
Фрезерно-центровочная
Фрезеровать торцы 9 и 14 в размеры 44h14 мм и 67js14 мм.
Сверлить центровое отверстия 17 4 на глубину 65js14 мм.
Сверлить фаску 8 16х45° на глубину 65js14 мм.
Тиски с подвижными призмами
Фрезерно-центровочный полуавтомат 2Г942
Точить наружные цилиндрические поверхности 2 4 5 6 выдерживая размеры 382h14 мм 321h14 мм 321h14 мм 212h14 мм соответственно.
Подрезать торцы 11 12 13 выдерживая размеры 10h14 мм 325js14 мм 49js14 мм
Одношпиндельный токарно-многорезцовый полуавтомат 1716Ц
Точить наружную цилиндрическую поверхность 1 выдерживая размер 941h14 мм.
Подрезать торец 15 выдерживая размер 1095h14 мм.
Точить наружные цилиндрические поверхности 2 4 5 6 выдерживая размеры 37h12 мм 309h12 мм 309h12 мм 20h12 мм соответственно.
Проточить канавку 3 с подрезкой торца 12 выдерживая размеры 28h12 мм 10h14 мм 325js14 мм.
Подрезать торцы 1113 выдерживая размеры 10h12 мм 49js12 мм.
Точить фаски 7 8 в размер 16х45°.
Точить наружную цилиндрическую поверхность 1 выдерживая размер 929h12 мм.
Подрезать торец 10 выдерживая размер 1095h12 мм.
Точить наружные цилиндрические поверхности 4 5 выдерживая размеры 304h10 мм 304h10 мм соответственно.
Подрезать торец 12 выдерживая размеры 325js10 мм.
Точить наружную цилиндрическую поверхность 1 выдерживая размер 924h10 мм.
Подрезать торец 10 выдерживая размер 1095h10 мм.
Фрезеровать шлицевую поверхность 5 выдерживая размеры на диаметр и ширину пазов h14.
Фрезеровать шлицевую поверхность 5 выдерживая размеры на диаметр и ширину пазов h12.
Сверлить отверстия 95H14 мм 235H14 мм выдерживая размер 9js14 мм.
Патрон токарный 3-х кулачковый
Вертикально-сверлильный 2Н135
Зенкеровать отверстия 10H12 мм 24H12 мм выдерживая размер 9js12 мм.
Нарезать резьбу 6 М20х15.
Резьбонарезной 5993П
Шлифовать наружные цилиндрические поверхности 4 5 выдерживая размеры 301h8 мм 301h8 мм соответственно.
Шлифовать торец 12 выдерживая размеры 325js8 мм.
Круглошлифовальный 3М153ДФ2
Шлифовать наружную цилиндрическую поверхность 1 выдерживая размер 921h8 мм.
Шлифовать торец 10 выдерживая размер 1095h8 мм.
Шлифовать шлицевую поверхность 5 выдерживая размеры на диаметр и ширину пазов h8.
Шлицешлифовальный 3В451ВФ20
Шлифовать окончательно наружные цилиндрические поверхности 4 5 выдерживая размеры 30k6 мм 30k8 мм соответственно.
Шлифовать окончательно наружную цилиндрическую поверхность 1 выдерживая размер 92u7 мм.
Шлифовать окончательно шлицевую поверхность 5 выдерживая размеры на диаметр и ширину пазов h6.