Расчет механизмов настенного поворотного крана гп 2,5 т


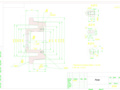
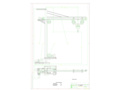
- Добавлен: 25.10.2022
- Размер: 1 MB
- Закачек: 0
Описание
Состав проекта
![]() |
![]() |
![]() |
![]() ![]() |
![]() ![]() |
![]() ![]() ![]() |
![]() ![]() ![]() ![]() |
![]() ![]() ![]() ![]() |
![]() ![]() ![]() |
![]() ![]() ![]() |
Дополнительная информация
2. Расчет механизма поворота.doc
1. Выбор схемы и параметров механизма поворота настенного крана
Для механизма поворота настенного крана применяем схему с подвижной колонной и кинематической схемой привода представленной на рис. 2.1.
Рис. 2.1. Кинематическая схема привода.
– электродвигатель; 2. – соединительная муфта с тормозом; 3 – редуктор; 3 - открытая зубчатая передача.
Для расчета основных параметров крана принимаем следующие недостающие данные:
- расстояние между опорами колонны h=5 м;
- масса фермы крана
тК=05Q= т; сила тяжести GK= тКg= H;
- расстояние от центра тяжести до оси вращения
- частота вращения крана n=1 мин-1.
2. Расчет опор крана
2.1. Составляем расчетную схему поворотного крана (рис. 2.1).
Рис. 2.1. Расчетная схема поворотного крана.
2.2. Определяем реакции в опарах крана
=12262+24525=36787 Н;
где - коэффициент использования крана по грузоподъемности
- средне допускаемый коэффициент использования механизма по грузоподъемности (табл. 1.9 [1]);
2.3. Выбираем подшипники под опоры крана
Так как частота вращения механизма поворота п10 мин-1 то подшипники принимаем по статической грузоподъемности.
Для нижней опоры принимаем два подшипника один шариковый упорный №8210 с статической грузоподъемностью С0=103000 Н>RAY= 36787 Н и один шариковый радиальный сферический подшипник №1212 с статической грузоподъемностью С0=15500 Н>RAХ=8124 Н.
Для верхней опоры принимаем шариковый радиальный сферический подшипник №1212 с статической грузоподъемностью С0=15500 Н>RВХ=8124 Н.
3. Определение момента сопротивления крана
Момент сопротивления вращению крана равен
где ТВР - момент сопротивления вращению крана равен от сил трения
ТТР= 0.5(RАXfAdA1+ RАY fAdA2+ RВXfAdB);
где dА1 dА2 и dВ – средние диаметры соответствующих опор
d и D – внутренний и наружный диаметры подшипников
fA fВ – коэффициенты трения в соответствующих опорах
ТУК - момент сопротивления вращению крана равен от уклона пути
тпов – масса поворотной части крана
тпов= тгр+ тпв +тк=2500+0+1250=3750 кг
lпов – расстояние от оси вращения крана до центра тяжести поворотной части крана
ТВР=2245+2801=227301 Нм.
4. Определение потребной мощности электродвигателя
4.1. Требуемая мощность электродвигателя
где п - частота вращения крана;
- общий КПД привода крана;
По табл.III.3.5. [1] по расчетному значению мощности и значению режима работы подбираем электродвигатель МТFК 011-6 с номинальной мощностью номинальной частотой вращения моментом инерции ротора и максимальным моментом .
4.2. Номинальный момент на валу электродвигателя
4.3. Допустимый коэффициент перегрузки
Общее передаточное число привода
Принимаем для привода червячный редуктор Ч-125 с передаточным числом и мощностью на быстроходном валу РБ=1500 Вт (см. рис. 2.1). Передаточное число открытой передачи
6. Проверяем выбранный электродвигатель по пусковому моменту
где - время неустановившегося движения при перемещении тележки принимаем ;
- коэффициент учитывающий влияние маховых масс вращающихся деталей при от вала электродвигателя до вала барабана принимаем
Коэффициент перегрузки
Выбранный электродвигатель будет работать без перегрева.
7.1. Расчетный тормозной момент
где - момент сил инерции на валу тормоза при торможении;
J – момент инерции ротора двигателя
JВР.ПОВ - момент инерции поворотной части крана
7.2. Минимальный диаметр тормозного шкива
где - допускаемое давление между шкивом и колодкой по табл.7 [3] c. 21 ;
- коэффициент трения тормозной пары табл. 1.38 с. 46 [1];
7.3. По значению ПВ и принимаем тормоз ТКТ-100 (рис. 1.11) и выписываем его характеристику:
-диаметр тормозного шкива ;
-плечи тормозных рычагов
-отход тормозных колодок от тормозного шкива
-ход штока якоря электромагнита
-плечо якоря электромагнита
7. Проверочный расчет тормоза.
7.1. Окружное усилие на тормозном шкиву
7.2. Усилие нормального давления тормозных накладок на тормозной шкив
7.3. Параметры тормозных колодок
-длина тормозной колодки
где - угол обхвата тормозной колодкой шкива. Принимаем
-ширина тормозной колодки
7.4. Проверка тормоза на износ и нагрев
Проверку тормоза на износ и нагрев производим по условию
где - давление между тормозным шкивом и колодкой
V – окружная скорость тормозного шкива
Выбранный тормоз будет работать без нагрева и износа.
8. Выбор и расчет соединительной муфты
8.1. По крутящему моменту для соединения вала электродвигателя с быстроходным валом редуктора выбираем по значению dэл=28 мм упругую втулочно-пальцевую муфту (МУВП) с тормозным шкивом (рис.1.12) и передаваемым момент 125 Нм.
где кр – коэффициент режима работы привода.
Муфта пригодна так как =2865 Нм125 Нм.
кран1.dwg

Инв.N подп. Взам. инв.N Инв.N дубл.
*Размеры для сравок.
Техническая характеристика
Высота подъема груза 3
Режим работы (ПВ) 25%
детали.dwg

Инв.N подп. Взам. инв.N Инв.N дубл.
Неуказанные литейные радиусы 3 мм тах.
Сварное соединение II класса точности по СТБ 1016-96.
Точность СК Р2 ГОСТ 30021-93.
* Размеры для справок.
3. РАСЧЕТ механизма передвижения.doc
1. Выбор конструкции механизма передвижения
Изучив существующие схемы тележек для нашего случая принимаем:
- подвесную тележку (рис. 3.1 а);
- механизм передвижения тележки гибкой тягой (рис. 3.1 б);
- беговая поверхность - тавровая балка.
Рис.3.1. Механизм передвижения тележки с гибкой тягой
а). подвесная тележка; б). расчетная схема механизма передвижения тележки гибкой тягой.
Барабан 1 установлен неподвижно вместе с приводом и соединен с тележкой 2 гибкой тягой 3 (канат). С другой стороны тележки гибкий орган огибает обводной блок 4. На тележке установлены блоки 5 подъемного механизма которые огибает канат 6 механизма подъема. При вращении барабана 1 одна ветвь тягового каната 3 сматывается с барабана а другая наматывается и тележка движется в ту или другую сторону в зависимости от направления вращения барабана. Показанное на рис. 3.1 (а) направление вращения барабана 1 соответствует движению тележки вправо. При перемещении тележки канат 6 механизма подъема перекатывается по блокам 5 а подвешенный груз перемещается вместе с тележкой оставаясь на одной и той же высоте.
2.Расчет ходовых колес механизма передвижения
2.1. Считаем что груз расположен симметрично следовательно нагрузка на колесо будет равна
где – ориентировочная масса тележки Н;
z – количество ходовых колес.
2.2. Определяем диаметр оси ходового колеса. В предварительных расчетах принимаем L=50 мм.
Рис.3.2. Расчетная схема ходового колеса
В качестве материала оси принимаем сталь 35 с пределом текучести 320 МПа. Допускаемые напряжения
где - коэффициент безопасности.
Принимаем 30 мм и под данный диаметр подбираем подшипники шариковые радиальные легкой серии №206 у которых диаметр d=30 мм D=62 мм В=16 мм динамическая грузоподъемность С=19500 Н статическая С0=10000 Н.
Так как С0=10000 Н>Fmax=6327 H то условие статической грузоподъемности выполняется.
2.3. Принимаем диаметр ролика DP=125 мм табл. 10.2 [1].
2.4. Частота вращения роликов тележки
где V=01 мс – скорость перемещения тележки (принята равной скорости подъема груза).
2.5. Так как подшипники работают при частоте вращения мин-1 то подшипники проверяем по долговечности. Эквивалентная нагрузка
где Х – коэффициент радиальной нагрузки;
Y – коэффициент осевой нагрузки;
кб – коэффициент безопасности;
кт – температурный коэффициент.
Долговечность подшипников (в одной опоре устанавливаем по два подшипника)
2.6. Проверяем колесо на контактную прочность. Контактные напряжения
где Кд – динамический коэффициент
а=02 – коэффициент зависящий от места укладки беговой поверхности (металлическая балка);
Коэффициент долговечности
где NE – число циклов нагружения ролика
Lh=27500 ч– долговечность работы с.44 [2].
Значение КHL= поэтому принимаем КHL=1.
Допускаемые контактные напряжения
=430 МПа – предельные контактные напряжения для стали 35.
Условие прочности колес по контактным напряжениям выполняется т.к.
3.Расчет каната механизма передвижения
3.1.Разность натяжения ветвей грузового полиспаста
где - КПД направляющих блоков;
z=4 – количество блоков.
3.2.Сопротивление от провисания хвостовой ветви тягового каната
=053 кг – ориентировочная масса одного метра смазанного каната (dK=12 мм);
- наибольшая длина хвостовой части каната;
H=0.01 0.02 м – допускаемое провисание каната.
3.3.Сопротивление передвижению тележки от трения
где FТР – сила сопротивления перекатыванию колес по рельсу состоит из сопротивлений: качения колеса трения в подшипниках в ребордах колес и торцах втулок
F0 – общая суммарная нагрузка на колеса Н;
- коэффициент трения качения колеса =03 – табл.4.2 [2];
f – коэффициент трения в подшипниках колес f=0015;
dср – средний диаметр подшипника
- коэффициент учитывающий сопротивления от трения реборд и торцов втулок =25 – табл.4.3 [2];
- сила сопротивления от инерции поступательно движущихся масс на колесе
tP – время разгона tP=2 3 c.
3.4.Усилие необходимое для передвижения тележки
=756+1121+406=2283 Н.
3.5.Натяжение каната на барабане
3.6.Разрывающее усилие каната
где к=55 – коэффициент запаса прочности для легкого режима работы (табл. 2.3 [1]).
3.7.По табл.III. 1.1 [1] принимаем канат с разрывным усилием в целом 34800 Н и полным обозначением:
канат 83-Г-I-Н-1568 ГОСТ 7665-80.
Расшифровка обозначения:
- канат – наименование изделия;
- 83 мм диаметр каната;
- I – канат изготовлен из материала марки I со светлой поверхностью проволок;
- правая свивка прядей;
- крестовая свивка элементов каната;
- Н – нераскручивающийся канат;
- 1568 МПа – маркировочная группа проволок.
3.8.Фактический коэффициент запаса прочности выбранного каната
4.1.Диаметр барабана по дну нарезной канавки рис. 3.3.
где е – коэффициент зависящий от типа машины привода механизма и режима работы механизма (табл. 2.7. с. 59 [1]);
Рис. 3.3. Профиль канавок на барабане.
Принимаем ближайшее значение длинны барабана из нормального ряда DБ=200 мм.
4.2. Диаметр барабана по средней линии навиваемого каната
- нарезная длина барабана (рис. 2.2.)
Рис. 3.4. Схема к определению длины барабана.
где 9 мм - шаг навивки (табл. 2.8. с. 59 [1]) мм;
- число рабочих витков для навивки каната находим исходя из значения вылета стрелы
- кратность полиспаста;
- число неприкосновенных витков для удержания каната на барабане силой трения
- длинна концевого участка барабана
=483=332 мм принимаем =35 мм.
мм принимаем LБ=200 мм.
4.4. Толщина стенки барабана
4.5. Проверяем стенку барабана по напряжениям сжатия
где - допускаемые напряжения сжатия;
=206 МПа - предел текучести чугуна (с. 83 П IV [2]);
- коэффициент безопасности.
Условие прочности выполняется.
4.6. Так как (200 мм 600 мм) то проверку стенки барабана на изгиб и кручение не производим.
5. Расчет привода механизма подъема
5.1. Требуемая мощность электродвигателя
где 08 - общий КПД привода.
По табл.III.3.5. [1] по расчетному значению мощности и значению режима работы подбираем электродвигатель МТFК 011-6 с номинальной мощностью номинальной частотой вращения моментом инерции ротора и максимальным моментом .
5.2. Номинальный момент на валу электродвигателя
5.3. Допустимый коэффициент перегрузки
5.4. Частота вращения роликов тележки
5.5. Общее передаточное число привода
5.6. Так как полученное передаточное число имеет большое значение то для привода барабана принимаем кинематическую схему с редуктором и открытой передачей.
Принимаем редуктор цилиндрический горизонтальный двухступенчатый Ц2У-180 с передаточным числом 40. Передаточное число открытой передачи
5.7. Проверяем выбранный электродвигатель по пусковому моменту
где - время неустановившегося движения при перемещении тележки принимаем ;
- коэффициент учитывающий влияние маховых масс вращающихся деталей при от вала электродвигателя до вала барабана принимаем
Коэффициент перегрузки
Выбранный электродвигатель будет работать без перегрева.
5.8. Составляем кинематическую схему привода
Рис. 3.5. Кинематическая схема механизма передвижения тележки
– электродвигатель; 2 – соединительная муфта с тормозом; 3 – редуктор; 4 – открытая зубчатая передача; 5 – барабан.
– электродвигатель МТFК 011-6 (17 кВт 850);
– тормоз; 4 и 6 – соединительные муфты;
– редуктор Ц2У-180 ();
– приводной барабан (DБ=200 мм пБ=955мин-1).
6. Расчет тормоза механизма передвижения тележки
6.1. Расчетный тормозной момент
где - коэффициент запаса тормозного момента при ПВ=25% 175;
=08 085 - КПД механизма тормоза;
=08 - КПД механизма передвижения тележки;
6.2. Минимальный диаметр тормозного шкива
где - допускаемое давление между шкивом и колодкой по табл.7 [3] c. 21 ;
- коэффициент трения тормозной пары табл. 1.38 с. 46 [1];
6.3. По значению ПВ и принимаем тормоз ТКТ-100 (рис. 1.11) с параметрами:
-диаметр тормозного шкив;
-плечи тормозных рычагов
-отход тормозных колодок от тормозного шкива
-ход штока якоря электромагнита
-плечо якоря электромагнита
6.4. Окружное усилие на тормозном шкиву
6.5. Усилие нормального давления тормозных накладок на тормозной шкив
6.6. Параметры тормозных колодок
-длина тормозной колодки
где - угол обхвата тормозной колодкой шкива. Принимаем
-ширина тормозной колодки
6.7. Проверка тормоза на износ и нагрев
Проверку тормоза на износ и нагрев производим по условию
где - давление между тормозным шкивом и колодкой
V – окружная скорость тормозного шкива
Выбранный тормоз будет работать без нагрева и износа.
7. Выбор и расчет соединительной муфты
По крутящему моменту для соединения вала электродвигателя с быстроходным валом редуктора выбираем по значению dэл=35 мм упругую втулочно-пальцевую муфту (МУВП) с тормозным шкивом (рис.1.12) с передаваемым моментом 125 Нм.
где кр – коэффициент режима работы привода.
Муфта пригодна так как =2865 Нм125 Нм.
1. РАСЧЕТ механизма подъема груза.doc
1.Расчет грузового каната
1.1.Максимальное рабочее усилие натяжения ветви каната наматываемой на барабан
где - КПД направляющих блоков
z=2 – количество блоков.
=2 - кратность подвески – отношение числа ветвей каната удерживающих груз к числу ветвей каната набегающих на барабан (рис. 1.1.);
Рис. 1.1. Схема полиспаста.
1.2.Разрывающее усилие каната
где к=55 – коэффициент запаса прочности для легкого режима работы (табл. 2.3 [1]).
1.3.По табл.III. 1.1 [1] принимаем канат с разрывным усилием в целом 86700 Н и полным обозначением:
канат 14-Г-I-Н-1372 ГОСТ 7665-80.
Расшифровка обозначения:
- канат – наименование изделия;
- 14 мм диаметр каната;
- I – канат изготовлен из материала марки I со светлой поверхностью проволок;
- правая свивка прядей;
- крестовая свивка элементов каната;
- Н – нераскручивающийся канат;
- 1372 МПа – маркировочная группа проволок.
1.4.Фактический коэффициент запаса прочности выбранного каната
2Расчет приводного барабана
2.1.Диаметр барабана по дну нарезной канавки рис. 2.1.
где е – коэффициент зависящий от типа машины привода механизма и режима работы механизма (табл. 2.7. с. 59 [1]);
Рис. 1.2. Профиль канавок на барабане.
Принимаем ближайшее значение длинны барабана из нормального ряда DБ=320 мм.
2.2. Диаметр барабана по средней линии навиваемого каната
- нарезная длина барабана (рис. 2.2.)
Рис. 1.3. Схема к определению длины барабана.
где - шаг навивки (табл. 2.8. с. 59 [1]) мм;
- число рабочих витков для навивки каната
- кратность полиспаста;
- число неприкосновенных витков;
число витков используемых для крепления каната к барабану;
- длинна концевого участка барабана
=2704 мм принимаем LБ=270 мм.
2.4. Толщина стенки барабана
2.5. Проверяем стенку барабана по напряжениям сжатия
где - допускаемые напряжения сжатия;
=206 МПа - предел текучести чугуна (с. 83 П IV [2]);
- коэффициент безопасности.
Условие прочности выполняется.
2.6. Так как (270 мм 960 мм) то проверку стенки барабана на изгиб и кручение не производим.
2.7. Для крепления каната к барабану применяем прижимную планку со шпилькой (рис. 2.3.).
Рис. 1.4. Схема крепления каната к барабану при помощи шпильки.
где - допускаемые напряжения растяжения
- предел текучести для стали 45;
- коэффициент безопасности;
- сила растягивающая винт
- коэффициент трения между канатом и барабаном;
- угол обхвата барабана витками каната рад.
По табл.4.6 [3] принимаем две шпильки с резьбой М12 у которой
3.Расчет вала приводного барабана
3.1. Составляем расчетную схему вала приводного барабана
Рис.1.5. Расчетная схема вала приводного барабана.
3.2. Определяем реакции в опорах вала приводного барабана
225+65225-130452-130452=0.
3.3. Изгибающие моменты в сечениях
Сечение 1: Нм. Сечение 2: Нм.
3.4. Крутящий момент
3.5. Эквивалентный изгибающий момент
3.6. Предварительный диаметр вала
где Т - крутящий момент Нмм;
- допускаемое напряжение при кручении
- допускаемые напряжения растяжения
Предварительный диаметр вала под:
Принимаем диаметр вала под соединительную муфту диаметр вала под подшипники под барабан
3.7. Проверка диаметра вала в опасном сечении
где =144 МПа - допускаемые напряжения растяжения
3.8. Расчет шпоночных соединений
Для закрепления на валу барабана и соединительной муфты применяем призматические шпонки выполненные по ГОСТ 23360 СТ СЭВ 189-75. Материал шпонок - сталь 45 для шпонок с пределом прочности МПа.
Рабочая длина шпонки определяется по формуле:
где T - наибольший крутящий момент на валу Нм;
d - диаметр вала мм;
h - высота шпонки мм;
МПа – допускаемые напряжения смятия (с. 48 [3]);
t1 - заглубление шпонки в валу мм.
Шпонка под соединительную муфту
Выбираем шпонку для диаметра мм с крутящим моментом Нм для которой 16 мм 10 мм 6 мм. Определяем минимальную длину:
Полная длина шпонки 792+16=952 мм.
Принимаем шпонка 1610100 ГОСТ 23360-78.
Для соединения барабана с валом принимаем шпонку для диаметра мм для которой 18 мм 11 мм 7 мм. Определяем минимальную длину:
Полная длина шпонки мм.
Принимаем шпонку 181190 ГОСТ 23360-78.
4. Расчет подшипников приводного барабана
4.1 Принимаем под диаметр вала d=65 мм предварительно подшипники радиальные сферические шариковые лёгкой узкой серии 1213. У которых статическая грузоподъёмность С0=17300 Н динамическая – С=31200 Н.
4.2. Эквивалентная нагрузка на подшипник
где Х – коэффициент радиальной нагрузки Х=1;
V – коэффициент вращения т.к. вращается внутреннее кольцо подшипника то V=1;
кб – коэффициент безопасности кб=15;
кт – температурный коэффициент кт=1.
4.3. Расчёт подшипника проводим по номинальной долговечности
где n – частота вращения приводного барана;
V –скорость подъема груза V=01 мс.
Так как частота вращения барабана n10 мин-1 то при определении долговечности принимаем n=10 мин-1 (с. 333 [3]). Тогда
Предварительно назначенный подшипник пригоден.
4.4. Для подшипников по наружному диаметру подшипника (D=120 мм) принимаем разъемные корпуса РШ 120 ГОСТ 13218.9-77.
5. Расчет элементов крюковой подвески
5.1. Устройство крюковой подвески
Для проектируемого механизма подъема груза принимаем нормальную крюковую подвеску наиболее универсальную и распространенную. устройство крюковой подвески показано на рис. 1.6.
Рис. 1.6. Конструкция нормальной крюковой подвески.
– крюк 2- траверса 3 – ось блоков 4 – основной блок 5 - уравнительный блок 6 – щека 7 – серьга.
По режиму работы (средний ПВ=25 %) и грузоподъемности (QГР=25 т) по табл.III.2.4. [1] принимаем крюк № 10.
Рис. 1.7. Эскиз крюка.
5.3. Расчет оси блоков
Принимаем DБ=320 мм.
Расчетная длина оси блоков
где - толщина серьги и кожуха (с. 85 П. VI [2]) (рис. 1.6)
Рис. 1.8. Эскиз и расчетная схема оси блоков.
zБ1=1 - количество блоков
lст – длина ступицы (с. 85 П. VII [2])
- зазор между торцами ступиц блоков.
Расчетный диаметр оси блоков
Принимаем dОС=35 мм.
Проверяем расчетный диаметр оси блоков по напряжениям смятия между серьгой и осью
где = - диаметр цапфы
5.4. Расчет траверсы (рис. 1.9)
Рис. 1.9. Эскиз и расчетная схема траверсы.
где h – высота траверсы
h=L-l-l1=165-85-45=35 мм
=32 мм- диаметр отверстия под крюк в траверсе;
DH=52 мм – наружный диаметр подшипника №8106 (dB=30 мм) С0=27000 Н>FГР=24252 Н.
Ширина траверсы должна соответствовать условию
В=1.2DH=1.2*47=564 мм.
Диаметр цапф траверсы
Проверяем диаметр цапфы на прочность по смятию между цапфой и отверстием в серьге
Условие прочности серьги
где ВС – ширина серьги
ВС= (15 20)dОС=2*35=70 мм.
Условие прочности серьги выполняется.
6. Расчет привода механизма подъема
6.1. Требуемая мощность электродвигателя
где 08 - общий КПД привода;
По табл.III.3.5. [1] по расчетному значению мощности и значению режима работы подбираем электродвигатель МТF 111-6 с номинальной мощностью 41 кВт номинальной частотой вращения моментом инерции ротора и максимальным моментом 87 Нм.
6.2. Номинальный момент на валу электродвигателя
6.3. Допустимый коэффициент перегрузки
6.4. Общее передаточное число привода
Так как полученное передаточное число имеет большое значение то для привода барабана принимаем кинематическую схему с редуктором и открытой передачей (рис. 1.10).
По значению мощности и режиму работы принимаем редуктор цилиндрический горизонтальный двухступенчатый Ц2-250 с мощностью на быстроходном валу 42 кВт при его частоте вращения (с. 318 [1]). Фактическое передаточное число редуктора Тогда частота вращения выходного вала редуктора
Передаточное число открытой передачи
6.5. Проверяем выбранный электродвигатель по пусковому моменту
где - время неустановившегося движения при перемещении тележки принимаем ;
- коэффициент учитывающий влияние маховых масс вращающихся деталей при от вала электродвигателя до вала барабана принимаем
Коэффициент перегрузки
Выбранный электродвигатель будет работать без перегрева.
6.6. Составляем кинематическую схему привода
Рис. 1.10. Кинематическая схема механизма подъема груза
– электродвигатель; 2 – соединительная муфта с тормозом; 3 – редуктор; 4 – открытая зубчатая передача; 5 – барабан.
– электродвигатель МТF 111-6 ( );
– тормоз; 4 и 6 – соединительные муфты;
– редуктор Ц2-250 ();
– приводной барабан (DБ=320 мм пБ=57 мин-1).
7. Расчет тормоза механизма подъема груза
7.1. Расчетный тормозной момент
где - коэффициент запаса тормозного момента при ПВ=25% 175;
=08 085 КПД механизма тормоза;
=094 КПД механизма подвески;
7.2. Минимальный диаметр тормозного шкива
где - допускаемое давление между шкивом и колодкой по табл.7 [3] c. 21 ;
- коэффициент трения тормозной пары табл. 1.38 с. 46 [1];
7.3. По значению ПВ и принимаем тормоз ТКТ-100 (рис. 1.11) с параметрами:
-диаметр тормозного шкив;
-плечи тормозных рычагов
-отход тормозных колодок от тормозного шкива
-ход штока якоря электромагнита
-плечо якоря электромагнита
Рис. 1.11. Схема двухколодочного тормоза типа ТКТ.
7.4. Окружное усилие на тормозном шкиву
7.5. Усилие нормального давления тормозных накладок на тормозной шкив
7.6. Параметры тормозных колодок
-длина тормозной колодки
где - угол обхвата тормозной колодкой шкива. Принимаем
-ширина тормозной колодки
7.7. Проверка тормоза на износ и нагрев
Проверку тормоза на износ и нагрев производим по условию
где - давление между тормозным шкивом и колодкой
V – окружная скорость тормозного шкива
Выбранный тормоз будет работать без нагрева и износа.
8. Выбор и расчет соединительной муфты
По крутящему моменту для соединения вала электродвигателя с быстроходным валом редуктора выбираем по значению dэл=35 мм упругую втулочно-пальцевую муфту (МУВП) с тормозным шкивом (рис.1.12) и следующими характеристиками:
Рис. 1.12. Упругая втулочно-пальцевая муфта
-передаваемый момент 250 Нм;
-допускаемая частота вращения п=3800 мин-1.
где кр – коэффициент режима работы привода.
Муфта пригодна так как =1305 Нм250 Нм.