Проектирование завода керамической плитки


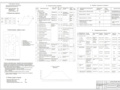
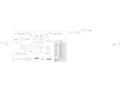
- Добавлен: 25.10.2022
- Размер: 561 KB
- Закачек: 0
Подписаться на ежедневные обновления каталога:
Описание
Проектирование завода керамической плитки
Состав проекта
![]() |
![]() ![]() ![]() ![]() |
![]() ![]() ![]() ![]() |
![]() ![]() ![]() |
Дополнительная информация
Контент чертежей
3001.dwg

Порядок приемного контроля
Завод по производству керамической плитки
Технологическая часть
Технологическая карта
Наименование контролируемого парамера
Нормативные значения
Водопоглощение %. не более
Термическая стойкость глазури С белой глазурью
Твердость глазури по шк. Мооса
Шкаф сушильный 150 С
Шкаф сушильный Весы технологические ГОСТ 24104
штангенциркуль гост 166 песок кварцевый гост 22551
штангенциркуль гост 166 прокладки резиновые 2.5 мм
Режим труда и отдыха
Количество рабочих дней в году Количество смен в сутки Количество часов в смену Годовой фонд рабочего времени ч год
Техника безопасности
Добыча и переработка сырья - разработка глины должна производится в соответствии с требованиями
утвержденными Госгортехнадзором при разработке месторождения полезных ископаемых открытым способом. 2.При ведении технологических процессов ( просев
обжиг) должны быть соблюдены. 1 Метрологические условия и содержание пыли в рабочей зоне произ- водственных помещений по ГОСТ 12.1.003.-80. 2.Очистка выбрасываемого в атмосферу воздуха в соответствии с ГОСТ 17.1302-80. 3.Параметры вибрации на рабочих местах ГОСТ 12.1.012-80 4.
Уровень звукового давления в открытых полосах частот на рабочих местах по ГОСТ 12.1.003-80.
Плитки керамические для внутренней облицовки стен ГОСТ 6141-91
Состав: Глина огнеупорная 20%. Кварцевый песок 7% Полевой шпат 3% Глина тугоплавкая 70%
Геометричес- кие параметры
Сост . звена (разряд).
Трудоем кость цел. мин
Оборудование инстум.
Доставка боя плитки на перер
Доставка добавки на склад сырья
Эксковатор одноковшовый
Переработка сырья и добавок
Просев и складирование шамота
Смешение компонентов
Доставка шликера в расходный бассейн
Операторы приема сырья (4)
переработки сырья (4)
Приготовление пресс порошка
Операторы перера- ботки сырья (4)
Первичный обжиг плитки
Укладка плитки на конвейер печи
Щелевая ролико- вая печ
Первичная глазуровка
Вторичная глазуровка
Глазуровачная установка
Обжиг для закрепления глазури
Щелевая ролико- вая печь
Разгрузка и складирование готовой продукции
Пакетирование Складирование гото. продукции
Оп.пакет. (5) Машинист (4)
Авто.пакетир Погрузчик
Технологические операции
Операционный контроль
Операция под- лежащая контр.
Метод и средст. контроля
Подготовка шли- кера
Влажность Плотность Текучесть
Взвешивание на весах
Приготовление пресс-порошка
Продолжитель- ность сушки
Давление рас- пыления
Хранение пресс- порошка
Первое давлен 2.Второе давлен 3.Продолжит 4.Прочность на изгиб 5.Глубина засыпки
Гидравлический пресс
Температура 2.Продолжит. 3.Пористость
Толщина глазу- рованного слоя
Обжиг для закреп- ления глазури
Температура 2.Продолжитель.
Склад глины 2. Склад добавок 3. Отделение переработки сырья 4. Отдел формования 5. Отдел утильного обжига 6. Отделение глазурования 7. Отделение разгрузки и пакетирования 8. Склад готовой продукции"
2001.dwg

Железнодорожные эстакады
Дезинтеграторные вальцы
Вальцы тонкого помола
Бегуны мокрого помола
Промежуточный питатель
Двухвальная глиномешалка
Смеситель пресса ленточного вакуумного пластического формования
Автомат многоструйной резки и укладки
Технологическая схема
производства керамического кирпича
Производство керамической плитки
Технологическая часть
Эксковатор одноковшовый
Вальцы камневыделительные
Распылительная сушилка
Бункер пресс порошка
Гидравлический пресс
Роликовая печь-сушилка
Устройство нанесения глаз.
Печь закрепления глазури
Склад готовой продукции
rrr-rrrrr-rr-rrrr1.docx
Рассмотрены стандарты принятые для изготовления кирпича и основные свойства сырья для их изготовления. В данном случае сырьем являются легкоплавкие глины металлургический шлак и бой изделий и доломит. Описаны основные процессы которые протекают в структуре материала под действием температур. Разработана технологическая схема производства данных строительным материалов и рассчитан материальный баланс для производства 40 млн.кирпича в год.
Номенклатура производства ..6
Сырьевые материалы ..10
Обоснование способа производства 12
Описание физико-химических процессов
получения материала 13
Описание технологического процесса .19
Расчетная производственная программа 21
Список используемых источников .30
Современный рынок керамических строительных материалов предоставляет огромный выбор продуктов конструкционного и функционального назначения. Особое место в строительной керамике занимают керамический кирпич и камень.
На сегодняшний день керамический кирпич является одним из самых популярных стеновых материалов который обычно применяется для возведения несущих стен и перегородок одноэтажны и многоэтажны зданий и сооружений внутренних перегородок а также для заполнения пустот в монолитно-бетонных конструкциях. Более чем тысячелетняя история использования кирпича позволяет однозначно отнести его к категории наиболее долговечных строительных материалов. Наряду этим технология кладки предоставляет архитекторам и дизайнерам неограниченные возможности для воплощения творчески решений. Из кирпича построено большинство зданий дореволюционного Санкт-Петербурга купеческая Москва а церковь в Гродно при строительстве которой использовался этот материал стоит уже 1000 лет.
За последнее десятилетие интерес к кирпичу существенно вырос. Это объясняется бумом частного домостроения которое по темпам возведения жилья в России смогло опередить строительство муниципальных жилых комплексов. Несмотря на широкое разнообразие материалов на рынке кирпич по-прежнему является наиболее востребованным. Даже в том случае если дом строится из популярного сегодня газобетона пенобетона или возводится из легких стальных конструкций – фасад его все равно облицовывается керамическим кирпичом. Этот материал является символом благосостояния успешности а его разнообразие позволяет реализовывать уникальные проекты.
Не так давно на рынке было два основных вида керамического кирпича: лицевой и рядовой. Цветовая палитра так же не радовала разнообразием: красный бежевый и соломенный кирпич составляли основу ассортимента большинства заводов. За последнее десятилетие ситуация кардинально изменилась: российские предприятия начали производить кирпич в широкой цветовой гамме появились сорта с фактурной лицевой поверхностью. Рядовой кирпич стали выпускать не только полнотелый и щелевой но и с различным процентом пустотности. Революцией в домостроении стало появление поризованных керамических камней и блоков способных заменить собой от 2 до 12 стандартных кирпичей. Применение этого материала увеличило темпы строительства позволило обходиться без теплоизоляции.
В данном курсовом проекте будет рассмотрена технология производства керамических кирпичей и камней с помощью пластического формования.
Номенклатура производства
Кирпич и камни ГОСТ 530-2012
Характеристики облицовочный керамический
Размеры кирпича (ширина;высота;длинна)
Масса одного кирпича
Количество на поддоне
Количество кирпичей в 1 м2
Количество кирпичей в 1 м3
Технические требования
Изделия должны изготавливаться в соответствии с требованиями настоящего стандарта по технологическому регламенту утвержденному предприятием-изготовителем.
1 Лицевые изделия должны иметь не менее двух лицевых граней - ложковую и тычковую. Цвет и вид лицевой грани устанавливают по согласованию между изготовителем и потребителем и оговаривают в документе на поставку.
Рядовые изделия изготавливают с гладкими или рельефными вертикальными гранями.
Лицевые кирпич и камень по виду лицевой поверхности изготавливают:
- с гладкой и рельефной поверхностями;
- с поверхностью офактуренной торкретированием ангобированием глазурованием двухслойным формованием или иным способом.
Изделия могут быть естественного цвета или объемно окрашенными.
2 На лицевых изделиях допускаются единичные вспучивающиеся (например известковые) включения глубиной не более 3 мм общей площадью не более 02% площади лицевых граней.
На рядовых изделиях допускаются вспучивающиеся включения общей площадью не более 10% площади вертикальных граней изделия.
3 На лицевых и клинкерных изделиях не допускаются высолы.
4 Дефекты внешнего вида изделия размеры и число которых превышают значения указанные в таблице 4 не допускаются.
Таблица 4 - Дефекты внешнего вида изделия
Отбитости углов глубиной отбитости ребер и граней длиной более 15 мм шт.
Отбитости углов глубиной отбитости ребер и граней длиной не более 15 мм шт.
Отдельные посечки суммарной длиной мм не более:
Отбитости глубиной менее 3 мм не являются браковочными признаками.
Трещины в межпустотных перегородках отбитости и трещины в элементах пазогребневого соединения не являются дефектом.
Для лицевых изделий указаны дефекты лицевых граней
5 У изделий допускаются черная сердцевина и контактные пятна на поверхности.
6 В партии не допускается половняк более 5% объема партии.
.2.1 Средняя плотность кирпича в зависимости от класса средней плотности должна соответствовать значениям приведенным в таблице 5.
Таблица 5 - Классы средней плотности изделий
Класс средней плотности изделия
Средняя плотность кгм
Отклонение единичного значения средней плотности (для одного образца из пяти) допускается не более:
+50 кгм- для классов 07; 08 и 10;
+100 кгм- для остальных классов.
2 Теплотехнические характеристики изделий оценивают по коэффициенту теплопроводности кладки в сухом состоянии. Коэффициент теплопроводности кладки в сухом состоянии в зависимости от группы изделий по теплотехническим характеристикам приведен в таблице 6.
Таблица 6 - Группы изделий по теплотехническим характеристикам
Группы изделий по теплотехническим характеристикам
Коэффициент теплопроводности кладки в сухом состоянии Вт(м·°С)
Высокой эффективности
Повышенной эффективности
Малоэффективные (обыкновенные)
Значения коэффициента теплопроводности приведены для кладок с минимально достаточным количеством кладочного раствора. Значение коэффициента теплопроводности с учетом фактического расхода раствора устанавливают в проектной или технической документации (строительные нормы и правила и др.) на основании испытаний или расчетов.
Теплотехнические характеристики сплошных (условных) кладок приведены в приложении Г.
3 Марку кирпича по прочности устанавливают по значениям пределов прочности при сжатии и при изгибе кирпича с горизонтальным расположением пустот и камня - по значению предела прочности при сжатии. Значения пределов прочности при сжатии и изгибе должны быть не менее значений указанных в таблице
Легкоплавкие глины — полиминеральные обычно железисто-монтмориллонитовые и гидрослюдистые (часто с примесью песка и органических веществ) показатель огнеупорности менее 1350 °С. Используются для приготовления грубокерамических изделий строительного глиняного кирпича черепицы дренажных труб цемента и др. Лучшие сорта пластичных глин применяются для изготовления гончарной посуды и скульптуры. Легкоплавкие глины используются для получения керамзита. Вредными примесями являются грубообломочные включения особенноизвестнякаигипса. Пригодность глины для производства того или иного вида изделий определяется технологическими испытаниями в результате которых в заводских условиях изготовляется изделие и определяется его качество. На глиняный кирпич дренажные керамические трубы керамзит и другие изделия грубой керамики вСССРустановлены государственные стандарты. ГОСТ 9169-75 "Сырьё глинистое для керамической промышленности" определяет основные признаки классификации сырья.
Шамот (кирпичный бой)
Шамот получают из обожженных отходов керамических изделий. Он является более эффективным отощителем чем кварцевый песок. Шамот сильнее снижает усадку глины чем многие другие отощители менее других снижает прочность кирпича. Поэтому когда необходимо обеспечить достаточную прочность кирпича применяют шамот.
В шихту вводят обычно 3% шамота. Если это количество увеличивают то уменьшается формуемость глин обладающих недостаточной пластичностью. Однако при вакуумироваиии глиняной массы и формовании кирпича на вакуумных прессах количество шамота в шихте может быть увеличено до 25% и более.
Шамот легко поддается измельчению до требуемого зернового состава который должен быть в интервале 15–015 мм. Если шамота получаемого из отходов недостаточно для требуемого отощения глины то его вводят в сочетании с другими видами отощающих и выгорающих добавок (шлаков опилок).
Шлаки — это продукты высокотемпературного взаимодействия компонентов исходных материалов (топлива руды плавней и газовой среды). Их химический состав и структура изменяются в зависимости от состава пустой породы вида выплавляемого металла особенностей металлургического процесса условий охлаждения и др.
Применяются в качестве отощающих добавок.
Доломит минерал из группы карбонатов. По химическому составу Доломит — двойнаяуглекислая соль кальция и магния: CaMg[CO3]2. Кристаллизуется в тригональной системе образуя хорошо огранённые кристаллы ромбоэдрического облика. В природе Доломит встречаются в крупно- мелко- и скрытокристаллических агрегатах иногда как породообразующий минерал в оолитовых почковидных ячеистых и др. формах. Крупнокристаллические агрегаты встречаются обычно в гидротермальных образованиях а также среди карбонатных толщ подвергшихся существенной перекристаллизации и метаморфизму.
Цвет серовато-белый иногда с желтоватым буроватым или зеленоватым оттенками. Твёрдость по минералогической шкале 35—4; плотность 2800—2900 кгм3. В отличие от кальцита не вскипает в холодной соляной кислоте но растворяется при нагревании.
) Осадочная горная порода на 90% и более состоящая из минерала доломита; при содержании Доломит 50—90% породу называют известковистым Доломит; при ещё меньшем содержании Доломит — доломитизированным известняком. Самой обычной примесью является кальцит нередко ангидрит или гипс иногда аутигенный кремнезём. Доломит по структуре и пористости бывают плотные с преобладанием основной минеральной массы или цементируемого материала и кавернозно-пористые с резким преобладанием цемента. Доломит по происхождению подразделяются на две генетические группы: экзогенные и эндогенные.
ОБОСНОВАНИЕ СПОСОБА ПРОИЗВОДСТВА
Современная технология производства керамических стеновых и других материалов базируется на двух принципиально отличных технологических схемах: производство пластическим способом (формование) и производство полусухим способом (прессование). Наиболее распространен пластический способ.
Пластический способ – исходные материалы при естественной влажности или предварительно высушенные смешивают с добавками воды до получения теста с влажностью от 18 до 28%. Этот способ производства керамических материалов является наиболее простым наименее металлоёмким и поэтому наиболее распространённым. Он применяется в случаях использования среднепластичных и умереннопластичных рыхлых и влажных глин с умеренным содержанием посторонних включений хорошо размокающих и превращающихся в однородную массу.
Описание физико-химических процессов получение материала
Физико-химические основы процесса сушки
Сушка - этотепловая обработкаматериала применяемаядляудаления влаги из материала путем ее испарения.
Основное назначение сушки– завершение изменения объема полученного полуфабриката обусловленное удалением влаги; обеспечение необходимой прочности полуфабриката позволяющей садить его на печные вагонетки и подвергать другому виду транспортировки; удаление связки до такого количества которое не влияет отрицательно на работу печей и не вызывает дефектов при обжиге.
При испарениивлага содержащаяся в материале переходитиз жидкой фазы вгазообразную котораяввиде водяныхпаровзаполняетокружающее пространство. Какизвестно такое фазовоепревращениесопровождается поглощением тепла поэтому для сушки материала требуется подвод тепловой энергии. Для испарения влаги недостаточно иметь только источник тепловой энергии необходимы также условия перехода водяных паров с поверхности материала в окружающую среду.
Интенсивность испарения влаги зависит от разности парциальных давлений пара на поверхности материала и окружающей среды и от притока тепла к поверхности материала.
При сушкесоздаётсяразность концентраций влагина поверхностииво внутренних слояхматериала чтообуславливает непрерывное поступление влаги от центра к поверхности материала. При наличии источника тепла протекает не только процесс испарения влаги но и процесс нагрева материала от поверхности к центру. Следовательно при сушке происходит сложный процесс влагообмена и теплообмена связанный с изменением теплосодержания и влагосодержания как материала так и окружающей среды.
В процессе сушкитеплокповерхности материалапривнешнемобогреве можетпередаваться излучением или теплопроводностьюот нагретой поверхности или конвекцией от горячих газов и нагретого воздуха. Графическую зависимость влагосодержания материала от времени называют кривой сушки а скорость сушки от времени - кривой скорости сушки. Изменение влагосодержания материала пропорционально времени сушки.
Весь процесс сушки разбит на три отдельных периода протекающих с разной скоростью.
Кпервомуотноситсяпериод подогрева от начальной температуры до температуры насыщенного воздуха. Влагосодержание полуфабриката при этом изменяется незначительно а скорость сушки возрастает скачкообразно.
Второй период –постоянной скорости сушки. Характеризуетсяналичием на кривой горизонтальногоучастка указывающего на то чтоскорость сушкичисленно равнаскорости испарениявлаги споверхностиполуфабриката. Во второй период из материала удаляется влага имеющая с ним непрочную связь т.е. физико-механическую. Температура поверхности полуфабриката остается постоянной; так как основная масса тепла расходуется на испарение влаги. Поверхность изделий остается смоченной влагой поступающей из внутренних слоев.
Период постоянной скорости сушкисохраняется до техпор пока количество испаряющейся споверхностиизделияводы меньше илиравноколичеству воды поступающему по капиллярам из внутренних слоев под действием диффузионно-осмотических и капиллярных сил. Этот процесс называется влагопроводностью (изотермической массопроводностью) материала. Интенсивность сушки во втором периоде зависит уже не от испарения влаги с поверхности изделия а от скорости перемещения ее из внутренних слоев наружу. При этом влага перемещается в основном в виде пара и изделие теряет большую часть физико-химической влаги. С понижением влажности затрудняется поступление влаги с глубинных слоев полуфабриката скорость сушки резко падает что фиксируется изломом кривой указывающей на окончание второго периода сушки. Влажность соответствующая окончанию второго периода называется критической для данного материала и при данных параметрах теплоносителя. Величина критической влажности является важным параметром при определении чувствительности глин к сушке.
К концувторогопериодатемпература изделийприближается ктемпературе теплоносителя. Влагосодержаниеповерхности материалавыравниваетсясего равновеснымвлагосодержанием. Фронт испарениявлагиперемещается внутрь материала и начинается третий период.
Третий период –период падающей скорости сушки характеризуетсядальнейшим снижениемскорости сушкииповышением температурыполуфабриката. Интенсивность влагоотдачи в этом периоде пропорциональна средней влажности материала в интервале от критической до конечной влажности.
Третий период сушкиможноусловноразделить на тричасти.
По характеру скорости удаления влаги называют: первый – период подогрева второй – период постоянной скорости сушки третий – период падающей скорости сушки.
Первый характеризуетсятем чтолишь наиболее мелкие капиллярыоказываютсяв состоянииподавать влагукповерхностным слоямизделия. Количество более крупныхкапилляров слишкоммало и зеркало испарения в этих капиллярах перемещается вглубь материала сокращается вся поверхность испарения и скорость сушки.
Вторая частьпериоданаступаеттогда когдапоследниемелкие капилляры отрываются от поверхностииспарения. На поверхностиизделияустанавливается равновеснаявлажность соответствующая параметрам теплоносителя. Зеркало испарения во всех капиллярах передвигается вглубь материала а возникающий там водяной пар диффиндирует через все возрастающую длину капилляров к поверхности (паропроводность).
Третья частьэтогопериодасушки наступает когда наиболее влажная часть изделия достигает гигроскопической влажности. Температура полуфабриката становится равной температуре сухого термометра. Скорость постепенно снижается до нуля причем в материале устанавливается равновесная влажность определяемая главным образом параметрами теплоносителя и адсорбционными свойствами массы изделия.7
Физико-химические основы процесса обжига
Обжигом называется процессвысокотемпературной обработкиматериалов врезультате которойкирпич –сырец превращается в камнеподобное тело стойкое к механическим физическим и химическим воздействиям. Только при обжиге изделия окончательно формируется структура материала т.е. происходит спекание керамики в результате чего сырец из конгломерата слабосвязанных частиц превращается в достаточно прочное твердое тело.
Процесс обжига делитсяна несколькопериодов:нагревдо 2000Сдосушка– удаление физически связанной влаги из глинистых минераловдальнейший нагревдо 8000С происходитдегидратация– удаление химически связанной влаги входящей в состав глинистого вещества и других минералов повышение температуры до 10000С ивыдержкапри этой температуре – периодсозревания черепкаохлаждениеизделий при дальнейшем охлаждении скорость уменьшения температуры повышается.
При выборе режима обжига необходимо учитывать всепроцессы протекающиевкаждом из периодов обжига.
Режим обжига представляет собойкомплекс взаимосвязанныхфакторов: скорости подъематемпературыобжига длительность обжига приконечной температуре характера газовой среды и скорости охлаждения. В процессе нагрева при различных температурах в материале керамических изделий происходит ряд сложных физико – химических явлений вызывающих изменения его свойств.
В интервалетемператур 20 – 1500С происходитдосушкакирпича – сырца. Досушка производится с целью полного удаления воды затворения и гигроскопической влаги а также равномерного прогрева массы полуфабриката. Наиболее интенсивно вода удаляется при температуре 80 – 1300С. Удаление адсорбционно-связанной воды сопровождается первым эндотермическим эффектом что связанно с возможностью растрескивания сырца. При этом образуется достаточное количество водяного пара который при быстром росте температуры выделяется столь бурно что может разорвать изделие. Температуру нужно поднимать медленно обеспечивая этим равномерное и своевременное удаление остаточной влаги из полуфабриката.
Вторая стадия обжига –подогревсырца до температуры 8000С (до начала упругих деформаций). В период подъема температуры в материале происходят следующие процессы: химически связанная вода начинает удаляться из кирпича – сырца при температуре 3500С а отдача главной массы этой воды идет при температуре 450 – 5000С и может продолжаться до 9000С происходит усадка изделия и снижение механической прочности. При температуре 200 – 8000С начинается выделение летучей части органических примесей глины и введенных в состав массы выгорающих добавок а так же окисляются органические примеси в пределах температуры их воспламенения.
В этот период материал обладает наибольшей пористостью способствующий беспрепятственному удалению воды илетучейчасти органических веществ. Одновременно с отдачейхимическисвязанной влаги оксид железа FeO в результате окисления переходит в оксид железа Fe2O3.
Глина меняет окраску и кирпич приобретает красный цвет. При нагреве до 500 – 6000С начинается разрушение каолинита Al4[Si4O10](OH)8. Процесс дегидратации протекает с образованием метакаолинита
В результате разложения каолинитаи удаления из сырцахимическисвязанной воды происходит полная потеря пластичности.
В интервалетемператур 300 – 10000С происходит разложение карбонатов содержащихся в глине.
При температуре≥4500С происходит разложение карбонатов железа FeCO3
При температуре 450 – 6000С разлагается карбонат магния MgCO3
При температуре 9000С разлагается карбонат кальция CaCO3
Также происходит процесс полиморфного перехода кварца сопровождающийся изменением объема на 2%.
Превращения SiO2при обжиге
Этот период является практическибезопасным. Происходит процесс спекания.
Четвертая стадия обжига (взвар) – характеризуется достижением максимально допустимой температуры обжига изделий созреванием черепка и выдержкой осуществляемой обычно при температуре 900—1050°С. Поднимают температуру осторожно так как при 800—900°С возникают упругие деформации что связано с разрушением кристаллической решетки глинистых минералов и значительными структурными изменениями черепка.
Эта стадия применяется для выравнивания температуры по всей толщине изделия обеспечивающего равномерное распределение жидкой фазы. Эта выдержка необходима также для выравнивания температуры сечения обжигательной печи так и от садки и метода сжигания топлива.
Физико-химические превращения начинающиеся в этом периоде и протекающие более интенсивно при дальнейшем повышении температуры оценивают по-разному.
Так принагревании например каолинита последнийраспадаетсяна свободные окислы собразованием γ-глинозема и кремнезема далее образуется силлиманит А12О32SiO2и SiO2и соединение метастабильной структуры типа метакаолинита А12О32SiO2 имеющего скрыто-кристаллическое почти аморфное строение а затем муллит ЗА12О32SiO2и другие соединения. Процессы образования новых соединений сложны протекание их связано с образованием промежуточных соединений наличием расплава условиями нагрева и др.Период взвара характеризуетсяизменением огневой усадки начинающейся при температуре 750—850°С в зависимости от свойств сырья и заканчивающейся к моменту достижения конечной температуры обжига. Вязкость массы изделий и пористость при 900—950°С резко снижаются в особенности у сырца из сырья богатого карбонатами. Диссоциация карбонатов к этому времени почти полностью заканчивается. Окислы щелочных и щелочно-земельных металлов делая глину легкоплавкой способствуют быстрому размягчению ее за счет увеличения количества расплава и тем самым резко уменьшают пористость массы изделий. Материал изделий переходит в пиропластическое состояние. Железосодержащие минералы наряду со щелочами являются наиболее легкоплавкими составляющими особенно закись железа FеО так как плавится она при температуре на 150—200°С ниже чем Fе2О3. Поскольку в глинах железо чаще всего встречается в виде окиси (Fе2О3) переход ее в закись возможен только в восстановительной среде получаемой при сгорании топлива запрессованного в изделия или при вводе воды в печь на конечной стадии обжига. Поэтому обжиг изделий в восстановительной среде при температуре 900—1000°С равносилен обжигу в обычной (окислительной) среде при 1050—1100° С без риска деформации изделий.
Для выравнивания температурывпечи иболееполногопротекания физико-химических процессоввконце взвара производится выдержка 3-5 ч.
Краткосрочная выдержка такжеспособствует интенсивному протеканию превращенийкремнезема образованиюмуллита хотя завершение этих процессовпереноситсяв областьболеевысокихтемператур чемтемпературыобжига изделий. Поэтому нарастание прочности черепка изделий начинающееся при температуре 800—850°С и продолжающееся до конца обжига (900—1050° С) объясняется не столько влиянием вновь образующихся соединений (из-за недостаточных для их образования температур и времени) сколько действием расплава который благодаря энергии поверхностного натяжения сближает и связывает более крупные частицы массы — дегидратированные частицы глинистого вещества и зерна кварца. Прочность охлажденного расплава (стекловидной фазы) достигает 490— 588 кгссм2(5000—6000 гссм2).
В изделиях пластическогоформования глинистыечастицыболееравномерно распределяются вмассезаполнителя (кварцевыезерна шамотидр.) обволакиваяегозерна. Приобжиге образующаяся на поверхности зерен заполнителя жидкая фаза цементирует их. Проникая в трещины и поры расплав еще больше увеличивает прочность связи.
Технологическая схема производственного процесса
Транспортирование глины из карьера(1) на производство осуществляется автосамосвалами.(2)
После доставки глины ее складируют на складе глин(3). Предварительную заготовку и хранение глины применяют для обеспечения непрерывной работы заводов особенно в зимнее время. Далее глина попадает в глинорыхлители(4) что при нескольких перевалках глины усредняется ее вещественный состав происходит перераспределение влаги и разрушение природной структуры. Это способствует улучшению формовочных и сушильных свойств глиняного сырья.
Затем глинистое сырье проходит через железоотделитель(7) и попадает в вальцы камневыделительные (8). И после попадает в бункер для глины огнеупорной(9).
Доломит привозится машиной (10) на склад доломита(11).Далее доломит проходит через железоотделитель (7) в молотковую дробилку (13). Измельченный доломит проходит к шаровой мельнице(15) для повторного измельчения. Далее доломит попадает в бункер дол0мита (17) через сито (16).
Металургический шлак привозится автомашиной ( 22) на склад шлака (23)и через сито (24) попадает в бункер шлака(25).
Брак кирпича везут погрузчиком (18) к молотковой дробилке (19) чтобы ее размолоть. Далее драбленый кирпич на конвейере (12) поступает в шаровую мельницу (20). А из нее помолотая плитка поступает через сито( 16) в бункер шамота (121).
Все компоненты из бункеров ( 9) (17) (21) и (25) дозируются через дозаторы (26) в смеситель (27). Далее сырье поступает на бегуны мокрого помола (28). Далее материал поступает на вальцы грубого помола (29). Полученный материал поступает в шихтозапастник (31) через плужковый сбрасыватель(30). Приготовленная шихта еще раз проходит через смеситель(32) в вальцы тонкого помола(33).Готовый к использованию шихта попадает а пресс экструдер(34) . Выходящий материал из экструдера режется на кирпичи резательным станком (43).
Автоматический укладчик (35) укладывает готовый сырец на вагонетку для сушки (36)далее изделие отправляется на сушку в камерную сушилку (37). В камерной сушилке происходит обезвоживание сырца.
Просушенный сырец перекладывается на обжиговую вагонетку (38) для обжига в печи (39). Готовый кирпич мостовым краном (40) укладывается на поддон(41) и отправляется на склад готовой продукции(42).
Расчет производственной программы цеха выпускаемого лицевого керамического кирпича производительностью 40 млн штгод
Расчет ведется в порядке обратном технологическому потоку.
Количество изделий поступающих на обжиг:
Qобж.=Q100(100-Побж.) тыс. (1.1)
где Qобж.-количество изделий поступающих на обжиг тыс.шт.
Q – годовая производительность предприятия в натуральных единицах (40000 тыс.шт.)
Побж.- потери при обжиге (2%)
Qобж.=100 40000(100-2)= 40816.3тыс.
Расход массы в абсолютно сухом состоянии на изделия поступающие на обжиг.
Qабс.=Q100q (100-(ппп.+Псуш.) т (1.2)
где: Qабс.-расход массы в абсолютно сухом состоянии на изделия поступающие на обжиг т.
Q – годовая производительность предприятия (40000 тыс. шт.)
q – масса одной плитки (3.5 кг).
ппп. – потери при прокаливании массы в % (387 %)
Qабс.= 400001003.5(100-387)= 145646.1 т.
Определяем расход массы на изделия поступающие на обжиг.
Qc=Qабс100(100-Wф) т. (1.3)
где: Qc – расход массы на изделия поступающие на обжиг с учетом
производственных потерь и формовочной влажности сырца т
Qобж – расход массы в абсолютно сухом состоянии на изделия поступающие на обжиг с учетом брака обжига тыс.шт.
Wф – влажность массы при формовании (8%).
Qc= 145646.1 100(100-8)= 158300.1 т.
Определяем расход массы на формование с учетом производственных потерь при формовании и формовочной влажности.
Gф=(Qс100)(100-Пф) т. (1.4)
где: Пф – потери при формовании (2%).
Yф-объемная масса массы (14)
Gф=( 158300.1 100)(100-2)= 161530.7 т.
Vф= 161530.7 14= 115379.1 м3
Определяем количество сформованных изделий.
где: Qф – количество сформованных изделий тыс.шт.
Gф - расход массы на формование т
gф - масса сформованных изделий ( 3.5 кг.).
Qф= 161530.7 3.5= 46151 тыс. шт.
Количество массы поступающей на перемешивание в абсолютно сухом состоянии.
Gn=( Gф(100- Wф))100 т. (1.7)
Gn=( 161530.7 (100-8))100= 148607.6 т.
Определяем расход компонентов шихты при транспортировке в абсолютно сухом состоянии.
Gсм=( Gn100)(100-Пт) т. (1.8)
где: Пт – потери при транспортировке (1%).
Gсм=(148607.6 100(100-1)= 150108.6 т.
Определяем расход каждого компонента шихты в абсолютно сухом состоянии.
Г=( Gсмг)100 т. (1.9)
Ш=( Gсмш)100 т. (1.10)
где: Г – содержание глины в шихте (85%)
Ш – содержание добавки (шлака) в шихте (10%)
Г=( 150108.6 85)100= 127592.3 т.
Ш=( 150108.6 10)100= 15010.8 т.
Б=( 150108.6 3)100= 4503.2 т
Д=( 150108.6 2)100= 3002.3 т
Определяем расход компонентов с учётом естественной влажности.
Ге=(Г100)(100-Wк) т. (1.11)
где: Wк – карьерная влажность глины (6%).
Yд – объемная масса рыхлого глины (18 тм3).
Г – расход глины в абсолютно сухом состоянии т.
Ге – расход глины с учетом карьерной влажности т.
Ге=( 127592.3 100)(100-6)= 135736.4 т.
Vг= 135736.4 18= 75409 м3.
Ш=(Ш100)(100-Wк) т.
где: Ш – Влажность шлака (0%).
YЩ – объемная масса шлака (2.5 тм3).
Ш – расход шлака в абсолютно сухом состоянии т.
Ше – расход шлака с учетом карьерной влажности т.
VШ= 15010.8 2.5= 6004 м3.
Б=(Б100)(100-Wб) т.
где: Б – карьерная влажность Бой (1%).
YБ – объемная масса рыхлого Бой (19 тм3).
Б – расход Бой в абсолютно сухом состоянии т.
Бе – расход Бой с учетом карьерной влажности т.
Б=( 4503.2 100)(100-1)= 4548.4 т.
VБ= 4548.4 19= 2393.9 м3.
Аналогично определяется расход добавки.
Д=(Д100)(100-Wк) т. (1.12)
где: Де – расход доломитас учетом естественной влажности.
WД – естественная влажностьдоломита (2%).
YД – объемная масса Доломита 2.8 тм3.
Ше=( 3002.3 100(100-2)= 3063.6 т.
Vш= 3063.6 2.8= 1094.6 м3.
Расход глины в плотном состоянии.
Vпл= VдКр м3. (1.14)
где: Vпл – объем глины в плотном теле.
Кр – коэффициент разрыхления глины (15).
Q – производительность ( 40000 тыс. шт.)
V- расход на 1000в м3.
Vпл= 135736.4 15= 90490.9 м3.
V= 90490.9 40000= 2.26 м3.
Расход шихты в естественном состоянии.
Ше= Ге+ Ше+ГТ+П т. (1.16)
Vших= Vг+ Vш м3. (1.17)
Шихе= 135736.4 + 15010.8 +4548.4 +3063.6 = 158357т.
Vших= 75409 + 6004+2393.9 + 1094.6 = 89900 м3.
Расход воды на формование.
Вф= Gф- Ше т. (1.18)
где: Gф – расход массы формовочной влажности т.
Ше – расход шихты в естественном состоянии т.
Вф – расход воды на формование
Вф= 161530.7 -158357 = 3173 т.
Производительность завода 40000000.усл. кирпича в год.
Количество рабочих дней:
N=365--ППР=365-15=350 рабочих дней в году
где ППР- профилактико-предупредительные работы; как правило на них отводится 15 дней.
Завод работает в 3 смены. Количество часов в одной смене – 8.
6 Материальный баланс.
Наименование материалов
Сырец свежеотформованный
Количество массы на формование с учетом формовочной влажности
Количество шихты поступающей на перемешивание с естественной влажностью в том числе
7 Основное технологическое оборудование
Наименование оборудования
Характеристика оборудования
Производительность 30 м3ч
Габариты 4000х1400х980мм
Производительность до 25 м3ч
Скорость ленты конвейера до 2 обмин
Габариты 6350х2530х1620 мм
Вальцы камневыделительные
Производительность 25 м3ч
Рабочий зазор между валками 10 мм
Диаметр гладкого валка 1000 мм
Диаметр ребристого валка 700 мм
Установленная мощность 43 кВт
Габаритные размеры 3185х2805х1325 мм
Производительность – 5 – 7т
Диаметр барабана – 2000мм
Длина барабана – 3000мм
Габаритные размеры – 1675х1827х1675мм
Производительность 64тчас
Установленная мощность 37 кВт
Габариты-5900-1700-1350мм
Вальцы тонкого помола
Производительность .5Тч
Установленная мощность 52 кВт
Габаритные размеры 3800х3230х1220 мм
Потребляемая мощность кВт 2
Извлекающая способность не хуже см.кг 805
Глубина зоны извлечения см 25
Ширина ленты технологического транспортера мм до 650-
Вальцы грублго помола
Производительность – 35м3час
Бегуны мокрого помола
Частота вращения вертикального вала обмин 227
Перерабатываемый материал Глина
Производительность по исходному материалу тч 43
Мощность электродвигателя кВт 80
Масса бегунов без электродвигателя кг 32700
Габаритные размеры мм:
Список использованной литературы
А.М. Салахов В.И. Ремезникова О.В. Спирина А.Ю. Мочалов «Производство строительной керамики». Казань 2003. 292с.
А.М. Саляхов « Увлекательная керамика». Казань. 2004. 192с..
М.Н. Горбовец « Строительные машины том 2». М. 1991. 496с.
Белецкий Б.Ф. Строительные машины и оборудование: Справочное пособие для строит. фак. вузов и техникумов производственников-механизаторов инженер.- техн. работников строит. орг – Ростов нД: Феникс 2002.-591с.
Гегерь В.Я. Городков А.В. Основы архитектурного проектирования промышленных зданий.- Брянск. БГИТА.2004.-118с.
Мороз и.и. технология строительной керамики. - Мска.: Эколит 2011г - 384с
Рекомендуемые чертежи
Свободное скачивание на сегодня
Обновление через: 15 часов 43 минуты