Проектирование производственного корпуса ремонтного предприятия


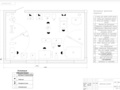
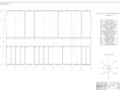
- Добавлен: 25.10.2022
- Размер: 2 MB
- Закачек: 1
Узнать, как скачать этот материал
Подписаться на ежедневные обновления каталога:
Описание
Проектирование производственного корпуса ремонтного предприятия
Состав проекта
![]() |
![]() ![]() ![]() ![]() |
![]() ![]() ![]() ![]() |
![]() |
![]() ![]() ![]() |
Дополнительная информация
Контент чертежей
Кузнечный отдел Силин Д.А. ПТС-17-1.dwg

Подвод холодной воды с отводом в канализацию
Условные обозначения
Стенд для загиба ушков рессор
Стенд для испытания рессор
Стенд для разборки и сборки рессор
Верстак для рессорщика
Обдирочно-шлифовальный станок
Вертикально-сверлильный станок
Гибозакалочная машина для рессорных листов
Плита правочная на подставке
Ванна для охлаждения рессорных листов
Щит управления к печи
Печь для нагрева рессор
Бабка ладильная для правки рессор
Кран поворотный свободоносящий
Печь для нагрева поковок
Молот приводной пневматический
Вентилятор дутьевой с электродвигателем
Ларь для кузнечного инструмента
Наковальня на подставке
Корпус Силин Д.А.ПТС-17-1.dwg

Геометрическая емкость ковша
Тип базовой машины Спец. оноос. шасси
Мощность силовой установки
машины эксплуатационная
Максимальная глубина резания
КП МЗР 190205 13 08 00 000 ВО
Экспликация производственного помещения
Производственный корпус
Разборочно-моечный участок
Слесарно-механический участок
Участок ТО и диагностики
Ремонтно-монтажный учаток
Мендницко-жестяное отделение
Электроремонтный участок
Инструментальный участок
Отделение по ремонту гидрооборудования
Компрессорный участок
Аккумуляторный участок
Дефектовочный участок
Шиномонтажное отделение
ПЗ Силин Д.А. ПТС-17-1.docx
РОССИЙСКОЙ ФЕДЕРАЦИИ
ФЕДЕРАЛЬНОЕ ГОСУДАРСТВЕННОЕ БЮДЖЕТНОЕ
ОБРАЗОВАТЕЛЬНОЕ УЧРЕЖДЕНИЕ
«ТЮМЕНСКИЙ ИНДУСТРИАЛЬНЫЙ УНИВЕРСИТЕТ»
Пояснительная записка к курсовой работе
по дисциплине: «Основы эксплуатации и ремонта транспортно-технологических средств и оборудования»
Тема: «Проектирование производственного корпуса ремонтного предприятия (г. Сочи 112 ед. техники кузнечный участок)»
ОПРЕДЕЛЕНИЕ ПЕРИОДИЧНОСТИ И КОЛИЧЕСТВА ПЛАНОВЫХ ТО И РЕМОНТОВ МАШИН6
1Расчёт количества ТО и ТР для одноковшовых экскаваторов (на одну единицу техники):6
2Расчёт количества ТО и ТР для стрелового автомобильного крана (на одну единицу техники):7
3Расчёт количества ТО и ТР для бульдозера с неповоротным отвалом (на одну единицу техники):8
4Расчёт количества ТО и ТР для одноковшового фронтального погрузчика (на одну единицу техники):8
5Расчёт количества ТО и ТР для самоходного катка (на одну единицу техники):9
6Расчёт количества ТО и ТР самосвалов (на одну единицу техники):9
7Расчёт количества ТО и ТР автобусов среднего класса (на одну единицу техники):10
8Расчёт количества ТО и ТР легковых автомобилей (на одну единицу техники):10
ТРУДОЕМКОСТЬ ПРОВЕДЕНИЯ ТО И ТР11
1Расчёт трудоёмкости проведения ТО и ТР11
2Расчёт трудоёмкости текущего ремонта (ТР) для одноковшовых экскаваторов12
3Расчёт трудоёмкости текущего ремонта (ТР) для стреловых автомобильных кранов12
4Расчёт трудоёмкости текущего ремонта (ТР) для бульдозеров с неповоротным отвалом12
5Расчёт трудоёмкости текущего ремонта (ТР) для одноковшовых фронтальных погрузчиков12
6Расчёт трудоёмкости текущего ремонта (ТР) для катков12
7Расчёт трудоёмкости текущего ремонта (ТР) для самосвалов12
8Расчёт трудоёмкости текущего ремонта (ТР) для автобусов среднего класса .13
9Расчёт трудоёмкости текущего ремонта (ТР) для легковых автомобилей13
РАСЧЁТ ТРУДОЁМКОСТИ ТЕХНИЧЕСКОГО ОБСЛУЖИВАНИЯ (ТО-2 И ТО-1) ПТСДМ14
1Расчёт трудоёмкости технического обслуживания (ТО-2 и ТО-1) для ЭО 14
2Расчёт трудоёмкости технического обслуживания (ТО-2 и ТО-1) для стреловых автомобильных кранов14
3Расчёт трудоёмкости технического обслуживания (ТО-2 и ТО-1) для бульдозеров с неповоротным отвалом15
4Расчёт трудоёмкости технического обслуживания (ТО-2 и ТО-1) для одноковшовых фронтальных погрузчиков15
5Расчёт трудоёмкости технического обслуживания (ТО-2 и ТО-1) для самоходного катка15
6Расчёт трудоёмкости технического обслуживания (ТО-2 и ТО-1) для самосвалов16
7Расчёт трудоёмкости технического обслуживания (ТО-2 и ТО-1) для автобусов среднего класса16
8Расчёт трудоёмкости технического обслуживания (ТО-2 и ТО-1) для легковых автомобилей16
ОПРЕДЕЛЕНИЕ КОЛИЧЕСТВА РАБОЧИХ И ПЛОЩАДЕЙ ПРОИЗВОДСТВЕННЫХ УЧАСТКОВ И ЦЕХОВ18
1Расчет количества производственных рабочих18
2Расчет технологически необходимого количества рабочих18
3Расчет штатного количества рабочих19
4Расчет количества непроизводственных рабочих20
5Определение площадей производственных участков и цехов21
ПРИНЦИП РАЗМЕЩЕНИЯ ОТДЕЛЕНИЙ ВНУТРИ КОРПУСА И ПЛАНА САМОГО КОРПУСА25
КУЗНЕЧНОЕ ОТДЕЛЕНИЕ32
СОСТАВЛЕНИЕ ПЛАН-ГРАФИКА ТО35
1Расчет дня в котором будет проводиться ТО-2 и ТО-135
2Расчет дня в котором будет проводиться ТО-1 и ТО-2 для одноковшовых экскаваторов (на одну единицу техники)35
3Расчет дня в котором будет проводиться ТО-1 и ТО-2 для стрелового автомобильного крана (на одну единицу техники)35
4Расчет дня в котором будет проводиться ТО-1 и ТО-2 для бульдозера с неповоротным отвалом (на одну единицу техники)36
5Расчет дня в котором будет проводиться ТО-1 и ТО-2 для одноковшового фронтального погрузчика (на одну единицу техники)36
6Расчет дня в котором будет проводиться ТО-1 и ТО-2 для самоходного катка (на одну единицу техники):36
7Расчет дня в котором будет проводиться ТО-1 и ТО-2 для самосвала (на одну единицу техники)36
8Расчет дня в котором будет проводиться ТО-1 и ТО-2 для автобусов среднего класса (на одну единицу техники)36
9Расчет дня в котором будет проводиться ТО-1 и ТО-2 для легкового автомобиля (на одну единицу техники)37
СПИСОК ИНФОРМАЦИОННЫХ ИСТОЧНИКОВ39
Обслуживание дорожно-строительных машин содержит работы по подготовке их к работе транспортированию хранению техническому обслуживанию и ремонту. Основная задача эксплуатации заключается в поддержании работоспособности машин при наименьших затратах на поддержание работоспособности и минимальных вредных воздействий на окружающую среду.
Возможность применения для дорожной техники более совершенной системы технического обслуживания и ремонта позволяет повысить качество этих мероприятий связанных с технической эксплуатацией машин.
Рациональная организация работы машинного парка максимальное увеличение времени использования машин и соответственно сокращение всех видов простоев повышение коэффициентов сменности и технической готовности улучшение качества технического обслуживания и ремонта машин – важнейшие задачи которые должны решаться в дорожных организациях при эксплуатации машин.
В данной работе мы проведем расчет предприятия парк которого включает:
Экскаватор одноковшовый 5 – ой размерной группы Terex TX 300 (15 единиц)
Кран стреловой автомобильный КС-35719 – 7 – 02 (15 единиц)
Бульдозер с неповоротным отвалом Б10М 0111 – 1Е (14 единиц)
Фронтальный погрузчик одноковшовый Амкодор 332В – 01 (16 единиц)
Самоходный каток DM – 10 – VD (14 единиц)
Самосвал КАМАЗ – 45143 – 50 (15 единиц)
Легковой автомобиль ВАЗ – 2114 (12 единиц)
Автобус среднего класса КАВЗ-4238 (11 единиц)
ОПРЕДЕЛЕНИЕ ПЕРИОДИЧНОСТИ И КОЛИЧЕСТВА ПЛАНОВЫХ ТО И РЕМОНТОВ МАШИН
Рассчитаем наработку на планируемый период - LП
где P – количество рабочих дней равное 299; Q – рабочая смена равная 8 часам.
Число КР (NКР) ТО-2 (NТО-2) и ТО-1 (NТО-1) за цикл на одну единицу техники для автомобилей и ПТДСМ наработка которых определяется в километрах можно представить в следующим виде:
Для ПТСДМ количество технологических воздействий КР (NКР) ТР (NТР) ТО-2 (NТО-2) и ТО-1 (NТО-1) за цикл определяется по формулам (1.) (1.2) (1.3) и (1.4):
где LП – наработка на планируемый период (данные предприятия); LТР – скорректированная наработка до ТР.
1Расчёт количества ТО и ТР для одноковшовых экскаваторов (на одну единицу техники):
Nто-2 = 10000÷500-(1+2) = 17
Nто-1 = 10000÷100-(1+2+17) = 80
Годовое число ТО-1 ТО-2 и ТР для ПТСДМ на весь парк машин одной модели можно рассчитать по формулам (1.6) (1.7) (1.8):
Годовое число ТО-1:
NТР.Г = NТР МИ (1.8)
где МИ – списочное число машин данной марки и модели.
2Расчёт количества ТО и ТР для стрелового автомобильного крана (на одну единицу техники):
Nто-2 = 5000÷250-(1+2) = 17
Nто-1 = 5000÷50-(1+2+17) =80
3Расчёт количества ТО и ТР для бульдозера с неповоротным отвалом (на одну единицу техники):
Nто-2 = 5760÷240-(1+2) = 21
Nто-1 = 5760÷60-(1+2+21) = 72
4Расчёт количества ТО и ТР для одноковшового фронтального погрузчика (на одну единицу техники):
5Расчёт количества ТО и ТР для самоходного катка (на одну единицу техники):
6Расчёт количества ТО и ТР самосвалов (на одну единицу техники):
Nто-2 = 300000÷12000-(1+4) = 20
Nто-1 = 300000÷3000-(1+4+20) = 75
7Расчёт количества ТО и ТР автобусов среднего класса (на одну единицу техники):
Nто-2 = 500000÷14000-(1+7) = 28
Nто-1 = 500000÷3500-(1+7+28) = 106
N1.Г = 106 11 = 1166
8Расчёт количества ТО и ТР легковых автомобилей (на одну единицу техники):
Nто-2 = 400000÷16000-(1+10) = 14
Nто-1 = 400000÷4000-(1+10+14) = 75
ТРУДОЕМКОСТЬ ПРОВЕДЕНИЯ ТО И ТР
1Расчёт трудоёмкости проведения ТО и ТР
Для определения удельной скорректированной трудоёмкости текущего ремонта (tТР) для автомобилей воспользуемся формулой:
tТР = tНТР К1 К2 КЗ К4 К5 (2.1)
Скорректированная трудоемкость текущего ремонта (TТР) ПТДСМ для ПТДСМ определяют по формуле
TТР = tНТР КЗ К4 К5 (2.2)
где - нормативная удельная трудоёмкость ТР автомобилей чел·час1000 км[1];
tНТР - нормативная удельная трудоёмкость ТР ПТСДМ чел·час.
КЗ - коэффициент корректирования нормативов в зависимости от природно-климатических условий;
К4 - коэффициент корректирования нормативов в зависимости от пробега с начала эксплуатации;
К5 - коэффициент корректирования нормативов в зависимости от количества технологически совместимых групп подвижного состава на предприятии.
Для определения трудоёмкости текущего ремонта для одного автомобиля на плановый период (tПТР) воспользуемся формулой:
tП ТР = tТР LП 1000 чел·час (2.3)
где LП – плановый пробег.
Для определения трудоёмкости на плановый период (tПТР) для одной единицы ПТСДМ воспользуемся формулой:
tПТР = tТР ТР чел·час (2.4)
где ТР – количество текущих ремонтов
Для группы автомобилей одной марки и модели при прочих равных условиях трудоемкость t М ТР рассчитывается по формуле
t М ТР = МА· t П ТР чел·час (2.5)
МА - количество автомобилей одной марки и модели.
2Расчёт трудоёмкости текущего ремонта (ТР) для одноковшовых экскаваторов
TТР = 800·09·13·105=9828 чел·час
t М ТР = 15·9828 = 14742 чел · час
Аналогично производим расчёт для остальных групп машин.
3Расчёт трудоёмкости текущего ремонта (ТР) для стреловых автомобильных кранов
TТР = 820·09·13·105=11193 чел·час
t М ТР = 15·11193 = 16790 чел · час
4Расчёт трудоёмкости текущего ремонта (ТР) для бульдозеров с неповоротным отвалом
TТР = 670·09·13·105=8231 чел·час
t М ТР = 14·8231 = 11523 чел · час
5Расчёт трудоёмкости текущего ремонта (ТР) для одноковшовых фронтальных погрузчиков
ТР = 380·09·13·105=4668 чел·час
t М ТР = 16·4668 = 7469 чел · час
6Расчёт трудоёмкости текущего ремонта (ТР) для катков
TТР = 195·09·13·105=2396 чел·час
t М ТР = 14·2396 = 33544 чел · час
7Расчёт трудоёмкости текущего ремонта (ТР) для самосвалов
TТР = 500·11·12·09·13·105=8108 чел·час
t М ТР = 15·8108 = 12162 чел · час
8Расчёт трудоёмкости текущего ремонта (ТР) для автобусов среднего класса
TТР = 950·11·12·09·13·105=15405 чел·час
t М ТР = 11·15405 = 16946 чел · ча
9Расчёт трудоёмкости текущего ремонта (ТР) для легковых автомобилей
TТР = 300·11·12·09·13·105= 4865 чел·час
t М ТР = 12·4865 = 5838 чел · час
РАСЧЁТ ТРУДОЁМКОСТИ ТЕХНИЧЕСКОГО
ОБСЛУЖИВАНИЯ (ТО-2 И ТО-1) ПТСДМ
Трудоёмкость i-го технического обслуживания на плановый период определяется по формуле
tТО i = N ТО i t Н i · К5 (3.1)
1Расчёт трудоёмкости технического обслуживания (ТО-2 и ТО-1) для ЭО
Трудоёмкость 1-го технического обслуживания на плановый период:
tТО 1 =80·8·105 = 672 чел · час
Трудоёмкость 2-го технического обслуживания на плановый период:
tТО 2 =17·25·105 = 446 чел · час
Общая трудоёмкость технического обслуживания для всего парка:
tТО1 общ =672 ·15= 1080 чел · час
tТО2 общ =446·15= 6690 чел · час
2Расчёт трудоёмкости технического обслуживания (ТО-2 и ТО-1) для стреловых автомобильных кранов
tТО 1 =80·7·105 = 605 чел · час
tТО 2 =17·28·105 = 500 чел · час
tТО1 общ =605·15=9075 чел · час
tТО2 общ =441 · 15 = 6615 чел · час
3Расчёт трудоёмкости технического обслуживания (ТО-2 и ТО-1) для бульдозеров с неповоротным отвалом
tТО 1 =72·6·105 = 454 чел · час
tТО 2 =21·18·105 = 397 чел · час
tТО1 общ =454·14= 6356 чел · час
tТО2 общ =152 · 14 = 2128 чел · час
4Расчёт трудоёмкости технического обслуживания (ТО-2 и ТО-1) для одноковшовых фронтальных погрузчиков
tТО 1 =72·3·105 = 227 чел · час
tТО 2 =21·12·105 = 265 чел · час
tТО1 общ =227·16= 3632 чел · час
tТО2 общ =265 · 16 = 4240 чел · час
5Расчёт трудоёмкости технического обслуживания (ТО-2 и ТО-1) для самоходного катка
tТО 1 =72·2·105 = 151 чел · час
tТО 2 =21·7·105 = 154 чел · час
tТО1 общ =151·14= 2114 чел · час
tТО2 общ =154 · 14 = 2156 чел · час
6Расчёт трудоёмкости технического обслуживания (ТО-2 и ТО-1) для самосвалов
tТО 1 =75·34·105 = 268 чел · час
tТО 2 =20·145·105 = 305 чел · час
tТО1 общ =268·15= 4020 чел · час
tТО2 общ =305 · 15 = 4575 чел · час
7Расчёт трудоёмкости технического обслуживания (ТО-2 и ТО-1) для автобусов среднего класса
tТО 1 =106·58·105 = 646 чел · час
tТО 2 =28·24·105 = 706 чел · час
tТО1 общ = 646·11 = 7106 чел · час
tТО2 общ = 706 · 11 = 7766 чел · час
8Расчёт трудоёмкости технического обслуживания (ТО-2 и ТО-1) для легковых автомобилей
tТО 1 =75·23·105 = 181чел · час
tТО 2 =14·92·105 = 135 чел · час
tТО1 общ =181·12= 2172 чел · час
tТО2 общ =135 · 12 = 1620 чел · час
Таблица 3.1 - Трудоёмкость проведения ТО и ТР
Трудоемкость чел * час
Одноковшовые экскаваторы
Стреловые автомобильные краны
Бульдозеры с неповоротным отвалом
Одноковшовые фронтальные погрузчики
Автобусы среднего класса
ОПРЕДЕЛЕНИЕ КОЛИЧЕСТВА РАБОЧИХ И ПЛОЩАДЕЙ ПРОИЗВОДСТВЕННЫХ УЧАСТКОВ И ЦЕХОВ
1Расчет количества производственных рабочих
Количество рабочих определяется исходя из расчетной трудоемкости на планируемый период. К производственным рабочим относятся рабочие зон и участков непосредственно выполняющие работы по капитальному ремонту. Различают технологически необходимое (явочное) и штатное (списочное) число рабочих. Технологически необходимое число рабочих обеспечивает выполнение суточной а штатное годовой производственной программы (объемов работ) по капитальному ремонту.
2Расчет технологически необходимого количества рабочих
Чтобы рассчитать технологически необходимое количество рабочих РТ на производстве необходимо объем работ в плановый период разделить на фонд рабочего времени в плановый период.
Технологически необходимое (явочное) число рабочих определяется по формуле (4.1):
где ТГ - годовой объем работ по капитальному ремонту чел-ч; ФТ - фонд рабочего времени ч.
За ФТ примем 2392 часов. Количество рабочих дней в 2020 году составляет 269 дней (299 рабочих дней и 30 дней отпуска) что при условии шестидневного рабочего графика и при 8-часовой рабочей нагрузке составит 2152 часов.
РТ = 160169÷ 2152 = 75
– человек -технологически необходимое количество рабочих для заданной годовой трудоемкости.
3Расчет штатного количества рабочих
После расчета технологически необходимого количества рабочих необходимо рассчитать штатное число рабочих РШ определяется по формуле (4.2)
где ФШ - годовой фонд времени «штатного» рабочего час.
Значение штатного количества рабочих РШ в отличие от технологически необходимого РТ скорректировано с условием потерь рабочего времени на период отпусков больничных и т.д.
Общие потери рабочего времени составляют примерно 4 5% от годового фонда технологически необходимого рабочего времени. Тогда найдем значение ФШ (4.3):
Фш = (Д к.г - Дв - Дп – Дот – Ду.п) · Тсм – Дпп ·1 (4.3)
ФШ = (365-52-14-30-10) ·8-2·1=2070 час
где Д К.Г - число календарных дней в году;
Д В - число выходных дней в году;
Д П - число праздничных дней в году;
ТСМ - продолжительность смены ч;
Д ПП - число субботних и праздничных дней в году;
- час сокращения рабочего дня перед выходными днями
где Д ОТ - число дней отпуска установленного для данной профессии рабочего;
Д У.П - число дней невыхода на работу по уважительны причинам
Примем ФШ как 2070 час рабочего времени в году так как потери приняты в размере 5% от годового фонда ФТ [3].
РШ = 160169 ÷ 2070 = 78
штатных рабочих необходимо для выполнения плана по капитальному ремонту данного парка машин.
4Расчет количества непроизводственных рабочих
Кроме работников производства так же необходимо рассчитать количество непроизводственных работников. Непроизводственный персонал - персонал не основной деятельности не принимающий непосредственного участия в производственном процессе.
Количество непроизводственных рабочих непосредственно зависит от количества штатных производственных рабочих поэтому их число принимается в процентном соотношении от штатного количества рабочих на производстве:
Вспомогательные рабочие к которым относятся контролеры транспортные рабочие кладовщики разнорабочие составляют 12 15% от численности основных рабочих.
Работники инструментального участка принимают равным 25%
Отдел главного механика (ОГМ) 17%
Численность инженерно-технических работников (ИТР) принимают в размере 13 15% от числа производственных рабочих причем 50% из них работает на производстве (в том числе мастера начальники цехов).
Счетно-конторский персонал (СКП) составляет 12 14% от числа производственных рабочих.
Младший обслуживающий персонал (уборщики цехов служебных помещений территории гардеробщики курьеры) принимают в размере 2 3% от числа производственных рабочих.
Таблица 4.1 – Непроизводственные рабочие
Категория непроизводственных работников
Вспомогательный персонал
Инструментальный участок
Младший обслуж. персонал
5Определение площадей производственных участков и цехов
Для определения производственных площадей необходимо произвести распределение рабочих по производственным участкам так как удельная площадь на одного рабочего может сильно различаться от вида производимых работ на данном производственном участке. Распределение трудоемкости по участкам предприятия по ремонту дорожно-строительных машин производится по рекомендованным значениям.
Таблица 4.2 – Распределение рабочих по производственным участкам
Производственные участки
Слесарно-механический
Медницко-жестяницкий
После распределения рабочих по производственным участкам можно произвести расчет площадей этих участков. Площади производственных участков определяют умножением удельной площади приходящейся на одного рабочего (табл. 4.2) на количество рабочих на данном участке в наибольшую смену.[4]
Удельная площадь на одного рабочего включает площади необходимые для выполнения работ в том числе для размещения объектов ремонта оборудования стеллажей и рабочих проходов.
Площади остальных бытовых помещений (в м2) определяют по числу всех категорий работников занятых в наибольшую смену:
на одного ИТР или СКП 5м2
кабинет начальника цеха 10м2
площади складских помещений принимают в размере 25% от производственных площадей.
гардеробы из расчета обслуживания всех производственных и вспомогательных рабочих составляют 08м2 на одного рабочего. (830м2)
Таблица 4.3 – Площадь участков
Участки ремонтного завода
Наружная мойка малярный испытательная станция выварочный гальванический
Разборочный сборочный деревообрабатывающий
Кузнечный термический металлизационный
Ремонта корпусных деталей рам сварочно-наплавочный мотороремонтный
Комплектовки дефектовки
Жестяницкий медницкий механический
Топливной аппаратуры инструментальный
Электроремонтный обойный
Таблица 4.4 – Проведем расчет площадей производственных участков и цехов
Площадь разборочно–моечного участка
Площадь ремонта агрегатов
Площадь слесарно-механического участка
Площадь ТО и диагностики
Площадь ремонтно-монтажного участка
Площадь кузнечного участка
Площадь сварочного участка
Медницко-жестяницкого
Площадь отделения по ремонту гидрооборудования
Компрессорного участка
Аккумуляторного участка
Площадь дефектовочного участка
Шиномонтажного участка
Расчетную площадь производственного корпуса состоящую из суммы площадей цехов и отделений увеличивают на 10 15% с учетом межцеховых проходов.
(2664+830) +10%=3744 м2
Общая площадь предприятия S = 3744 м2
ПРИНЦИП РАЗМЕЩЕНИЯ ОТДЕЛЕНИЙ ВНУТРИ КОРПУСА И ПЛАНА САМОГО КОРПУСА
Определив габаритные размеры основного производственного здания размещают в пролетах корпуса все цехи и помещения так чтобы они располагались в порядке технологического потока ремонта машин избегая излишних грузопотоков. Тепловые цехи должны быть расположены группой в одном из пролетов корпуса и отделены огнестойкими стенами от других цехов. Испытательная станция должна размещаться в одном из крайних пролетов корпуса недалеко от сборочного цеха и рядом с моторным цехом. Комплектовочное отделение со складом должно размещаться непосредственно у сборочных участков основного производства и иметь по соседству склад запасных частей и материалов. В практике проектирования ремонтных предприятий в зависимости от пути движения рамы для агрегаторемонтных предприятий базовых деталей могут быть приняты следующие варианты схем технологического процесса.
Прямоточная планировка.
Г-образная планировка.
П-образная планировка.
Тупиковый способ сборки.
Преимуществами прямоточной схемы (рис. 3) являются прямолинейность и соответственно удобство перемещения базовой детали и других крупногабаритных и тяжелых деталей минимальное пересечение транспортных потоков недостатками - ограничение длины разборочных и сборочных поточных линий относительное увеличение дальности транспортирования деталей от мест разборки к местам сборки плохая возможность изоляции разборочно-моечного участка от других участков.
Применение Г-образной и П-образной схем позволяет более эффективно изолировать разборочно-моечный участок от других участков несколько сократить дальность транспортирования деталей; значительно уменьшается необходимость ограничения длины разборочных и сборочных поточных линий (особенно при П-образной схеме).
Однако не прямолинейность перемещения базовой детали и других крупногабаритных и тяжелых деталей обусловливает повышенное число пересечений транспортных потоков и трудности в их организации.
Разработку компоновочного плана начинают с выбора сетки колонн (t L) и определения размеров здания. Для одноэтажных зданий наиболее часто применяется сетка колонн 12×6 м которая определяет размеры здания. Исходя из принятой компоновочной схемы задают число пролетов регламентируя этим ширину здания. Длину здания определяют делением его площади на ширину. Рекомендуемые соотношения ширины и длины здания от 1:13 до 1:2. Добиться рекомендуемых соотношений можно изменяя число пролетов а при необходимости - и сетку колонн выбирая ее из следующих значений: 18×6 м; 18×12 м; 24×12 м. Размеры пролетов и шагов колонн могут быть и большими но обязательно кратными 6 м что необходимо по требованиям унификации изделий строительной индустрии.
Рис. 5.1. Маркировка разбивочных осей.
Принципиальные схемы компоновочных решений для различных вариантов направления главного потока изображены на рис. 2 3 4 и 5.
Рис. 5.2. Схема прямоточной планировки предприятия по ремонту полнокомплектных машин:
- бытовые помещения; 2 - склад запасных частей и материалов; 3 - отделение топливной аппаратуры и электрооборудования; 4 - отделение ремонта и сборки двигателей; 5 - испытательная станция; 6 - разборочно- моечное отделение; 7 - контрольно-сортировочное отделение; 8 - комплектовочное отделение со складом; 9 - рамное отделение; 10 - агрегатное отделение; 11 - участок устранения дефектов; 12 - отделение сборки машин; 13 - слесарно-механическое отделение; 14 - участок ремонта навесного оборудования; 15 - жестяницкое отделение; 16 - участок ремонта кабин; 17 - гальваническое отделение; 18 - термическое отделение; 19 - кузнечное отделение; 20 - сварочно-металлизационное отделение; 21 - медницко- радиаторное отделение; 22 - склад деталей ожидающих ремонта; 23 - компрессорная; 24 -- инструментально-раздаточная кладовая; 25 - инструментальное отделение; 26 - отдел главного механика; 27 - деревообрабатывающее и обойное отделения;28 - малярное отделение
Рис. 5.3. Схема Г-образной планировки предприятия по ремонту полнокомплектных машин:
- гальваническое отделение; 2 - термическое отделение: 3 - кузнечное отделение; 4 - сварочно-металлизационное отделение; 5 - медницко- радиаторное отделение; 6 - бытовые помещения; 7 - отделение топливной аппаратуры и электрооборудования; 8 - отделение ремонта и сборки двигателей; 9 - испытательная станция; 10 - слесарно-механическое отделение; 11 - инструментальное отделение; 12 - отдел главного механика; 13 - комплектовочное отделение со складом; 14 - агрегатное отделение; 15 - рамное отделение; 16 - отделение сборки машин; 17 - участок ремонта навесного оборудования; 18 - участок ремонта кабин; 19 - участок устранения дефектов; 20 - компрессорная; 21 - инструментально-раздаточная кладовая; 22 - склад запасных частей и материалов; 23 - склад деталей ожидающих ремонта; 24 - контрольно-сортировочное отделение; 25 - разборочно-моечное отделение; 26 - деревообрабатывающее и обойное отделения; 21 - жестяницкое отделение; 28 - малярное отделение.
Форма потока обусловливает взаимное территориальное размещение цехов отделений и участков т. е. принцип их компоновки в производственном корпусе. Компоновка цехов отделений и участков является ответственной и трудоемкой работой. Выполняя компоновку необходимо учитывать также следующие основные положения:
Все производственные цехи отделения и участки целесообразно размещать в одном здании (производственном корпусе) так как затраты на строительство в этом случае будут значительно ниже чем при строительстве отдельных разрозненных зданий. Производственные здания ремонтных предприятий строят как правило одноэтажными и многопролетными.
Периметр здания производственного корпуса при заданной площади должен быть наименьшим так как это сокращает расходы на возведение наружных стен отопление и т. д.
Должна быть обеспечена прямоточность производственного процесса без встречных грузопотоков.
Длина пути транспортирования тяжелых корпусных деталей и агрегатов должна быть минимальной.
Производственные отделения и участки не рекомендуется отделять друг от друга перегородками если это не диктуется условиями технологии требованиями техники безопасности или пожарной безопасности.
В здании производственного корпуса рекомендуется предусматривать несколько взаимно перпендикулярных проездов желательно иметь их сквозными и один или два из них должны быть расположены против въездных или выездных ворот здания.
Рис. 5.4. Схема П-образной планировки предприятия по ремонту полнокомплектных машин:
- разборочно-моечное отделение; 2 - контрольно-сортировочное отделение; 3 - комплектовочное отделение со складом; 4 - склад запасных частей и материалов; 5 - компрессорная; 6 - склад деталей ожидающих ремонта; 7 - сварочно-металлизационное отделение; 8 - кузнечное отделение; 9 - термическое отделение; 10 - гальваническое отделение; 11 - участок разборки на агрегаты; 12 - рамное отделение; 13 - малярное отделение; 14 - участок ремонта кабин; 15 - жестяницкое отделение; 16 - участок ремонта навесного оборудования; 17 - отделение сборки машин; 18 - агрегатное отделение; 19 - слесарно-механическое отделение; 20 - инструментальное отделение; 21 - отдел главного механика; 22 - испытательная станция; 23 - отделение ремонта и сборки двигателей; 24 - отделение топливной аппаратуры и электрооборудования; 25 - медницко-радиаторное отделение; 26 - инструментально-раздаточная кладовая; 27 - деревообрабатывающее и обойное отделения; 28 - участок устранения дефектов; 29 - бытовые помещения.
Рис. 5.5. Схема П-образной планировки предприятия по ремонту двигателей:
- отделение ремонта и сборки двигателей; 2 - разборочно-моечное отделение; 3 - контрольно-сортировочное отделение; 4 - склад деталей ожидающих ремонта; 5 - инструментально-раздаточная кладовая; 6 - склад запасных частей и материалов; 7 - административно-бытовая часть; 8 - инструментальное отделение; 9 - отдел главногомеханика; 10 - слесарно-механическое отделение; 11 - комплектовочное отделение со складом; 12 - кузнечно-термическое отделение; 13 - сварочно- металлизационное отделение; 14 - гальваническое отделение; 15 - компрессорная; 16 - медницкое отделение; 17 - отделение топливной аппаратуры и электрооборудования; 18 - испытательная станция; 19 - малярное отделение.
Размещение в производственном корпусе производственных складских и вспомогательных помещений удобно начинать с определения расположения продольных магистральных проездов. Нормы ширины проходов и проездов следующие: проход для рабочих - 2 м транспортный проезд при одностороннем движении электрокаров и электропогрузчиков грузоподъемностью до 3 т - 3 м то же при двухстороннем движении - 4 м транспортный проезд при двухстороннем движении электрокаров автопогрузчиков и электропогрузчиков грузоподъемностью более 3 т - 5 м.
Расположение в производственном корпусе производственных складских и вспомогательных помещений должно удовлетворять следующим требованиям:
)расположение производственных участков основного производства должно соответствовать технологической последовательности выполнения работ при минимальном грузообороте;
)производственные участки вспомогательного производства следует располагать вблизи обслуживаемых ими участков основного производства;
)склады следует располагать вблизи обслуживаемых ими производственных подразделений;
)изолировать производственные участки и склады от других помещений стенами следует только при необходимости по условиям противопожарных и санитарных требований а также требований сохранности материальных ценностей.
Расчет отделений участков и цехов ремонтного завода на стадии технического проекта изложен в главе 4 данного учебного пособия.
EMC создана для сокращения количества типоразмеров конструкций и строительных деталей и дает основу для типизации и стандартизации в проектировании и строительстве.
Рис.5.6 Производственное помещение:
-Разборочно-моечный участок; 2- Ремонт агрегатов;
- Слесарно – механический участок; 4-Участок ТО и диагностики; 5-Ремонтно монтажный участок;6-Кузнечный участок; 7-Сборочный участок; 8-Сварочный участок; 9-Медницко-жестяницкое отделение; 10-Электроремонтый участок; 11-Инструментальныйй участок; 12-Отделение по ремонту гидрооборудования; 13-Компрессорный участок ;14-Аккумуляторный участок ; 15-Дефектовочный участок; 16-Моторный участок; 17-Топливный участок; 18-Шиномонтажное отделение;
Основными параметрами обеспечивающими типизацию и стандартизацию объемно-планировочными и конструктивными элементов зданий являются:
пролет – расстояние между продольными разбивочными осями зданий
шаг – расстояние между поперечными разбивочными осями здания;
высота – расстояние от уровня чистого пола до низа несущих конструкций
Была выбрана прямоточная планировка так как она занимала меньше всего места. На рис.5.6 представлен план производственного корпуса с обозначенными отделениями и участками.
Отделение предназначено для выполнения работ по ремонту изношенных деталей способом давления изготовления усиливающих накладок для рам гусеничных тележек стрел экскаваторов и других машин. Отделение также выполняет поковки и штамповки как для основного производства так и для нужд инструментального цеха и отдела главного механика (ОГМ).
Годовая производственная программа кузнечного отделения выражается весом ремонтируемых или изготовляемых деталей с разбивкой по видам выполняемых работ. Программа может быть также выражена трудоемкостью в человеко-часах для ремонтируемых деталей и весом в килограммах для изготовляемых деталей. При расчете производственной программы необходимо предварительно составить ведомости изготовляемых и ремонтируемых деталей с указанием их веса а также коэффициентов ремонта и сменности. На основе этих данных а также потребностей в изготовлении поковок для собственных нужд предприятия составляется ведомость годовой загрузки кузнечного отделения по видам работ.
По данным действующих ремонтных предприятий можно ориентировочно принять что годовой объем работ в кузнечном отделении составляет по ремонту деталей 70 90% от общего годового объема работ по изготовлению поковок — 10 30%.
Общий годовой объем по видам работ распределяют (%):
ковка вручную 80 100
Изготовление деталей:
машинная ковка 60 95
ковка под прессом 5 10
В кузнечном отделении производят также ремонт рессор и изготовление новых рессорных листов для ремонтируемых машин.
Трудоемкость выполнения рессорных работ обычно составляет 05 07% от общей трудоемкости ремонта машин и ориентировочно распределяется на следующие виды (%):
разборка и сборка рессор 30
сверлильные работы 3
термические работы 35
подгонка и рихтовка 25
Технологический процесс. Крупные детали поступают в кузнечное отделение непосредственно из разборочно-моечного отделения после их обезжиривания мойки и контрольного осмотра. Все остальные детали поступают как правило из контрольно-сортировочного отделения или со склада ожидающих ремонта деталей. Материал для новых поковок поступает в кузнечное отделение со склада металлов обычно уже в нарезанном виде. Из заготовок изготовляют новые поковки свободной ковкой или штамповкой в подкладных штампах. Нагрев заготовок осуществляют в специальных нагревательных печах или горнах. Детали и поковки после кузнечной обработки поступают в соответствующие отделения для их дальнейшей обработки. Расстановка оборудования в кузнечном отделении производится по групповому признаку т. е. оборудование ручной ковки располагается в одной группе молоты и прессы — в другой.
Пол в кузнечном отделении рекомендуется делать кирпичный (клинкерный). В отделении необходимо предусматривать устройство обще-обменной и местной вентиляции от нагревательных печей кузнечных горнов и ванн для охлаждения. При размещении печей и кузнечных горнов в одноэтажном здании вытяжку от них надлежит предусматривать за счет теплового побуждения. Вытяжка из верхней зоны помещения должна быть не менее трехкратного объема помещения в 1 ч. Подачу воздуха для компенсации вытяжки рекомендуется предусматривать в рабочую зону. Температура помещения должна быть не ниже 14 17° С а относительная влажность воздуха - не более 60%. Примерная планировка кузнечного отделения ремонтного предприятия представлена на рис. 6.1.
Рис. 6.1. Примерная планировка кузнечного отделения:
- стенд для загиба ушков рессор; 2 - стенд для испытания рессор; 3 - стенд
для разборки и сборки рессор; 4 - верстак для рессорщика; 5 - обдирочно-
шлифовальный станок; 6 - вертикально-сверлильный станок; 7 - гибо-
закалочная машина для рессорных листов; 8 - плита правочная на подставке;
- ванна для охлаждения рессорных листов; 10 - щит управления к печи;
- печь для нагрева рессор; 12 - бабка ладильная для правки рессор;
- таль электрическая; 14 - кран поворотный свободностоящий; 15 - печь
для нагрева поковок; 16 - молот приводной пневматический; 17 - вентиля-
тор дутьевой с электродвигателем; 18 - ларь для кузнечного инструмента;
- горн кузнечный; 20 - наковальня на подставке
СОСТАВЛЕНИЕ ПЛАН-ГРАФИКА ТО
1Расчет дня в котором будет проводиться ТО-2 и ТО-1
Месячным планом-графиком устанавливаются дата технического обслуживания или ремонта и продолжительность простоя машины. Порядковый рабочий день месяца (D) в который начинается проведение технического обслуживания или ремонта машин определяется по формуле:
где n – число рабочих дней в планируемом месяце;
LНАЧ - наработка на начало месяца;
LП – планируемая наработка на расчетный месяца.
Если D > n соответствующий вид технического обслуживания или ремонта в этом месяце не проводится.
2Расчет дня в котором будет проводиться ТО-1 и ТО-2 для одноковшовых экскаваторов (на одну единицу техники)
3Расчет дня в котором будет проводиться ТО-1 и ТО-2 для стрелового автомобильного крана (на одну единицу техники)
4Расчет дня в котором будет проводиться ТО-1 и ТО-2 для бульдозера с неповоротным отвалом (на одну единицу техники)
5Расчет дня в котором будет проводиться ТО-1 и ТО-2 для одноковшового фронтального погрузчика (на одну единицу техники)
6Расчет дня в котором будет проводиться ТО-1 и ТО-2 для самоходного катка (на одну единицу техники):
7Расчет дня в котором будет проводиться ТО-1 и ТО-2 для самосвала (на одну единицу техники)
8Расчет дня в котором будет проводиться ТО-1 и ТО-2 для автобусов среднего класса (на одну единицу техники)
9Расчет дня в котором будет проводиться ТО-1 и ТО-2 для легкового автомобиля (на одну единицу техники)
Календарные даты ТО рассчитываемые проведённым выше образом заносятся в соответствующие ячейки план-графика.
На последнем этапе необходимо откорректировать план-график распределяя ТО-1 ТО-2 по рабочим дням в зависимости от пропускной способности постов.
Выполнив курсовую работу я научился определять количество ремонтно – обслуживающих воздействий на машинно – тракторный парк уяснил как правильно нужно определить годовую наработку ремонтного предприятия научился эффективно использовать производственные площади и оборудования выбирать необходимое оборудование и расставить так чтобы облегчить условия труда рабочих.
При проектировании производственного корпуса ремонтного предприятия рассчитал необходимое количество оборудования и ремонтных рабочих для выполнения производственного плана данного парка машин - это позволяет повысить рост производительности труда и улучшения качества ремонта машин и агрегатов.
СПИСОК ИНФОРМАЦИОННЫХ ИСТОЧНИКОВ
Апанасенко В. С. Проектирование авторемонтных предприятий В. С. Апанасенко Н. А. Артеменко. Минск : Высшей. шк. 1988. – 240 с.
Ба6усенко С. М. Проектирование ремонтно-обслуживающих предприятий С. М. Бабусенко. М. : Агропромиздат 1990. – 352 с.
Бабусенко С. М. Ремонт тракторов и автомобилей С. М. Бабусенко. – М. : Агропромиздат 1987. – 351 с.
Мерданов Ш. М. Проектирование предприятий по эксплуатации и ремонту машин Ш. М. Мерданов В. В. Шефер В. В. Конев. - Тюмень: ТюмГНГУ 2009. - 243 с.
Мерданов Ш. М. Организация ремонта строительно-дорожных машин Ш. М. Мерданов Н. Н. Карнаухов В. В. Шефер А. А. Иванов - Тюмень: ТюмГНГУ 2013. - 311 с
Рекомендуемые чертежи
- 25.01.2021
- 25.01.2023
Свободное скачивание на сегодня
Обновление через: 4 часа 55 минут