Приводная станция дискового триера очистки зерна от коротких примесей в складах зерноперерабатывающих и хлебоприемных предприятий





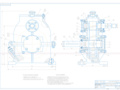
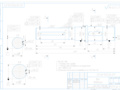
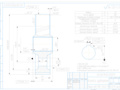
- Добавлен: 25.10.2022
- Размер: 4 MB
- Закачек: 0
Описание
Состав проекта
![]() |
![]() |
![]() ![]() ![]() |
![]() ![]() |
![]() ![]() ![]() |
![]() ![]() |
![]() ![]() |
![]() ![]() ![]() ![]() |
![]() ![]() |
![]() ![]() ![]() |
![]() ![]() |
![]() ![]() ![]() |
![]() ![]() |
![]() |
![]() |
![]() ![]() |
![]() ![]() |
![]() |
![]() ![]() |
![]() ![]() |
![]() ![]() |
![]() ![]() |
![]() |
![]() ![]() ![]() ![]() |
![]() ![]() |
![]() ![]() ![]() ![]() |
![]() ![]() |
![]() ![]() ![]() |
![]() ![]() ![]() ![]() |
![]() ![]() ![]() ![]() |
![]() ![]() ![]() |
![]() |
![]() ![]() |
![]() |
![]() ![]() |
![]() ![]() |
![]() ![]() ![]() ![]() |
![]() ![]() |
![]() ![]() ![]() ![]() |
![]() |
![]() |
![]() |
Дополнительная информация
КУРСОВОЙ.docx
Заданием на курсовой проект предусмотрено спроектировать приводную станцию для дискового триера очистки зерна от коротких примесей в складах зерноперерабатывающих и хлебоприемных предприятий.
Приводная станция включает в себя электродвигатель редуктор цилиндрический и ременную передачу.
Редуктор служит для передачи крутящего момента от электродвигателя к потребителю. Он позволяет получить выигрыш в моменте за счет уменьшения частоты вращения.
В результате на выходе из редуктора мы получаем большой крутящий момент и малую частоту вращения необходимую для привода дискового триера очистки зерна от коротких примесей.
Описание конструкции привода
Дисковый триер для очистки зерна от коротких примесей используют для очистки зерна от коротких примесей (куколя и других семян сорных растений). Триер (рис. 1) состоит из корпуса с дисковым ротором и приемно-распределительного устройства.
Зерно поступает в триер через приемное устройство 7. В корпусе 9 машины на горизонтальном валу 2 установлено 22 кольцеобразных диска 6 образующих ротор. Триер разделен на три последовательно работающих отделения: рабочее перегружающее и контрольное. В рабочем отделении установлено 15 дисков в перегружающем - ковшовое колесо 3 а в контрольном - семь дисков снабженных гонками для транспортирования зерна к накопительному отделению.
Параллельно валу с дисками в нижней части корпуса 9 находится шнек для перемещения примесей отобранных дисками рабочего отделения в контрольное отделение.
Технологический процесс в триере. Зерновая смесь (рис.1) из приемно-распределительного устройства 7 лотковым распределителем тремя равными
потоками подается в рабочее отделение. Короткие примеси и отдельные зерновки поступают в ячейки поднимаются дисками и выпадая из ячеек попадают на верхние лотки 13 и далее в шнек 1. Основная масса зерна захватывается вращающимися дисками и попадает на нижние лотки 72 которыми выводится через сборник из машины.
Смесь зерна с короткими примесями шнеком подается в контрольное отделение (см. рис. 12.2) где происходит окончательное разделение зерна и коротких примесей 77 которые собираются в сборнике и выводятся из машины. Зерно по мере накопления в контрольном отделении через регулируемое отверстие с заслонкой перемещается в перегружающее отделение где подхватывается ковшовым колесом и через сливной лоток снова направляется в рабочее отделение триера для дополнительной очистки.
Уровень зерна в контрольном отделении регулируют положением заслонки 14 что существенно влияет на эффективность работы машины. Удаление мелких минеральных примесей IV осуществляется через люки с крышками. Для отключения триера при подпоре его зерном через отводящие коммуникации на них устанавливают мембранный датчик уровня.
Рис. 1. Дисковый триер очистки зерна:
а - конструкция; б - технологическая схема; 1 - шнек; 2 - вал; 3 - колесо ковшовое; 4 20 - заслонки; 5 16 - перегородки; 6 - диск; 7 - устройство приемное; 8 - окно смотровое; 9 - корпус; 10 - стойка; 11 - крышка откидная; 12 - лотки для зерна; 13 - лоток для коротких примесей; 14 - рукоятка заслонки;
- балки продольные; 77 - электродвигатель; 18 - передача клиноременная; 19 - редуктор; I - зерно; II - зерно очищенное; III - примеси короткие;
IV - примеси минеральные; V – воздух
ВЫБОР ЭЛЕКТРОДВИГАТЕЛЯ И КИНЕМАТИЧЕСКИЙ РАСЧЕТ ПРИВОДА
1 Кинематическая схема привода
Рис.2.1 Кинематическая схема приводной станции дискового триера очистки зерна от коротких примесей в складах зерноперерабатывающих и хлебоприемных предприятий: 1-муфта соединительная; 2-редуктор одноступенчатый вертикальный; 3-поликлиновая ременная передача; 4-электродвигатель; 5- устройство натяжения ремня.
2 КПД приводной станции
где потери на трение и зацепление в передачах и соединительной муфте: в муфте м=098; в зубчатом цилиндрическом зацеплении цп=098; в ременной передаче р=097; в паре подшипников п=097.
Значение потерь на трения в передачах и подшипников качения принято табл.1.1.[1]. В приводной станции число пар подшипников i=2.
=097 · 098 · 098· 0992=091
3 Требуемая мощность электродвигателя при Рт=27кВт(см.задание)
4 Ориентировочные значения передаточных чисел ступеней привода. Из табл. 1.1 [1] принимаем для ременной передачи Uр=2 для зубчатого зацепленияUцп=2 5(устанавливаем Uцп’=5)
5 Передаточное число привода и ориентировочная частота вращения вала электродвигателя при nТ=48 мин-1(см.задание)
6 По таблице табл П.1[1] выбираем электродвигатель трехфазный с короткозамкнутым ротором марки: М112МВ8НУ3 у которого Pэ=кВт nэ=700 мин-1 вал электродвигателя dэ=32 мм.
Рис 2.2. Электродвигатель М112МВ8У3 основные размеры мм:
t30=452; h31=310; d20=260; d1=32; d10=12; b1=8; b10=190; h=112; h1=8; h8=35; h10=12.
7. Уточненное передаточное число привода и окончательная разборка его по ступеням
Устанавливаем Uцп=5 тогда для ременной передачи
8 Мощности на элементах приводной станции
8.1 На первом входном валу редуктора(шестерне)
8.2 Мощность на выходном валу редуктора (на валу цилиндрического колеса)
8.3 Мощность на муфте
Pм=II п = 274099=27 кВт.
9 Частота вращения валов
9.1 Входного вала(цилиндрической шестерни)
9.2 Частота вращения выходного вала редуктора (колеса)муфты соединительной
nII=nкол=nм==48 мин-1 .
10 Моменты кручения на элементах привода
10.1 Момент на ведущем шкиве
10.2 На входном валу (цилиндрической шестерни)
10.3 Момент на выходном валу на зубчатом колесе
10.4 Момент на муфте
Расчет зубчатого зацепления
P2 = 274 кВт; ; Lh = 47·103;
Рисунок 3.1 Зубчатое зацепление цилиндрическими косозубыми колесами
1 Выбор материалов и определение допускаемых контактных напряжений и напряжений изгиба.
1.1 По таблице 4.1 [1] назначаем для шестерни и колеса сталь 40Х улучшенную с твердостью НВ1 = 260 280 и НВ2 = 230 260 (индексы: 1– шестерня 2 – колесо).
По среднему значению(МПа):
НВ1 = 05(260+280) = 270;
НВ2 =05 (230+260) = 245.
1.2 Расчетное число циклов нагружений
1.3 Базовое число циклов
1.4 Коэффициент долговечности при тогда
1.5 Предел контактной выносливости зубьев
1.6 Допускаемые контактные напряжения при коэффициенте запаса прочности (таблица 4.3 [1]).
С учетом рекомендации стр. 105 [1] расчетное допускаемое контактное напряжение для косозубого зубчатого зацепления
что меньше поэтому .
1.7 Для определения допускаемых напряжений изгиба установим (таблица 4.3 [1]) предел выносливости на изгиб и базовое число напряжений при изгибе (стр. 107 [1]) тогда коэффициент долговечности
Коэффициентом учитываем приложение нагрузки и при одностороннем прохождении (колеса вращаются в одну сторону)тогда допускаемые напряжения изгиба:
2 Согласно схеме в рисунке 4.4[1] по таблице 4.10 [1] принимаем коэффициент ширины венца по межосевому расстоянию тогда коэффициент ширины венца по делительному диаметру шестерни
Тогда по рисунку 4.4[1] при значении тогда коэффициент учитывающий распределение нагрузки по длине контактных линий:
3 Межосевое расстояние зубчатого зацепления при значении коэффициента (стр. 116 [1])
4 Ширина венца зубчатого колеса
устанавливаем =62 мм
5 Ширина венца шестерни
6 Нормальный модуль зацепления
Исходя из таблицы 4.13 [1] и ГОСТ 9563-60
7 При предварительно принятом угле наклона зубьев
8 Суммарное число зубьев
9 Число зубьев шестерни и колеса
10 Окончательное значение угла
Потому принимаем Z1=20
11 Диаметры колес (см. рисунок 2.1) без смещения (x1=0 и x2=0)
- межосевое расстояние
- диаметры вершин зубьев
- диаметр впадин зубьев
12 Окружная скорость в зацеплении
В соответствии с таблицей 4.6 [1] принимаем 8-ю степень точности изготовления зубчатых колес а т.к это 35мс то подшипниковые пространства отделяем от внутренней части редуктора маслоудерживающими кольцами.
13 Силы действующие в зацеплении
Рисунок 3.3 – Схема нагружения валов силами зубчатого зацепления.
14 Проверочный расчет на выносливость по контактным напряжениям
где – коэффициент учитывающий форму сопряженных поверхностей;
для стальных колес коэффициент учитывающий механические свойства материалов;
– коэффициент учитывающий суммарную длину контактных линий для косозубых передач здесь:
– коэффициент торцевого перекрытия для передач без смещения:
– удельная расчетная окружная сила
где - коэффициент учитывающий распределение нагрузки между зубьями (07 таблица 4.5 [1]);
- коэффициент учитывающий распределение нагрузки по длине контактных линий при НВ 350 и значение коэффициента венца колеса по делительному диаметру шестерни
= 104 (рисунок 4.4 кривая 6 [1]);
– коэффициент учитывающий динамическую нагрузку (таблица 4.8 [1]);
Поэтому уменьшаем bк до 50мм шестерню bш=52мм.
Для этого при % недогрузки =45
х= Н= 455213=1005213-100х
устанавливаем х= Н=500 Мпа
Тогда 5002=188225720792где x*=ht
отсюда х*= ht=943Нмм а т.к. ht=КНαКНКНVто
15 Проверочный расчет по изгибным напряжениям
где – коэффициент формы зуба по рисунку 4.7 [1] в зависимости от приведенного числа зубьев так при:
– коэффициент учитывающий перекрытие зубьев и при значении коэффициента осевого перекрытия
– коэффициент учитывающий наклон зубьев
Что соответствует рекомендации на странице 123 [1]
– коэффициент нагрузки и аналогично как и при нахождении составляющих получается:
(рисунок 4.4 кривая 6[1]);
для шестерни 5213353 = 14767 МПа
для колеса 5233357 = 14658 МПа.
И проверку просчитываем по изгибу для колеса как менее прочному по соотношению
Вывод: подобранный материал (сталь 40Х) и полученные размеры зубчатого цилиндрического косозубого зацепления удовлетворяют работоспособности передачи так как
Расчет ременной передачи
Рис.4.1 Расчетная схема и схема фрагмента сечения ремня
d1- ведущий шкив; d2 – ведомый шкив; Up= 292; Рэ’= 297 кВт.; nэ= 700 мин-1.
1 Момент на ведущем шкиве
2 Тип ремня (сечение)
Табл. 7.3[2] (ТУ 38-105763-84)
Выбираем тип ремня «Л» с ТЭ’=4051 Н·м
3 Диаметр ведущего шкива
Из стандартных значений диаметра (см. стр.177[2]) d1=106 мм
5 Диаметр ведомого шкива при значении коэффициента упругого скольжения E=0010
d2=d1· Uр· (1-E)=106 · 292(1-0010)= 30642мм
Из нормативных значений диаметра (см. стр. 177[2]) d2=300 мм
6 Уточненное передаточное число
7 Отклонение от заданного
что допустимо т.к. % =5%
8 Межосевое расстояние
5· ( d1+ d2) + h≤ a ≤ 2·( d1+ d2)
5· (106+300) + 485 a 2·(106 + 300)
Устанавливаем а=700 мм
По стандартному ряду из ГОСТа 1284.1-89: L=2000 мм
10 Проверка ремня на долговечность по числу пробегов в секунду
Условие соблюдается []
11 Уточненное межосевое расстояние
ау =01252L-+ )+ =674.32 мм
Устанавливаем ау = 675 мм.
12 Угол обхвата ведущего шкива
Условия по углу обхвата ведущего шкива соблюдается:
= 1-0003(180°- α1) = 1-0003(180°-163.6°) =051
Ср при умеренных колебаниях и односменной работе (см. п. 7.5)
СL из табл. 7.14 по LLP=20001600 =1.25
LP= 1600- базовая длина ремня « Л» табл. 7.13
14 Допускаемая приведенная мощностью [P]0передаваемая 10-ю ребрами поликлинового ремня
15 Поправка учитывающая влияние уменьшения изгиба на ведомом (большом) шкиве
ΔТ1=43 Н·м (табл. 7.15)
ΔP=0.0001·54·700 = 0378 кВт
16 Допустимая мощность передаваемая в условиях эксплуатации 10-ю ребрами поликлиновыми
[P] = ([P]0··CL+ ΔP)·CP = (4.23·051·1.04+0378)·09 =2.35 кВт
17 Число ребер поликлинового ремня
18 Сила предварительного натяжения поликлинового ремня с Z =13 и
19 Сила действующая на валы
20 Ширина ремня при шаге между ребрами (р =48 для ремня «Л»)
b = p· Z =48·13=62.4 мм
21 Размеры обода шкивов (рис.7.16г и д) ширина (e и f по табл. 7.20а и 7.21)
B= (Z-1)e+2f= (10-1)·485+2·55 =54.65мм
внешний диаметр (b* и Δ по табл.7.20а и 7.21)
de1 = d1(dp1) -2Δ =106-2·2.4 =101.2 мм
de2 = d2(dp2)- 2Δ=300-2·2.4 =2952 мм
внутренний диаметр (h по табл. 7.20а и 7.21)
df1 = de1- 2·h=101.2-2·4.8=91.6 мм
df2 = de2- 2·h=2952-2·4.8=2856 мм
толщина обода стальных шкивов
= 128· h=1.28·4.8 = 6.14 мм
С=(12 13) = (12 13)· 614 =73 8
Ориентировочный расчет валов
1 Ведущий (входной) вал
Диаметр входного конца вала определяется по крутящему моменту и в нашем случае соединения его со шкивом:
Устанавливаем а остальные устанавливаем конструктивно (см. рис. 5.1). Подшипники предварительно используем шариковые радиальные однорядные (ГОСТ 8338-75) средней серии (табл. 11.6 [2])
Рисунок 5.1 – Предварительная конструкция ведущего вала:
– вал ведущий(входной); 2 – подшипники 36206№ (4 шт.); 3 – шестерня зубчатого зацепления; 4- шпонка (2 шт.); 5- втулка распорная.
Определение способа изготовления шестерни с валом (см. рис. 5.2)
Рис 5.2 определение .
что следовательно шестерня изготовлена совместно с валом (вал-шестерня).
Рис 5.3 Уточненная конструкция ведущего вала
2 Ведомый вал (диаметр вала под соединительной муфтой)
Диаметр вала под соединительной муфтой при Мпа и (п. 2.10.3 ПЗ)
устанавливаем а остальные диаметральные размеры конструктивно (см. рис. 5.3).
Рисунок 5.4 Ведомый вал: 1 –вал выходной( ведомый); 2 –шпонка (2 шт.); 3 –подшипники №36311 (4 шт) 4 –втулка распорная 5 – шестерня зубчатого зацепления.
Выбор и расчет соединительных муфт
На выходном валу редуктора находится муфта для соединения вала редуктора с дисковым триером очистки зерна. Принимаем для соединения вала редуктора и валом триера упругую втулочно-пальцевую муфту МВУП ГОСТ 21424-75.
Рис. 6.1. Основные данные муфты соединительной по ГОСТ 21424-93
где К—коэффициент режима работы К=15 20 принимаем =15 по стр.383. таб.17.1" Расчеты деталей машин"И.М. Чернин.
Тр=1553718=80577 Нм;
По табл. 17.8 стр. 388 принимаем муфту с наружным диаметром D=190 мм и допускаемым расчётным моментом Т=1000 Нм.
Характеристика муфты:
диаметр полумуфты d=50 мм;
расчётный момент Тр=53718 Н м;
наружный диаметр D=190 мм;
диаметр расположения пальцев D0=140 мм
диаметр пальца dn=18 мм
длина пальца ln=42 мм
число пальцев z=8 мм
диаметр втулки dв=35мм
длина втулки lв=36 мм
Проверяем пальцы на изгиб:
где и—наибольшее напряжение при изгибе в опасном сечении пальца МПа;
[и]—допускаемое напряжение при изгибе пальцев МПа [и]=80 90 МПа стр.372 1.
Условие прочности пальцев на изгиб выполняется.
Проверяем условие прочности втулки на смятие:
где [см]—допускаемое напряжение на смятие для резины МПа [см]=18 2 МПа стр. 372 1.
Назначение размеров основания корпуса крышки редуктора
Рис. 7.1. К определению основных размеров крышки редуктора.
1 Толщина стенок основания и крышки по
- основания разъема с крышкой
- крышки с основанием
- соединяющих основание с крышкой по периметру
- крепящие смотровую крышку
- верхний фланец основания и крышки у подшипников:
устанавливаем 32 мм;
- фундаментное основание:
Рисунок 7.2. Компоновочная схема редуктора
Схема нагружения опор валов силами в зацеплениях и расстояния между силами и серединами опор
Основываясь на предыдущих расчетах зубчатых зацеплений валов и полученных в главе 7 размеров корпуса и зазорами между зацеплениями и используя чертеж редуктора с расставленными размерами рассчитываем расстояния между опорами и местами приложения сил.
Исходя из схемы задания вычерчиваем зубчатые зацепления схематически и расставляем усилия в зацеплениях.
Рисунок 8.1 – Усилия в зубчатых зацеплениях
=4242 Н; =16265 Н; =1401 Н; Fр=283527 Н; =52.67 мм; =46.42 мм;
Рис.9.1 Схема нагружения и эпюры моментов ведущего вала
Горизонтальная плоскость:
- Реакция опор от воздействия силы и эпюра т.к. a=a’=58 мм то
-А 5810-3=-21215810-3= 123 Н м
Вертикальная плоскость от воздействия сил и
-3110.69+16265+4319.71-2835.27=0
Под шестерней слева:
Под опорой “B” справа:
Скачек 180.42-143.56=368 обуславливается 368 Н м.
Эпюра Т1 распространяется от шкива до шестерни.
На основании рисунка можно сделать вывод что существует два места с наибольшим нагружением вала под шестерней и опорой «В» вала
эквивалентный момент под шестерней
Диаметр вала под шестерней при =50 МПа
что мм следовательно прочность вала в этом сечении по обеспечивает его размерами.
Суммарные реакции в опорах
2 Ведомый (выходной) вал
=263.33 мм; =257.08 мм; =4242 Н; =1626.5 Н; ;
Рис 9.2 Схема нагружения и эпюры моментов ведомого вала
-102112+391619-4242+134723=0
Под опорой «К» слева -
Под шестерней справа: Нм.
Вертикальная плоскость
-67435-16265+23008=0
Под шестерней слева: Нм.
Под шестерней справа:L’
Скачек 14264+418=18444 обуславливается
Анализ эпюр и указывает на наиболее нагруженное сечение под колесом.
Суммарный момент изгиба
Эквивалентный момент
что мм установленного при ориентировочном расчете вала(см. рис. 5.3). Следовательно размеры вала обеспечивают его прочность.
Расчет и выбор подшипников
Исходные данные: dn=30 мм; n1=23973 мин-1; Lh=4700 час; RA=376497 H; RB=481233 Н; Fa=1401 Н.
Поэтому вал устанавливаем в шариковых радиально-упорных однорядных подшипниках по ГОСТ 831-75. Предварительно по dn=30 мм №36206у которого Сr=220 кН; С0=120; α=12.
По = параметры е= 041; Х=045; Y= 134.
Рисунок 10.1- Расчетная схема ведущего вала
Осевые составляющие подшипников
SA=e RA=041376497=154363 Н
SB= eRB=0.41481233=197305 Н
Поэтому осевые нагружения на опоры равны:
FaA=SB+Fa=197305+1401=337405 H;
По соотношению определим коэффициенты радиальной Х и осевой Y нагрузки:
X=0.45; Y=1.34(c. 330 [1])
Динамические нагрузки подшипников:
PэА=(XVRA+YFaA)KбКt=
=(0.451376497+1.34337405)1.31=8080 Н808 кН;
РэB=(XVRB+YFaB)KбКt=
=(11481233+0197305)1.31=625603Н 625 кН
V=1 т.к. вращается внутреннее кольцо;
Для более нагруженной опоры «А» динамическая расчетная грузоподъемность:
>Cr=22.0 кН следовательно выбираем подшипник № 66406у которого Сr=438 кН что > =3291 кН.
Рис. 10.2 Установка подшипника №66406 на вал и в отверстие корпуса
S=0.15(D-d)=0.15(90-30)=9 мм
Исходные данные: dn=55 мм; n2=48 мин-1; Lh=4700 час; RK=; RL=Н; Fa=1401 Н.
Поэтому вал устанавливаем в шариковых радиально-упорных однорядных подшипниках по ГОСТ 831-75. Предварительно по dn=55 мм №36211у которого Сr=584 кН; С0=3420; α=12.
По = параметры е= 035; Х=045; Y= 154.
Рисунок 10.3- Расчетная схема ведомого вала
SK=e RK=035=139081 Н
SL= eRL=0.35=93317 Н
SK>Sl SK направлена как поэтому осевые нагружения на опоры равны:
FaL= SК+=139081+1401=279181 H.
По соотношению определим коэффициенты радиальной Х и осевой Y нагрузки
X=1; Y=0(c. 330 [1])
X=0.45; Y=1.54(c.330 [1])
PэK=(XVRK+YFaK)KбКt=
=(11+02334.17)1.51=5960.64 H6 кН;
РэL=(XVRL+YFaL)KбКt=
=(0.4512666.21+1.542791.81)1.51=8248.77 H8.25 кН
Для более нагруженной опоры «L» динамическая расчетная грузоподъемность:
Cr=58.4 кН следовательно выбранный подшипник подходит.
Рис. 10.4 Установка подшипника №36211 на вал и в отверстие корпуса
S=0.15(D-d)=0.15(100-55)=6.75 мм
S’=0.5S=0.56.75=3.38 мм
Шпонки призматические
По диаметру вала d из рекомендаций ГОСТа 23360-78 назначаем размеры шпонки (ширина и высота) глубины пазов в валу и ступице Длина шпонки l назначается на 5 10 мм короче и согласовывается со стандартным размером или расчетом.
Рис.11.1. Шпоночное соединение
В курсовом проекте исходя из работы шпоночного соединения на смятие ([] = 80 100 МПа) для валов редуктора длину шпонки определим через рабочую ее длину т.е.
Шпонка под ведомым шкивом на d = 28 мм
Шпонка под колесом на d=58 мм
Шпонка под муфтой на d=50 мм
Расчет размеров зубчатого колеса
Рис. 12.1 Размеры зубчатых колес.
1. Основные размеры колес сведены в таблицу 11.1
Таблица 12.1 Основные параметры зубчатых колес
Диаметр вала dв; модуль m; длина шпонки
Толщина обода 1=25m+2≥8
Длина ступицы lст=(12 18)dв lст≥b
Диаметр ступицы dст=16dв
Толщина диска с=(02 03)b
Диаметр обода Do=df - 20
Диаметр отверстий dотв=(15 52) мм
Диаметр оси отверстий Dотв=05(Do+dст)
Выбор швеллера и проектирование сварной рамы
1. Крепление редуктора
Болты для крепления редуктора должны размещаться под полкой выбранного проката.
В нашем случае для фундаментного болта редуктора М18 размер полки швеллера:
Тогда согласно ГОСТ 8240-97 выбираем швеллер №12 размеры которого приведены на рисунке 14.1.
Рис.14.1. Швеллер и шайба косая для рамы.
2. Монтаж электродвигателя
Соединение электродвигателя с редуктором осуществляется через соединительную муфту или ременную передачу. В нашем случае вращение от электродвигателя к редуктору передается посредством плоскоременной передачи. Так как ремень в процессе эксплуатации удлиняется то в установке предусматриваем салазки для компенсации этого удлинения. Салазки снабжаются пазами под болты крепления электродвигателя. От размеров этих болтов зависит форма и размеры салазок. Так как в электродвигателе М160М8У3 отверстие под болт для крепления к раме то подбираем салазки типа С-3 (см.рис.14.2.)
Рис. 14.2. Размеры салазки С-3.
3. Конструирование сварной рамы
Рама и ее размеры зависят от компоновки монтируемых механизмов и определяется по общему виду задания. Исходя из установочных и присоединительных размеров редуктора электродвигателя и межосевого расстояния ременной передачи устанавливаем размеры рамы в плане.
Рис. 14.3. Рама установки в плане.
Смазка зацеплений и подшипников
1 Средняя скорость в зацеплении
2 Кинематическая вязкость масла для смазки зубчатого зацепления по при t 100 °C 85 мм2с из таблицы ГОСТ 20799-75 назначаем смазочный материал – масло индустриальное И – 100 А.
3 Объем смазочного материала
где соответственно длина и ширина внутренней полости редуктора (замеряем на компоновочной схеме) - высота уровня смазки.
т.е. 109 мм обеспечивает .
Рисунок 13.1 – Схема для расчета уровня смазки
При картерном смазывании передач подшипники могут смазываться брызгами масла если окружная скорость колеса погруженного в масло больше 35 мс. А так как в рассматриваемом редукторе V = 0.66 мс то подшипники смазываются пластичным смазочным материалом (Литол) закладываемым в подшипниковое пространство.
При работе передач продукты изнашивания постепенно загрязняют масло. С течением времени оно стареет свойства его ухудшаются. Поэтому масло залитое в корпус редуктора периодически меняют. Для замены масла в корпусе предусматривают сливное отверстие закрываемое пробкой с конической резьбой.
Для наблюдения за уровнем масла в корпусе устанавливаем контрольную пробку с конической резьбой.
При длительной работе в связи с нагревом воздуха повышается давление внутри корпуса. Это приводит к просачиванию масла через уплотнения и стыки. Чтобы избежать этого внутреннюю полость корпуса сообщают с внешней средой путем установки отдушины в его верхней части.
Уточненный расчет вала
Анализ размеров редуктора на листе графической части показал что расстояния от подшипников до мест приложения сил изменились (см. рис. 15.1) в сторону увеличения больше чем на 5 %. Поэтому прежде чем выполнять уточненный расчет вала осуществим перерасчет этого вала.
1 Ведомый (выходной) вал:
Рис 15.1 Схема нагружения и эпюры моментов ведомого вала
-102112+424431-4242+10188=0
Под шестерней справа: Н м.
-68746-16265+231396 = 0
Под шестерней справа: K’
Скачек 14577+4193=1877 обуславливается
что мм установленного при ориентировочном расчете вала(см. рис. 5.4). Следовательно размеры вала обеспечивают его прочность.
2.1 Назначаем на изготовление вала материал – сталь 40Х у которого (из табл. 9.8 [2]): .
В сечении вала под опорой “K” действует изгибающий момент и крутящий момент (см. П. 9 ПЗ). Концентрация напряжения вызывается напрессовкой подшипника на вал и галтелью для выхода шлифовального круга на месте перехода вала диаметром 55 мм в диаметр 60 мм (рис. 15.2).
Рис. 15.2 Канавка для выхода шлифовального круга
2.2 Эффективные коэффициенты концентрации напряжений:
для сечения вала ослабленного галтелью(при ):
2.3 Коэффициенты качества обработки и упрочнения (см. стр. 17[2]):
под подшипником: (шлифование); (без термической обработки);
галтели: (чистое обтачивание); (без термической обработки).
2.4 Постоянные и переменные составляющие циклов изменения напряжений при симметричном цикле изменения напряжений изгиба и пульсирующем (отнулевом) цикле изменения напряжений кручения
(вал работает в нереверсивном режиме) принимая из-за малого расстояния от точки K до галтели (см. рис. 15.2) значения суммарного момента изгиба равный :
средние и переменные составляющие цикла (т.к. диаметры обоих сечений вала отличаются друг от друга незначительно):
2.5 Приведенные эффективные коэффициенты концентраций напряжений:
2.6 Коэффициенты запаса усталостной прочности вала в сечениях по изгибу и кручению:
2.7 Общий коэффициент запаса прочности вала:
Вывод: запас усталостной прочности получился очень высоким ([S]=18 25) он продиктован материалом вала-шестерни и диаметрами вала назначенными по а не по показателям прочности .
Выбор посадок сопряжённых деталей
Для установки элементов передач и редуктора назначаем следующие посадки:
- установка полумуфты на ведущий вал - ;
- установка подшипников: на вал – ; в корпус –
- установка зубчатого колеса и шестерни на вал - ;
- установка шкива ведомого на вал - ;
- установка колец на выходной вал - ;
- установка шпонок - на вал -;в ступицу зубчатых колёс шкива ведомого и муфты - ;
- установка глухих крышек подшипников:
Сборка регулировка и разборка редуктора
Перед сборкой внутреннюю полость корпуса редуктора тщательно очищают и покрывают маслостойкой краской.
Сборку производят в соответствии со сборочным чертежом начиная с узлов валов.
В шпоночный паз тихоходного вала (под муфту) закладывают шпонки затем устанавливают дистанционные мазеудерживающие втулки и предварительно разогретые в масле шарикоподшипники.
В шпоночные пазы тихоходного вала закладывают шпонки и напрессовывают колесо тихоходной передачи затем устанавливают дистанционные мазеудерживающие втулки и предварительно разогретые в масле шарикоподшипники.
На валы со стороны выходных концов на участки где установлены подшипники надевают компенсационные кольца в сквозные крышки подшипниковых узлов предварительно заложенны манжеты.
В отверстия подшипниковых узлов в основании корпуса редуктора устанавливают компенсационные кольца и глухие закладные крышки подшипниковых узлов. Под крышки прокладки из картона.
Затем собранные валы укладывают в основание корпуса редуктора и надевают крышку корпуса покрывая предварительно поверхности стыка спиртовым лаком. Для центровки крышку устанавливают на корпус с помощью двух цилиндрических штифтов. После этого затягивают болты крепящие крышку к корпусу.
Затем ввинчивают пробку маслосливного отверстия устанавливают маслоуказатель и заливают масло. Закрывают смотровой люк крышкой-отдушиной которую крепят болтами.
На этом сборка окончена.
Разборка редуктора осуществляется в обратном порядке. Цилиндрические передачи не нуждаются в регулировке. Взаимное положение колес определяется конструкцией редуктора. Шариковые радиальные подшипники также не регулируются.
В результате выполнения задания по курсовому проектированию была разработана типовая конструкция одноступенчатого горизонтального цилиндрического редуктора общего назначения. Данный редуктор предназначен для длительной работы.
Выполнение задания разделено на 2 этапа. Первым этапом задания является пояснительная записка. Вторым –графическая часть.
Пояснительная записка состоит из необходимых расчетов отдельных деталей и узлов редуктора и содержит пояснения этих этапов расчета.
Графическая часть включает в себя три чертежа: один рабочий и два сборочных. Рабочий чертеж выполнен на ведомый вал редуктора. Сборочные чертежи выполнены на полнокомплектный редуктор приводную станцию и сопровождаются соответствующей спецификацией.
Пояснительная записка и чертежи выполнены в соответствии со всеми требованиями предъявляемыми к нормативной документации на производстве.
В процессе проектирования редуктора были усвоены и закреплены знания по следующим предметам: теоретическая механика; сопротивление материалов детали машин; инженерная графика; нормирование точности и технические измерения; стандартизация и качество продукции.
Спроектированный редуктор может применяться для привода различных типов рабочих машин и соответствует всем нормам предъявляемым к данному типу редукторов.
СПИСОК ИСПОЛЬЗОВАННОЙ ЛИТЕРАТУРЫ
Детали машин и основы конструирования. Часть 1 В.А. Агейчик. Минск. БГАТУ. 2009 год.
Детали машин. Теория и расчет. А.Т Скойбеда. Минск.
Расчеты деталей машин. Справочное пособие. Минск.
Вышэйшая школа.1986 год.
Требования и рекомендации по выполнению чертежей. Детали машин. Пособие. Минск. БГАТУ.2014 год.
Реферат.docx
Перечень ключевых слов: сборная единица приводная станция редуктор передача вал двигатель колесо ремень модуль диаметр шпонка подшипник соединение посадка шероховатость точность.
-описание технического задания на проектирование;
-кинематический и энергетический расчет приводной станции;
-расчет механических передач валов зубчатых колес шкивов элементов
- выбор подшипников качения смазочного материала посадок сборка и разборка редуктора.
Ведомость проекта.dwg

дисковому триеру очистки знрна от коротких примесей
Титульный лист.docx
ПРОДОВОЛЬСТВИЯ РЕСПУБЛИКИ БЕЛАРУСЬ
УЧРЕЖДЕНИЕ ОБРАЗОВАНИЯ «БЕЛОРУССКИЙ ГОСУДАРСТВЕННЫЙ АГРАРНЫЙ ТЕХНИЧЕСКИЙ УНИВЕРСИТЕТ»
ФАКУЛЬТЕТ ТЕХНИЧЕСКОГО СЕРВЕСА АПК
материалов и деталей машин»
по дисциплине «Прикладная механика»
на тему: « Приводная станция дискового триера очистки зерна от коротких примесей в складах зерноперерабатывающих и хлебоприемных предприятий »
Пояснительная записка
Руководитель: Кононович И.Н.
Содердание.docx
Выбор электродвигателя и кинематический расчет привода ..9
Расчет зубчатого зацепления ..12
Расчет ременной передачи 19
Ориентировочный расчет валов 24
Выбор и расчет соединительной муфты 26
Назначение размеров основания корпуса крышки редуктора .28
Схема нагружения опор валов силами в зацеплениях 31
Расчет и выбор подшипников для валов ..37
Шпонки призматические..41
Расчет размеров зубчатого колеса 43
Выбор швеллера и проектирование сварной рамы 44
Смазка зацеплений и подшипников46
Уточненный расчет вала .48
Выбор посадок сопряженных деталей ..52
Сборка регулировка и разборка редуктора 53
Список использованной литературы .55
вал ведомый.dwg

** Размер обеспечивается инструментом
Остальные технические требования по СТБ 1014-95.
Сталь 45 ГОСТ 1050-88
РЕДУКТОР.dwg

Передаточное число редуктора U=5;
Крутящий момент на шестерне Т
Частото вращения быстроходного вала n
Технические требования
Редуктор заполнить маслом индустриальным И-100 А
а в подшипниковые пространства - Литол
Привод допускается эксплуатировать с отклонением
от горизонтального положения на угол до 3
должен быть обеспечен уровень масла достаточный для
смазки зацепления подшипниковых узлов
После сборки редуктор подвегнуть обкатке в течении 2-ух часов;
Температура масла после обкатки не должна превышать 80
Редуктор одноступенчатый
косозубый цилиндрический
спецификация приводной станции.doc
Ремень поликлиноременный
Гайка прорезная ГОСТ 2528-73
колесо зубчатое.dwg

Остальные технические требования по СТБ 1014-95.
Нормальный исходный контур
Коэффициент смещения
Степень точности по ГОСТ 1643-81
Диаметр вершин зубьев
Диаметр впадин зубьев
Сталь 40Х ГОСТ 4543-71
редуктор вертикальный.dwg

Передаточное число редуктора U=5;
Крутящий момент на шестерне Т
Частото вращения быстроходного вала n
Технические требования
Редуктор заполнить маслом индустриальным И-100 А
а в подшипниковые пространства - Литол
Привод допускается эксплуатировать с отклонением
от горизонтального положения на угол до 3
должен быть обеспечен уровень масла достаточный для
смазки зацепления подшипниковых узлов
После сборки редуктор подвегнуть обкатке в течении 2-ух часов;
Температура масла после обкатки не должна превышать 80
Редуктор одноступенчатый
косозубый цилиндрический
Спецификация редуктора.doc
Мазеудерживающее кольцо
Манжета ГОСТ 8752-79
Подшипник ГОСТ 27365-87
Шпонка ГОСТ 23360-78
приводная станция.dwg

1.Перекос валов двигателя и редуктора не более 1
2.Радивльное смещение валов двигателя и редуктора не более 2мм.
3.Натяжение клиноременной передачи должно быть равномерным
перекосы не допускаются.
4.Перед началом работы заполнить подшипниковые пространства
и редуктор смазочными материалами: масло индустриальное И-100А
ГОСТ 20799-75 и масло трансформаторное ТАп-15В ГОСТ 23652-79.
Техническая характеристика:
1 Мощность электродвигателя Р=3 кВт.
2 Частота вращения вала электродвигателя 700 мин
3 Общее передаточное число U=14
4 Крутящий момент на выходном валу Твых=545
крышка подшипника.dwg

Остальные технические требования по СТБ 1014-95.