Одноступенчатый цилиндрический зубчатый редуктор




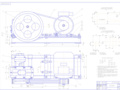
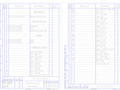
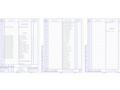
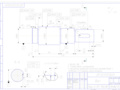
- Добавлен: 25.10.2022
- Размер: 1 MB
- Закачек: 1
Описание
Состав проекта
![]() |
![]() |
![]() ![]() ![]() ![]() |
![]() ![]() ![]() ![]() |
![]() ![]() ![]() ![]() |
![]() ![]() ![]() ![]() |
![]() |
![]() ![]() ![]() ![]() |
![]() |
![]() ![]() ![]() ![]() |
![]() ![]() ![]() ![]() |
![]() ![]() ![]() |
![]() ![]() ![]() |
![]() |
![]() ![]() |
![]() |
![]() |
![]() |
![]() ![]() |
![]() ![]() |
![]() ![]() |
![]() ![]() |
![]() ![]() |
![]() ![]() |
![]() |
![]() |
![]() ![]() |
![]() |
Дополнительная информация
Спецификация к редуктору.dwg

Привод2.dwg

крепления рамы к фундаменту
крепления элементов привода к раме
Техническая характеристика
Непараллельность осей шкивов не более 0
длине 100 мм. Смещение рабочих поверхностей
Привод обкатать без нагрузки в течение не менее
часа. Стук и резкий шум не допускаются
После обкатки масло из редуктора слить и залить
масло индустриальное И-40А ГОСТ 20799-75 коли-
Ограждения условно не показаны. Ограждения ремён-
ной передачи и муфты установить и окрасить в
Вал.dwg

Размер обепеч. инструментом
Неуказанные предельные отклонения размеров: валов -t
t2 среднего класса точности
Редуктор2.dwg

Объём масляной ванны- 3
Подшипники установлены "в распор" ( вал между подшипниками сжат ).
Крышки подшипников выполнены врезными.
Поверхности соединения "корпус-крышка
перед сборкой покрыть уплотнительной
пастой типа Герметик.
После сборки валы редуктора должны про-
ворачиваться свободно
Редуктор обкатать по 10-15 мин на всех
Спецификация к приводу.dwg

Гайка М14 ГОСТ 5915-70
Гайка М16 ГОСТ 5915-70
Муфта 2-1000-42-1-40-1
Колесо зубчатое.dwg

Коэффициент смещения
Радиусы скруглений 1
Неуказанные пред. откл. размеров: отверстий +t
Крышка.dwg

Неуказанные предельные отклонения размеров:
Пояснительная записка по Деталям.doc
Федеральное государственное образовательное
учреждение высшего профессионального образования
«СИБИРИСКИЙ ФЕДЕРАЛЬНЫЙ УНИВЕРСИТЕТ»
Кафедра «Проектирование и экспериментальная механика машин»
ПРИВОД ЛЕНТОЧНОГО ТРАНСПОРТЁРА
Пояснительная записка
Техническое задание
Спроектировать привод ленточного транспортёра состоящего из электродвигателя серии АИР ремённой передачи и одноступенчатого цилиндрического зубчатого редуктора.
Рисунок 1 – Кинематическая схема привода
Таблица 1 – Исходные данные
Срок службы тыс. час
Рисунок 2 – Циклограмма нагружения
Целью данного курсового проекта является освоение навыков расчёта и конструирования основных видов механизмов предназначенных для передачи и преобразования крутящего момента.
В данной работе приведён пример проектирования привода ленточного транспортёра. В него входят подбор электродвигателя проектирование и расчёт цилиндрического одноступенчатого редуктора а так же проектирование самого привода в сборе.
Кинематический расчёт привода
1Подбор электродвигателя
где - требуемая мощность электродвигателя кВт
- выходная мощность кВт;
- коэффициент полезного действия привода.
где - коэффициент полезного действия цилиндрической передачи
- коэффициент полезного действия ремённой передачи.
Зная мощность подбираем двигатель серии АИР. При = 4 кВт двигатель серии 112МВ950 c асинхронной частотой вращения 1000 .
где - угловая скорость двигателя
- частота вращения обмин.
Таблица 2 – Кинематические параметры редуктора
Выбираем стандартное значение передаточного числа редуктора = 5
Корректировка передаточных чисел.
2 Определение частот вращения и вращающихся моментов на валах
Определим мощность частоту вращения n угловую скорость вала и крутящий момент T.
где P – мощность кВт;
- коэффициент полезного действия.
где n – частота вращения обмин;
U – передаточное число.
где - угловая скорость
U – передаточное число.
где Т – крутящий момент м
Расчёт цилиндрической передачи
1 Выбор материала. определение допускаемых контактных напряжений и напряжений изгиба.
Для цилиндрических и конических передач существуют группы материалов: сталь 45 40Х 40ХМ 20 20Х 20ХМ легированные.
Я выбираю сталь 40Х.
2.Определение допускаемых контактных напряжений и напряжений изгиба.
Шестерню подвергаем закалкой ТВЧ твёрдость HRC 45 50
Колесо подвергается улучшению твёрдость HB 269 302.
где - допускаемое контактное напряжение колеса мПа;
где - допускаемое контактное напряжение шестерни мПа;
где - допускаемое напряжение изгиба для колеса мПа;
3.1. Межосевое расстояние
где - предварительное значение межосевого расстояния мм;
- коэффициент зависящий от поверхности твёрдости зуба;
U – передаточное число редуктора;
- момент на валу шестерни ;
знак «+» (в скобках) относят к внешнему зацеплению знак «-» - к внутреннему.
- частота вращения обмин.
Уточняют предварительно найденное значение межосевого расстояния.
где - коэффициент учитывающий направление зуба для прямозубых =450 для косозубых =410;
- коэффициент ширины принимают из ряда стандартных чисел в зависимости от положения колёс относительно опор:
при симметричном расположении =0.4;
- коэффициент нагрузки в расчётах на контактную прочность;
где - коэффициент учитывающий динамику работы передачи принимается по таблице в зависимости от степени точности передачи по нормам плавности окружной скорости и твёрдости рабочих поверхностей . =1.17
- коэффициент неравномерности распределения нагрузки по длине контактных линий после приработки;
где - коэффициент неравномерности распределения нагрузки по длине контактных линий до приработки принимают в зависимости от схемы передачи твёрдости зубьев и коэффициента . По таблице = 1.06.
- коэффициент учитывающий распределение нагрузки между зубьями;
для прямозубых передач
где - степень точности. По таблице в зависимости от окружной скорости и направления зуба определяем степень точности по ГОСТ 1643-81.
- коэффициент учитывающий приработку зубьев его значения находят в зависимости от окружной скорости для зубчатого колеса с меньшей твёрдостью. =0.78.
Уточняю предварительно найденное значение межосевого расстояния:
3.2. Предварительные основные размеры колеса
3.3. Модуль передачи мм
где для прямозубых передач – ;
- коэффициент нагрузки при расчёте по напряжениям изгиба
- учитывает внутреннюю динамику нагружения и выбирается в зависимости от степени точности по нормам плавности окружной скорости и твёрдости рабочих поверхностей. Выбираю =1.21;
- коэффициент учитывающий неравномерность распределения напряжений у основания зубьев по ширине зубчатого венца
- коэффициент учитывающий влияние погрешностей изготовления шестерни и колеса на распределение нагрузки между зубьями = = 1.18;
Из диапазона модулей выбираю меньшее согласуя со стандартным
3.4. Суммарное число зубьев и угол наклона
Так как колёса прямозубые то угол следовательно
где - суммарное число зубьев;
- межосевое расстояние мм
- угол наклона зуба;
3.5. Число зубьев шестерни и колеса
округляем в большую сторону получаем
3.6. Фактическое передаточное число
Число зубьев колеса внешнего зацепления
3.7. Диаметры колёс. Делительные диаметры d мм:
колеса внешнего зацепления
Диаметры и окружностей вершин и впадин зубьев колёс внешнего зацепления мм:
где - делительный диаметр шестерни;
- делительный диаметр колеса внешнего зацепления;
- коэффициент смещения у шестерни;
- коэффициент воспринимаемого смещения
где - межосевое расстояние;
- делительное межосевое расстояние
где - коэффициент смещения у колеса
3.8. Размеры заготовок. Чтобы получить при термической обработке принятые для расчёта механические характеристики материала колёс требуется чтобы размеры или .
Значения мм см. по таблице в зависимости от материала и твёрдости зубьев
где - ширина колеса мм
При невыполнении неравенств изменяют материал деталей или способ термической обработки.
4.Проверочный расчёт. Проверка зубьев колёс по контактным напряжениям.
Расчётное значение контактного напряжения МПа
Вывод. на 1% следовательно ранее принятые параметры передачи принимаю за окончательные.
4.1.Силы в зацеплении Н
4.2. Проверка зубьев колёс по напряжениям изгиба. Расчётное напряжение изгиба в зубьях колеса
где коэффициент учитывает форму зуба и концентрацию напряжений так как в данном курсовом проекте зецепление внешнее следовательно коэффициент принимаю по таблице в зависимости от количества зубьев.
- коэффициент учитывающий угол наклона зуба и для прямозубых передач 8 степени точности равен 1;
- коэффициент учитывающий перекрытие зубьев и для прямозубых передач 8 степени точности равен 1;
4.3.Проверочный расчёт на прочность зубьев при действии пиковой нагрузки.
Целью расчёта является предотвращение остаточных деформаций или хрупкого разрушения поверхностного слоя или самих зубьев при действии пикового момента . Действие пиковых нагрузок оценивают коэффициентом перегрузки где - максимальный из длительно действующих (номинальный) момент. Коэффициент перегрузки характеризует режим нагружения; его значения задают в циклограмме моментов.
Для предотвращения остаточных деформаций или хрупкого разрушения поверхностного слоя контактное напряжение не должно превышать допускаемое напряжение :
где - контактное напряжение при действии номинального момента ;
Для предотвращения остаточных деформаций и хрупкого разрушения зубьев напряжение изгиба при действии пикового момента не должно превышать допускаемое:
где - напряжение изгиба вычисленное при расчётах на сопротивление усталости.
Проверку выполняют для зубьев шестерни и колеса в отдельности. Допускаемое напряжение вычисляют в зависимости от вида термической обработки и возможной частоты приложения пиковой нагрузки:
где - предел выносливости при изгибе и равен 500 МПа;
- максимально возможное значение коэффициента долговечности ( для сталей с объёмной термообработкой: нормализация улучшение объёмная закалка);
- коэффициент влияния частоты приложения пиковой нагрузки (в случае единичных перегрузок =1.2 1.3);
- коэффициент запаса прочности (обычно =1.75)
Расчёт клиноремённой передачи
По номограмме в зависимости от частоты вращения и мощности электродвигателя выбираю сечение ремня Б мм. Подбираем диаметр ведущего шкива установленного на валу электродвигателя согласно ГОСТ мм.
Подбираем диаметр ведомого шкива установленного на валу редуктора
где - передаточное число ремней передачи;
- коэффициент скольжения = 0.01-0.02
Определяют фактическое передаточное число и проверяют его отклонение от заданного :
Выбираем ориентировочное межосевое расстояние мм:
где - высота сечения клинового (клинового поликлинового) ремня выбираю в зависимости от сечения ремня =10.5
Рассчитываю длину ремня мм:
Значение округляю до ближайшего стандартного =900
Рассчитываю скорость ремня мс:
где и - соответственно диаметр ведущего шкива мм и его частота вращения обмин;
- допускаемая скорость мс для клиновых ремней =25мс
следовательно неравенство выполняется.
Определяем частоту пробегов ремня U:
где - допускается частота пробегов ремня. Соотношение условно выражает долговечность ремня и его соблюдение гарантирует срок службы – 1000-5000ч.
Вычисляю допускаемую мощность передаваемую ремнём кВт:
где - допускаемая приведенная мощность кВт выбирается по таблице в зависимости от типа ремня его сечения скорости мс и диаметра ведущего шкива мм;
- поправочные коэффициенты;
Определяют количество клиновых ремней :
где - номинальная мощность двигателя кВт;
- допускаемая мощность передаваемая ремнями кВт;
так как в проектируемой передачи средней мощности рекомендуется принимать число клиновых ремней следовательно принимаю .
Рассчитываю силу предварительного натяжения :
где - скорость ремня мс;
- номинальная мощность двигателя кВт;
- поправочные коэффициенты выбираются по таблице;
Определяю окружную силу :
Определяю силы натяжения ведущей и ведомой ветвей ремня :
Определяю силу давления ремня на вал
Проверяют прочность одного клинового ремня по максимальным напряжениям в сечении ведущей ветви (набегающей при обхвате малого шкива).
Долговечность поликлинового ремня от 1000-5000 ч. гарантируется при соблюдении условия ;
где - напряжение растяжения от силы ;
- напряжение изгиба ;
- напряжение от центробежных сил ;
где - плотность материала =1000-1400 ;
- окружная скорость ремня ;
допускаемое напряжения растяжения и равно 10
Неравенство выполняется: .
Долговечность ремня (рабочий ресурс) ч:
где - диаметр ведущего шкива мм;
- частота вращения ведущего шкива обмин;
- предел выносливости материала ремня;
- максимальное напряжение в ведущей ветви ремня при набегании её на малый шкив ;
- коэффициент учитывающий влияние передаточного числа ремённой передачи;
- коэффициент нагрузки;
- расчётная (принятая по стандартному ряду) длина ремня м;
- базовое число циклов нагружения ;
Эскизное проектирование
1. Проектные расчёты валов.
Приведена конструкция выходного вала цилиндрического зубчатого редуктора а также расчётная схема и эпюры изгибающих моментов и крутящего моментов продольной осевой силы. Силы в зубчатом зацеплении:
. Коэффициент перегрузки при расчёте на статическую прочность .
Вал изготовлен из стали марки 45 со следующими характеристиками статической прочности и сопротивления усталости: временное сопротивление ; предел текучести ; предел текучести при кручении предел выносливости при изгибе предел выносливости при кручении коэффициент чувствительности к ассиметрии цикла нагружения .
Минимально допустимые запасы прочности по пределу текучести и сопротивлению усталости соответственно и .
1.1. Радиальные реакции опор от сил в зацеплении в плоскости YOZ.
Проверка: следовательно реакции найдены правильно.
Проверка: следовательно реакции найдены правильно.
Суммарные реакции опор:
Радиальные реакции опор от действия муфты. Радиальная жёсткость муфты со стальными стержнями
Радиальная сила на валу от упругой муфты
Определим силовые факторы для опасных сечений.
- в плоскости YOZ слева от сечения
- в плоскости YOZ справа от сечения
- момент от консольной силы
Суммарный изгибающий момент
1.2. Вычисление геометрических характеристик опасных сечений вала
1.3. Расчёт вала на статическую прочность. Вычислим нормальные и касательные напряжения а также значение общего коэффициента запаса прочности по пределу текучести в каждом из опасных сечений вала.
Напряжение изгиба с растяжением (сжатием) и напряжение кручения
Частые коэффициенты запаса прочности по нормальным и касательным напряжениям
Общий коэффициент запаса прочности по пределу текучести
Напряжение изгиба с растяжением (сжатием) и напряжение кручения .
Частные коэффициенты запаса прочности по нормальным и касательным напряжениям
Статическая прочность вала обеспечена во всех опасных сечениях =2.0
1.4. Расчёт вала на сопротивление усталости. Вычислим значения общего коэффициента запаса прочности в каждом из опасных сечений вала.
Определим амплитуды и среднее напряжение цикла
Зубчатое колесо установлено на валу с натягом. Поэтому концентратор напряжений в сечении – посадка с натягом.
Пределы выносливости вала в рассматриваемом сечении
Коэффициент влияния ассиметрии цикла
Коэффициент запаса по нормальным и касательным напряжениям
Коэффициент запаса прочности в рассматриваемом сечении
Определим амплитуды напряжений и среднее напряжение цикла
Внутреннее кольцо подшипника качения установлено на валу с натягом поэтому концентратор напряжений в сечении – посадка с натягом. ; . Посадочную поверхность вала под подшипник шлифуют (); ; ; .
Коэффициенты снижения предела выносливости
Коэффициенты запаса по нормальным и касательным напряжениям
Определим амплитуду и среднее напряжение цикла
Коэффициент снижения предела выносливости
где - коэффициент концентрации напряжений =2.65;
- коэффициент влияния абсолютных размеров =0.68;
- коэффициент учитывающий параметр шероховатости =0.95;
- учитывает вид поверхности упрочнения вала.
Предел выносливости вала в рассматриваемом сечении
Коэффициент запаса прочности в рассматриваемом сечении равен в данном случае коэффициенту запаса по касательному напряжению
Сопротивление усталости вала обеспечено: во всех опасных сечениях =2.0
Подбор и расчёт подшипников
1. Подбор подшипников. За счёт того что не преобладают радиальные нагрузки выбираю роликовые шариковые однорядные подшипники повышенной грузоподъёмности лёгкой серии 218А на тихоходном валу и 210А на быстроходном.
2. Определение всех сил действующих на подшипник.
Рисунок 5.2. – Расчётная схема при условии установки подшипников «враспор»
Радиальная нагрузка в подшипниках Н:
Минимальная осевая сила
где e – коэффициент принимаемый по таблице 24.16 (1 с.465);
Для нормальной работы подшипника необходимо чтобы выполнялось условие:
Кроме того должно выполняться условие равновесия:
Учитывая что осевые силы определяем по следующим зависимостям:
Полученные результаты удовлетворяют условию
3. Расчёт подшипников на статическую грузоподъёмность.
Статическая прочность обеспечена если выполнено условие:
где - статическая радиальная грузоподъёмность для подшипника 210А
- эквивалентная статическая радиальная нагрузка.
Определим эквивалентную статическую радиальную нагрузку Н:
Значение коэффициента радиальной статической нагрузки и коэффициента осевой статической нагрузки выбираем по таблице 7.3 (1 с.106).
Полученные результаты удовлетворяют условию .
4. Расчёт подшипников на заданный ресурс.
Fr1=134396 Fr2=193898
Y=14 коэффициент радиальной нагрузки
X=04 коэффициент осевой нагрузки
Вычисляем эквивалентную динамическую нагрузку:
где V – коэффициент вращения кольца
- коэффициент безопасности по таблице 7.4 (1 с.107)
- температурный коэффициент.
Определим скорректированный по уровню надёжности и условиям применения расчётный ресурс (долговечность) подшипника ч:
где С – базовая динамическая грузоподъёмность подшипника (радиальная Сr)
Р – эквивалентная динамическая нагрузка ( радиальная )
- коэффициент долговечности по таблице 7.5 (1 с.108)
- коэффициент характеризующий совместное влияние на долговечность особых свойств металла деталей подшипника и условий его эксплуатации.
Полученные результаты удовлетворяют заданному ресурсу.
Выбор смазочных материалов и систем смазывания
Смазывание зубчатых зацеплений производится картерным методом: окунанием зубчатых колёс в масло заливаемое во внутрь корпуса до уровня обеспечивающего погружение колеса на длину зубьев.
Объем масляной ванны определяется из расчета: 0.5 масла на один киловатт передаваемой мощности:
По таблице в зависимости от контактного напряжения МПа и окружной скорости V мс устанавливаем вязкость масла. При температуре 40° вязкость =50 . В зависимости от вязкости подбираем масло. Марка масла И-Г-А-46 (масло индустриальное для гидравлических систем без присадок).
Выходной вал передаёт наибольший в приводе крутящий момент и вращается с относительно небольшой скоростью. На выходном валу целесообразнее устанавливать зубчатую муфту по ГОСТ 5006-83.
Выбор и расчёт шпонок
Шпонки выбираю призматические (из ГОСТ 23360-78) по таблице в зависимости от диаметра вала.
Рассчитаем шпонку тихоходного вала служащей для крепления колеса.
Расчёт шпонок на смятие
Расчёт шпонок на срез
Техническое задание 3
Кинематический расчёт привода 5
1. Подбор электродвигателя 5
2. Определение частот вращения и вращающих моментов на валах 6
Расчёт цилиндрической передачи 7
1. Выбор материала 7
2. Определение допускаемых контактных напряжений и напряжений изгиба 7
3. Проектный расчёт 8
4. Проверочный расчёт 13
Расчёт клиноремённой передачи 16
Эскизное проектирование 20
1. Проектные расчёты валов 20
Подбор и расчёт подшипников 28
1. Подбор подшипников 28
2. Определение всех сил действующих на подшипник 28
3. Расчёт подшипников на статическую грузоподъёмность 29
4. Расчёт подшипников на заданный ресурс 29
Выбор смазочных материалов и систем смазывания 31
Выбор и расчёт шпонок 33
Подбор посадки с натягом 34
Список литературы 38
П.Ф. Дунаев О.П. Лёликов. Конструирование узлов и деталей машин . – М.: Высшая школа 2000.
Детали машин. Атлас конструкций. Под ред. Д.Н.Решетова. Издание 5-е в двух частях. М.: Машиностроение 1992.
Расчёт посадки с натягом(норм).doc
Вращающий момент на колесе Т=37843 Нм;
Диаметр соединения d=110 мм;
Диаметр отверстия пустотелого вала d1=0 мм;
Условный наружный диаметр втулки d2=130 мм;
Подбор посадок производят в следующем порядке.
Среднее контактное давление (МПа)
где К-коэффициент запаса сцепления f- коэффициент сцепления (трения);
Деформация деталей (мкм)
где С -коэффициенты жесткости:
где Е - модуль упругости; - коэффициент Пуассона;
Поправка на обмятие микронеровностей (мкм)
U= 55 ; где - средние арифметические отклонения профиля поверхностей.
Поправка на температурную деформацию (мкм)
где и - объемная средняя температура соответственно обода центра и венца колес.
Минимальный натяг (мкм)
Максимальный натяг (мкм)
мкм- максимальная деформация (МПа)- максимальное давление
По полученным значениям выбираем посадку
Для выбранной посадки определяют силу запрессовки или температуру нагрева детали.
Температура нагрева охватывающей детали
Рекомендуемые чертежи
- 21.10.2021
- 24.01.2023
- 24.01.2023