Одноковшовый погрузчик с челюстным захватом на базе трактора Т-150К г/п 6 тонн




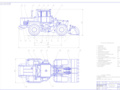
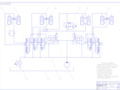
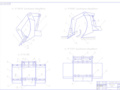
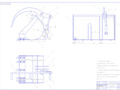
- Добавлен: 25.10.2022
- Размер: 2 MB
- Закачек: 1
Описание
Состав проекта
![]() |
![]() ![]() |
![]() ![]() |
![]() ![]() |
![]() ![]() |
![]() ![]() |
![]() |
![]() ![]() ![]() ![]() |
![]() ![]() |
![]() |
![]() ![]() ![]() ![]() |
![]() ![]() ![]() ![]() |
![]() ![]() ![]() ![]() |
![]() ![]() ![]() ![]() |
![]() ![]() ![]() ![]() |
![]() ![]() |
![]() ![]() |
![]() ![]() |
![]() ![]() |
![]() ![]() ![]() |
![]() ![]() |
![]() ![]() |
Дополнительная информация
Спец-РО.dwg

ГС.dwg

Технические требования
Уровень рабочей жидкости должен
располагаться между верхней и нижней
метками смотрового окна гидробка
при установке погрузчика
на горизонтальной площадке.
Не допускать подтекания
рабочей жидкости в местах
соединения трубишлангов.
Работать с повышением параметров
гидропривода запрещено.
РО.dwg

* Размеры для справок.
Сварные швы по ГОСТ 5264-80.
Сварку производить электродом Э42 А
Наплавку поверхности зуба производить
Покрытие: грунтовка ФЛ-03к коричневая ГОСТ
09-76; эмаль ХВ-110 оранжевая ГОСТ
СпецификацияГС.dwg

Гидроцилиндр поворота
Гидроцилиндр захвата
Патентный поиск.dwg

А.с. № 891854 "Бульдозерное оборудование
А.с. № 1382916 "Бульдозерное оборудование
А.с. № 972011 "Бульдозерное оборудование
ОВ.dwg

*Размеры для справок
Гидросистему дозаправить маслом М-8В ГОСТ-8581-78 в количестве
Максимальный угол запрокидывания ковша
Производительность гидронасосов
погрузочного оборудования
Максимальное выглубляющее усилие на режущей
Курсовой проект по МЗР
Техническая характеристика
Максимальная скорость
Грузоподъемность номинальная
Емкость ковша номинальная
Максимальный угол разгрузки
Номинальное давление в гидросистеме
Масса погрузочного оборудования
Записка.docx
Государственное образовательное учреждение
высшего профессионального образования
Пермский научно-исследовательский политехнический университет
Кафедра строительных и дорожных машин
Тема: «Одноковшовый погрузчик с челюстным захватом на базе трактора Т-150К»
Определение основных параметров
Расчет элементов рабочего оборудования
Расчет производительности
Техника безопасности
Основное назначение одноковшовых погрузчиков в строительстве – выполнение различных погрузочных операций с сыпучими кусковыми и штучными грузами. В последнее время увеличение мощности и рабочих усилий этих машин расширило область их применения. Сейчас они успешно используются не только для погрузки в карьерах сыпучих мелкокусковых и крупнокусковых грунтов но и для производства некоторых видов земляных работ (например для разработки с погрузкой в транспорт слабосвязных грунтов без крупных каменных включений). Поэтому некоторые типы одноковшовых погрузчиков можно относить к машинам для земляных работ.
Одноковшовые погрузчики используемые для земляных работ классифицируются по:
направлению разгрузки ковша;
типу базовой машины и другими конструктивными признаками.
По грузоподъемности погрузчики делятся на:
малогабаритные(грузоподъемность до 05т);
легкие (грузоподъемность 06 2т);
средние (грузоподъемность 21 4т);
тяжелые (грузоподъемность 41 10т);
большегрузные (грузоподъемность свыше 10т).
(ГОСТами предусмотрен выпуск погрузчиков грузоподъемностью 3 4 6 и 10т).
По направлению разгрузка может быть:
При этом погрузочное оборудование бывает полуповоротное комбинированное перекидное и фронтальное. Для полуповоротного оборудования характерна боковая разгрузка ковша; комбинированное оборудование позволяет производить и переднюю и заднюю разгрузку.
Погрузчики могут быть использованы для послойной разработки грунтов I III категорий и более прочных грунтов с предварительным рыхлением.
Одноковшовый погрузчик представляет собой самоходную машину оснащенную ковшовым рабочим органом. Погрузчик может иметь специальное гусеничное или пневмоколесное устройство. Часто рабочее оборудование погрузчика монтируют на гусеничном или пневмоколесном тракторе-тягаче.
Рабочее оборудование (см.рис.1) включает ковш 1 стрелу 5 рычаги 2 поворота ковша и гидросистемы для привода рабочих органов. Гидроцилиндры 4 поднимают и опускают стрелу со всем оборудованием а гидроцилиндры 3 изменяют положение ковша в процессе работы погрузчика и опрокидывают его при разгрузке.
Заполнение ковша погрузчика материалом происходит под действием тягового (толкающего) усилия на величину Lвр. В мягких грунтах ковш внедряется в штабель материала на полную глубину поворачивается и приподнимается затем погрузчик задним ходом отходит от забоя для погрузки материала в транспортные средства или перемещается на необходимое расстояние для разгрузки в отвал. По возвращении погрузчика в забой цикл повторяется.
Колесные погрузчики имеют массу 03 85 т вместимость ковша 005 35 м3 и выше мощность 6 500 кВт и более производительность в 25 3 раза выше чем у экскаваторов такой же массы. Ими можно выполнять некоторые работы без специального вспомогательного транспорта. Основной недостаток погрузчиков – в 2 3 раза меньшая высота копания чем у одноковшовых экскаваторов и очень малый радиус действия требующий подъезда почти вплотную к забою.
Весьма ограниченное применение имеют другие типы погрузчиков производящих разгрузку на месте опрокидывания ковша назад что позволяет почти полностью исключить маневры между циклами а также и полуповоротные у которых рабочее оборудование может поворачиваться на 210 270. Эти погрузчики могут работать в мягких грунтах как полуповоротные экскаваторы. Погрузчики могут снабжаться ковшом с боковой разгрузкой что упрощает маневрирование машины.
Достоинством гусеничных погрузчиков является в 12 15 раза большее чем у колесных усилие при внедрении в грунт силой тяги и большая маневренность вследствие возможности разворота на месте что сокращает продолжительность цикла на 3 6 с или на 8 25%. При этом производительность повышается на 20 30%. В соответствии с большей силой тяги гусеничные погрузчики чаще снабжаются оборудованием рыхлителя.
Погрузчики с ковшами вместимостью 115 3 м3 и мощностью 50 180 кВт имеют наибольшее число моделей.
Следует отметить что шарнирно-сочлененная рама уменьшая на 20 30% минимальный радиус поворота и значительно увеличивая этим маневренность погрузчиков в то же время уменьшает их устойчивость как при копании так и при транспортных операциях во время прохождения по кривым и по участкам с большим уклоном особенно одновременно с торможением. Поэтому копание такими погрузчиками рекомендуется производить при угле поворота частей шарнирно-сочлененной рамы относительно друг друга на угол в мягких грунтах на более 25 а крепких – не более 15. Максимальный взаимный поворот частей шарнирно-сочлененной рамы составляет 35 45 при этом наибольшая грузоподъемность погрузчиков снижается на 10 12%. Наибольшую опасность представляет возможность такой рамы при резком торможении складывается что непременно ведет к аварии.
На колесом погрузчике сзади иногда устанавливают второе обычно экскаваторное оборудование. В некоторых случаях сбоку трактора устанавливают и третье оборудование – трубоукладчик. Погрузчики при которых рабочее оборудование располагается над задней осью трактора или тягача обычно имеют дополнительное оборудование – рыхлителя или бульдозера увеличивающее их устойчивость. Если вторым сменным оборудованием является экскаваторное то оборудование погрузчика являющегося в данном случае и противовесом для экскаватора чаще располагается на моторной части шасси особенно если передние управляемые колеса имеют малый диаметр.
А.с. № 891854 «Бульдозерное оборудование»
Бульдозерное оборудование (рис.2) включает толкающие брусья 1 отвал 2 с ножом 3 и передней челюстью с боковыми стенками 4 оснащенными в нижней части клыками 5 ножом 6 который с помощью рычагов 7 и шарниров 8 прикреплен к боковым стенкам челюсти 4. На рычагах 7 установлены боковые подрезающие ножи 9. Управление челюстью осуществляется с помощью гидроцилиндров 10.
Бульдозерное оборудование работает следующим образом.
При разработке прочных грунтов с помощью гидроцилиндров 10 передняя челюсть поворачивается против часовой стрелки и устанавливается в крайнее положение. При этом нож челюсти 6 располагается ниже ножа 3 отвала 2 образовывая выступающий средний нож чем достигается увеличение удельного давления на режущую кромку и обеспечивается возможность разработки более прочных грунтов.
Конструкция бульдозерного оборудования обеспечивает возможность захвата различного рода грузов как единичных так и складированных в штабелях. Для этого челюсть с помощью гидроцилиндров 10 отводится в крайнее верхнее положение отвал бульдозера 2 подводится к грузу подлежащему транспортировке а затем челюсть опускается вниз. При этом боковые стенки челюсти 4 клыками 5 внедряются в штабель с материалов и прижимают его к отвалу бульдозера 2. Нож челюсти 6 на рычагах 7 проворачивается относительно шарниров 8 не оказывая сопротивления внедрению клыков 5.
Предлагаемое оборудование обладает расширенными технологическими возможностями связанными с захватом штучных и штабилированных грузов.
А.с. № 972011 «Бульдозерное оборудование»
Бульдозерное оборудование (рис.3) содержит толкающие брусья 1 отвал 2 и переднюю челюсть выполненную из двух боковин 3 и 4. К боковинам жестко прикреплены противоположными концами раздельные секции 5 и 6 выступающего ножа установленные с возможностью продольного перемещения параллельно друг другу. Боковина 4 снабжена в нижней части жестко закрепленной горизонтальной штангой 7 установленной в отверстии противоположной боковины 3. В свою очередь боковина 3 снабжена такой же горизонтальной штангой 8 в верхней части причем горизонтальная штанга 8 установлена в отверстии боковины 4. Сверху на обеих секциях 5 и 6 выступающего ножа закреплены проушины 9 и 10 соответственно установленные на нижней горизонтальной штанге 7. Верхняя горизонтальная штанга установлена в проушинах 11 крепления челюсти к отвалу 2. На верхнем конце боковины 4 жестко закреплена дополнительная горизонтальная штанга 12 установленная в отверстии верхнего конца другой боковины 3 причем дополнительная штанга 12 соединена с гидроцилиндром 13 поворота челюсти. Между верхними концами боковин 3 и 4 смонтирован гидроцилиндр 14 раздвижения боковин выступающего ножа. На отвале 2 установлен обычным образом нож 15. На свободных концах горизонтальных штанг 7 8 и 12 смонтированы ограничительные упоры 16.
Работа бульдозерного оборудования осуществляется следующим образом.
При копании грунта ножом 15 отвала 2 шток гидроцилиндра 13 поворота челюсти втянут и передняя челюсть повернута вверх при разработке более прочных грунтов шток гидроцилиндра 13 выдвигается воздействуя на дополнительную горизонтальную
штангу 12 и поворачивая вниз переднюю челюсть до упора секций 5 и 6 выступающего ножа в нож 15 отвала; выдвинутый шток гидроцилиндра 14 обеспечивает максимальную ширину В2 копания грунта выступающим ножом. Нагрузки воспринимаемые секциями 5 и 6 выступающего Ножа при копании грунта передаются через проушины 9 и 10 на нижнюю горизонтальную штангу 7 и через нее боковины 3 и 4 челюсти. Выдвижение штока гидроцилиндра 14 ограничено упорами 16.
За счет адаптации ширины выступающего ножа к прочности разрабатываемых грунтов существенно повышается эффективность бульдозерного оборудования увеличивается производительность бульдозера. Кроме того при захвате передней челюстью и перемещения длинномерных грузов например балок бревен столбов и т.п. раздвижение боковин передней челюсти улучшает захват и удержание таких грузов; при перемещении мелких грузов – валунов контейнеров и т.п. – захват и удержание грузов существенно улучшается сближением боковин передней челюсти.
А.с. № 1382916 «Бульдозерное оборудование»
Бульдозерное оборудование (рис.4) включает толкающие брусья 1 смонтированный на них отвал 2 шарнирно соединенную с кронштейнами 3 отвала 2 переднюю челюсть 4 с подножевой плитой 5 на которой установлен нож челюсти выполненный из жестко закрепленной на подножевой плите 5 средней секции 6 и других секций 7 смонтированных на плите с возможностью ограниченного продольного перемещения. Секции 7 имеют выступы 8 которые размещены в пазах 9 подножевой плиты 5. Пазы 9 имеют на входе и выходе ограничители 10. На верхней торцовой стороне средней секции 6 жестко закреплена гибкая пластина 11 в которую упираются своими торцами секции 7. Для управления челюстью предназначен гидроцилиндр 12.
При копании грунта отвалом 2 шток гидроцилиндра 12 втянут и передняя челюсть повернута вверх. При разработке более прочных грунтов шток гидроцилиндра 12 выдвигается и поворачивает переднюю челюсть вниз до упора подножевой плиты 5 в отвал 2 и копание грунта осуществляется секциями ножа
челюсти. Давление грунта на подвижные секции 7 через их верхние торцовые части передается на гибкую пластину 11 и при значении его меньшем чем усилие деформации пластины 11 разработка грунта осуществляется при прямоугольной конфигурации ножа челюсти 4.
А.с. № 1647085 «Бульдозерное оборудование»
Бульдозерное оборудование (рис.5) включает толкающие брусья 1 отвал 2 с ножом 3 и боковыми щеками 4 переднюю челюсть 5 соединенную с отвалом 2 шарнирно своими боковинами 6 и 7. Ножи передней челюсти 5 выполнены из секций 8 и 9 расположенных одна над другой и закрепленных секция 8 на боковине 6 и секция 9 – на боковине 7. Гидроцилиндр 10 двустороннего действия раздвижения боковин 6 и 7 передней челюсти 5 смонтирован между верхними концами боковин.
Оборудование работает следующим образом.
При копании грунта ножом 3 отвала 2 шток 13 гидроцилиндра втянут и передняя челюсть повернута вверх. При разработке более твердого грунта шток 13 гидроцилиндра выдвигается воздействуя на корпус гидроцилиндра 10 и поворачивая вниз переднюю челюсть до упора секций 9 и 10 и ножа челюсти в нож 3 отвала 2.
При разработке менее твердого грунта фиксаторы 25 с внешней стороны боковин 6 и 7 вынимаются и при выдвижении штоков гидроцилиндра 10 боковины 6 и 7 раздвигаются перемещая вдоль отвала параллельно друг другу секции 8 и 9 ножа челюсти до установки необходимой ширины копания грунта ножом челюсти после чего боковины 6 и 7 фиксируются фиксаторами 25 в пазах 24 штанг 11 и 12. Выдвижение штоков гидроцилиндра 10 ограничено боковыми щеками 4 отвала. Боковины 6 и 7 препятствуют потерям грунта при разработке сыпучих грунтов. При этом достигается максимальная ширина копания грунта ножом челюсти.
В случае необходимости работы в стесненных условиях фиксаторы 25 боковины 6 вынимаются штоки гидроцилиндра 10 выдвигаются и боковина 6 с секцией 8 перемещаются до необходимого положения в котором фиксируется фиксаторами 25 в пазах 24 штанг 11 и 12.
При захвате сыпучих материалов пальцы 20 вынимаются секции 8 и 9 поворачиваются относительно штанги 12 и фиксируются пальцами 20 в свободных отверстиях 22 боковин 6 и 7. Шток 13 гидроцилиндра выдвигается при этом задняя режущая кромка 17 внедряется в разрабатываемый материал до упора в нож 3 отвала 2. Разрабатываемый материал при этом находится в ковше образованном боковинами 6 и 7 боковыми щеками 4 отвала секциями 8 и 9 ножа челюсти и отвалом 2.
Проанализировав представленные авторские свидетельства я решил взять за основу авторское свидетельство № 891854 но проделать некоторые доработки (исключаем некоторые детали что уменьшит количество видов выполняемых работ но будет выполнять необходимую работу которая была задана при проектировании) что в последствии упростит конструкцию гидроуправляемой челюсти.
Исходными данными для расчётов механизмов и узлов одноковшовых погрузчиков являются параметры специальных колёсных базовых шасси. Параметры одноковшовых фронтальных погрузчиков рассчитывают с основным ковшом. Для погрузчиков грузоподъёмностью 2-10 тонн некоторые параметры (высота и вылет разгрузки углы запрокидывания и разгрузки) определены ГОСТ 12568-67.
Номинальная грузоподъёмность. Принимаем согласно технических данных фронтального одноковшового погрузчика – 6000 кг.
Эксплуатационный вес погрузчика – вес базового шасси и погрузочного оборудования согласно технических данных равен GП = 21000 кг.
Вес базовой машины GT = 16800 кг.
Определение веса погрузочного оборудования :
Вес погрузочного оборудования Go = 4200 кг.
гдеQ – номинальная грузоподъемность Q=6т;
– плотность материала =(13 16)тм3 (грунт II категории) =16тм3;
kн – коэффициент наполнения kн= (11 13) kн=125;
Для предварительного определения размеров ковша по заданной его емкости может быть использована взаимосвязь размеров ковша: длины l ширины В высоты задней стенки h.
Для данной формы ковша принимаем формулы:
Определим напорное усилие которое определяют по тяговой характеристике базового шасси с учётом догрузки его массой равной погрузочному оборудованию.
где Nдmax – наибольшая эффективная мощность двигателя л. с.
vm – теоретическая скорость движения базового шасси на рабочей передаче кмч;
тр – коэффициент полезного действия трансмиссии для гидромеханической трансмиссии тр = 067;
Gn – вес погрузчика;
f – коэффициент сопротивления качению для колёсных погрузчиков f= 003;
Тогда напорное усилие равно:
Максимальное напорное усилие с учётом увеличения крутящего момента по внешней характеристике двигателя и увеличения буксования определяется соотношением:
где – коэффициент перегрузки двигателя; =11 115;
Р – расчётное буксование движителей для колёсных погрузчиков принимают Р = 02;
Наибольшее напорное усилие проверяют по сцепному весу погрузчика
где G – эксплуатационный вес погрузчика;
φ – коэффициент сцепления движителей принимаем φ = 07.
Тяговое усилие по двигателю больше тягового усилия по сцеплению.
Расчет ведется по наиболее опасным случаям нагружения. К наиболее опасным нагружениям относят три случая:
Удар края ковша о труднопреодолимое препятствие при движении погрузчика с запертыми гидроцилиндрами стрелы и ковша по горизонтальному участку (рис.7).
Вывешивание погрузчика вокруг салазок или передней оси при повороте внедренного в штабель ковша за счет усилия развиваемого гидроцилиндрами поворота ковша (рис.8).
Вывешивание погрузчика вокруг задней оси под действием цилиндров подъема стрелы (рис.9).
Для всех трех случаев внешние усилия считаются сосредоточенными силами приложенными к концу режущей кромки ковша (или к крайнему зубу). Боковые составляющие сил сопротивления возникновение которых маловероятно не учитывают. Во всех трех случаях к ковшу приложена горизонтальная сила равная максимальному в данных условиях тяговому усилию.
Первое расчетное положение.
Для первого случая горизонтальное усилие определяется тяговым усилием массой машины и скоростью ее движения:
гдеRХс – статическое напорное усилие равное номинальному тяговому усилию Тн RХс=1865 кН;
RХд –динамическое усилие:
гдеvр – рабочая скорость внедрения ковша vр=01 мс;
С – приведенная жесткость определяется жесткостью погрузочного оборудования и возможных препятствий:
гдеС1 – жесткость погрузочного оборудования:
С1=kж·Gп=01·165300=1653 кНсм
гдеkж – коэффициент жесткости оборудования на 1 кг веса равный 01
С2 – жесткость препятствий С2=11000 кНсм (железобетонный столб врытый на глубине 120 см F=400 см2)
М – приведенная масса погрузчика:
Второе расчетное положение.
Вертикальная и горизонтальная силы приложены по оси крайнего зуба основного ковша установленного в положение внедрения. Величину вертикальной силы определяют из условия устойчивости машины (для случая когда стрела не опирается башмаками на грунт) по выглубляющему усилию развиваемому гидроцилиндрами поворота ковша.
Горизонтальную силу принимают равной номинальному тяговому усилию погрузчика (Rх=Тн).
Третье расчетное положение.
Вертикальная и горизонтальная силы действуют по оси крайнего зуба. В качестве вертикальной силы принимают усилие отпора создаваемое при вывешивании трактора на задних колесах и на зубьях ковша который установлен в положение внедрения.
Горизонтальную силу определяют по сцепной силе тяжести с учетом разгрузки машины:
Rх=(Gп–Ry)=(1653–488)08=932 кН
Рассмотрим вторую расчётную схему.
Вертикальная и горизонтальная силы приложены по оси зуба или на режущей кромке на расстоянии 14 ширины основного ковша установленного в положении внедрения.
Рис.10. Схема сил действующих на рабочее оборудование.
Так как нагрузки приложены к ковшу не по оси симметрии возникают моменты сил воспринимаемые конструкцией стрелы:
Реакции в опорах стрелы О1и О1от действия моментов составляют:
вс = 098 м – ширина стрелы.
С учётом действия нагрузок от тяг поворота ковша определяемых по уравнениям:
где 11 = 1.4м; 12 = 054м; 13 = 025м; 14 = 05м – плечи соответствующих сил.
Рис.11. Схема сил действующих на ковш.
Полные реакции в опорах О1 О11 получим:
Полученные в шарнирах О1 О11 реакции перенесём в точки крепления поперечины к продольным балкам стрелы заменив их действие моментами и силами лежащими в плоскости стрелы и перпендикулярными к ней (рис.12).
Рис.12. Схема расчёта стрелы.
Эта система является статически неопределимой. Чтобы устранить статическую неопределимость воспользуемся методом сил приняв в качестве основной систему разрезанную в центре поперечины со вставленным стержнем. Это обусловлено тем что данная рама кососимметрична а при кососимметричных нагрузках рама с приложенными нагрузками в силу симметрии самой рамы имеет на четыре связи меньше чем при произвольном приложении нагрузки то есть является один раз статически неопределимой системой.
В качестве эквивалента неизвестной связи выберем крутящий момент относительно оси z приложенный в месте разреза (рис.13).
Рис.13. Схема раскрытия статической неопределимости
Разрежем поперечную связь стрелы. Нагрузим раму в месте разреза крутящим моментом равным единице и построим эпюры крутящих и изгибающих моментов от этой нагрузки:
Рис.10. Эпюры изгибающих моментов от единичной нагрузки
На поперечине: Мк = 1;
Нагружаем раму рабочими нагрузками и строим эпюры моментов:
Рис.11. Эпюры изгибающих моментов от внешней нагрузки
Силу Рк определяем из уравнения моментов относительно оси О3О3
Находим жёсткости Сi продольных брусьев и поперечины:
Поперечина – труба D =126 мм; d = 100 мм.
где Е – модуль упругости для стали при растяжении Е=21105МПа;
G – модуль упругости при кручении для стали G=85·104МПа;
Си1 = ЕJx=21*1011*746*10-6=l57 MПa
Скр1 = G JР=85*104*149*10-5=l27 MПa
Балка: Н = 380 мм; В = 120 мм; д = 8 мм
Рис.14. Поперечное сечение балки.
Си2 = ЕJx=21*1011*375*10-6=0788*106 кгсм2=772MПa
Скр2 = G JР=85*1010*388*10-5=033*106=323 MПa
Каноническое уравнение для принятой системы имеет вид:
Перемещения определяем по способу Верещагина:
Построим эпюры расчётных крутящих и изгибающих моментов:
Рис. 13. Эпюры внутренних силовых факторов.
Находим нормальные и касательные напряжения в поперечине и стреле в зоне прикрепления поперечины к балкам стрелы.
Сделаем прочностной расчёт элемента челюстного захвата. Произведем расчет зуба челюстного захвата.
Воспользуемся расчетной схемой (рис.14).
Рис.14. Расчетная схема
Сила N – реакция от удержания груза принимаем 40 кН; РГ – усилие развиваемое гидроцилиндром (неизвестна); G – сила тяжести челюстного захвата принимаем 10 кН.
Из условия равновесия относительно т.О можно найти усилие развиваемое гидроцилиндром РГ.
ΣМ(О)=0: N·058-G·037-РГ·029=0 т.е.
РГ=(N·058-G·037)029=(40·058-10·037)029=672 кН
Найдем изгибающий момент в опасном сечении (место где действует сила N) воспользуясь расчетной схемой (рис.15).
Ми=G·0375-РГ·101=10·0375-672·101=-641 кНм
Теперь надо определить геометрические характеристики поперечного сечения (рис.16).
Определим момент сопротивления изгибу опасного сечения:
Тогда нормальное напряжение от изгибающего момента в опасном сечении будет равно:
Материал челюстного захвата – низколегированная марганцовистая сталь 09Г2 с пределом текучести т=300МПа.
Определим запас прочности:
Запас прочности очень большой т.е. мы можем применить материал более дешевый с низкими прочностными характеристиками.
Производительность погрузчика как и всякой машины циклического действия определяется объемом черпаемого за цикл материала и длительность цикла.
Объем материала в ковше зависит от вместимости ковша и коэффициента его заполнения а длительность цикла в первую очередь – от принятой схемы погрузки дальности транспортирования материала на погрузку и квалификации машиниста (его умения совмещать операции и выбирать оптимальный режим работы для каждой из операций цикла).
Техническая производительность:
гдеVк – геометрическая емкость ковша; Vк=3 м3;
kнап – коэффициент наполнения; kнап=11;
kразр – коэффициент разрыхления грунта; kразр=12;
tц – теоретическая продолжительность цикла:
tц=tн+tр+tт+tо+tх+tп
гдеtн – время наполнения ковша:
Vр – рабочая скорость внедрения Vр=036 кмч;
kv – коэффициент учитывающий буксование ходовой части и потери в трансмиссии kv=15.
tр – время рабочего хода:
гдеSр – путь рабочего хода Sр=50 м;
Vз – задняя скорость движения Vз=23 кмч.
tт – время маневрирования транспортного средства:
tт=0 т.к. мы рассчитываем поворотный погрузчик.
tо – время опорожения ковша:
tх – время холостого хода (возврат к месту внедрения):
гдеSх – путь холостого хода Sр=50 м;
Vр – рабочая скорость движения Vз=52 кмч.
tп – суммарное время на переключение передач и гидрораспределителя:
tц=tн+tр+tт+tо+tх+tп=16+78+0+10+35+10=149с
Эксплуатационная производительность:
Это количество погружаемого машиной груза в час за общее время работы машины в эксплуатационных условиях включая подготовительно-заключительные операции и простои по организационным и техническим причинам.
гдеТсм – число часов работы в смену Тсм=68 ч;
kвр – коэффициент учитывающий простои машины kвр=(082 092)=085;
kу – коэффициент учитывающий влияние качества управления состояния машины и квалификацию машиниста kу=(095 096)=095.
Для расчета устойчивости колесного погрузчика с балансирной подвеской все весовые силы приводят к осям машины. Это особенно удобно при определении силового влияния одной части машины на другую в зависимости от конструктивного исполнения ходовой части или от того на какой поверхности (горизонтальной или наклонной) находится машина. Способ приведения сил позволяет оценить устойчивость машины в зависимости от устойчивости отдельных ее частей.
Рис.6. Схема расчета устойчивости погрузчика.
Расчетное положение для расчета на устойчивость – при максимальном вылете ковша. Опрокидывание возможно через т.А.
Составим уравнение коэффициента устойчивости:
Силу тяжести погрузочного оборудования приняли выше и она составила 4200·98=42 кН а координаты – конструктивно.
Посчитаем удерживающий и опрокидывающий моменты.
Тогда коэффициента устойчивости будет равен:
Рассчитываемый погрузчик будет устойчив с запасом.
Во время работы машинист не должен отвлекаться от своих прямых обязанностей. В случае наличия в машине стажера ни один из них не имеет права отлучаться даже на короткое время не предупредив другого. Перед отлучкой машинист обязан остановить двигатель и убрать ключ зажигания двигателя внутреннего сгорания.
Нельзя входить на машину или сходить с нее во время передвижения подъема и опускания рабочего оборудования и т.п.
По окончании работы машинист обязан сделать запись в сменном журнале о замеченных неисправностей и предупредить об этом машиниста принимающего смену а при односменной работе – механика или лицо ответственное за эксплуатацию машины.
После смены все горючие и смазочные материалы необходимо сдать на склад огнеопасных материалов. Загрязнять место стоянки машины нефтепродуктами и использованными материалами запрещается.
Машинист должен участвовать в планово-предупредительном ремонте обслуживаемой им машины и принимать участие в сдаче ее инспекции Госгортехнадзора.
Во время своей смены машинист несет ответственность за вверенную ему машину и относящиеся к ней имущества. Если в результате работы машины произошла авария или несчастный случай машинист должен остановить машину и не производить никаких работ впредь до прихода начальства в ведении которого находится эта машина.
Машинист обязан соблюдать частоту и порядок в кабине машины.
Строительные машины: СправочникПод общ.ред. Э.Н.Кузина – М.: Машиностроение 1991
Погрузочные машины для сыпучих и кусковых материаловК.С.Гурков – М.: Машиностроение 1962
Машины для земляных работ: Атлас конструкцийПод ред. А.А.Бромберга – М.: 1968
Расчет параметров ковша.
Все параметры ковша выбирают с учетом соотношений рис.6.
Расчетный радиус ковша высчитывается по формуле:
гдеVн – номинальная вместимость ковша Vн=3 м3;
В0 – ширина ковша принимаем конструктивно В0=173 м;
гдеλд – относительная длина днища ковша λд=14 15 принимаем 14;
λз – относительная длина задней стенки λз=11 12 принимаем 11;
λк – относительная высота козырька λк=012 014 принимаем 012;
λr – относительный радиус сопряжения днища и задней стенки λr=035 04 принимаем 035;
γ1 – угол между плоскостью козырька и продолжением плоскости задней стенки γ1=5 100 принимаем 100;
γ0 – угол между задней стенкой и днищем γ0=48 520 принимаем 500.
Тогда расчетный радиус ковша будет равен:
lд=λд·R0=14·09=126 м.
Длина задней стенки:
lз=λз·R0=11·09=10 м.
lк=λк·R0=012·09=011 м.
r0=λr·R0=035·09=032 м.
Высота шарнира крепления ковша к стреле:
hш=006 012·R0=010·09=009 м.
Угол наклона режущих кромок боковых стенок относительно днища ковша α0=50 600. Угол заострения режущих кромок 0=30 400.
Расчет гидроцилиндра челюстного захвата.
Для расчета гидроцилиндра челюстного захвата необходимо знать усилие которое должен развивать гидроцилиндр. Выше (при расчете на прочность зуба челюстного захвата) мы определили усилие которое необходимо подвести для удержания груза.
Так как мы используем два гидроцилиндра то найденное усилие необходимо поделить пополам т.е.
Рг=Рг2=6722=336 кН34 кН
Внутренний диаметр гидроцилиндра определяют из выражения:
гдеРг – усилие на штоке Рг=34 кН;
Р – давление в системе Р=20 МПа;
г – гидравлический КПД г=096;
м – механический КПД м=09.
По ГОСТ 12447-80 выбираем стандартный внутренний диаметр гидроцилиндра Dр=50 мм.
Определяем диаметр штока dш
dш=06*Dп=06*50=30 мм
Зная внутренний диаметр гидроцилиндра можно найти истинное значение усилия развиваемое гидроцилиндром т.е.
Мощность гидроцилиндра:
Nг=Рг·Vп=34·04=136 кВт
гдеРг– усилие на штоке Рг=34 кН;
Vп – скорость движения поршня принимаем Vп=04 мс.
Рекомендуемые чертежи
- 18.05.2021