Модернизация рабочей камеры щёковой дробилки СДМ-108А с целью снижения износа дробящих плит




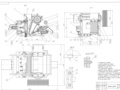
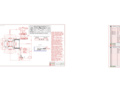
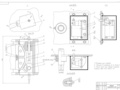
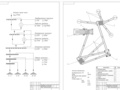
- Добавлен: 25.10.2022
- Размер: 2 MB
- Закачек: 1
Описание
Состав проекта
![]() |
![]() |
![]() ![]() ![]() ![]() |
![]() ![]() ![]() ![]() |
![]() ![]() ![]() ![]() |
![]() ![]() ![]() ![]() |
![]() ![]() ![]() ![]() |
![]() ![]() ![]() ![]() |
![]() ![]() ![]() ![]() |
![]() ![]() ![]() ![]() |
![]() ![]() ![]() ![]() |
![]() ![]() ![]() |
Дополнительная информация
Привод механизма.dwg

Частота вращения вала обмин
ДПДМ2011.815.00.03.00СБ
передняя щека.dwg

Количество прокладок поз.7 под
клинья поз. 3 и 4 определяется при сборке
11.dwg

ЭКОНОМИКА.dwg

Технико - экономические показатели
Единицы q*; измерения
Значения показателей
Наименование показателей
Дополнительные капи тальные вложения
Текущие затраты на ТО и Р
10.dwg

Наименование смазываемых поверхностей
Подшипники подвижной оси щеки
Смазка распорных плит
Роликоподшипник вала привода
Тип смазы- ваемых поверхнос- тей
Размеры смазываемых поверхностей
Число оборотов вала в мин
Тип смазочного питателя
Поверх. скольжения Вxl(мм)
Условно для скольжения
Смзка применяемая в летних условиях: Индустриальная ИП1-Л ГОСТ 3257-84
Смазка применяемая в зимних условиях: Индустриальная ИП1-3 ГОСТ 3257-84
сварку и крепление труб заказанных общим метражом производить на монтаже по месту. Минимальные радиусы гиба труб 3-4 наружных диаметра трубы. 2. Резьбовые соединения выполнить с трубной конической резьбой повышенной точности по ГОСТ 6211-82. 3. Резьба с сорванными витками допускается на монтаж
если в сумме они не превышают 10% длины нарезки. 4. Перед монтажом внутреннюю поверхность труб необходимо протравить 20% раствором соляной кислоты
нейтрализовать 3-5% известковым раствором
просушить и смазать минеральным маслом. Протравленными считать трубы
внутренняя поверхность которых имеет сплошной светлостальной цвет. 5. Монтаж покупной аппаратуры и приборов производить согласно паспортов и технических условий заводов-изготовителей. 6. После монтажа системы смазки произвести испытание на давление Рпроб=100-120 кгсм в течении 5-8 мин. для каждой линии системы смазки. Допустимое падение давления за это время не более 20%. При падении давления более 20% выявляются места утечки смазки
после их устарнения система испытывается повторно. 7. После испытания на пробное давление система настраивается на рабочее давление. 8. Количество мази необходимое для заполнения труб системы густой смазки - 10 кг. 9. Месячный расход мази - 20кг при условии
что дробилка будет работать 26 дней в месяц круглосуточно
а мазь будет подаваться к поверхностям трения через каждые 4 часа.
Болт М12х25 ГОСТ 7798-62
Гайка круглая М150х2
Гайка М6 ГОСТ 5916-62
Шайба пружин 12м ГОСТ 6402-61
Шплинт 10х100 ГОСТ 397-54
Шпонка 80х40х355 ГОСТ 8789-58
Винт грузовой М48 ГОСТ 4751-82
Винт М56 ГОСТ 4752-83
Проволока 004 l=3000
ДПДМ2011.815.00.10.00СБ
ДПДМ2011.815.00.10.01
ДПДМ2011.815.00.10.02
ДПДМ2011.815.00.10.03
ДПДМ2011.815.00.10.04
ДПДМ2011.815.00.10.05
ДПДМ2011.815.00.10.06
ДПДМ2011.815.00.10.07
Схема соединения системы смазки со станцией
агрегат дробления1+2.dwg

Диапазон регулирования выходной щели
Максимальный размер дробимого материала
Техническая характеристика
Установочная мощность
*Размеры для справок
Лестницы при виде сзади условно не показаны
Допуск на смещение канавок шкива привода
относительно шкава дробилки не более 1
Технические требования
дробилка щековая.dwg

Допуск радиального биения
шкива дробилки не более 0
торцевого не более 10 мм
подвижных частей дробилки о неподвижные
Не допускается задевание
Регулировки угла наклона распорных
плит поз.22 к горизонтали -8° осуществляется
подбором толщины и количества прокладок поз.30
Разница зазоров Н и К не более 2 мм
обеспечивается подбором числа и толщины
поз.16 под планки поз.15
схема компоновочная.dwg

сортировочная установка
Схема технологическая
Исходная горная масса
Предварительное грохочение
Промежуточное грохочение
Контрольное грохочение
Техническая характеристика
Производительность м ч
Максимальный размер дробимого
Колосниковый грохот и щековая
Промежуточный грохот
Конусная дробилка и контрольный
Транспортерные ленты
механизм регулирования.dwg

Разница в размерах Д не более 5 мм
Винт поз.4 при сборке покрыть
смазкой ПВК ГОСТ 19537-74
ПЗ ок.doc
Проведение патентных исследований и анализ их результатов
Разработка задания на проведения патентных исследований
Разработка регламента поиска информации
Поиск и отбор патентной научно-технической информации
Сущность модернизации
Расчет графика технологической схемы ПДСУ
Расчёты подтверждающие работоспособность и надёжность конструкции
Выбор и расчёт основных параметров дробилки
Расчёт на прочность элементов дробилки
Выбор и расчёт конструктивных элементов дробилки
Расчет и выбор опорных пружин передней щеки
Расчет привода механизма регулирования размера
Технологический расчет
Заготовительная операция
Шлифовальная операция
Безопасность жизнедеятельности
Технико-экономические показатели
В настоящее время для использования местных строительных материалов из месторождений малой мощности на которых нерентабельно создавать стационарные заводы (например при строительстве дорог) успешно применяются дробильно-сортировочные установки (ПДСУ).
ПДСУ называется комплект машин предназначенных для переработки горных пород и выделение готового продукта – щебня и песка. Особенностью ПДСУ является их мобильность.
Отечественная промышленность выпускает ПДСУ малой мощности (до 10тч) средней (до 50 тч) и большой (свыше 50тч) мощности. Комплект ПДСУ состоит из самостоятельных унифицированных агрегатов выполняющих только технологическую операцию. В зависимости от горно-геологических условий и требований к щебню из этих агрегатов используемых в различных сочетаниях можно составлять несколько технологических схем. В агрегатах ПДСУ используют серийно выпускаемые дробилки и грохота которые монтируются на рамках снабженных пневмоколёсным ходом. Привод машин осуществляется от индивидуальных электродвигателей.
В настоящее время наиболее распространена компоновочная схема 2-х стадийного дробления состоящая из агрегатов среднего и мелкого дробления и агрегата сортировки.
На агрегате среднего дробления используется щёковая дробилка используется со сложным движением щеки СМД-108А с приёмных отверстием 250*900мм и предназначена для переработки каменных материалов средней прочности и малоабразивные. В качестве дробилки агрегата мелкого дробления используется конусная дробилка типа КМД с диаметром нижнего основания подвижного конуса 900мм кроме того используются агрегаты промежуточной и окончательной сортировки.
Наряду с несомненными достоинствами данных агрегатов необходимо отметить что агрегат среднего дробления с использованием данной дробилки не является универсальным т.к. его применение ограничено горной породой малой и средней прочности и повышенным расходом дробящих плит. Поэтому чтобы исключить данный недостаток агрегата среднего дробления можно предложить модернизацию щёковой дробилки СДМ-108А которая позволит перерабатывать любые горные породы с гораздо меньшим расходом быстроизнашивающихся частей дробилки – дробящих плит.
Данная модернизация заключается в том что неподвижная щека за счёт конструктивных изменений становится подвижной т.е. дробилка со сложным движением щеки переходит в дробилку с двумя подвижными щеками. Это позволит перерабатывать высокообразивную горную породу прочностью до 350мПа.
Механический процесс разрушения или измельчения кусков каменной породы называется дроблением и производится при помощи дробильных машин — камнедробилок.
Дробление осуществляется методами раздавливания (сжатия) раскалывания и истирания. В дробильных машинах применяют различные сочетания этих способов с учетом физико-механических свойств дробимой породы и крупности дробления. Крупные куски обычно дробят методом сжатия; куоки средней величины а также мелкие — методом удара или сжатия с ударом. Проводятся исследовательские работы по применению для дробления вибрации ультразвуковых колебаний а также взрывного и электрогидравлического эффектов.
Материал поступающий в дробилку называют исходным материалом или продуктом питания. Раздробленный материал выходящий из дробилки называется продуктом дробления или готовым продуктом.
Различают крупное среднее мелкое и тонкое дробление. Крупным дроблением называется измельчение на куски размером 70—300 мм; средним дроблением—на куски 20—70 мм; мелким — на куски 1—20 мм и тонким (помол)—до размеров в долях миллиметра.
Дробление ведется в несколько приемов (стадий) с постепенным уменьшением размеров кусков. Различают дробление одно-стадийное двухстадийное и т. д.
В соответствии с этим дробильные машины условно подразделяют «а дробилки крупного (первичного) дробления среднего (вторичного) и мелкого дробления.
В зависимости от назначения и физико-механических свойств дробильных пород применяемые в строительном производстве дробилки подразделяются на щековые (челюстные) конусные валковые молотковые и роторные (рис. 1.1 а—е). Для тонкого измельчения применяют различного типа мельницы: шаровые стержневые вибрационные и бегуны (рис. 1.1 ж—и).
Рисунок 1.1 - Схемы дробильных машин:
а — щековая дробилка с простым качанием; б — щековая дробилка со сложным качанием; в — конусная дробилка с крутым конусом; г — конусная дробилка с пологим конусом; д — молотковая дробилка с шарнирно закрепленными молотками; е — валковая дробилка; ж — шаровая мельница; з — бегуны; и — вибрационная мельница
Процесс дробления материала в щековых дробилках осуществляется между двумя дробящими плитами прикрепленными к неподвижной и качающейся щекам дробилки. Разрушение дробимого материала происходит при периодическом нажатиигна него качающейся щеки.
Щековые дробилки по принципу действия делят на дробилки с простым сложным и комбинированным движением подвижной щеки. Первые дробят материал в основном методом сжатия и частично за счет изгиба; их применяют главным образом для первичного крупного дробления. Дробилки со сложным движением щеки дробят материал методом сжатия в сочетании с истиранием и скалыванием; их применяют преимущественно для среднего и мелкого дробления.
Первая щековая дробилка была изобретена в начале второй половины прошлого столетия. Принципиальная схема известная под названием двухрычажной дробилки с простым движением щеки применяется при конструировании щековых дробилок и до настоящего времени. Широкое распространение щековых дробилок такого типа объясняется простотой их конструкции и высокой надежностью в работе.
Щековая дробилка с простым движением щеки показана на рис. 1.2. Рабочим органом дробилки являются неподвижная и подвижная дробящие плиты укрепленные соответственно на стенке станины и качающейся щеке которая смонтирована на оси. Дробящие плиты в нижней части имеют криволинейную форму и образуют зону с параллельными поверхностями которая обеспечивает выдачу более равномерного щебня.
Подвижная щека и передняя стенка станины образуют камеру дробления. Расстояние между дробящими плитами в нижней части камеры дробления называется выходной (разгрузочной) щелью; ширина ее регулируется специальным регулирующим механизмом во всех дробилках кроме крупных где этого не требуется по условиям дробления. Качание подвижной щеки осуществляется при помощи шарнирно-рычажного механизма состоящего из эксцентрикового вала 6 шатуна и двух распорных плит. По концам эксцентрикового вала смонтированы маховики один из которых служит ведущим шкивом. Боковые стенки станины дробилки футеруются в рабочей зоне стальными плитами в виде клиньев.
Поддержание элементов системы в положении необходимом для обеспечения заданной кинематики движения всех элементов дробилки обеспечивается тягой и пружиной.
В кинематическую цепь привода дробилки входят две муфты включаемые и выключаемые при помощи гидропривода. Жидкость в муфты подается по трубкам. При попадании в дробилку недробимых предметов происходит проскальзывание муфт и детали дробилки таким образом предохраняются от поломки. Кроме того фрикционные муфты дают возможность пускать дробилку с поочередным включением движущихся масс — шкива подвижной щеки и маховика.
В дробилках предусмотрена жидкая циркуляционная смазка для коренных подшипников главного вала и шатуна.
При холостом ходе щеки часть энергии расходуется на преодоление вредных сопротивлений а избыточная часть поглощается маховиками т. е. превращается в кинетическую энергию. При рабочем ходе маховики отдают эту накопленную энергию помогая двигателю преодолевать сопротивление камня дроблению.
Экспериментальные исследования показали что разрушение камня в щековой дробилке происходит главным образом в результате растягивающих напряжений возникающих при действии на камень двух сосредоточенных нагрузок.
Рисунок 1.2 - Щековая дробилка с простым движением щеки
Рисунок 1.3 - Щековая дробилка со сложным движением щеки
Щековая дробилка с однорычажным механизмом и сложным движением щеки показана на рис. 1.3. Дробилка состоит из станины эксцентрикового вала с клиноременным шкивом маховика подвижной щеки; неподвижной щеки распорной плиты боковых клиньев узла регулирования ширины разгрузочной щели 9 и тяги с оттяжной пружиной. Подвижная щека совершает сложные движения относительно оси подвеса. При этом каждая точка щеки описывает траекторию по овалу; в верхней части щеки эти овалы по форме приближаются к окружности а в нижней они имеют форму сильно вытянутых эллипсов. Такое движение щеки ускоряет продвижение материала вниз в сторону разгрузки и тем самым способствует повышению производительности дробилки на 20—30% по сравнению с дробилками с простым движением.
Основные параметры щековых дробилок — ширина и длина загрузочного отверстия. Первый из них ограничивает наибольший размер загружаемого камня (он не должен превышать 09 ширины отверстия) второй в значительной мере определяет производительность дробилки.
Дробящие плиты изготовляют из износоустойчивого материала — литой марганцовистой стали с содержанием марганца до 10—16%. Рабочая поверхность дробящих плит имеет вертикальное рифление; противолежащие плиты расположены в дробилке так чтобы выступы рифления одной плиты приходились против впадин другой. Благодаря этому разрушение камня происходит в значительной мере под действием изгиба которому горные породы сопротивляются слабо. В поперечном сечении рифли имеют вид треугольника со скругленной вершиной.
Дробящие плиты обычно симметричны относительно гори-зойтальной оси; это позволяет переставлять плиту нижней более быстро изнашивающейся частью вверх. Изношенные дробящие плиты восстанавливают наплавкой твердыми сплавами.
Тяга с оттяжной пружиной обеспечивает требуемый для открытия разгрузочного отверстия отход подвижной щеки и вместе с тем стягивает всю систему шарниров подвижной щеки и распорных плит с регулировочным механизмом и задней стенкой предотвращая выпадение распорной плиты.
Главный вал преобразует вращательное движение в качание шатуна (у дробилок с простым качанием) или подвижной щеки (у дробилок со сложным качанием). Вал испытывает значительные ударные нагрузки; он выполняется из легированной стали (обычно хромоникелевой) и подвергается термической обработке.
Станины дробилок выполняют цельными (стального или чугунного литья) сборными на болтах или сварными.
Шарнирно-рычажный механизм положенный в основу конструкции щековых дробилок чрезвычайно выгоден в механическом отношении так как дает возможность получить огромные раздавливающие силы (в крупных дробилках свыше 1000 тс) превосходящие во много раз окружные усилия на главном валу дробилки.
Дробилки с простым движением щеки имеют небольшую вертикальную составляющую хода сжатия поэтому дробящие плиты у них служат в 4—5 раз дольше чем у дробилок со сложным движением где величина этого хода значительно больше. В этом заключается преимущество кинематической схемы дробилок с простым движением щеки. Другим достоинством этих дробилок является обеспечение большого выигрыша в силе верхней части зева что очень важно при дроблении кусков горной массы больших размеров и высокой прочности.
Недостатком такого типа дробилок является малая величина хода сжатия в верхней части загрузочного отверстия между тем как ход сжатия должен быть тем больше чем крупнее кусок дробимого материала. В дробилках с простым движением щеки усилие действующее по распорным плитам примерно в 15 раз больше чем усилие по шатуну вследствие чего создаются невыгодные условия надежного захвата и дробления материала в верхней части загрузочного отверстия.
Дробилки со сложным движением щеки конструктивно проще дробилок с простым движением щеки; кроме того они имеют меньшие габариты и менее металлоемки. Однако вследствие большой вертикальной составляющей хода в нижней части зева этих дробилок происходит интенсивное истирание камня что при дроблении прочного и абразивного материала приводит к более интенсивному износу дробящих плит.
2 Тенденции модернизации щековых дробилок
За последнее время появились различные конструкции дробилок с двумя; подвижными щеками каждая из которых имеет сложное движение. Эти дробилки сочетают преимущества обычных дробилок со сложным движением щеки—компактность и высокую производительность — с основным достоинством дробилок с простым движением — малой степенью износа дробящих плит. Удельная производительность их выше чем у обычных дробилок со сложным движением щеки а металлоемкость ниже.
Ведутся также значительные работы по модернизации щековых дробилок.
Эти усовершенствования предусматривают увеличение глубины камеры дробления замену прямолинейных дробящих плит плитами криволинейными с безболтовым их креплением регулирование и поддержание в заданных пределах разгрузочной щели применение на главном эксцентриковом валу подшипников качения вместо подшипников скольжения увеличение числа качаний щеки и повышение жесткости станин а также усовершенствование .привода дробилок.
Степень измельчения у щековых дробилок с шарнирно-рычажным механизмом движения подвижной щеки находится в пределах от 4 : 1 до 7: 1. Соотношение между шириной и длиной загрузочного отверстия равно примерно 16:1. Относительный износ дробящих плит по весу ориентировочно составляет 50— 100 г на 1 т продукта дробления. Удельную производительность современных щековых дробилок можно приближенно принимать в пределах 15—22 мгч на 1 г веса машины и удельный расход мощности — 033—11 кет (045—15 л. с.) на 1 м3 часовой производительности при дроблении первичными дробилками мятких пород и 075—185 кет (1—25 л. с.) на 1 м3ч при дроблении твердых пород.
Производительность и мощность двигателей щековых дробилок. Оптимальная работа щековых дробилок зависит от ряда конструктивных параметров к числу которых относятся угол захвата (угол между дробящими плитами) геометрическая форма загрузочного отверстия дробилки величина хода подвижной щеки.
Процесс дробления будет протекать нормально при условии что дробимый камень при нажатии на него щек дробилки не выталкивается из камеры дробления. Это зависит от величины угла захвата а.
Выбор типоразмера дробилки определяется по требуемой производительности и максимальному размеру загружаемых кусков материала подлежащих дроблению.
Потребная мощность двигателя дробилки зависит от физико-механических свойств дробимого материала и его объема формы размеров кусков и степени измельчения а также формы величины и степени изношенности рифлей дробящих плит.
Основными направлениями использования патентной информации является:
- увеличение глубины камеры дробления;
замену прямолинейных дробящих плит плитами криволинейными с безболтовым их креплением;
регулирование и поддержание в заданных пределах разгрузочной щели.
проверка патентной чистоты данных разработок и возможности их патентования за границей.
Поиск проводится по фондам патентной научно-технической и другой литературы.
Общие сведения об объектах исследования
Исполнитель: Сазонов И.А.
Объект Щековая дробилка
Назначение область применения краткое описание объекта исследования: механический процесс разрушения или измельчения кусков каменной породы – дробление производится при помощи дробильных машин — камнедробилок. Относятся к строительно-дорожным машинам.
Дробильные машины условно подразделяют на дробилки крупного (первичного) дробления среднего (вторичного) и мелкого дробления.
В зависимости от назначения и физико-механических свойств дробильных пород применяемые в строительном производстве дробилки подразделяются на щековые (челюстные) конусные валковые молотковые и роторные. Для тонкого измельчения применяют различного типа мельницы: шаровые стержневые вибрационные и бегуны.
1 Разработка задания на проведения патентных исследований
Утверждаю зав. кафедрой ПТ и ДМ
Наименование организации АДИ
(расшифровка подписи)
------------ Герасимов М.Д.
Задание № 1 на проведение патентных исследований
Наименование темы: Модернизация щековой дробилки
Задачи патентных исследований Поиск технических решении с целью модернизации щековой дробилки с целью снижения степени износа дробящих плит
Исполнители работ: Сазонов И.В.
Подразделения - Исполнители соискатели)
Краткое содержание работ
Ответственный исполнитель
описаний изобретений или
Пояснительная записка
Руководитель подразделения - исполнителя
Исполнитель патентного поиска
2 Разработка регламента поиска информации
Для определения предмета поиска при проведении патентных исследований сушильной установки первоначально был просмотрен официальный бюллетень изобретений (ОБИ) «Открытые изобретения промышленные образцы и товарные знаки» за 10 лет. В результате просмотра была определена область поиска охватывающего как вопросы повышения эффективности так и модернизации конструкции узлов и агрегатов.
Изучение указанных источников информации позволило определить следующие ключевые слова и словосочетания которые легли в основу определения предмета поиска: сушильная установка инертные материалы устройство для сушки.
Шифр темы: ДПДМ2011.815.00.00.00 ПЗ
Начало поиска 03. 2011 Окончание поиска 06.2011
(тема объект его составные части)
информации (для решения поиска
технических проблем или обеспечения каких
Классификационные индексы (УДК МКИ НКИ МКПО)
Ретроспективность поиска
Наименование источников информации по которым производится поиск
Способы и устройства разгрузки ЖД вагонов
Рзрботка способа устройстваразгрузки ЖД вагоов с целью повышения мобильности снижения стоимости
свидетельствам или патентам
3 Поиск и отбор патентной научно-технической информации
Для поиска патентной информации мы используем иформационно-поисковую систему (ИПС). В ИПС возможен поиск по изобретениям рефератам патентных документов на русском и английском языках перспективным изобретениям полезным моделям товарным знакам общеизвестным товарным знакам наименованиям мест происхождения товаров заявкам на российские товарные знаки международным товарным знакам с указанием России промышленным образцам классификаторам и документам из последних бюллетеней. В БД возможен поиск по текстовым полям по номерам и по датам с использованием масок подстановок интервалов и т.д.
Открытые реестры представляют собой структурированный список документов по номеру регистрации или заявки по определенному объекту промышленной собственности. Пользователям предоставляется доступ к информации о регистрациях с указанием правового статуса или стадии делопроизводства по заявкам.
На портале открыты реестры российских товарных знаков и знаков обслуживания российских изобретений наименований мест происхождения товара общеизвестных в России товарных знаков российских полезных моделей и промышленных образцов международных товарных знаков с указанием России также доступны открытые реестры по заявкам на российские товарные знаки и знаки обслуживания и изобретения.
Электронные бюллетени являются цифровым аналогом бумажного носителя. На портале размещены электронные бюллетени «Изобретения и полезные модели» «Товарные знаки знаки обслуживания и наименования мест происхождения товаров» и «Промышленные образцы» за последний месяц а также бюллетень «Программы для ЭВМ Базы данных Топологии интегральных микросхем».
Задание на проведение патентных исследований (номер дата) Задание № 1__
Дата и номер регламента поиска Регламент поиска № 1 от
Предмет поиска (объект его составные элементы)
Классификационный индекс
По фонду какой организации проводится поиск
Источники информации
Щековая дробилка дробящие плиты
СССР Россия и страны СНГ
Патентный отдел государственной универсальной научной библиотеки
Научно-техническая документация наименование дата опубликования выходные данные с указанием предметов просмотра (от и до)
Патентная документация наименование патентного бюллетеня журналов охранных документов номера и дата их публикации с указанием предела просмотра (от и до)
Таблица 3.1 – Патентная документация отобранная для последующего анализа
Страна вид и номер охранного документа классификационный индекс
Заявитель с указанием страны номер заявки дата приоритета конвекционный приоритет
Сущность заявленного технического
решения и цели его создания (формула
Сведения о действии охранного документа
Рабочее оборудование сушильной установки
Заявка: 200312177803 15.07.2003
Дробилка щековая непрерывного действия содержит станину состоящую из передней задней двух боковых стенок и основания неподвижную и подвижную щеки распорные плиты при этом она дополнительно снабжена вторыми неподвижной и подвижной щеками направляющими роликами закрепленными на боковых стенках станины и ползуном совершающим возвратно-поступательное движение по вертикали установленным в направляющих роликах при этом неподвижные щеки шарнирно сочленены соответственно с передней и с задней стенкой станины а подвижные щеки выполнены из двух частей нижней опирающейся на основание станины и верхней части опирающейся на нижнюю часть щеки причем каждая из частей подвижных щек шарнирно соединена с ползуном при этом распорные плиты верхних частей подвижных щек установлены в положении крайних точек холостого хода а в нижних частях - в положении крайних точек рабочего хода нижних частей подвижных щек.
Статус: по данным на 27.05.2011 - действует
Заявка: 200312177903 15.07.2003
Гамоля Ю.А. Соколов В.Б. Красовский П.С.
Изобретение предназначено для дробления высокопрочных пород камня на предприятиях карьерного хозяйства. Щековая дробилка непрерывного действия с простым качанием щеки содержит станину со стенками подвижную щеку подвешенную на оси эксцентриковый вал со шкивом-маховиком электродвигатель и шатун подвешенный на эксцентриковом валу и шарнирно сочлененный с помощью распорных плит с подвижной щекой и стенкой станины при этом она дополнительно снабжена второй подвижной щекой подвешенной на оси и вторым шатуном установленным вместе с первым на одном и том же эксцентриковом валу так что концы шатунов обращены в диаметрально противоположные стороны а станина выполнена двухъярусной причем вторая подвижная щека установлена на втором ярусе станины а конец второго шатуна соединен с помощью распорных плит со второй подвижной щекой и стенкой станины. Изобретение позволяет обеспечить работу дробилки в непрерывном режиме и сократить энергоемкость процесса дробления.
Заявка: 200711935603 24.05.2007
Изобретение может быть использовано в горнорудной и строительной промышленности для дробления исходного материала. Дробилка содержит станину маховик подвижную и неподвижную дробящие щеки ось шарнирного подвеса подвижной щеки опирающуюся подшипниками на боковые стенки станины эксцентриковый привод шатун клиноременную передачу детали крепления шатуна к подвижной щеке и шатуну. Подвижная щека имеет точку подвеса в нижней половине станины на высоте равной 13 ее полной длины у точки подвеса обе щеки имеют изгиб по отношению к центральным осям щек направленный в сторону установки неподвижной щеки так что в процессе движения подвижной щеки создаются верхняя и нижняя камеры дробления в которых дробление материала происходит попеременно: то в верхней камере - крупное дробление то в нижней камере - мелкое дробление исключая холостой ход. Изобретение увеличивает степень дробления и снижает расход электроэнергии
Статус: по данным на 27.05.2011 - прекратил действие но может быть восстановлен
Заявка: 200811773803 04.05.2008
Изобретение относится к дробильному оборудованию а именно к щековым дробилкам и может быть использовано при дроблении различных горных пород - руд и нерудных минералов в том числе со слоистой структурой при циклично-поточной технологии обработки месторождений открытым способом и в подземных условиях. Щековая дробилка содержит станину неподвижную и подвижную щеки с выполнением подвижной щеки ступенчатой формы угол захвата верхней ступени камеры дробления принят меньшим допустимой величины. Нижерасположенные ступени размещены со смещением их верхних кромок в сторону противоположную от неподвижной щеки с углами захвата не превышающими допустимую величину а геометрические параметры камеры дробления определяются следующими соотношениями
где h - высота переходного участка между смежными ступенями Н - высота ступени а - минимальное расстояние между нижними кромками ступеней и неподвижной щекой при этом угол наклона к горизонту переходного участка между смежными ступенями принят равным углу захвата упомянутых выше ступеней. Изобретение позволяет увеличить пропускную способность щековой дробилки при гарантированном дроблении и прохождении горной породы в том числе со слоистой структурой в камере дробления без увеличения высоты дробилки.
4 Сущность модернизации
На рис. 2.1 показана конструктивная схема дробилки вид сбоку в разрезе
Рисунок 2.1 - Конструктивная схема дробилки
В корпусе 1 предложенной дробилки смонтирована передняя дробящая щека 2 с дробящей плитой 3 и задняя дробящая щека 4 с дробящей плитой 5 верхняя часть которой установлена на приводном эксцентриковом валу 6 а нижняя часть опирается на наклонную распорную плиту 7. Передняя щека 2 опирается на горизонтально установленные распорные плиты 8 выполняющие функцию направляющих вертикальных перемещений этой щеки причём в этой функции могут быть применены тела качения.
Силовое замыкание кинематических звеньев осуществляется узлами 9 называемыми замыкающими устройствами состоящие из тяг и пружин. По средствам упругих элементов 10 щека 2 подпружинена относительно корпуса в вертикальном направлении.
В процессе работы дробилки при вращении эксцентрикового вала загружаемый материал дробится между щеками 2 и 4. Горизонтальная составляющая хода щеки 4 по соответствующим фазам реализуется в раздавливании кусков материала вверху и внизу и воспринимается распорными плитами как усилие сжатия а вертикальная составляющая приводит щеку 2 через дробимый материал (силами трения) в колебание синхронным колебанием щеки 4. В результате такого воздействия щёк существенно уменьшается истирание дробящих плит дробильным материалом что обеспечивает повышение экономичности в эксплуатации
Технологические процессы изображаются в виде качественной количественной схем и цепи аппаратов. Качественная схема содержит данные о размерах фракций качестве материалов режиме переработки на участках процесса; количественная – показывает количество перерабатываемого материала (объём массу процент) на определённых участках процесса: цепь аппаратов показывает путь следования материала данные об оборудовании. Часто схемы совмещают в один график технологической схемы.
Исходные данные для расчёта:
Производительность установки -22 м3ч;
Максимальный размер куска Dma
Готовый продукт – щебень: 5-10 10-20 20-40мм; песок: 0-5мм.
Дробилка первичного дробления выбирается по размеру загружаемого камня Dmax и производительности П. Предварительно корректируется заданная производительность.
Ширина приёмного отверстия:
В= Dmax 085= 210085=247мм
Где Кн -коэффициент неравномерного питания
Прасч.= 22*115=253м3ч
Узнаем предположительные паспортные данные дробилки по формуле:
Прасч = Ппасп.* Кдр *Кб* Кф* Ккр
Прасч - паспортная производительность дробилки;
Ппасп - расчётная производительность дробилки;
Кдр - поправочный коэффициент на дробимость материала(для особо прочных материалов =300мПа; Кдр =065)
Кб - поправочный коэффициент учитывающий насыпную плотность дробимого материала =17;
Кф - Поправочный коэффициент учитывающий форму дробильного материала Кф =1
Ккр - поправочный коэффициент на крупность материала
d= 0.5B=0.5*247=123.5мм
d Dmax =13.5210=0.588=>Ккр =1.03
По рассчитанному паспортному значению выбираем дробилку щёковую со сложным качением щеки СДМ-108А. П=16 28; в=30 50мм
Ширину разгрузочной щеки при которой будет достигнута заданная производительность можно определить по формуле:
- минимальная ширина разгрузочной щеки =30мм
- максимальная ширина разгрузочной щеки =50мм
- производительность дробилки при ; =16
- производительность при ; =28;
- проектируемая паспортная производительность; =222
Определяем количество материала с размером до Dmax =40мм
крупность в долях ширины разгрузочной щеки
По рис.7[12] Находим суммарный выход кусков с размером 40мм что составляет 40%. Значит суммарный выход (содержание) готового продукта 0-40мм
Размер максимального куска дробления определяется по тому же графику
Где - значение крупности в долях ширины разгрузочной щели соответствующее нулевому содержанию продуктов дробления т.е. точка пересечения кривой 1 с абсциссой
Дробилка вторичного дробления рассчитывается аналогично только при этом крупность максимального куска первичного дробления принимается за исходный размер т.е. и производительность вторичной дробилки рассчитывается с учётом выделения продукта с размером до dmax
Настраиваем дробилку на размер разгрузочной щели соответствующий минимальной производительности
По рис. 10 ( ) находим max размер готового продукта где
dmaxII = 15*2.6=39мм
Таким образом организовываем открытый цикл т.е. размер готового продукта не превышает заданного 40мм. По аналогии с рис.2 ( ) строим график технологической схемы двухстороннего дробления ПСДУ. Далее производим расчёт данной схемы. Расчёт схемы производим по стадиям дробления. В первую стадию дробления входит продукт 1 а выходят продукты 4 и 7.
Естественно что каждая операция должна сбалансироваться по выходам отдельных компонентов в весовых единицах т.е.
Расчёт первой стадии дробления.
Определение выходов продуктов 2 3 4
где - содержание класса в исходном материале принимается по характеристике крупности исходной горной массы рис.
- общая эффективность операции грохочения
где - содержание класса в исходном материале принимается по характеристике крупности исходной горной массы
- общая эффективность второй операции грохочения
Расчёт второй стадии дробления
Определение выходов 8 9 10 11
Где - содержание класса в продукте 7 определяемое из выражения:
где - содержание класса (5-40) в исходном материале
- содержание класса -40 в продукте 6
Расчёт операции сортировки
Расчёт начинается с определения выходов 15; 16; 17; 18
Располагая данными о гранулометрическом составе продукта 10 который будет равен:
-5мм 515=033 100-95=5%
-10мм 1015=066 95-83=12%
-20мм 2015=13 83-42=41%
-40мм 4015=26 100-58=42%
Находим выходы готовых продуктов
Расчётная производительность вибрационных грохотов определяется
Поскольку расчётная производительность грохотов определяется расчётом соответствующих выходов то задачей расчёта является определение площади просеивающей поверхности сит:
с – коэффициент использования рабочей поверхности сита с=1 при загрузке по всей ширине;
q–удельная производительность на 1поверхности сита по табл. 7 (12)
q = 38 для отверстия L=40мм
q = 28 для отверстия L=20мм
q = 19 для отверстия L=10мм
q = 11 для отверстия L=5мм
rem – поправочные коэффициенты определяются по табл.8(12) в зависимости от эффективности
n - коэффициент характеризующий форму заполнителя n=1 для щебня;
p – значение этого коэффициента учитывающего характеристику материала и размер отверстия сита определяется по табл. 9(12);
o – данный коэффициент учитывающий вид грохочения (сухой или с орошением)и размер отверстия сита определяется по табл. 10 (12) о =1
По расчётным площадям просеивающих поверхностей подбираются соответствующие грохоты.
1 Расчёты подтверждающие работоспособность и надёжность конструкции
1.1 Выбор и расчёт основных параметров дробилки
Производительность - 22
Наибольший размер куска дробильного материала -210
Ширина выходной щеки мм - 40
Предел прочности дробильного материала при сжатии мПа - 300
Модуль прочности дробильного материала мПа - 46000
Определить основные параметры щёковой дробилки со сложным качением щеки
угол захвата «» между дробящими щеками;
наивыгоднейшую частоту вращения эксцентрикового вала «П» обс;
мощность привода дробилки N. кВт
наибольшее усилие дробления Q Н
Определение ширины загрузочного отверстия.
Ширина загрузочного отверстия В мм определяется по формуле:
где: - максимальный размер кусков исходного продукта мм
Размеры приёмного отверстия регламентированы Государственным стандартом поэтому принимаем
Определение угла захвата
От образованного рабочими поверхностями дробящих щёк зависит будет ли кусок дробимого материала втягиваться в дробилку или выталкиваться из неё.
Согласно рекомендациям [1] для надёжной работы дробилки принимаем угол захвата α=20.
Наивыгоднейшая частота вращения эксцентрикового вала
Она определяется из условий свободной выгрузки материала под действием силы тяжести. Определяется она по формуле:
Где: - угол захвата градусы;
По рекомендациям ВНИИ СДМ ход щеки (мм) может быть определён из выражения:
Где: d –наибольшая ширина выходной щеки мм
Тогда: S=7+01*40= 11мм
Определение длины загрузочной щеки
Длина загрузочной щеки L определяется из формулы производительности дробилки:
n – частота вращения эксцентрикового вала обс
L – длина загрузочной щели м
- коэффициент разрыхления дробимого материала [1]
- средний размер продукта дробления м
Средний размер продукта дробления определяется по формуле:
L – минимальный размер выходной щели м
Из формулы (34) для определения производительности выведем формулу для определения длины загрузочной щели
Размеры приёмных отверстий регламентированы Государственным стандартом поэтому принимаем L=0.9м=900мм
Определение мощности привода
Мощность привода дробилки N(квт) определяется по формуле:
- предел прочности дробимого материала Па;
- длина загрузочной щели м;
- частота вращения эксцентрического вала обс;
- модуль упругости дробимого материала Па;
- размер исходного материала м;
- размер готового продукта м
Определённая по данной формуле мощность даёт завышенный результат на 35-40% поэтому для инженерных расчётов её необходимо корректировать т.е. умножить на коэффициент 065 06. Тогда получим: N=89*060=534
Ближайший электродвигатель который подходит по мощности: электродвигатель 4А250М6У3 ГОСТ 19523-81. Мощность данного электродвигателя Ng=55кВт n=1000 обс.
Коэффициент скольжения S=1.3%
Определение максимального усилия дробления
Максимальное усилие дробления определяем по формуле:
- предел прочности дробимого материала на сжатие Па;
- ход подвижной щеки в месте приложения дробящего усилия м;
- размеры исходного и готового продукта м;
Ход подвижной щеки в месте приложения дробящего усилия определяем графически
Рисунок 3.2 - Схема для определения хода щеки в месте приложения Q
Учитывая возможность перегрузки дробилки при попадании недробимого материала рекомендуется принимать усилие дробления:
Определяем усилие в распорной плите сжимающие усилие действующее вдоль распорной плиты определяется по формуле: рис. 3.3.
Рисунок 3.3 - Схема для определения усилий в деталях щековой дробилки
- усилие дробления кН
- плечи действия сил (рис. 3.3.) определяется графически
1.2 Расчёт на прочность элементов дробилки
Расчёт на прочность распорных плит передней щеки
Задача расчёта: определить толщину распорных плит передней щеки дробилки.
Рисунок 3.4 - Расчётная схема для определения усилий в распорных плитах.
Ширина распорной плиты
Материал С418-36[]=931*Па
Условия расчёта: на дробящую плиту действует усилие дробления приложенное на расстояние 13L от верха камеры дробления
- плечо действия силы мм
- усилие в нижней распорной плите кН
Где - усилие в верхней распорной плите кН
Конструктивно распорные плиты должны быть одинаковыми поэтому дальнейший расчёт ведём по большому усилию им является усилие =1441кН
Напряжение сжатия в распорной плите определяется по формуле:
- направление сжатия в распорной плите Па
Т – усилие в распорной плите Н
F – площадь поперечного сечения распорной плиты
Площадь поперечного сечения распорной плиты определяется по формуле:
a - толщина распорной плиты м
b - ширина распорной плиты м
Расчёт на прочность ведётся из условия:
Где -допускаемое напряжение Па
Расчёт на прочность передней дробящей щеки
Задача расчёта: проверка сечения дробящей щеки на прочность в зоне действия дробящего усилия .
Материал –сталь 30ГЛ; =16*
L=650мм; =1441кН; =7205кН
Рисунок 3.5 - Расчётная схема для расчёта дробящей щеки на прочность
Щёку рассчитываем как балку опирающуюся на распорные плиты. При этом в щеке возникает напряжение изгиба.
Условия прочности на изгиб
- номинальное напряжение изгиба Па
- допускаемое напряжение изгиба Па
Номинальное напряжение изгиба возникающее в дробящей щеке определяем по формуле:
м - изгибающий момент
W - момент сопротивления сечения щеки
Изгибающий момент определяем по рис. 3.5.
- нормальная составляющая усилия в распорной плите кН;
L – плечо действия силы
Нормальную составляющую усилия в распорной плите определяет как
- усилие в распорной плите кН
- угол наклона распорной плиты
Момент сопротивления сечения щеки:
- момент инерции сечения
n - толщина сечения м
y - координаты центра тяжести сечения м
Координаты центра тяжести:
Рисунок 3.6 - Сечение а-а передней щеки
Момент инерции сечения а-а
Тогда момент сопротивления сечения а-а
Отсюда напряжение от изгиба в сечении а-а
Сравним с допустимы.
Следовательно данное сечение в месте приложения подходит по условию прочности на изгиб.
Проверка на прочность передней балки станины и боковой станины.
Исходные данные: Материал:
Рисунок 3.7 - Расчётная схема станины
Сварную станину рассчитывают как жёсткую раму.
Передняя стенка состоит из двух балок. Большее усиление приходится на верхнюю балку поэтому её и рассчитывают на прочность.
Рисунок 3.8 - Расчётная схема передней балки станины
На концах балки АВ действуют моменты которые препятствуют свободному повороту этих концов и заменяют действие боковых стенок на переднюю. направление действия момента показано на рис. 3.7.
Значение определяем по формуле:
Q – усилие действующее на балку кН
- расстояние между осями инерции передней и задней балки
- моменты инерции сечений боковых стенок и передней балки
Моменты инерции сечения балки равен:
Рисунок 3.9 - Сечение боковой станины
Момент операции сечения боковой станины:
Момент изгибающий переднюю стенку
Q - усилие действующее на балку
- момент заменяющий действие боковых стенок на балку нм
Наибольшее напряжение от передней балки
М – момент изгибающий переднюю стенку нм
х – координата центра тяжести сечения балки
J – момент инерции сечения балки М; х=015м (рис.3.7)
Где - допускаемое напряжение на изгиб Па
Данное сечение передней балки подходит по условию прочности.
Боковые станины подвергаются напряжению изгиба и растяжения
- изгибающий момент нм
- координата центра тяжести сечения м
- момент инерции сечения боковой станины
- усилие дробления н
F - площадь поперченного сечения
Площадь поперченного сечения
Допускаемое напряжение: т.е. данное сечение боковой станины подходит по условию прочности.
2 Выбор и расчёт конструктивных элементов дробилки
2.1 Расчёт и выбор опорных пружин передней щеки
Задача расчёта: выбрать опорные пружины передней щеки.
рабочий ход – h мм – 38мм;
сила тяжести передней щеки Р кН 20;
число пружин n –5шт.
Определим усилие приходящее на одну пружину
Р –сила тяжести щеки кН
По формуле (3.33) определяем силу пружины при максимальной деформации:
- рабочее усилие в пружине кН
- относительный инерционный зазор пружины сжатия=(005 025)
В заданном интервале по ГОСТ 13772-68 имеются следующие пружины
Из соображения габаритов выбираем пружину №185
d =15мм – диаметр проволоки
D =80мм – наружный диаметр пружины
-жёсткость одного витка
- наибольший прогиб донного витка
Определяем жёсткость пружины
Число рабочих витков пружины
- жесткость одного витка нмм
- жёсткость пружины нмм
При полутора нерабочих витках
Шаг пружины определяется по формуле:
- наибольший прогиб одного витка мм
- диаметр проволоки мм
Длина пружины в свободном состоянии
Высота пружины при рабочей деформации
- рабочий ход пружины мм
Определяем диаметр гильзы
Где: диаметр пружины мм
3. Расчёт привода механизма регулирования размера выходной щеки.
Рисунок 3.10 - Схема механизма регулирования выходной щели
Электродвигатель; 2. редуктор; 3. винт; 4. клин со встроенной гайкой; 5. сухарь; 6. рукоятка .
Данную дробилку оборудуем вспомогательным прибором для дистанционного управления механизмом регулирования выходной щели.
Клиновой механизм регулирования выходной щели (3.10) состоит из: сухаря 5 в который упирается распорная плита и клиньев 4 со встроенными гайками.
При вращении винта 3 имеющего на сопрягаемых с клиньями участков левую и правую резьбу клинья могут сближаться выжимая сухарь влево или расходится давая возможность отодвигаться ему вправо и таким образом изменять размер выходной щели.
Вращение винта может производится вручную специальной рукояткой 6 или дистанционно с помощью двигателя 1 и редуктора 2. В этом случае имеется возможность дистанционно управлять выпусков недробимых предметов из камеры дробления максимально разводя клинья 4 и соответственно увеличивая ширину разгрузочной щели.
резьба трапециидальная
- внутренний диаметр
Усилие со стороны распорной плиты
Крутящий момент на конце винта равен моменту в резьбе . Для вычисления момента в резьбе определяем угол её подъёма:
- средний диаметр резьбы
И проведённый угол трения
-приведённый коэффициент трения
При этом момент резьбе
- осевое усилие на винте. Это усилие будет равно силам трения клиньев о опорные поверхности (см. рис.3.10)
- коэффициент трения скольжения стали по стали при периодической смазке
Определим мощность движения механизма регулирования размера выходной щели:
- крутящий момент нм;
- угловая скорость винта родс
принимаем 785 радс (nв = 75обмин)
По таблице П1 [11] по требуемой мощности 2456кВт выбираем электродвигатель трёхфазный с синхронной частотой вращения 1500 обмин 4А100S4 УЗ с параметрами: N=3кВт; n=1500обмин; скольжение – 44%
Номинальная частота вращения
По таблице П2[11]диаметр выходного конца вала ротора
Определим передаточное отношение
По мощности и передаточному отношению выбираем червячный редуктор 24-80-20-51-1-2-УЗ с передаточным числом 20=Ир.
Так как Ир – несколько отличается от расчётного необходимо уточнить частоту вращения винта
Для соединения двигателя с редуктором и редуктора с винтом выбираем муфты МУВП (муфты упругие втулочно-кольцевые) по ГОСТу 21424-75 с расточками полумуфты под :
Проверка прочности шпоночных соединений
Для соединения полумуфт с валами принимаем шпонки призматические со скрученными торцами.
Размеры сечений шпонок и пазов и длины по ГОСТу 23360-78
Материал шпонок - сталь 45 нормализованная.
Напряжение смятия и условия прочности по формуле [11]
М - крутящий момент нм;
d – диаметр вала в месте установки шпонки мм;
h – высота шпонки мм;
в – ширина шпонки мм;
L – длина шпонки мм;
- глубина паза вала мм
- допускаемое напряжение смятия мПа
Для валов и выбираем шпонку в*h*L=8*7*50мм
Для валов выбираем шпонку
Технологический расчёт
1 Заготовительная операция
Для проведения кузнечных работ отрезаем заготовку длиной L-125мм. Длину L-125мм получаем из расчета что нам нужно получить на обработку на d=250мм.
Назначаем припуска на обработку t=5мм.
Расчет длины заготовки.
При ковке объем металла сохраняется постоянным поэтому назначаем размеры заготовки с необходимыми припусками а затем подсчитываем заготовку какой длины нужно отрезать от круглого проката d=254мм.
Объём металла после ковки;
Отсюда находим длину заготовки:
Для отрезания заготовки выбираем ножовочный станок 8б72 с мощностью электропривода 15квт.
Выбираем подачу (таблица 29 [3])
Скорость находим по формуле:
Где: п=75обмин- частота вращения шпинделя (инструмента)(табл.30[3])
Основное время резания:
Вспомогательное время :
Дополнительное время;
2 Кузнечная операция
После отрезки заготовку подвергаем ковке на пневматическом ковочном молоте ГОСТ712-82 с массой падающей части 05т.
А1. предварительно нагретую заготовку до Ткр=04*Тпл=480 С устанавливаем на молот и осаживаем с L=125мм до L=120мм при этом диаметр d-260мм раздаётся до d-265мм.
Б. снимаем заготовку с молота.
В. Устанавливаем на молот оправку затем устанавливаем заготовку.
Прошивкой d=60мм прошиваем в заготовке отверстие d=60мм.
Г. Снимаем заготовку с молота.
После ковки заготовку медленно охлаждаем на воздухе. Для перемещения заготовки нужно пользоваться кузнечными щипцами.
Для токарной операции используют токарно-винторезный станок 16К20.
А.3.1. Торцуем заготовку в размер L=118мм. Толщина срезаемого слоя t=2мм. Резец проходной Т15К6. Стойкость резцаТ=90мм.(4)
Режимы резания принимаем из стр. 29. [3]
Скорость резания: =1746ммин
Частота вращения шпинделя:
Где D=255мм – диаметр обрабатываемой детали (табл. 29 [3]).
Где: S-подача при чистовом проходе. Вспомогательное время:
Время дополнительное:
А. 3.2. Расточить с ø60 на ø63 за один проход на длине L=118мм. Толщина срезаемого слоя на сторону t=15мм. Резец расточной для сквозных отверстий ГОСТ 18062-72 (табл. 15 стр. 124 [4]). Т=90мин.
Режим резания принимаем по таблице 29[3]
Время резания: (табл.29 [3])
Где: S=036 –подача продольная мм.
Вспомогательное время:
Дополнительное время:
А.3.3. Расточить с ø63 на ø65 за один проход на длине L=118мм. Толщина срезаемого слоя на сторону t=1мм. Резец расточной. Режимы резания принимаем по табл. 29 [3].
Скорость вращения (табл. 5 [3])
Где: S=35мм-подача продольная.
А. 3.4. Расточить с ø255 на ø110 за 8 проходов начерно при глубине резания 4мм на длину L=32мм. Резец расточной ГОСТ 18883-73 (табл.4 стр. 123). Режимы резания принимаем по табл. 29 [3]. Скорость резания =70ммин
Продольная подача: S=05ммоб
А. 3.5.Проточить с ø 180 на ø110 за 3 прохода начерно с глубиной резания 4мм на длину L=12мм.
Резец расточной ГОСТ 18883-73 (табл.14 стр. 123[4]). Режимы резания принимаем по табл. 29 [3]. Скорость резания =70ммин
Поперечная подача: S=05ммоб
А. 3.6. Расточить с ø 180 на ø110 за 1 чистовой проход с глубиной резания 2мм на длину L=2мм.
Резец расточной ГОСТ 18883-73. Режим резания принимаем по табл. 29 [3].
Скорость резания =1746ммин
Поперечная подача: S=041ммоб
А. 3.8. Расточить с ø 110 на ø106 за 1 чистовой проход с глубиной резания на одну сторону t=2мм на длину L=48мм.
Резец расточной ГОСТ 18883-73.
Режим резания принимаем по табл. 29 [3].
Скорость резания =50ммин
Продольная подача: S=035ммоб
Б. Переустановить заготовку другой стороной. Заготовку крепим в трех- кулачковый патрон за внутренний диаметр ø 65мм.
Б.3.1. Торцуем заготовку в размер 116мм. Глубина срезаемого слоя t=2мм.Резец проходной Т15К6 Т=90мин.Частота вращения шпинделя находим из таблицs 29[3]:
Где: S=041ммоб- подача при чистовом проходе.
Б.3.2 Проточить с ø255 до ø110 за 2 прохода начерно при глубине резания 3мм на длину 6мм. Резец расточной ГОСТ18883-73 (таблица 14 123 [4]).
Скорость резания принимаем : =70ммин.
Б3.3. Проточить с ø255 до ø110 за 1 проход начисто при глубине резания 2мм на длину 2мм.
Резец проходной ГОСТ 18870-73.
Б.3.4. Проточить с ø180 до ø110 за 1 проход начерно с глубиной резания 4мм на длину L=4мм. Резец расточной ГОСТ18883-73 (таблица 14 123 [4]).
Режим резания принимаем из (таблица 29 [3]).
Б.3.5. Проточить с ø180 до ø110 за 1 проход чистовой с глубиной резания t =2мм на длину L=2мм. Резец расточной ГОСТ18883-73 (таблица 14 123 [4]).
Б.3.6. Проточить с ø110 до ø106 за 1 проход чистовой с глубиной резания t=2мм на длину L=20мм. Резец расточной ГОСТ18883-73 (таблица 14 123 [4]).
Продольная подача: S=035 ммоб
Б.3.7. Проточить венец с ø255 до ø252 за 1 проход чистовой с глубиной резания t=15мм на длину L=72мм. Резец расточной ГОСТ18883-73 (таблица 14 123 [4]). Т=90. Режим резания принимаем из (таблица 29 [3]).
Скорость резания =105ммин
Продольная подача: S=08 ммоб
Б.3.8. Проточить венец с ø252 до ø250 за 1 проход чистовой с глубиной резания t=1мм на длину L=72мм. Резец расточной ГОСТ18868-73 (таблица 14 123 [4]). Т=90. Режим резания принимаем из (таблица 29 [3]).
Скорость резания =120ммин
Продольная подача: S=05 ммоб
Б.3.9. Снять две фаски под углом 45 за один чистовой проход на длину 2мм.
Резец проходной ГОСТ 18868-73. Режим резания принимаем из (таблица 29 [3]).
4 Долбежная операция
Для долбёжной работы используем долбёжный станок 7д430
Деталь устанавливаем в машинные тиски долбление производим за 6 проходов с глубиной резания t=1мм на длину 116мм.
Резец строгальный ГОСТ 18891-73. Режим резания принимаем из (таблица 29 [3]). Скорость резания =2673ммин
Где: L=116мм- длина прохода.
=22ммин- рабочая скорость.
=3146ммин – скорость холостого хода.
Продольная подача: S=15 ммоб.
Где: В=20мм – ширина шпонки.
А=143- коэффициент учитывающий время холостого хода.
5 Слесарная операция
А.1. Устанавливаем деталь в машинные тиски под сверления к вертикально-сверлильному станку 2Н125.
Размечаем 4 отверстия контролируя размер по ø140 под углом 90.
Б.1. Сверление производим за 4 прохода с глубиной резания t=46мм.
Сверло ø20 ГОСТ 12121-73. Материал Т15К6.
Режим резания принимаем из (таблица 29 [3]). Скорость резания =224ммин.
Продольная подача: S=025 ммоб
6 Фрезерная операция.
А.1. Устанавливаем деталь в зубофрезерный станок 53А30П.
Нарезку зуба производим дисковой фрезой ГОСТ 10996-64. Модуль зуба m=5.
Число проходов 48 глубина резания t=1мм на длину L=72мм.
Скорость резания =30ммин.
Подача поперечная: S=1 ммоб
Дф=90мм- диаметр фрезы;
В= 72мм – ширина заготовки.
Изготовленную шестерню будем закаливать ТВЧ при твёрдости материала НВ230. Калить будем в термопечи нагревая деталь до температуры t=800 C c последующим отпуском.
8 Шлифовальная операция
А.1. Устанавливаем деталь в зубошлифовальный станок5821. Шлифовку зуба производим кругом шлифовальным ГОСТ 3060-75. Модуль круга m=5. Припуск на толщину зуба в пределах от 005015 начерно и от 001002 начисто. Длина прохода L=72мм. Число двойных ходов в минуту:
Скорость шлифовки определяем по формуле :
Где : - диаметр круга (по таблицы 170 стр. 253[4])
=(63500)принимаем 250мм.
Основное время определяем по формуле (таблица 29 [3]) :
Где: на переключение изделия мин.
Безопасность жизнедеятельности
Анализ вредных и опасных факторов.
Обслуживающий персонал агрегата среднего дробления состоит из одного оператора. Во время работы оператор со своего рабочего места (кабины) должен следить за работой и нормальной загрузкой агрегата. Регулировка механизма дробилки и устранение неисправностей производиться только при полной остановке агрегата. Находиться на работающем агрегате не допускается .
Современное дробильное оборудование по своим санитарно-гигиеническим нормам не удовлетворяют установленным требованиям и нормам обеспечения нормальных условий работы обслуживающего персонала. Поэтому выбор способ установки и эксплуатации оборудования следует уделить особое внимание
Опасные и вредные производственные факторы
Источники местпричины возникновения опасных и вредных факторов.
Основные средства защиты от опасных и вредных факторов.
Недостаточное освещение
Темное время суток кабина оператора.
Установка прожекторов на территории светильников в кабине оператора освещение рабочих мест
Повышенная температура в рабочей зоне.
Установка кондиционера наклон стекла кабины наружу наклейка солнцезащитной пленки.
Пониженная температура в рабочей зоне.
Установка кондиционера обогреватель.
Повышенная запыленность в рабочей зоне.
Вентиляция очистка воздуха.
Грохота кабина оператора
Вибро гасящие вибропоглащающие приспособления.
Повышенный уровень звука.
Грохота дробилка кабина оператора
Звука изолирующие приспособления глушители звука.
Движущиеся машины и механизмы
Обслуживающий технологический транспорт.
Четко обозначаемые подъездные пути скорость не более 5
Движущиеся элементы оборудования
Ограждение этих элементов.
Падение инертных материалов.
Индивидуальные средства защиты установка бортов.
Эл. ток опасной величины.
Установка заземления эл. оборудования изоляция токоведущих частей и кобелей.
Индивидуальные средства защиты.
Шум и мероприятия по его снижению.
Дробление материалов в дробильных установках связано со значительным шумообразованием возникающими при расколе кусков и вибрации деталей от импульсных воздействий и усилий дробления.
ВНИИстройдормаш были проведены исследования шумовых характеристик дробильного оборудования. Ниже приведены данные этих исследований для щёковых дробилок
Октавные полосы со среднегеометрическими частотами Гц
Уровни звукового давления Дб
В свою очередь допустимые уровни звукового давления на рабочих местах согласно ГОСТ 12.1.003-88 имеют следующие значения (табл. 5.2.)
Для уменьшения шумового воздействия на обслуживающий персонал рассматриваются два основные способа:
снижение шума излучаемого технологическими устройствами;
борьба с проницаемостью излучаемого шума.
По первому способу выбирают оптимальную толщину стенок усиливают изолирующие элементы применяют эластичные соединения отдельных деталей с корпусом устанавливают дробилки на упругих элементах разделяют течки эластичными фланцами
По второму способу применяют различного вида укрытия устанавливают оборудование в отдельных помещениях удаляют пульты управления из рабочей зоны от непосредственной близости с дробилками.
Эффективность некоторых мероприятий приведена в таблице 5.3.
Установка прокладок толщиной 10ммиз резиновой смеси1345 (ТУ 38-1059-72) под футеровки отражательных плит.
Шумоизоляция корпуса дробилки нанесением противошумной мастики №549 (ТУ -10-1268-70) толщина слоя 5 10мм.
Шумоизоляция течек нанесением противошумной мастики №579 (ТУ – 6 - 10-1268-70) толщина слоя 5 6мм.
Перенос рабочего места на расстояние 10м от корпуса дробилки
Вибрация и её устранение
Вибрация при работе щёковых дробилок возникают в следствии того что на жёстко связанной с машиной фундамент передаются вертикальные и горизонтальные периодические движения дробящей щеки и звеньев механизма привода. При дроблении материала в щёковых дробилках возникают также горизонтальны импульсивные нагрузки. Ниже приведены показатели для расчёта виброизоляции щёковой дробилки СДМ-108А.
Динамические нагрузки Т:
вертикальные составляющие инерционных сил - 2В;
горизонтальные составляющие инерционный сил – 15В
геометрические характеристики и нормы вибрации приведены в ГОСТ 12.1.012-78
Для ограничения вращательных колебаний установки в вертикальной плоскости и обеспечения эффекта виброизоляции в горизонтальном направлении виброизоляторы должны обладать большой вертикальной и малой горизонтальной жёсткостью.
Конструктивно виброизоляторы могут быть выполнены в виде подвесок или в виде специальных виброизоляторов с гидравлическими шарнирами причём установка дробилок на виброизоляторы не требует каких-либо изменений в самих машинах. Вынос пульта управления дробилкой в отдельную кабину практически полностью защищает оператора от действия вибрации.
Пылеобразование и пылеподавление.
При эксплуатации дробильного оборудования важнейшей задачей является защита обслуживающего персонала от вредных воздействий пыли. Процесс дробления кусков материала в дробилках происходит с образованием мелкодисперсных частиц. Кроме того поступающие в дробилку материалы так же содержат мелкие пылевидные фракции образовавшиеся в результате разрушения горной породы взрывом в карьере а также от истирания при перегрузках и транспортировании. Воздушные потоки возникающие от движения рабочих органов дробилок и свободного движения кусков материала увлекают с собой мелкодисперсные фракции выносящих в окружающую зону создают неблагоприятные условия для обслуживающего персонала.
В щёковых дробилках возвратно-поступательного движения рабочего органа выталкивает воздух из внутренней полости дробилки последовательными порциями в приёмное отверстие и выходную щель. При этом скорость пылевоздушных потоков достигает 3 мс.
Содержание вредных веществ в воздухе рабочей зоны не должно превышать предельно-допустимых концентраций указанных в ГОСТ 12.1005-76.
Для защиты производственного помещения от выброса пыли применяют герметические укрытия оборудования течек мест пересылки.
К укрытиям предъявляются следующие требования:
объёмы укрытия должны быть оптимальными;
укрытия должны быть просторными и обеспечивать свободный
доступ к рабочим местам оборудования;
форма должна соответствовать требованиям аэродинамике пылевоздушных потоков
Для эффективного пылеподавления в тех случаях когда позволяет технологический процесс широко используют гидро- и парообеспыливание благодаря которым с помощью распылённой воды и пароводяного тумана увлажняется материал и подавляется пылевое облако. Увлажнение изверженных пород на 8..10% и осадочных на 4 6% практически сводит к минимуму выделение пыли.
В необходимых случаях конструкции производственного оборудования должно иметь средства местного освещения соответствующие условиям эксплуатации (взрывоопасная среда повышенная влажность и т.д.) при этом должна исключаться возможность случайных прикосновений к токоведущим частям установленных средств. Система управления производственным оборудованием должна быть выполнена так чтобы не могло возникнуть опасности в результате совместного действия функциональных систем.
Конструкцией должны быть предусмотрена сигнализация в необходимых случаях - средства автоматического останова и отключения оборудования от источников энергии при опасных неисправностях авариях. Производственное оборудование в необходимых случаях должно иметь средства торможения эффективность действия которых достаточна для обеспечения безопасности и соответствует требованиям стандартов.
Соединение заземляющего оборудования с землёй осуществляется при помощи заземляющего устройства состоящего из заземлителя и заземляющих проводников. Последние служат для соединения заземлённого оборудования с заземлителем.
Защитное заземление – это преднамеренное электрическое соединение с землёй или её эквивалентом металлических нетоковедущих частей оборудования которые могут оказаться под напряжением. Заземление применяют в сетях с изолированной нейтрально напряжением до и выше 1000В
Зануление – это преднамеренное электрическое соединение с нулевым защитным проводником металлических нетоковедущих частей которые могут оказаться под напряжением. Зануление применяют в четырёхпроводных сетях с глухозаземлённой нейтралью напряжением до 1000В.
Отключающая способность зануления обеспечивается при соблюдении условия:
Пусковой ток определяется по формулам для одного двигателя:
- коэффициент кратности пускового тока (для трёхфазного двигателя переменного тока =5 7); =5.
Р – мощность двигателя -55кВт;
- линейное напряжение сети – 380В;
Cos φ – коэффициент мощности -0.7;
– КПД двигателя (определяется по паспорту) -0.8;
Номинальный ток плавной вставки определяется по пусковому току двигателя с учётом режима его работы:
- коэффициент учитывающий режим работы двигателя =16
Ток короткого замыкания:
Где: -расчетное сопротивление трансформатора Ом для трансформатора 100кВА-0266Ом .
Сечение жилы четырехжильного кабеля S=78.5мм. Активное сопротивление и нулевой жилы:
Где: - для алюминия;
е-100м –длина кабеля
Активное сопротивление петли ’’фаза-ноль ’’:
Условия срабатывания защиты:
т.е. условия соблюдены.
- заземление нулевой точки трансформатора;
-сопротивление обмотки трансформатора;
- сопротивление нулевого провода;
-ток короткого замыкание;
- сопротивление фазного провода;
- сопротивление заземления.
Прожекторное освещение зоны работы установки.
Расчет числа прожекторов производят исходя из нормируемой освещенности и мощности лампы. Ориентировочное число прожекторов:
- коэффициент учитывающий световую отдачу источника света КПД прожекторов и коэффициент использования светового потока для ЛН=02025 ДРЛ и ГЛ=012016
- нормированная освещенность горизонтальной поверхности ЛК;
k- коэффициент запаса;
А-освещаемая площадь ;
Минимальная высота установки прожекторов над освещаемой поверхностью:
-максимальная сила света.
В соответствии с СН 81-80 Ен=2лкk=15 (по таблице XIII[6]) по таблице XIII [10]
Подбираем подходящий тип прожектора ПЗС-45 с ЛНГ200-1000.
ПЗС-45 с ЛНГ200-1000 имеет =13000
В нашем случае удобно в середине двух противоположных сторон установить по одной мачте с 1прожектором на высоте 16м.
Для общего равномерного освещения можно воспользоваться рекомендуемыми
Схемами расположения осветительных приборов
Если Ен=2лк или 05лк (таблица). Для рассматриваемой рекомендуется ПЗС-45 с ЛН=1000Вт; угол наклона прожекторов V=18 и угол между оптическими осями . При этом коэффициент неравномерности а удельная мощность
Расчёт экономической эффективности от использования новой дробилки
Выбор базового варианта.
Для сравнения в качестве базового варианта принимается щёковая дробилка СМД-108А.
Выявление конструктивно-эксплуатационных особенностей новой техники.
Целью создания новой дробилки является повышение экономичности в эксплуатации. Для этого передняя щека подпружинена относительно корпуса в вертикальном направлении с возможностью сообщения ей колебаний задней щекой через дробильный материал. Это уменьшает истирание дробящих плит расходы на которые по данным эксплуатирующих организаций составляют 13 39% от стоимости общих затрат на дробление.
Исходные данные приведены в таблице 6.1.
Наименование параметров
Техническая производительность
Ресурс до капитального ремонта час.
Часовая тарифная ставка оператора агрегата среднего дробления III разр. руб.
Потребляемая мощность кВт.ч.
Периодичность выполнения ч.:
Масса модернизируемых узлов кг
Срок службы быстроизнашивающихся частей (дробящих плит) час
Определение оптовой цены новой техники.
Оптовая цена новой дробилки определяется по формуле;
где: С-себестоимость изготовления машины руб.
Рс- рентабельность в процентах к себестоимости.
Модернизация дробилки заключается в изменении траектории движения подвижной щеки при этом изготавливается дополнительное незначительное количество деталей (кривошип вал и пр.). Поэтому расчёт ведём по формуле;
Где : Сд-200000руб себестоимость дробилки;
См-затраты на приобретение изготовление и монтаж 1кг.массы модернизируемых узлов руб;
Вн - масса модернизируемых узлов новой машины кг.
В – масса модернизируемых узлов проектируемой конструкции кг;
К – коэффициент корректировки учитывающий применение более дорогих или более дешёвых материалов и покупных изделий (от 065 до 125)
Ц=См+(1+Рс)=222034*(1+03)=288644руб.
Определение годовой эксплуатационной производительности.
Годовая эксплуатационная производительность определяется по формуле:
Где: - эксплуатационная средняя часовая производительность ед. продукции
- количество машино-часов работы техники в году маш.чгод.
Эксплуатационная среднечасовая производительность базовой техники определяется по формуле:
Где: -часовая техническая производительность
- коэффициент перехода от технической производительности к эксплуатационной;
Эксплуатационная среднечасовая производительность новой техники определяется по формуле:
Где: - Эксплуатационная среднечасовая производительность аналога
- коэффициент учитывающий изменение использования показателей входящих в формулу технической производительности;
- коэффициент учитывающий изменение использования техники по времени в смену.
Количество машина - часов работы дробилки в году определяется по формуле:
Где: -годовой фонд рабочего времени дн;
-продолжительность сезонного обслуживания дн;
- продолжительность смены ч.
- коэффициент сменности;
-простои во всех видах ремонтов и техобслуживаний днмаш.ч;
- продолжительность одной перебазировки дн.
-время работы на объекте машч;
Простои во всех видах ремонтов и техобслуживанию определяется по формуле:
Где: -удельная оперативная трудоёмкость технического обслуживания челчмото*час;
Б- число рабочих осуществляющих техническое обслуживание чел.
- коэффициент перевода оперативного времени в общее время работы;
- продолжительность смены ч.;
- продолжительность пребывания техники в текущем и капитальном ремонтах соответственно дн.;
- продолжительность ожидания доставки техники в текущий и капитальный ремонт и обратно дн.;
- количество текущих ремонтов в межремонтном цикле шт.;
- среднее время на устранение одного отказа маш.ч;
- наработка на отказ мото.ч
-средний ресурс до капитального ремонта мото.ч.
- коэффициент перевода мото - часов в машино - часы.
Продолжительность одной перебазировки агрегата среднего дробления определяется по формуле;
Где: -среднее расстояние перебазировки км;
- средняя скорость переезда кмч.;
- средняя продолжительность нагрузки маш. ч.;
- продолжительность смены час;
Количество машино-часов работы дробилки в году;
Годовая эксплуатационная производительность дробилки равна:
Определение годовых текущих издержек потребителя.
Годовые текущие издержки потребителя при использовании дробилки рассчитываются по формуле:
Сг=(Са+Ср+Скр+Сз+Сэг+Ссм+Спб+Сч)*(1+Нр)
Где: Са- амортизационные отчисления на реновацию руб.;
Ср- затраты на выполнение текущих неплановых ремонтов руб.;
Скр- затраты на выполнение капитальных ремонтов руб.
Сз- заработная плата рабочих управляющих техникой руб.
Сэг- затраты энергоносителей руб.;
Ссм- затраты на смазочные материалы руб.;
Спб- затраты на перебазировку руб.;
Сч- затраты на быстро изнашиваемые части руб.;
Нр- норма накладных расходов связанных с эксплуатацией строительных и дорожных машин.
Амортизационные отчисления на реновацию;
Где; На- норма амортизационных отчислений на реновацию в %.
К- капитальные вложения потребителя связанные с приобретением дробилки её доставкой и монтажом руб.
Где: Ц-цена техники руб.
Кд- коэффициент перехода от цены к балансовой стоимости с учетом транспортных расходов.
Отсюда на амортизационные отчисления на реновацию:
Затраты на выполнение технических обслуживаний текущих и неплановых ремонтов:
- средний ресурс до капитального ремонта мото.час;
- средняя тарифная ставка работы по ремонту машин руб.чел.- ч.;
- средний коэффициент к тарифной ставке;
- коэффициент учитывающий премии ремонтным рабочим;
- удельная оперативная трудоёмкость технических обслуживаний чел.- ч.мото-час;
- продолжительность пребывания техники в текущем и капитальном ремонте дн.;
- трудоёмкость текущего ремонта чел. – ч.;
- среднее время на устранение одного отказа маш.час;
- количество рабочих занятых устранением отказа чел.;
- наработка на отказ мото.час;
- коэффициент перевода моточасов в машиночасы;
- расход запасных частей на год работы техники руб.год
Годовые затраты на выполнение капитального ремонта рассчитываются по формуле:
Где - трудоёмкость капитального ремонта чел.ч.;
- расход запасных частей на один капитальный расход руб.;
Заработная плата рабочих управляющих техникой определяется по формуле:
Где: - коэффициент учитывающий доплаты за 2-ю и 3-ю смены.
- количество рабочих занятых управлением техникой в одну смену.
- часовая тарифная ставка рабочего
Отсюда заработная плата рабочих управляющих дробилкой равна
Затраты на электроэнергию :
Где: -цена электроэнергии рубкВт*ч;
-часовой расход электроэнергии кВт*ч;
Часовой расход электроэнергии определяем по формуле:
Где; - номинальная мощность электродвигателя кВт;
- коэффициент спроса i-го электродвигателя.
Отсюда затраты на электроэнергию;
Затраты на смазочные материалы для техники с электроприводом:
Где: затраты на смазочные материалы на 10квт*ч электроэнергии руб.
Затраты на замену быстроизнашивающихся частей (дробящих плит):
- цена быстроизнашивающихся
- количество одновременно заменяющихся быстроизнашивающихся i-х частей шт
Затраты на перебазировку при перевозке техники на буксировку:
- заработная плата экипажа перевозимой машины руб.;
- затраты на эксплуатацию автомобиля руб.
Заработная плата экипажа перевозимого агрегата дробления определяется по формуле:
Где: =продолжительность одной перебазировки дни.
Б- количество рабочих занятых управлением машины в одну смену чел.;
- часовая тарифная ставка руб.маш.ч
Затраты на эксплуатацию автомобиля:
Где: - стоимость одного автомобиля-часа рубч.
- плата за 1 км пробега руб.км
Отсюда затраты на перебазировку равны:
Полученные результаты сводим в таблицу 6.2. и определяем общую сумму годовых издержек при использовании агрегата среднего дробления
Значение показателей
Амортизационные отчисления на реновацию
Затраты на выполнение Т.О. и ремонтов
Затраты на выполнение капитального ремонта
Заработная плата рабочих управляющих техникой
Затраты на электроэнергию
Затраты на смазочные материалы
Затраты на перебазировки
Затраты на быстроизнашивающиеся части (дробящие плиты)
Общая сумма годовых текущих издержек
Определение годового экономического эффекта
Экономический эффект в расчёте на одну машину за год работы определяется по формуле:
Где: - стоимостная оценка результатов руб.год
- себестоимость эксплуатации (текущие издержки потребителя) рубгод
- нормативный коэффициент эффективности ;
К- капитальное вложения потребителя руб.
Стоимостная оценка результатов работы дробилки рассчитывается по формуле;
Где: Цп- цена единицы конечной продукции производимой дробилкой
В-масса продукции производимой дробилкой
Где: Сп-156200руб1000-по данным предприятия.
Нр-021-21%-норма накладных расходов.
Пн - норма плановых накоплений к полной себестоимости.
Стоимостная оценка результатов работы дробилки;
Экономический эффект в расчете на одну машину за год составит;
Годовой экономический эффект от внедрения данной дробилки определяется из разности экономических эффектов и
=-=50403475-4920514=1198335 руб.
Срок окупаемости без учета годовых издержек определяется:
Где: К- капитальное вложения потребителя руб.
Эг- годовой экономический эффект руб.
Срок окупаемости дополнительных вложений:
Где: - издержки потребителя на установку новой щеки руб.
Эу.ч.- Годовой экономический эффект руб.
Наименование показателя
Балансовая стоимость
Годовая эксплуатационная производительность
Годовые текущие издержки потребителя
Годовой экономический эффект
Срок окупаемости новой дробилки
Срок окупаемости дополнительных капитальных вложений
К.А. Артемьев и др. «Дорожные машины» в 2-х частях.4II. Машины для устройства дорожных покрытий. Учебник для ВТУЗов по специальности «Строительные и дорожные машины и оборудование» (К.А. Артемьев Т.В. Алексеева В.Г. Белокрылов и др.). М.: Машиностроение 1982г. 396 стр.
Б.В. Киушанцев и др. Дробилки. Конструкция расчёт особенности в эксплуатации. М.: Машиностроение 1990г. 320 стр.
Справочник технолога-машиностроителя. В 2-х томах. Под редакцией А.Г. Косиловой и Р.К. Мещеряковой. 4-ое изд. переработанное и допол. М.: Машиностроение 1985г. 656 стр.
В.А. Бауман Б.В. Киушанцев В.Д Мартьенов «Механическое оборудование предприятий строительных материалов изделий и конструкций» М.: Машиностроение 1981г. 323 стр.
В.И. Анурьев «Справочник конструктора-машиностроителя» в 3-х томах.Т.2. 5-ое изд. переработанное и допол. М.: Машиностроение 1978г. 559 стр.
В.И. Анурьев «Справочник конструктора-машиностроителя» в 3-х томах.Т.3. 5-ое изд. переработанное и допол. М.: Машиностроение 1978г. 736 стр.
«Точность и производственный контроль в машиностроении» Справочник. Под ред. А.К. Крутая Б.М. Сорокина. Л.: Машиностроение 1983г. 385 стр.
П.А. Долин. Справочник по технике безопасности. 6-ое изд. М.: Энергоатомиздат 1985г. 824 стр.
Г.Г. Орлов. Инженерные решения по охране труда в строительстве.
И.И. Устюгов «Детали машин». М.: Машиностроение 1988г. 399 стр.
С.А. Чернавский «Курсовое проектирование деталей машин». 1988г. 415 стр.
А.В. Мельников «Расчёт оборудования дробильно - сортировочных предприятий» Методические указания для технологического расчёта курсовых проектов. Иркутск. ИПИ 1983г. 38 стр.
«Допуски и посадки.» Справочник том 12. под редакцией Мягкова В.Д. М.: Машиностроение 1983г.