Модернизация путевой машины ВПР-02




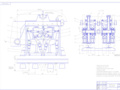
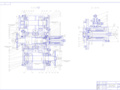
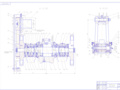
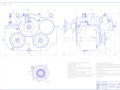
- Добавлен: 25.10.2022
- Размер: 4 MB
- Закачек: 1
Описание
Состав проекта
![]() |
![]() |
![]() ![]() ![]() ![]() |
![]() ![]() ![]() |
![]() ![]() ![]() |
![]() ![]() ![]() |
![]() ![]() ![]() ![]() |
![]() ![]() ![]() ![]() |
![]() ![]() ![]() ![]() |
![]() ![]() ![]() ![]() |
![]() ![]() ![]() |
![]() ![]() ![]() ![]() |
![]() ![]() ![]() |
![]() ![]() ![]() |
![]() ![]() ![]() |
![]() ![]() ![]() ![]() |
![]() ![]() ![]() |
![]() ![]() ![]() ![]() |
![]() |
![]() ![]() ![]() |
Дополнительная информация
Раздаточный_редуктор1.spw

Блок_подбивочный_1.cdw

Подбивочный_блок1.spw

Раздаточный_редуктор_2.cdw

Блок_подбивочный_2.cdw

Раздаточный_редуктор_1.cdw

ВПР-02-Общий_вид.cdw

ВПР-02_Общий_вид1.spw
