Кран поворотный с внешними опорами, г/п 8 т




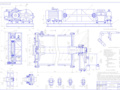
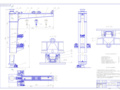
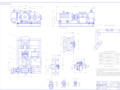
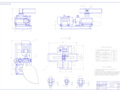
- Добавлен: 25.10.2022
- Размер: 4 MB
- Закачек: 0
Описание
Состав проекта
![]() |
![]() |
![]() ![]() ![]() ![]() |
![]() ![]() ![]() ![]() |
![]() ![]() ![]() ![]() |
![]() ![]() ![]() ![]() |
![]() ![]() ![]() ![]() |
![]() ![]() ![]() ![]() |
![]() ![]() ![]() ![]() |
![]() ![]() ![]() ![]() |
![]() ![]() ![]() ![]() |
![]() ![]() ![]() ![]() |
![]() ![]() ![]() ![]() |
![]() ![]() ![]() ![]() |
![]() ![]() ![]() ![]() |
![]() ![]() ![]() ![]() |
![]() ![]() ![]() ![]() |
![]() ![]() ![]() ![]() |
![]() ![]() |
![]() ![]() |
![]() ![]() |
![]() ![]() |
![]() ![]() |
![]() ![]() ![]() |
![]() ![]() |
![]() ![]() |
![]() ![]() |
![]() ![]() |
![]() ![]() |
![]() ![]() |
![]() |
![]() ![]() |
![]() ![]() |
![]() ![]() |
![]() ![]() |
![]() ![]() |
![]() ![]() |
![]() |
![]() ![]() |
![]() ![]() |
![]() ![]() |
![]() ![]() |
![]() ![]() |
![]() ![]() |
![]() ![]() |
![]() ![]() |
![]() ![]() |
![]() ![]() |
![]() ![]() |
![]() ![]() |
![]() ![]() |
![]() ![]() |
![]() ![]() |
Дополнительная информация
Спец мех перед_2.dwg

Спец мех под_1.dwg

Мк стрелы.dwg

Спец мех перед_1.dwg

Обший вид.dwg

спец_общ вид_1.dwg

Спец мех повор_1.dwg

Спецификация металлоконструкции.dwg

Мех поворота.dwg

Спец мех под_2.dwg

Мк крана.dwg

Спец мех под_3.dwg

Спец мех повор_2.dwg

Мех передвижения.dwg

спец_общ вид_2.dwg

Мех подъема.dwg

Рекомендуемые чертежи
Свободное скачивание на сегодня
- 22.08.2014
- 29.08.2014