Кран козловой г/п 3,2 т. Курсовой проект.




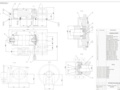

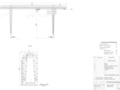
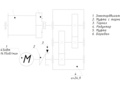
- Добавлен: 25.10.2022
- Размер: 1 MB
- Закачек: 0
Описание
Состав проекта
![]() |
![]() ![]() ![]() |
![]() ![]() |
![]() |
![]() ![]() ![]() ![]() |
![]() |
![]() ![]() ![]() ![]() |
![]() ![]() ![]() ![]() |
![]() ![]() ![]() |
![]() ![]() ![]() |
![]() |
![]() ![]() ![]() ![]() |
![]() ![]() ![]() |
![]() ![]() ![]() |
Дополнительная информация
Сопромат оси барабана.dwg

Лебедка.dwg

Клапан М112.000 816.200 СБ
Эл.магнитная катушка М112.000 816.400 СБ
Изделие Распределитель
Тарелка М112.000 816 .104
Инв.№ подл. и дата Взам. инв.№
Втулка М112.000 816. 301
Трубка М112.000 816.201
Втулка М112.000 816.103
Сердечник М112.000 816.102
Корпус М112.000 816.101
Винт 3М 4х10 ГОСТ 17475-72
Болт М8х25 ГОСТ7798-80
Болт М10х25 ГОСТ 7798-80
Болт М8х20 ГОСТ7798-80
Гайка М12 ГОСТ 15521-70
Болт М12х580 ГОСТ7798-80
Вновь разрабатываемые изделия
Пресс-масленка ГОСТ1303-56
Подшипник N8324 ГОСТ6874-75
Подшипник N314 ГОСТ8338-78
ГПМ.М411.16.03.00 ВО
Шайба 20 ГОСТ6402-70
Мощность редуктора 43
Передаточное число редуктора 40
Мощность двигателя 36 кВт.
Техническая характеристика
Высота подъема груза 16 м.
Шайба 25 ГОСТ6402-70
Шайба 25 ГОСТ11371-68
Кожух открытой передачи
Электродвигатель MTF412-6
Болт М25х60 ГОСТ7798-80
Муфта МЗ4 с тормозным шкивом
Шайба 8 ГОСТ11371-68
Гайка М25 ГОСТ15521-70
Болт М25x60 ГОСТ7798-80
Гайка М8 ГОСТ15521-70
Болт М20x170 ГОСТ7798-80
Болт М20x70 ГОСТ7798-80
Болт М6x30 ГОСТ7798-80
Болт М8x50 ГОСТ7798-80
Болт М25х50 ГОСТ7798-80
Гайка М24 ГОСТ 15521-70
Гайка М20 ГОСТ 15521-70
Гайка М42 ГОСТ 15521-70
Болт М24х50 ГОСТ 7796-70
Шайба 24 ГОСТ 6402-70
Шайба 42 ГОСТ 6402-70
Пресс-масленка ГОСТ 1303-56
Шайба 12 ГОСТ 6402-70
Шайба 20 ГОСТ 6402-70
Болт М24х65 ГОСТ 7796-70
Болт М24х75 ГОСТ 7798-70
Болт М20х50 ГОСТ 7796-70
Болт М12х40 ГОСТ 7796-70
Болт М42х100 ГОСТ 7798-70
Болт М20х110 ГОСТ 7798-70
Болт М24х170 ГОСТ 7798-70
Подшипник №1222 ГОСТ 28428-90
Муфта с тормозным шкивом
Электродвигатель МТF 412-6
Болт М8x30 ГОСТ7798-80
ПТМ.МС313.18.00.00.00 ВО
ПТМ.МС313.18.00.00.22
ПТМ.МС313.18.00.00.23
ПТМ.МС313.18.00.00.24
ПТМ.МС313.18.00.00.25
ПТМ.МС313.18.00.00.26
ПТМ.МС313.18.00.00.27
ПТМ.МС313.18.00.00.28
ПТМ.МС313.18.00.00.29
ПТМ.МС313.18.00.00.31
ПТМ.МС313.18.00.00.30
Привод механизма подъема
Общий вид крана.dwg

Группа режима работы
Высота подъема груза
Техническая характеристика крана
Механизм подьема груза
Вновь разрабатываемые изделия
Механизм передвижения тележки
Механизм передвижения крана
Привод механизма подъема
ПТМ.МС313.18.00.00.00 ВО
Уровень головки рельса
Техническая характеристика
Кран козловой. Общий вид
Подвеска крюковая.dwg

ПТМ.МС313.18.00.00.00 ВО
Болт М10х30 ГОСТ 7805-70
Гайка М18 ГОСТ 15525-70
Крюк №19 ГОСТ 6627-74
Подшипник 324 ГОСТ 8338-75
Пресс-масленка ГОСТ 19853-74
Подшипник 8118Н ГОСТ 7872-89
Шайба 10 ГОСТ 6958-78
Шайба 10 ГОСТ 6402-70
Шайба 18 ГОСТ 6402-70
Шайба 18 ГОСТ 6958-78
Шпилька 18х585 ГОСТ 22041-76
Предохранительный замок
ПТМ.МС313.18.00.00.01
ПТМ.МС313.18.00.00.02
ПТМ.МС313.18.00.00.03
ПТМ.МС313.18.00.00.04
ПТМ.МС313.18.00.00.11
ПТМ.МС313.18.00.00.10
ПТМ.МС313.18.00.00.09
ПТМ.МС313.18.00.00.12
ПТМ.МС313.18.00.00.05
ПТМ.МС313.18.00.00.06
ПТМ.МС313.18.00.00.07
ПТМ.МС313.18.00.00.08
ПТМ.МС313.18.00.00.13
ПТМ.МС313.18.00.00.14
Курсовой проект по ПТМ.doc
Описание управления машиной и устройств безопасности
Козловые краны являются одним из основных видов средств механизации перегрузочных и складских работ в различных отраслях народного хозяйства.
По назначению козловые краны разделяют на три основные группы: общего назначения или перегрузочные строительно-монтажные и специального назначения.
Перегрузочные краны эксплуатируют на открытых складах и погрузочных площадках обслуживаемых средствами наземного рельсового и безрельсового транспорта; грузоподъемность их обычно 32 50 т пролеты 10 40 м высота подъема в зависимости от условий загрузки-разгрузки транспортных средств или стабилизирования грузов 7 16 м.
Строительно-монтажные краны предназначены преимущественно для монтажа оборудования промышленных предприятий энергетических установок и сборных транспортных сооружений. Грузоподъемность этих кранов 300 400т пролеты 60 80 м и высота подъема 20 30 м. Краны рассчитаны на легкий режим работы; конструкция их часто обеспечивает быстрое перебазирование сборку в различных исполнениях с варьированием грузоподъемности пролета высоты подъема и т.п.
Краны специального назначения обслуживающие гидротехнические сооружения обеспечивающие секционную сборку судов и др. крайне разнообразны по конструкции и рабочему оборудованию; их параметры изменяют в самых широких пределах [1].
Независимо от типа козловые краны имеют мост (пролетное строение) опирающиеся на две опоры снабженный рельсо-колесными ходовыми частями. По мосту перемещается тележка.
В зависимости от конструктивной схемы моста различают консольные и бесконсольные краны. Возможность выхода грузовой тележки на консоль позволяет располагать под ней транспортные рельсовые и безрельсовые пути а площадку под пролетной частью моста использовать для устройства склада или технологического объекта. Помимо этого увеличивается общая площадь складирования.
Бесконсольные краны несколько проще по конструкции но размещение в пролете транспортных путей часто препятствует рациональной организации складов; снижается также безопасность лиц работающих на таких складах.
Краны могут иметь две жесткие или одну жесткую а другую гибкую опоры. Стойки жестких опор выполняют с увеличивающимися по высоте размерами сечения стоек. Такие краны характеризуются более плавным ходом их несущие конструкции в значительно меньшей мере подвержены колебаниям. Однако они весьма чувствительны к отклонениям крановых рельсовых путей и точности установки ходовых колес в горизонтальной плоскости. Превышение этих отклонений сверх предусмотренных нормативами величин приводит к быстрому износу реборд ходовых колес.
У кранов с одной жесткой а другой гибкой опорами стойки последней обладают весьма значительной по сравнению со стойками жесткой опоры податливостью иногда они крепятся к мосту с помощью шарниров. Такие
краны обычно могут перемещаться по путям отклонения рельсов которых в горизонтальной плоскости на 25-40% превышают предельно допустимые они также менее чувствительны к отклонениям в точности установки ходовых колес в горизонтальной плоскости. Однако у них как ходовые колеса так и рельсовый путь жесткой опоры испытывают осевые нагрузки в два-три раза превосходящие соответствующие нагрузки у кранов с двумя жесткими опорами.
Краны с одной жесткой а другой гибкой опорами часто испытывают медленно затухающие низкочастотные продольные колебания. Это неблагоприятно сказывается на точности работы крана и ухудшает условия работы крановщика.
У большинства кранов мост опирается на двухстоечные опоры через проемы которых груз транспортируют с консолей в пролет при этом максимальная длина груза определяется расстоянием между стойками опор.
У кранов с консольной грузовой тележкой и одностоечными опорами длинномерные грузы подаваемые под консоли разворачивают на весу на 90° и независимо от их длины беспрепятственно перемещают мимо опоры пролетной части. В случае необходимости груз снова можно развернуть на 90°.
В зависимости от расположения подъемного механизма относительно подтележечных путей различают краны с подвесными опорными и консольными грузовыми тележками. Краны с подвесными монорельсовыми грузовыми тележками наиболее просты по конструкции. Однако при работе повышенной а также средней интенсивности нижние ездовые полки монорельса отгибаются. Кроме того монорельсовые тележки не защищены от поперечного раскачивания.
Этих недостатков лишены краны с подвесными двухрельсовыми тележками которые однако характеризуются более сложной конструкцией.
Опорные грузовые тележки наиболее удобны в эксплуатации. Однако их можно применять только на обладающих сравнительно большой массой двухбалочных кранах или на неэффективных в ряде случаев бесконсольных кранах.
Краны выполняют с управлением с пола с помощью подвесного кнопочного пульта или из кабины. Краны с управлением с пола обычно имеют пролеты не более 16 м и оборудованы электрической талью. При пролетах до 16-25 м кабины обычно устанавливают на одной из опор или на мосту около опоры.
При больших пролетах краны предназначенные для перегрузочных работ должны снабжаться подвижными кабинами которые обычно перемещаются совместно с грузовыми тележками.
По способу монтажа различают самомонтирующиеся и несамомонтирующиеся краны. Большая часть кранов – самомонтирующиеся с осуществлением подъема моста в проектное (рабочее) положение путем по парного стягивания стоек опор.
По технологическому процессу различают крюковые краны для перегрузочных работ монтажные грейферные контейнерные строительные для обслуживания гидротехнических сооружений и судостроительные.
Токопровод для кранов выполняют обычно с помощью гибкого кабеля.
Ряд кранов снабжают автоматическими кабельными барабанами рассчитанными на наматывание 50-100 м кабеля. При расположении коробки питания в центре пути это обеспечивает перемещение крана на удвоенное расстояние. Для укладки кабеля вдоль путей устраивают деревянный лоток.
Такой же лоток предусматривают и при креплении конца кабеля непосредственно к конструкции крана. Токопровод перетаскиваемым по лотку кабелем достаточно надежен для относительно редко и на небольшие расстояния перемещающихся кранов (3-5 циклов в час при протяжении пути до 20-30 м).
При более интенсивной работе оболочка кабеля будет быстро изнашиваться. В ряде случаев для токопривода к крану можно использовать гирляндную подвеску кабеля. Петли кабеля крепят к петлям или кареткам перемещающимся по натянутым вдоль путей проволоке или тросу.
Крановые рельсовые пути должны устраиваться в соответствии с указаниями приведенными в эксплуатационной документации на кран. Проект крановых путей должен разрабатываться в каждом конкретном случае с учетом местных геологических условий. Рельсовые пути на земляном полотне следует ремонтировать и проверять не реже двух раз в год – в конце весны и в конце осени.
Краны изготовляют как правило для эксплуатации при температуре воздуха от плюс 40 до минус 40°С. Иногда нижний предел температуры ограничивают минус 20°С. Эксплуатация кранов при температурах ниже указанных в паспорте крана может быть допущена только при наличии разрешения
завода-изготовителя при согласовании с органами Росгортехнадзора.
Так как для козловых кранов опасным является действие ветра вдоль подкрановых путей они обычно снабжаются ветроизмерительными приборами направленного действия – сигнализаторами давления ветра СДВ-М содержащий датчик и электронный сигнальный блок. После срабатывания датчика зажигается установленная на блоке лампа предварительной сигнализации; одновременно приводится в действие реле времени (12; 2 или 3 с) по истечении этого времени замыкается цепь устройств (звуковая сигнализация противоугонные захваты).
Противоугонные устройства должны предотвращать самопроизвольное движение крана и грузовой тележки при ветре давлением превосходящим допустимое для кранов рабочего состояния.
Для козловых кранов общего назначения можно выделить следующие основные группы этих устройств: стопоры ручные и приводные рельсовые захваты (автоматического и принудительного действия).
Устройства для гашения вибраций и защиты от нее целесообразны для всех видов кранов они повышают уровень комфортности оператора улучшают
условия управления краном и снижают нагруженность элементов
Рисунок 1.1 – Кран козловой
Монтаж самомонтирующегося козлового крана производят в следующем порядке:
мостовое строение 1 собирают на подставках на небольшом расстоянии от земли что облегчает производство монтажа;
поддерживающие ноги 2 соединяют шарнирами с мостом 1 и с балансирными тележками 4;
для подъема моста ноги соединяют полиспастами канаты которых закреплены на барабанах 5 стягивающих механизмов имеющих ручной привод;
когда мост занимает рабочее положение балансирные тележки 4 соединяют балкой 3 а полиспастная система разбирается [1].
Основные параметры крана. Выбор прототипа
где H – высота подъёма груза м ().
База тележки назначается из ряда: 10; 12; 29; 33 м.
Принимаем базу тележки
Высота пролетного строения фермерного типа м:
где L – пролёт крана м ().
Высота концевого сечения балки :
Ширина опоры вверху :
Ширина опоры внизу назначается из интервала 03 06 м.
Габаритная длина моста :
где – вылет консоли м:
Габаритная ширина крана :
Габаритные размеры тележки принимаются по ГОСТ 7352-81:
внутренний габарит тележки
наружный габарит тележки
высота ходовой тележки
По исходным данным и полученным размерам по ГОСТ 7352-81 «Краны козловые электрические. Типы основные параметры и размеры» выбран прототип: кран козловой электрический общего назначения с электрической талью грузоподъемностью 32 т ККТ-32.
Монтаж крана осуществляется монтажными электролебедками путем стягивания и поворотом опор относительно шарниров соединяющих опоры с пролетным строением крана [1].
Принимаем прототип крана: кран козловой электрический общего назначения с электрической талью грузоподъемностью 32 т ККТ-32.
[6]. Техническая характеристика крана представлена в таблице 1.
Таблица 2.1 – Техническая характеристика прототипа
Основные размеры крана представлены на рисунке 2.1.
Рисунок 2.1 – Основные размеры козлового крана.
Расчет механизма подъема груза
1. Выбор типа крюковой подвески
Крюковые подвески предназначены для соединения грузозахватного органа (в частности крюка) с канатом механизма подъёма.
Основные типы крюковых подвесок: нормальные укороченные и с разнесёнными блоками.
Укороченные подвески имеют меньший размер по высоте по сравнению с нормальными и применять их рекомендуется на кранах с малой высотой подъёма при четной кратности полиспаста. Подвески с разнесёнными блоками применяются на кранах с большой высотой подъёма (преимущественно башенных) с целью исключения скручивания канатов подвески.
По справочнику [3] выбираем крюковую подвеску нормальной длины.
1.1 Выбор кратности полиспаста
На конструкцию механизма подъема оказывает существенное влияние тип и кратность полиспаста. Увеличение кратности усложняет конструкцию и приводит к дополнительным потерям мощности. Малая кратность существенно повышает грузовой момент на барабане увеличивает массу размеры и стоимость механизма.
У козловых кранов где канат наматывается на барабан минуя направляющие блоки требуется строго вертикальный подъем груза. Для этого применяются сдвоенные полиспасты. [1].
Выбор кратности полиспаста производится в зависимости от грузоподъемности крана. Для сдвоенного полиспаста при грузоподъемности 20 т принимается кратность полиспаста uп = 4 [8]. Схема запасовки каната для кратности полиспаста uп=4 приведена на рисунке 3.1.
Рисунок 3.1 – Схема запасовки каната
где – КПД блока (=098 [4]).
Крюк подбирается по ГОСТ 6627-74 по заданной грузоподъемности с учетом режима работы механизма.
Поскольку в задании особых условий не оговорено принят однорогий крюк. Длина крюка зависит от типа крюковой подвески. Поскольку принята нормальная подвеска принимаем крюк типа А.
Для группы режима работы 2М с грузоподъемностью Q = 20 т принимается однорогий кованый крюк № 19 ([8]).
Рисунок 3.2 – Эскиз хвостовика крюка
Таблица 3.1 – Основные размеры и наибольшая грузоподъемность крюка
Наибольшая грузоподъемность крюка для группы
Диаметр ненарезанной шейки хвостовика d1 мм
Длина нарезанной части хвостовика с шейкой l1 мм
2 Расчет и выбор каната
Наибольшее натяжение каната Fк Н:
где Q – грузоподъемность крана кг (Q=20000 кг);
g – ускорение свободного падения мс2 (g=981 мс2);
N – число ветвей каната навиваемых на барабан (N=2);
uп – кратность полиспаста (uп=4);
П – число направляющих блоков (П=0 т.к. направляющие блоки отсутствуют).
Разрывное усилие каната F Н:
где – минимальный коэффициент использования каната (для режима работы 3М 5[4]).
По справочнику [8] выбираем канат. Принимаем канат двойной свивки типа: ЛК–О конструкции 6х19 с одним органическим сердечником по ГОСТ 3077 - 80. Диаметр каната dК равен 14 мм разрывное усилие Fст = 1165 кН.
Условное обозначение принятого каната:
Канат 14-Г-II-Л-Н-1960 ГОСТ 3077-80.
3 Определение размеров барабана
Принят нарезной барабан с однослойной навивкой.
Рисунок 3.2 – Эскизная компоновка барабана
Диаметр барабана по наружной поверхности Dб мм:
где h1 – коэффициент выбора диаметра барабана (для режима работы 3М h1=18[4]).
Полученное значение Dб округляют в большую сторону до стандартного значения из нормального ряда диаметров. Примем
Диаметр по средней линии навиваемого каната D мм:
Полная длина двухканатного барабана Lб м:
где Lр – длина рабочей части барабана м;
Lк – длина участка необходимого для закрепления каната на барабане м;
Lн – длина ненарезанной части барабана м.
Длина рабочей части барабана Lр м:
где – число рабочих витков на барабане;
– число запасных витков ([4]);
– шаг навивки каната на барабан мм.
Число рабочих витков на барабане :
Шаг навивки каната на барабан мм:
Длина участка необходимого для закрепления каната на барабане м:
Длину ненарезанной части барабана примем равной 150 мм. Тогда полная длина барабана Lб м:
Толщина стенки барабана мм определяется по эмпирической формуле:
Диаметр реборды Dрб мм:
Принятый барабан проверяется на соотношение длины Lб и диаметра Dб барабана. Рассчитанные параметры барабана принимаются окончательно если выполняется условие:
Условие (3.13) не нарушено. Рассчитанные параметры барабана принимаем окончательно.
4 Определение потребной мощности. Выбор двигателя
Максимальная статическая мощность двигателя Pст max Вт:
где – грузоподъемность т ();
– скорость подъема груза мс ();
– КПД привода ( [4]);
– КПД полиспаста ().
Номинальная мощность двигателя может быть принята меньше максимальной статической так как эквивалентная мощность развиваемая двигателем при работе с грузом разного веса и зависящая от использования механизма по грузоподъёмности всегда меньше [5]. Учитывая это для кранов общего назначения можно принять:
По справочнику [8] по номинальной мощности Рдв выбираем трехфазный асинрхонный электродвигатель с короткозамкнутым ротором 4А250M8У3. Характеристики двигателя представлены в таблице 3.1.
Таблица 3.1 – Характеристики двигателя
Мощность на валу кВт
Частота вращения обмин
Момент инерции ротора кг.м2
Номинальный момент двигателя :
5 Кинематический расчет механизма
Кинематическая схема лебедки приведена на рисунке 3.4.
Рисунок 3.4 – Кинематическая схема лебедки
Частота вращения барабана nб обс:
Общее передаточное отношение u:
6 Выбор редуктора и соединительных муфт
С учетом требуемого передаточного числа частоты вращения быстроходного вала и мощности на быстроходном валу редуктора принимаем двухступенчатый горизонтальный цилиндрический редуктор Ц2–650. Параметры редуктора представлены в таблице 3.2 [8].
Таблица 3.2 – Характеристики редуктора
Фактическое передаточное
Частота вращения быстроходного вала
Мощность на быстроходном валу
Диаметр быстроходного вала
6.2 Выбор соединительных муфт
Для соединения вала двигателя с быстроходным валом редуктора используем муфту имеющую на приводном валу тормозной шкив. Для смягчения ударных нагрузок рекомендуется устанавливать упругие муфты. Кроме этого тихоходный вал редуктора выполнен в виде зубчатой полумуфты которая соединяется со второй полумуфтой являющейся отъемным фланцем барабана крепящегося к нему при помощи болтов. Выбор муфт ведут по расчетному крутящему моменту с учетом диаметров соединяемых валов.
где k1 – коэффициент учитывающий степень ответственности механизма (k1=12 [4]);
k2 – коэффициент учитывающий режим работы механизма
– наибольший статический момент на валу муфты Нм.
Наибольший статический момент на быстроходном валу
Необходимые при выборе муфты геометрические параметры представлены в таблице 3.3.
Таблица 3.3 – Геометрические параметры электродвигателя и редуктора [марон]
Для соединения вала электродвигателя и быстроходного вала редуктора принимается муфта упругая втулочно-пальцевая с тормозным шкивом. Основные характеристики выбранной муфты представлены в таблице 3.4.
Таблица 3.4 – Основные характеристики втулочно-пальцевой муфты [8]
Наибольший передаваемый крутящий момент Нм
Ширина тормозного шкива Bт мм
Момент инерции муфты
Наибольший статический момент на тихоходном валу
Основные размеры тихоходного вала редуктора выполненного в виде зубчатой полумуфты представлены в таблице 3.5.
Таблица 3.5 – Основные размеры тихоходного конца вала редуктора выполненного в виде зубчатой полумуфты [8]
7. Проверка двигателя на надежность пуска
Выбранный двигатель проверяется на надежность пуска по ускорению подъема груза.
Фактическое ускорение при пуске мс2:
где tп – время пуска с.
где d – коэффициент учитывающий неучтенные вращающиеся и поступательно движущиеся массы механизма подъема груза (d = 11 [4]);
– угловая скорость вращения вала двигателя ;
Iр – момент инерции ротора двигателя кг×м2 (Iр = 136 кг×м2);
Iм – момент инерции муфты с тормозным шкивом кг×м2 (Iр = 225 кг×м2);
Iгр – момент инерции груза приведенный к валу двигателя кг×м2
Тср. п – средне-пусковой момент двигателя Н×м
Условие надежного пуска двигателя:
где а – наибольшее допустимое ускорение механизма подъема груза мс2
(а = 07 мс2 для кранов работающих при массовых перегрузочных
Условие (3.26) выполняется следовательно двигатель выбран правильно.
8. Определение тормозного момента. Выбор тормоза
Тормоз выбирается по необходимому тормозному моменту и диаметру тормозного шкива выбранной втулочно-пальцевой муфты.
Необходимый тормозной момент :
где k – коэффициент запаса торможения (для режима работы 3М k = 15 [4]).
Принимаем тормоз колодочный с одноштоковым электрогидротолкателем ТКГ-400 . Технические характеристики тормоза представлены в таблице 3.6.
Таблица 3.6 – Технические характеристики тормоза
Диаметр тормозного шкива Dт мм
Наибольший тормозной момент
9 Прочностные расчеты узла барабана
Примем материал барабана чугун СЧ-20. Барабан не потеряет прочность если будет выполняться условие:
где – приведенные напряжения МПа;
– допускаемые напряжения МПа (для режима работы 3М ).
Приведенные напряжения :
где – напряжения сжатия МПа;
– напряжения изгиба МПа;
– касательные напряжения при кручении МПа.
Схема нагружения барабана представлена на рисунке 3.5.
Рисунок 3.5 – Схема нагружения барабана
Напряжения сжатия при однослойной навивке :
При определении напряжений изгиба барабан принимаем как балку на двух опорах нагруженную двумя силами .
где – максимальный изгибающий момент Нм;
– момент сопротивления поперечного сечения барабана м3.
Момент сопротивления поперечного сечения барабана м3:
Для определения максимального изгибающего момента определим реакции опор и . Из схемы нагружения видно что
Максимальный изгибающий момент на участке E-D.
Касательные напряжения при кручении барабана :
где – крутящий момент на барабане кНм;
– полярный момент инерции м3.
Крутящий момент на барабане для двухканатного барабана кНм:
Полярный момент инерции м3:
Условие (3.28) выполняется значит барабан выдержит приложенные нагрузки.
10 Расчет крюковой подвески
Выбранный крюк проверяется на разрыв в сечении по резьбе хвостовика при этом должно соблюдаться условие:
где d0 – внутренний диаметр резьбы хвостовика мм (d0 = 70 мм);
sp доп – допускаемые напряжения на разрыв МПа:
где sт – предел текучести материала МПа (для стали 20 sт=250 МПа);
n – запас прочности крюка при растяжении (для режима работы 3М n =20[8]).
sp доп = 2502=125 МПа.
Условие (3.37) выполняется следовательно прочность крюка достаточна.
10.2 Подбор подшипника крюка
Подшипник подбирается по статической грузоподъемности и ненарезанной шейки крюка.
Статическая грузоподъемность Qст кН:
Qст = 12×20×981 = 23544 кН.
Принимается упорный однорядный шарикоподшипник легкой серии 8118 Н со статической грузоподъемностью С0=280 кН внутренним диаметром dп=90мм и наружным Dп=120мм высотой Нп=20 мм [9].
10.3 Эскизная компоновка подвески
Эскизная компоновка выполняется с целью предварительного определения размеров необходимых для проведения прочностных расчетов элементов подвески.
Ширина траверсы В мм:
В = Dп + (10 50) мм. (3.40)
В = 120 + 30 = 150 мм.
Высота траверсы h мм:
H = l1 + l2 – (H1 + H) (3.41)
Н1 – высота подшипника крюка мм (Н1 = 20 мм);
H – высота гайки крюка мм (Н = 100 мм).
h = 250 + 150 – (38 + 275) = 87 мм.
Диаметр отверстия в траверсе под хвостовиком крюка dт мм:
dт = d + (2 3) мм. (3.42)
dт = 87 + 3 = 90 мм.
Диаметр цапфы dц мм:
dц = (07 10)h. (3.43)
Часть элементов принимается конструктивно в зависимости от грузподъемности:
толщина щеки d1 принимается равной 15 мм [6];
расстояние между блоками принимается равным 10 мм [6];
расстояние между блоками и внутренней поверхностью щеки принимается равным 10 мм [4];
где h2 – коэффициент выбора диаметра основного блока (при 3М h2=20 [4]).
Принимаем . По справочнику выбираем блок ОБК–1 основные размеры которого приведены на рисунке 3.6.
Рисунок 3.6 – Блок крановый
Эскизная компоновка крюковой подвески представлена на рисунке 3.7.
Рисунок 3.7 – Эскизная компоновка крюковой подвески.
Организация надзора за безопасной эксплуатацией грузоподъемных машин
Мероприятия по организации надзора и обслуживания можно представить в виде трех блоков: люди техника документы.
Правильно (безопасно) обслуживать грузоподъемные машины могут только специально обученные люди (инженерно-технические работники).
На предприятии где в производстве используются грузоподъемные машины должны быть назначены лицо ответственное по надзору за безопасной эксплуатацией грузоподъемных машин лицо ответственное за исправное состояние грузоподъемных кранов лица ответственные за безопасное производство работ кранами.
Ответственным по надзору может быть назначен главный инженер технический директор руководитель предприятия. Ответственным за исправное состояние – главный механик главный энергетик. Ответственным за безопасное производство работ – мастер прораб начальник цеха иногда бригадир.
Ответственные лица назначаются приказом по предприятию после прохождения обучения в специализированных организациях имеющих лицензию на этот вид деятельности.
Повторная проверка знаний этих лиц производится раз в три года а для ответственных за безопасное производство работ дополнительно ежегодно комиссией предприятия. Для этого на предприятии создается постоянно действующая комиссия в составе: ответственный по надзору ответственный за исправное состояние инженер по технике безопасности и представитель профсоюзной организации.
Фамилия и номер удостоверения ответственного за исправное состояние вписывается в паспорт крана. Во время отсутствия ответственных лиц приказом назначаются лица их заменяющие (тоже аттестованные по всем правилам).
Обслуживают грузоподъемные машины крановщики помощники крановщиков если инструкция по обслуживанию крана предусматривает наличие крановщика стропальщики слесари-ремонтники грузоподъемных машин электромонтеры наладчики приборов безопасности. Весь обслуживающий персонал проходит обучение и аттестацию и назначается приказом по предприятию. Условия необходимые для назначения на вышеперечисленные должности следующие: возраст не моложе 18 лет медицинское освидетельствование на соответствие физических возможностей характеру работ обучение в учреждениях имеющих лицензию аттестация в комиссии учебного заведения причем при аттестации крановщиков и их помощников необходимо присутствие инспектора Росгортехнадзора. По результатам аттестации крановщикам выдается удостоверение в котором указаны типы и индексы кранов на которых он может работать. В удостоверении должно быть фото и росписи председателя комиссии и инспектора Росгортехнадзора. Удостоверение должно быть все время при работнике во время производства работ.
При переходе на другое место работы проводится повторная проверка по требованию ответственного по надзору или инспектора.
Крановщики и помощники при перерыве в работе больше года аттестуются в комиссии предприятия после этого стажируются для восстановления профессиональных навыков.
На предприятии должна быть создана ремонтная служба. Установлен порядок периодических осмотров технических обслуживаний и ремонтов обеспечивающих содержание в исправном состоянии грузоподъемных машин съемных грузозахватных приспособлений крановых путей и тары.
На предприятии где производятся работы грузоподъемными машинами разрабатываются следующие документы: инструкции для ответственных лиц и обслуживающего персонала проекты производства работ технологические карты (при производстве погрузочно-разгрузочных работ) технические условия на погрузочно-разгрузочных работах схемы строповок (для нестандартного груза) журналы учета работ для каждого крана журналы учета съемных грузозахватных приспособлений.
Титульник.doc
Кафедра «Механизация путевых погрузочно-разгрузочных и
Курсовой проект по дисциплине
«Подъемно-транспортные машины»
Пояснительная записка
ПТМ.МС313.18.00.00.00 ПЗ
профессор студент гр. МС- 313
Назначение машины краткое описание ее устройства и работы.
Описание управления машиной и устройств безопасности 4
Определение основных параметров крана. Выбор прототипа 8
Расчет механизма подъема груза 10
1 Выбор типа крюковой подвески 10
1.1 Выбор кратности полиспаста 10
1.2 Подбор крюка 11
2 Расчет и выбор каната 12
3 Определение размеров барабана 12
4 Определение потребной мощности. Выбор двигателя 14
5 Кинематический расчет механизма 15
6 Выбор редуктора и соединительных муфт 16
6.1 Выбор редуктора 16
6.2 Выбор соединительных муфт 16
7 Проверка двигателя на надежность пуска 17
8 Определение тормозного момента. Выбор тормоза 18
9 Прочностные расчеты узла барабана 19
10 Расчет крюковой подвески 21
10.1 Расчет крюка 21
10.2 Подбор подшипника крюка 21
10.3 Эскизная компоновка подвески 21
Организация надзора за безопасной эксплуатацией
грузоподъемных машин. 24
Список литературы 26
Александров М.П. Подъемно-транспортные машины. М. 1985 520 с.
Гохберг М.М. Справочник по кранам. Л.: Машиностроение. 1988. 536 с. Том I.
Гохберг М.М. Справочник по кранам. Л.: Машиностроение. 1988. 559 с. Том II.
Филатов А.П. Тимофеев Г.Ф. Анферов В.Н. Грузоподъемные машины: методические указания к практическим занятиям. Новосибирск 2000. 46 с.
Казак С.А. Курсовое проектирование грузоподъемных машин. М. 1989.
Вайнсон А..А. Подъемно – транспортные машины строительной промышленности. Атлас конструкции. М.1976. 150 с.
СТП СГУПС 01.01-2000. Курсовой и дипломный проекты. Требования к оформлению. Новосибирск 2000. 40 с.
Кузьмин А.В. Марон Ф.Л. Справочник по расчетам механизмов подъемно-транспортных машин. Минск. 1983. 351.
Проектирование механических передач С. А. Чернавский Б. А. Снесарев и др. М. 1984. 560 с.
Кинем.схема лебедки подъема.dwg

Сопромат барабана.dwg

Желоб блока.dwg
