Кран консольный настенный поворотный, г/п 1.6 т.




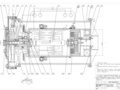
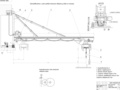
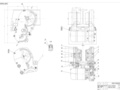
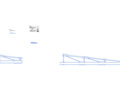
- Добавлен: 25.10.2022
- Размер: 1 MB
- Закачек: 0
Описание
Состав проекта
![]() |
![]() ![]() ![]() ![]() |
![]() ![]() ![]() |
![]() ![]() ![]() |
![]() ![]() ![]() |
![]() ![]() ![]() ![]() |
![]() ![]() ![]() |
![]() ![]() ![]() ![]() |
![]() ![]() ![]() |
![]() ![]() ![]() |
![]() ![]() ![]() ![]() |
Дополнительная информация
Общий вид_.dwg

Механизм подьема_.dwg

Механизм передвижения_.dwg

Металоконструкция_.dwg

Рекомендуемые чертежи
- 25.10.2022
- 25.10.2022