Конвейер ленточный курсовой проект




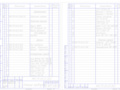

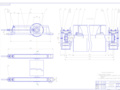
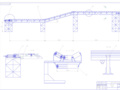
- Добавлен: 25.10.2022
- Размер: 2 MB
- Закачек: 0
Описание
Состав проекта
![]() |
![]() |
![]() ![]() |
![]() ![]() |
![]() ![]() |
![]() ![]() |
![]() ![]() |
![]() ![]() |
![]() ![]() |
![]() |
![]() ![]() ![]() ![]() |
![]() |
![]() ![]() ![]() ![]() |
![]() ![]() ![]() ![]() |
![]() ![]() ![]() ![]() |
![]() |
![]() ![]() ![]() ![]() |
![]() ![]() ![]() ![]() |
![]() ![]() ![]() ![]() |
![]() |
![]() |
![]() ![]() |
![]() ![]() |
![]() ![]() |
![]() ![]() |
![]() ![]() |
![]() ![]() |
![]() ![]() ![]() |
![]() |
![]() ![]() ![]() ![]() |
![]() ![]() ![]() ![]() |
![]() ![]() ![]() ![]() |
![]() ![]() ![]() ![]() |
![]() ![]() ![]() ![]() |
![]() ![]() ![]() ![]() |
Дополнительная информация
Лист 1.dwg

Лист 3-2.dwg

роликооопоры 111.dwg

Лист 4.dwg

Лист 5.dwg

Лист 2.dwg

Лист 3-1.dwg

Спецификация2.dwg

Спецификация5.dwg

Спецификация1.dwg

Спецификация31.dwg

Спецификация4.dwg

Спецификация32.dwg

Рекомендуемые чертежи
Свободное скачивание на сегодня
Другие проекты
- 29.08.2014