Консольный поворотный кран




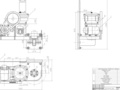
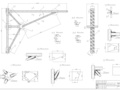
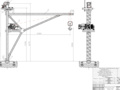
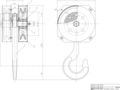
- Добавлен: 25.10.2022
- Размер: 3 MB
- Закачек: 0
Описание
Состав проекта
![]() |
![]() ![]() ![]() |
![]() ![]() ![]() |
![]() ![]() ![]() ![]() |
![]() ![]() ![]() ![]() |
![]() ![]() ![]() ![]() |
![]() ![]() ![]() |
![]() ![]() ![]() ![]() |
![]() ![]() ![]() |
![]() ![]() ![]() |
![]() ![]() ![]() |
Дополнительная информация
КП.расчет консольного поворотного крана с постоянным вылетом.doc
2 Режим работы механизма .. . 3
3 Режим работы электрооборудования . 3
4 Расчет двигателя . 4
5 Расчетные нагрузки и расчетное число нагружений . . .. 6
Выбор двигателя и определение передаточного числа механизма поворота . 7
1 Режим работы электрооборудования .. 7
2 Выбор двигателя и определение передаточного числа механизма . 8
3 Передпточное число механизмов .. 11
Определение расчетных нагрузок и расчетного числа нагружений деталей механизма поворота .. .. 12
Расчет передач механизма поворота . .. 14
1 Расчет червячной передачи .. . 14
2 Определение размеров второй и третей передачи .. 17
3 проверочный расчет передачи . . 19
Расчет фрикциона .. 21
Расчет валов механизма поворота 25
Расчет опорных подшипников механизма поворота 29
1 Подшипники первого вала редуктора . . 29
2 Подшипники второго и третьего вала .. 32
Тормоз механизма поворота .. 33
Расчет металлической конструкции 34
1 Первый расчетный случай .. .. 35
2 Второй расчетный случай . 39
3 Опорная рама .. 41
Список литературы . 45
Подъемно-транспортные машины являются важнейшим оборудованием для механизации работ во всех отраслях народного хозяйства – в промышленности строительстве на транспорте; применяются для перемещения людей.
В современных условиях поточного и автоматизированного производства значение подъемно-транспортных машин изменилось. Они вышли за рамки своего первоначального назначения – вспомогательного оборудования для механизации трудоемких процессов производства — и являются связующими звеньями в технологической цепи обеспечивающими непрерывность производства.
Данный курсовой проект является одним из основных в общеинженерной подготовке студентов он способствует развитию конструкторских навыков. На примере расчета консольного поворотного крана с постоянным вылетом усваиваются основные виды расчета кранов закрепляются теоретические знания.
РАСЧЕТ МЕХАНИЗМА ПОДЪЕМА ГРУЗА
1 Режим работы механизма. В соответствии с условиями работы цеха кран используется в течение всего года (300 рабочих дней) при двухсменной работе. Коэффициент использования крана в течение года по формуле (2 1-ст.7):
где =300 – число дней работы механизма в году.
Коэффициент использования крана в течение суток:
где =14 – число часов работы механизма в сутки.
Коэффициент использования грузоподъемности Кгр=075 (кран работает с грузами одинаковой массы q = 6 т).
Исходя из этих коэффициентов по [табл. 2 1-ст.7 ]должен быть назначен тяжелый режим работы механизма этот же режим должен быть принят и для крана в целом.
2 Режим работы электрооборудования. Продолжительность включении механизма по формуле (4)
где t2 t4 t6 t8 — время работы механизма в течение цикла; Т — общая продолжительность цикла [табл. 46 1-ст.7 ].
Число рабочих включений за один цикл в соответствии с данными табл. 46 Z’вк=4. Учитывая необходимость в дополнительных (регулировочных)
включениях принимаем Z’вк=6.
Число рабочих циклон в час
число включений и час
Zвк=aц× Z’вк=26×6=156.
Заданная температура помещения где работает край t=20o С.
По [табл. 3 1-ст.8 ] найденным коэффициентам использования крана и продолжительности включении 30% соответствует тяжелый режим работы электрооборудования исходя из которого должна быть выбрана необходимая аппаратура управления краном.
3 Расчет двигателя. Поскольку график работы крана известен расчет необходимой мощности двигателя производим по среднеквадратичной нагрузке. Величина этой нагрузки исходя из формулы (69 1-ст.29) и обозначений принятых в табл. 46
где Рп — нагрузка механизма при пуске;
Рп=Qср=6000×15=9000 кгс;
ср =1516 — средний коэффициент пусковой перегрузки двигателя.
Необходимая мощность двигателя по формуле (63 1-ст.28) при Р = Рэ
где о — к. п. д. механизма принятый по [табл. 23 1-ст.68]
Необходимая мощность двигатели при продолжительности включения 25% ближайшей к подсчитанной по формуле (70)
В соответствии с этой мощностью на кране установлен двигатель типа МТF 411-6 мощностью Nд = 22 кВт при ПВ = 25% с частотой вращения пд = 965 обмин и предельным моментом Мпр. Выбранный двигатель далее проверяем по условию пуска.
Необходимая мощность двигателя при подъеме номинального груза q = 6000 кгс
Рабочий момент от массы груза приведенный к валу двигателя
Наименьший пусковой момент двигателя
где — наименьший коэффициент пусковой перегрузки.
Наибольший пусковой момент двигателя определяем из условия чтобы продолжительность пуска механизма исходя из графика работы крана была не более 15 с. Маховой момент механизма и груза равен:
Момент сил инерции при заданном времени пуска по формуле (10 1-ст.11) при
где - время пуска (или торможения) с.
Средний пусковой момент двигателя исходя из формулы (16 1-ст.11)
Мср =Мс+ Ми=198+203=2183 кгс×м.
Необходимый наибольший пусковой момент двигателя
Мmax =2Мср-Мmin =2×2183-2188= кгс×м.
Номинальный момент двигателя при ПВ = 25%
Окончательно принятый наибольший коэффициент пусковой перегрузки двигателя что соответствует моменту
В данном случае фактическое время пуска будет менее требуемого tп=15 с.
4 Расчетные нагрузки и расчетное число нагружений. За расчетную принимаем нагрузку от массы номинального груза q = 6000 кг. Расчетное число нагружений механизма в данном случае определяется по заданному графику работы крана [табл. 45 1-ст.198].
Для первого вала редуктора выполненного за одно целое с шестерней по [табл. 13 1-ст.22] принимаем расчетный срок службы A = 8 лет. Общее число часов работы этого вала при принятых выше коэффициентах использовании крана Кг и Кс по формуле
T=8760×A×Кг×Кс=8760×8×085×059=35200 ч .
Число нагружений вала при расчете на изгиб по формуле
Z0=60Tn=60×38200×965×03=66×107.
где n – частота вращения обмин; – относительная продолжительность включения механизма; Т – заданное время.
Как видно из табл. 46 это число нагружений распределяется поровну между рабочими и нерабочими нагрузками. Коэффициент приведения к расчетному числу циклов при m= 9 определяем по формуле (49)
где = 250 кг — масса грузозахватного приспособления принятая выше.
Расчетное число нагружений по формуле
Zp=Z0φпр=66×107×05=33×107
Согласно данным приведенным выше принимаем число подъемов в час aп=26 число нагружений за один подъем ан=1. Общее число нагружений вала при расчете на кручение в этом случае согласно формуле (49)
Z’0=Tanaн=35200×26×1=92×105
Расчетное число нагружений
Zрк=Z’0φпр=92×105×05=46×105
ВЫБОР ДВИГАТЕЛЯ И ОПРЕДЕЛЕНИЕ ПЕРЕДАТОЧНОГО ЧИСЛА МЕХАНИЗМА ПОВОРОТА
1 Режим работы электрооборудования. Продолжительность включения рассчитываемого механизма по формуле (4)
где — продолжительность работы механизма в течение цикла; Т — общая продолжительность цикла (табл. 46).
Исходя из условий работы крана указанных в табл. 46 имеем число включений за один цикл Z”вк=2; с учетом дополнительных (регулировочных) включении принято Z”вк=3.
Расчетное число включений при числе циклов ац=26
Zвк= ац Z'вк=26×3=78
Для принятых выше коэффициентов использовании крана Кг=085 Кc=059 и Кгр=075 и найденной продолжи
тельности включения должен быть принят тяжелый режим работы электрооборудования. Поэтому режиму производится подбор аппаратуры управления краном.
2 Выбор двигателя и определение передаточного числа механизма. Необходимую мощность двигателя определяем исходя из заданного времени пуска tп которое на основании табл. 46 выбрано равным 15 с.
Для последующих расчетов предварительно выбираем массу поворотной части крана G=3000 кг; предварительно принятые диаметры верхней и нижней цапф d=d1=70 мм. Расстояние от центра тяжести до оси вращения крана предварительно выбранное по компоновочному чертежу l=15 м.
Горизонтальные нагрузки на опоры крана по схеме приведенной на рис. 74
где h — расстояние между верхней и нижней опорами.
Вертикальная нагрузка на нижнюю опору
Рабочий момент необходимый для поворота крана при установившемся движении
где =0l — принятый коэффициент трения для опор скольжения.
Мощность необходимая для поворота крана при установившемся движении по формуле (64)
Здесь n=1 — частота вращения крана обмин; — к. п. д. механизма принятый по [табл. 23 1-ст.68].
Маховой момент крана с грузом предварительно определяем из условия
Момент сил инерции при заданном времени пуска tп=15 с по формуле (10 1-ст.11) при =
Необходимый пусковой момент двигателя по формуле (67 1-ст.28)
Коэффициент 12 учитывает дополнительные нагрузки от сил инерции механизма (ротор двигателя тормозная муфта и т. п.). Пусковая мощность двигателя по формуле (64 1-ст.28) при М=M1
Предварительно принимаем средний коэффициент пусковой перегрузки двигателя ср=15 [см. п. 6 1-ст.28]. Необходимая мощность Двигателя в этом случае
Мощность двигателя при продолжительности включения 25% указанной в каталоге и ближайшей к требуемой (ПВ= 19%). по формуле (70)
В рассчитываемом механизме установлен двигатель типа MTF012-6 мощностью =27 кВт при ПВ=25% с частотой вращении =840 обмин.
Маховой момент ротора двигателя =012 кгс×м2 максимальный (предельный) момент Мпр=67 кгс×м. Этот двигатель дополнительно проверяем по условиям пуска. При этом расчете уточняем выбранную величину махового момента крана с грузом исходя из схемы приведенной на рис. 75. Маховые моменты отдельных элементов крана при этом будут равны:
стержень 1 (верхний пояс фермы крана)
стержень 2 (нижний пояс фермы)
маховые моменты остальных масс не учтенные в расчете
В приведенных формулах G1 G2 и G0 — массы соответствующих элементов конструкции.
Общий маховой момент крана с грузом
Величина этого момента приведенная к валу двигателя по формуле (14)
Принятый диаметр тормозной муфты DT=200 мм ее маховой момент по табл. XXIII =04 кгс×м2. Общий маховой момент механизма приведенный к валу двигателя по формуле (15)
где - маховые моменты ротора двигателя и тормозной муфты; - маховые моменты массы крана с грузом.
Принимаем далее наибольший и наименьший коэффициенты пусковой перегрузки двигателя max=22 и min = 12 (1-ст.31).
Средний коэффициент пусковой перегрузки в этом случае
Номинальный момент выбранного двигателя
Наибольший пусковой момент двигателя
что менее предельного момента =67 кгс×м.
Средний пусковой момент по формуле (80)
Рабочий момент приведенный к валу двигателя
Избыточный момент (момент сил инерции)
Фактическое время пуска при выбранном двигателе по формуле (82)
3 Передаточное число механизма. Необходимое передаточное число при частоте вращения крана п=2 обмин
В рассчитываемом механизме принята трехступенчатая передача с передаточными числами =28 (червячная передача) =43 и =68 (передачи цилиндрическими зубчатыми колесами).
ОПРЕДЕЛЕНИЕ РАСЧЕТНЫХ НАГРУЗОК И РАСЧЕТНОГО ЧИСЛА НАГРУЖЕНИЙ ДЕТАЛЕЙ МЕХАНИЗМА ПОВОРОТА
Исходя из найденных выше коэффициентов использования крана Кг= 085 Кс=059 и Кгр=075 по табл. 2 за расчетный должен быть принят тяжелый режим работы механизма. Расчет производим по двум случаям нагрузки: рабочей (первый расчетный случай) и предельной (второй расчетный случай). При расчете деталей на усталостную прочность при изгибе (валы зубчатые колеса) по первому расчетному случаю исходим из среднего пускового момента двигателя. Этот момент на первом валу редуктора по формуле (17)
где Мс — рабочий момент; Ми — момент сил инерции приведенный к валу редуктора; и — маховые моменты подсчитанные выше. Коэффициент 11 учитывает влияние масс расположенных за первым валом.
Момент на втором валу редуктора
Здесь u1 и 1 — передаточное число и к. п. д. червячной передачи. Аналогично подсчитываются моменты на третьем и четвертом валах (табл. 47).
Момент на третьем валу редуктора
Расчет валов на кручение и проверку на статическую прочность на изгиб и кручение для первого расчетного случая производим исходя из наибольшего пускового момента двигателя Mmax=65 кгс×м. Избыточный момент имеющий место при этом
Mи=Mmax- Mc=65-012=638 кгс×м.
Расчетный момент на первом валу редуктора при проверке на
усталостную прочность
Расчетный момент на этом валу при проверке на статическую прочность по первому расчетному случаю
где — динамический коэффициент.
Ввиду возможности заедания фрикциона в ряде случаев имеющего место при эксплуатации расчет по второму расчетному случаю производим исходя из предельного момента двигателя Мпр=67 кгс×м.
Расчетный момент с учетом динамического коэффициента
Моменты на последующих валах определенные аналогично приведенным выше даны в табл. 47.
При подсчете числа нагружений первого вала по табл. 13 принимаем расчетный срок его службы А=8 лет. Число часов работы для принятых выше коэффициентов использования крана Кг = 085 и Кс=059 по формуле (44)
Т = 8760А Кг Кс=8760×8×085×059=35200 ч.
Расчетное число нагружений Zp по формуле (48) при изгибе (Zp1= Z0)
где и — средняя продолжительность включения и расчетное число
Число нагружений второго и третьего валов:
Расчетное число нагружений валов при кручении сроке службы 10 лет и числе часов работы = 35200 = 44000 ч.
Это число нагружений остается одинаковым для всех валов.
РАСЧЕТ ПЕРЕДАЧ МЕХАНИЗМА ПОВОРОТА
1 Расчет червячной передачи. Как и в зубчатых передачах расчет на контактную прочность производим по среднему пусковому моменту на червячном колесе М2=8800 кгс×см. Прилитое число заходов червяка z1=2. Число зубьев колеса при этом числе заходов и передаточном числе передачи u=28
В качестве материала червяка принята углеродистая конструкционная сталь 45 с поверхностной закалкой до твердости HRC 45—50. Обод червяка колеса одновременно является кольцом фрикционного устройства (см. рис. 77) и вы полней из бронзы марки БрАЖ9-4-Л с пределом прочности в=4000 кгссм2.
Из конструктивных соображений возможности размещения конуса фрикциона в рассчитываемой передаче) выбран модуль т=63 мм (табл. 25). Принятый коэффициент диаметра червяка q=dm=10
Межосевое расстояние соответствующее выбранным величинам q и z2
по формуле (2) табл. 48
Принято =210 мм В соответствии с этим расстоянием исходя из [табл. 48 1-ст.218] определяем необходимую величину коэффициента смещения инструмента
Диаметр начального цилиндра червяка по формуле (6) табл. 48
Начальный диаметр колеса
Средние диаметры вершин и впадин колеса:
Диаметры вершин и впадин червяка при коэффициентах высоты головки и ножки ha1=1 и hf1= 12 (рис. 76):
При изготовлении колеса из бронзы АЖ9-4 допускаемые контактные напряжения должны определяться из
условия отсутствия заедания поверхностей зубьев исходя из скорости скольжения
где =098 ( — угол подъема витков червяка);
Допускаемые контактные напряжения []к=1800 кгссм2.
Расчетный момент по формулам
Коэффициент режима работы =12 принят по табл. [10 1-ст.20]; коэффициент =1 и =11.
Необходимое межосевое расстояние по формуле (1) табл. 48
При изготовлении колеса из бронзы ОФ10-1 с пределом прочности в= 20 кгсмм2 допускаемые напряжения могут быть выбраны из условии контактной выносливости соответственно расчетному числу нагружений ZP2=35×105 подсчитанному выше.
Исходя из формулы (114 1-ст.43) имеем
Напряжения в зубьях колеса при среднем пусковом моменте по формуле (7) табл. 47
Коэффициент формы зуба y=049 в данном случае принят по табл. 30 исходя из эквивалентного числа зубьев [формула (8) табл. 48]
Допускаемые напряжения на изгиб для колеса из бронзы АЖ9-4 с
пределом прочности в = 4000 кгссм2 при Zб=1×106 по формуле (115)
Напряжения в зубьях колеса при действии предельного момента M’2=10200 кгс×см (табл. 47)
Запас прочности относительно предела текучести т=2000 кгссм2
Допустимый запас прочности согласно п. 4 [n]~2.
2 Определение размеров второго и третьей передачи. В качестве материала шестерни этой передачи принята углеродистая конструкционная сталь 45 с пределом прочности =61 кгсмм2 и пределом текучести =42 кгсмм2 (см. табл. II). Расчетное число нагружений шестерни подсчитанное выше Zp3=. Моменты на валу шестерни при среднем пусковом моменте двигателя М3=3027 кгс×см при наибольшем пусковом моменте М’3=23320 кгс×cм предельный момент М”3=25600 кгс×см.
Расчетный момент на валу шестерни при расчете на усталостную прочность по формуле (100) при М = М 3
где — предварительно принятый коэффициент нагрузки.
Допускаемые контактные напряжения из условий усталостной прочности по формуле (103)
Величины = 1×107 и m=6 приняты по [табл. 6 1-ст.12].
Ввиду малого числа нагружений зубьев контактные напряжения в рассматриваемом случае определяются из условий статической прочности
(отсутствие остаточных деформаций поверхности зубьев). Предельно допустимые контактные напряжения в зубьях шестерни допускаемые из этого условия при предельном пусковом моменте двигателя по формуле (105)
Эти напряжения приведенные к среднему моменту исходя из формулы (8) табл. 16
В качестве материала колёса принято стальное литье марки 40ЛII с пределом прочности =53 кгсмм2 и пределом текучести т=35 кгсмм2 (см. табл. IV 1-ст.293).
Расчетное число нагружений колеса
Наибольшее допускаемое контактное напряжение при действии предельного момента
Это напряжение приведенное к среднему пусковому моменту
Допускаемые напряжения из условия усталостной прочности
За расчетное принимаем наименьшее из найденных напряжений =8400 кгссм2.
Необходимое межосевое расстояние по формуле (1) [табл. 16 1-ст.38]
Коэффициент 020 принят по табл. 16.
Наименьшая допустимая ширина шестерни
Принято 500 мм ширина шестерни 100 мм.
Начальный диаметр шестерни в соответствии с принятым межосевым расстоянием по формуле (6) табл. 16
Исходя из условий работы передачи (открытая при малой точности установки осей колес) принят модуль т=8 в соответствии с этим суммарное число зубьев колес
Число зубьев шестерни
Принятые чиста зубьев шестерни и колеса: =16 109.
Начальные диаметры шестерни и колеса:
d1 = 16×8 = 128 мм; d2 = 109×8=872 мм.
Согласно п. 8 зацепление следует выполнить со смещением производящего контура; принятые коэффициенты смешения: х1=+03 х2=-0.3.
3 Поверочный расчет передачи. При этом расчете исходя из отношения bd1=100128 = 08 и учитывая консольное расположение шестерни по [табл. 29 1-ст.80] принимаем коэффициент концентрации нагрузки по ширине зуба kкц=13.
Окружная скорость шестерни при частоте вращения n3=13.6 обмни
Динамический коэффициент в соответствии с этой скоростью для передач 8-й степени точности по [табл. 28 1-ст.79] kд=105.
Коэффициент нагрузки по формуле (101)
kн= kкц kд kр=13×105×12=163
где kр=12 — коэффициент режима работы принятый по [табл. 10 1-ст.20].
Поскольку фактическая величина kн близка к ранее выбранной в предварительном расчете далее ограничиваемся проверкой прочности зубьев из условии их изгиба.
Момент на валу шестерни при среднем пусковом моменте двигателя согласно табл. 47 М3=8310 кгс×см. Расчетный момент по формуле (100)
При действии наибольшего пускового момента (с учетом динамического коэффициента kд=13) M’3=13300 кгс×см (табл. 47) имеем
Предел выносливости материала шестерни по формуле (26 1-ст.15)
где =2600 кгс×см2 и =4200 кгссм2 приняты по [табл. II 1-ст.292] величины 6 и т=6 — по [табл. 6 1-ст.15].
В дальнейшем исходим из напряжения оп=4200 кгссм.
Напряжения в зубьях шестерни при среднем и наибольшем пусковых моментах двигателя по формуле (11) [табл. 16 1-ст.38]:
Коэффициент у= 0408 принят по [табл. 30 1-ст.81]
Запас прочности по усталостному разрушению при коэффициенте концентрации k=k0=15 [табл. 12 1-ст.21]
по статическому разрушению при наибольшем пусковом моменте
Допускаемые запасы прочности: в первом случае по [табл. 11 1-ст.20] [n]=16 во втором [n]~22.
Поскольку число нагружений зубьев колеса менее 1×105 его поверочный расчет производится только из условия статической прочности исходя из наибольшего и предельного моментов.
Рассчитываемый фрикцион (рис. 77) состоит из двух стальных конусов 4 расположенных на втором валу редуктора 3 между которыми зажат бронзовый венец 5 колеса червячной передачи. Усилие сжатия конусов создается пружиной 2 и регулируется гайкой 1 в зависимости от требуемой величины предельного момента. Для предохранения от вытекания смазки из редуктора нижняя половина его корпуса имеет прилив 6 верхняя кромка которого расположена выше рабочего уровни масла в редукторе. При расчете фрикциона исходя на возможности размещении конусов в ободе черничного колеса назначаем средний конуса Dc=300 мм и длину его образующей (ширина рабочей конуса) b=50 мм. Во избежание заедания трущихся поверхностей угол при вершине конуса должен отвечать условию >2ρ где ρ — угол трения. Этот угол для стальных конусов работающих по бронзе обычно принимается в пределах 16—25о. В рассчитываемом фрикционе принято =16о
Расчетный момент на валу фрикциона определяем исходя из наибольшего пускового момента двигателя M’2=4710 кгс×см. Числовое значение расчетного момента
где =1.213 — коэффициент запаса.
Необходимое усилие сжатия пружины при этом моменте (рис. 78)
где =006 — коэффициент трения принятый для бронзового обода работающего со стальным конусом при наличии смазки.
Принятые пределы регулирования фрикциона ±20% в соответствии с этим наибольшее сжатие пружины
Рmax=12P=12×573=687 кгс.
Наибольший и наименьший диаметры конуса согласно рис. 78:
Удельное давление на рабочей поверхности конуса
Допускаемое значение этого давлении для стали по бронзе или чугуну может быть принято в пределах 610 кгссм2 для тормозных материалов — до 6 кгссм2.
Пружина фрикциона рассчитывается на статическую прочность по наибольшему усилию Pmax подсчитанному выше.
Учитывая особую ответственность механизма целесообразно применять пружины второго класса.
В качестве материала направляющей шпонки принята сталь 45 с пределом текучести т=3600 кгссм2 (см. табл. II 1-ст.292). Размеры шпонки выбираем по ГОСТ 8768—68 исходя из принятого диаметра вала d=65 мм (рис. 79): ширина шпонки b=18 мм высота h=11 мм. Эти размеры проверяем на статическую прочность из условий среза и смятия паза ступицы исходя из
наибольшего пускового и предельного моментов.
Расчетный момент для первого расчетного случая при коэффициенте γ=12 Mф=5650 кгс×см. Момент передаваемый каждым конусом
Расчетная длина шпонки:
где и — полная длина каждой ступицы.
на нижней ступице (рис. 79)
Допускаемые напряжения смятия по [табл. 49 1-ст.226]:
для верхней ступицы имея в виду возможность ее перемещения под нагрузкой
В обеих формулах — предел текучести наиболее слабого материала в данном случае — шпонки.
Напряжения среза для наиболее нагруженной нижней шпонки
Допускаемые напряжения по табл. 49
Для второго расчетного случая (действие предельного момента) имеем расчетный момент M’’р2=10200 кгс×см. Напряжения смятия на наиболее нагруженной нижней ступице
Допускаемые напряжения для этого случая по табл. 49
см=08т=083600=2860 .
Допускаемые напряжения при пределе текучести материала шпонки =2300 кгссм2 (табл. 49)
Таким образом выбранная шпонка отвечает условиям прочности.
РАСЧЕТ ВАЛОВ МЕХАНИЗМА ПОВОРОТА
Методика расчета валов рассматриваемого механизма одинакова поэтому далее ограничимся рассмотрением расчета первого нала редуктора. Определение нагрузок при расчете этого валя на изгиб производим исходя из момента М2=8800 кгс×см действующего на червячном колесе при среднем пусковом моменте двигателя.
Осевая нагрузка на вал при диаметре колеса d2~353 мм
Принятый угол подъема витков червяка λ=11°19'.
Окружное и радиальное усилия на червяке (рис. 80):
В этих формулах: ρ= 6° — угол трения (tgρ=) соответствующий коэффициенту трения =01; α — угол зацепления.
Нагрузки Р и Р0 действуют в вертикальной плоскости. Опорные давлении от этих нагрузок но схеме приведенной на рис. 80;
Нагрузка на опоры от силы Р0 в горизонтальной плоскости
Наибольшие изгибающие моменты в среднем сечении вала:
в вертикальной плоскости
в горизонтальной плоскости
Равнодействующий момент
Дополнительно к валу приложен крутящий момент Мк=530 кгс×см Приведенный момент по формуле (5) [табл. 17 1-ст.51]
Согласно табл. 17 коэффициент α=1 для симметричного цикла принятого в расчете.
Как было указано выше в качестве материала червяка принята углеродистая конструкционная сталь 45 с поверхностной закалкой до твердости HRC 45-50. Предел выносливости материала сердцевины вала в данном случае принятый по табл. II -1=26 кгсмм2. Для предварительного выбора размеров вала допускаемые напряжения подсчитываем по формуле (39)
Коэффициенты и приняты по [табл. 11 и 12 1-ст.20].
Необходимый диаметр вала в среднем сечении по формуле (7) [табл. 17 1-ст.51].
Концевой участок вала рассчитываем на кручение при наибольшем пусковом моменте двигателя. Расчетный момент для этого случая M’1=530 кгс×см предел выносливости материала вала при кручении по [табл. II 1-ст.292] -1=1300 кгссм2. Допускаемые напряжения
Необходимый диаметр вала по формуле (4) табл. 17
Принятые размеры вала приведены на рис. 81. Поверочный расчет вала производится в сечениях II—II III— III и IV—IV
соответствующих возможному максимуму (с учетом концентрации) напряжений. Этот расчет аналогичен рассмотренному выше для тележки мостового крана.
Для обеспечения правильного зацепления червяка с колесом и необходима дополнительная проверка прогиба рассчитываемого вала от равнодействующей горизонтальной и вертикальной нагрузок Р0=152 кгс и Рр = 189 кгс (рис. 80):
Момент инерции поперечного сечения червяка определенный по диаметру впадин.
Расчетный момент инерции этго сечения с учетом разгружающего влияния витков червяка
где 1.36— поправочный коэффициент ориентировочно определяемый по формуле
и — диаметры вершин и впадин витков червяка.
Поскольку диаметр вала является переменным определяем его расчетную длину приведенную к одному диаметру с моментом инерции J=35.1 см4. Длина концевых участков вала в этом случае будет равна [формула (137)]
где см4 и =105 мм — момент инерции и длина этих участков.
Расчетная (приведенная) длина вала
где =90 мм — длина червяка.
Допускаемая величина этого прогиба согласно
РАСЧЕТ ОПОРНЫХ ПОДШИПНИКОВ МЕХАНИЗМА ПОВОРОТА
1 Подшипники первого вала редуктора. В рассчитываемом механизме вал червяка установлен на радиальных шариковых подшипниках на которые передаются радиальные нагрузки. Осевая нагрузка на вал передастся на дополнительный упорный подшипник установленный на его конце. Поскольку график работы Крана известен подшипники выбираем по эквивалентной нагрузке далее этот расчет рассмотрен на примере радиальных подшипников принятый срок их службы при заданном тяжелом
режиме работы механизма по [табл. 13 1-ст.22] А=5 лет.
Число часов работы крана за этот срок по формуле (44)
Т=8760АКгКс=8760×5×085×059 ч
где Кг и Кс — коэффициенты использования крана принятые выше.
Число часов работы механизма при заданной продолжительности его включения =019
Дальнейший расчет производим по наиболее нагруженному подшипнику расположенному на опоре В (рис. 80). Горизонтальная и вертикальная нагрузки на эту опору RВ=150 кгс R'В = 76 кгс.
Равнодействующая нагрузка
Моменты на рассчитываемой валу при наибольшем пусковом моменте двигателя Mmax=М’1=53 кгс×м при наименьшем пусковом моменте Mmin = 315 кгс×м при среднем моменте М1=397 кгс×м.
Расчетный момент по формуле (130)
Нагрузка на подшипник при этом моменте
Эквивалентная нагрузка но формуле (118)
где 13 — динамический коэффициент принятый по [табл. 32 1- ст.90]
Коэффициент вращении V=1 (вращается внутреннее кольцо подшипника).
Число оборотов вала за весь срок службы при установившемся движении и частоте вращения n=840 обмин по формуле (121)
Нагрузка на подшипник при установившемся движении и рабочем моменте Мс=012 кгс×м
Чисто оборотов вала за время пусков для принятых выше числа включений в час Zвк=78 продолжительности включения tвк=1 с и времени пуска механизма tп=096 с по формуле (129)
Требуемая долговечность подшипника в млн оборотов
L=Lv+Lп=219+620=2252 млн.
Коэффициент приведения к эквивалентной нагрузке по формуле (128)
Приведенная нагрузка па подшипник но формуле (126)
Необходимая динамическая грузоподъемность подшипника при этой нагрузке и долговечности L=2252 млн оборотов исходя из формулы (120) при P=Pэ
Нагрузка на подшипник при действии предельного момента двигателя на валу Мпр=67 кгс×м соответствующая статической грузоподъемности
Из конструктивных соображений (исходя из заданного диаметра нала) рассматриваемый вал установлен па двух радиальных подшипниках легкой
серии № 206 (см. табл. XVIII). Статическая грузоподъемность выбранных
подшипников С0=1020 кгс динамическая С=1020 кгс.
2 Подшипники второго и третьего вала. Принятый тип этих подшипников — сланцевые с втулками выполненными из бронзы марки ОЦС5-5-3. Диаметры опорных частей вала работающих в этих втулках d=75 мм; длины втулок обоих подшипников приняты одинаковыми и рапными l=75 мм. Дальнейшую проверку этих втулок производим исходя из нагрузок на опоры вала имеющих место при среднем и наибольшем пусковых моментах двигателя. В первом случае момент на валу M3=3027 кгс×см. Окружные усилия:
на шестерне при диаметре d1=128 мм
на колесе при диаметре d2=256 мм
Расчетные нагрузки (рис. 82):
Коэффициент 105 учитывает влияние радиальной составляющей нагрузки на зуб колеса.
Нагрузка на наиболее нагруженную опору В по схеме приведенной на рис. 82
Удельное давление но втулке подшипника опоры В
Частота вращении рассчитываемого вала n3=136 обмнн. Окружная скорость цапфы
Наибольшие допустимые величины и по [табл. 45 1-ст.198]
[p]=80 кгссм2. [p]=1530 кгс×мс×см2.
Момент на рассчитываемом валу при наибольшем пусковом моменте двигателя (табл. 47) M’’3=25653 кгс×см. Сдельное давление в подшипнике при этом моменте
Учитывая кратковременную работу механизма при этом моменте допускаемые удельные давления п данной случае могут быть повышены на 20—30% по сравнению с указанными в табл. 45. Проверка по удельной работе трения в данном случае не требуется.
ТОРМОЗ МЕХАНИЗМА ПОВОРОТА
В механизме поворота рассчитываемого крана установлен колодочный тормоз с короткоходовым электромагнитом. Необходимый момент этого тормоза определяем исходя из среднего замедления аср которое принято равным 04 мс2.
Необходимое время торможения при равнозамедленном движении груза
где — линейная скорость конца стрелы.
Избыточный момент (момент сил инерции) по формуле (10) при GD2= и tн =tт
Момент необходимый для поворота крана при установившемся движении приведенный к тормозному валу (первый нал редуктора) Мс=012 кгс×м. В рассматриваемом случае этот момент складывается с моментом тормоза. Соответственно необходимый тормозной момент
Мт=Ми-Мс=27-012=258 кгс×м.
Во избежание проскальзывания фрикциона при торможении этот момент приведенный к валу фрикциона не должен быть больше момента . В рассматриваемом случае тормозной момент приведенный к валу фрикциона
где и — к. п. д. и передаточное число червячной передачи.
Запас по отношению к расчетному моменту фрикциона
что вполне допустимо.
РАСЧЕТ МЕТАЛЛИЧЕСКОЙ КОНСТРУКЦИИ
Металлическая конструкция рассчитываемого крана выполнена сварной из стали марки СтЗпспЗ.
Определение расчетных усилий в стержнях в данном случае производим исходя из следующих двух возможных случаев работы крана: первый — при мгновенном торможении опускаемого груза и неподвижном кране и второй — при резком торможении вращающегося крана с подвешенным грузом.
1 Первый расчетный случай. При определении динамического коэффициента для первого расчетного случая исходим из статического удлинения грузовых канатов деформацию самой конструкции в данном случае не учитываем что идет в запас прочности.
В рассчитываемом кране груз подвешен на одинарном полиспасте с передаточным числом iп=2 принятый диаметр грузового каната d = 83 мм площадь сечения его проволок f =026 см3 расчетная длина вертикального участка l=35 м наклонного расположенного между направляющим блоком и барабаном l1=5 м.
Статическое удлинение вертикального участка каната по формуле (93)
то же для наклонного участка каната
где - площадь сечения проволок каната см2; - модуль упругости каната (); - расчетная длина каната.
Суммарное удлинение каната
λст=λ1+λ2=4+28=68 см.
Скорость подъема груза
Динамический коэффициент по формуле (92)
Расчетная нагрузка от массы поднимаемого груза по формуле (88)
Q’p=Qд=6000×13=7800 кгс.
Эту нагрузку принимаем равномерно распределенной между обеими фермами составляющими конструкцию. Соответственно нагрузка на одну ферму
Нагрузка от натяжения грузового каната
где и — передаточное число и к. п. д. полиспаста. Нагрузка на каждую ферму от этого натяжения
Sк =06S’к=06×3979=2387 кгс.
Коэффициент 0.6 в данном случае учитывает неравномерное распределение этой нагрузки между фермами при крайнем положении грузового каната на барабане.
Дополнительной нагрузкой является собственная масса поворотной части G=3000 кгс которую распределяем по отдельным узлам в соответствии со схемой приведенной на рис. 83.
Усилия в стержнях от этих нагрузок определены графическим путем из диаграмм которые построены отдельно дли сосредоточенных нагрузок от массы поднимаемого груза и натяжении каната (рис. 83 а) и нагрузок от собственной массы (рис. 83 6). Порядок обхода узлов принятый при построении диаграмм указан на рисунках римскими цифрами.
При построении диаграммы по рис. 83 a усилие от натяжения каната Sк переносим по линии его действия в точку В расположенную на стержне 5’ и распределяем между узлами А и С. Соответственно имеем:
Величины горизонтальных и вертикальных реакций опор от массы поднимаемого груза:
где — расчетная высота схемы (рис. 83).
По скольку усилия от натяжения каната относятся к внутренним силам их момент относительно опор равен нулю.
Горизонтальная и вертикальные реакции от собственной массы согласно рис. 83 б
Найденные из диаграмм усилия в стержнях.
Основные стержни главных ферм выполнены из швеллеров. В горизонтальной плоскости эти фермы связаны решетками из угловой стали.
Расчетная нагрузка стержня 1 S1=-4570 кгс длина этого стержня по схеме приведенной на рис. 83 l1= 492 см. В горизонтальной плоскости стержни 1 обеих ферм связаны решеткой в соответствии с этим наименьший расчетный радиус инерции будет иметь место относительно горизонтальной оси х—х . Наименьшую допустимую величину этого радиуса в данном случае определяем исходя из формулы λ=li по наибольшей допустимой гибкости для сжатых стержней λmax=120
По ГОСТ 8240— 72 этому радиусу инерции соответствует швеллер № 12 с площадью поперечного сечения F =133 см2 и моментами инерции Jx=304 см4 и Jу=312 см4 радиус инерции ix=478 см и iу=153 см.
Фактическая гибкость стержня при выбранном швеллере
Соответствует коэффициенту гибкости φ=06
Напряжения сжатия в рассчитываемом стержне
Наибольшие напряжения допускаемые по условиям устойчивости по формуле (95)
где =1400кгссм2 — основные напряжения.
Наибольшее допустимое расстояние между узлами горизонтальных решеток связывающих обе фермы определяем из условия равенства гибкости рассчитываемого стержня как в горизонтальной так и в вертикальной плоскостях
l’1=λxiу=103×153=158 см.
Принято l’1 = 128 см.
Из конструктивных соображений (сокращение применяемого сортамента при изготовлении конструкции) стержень 2 выполнен того же профиля что и стержень 1. Усилие в этом стержне S2=4130 кгс расчетная длина l2=600 см. гибкость
Наибольшая допустимая гибкость в данном случае λ=150.
Как и стержень 1 в горизонтальной плоскости оба стержня 2 связаны решетками. Наибольшее допустимое расстояние между узлами этой решетки из условия гибкости
l’2=λiу=150×153=230 см.
2 Второй расчетный случай. При расчете по этому случаю (резкое торможение при повороте крана с грузом) полагаем что горизонтальные силы инерции целиком передаются на горизонтальные связи верхнего пояса фермы (стержни 2). Момент касательных сил инерции определяем исходя из предельного момента фрикциона
где и — передаточные числа второй н третьей передач помещенных между валом фрикциона и осью вращения крана; — момент на валу фрикциона подсчитанный выше; — к. п. д. передачи.
Величиной центробежных сил (нормальных сил инерции) в данном случае пренебрегаем.
Усилие от этого момента в верхнем поясе 2 согласно схеме на рис. 84
Усилие от массы поднимаемого груза подсчитанное аналогично приведенному выше дли первого случая но при коэффициенте д=1. и массы самой конструкции — S2 =2760 кгс.
Суммарные усилия (при действии момента Мф)
S2p=2760 + 1680= 4440 кгс;
S2c =2760- 1680= 080 кгс.
Ввиду малых значений этих напряжении дальнейшая проверка выбранного сечения для рассматриваемого случаи нагрузки не требуется.
3 Опорная рама. Рама состоит из двух вертикальных стоек (стержни 5 на рис. 83). выполненных из швеллеров 16а. которые в верхней и нижней частях связаны поперечными швеллерами усиленными листами в которых укреплены цапфы крана.
Площадь поперечного сечения каждого швеллера F=195 см2 моменты инер-ции Jx=823 см4 Jv =788 см4 момент сопротивления отно-сительно оси х—х Wt=103 см3. За расчетный в дальней-шем принимаем первый расчетный случай.
Вертикальная стоика ра-мы нагружена растягива-ющим усилием S5=1970 кгс и поперечными силами H=1450 кгс. H’= 700 кгс и Sк=460 кгс подсчитанными выше. Рас-четная схема стойки при изгибе приведена на рис. 85 а.
Опорные реакции от сил H и H’
В точке С (узел крепления стержни 2 на рис. 83)
в точке D (точка приложения усилии от натяжения каната)
М’и=RA(l1+ l2)-(H+H’) l2=4050(23+715)-(3900+600)715=60975 кгс×см.
Напряжения от изгиба:
Дополнительные напряжения от растяжения силон S5
Суммарное напряжение в сечении С
Дополнительный изгибающие момент п точке D от натяжения грузового каната (рис 85 б)
М’и=RFl2=284×445=12600 кгс×см
где RF — реакция опоры F.
Дополнительные напряжения от момента М’и
Суммарные напряжения в точке D
=519+122+101=752 кгссм3.
Допускаемые напряжения согласно =1400 кгссм2; чтобы обеспечить достаточную жесткость рамы эти напряжения целесообразно снизить до 800—1000 кгссм2.
Наиболее нагруженная нижняя опорная балка крана работает на изгиб от вертикальной V0 и горизонтальной H0 опорных реакций и кручение моментом от внецентрового приложения силы H0 (рис. 86. 6).
Величина вертикальной нагрузки при расчете по первому случаю
V0=Qд+G=6000×15+3000=12000 кгс.
Горизонтальная нагрузка (рис. 85)
H0=Qд(Lh)+G(lh)= 6000×15(6545)+3000(1545)=14000 кгс.
Крутящий момент от внецентренного приложения силы H0 (рис. 86 а)
Мкр = H015=14000×210000 кгс×см.
Изгибающие моменты в среднем сечении рассчитываемой балки:
от вертикальной нагрузки
от горизонтальных нагрузок
Моменты инерции этого сечения относительно горизонтальной оси
относительно вертикальной оси
Моменты сопротивления
Напряжения от изгиба в рассматриваемом сечении от вертикальных нагрузок
Дополнительные напряжения от момента Мкр определяем приближенно рассматривая сечение как прямоугольник образованный вертикальными стенками шнеллеров и горизонтальными листами (рис. 86 в). Для этого случая напряжения могут быть приближенно определены по формуле
где =165×17=281 см2 — площадь прямоугольника ограниченного осями проходящими через середины стенок сечении; = 5 мм — толщина стенки швеллера.
Суммарное напряжение в сечении по третьей теории прочности
Допускаемые напряжения согласно указанному выше =10001800 кгссм2.
Павлов Н.Г. Примеры расчётов кранов. М.: Машиностроение 1968.
Бромберг А.А. Подъёмно-транспортные машины АТЛАС.
М.: Машиностроение 1950.
Александров М.П. Подъёмно-транспортные машин.
М.: Маниностроение - 1984.
Спецификация - Металлоконструкция.doc
Пояснительная записка
Швеллер №18 ГОСТ 8240 - 89
Швеллер №14 ГОСТ 8240 - 89
Неравнополочный уголок №117 ГОСТ 8510 - 93
Металлическая пластина Ст3 ГОСТ 535 - 88
Металлоконструкция.dwg

Общий вид.dwg

Техническая характеристика крана
Прегрузка сборочных узлов
Приспособление для захвата груза
Скорость подъема груза
Частота врашения крана
Механизм поворота.dwg

Характеристика Червячной передачи
доклад_к_курсовой_работе.doc
Основные характеристики крана: Захват груза производится специальным приспособлением массой 0.25 т. навешиваемым на крюк. Скорость подъема груза 16 метров в минуту поворот 1 обмин вылет крюка 65 м а максимальная высота подъема груза 35м.
Основными узлами крана являются механизм подъема выполненный по схеме одной закрытой и одной открытой передачами механизм поворота и металлическая конструкция выполненная в виде сварной фермы. Вертикальные нагрузки от собственной массы и массы поднимаемого груза в данном случае передаются на нижнюю опору горизонтальные от моментов этих масс—на верхнюю опору и радиальный подшипник нижней опоры.
Схема механизма поворота более подходящая для этого крана с фланцевым двигателем соединенным через ременную передачу с червячным редуктором вал которого расположен вертикально что исключает необходимость в устройстве конической передачи. В этом механизме вращение от двигателя передается через ременную передачу на вал червячного редуктора и далее через цилиндрические зубчатые колеса на ведомое колесо связанное с рамой крана. Во избежание поломки механизма при резком торможении в нем установлен фрикцион расположенный на валу червячного колеса. Червячный редуктор позволяет значительно сократить размеры механизма поворота что весьма важно при больших передаточных числах. Недостатком этой червячной передачи является его несколько меньшая надежность в работе по сравнению с передачами зубчатыми колесами а также необходимость применения бронзы как материала обода червячного колеса.
Металлоконструкция крана выполнена по решеточной схеме. Данная конструкция применяется при больших вылетов кранов для обеспечения устойчивости стержней. Достоинством решетчатой конструкции является простата ее изготовления и возможность применять сварку при изготовлении рамы.
Крюковая подвеска крана состоит из крюка 6 на нарезную часть которого навинчена гайка 1 опирающаяся на упорный шариковый подшипник 2. Этот подшипник позволяет легко поворачивать груз в требуемое положение не вызывая перекручивания грузовых канатов полиспаста. Подшипники 2опирается на поперечину 4 на цапфах которой вращаются блоки полиспаста установленные на шарика подшипниках. Для безопасности работы и предохранения канатов от выпадения из блоков последние закрыты специальными сварными кожухами 5. Смазка подшипников блоков – консистентная при помощи масленок 7 ввертываемых в торцы цапф поперечины. Войлочные уплотнительные кольца 3 предохраняют подшипники от вытекания смазки.
Крюковая подвеска.dwg

Спецификация - Крюковая подвеска.doc
Пояснительная записка
Гайка М18 ГОСТ 15521 - 70
Упорный шариковый подшипник ГОСТ 8338 - 75
Войлочное уплотнительное кольцо
Масленок ГОСТ 7796 -70
Спецификация - Механизм подъема.doc
Пояснительная записка
Электродвигатель MTF
Болт М16 ГОСТ 7796 -70
Болт М20 ГОСТ 7796 -70
Гайка М24 ГОСТ 15521 -70
Болт М16 ГОСТ 15521 -70