Колосниковый охладитель “Волга – 50”




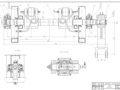
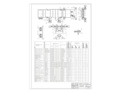
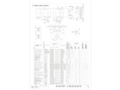
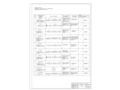
- Добавлен: 25.10.2022
- Размер: 4 MB
- Закачек: 0
Описание
Состав проекта
![]() |
![]() ![]() ![]() |
![]() ![]() ![]() ![]() |
![]() ![]() ![]() |
![]() ![]() ![]() |
![]() ![]() ![]() ![]() |
![]() ![]() ![]() |
![]() ![]() ![]() ![]() |
![]() ![]() ![]() |
![]() ![]() ![]() |
![]() ![]() ![]() ![]() |
Дополнительная информация
Карта смазки.dwg

Карта ремонта Вала (1).dwg

Карта смазки на записку.dwg

вал приводной.dwg

Рекомендуемые чертежи
- 09.07.2014