Кальцинатор 3,9х28,8. Производство цемента.




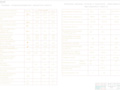
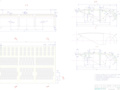
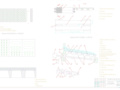
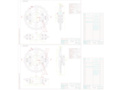
- Добавлен: 25.10.2022
- Размер: 5 MB
- Закачек: 1
Описание
Состав проекта
![]() |
![]() ![]() ![]() |
![]() ![]() ![]() |
![]() ![]() ![]() ![]() |
![]() ![]() ![]() ![]() |
![]() ![]() ![]() ![]() |
![]() ![]() ![]() ![]() |
![]() ![]() ![]() ![]() |
![]() ![]() ![]() ![]() |
![]() ![]() ![]() ![]() |
![]() ![]() ![]() ![]() |
![]() ![]() ![]() ![]() |
![]() ![]() ![]() ![]() |
![]() ![]() ![]() |
Дополнительная информация
Балка.dwg

несущий путь.dwg

Карта ремонта.dwg

колосник мод.dwg

патентные исследования.dwg

Экономика.dwg

Звездочки.dwg

Разгрузочная часть.dwg

эл схема привода.dwg

Технологическая схема.dwg

Кальцинатор общий вид.dwg
