Горно-геологические вскрытия шахты




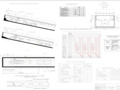
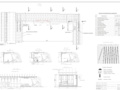
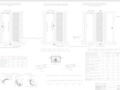
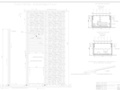
- Добавлен: 25.10.2022
- Размер: 5 MB
- Закачек: 1
Описание
Состав проекта
![]() |
![]() |
![]() |
![]() |
![]() |
![]() |
![]() |
![]() ![]() ![]() ![]() |
![]() ![]() ![]() ![]() |
![]() ![]() ![]() ![]() |
![]() ![]() ![]() ![]() |
![]() ![]() ![]() ![]() |
![]() ![]() ![]() ![]() |
![]() |
![]() |
![]() ![]() ![]() |
Дополнительная информация
проходка.dwg

Спец часть.dwg

Паспорт лавы.dwg

Вскрытие и подготовка.dwg

Система разработки.dwg

вентиляция.dwg

Рекомендуемые чертежи
- 04.11.2022
- 20.08.2014
- 20.08.2014
- 20.08.2014
- 20.08.2014
Свободное скачивание на сегодня
- 22.08.2014
- 29.08.2014