Гидропривод одноковшового гидравлического экскаватора расчёт



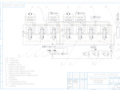
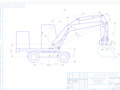
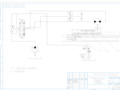
- Добавлен: 25.10.2022
- Размер: 986 KB
- Закачек: 0
Описание
Состав проекта
![]() |
![]() ![]() ![]() |
![]() ![]() ![]() |
![]() ![]() ![]() |
![]() ![]() ![]() |
![]() ![]() ![]() |
![]() |
![]() ![]() |
![]() ![]() |
![]() ![]() |
![]() ![]() ![]() ![]() |
![]() ![]() ![]() ![]() |
![]() ![]() |
![]() ![]() |
![]() ![]() ![]() ![]() |
![]() ![]() |
![]() ![]() ![]() |
Дополнительная информация
Содержание.docx
Определение мощности первичного двигателя
Определение параметров насосной установки .
Определение геометрических размеров рабочего оборудования
Определение энергоёмкости операций и подбор гидроцилиндров .
1 Зачерпывание материала погрузочным ковшом ..
2 Подъем рабочего оборудования
Расчёт механизма поворота .
Список литературы ..
Приложение 1 Регулятор расхода ..
Приложение 2 Пример применения гидрозамков
Приложение А Параметры рабочего оборудования экскаватора
Приложение Б Принципиальная схема гидропривода экскаватора
Приложение В Схема механизма поворота платформы
Титульник основной.docx
Белорусский Государственный Университет Транспорта
Кафедра «Экология и рациональное использование водных ресурсов»
РАСЧЕТ ГИДРОПРИВОДА МЕХАНИЗМОВ ОДНОКОВШОВОГО ЭКСКАВАТОРА
студент гр. МС-31 преподаватель
Ковалев И.Ю. Мохарева С.П.
Пояснительная титульник.docx
Белорусский Государственный Университет Транспорта
Кафедра «Экология и рациональное использование водных ресурсов»
ПОЯСНИТЕЛЬНАЯ ЗАПИСКА
к курсовой работе по дисциплине
«Гидравлика гидравлические машины и гидропривод»
студент гр. МС-31 преподаватель
Ковалев И.Ю. Мохарева С.П.
Курсач.docx
С конструктивной точки зрения гидропривод позволяет реализовать большие передаточные числа от ведущего звена источника энергии к рабочим механизмам и органам машин без применения громоздких и сложных по кинематике устройств; обеспечить простое преобразование вращательного движения в поступательное; иметь независимое расположение источника энергии и рабочих механизмов а также осуществлять удобное и независимое регулирование скоростей рабочих движений в широком диапазоне.
С технологической точки зрения улучшаются условия заполнения ковша при копании на большой глубине за счёт возможности реализовать большие усилия копания а также за счет поворота ковша относительно рукояти в конце процесса копания. Это способствует повышению производительности экскаватора.
Экономические преимущества являются следствием конструктивных и технологических преимуществ которые позволяют в конечном итоге повысить темпы строительных и других видов работ и снизить стоимость разработки грунта или перемещения груза.
Указанные преимущества гидравлического привода обусловили широкое его распространение в машинах различного назначения и в первую очередь в землеройных. Поэтому успешная эксплуатация таких машин требует достаточно высокого уровня подготовки по гидравлическим приводам. Этой цели и служит предусмотренная учебным планом курсовая работа по проектированию гидравлической системы одноковшового экскаватора.
-вместимость ковша – q=12 м3;
-вид рабочего оборудования – погрузочный ковш.
Выбор гидравлической схемы
Применяемые схемы подразделяются на одно- и многопоточные. Однопоточные схемы находят применение только на неполноповоротных экскаваторах вместимостью ковша до 03 м3.
С целью сокращения продолжительности цикла путём совмещения рабочих операций принимаем двухпоточную систему [1 рисунок 7.1 стр. 35].
Схемой предусматривается возможность работы с обратной лопатой погрузчиком и грейфером. В состав её входят два насоса 1 и 13 два гидрораспределительных блока 17 и 20 гидрораспределители поворота грейфера P8 и следящей системы поворота колес 12 гидромоторы поворота платформы 3 и передвижения экскаватора 6 а также гидроцилиндры: рукояти 5 стрелы 7 ковша обратной лопаты 8 поворота грейфера 9 и поворота колес 10. Помимо указанных имеются также не показанные на схеме гидроцилиндры ковша погрузчика и гидроцилиндр челюстей грейфера.
Основные механизмы приводятся в движение от двухсекционного автоматически совместно регулируемого аксиально-поршневого насоса 1. Второй насос 13 (шестеренный нерегулируемый) используется для питания гидроцилиндров поворота грейфера 9 и поворота колес 10.
От секций А и Б насоса 1 рабочая жидкость параллельными потоками подается в гидрораспределительные блоки соответственно 20 и 17 и от них на питание гидродвигателей. Исключение составляет рабочая секция P7 имеющая раздельное от всех остальных секций питание за счет использования промежуточной секции 16.
Включение в действие того или иного механизма экскаватора производится с помощью соответствующих трехпозиционных золотников. В положении показанном на рисунке все золотники находятся в нейтральном положении. В этом случае обе секции насоса подают полный поток к гидрораспределительному блоку 17. При включении любого из золотников гидрораспределительного блока 20 потоки жидкостей от секций А и Б разъединяются и питание блока 17 производится только от насоса Б.
Полный поток может подаваться также и в гидроцилиндр рукояти при приведении его в действие от гидрораспределительной секции P7. Но при необходимости совмещения операций он может быть включен и через золотник секции PЗ. В этом случае потоки разъединяются и это дает возможность совмещать движение рукояти (гидроцилиндр 5) с движением стрелы (гидроцилиндр 7) или же ковша обратной лопаты.
При работе с грейфером рабочие гидролинии 4 резервной секции P2 используются для управления гидроцилиндром подъема (опускания) верхней части составной стрелы секция P6 – для управления гидроцилиндром челюстей грейфера а гидрораспределитель 11 – для управления гидроцилиндром поворота грейфера 9.
Слив рабочей жидкости в бак от всех гидродвигателей производится через золотник 18. С помощью этого золотника поток может направляться либо в охладитель 15 если в этом имеется надобность либо минуя его на параллельно установленные фильтры 14. При их засорении поток может перепускаться через предохранительные клапаны в бак мимо фильтров.
Число фильтров установленных в сливной линии определяется необходимостью обеспечить минимальное сопротивление движению жидкости.
Напорные гидролинии обеих секций насоса 1 и насоса 13 защищены от давлений превышающих допускаемые с помощью предохранительных клапанов. Кроме того в напорных гидролиниях секций А и Б насоса 1 установлены еще и обратные клапаны.
В рабочих гидролиниях гидромоторов 3 и 6 а также гидроцилиндров 5 и 7 установлены предохранительные и обратные клапаны. Первые из них служат для защиты по допускаемому давлению. Через вторые может осуществляться подпитка или же перепуск рабочей жидкости из одной гидролинии в другую при срабатывании предохранительного клапана.
Для контроля настройки предохранительных клапанов в напорных гидролиниях установлен манометр 2 который поочередно может подключаться к напорным линиям секций А и Б насоса 1 и насоса 13. В сливной гидролинии давление может контролироваться с помощью манометра 19.
Определение мощности первичного двигателя
Мощность первичного двигателя определяется из условия обеспечения процесса копания с заданной скоростью.
Максимальную продолжительность копания определяем по формулам 2.1 и 2.2
где q – вместимость ковша м3.
Подставляем значения в формулы 2.1 и 2.2
Мощность двигателя из условия заполнения ковша при заданных значениях tк и Ауд определяется по формуле 2.3
где kнkp – отношение коэффициента наполнения к коэффициенту разрыхления (kнkp= 1);
сум – расчётный суммарный коэффициент полезного действия привода и рабочего оборудования (сум=045 056 – при использовании насосов постоянной подачи; сум = 052 064 – при использовании насосов с регуляторами мощности) сум=055;
kвых – коэффициент снижения выходной мощности двигателя ( kвых= = 075 – при использовании насосов постоянной подачи; kвых = 09 и более – при использовании насосов с регуляторами мощности) kвых = 09;
kи – коэффициент использования мощности насосной установкой kи = 085.
Подставляем численные значения в формулу 2.3
Радиус ковша находим по одной из формул
где bк – ширина режущей кромки м.
Подставляем числовые данные в формулы 2.4 и 2.5
Радиус ковша принимаем равным Rк=149 м.
Массу экскаватора находим по формуле 2.7
Pвн.max =10Cα(Lвн)125 bк kh kф
где С – коэффициент зависящий от крупности и степени разрыхления материала С = 175;
α – коэффициент учитывающий плотность и абразивные свойства материала α = 0121;
Lвн – глубина внедрения ковша в штабель см;
Lвн = 063 + 03112= 1002 м = 1002 см.
bк – ширина ковша см;
bк = 1+ 03512= 142 м = 142 см.
kh – коэффициент учитывающий влияние высоты штабеля kh = 125;
kф – коэффициент формы ковша kф = 094;
– коэффициент сцепления ходового устройства с грунтом = 07;
g – ускорение свободного падения g = 981 мс2.
Подставляем численные значения в формулу 2.8
Pвн.max =101750121(1002)125142125094=112004 кН
Находим массу экскаватора подставив численные значения в формулу 2.7
Выбираем двигатель марки СМД-20Н [1 таблица 2.2 стр. 9] для него:
мощность – Ne=88 кВт;
частота вращения – n=2000 обмин;
удельный эффективный расход топлива – qe=0252 кгкВтч;
Определение параметров насосной установки
Подачу насосной установки определяем по формуле 3.1
Qн = (60nNeп.нн)рmax p
где n – диапазон регулирования n = 2;
Ne – мощность первичного двигателя Ne = 88 кВт;
п.н – КПД привода насоса п.н = 09;
н – КПД насоса н = 085;
рmах. р – максимальное расчётное давление МПа;
pmax p = (089 09)·pmax
где pmax – предельное давление в гидроприводе pmax = 32 МПа.
pmax p = 09·32 = 288 МПа.
Подставляем числовые данные в формулу 3.1 и находим подачу насосной установки
Qн = (6028809085)288=2805 лмин.
Принимаем сдвоенный регулируемый аксиально-поршневой насос тип 313.3.160. Для него:
Определение геометрических размеров рабочего оборудования
Исходной величиной для определения геометрических параметров рабочего оборудования является полубаза экскаватора. Размер полубазы определяется по формуле 4.1
где m – масса экскаватора m = 1631 т.
Все прочие параметры рабочего оборудования определяются по зависимости
В – полубаза экскаватора м;
kв – коэффициент вариации.
Таблица 1–Конструктивные размеры
Расстояние от пяты стрелы до оси поворота платформы
Высота шарнира поворота стрелы
Расстояние от шарнира цилиндра поворота стрелы до оси поворота платформы
Расстояние от пяты стрелы до шарнира штока цилиндра стрелы
Таблица 1. Продолжение
Расстояние от шарнира штока цилиндра стрелы до оси поворота рукояти
Длина консоли рукояти
Расстояние между шарнирами
Расстояние от пяты стрелы до шарнира рукояти
Угол излома стрелы град
Определение энергоемкости операций и подбор гидроцилиндров
1 Копание поворотом рукояти гидроцилиндров
При копании поворотом рукояти принимают что путь наполнения ковша равен сумме длин рукояти lр и радиуса ковша Rк т. е.
lн.к = 233+144=377 м.
Минимальное время копания определяем по формуле 5.2
– отношение площади и полости цилиндра F1 к площади штоковой полости F2 =165;
vшт – допустимая скорость движения штока vшт = 021 мс.
tmin =(165094)021=738 с.
Работа копания поворотом рукояти может быть определена по формуле
где Ауд – удельная работа копания Ауд = 200 280 кНмм3;
kн и kр – коэффициенты наполнения и разрыхления kнkр = 10.
Ар = Ауд(kнkp) q=280112=336 кНм.
Расчётное давление в гидроцилиндре при насосах переменной подачи определяется зависимостью
где рmах – давление настройки предохранительного клапана рmах = 32 МПа;
n – диапазон регулирования насоса n=2.
Потребная площадь поршневой полости гидроцилиндра
F1 = Ap(pрасч xк р.о)
где р.о – коэффициент полезного действия рабочего оборудования (р.о= 08 09) р.о = 08.
F1 = 336103(1610609408)=00279 м2.
Диаметр гидроцилиндра находится по формуле 5.1.6
Полный ход поршня определяем по формуле 5.1.7
φр – угол поворота рукояти (φр = 95 1000) φр=1000.
Подставляем числовые данные в формулу 5.1.7
По ГОСТ 6540-68 принимаем гидроцилиндр 1.2 – 200×1600.
2 Копание поворотом ковша
Работа копания поворотом ковша Ак определяется по формуле 5.2.1
где Ауд – удельная работа копания Ауд = 250 кНмм3;
kнkp – отношение коэффициентов наполнения и разрыхления kнkp= = 10;
к – коэффициент учитывающий отношение полного угла поворота ковша к углу его поворота при наполнении (рабочему) к = 12.
Ак = 12250121=360 кНм.
Необходимый рабочий объём гидроцилиндра
где п.к. – коэффициент полезного действия механизма поворота ковша включая коэффициент полезного действия гидроцилиндра п.к.=088.
W = 360(16106088) = 00255 м3.
Полный угол поворота ковша принимаем равным αк=1550.
Угол поворота звена l4 находим по формуле 5.2.3
α4 = 155(04706) = 12140.
xп 206sin(12142) = 104 м.
Рабочий объем цилиндра
W' = (3140192104)4=00296 м3.
Величину максимальной скорости перемещения штока гидроцилиндра находим по формуле 5.2.6
где Qн – номинальная подача насоса;
– объёмный коэффициент полезного действия системы от насоса до гироцилиндра 0 = 096.
vшт = (4·18210-3096)(603140192) = 01 мс.
αк = 155573 = 27 рад.
Время перемещения штока
tшт = 10401 = 104 с.
3 Зачерпывание материала погрузочным ковшом
Максимальную силу внедрения ковша в штабель находим по формуле 5.3.1
Рвн. mах = 86000 (1 + 0023m)(063 + 001m)125
Рвн. mах = 86000 (1 + 00231631)(063 + 0011631)125 = 88512 Н.
Энергоёмкость операции внедрения ковша в штабель определяется произведением среднего значения усилия внедрения на путь внедрения т. е.
где Lвн – глубина внедрения ковша в штабель Lвн = 1002 м.
Авн = 05·885121002 = 443445 Нм.
Максимальное значение момента поворота ковша определяется по формуле 5.3.3
Мк max = 14Рвн mахLвн
Мк max = 14885121002 = 1241646 Нм.
Энергоёмкость операции поворота ковша
Ап.к = 05·1211646 = 620823 Нм.
Объём рабочей полости цилиндра внедрения
Wвн = 443445(16106088) = 00031 м3.
Объём рабочей полости цилиндра поворота
Wп.к = Ап.к(ррасчп.к)
Wп.к = 620823(16106088) = 00044 м3.
Ход поршня поворота ковша при шестизвенном соединении с рукоятью находим по формуле 5.3.7
xпк 2l4sin(αк l62l4)
где αк – угол поворота ковша αк = 1400.
xпк 206sin(140047206) = 098 м.
Диаметр цилиндра поворота ковша
По ГОСТ 6540-68 принимаем гидроцилиндр 1.2–220×2000.
4 Подъем рабочего оборудования
Работу затрачиваемую на подъем рабочего оборудования определяем исходя из графика показанного на рисунке 1.
Рисунок 1–Зависимость энергоёмкости подъёма стрелы с груженым ковшом от его вместимости q и массы экскаватора G
Исходя из графика работу затрачиваемую на подъем рабочего оборудования принимаем равной Ас = 300103 Нм.
Рабочий объём гидроцилиндров подъёма стрелы определяется зависимостью
где pрасч – расчётное давление рабочей жидкости;
с.м – КПД стрелоподъёмного механизма с.м = 08;
z – число цилиндров (обычно z = 2).
W = 300103(16106208) = 00117 м3.
Ход поршня определяется из схемы стрелоподъемного механизма
Рисунок 2–Схема стрелоподъёмного механизма
Из рисунка 2 следует
Значение ОА известно из схемы стрелоподъёмного механизма. Значение ОС определяется по известным координатам точек О и С
Углы φ и φ' определяются по формулам 5.4.6 и 5.4.7 соответственно
φ = arctg[(y0 – yc)(xc –x0)] + αc'+Δ
φ' = arctg[(y0 – yc)(xc –x0)] + αc''+Δ
где αc' и αc'' – углы между горизонтальным направлением и направлением соединяющим шарниры стрелы и штока гидроцилиндра взятыми со знаком "-" если угол расположен вниз от горизонтального направления или "+" если угол расположен вверх от горизонтального направления.
Δ – угол излома стрелы.
Подставляем численные значения в формулы 5.4.6 и 5.4.7 и находим углы φ и φ'
φ = arctg[(198 – 152)(121 –062)] + 15 + 322 = 85140
φ' = arctg[(198 – 152)(121 –062)] + 70 + 322 = 140140.
Определяем значение ОС
Определяем ход поршня
Диаметр цилиндра при выбранном значении хода поршня определяется по формуле 5.4.8
По ГОСТ 6540-68 принимаем гидроцилиндр 1.2–160×1250.
Расчет механизма поворота
Согласно принципиальной схеме гидропривода экскаватора гидромотор механизма поворота может питаться только от секции А насоса 1.
подача насоса – Qн.ma
номинальное давление насоса – pн = 20 МПа;
угол поворота платформы – φ0 = 900;
диапазон регулирования насоса – n' = 2.
Момент инерции поворотной части платформы определяется по формуле 6.1
I = 900163153 = 944059 Н.мс2.
Момент сил сцепления ходовой части экскаватора с грунтом
Mсц = 1850163143 = 7652036 Н.мс2.
Допустимый тормозной момент
Мт = 087652036 = 535642 Н.мс2.
В зависимости от типа используемого в гидроприводе гидромотора принимается значение коэффициента r представляющем собой отношение
где Мр – разгоняющий момент;
Мт – тормозной момент;
с – суммарный КПД механизма поворота включающий гидромеханический КПД гидромотора гм и КПД механических передач мп.
Принимаем с = 078 и r = 06.
Мр = 06535642 = 321385 Н.мс2.
Допустимое ускорение при разгоне
р = 321385944059 = 034 с-2.
Допустимое ускорение при торможении
т = 535642944059 = 0567 с-2.
Скорость вращения платформы в конце разгона
Время разгона определяем по формуле 6.9
tp = 0817034 = 24 с.
Время торможения находим из формулы 6.10
tт = 08170567 = 144 с.
Время включения и выключения механизма при распределителях с ручным управлением принимается в пределах tвв = 035 04 с. Принимаем tвв=04 с.
Общее время поворота на расчетный угол
tп = 24 + 144 + 04 = 424 с.
Потребная мощность гидромотора
Nгм = (Мрп)(1000мпn')
где – мп – коэффициент полезного действия механической передачи от вала гидромотора до поворотного круга мп = 096.
Nгм = (3213850817)(10000962) = 1367 кВт.
Мощность забираемая от первичного двигателя на осуществление поворота платформы
Nп = (rМр п)(1000с n')
где с – общий коэффициент полезного действия учитывающий все потери первичного двигателя до поворотного круга с = 078.
Nп = (063213850817)(1000078 2) = 101 кВт.
По величине потребной мощности выбираем гидромотор 303.2.28 [1 таблица 6.1 стр. 29-30] имеющий следующие паспортные данные:
рабочий объем – qм = 28 см3;
давление на выходе: номинальное – 20 МПа;
максимальное – 35 МПа;
частота вращения: номинальная – 2000 обмин;
максимальная – 6250 обмин;
номинальный расход – 59 лмин;
номинальная эффективная мощность – 17 кВт;
гидромеханический КПД – гм = 095;
Передаточное число редуктора определяется по формуле 6.14
ip = (1000Qнmax об)(30qм п)
где qм – рабочий объём гидромотора qм = 28 см3;
об – объёмный коэффициент полезного действия гидропередачи от насоса до гидромотора об = 09.
ip = (10005931409)(30280817) = 243
Частота вращения вала гидромотора соответствующая найденному значению iр определяется по формуле 6.15
nм = 302430817314 = 18968 обмин.
Сравнивая частоту вала гидромотора с максимальной имеем
nм = 18968 обмин 6250 обмин.
Максимальный крутящий момент на валу гидромотора определяется по следующей формуле
Mм max = 321385243 = 13225 Н.мс2.
Давление настройки предохранительных клапанов
Pк = [(628Mp )(qм ip гм мп)] + pсл
где гм – гидромеханический КПД гм = 095;
мп – полный КПД мп = 09;
pсл – давление в сливной магистрали за гидромотором pсл = 05 15 МПа.
Pк = [(628321385)(2824309509)] + 05 = 3469 МПа.
Проверяем выполнение условия РкРmax = 06 08
РкРmax = 346932 = 108 – условие не выполняется.
Так как это условие не выполняется то увеличиваем iр на 20 % чтобы тем самым уменьшить максимальную скорость поворота платформы.
iр = 24314 = 3402 обмин.
nм = 1896814 = 227616 обмин
Pк = [(628321385)(28340209509)] + 05 = 2528 МПа.
РкРmax = 252832 = 079 – условие выполняется.
Подача насоса при давлении настройки предохранительных клапанов
Q0 = 601367(2528095) = 3415 лмин.
Скорость вращения платформы в конце первого этапа разгона
Фактическое значение разгоняющего момента определяем по формуле 6.26
Мр = 0159(095Рк - pсл)qм iр гм мп
Мр = 0159(0952528 – 05)28340209509 = 304522 Н.мс2.
Фактическое значение тормозного момента определяем по формуле 6.27
Мт = 304522(09509)2 = 416569 Н.мс2.
Значение коэффициента r представляет собой отношение
r = 304522416569 = 073.
Фактическое ускорение при разгоне
р = 304522944059 = 032 с-2.
Фактическое ускорение при торможении
т = 416569944059 = 044 с-2.
Фактическая максимальная скорость вращения платформы
Фактическое время разгона определяем по формуле 6.32
tp = 076032 = 237 с.
Фактическое время торможения находим из формулы 6.33
tт = 076044 = 172 с.
Фактическое время поворота на расчетный угол
tп = 237 + 172 + 04 = 449 с.
Общие затраты энергии
Ао = 101103·449 = 45349 Дж.
Апол = (Iп2)2 + Мсφо (Iп2)2
Апол (9440590762)2 = 272644 Нм.
В процессе выполнения данной курсовой работы была составлена гидравлическая схема одноковшового экскаватора на пневмоколесном ходу имеющего в качестве рабочего оборудования погрузочный ковш. Рассчитана мощность первичного двигателя и насосной установки определены энергоемкости рабочих операций подобраны силовые гидроцилиндры рабочего оборудования а также рассчитан механизм поворота платформы.
В пояснительной записке к курсовой работе изложены все расчеты и обоснованы все принятые технические решения необходимые для точного расчета оборудования данного экскаватора.
Абрамович В.А. Довгяло В.А «Расчет гидропривода механизмов одноковшового экскаватора»: Пособие к курсовой работе по дисциплине “Гидравлика и гидравлические машины”.– Гомель: БелГУТ 2002.– с.
Беркман И. Л. Одноковшовые строительные экскаваторы.– М.1986.–269с.
Щемелев А. М. Проектирование гидропривода машин для земляных
работ.– Могилёв: ММИ 1995.– 322 с.
Проектирование машин для земляных работПод ред. А. М. Холодова.– Харьков 1986.–270 с.
Приложение 1.docx
Эти устройства применяются для поддержания постоянного расхода независимо от изменения давления. Принцип работы регулятора расхода показан на рисунке 3.
Рисунок 3–Принцип работы регулятора расхода
Регулятор расхода состоит из следующих основных элементов: дозирующего дросселя 1 и компенсатора давления 2 с пружиной 3. Изменение температуры и соответственно вязкости рабочей жидкости изменяет перепад давления. Чтобы уменьшить влияние этих факторов применяется специальная форма дросселирующей щели.
Тип регулятора расхода зависит от конструкции компенсатора давления. Если компенсатор давления расположен последовательно с дозирующим дросселем гидроаппарат является двухлинейным регулятором расхода если параллельно – трехлинейным регулятором расхода.
В двухлинейных регуляторах расхода дозирующий дроссель и компенсатор давления расположены последовательно. При этом компенсатор давления может располагаться перед дросселем на входе (рис. 4 а) или после него на выходе (рис. 4 б).
Рисунок 4–Условное обозначение (а) и принцип работы (б) двухлинейного регулятора расхода с компенсатором на входе
Золотник компенсатора нагружен справа давлением Р2 и слева давлением Р3 и усилием пружины FF.
Перепад давления на регулируемом дросселе в двухлинейном регуляторе расхода является отношением усилия регулируемой пружины регулятора давления FF к торцовой площади золотника АК и не зависит от последовательности расположения компенсатора давления: перед дросселем или после него.
На рисунке 5 показаны условное обозначение и принцип работы двухлинейного регулятора расхода с компенсатором давления на выходе.
Из рисунка 5 видно что дозирующий дроссель и компенсатор давления двухлинейного регулятора расхода расположены последовательно. Место расположения компенсатора давления (на входе или на выходе) в двухлинейных регуляторах расхода определяется конструктивными соображениями.
Рисунок 5–Условное обозначение (а) и принцип работы (б) двухлинейного регулятора расхода с компенсатором давления на выходе
Рассмотрим особенности применения двухлинейных регуляторов расхода при дросселировании потока рабочей жидкости: на входе (первичное управление) на выходе (вторичное управление) и в ответвлении.
При управлении расходом рабочей жидкости на входе регулятор расхода устанавливают в напорной гидролинии насоса после предохранительного клапана перед гидродвигателем. Эта схема дросселирования рекомендуется для гидросистем в которых регулируется скорость движения гидродвигателя преодолевающего противодействующее усилие (положительное сопротивление). В этом случае перед регулятором расхода действует нагрузка определяемая внешним сопротивлением на гидродвигателе.
Недостатком этой схемы является необходимость настройки предохранительного клапана установленного перед регулятором расхода на максимально возможное давление в гидродвигателе. В результате насос постоянно работает под максимальным давлением даже когда гидродвигатель преодолевает небольшую нагрузку. Кроме этого потери мощности при дросселировании потока превращаются в нагрев рабочей жидкости которую необходимо охлаждать для стабилизации теплового режима.
При управлении расходом рабочей жидкости на выходе регулятор расхода устанавливают на выходе из гидродвигателя перед баком. Такая схема управления расходом рекомендуется для гидросистем с попутной рабочей нагрузкой (отрицательной) которая стремится перемещать шток гидроцилиндра или вращать вал гидромотора быстрей чем скорость потока РЖ определяемая подачей насоса. Сохраняется основной недостаток схемы дросселирования – необходимость настройки предохранительного клапана на максимальное давление и воздействие максимального давления на уплотнительные элементы гидроцилиндра даже при холостом ходе т. е. с более высоким уровнем трения.
При управлении расходом в ответвлениирегулятор устанавливают паралелльно гидродвигателю. В этой схеме регулятор ограничивает расход рабочей жидкости поступающей в гидродвигатель путем перепуска части потока нагнетаемого насосом в бак гидросистемы. Если рабочий орган доходит до упора давление в гидросистеме ограничивается настройкой предохранительного клапана и слив потока рабочей жидкости через клапан вновь преобразуется в нагрев.
Преимуществом этой схемы регулирования расхода является ограниченное рабочее давление которое определяется внешней нагрузкой на рабочем органе или на исполнительном механизме. При этом меньше мощности преобразуется в нагрев рабочей жидкости а выделяемое при дросселировании тепло отводится в бак гидросистемы.
Из приведенного выше сравнения дросселирующих и регулирующих гидроаппаратов управления расходом рабочей жидкости следует явное преимущество регуляторов расхода которые представляют собой комбинацию дросселя с регулятором поддерживающим постоянный перепад давления на дросселирующей щели.
В отличие от двухлинейных регуляторов расхода дозирующие А2 и управляющие А1 отверстия в трехлинейных регуляторах расхода расположены не последовательно а параллельно.
Приложение 2. Пример применения гидрозамков
Гидрозамкомназывается направляющий гидроаппарат предназначенный для пропускания потока рабочей жидкости в одном направлении при отсутствии управляющего воздействия а при наличии управляющего воздействия - в обоих направлениях.
По числу запорно-регулирующих элементов гидрозамки могут быть одно- и двухсторонними.
Рисунок 6–Односторонний гидрозамок:
а - подача рабочей жидкости к полости А; б - течение жидкости из полости А в полость Б; в - подача рабочей жидкости в полость Б; г - течение жидкости из полости Б в полость Апри наличии управляющего воздействия; д - условное обозначение одностороннего гидрозамка.
Односторонний гидрозамок (рис. 6) имеет толкатель 3 запорно-регулирующий элемент 1 и нерегулируемую пружину 2 которые образуют подобие обратного клапана. У одностороннего гидрозамка выполнено три подвода соединенные с тремя полостями гидрозамкаАБиУ. При подаче рабочей жидкости под давлением в полостьА(рис.6 а) открывается запорно-регулирующий элемент 1 и жидкость начинает свободно проходить в полостьБ(рис.6 б). Управляющее воздействие отсутствует т.е. в полостьУдавление жидкости не подается. При подводе рабочей жидкости к полости Б клапан закрыт (рис.6 в). Однако если одновременно с этим подвести жидкость к полостиУ(подать управляющее воздействие) то толкатель 3 перемещаясь вверх откроет запорно-регулирующий элемент. В этом случае жидкость будет свободно проходить из полостиБв полостьА(рис.6 г) пока будет присутствовать управляющее воздействие в полостиУ.
Односторонние гидрозамки применяются для блокировки движения выходного звена гидродвигателя в одном направлении. Для блокировки выходного звена в двух направлениях применяются двухсторонние гидрозамки.
Двухсторонний гидрозамок (рис.7) имеет в своем корпусе два запорно-регулирующих элемента 1 две нерегулируемые пружины 2 а между ними плавающий толкатель 3 (рис.7 а). При подводе рабочей жидкости под давлением к каналуАоткрывается запорно-регулирующий элемент 1 и жидкость свободно поступает в каналВи далее к гидродвигателю (например в поршневую полость гидроцилиндра). Одновременно с этим толкатель 3 гидрозамка перемещается вправо и открывает второй запорно-регулирующий элемент обеспечивая пропуск жидкости (например от штоковой полости гидроцилиндра) из каналаГв каналБи далее в сливную магистраль. Аналогично гидрозамок работает при реверсе движения выходного звена гидродвигателя.
Если жидкость под давлением не подводится ни к одному из каналов (А илиВ) то рабочие элементы 1 снова занимают положение указанное на рисунке 7 а. Полости гидродвигателя блокируются от слива тем самым блокируя выходное звено гидродвигателя от перемещений.
Рисунок 7–Двухсторонний гидрозамок:
а - нейтральное положение; б - положение толкателя при подводе
давления в канал А; в - положение толкателя при подводе давления в канал В;
г - условные обозначения.
При установке гидрозамков необходимо учитывать их конструктивное исполнение (тип) способ нагружения выходного звена гидродвигателя а также место размещения при этом дросселей с обратными клапанами - до или после гидрозамка. Дроссели с обратными клапанами свободно пропускают поток рабочей жидкости на подъем рабочего органа и ограничивают расход рабочей жидкости и соответственно скорость рабочего органа при его опускании (рис. 8).
Рисунок 8–Схема установки одностороннего гидрозамка:
а - без дросселя с обратным клапаном; б - дросселем и обратным клапаном.
Если в схеме привода гидроцилиндра грузоподъемного механизма с гидрозамком не будет установлен дроссель с обратным клапаном (рис. 8 а) то при перемещении золотника гидрораспределителя в позицию "опускание" в гидролинии насоса и управления гидрозамком создается давление достаточное для открытия гидрозамка. После его открытия рабочая жидкость из штоковой полости гидроцилиндра поступает на слив и шток опускается под действием внешней нагрузкиF. При этом скорость перемещения штока гидроцилиндра может превысить скорость обусловленную подачей насоса. Тогда давление в противоположной (поршневой) полости гидроцилиндра и в гидролинии управления уменьшается запорный элемент гидрозамка под действием пружины закрывается и движение прекращается. Затем давление в напорной гидролинии и в гидролинии управления снова возрастает и гидрозамок открывается. Таким образом происходят прерывистое движение рабочего органа и пульсация давления. Для исключения этого явления между гидрозамком и гидроцилиндром рекомендуется устанавливать дроссель с обратным клапаном (см. рис.8 б) сопротивление которого при опускании штока создает давление необходимое для открытия обратного клапана гидрозамка и поддержания его в том положении.
Давление управления для гидрозамков составляет от 002 (минимальное давление срабатывания ненагруженного клапана) до 32 МПа.
В гидросистемах мобильных машин наибольшее применение получили односторонние гидрозамки с коническим запорным элементом имеющие условный проход 16 20 25 и 32 мм.
Чертеж 3.dwg

Чертеж 1.dwg

Чертеж 2.dwg

- гидроцилиндр стрелы
- гидроцилиндр погрузочного ковша
- гидроцилиндр поворота колес
- гидрораспределитель поворота колес
- промежуточная секция
- гидрораспределительные блоки
КР.ГиГМ.МС-31.20.00.02
Принципиальная схема
1 Выбор гидравлической схемы.docx
Применяемые схемы подразделяются на одно- и многопоточные. Однопоточные схемы находят применение только на неполноповоротных экскаваторах вместимостью ковша до 03 м3.
С целью сокращения продолжительности цикла путём совмещения рабочих операций принимаем двухпоточную систему [Приложение Б].
Схемой предусматривается возможность работы с обратной лопатой погрузчиком и грейфером. В состав её входят два насоса 1 и 13 два гидрораспределительных блока 15 и 16 и следящей системы поворота колес 10 гидромоторы поворота платформы 3 и передвижения экскаватора 6 а также гидроцилиндры: рукояти 5 стрелы 7 погрузочного ковша 8 и поворота колес 9. Помимо указанных имеются также не показанные на схеме гидроцилиндры ковша погрузчика и гидроцилиндр челюстей грейфера.
Основные механизмы приводятся в движение от двухсекционного автоматически совместно регулируемого аксиально-поршневого насоса 1. Второй насос 13 (шестеренный нерегулируемый) используется для питания гидроцилиндров погрузочного ковша и поворота колес 9.
От секций А и Б насоса 1 рабочая жидкость параллельными потоками подается в гидрораспределительные блоки соответственно 15 и 16 и от них на питание гидродвигателей. Исключение составляет рабочая секция P7 имеющая раздельное от всех остальных секций питание за счет использования промежуточной секции 14.
Включение в действие того или иного механизма экскаватора производится с помощью соответствующих трехпозиционных золотников. В положении показанном на рисунке все золотники находятся в нейтральном положении. В этом случае обе секции насоса подают полный поток к гидрораспределительному блоку 15. При включении любого из золотников гидрораспределительного блока 16 потоки жидкостей от секций А и Б разъединяются и питание блока 15 производится только от насоса Б.
Полный поток может подаваться также и в гидроцилиндр рукояти при приведении его в действие от гидрораспределительной секции P7. Но при необходимости совмещения операций он может быть включен и через золотник секции PЗ. В этом случае потоки разъединяются и это дает возможность совмещать движение рукояти (гидроцилиндр 5) с движением стрелы (гидроцилиндр 7) или же погрузочногоковша.
При работе с грейфером рабочие гидролинии 4 резервной секции P2 используются для управления гидроцилиндром подъема (опускания) верхней части составной стрелы секция P6 – для управления гидроцилиндром челюстей грейфера а гидрораспределитель 11 – для управления гидроцилиндром поворота грейфера 9.
Слив рабочей жидкости в бак от всех гидродвигателей производится через золотник 17. С помощью этого золотника поток может направляться либо в охладитель 12 если в этом имеется надобность либо минуя его на параллельно установленные фильтры 11. При их засорении поток может перепускаться через предохранительные клапаны в бак мимо фильтров.
Число фильтров установленных в сливной линии определяется необходимостью обеспечить минимальное сопротивление движению жидкости.
Напорные гидролинии обеих секций насоса 1 и насоса 13 защищены от давлений превышающих допускаемые с помощью предохранительных клапанов. Кроме того в напорных гидролиниях секций А и Б насоса 1 установлены еще и обратные клапаны.
В рабочих гидролиниях гидромоторов 3 и 6 а также гидроцилиндров 5 и 7 установлены предохранительные и обратные клапаны. Первые из них служат для защиты по допускаемому давлению. Через вторые может осуществляться подпитка или же перепуск рабочей жидкости из одной гидролинии в другую при срабатывании предохранительного клапана.
Для контроля настройки предохранительных клапанов в напорных гидролиниях установлен манометр 2 который поочередно может подключаться к напорным линиям секций А и Б насоса 1 и насоса 13. В сливной гидролинии давление может контролироваться с помощью манометра 18.
Рекомендуемые чертежи
- 05.12.2023