Гидроманипулятор Синегорец – 75




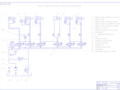
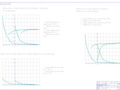
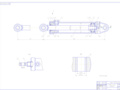
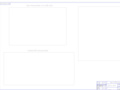
- Добавлен: 25.10.2022
- Размер: 3 MB
- Закачек: 2
Описание
Состав проекта
![]() |
![]() |
![]() |
![]() |
![]() ![]() ![]() ![]() |
![]() |
![]() ![]() ![]() ![]() |
![]() ![]() ![]() ![]() |
![]() ![]() ![]() ![]() |
![]() ![]() |
![]() |
![]() ![]() |
![]() |
![]() ![]() |
![]() |
![]() ![]() ![]() |
![]() ![]() |
Дополнительная информация
гидравл. схема.dwg

общий вид.dwg

гидравлические графики.dwg

чертеж гидроцилиндра.dwg
