Балка мостового крана


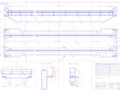

- Добавлен: 25.10.2022
- Размер: 1 MB
- Закачек: 0
- ВКонтакте
- РћРТвЂВВВВВВВВнокласснРСвЂВВВВВВВВРєРСвЂВВВВВВВВ
- Telegram
Подписаться на ежедневные обновления каталога:
Описание
Балка мостового крана
Состав проекта
![]() |
![]() ![]() ![]() |
![]() ![]() |
![]() ![]() ![]() ![]() |
![]() ![]() ![]() ![]() |
Дополнительная информация
Контент чертежей
РПЗ КР ПМК.docx
Объект проектирования – мост крана.
Цель работы – спроектировать главную балку мостового крана и выполнить ее проверочные расчеты. В проекте приводится выбор способа расчета.
В проекте рассчитаны основные геометрические параметры главной и концевой балок мостового крана. Была выполнена проверка устойчивости стенок балки статической и динамической жесткости моста рассчитан строительный подъем и разработана раскройка листов боковых стенок главной балки кроме того проведены проверочные расчеты сварных швов и выбраны электроды для проведения сварочных работ.
Металлоконструкция является наиболее металлоемкой и как следствие наиболее дорогостоящей частью мостового крана. В тоже время она является и наиболее ответственной его частью. Это обуславливает тенденцию к снижению металлоемкости путем применения низколегированных сталей и повышению надежности металлоконструкций вновь разрабатываемых машин.
БАЗА КРАНА КОНЦЕВАЯ БАЛКА ГЛАВНАЯ БАЛКА ЭЛЕКТРОД РАСЧЕТНАЯ СХЕМА СИЛОВОЙ ФАКТОР.
ОБОСНОВАНИЕ ОБЩЕЙ СХЕМЫ МЕТАЛЛОКОНСТРУКЦИИ7
ОПРЕДЕЛЕНИЕ ОСНОВНЫХ КОНСТРУКЦИОННЫХ РАЗМЕРОВ КРАНА9
ВЫБОР МЕТОДА РАСЧЁТА14
ВЫБОР МАТЕРИАЛА ДЛЯ НЕСУЩИХ И ВСПОМОГАТЕЛЬНЫХ ЭЛЕМЕНТОВ ОПРЕДЕЛЕНИЕ ДОПУСТИМЫХ РАСЧЁТНЫХ СОПРОТИВЛЕНИЙ И НАПРЯЖЕНИЙ17
ОПРЕДЕЛЕНИЕ НАГРУЗОК И ИХ РАСЧЁТНЫХ СОЧЕТАНИЙ20
ВЫБОР РАСЧЁТНЫХ СХЕМ И ОПРЕДЕЛЕНИЕ ВНУТРЕННИХ СИЛОВЫХ ФАКТОРОВ В ЭЛЕМЕНТАХ26
ОПРЕДЕЛЕНИЕ РАЗМЕРОВ НЕСУЩИХ ЭЛЕМЕНТОВ МЕТАЛЛОКОНСТРУКЦИИ30
ОБЕСПЕЧЕНИЕ МЕСТНОЙ И ОБЩЕЙ УСТОЙЧИВОСТИ35
1 Размещение поперечных рёбер жёсткости35
2 Размещение продольных рёбер жёсткости40
ПРОВЕРКА ПРОЧНОСТИ ОПОРНОГО СЕЧЕНИЯ ПРОЛЁТНОЙ БАЛКИ43
ПРОВЕРКА ПРОЧНОСТИ СВАРНЫХ ШВОВ47
ПРОВЕРКА МЕТАЛЛОКОНСТРУКЦИИ МОСТА НА СТАТИЧЕСКУЮ ЖЁСТКОСТЬ49
РАСЧЁТ СТРОИТЕЛЬНОГО ПОДЪЁМА50
ЗАЩИТА МЕТАЛЛОКОНСТРУКЦИИ ОТ КОРРОЗИИ53
НАУЧНО-ИССЛЕДОВАТЕЛЬСКАЯ РАБОТА54
1 Изготовление главной балки коробчатого сечения54
2 Рельсы и крановые пути59
Мостовые краны общего назначения широко применяются практически во всех отраслях народного хозяйства при технологических погрузочно-разгрузочных монтажных складских и других работах. Они имеют большую номенклатуру типоразмеров и исполнений их грузоподъёмность достигает 800т. наиболее широко используются краны грузоподъёмностью от 5 до 320т.
Современное краностроение характеризуется совершенствованием конструкций применением новых материалов методов и средств изготовления и контроля внедрением более совершенных методов расчёта и основанных на них снижении массы кранов повышении их надёжности.
Большинство мостовых козловых и других грузоподъемных кранов были изготовлены и установлены 25-30 лет назад (более 70% кранов).
Однако настоящие время существует ряд проблем для замены старых кранов на новые. К этим сложностям относятся: большая стоимость нового крана сложность финансирования энергоресурсов. Приобретение новых кранов фирмами и предприятиями становиться в большинстве случаев практически невозможными.
В связи с этим возникает потребность в модернизации уже существующих кранов установленных в цехах на эстакадах и т.п. Их ремонт и восстановления с целью их дальнейшей эксплуатации. Одно из важнейших частей технологического оборудования является подъемно-транспортные машины которые уже при их использовании расходуют свой ресурс. Основной частью любой подъемно-транспортные машины является металлоконструкция и ей в свою очередь отводится важная роль при ремонте и ее восстановления.
ОБОСНОВАНИЕ ОБЩЕЙ СХЕМЫ МЕТАЛЛОКОНСТРУКЦИИ
Запланированное место работы крана – мартеновский цех машиностроительного завода. Режим работы крана – 8К. Целесообразней выбрать металлоконструкцию главных балок коробчатой конструкции т.к. меньшая трудоёмкость изготовления: проще разметка правка и резка листов возможность применения автоматической сварки также металлоконструкция коробчатой конструкции удобней для обслуживания тех. персоналом чем металлоконструкция ферменной конструкции.
Металлические конструкции мостовых кранов – это мосты и рамы тележек. Мост грузоподъёмного мостового крана общего назначения состоит из пролётных и концевых балок коробчатого сечения.
Основными элементами мостового крана являются главные и концевые балки. Главные балки мостового крана воспринимает основную нагрузку. На ней расположены рельсы по которым передвигается грузовая тележка. Так как на тележку действует основная нагрузка от веса груза то главная балка является основным нагруженным элементом металлоконструкции мостового крана на них располагаются также смотровая площадка и кабина машиниста. На концевых балках крепятся буксы и ходовые колеса. Они выполняет функцию опоры главных балок.
Схема металлоконструкции бвубалочного мостового крана общего назначения показана на рисунке 1.1.
Рисунок 1 – Конструктивная схема двухбалочного моста грузоподъемного крана
ОПРЕДЕЛЕНИЕ ОСНОВНЫХ КОНСТРУКЦИОННЫХ РАЗМЕРОВ КРАНА
Размеры металлоконструкции назначаются по рекомендациям основанных на опытах предыдущих проектирований [125].
Определяем базу крана:
Принимается BТ =40 м.
Высота главной балки:
Расстояние между вертикальными стенками:
Толщину вертикальных листов главной и концевой балок принимаем исходя из грузоподъёмности: при мм. При выборе толщины листа ее следует принимать из возможных стандартных значений.
Высота сечения концевой балки:
Ширина концевой балки:
Скосы на концах главной балки:
Определим геометрические характеристики сечения главной и концевой балки:
Момент инерции главной балки относительно оси х-х:
Момент инерции главной балки относительно оси у-у:
Момент сопротивления сечения главной балки относительно оси х-х:
Момент сопротивления сечения главной балки относительно оси у-у:
Площадь поперечного сечения главной балки в середине пролёта:
Момент инерции концевой балки относительно оси х-х:
Момент инерции концевой балки относительно оси у-у:
Момент сопротивления сечения концевой балки относительно оси х-х:
Момент сопротивления сечения концевой балки относительно оси у-у:
Площадь поперечного сечения концевой балки:
Рисунок 2 – Схема моста крана с предварительно определенными конструктивными параметрами
ВЫБОР МЕТОДА РАСЧЁТА
Одним из самых важных этапов в проектировании любой машины является выбор метода расчётов. Выбранный метод должен не только обеспечить прочность надёжность и безопасность эксплуатации изделия но и обеспечить минимальную металлоёмкость а следовательно и стоимость. В данное время наиболее современным и прогрессивным является метод предельных состояний.
Преимущества метода предельных состояний перед методом допускаемых напряжений:
)Каждый вид нагрузки вводится со своим коэффициентом перегрузки чем точнее определена нагрузка тем меньше этот коэффициент;
)Исключается субъективизм при выборе запасов прочности;
)Позволяет выполнить вероятностный расчёт достижения элементом предельного состояния.
Различают два вида предельных состояний: первое предельное состояние – по несущей способности; второе предельное состояние – по деформации или местным повреждениям.
Задача расчёта металлоконструкции по этому методу состоит в том чтобы за весь срок службы в ней не возникло ни первое ни второе предельное состояние.
Критериальное условие отсутствия предельного состояния имеет вид
где N – расчётное усилие в элементе конструкции;
Ф—несущая способность элемента.
Расчётное усилие определяется по формуле
гдеPНI – нормативная нагрузка действующая на конструкцию;
– коэффициент передачи I-ой нормативной нагрузки на рассчитываемый элемент.
Таким образом расчёт заранее предусматривает что в реальной жизни фактическая нагрузка может превысить нормативную чем и обеспечивается высокая гарантия надёжности.
Несущая способность элемента определяется по формуле
гдеF – геометрический фактор сечения;
Rp – расчётное сопротивление материала конструкции:
– коэффициент условий работы
где– коэффициент учитывающий степень ответственности конструкции;
– коэффициент учитывающий возможное уменьшение геометрических характеристик от тех которые были заложены в расчёт;
– коэффициент учитывающий неточность расчётных схем.
Определим коэффициент условий работы для нашего случая.
– разрушение с предупредительным признаком (отказ элемента вызывает непосредственную угрозу для жизни человека).
–при наличии гарантированных данных о фактических значениях допусков на профили элементов.
–для коробчатых пролётных балок при расположении подтележечного рельса в середине балки.
ВЫБОР МАТЕРИАЛА ДЛЯ НЕСУЩИХ И ВСПОМОГАТЕЛЬНЫХ ЭЛЕМЕНТОВ ОПРЕДЕЛЕНИЕ ДОПУСТИМЫХ РАСЧЁТНЫХ СОПРОТИВЛЕНИЙ И НАПРЯЖЕНИЙ
Металлические конструкции грузоподъёмных кранов изготовляют преимущественно из малоуглеродистых и низколегированных сталей поставляемых в виде проката различных типов.
Выбор марки стали для несущих элементов грузоподъёмных кранов осуществляют в зависимости от температурных условий в которых будет эксплуатироваться кран и режима работы.
В данном случае минимальная температура при которой будет эксплуатироваться машина – а режим работы - тяжелый. Исходя из этого принимаем в качестве материала сталь ВСт3сп5
Вид поставок – сортовой прокат: ГОСТ 2590-71 ГОСТ 2591-71 ГОСТ 535-79 ГОСТ 2879-69 ГОСТ 19771-74 ГОСТ 19772-74 ГОСТ 8278-83 ГОСТ 8281-80 ГОСТ 8282-83 ГОСТ 8283-77 ГОСТ 380-71 ГОСТ 8509-86 ГОСТ 8510-86 ГОСТ 8239-72.толстый ГОСТ 19903-74.тонкий ГОСТ 19903-74. Стрічка ГОСТ 503-81 ГОСТ 6009-74. Смуга ГОСТ 103-76 ГОСТ 82-70 ГОСТ 535-79. Паковки и кованные заготовки ГОСТ 8479-70. Труби ГОСТ 8734-75 ГОСТ 10706-76 ГОСТ 10705-80.
Физико-механические свойства и химический состав стали ВСт3с5 приведены в таблицах 1 и 2.
Таблица 1—Физико-механические свойства стали ВСт3с5
Напряжённое состояние
Смятие торцевой поверхности (при наличии пригонки)
Смятие местное - в цилиндрических шарнирах при плотном касании
Диаметральное сжатие катков при свободном касании
Напряжённое состояние сварного соединения
полуавтом. и ручная сварка с физическим контролем качества швов
Встык –полуавт. и ручная сварка при обычных методах контроля
Таблица 2—Химический состав стали 09Г2С
Для сварки стальных конструкций электроды должны соответствовать требованиям ГОСТ 9466-75 и ГОСТ 9467-75. В соответствии с [2] выбираем тип и марку электродов для ручной сварки при расчетной температуре до -200С (РТМ 24.090.52–85):
ОПРЕДЕЛЕНИЕ НАГРУЗОК И ИХ РАСЧЁТНЫХ СОЧЕТАНИЙ
Собственный вес моста принимаем равномерно распределённым по пролёту. Вес пролетной части моста определим используя усредненные
Принимаем вес пролетных частей моста крана (здесь 12– коэффициент учитывающий вес нерасчетных частей – 20%).
Интенсивность распределённой нагрузки от собственного веса пролётной части моста двухбалочного мостового крана находим по формуле:
где – пролет крана ;
– коэффициент перегрузки для веса металлической конструкции ;
Вес привода механизма передвижения крана определим по усредненным данным [1] . С учетом коэффициента перегрузки:
где – коэффициент перегрузки для веса механизма передвижения .
Кабину принимаем закрытую. В соответствии с [1] принимаем усредненный вес кабины С учетом коэффициента перегрузки:
где – коэффициент перегрузки для веса кабины .
Вес тележки принимаем по усредненным данным [1]
Коэффициент толчков учитывающий вертикальные динамические нагрузки возникающие из-за неровности пути [2].
Для первого случая нагружения коэффициент толчков определяется по формуле:
Значение динамических коэффициентов и определяют по формуле [9 с. 64] :
) при плавному пуску механизма
) при резком пуске механизма
где - приведенная к точки подвеса груза масса металлической конструкции крана и грузовой тележки
здесь - масса пролетного строения ( без опор и конечных балок) ;
- масса грузовой тележки
- перемещение точки подвеса груза вследствие статического удлинения канатов
здесь – длина участков каната (H – высота подъема груза) ;
n - число ветвей каната на котором весит груз n = 8 (принимается в зависимости от грузоподъемности);
– модуль упругости каната для средних условий ;
– площадь поперечного сечения каната ЛК - Р – 1400 d=19 5 мм ; .
– статический вертикальный прогиб конструкции от веса груза в месте его приложения
здесь L - пролет крана L = 345 м;
J - момент инерции одной половины моста;
E – модуль упругости материала металлоконструкции .
– скорость отрыва груза от основания ( для режимной группы 8К) [2 с. 135]
– поправочный коэффициент для кранов общего назначения можно принимать .
– коэффициент твердости металлоконструкции
где – приведенная к точки подвеса груза масса металлической конструкции.
Коэффициент режима нагрузки для кранов режимной группы 8К
При расчетов внутренних силовых факторов учитываем что число ходовых колес тележки потому что грузоподъемность крана 63 тон [1] и вес тележки и груза распределяются равномерно на все колеса то есть . Возможные сочетание нагрузок на ходовые колеса тележки приведенные в таблице 3
Таблица 3 - Подвижные нагрузки на мост крана
Расчетные сочетание я нагрузок
Сочетание нагрузок 1а max:
где–- коэффициент динамичности при плавном разгоне механизма подъема груза ;
– масса эквивалентного груза
где -коэффициент эквивалентности [2 с. 50 51 51]
Сочетание нагрузок Iа min:
Сочетание нагрузок 1в max:
где – коэффициент толчков при движении крана по неровностям подкрановой колеи с половинной скоростью =105.
Сочетание нагрузок Iв min:
Сочетание нагрузок Iia:
где— значение коэффициента перегрузок для веса груза [1 с. 118; 2 с. 166];
– коэффициент динамичности при резкому пуску механизма подъема .
Сочетание нагрузок Iiв:
где – коэффициент толчков при движении крана по неровностям подкрановой колеи с максимальной скоростью .
Сочетание нагрузок Iiс:
Сочетание нагрузок III:
Результаты вычислений сводим в таблицу 4
Таблица 4-Подвижные нагрузки которые действуют на мост крана
Давление ходового колеса тележки
Расчетные сочетание нагрузок
ВЫБОР РАСЧЁТНЫХ СХЕМ И ОПРЕДЕЛЕНИЕ ВНУТРЕННИХ СИЛОВЫХ ФАКТОРОВ В ЭЛЕМЕНТАХ
Для определения необходимого момента сопротивления сечения главной балки необходимо знать нагрузки действующие на балку и места их приложения. Неподвижные нагрузки являются закреплёнными поэтому места их приложения определяются из конструктивных соображений. Подвижные нагрузки изменяют своё влияние в зависимости от положения тележки поэтому необходимо поставить тележку в такое положение при котором её влияние будет максимальным то есть установим тележку по правилу Винклера. Расчётная схема для определения максимального изгибающего момента с установленной тележкой по правилу Винклера показана на рисунке 3.
Рисунок 3 – Расчётная схема приложения вертикальных нагрузок
комбинаций IIa и IIb
Расчёты (табл.3) показали что наибольшее значение давления ходовых колёс тележки имеет расчётный случай IIb следовательно при определении максимального изгибающего момента будем использовать этот расчетный случай.
Максимальный изгибающий момент действующий в сечении под колесом с давлением при четырехколесной тележке определим по формуле [8 с. 120]:
где – расстояние от равнодействующей до наиболее нагруженного колеса ;
–- расстояние от оси подкранового рельса до центра тяжести механизма передвижения ;
– расстояние от оси подкранового рельса до центра тяжести кабины .
Нагрузки действующие на металлоконструкцию в горизонтальной плоскости определяем для расчётной схемы показанной на рисунке 3. Горизонтальные нагрузки возникают при разгоне и торможении крана как силы инерции от вертикальных нагрузок. Как показывает практика горизонтальные составляющие от массы механизма передвижения и кабины незначительны ими можно пренебречь.
При определении горизонтальных инерционных нагрузок на крановый мост ускорение возникающее в период неустановившейся работы механизма передвижения следует определять по формуле
где – номинальная скорость передвижения крана ;
– время разгона крана которое можно принять равным .
Рисунок 4 — Расчётная схема приложения горизонтальных нагрузок
Определим суммарный горизонтальный изгибающий момент в расчётном сечении пролёта
где —горизонтальная составляющая от распределённой нагрузки
– горизонтальная составляющая от равнодействующей давления колес
S – коэффициент вычисляемый по формуле
—момент инерции пролётной балки относительно вертикальной оси ;
– момент инерции концевой балки относительно вертикальной оси.
ОПРЕДЕЛЕНИЕ РАЗМЕРОВ НЕСУЩИХ ЭЛЕМЕНТОВ МЕТАЛЛОКОНСТРУКЦИИ
Размеры поперечного сечения определяют из условия обеспечения прочности балки при действии нагрузок комбинации IIа. Момент сопротивления балки при изгибе в вертикальной плоскости должен отвечать условию
Исходя из этого определим момент сопротивления сечения при котором будет выполняться условие прочности
где – максимальный изгибающий момент в расчетном сечении главной балки в вертикальной плоскости (см. п. 6) ;
– коэффициент условий работы (см. п. 4) ;
– расчетное сопротивление материала на изгиб .
Оптимальную по условию минимума веса при обеспечении заданной прочности высоту стенки для балки с двумя осями симметрии определим по выражению
Принимает высоту сечения главной балки .
По рекомендациям ВНИИПТМАШа гибкость стенок целесообразно назначать в пределах Sc=100 300. в нашем случае гибкость стенки составляет
Условие рекомендуемой гибкости стенки обеспечивается так как .
Из условия обеспечения заданной минимальной жёсткости определим момент инерции балки в вертикальной плоскости
где – коэффициент жесткости моста
здесь – предельный относительный прогиб моста при действии номинальной подвижной нагрузки [1].
Оптимальную по минимуму веса высоту стенки при обеспечении заданной жёсткости определяют по формуле
Выше приведенные вычисления показывают что высота главной балки из условия прочности должна составлять . В связи с этим принимаем .
Рисунок 5 – Уточнённое сечение пролётной балки
Определим геометрические характеристики сечения главной балки c уточненными размерами:
Момент инерции главной балки относительно оси х–х
Момент инерции главной балки относительно оси y–y
Момент сопротивления сечения главной балки относительно оси х–х
Момент сопротивления сечения главной балки относительно оси y–y
Площадь поперечного сечения во втором приближении составляет
Разница площади между первым и вторым приближением
Так как разница меньше 10% уточняющий расчет не проводим.
Проверка прочности балки с вредней части пролета
Условия обеспечения прочности балки
Расчет проведен верно
ОБЕСПЕЧЕНИЕ МЕСТНОЙ И ОБЩЕЙ УСТОЙЧИВОСТИ
Размещение рёбер жёсткости.
Рёбра жёсткости (поперечные основные поперечные дополнительные и продольные) должны обеспечивать геометрическую неизменяемость поперечного сечения балки местную устойчивость стенок и сжатых поясов а при расположении рельса по оси верхнего пояса – прочность рельса и пояса при местном воздействии давлений колёс тележки. Определим гибкость стенки
В нашем случае гибкость стенки поэтому необходимо устанавливать поперечные и два продольных ребра жёсткости.
1 Размещение поперечных рёбер жёсткости
Для отсеков примыкающих к опорам шаг основных поперечных ребер в последующих отсеках . Ширина выступающей части основного поперечного ребра
Толщина ребра из условия обеспечения его устойчивости должна быть
Так как толщина стенки примем толщину ребра .
Момент инерции поперечного ребра относительно плоскости стенки должен быть
здесь – момент инерции поперечного ребра
При определении момента инерции ребра в расчёт должна включаться часть стенки шириной по обе стороны от ребра (рисунок 6)
Рисунок 6 — Расчётная схема при определении момента инерции ребра
Следовательно условие жесткости ребра выполняется так как
Проверим поперечное ребро по условиям работы верхней кромки на сжатие от местного давления колеса
гдеД— максимальное давление колеса тележки (сочетание IIа) ;
– длина линии контакта рельса и пояса для крановых рельс
здесь – ширина подошвы рельса для рельса КР100 (ГОСТ 7174-75).
z — расчётная зона распределения давления колеса по ребру
здесь – момент инерции рельса относительно собственной нейтральной оси х-х
– момент инерции пояса относительно собственной нейтральной оси х-х
Условие прочности верхней кромки выполняется
Шаг основных и дополнительных рёбер жёсткости являющихся опорами для рельса определим из условия прочности последнего
где – минимальный момент сопротивления рельса при изгибе
– допускаемое напряжения изгиба материала рельса .
Для обеспечения прочности пояса при действии местных напряжений от давления колес тележки принимаем конструктивно шаг малых диафрагм шаг больших диафрагм а=3а1=3*10=30м. В концевых частях балки ребра жесткости ставим в соответствии с необходимостью приварки фундаментов под привод механизма передвижения крана. Размещение основных и дополнительных поперечных рёбер жёсткости показано на рисунке 7.
Рисунок 7 — Схема установки основных и дополнительных поперечных рёбер жёсткости
При контакте подошвы рельса с поясом балки пояс находится в плоском напряжённом состоянии и его прочность необходимо проверить по условию
где – напряжения определяемые по формуле
здесь – напряжение в балке от её общего изгиба в продольном направлении
– местные нормальные напряжения в поясе поперёк продольной оси балки
здесь – коэффициент принимаемый по таблице [1] ;
– сила передающаяся на поясной лист через рельс от давления ходового колеса тележки
– местные нормальные напряжения в поясе вдоль продольной оси балки
Условие прочности пояса выполняется.
2 Размещение продольных рёбер жёсткости
Продольные ребра жесткости ставятся на расстоянии от крайней сжатой кромки стенки: первое – второе [1].
Примем следующее расположение продольных ребер жесткости: . Толщина ребра . Ширина ребра .
Требуемое значение момента инерции продольного ребра относительно плоскости стенки [1]
Момент инерции продольного ребра относительно стенки
Условие выполняется так как .
Момент инерции продольного ребра относительно кромки пояса должен быть
Определим момент инерции продольного ребра относительно кромки пояса
Установка продольных ребер показана на рисунке 8.
Рисунок 8 —Схема установки поперечных рёбер жёсткости
ПРОВЕРКА ПРОЧНОСТИ ОПОРНОГО СЕЧЕНИЯ ПРОЛЁТНОЙ БАЛКИ
Прочность опорного сечения пролётной балки проверяем для случая действия нагрузок IIа.
Определим суммарный изгибающий момент в узле соединения пролётной балки с концевой. Наибольший момент будет со стороны колеса с давлением .
Определим суммарный момент возникающий в узле сопряжения главной балки с концевой при установки тележки в крайнее положение (рис.9).
Рисунок 9 — Расчётная схема приложения горизонтальных нагрузок при установке тележки в крайнее положение
Наибольший горизонтальный изгибающий момент для пролетной балки действует в узле ее сопряжения с менее нагруженной концевой балкой и будет равен
где – коэффициент рассчитываемый по формуле
– коэффициент рассчитываемый по формуле
– давление на приводные колеса
здесь – давление на приводные колеса со стороны менее нагруженной концевой балки (рис. 9)
– коэффициент сцепления колес с рельсами для открытого воздуха ;
– количество приводных колес ;
– общее количество колес .
Рисунок 10 – Схема определения максимальных давлений на ходовые колеса
Наибольший горизонтальный изгибающий момент для пролетной балки действует в узле ее сопряжения с более нагруженной концевой балкой и будет равен
ПРОВЕРКА ПРОЧНОСТИ СВАРНЫХ ШВОВ
Прочность сварных швов соединяющих пояс со стенкой проверяют по формуле
где –- наибольшая поперечная сила в рассматриваемом сечении возникающая при установке тележки в крайнее положение (см. рис.9)
–- статический момент брутто пояса балки относительно её общей нейтральной оси
– коэффициент принимаемый в зависимости от вида сварки для полуавтоматической однопроходной сварки
– толщина углового шва принимаемая равной катету вписанного в сечение шва равнобедренного треугольника ;
–-момент инерции брутто сечения балки
Прочность поясного шва обеспечена.
ПРОВЕРКА МЕТАЛЛОКОНСТРУКЦИИ МОСТА НА СТАТИЧЕСКУЮ ЖЁСТКОСТЬ
Статическую жёсткость моста в вертикальной плоскости оценивают по статическому прогибу балок в середине пролёта при действии нагрузок комбинации.
Прогиб каждой пролётной балки двухбалочного моста от действия подвижной нагрузки равен
где – равнодействующая давлений колёс тележки
– момент инерции балки при изгибе в вертикальной плоскости
– размер вычисляемый по формуле
– предельный относительный прогиб [1].
Статическая жёсткость моста удовлетворительная.
РАСЧЁТ СТРОИТЕЛЬНОГО ПОДЪЁМА
При пролётах мостов более 17м пролётным балкам должен придаваться строительный подъём который должен быть равен
где – прогиб пролётной балки от действия постоянных нагрузок
– прогиб пролетной балки от действия подвижных нагрузок .
Принимаем строительный подъем
Теоретический закон изменения ординаты строительного подъёма по пролёту f(z) принимают обычно в виде синусоиды. Из технологических соображений линию строительного подъёма выполняют ломанной за счёт раскроя листов в виде трапеций или путём соответствующей раскладки листов.
Скос при схеме раскроя по рисунку 11 равен
Рисунок 11 – Схема раскроя листов пролётной балки
ЗАЩИТА МЕТАЛЛОКОНСТРУКЦИИ ОТ КОРРОЗИИ
Согласно документации по ГОСТ 9402–80 – единая система защиты металлоконструкции от коррозии. Защита металлоконструкций от коррозий производится при помощи покрытия лакокрасками.
С Н и П – строительные нормы и правила требуют три основных операции:
- подготовка поверхности;
- грунтовка поверхности;
- нанесение слоев краски;
Учитывая что данный кран работает в химическом цехе с агрессивной средой принимаем:
– покраска – М – 226 ПФ – 433 в 5 слоев.
НАУЧНО-ИССЛЕДОВАТЕЛЬСКАЯ РАБОТА
1 Изготовление главной балки коробчатого сечения
Главная балка коробчатого сечения электромостовых кранов состоит из нижнего пояса боковых вертикальных стенок больших и малых диафрагм верхнего пояса и уголков. Вертикальные стенки нижний и верхний пояса состоят из отдельных элементов сваренных встык. Для обеспечения строительного подъема вертикальные стенки изготовляют из отдельных элементов специального раскроя.
Главные балки в зависимости от грузоподъемности моста и его пролета отличаются размерами сечения коробки и количеством вваренных диафрагм. Проведенная унификация главных балок позволила получить восемь типоразмеров балок по высоте и четыре по ширине с длиной пролета от 10 000 до 34 500 мм и массой от 09 до 190т и разработать типовой технологический процесс изготовления положенный в основу создания переменно - поточной механизированной линии с применением специальной оснастки. Переменно - поточная механизированная линия сборки и сварки главных балок состоит из пяти специализированных рабочих мест.
На рассматриваемой поточной линии применен способ сборки главной балки «россыпью». Сущность этого способа заключается в том что строительный подъем создается с помощью специального раскроя и последовательной сборки элементов вертикальных стенок с верхним поясом и между собой. Линия оборудована специальными самоходными порталами оснащенными траверсами с вакуумными грузозахватными приспособлениями (вакуумприсосами) для захвата листов в горизонтальном и вертикальном положении и передачи их на сборку. Для перемещения балки с первого рабочего места на второе служат пневмотолкатели и челночные тележки. Линия снабжена также четырехкрюковым электромостовым краном предназначенным для перемещения и кантовки главной балки со второго рабочего места на последующие рабочие места.
Управление порталом и захватом производится с пульта управления установленного на металлоконструкции портала. Траверса представляет собой жесткую раму закрытую сверху кожухом и имеющую ушко для подвеса. На раме смонтированы: электродвигатель электрошкаф вакуумный насос с ресивером и четырьмя вакуумными присосами соединенными между собой трубопроводом и сирена для подачи сигнала. Вакуумный насос создает разрежение воздуха в ресивере 93 кПа (700 мм рт. ст.) замеряемое вакуумметром. Применение ресивера дает возможность сократить время на зажим заготовки снизить мощность насоса увеличить безопасность работы при вынужденной остановке вакуумного насоса. Вакуумный присос представляет собой чашу из листовой резины внутри которой имеется отверстие для откачки воздуха. Пружина служит для улучшения качества работы присоса надежности присасывания и возвращения чаши в исходное положение. Вакуумные грузозахватные приспособления обеспечивая жесткую связь с поднимаемым грузом и быстроту его захвата являются перспективными как с точки зрения повышения производительности труда так и с точки зрения возможности автоматизации подъемно - транспортных работ. Вакуумные захваты работают по принципу непосредственной передачи атмосферного давления на поднимаемый груз.
Работоспособность вакуумного захвата поднимающего и транспортирующего груз обеспечивается только при условии создания такой силы прижатия Q которая уравновешивает все противодействующие силы Q0 т. е. необходимо выполнить неравенство Q > Q0 причем вакуумный захват рекомендуется располагать над центром масс груза в противном случае появляются моменты сил отрыва.
К противодействующим (отрывающим) силам Q0 относятся собственная масса груза инерционные силы силы лобового сопротивления и силы связанные с изменением давлений атмосферного и внутри вакуумной камеры и др. Кроме того учитывая разнохарактерность эксплуатационных условий и для обеспечения абсолютной безопасности работы вакуумных захватов целесообразно
Изготовление главных балок на переменно - поточной линии производится в следующем порядке.
Первое рабочее место состоит из двух сборочно-сварочных стендов на которых производятся сборка и полуавтоматическая сварка верхнего пояса на магнитно - флюсовой подушке расстановка и приварка диафрагм и уголков жесткости. Элементы верхнего пояса в горизонтальном положении подаются на сборочный стенд последовательно с помощью самоходного портала снабженного траверсой с вакуумными присосами. Стыки элементов верхнего пояса последовательно располагаются над магнитно - флюсовой подушкой служащей для выравнивания кромок стыкуемых элементов после чего они прихватываются друг к другу. Здесь же на стыках по обе стороны устанавливают и приваривают фальшпланки. Далее поочередно с помощью сварочного полуавтомата завариваются стыки зачищают заподлицо пневмо-шлифовальной машинкой стыковые швы в местах прилегания вертикальных стенок и размечают пояса для постановки вертикальных стенок и диафрагм. На пояс по разметке вручную под угольник устанавливают и прихватывают диафрагмы и уголки жесткости между большими диафрагмами. Собранный узел (гребенка) с помощью челночных тележек передается на второй сварочный стенд где и выполняется полуавтоматическая сварка диафрагм к поясу от середины к краям.
Второе рабочее место предназначено для установки и прихватки вертикальных стенок к «гребенке». С первого рабочего места «гребенка» подается с помощью челночных тележек. Самоходный портал с помощью вакуумных присосов подает два концевых листа на сборку в вертикальном положении. Другой самоходный портал поджимает пневмозажимами эти листы и прихватывает их к поясу диафрагмам и уголкам жесткости. Аналогичную операцию повторяют и с другими листами.
Третье рабочее место состоящее из двух сварочных стендов служит для приварки диафрагм и уголков жесткости к вертикальным стенкам подваркам внутренних поперечных стыков вертикальных стенок. Балка подается на третье рабочее место с помощью крана вначале с кантовкой ее на 90° а затем на 180°. Сварку ведут вручную.
Четвертое рабочее место также состоит из двух сборочно - сварочных стендов. На втором стенде происходит сборка и сварка нижнего пояса аналогично первой операции. На первый стенд балка подается с помощью крана подводится к ней тележка с гидродомкратами и балка растягивается до полного удаления гофр возникших от деформаций при сварке. Далее с помощью кантователя и сборочного портала балка накрывается нижним поясом с последующей прихваткой к вертикальным стенкам от середины к концам. Поджатие нижнего пояса к вертикальным стенкам достигается с помощью пневмоприжимов сборочного портала и с использованием струбцин. После прихватки нижнего пояса тележку с гидродомкратами отводят в исходное положение и подводят сварочный полуавтомат для заварки стыков нижнего пояса и верхнего пояса с кантовкой балки на 180° с помощью крана.
На пятом рабочем месте выполняется автоматическая сварка поперечных и продольных швов главных балок. С четвертого рабочего места на пятое главная балка подается с помощью четырехкрюкового мостового крана. Здесь заваривают ручной сваркой все незаваренные автоматом участки поясных швов пневмошлифовальной машинкой зачищают швы и балка передается на рентгеновскую установку для просвечивания сварных швов. К числу недостатков данной линии необходимо отнести следующее:
- ввиду того что при изготовлении элементов вертикальных стенок бывает неточный раскрой листа и в процессе сборки в местах стыка получаются зазоры разной величины в результате сборки вертикальные стенки часто получают строительный подъем отличающийся от требуемого. Замеряют же строительный подъем после полной сборки главной балки когда уже собранную с дефектом балку трудно исправить;
- сварка диафрагм уголков жесткости внутренних стыковых швов вертикальных стенок выполняется внутри балки вручную в тяжелых условиях (сварщику приходится дышать сварочными газами вредными для здоровья). Все это не исключает возможности появления различных дефектов вплоть до отрыва диафрагм от вертикальных стенок. Ручная сварка малопроизводительна и является слабым звеном на потоке.
При проектировании второй поточной линии по изготовлению главных балок коробчатого сечения длиной до 30м для учета этих недостатков может быть использован «гардинный» способ сборки балок. Сущность его заключается в том что на «гребенку» (верхний пояс с диафрагмами) устанавливают не отдельные элементы вертикальных стенок а обе вертикальные стенки в виде гардин собранных на отдельных специальных стендах по тщательно выверенным упорам. При сборке гардин все погрешности раскроя элементов самокомпенсируются при их выставлении благодаря регулированию зазора в стыках таким образом гардины получаются в точном соответствии с необходимым строительным подъемом. В вертикальной плоскости гардины являются весьма жесткими и в дальнейшем они служат как бы шаблонами к которым поджимается гибкая «гребенка» и прихватывается.
В данном случае значительно повышается качество сборки и производительность труда. При использовании кантователей позволяющих кантовать пояса непосредственно над стендом есть возможность сваривать пояса с обеих сторон высокопроизводительными способами.
2 Рельсы и крановые пути
Для направления движения кранов и тележек применяют стальные рельсы и направляющие. Для колес с цилиндрическим ободом применяют рельсы с выпуклыми и плоскими головками для колес с цилиндрическим ободом — только с выпуклыми головками. Горизонтальные ролики взаимодействуют либо с боковыми поверхностями головок рельсов либо с дополнительными плоскими и выпуклыми направляющими закрепляемыми на подкрановых балках. В качестве рельсов с выпуклыми головками применяют (рис.11) крановые рельсы (а) типа КР по ГОСТ 4121—76 и железнодорожные рельсы (б) типа Р по ГОСТ 6368—52 а в качестве рельсов с плоскими головками — сталь квадратного профиля (в).
Для компенсации неточности установки колес и укладки рельсов ширина последних должна быть меньше ширины рабочей части обода колес: крановых двухребордных с цилиндрическим ободом — на 30 мм крановых двухребордных с коническим ободом — на 40 мм тележечных двухребордных — на 15—20 мм тележечных одноребордных — на 30 мм.
Крановые рельсы закрепляют к подкрановым балкам строительной конструкции которые изготовляют из профильного стального проката а рельсы тележек — непосредственно к металлоконструкции моста крана.
Значительно уменьшает износ ходовых колес выполнение стыков рельсов сварными с расположением стыков в шахматном порядке со смещением не менее 3 м. При этом ударные нагрузки снижаются примерно в 2 раза. Для устранения дефектов подкрановых балок целесообразна укладка под рельс сменного стального листа а для повышения долговечности кранов работающих в режиме Т и их рельсов — применение эластичных подкладок из неопрена. Такие подкладки не только снижают ударные нагрузки (при толщине прокладок 8 мм — до 30%) но и уменьшают степень концентрации вертикальной нагрузки передаваемой с пояса на вертикальную стенку подкрановой балки.
Закрепление рельсов должно исключить возможность их продольного и бокового смещения при работе крана (рис.12 а). При закреплении рельсов с помощью сварки должна исключаться возможность их деформации.
В ряде стран крепление рельсов к балкам выполняется как жестким так и подвижным. Жесткие крепления (рис.12 б) допускают выверку рельса благодаря овальным отверстиям в прижимных планках. При этом отверстия в подкладках сверлятся по месту. Крепление этого же типа с планками соответственно из ковкого чугуна или из пружинной стали используется при легком режиме работы крана.
Рисунок 12 - Крепление рельсов
Подвижное крепление (рис.12 в) допускает перемещение рельса за счет выборки зазора между подкладками и подошвой рельса. Возможность поперечного перемещения рельса обеспечивается и при использовании упругих прижимов которые крепятся к балке шпильками и платиками или шпильками и фигурными шайбами. Подвижное крепление позволяет в ряде случаев увеличить срок службы колес так как при этом креплении уменьшается давление в точке контакта рельса с ребордой колеса.
Узел крепления рельса к балке при использовании которого достигается возможность закрепления рельсов разных типов показан на рис.12 (г). Он включает пластины которые привариваются к подкрановой балке на участках Б и устанавливаются относительно подошвы рельса с небольшим зазором. Пластины имеют косые пазы и гнезда в которые ставят болты со сферическими головками. Последние самоустанавливаясь позволяют накладкам 3 занимать нужное положение. Косое расположение пазов препятствует смещению болтов даже при ослаблении их затяжки.
Применение механизмов передвижения с безребордными колесами и горизонтальными роликами вызывает дополнительные требования к креплению подкрановых рельсов к балкам. Ребордные колеса воздействуют на рельсы в горизонтальной плоскости (поперечные силы при соприкосновении реборды колеса с рельсом и при поперечном проскальзывании колеса по рельсу инерционные силы при разгоне и торможении). Однако при этом возможность поперечного перемещения рельса ограничивается величиной зазоров между ребордами и рельсом. При безребордных колесах такие ограничения смещения рельсов отсутствуют. В связи с этим происходит постепенное ослабление крепления рельсов и сдвиг их в поперечном направлении. Аналогичные явления наблюдаются с подкрановыми балками при наличии зазоров в их креплении. Одним из способов устранения смещения рельсов является приварка к подкрановой балке платиков с шагом около 800 мм для упора в них подошвы рельса.
В курсовой работе был подробно рассмотрен и изучен мост грузоподъемного крана.
В ходе работы был избран и обоснован материал для несущих и вспомогательных элементов определенны их расчетные сопротивления и допустимые напряжения спроектирована главная балка выбрана общая схема металлоконструкции и их соединения с основными конструктивными параметрами. В процессе выполнения работы ознакомились с подобной продукцией которая выпускается современным машиностроением.
Были определены нагрузки и их расчетные соединения. Сделан выбор расчетных схем и определенные внутренние силовые факторы в элементах.
Сделаны необходимые проверочные расчеты в том числе проверка на твердость и стойкость и расчет строительного подъема.
В ходе работы ознакомились с основными видами сварных швов и методами их обозначения на чертежах.
Казак С.А. Курсовое проектирование грузоподъёмных машин: учебное пособие для студентов машиностр. спец. вузов С.А.Казак В.Е. Дусье Е.С. Кузнецов [и др.].-М.: Высш. шк. 1989. – 319 с.: ил. ISBN 000-000-000-000-0.
Гохберг М.М. Справочник по кранам. В 2 т. Т. 1. Характеристики материалов и нагрузок расчёт металлоконструкций М.М. Гохберг.– М.: Машиностроение 1988. – 536 с. ISBN 000-000-000-000-0.
Федоткин М. Сортамент чёрных металлов М. Федоткин–М.: Издательство стандартов 1991. – 540 с. ISBN 000-000-000-000-0.
Александров М.П. Курсовое проектирование грузоподъемных машин М.П.Александров Н.Ф.Руденко И.Г.Лысяков.– 3-е узд. перераб. и доп.М.: Машиностроение 1971.-464с.: ил. ISBN 000-000-000-000-0.
list_2.dwg

list_1.dwg

Раскрой нижнего пояса
ПТМ.КР.01.01.00.00.00.ЗБ
Рекомендуемые чертежи
- 20.06.2021
Свободное скачивание на сегодня
Обновление через: 6 часов 5 минут