Автоматизированная система управления конвертированием медно-никелевого штейна в конверторе


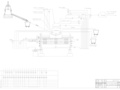
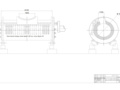
- Добавлен: 25.10.2022
- Размер: 2 MB
- Закачек: 3
Подписаться на ежедневные обновления каталога:
Описание
Автоматизированная система управления конвертированием медно-никелевого штейна в конверторе
Состав проекта
![]() |
![]() |
![]() ![]() ![]() ![]() |
![]() |
![]() ![]() ![]() ![]() |
![]() ![]() ![]() |
Дополнительная информация
Контент чертежей
funktsionalnaya_skhema.dwg

т. для конвертирования
медно-никелевого штейна
В цех по производству
skhema.dwg

т. для конвертирования
медно-никелевого штейна
Расстояние между осями фурм 150 мм
gotovy.doc
Описана технология процесса конвертирования. Произведен расчет материального и теплового балансов газоходной и воздухопродводящей систем горизонтального конвертера. Составлена математическая модель. Приведены статьи экологии электроснабжения экономики производства и организации производства.
Дипломный проект содержит 120 страниц 31 таблиц 19 рисунок графический материал представлен на 2 листах формата А1.
The subject of this graduation paper is "Automated control system conversionof copper-nickel mattein the convertercapacity of 200 tonsper year" deals with converting technology process.
The calculation of the material and heat equilibrium gas air feeding systems and horizontal converter has been made. The mathematical model has been made. The graduation paper consist of some parts. They are devoted to ecology electrical supply economicsof production and production systematizations.
Graduation paper contains: pages 120 tables 31 and 19 illustrations drawings 2 A1.
ТЕХНОЛОГИЧЕСКАЯ ЧАСТЬ7
1. Общие сведения о процессе конвертирования Сu –Ni штейнов на ГМК «Печенганикель»7
1.1. Исходное сырье7
1.2 Конечные продукты конвертирования8
1.4. Конвертерный шлак9
1.5. Конвертерные газы10
2. Принципиальная технологическая схема переработки11
сульфидных медно-никелевых руд.11
3. Порядок ведения процесса конвертирования12
3.1. Зарядка конвертера12
3.2. Период набора массы12
3.3. "Варка" файнштейна.14
3.4. Разливка и охлаждение файнштейна16
4. Расчёт основных статей материального баланса конвертирования17
4.1. Вещественный состав штейна17
4.2.металлов в каждом продукте19
4.3.и состав файнштейна21
4.6.кварцевого флюса масса и состав конверторного шлака26
4.7. Количество воздуха и отходящих газов29
4.8. Материальный баланс процесса конвертирования31
5. Расчёт основных статей теплового баланса КОНВЕРТИРОВАНИЯ31
5.1. Статьи прихода тепла33
5.2. Статьи расхода тепла34
6. Расчет газоходной системы35
6.1. Участок печь - котел36
6.2. Участок котел - пылевая камера37
6.3. Участок пылевая камера - дымосос37
6.4 Участок дымосос - электрофильтр37
6.5. Участок печь - котел37
6.6. Участок котел - пылевая камера38
6.7. Участок пылевая камера - дымосос38
6.8. Участок дымосос - электрофильтр38
СПЕЦИАЛЬНАЯ ЧАСТЬ.40
1. Назначение конвертера.40
2. Анализ управляемости горизонтального конвертера40
3. Основные цели управления технологическим процессом и назначение АСУТП42
4. Описание функций АСУТП43
4.1.Нижний уровень45
4.2.Средний уровень54
4.3.Верхний уровень57
5. Описание аналоговой информации64
6. Перечень дискретных сигналов65
7. Характеристика параметров контроля и регулирования процесса конвертирования медно-никелевых штейнов.66
ТЕОРЕТИЧЕСКАЯ ЧАСТЬ71
1. Описание математической модели71
ЭЛЕКТРОТЕХНИЧЕСКАЯ ЧАСТЬ76
1. Расчет нагрузки79
БЕЗОПАСНОСТЬ ЖИЗНЕДЕЯТЕЛЬНОСТИ83
1.1. Анализ вредных и опасных факторов производства83
1.2. Статистика травматизма и профессиональных заболеваний85
1.3. Техника безопасности87
1.4. Промсанитария. Нормы для данного производства94
1.5. Расчет искусственного освещения при использовании светильников с лампами накаливания96
1.6. Пожарная безопасность97
2. Безопасность жизнедеятельности при чрезвычайных ситуациях98
2.1. Анализ потенциально-возможных чрезвычайных ситуаций98
2.2. План предупреждения и ликвидации чрезвычайной ситуации98
ЭКОНОМИКА ПРОИЗВОДСТВА ОРГАНИЗАЦИЯ ТРУДА100
1. Условия оплаты100
2. Количество рабочих и выходных дней в году101
3. Расчет численности работников103
4. Обоснование доплат106
5. Расчет затрат на производство продукции110
6. Расчет финансовых результатов проекта113
7. Расчет показателей эффективности проекта114
СПИСОК ИСПОЛЬЗОВАННОЙ ЛИТЕРАТУРЫ116
В настоящее время на ГМК “Печенганикель” намечается реконструкция. В связи с тем что экология вокруг плавильного цеха достигла критической отметки нужно решать задачи по правильной утилизации газов содержащих SO2 которые могут привести к улучшению экологии и повысить технико-экономические показатели работы сернокислотного цеха. Следовательно одним из основных направлений реконструкции является плавильный цех где актуальной является задача разработки ситуационной системы управления газовым режимом конвертера.
Конвертерный передел является частью плавильного цеха. В нём размещаются горизонтальные конвертеры – агрегаты в которых продувается воздухом медно-никелевый штейн поступающий из рудно-термических печей с целью удаления из него железа и частично серы.
Управление подачей газов на сернокислотное производство на ГМК “Печенганикель” осуществляется оператором вручную который наблюдая за показанием стрелочных приборов расположенных на щите и отображающих расход дутья разрежение в газовом тракте и температурой газов переключает заслонки на газоходах направляя газы в сернокислотный цех или в дымовую трубу. Поскольку наблюдение за большим количеством приборов затруднительно оператор часто допускает ошибки срабатывает “человеческий фактор” приводящий к снижению технологических показателей.
ТЕХНОЛОГИЧЕСКАЯ ЧАСТЬ
1. Общие сведения о процессе конвертирования Сu –Ni штейнов на ГМК «Печенганикель»
Целью конвертерного процесса является удаление из штейна практически всего железа и получение продукта который называется файнштейном. В файнштейн с возможной полнотой должны быть извлечены никель медь кобальт и благородные металлы (платина рутений родий иридий осмий).
Удаление из штейна железа достигается за счет продувки сжатого воздуха через слой расплавленного штейна залитого в конвертер. Образовавшаяся закись железа нерастворима в штейне удельный вес ее меньше веса штейна поэтому она всплывает на поверхность ванны и соединяется с загруженным в конвертер кремнеземом образуя силикатный шлак.
По мере окисления железа происходит постепенное обогащение конвертерной массы сульфидами никеля меди кобальта. Продувку заканчивают когда в массе остается 25 – 35% железа. В результате почти полного перевода железа в шлак получается сплав сульфидов никеля Ni3S 2 и меди СuS – файнштейн.
Кроме файнштейна и конвертерного шлака продуктами конвертирования являются конвертерные газы содержащие сернистый ангидрид и уносящие из конвертера значительное количество пыли. Конвертерная пыль уловленная в пылевой камере газоходной системе электрофильтрах является оборотным продуктом и возвращается в конвертеры.
Исходными металлосодержащими материалами для получения файнштейна в конвертерах являются:
Штейн из руднотермических печей получаемый при плавке в РТП руды обожженных окатышей оборотного шлака и флюса.
Оборотные материалы:
- оборотные корки (скрап файнштейна выбивки из штейновых и шлаковых ковшей желобов и др.);
- конвертерная пыль из пылевых камер газоходов электрофильтров;
- медно-никелевый шлак с родственных комбинатов;
- вторичное сырье (лом цветных металлов) с высоким содержанием никеля меди и кобальта.
Возможна переработка в конвертерах высокосернистой (25-27% серы) сульфидной медно-никелевой руды (типа норильской руды).
В качестве флюса при конвертировании используют речной песок (65-68% SiO2) и кварцит (70-75% SiO2).
1.2 Конечные продукты конвертирования
Конечными продуктами конвертирования являются: медно-никелевый файнштейн конвертерный шлак конвертерные газы и конвертерная пыль.
Файнштейн содержит 36-45% Ni 28-36% Cu 06-11% Со 225-24% S 25-35% Fe незначительное количество золота серебра и металлов платиновой группы (Pt Pd Ru Jr Os).
Соотношение между медью и никелем в файнштейне определяется составом исходного штейна и не должно превышать 1:1.
Продувать файнштейн до содержания Ni+Cu выше 77% не выгодно так как это приведет к полному окислению железа и вызовет значительный переход в шлаки кобальта и никеля.
Поэтому для удержания кобальта в файнштейне оставляют 25-35% железа.
Особенностью медно-никелевого файнштейна является наличие в нем некоторого количества (2-4%) металлического сплава меди и никеля. Действительно если пересчитать содержание серы в файнштейне на сплав сульфидов Ni3S2 и Cu2S то окажется что количество серы недостаточно до полного связывания металлов в сульфиды. Дефицит серы и наличие свободных металлов объясняется протеканием в период «варки» файнштейна следующих реакций:
Cu2S +2Cu2O = 6Cu + SO2
Cu + Ni3S2 = 3Ni + 2Cu2S
Образующийся в результате этих реакций медно-никелевый сплав содержит 55-65% Ni до 20-22% Cu и 5-10% S. В сплаве концентрируется около 90% содержащихся в файнштейне благородных металлов. Сплав обладает магнитными свойствами и может быть выделен магнитной сепарацией тонко размолотого файнштейна.
Температура плавления файнштейна находится в пределах 880-9000С удельный вес – 55гсм3.
Охлажденный медно-никелевый файнштейн имеет ярко выраженное кристаллическое строение. Оно состоит из кристаллического сульфида никеля с незначительной примесью меди кристаллов сульфида меди с примесью никеля и кристаллов металлического сплава никеля и меди.
1.4. Конвертерный шлак
Конвертерный шлак представляет собой сложный расплав из никеля меди кобальта серы железа двуокиси кремния окиси магния окиси алюминия и окиси кальция. В конвертерном шлаке суммарное содержание фаялита 2FeO*SiO2 и магнетита Fe3O4 достигает 90%. Температура плавления конвертерных шлаков составляет 1150-11800С удельный вес 35-42 гсм3. Вязкость при 12000С 5 пуаз. Цветные металлы в шлаке находятся в различной форме и распределяются следующим образом:
-никель на 50% в виде сульфидных включений и на 50% в виде окисла (силиката)
-медь на 65% в виде растворенного сульфида и на 35% в виде сульфидных включений
-кобальт на 90% в виде окисла (силиката) и на 10% в виде сульфида.
На свойства конвертерного шлака большое влияние оказывает содержание магнетита. Растворяясь в шлаке магнетит ухудшает его свойства повышая вязкость температуру плавления и удельный вес увеличивает в шлаке содержание никеля и других металлов. Содержание магнетита в шлаке зависит от температуры процесса и содержания кремнезема в конвертерном шлаке. Образование магнетита происходит при температуре ниже 12300С.
Разложение магнетита происходит при температуре более 12300С по реакции:
Fe3O4 + FeS + 5SiO2 = 5(2FeO*SiO2) + SO2
Увеличение содержания кремнекислоты в шлаках способствует уменьшению содержания в них магнетита. При «рядовых» конвертерных шлаках содержащих 19-21% SiO2 содержание магнетита составляет 20-22%.
В зависимости от состава штейна флюсов и холодных приставок выход конвертерного шлака достигает 110% от горячего штейна.
Высокое содержание цветных металлов в конвертерном шлаке объясняется постоянным перемешиванием ванны конвертера в процессе продувки штейна и плохим отстаиванием шлака перед его сливом из конвертера так как содержимое ванны не выдерживается достаточное время в покое.
В связи с этим конвертерный шлак не является отвальным продуктом направляется в дальнейшую переработку в РТП для извлечения кобальта никеля и меди.
1.5. Конвертерные газы
Основными составляющими конвертерного газа являются азот кислород сернистый ангидрид. В незначительном (01-05%) количестве содержится в газах SO3 получаемый в результате окисления SO2 при выходе его из ванны конвертера.
При выходе из горловины конвертера газы сильно разбавляются воздухом так как подсосы в напыльник и пылевую камеру составляют 300-400%. Подсосы создаются при плохой герметичности оборудования под действием разряжения в газоходной системе (10-20 мм вод.ст.) создаваемого дымовой трубой или дымососом. Из-за подсоса воздуха концентрация сернистого газа после пылевой камеры снижается до 2-35%.
В результате подсосов температура отходящих из горловины конвертера газов снижается с 1000 - 11000С после пылевой камеры.
Конвертерные газы с содержанием SO2 более 28% направляется в сернокислотное производство с содержанием менее 28% SO2 – в дымовую трубу.
Конвертерная пыль образуется в результате разбрызгивания массы в процессе интенсивной продувки расплава воздухом. Конвертерные газы выносят из горловины конвертера образующуюся пыль. Большая часть пыли (крупная фракция более 01 мм) оседает в системе пылеулавливания конвертера (пылевая камера газоходы) меньшая (тонкая фракция менее 01мм) улавливается в электрофильтрах частично сбрасывается в трубу.
Количество выносимой из конвертера пыли составляет 07 – 15% от веса горячего штейна и зависит от характера загружаемых в конвертер материалов.
Средняя запыленность отходящих газов составляет 125гнм3 (при отсутствии в шихте сыпучих материалов); после пылевой камеры 02 – 062гнм3; после электрофильтра 002гнм3.
Химический состав конвертерной пыли: никель 11 – 15% медь 7 – 9% кобальт 03 – 04%железо 25 – 45% сера 15 – 25% двуокись кремния 15 – 25%.
2. Принципиальная технологическая схема переработки
сульфидных медно-никелевых руд.
3. Порядок ведения процесса конвертирования
При конвертировании штейнов выделяют следующие технологические операции:
Период набора массы.
Разливка и охлаждение файнштейна.
3.1. Зарядка конвертера
В конвертер заливают 3 – 5 ковшей штейна рудно-термических печей. Для сокращения времени зарядки и следовательно сохранения температуры конвертера и теплосодержания штейна залитого в конвертер зарядку необходимо выполнять как можно быстрее: выдавать штейн одновременно из нескольких печей не допускать простоя штейна в ковшах.
После заливки штейна в конвертер устанавливают под дутье и сразу прочищают фурмы.
3.2. Период набора массы
В начале продувки штейна из-за низкой температуры расплава в конвертере (1100 – 1150 0С) окисление сульфида железа протекает в основном до магнетита Fe3O4. При этом температура в ванне конвертера повышается. Через 10 мин. после установки конвертера под дутье когда масса конвертера достаточно разогрелась (»1210 0С) в конвертер загружается кварцевый флюс и начинается процесс шлакования закиси железа.
Загрузка кварцевого флюса в конвертер производится через горловину конвертера совком (6т).
Количество загрузочного флюса определяется из расчета получения шлака с содержанием не менее 22% SiO2.
Несвоевременная подача флюса может привести к аварийному состоянию т.к. при продувке с недостатком кремнезема в ванне накапливается много магнетита и когда загружают флюс происходит бурная реакция - ванна вскипает. В результате образуется пенистый шлак который не вмещается в объеме конвертера и расплав начинается переливаться через горловину.
Во время дутья производится регулярная чистка фурм с поддержанием расхода не менее 36000 нм3 час (600 нм3 мин).
Упругость дутья в фурмоколлекторе должна быть не менее 08 атм. Давление и расход воздуха контролируется приборами установленными на пульте управления конвертером.
При указанном расходе воздуха процессы окисления сульфидов протекают достаточно интенсивно и температура в конвертере повышается. Оптимальное значение температуры процесса – 1240 0C. Регулировка температуры процесса производится загрузкой флюса холодных присадок расходом воздуха.
Через 50 мин. в конвертер заливают еще 2 ковша штейна и добавляют 1 совок (6т) кварцевого флюса.
Общая продолжительность первой продувки составляет 90 мин. К концу продувки в ванне конвертера накапливается шлак. По готовности шлака и его переполнении в конвертере цвет факела конвертерных газов приобретает желтоватый оттенок и над горловиной появляются шлаковые всплески ярко-белого цвета (в виде искр). Конвертер останавливают на слив шлака.
Перед сливом шлака первой продувки в конвертер заливают 1 ковш металлизированного штейна с обеднительных печей и конвертер ставят под дутье на 2 – 3 мин. Эта операция называется «рафинированием» шлака. Проведение данной операции позволяет снизить содержание цветных металлов в конвертерном шлаке особенно за счет протекания обменных реакций:
MeO + FeМЕТ = Me +FeO
После «рафинирования» шлака производится его отстаивание в течение 3 –5 мин а затем шлак сливают в заранее приготовленные ковши. Температура сливаемого шлака должна быть в пределах 1200 – 1250 0С. С первой продувки сливают 3 – 4 ковша шлака. Чтобы вместе со шлаком в ковш не сливался штейн шлак нужно сливать широкой и тонкой струей. Качество шлака опробуется путем пересечения струи ломиком диаметром 24 мм. Проба бедного кремнистого шлака равномерно остывает на ломике и при охлаждении имеет черно-глянцевый вид. Если шлак богатый то на остывшей на ломике корке шлака заметны ярко-раскаленные звездочки штейна. Появление на ошлакованной поверхности ломика светлых пятен свидетельствует о появлении обогащенной массы в струе шлака. Слив шлака прекращают. Слитый конвертерный шлак направляют на обеднение в руднотермические электропечи.
После слива шлака из конвертера убыль ванны восполняется новой порцией штейна (2-3 ковша) и продолжается продувка. Во второй и следующих продувках загрузку кварцита производят через 10-15 мин после установки конвертера под дутье. Продолжительность продувок составляет 45-60 мин. Перед сливом шлака как и в первой продувке в конвертер заливают 1 ковш металлизированного штейна для рафинирования шлака.
Избыток тепла выделяющийся в процессе продувки штейна позволяет перерабатывать в конвертере значительное количество присадок (шлаковые корки холодный штейн богатая руда скрап файнштейна и т. д.). Вес холодных присадок может достигать до 30% от веса горячего штейна при этом температура расплава должна быть в пределах 1220-1240°С. Холодные присадки обычно загружаются в конвертер до подачи кварцевого флюса.
Постепенно в конвертере накапливается обогащенная масса. Набор штейна может продолжаться до тех пор пока конвертер не заполнится на 25-30% своего объема богатой массой с содержанием 25-27% железа и около 30% никеля 15-20 % меди. Однако на практике в зависимости от конкретной производственной обстановки и содержания металлов в штейне набор ограничивают переработкой 10-17 ковшей щтейна. Например при содержании в штейне Ni + Си равном 14% набор составляет 16 ковшей (~190 т) и продолжается 2 смены. За этот период в конвертер загружено 60 т кварцевого флюса и 40 т холодных присадок получено: 18 ковшей конвертерного шлака и 50 т обогащенной массы с содержанием 30% Ni 195% Сu 23% Fe 26% S 09% Со.
3.3. "Варка" файнштейна.
После прекращения набора штейна начинается период "варки" файнштейна. В задачу этого периода входит почти полное удаление сульфида железа из обогащенной конвертерной массы. Согласно техническим условиям на файнштейн содержание железа в нем должно быть не более 35%.
Во время "варки" проводят ряд "холостых" продувок (от 20 до 40 мин) при которых в ванну конвертера загружают только кварцевый флюс. Загрузка холодных оборотов запрещается (кроме скрапа файнштейна). "Варку" файнштейна можно выполнять без перелива обогащенной массы и с переливом. В первом случае набор массы и "варку" файнштейна выполняют в одном и том же конвертере. При работе с "переливом" холостые продувки проводят в 2-3 конвертерах в которых ранее осуществляли набор массы а затем обогащенную (до 10-15% по Fe) массу переливают в один "варочный" конвертер в котором доводят до файнштейна.
Работа с "переливом" позволяет значительно сократить продолжительность "варки" файнштейна и улучшает использование оборудования во времени.
Для сокращения дефицита серы и уменьшения образования свободных металлов в файнштейне конвертирование в период "варки" следует вести при температуре не превышающей 1150-1180°C. Полученный при такой температуре файнштейн содержит 23-24% S что обеспечивает минимальную металлизацию файнштейна и высокие показатели последующего флотационного разделения файнштейна на никелевый и медный концентраты.
Регулирование температуры процесса достигается выполнением "варки" короткими холостыми продувками (с получением 1-2 ковшей шлака) в сочетании с загрузкой в конвертер значительного избытка кварцевого флюса. Этот избыток должен вдвое превышать количество флюса требуемого для ошлакования закиси железа.
При продувке массы избыток кварцевого флюса отнимает тепло от расплава и таким образом является регулятором температуры. При этом способе понижения температуры шлаки получают холодными и вязкими. Содержание металлов в них велико «варочные» шлаки 2 первых холостых продувок необходимо направлять в электропечь шлаки последней холостой продувки (1-2 ковша) в обязательном порядке следует направлять в конвертер в котором производится набор штейна.
Обеднение шлаков достигается обработкой их бедной массой в этом конвертере в течение 7 – 10 мин. и последующего отстаивания не менее 3 – 5 мин.
Расход воздуха при «варке» файнштейна должен поддерживаться не менее 600 – 650 нм3 мин. давление дутья 08 – 10 атм.
В результате «варки» файнштейна содержание железа в богатой массе снижается до 25 – 35 % что соответствует техническим условиям на файнштейн. Готовность файнштейна определяется по цвету корочки богатой массы остающейся на фурмовке. По мере снижения железа в массе она из черной становится темно-синей затем на ней появляются желтые пятна.
Для окончательного определения готовности файнштейна из конвертера отбирается ложечная проба массы. Содержание железа в этой пробе анализируется спектральным методом при помощи стилоскопа или радиометрическим методом на приборе «Барс – 3».
3.4. Разливка и охлаждение файнштейна
Полученный медно-никелевый файнштейн перевозится в разливочный пролет цеха и разливается в стальные формы – изложницы зафутерованные плитами из графита. Емкость изложницы составляет 15 – 18 т расплава. В разливочном пролете располагается 100 изложниц.
Разлив файнштейна производится ошлакованными ковшами емкостью 7 м3. После разливки с поверхности файнштейна рабочие-разливщики деревянными скребками снимают шлаковые включения.
Для извлечения слитка файнштейна из формы в расплав вставляют 4 скобы (серьги) изготавливаемые из стального прутка диаметром 19 мм. Предварительно на поверхность расплава в месте установки серег устанавливают теплоизолирующий материал (насыпают 3 – 4 лопаты песка или устанавливают блок из асбестовых листов размеры 250х200х150 мм). Через 25 – 30 часа после охлаждения расплава до 800 0С теплоизолятор убирают и вставляют серьги.
Технические условия на файнштейн предусматривают чтобы его охлаждение в интервале 700 – 400 0С проводилось со скоростью не более 10 град час. При такой скорости охлаждения слитка создаются условия укрупнения кристаллов сульфидов меди и никеля. В результате файнштейн приобретает структуру необходимую для его последующего флотационного разделения на медный и никелевый концентраты.
На практике регулировку скорости охлаждения можно осуществлять толщиной слоя песка наносимого на поверхность отливки файнштейна. Время охлаждения слитка файнштейна зависит от его массы. Слиток массой 15 т должен охлаждаться не менее 34 часов.
Файнштейн извлекается из изложниц при температуре не более 400 0С. Охлажденные слитки файнштейна обдувают сжатым воздухом для очистки от пыли (песка) и взвешивают на платформенных весах (с точностью до 1 кг).
4. Расчёт основных статей материального баланса конвертирования
4.1. Вещественный состав штейна
По данным литературы принимаем что цветные металлы находятся в штейне в виде Ni3S2 Cu2S и СоS железо – в виде свободного металла (абсолютное содержание 4 %) FeS и Fe3O4.
Расчеты ведем по стехиометрическим соотношениям элементов в соединениях. Для расчета массы Ni3S2 сначала находим массу серы в Ni3S2:
а затем находим массу Ni3S2:
Для расчета массы Сu2S сначала находим массу серы в Cu2S:
а затем находим массу Сu2S:
Для расчета массы СоS сначала находим массу серы в CоS:
а затем находим массу СоS:
Для расчета массы FeS сначала нужно найти массу серы в FeS найдем ее как разность между массой общей серы и сумма соединений Ni3S2 Сu2S и СоS:
затем рассчитываем массу FeS:
Для расчета массы Fe3O4 сначала рассчитаем массу железа в Fe3O4:
а затем массу кислорода:
и тогда масса Fe3O4:
Полученные результаты записываем в таблицу 1.1.
Вещественный состав медно-никелевого штейна кг
4.2.металлов в каждом продукте
Распределение металлов по продуктам конвертирования в процентах принимаем поданным литературы и рассчитываем массу металлов в каждом продукте.
Рассчитаем массу Ni в каждом продукте:
Рассчитаем массу Сu в каждом продукте:
Рассчитаем массу Сo в каждом продукте:
Рассчитаем массу Fe в каждом продукте:
Результаты расчетов сводим в таблицу 1.2.
Распределение металлов штейна между продуктами конвертирования
4.3.и состав файнштейна
По данным литературы примем что суммарное содержание в файнштейне никеля меди кобальта и железа равным 803 % т.е. Ni = 42 % Cu = 35 % Co = 08 % и Fe = 25 %. Далее определим выход файнштейна:
Для расчета вещественного состава файнштейна и содержания в нем серы примем что часть никеля кобальта железа и меди находятся в виде сплава металлов и в виде сульфидов (Ni3S2 СоS FeS и Cu2S):
затем рассчитаем массу серы в Ni3S2:
Далее найдем массу Ni3S2:
Определим содержание Ni в файнштейне %:
По аналогии рассчитаем для меди кобальта и железа.
Масса металлической меди: .
Содержание Cu в файнштейне %:
Масса металлического кобальта:
Масса кобальта в СoS:
Содержание Cо в файнштейне %:
Масса металлического железа:
Масса железа в FeS: .
Содержание Fe в файнштейне %: .
Полученные результаты массы и вещественного состава файнштейна заносим в таблицу 1.3.
Масса и состав файнштейна кг.
По данным литературы примем что суммарное содержание никеля меди кобальта железа в пыли равным 454 % тогда выход пыли получим:
Для расчета вещественного состава пыли принимаем что данные металлы находятся в виде сульфидов Ni3S2 Cu2S СoS и FeS (50 %) оксидов NiO Cu2O CoO и FeO (30 %).
Найдем массу Ni в Ni3S2:
затем найдем массу серы в Ni3S2:
Потом найдем содержание Ni3S2 в пыли:
Определим массу Ni в NiO:
далее найдем массу кислорода в NiO:
Потом определим содержание NiO в пыли:
Содержание никеля в пыли:
Аналогично определяем массу пыли и ее вещественный состав для сульфидов Cu2S СoS FeS и оксидов Cu2O CoO FeO.
Для сульфидов Cu2S СoS и FeS:
- масса кобальта в CoS
Для оксидов Cu2O CoO и FeO:
- масса кобальта в CoO
- масса кислорода в Сu2O
- масса кислорода в СoO
- масса кислорода в
- содержание меди в пыли
- содержание кобальта в пыли
- содержание железа в пыли
- содержание серы в пыли
- содержание кислорода в пыли
- содержание прочих соединений в пыли Результаты расчета массы и вещественного состава пыли сводим в таблицу 1.4.
Масса пыли и ее вещественный состав
4.6.кварцевого флюса масса и состав конверторного шлака
Для расчета массы кварцевого флюса будем учитывать флюсующую способность. Определим массу кремнезема необходимого для ошлакования 478016 кг железа содержащегося в конверторном шлаке и 51 кг железа содержащегося в кварцевом флюсе.
кг Fe требуют 205 кг SiO2
кг Fe требуют SiO2 .
Определим шлакующую способность кварцевого флюса . Найдем массу кварцевого флюса . Определим количество кварцевого флюса которое поступит в конвертер:
Примем по данным литературы что никель в конверторном шлаке находится на 50% в виде Ni3S2 и на 50% в виде NiO медь на 80% в виде Cu2S и на 20% Cu2O кобальт на 30% в виде CoS и 70% в виде CoO. Железо на 15% в виде FeS на 30% в виде Fe3O4 и на 55% в виде FeO от его массы в конверторном шлаке. Содержание прочих в шлаке найдем из баланса их прихода и расхода:
- масса никеля в Ni3S2
- масса меди в Cu2S
- масса кобальта в CoS
- масса серы в Ni3S2
- масса серы в Cu2S
- масса в конверторном шлаке
- масса в конверторном шлаке
- масса в конверторном шлаке;
- масса никеля в NiO
- масса меди в Cu2O
- масса кобальта в CoO
- масса кислорода в NiO
- масса NiO в конверторном шлаке
- масса Cu2O в конверторном шлаке
- масса CoO в конверторном шлаке
- масса FeO в конверторном шлаке
- масса Fe3O4 в конверторном шлаке.
Результаты расчетов сводим в таблицу 1.5.
Масса конвертерного шлака и его вещественный состав
4.7. Количество воздуха и отходящих газов
Масса серы переходящей в газовую фазу:
Примем что в газовой фазе сера полностью находится в виде SO2.кислорода потребного для связывания серы в SO2:
- объем SO2 (объем рассчитан при нормальных условиях).
Теоретически масса и объем кислорода для переработки 100 кг штейна соответственно:
Примем коэффициент использования кислорода дутья ванной конвертера равным 95% тогда практический объем и масса кислорода:
Масса воздуха подаваемого в конвертер 2941191 : 023 = 1278778 кг. Воздух содержит 1278778 – 2941191 = 984659 кг или (984659*224) : 280 = 787727 м3 азота.и объем избыточного кислорода в газах 2941191 – 2794132 = 14705 кг и 2058834 – 1955892 = 10294 м3 .
Данные расчета количества и состава отходящих газов сводим в таблицу 1.6.
Содержание отходящих газов и их состав
Массовое содержание %
Объемное содержание %
4.8. Материальный баланс процесса конвертирования
Для проверки правильности выполненных расчетов сводим их в таблицу материального баланса (таблица 1.7.).
Материальный баланс конвертирования медно-никелевого штейна кг
5. Расчёт основных статей теплового баланса КОНВЕРТИРОВАНИЯ
Базой для расчета теплового баланса является закон сохранения энергии термохимические и теплофизические константы индивидуальных веществ ионов и химических реакций.
Тепловой баланс составляют для анализа и определения структуры поступления и расхода тепла; расхода энергоносителя (топливо пар электроэнергия) при дефиците тепла или количества хладоагента – при избытке тепла.
Тепловой баланс составляют с учетом данных материального баланса на переработку единицы сырья за операцию за единицу времени. Он включает статьи прихода тепла (физическое тепло поступающих материалов тепло с энергоносителем тепло экзотермических реакций) и статьи расхода тепла (физическое тепло продуктов процесса тепло эндотермических процессов потери тепла в окружающую среду через стенки аппарата открытые отверстия).
Для расчета теплового баланса составим вспомогательную таблицу 1.8. значения которой берем из предыдущих таблиц.
Вспомогательная таблица конвертирования медно-никелевого штейна
Процесс конвертирования медно-никелевых штейнов представим следующими основными реакциями:
5.1. Статьи прихода тепла
Тепло вносимое горячим (жидким) штейном где tш = 1200 0С; Сш = 02 ккалкг0С = кДж(кг0С).
Тепло воздуха где tв = 40 0С; Сш = 031 ккалкг0С = кДж(кг0С).
Тепло кварцевого флюса где tф = 30 0С; Сф = 031 ккалкг0С = кДж(кг0С).
Тепло экзотермических реакций представим результаты в таблице 1.9.
5.2. Статьи расхода тепла
Тепло файнштейна где tф = 1250 0С; Сф = 02 ккалкг0С = 084кДж(кг0С).
Тепло шлака где tшл = 1200 0С; Сф = 03 ккалкг0С = 126кДж(кг0С).
Тепло газов tг = 1000 0С; СSO2 = 0536 ккалкг0С = 225 кДж(кг0С); СO2 = 0353 ккалкг0С = 148кДж(кг0С); СN2 = 0334 ккалкг0С =14 кДж(кг0С)
Тепло эндотермических реакций представим результаты в таблице 1.10.
Потери тепла во внешнюю среду. Рассчитаем балансовое время переработки 100 кг штейна при суточной производительности 450 тсутки:
= 24450*01 = 00053 часа; балансовое время определяется из отношения количества воздуха подаваемого в конвертер: = 0005312787*2941191 = 00012 часа.
а) Потеря тепла поверхностью кожуха конвертера. Поверхность кожуха конвертера вычисляется как поверхность цилиндра диаметром 39 м и длиной 10 м за вычетом площади горловины 6 м2 с учетом ребристости кожуха. креб = 13 – 15 примем креб = 13 получим подставляя данные получим Fcт = 182442 м2.
При температуре наружной поверхности кожуха 200 0С qуд = 3500 ккалм2 час
Qcт = qуд Fcт = 3500*182442*00012*4192 = 3212 кДж
б) Потеря тепла излучением через открытую горловину. Приняв коэффициент дефрагмирования Ф = 06 при температуре внутренней полости конвертера 1300 0С по графику определяем qуд = 170000 ккалм2 час;
Qизл = qуд Fгорл = 170000*6*00012*4192 = 5131 кДж; Всего потери тепла во внешнюю среду:
Qвн = Qcт + Qизл = 3212 + 5131 = 8343 кДж.
После проделанных расчетов теплового баланса результаты занесем в таблицу 1.11.
Тепловой баланс конвертирования медно-никелевого штейна
6. Расчет газоходной системы
Состав системы газоочистки принимаем в соответствии с рис. 1.1 Эта схема обеспечивает требуемую степень утилизации отходящих газов и достаточно полное улавливание пыли.
Рис.1.1. Схема системы газоочистки.
Температура газов 1250 °С удельный вес 1.475 кгм3 температура газов на выходе котла утилизатора составляет по условию его работы 550°С.
Подсос при выходе газов возьмем за 100 % по остальным участкам величина подсоса составляет 5 %.
Количество газов образующихся в печи:
а) печь - котел: 4.825 . 2 = 9.65 м3сек;
б) котел - пылевая камера: 4.825 . 2 .05 = 9.89 м3сек;
в) пылевая камера - дымосос: 4.825 . 2 .1 = 10.13 м3сек;
г) дымосос - электрофильтр: 4.825 . 2 .15 = 10.37 м3сек.
Температуру газов при выходе из печи возьмем 1000°С. Температура газов на входе в котел при падении температуры 5°С на 1 погонный метр газохода 1000°С - 5°С . 6 = 970°С.
Температура газов на выходе из котла 550°С с учетом подсоса - 5501.05 = 524°С.
Температура газов на входе в пылевую камеру 524°С - 2 . 5°С = 514°С. Температура газов на выходе из пылевой камеры 350°С с учетом подсоса - 350°С 1.05 = 333°С.
Температура газов перед дымососом 333°С - 2°С . 24 = 285°С. Температура газов после дымососа 250°С с учетом подсоса 250°С 1.05 = 238°С.
Температура газов перед электрофильтром 238°С - 2°С . 12 = 214°С.
6.1. Участок печь - котел
Средняя температура газов (1000°С + 970°С)2 = 985°С объем газов
При скорости газа 6 мсек сечение газохода равно 40746 = 679 м2.
При газоходе прямоугольного сечения и отношении высоты к ширине газохода 0.8 определим его размеры:
ab = 0.8; 0.8 . b2 = 679 a = 291 м b = 233 м.
Допустим что котел работает на нагретой до 100°С воде с получением пара 40 ат. Количество тепла отдаваемое газами котлу при учете потерь тепла во внешнюю среду 5% равно:
Q = 0.95 . cг . Vгρг . (tг вх - tг вых)
Q = 0.95 . 1450 (Джкг.°С) . 1423 (кг). (970°С - 550°С) = 8235 МДжсек
Поверхность котла: F = QK
где K - коэффициент теплопередачи принятый равным 168 (кДжм2.час) (с учетом обдува рабочих поверхностей).
Тогда поверхность котла равна F = 49 м2.
При получении насыщенного пара 40 ат паропроизводительность котла D может быть определена из соотношения:
D = Q(iпара - iводы) = 933 кгчас
где iпара - теплосодержание получаемого пара 686 ккалкг:
iводы - теплосодержание питающей воды 100 ккалкг.
6.2. Участок котел - пылевая камера
Средняя температура газов (524 + 514)2 = 519°С объем газов 989 . (519 + 273)273 = 287 м3сек сечение газохода 2876 = 478 м2 диаметр газохода d = 247 м средняя температура газов в пылевой камере (514 + 350)2 = 432°С объем газов проходящих через пылевую камеру 989 . (432 + 273)273 = 2554 м3сек
6.3. Участок пылевая камера - дымосос
Средняя температура газов (333+285)2=309°С объем газов 1013×(309+273)273= 216 м3сек сечение газохода 2166 = 36 м2 диаметр газохода d = 215 м. Количество газов перед дымососом 1013×(558273) = 207 м3сек
6.4 Участок дымосос - электрофильтр
Средняя температура газов (238+214)2=226°С объем газов 1037×(226+273)273 = 1895 м3сек сечение газохода 18956 = 316 м2 диаметр газохода d = 2 м. Количество газов в электрофильтре 1037×(285+273)273 = 212 м3сек.
Для выбора дымососа необходимо определить сопротивление (сумму потерь напора) газоходной системы.
6.5. Участок печь - котел
) Поворот газа на 90° при выходе из печи по формуле
hпот = x×wt22g× gt кгм2
x = 0.5 (плавный поворот на 90°)
gt = 1.32× 273(273+985) = 0.286 кгм3
h1пот=0.5×622×9.81× 0.286 = 0.24 кгм2
) Внезапное сужение по формуле
при значении x = 0.5
h2пот = 0.5×622×9.81× 0.286 = 0.24 кгм2
) Потери напора на трение по формуле
hпот = m× ld× wt22g× gt кгм2
d = 4× F1p где р - периметр газохода;
d = 4× 6791048 = 259 м
h3пот = 0.05× 62.59× 622×9.81× 0.286 = 0.06 кгм2
) Потери в нишах шиберов до и после котла (имеется обводный газаход) по формуле
При значении x = 0.3
h4пот =2× 0.3× 622×9.81× 0.286 = 0.314 кгм2
) Потери напора в котле принимаем 40 кгм2 h5пот = 8 кгм2
6.6. Участок котел - пылевая камера
) Потери напора на трение по формуле при значениях m = 0.05; d = 247м
h6пот = 0.05× 52.47× 622×9.81× 0.455 = 0.084 кгм2
) Потери напора в пылевой камере считаем равными h7пот = 10 кгм2
6.7. Участок пылевая камера - дымосос
h8пот = 0.05× 242.15× 622×9.81× 0.62 = 0.635 кгм2
где l = 24м d = 2.15 м
) Два поворота (плавных) на 90° при x = 0.5×2=1
h9пот = 1×622×9.81×0.62 = 114 кгм2
6.8. Участок дымосос - электрофильтр
) Потери в электрофильтре принимаем равными 5 кгм2
) Потери на трение по формуле
h11пот = 0.05× 122× 622×9.81× 0.73 = 0.399 кгм2
) Два поворота (плавных) на 90° при x = 0.5×2 = 1
h12пот = 1×622×9.81× 0.73 = 1.33 кгм2
Суммарные потери напора:
h пот = hi пот = 2744 кгм2
1. Назначение конвертера.
Конвертеры – агрегаты в которых перерабатывается медно-никелевый штейн поступающий из рудно-термических электропечей.
Основной технологической задачей процесса конвертирования штейнов является продувка жидкого штейна воздушным дутьем и получения файнштейна заданного качества. При продувке железо и другие компоненты окисляются и переходят из штейна в шлак сера окисляясь переходят в газовую фазу. В файнштейне с возможной полнотой должны быть извлечены никель медь кобальт благородные (платина рутений родий иридий осмий) металлы.
2. Анализ управляемости горизонтального конвертера
Процесс конвертирования является циклическим и состоит из двух технологических периодов. Два основных процесса — теплогенерации и технологический — пространственно совпадают и объединяются в ванне конвертера. Это приводит к взаимному влиянию процессов и необходимости рассмотрения взаимосвязанных величин объекта регулирования.
На процесс плавки в конвертере действует большое число неконтролируемых возмущений (по составу загружаемых потоков по их расходу по расходу дутья и др.). Управляющие воздействия являются как дискретными (различные добавки) так и непрерывными (расход кислорода).
Из условий управляемости каждому компоненту вектора выхода должны соответствовать две компоненты входных векторов: одно управление (ui) и одно возмущение (zi) то есть выходные величины (xвых) есть функция от входных величин xвых = F[ui zi].
Таким образом управляемость объекта – это его способность откликаться на воздействия которые мы считаем управляющим нужным образом.
Практически все металлургические агрегаты представляют собой сложные нестационарные объекты регулирования которые описываются уравнениями высоких порядков имеют нелинейные зависимости между входными и выходными величинами. Сложные объекты управления к которым относятся практически все металлургические агрегаты можно подразделить на ряд элементарных звеньев.
Последовательное и параллельное соединение элементарных звеньев позволяет при рассмотрении таких объектов использовать положения теории автоматического управления.
Нелинейность металлургических объектов обуславливается тремя причинами: нелинейность характеристик регулирующих органов нелинейным характером физико-химических процессов происходящих в агрегате и нелинейностью характеристик измерительной аппаратуры.
Общей задачей управления конвертерным процессом является достижение оптимума конкретный выбор которого определяется условиями работы конвертерного цеха например максимальная производительность конвертера. Независимо от выбранного критерия оптимальности должно выполняться основное технологическое требование — получение файнштейна заданного состава.
Информация о возмущениях позволяет создавать системы инвариантные к этим возмущениям.
Создание систем управления процессом конвертирования осложняют следующие факторы:
Конвертер относится к агрегатам периодического действия. Величины характеризующие периодические процессы претерпевают как правило значительно большие колебания по сравнению с непрерывными процессами а управляющие воздействия могут варьироваться по абсолютной величине. При этом в большей степени проявляются нелинейные зависимости. Все это значительно усложняет управление такими процессами.
В течение продувки ванны происходит значительное изменение основных параметров объекта управления. Поэтому необходим учет таких изменений для обеспечения требуемого качества управления.
Ограниченная емкость при относительно больших колебаниях прихода материалов и энергии частые остановки конвертеров на ремонт фурменного пояса транспортировка материалов и продуктов в ковшах при помощи мостовых кранов не позволяющая полностью механизировать и автоматизировать процессы загрузки исходных материалов и передачу продуктов конвертирования. До настоящего времени повсеместно еще не решена проблема механизации прочистки фурм при погруженном подводе дутья в ванну.
Недостаточная изученность протекания основных химических реакций в печи из-за сложностей экспериментального исследования процессов при высокой температуре и агрессивности расплава.
Отсутствие простых в эксплуатации и надежных в работе датчиков для измерения температуры расплава отсутствие простых способов оперативного контроля содержания компонентов в расплаве.
Отсутствуют удобные методы плавного регулирования температуры конвертеров и нет точных методов ее измерения.
Широкое использование визуальных методов контроля основных технологических параметров процессов плохо формализуемых и не поддающихся автоматизации.
В целом процесс конвертирования в современном его аппаратурном оформлении недостаточно пригоден даже для частичного стабилизирующего автоматического регулирования отдельных параметров не говоря уже о комплексной его автоматизации.
3. Основные цели управления технологическим процессом и назначение АСУТП
Общей задачей управления конвертерным процессом является достижение критерия оптимальности конкретный выбор которого определяется условиями работы конвертерного цеха например максимальная производительность конвертера. Выполнение этого требование можно достичь внедрением следующим контуров автоматизации и контроля:
Автоматический контроль параметров:
-давление воздуха перед фурмами;
-температура расплава;
-содержание SO2 в газах после электрофильтров;
-температура отходящих газов;
-разрежение в пылевой камере.
Стабилизация температуры изменением задания на расход воздуха.
Автоматическая стабилизация расхода воздуха подаваемого в печь.
Автоматическая стабилизация температуры в пылевой камере.
Автоматическая стабилизация температуры воды в напыльнике.
АСУ ТП предназначена для выполнения следующих функций:
Сбор данных по средствам измерения опроса датчиков;
Контроль технологических параметров названных выше;
Автоматическое управление исполнительными механизмами;
Измерительные преобразования;
Контроль и сигнализация состояния оборудования и отклонения параметров;
Стабилизирующее регулирование;
Дистанционное управление приводами технологического оборудования;
Регистрация параметров.
4. Описание функций АСУТП
Система автоматизации процесса конвертирования представляет собой комплекс технических средств отображение информации о ходе процесса.
Она реализована по иерархическому принципу где на каждом уровне системы обеспечивается сбор и хранение информации.
Рис 2.1. Иерархия современной распределённой системы автоматизации.
— контроль расходов воздуха флюса; температур кладки фурменного пояса и отходящих газов в газоходе; уровня в бункере; содержания SO2 в отходящих газах; масс загружаемого штейна и выгружаемых шлака и файнштейна; содержании металлов в файнштейне и шлаке и SO2 в шлаке; давление дутья и разряжение в пылевой камере;
— обработка аналоговых и дискретных входных сигналов;
— реализация контуров регулирования расходов дутья флюса положения напыльника и конвертера уровня в бункерах флюса;
— система защиты фурм от заливки расплавом при падении давления на воздухопроводе методом аварийного поворота конвертера.
— система предотвращения разбавления газов воздухом при прекращении дутья изменением положения заслонки на газоходе.
— система управления положением напыльника при сливе продуктов плавки и загрузке исходных материалов.
— включение и отключение подачи флюса и холодных оборотов в бункеры и из бункеров на конвейер.
— стабилизация расхода дутья (воздуха).
— сигнализация о падении давления на подаче дутья;
— запись истории за длительный период;
— составление сменных отчетов;
— вычисление балансов;
— сигнализация о падении давления дутья и о падении напряжения в питающей сети.
Из состава задач АСУТП на верхнем уровне управления реализуются следующие задачи:
— обслуживание функций обмена информацией с микропроцессорными устройствами нижнего уровня и обновление информации в глобальной базе данных.
— проверка соблюдения технологических границ для основных технологических параметров.
— обслуживание диалога оператора-технолога с ППК и протокола работы АСУТП.
автоматический рестарт задач АСУТП.
Представление информации:
Расчет показателей эффективности работы основного оборудования;
Формирование отчетных документов и рапортов о работе печи;
Информация о работе систем автоматического контроля и регулирования;
Выявление сбоев в работе аппаратуры контроля и регулирования;
Формирование сообщений об отказе аппаратуры;
проверка достоверности информации;
Представление данных о надежности АСУТП и контролируемого агрегата;
a. Промышленная сеть
Уровень полевой автоматики в данном проекте представлен набором датчиков установленных по месту. Связь между датчиками исполнительными механизмами и ПЛК осуществляется с помощью AS – интерфейса.
AS – интерфейс (ActuatorSensor Interface) был представлен в виде концепции в1993 году.
Поддерживается консорциумом ведущих производителей средств АСУ ТП в числе которых фирмы Siemens Pepperl+Funchs и другие. Относится к классу ПС оконечных устройств осуществляя непосредственную интеграцию датчиков и исполнительных механизмов в систему автоматизации. Позволяет полностью исключить из АСУ ТП аналоговые линии связи кроссировочные шкафы и другое вспомогательное оборудование.
Оболочка кабеля AS – интерфейса имеет специальный профиль исключающий возможность неправильного подключения сетевых компонентов. Большая часть сетевых компонентов подключается к кабелю методом прокалывания изоляции и сделать это можно практически в любой точке соединительного кабеля что обеспечивает гибкость сетевой архитектуры и сокращает сроки монтажа.
Локальная вычислительная система низкого уровня на базе AS – интерфейса может иметь только одно ведущее устройство (master). До недавнего времени к нему можно было подключить 31 ведомое устройство (slave). По новой спецификации версии 2.1 стандарта на AS – интерфейс появившейся весной 2000 года количество ведомых устройств в одной сети увеличено до 62 за счёт разделения адресного пространства ведущего сетевого устройства на две подобласти: А и В.
AS – интерфейс использует метод доступа к ведомым устройствам основанный на их циклическом опросе (polling). В AS – интерфейсе версии 2.1 используется только ведомые устройства подобласти адресного пространства А или В то время цикла опроса также не превышает 5 мс. В случае использования всего адресного пространства доступного для данной версии ведомые устройства подобластей А и В обслуживаются по очереди: в первом цикле производится опрос ведомых устройств подобласти А во втором – подобласти В и в такой последовательности циклический процесс опроса повторяется далее. Таким образом в этом случае суммарное время обслуживания всех ведомых устройств не превышает 10 мс то есть сравнимо с циклом отработки программы в контроллере. Благодаря этому сети на базе AS – интерфейса активно применяются в распределенных АСУ ТП реального времени например в системах управления конвейерными производствами.
Первоначально AS – интерфейс был ориентирован на работу исключительно с бинарными данными поэтому длину информационной посылки рекордно малая – всего 4 бита! Тем не менее новая редакция спецификации AS – интерфейса позволяет подключать к сети аналоговые датчики и поворотные шифраторы. Максимальное количество узлов равно 62 максимальная длина с использование повторителей – 300 м. Данные и питающее напряжение передаются по одной паре проводов. Сети на базе AS – интерфейса отличаются экономичностью и очень большим выбором средств комплексирования с другими ПС.
Аппаратные и программные средства
Современные общепромышленные ИПД (измерительный преобразователь давления) – это интеллектуальные со встроенным микропроцессором интегральные преобразователи с цифровым интерфейсом. Они обладают свойствами диагностики конфигурирования на расстоянии обеспечение более высокое соотношение измеряемых диапазонов улучшенную температурную компенсацию повышенную основную точность. Однако это не значит что другие ИПД уже не нужны: каждый тип ИПД имеет свою эффективную пользовательскую нишу. На комбинате «Печенганикель» в основном используется преобразователи фирмы «Метран» - «Сапфир - 22».
В связи с тем у этих датчиков имеется два существенных недостатка: низкими интеллектуальными и интерфейсными возможностями. В этих условиях экономически оправданным может оказаться приобретение ИПД ведущих мировых производителей или их отечественных аналогов (например: «Метран_1151» является аналогом интеллектуального датчика «Alphaline 1151» фирмы Fisher_Rosemount).
В нашем случае я остановился на высоконадежных и высокоточных интеллектуальных ИПД SITRANS P (серии MKII DS HK) фирмы Siemens предназначенные для измерения уровня избыточного дифференциального и абсолютного давления жидкости и газа от 4 кПа до 25 МПа (рис. 5.4). Для различных задач можно воспользоваться различными преобразователями с разнообразными соединениями и насадками.
Возможно использование местных индикаторов. Устройства SITRANS P существуют в стандартном исполнении (выход 4 - 20 мА) с использованием AS - интерфейса и с подключением Profibus - PA и Fieldbus. Обеспечивается возможность бесступенчатой перестройки диапазона измерения по месту. Датчики зарегистрированы в Государственном реестре средств измерений и допущены к применению в Российской Федерации. Имеется свидетельство взрывозащищенности электрооборудования.
Отличаются малым весом и габаритами. Датчик состоит из тонкоплёночной измерительной ячейки с керамической мембраной и электронной схемы которые встроены в корпус из нержавеющей стали (IP65). В эксплуатации преобразователи не требуют технического обслуживания кроме периодической проверки нуля диапазона. В проекте используется 2 прибора SITRANS P один установлен на фурмоколлекторе другой в пылевой камере.
Датчики температуры:
Для снятия высоких температур в металлургии и в других областях промышленности применят термопары. На данное время термопары являются самым дешевым и качественным устройством для снятия температур.
В основу термопары заложено явление термоэлектричества открытое немецким физиком Т. Зеебеком и состоит в следующем.
Если соединить два проводника (термоэлектрода) из разнообразных металлов или сплавов таким образом чтобы они образовали замкнутую электрическую цепь (рис 5.5) и затем поддерживать места контактов (спаи) при различной температуре то в цепи будет протекать постоянный ток.
Ниже приведена таблица сравнения основных термопар.
Таблица 2.1 Основные типы термопар и их параметры в соответствии с международной спецификацией
Материал термозлектродов
°С или 075% выше 0°С 22 °С или 2% ниже
°С или 075% выше 0°С 1 °С или 15% ниже
°С или 05% выше 0°С 17 °С или 1% ниже
Помимо выбора самой термопары то есть сплава металлов и т.д. надо подобрать ещё и её конструктивное исполнение. В таблице представлены конструктивные исполнения термопар мой выбор остановился на изолированной в керамической оболочке термопаре. Основными достоинствами являются: гибкая конструкция стойкость к стиранию работа при высоких температурах (до 1300°С) не большая постоянная времени.
Таблица 2.2 Основные варианты конструктивного исполнения термопар.
Конструкция термопары
Неизолировная тонкопроволочная с открытым контактом
с открытым контактом
Изолирован. в керамич.
В металлическом корпусе с встроен. клеммами для установки в гильзу
Допустимая раб.температ
Основные достоинства
Малые размеры малая постоянная
времени возможность точечного измерения не отводит тепло
от измеряемого объекта
Ограниченная длина проводников для
удобная самоклеящаяся
стойкость к истиранию
Высокая коррозионная
стойкость в промышленных
условиях возможность
Биофизикамедицинакриогенная техника измерение быстро изменяющихся температур.
Не подходит для использования в жидкостях
и агрессивных средах.
Измерение температур
Изоляционая оболочка
из тефлона или стекла
обеспечивает химическую и термическую
Измерение температуры
поверхностей легко снимается и устанавливается
Печи термошкаф станкостроение
промышленных условиях
с гильзами различных
Помимо точного измерения термоЭДС нашей термопары надо преобразовать эту термоЭДС в температуру. К сожалению у большинства термопар зависимость термоЭДС от температуры в некоторых диапазонах имеет нелинейный характер.
Основная причина этого — зависимость коэффициента Зеебека от температуры примерный вид которой показан на рис. 5.6. Для достижения высокой точности измерений во всём диапазоне рабочих температур необходима его калибровка.
Простейший (и кстати наиболее точный) метод калибровки заключается в составлении и размещении в памяти ЭВМ таблицы соответствия значений термоЭДС и температуры измеренной с помощью образцового термометра.
Поскольку выходной сигнал термопары очень мал необходимо принимать специальные меры для снижения уровня шумов (и соответственно погрешности измерения).
Необходимо стремиться к максимальному сокращению длины соединительных проводников между термопарой и цифровым измерительным устройством. В случае большого удаления термопары от контроллера следует использовать располагаемые в непосредственной близости от термопар специальные модули нормализации сигналов превращающие термоЭДС в токовый сигнал (например 4-20 мА) или непосредственно в цифровой отсчет (рис. 2.3.)
Кроме того эти модули как правило обеспечивают гальваническую развязку сигналов и содержат устройства компенсации холодного спая. Дополнительные затраты сторицей окупаются надежностью точностью и стабильностью работы системы.
В своём проекте при измерении температуры в конверторе используется термопара ТХА в керамической оболочке а для снятия температуры отходящих газов использую Т (в соответствии с о стандартом ANSI) – изолированную с открытым контактом. Между термопарой и контроллером расположено по одному УСО ADAM фирмы Advantech с поддержкой AS – интерфейса.
Метран – 360 – расходомер предназначен для измерения массового и вычисления объемного расхода жидких и газообразных сред; используется в системах автоматического контроля и управления технологическими процессами в различных отраслях промышленности.
Расходомер Метран – 360 имеет модульную конструкцию (рис 2.4.) состоящую из:
- датчик расхода (сенсора);
- измерительного микропроцессорного преобразователя моделей 1700 или 2700;
- основного процессора;
- фланцев для присоединения к магистралям.
Основными элементами датчика расхода являются две расходомерные трубки на которых монтируются:
- соединительная коробка с силовой
электромагнитной (задающей) катушкой возбуждения и магнитом;
- два тензодатчика с магнитами и электромагнитными катушками;
Элементы датчика закрыты защитным кожухом на котором нанесен указатель направления потока.
Масса датчика расхода не превышает 25 кг.
Внутри расходомерных трубок специальной формы движется измеряемая среда.
Под воздействием задающей катушки расходомерная трубка колеблется с резонансной частотой.
В результате эффекта Кориолиса возникающем при движении среды (рис 5.9)
в колеблющейся трубке различные ее части изгибаются друг относительно друга.
Рис 2.5. Конструкция сенсора расхода и эффекта Кориолиса.
Этот изгиб приводит к взаимному рассогласованию по фазе колебаний различных участков расходомерной трубки которое преобразуется электромагнитными детекторами скорости в выходной сигнал датчика расхода.
Резонансная частота трубки зависит от ее геометрии материала конструкции и массы.состоит из двух частей: масса самой трубки и масса измеряемой среды в трубке.трубки (трубок) постоянна для данного датчика. Поскольку масса среды в трубке равна произведению плотности среды и внутреннего объёма трубки а объем трубки является константой для данного датчика то резонансная частота колебаний трубки может быть привязана к плотности среды и определена путем измерения резонансной частоты колебаний периода колебаний трубки и температуры (изменение модуля упругости материала трубки при изменении температуры температурный сенсор).
Плотность среды вычисляется на основании линейной зависимости между частотой и периодом колебаний трубки с использованием калибровочных констант.
- текущие значения массового объемного расхода суммарной массы объема плотности. Появление значений переменных процесса может осуществляться автоматически или ручным нажатием оптического переключателя («кнопки») на панели ЖКИ;
- размерность технических единиц в которых измеряется массовый (объемный) расход суммарная масса (объем) и плотность.
Управление ЖКИ осуществляется посредством оптических переключателей которые работают через стекло и имеют красные светодиоды обратной связи указывающие на нажатие «кнопки».
ЖКИ имеет возможность поворота нВ преобразователе на 360°С с шагом 90°.
С помощью трехцветного светодиодного индикатора на панели ЖКИ можно оценить состояние расходомера. Это состояние определяется непрерывно светящимся или мигающим зеленым желтым или красным цветом индикатора. Световой индикатор позволяет определить степень серьезности возникшей неполадки.
Основной процессор служит для преобразования служебных сигналов поступающих сенсора в стандартный цифровой протокол RS – 485.
Данный уровень реализован на Foundation Fieldbus – пожалуй наиболее «продвинутый» стандарт промышленный сетей (ПС) появившейся на свет только в 1995 году как результат усилий консорциума крупных в основном североамериканских производителей. По многим параметрам эта система схожа с PROFIBUS-PA: возможность установки во взрывоопасных зонах передача информационного сигнала вместе с питающим напряжением по одной паре проводов двухуровневая иерархия и т.д. В Foundation Fieldbus на верхнем уровне используется высокоскоростная магистраль Ethernet а на нижнем – технология передачи по стандарту IEC 61158.2 как и в PROFIBUS – PA.
Две особенности выделяют Foundation Fieldbus среди других ПС. Во –первых был разработан специальный язык описания оконченных устройств (Device Description Language) использование которого позволяет подключать новые узлы к сети по широко применяемой в обычных IBM PC компьютерах технологии plug-and-play. Достаточно физически подключить новое устройство и оно тут же самоопределится на основании заложенного описания DD (Device Description) после чего все функциональные возможности нового узла становится доступными в сети. При конфигурировании инженеру достаточно соединить входы и выходы имеющихся в его распоряжении функциональных блоков чтобы реализовать требуемый алгоритм.
Пользователям доступны как типовые DD для стандартных устройств (клапанов датчиков температуры и т.д.) так и возможность описания нестандартных изделий.
Таблица 2.3. Сводная таблица характеристик промышленных сетей.
Во-вторых в отличие от других промышленных сетей Foundation Fieldbus ориентирована на обеспечение одноранговой связи между узлами без центрального ведущего устройства. Этот подход даёт возможность реализовать системы управления распределенные не только физически но и логически что во многих случаях позволяет повысить надежность и живучесть АСУ ТП. В Foundation Fieldbus реализованы самые сложные технологии обмена информацией: подписка на данные режим «клиент-сервер» синхронизация распределённого процесса и т.д.
Режим «Подписка». В этом режиме узел нуждающийся в регулярном поступлении какой-либо информации подписывается на её получение от другого узла после чего получает регулярные рассылки данных без дополнительных запросов. Режим имеет два варианта: в первом случае данные передаются циклически с определённым интервалом вне зависимости от динамики информации; во втором случае данные передаются только в случае их изменения.
Режим «Клиент-сервер». Данный режим имеет иного общего с режимом «Ведущий-ведомый» и используется в системах с гибким распределением функций. Узел-клиент запрашивает данные а узел-сервер их предоставляет. При этом клиент может запрашивать несколько узлов а сервер – иметь несколько клиентов. Также функции клиента и сервера могут совмещаться на одном узле.
Контроль и автоматическое регулирование процессом осуществляется на базе микроконтроллерной технике. В данном проекте используется контроллер Series 90-30.
Series 90-30 был выбран из следующих его качеств:
Series 90-30 (рис 2.6.) строится на блочно-модульном принципу: процессор шасси модуль питания модули аналогового и дискретного ввода вывода и специализированные модули.
Разнообразие высокая производительность и совместимость платформы автоматизации Series 90-30 фирмы General Electric позволяет создавать нужные системы управления. Его архитектура является модульной и масштабной поэтому она конфигурируется в соответствии с наиболее жесткими требованиями к производительности систем управления среднего и крупного масштаба.
Системы Series 90-30 очень компактны и имеют надежную промышленную конструкцию обеспечивающую экономичность и безотказность при установке в наиболее жестких производственных условиях. Эти системы просты в монтаже и эксплуатации они пригодны для решения широкого круга задач.
ПЛК (программно логический контроллер) Series 90-30 обеспечивает полный набор модулей ввода–вывода предназначенных для взаимодействия с широким кругом полевых устройств. Все модули соответствуют международному стандарту IEC что обеспечивает надежность в жестких условиях эксплуатации. Дополнительное усиление защиты и увеличения срока службы достигается за счет специального покрытия модулей.
Возможность программной установки адресов ввода-вывода для каждого модуля облегчает добавление или замену модулей в конфигурации системы практически без изменения прикладных программ.
Имеется возможность гибкого конфигурирования системы и входящих в ее состав устройств в зависимости от количества и вида контролируемых параметров а также от расположения контролируемых объектов.
Глубина модуля включая полевую разводку составляет лишь 104 мм поэтому платформа автоматизации Series 90-30 гораздо менее требовательна к габаритам шкафов. Она устанавливается в стандартных электротехнических шкафах 156 мм что позволяет экономить до 50% от стоимости стандартных шкафов управления. Она легко монтируется на шасси стандартных шкафов или в стойку 500 мм. Несмотря на свою компактность модули Series 90-30 соответствуют высочайшим стандартам производительности и надежности изделий фирмы General Electric.
Подключение к сетям масштаба предприятия и полевым шинам осуществляется при помощи дополнительных устройств связи поддерживающих более восьми типов стандартных промышленных протоколов от Ethernet до ASCH.
Уникальность ПЛК Series 90-30 состоит в возможности их применения при решении любых задач автоматизации.
Series 90-30 можно устанавливать непосредственно вблизи объекта что существенно упрощает подключение к нему датчиков позволяет существенно снизить затраты на монтаж а также обеспечивает повышенные удобства в процессе обслуживания. Информация с помощью повторителей может передаваться на большие расстояния. У каждого конвертера установлено по одному контроллеру Series 90-30.
На верхнем уровне используется высокоскоростная магистраль Ethernet. Промышленный Ethernet был разработан совместно компаниями Xerox Intel и Digital Equipment и выпущен на рынок в 1980 году на данный момент существует и активно расширяет сферу своего применения. Ethernet является стандартом де-факто и близко хоть и не полностью соответствует спецификациям IEEE 802.3 (ISO 8802.3). Обе спецификации используют один и тот же механизм управления доступом к среде – CSMACD. Прежде всего следует сказать о том что еще на уровне офисных приложений была решена проблема недетерминированности Ethernet. Переход от концентраторов (hub) к коммутаторам (switch) и от полудуплексных каналов связи к дуплексным позволил снять вопрос о возможности блокировки обмена по сетевому каналу из-за многочисленных коллизий информационных кадров. Благодаря своим «интеллектуальным» возможностям коммутатор направляет полученный информационный кадр только на то подключение где реально находится абонент а не широковещательно во всю сеть. В результате общий объем трафика в сети многократно сокращается. Фактически топология «общая шина» на логическом уровне трансформируется в топологию «каждый с каждым» обеспечивая гарантированную доставку данных.
На физическом уровне Ethernet работает как с узкополосными так и с широкополосным кабелем. Узкополосный кабель используемый в Ethernet - это экранированный коаксиальный кабель к которому периферийные устройства присоединяются с помощью коннекторов.
Рис 2.7. Типичная конфигурация сети Ethernet.
Участок сети между двумя повторителями называется сегментом (segment). Вся шина может состоять максимум из пяти сегментов три из которых можно использовать для подключения станций.
Кроме того одним из основных препятствий к применению Ethernet в АСУ ТП всегда было несоответствие между исполнением аппаратных средств и условиями их применения в промышленности. Сейчас ситуация изменилась: появился целый ряд концентраторов и коммутаторов выполненных в соответствии с требованиями промышленных условий эксплуатации. Такие устройства в частности выпускаются фирмами Advantech (ADAM – 6510) Hirschmann (Rail- серия) и WAGO (758 – 500).
Исполнение коммутатора RS2 – FXFX фирмы Hirschmann (рис 5.24.) традиционно для компонента АСУ ТП:
монтаж на DIN – рейку
питание от источника нестабилизированного напряжения 10-30 В постоянного тока
диапазон рабочих температур от -40 до +85 °С
влажность в пределах 5-95% (без конденсации влаги)
соответствие международным стандартам по вибро- и пожароустойчивости электробезопасности и электромагнитному излучению
малые габаритные размеры и низкое энергопотребление.
Помимо этого устройство обладает всеми необходимыми характеристиками современного коммутатора:
шесть портов RJ -45 для подключения витой пары
поддержка всех стандартных протоколов Ethernet
высокая пропускная способность (14 Гбитс)
автоопределение параметров линии обмена (дуплексполудуплекс 10100 Мбитс).
Следующее направление развития АСУ ТП на базе Ethernet – распределенные УСО с Ethernet – интерфейсом. ADAM – 6000 (рис 5.25.) фирмы Advantech – осуществлена поддержка интерфейса RS-485 протоколов TCPIP UDPIP а также стандартный промышленный протокол ModBusTCP для прямого сопряжения со SCADA – системами посредством OPC – сервера. Новые УСО идеально подходят для построения АСУ ТП на базе Интернет – технологий поскольку имеют встроенную поддержку web – страниц и удалённой загрузки программного обеспечения.
Практика применения ПС на производстве неизбежно приводит к тому что на разных участках предприятия функционируют сети разных стандартов использующих неодинаковые среды передачи данных и протоколов. Одним из возможных решений является применение конверторов протоколов PKV фирм Hilscher.
Одним из наиболее интересных устройств данного типа являются конвертеры протоколов ПС в среду Ethernet серии PKV 30.
Устройство PKV 30 с одной стороны поддерживает такие основные протоколы ПС как CANopen DeviceNet PROFIBUS – DP ModBus – Plus AS – интерфейс а также стандартные последовательные шины RS – 232422485. C другой стороны доступ к данным осуществляется по протоколу TCPIP обеспечивая прозрачную интеграцию в любую систему верхнего уровня автоматизации. Кроме доступа посредством TCPIP PKV 30 обеспечивает пользователя целым рядом «продвинутых» функций. Приверженцы Интернет – технологий в автоматизации могут воспользоваться встроенным Web – сервером. Создание страниц в стандартном формате html осуществляется любым редактором после чего они передаются по сети в память устройства. Дальнейший просмотр накопленных устройством PKV30 данных осуществляется обычным Интернет – браузером то есть практически с любого компьютера из любой точки земного шара.
Кроме того PKV 30 может использоваться как самостоятельный ПЛК благодаря наличию процессора и предустановленной операционной системы ОС Windows CE.
ПК на котором будут обрабатываться данные выбираю следующий: MIPC-70 CT – компьютер для панелей управления с открытой рамой с 104” цветным ЖКИ дисплеем с активной матрицей. Он включает в себя плоскопанельный дисплей и высокоинтегрированную процессорную плату с процессором Pent аналоговый резистивный сенсорный экран; прочный металлический каркас обеспечивает простоту монтажа. Рекомендуется установка ПК на пульт управления конвертером и у главного мастера конвертерного передела.
В силу тех требований которые предъявляются к системам SCADA спектр их функциональных возможностей определен и реализован практически во всех пакетах. Перечислим основные возможности и средства присущие всем системам и различающиеся только техническими особенностями реализации:
автоматизированная разработка дающая возможность создания ПО системы автоматизации без реального программирования;
средства сбора первичной информации от устройств нижнего уровня;
средства управления и регистрации сигналов об аварийных ситуациях;
средства хранения информации с возможностью ее постобработки (как правило реализуется через интерфейсы к наиболее популярным базам данных);
средства обработки первичной информации;
средства визуализации информации в виде графиков гистограмм и т.п.;
возможность работы прикладной системы с наборами параметров рассматриваемых как "единое целое" ("recipe" или "установки").
Основу большинства SCADA-пакетов составляют несколько программных компонентов (база данных реального времени ввода-вывода предыстории аварийных ситуаций) и администраторов (доступа управления сообщений).
Следует отметить что в целом технология проектирования систем автоматизации на основе SCADA-систем очень похожа:
Разработка архитектуры системы автоматизации в целом. На этом этапе определяется функциональное назначение каждого узла системы автоматизации.
Решение вопросов связанных с возможной поддержкой распределенной архитектуры необходимостью введения узлов с "горячим резервированием" и т.п.
Создание прикладной системы управления для каждого узла. На этом этапе специалист в области автоматизируемых процессов наполняет узлы архитектуры алгоритмами совокупность которых позволяет решать задачи автоматизации.
Приведение в соответствие параметров прикладной системы с информацией которой обмениваются устройства нижнего уровня (например программируемые логические контроллеры - PLC) с внешним миром (датчики температуры давления и др.)
Отладка созданной прикладной программы в режиме эмуляции и в реальном режиме.
Перечисленные выше возможности систем SCADA в значительной мере определяют стоимость и сроки создания ПО а также сроки ее окупаемости.
Очевидно что для эффективного функционирования в этой разнородной среде SCADA-система должна обеспечивать высокий уровень сетевого сервиса. Желательно чтобы она поддерживала работу в стандартных сетевых средах (ARCNET ETHERNET и т.д.) с использованием стандартных протоколов (NETBIOS TCPIP и др.) а также обеспечивала поддержку наиболее популярных сетевых стандартов из класса промышленных интерфейсов (Foundation Fieldbus PROFIBUS CANBUS LON MODBUS и т.д.)
Большинство SCADA-систем имеют встроенные языки высокого уровня Visual Basic-подобные языки позволяющие сгенерировать адекватную реакцию на события связанные с изменением значения переменной с выполнением некоторого логического условия с нажатием комбинации клавиш а также с выполнением некоторого фрагмента с заданной частотой относительно всего приложения или отдельного окна.
Практически все SCADA-системы в частности CIMPLICITY PE InTouch используют ANSI SQL синтаксис который является независимым от типа базы данных. Таким образом приложения виртуально изолированы что позволяет менять базу данных без серьезного изменения самой прикладной задачи создавать независимые программы для анализа информации использовать уже наработанное программное обеспечение ориентированное на обработку данных.
Для специалиста-разработчика системы автоматизации также как и для специалиста-"технолога" чье рабочее место создается очень важен графический пользовательский интерфейс. Функционально графические интерфейсы SCADA-систем весьма похожи. В каждой из них существует графический объектно-ориентированный редактор с определенным набором анимационных функций. Используемая векторная графика дает возможность осуществлять широкий набор операций над выбранным объектом а также быстро обновлять изображение на экране используя средства анимации.
Современные SCADA-системы не ограничивают выбора аппаратуры нижнего уровня так как предоставляют большой набор драйверов или серверов ввода-вывода и имеют хорошо развитые средства создания собственных программных модулей или драйверов новых устройств нижнего уровня. Сами драйверы разрабатываются с использованием стандартных языков программирования. Вопрос однако в том достаточно ли только спецификаций доступа к ядру системы поставляемых фирмой-разработчиком в штатном комплекте (система Trace Mode) или для создания драйверов необходимы специальные пакеты (системы CIMPLICITY PE FactoryLink InTouch) или же вообще разработку драйвера нужно заказывать у фирмы разработчика.
Для подсоединения драйверов ввода-вывода к SCADA используются два механизма - стандартный DDE (Dynamic Data E во-вторых OPC устраняет необходимость использования различного нестандартного оборудования и соответствующих коммуникационных программных драйверов. С точки зрения SCADA-систем появление OPC серверов означает разработку программных стандартов обмена с технологическими устройствами. Поскольку производители полностью разбираются в своих устройствах то эти спецификации являются для них руководством к разработке соответствующих серверов. Так как эти программные драйверы уже появляются на рынке разработчики SCADA-систем предлагают свои механизмы связи с OPC драйверами. OPC интерфейс допускает различные варианты обмена: получение "сырых" данных с физических устройств из распределенной системы управления или из любого приложения (рис.2). На рынке появились инструментальные пакеты для написания OPC-компонентов например OPC-Toolkits фирмы FactorySoft Inc. включающий OPC Server Toolkit OPC Client Toolkit примеры OPC-программ.
Большинство SCADA-систем являются контейнерами которые уведомляются ActiveX о происшедших событиях. Любые ActiveX объекты могут быть загружены в систему разработки большинства SCADA и использованы при создании прикладных программ. Управление ActiveX объектами осуществляется с помощью данных методов и событийных функций свойственных выбранному объекту.
По функциональным возможностям все рассмотренные SCADA-системы в целом сравнимы. Технология программирования близка к интуитивному восприятию автоматизируемого процесса. Плюс мощное объектно-ориентированное программирование используемое в большинстве этих пакетов делает эти продукты легкими в освоении и доступным для широкого круга пользователей.
Все системы можно считать в той или иной степени открытыми обеспечивающими возможность дополнения функциями собственной разработки имеющими открытый протокол для разработки собственных драйверов развитую сетевую поддержку возможность включения ActiveX объектов и доступность к стандартным базам данных.
Важной особенностью всех SCADA-систем является количество поддерживаемых разнообразных PLCs. Системы InTouch CIMPLISITY PE Factory Link GENESIS RealFlex поддерживают десятки и сотни драйверов что делает их безусловными лидерами по этому показателю.
Построение прикладной системы на основе любой из рассмотренных SCADA-систем резко сокращает набор необходимых знаний в области классического программирования позволяя концентрировать усилия по освоению знаний в прикладной области.
У разработчиков SCADA-систем на платформе Windows 2000 появилась возможность использовать расширение реального времени (RTX) чтобы преодолеть недостатки Windows 2000 в задачах реального времени.
Следует отметить тенденции включения SCADA-систем в системы комплексной автоматизации предприятия. Это обеспечивает точную своевременную информацию на каждом уровне производства.
Применение в SCADA-системах новых технологий разработка инструментальных средств комплексной автоматизации предприятия свидетельствуют о стремлении и возможности фирм-разработчиков постоянно совершенствовать свои продукты что является немаловажным фактором при выборе инструментального средства даже если не все его технологические решения в ближайшее время будут использованы Вами.
Коль скоро общее поле деятельности ведущих компаний производителей описываемых инструментальных систем сегодня концентрируется в области MS Windows 2000 коль скоро общие технические возможности систем достаточно близки то главный упор делается на качество технической поддержки на качество обучения пользователей на концентрацию и качество дополнительных комплексных услуг по освоению и внедрению конечной системы управления. Другими словами на сокращение издержек системных интеграторов и конечных пользователей на инжиниринг и менеджмент своих проектов на уменьшение стоимости сопровождения конечной системы. Именно эти показатели сегодня в основном влияют на рейтинг и рыночный успех той или иной SCADA системы. Пожалуй эти показатели даже более важны чем абсолютные стоимостные характеристики SCADA-систем.
5. Описание аналоговой информации
Расход дутьевого воздуха. Сигнал от сенсора расхода “Метран - 360” поступает на вход ИП имеющего выход 4-20 mA.
Температура. От термопары ТХА сигнал термоЭДС поступает на УСО ADAM фирмы Advantech имеющего выход 4-20 mA.
Давление подаваемого воздуха. Импульсная трубка 2.5-70-15 с которой сигнал поступает преобразователь SITRANS P фирмы Siemens имеющего выход 4-20 mA.
Разряжение в пылевой камере. Измерительный комплект SITRANS P фирмы Siemens имеющего выход 4-20 mA.
Содержание SO2 в отходящих газах. Газоанализатор “Диск-108” с выходным сигналом 0-5 mA.
6. Перечень дискретных сигналов
Привод заслонки на трубопроводе подачи воздуха
Привод поворота клапана на трубопроводе с водой на охлаждение напыльника.
Привод поворота клапана на трубопроводе дымососа на разряжение пылевой камеры.
Функционирование описываемой системы может осуществляться в трех режимах: автоматическом; ручном.
Автоматический режим не требует вмешательства в процесс управления и поддерживается все время пока система работает безотказно. При этом реализуется непосредственно цифровое управление.
Ручной режим может осуществляться в следующих операциях:
- отключение питания управляющей машины;
- отказе управляющей машины;
- отказе какого-либо из узлов системы управления (датчика нормирующего преобразователя и др.);
- возникновение аварийной ситуации требующей решений не предусмотренных алгоритмами управления.
При необходимости ручного управления оператор может переводить ключ выбора режима в положение «ручное» и например направляет газы при помощи имеющихся средств ручного управления заслонками основываясь на показаниях приборов технологического контроля параметров процесса.
7. Характеристика параметров контроля и регулирования процесса конвертирования медно-никелевых штейнов.
Таблица исходных данных для проектирования КИП и А.
Наименование измеряемого параметра
Количество точек измерения
Место установки прибора
Тип вторичного прибора
Расход дутьевого воздуха на конвертер нм3ч
Давление воздуха перед фурмами конвертера кгссм2
Температура кладки фурменного пояса оС
Кладка фурменного пояса
Температура расплава оС
Температура отходящих газов оС
Разрежение в пылевой камере мм. вод. ст.
Содержание SO2 в газах %
Температура в пылевой камере оС
8. Структура комплекса технических средств АСУТП
Датчики технологических параметров позволяют иметь правильное представление о процессе и возможность управления им (первичные приборы). Первичные приборы вырабатывают сигнал измерительной информации в той форме которая удобна для передачи а дальше для преобразования в унифицированные стандартные сигналы и поступают на средний уровень иерархии затем на средства отображения информации – верхний уровень а потом на вычислительный комплекс УВК. Сигнал идет через устройство связи с объектом.
В состав КТС входят управляющие вычислительные а также исполнительные устройства.
Выходы регулятора управляют электрическими исполнительными механизмами. Между выходными цепями и исполнительными механизмами включены магнитные пускатели (ПБР).
Техническое обеспечение включает в себя средства автоматики и АСУТП вычислительной техники достаточной для выполнения всех функций системы.
Успешное ведение любого технологического процесса возможно лишь при условии правильного соблюдения технологического режима. Для этого необходим точный и непрерывный контроль и регулирование параметров процесса которые осуществляет комплекс технических средств (КТС) АСУТП.
Комплекс технических средств АСУТП передела включает:
- Средства получения информации о состоянии объекта датчики систем автоматического контроля и дискретных сигналов о состоянии оборудования;
- Средства получения передачи и преобразования информационных и управляющих сигналов (пользовательский интерфейс).
- Средства формирования и управляющих воздействий в системе - контроллер и промышленный компьютер;
-Средства ввода-вывода информации для оперативного персонала - монитор принтер сенсорный экран.
Автоматическое регулирование параметров процесса конвертирования осуществляется по следующим цепочкам:
Контроль давления дутья.
Сигнал отбирается с помощью импульсной трубки и поступает на преобразователь давления SITRANS P фирмы S на двигатель производящий перемещение напыльника при падении давления дутья и на механизм однооборотный МЭО-65025-0.25 К-84 для поворота заслонки на газоходе.
Контроль температуры кладки.
Датчик ТХА – на вход УСО ADAM фирмы Advantech далее сигнал подается на вход модуля ввода IC693ALG220 затем на ПК.
Контроль разрежения в пылевой камере.
Измерительный комплект SITRANS P фирмы Siemens – модуль ввода IC693ALG220 затем в ПК.
Контроль температуры отходящих газов.
Датчик ТХА - 0179 – на вход модуля ввода IC693ALG220 затем на персональный компьютер.
Содержание SO2 в отходящих газах.
На выходе из пылевой камеры установлен газоанализатор “Диск-108” с выходным сигналом 0-5 mA который подается на модуль ввода IC693ALG220 а далее — на ПК.
9. Перечень документов АСУТП и описание мнемосхемы
Информационный обмен между компонентами АСУТП осуществляется в автоматическом режиме в реальном масштабе времени.
Информация с датчиков поступает с частотой один раз в полсекунды. Для максимального сохранения информации используется ее сжатие. Информация поступающая непрерывно (расход воздуха давление дутья разряжение в пылевой камере) усредняется за три минуты. При накоплении десяти значений — вновь усредняется.
Информация о количестве загружаемых компонентов и продуктов конвертирования сохраняется полностью.
Пробы для анализа на содержание металлов и SiO2 берутся с каждого ковша и сохраняются их средние значения по варкам. По истечении каждой смены делаются две распечатки — начальнику цеха и главному инженеру — сменные отчеты. Эта же информация сохраняется на дискетах.
Выходная информация помимо сохранения в главной информационной базе АСУТП представляется несколькими способами:
- в виде графиков изменения параметров во времени
Все они представляются либо на экране монитора либо на бумаге.
Информация в табличном виде включает в себя следующие документы:
Текущие технологические параметры.
Сводка технологических параметров конвертера за один час.
Сводка о длительности отказов отдельных узлов АСУТП.
Сводка технологических показателей работы конвертера за смену.
Сводка технологических показателей работы конвертера за сутки.
Сводка показателей работы оборудования за сутки.
План-график работы конвертера по сменам и за сутки.
Таблица положения ключей режимов управления ЛСКР.
Таблица результата анализа качества полученного файнштейна.
На экране у технолога постоянно находится информация о наиболее важных технологических параметрах (расходе температуре и т.д.). Суточная сводка отчетной документации АСУТП передела:
Таблица 2.5.Среднесуточный состав файнштейна%
Таблица 2.6. Среднесуточный состав конвертерных газов при продувки медно-никелевого штейна (пробы отобраны на расстоянии 1 м над ванной конвертера
Периодработы конвертера
Содержание в % (объемные)
Начало операции (после зарядки)
Середина операции (набора массы)
В АСУ ТП конвертирования информация в графическом виде включает в себя видеограммы:
График изменения температуры отходящих газов.
График изменения подачи дутьевого воздуха.
Видеограмма-график содержания Ni Cu Co в файнштейне.
Мнемосхема технологического оборудования.
Мнемосхема аппаратуры контроля и регулирования.
Информация в виде файлов содержит:
Файл корректировки установок.
Файлы технологических замеров и заданий.
Протокол работы АСУТП.
Обеспечивается защита от несанкционированного доступа к базе данных и от программных вирусов при помощи антивирусных программ.
Технологическая и управляющая информация формируются контроллером и передается от ТОУ с помощью кабельных трасс соединяющих контроллер в операторском помещении с исполнительным механизмом рабочей площадки.
Итоговая информация выводится на печатающие устройства и мониторы терминалов АСУТП. Информация о процессе хранится в составе загрузочного модуля на внешнем носителе информации для быстрого перезапуска системы.
Итоговая информация помимо внутренней памяти сбрасывается на внешнее запоминающее устройство (раз в 2-5 мин.) для восстановления и исключения искажений при сбоях операционной системы.
Технологическая информация аналогового типа в каждом цикле контролируется на достоверность. Кроме того периодически выполняется аппаратурная проверка точности формирователей и каналов передачи сигналов процессе профилактических осмотров КТС АСУТП (не реже 1 раза в 10 дней).
Архивация данных АСУТП производится для надежного рестарта задач АСУТП при сбоях операционной системы а также для технического обеспечения анализа эффективности работы конвертера.
Для обеспечения выполнения этих задач в ППК АСУТП архивируются следующие массивы информации:
-текущая информация за три смены;
-отчетная сменная информация за десять суток;
-отчетная суточная информация за месяц;
протоколы работы АСУТП не менее чем за десять суток.
1. Описание математической модели
Запишем уравнение установившегося теплового баланса конвертера.
где Q – тепловые потоки кДжч. связанные либо с физическим теплом потоков материалов (штейн флюсов холодных присадок воздуха файнштейна шлака газов) либо с выделением и поглощение тепла в химических реакциях либо с потерями тепла в окружающее пространство.
Уравнение мгновенного баланса на период продувки штейна будет иметь вид:
Где - масса в конверторе кг
С – теплоёмкости материалов
- температура в ванне конвертера °С
g - материальные потоки
Путём алгебраических преобразований и выражения тепловых потерь через коэффициент суммарной теплоотдачи через стенки конвертера К который зависит от температуры ванны и температуры окружающей среды выражения тепловых эффектов химических реакций через результирующий тепловой эффект энергетического процесс получим дифференциальное уравнение объекта управления:
Преобразуем полученное уравнение:
Разделим обе части уравнения на А:
Проведём исследование статических и динамических объекта управления по каналам управлений и возмущений. В нашем случае каналами возмущения и управления будут являться: поток штейна и поток воздуха дутья.
Найдём коэффициенты усиления чтобы определить какой из каналов взять за возмущение какой за управление. Для этого необходимо изменять исследуемые параметры в ту или иную сторону построить график изменения температуры в ванне конвертера.
Определяем коэффициенты усиления. Наибольшее значение К будет соответствовать каналу управления а второй по величине – каналу возмущения.
Рис 3.1. График изменения температуры при изменении потока штейна
Рис 3.2. График изменения температуры при изменении потока воздуха дутья
Из построенных графиков видно что самый высокий коэффициент усиления получили при изменении расхода воздуха поэтому примем его за управляющее воздействие а поток штейна будет являться возмущающим воздействием т.к. .
С целью оценки запаздывания и постоянной времени по графику для канала управления (измерение расхода воздуха) определим t033 и t067.
для канала возмущения (измерение расхода штейна) определим t033 и t067.
Оптимальные настройки регулятора оценивают с учётом критерий качества работы системы (минимум времени регулирования минимум интегральной квадратичной ошибки) и закона управления.
Передаточная функция ОУ по каналу управления:
Передаточная функция ОУ по каналу возмущения:
Для определения устойчивости объекта управления зная значения динамических параметров T и построим амплитудно-фазовую частотную характеристику АФЧХ объекта управления в этом случаи передаточная функция будет иметь вид:
Поскольку годограф строится на комплексной плоскости то для его построения заменим оператор Лапласа в передаточной функции тогда передаточная функция разомкнутой системы будет иметь следующий вид:
Для данной модели в качестве регулятора выберем линейный регулятор с ПИ законом регулирования так как он обеспечивает быстродействие и отсутствие статической ошибки а так же легко реализуем на практике.
где - коэффициент передачи пропорциональной части регулятора;
Динамическая ошибка на выходе регулятора – разница между текущим значением выходного параметра и заданным:
Выполнив прямое преобразование Лапласа получим:
С учётом того что параметры регулятора контура обратной связи выбираются по статическим и динамическим характеристикам объекта управления по каналу управления то:
По формулам определения оптимальных настроек линейных регуляторов обратной связи с учётом критерия оценки качества процесса (интегральный квадратичный) для ПИ – регулятора время изодрома будет:
Передаточная функция ПИ – регулятора выражается формулой:
Воспользовавшись приложением Simulink была простроенная схема объекта управления и реализована переходная характеристика.
Рис 3.3. Схема объекта управления
Рис 3.4. Переходная характеристика процесса конвертирования
ЭЛЕКТРОТЕХНИЧЕСКАЯ ЧАСТЬ
Необходимо произвести расчет электронагрузок выбрать тип мощность и количество цеховых трансформаторных и главных подстанций выбрать и рассчитать сеть. Выбрать тип и мощность компенсирующих устройств.
Питание приемников обжигового участка осуществляется от главной понизительной подстанции завода 220356 кВ.
Подвод электрической энергии осуществляется через защитную и пусковую аппаратуру. В качестве такой аппаратуры используются: автоматические выключатели рубильники магнитные пускатели контакторы.
Установленные мощности электроприемников Рн их напряжения Uн и расстояния от питающих подстанций L.
Наименование электроприемника
Подъемник телескопический
Электронагрузки создаваемые электроприемниками определяются методом коэффициента спроса:
где и принимаются по справочным данным.
Мощность приемников повторно-кратковременного режима приводится к мощности длительного режима:
где Рн – номинальная мощность в повторно-кратковременном режиме;
ПВ – продолжительность включения в долях.
Для кранов установленная мощность принимается равной сумме мощностей двух наиболее мощных двигателей и принимается за общую мощность:
Мощность потребляемая для освещения определяется по суммарной площади цеха Fц и удельной мощности Руд:
Pосв = Pц Pуд = 4320 16 10-3 = 68 кВт.
Расчет нагрузок приведен в табл. 5.2.
Потери в сети низкого напряжения:
Pc = 002 Pp = 002 747 = 15 кВт
Qc = 003 Qp =003 516 = 15 квар
Расчетная мощность трансформаторов:
Номинальная мощность трансформаторов:
где кn – коэффициент допустимой послеаварийной перегрузки трансформаторов;
n – число трансформаторов на подстанции n = 2 так как электроприемники цеха принадлежат ко 2-й и 1-й категориям по бесперебойности электроснабжения.
Принимаем комплектную трансформаторную подстанцию КТП-М-10006 с двумя трансформаторами Sн = кВА
Коэффициент мощности на высоком напряжении будет равен:
Всего нагрузки на напряжении 6 кВ:
Всего на напряжении 380 В
Неучтенные нагрузки 3%
Расчетная нагрузка на низком напряжении
Необходимая мощность компенсирующих устройств:
Принимаем комплектную нерегулируемую конденсатную установку УК-038-150 мощностью 150 квар.
Питание технологических приемников осуществляется по радиальным кабельным линиям освещение – по магистральным линиям.
Типы кабелей их сечения и способы прокладки указаны в табл. 5.3
Типы кабелей их сечения и способы прокладки
Потери напряжения % нормпусков
Кабель число жил*сечен мм2
Расчетный ток линии и выбор ее сечения по допустимому нагреву:
а) для одиночного приемника:
б) для группы приемников:
Сечение линий S выбираем так чтобы:
где к – поправочный коэффициент (к = 075-10);
Iдоп – допустимый ток для сечения S данного вида кабелей при определенном способе их прокладки.
Потери напряжения в распределительной сети:
а) при нормальном режиме:
б) при пусковом режиме:
- удельная проводимость;
S - сечение выбранное по нагреву.
а) для асинхронных и синхронных двигателей:
б) для групп двигателей:
где Iпmax и Iнmax – пусковой и номинальный токи наибольшего двигателя.
В качестве коммутационной аппаратуры низкого напряжения применяются комплектные ящики ЭУ-5000 для приемников мощностью до 75 кВт.
Для управления высоковольтными приемниками применяются высоковольтные щиты типа КВП-6-01-603 выбираемые по номинальному напряжению и току и представляющие собой комплектный ящик с масляным выключателем и электромеханическим приводом.
Принципиальная схема электроснабжения участка обжига представлена на рис. 1.1.
Рис.4.1. Принципиальная схема электроснабжения конвертерного участка.
КТП-М 10006(10)04 - Комплектная трансформаторная подстанция мачтовая предназначена для приема преобразования и распределения электрической энергии трехфазного переменного тока промышленной частоты 50 Гц.
КТ-6000 – контактер предназначен для включения и отключения приемников электрической энергии и расчитаны на номинальное напряжение 380 В 50 Гц.
ВМК-35 Э – масляный выключатель
КРМ – автоматическая конденсаторная установка. КРМ позволяет снизить потребляемый из сети ток (на 30-50%) практически свести к нулю оплату за реактивную энергию значительно увеличить пропускную способность распределительной сети (наращивание потребляемой мощности предприятия без реконструкции энергосистемы) и ее надежность. Таким образом эффективно “разгружается” электросеть что позволяет снизить на 5-15% потребление активной энергии.
БЕЗОПАСНОСТЬ ЖИЗНЕДЕЯТЕЛЬНОСТИ
1.1. Анализ вредных и опасных факторов производства
Практика показывает что далеко не везде и не всегда технически обеспечиваются нормальные условия труда на рабочих местах около конвертеров.
Специфические условия работы создаются под подиной конвертера. Чаще всего работа связана с ревизией и заменой воздухораспределительных фурм. Нельзя допускать производство подобных работ без полной очистки подины. Особы опасны работы в дутьевых фурмах при наличии в конвертере горячего материала.
При чистке футеровки и подины конвертера от настылей а также при других работах внутри конвертера (установка защитных блоков для термопар установка дутьевых сопел и т.д.) возможны падения спеков или кирпичей от свода или высокорасположенных боковых поверхностей стен. Для производства работ на конвертере организуют несколько ярусов монтажных перекрытий из прочных досок.
Чистку или ремонт газоходов или поверхностей охлаждения газов при кратковременных горячих остановках конвертера следует выполнять после сравнительно длительной продувки для полной эвакуации сернистых газов и снижения температуры в конвертере и газоходном тракте. Порядок действий и распределение обязанностей персонала при возникновении опасных ситуаций при любых работах регламентируется инструкциями и стандартами предприятия.
Систематические осмотры с занесением в специальные журналы состояния оборудования конструкций и технологии являются основой для профилактической работы по созданию безаварийной и безопасной технологии конвертирования медных штейнов.
К факторам влияющим на здоровье и работоспособность человека при работе на участке конвертирования медных штейнов относятся:
воздушная среда характеризующаяся повышенной загазованностью связанной с присутствием в воздухе газов среди них SO2 и пыль;
большое количество пыли на площадках;
акустические колебания создаваемые конвертером при его работе;
высокая температура воздуха около печи газоходов и циклонов.
Источниками выделения газов и пыли являются: отверстие на загрузочной камере конвертера для подачи штейна; течки для выгрузки огарка и пыли; люки на газоходах циклонах котлах-утилизаторах; уплотнение термопар; щели на сварочных швах и др. При недостатке средств тяги и зарастании газопроходных отверстий создаются очень тяжелые по газу условия работы в районе установки конвертера.
Для коренного улучшения санитарных условий труда необходимо обращать внимание на конструкцию запорных и дозирующих устройств различного назначения и места их установки. Для загрузки штейна в конвертер рекомендуется устанавливать двухшиберный затвор широко применяемый на заводах. Необходимо усиливать и аспирационные отсосы.
На рабочих площадках полах лестницах на поверхности газоходов циклонов и другого строительного и технологического оборудования необходимо организовать плановую уборку пыли с помощью пневматических вакуумных систем. В некоторых случаях целесообразна гидроуборка площадок и полов Этими мерами достигаются не только лучшие условия труда но и уменьшаются механически потери цветных металлов.
Шум вызывается работой дисковых питателей ленточных конвейеров а также химическими процессами происходящими в самом конвертере. Уровень шума меняется в зависимости от производственного участка и может достигать 100Дб и выше. Высокий уровень шума препятствует сосредоточению внимания затрудняет речевой обмен. Из-за шума происходят изменения в нервной сердечно-сосудистой и пищеварительной системах ухудшается сон.
Уменьшение теплового излучения от горячих поверхностей достигается прежде всего усилием внутренней теплоизоляции и затем установкой экранов обеспечивающих удобный доступ для осмотров и обслуживания соответствующих мест конвертерной установки.
1.2. Статистика травматизма и профессиональных заболеваний
К наиболее тяжелым последствиям приносящим материальный ущерб и групповые несчастные случаи приводят аварии на взрывопожароопасных производствах имеющихся на каждом крупном металлургическом предприятии. По количеству аварий связанных со взрывами и пожарами металлургическая промышленность стоит на втором месте – после химической промышленности число пожаров и взрывов в которой в 4–5 раз меньше чем в химической отрасли но превышает число взрывов в других отраслях промышленности.
По сравнению с 2009 годом за 2010 год количество чрезвычайных ситуаций на производстве снизилось на 276 % (на 79 случаев).
Количество пострадавших снижено на 283 % (на 96 человек) погибших на 301 % (на 58 человек).
Произошло 4 групповых несчастных случая при которых погибло 8 человек и 2 были тяжело травмированы за 2009 год - 4 групповых случая при которых погибло 6 человек и 7 тяжело травмировано.
На предприятиях и объектах подконтрольных территориальным органам МЧС в области промышленной безопасности за 2010 год по сравнению с 2009 годом травматизм с тяжелым исходом снижен в 2 раза травматизм со смертельным исходом в 14 раза.
Основной причиной несчастных случаев являются обрушения горной массы низкий уровень производственной дисциплины и организации работ личная неосторожность пострадавших.
За 9 месяцев 2011 года:
По сравнению с прошлым годом за отчетный период количество чрезвычайных ситуаций на производстве снизилось на251%(на 44 случая).Количество пострадавшихсниженона213% (на 42 человека) погибших на327% (на 35 человек).
На предприятиях и объектахподконтрольных территориальным органам МЧС в области промышленной безопасностиза9 месяцев 2011 года в результате несчастных случаев на опасных производственных объектах погибли14человек тяжело травмированы18человек. За этот же период 2010 года тяжело травмированы13человек17человек погибли.
Несчастные случаи на производстве происходят в основном по следующим причинам:
неудовлетворительная организация работ – 405%;
нарушение технологических процессов и проведения ремонтов – 232%;
нарушения техники безопасности – 201%;
нарушение производственной и трудовой дисциплины (в том числе и нахождение в состоянии алкогольного опьянения) – 162 и др.
Основными травмирующими факторами являются:
машины и механизмы технологическое оборудование – 412%;
падение с высоты людей предметов – 272%;
отравление газами – 194%;
хлопки и выбросы раскаленного металла или газа – 151% и др.
Более 50% несчастных случаев приходится на долю ремонтного персонала.
Неудовлетворительное состояние оборудования особенно газоходов и газопроводов (из-за их негерметичности вследствие коррозирующего разрушения) часто приводит к попаданию газов в воздух рабочей зоны.
Основными причинами влияющими на статистику профессиональных заболеваний являются:
Санитарно-гигиенические:
загрязненность воздуха (заболевания дыхательных органов)502%;
плохое осветительное и вентиляционное оборудование 236%;
ненормальные метеорологические условия (температура скорость движения воздуха) 105% и др.
недостаточная обученность рабочих (в том числе и пользованием средствами индивидуальной защиты);
применение опасных способов работы (ремонтные работы) внутри конвертера.
Как указано выше практически основной причиной профессиональных заболеваний является загрязненность воздуха и шум поскольку процесс конвертирования отличается большим пылевыносом. Из-за недостаточной герметичности газоходного тракта пыль и газы попадают в воздух рабочей зоны. Проникая в легкие пыль вызывает специфические заболевания - пневмокониозы а также раздражает кожу слизистую оболочку глаз и десен.
1.3. Техника безопасности
Для переработки штейнов "черной" меди в конвертерах имеют место следующие требования:
Конвертер оборудован системой световой и звуковой сигнализации обеспечивающей автоматическую подачу предупредительного сигнала о повороте конвертера на слив или дутье.
Площадка фурмовщика имеет не менее двух выходов расположенных с противоположных сторон. Над площадкой фурмовщика предусмотрено защитное ограждение предохраняющее рабочего от падающих твердых частиц брызг расплава из горловины и напыльника конвертера.
При расчистке горловины конвертера с помощью мостового крана применяються специальные приспособления ("крюк" "якорь" и др.) с предохранительными устройствами ограничениянагрузки. Конструкция приспособлений должна обеспечивать механическую связь с крюком крана приразрушении предохранительного элемента.
Не допускается использовать механизм поворота (привод) конвертера для срыва настыли с горловины.
Расчистка и обмазка горловины конвертера производится с откидных или выдвижных площадок оборудованных перилами.
Привод поворота конвертера имеет не менее двух двигателей. Питание двигателей производится от независимых источников.
При прекращении подачи энергии на один из двигателей поворота прогаре фурм или кожуха конвертера наличии под ним влаги следует немедленно перевести конвертер в нерабочее положение и принять меры к устранению неполадок.
Привод горизонтального конвертера оборудован автоматической системой поворота срабатывающей при падении давления дутья ниже регламентируемой величины и сопровождаемой звуковым сигналом.
Линияподачи дутья на конвертер оборудована задвижкой с механизированным приводом.
Поворот конвертера на дутье сблокирован с системой подачи воздуха на фурмы.
Подача кислорода в конвертер производится только после пуска конвертера под дутье.
Не допускается применение гидравлических приводов в механизмах поворота вертикального конвертера а также использование червячной передачи механизма поворота конвертера в качестве тормоза.
Фурмы имеют свободный доступ для осмотра и ремонта. Чистка фурмы производится сверху со специальной площадки.
Положение фурмы в конвертере контролируется с помощью показывающих и регистрирующих приборов установленных на пульте управления.
Механизм вертикального передвижения фурмы оборудован конечным выключателем и устройствами исключающими возможность падения фурмы в конвертер.
Конвертер оборудован автоматически сигналом вертикального положения.
Конвертер имеет блокировку исключающую его поворот при опущенной в него фурме.
В системе охлаждения фурмы предусмотрен резервный насос. Питание электродвигателей насосов осуществляется от разных или независимых источников электроснабжения.
Конвертер имеет блокировки исключающие опускание фурмы в случаях когда:
а) фурма находится не на оси рабочего положения;
б) конвертер находится не в вертикальном положении;
в) отсутствует циркуляция воды в системе охлаждения фурмы;
г) отклонен дымосос.
Конвертер оборудован устройствами автоматического подъема фурмы в случае:
а) падения давления газа в кислородной (азотной) линии ниже установленного;
б) снижения давления и расхода воды на фурму;
в) аварийной остановке дымососа.
Подача кислорода (воздуха) в фурму производится автоматически при опусканиисопладо уровня горловины конвертера а отключение - при подъеме сопла выше уровня горловины конвертера.
Механизм передвижения фурменной тележки имеет блокировку исключающую ее перемещение при опущенной в конвертер фурме.
В случае применения подшипниковскольженияизносцапф конвертеров во всехизмеренияхне превышать 10% от их первоначальных размеров.
Проверка цапф методом неразрушающего контроля производится по окончании монтажа и капитального ремонта конвертера.
Результаты проверки оформляются актом.
Металлические части конвертера которые могут оказаться под напряжением заземлены.
Заземляющие устройства защищены от коррозии и иметь обозначение "Земля".
Устройство фурменных площадок конвертеров обеспечивает удобное и безопасное обслуживание фурм. Площадка имеет ширину не менее 25 м.
Над площадкой фурмовщика предусмотрено защитное приспособление предохраняющее рабочего от попадания на него брызг и твердых частиц из горловины конвертера во время работы и при повороте его.
Рабочая площадка для взятия пробы шлака конвертера имеет ширину не менее 15 м и экран для защиты рабочего от лучистого тепла.
Расстояние между бортами загрузочной площадки и наиболее выступающими частями транспортных устройств не менее 15 м.
Площадка для чистки напыльника имеет ширину не менее 13 м а длину не менее 2 м. Расстояние (по высоте) между этой площадкой и нижней точкой мостового крана имеет не менее 23 м.
Рабочие площадки у конвертеров свободны от посторонних предметов.
Для отдыха рабочих обслуживающих конвертеры имеются кабины с кондиционированным воздухом.
Конструкция напыльника конвертера предусматривает:
а) максимально плотное сочленение с бочкой;
б) охлаждение напыльника или другие конструктивные решения предотвращающие образование прочных трудноочищаемых настылей на стенках и крышке напыльника;
в) удаление всего количества газов образующихся на всех стадиях процесса и допускать свободную и удобную загрузку материала в конвертер.
Во вновь строящихся конвертерных цехах устройства для аэрации обеспечивается быстрое и полное удаление газов поступающих в атмосферу здания при повороте конвертера.
Перед поворотом конвертера на слив или дутье подается предупредительный сигнал а люди удалены с фурменной площадки.
Пульт управления конвертером расположен так чтобы конвертерщик мог свободно вести наблюдение за работой конвертера и в то же время находиться вне зоны возможного попадания выбросов и брызг при повороте конвертера.
Пульт управления оборудован необходимыми контрольно-измерительными приборами (далее - КИП) иметь аварийный выключатель для снятия напряжения на случай залипания контактов основного устройства поворота а также оснащен необходимыми средствами связи со всеми взаимодействующими участками.
Механизм пуска и остановки дутья надежны быстродействующий и расположен вблизи от конвертерщика.
Конвертер оборудован автоматическим поворотом срабатывающим при прекращении подачи дутья падении давления дутья и прекращении подачи электроэнергии.
Аварийный поворот сблокирован со звуковой сигнализацией. Работа конвертера с неисправным механизмом поворота запрещается.
Для предотвращения заливки фурм включение дутья при повороте конвертера сблокировано с механизмом поворота.
.Электродвигатели и тормоза надежно защищены от брызг расплава и механических повреждений.
Проверка состояния механизма поворота конвертера производиться ежесменно.
Запрещается нахождение людей на фурменной площадке во время загрузки в конвертер штейна и холодных присадок а также под конвертером и в его приямке во время работы конвертера.
Во время загрузки в конвертер штейна и холодных присадок с помощью мостового крана а также слива шлака или расплавленной массы из конвертера лица не имеющие отношения к указанным операциям удалены передних площадок конвертера .
Уплотнение и ремонт фурм производится на остановленном конвертере.
Загрузка в конвертер холодных присадок механизирована и обеспечена взвешивающими или дозирующими механизмами. Загрузка в конвертер влажных присадок запрещается.
Для предотвращения выброса расплавленной массы из конвертера заливки штейна на передутую медь запрещается.
При снижении давления дутья ниже установленного заводской нструкцией прогаре кожуха или появлении под конвертером воды конвертер переводится в нерабочее положение и принимаются меры к устранению неполадок.
Охлаждение раскаленных мест на кожухе конвертера водой запрещается. При перегреве кожуха охлаждение его допускается сжатым воздухом.
Отбор проб допускается только при нерабочем положении конвертера отсутствии дутья и наличии экрана защищающего рабочего от воздействия лучистого тепла. Ложки и другие приспособления для отбора проб используются сухими и подогретыми.
При сливе из конвертера шлака или расплавленной массы в ковши нахождение рабочих у ковшей запрещается.
Для защиты рабочих от теплоизлучения при сливе установлен защитный экран.
Приступать к прочистке фурм допускается не ранее чем через 2-3 мин. после пуска конвертера. При фурмовке конвертера рабочие стоят сбоку фурмы.
Заводить и натравлять крючья под настыль при очистке горловины разрешается длинными штангами стоя на площадке. Выполнять эту операцию стоя на кожухе конвертера запрещается.
Расчистка и обмазка горловины конвертера производиться с опущенной перекидной площадки огражденной перилами.
При снятии настылей с горловины конвертера нахождение рабочих в зоне действия мостового крана и под рабочими площадками запрещается.
Чистка напыльника и поворотного механизма допускается только после остановки дутья. Чистка и уборка настылей должны производиться последовательно сверху вниз.
На время чистки газоходов напыльников или уборки под конвертером вывешиваются плакаты: "Не ходить производится уборка!".
Все водоохлаждаемые детали работающие в зоне высоких температур и расплавленного металла оборудованы автоматической сигнализацией оповещающей о падении давления воды или прекращении ее циркуляции.
Перед сдачей смены горловина напыльник и кожух конвертера освобождаются от настылей и производится уборка под конвертером и всех площадок.
При работе на установках пылеулавливанияи очистки газов имеют место следующие требования безопасности :
Все наружные металлические части электрофильтров находящиеся под напряжением ограждены или закрыты защитными колпаками. Выпрямитель высоковольтный агрегат и разъединитель надежно ограждены сетчатым ограждением высотой не менее 25 м.
Все металлические части электрофильтра не находящиеся при работе под напряжением а также все металлические конструкции связанные с электрофильтром (газоходы шнеки и т.п.) заземлены в соответствии с проектом.
Не допускается нахождение в помещении электрофильтров лиц не связанных с их обслуживанием без специального разрешения и сопровождающего.
Все работы внутри электрофильтров газоходов и другого аналогичного оборудования производятся по наряду-допуску с соблюдением требований инструкции по организации безопасного проведения газоопасных работ и технологических инструкций разработанных и утвержденных в установленном порядке с учетом следующих требований:
а) внутренний осмотр ремонт и чистка электрофильтров производятся только под непосредственным наблюдением или при участии лица ответственного за его эксплуатацию;
б) электрофильтр отключен от газа с обеих сторон плотными исправными шиберами и заглушками;
в) с устройства снято напряжение;
г) коронирующие электроды заземлены и произведено отряхивание коронирующих и осадительных электродов;
д) пыль из бункера полностью удалена а электрофильтр - охлажден
е) корпус электрофильтра продут до полного освобождения его от остатков газа;
ж) в электрофильтрах очистки токсичных или взрывоопасных газов кроме того проводится анализ воздуха на содержание вредных примесей.
В случае зависания пыли в электрофильтрах шуровка их разрешается только после снятия напряжения с коронирующих элементов и их заземления. Шуровка бункера производится под наблюдением дежурного по электрофильтрам. Рабочие производящие шуровку пользуются соответствующими СИЗ спецодеждой и спецобувью.
Не допускается производить ревизию встряхивающего механизма рукавного фильтра на ходу и проверять состояние рукавов во время работы встряхивающего механизма.
Привод разгрузочного шнека снабжен местной кнопкой "Стоп" для аварийной обстановки устройства.
Циклоны предназначенные для улавливания взрывоопасных пылей оборудованы предохранительными устройствами.
Не допускается одновременная чистка (шуровка) нескольких бункеров батарейных циклонов и коллекторов.
Установки улавливающие хлор оборудованы автоматическими газоанализаторами для определения содержания хлора в очищенных газах перед их выбросом в атмосферу.
При аварийной остановке хлорулавливающей установки прекращены все технологические процессы связанные с выделением хлора в соответствии с технологической инструкцией и ПЛА утвержденных в установленном порядке.
Открытие и закрытие шиберов центральных газоходов механизировано.
Подземные газоходы газонепроницаемы (герметичными) а своды боровов - теплоизолированы.
Для осмотра состояния подземных газоотводящих каналов устроены специальные лазы размером не менее 065 x 065 м с удобным спуском.
Выгрузка и транспортирование пыли из газоходов и установок пылеулавливания производится способами исключающими выделение вредных веществ.
Для обслуживания и ремонта сводов пылевых камер боровов и газоходов предусмотрены площадки и переходные мостики. Нахождение людей на сводах технических устройств не допускается.
Действия обслуживающего персонала при возгорании пыли в системах пылеулавливания и очистки газов определяться технологической инструкцией и ПЛА утвержденных в установленном порядке.
1.4. Промсанитария. Нормы для данного производства
Наряду с требованиями безопасности описанными выше существуют определенные нормы которые снижают опасность факторов имеющих место на данном производстве. К ним можно отнести следующие общие правила:
территория помещения участка конвертирования содержится в чистоте и систематически очищаться от отходов производства;
накопление пыли на стенках конструкциях и оборудовании не допускается;
освещение территории проходов проездов во всех помещениях и отельных рабочих местах соответствует установленным нормам: для переносного электрического освещения применяются светильники напряжением не выше 36В; при работе внутри емкости напряжение осветительной сети не превышает 12В;
уровень шума на рабочих местах не превышает нормируемого уровня звука. Согласно ГОСТ 12.1.003-83 нормируемый уровень звука не более 80 децибел. При превышении этого уровня рабочий персонал работающий вблизи источника шума обязан для подавления шума применять наушники;
все эксплуатационное оборудование а также используемые инструменты и приспособления для обслуживания исправны;
аспирационные системы включаются в работу до пуска технологического оборудования а отключаться после его остановки и обеспечивать удаление пыли и газа от места их образования;
аспирационные системы максимально герметичны;
Кроме средств индивидуальной защиты (СИЗ) обеспечивается и работает искусственная (приточная) вентиляция. Роль приточной вентиляции сводится к подаче свежего чистого воздуха взамен отсасываемого грязного.
Воздух для вентиляции поступает по приточной камере от центральной вентиляционной станции оборудованной вентилятором большой мощности. Выброс в атмосферу загрязненного воздуха производится непосредственно из здания. Кроме того на участке осуществляется местная вентиляция заборники которой расположены в непосредственной близости от аппаратов.
Вентиляция является эффективным средством обеспечения нужных гигиенических качеств воздуха соответствующих требованиям санитарных норм проектирования промышленных предприятий (СН 245-71).
Для характеристики условий труда на участке конвертирования важное значение имеет производственный микроклимат – комплекс значений физических характеристик метеорологических факторов в ограниченном пространстве производственного помещения. К таким факторам относятся температура воздуха влажность скорость движения газов атмосферное давление. Последний фактор не имеет значения для металлургического цеха однако здесь есть другой важный фактор – тепловое излучение. Санитарными нормами СН 245-71 установлены нормативы метеорологических условий производственных помещений. Так для участка конвертирования допустимое значение температуры воздуха 19 – 200С; относительная влажность воздуха – не более 75%; скорость движения воздуха – не более 05 мс.
1.5. Расчет искусственного освещения при использовании светильников с лампами накаливания
В качестве источника света используем лампы накаливания типа Г220-500-1 со световым потоком 8300 лм.
Рассчитаем освещение в помещении участка конвертирования. Характер зрительной работы грубый (разряд VI) поэтому норма освещенности для данного вида работ составляет EH =100 лк.
При высоте помещения 9м и высоте рабочей поверхности над полом hp=08м величине подвески светильников hc=05 м расчетная величина подвеса светильников над освещаемой поверхностью: Hp=H-hp-hc=77 м
Рассчитаем индекс помещения по формуле:
где А и В – соответственно длина и ширина помещения А = 80 м В = 54 м.
i = (80*54)7.7*(80+54)=418
Коэффициент отражения потолка стен рабочих поверхностей ρп=50%; ρс=30%; ρр=10%. Коэффициент использования светового потока равен =52%. Тогда число лапм можно вычислить по формуле:
где Кз – коэффициент запаса учитывающий загрязнение светильника в ходе эксплуатации (Кз = 17);
S – площадь помещения;
z – поправочный коэффициент учитывающий неравномерность освещения (z = 115).
N=(100*1.7*80*54*115)(8300*0.52)=192 лампы
Таким образом для создания на рабочей поверхности освещенности 100 лк необходимо установить 192 лампы Г220-500-1 (96 светильников У-15 по 2 лампы).
Лампы располагаются в 3 ряда по центральной продольной оси участка вдоль стен расстояние между рядами 17 м; расстояние между лампами 90 см; расстояние между торцевой стенкой и лампой 3 м расстояние между светильниками 2 м.
Рассчитаем общую мощность осветительной установки:
Для светильников типа У-15 при площади помещения S=4320м2 высоте подвеса 77 и освещенности 50 лк находим w= 10.2 Втм2.
Рассчитаем необходимую удельную мощность для создания нормальной освещенности:
Мощность осветительной установки:
Рл=204*4320=8813 кВт
1.6. Пожарная безопасность
Пожары на производстве представляют опасность для работающих причиняя значительные повреждения и материальный ущерб могут вызвать остановку работы.
Причины возникновения пожаров:
недостатки в строительных конструкциях сооружениях;
недостатки в планировке помещений;
недостатки в устройстве коммуникаций;
дефекты оборудования;
нарушения режимов технологических процессов;
неправильное проведение работ неосторожность и небрежность персонала.
Согласно нормам СН 245-71 участок конвертирования по оценке пожарной безопасности относится к категории «Г» а здания – к первой категории огнестойкости.
Для предупреждения и локализации пожаров производится комплекс организационных и технических мероприятий:
установка пунктов с противопожарными инструментами и ящиками с песком;
монтаж электрической пожарной сигнализации;
наличие пенных огнетушителей ОХП-10;
наличие пожарного водопровода находящегося под давлением и гидратов расположенных в местах определяемых инструкцией по пожарной безопасности;
пожарные рукава должны храниться сложенными непосредственно у выводных труб пожарного водопровода;
наличие и исправное состояние пожарных лестниц;
обеспечение свободных проходов к средствам пожаротушения и инвентарю а также к средствам пожарной сигнализации;
противопожарный водопровод должен быть объединен с хозяйственным и производственным водопроводами.
Для обеспечения бесперебойной подачи воды при разрыве водопровода сети пожарных водопроводов делают кольцевыми с диаметром труб наружного водопровода не менее 100 мм. Пожарные краны устанавливают на высоте 135 м от уровня пола внутри помещений у выходов.
2. Безопасность жизнедеятельности при чрезвычайных ситуациях
2.1. Анализ потенциально-возможных чрезвычайных ситуаций
Наибольшую опасность на участке конвертирования представляют: сернистый газ оксиды металлов и пыль. При проникновении в помещение сернистый газ раздражающе действует на слизистые оболочки глаз и верхних дыхательных путей человека. Причиной аварийной ситуации может быть нарушение герметичности конвертаров газоходных систем и недостаточной тяги в них.
Пожар может возникнуть по халатности обслуживающего персонала (курение применение открытого огня) что является нарушением техники безопасности.
Во избежание таких ситуаций применяется герметизация оборудования местная и усиленная обменная вентиляция. Персонал должен быть ознакомлен с вопросами безопасности во всем объеме и каждый работающий должен иметь соответствующий костюм рукавицы и противогаз.
2.2. План предупреждения и ликвидации чрезвычайной ситуации
План ликвидации аварий – официальный документ определяющий мероприятия и действия ответственных лиц по спасению людей на начальной стадии ликвидации аварий.
План ликвидации аварии должен вводиться в действие главным инженером предприятия или лицом его заменяющим немедленно после аварии. План ликвидации пожара отображен в таблице 5.1.
План ликвидации пожара.
Мероприятия по спасению людей и ликвидации аварии
Вызвать пожарную часть
Отключить электроэнергию и подачу газа
Оповестить об аварии и вывести всех людей находящихся на участке
Сменные ИТР участков
Обеспечить подъезд пожарных машин
Направить членов энергомеханической службы с респираторами и огнетушителями в здание участка для вывода людей и тушения пожара
Анализ риска аварий дает возможность оценить степень опасности конвертерного производства для людей и окружающей среды состояние его промышленной безопасности и на основании полученной информации разработать рекомендации по улучшению состояния промышленной безопасности.
Выполнен анализ вредных и опасных факторов процесса конвертирования на производстве.
Проанализированы возможные чрезвычайные ситуации на производстве.
Описаны причины травматизма и профессиональных заболеваний с приведением статистических данных.
Изложена техника безопасности непосредственно на участке конвертирования – требования при работе непосредственно с конвертером а также требования при работе с системой газоудаления.
Приведены нормы для данного производства.
Рассчитано освещение в помещении участка конвертирования необходимое для наилучшей зрительной работы.
Представлено описание пожарной безопасности причина возникновения пожаров. Составлен план к их устранению.
ЭКОНОМИКА ПРОИЗВОДСТВА ОРГАНИЗАЦИЯ ТРУДА
Пятибригадный график сменности
Смена 1 с 0.00 до 8.00
Смена 2 с 8.00 до 16.00
Смена 3 с 16.00 до 24.00
Работа в праздничные дни подлежит оплате согласно ТК РФ ст. 153
Рабочее время за дополнительные смены подлежит оплате в одинарном размере
Оплата за смены и режим работы производится в следующем порядке:
за вечернюю смену – 20% за всю смену
ночная смена – 40% доплаты.
районный коэффициент – 80%
северный коэффициент – 80%
премиальные – 160 % (по заводским данным)
2. Количество рабочих и выходных дней в году
По приведенному графику количество рабочих дней составит:
где Ткал – календарное время сутки; tц – длительность цикла сутки; tрц – количество рабочих дней в цикле сутки.
tраб = 365915 = 219 дней.
Количество выходных дней:
tвых = 365 – 219 = 146 дней.
Количество часов работы за неделю:
где tр – число рабочих дней в цикле дни; g – длительность смены час; n – цикл графика дни.
tнед = 98715 = 336 часа.
Недоработка за неделю составит:
tнедораб(неделя) = 36 – 336 = 24 часа.
tнедораб(год) = 243657 = 1251 часа.
Количество дополнительных смен:
tдоп. смен = 12518 » 16 смен.
Дополнительные смены вводятся вместо выходных дней.
tвых = 146 – 16 = 130 дней.
Количество рабочих дней:
tраб = 219 + 16 = 235 дней.
Номинальный фонд рабочего времени равен 235 дней.Эффективный фонд рабочего времени равен: 235 – 28 – 10 – 24 – 5 – 2 = 166дней где 28 – основной отпуск по трудовому договору 10 – дополнительный отпуск за вредные условия труда 24 – дополнительный отпуск за работу в условиях крайнего севера 5 – дополнительны отпуск для прохождения профилакторно-санаторного лечения выделенный по соглашению с профсоюзом; 2 – отпуск по учёбе или декретный отпуск.
Тогда коэффициент списочного состава будет равен:
где Тном. – номинальный фонд рабочего времени в днях; Тэфф – эффективный фонд рабочего времени в днях.
Плановый баланс рабочего времени.
Календарный фонд времени
Номинальный фонд времени
Невыходы по уважительным причинам:
б) дополнительный отпуск за вредные условия труда
в) дополнительный отпуск за работу в условиях крайнего севера
г) дополнительны отпуск для прохождения профилакторно-санаторного лечения
Эффективный фонд времени
Коэффициент списочного состава
3. Расчет численности работников
Явочная численность конвертерщиков:
где N – количество работающего оборудования шт.; Нчо – норматив численности обслуживания равен 2 (учитывая бригадира).
Чясм = 2·2 = 4 человека.
Суточная численность составит:
где с – количество смен в сутках с = 3.
Чя = 4 · 3 = 12 человек.
Штатная численность конвертерщиков:
Чшт = Чясм · (с + п)
где п – число подменных бригад.
Чшт = 4 · (3 + 2) = 20 человек.
Списочная численность конвертерщиков:
Чсп = Чшт · Ксп = 20 · 142 = 28 человека
Списочная численность стропальщиков:
Чсп = Чясм · (с+п.) · Ксп = 2 · 5 · 142 = 14 человек
Списочная численность машинистов крана:
Списочная численность разливщиков:
Списочная численность машинистов электровоза:
Чсп = Чясм · (с+п.) · Ксп = 1 · 5 · 142 = 7 человек.
Дежурный персонал работает по тому же графику что и основные рабочие. Ремонтный персонал работает 5 дней в неделю с выходными в субботу и воскресенье и праздничные дни.
Дежурный слесарь ремонтник:
Дежурный электросварщик:
Дежурный электромонтер:
В таблице 6.3. представлены результаты расчета численности рабочих трудящихся посменно.
Суточная численность
Списочная численность
Машинист электровоза
Дежурный слесарь ремонтник
Дежурный электросварщик
Дежурный электромонтер
Численность РСС принимаю аналогично заводу – аналогу.
Списочная численность основных и вспомогательных рабочих.
Вспомогательные рабочие (дежурные)
Вспомогательные рабочие (ремонтные)
Вспомогательный персонал
Списочная численность РСС
4. Обоснование доплат
Доплаты за ночное вечернее и праздничное время:
Оплата за работу в ночную смену – 40% часовой тарифной ставки за каждый час работы за работу в вечернюю смену – 20%. Оплата выходных и праздничных – двойной тариф за отработанные часы.
Ночное время Кд = (8 24) · 40 = 1333 %.
Вечернее время Кд = (8 24) · 20 = 666 %.
Праздничные дни Кд = 12 365 · 100 = 33 %.
Доплаты за отпуск и прочие статьи:
Доплаты за основной и дополнительный отпуск Кд = 67 166 · 100 = 4036%.
Доплаты за прочие статьи Кд = 2 166 · 100 = 120%.
Премиальный фонд составляет 160% (рабочим) и 120 % (РСС) от тарифного фонда.
Районный и северный коэффициенты в сумме составляют 160 %.
Результаты расчета заработной платы сведены в таблицу 18. Фонд заработной платы РСС приведен в таблице 19.
Расчет планового фонда заработной платы рабочих
Тарифный фонд тыс. руб.
Всего с районным и северным коэф. (16)
Фонд допол. зарплаты
Годовой фонд заработной платы тыс. руб.
Ночное вечернее (20%)
Фонд заработной платы РСС.
Районный и северный коэф.
Годовой фонд зарплаты
Сводная таблица заработной платы.
Категория трудящихся
5. Расчет затрат на производство продукции
Целью данного раздела является определение общих затрат на производство и оценка себестоимости единицы продукции.Планирование расхода сырья материалов и энергетических затрат производится на основе нормативно-балансового метода планирование оплаты труда и комплексных статей – на основе сметного.В калькуляции планирование сырья проводится на основе материального баланса и рассчитанных на его основе расходных коэффициентах.Планирование вспомогательных материалов на технологические цели основано на нормах расхода ресурса на единицу продукции.Смета расходов на содержание и эксплуатацию оборудования представлена в таблице 6.9. Смета цеховых расходов – в таблице 6.10.
Смета расходов на содержание и эксплуатацию оборудования (РСЭО)
Амортизация основного оборудования
Амортизация силового оборудования
Амортизация транспорта
Амортизация инструментов и инвентаря
Содержание оборудования и транспортных средств
Ремонт оборудования и транспортных средств (5 % от стоимости оборудования и транспортных средств)
Износ инвентаря (10 % от стоимости инвентаря оборудования и транспортных средств )
Внутрицеховое перемещение грузов (2 % от стоимости транспортных средств)
Прочие расходы (7 % от суммы учтенных расходов)
Смета цеховых расходов
Заработная плата РСС
Взносы на обязательное социальное страхование (30%)
Амортизация пассивной части основных средств
Содержание зданий сооружений передаточных устройств (15% от стоимости )
Ремонт зданий сооружений передаточных устройств и инвентаря (25% от стоимости )
Расходы на испытания опыты исследования содержание лабораторий (2% от общего фонда заработной платы )
Охрана труда и техника безопасности (45% от фонда заработной платы рабочих )
Прочие расходы (75% от суммы учтенных расходов )
Составляем калькуляцию себестоимости черновой меди (таблица 6.11).
Общехозяйственные расходы принимаем 10% от цеховой стоимости. Коммерческие расходы принимаем 5% от производственной стоимости.
Калькуляция себестоимости черновой меди
На единицу (1т черновой Cu)
На годовой выпуск черновой Cu
Сырье и основные материалы:
Энергетические затраты:
Эл. энергия тыс.кВтч
Единый социальный налог
Общехозяйственные расходы
Итого производственная сс
Коммерческие расходы
Полная себестоимость
* – цена сырья определяется себестоимостью предшествующих переделов и содержанием ценных компонентов; цена возвратов определяется содержанием ценных компонентов и затратами на их извлечение.
Проведенные расчеты показывают что себестоимость одной тонны черновой меди составляет 8526814 рублей. Соответственно на годовой выпуск эта величина – 238750782 рублей.
6. Расчет финансовых результатов проекта
К финансовым результатам относятся товарная продукция и прибыль предприятия.
Расчет товарной продукции проводится по формуле:
где Цi – цена i-го вида продукции (принимаем цену 1т черновой меди 87000руб.) Вi – выпуск i-го вида.
ТП = 87000 280000 = 24360000 тыс.руб.
где Сгод – годовая себестоимость продукции
П вал = (87000 – 8526814) 280000 = 4849208тыс.руб.
Пчист = Пвал – (Пвал – Нм – Л) Кн
где Нм – местные налоги Л – льготы по налогу на прибыль Кн – ставка налога на прибыль.
налог на имущество (2% от Фн 22520031 руб. (производственные фонды)) 225200308 002 = 4504006 руб.
Прибыль после уплаты налогов
4920800 – 4504006 = 480416794 руб.
Налог на прибыль (24%) и составляет 480416794 024 = 1153000306руб.
Пчист = 480416794– 1153000306= 3651167634 руб. = 36511676тыс. руб.
7. Расчет показателей эффективности проекта
К таким показателям относятся: технические и экономические показатели эффективности использования отдельных ресурсов (извлечение фондоотдача производительность труда и т.д.) и показатели эффективности работы предприятия в целом (рентабельность).
Фондоотдача Fо = BСос или Fо = ТП Сос где
Сос – стоимость основных средств.
Fо = 280000000225200308 = 124 кгруб или
Fо = 24360000000225200308 = 10817рубруб.
Производительность труда ПТ = ВЧППП
где ЧППП – численность.
ПТ = 280000122 = 229508 тчел. или ПТ = 24360000122 = 19967213 тыс. руб.чел
Рентабельность продукции Рп = Пвал Сгод100%.
Рп = 484920823861210100% = 203%.
Рентабельность продаж Рпр = Пвал ТП100%.
Рпр = 4849208 24360000 100% = 199%.
Рентабельность производства
где Собс – стоимость оборотных средств (15-30% от основных средств).
Рп-ва = 4849208 (22520031 + 03022520031) 100% = 16564 %.
Показатели эффективности проекта
Выпуск черновой меди т
Товарная продукция тыс. руб
Численность работников чел
Среднемесячная зарплата одного
Производительность труда тыс.руб чел
Стоимость основных средств тыс. руб.
Себестоимость 1т руб
Себестоимость годового выпуска тыс. руб
Прибыль от реализации продукции тыс. руб.
Рентабельность продукции %
Рентабельность производства %
Вывод: Проведенные расчеты подтвердили эффективность внедряемого мероприятия. Рентабельность продукции составила 203%. Рентабельность продаж составила 199%. Рентабельность производства 16564 %.
Приведены статьи расчёта материального и теплового баланса. Обоснована трехуровневая иерархическая структура системы автоматического управления горизонтального конвертера. Описана математическая модель электротехническая часть безопасность жизнидеятельности и экономика предприятия.
СПИСОК ИСПОЛЬЗОВАННОЙ ЛИТЕРАТУРЫ
Айзерман М.А. Лекции по теории автоматического управления М. 1960
Альтшуль А.Д. и др. Гидравлика и аэродинамика М.: Стройиздат 1987
Анашкин А.С. «Расчет материального баланса процесса конвертирования медно-никелевых штейнов в плавильном цехе ГМК "Печенганикель"» Отчет по НИРС каф. ПКАМП СПбГГИ 1997
Анашкин А.С Власов К.П. Гальнбек А.А. «Оптимальное управление газовым
режимом конвертеров» Сборник трудов МИСиС 2000 г.
Анашкин А.С Власов К.П. Гальнбек А.А. Чумаков Ю.А. «Система оптимального
управления газовым режимом конвертерного отделения плавильного
цеха комбината «Печенганикель» «Цветные металлы» Ш 8 2001 г.
Анхимюк В.Л. Теория автоматического управления М.: "Высшая школа" 1968
Баранов В.Я. и др. Промышленные приборы и средства автоматизации. Справочник. Л-д. "Машиностроение" 1987 г
Беленький A.M. Автоматическое управление металлургическими процессами М.: "Металлургия" 1989
Белый Н.В. Власов К.П. Клепиков В.Б. Основы научных исследований и технического творчества. Харьков: Высшая школа 1986
Бесекерский В.А. Микропроцессорные системы автоматического управления. Машиностроение Л-д 1988
Бесекерский В.А. Попов Е.П. Теория систем автоматического регулирования. М.: Наука 1975
Бир С. Кибернетика и управление производством. М. 1965
Бутковский А.Г. Оптимальное управление нагревом металла М.: "Металлургия" 1972
Вартовский М. Модели. Репрезентация и научное понимание. М. 1988
Власов К.П. и др. Микропроцессоры в системах управления процессами обогащения. М.: Недра 1992
Власов К.П. Методы научных исследований и организации эксперимента. Изд-во СПГГИ 2000
Власов К.П. Анашкин A.C. Теория автоматического управления: специальные методы изд-во СПГГИ 2001
Вычислительная техника и программирование под редакцией проф. A.B. Петрова М. Высшая школа 1990г
Галактионов А.И. Основы инженерно-психологического проектирования АСУТП. М. 1987
Гальнбек A.A. Водовоздушное хозяйство металлургических заводов. ЛГИ 1974
Гальнбек A.A. Гидроаэромеханика в металлургическом производстве ЛГИ. 1991
Гальнбек A.A. и др. Расчеты пирометаллургических процессов и аппаратуры
цветной металлургии Челябинск Металлургия 1990 г.
Гальнбек A.A. Непрерывное конвертирование штейнов М. Металлургия 1993
Гейлер Л.Б. Введение в теорию автоматического управления Минск "Наука и техника" 1967
Глинков Г.М. Климовицкий М.Д. Теоретические основы автоматического управления металлургическими процессами. М.: Металлургия. 1985
Голубь АП. Кузнецов Б.И. и др. Системы управления электроприводами Киев УМК ВО 1992
Гольдфарб Л.С. Теория автоматического управления М. "Высшая школа" 1969
Гречко A.B. и др. Новое в технологии и аппаратуре конвертирования штейнов. М.: ЦНИИцветмет экономики и информации. 1987
Губанов В.А. Введение в системный анализ ЛГУ 1988
Гузенко А.И. Основы теории автоматического управления М.: "Высшая школа" 1967
Джонсон P.E. и др. Обзор мировой практики использования конвертеров в производстве меди М.: ЦНИИцветмет экономики и информации. 1989
Джордж Ф. Основы кибернетики М.: "Радио и связь" 1975
Диомидовский Д.А. Металлургические печи цветной металлургии. М. Металлургия. 1970
Диомидовский Д.А. Шалыгин Л.М. Гальнбек A.A. Южанинов И.А. Расчеты
пиропроцессов и печей цветной металлургии М. "Металлургия" 1963
Емельянов СВ. Системы автоматического управления с переменной структурой М.:"Наука" 1967
Жуховицкий A.A. Физико-химические основы металлургических процессов
М.: "Металлургия" 1973
Жуховицкий A.A. Физическая химия М. "Металлургия" 1976
Зельченко В.Я. Расчет и проектирование АСУ с нелинейными динамическими
звеньями Л-д "Машиностроение" 1977
Зубов В.Н. Математические методы исследования систем автоматического
регулирования Судпромгиз 1959
Исаченко В.П. Теплопередача М.: "Энергия" 1969
Калман Р. Очерки по математической теории систем М.: "Мир" 1990
Каслей Г.Е. и др. Детальный анализ конвертерных операций с целью улучшения
производительности конвертеров завода Маунт Айза. М.: ЦНИИ-
цветмет экономики и информации. 1989
Каталог частотных преобразователей производства корпорации Триол 2000
Кожеуров В.А. Статстическая термодинамика М.: "Металлургия" 1975
Козлов В.Н. Вьиислительные методы синтеза систем автоматического
Колесников А.А. Последовательная оптимизация нелинейных автоматических
систем управления М.: "Энергоатомиздат" 1989
Колмогоров А.Н. Элементы теории функций и функционального анализа М.: "Наука" 1987
Костенко М.П. Пиотровский Л.М. Электрические машины М. «Энергия» 1965
Котов К.И. Промышленные системы автоматизации металлургических агрегатов.
Краткий справочник физико-химических величин под редакцией А.А. Равделя и Н.М. Пономаревой Л-д "Химия" 1983 г
Краткий технический справочник под редакцией проф. Зиновьева. Москва -
Ленинград Гос. издательство технико - теоретической литературы 1949 г
Кругов В.И. Основы теории автоматического регулирования М.: "Машиностроение" 1984
Куфнер А. Нелинейные дифференциальные уравнения М.: "Наука" 1988
Ли Э и др. Основы теории оптимального управления М.: "Наука" 1982
Лисиенко В.Г. Улучшение топливоиспользования и управление теплообменом
в металлургических печах М.: "Металлургия" 1988
Рекомендуемые чертежи
- 17.04.2022
- 04.11.2022
- 24.01.2023
Свободное скачивание на сегодня
Обновление через: 13 часов 9 минут