Автогрейдер для профилировочных работ (МЗР) Курсовой проект





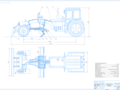
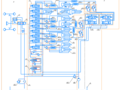
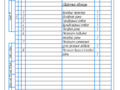
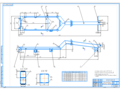
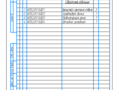
- Добавлен: 06.12.2022
- Размер: 5 MB
- Закачек: 2
Описание
Содержание
1. Требования к машине (по ГОСТ)
2. Выбор и обоснование типа рабочего оборудования, хода, привода и системы управления
3. Описание схем привода рабочего оборудования
4. Описание устройства, принципа действия машины и технологии производства работ
5. Расчетная часть:
5.1. Определение параметров рабочего оборудования и мощности двигателя
5.2. Выбор базовой машины
5.3. Расчет устойчивости
5.4. Расчет сопротивлений при работе машины
5.5. Определение нагрузок на рабочее оборудование
5.6. Прочностной расчет
5.7. Расчет привода рабочего оборудования
5.8. Технико-экономический расчет
6. Автоматизация рабочего процесса
Заключение
Литература
Состав проекта
![]() |
![]() ![]() |
![]() ![]() ![]() ![]() |
![]() ![]() |
![]() ![]() ![]() |
![]() ![]() |
![]() ![]() ![]() ![]() |
![]() ![]() ![]() ![]() |
![]() ![]() |
![]() ![]() |
![]() ![]() ![]() ![]() |
![]() ![]() |
![]() ![]() ![]() ![]() |
![]() ![]() ![]() ![]() |
![]() ![]() ![]() ![]() |
![]() ![]() ![]() ![]() |
Дополнительная информация
гидравлическая схема.cdw

Схема гидравлическая
автогрейдера легкого типа
Гидроусилитель сцепления
Гидроусилитель тормозов
Гидрозамок двусторонний системы
управления рабочим органом
Клапан предохранительный
Гидроцилиндр поворота отвала
Гидрораспределитель рулевого
Гидроцилиндр подъема и опускания
Гидроцилиндр наклона колес
Гидроцилиндр выноса тяговой рамы
Гидроцилиндр дополнительного
Гидроцилиндр изменения угла
Гидроцилиндр поворота тяговой
ИТОГОВЫЙ КУРСАЧ.docx
Федеральное государственное бюджетное образовательное учреждение высшего образования
«Санкт-Петербургский государственный архитектурно-строительный университет»
Наземные транспортно-технологические
Машины для землеройных работ
Автогрейдер для профилировочных работ
Дубовицкий Владислав Алексеевич
Направление подготовки (специальность):
Наземные транспортно-
технологические средства
Репин Сергей Васильевич
СПбГАСУ кафедра НТТМ 2021-2022 г.
Студент IV курса АДФ Дубовицкий Владислав Алексеевич
Задание на курсовой проект по дисциплине "МАШИНЫ ДЛЯ ЗЕМЛЕРОЙНЫХ РАБОТ
Состав проекта Кол-во листов
Чертежи (формат А1);
- вид общий (две проекции) 10
Требования к машине (по ГОСТ)
- схемы привода (гидравлическая) 10
Выбор и обоснование типа рабочего оборудования
- рассчитываемая деталь 05 - 10
хода привода и системы управления
Пояснительная записка (формат А4) 35 - 40
Описание схем привода рабочего оборудования
Описание устройства принципа действия машины
Стадии проекта Сроки выполнения
и технологии производства работ
Выбор базовой машины 30.09
Расчетная часть 20-27.10
1. Определение параметров рабочего оборудования
и мощности двигателя
2. Выбор базовой машины
3. Расчет устойчивости
Дата защиты проекта 10-15.12
4. Расчет сопротивлений при работе машины
5. Определение нагрузок на рабочее оборудование
Руководитель проекта д.т.н. профессор Репин С.В.
6. Прочностной расчет
7. Расчет привода рабочего оборудования
Дата выдачи задания на КП
8. Технико-экономический расчет
Автоматизация рабочего процесса
Обоснование технико-эксплуатационных требований к автогрейдерам по ГОСТ 11030-20176
Выбор и обоснование типа рабочего оборудованияхода привода и системы управления13
Описание схемы привода рабочего оборудования16
Описание устройства принципа действия машины19
и технологии производства работ19
1. Определение параметров рабочего оборудования и мощности двигателя25
2 Выбор базовой машины28
5 Определение нагрузок на рабочее оборудование38
6 Прочностной расчет39
7 Расчет привода рабочего оборудования55
8 Технико-экономический расчет58
Автоматизация рабочего процесса65
Список использованной литературы70
Автогрейдер- самоходная колесная машина с регулируемым отвалом расположенным между передними и задними колесами которая режет перемещает и распределяет материал обычно в целях профилирования. Используется преимущественно при дорожных работах например для вырезания кюветов и профилирования поверхности (т.е. разравнивания поверхности) создания необходимых поперечных и продольных уклонов и для срезания старого дорожного полотна. Также в область применения автогрейдеров входят возведение площадок насыпей и даже уборка от снега.
Данные виды работ автогрейдер выполняет с помощью своего основного рабочего органа - отвала с ножом встроенным в раму. В зависимости от специфики выполняемых работ рабочий орган может выполнять повороты по горизонтали и вертикали подниматься и опускаться а также выносить отвал в сторону.
Автогрейдеры являются высокоэффективными землеройными машинами. Инновационное совершенствование автогрейдеров связано с развитием перспективных тенденций машиностроения: широкое использование в структуре привода машин гидроэлектрических микропроцессорных систем управления компьютеризации и интеллектуализации машин гибридизации создания многоцелевой техники и машин с безотходной технологией обеспечения высокого уровня комфорта и безопасности оператора повышения надежности техники обеспечения эффективного сервиса и оптимизации параметров автогрейдеров. Использование достижений фундаментальных наук: нанотехнологических материалов газовой и гидродинамики ультра- и инфраколебаний СВЧ и др. является перспективным резервом повышения эффективности. Проблемы создания эффективной грейдерной техники на основе реализации инновационных программ решаются в комплексе с обеспечением повышения уровня ее эксплуатационной надежности. На этапе производственной эксплуатации важно чтобы автогрейдеры соответствующего типоразмера эксплуатировалась в условиях в которых они дают наибольший эффект. На этапе технического сервиса важно сократить до минимума непроизводственные простои машин.
Обоснование технико-эксплуатационных требований к автогрейдерам по ГОСТ 11030-2017
Производство автогрейдеров в России регламентируется двумя государственными стандартами: ГОСТ 27535–87 (ISO 7134:1985) и ГОСТ 11030–93.
1.2. Климатические исполнения и категории размещения автогрейдеров по ГОСТ 15150.
1.3. Конструкция автогрейдеров в течение срока службы должна обеспечивать работоспособность их при соблюдении потребителем правил эксплуатации.
1.4. Конструкция автогрейдеров должна обеспечивать:
- планирование и профилирование земляного полотна с кюветами глубиной не менее 05 м и наклоном внутренних стенок от 1:2 до 1:3 наружных от 1:1 до 1:15 а также с откосами крутизной от 1:15 до 1:4 на насыпи высотой до 25 м;
- агрегатирование с дополнительным оборудованием перечень которого установленный по требованию потребителя должен быть приведен в технических условиях на автогрейдеры конкретных моделей;
- устойчивость в поперечной плоскости до 035 рад (20°) к горизонтали при вырезании кювета;
-установку на пульте управления приборов дающих оператору информацию о давлении и температуре в системе гидротрансмиссии;
- установкусчетчика наработки автогрейдера;
- контрольуровня топлива в баках;
- возможность установки устройства для запуска двигателя при отрицательныхтемпературах;
- буксировку и строповку автогрейдера для подъема краном; наработку без дозаправки топливом не менее 9 моточасов работ (18 ч сменного времени);
- диагностирование в соответствии с требованиямиГОСТ 27518ГОСТ 25044 при этом конкретные требования по приспособленности к диагностированию и уровню автоматизации процессов диагностирования должны быть установлены в технических условиях на автогрейдеры конкретных моделей;
- оборудование необходимых мест ввода портативных приборов и приспособлений для диагностической проверки технического состояния.
При этом перечень приборов и приспособлений устанавливают в технических условиях в соответствии сГОСТ 27253и требованиями заказчика.
Присоединительные места для подключения диагностических приборов к гидросистемам должны соответствовать требованиям приложения1.
1.5. В конструкции автогрейдера по согласованию с потребителем (заказчиком) рекомендуется: устанавливать систему автоматической стабилизации положения отвала обеспечивающую при высококвалифицированном управлении автогрейдером выполнение планировочных и профилировочных работ с оценкой "на отлично" - поСНиП 3.06.03-85;
- предусматривать возможность зачистки откосов с углом 156 рад (90°) при угле захвата в плоскости откоса не менее 078 рад (45°).
1.6. Требования к конструкции гидропривода автогрейдера поГОСТ 17411(кромеп.2.2).
1.6.1. Гидроприводы и гидроустройства должны функционировать с сохранением заданных параметров после испытания статическим давлением не менее 15 номинального.
1.7. Размеры наливных горловин топливных баков - поГОСТ 27533.
1.8. Спускные наливные и контрольные пробки - поГОСТ 27720.
Примечание. Допускается по согласованию с заказчиком применение на комплектующих изделиях покупаемых в других отраслях пробок с размерами соответствующими нормативно-технической документации этих отраслей.
1.9. Смазочные масленки-поГОСТ19853.
1.10. Ножи автогрейдеров - поГОСТ 28771. Для машин техническое задание на которые утверждено до введения в действие настоящего стандарта допускается применение ножей с радиусом закругления 280 мм.
1.11 Требования эргономики и безопасности - поГОСТ 12.2.011ГОСТ 27254ГОСТ 27257ГОСТ 27921ГОСТ 28769ГОСТ 12.1.012.
1.11.1. Шумовые характеристики автогрейдеров - поГОСТ 12.1.003.
1.11.2. Конструкция автогрейдера должна обеспечивать обзорность рабочих органов во всех технологических положениях кроме кирковщика заднего расположения.
1.11.3. Внешние световые приборы должны соответствоватьГОСТ 8769и обеспечивать необходимую освещенность при передвижении по дороге а также необходимую освещенность рабочей площадки в дополнение к ее общей освещенности. Допускается по согласованию с потребителем изменение расположения некоторых световых приборов если это обусловлено конструктивными особенностями автогрейдера и не нарушает безопасности движения.
1.11.4. Цвета сигнальные и знаки безопасности должны соответствоватьГОСТ12.4.026.
1.11.6. Способы приведения в действие и расположение основных органов управления должны соответствовать приведенным в табл.2.
Наименование органа управления
Управляющее воздействие оператора
Направление перемещения
Приведение в действие двумя руками
Вращение по часовой стрелке для поворота машины вправо против часовой стрелки - влево
Рычаг управления поворотом полурам*
Перемещение назад - для поворота машины вправо перемещение вперед - для поворота машины влево
Педаль управления рабочим тормозом
Перемещение нажатием вперед и (или) вниз при торможении
Рычаг стояночного тормоза
Правой или левой рукой
Тянущее движение при торможении
Рычаг подачи топлива
Перемещение вперед вверх параллельно плоскости продольной оси машины - для увеличения числа оборотов двигателя
Педаль подачи топлива*
Перемещение нажатием вперед и (или) вниз - для увеличения числа оборотов двигателя
Рычаги переключения передач
Направления перемещения относительно нейтрального положения должны обозначаться мнемосхемой
Перемещение вперед - для переднего хода
Нажатие на педаль передней частью ступни - для движения передним ходом нажатие на педаль каблуком - для движения назад
Рычаг поворота отвала
Перемещение вперед поворачивает отвал против часовой стрелки
Перемещение назад поворачивает отвал по часовой стрелке
Рычаг подъема отвала
Перемещение вперед или вниз вызывает опускание отвала назад или вверх - подъем отвала
Рычаг бокового выноса тяговой рамы
Перемещение вперед или влево вызывает вынос поворотного круга с отвалом влево
Рычаг наклона колес*
Перемещение вперед или влево вызывает наклон колес влево; назад или вправо - наклон колес вправо
Рычаг выдвижения отвала*
Перемещение вперед или влево вызывает выдвижение отвала влево; назад или вправо - выдвижение отвала вправо
Рычаг изменения угла резания отвала*
Перемещение вперед вызывает движение верхнего края отвала вперед; перемещение назад - движение верхнего края отвала назад
Рычаг управления кирковщиком рыхлителем и другими видами дополнительного оборудования
Перемещение вверх или назад вызывает подъем оборудования; вниз или вперед - опускание оборудования
1.11.7 Колеса заднего моста автогрейдера должны иметь защитные устройства. Если эти устройства используются для доступа то они не должны иметь острых кромок их поверхность не должна быть скользкой и они должны выдерживать вертикальную нагрузку не менее 1500 Н.
1.11.8 Вентилятор двигателя должен быть снабжен ограждением.
Ограждение должно быть достаточно прочным во избежание прогиба в сторону подвижных лопастей и должно обеспечивать защиту от случайного контакта машиниста с лопастями вентилятора.
1.11.9 При давлении в гидросистеме более 5 МПа и при температуре рабочей жидкости более 50°С рукава высокого давления расположенные в кабине в пределах 05 м от машиниста должны иметь защитные устройства обеспечивающие безопасность машиниста в случае их разрыва.
1.11.10 Конструкция системы доступа должна соответствовать требованиям нормативного документа государств проголосовавших за принятие настоящего стандарта* и обеспечивать безопасность подъема и входа оператора на рабочее место и обслуживание автогрейдера.
* В Российской Федерации действуетГОСТ Р ИСО 2867-2011"Машины землеройные. Системы доступа".
1.11.11 Системы ремня безопасности места их крепления должны соответствовать требованиям приложения Б.
1.11.12 Выпускная система должна обеспечивать гашение искр до выхода отработавших газов в атмосферу. Струя отработавших газов не должна быть направлена на оператора или горючие материалы.
В местах соединений прорыв газов и искр не допускается.
1.11.13 Звуковая сигнализация автогрейдеров должна соответствоватьГОСТ 12.2.011.
1.11.14 Уровень радиопомех - по нормативному документу государств проголосовавших за принятие настоящего стандарта**.
1.12 Требования технического обслуживания и ремонта
1.12.1 В конструкции автогрейдеров рекомендуется обеспечивать:
- техническое обслуживание двигателя шасси трансмиссии без демонтажа кабины;
- возможность агрегатного ремонта;
- применение систем групповой и картерной смазки. Допускается применение индивидуальной смазки (с предпочтительным применением долговременной смазки);
- ежесменное техническое обслуживание одним оператором при этом оперативная трудоемкость ежесменного технического обслуживания не более:
- 05 - для классов 100 и 140
- 07 - для класса 180
- 095 - для класса 250;
- удельная суммарная оперативная трудоемкость плановых технических обслуживаний чел.-чмоточас не более:
- 0070 - для классов 100140
- 0090 - для класса 180
- 0118 - для класса 250.
Выбор и обоснование типа рабочего оборудованияхода привода и системы управления
АвтогрейдерДЗ-201: : 1 - бульдозерный отвал; 2 - рама; 3 - механизм подвески; 4 - базовый тракторный модуль; 5 - грейдерный отвал; 6 - поворотный круг
Выбор и обоснование типа рабочего оборудования рассмотрим на примере автогрейдера ДЗ-201 рис. 1.
Основное рабочее оборудование автогрейдера – установленный на тяговой раме отвал (рис. 1).
Рабочее оборудование автогрейдера ДЗ-201: 1 – шкворень; 2 – несущая балка; 3 – опорный лист несущей балки; 4 – поворотный круг; 5 – нож; 6 – отвал; 7 – опора отвала; 8
– кронштейн поворотного круга; 9 – щека поворотного круга; 10 – гидроцилиндр изменения угла резания; 11 – гидроцилиндр выноса тяговой рамы; 12 – гидроцилиндры подъема-опускания отвала; 13 17 – кронштейны подвески; 14 – поршень-защелка; 15 – левый рычаг; 16 – тяга; 18 – правый рычаг; 19 – гидроцилиндры поворота отвала.
Отвал 6 коробчатого сечения со сменными ножами подвижно соединен с опорой 7 отвала в направляющие которой отвал входит своей задней стенкой. По этим направляющим отвал может смещаться в стороны с помощью гидроцилиндра выдвижения. Опора 7 отвала крепится к кронштейнам 8 поворотного круга 4 с помощью пальцев вокруг которых опора вместе с отвалом может поворачиваться для изменения угла резания отвала с помощью гидроцилиндра. Поворотный круг 4 с опорой 7 и отвалом 6 присоединяются к несущей балке 2 с помощью трех кронштейнов 10. В этих кронштейнах поворотный круг с опорой и отвалом имеют возможность поворота в горизонтальной плоскости. Поворот осуществляется двумя гидроцилиндрами поворота отвала штоки которых крепятся к щекам 9 поворотного круга а гильзы цилиндров – к несущей балке 2. В тяговой раме предусмотрена регулировка вертикального зазора между поворотным кругом и опорным листом 3 несущей балки с помощью прокладок 11. Вертикальный зазор должен составлять 15 2 мм. При износе пазов в поддерживающих отвал нижних направляющих опоры 7 более 4 мм необходимо в нижние пазы установить скобы 067.37.11.072. Подвеска тяговой рамы состоит из левого 34 15 и правого 18 рычагов которые установлены на двух кронштейнах 13 и 17 приваренных в средней части передней рамы автогрейдера. Крепление тяговой рамы к подвеске выполнено через посредство трех цилиндров гидросистемы автогрейдера. Два из них служат для подъема и опускания а один – для выноса тяговой рамы. Рычаги 15 и 18 соединенные тягой 16 синхронно перемещаются относительно рамы автогрейдера и фиксируются в одном из трех положений с
помощью пневматической поршень-защелки 14. Перемещение осуществляется цилиндрами подъема и опускания при опущенном на грунт отвале выполняющем роль упора. На рис. 2 показано основное рабочее положение подвески тяговой рамы.
Система управления автогрейдера ГС-10.08
Рулевое управление служит для управления поворотом передних колес автогрейдера. Рулевое управление работает как независимый контур имея с гидросистемой автогрейдера общий гидробак и фильтр (см. рис. 3). Давление в рулевом управлении автогрейдера создается шестеренным насосом НШ-10В-3-Л конструктивно входящим в состав двигателя. В автогрейдере давление создается насосом НШ-10Е входящим в состав редуктора привода насосов. Насосом рабочая жидкость нагнетается в гидроруль с помощью которого в зависимости от направления поворота рулевого колеса установленного на гидроруле жидкость направляется в один из гидроцилиндров. Шток гидроцилиндра действует на рычаг ступицы колеса усилие от которого через поперечную тягу переднего моста передается и на ступицу другого колеса. При этом колеса автогрейдера поворачиваются.
Описание схемы привода рабочего оборудования
Для подъема и опускания отвала служит гидроцилиндр гидросистемы автогрейдера. Схема гидросистемы приведена на рис. 3.
Гидросистема автогрейдера ГС-10.08: А1 – механизм рулевой; А2 – усилитель сцепления;– усилитель передних тормозов; А4 – калорифер; Б – гидробак; ЗМ – гидрозамок; КО – обратный клапан; Ц – гидроцилиндр; Р – распределитель;
Описание работы гидросистемы:
Гидравлическая система автогрейдера легкого типа устроена следующим образом: рабочая жидкость из гидравлического бака подается с помощью насоса через распределители к исполнительным органам.
Распределитель Р2 подает гидравлическую жидкость на рулевой механизм А1. Усилителями А2 иосуществляется управление гидроприводом сцепления и передним тормозным механизмом. От распределителя Р1 питаются следующие гидроцилиндры:
Контур А включает: гидронасос 1 напорную линию секции гидрораспределителя 2 для управления гидроцилиндрами 3 (подъема и опускания левой и правой сторон отвала) гидромотором 4 поворота отвала гидроцилиндрами 5 (может быть один гидроцилиндр) подъема и опускания дополнительного оборудования гидроцилиндром 6 выноса тяговой рамы гидроцилиндром 7 выноса отвала и гидроцилиндром 8 наклона передних колес; сливную линию фильтром 9 и перепускным клапаном 10; гидроусилители сцепления 11 и тормозов 12. Кроме того контур А может включать секции гидрораспределителя и гидроцилиндры с соответствующим оборудованием для управления углом резания (наклоном) отвала стопорением подвески тяговой рамы и самостоятельным подъемом рыхлителя (при установке его одновременно с бульдозерным отвалом) как например на автогрейдерах ДЗ-143.
Контур Б включает гидронасос 13 напорную линию два трехпозиционных гидрозолотника 14 с электрогидравлическим управлением четыре обратных клапана 15 на трубопроводах подсоединяющих гидрооборудование автоматической системы управления к гидроцилиндрам 3 подъема и опускания отвала сливной трубопровод присоединенный к сливной линии контура А до фильтра 9.
Контур В включает гидронасос 16 напорную линию к гидрораспределителю 17 рулевого управления а от него к гидроусилителю руля 18. Сливной трубопровод подводится к общей для всех контуров сливной линии.
В контурах А Б и В на напорных линиях предусмотрены предохранительные клапаны 19 сбрасывающие при необходимости рабочую жидкость в сливной трубопровод минуя все гидрооборудование (они настроены на давление порядка 6 10 МПа) а также гидрозамки 20 после гидрораспределителей.
На всасывающем участке трубопровода перед гидронасосом часто ставится запорный вентиль для предупреждения вытекания рабочей жидкости из гидробака при ремонтах в системе.
и технологии производства работ
Согласно заданию (масса машины 8 т – автогрейдер легкого типа с колесной формулой 1х2х2) выбираем полноприводной автогрейдер легкого класса ГС-10-08 на базе трактора МТЗ-92П.
Автогрейдер выполнен на базе трактора имеющего восьмискоростную коробку передач позволяющую всегда подобрать нужную скорость работы отвалом как вперед так и назад в зависимости от характера разрабатываемого грунта а предусмотренный в ней реверс-редуктор позволяет быстро изменять направление движения в противоположную сторону.
Основной рабочий орган грейдера – отвал длиной 2750 мм имеет углы резания от 40 до 60 градусов и угол поворота до 40 градусов в каждую сторону. Дополняют его щетка на задней навеске с шириной захвата 1800 мм производительностью до 21600 квадратных метров в час. Для бульдозерных работ предусмотрен двухметровый передний отвал с глубиной резания до 100 мм. Для снижения числа оборотов поворотной платформы до 1 обмин и хода до 035 кмч в двухскоростном редукторе поворотного механизма изменено передаточное отношение шестерен.
Ходовая часть автогрейдера состоит из двух ведущих мостов. Привод переднего моста – постоянный через карданный вал от раздаточной коробки.
Рассмотрим кинематическую схему на примере автогрейдера ГС-18.05
Кинематическая схема автогрейдера ГС-18.05 с двигателем ЯМЗ-236М2: 1 – двигатель; 2 – карданная передача; 3 – насос гидромеханической передачи; 4 – гидротрансформатор; 5 – коробка передач; 6 – стояночный тормоз; 7 – балансирная тележка; 8 – колесо; 9 – б
На автогрейдере устанавливаются шестицилиндровые дизельные двигатели А-01МС-3 или ЯМЗ-236М2 которые располагаются в задней части основной рамы. Гидромеханическая трансмиссия автогрейдера (рис. 4) состоит из сцепления (для двигателя А-01МС-3) или промежуточного редуктора 10 (для двигателя ЯМЗ-236М2) гидромеханической передачи (ГМП) стояночного тормоза 6 и карданной передачи 2 через которую происходит передача мощности от сцепления или промежуточного редуктора на гидротрансформатор 4 ГМП (верхний карданный вал) и от коробки передач 5 ГМП на балансирную тележку 7 (нижний карданный вал).
Ходовая часть включает в себя шарнирно-сочлененную раму и установленные на ней передний и задние мосты с колесами 8. Задние мосты представляют собой балансирную тележку с двумя балансирами 9 для крепления на каждом по два колеса. Все колеса установленные на балансирной тележке являются ведущими. Передний мост при помощи двух горизонтальных осей размещенных поперек моста в его середине соединяется с головкой рамы автогрейдера. Такое соединение обеспечивает возможность поворота моста в поперечной плоскости при движении по неровной дороге. Конструкция переднего моста позволяет осуществлять поворот передних колес а также их наклон что повышает устойчивость автогрейдера против заноса и уменьшает радиус его поворота. Кабина автогрейдера цельнометаллическая одноместная с круговым остеклением герметизированная снабжена системой отопления и вентиляции. Ее внутренние стенки облицованы декоративным покрытием. Полости между наружным каркасом и внутренней облицовкой заполнены теплоизоляционным материалом. Все соединения кабины герметизированы. Крепление кабины на раму выполнено с применением резиновых амортизаторов. Сиденье оператора подрессорено и может регулироваться по росту и массе оператора. В кабине установлена регулируемая рулевая колонка и отопитель работающий на разогретой жидкости системы охлаждения и разогрева двигателя. Рабочее оборудование. В состав рабочего оборудования автогрейдера входят тяговая рама с установленным на ней отвалом и подвеска тяговой рамы.
Рама автогрейдера ГС-10.08: 1 – передняя рама; 2 3 6 – кронштейны; 4 – головка рамы; 5 13 – крюки; 7 – передняя балка; 8 – левый прогон; 9 – левый лонжерон; 10 – труба; 11 – корма; 12 – аккумуляторный ящик; 14 – крышка; 15 – опора; 16 – правый прогон; 17 – правый лонжерон; 18 – задняя рама
Рама шарнирно-сочлененной конструкции служит для размещения и крепления на ней составных частей автогрейдера. Она состоит из передней рамы 1 (рис. 5) и задней рамы 18 шарнирно-сочлененных между собой. Шарнирное сочленение обеспечивает возможность поворота передней и задней рам относительно друг друга (складывания) в горизонтальной плоскости оно выполнено в двух местах – верхнем и нижнем шарнирах. Верхний шарнир не имеет опоры в вертикальной плоскости и воспринимает только горизонтальные радиальные усилия. Конструкция нижнего шарнира обеспечивает устранение вертикальных люфтов регулировочными прокладками. Это позволяет равномерно распределить вертикальные усилия воспринимаемые шарниром между его верхней и нижней плитами. Передняя рама является сварной металлоконструкцией выполненной из листов в виде балки коробчатого сечения. Головка 4 рамы служит для крепления переднего моста шкворня тяговой рамы дополнительного рабочего оборудования. На боковых листах головки рамы расположены два крюка 5. В средней части передней рамы приварены два кронштейна 3 и 6 для крепления подвески тяговой рамы. Кронштейны 2 служат для крепления штоков гидроцилиндров складывания рамы.
Задняя рама является сварной металлоконструкцией основу которой составляют два лонжерона 9 17 и связывающие их поперечно передняя балка 7 и корма 11. Через переднюю балку задняя рама соединяется шарнирно с передней рамой. Корма служит для крепления на ней рыхлительного оборудования. Для строповки автогрейдера на наружных стенках лонжеронов приварены крюки 13. На нижних полках лонжеронов расположены опоры 15 с крышками 14 для установки балансирной тележки автогрейдера. Труба 10 служит для связи лонжеронов между собой в месте установки балансирной тележки а также для удержания тележки в нужном положении. Оба лонжерона кроме своего прямого назначения используются в качестве ресиверов для пневмосистемы автогрейдера. При необходимости исключить возможность складывания рамы в отверстие передней балки 7 рядом с верхним шарниром сочленения рамы устанавливается шкворень. Для хранения шкворня на передней балке 7 под правым прогоном 16 приварена втулка. Смазывание шарниров сочленения рамы и шарниров гидроцилиндров складывания рамы производится через прессмасленки на осях шарниров.
Рабочий процесс грейдера схож с рабочим процессом бульдозера оборудованного поворотным в плане отвалом. Нижняя рабочая кромка ножа грейдерного отвала погружается в слой грунта гравия щебня асфальтобетонного или другого дорожного покрытия на нужную глубину. После этого отвал перемещает массу материала в направлении движения грейдера. Скорость движения грейдера при срезании грунта до 10 кмч при перемещении — до 30 кмч.
Грейдеры эффективны при длине рабочих участков более 500 метров. На коротких участках эффективность грейдеров снижается из-за увеличения числа разворотов машины и перестановок рабочего органа. При возведении насыпей из боковых резервов грейдеры эффективно применять при дальности перемещения грунта до 30 метров.
При работе грейдера важное значение имеет правильное положение отвала определяемое величиной угла захвата угла резания и угла наклона. Углы захвата и наклона грейдерного отвала могут изменяться в процессе движения грейдера а угол резания должен устанавливаться во время остановки грейдера.
Грейдеры (рис.6) предназначены для планировочных и профилировочных работ при строительстве дорог аэродромов и других линейных и площадных объектов. По трудности разработки грейдерами грунты подразделяют на I II и III группы. Грейдеры применимы в грунтах с отметкой выше уровня грунтовых вод и неработоспособны на заболоченных землях.
Рис.6 Конструкция и схемы работы грейдера:
а- вид сбоку;б- резание грунта;вд- планирование дорожного полотна откоса выемки;г- поворот отвала;1- рама;2- поворотный круг;3- тяговая рама;4- ось тяговой рамы;5- ось поворотного круга;6- отвал
1. Определение параметров рабочего оборудования и мощности двигателя
Мощность автогрейдера
Рис.6 График мощности
Длина отвала автогрейдера
Рис.7 График длины отвала
Высота отвала автогрейдера
Рис.8 График высоты отвала
2 Выбор базовой машины
Произведем расчет основных параметров автогрейдера
Общая масса автогрейдера Ga и сцепная масса Gсц связаны следующей зависимостью:
где – коэффициент равный единице в колесных формулах 3х3х3 1х3х3 2х2х2 и 07-075 при 1х2х2.
Вес машины Ga = 800098= 78400 H = 784 кН.
Далее определяем максимальную свободную силу тяги автогрейдера по сцепной массе:
Где – коэффициент сцепления с грунтом ;
Определим площадь стружки из равенства:
Kрез принимаем 25000 кгм3.
Число проходов за которые вырезают большие площади сечения корыта определяем из формулы:
Где – коэффициент учитывающий неравномерность сечения стружки при отдельных проходах. (;
площадь сечения корыта hк = 06 м (глубина копания)
Тогда определяем оптимальную массу машины:
)Мощность автогрейдера: y =00093*8000 - 15849 = 5855 кВт.
)Длина отвала автогрейдера: y = 01307*8000 + 1703 = 27486 мм;
)Ширина отвала автогрейдера: y =00195*8000 + 37822 = 53422 мм;
По рассчитанным параметрам выбираем серийно выпускаемый автогрейдер являющийся прототипом проектируемого на основе рассчитанной оптимальной массы мощности двигателя и размеров рабочего оборудования.
М = 7835 кг – масса автогрейдера;
N = 60 кВт – мощность автогрейдера;
L = 2750 мм – длина отвала;
H = 535 мм – ширина отвала.
Исходя из рассчитанных данных выбираем прототип автогрейдера ГС-10.08
Технические характеристики:
База автогрейдера мм
3 Расчет устойчивости автогрейдера
В процессе работы потеря устойчивости и опрокидывание автогрейдера могут произойти при его движении по наклонной поверхности и при повороте.
Автогрейдер – длиннобазная машина. Поэтому продольная его устойчивость к опрокидыванию гарантирована на уклонах являющихся предельными по условию сцепления движителя с дорогой.
Расчет продольной устойчивости
Рис.9 Схема определения устойчивости автогрейдера
Предельный угол подъема преодолеваемый автогрейдером по условию сцепления движителя с дорогой:
Для машин только с задними ведущими колесами
Где – координаты центра тяжести машины относительно точки контакта переднего колеса с дорогой (м). ; .
– коэффициент буксования:
L =5 м – база автогрейдера;
– коэффициент сцепления колёс с грунтом.
Тогда предельный угол подъёма .
Наибольший угол подъема преодолеваемый по условию реализации 100%-ной мощности двигателя находится из уравнения тягового баланса
Где N – мощность двигателя Вт; - к. п. д. трансмиссии и ходового оборудования автогрейдера; - сила тяжести автогрейдера Н; v - скорость движения автогрейдера мс.
Приняв что получим формулу
Предельный уклон по условию сцепления тормозных колес с грунтом
Расчет поперечной устойчивости
Поперечная устойчивость автогрейдера оценивается по условиям опрокидывания на наклонной поверхности (рис. 10а) либо при движении на закругленных участках дорог (рис. 10б) а также исходя из потери сцепления движителя с дорогой.
Допустимый угол поперечного уклона по условию опрокидывания определяется из выражения:
Где В = 18 м – колея машины; е = 0 - эксцентриситет центра тяжести относительно продольной оси машины; – высота центра тяжести.
Тогда допустимый угол поперечного уклона по условию опрокидывания будет равен
Допустимый угол поперечного уклона по условию сцепления движителя с дорогой находят с помощью равенства
Тогда допустимый угол поперечного уклона по сцепления движителя с дорогой будет равен
Коэффициент запаса устойчивости при движении на закруглениях дороги по условию опрокидывания:
Где – радиус закругления дороги; g – ускорение свободного падения мс2; v = 11 - скорость движения мс.
Отсюда найдём максимальную скорость движения:
Условие выполняется.
Коэффициент запаса поперечной устойчивости при движении на закруглениях дороги по условию сцепления движителя
Используя результаты расчётов в техническую характеристику автогрейдера вносят наименьшее из полученных предельных углов поперечной устойчивости. Таким образом предельный продольный уклон по условию сцепления тормозных колес с грунтом допустимый угол поперечного уклона по условию сцепления движителя с дорогой равен
4 Расчет сопротивлений при работе машины
Чтобы достичь максимальной производительности автогрейдера необходимо выполнить условие соответствия возникающим при работе машины сопротивлений её тяговым возможностям на данной передаче.
В общем случае сумма сопротивлений действующих на автогрейдер определяется равенством
Где - сопротивление перекатыванию автогрейдера с учетом уклона местности; - сопротивление резанию грунта; сопротивление трению грунтовой призмы о грунт; - – сопротивления возникающие от перемещения грунта вверх и вдоль по отвалу.
Составляющие суммарного сопротивления (W Н; V м3) рассчитываются по формулам
Где – сила тяжести автогрейдера Н; f = 005 - коэффициент сопротивления передвижению автогрейдера; удельное сопротивление резанию грунта кПа принимаемое с учетом угла резания; F - площадь поперечного сечения срезаемой стружки м2 ; объем призмы грунта перед отвалом м3 принимаемый в зависимости от выполняемой операции по данным табл. 4.1; объемная масса грунта в плотном теле кгм3; коэффициент разрыхления грунта; коэффициент трения грунта о грунт; коэффициент трения грунта о поверхность отвала; угол захвата; – угол резания; hср = 016 - средняя толщина стружки м; - угол естественного откоса грунта.
кгм3 (IV категория грунта);
Для нормального протекания процессов резания перемещения грунта или планирования поверхностей необходимыми являются условия
Где – номинальное значение силы тяги автогрейдера на используемой передаче;
- предельное значение тягового усилия по сцеплению с грунтом.
– коэффициент нагрузки ведущих колес автогрейдера
Условие соблюдается значит автогрейдер подходит для выбранных условий работ.
5 Определение нагрузок на рабочее оборудование
При механическом способе разработки грунта рабочий орган землеройной машины как правило представляет собой клин характеризуемый углом резания α заострения задним углом и углом заострения в плане (углом захвата γ. При резании наиболее распространенных связных грунтов первоначально происходит уплотнение сжимаемого пласта а затем сдвиг по плоскостям касательных напряжений расположенных под некоторым углом к горизонту. Деформированный пласт грунта перемещается под напором вновь поступающего по рабочей поверхности клина в отвал.
Рис. 11 Схема резания грунта клином
Рис. 12 Схема усилий действующих на косой клин грунта
6 Прочностной расчет
Расчёт основной рамы
Первое расчётное положение. В первом расчётном положении соответствующем нагрузкам возникающим в процессе нормальной эксплуатации автогрейдера наиболее неблагоприятные условия возникают в конце зарезания когда отвал режет грунт одним концом опущенным настолько что передний мост вывешен и упирается в край кювета задние колёса буксуют на месте работа производится на поперечном уклоне с углом λ = 16°.
В этих условиях основная рама оказывается максимально нагруженной нормальными нагрузками (рис.24). В центре тяжести автогрейдера сосредотачивается сила его веса и равнодействующая сил инерции которая раскладывается на составляющие так как автогрейдер работает на уклоне. Первая равная G cosλ действует перпендикулярно опорной поверхности а вторая G sinλ - параллельно ей.
Координаты Н(м) и l(м) центра тяжести современных автогрейдеров приблизительно определяют из соотношений:
где rс – статический радиус колеса rс = 093 rк = 093 . 06 = 056м
Рис. 13 - Схема сил действующих на автогрейдер в первом расчётном положении
В центре тяжести автогрейдера помимо его веса сосредотачивается равнодействующая инерционных сил
где Кд = 15 – коэффициент динамичности
max = 085 – максимальный коэффициент использования сцепного веса машины
G2 = 63 кН – сила тяжести автогрейдера приходящейся на задний мост
В точке О которой обозначен конец режущей кромки ножа отвала сосредотачиваются усилия Рх Рy и Рz возникающие в результате сопротивления грунта резанию.
В точках О’2 и О’’2 соответствующих проекциям середин балансиров на опорную поверхность действуют вертикальные реакции задних правых и левых колёс Z2п и Z2л свободные силы тяги X2п и X2л и боковые реакции Y2п и Y2л
Y2п = Y2л = 05G sinλ = 0.5 . 768 . sin 16° = 106 кН
В точке О3 в которой передний мост касается кювета возникает боковая реакция Y1
Составим систему уравнений равновесия:
X = 0: X2п + X2л + Ри – Р
Y = 0: Y2п + Y2л - G s
Z = 0: Z2п + Z2л – Gcosλ + Pz = 0;
Мy = 0: Pz L1 – Gcosλ
Мz = 0: (Y2п + Y2л)L1 + X2л b + Pи b2 + G s
Определим неизвестные силы и реакции Рx Pz Z2п и Z2л из уравнений равновесия используя систему уравнений:
Силы тяги правого и левого задних колёс могут быть выражены через вертикальные реакции
X2п = Z2п max = 226. 085= 192 кН
X2л = Z2л max = 257 . 085 = 218 кН
Рy = Y2п + Y2л - G sinλ + Y1 = 106+ 106 –768sin16° + 1023 = 1377кН
Далее необходимо найти усилия действующие в т. О4 – шаровом шарнире тяговой рамы служащем опорой для правой части основной рамы. Левой частью основная рама двумя точками соответствующими точкам О’2 и О’’2 опирается на задний мост а средней частью – на систему подвески тяговой рамы.
Считая детали подвески тяговой рамы расположенными в одной плоскости Q можно рассматривать пересечение этой плоскости с основной рамой как место заделки последней являющееся опасным расчётным сечением. Для упрощения расчёта принимают что тяги подвески находятся в вертикальной плоскости Q’ хотя в действительности плоскость Q в которой они расположены наклонена к вертикали под небольшим углом . Принятое допущение несколько увеличит получаемые значения усилий Z4 Y4 X4 действующих на шаровой шарнир и следовательно приведёт к увеличению запаса надёжности.
Рис. 14- Схема сил действующих на шаровой шарнир тяговой рамы в первом расчётном положении
Из уравнений моментов составленных относительно осей y’ и z’ лежащих в плоскости Q’ проходящей через точку О4 и перпендикулярной к оси О’4 О4 находим усилия Z4 и Y4
Усилие Х4 находим из уравнения X = 0 откуда Х4 = Р4 = 742 кН.
Определив все силовые факторы основной рамы в первом расчетном положении можно посчитать возникающие в ней напряжения.
На рис.26 показана схема нагружения основной рамы в первом расчетном положении. Пользуясь этой схемой определяем изгибающие моменты действующие в опасном сечении I-I.
Рис. 15 - Схема нагружения основной рамы в первом расчетном положении
Слева от сечения I-I (со стороны моста):
Справа от сечения I-I (со стороны переднего моста):
Необходимо выбрать поперечное сечение и определить его геометрические характеристики – моменты сопротивления и площадь поперечного сечения
Также следует выбрать материал и найти допускаемое напряжение. Допускаемое напряжение равно отношению предельного напряжения к коэффициенту запаса равному 11 15
Выбираем нестандартный профиль бруса с размерами поперечного сечения b1=160мм b2=180мм h1=200мм h2=240мм.
Площадь и моменты инерции прямоугольного поперечного сечения определяют:
Рис. 16 - Поперечное сечение
Полярный момент инерции прямоугольного сечения вычисляем:
где 1 и 2 – коэффициенты зависящие от отношения сторон прямоугольного сечения.
Выбираю материал – сталь 40Х с = 650МПа и рассчитываю допускаемое напряжение:
[] = прК3 [] = 65012 = 5417 МПа
Зная геометрические размеры сечения и его форму можно посчитать возникающие в нём максимальные напряжения :
где сум – суммарное напряжение от изгиба и растяжения-сжатия
– напряжение от кручения
где Мив Миг – суммарные изгибающие моменты в вертикальной и горизонтальной плоскостях Р – сжимающее усилие кН
Мкр – суммарный крутящий момент действующий на расчётное положение
Wy Wz Wp F – моменты сопротивления сечения изгибу и кручению и площадь этого сечения
Возникающие в опасном сечении I-I основной рамы напряжения от воздействия на него силовых факторов действующих слева и справа от сечения подсчитывают раздельно и принимают в расчёт наибольшее.
Для сечения I-I (со стороны заднего моста):
Тогда максимальное напряжение для сечения I-I со стороны заднего моста:
Для сечения I-I (со стороны переднего моста):
Тогда максимальное напряжение для сечения I-I со стороны переднего моста:
Максимальные напряжения со стороны переднего моста превышают допускаемое напряжение.
Для выполнения условий прочности увеличивают толщину стенки поперечного сечения или меняют материал на более прочный и в результате при b1=160мм b2=210мм h1=200мм h2=250мм получаем площадь и моменты инерции прямоугольного поперечного сечения:
Условие выполняется значит выбранное сечение удовлетворяет условиям прочности и может быть использовано в рабочем оборудовании.
Второе расчётное положение.
Во втором расчётном положении на автогрейдер действуют случайные нагрузки возникающие при встрече его с непреодолимым препятствием. Наиболее неблагоприятные условия при этом складываются когда наезд на препятствие происходит краем выдвинутого в сторону отвала при движении автогрейдера по горизонтальной поверхности на максимальной рабочей скорости с малым пробуксовыванием ведущих колёс что имеет место при работах по разравниванию и перемещению грунта.
При внезапной встрече конца отвала с жёстким препятствием происходит их соударение что приводит к возникновению дополнительной динамической нагрузки на основную раму.
При расчёте на прочность рабочего оборудования принимают что масса и жесткость препятствия во много раз превышает массу и жёсткость автогрейдера. Тогда дополнительную динамическую нагрузку на автогрейдер определяют только массой и жёсткостью последнего а также скоростью столкновения и подсчитывают:
где v – скорость автогрейдера в момент встречи с препятствием
Gсц – вес автогрейдера с оборудованием Gсц = 114286 Н
g – ускорение свободного падения
С – суммарная жёсткость автогрейдера
здесь С1 = 120кНм – жесткость металлоконструкции автогрейдера зависящая от величины сцепного веса
Нотв = 0535м – высота отвала
Lотв = 275 м – длина отвала
С2 = 2Сш = 2 . 45 = 90кНм – суммарная жёсткость передних колёс
На рис.28 показана схема сил действующих на автогрейдер во втором расчётном положении. В центре тяжести сосредотачиваются сила веса автогрейдера и дополнительная динамическая нагрузка. В точке О контакта отвала с препятствием действуют усилия Рх и Ру а Рz = 0 так как резание грунта не производится. В условных точках О2 и О3 действуют боковые усилия Y2 и Y1
Рис. 17 - Схема сил действующих на автогрейдер во втором расчётном положении
Возникающие вертикальные реакции на задний и передний мосты обозначены соответственно через Z2 и Z1. Эти реакции с учётом динамической нагрузки определяют из уравнений моментов составляемых относительно точек О2 и О3:
где G1 и G2 – соответственно силы тяжести приходящиеся на передний и задний мосты.
Размеры а1 = 05м; с’ = 087м; n’ = 09м снимаем с чертежа.
Остальные неизвестные силы определяем составляя следующие уравнения равновесия:
Y = 0: Y1 – Py – Y2 = 0;
X2п = X2л Y1 = Z1max
Решая эти уравнения относительно неизвестных членов находим
=(05*856*085(2*05+20)+34(05+1)-416*085*275)225=28кН
Py = Z1max - Y2 = 416 . 085 – 28= 74 кН
Рx = Z2max + Ри = 856 . 085 + 34 = 1068кН
Y1 = Z1max = 416 . 085 = 354 кН
В момент внезапной встречи с жёстким препятствием ведущие колёса автогрейдера начинают полностью пробуксовывать развивая суммарную силу тяги Х2
X2 = X2п + X2л = 368 + 368 = 736 кН
Рис. 18 - Схема сил действующих на шаровой шарнир тяговой рамы во втором расчётном положении
Пользуясь приведённой на рис.30 для второго расчётного положения схемой сил действующих на шаровой шарнир тяговой рамы определяем возникающие в этом шарнире усилия Х4 Y4 Z4:
X = 0: Х4 – Рx = 0 Х4 = Рx = 1068 кН
Рис. 19 - Схема нагружения основной рамы во втором расчётном положении
Схема нагружения основной рамы во втором расчётном положении на рис.9. Точка Е на схеме обозначена условная точка приложения динамической нагрузки от масс приходящихся на задние мосты. Координаты К для точки Е определяются из соотношения:
Точкой приложения суммарной силы тяги Х2 и реакции Z2 показана средняя точка О2 условной оси задних мостов. В такой же средней точке О1 оси переднего моста приложены реакция и динамическая нагрузка от масс приходящихся на передний мост.
Слева от сечения I-I (со стороны заднего моста):
Площадь и моменты инерции прямоугольного поперечного сечения составляют:
Допускаемое напряжение [] = 5417МПа
Профиль бруса выбираем с соответствующим первому расчётному положению. Зная геометрические размеры сечения и его форму можно подсчитать возникающие в нём максимальные напряжения:
где Мив Миг – суммарные изгибающие моменты в вертикальной и горизонтальной плоскостях
Р – сжимающее усилие кН
7 Расчет привода рабочего оборудования
Мощность насосов по удельной энергоемкости копания N (Вт) определяем в зависимости от коэффициента удельного сопротивления копанию К (Па).
k01– коэффициент удельного сопротивления копанию;
k01 = 400000 – для грунтов III категории
kр – коэффициент разрыхления грунта kр = 13;
kн – коэффициент наполнения ковша kн = 11;
tкоп – время копания;
коп – КПД системы поворота рукояти или ковша коп = 08;
пр – КПД использования мощности привода пр = 08;
q – объём ковша (q = 1 м3);
Lц – ход поршня (принимаем по ГОСТ)
Подставим эти данные определим мощность необходимую при копании грунтов III категории.
Находим мощность привода насоса.
tкоп= 03· tц = 555 с
N = (k01·q· kн) (tкоп· kp·коп· пр) = 106 014 Вт
Исходя из необходимой мощности выбираем двигатель ЯМЗ-236Д4 мощностью 169 кВт.
Рабочий объем гидроцилиндра поворота рукояти определим по формуле:
qц = (k01·q·kн)(p· tкоп· kp·коп·пр) = 516 10-3 м3
Принимаем по ГОСТ 22-1417-79 ближайший больший диаметр цилиндра:
Dц = 012 м = 120 мм
Определим далее необходимую подачу насоса для обеспечения потребного времени копания:
Q = qцtкоп = 000092м3c
Необходимая подача насоса Q составляет 000092м3с (552 лмин). Принимаем по передаваемой мощности и подаче нерегулируемый аксиально-поршневой насос марки 210-20 с характеристиками:
рабочий объем 548 см3об;
давление номинальное – 16 МПа; максимальное – 25 МПа;
Частота вращения 1800 обмин.
Окончательно приняты следующие диаметры цилиндров:
D = 120 мм d = 72 мм.
Условие прочности стенок цилиндра определяется по формуле Ламе:
где рmax = 20 МПа — максимальное давление (давление срабатывания предохранительного клапана) в гидросистеме равное (12 13)рном.
Из условия прочности определяется допустимая минимальная толщина min (м) стенки силового цилиндра:
где [р] – допускаемое напряжение материала цилиндра при растяжении по на продольный разрыв под действием внутреннего давления для стального литья принимается равным 30 35% временного сопротивления в
т.е.(03 035)*550*106=(165 195)*106Па; – коэффициент Пуассона для стали – 029.
К найденной по формуле минимальной толщине стенки min цилиндра прибавляется припуск на механическую обработку металла. Для диаметров цилиндра D = 30 180 мм он принимается равным 05 10 мм.
Расчёт на продольный разрыв прямых тонкостенных трубопроводов (Dн>16) нагруженных внутренним давлением рmax производится по условию прочности:
где Dн - наружный диаметр трубопровода;
Условия прочности выполнены.
8 Технико-экономический расчет
Цена завода-изготовителя
Оплата труда рабочего
Показатель расхода дизельного топлива
Цена приобретения топлива
Затраты на доставку топлива
Цена на смазочные материалы
Норма расхода дизельного топлива
Показатель вместимости (ёмкости) гидравлической системы
Плотность гидравлической жидкости
Коэффициент доливок гидравлической жидкости
Цена приобретения гидравлической жидкости
Коэффициент затрат на доставку гидравлической жидкости
Рыночная текущая цена шины
Коэффициент затрат на доставку шин
Количество шин одновременно заменяемых
Норма затрат на восстановление износа и ремонт шин
Наш %1000 км пробега
Среднегодовой пробег
Нормативный пробег шины
Норма амортизационных отчислений на полное восстановление
Коэффициент к норме аморт. отчислений
В состав сметных расценок на эксплуатацию машин входят следующие статьи расходов:
Смаш = А+ Р+ З+ Э+ С+ Г+ П+ Б (руб.маш-ч)
А – амортизационные отчисления на полное восстановление;
Р – затраты на выполнение всех видов ремонта диагностирование и техническое обслуживание;
З – оплата труда рабочих;
Э – затраты на энергоносители;
С – затраты на смазочные материалы;
Г – затраты на гидравлическую и охлаждающую жидкость;
Б – затраты на замену быстроизнашивающихся деталей;
Амортизационные отчисления на полное восстановление.
Нормативный показатель амортизационных отчислений на полное восстановление (Асм)
где Вс– средняя восстановительная стоимость
Вс = ЦКз.д= 4500 000115 = 5 175 000 руб.
Кз.д– коэффициент затрат на первоначальную доставку (115);
На – норма амортизационных отчислений %год (125%);
Ка– коэффициент к норме амортизационных отчислений составляет – 13;
Т – среднегодовой режим эксплуатации машины 2300 маш-чгод.
Асм =10335 рубмаш-ч.
Затраты на выполнение всех видов ремонта диагностирование и техническое обслуживание.
Нормативный показатель затрат на выполнение всех видов ремонта диагностирование и техническое обслуживание
где Нр – годовая норма затрат на ремонт и техническое обслуживание %год
где (Р+ТО) – сумма среднегодовых затрат на Р и ТО которые включают:
а) затраты на приобретение запасных частей сменных узлов и агрегатов с учетом затрат на их доставку
- на эксплуатацию (328000 009 115) = 33948 руб.
- на капитальный ремонт (287000 012 115) = 39606 руб.
То же в расчете на год:
(Р+ТО) = 33948 + (396066000 2300) = 491303 руб.
б) стоимость ремонтных материалов с учетом затрат на их доставку по фактическим данным (10% от стоимости запасных частей):
(Р+ТО) = 491303 01 = 491303 руб.
в) оплата труда рабочих:
Трудоемкость выполнения ТО-1 и ТО-2:
Трудоемкость выполнения текущих ремонтов:
Трудоемкость выполнения капитальных ремонтов:
Средний квалификационный разряд рабочих – 4.
Оплата труда рабочего 4 разряда в соответствии с отраслевым тарифным соглашением составляет 200 рубчел-ч.
Оплата труда ремонтных рабочих на год эксплуатации:
(Р+ТО) III= (1614 200) = 322800 руб.
Оплата труда ремонтных рабочих на 1 маш-ч:
2800 2300 = 14035 руб.
г) амортизация и затраты на эксплуатацию ремонтных баз и технологического оборудования включая передвижные ремонтные мастерские по фактическим данным (40% от оплаты труда рабочих):
(Р+ТО) IV = (322800 04) = 129120 руб.
д) накладные расходы по организации осуществлению технического обслуживания и ремонта машин принимаются по индивидуальной норме в размере 70% от фонда оплаты труда ремонтных рабочих;
(Р+ТО) V = (32280 07) = 225960 руб.
е) прибыль принимается в индивидуальном размере (30%) от фонда оплаты труда:
(Р+ТО) V1= (322800*03) = 96840 руб.
(Р+ТО) = 491303 + 491303 + 322800 + 129120 + 225960 + 96840= 82876333
Нр = 82876333100 5175000 = 16%
Оплаты труда машиниста
Количество – 1 чел. квалификационный разряд – 6.
Нормативный показатель затрат на оплату труда машиниста (З) определяется так:
Зр – оплата труда рабочего 6 разряда определяемая на основе тарифных ставок устанавливаемых отраслевым тарифным соглашением. Показатель Зр для рабочего 6 разряда составляет 230руб.чел-ч;
t – затраты труда рабочего 6 разряда 1 чел.-чмаш-ч.
З = 2301=230 руб.маш-ч.
Затраты на дизельное топливо
Нд – усредненный нормативный показатель расхода дизельного топлива для экскаваторов (по сборнику норм и расценок на эксплуатацию строительных машин СНиП 4.03-91).
Затраты на дизельное топливо в стоимостной форме:
Цд – региональная рыночная цена приобретения дизельного топлива нефтеналивная база (автозаправка) рубкг;
Зд.д– затраты на доставку дизельного топлива до заправляемой машины сложившееся в регионе рубкн.
Эд = 12 37 115 = 5106 руб.маш-ч.
Затраты на смазочные материалы
Нормативный показатель затрат на смазочные материалы определяется с использованием средневзвешенной рыночной текущей цены по всем видам смазочных материалов:
Сд = 0063 Цс.м. Нд Кп
где 0063 – коэффициент учитывающий расход смазочных материалов;
Цс.м. – средняя региональная рыночная цена на смазочные материалы с учетом затрат на их доставку рубкг;
Нд Кп – норма расхода дизельного топлива для скреперов с учетом затрат связанных с работой пускового двигателя кгмаш.-ч.;
Нормативный показатель затрат на смазочные материалы:
Сд = 0063*200*12 = 1512рубмаш-ч.
Затраты на гидравлическую жидкость
где О – средний показатель вместимости гидравлической системы экскаватора-погрузчика;
Дг – плотность гидравлической жидкости;
Кд – коэффициент доливок гидравлической жидкости;
Пг– периодичность полной замены гидравлической жидкости принимается равным 2;
Цг – цена приобретения гидравлической жидкости рубкг;
Кд.г– коэффициент затрат на доставку гидравлической жидкости;
Т – годовой режим работы равен 2300 маш-чгод
Затраты на замену шин
Нормативный показатель затрат на замену шин:
где Цш – рыночная текущая цена гусеницы (47 звеньев);
Кд.ш– коэффициент затрат на доставку гусеницы на базу;
Кш – количество гусениц одновременно заменяемых на машинах данной типоразмерной группы;
Наш – норма затрат на восстановление износа и ремонт гусениц %1000км пробега;
Гп – среднегодовой пробег тыс.кмгод;
Сш – нормативный пробег гусениц тыс.км;
На– норма амортизационных отчислений на полное восстановление процентгод (1000 км);
Ка – коэффициент к норме амортизационных отчислений;
Т – годовой режим работы машины маш-чгод.
Нормативный показатель на замену шин составит:
Смаш = 10335 + 577 + 230 +5106 + 1512 +776 +5486 = 14212 рубмаш-ч.
Основным технико-экономическим показателем является производительность:
где Q – емкость ковша Q =16 м;
kн– коэффициент наполнения kн=1;
kв– коэффициент использования машины по времени kв=075;
– коэффициент разработки грунта = 1;
tц– время одного цикла; t =25 с;
k– коэффициент разрыхления k=12.
Стоимость разработки одного кубометра грунта:
С1м3 = 14212 144 = 987 рубм3
Автоматизация рабочего процесса
Автоматическое управление машин для земляных работ является одним из перспективных направлений использования этих машин.
Производственные процессы выполняемые машинами сложны и разнообразны. Сопротивления рабочих органов при копании изменяются в широких пределах. Все возрастающие требования к качеству земляных работ и улучшению условий труда оператора неизбежно приводят к необходимости введения автоматического управления машин.
При ручном управлении машины оператор наблюдая за ходом рабочего процесса вручную переключает рычаги управления стремясь обеспечить наиболее выгодные режимы работы заданные траектории рабочих органов требуемую последовательность операций. Одновременно он должен учитывать большое количество разнородных и быстро меняющихся факторов (неровности поверхности по которой перемещаются машины механические и физические свойства грунта и др.). Все это делает режим работы оператора чрезвычайно напряженным. На некоторых машинах число переключений рычагов управления достигает до тысячи в час.
Зачастую оператор может оценить изменение внешних условий и результаты работы только глазомером или ориентировочно. Поэтому выбираемые им режимы работы далеки от оптимальных а качество работ часто не удовлетворяет техническим условиям.
Так например погрешности поперечного уклона земляного полотна автомобильных дорог при планировании его автогрейдером с ручным управлением достигают величины 3—5° при допуске 05°.
Автоматическое управление машин для земляных работ может решать следующие задачи:
Обеспечение безопасности производства работ и безаварийности ограничение перегрузок остановка или снятие напряжения с опасных для человека агрегатов в случае снятия ограждения автоматическая сигнализация о приближении рабочего органа к токонесущему кабелю.
Автоматическое регулирование процесса копания с целью стабилизации какого-либо параметра (мощности тягового усилия) или обеспечения минимума энергоемкости процесса.
Автоматическое ведение рабочего органа планировочных машин по заданной траектории в пространстве.
Автоматическое ведение рабочего органа по траектории задаваемой рукой человека (следящее управление например для экскаваторов при выполнении отделочных работ).
Дистанционное управление рабочим органом машины при помощи оптического луча.
Автоматический учет объема выполненной работы.
Автоматическое выполнение заданной последовательности операций (пуск энергоагрегата цикл операций экскаватора и т. п.)
Автоматическое поддержание режима оптимального по экономической эффективности или себестоимости продукции.
Телеуправление рабочим процессом по проводной или радиорелейной связи.
Автоматическое ведение рабочего органа по заданной траектории.
Основная часть ручного труда при производстве земляных работ затрачивается на зачистку дна котлованов и траншей планирование откосов и берм что вызвано существующим методом их разработки с «недобором» который составляет 10-30 см. Все это можно объяснить несовершенством машин для земляных работ и их систем управления которые не обеспечивают разработку грунта под заданную отметку с достаточной степенью точности.
Доработку до проектной отметки обычно производят с применением легких землеройных и планирующих машин имеющих хорошую маневренность в стесненных условиях строительных площадок.
Однако при выполнении зачистных планировочных и профильных работ даже этими машинами заданная точность планировки не обеспечивается и траншеи разрабатываются со значительным недобором.
Автогрейдеры выполняют значительный объем планировочных и отделочных работ при устройстве в основном земляного полотна с требуемыми продольным и поперечным профилями. На этих машинах устанавливают различные комплекты аппаратуры системы «Профиль».
Система автоматики «Профиль-10» предназначена для автоматического управления положением отвала автогрейдера только в поперечной плоскости машины. Комплект этой аппаратуры состоит из пульта управления датчика углового положения ДКБ сравнивающего и усиливающего устройства и реверсивного гидрораспределителя с электроуправлением.
Для дистанционного и автоматического управления отвалом автоматической стабилизации углового положения отвала в поперечной плоскости и управления им по высоте используют систему «Профиль-20».
Рис.20 Автогрейдер с системой «Профиль 20»
В состав комплекта аппаратуры входит то же самое оборудование что и в аппаратуре предыдущего поколения «Профиль-10» с добавлением датчика высотного положения ДЩБ установленного на специальном кронштейне с правой стороны грейдерного отвала по ходу автогрейдера. Работа этой системы ведется с использованием жестких направляющих.
При стабилизации положения отвала1в поперечной плоскости (рис.205) применяют маятниковый датчик 2 установленный на тяговой раме. Стабилизация высотного положения отвала в профильной плоскости и движения автогрейдера по курсу осуществляется при совместном действии щуповых датчиков соответственно5и4установленных на отвале и на выносной штанге и копирного троса6.Одновременно в сочетании с датчиком4работает датчик угла поворота3который контролирует положение колес автогрейдера. При этом в первом случае положение установки копирного троса должно соответствовать.
В ходе выполнения курсового проекта был рассмотрен автогрейдер предназначенный для выполнения планировочных работ при строительстве дороги. Были произведены расчёты нагрузок на рабочее оборудование расчёты устойчивости в различных положениях расчёты привода рабочего оборудования а также прочностные и проверочные расчёты а также был произведён технико-экономический расчёт демонстрирующий эффективность выбранного рабочего оборудования.
Также выявлены достоинства и недостатки имеющихся конструкций и приведены возможности улучшения и автоматизации процесса работы автогрейдера для автоматического ведения органа по заданной траектории.
Список использованной литературы
Алексеева Т.В. «Машины для земляных работ» М. Машиностроение 1972.
Беркман Л. И. Раннев А. В. Рейш А. К. Универсальные одноковшовые строительные экскаваторы. – М.: Машиностроение 1994. – 304 с.
Волков С.А. Машины для земляных работ: наглядное пособие по дисциплине «Машины для земляных работ» сост.: С.В. Репин А.В. Зазыкин; СПбГАСУ. – СПб. 2012 – 59 с.
Машины для земляных работ: рабочая тетрадь к выполнению практических лабораторных работ и самостоятельных занятий по дисциплине «Машины для земляных работ» сост.: С.В. Репин А.В. Зазыкин; СПбГАСУ. – СПб. 2015 – 34 с.
Чмиль В.П. Гидропневмопривод. Монография СПбГАСУ-СПб2016
Методические указания по курсовому проектированию по дисциплине «МАШИНЫ ДЛЯ ЗЕМЛЯНЫХ РАБОТ»
МДС 81-3.99 методические указания
Автогрейдеры. Устройство основы расчета: учеб. пособие В.И. Баловнев Р.Г. Данилов Г.В. Кустарев [и др.]; под общ. ред. Г.В. Кустарева. – М.: МАДИ 2014. – 144 с.
Репин С. В. MS Teams Курс лекций по теме «Машины для землеройных работ»
Репин С. В. Moodle «Машины для землеройных работ» прочностной расчет.
Шмаков А.Т. Бульдозеры скреперы и грейдеры в дорожном строительстве: Учебное пособие для подготовки машинистов дорожных машин. – М.: Транспорт 1991.
общий вид автогрейдера.cdw

Технические характеристики:
Базовый трактор МТЗ-2022
кВт 156 при 2100 обмин
Эксплуатационная масса
Тип отвала клиновидный
Габаритные размеры отвала
Глубина опускания 250
Управление отвало гидравлическое
Основная рама.cdw

Для сварных швов электрод по ГОСТ 9467-75
Неуказаные предельные отклонения размеров
направленного металла 19кг.
Клеймить сварные швы номером клейма сварщика ударным
СП РАМА ИСПРАВИЛ.cdw

Спецификация Общего вида.cdw

Пояснительная записка
Механизм выноса тяговой
Gidroskhema_Avtogreydera.cdw

Гидроусилитель сцепления
Гидроусилитель тормозов
Гидрозамок двусторонний системы
управления рабочим органом
Клапан предохранительный
Гидромотор шестеренный ГМШН25
Насос шестеренный НШ-32У-3
Гидрораспределитель рулевого
Дополнительный гидрораспределитель
Гидроцилиндр подъема и опускания
Гидроцилиндр выноса отвала
Гидроцилиндр наклона колес
Гидроцилиндр выноса тяговой рамы
Гидроцилиндр бульдозерного оборудования
Гидроцилиндр изменения угла резания
Гидроцилиндр поворота основной рамы
Гидроцилиндр уширителя
Гидроцилиндр изменения угла отвала в плане
Гидроцилиндр изменения угла срезаемого
VO.cdw

Колея передних и задних колес
Эксплуатационная масса 157
полная номинальная мощность
Рабочее оборудование:
отвал: высота с ножом по хорде
Дополнительное сменное оборудование:
Угол складывания основной рамы в плане
Радиус поворота (min) по следу внешнего переднего колеса:
шарнирно-сочлененная рама
Смещение колес переднего моста относительно
ведущего в положении "Краб"
VO_SP.cdw

Пояснительная записка
Механизм выноса тяговой