ВАЗ. Технологическая карта восстановления полуоси автомобиля


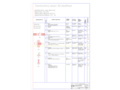
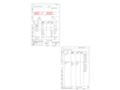
- Добавлен: 25.01.2023
- Размер: 718 KB
- Закачек: 1
Описание
Состав проекта
![]() |
![]() ![]() ![]() ![]() |
![]() ![]() ![]() |
![]() ![]() |
![]() ![]() ![]() |
![]() ![]() ![]() |
![]() ![]() ![]() ![]() |
![]() ![]() ![]() |
![]() ![]() ![]() |
![]() ![]() ![]() |
![]() ![]() ![]() |
![]() ![]() ![]() |
Дополнительная информация
Карта дефектации полуось.dwg

Деталь (сборочная единица):
детали (сборочной единицы):
5 Устройство для электролитического натирания.doc
Сущность процесса электролитического натирания заключается в том что определенной формы электрод обмотанный адсорбирующим электролит материалом приводят в контакт с деталью и включают в цепь постоянного тока. Деталь подлежащая натиранию соединяется с отрицательным полюсом а электрод - с положительным. Адсорбирующий материал насыщенный электролитом служит электролитической ванной и при включении тока в нем происходит процесс электролиза. На поверхности детали происходит наращивание металла ионы которого находились в растворе. Принципиальная схема установки для восстановления картеров коробок передач гальваническим натиранием показана на рисунке 3.
Схема установки для восстановления деталей гальваническим натиранием
– бак с электролитом; 2 – стол станка; 3 – селеновый выпрямитель; 4 – щит управления; 5 – шпиндель сверлильного станка; 6 – вращающийся электрод; 7 – деталь подлежащая восстановлению; 8 – насос ПА-22 для подачи электролита; 9 – токоподводящие щитки.
Для восстановления валов и осей используется любой токарный станок. Деталь являющаяся катодом закрепляется в патроне. Соприкасающийся с ее поверхностью анод перемещаются друг относительно друг друга с определенной скоростью. Анод обматывается адсорбирующим материалом ватой чехлом из сукна. В процессе электролиза электролит пополняется непрерывной подачей или путем опускания электрода в сосуд с раствором.
Разработана установка для электронатирания 0113-006 Ремдеталь. Она включает в себя вращатель; ванны для приготовления электролита обезжиривания и железнения; электрический шкаф; насосный агрегат Х240 и выпрямительный агрегат ВАКР-630-12УЧ. Производительность нанесения покрытия при толщине слоя 1 мм составляет более 01 м2ч
С помощью гальванического натирания можно наносить на изношенные поверхности стальные никелевые хромовые цинковые алюминиевые и медные покрытия.
Технологический процесс электролитического натирания включает в себя: предварительную механическую обработку обезжиривание промывку горячей и холодной водой травление (декапирование) с последующей промывкой водой нанесением покрытия.
Обезжиривание и травление удобно вести натиранием используя для этих целей специальные тампонодержатели и растворы. Для электролитического обезжиривания рекомендуют электролит следующего состава: 20 гл едкого натра NaOH 30 гл карбоната натрия Nа2СОЗ ·10Н2О 10 гл тринатрийфосфата NаЗРО4·12Н20. Время обезжиривания 25 30 с при Dк= 15 25 кАм2.
Анодное травление ведут в течение 3 6 с раствором соляной кислоты HCl (30 40 гл) или серной H2SO4 (100 130 гл) при Dа= 10 .. .15 кАм2.
Для улучшения прочности сцепления в начальный пeриод осаждения металла следует поддерживать плотность тока не более 3 4 кАм2 затем постепенно ее повышать до номинальных значений 15 25 кАм2.
Большими преимуществами этого способа являются плотность и достаточная твердость покрытий устойчивость процесса. Способ обеспечивает меньший расход ресурсов нанесение покрытий в размер или исключением их механической обработки.
Снижение трудоемкости процесса уменьшение потребления энергии химикатов и воды возможно за счет сокращения числа подготовительных и заключительных операций.
2 Разработка маршрутов восстановления.doc
С учетом наличия каждого из дефектов предлагаются возможные маршруты восстановления:
)погнутость оси износ шейки под сальник износ шлицев по ширине;
)погнутость оси износ шейки под сальник;
)погнутость оси износ шлицев по ширине;
)износ шейки под сальник износ шлицев по ширине;
В качестве примера приводится разработка технологического процесса на маршрут №1 который содержит восстановление всех дефектов.
Погнутость восстанавливают правкой шейки под сальник можно восстанавливать гальваническим наращиванием восстановление шлицев производится преимущественно продольной подфлюсовой наплавкой. Но наплавка вызывает нагрев детали поэтому предлагается способ восстановления накаткой роликами.
Графики.doc
Процедура описания дифференциальных уравнений:
procedure func(y:var f:mas);
F[3]:=(csh*(hn1-y[1])-cp*(y[1]-y[2])+ksh*(vhn1-y[3])-kp*(y[3]-y[4]))
F[4]:=(cp*(y[1]-y[2])+kp*(y[3]-y[4]))
Процедура описания формы неровности:
procedure nerv1(t:rea
if (l>=0.5) and (l=0.85) then
if (l>=0.85) and (l=1.2) then
vhn1:=-0.15*cos(3.14+(
if (l0.5) and (l>1.2) then
Графики перемещений х(м)
Графики скоростей x’(мс)
Техпр-полуось.dwg

Патрон 7100-009 ГОСТ2675 Захват ПС-1017
Резец Т15К6 ГОСТ 8879-73 Стойка С-III-8-50 ГОСТ 10197-70 Индикатор ИЧ-10 ГОСТ 577-68 Штангенциркуль ШЦ-1
ГОСТ 166-88 Образец шероховатости ГОСТ 9378-75
Головка шлифовальная ГЦ 32х32 24А25-НСГ 16КА ГОСТ 2447-76 Образец шероховатости ГОСТ 9378-75 Паста КТ ПВТ 2014ТУ2-037-273-78
Коробление плоскости разъёма
Фрезерная операция: -фрезеровать плоскость разъёма до вывёртывания следов износа и придания правильной геометрической формы.
Горизнтально-фрезерный станок
Износ внутренних посадочных поверхностей под подшипники качения
Осталивание: -изолировать места не подлежащие осталиванию; -обезжирить отверстия под подшипники; -промыть холодной водой; -произвести химическое травление; -промыть в холодной проточной воде; -произвести осталивание посадочных поверхностей до ø мм; -промыть посадочные поверхности горячей водой; -просушить; -удалить изоляцию.
Установка для вневанного осталивания собственного изготовления
Бакелитовый лак Венская известь Раствор концентрированной соляной кислоты Электролит: хлористое железо FeCl2*4H2O.
Вдавливание. Накатать роликами с припуском на сторону по 0
Пресс ГАРО типа 2135
Технологический процесс восстановления
Править до устранения изгиба
выдерживая биение не более 1
Погнутость полуоси 2.Износ шейки под сальник 3.Износ шлицев по ширине
Наименование дефектов и эскиз
Наименование и содержание операции
Наименование детали- полуось заднего моста; Материал детали- Сталь 48ХГС; Твердость рабочих поверхностей- HRC 48 56; Суммарное время восстановления- 92
Режущий и измерительный нструмент
Технологичес- кая оснастка
Шлифовать до размера не менее ø50-0
Термическая Нагреть шлицевую часть полуоси ТВЧ до 700°С на i5
каждом конце (рис.2)
Накатать роликами торец шлицев с раздачей боковой поверхности не менее 0
мм на сторону на каждом конце (рис.3)
Токарная. Проточить наружную поверхность до ø47-0
Снять фаску на торцовой поверхности полуоси 5х30° на каждом конце.
Шлицефрезерная. Фрезеровать шлицы на каждом конце до внутренне- го диаметра ø44-0
Станок токарно-винто- резный 16K62
Станок шлице- фрезерный 5350
Тиски с призмами ГОСТ 21168-79
Центра ГОСТ 13212-79
Твердомер Роквелла 20 70НRC ГОСТ 23677-79
центра ГОСТ 13212-79
Cтанок круглошлифоваль- ный 3В423
Патрон трехкулачковый ГОСТ 2675-80
Резец проходной с пластинкой Т16К20 ГОСТ 18866-95
микрометр 25 50 ГОСТ 2675-80
Оправка ГОСТ 16212-79
Круг ПП900Х350Х63 ЭБ40СТ27К5 ГОСТ2424-83
микрометр 25 50 ГОСТ 6507-78
Штангенциркуль ШЦ-1-125 ГОСТ 166-80
Индикатор ГОСТ 9696-79
Установка для электронатирания 0113-006 Ремдеталь
Микрометр 25 50 ГОСТ 6507-78
Установка для перемещения вала между роликами
Фреза червячная однозаходняя ø90 мм ГОСТ 18866-95
Термическая. Закалить ТВЧ шлицевую часть полуоси по всей длине. Отпустить при 575 600°С с охлаждением на воздухе (рис.2).
Шлицешлифовальная. Шлифовать шлицы до диаметра по роликам 56
Устройство делительное
Станок шлицешлифоваль- ный 3451
Круг ПП900х350х63 ЭБ40СТ27К5 ГОСТ 2424-83
микрометр 25 50 ГОСТ 6507-78
Контрольная. Контролировать: -биение в средней части не более 1
мм; -диаметр под сальник не менее ø5-0
мм; -диаметр шлицев по роликам ø56
Полуось заднего моста Икарус-260
Технологический процесс ремонта
4 Расчет производственной программы.doc
Расчет производственной программы ведется по подготовительной операции:
где Фро – годовой фонд работы оборудования. Принимаем Ф=4032 ч;
Кзо – коэффициент загрузки оборудования. Принимаем К= 075;
t – штучное время на выполнение операции мин.
Принимаем N=2500 штук.
Количество оборудования на участке определяется по формуле:
Количество гидравлических прессов:
Количество установок для электролитического натирания:
Принимаем 1 установку.
Количество установок для накатывания:
Количество шлицефрезерных станков:
Количество шлицешлифовальных станков:
Ввиду малой производственной программы для обеспечения технологического процесса восстановления устанавливаем токарно-винторезный станок 16К20 и круглошлифовальный станок 3В423. Тепловые работы планируется выполнять на термическом участке. Необходимое количество стеллажей принимаем технологически.
Схема организации рабочего места представлена на рисунке 2.
– пресс гидравлический; 2 – стеллаж; 3 – установка для электронатирания; 4 – круглошлифовальный станок; 5 – установка для накатывания; 6 – токарно-винторезный станок; 7 - шлицефрезерный станок; 8 - шлицешлифовальный станок.
3 Нормирование технологических операций.doc
Штучное время на выполнение технологических операций включает в себя основное (машинное) время То вспомогательное время Тв (время на установку и снятие детали и время связанное с переходом ) и время на обслуживание рабочего места Торм.
Операция 005. Прессовая
Основное время для исправления погнутости вала с учетом 10-разового приложения нагрузки с выдержкой 15-20 мин.: То= 20 мин.
Вспомогательное время Тв =036 мин.
Время на обслуживание рабочего места находится в процентах от оперативного:
где с - время на обслуживание рабочего места находится в процентах от оперативного. Для станочных и слесарных работ с=6% [Малышев табл.IV.3.34]
Штучное время на выполнение прессовой операции:
Тшт=20+036+12=2156 мин.
Операция 010.Гальваническая
Время на установку и снятие детали: Тв=052 [Малышев табл.IV.3.58].
Время на электролитическое обезжиривание: Тоб=05мин.
Промывка в горячей и холодной воде: Тпром=1 мин.
Анодное травление: Ттр=01мин.
Время осаждения металла:
где h – толщина слоя покрытия мм;
γ – плотность покрытия гсм3;
Дк – катодная плотность тока Адм2;
с – электрохимический эквивалент гА·ч;
Промывка в холодной и горячей воде: Тпром=1 мин.
Время на сушку: Тс=5 мин.
Штучное время: Тшт=052+05+10+01+05+95+10+50=1825 мин.
Операция 015.Шлифовальная
Основное время при наружном круглом шлифовании определяется по формуле:
где Д – диаметр обрабатываемой поверхности мм;
h – припуск на обработку мм;
vз – скорость резания ммин;
t – глубина резания ммоб;
f – коэффициент учитывающий число проходов без поперечной подачи.
С учетом рекомендаций [Малышев табл.II.6.3] получим:
Вспомогательное время: Тв=004 мин. [Малышев табл.IV.3.97] .
Время на обслуживание рабочего места: Торм=006·(0147+004)=001 мин.
Штучное время на шлифовальную операцию:
Тшт=0147+004+001=019702 мин.
Операция 020.Термическая
Основное время с учетом обработки с 2 сторон: То=04 мин.
Вспомогательное время: Тв=08 мин.
Штучное время: Тшт= 04+08=12 мин.
Операция 025. Слесарная
Машинное время на накатывание роликами определяется по формуле:
v – скорость резания ммин;
Вспомогательное время на установку и переход:
Тв= 09 мин. [Малышев табл.IV.3.58].
Время на обслуживание рабочего места: Торм=006·(134+09)=08 мин.
Штучное время: Тшт= 134+09+08=151 мин.
Операция 030.Токарная
Машинное время на обтачивание:
Вспомогательное время: Тв=052 мин. [Малышев табл.IV.3.58] .
Время на обслуживание рабочего места: Торм=006·(17+052)=013 мин.
Штучное время: Тшт= 17+052+013=235 мин.
Операция 035.Шлицефрезерная
Машинное время при фрезеровании шлицев определяется по формуле:
где Дф – диаметр фрезы мм;
vф – скорость резания ммин;
Вспомогательное время: Тв=09 мин.
Время на обслуживание рабочего места: Торм=006·(236+09)=15 мин.
Штучное время: Тшт= 236+09+15=26 мин.
Операция 040.Термическая
Операция 045.Шлицешлифовальная
Машинное время при шлифовании шлицев определяется по формуле:
где h – припуск на обработку мм;
v – скорость стола ммин;
Вспомогательное время: Тв=004 мин. [Малышев табл.IV.3.95] .
Время на обслуживание рабочего места: Торм=006·(45+004)=03 мин.
Штучное время: Тшт= 45+004+08=484 мин.
Операция050.Контрольная
Штучное время: Тшт=20 мин.
Суммарное штучное время на восстановление полуоси Икарус-260 составляет Тшт=927 мин.
1 Анализ конструкции детали и условия работы.doc
Полуось автобуса Икарус-260 относится к классу валы. Шлицевые концы передают крутящий момент от главного дифференциала к планетарной передаче. Момент носит знакопеременный характер деталь работает в условиях высоких циклически меняющихся нагрузок. Полуось изготовлена из легированной стали 38ХГС. Основными рабочими поверхностями являются поверхность под сальник и поверхности шлиц. Условия работы детали диктуют необходимость чтобы поверхности шлиц имели твердость 48-56 НRC и шейка под сальник 52-62 HRC.
Характер износа поверхностей этой детали следующий: шлицы изнашиваются по боковым поверхностям наружный диаметр шлицевого конца не изнашивается. Перегрузка и усталость металла нарушение смазки трущихся поверхностей вызывают нагрев и деформацию детали задиры и схватывание на поверхности трения (поверхность под сальник). Усталость материала детали влечет за собой поломку трещины и обломы скручивание полуоси. При данных дефектах деталь выбраковывается. Анализ дефектов с возможными способами восстановления проведен в карте дефектации. Эскиз детали представлен на рисунке 1.
-трещины или обломы; 2- скручивание; 3- погнутость; 4- износ или задиры шейки под сальник; 5- износ шлицев по ширине.
Бел. нац..doc
Кафедра «Техническая эксплуатация автомобилей»
Технологический процесс восстановления полуоси заднего моста Икарус - 260.
Отчет по практическим занятиям
по дисциплине “Оборудование и технология восстановительного ремонта”
Исполнитель: А.В. Беспалый
Руководитель: А.В. Казацкий
Рекомендуемые чертежи
- 25.10.2022
- 22.07.2023
- 08.05.2023
Свободное скачивание на сегодня
Другие проекты
- 28.12.2022