Разработка технологического процесса восстановления задней полуоси погрузчика Амкодор 134



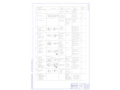
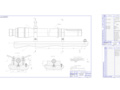
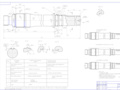
- Добавлен: 25.10.2022
- Размер: 1 MB
- Закачек: 2
Описание
Состав проекта
![]() |
![]() |
![]() ![]() ![]() |
![]() ![]() ![]() ![]() |
![]() ![]() ![]() ![]() |
![]() ![]() ![]() ![]() |
![]() ![]() ![]() ![]() |
![]() ![]() ![]() ![]() |
![]() ![]() ![]() |
![]() ![]() ![]() ![]() |
![]() ![]() ![]() |
![]() |
![]() ![]() ![]() |
![]() ![]() ![]() |
![]() ![]() ![]() |
![]() ![]() ![]() |
Дополнительная информация
приспособа.dwg
* Размеры для справок
Неуказанные предельные отклонения размеров Н14
Остальные технические требования по СТБ 1022-96
Развиваемое усилие закрепления детали
в приспособление деталей
Приспособление станочное
зажимное для фрезерования
Шпилька М12-6gx120.58
Технические характеристики:
Интервал габаритных размеров устанавливаемых
маршрутный техпроцессv13.cdw

Продольная подача 75
выдерживая размеры 11-12
Шлифовать поверхности
выдерживая размеры 13-15
Проверить вал на биение 1
Проверить размеры 15 и 16
калибрМикрометр МК 75
b-10x88x92H12a11x14D9f8
b-8x62x68H12a11x12D9f8
техпроцесс восстановления
приспособа.cdw

* Размеры для справок
Неуказанные предельные отклонения размеров Н14
Остальные технические требования по СТБ 1022-96
Развиваемое усилие закрепления детали
в приспособление деталей
Приспособление станочное
зажимное для фрезерования
Шпилька М12-6gx120.58
Технические характеристики:
Интервал габаритных размеров устанавливаемых
маршрутный техпроцесс.cdw

Продольная подача 75
выдерживая размеры 11-12
Шлифовать поверхности
выдерживая размеры 13-15
Проверить вал на биение 1
Проверить размеры 15 и 16
калибрМикрометр МК 75
b-10x88x92H12a11x14D9f8
b-8x62x68H12a11x12D9f8
техпроцесс восстановления
приспособаv13.cdw

* Размеры для справок
Неуказанные предельные отклонения размеров Н14
Остальные технические требования по СТБ 1022-96
Развиваемое усилие закрепления детали
в приспособление деталей
Приспособление станочное
зажимное для фрезерования
Шпилька М12-6gx120.58
Технические характеристики:
Интервал габаритных размеров устанавливаемых
Чертеж 1 (полуось).cdw

Допускаемые способы
Износ посадочных мест под
Износ наружной поверхности под
Наплавить стальную ленту
Схемы базирования детали:
Технологический маршрут: очистить
); наварить (Деф. 2); заплавить (Деф. 4); наплавить (Деф. 5); фрезеровать
); шлифовать (Деф. 1
Напылить газовой струей
* Размеры для справок
Неуказанные предельные отклонения размеров отверстий по Н14
Править центра после обработки детали
Ресурс восстановленной детали должен
менее 100% от ресурса новой детали
Износ шлицев по толщине
Плазменное напыление
Приварить стальную ленту
Наплавить порошковой проволокой
Заплавить порошковой проволокой
при фрезеровании шпоночного паза и шлицев
маршрутный техпроцесс.dwg
Продольная подача 75
выдерживая размеры 11-12
Шлифовать поверхности
выдерживая размеры 13-15
Проверить вал на биение 1
Проверить размеры 15 и 16
калибрМикрометр МК 75
b-10x88x92H12a11x14D9f8
b-8x62x68H12a11x12D9f8
техпроцесс восстановления
Чертеж 1 (полуось)v13.cdw

Допускаемые способы
Износ посадочных мест под
Износ наружной поверхности под
Наплавить стальную ленту
Схемы базирования детали:
Технологический маршрут: очистить
); наварить (Деф. 2); заплавить (Деф. 4); наплавить (Деф. 5); фрезеровать
); шлифовать (Деф. 1
Напылить газовой струей
* Размеры для справок
Неуказанные предельные отклонения размеров отверстий по Н14
Править центра после обработки детали
Ресурс восстановленной детали должен
менее 100% от ресурса новой детали
Износ шлицев по толщине
Плазменное напыление
Приварить стальную ленту
Наплавить порошковой проволокой
Заплавить порошковой проволокой
при фрезеровании шпоночного паза и шлицев
Чертеж 1 (полуось).dwg
Допускаемые способы
Износ посадочных мест под
Износ наружной поверхности под
Наплавить стальную ленту
Схемы базирования детали:
Технологический маршрут: очистить
); наварить (Деф. 2); заплавить (Деф. 4); наплавить (Деф. 5); фрезеровать
); шлифовать (Деф. 1
Напылить газовой струей
* Размеры для справок
Неуказанные предельные отклонения размеров отверстий по Н14
Править центра после обработки детали
Ресурс восстановленной детали должен
менее 100% от ресурса новой детали
Износ шлицев по толщине
Плазменное напыление
Приварить стальную ленту
Наплавить порошковой проволокой
Заплавить порошковой проволокой
при фрезеровании шпоночного паза и шлицев
ПЗ.docx
Анализ неисправностей заднего моста погрузчика Амкодор 1349
Технические требования на дефектацию задней полуоси погрузчика Амкодор 13414
Анализ научно-технической литературы по ремонту полуосей16
Проектирование техпроцесса восстановления полуоси погрузчика Амкодор 13426
1. Расчет технических режимов и норм времени28
2. Проектирование технологического процесса восстановления полуоси заднего моста погрузчика Амкодор 134Документация единичного технологического процесса восстановления полуоси (маршрутная и операционная карты)37
Конструкторская разработка (Приспособление для фрезерования шпоночных пазов)39
1. Технические расчеты39
2. Устройство и принцип работы39
Список использованных источников43
Целью данного курсового проектирования является разработка технологического процесса восстановления задней полуоси погрузчика Амкодор 134 (на базе трактора МТЗ-82).Требуется проанализировать неисправности заднего моста определить технические требования на дефектацию.
В ходе выполнения курсовойработынеобходимо ознакомиться сконструкцией и принципом работы полуоси заднего моста погрузчика рассчитать технические режимы и нормы времени спроектировать техпроцесс восстановления полуоси и составить маршрутную и операционную карты.
Исходные данные представляют собой нормативно-техническую документацию на капитальный ремонт трактора МТЗ-8082.
Назначение и технические характеристики погрузчика Амкодор134
Рисунок 1.1 – Погрузчик Амкодор 134
Погрузчик АМКОДОР 134 (рисунок 1) является базовой моделью.
В состав погрузчика входит базовое шасси промышленного назначения "Беларус-82П" фронтальное погрузочное оборудование с двухчелюстным ковшом без быстросменного устройства.Погрузчик предназначен для выполнения земляных работ на грунтах I-II категории и погрузочно-разгрузочных работ планировки строительных площадок и грунтовых дорог засыпки траншей и ям подъема и перемещения штучных грузов и других хозяйственных нужд.Область применения погрузчика расширяется при комплектовании его дополнительными сменными рабочими органами.
Погрузчик может быть использован в строительстве коммунальном и сельском хозяйстве.Сменные рабочие органы погрузочного оборудования поставляется по требованию потребителя и по согласованию о изготовителем за отдельную плату. Сменные рабочие органы устанавливается потребителем согласно инструкции по их монтажу.Погрузчик предназначен для эксплуатации в диапазоне температур окружающего воздуха от минус 40 °С до плюс 40 °С.
Технические характеристики
Наименование показателя
Номинальное тяговое усилие трактора кН не менее
Эксплуатационная мощность двигателя кВт
Максимальная транспортная скорость кмч
Дорожный просвет мм не менее
Минимальный радиус поворота в транспортном положении м не более
Тип привода рабочих органов
Рабочее давление в гидросистеме МПа
- в распределителе трактора
- в штоковых полостях гидроцилиндров поворота ковша
Габаритные размеры погрузчика с оборудованием в транспортном положении мм
в том числе масса дополнительных грузов на задних колесах трактора не более
Номинальная грузоподъемность т
Вместимость основного ковша м не менее:
Ширина ковша (по режущей кромке) мм не менее
Максимальная высота разгрузки ковша по режущей кромке при угле разгрузки 45° мм не менее
Максимальная высота разгрузки двухчелюстного ковша мм не менее (А-134)
Максимальная высота разгрузки двухчелюстного ковша мм не менее (А-134-01)
Вылет ковша по режущей кромке на максимальной высоте при угле разгрузки 45° мм не менее
Максимальный угол разгрузки ковша на максимальной высоте подъема не менее
Опрокидывающая нагрузка кН не менее
Вырывное усилие кН не менее:
- развиваемое гидроцилиндрами поворота ковша
- развиваемое гидроцилиндрами поворота стрелы
Масса конструктивная погрузочного оборудования (без грузов) включая ковш кг не более
Анализ неисправностей заднего моста погрузчика Амкодор 134
Основные механизмы заднего моста[1]
Механизмы заднего моста служат для передачи крутящего момента от вторичного вала коробки передач на ведущие колеса. Задний мост (рисунок2.1) состоит из главной передачи 2 дифференциала 3 конечных передач 4 механизма 6 блокировки дифференциала. Эти механизмы помещены в чугунном корпусе 7. К корпусу заднего моста снаружи крепятся тормоза 8.
Рисунок 2.1 – Схема механизмов заднего моста:
— коробка передач; 2 — главная передача; 3 — дифференциал; 4 — конечная передача; 5 — полуось ведущего колеса; 6 — механизм блокировки дифференциала; 7 — корпус; 8 — тормоз.
Дифференциал (рисунок2.2) предназначен для распределения крутящего момента между ведущими колесами и обеспечивает разную частоту их вращения при повороте.
Внутри корпуса 2 дифференциала расположены сателлиты 4 надетые на стальные пальцы 10 и две полуосевые коническиешестерни 5. Полуосевые шестерни жестко связаны с полуосями 1 ведущих шестерен конечных передач 8 и находятся в постоянном зацеплении с сателлитами. При движении трактора вращение от главной передачи передается корпусу дифференциала вместе с которым вращаются пальцы с сателлитами. В случае прямолинейного движения трактора по ровной местности когда частота вращения ведущих колес трактора одинакова полуосевые шестерни имеют равную частоту вращения испытывая одинаковое давление от зубьев сателлитов.
На повороте колеса трактора проходят разную длину пути. Вращение внутреннего колеса трактора замедляется а наружного увеличивается за счет проворачивания сателлитов вокруг пальцев. Вращаясь вместе: корпусом сателлиты зубьями упираются в зубья замедлившей вращение полуосевой шестерни и сообщают дополнительную скорость другой полуосевой шестерне.
Когда одно из ведущих колес попадает на скользкую почву оно начинает буксовать. Чтобы исключить буксование одного из ведущих колес при прямом ходе трактора включают механизм блокировки дифференциала который жестко соединяет одну из полуосей колес с корпусом дифференциала или с другой полуосью.
Рисунок 2.2 – Схема дифференциала:
— полуось 2 — корпус дифференциала 3 — ведомая шестерня главной передачи 4 — сателлит 5 — полуосевая коническая шестерня 6 — муфта блокировки дифференциала 7 — рычаг включения механизма блокировки дифференциала 8 — конечная передачи 9 — ведущее колесо 10 — пальцы сателлитов
Ведущая шестерня1главной передачи заднего моста (рисунок2.3) изготовлена отдельно от вторичного вала. Венец ведомой шестерни 5 главной передачи приклепан к ступице.
Дифференциал выполнен закрытым с разъемным корпусом 6 и четырьмя сателлитами 20. Корпус дифференциала прикреплен болтами к ступице ведомой шестерни и вращается в двух конических роликовых подшипниках которые регулируют во время эксплуатации трактора. Полуосевая шестерня 4 дифференциала изготовлена отдельно от ведущей шестерни конечной передачи. Ведущая шестерня 17 конечной передачи выполнена заодно с валом имеющим на концах шлицы.
Рисунок 2.3 – Задниймост трактора МТЗ-82:
— ведущая шестерня главной передачи 2 — корпус заднего моста 3 — педаль механизма блокировки дифференциала 4 — полуосевые шестерни 5 — ведомая шестерня главной передачи 6 — корпус дифференциала 7 — неподвижная кулачковая муфта 8 — подвижная кулачковая муфта 9 — пружина 10 — ведомая шестерня конечной передачи 11 — рукав 12 — масленка 13 — полуось ведущего колеса 14 — кожух 15 — соединительные диски 16 — нажимные диски 17 — ведущая шестерня конечной передачи 18 — стакан подшипников 19 — регулировочные прокладки 20 — сателлит.
На шлицы вала с внутренней стороны надета полуосевая шестерня дифференциала а с наружной стороны размещают детали тормоза который монтируют на стакане подшипников.
Вал главной передачи на тракторе МТЗ-82 отсутствует. Его роль выполняют валы ведущих шестерен. Ведомая шестерня 10 конечной передачи опирается на два шариковых подшипника. На внешнем конце полуоси 13 ведущего колеса выполнены поперечные прорези для бесступенчатой регулировки колеи трактора.
На шлицы внутренних концов полуосей жестко закрепляют кулачковую муфту 7 механизма блокировки дифференциала.
Основные дефекты заднего моста[1]
Перед тем как устранять дефекты полуоси заднего моста необходимо провести анализ неисправностей при эксплуатации экскаватора-погрузчика. Основные дефекты обнаруженные при анализе метятся и выполняется ремонтный чертеж с указанием данных дефектов.
Правый и левый кожух может иметь следующие повреждения и износы: нарушение сварных швов крепления подушки рессоры; износ отверстий под подшипники и сальники полуосей; под подшипник коробки дифференциала; под подшипники ведущей шестерни.
Нарушение сварных швов крепления подушки рессоры устраняют сваркой.
Изношенные отверстия под подшипники и сальник восстанавливают наплавкой гальваническими покрытиями или постановкой втулок с последующей механической обработкой до номинального размера.
Ведущая шестерня поступает в ремонт с износом шеек под подшипники. Эти износы устраняются наплавкой (вибродуговой или в углекислом газе) или гальваническими покрытиями (осталиванием или хромированием).
Коробка дифференциала цельная неразъемная отлитая из ковкого чугуна КЧ 35-10 имеет следующие износы и повреждения: риски задиры или неравномерный износ торцов под шайбу шестерни полуоси; износ отверстий под ось сателлитов; риски задиры или неравномерный износ сферической поверхности под шайбы сателлитов; износ шеек под роликовые подшипники.
Изношенные внутренние плоские и сферические поверхности коробки дифференциала под шайбы полуосевых и сателлитовых шестерен ремонтируют подрезкой их до ремонтных размеров. Увеличение размера при сборке компенсируют за счет постановки разных по толщине шайб под торцы полуосевых и сателлитовых шестерен.
Механическую обработку сферы выполняют на вертикально-сверлильном станке сборной оправкой. Деталь устанавливают и зажимают на столе станка в приспособлении. Оправка без режущей части своим коническим концом установлена в шпиндель станка. Ее вводят в отверстие под ось сателлитов а затем на нее устанавливают и закрепляют режущую сферическую шарошку. Режущий инструмент может быть изготовлен из углеродистой инструментальной или быстрорежущей стали.
Обработку сферической поверхности ведут до вывода следов износа или задиров по радиусу. Контроль обработки осуществляют шаблоном.
Износ отверстия под ось сателлитов устраняют постановкойвтулки с последующей механической обработкой ее внутреннего диаметра.
Для восстановления размеров шеек под подшипники может быть использован процесс поднятия диаметра путем предварительного накатывания шлиц и окончательного шлифования под номинальный размер.
Шлицы накатывают на токарном станке. Коробку дифференциала устанавливают на оправку и зажимают в центрахстанка.
Накатный ролик диаметром 60 мм изготовлен из стали марки У12 после термообработки твердость ролика HRC 55-60.Накатку с роликом устанавливают и зажимают в суппорте как обычный резец.Деталь вращается с частотой 80 обмин. Диаметр накатанной шейки должен быть равен 502—504 мм.После накатки шейки шлифуют до номинального диаметра на круглошлифовальном станке модели 3151.
Коробку дифференциала устанавливают на центровую оправку и зажимают гайкой. Оправку в свою очередь устанавливают в центрах станка. Шлифование выполняют абразивным кругом ПВД 600X63X305 зернистостью 40 твердостью СТ на керамической связке.Частота вращения детали равна 150 обмин а абразивного круга 1080—1240 обмин.
Не исключена возможность восстановления размера изношенных шеек под подшипники вибродуговой наплавкой или гальваническими покрытиями.
Шестерня полуоси имеет износшейки по диаметру.
Полуоси заднего моста изготовлены из стали марки 40Х. Основными повреждениями и износами полуоси являются погнутость износ шеек под подшипники и зажимное кольцо и износ отверстий под болты крепления колеса.
Погнутость полуоси проверяют в центрах приспособления или токарного станка при помощи индикатора часового типа с точностью измерения 001 мм. При изгибе полуоси более 007 мм полуось – правят.
Изношенные шейки под подшипник и зажимное кольцо ремонтируют гальваническими покрытиями (осталиванием или хромированием) с последующим шлифованием.
Износ шлицев полуоси устраняют вибродуговой наплавкой. Режим наплавки: напряжение 18В сила тока 150—200А подача 18—22 обмин. Частота вращения полуоси 35 обмин. Охлаждающий 5—6%-ный содовый раствор подается только для охлаждения наплавочного мундштука. В качестве электрода применяют проволоку второго класса (ГОСТ 9389-75) диаметром 18 мм.
При износе отверстий во фланцах полуоси под болты крепления колеса отверстия заваривают а затем обрабатывают до номинального размера.
Технические требования на дефектацию задней полуоси погрузчика Амкодор 134
Рисунок 3.1 – Основные дефекты полуоси погрузчика Амкодор 134
На рисунке 3.1 представлен ремонтный чертеж полуоси с указанием основных дефектов требующих устранения.
Основные дефекты полуоси:
дефект 13: износ посадочных мест под подшипники;
дефект 2: износ наружной поверхности под ступицу;
дефект 4: износ шлицев по толщине;
дефект 5: износ шпоночного паза по ширине;
дефект 6: изгиб вала.
Чаще всего встречаются следующие неисправности валов и осей: поломки; трещины; погнутость; скручивание; износ шпоночных пазов и шлицев; износ смятие и забоины резьбы; повреждение центров; износ и задиры поверхностей посадочных шеек; нарушение правильного положения в сборочных единицах.
Валы и оси имеющие трещины и поломки в большинстве случаев заменяют новыми. Если сломанный вал нельзя заменить новым то его восстанавливают слесарно-механическими способами и сваркой. Если трещина имеет продольное направление возможно восстановление вала путем заварки. С этой целью трещина разделывается по ширине и по длине таким образом чтобы металл находящийся в непосредственной близости от трещины был изъят на всю глубину. После разделки трещину заваривают предупреждая деформацию вала.
Валы и оси имеющие стрелу прогиба 0005—0008 своей длины правятся в холодном состоянии а при большем прогибе — в нагретом. Правку в холодном состоянии осуществляют на гидравлических прессах или при помощи домкратов.
Правку в нагретом состоянии также производят на гидравлических прессах но место изгиба нагревается до температуры 500— 600 °С ацетиленокислородными горелками или паяльными лампами. Места правки проверяются с помощью магнитных приборов на отсутствие трещин. При обнаружении трещин деталь должна быть выбракована.
Износ опорных и посадочных мест устраняется наплавкой металла электролитическим наращиванием запрессовкой втулок и механической обработкой шеек под ремонтный размер.Изношенные концевые шейки валов под подшипники качения растачивают до определенного размера а затем напрессовывают на них втулки после чего наружную поверхность втулки обтачивают и шлифуют под номинальный размер подшипника.
В некоторых случаях когда ремонтируемый вал или цапфа недоступны для постановки целой втулки применяют полувтулки. Примером может служить ремонт цапфы и подшипника толкающего бруса бульдозера. Этот узел работает в тяжелых условиях ибыстро изнашивается. Изношенные цапфы протачивают и устанавливают на них полувтулки.
В шпоночных и шлицевых соединениях износу подвергаются торцовые поверхности шпоночных канавок и шлицев. Размеры шпоночных канавок проверяют по шаблону а размеры шлицев — штангенциркулем. Износ шлицев устраняют наплавкой металлом каждого шлица по боковой поверхности со стороны износа под флюсом с последующим фрезерованием шлицев под номинальный размер.
Изношенные пазы фрезеруют под ремонтный размер или заваривают и фрезеруют под номинальный размер в новом месте.
Анализ научно-технической литературы по ремонту полуосей
При выполнении основных операций восстановления ступенчатых валов за установочные базы принимают поверхности центровых отверстий вала. Если его устанавливают на плавающий передний центр то установочной базой будет торец заготовки примыкающий к торцу переднего центра. Применение плавающего переднего центра исключает погрешность базирования при выдерживании длин ступеней от левого торца.
Рассмотрим отдельные операции обработки ступенчатых валов[357].
Плазменное напыление.
Наплавляемый материал (порошок проволока) плавится струей плазмы которая образуется в плазмотроне нагревом электрической дугой плазмообразующего газа температура которого достигает 15000°С.Достоинства способа - высокая производительность процесса (до 12кгч напыляемого металла) прочность сцепления покрытия с поверхностью детали до (45 50МПа) автоматизация управления процессом возможность нанесения покрытий из любых металлов и сплавов. Однако возможность нанесения плазменного покрытия и его эксплуатационная добротность реализуется только в условиях современного производства с высоким уровнем культуры прогрессивных технологий участвующих в технологической цепочке плазменного напыления.
Номенклатура восстанавливаемых деталей разнообразна: клапаны двигателей внутреннего сгорания гусеничные пальцы оси балансиров шкворни детали гидронасосов валы роторов электродвигателей крестовины и другие.
Незначительная глубина плавления основного металла (до 05мм) его низкое содержание в наплавленном слое (до 5%)слабый нагрев деталей (120 - 180°С)позволяют сохранить практически без изменения исходные свойства наплавляемого материала. Плазменное напыление позволяет наносить слои толщиной от 03 до 5мм что дает возможность восстанавливать детали с большим износом.
Процесс нанесения покрытий включает подготовку детали к напылению нанесение покрытия и обработку деталей после напыления.
Подготовка деталей к напылению включает обезжиривание и очистку детали от загрязнений механическую обработку и создание шероховатости поверхности детали.
При механической обработке с поверхности детали снимают такойслой металла чтобы после окончательной обработки напыленнойдетали на ее поверхности осталось покрытие толщиной не менее 05 08мм.
Для получения необходимой шероховатости поверхность детали подвергают дробеструйной обработке или накатывают зубчатым роликом. Дробеструйную обработку производят в специальных камерax крупной колотой дробью ДЧК - 15при расстоянии от сопла дробеструйного аппарата до детали 25 50мм давлением сжатого воздуха 05 06МПа в течение 2 5мин.
Материалы применяемые при металлизации. При газопламенной электродуговой высокочастотной металлизации для нанесения покрытия применяется проволока различного химического состава в зависимости от материала восстанавливаемой детали и требований к нанесенному металлу. При восстановлении неподвижных поверхностей можно применять проволоку с содержанием углерода 03% для поверхностей работающих в условиях трения необходимо применять проволоку с повышенным содержанием углерода и легирующих элементов.
При плазменной металлизации применяют порошки размером частиц 50 150 мкм. Для регулирования свойств порошков в них вводят никель бориды карбиды железные порошки. Порошки выпускаемые промышленностью на основе никеля (ПГ-ХН80СР2 ПГ-ХН80СРЗ ПГ-ХН80СР4) обладают многими ценными свойствами в том числе низкой температурой плавления (950 1050°С).регулируемой твердостью (35 60HRC) жидкотекучестью высокой износостойкостью и свойством самофлюсования. Однако эти сплавы очень дороги и трудно обрабатываются потому стоимость восстановленной детали может превысить стоимость новой детали.
Для уменьшения стоимости порошков разработаны композиционные порошки с добавлением дешевых железных порошков ПЖ-5М. алюминия АКП медного порошка ПМС-2 в разных сочетаниях в дорогие порошки типа ПГ-ХН80СР2-4 СНГН-1 КБХ ФБХ-6-2 ПГ-У30Х28Н4С4 ПГ-У28Н4С4РЗ и др. при условии чтобы свойства новых покрытий не отличались от допустимых для данной детали. Это снижает стоимость порошков в 4 раза с сохранением эксплуатационных свойств требуемой износостойкости и прочности материала.
Обработка после металлизации. Обработка деталей после металлизации затруднительна и по трудоемкости выше чем обработка наплавленных поверхностей или основного металла при обработке под ремонтный размер. Для токарной обработки нужно использовать резцы с пластинами из твердых сплавов и применять режимы с пониженными требованиями: скорость резания 15 20 ммин; глубина резания 01 02 ммоб. При шлифовке металлизационных покрытий рекомендуется применять алмазные круги на вулканитовой основе а при их отсутствии можно применять карборундовые круги на керамической связке. Скорость шлифования 30 35 мс; продольная подача выражается в долях ширины круга В и равна (03.. 04)В ммоб.дет.; поперечная подача 001 мм на двойной ход.
Наплавка в среде углекислого газа.
Наплавку в защитных газах применяют в тех случаях когда невозможно или затруднены подача флюса и удаление шлаковой корки.
Наплавка в среде углекислого газа имеет следующие достоинства: процесс автоматизирован (по сравнению с наплавкой под флюсом); визуальное наблюдение за процессом; качество наплавленного металла выше чем при наплавке вибродуговым способом.
Уменьшение зоны термического влияния позволяет восстановить детали малого диаметра (практически начиная с 10 мм).
Чаще всего применяют углекислый газ для наплавки углеродистых низколегированных сталей. Наплавку в углекислом газе целесообразно применять при восстановлении изношенных деталей цилиндрической формы небольших размеров.
В ремонтном производстве сварка в среде углекислого газа незаменима при ремонте кузовов. Наибольшее распространение получила наплавка в углекислом плавящимся электродом на постоянном токе обратной полярности. При наплавке применяют как проволоку сплошного сечения так и порошковую. Для наплавки из углеродистых и низколегированных сталей применяют сварочные проволоки сплошного сеченияСв-08ГС Св-08Г2С Св-12ГС а также наплавочные Нп-40 Нп-50 Нп-30ХГСА и др. При необходимости получения наплавленного слоя с особыми свойствами применяют порошковые проволоки.
Недостатком способа является то что в процессе наплавки в углекислом газе наблюдается сильное разбрызгивание жидкого металла приводящее к налипанию брызг на мундштук и засорению соплагорелки. Кроме того возможность сдувания струи ветром затрудняет наплавку на открытом воздухе.
При наплавке в среде углекислого газа большое значение имеет и полярность тока сила тока величина напряжения на дуге диаметр и вылет электродной проволоки.
Фрезерная обработка.
Валы имеют ряд конструктивных элементов необходимых для установки и крепления зубчатых колес втулок шкивов звездочек и других деталей. К таким элементам относятся лыски шпоночные пазы шлицевые поверхности. В мелкосерийном и индивидуальном производстве фрезерование лысок шпоночных пазов выполняют на универсальных горизонтально- и вертикально-фрезерных станках.
Шпоночные канавки под сегментные шпонки фрезеруют дисковыми пазовыми фрезами радиус которых соответствует радиусу паза. Фрезерование врезных шпоночных канавок обычно выполняют концевыми фрезами. Для облегчения врезания фрезы на входе канавки высверливают отверстия диаметром равным ширине паза.
В крупносерийном и массовом производстве для фрезерования врезных шпоночных пазов используют специализированные шпоночно-фрезерные станки работающие по принципу маятниковой подачи с углублением фрезы на 02 03 мм на каждый ход. При этом нет необходимости высверливать отверстия. При наличии на валу нескольких шпоночных пазов обработку ведут на многошпиндельных шпоночно-фрезерных станках. Операцию фрезерования лысок в серийном и массовом производстве выполняют обычно в многоместных приспособлениях. Двусторонниелыски обрабатывают на многошпиндельных станках с помощью набора дисковых фрез. Наиболее производительным процессом обработки лысок может быть протягивание на станках для наружного протягивания.
Шлицевые поверхностивалов по конструкции могут быть прямобочными треугольными эвольвентными. Шлицевые соединения с прямобочными шлицами можно выполнять с центрованием втулки по внутреннему и наружному диаметрам соединения с эвольвентными и треугольными шлицами — с центрованием по боковым поверхностям.
На шлицевые соединения устанавливают жесткие нормы точности и технические условия. Так допустимые отклонения неравномерность шага шлицев и смещение их относительно оси не должны превышать 002 003 мм.
Обработку шлицев на валах можно выполнять фрезерованием строганием долблением протягиванием и накатыванием. Наиболее распространено фрезерование на шлицефрезерных станках обкаткой. Этим же способом можно фрезеровать шлицы всех профилей на зубофрезерных станках. Обработка ведется червячными фрезами за один или два (при диаметре 80 мм) прохода.
В индивидуальном и мелкосерийном производстве обработку шлицев можно выполнять на фрезерных станках общего назначения применяя копирование и профильные фрезы. Для делениявала на заданное число шлицев применяют универсальные делительные головки.
Строгание шлицев на валах выполняют многорезцовыми строгальными головками способом копирования. Долбление можно осуществлять многорезцовыми головками путем копирования и долбяками путем обкатки. Этими способами обычно обрабатывают короткие шлицевые поверхности.
Значительно более производительным (в 5-10 раз) по сравнению с фрезерованием является протягивание которое широко применяется для обработки открытых шлицевых пазов чтобы инструмент имел выход. При протягивании пазов с радиальным выходом усложняется конструкция протяжки (выдвижные зубья).
При изготовлении шлицевых поверхностей практически любого размера наиболее перспективным является процесс холодного накатывания шлицев. Накатывание можно осуществлять рейками валиками роликами многороликовыми профильными головками. Согласно экспериментальным данным накатанные шлицы при скручивании на 10 20 % прочнее шлицев полученных резанием.
Рассмотренные способы получения шлицевых поверхностей обычно позволяют добиваться требуемого качества без дополнительной обработки.
Шлицы закаливаемых валов шлифуют на шлицешлифовальных полуавтоматах. Схемы шлифования зависят от способа центрования. Так при центровании по внутреннему диаметру шлифование может производиться профильным кругом с одновременным шлифованием боковых поверхностей (рисунок4.1 а). При центровании по наружному диаметру боковые поверхности шлифуются двумя кругами (рисунок4.1 б).Шлифование наружной поверхности выполняется на обычных круглошлифовальных станках.
Рисунок4.1 –Схемышлифования шлицев
Сверление отверстий.
Для получения отверстий на торцах или поверхностях вращения валов используют сверлильные операции. Обработку концентрических отверстий на торцах валов можно выполнять в процессе подготовительных операций на фрезерно-центровальных полуавтоматах. При этом вместо центровального сверла используют спиральное сверло требуемого диаметра. При сверлении глубоких отверстий (длина в пять раз больше диаметра) применяют сверла для глубокого сверления с принудительной подачей охлаждающей жидкости в зону резания. Обработку ведут на горизонтально-сверлильных и сверлильных станках для глубокого сверления. Остальные отверстия обрабатывают на сверлильных станках общего назначения с использованием специальных приспособлений — кондукторов. Для повышения производительности можно применять многоместные приспособления.
Если в валах надо обработать большое количество отверстий то целесообразно применять агрегатные многошпиндельные станки. Если отверстия занимают определенное угловое положение относительно ранее обработанных пазов лысок и других элементов в конструкции приспособлений то следует ввести дополнительные установочные элементы (ориентировочные). Для направления инструмента приспособления снабжают кондукторными втулками.
В индивидуальном и мелкосерийном производстве сверление отверстий выполняют по разметке без применения каких-либо специальных приспособлений. В среднесерийном производстве можно использовать сверлильные станки с программным управлением. В качестве приспособлений наиболее экономично применять универсально-сборные приспособления.
При обработке заготовок деталей типа валов в машиностроении задачу образования основных конструктивных поверхностей вращения в большинстве случаев удается решить токарной обработкой. Однако при обработке шеек валов по квалитетам 6 8 при шероховатости Ra= 25 063 мкм и выше экономичнее применять шлифование. Оно является основным при обработке закаленных поверхностей валов. В связи с развитием силового шлифования обработку шеек жестких валов ведут сразу на круглошлифовальных станках вместо предварительного многорезцового обтачивания. При этом с заготовки получаемой путем точной штамповки снимают припуск на сторону 2.0 25 мм.
В технологическом маршруте обработки заготовок валов шлифовальные операции могут занимать различное место в зависимости от конструктивных и технологических особенностей деталей. При обработке заготовок подвергнутых закаливанию шлифовальные операции являются завершающими. При этом часто возникает необходимость правки центровых отверстий (путем их зачистки притирки шлифования и т.п.) для снятия окалины и устранения дефектов образовавшихся в процессе термообработки.
Шлифование термически необработанных валов выполняют после окончания всех фрезерных сверлильных и других операций что предохраняет шлифованные поверхности от повреждения при дальнейшей обработке и транспортировке. Выполнение шлифования после токарной обработки повышает точность обработки так как поверхности не прерываются шпоночными пазами лысками отверстиями. Такая последовательность создает удобства для выполнения дальнейшей механической обработки. Окончательно обработанные шейки вала можно использовать в качестве установочных и измерительных баз.
Шлифование валов производят на круглошлифовальных и бес-центрово-шлифовальных станках одним из существующих способов (рисунок4.2).
Рисунок 4.2 –Схемыобработки заготовок валов: а — на круглошлифовальных станках; б — на бесцентрово-шлифовальных; I — способом продольной подачи; II — способом глубинного шлифования; III — способом поперечной подачи (врезания); IV — способом продольной подачи; V — способом поперечной подачи
Продольную подачу применяют при обработке поверхностей значительной длины. Шейки малой длины обрабатывают путем врезания. В массовом производстве шлифование этим способом часто выполняют по автоматическому циклу с применением приборов активного контроля которые выключают поперечную подачу при достижении заданного размера. При обработке на бесцентрово-шлифовальных станках не требуется баз для установки и крепления деталей. Гладкие валы (пальцы оси) на этих станках шлифуют способом продольной подачи. Простота обработки позволяет в массовом производстве компоновать автоматические линии из таких станков с простейшей транспортной системой и приборами активного контроля для черновой и получистовой обработки.
Контроль валов включает проверку диаметров шеек длин участков биения шеек валов относительно оси проверку отдельных конструктивных элементов валов (шлицевых поверхностей шпоночных канавок резьб галтелей и т.п.). Помимо этого выполняют контроль твердости деталей или заготовок после термической обработки и дефектоскопию.
При серийном и массовом производстве контроль диаметров валов выполняется с помощью предельных и индикаторных скоб проверка длин участков — с помощью предельных шаблонов или линейных скоб. При мелкосерийном производстве используется универсальный инструмент: штангенциркули микрометры линейки. Контроль биения шеек вала осуществляется после его установки в центрах или на призмах. Биение определяется с помощью прибора индикаторного типа. Для проверки радиусов галтелей применяются шаблоны. Шлицевый участок вала контролируется с помощью предельных калибров. Предельными скобами проверяют наружный и внутренний диаметры (если они подлежат контролю) и ширину гребня. Кроме того с помощью проходного комплексного шлицевого кольца проверяют правильность взаимного расположения отдельных элементов профиля. Шпоночные пазы контролируют плоскими предельными калибрами резьбы на валах — предельными резьбовыми кольцами.
Для оценки отклонений от круглости (овальности) огранки волнистости валов в сечениях перпендикулярных к их осямиспользуются кругломеры моделей 218 255 ВЕ-20А и ВЕ-37 регистрирующие результаты измерений электротермическим способом на круглограммах в полярных координатах. Из зарубежныхкругломеров наиболее известен «Телиронд» (Великобритания). В этих приборах применяются индуктивные ощупывающие головки.
Белорусско-Российским университетом совместно с Белорусским государственным университетом модернизирован профилометр-профилограф модели 201 путем его автоматизации на основе ЭВМ и наделения способностью регистрировать отклонения от круглости и строить круглограммы.
Для экспериментальной оценки круглости деталей используются образцы с центровыми гнездами. Их круглограммы записываются с помощью измерительного комплекса и профилометра-профилографа. Схема записи круглограмм при использовании данного средства измерения приведена на рисунке4.3.
Рисунок4.3 –Схема записи круглограмм с использованием измерительного комплекса: 1— преобразователь угловых перемещений; 26— кронштейны; 3— индукционный датчик; 4— вертикальная стойка; 5 — блок-преобразователь; 7 — основание; 8 9— соответственно плавающий и жесткий центры
При записи круглограмм в качестве первичного преобразователя используется индукционный датчик применяемый в профилометрах-профилографах модели 201 которые выпускаются Московским заводом «Калибр». Сигнал от первичного преобразователя регистрируется при вращении исследуемого образцапо команде соответствующей формированию каждого импульса от преобразователя угловых перемещений ВЕ-178А который при измерении круглости связан с вращающимся образцом с помощью жесткого вращающегося центра.
Зарегистрированные сигналы от индукционного датчика для каждого образца т.е. для каждого эксперимента сохраняются в виде отдельных файлов которые затем подвергаются математической обработке по специальным программам и представляются в виде графика развертки профилограммы. Результаты обработки экспериментальных данных экспортируются в среду MicrosoftExcel где и сохраняются в виде Excel файлов.
Наибольшее отклонение от круглости деталей обработанных на металлорежущих станках в разных странах определяют по-разному:
как наибольшее расстояние от окружности вписанной в реальный профиль;
как наибольшее расстояние от окружности описанной вокруг реального профиля;
как наибольшее отклонение от средней окружности профиля;
как наибольшее расстояние от окружности прилегающей к реальному профилю.
В зависимости от способа измерения круглости различия в ее величине не превышают 10 % поэтому для анализа можно пользоваться любым способом. Однако наиболее подходящим для измерения круглости с помощью ЭВМ является способ измеренияотклонения от средней окружности. В этом случае отклонение от круглости соответствует размаху развертки реального профиля который можно легко измерить при проведении исследований. Овальность можно оценить как наибольшую полуразность взаимно перпендикулярных диаметров реального профиля.
На рис. 4.4 представлены результаты измерения круглости поверхности (круглограмма ее развертка и амплитудно-частотный спектр). Показано что отклонение от круглости образца составляет 013 мм. При этом амплитуда каждой из представленных на рис. 4.3.4в гармонических составляющих округлости существенно меньше ее наибольшей величины.
Дискретные амплитудно-частотные спектры круглограмм полученные при точении образцов с различными частотами вращения шпинделя показывают что наиболее значимыми составляющими спектра являются первая и вторая. Первая гармоника имеет величину в пределах 005 009 мм вторая — 002 004 мм. Гармонические составляющие с номерами 3-6 характеризуются значениями своих амплитуд не превышающими 001 мм. Более высокочастотные составляющие имеют незначительные амплитуды соответствующие уровню шероховатости обработанных поверхностей.
Рисунок4.4 –Круглограмма(а) развертка (б) и амплитудно-частотный спектр (в) профиля поверхности обработанной точением при п= 250 мин
t= 1 мм S = 01 ммоб.
На основании проведенного анализа выбраны следующие способы устранения дефектов:
полуось править гидравлическим прессом;
поверхности под подшипники напылить порошковой проволокой с последующим шлифованием;
поверхность под ступицу наплавить лентой с последующим шлифованием;
шлицы и шпоночный паз заплавить проволокой с последующим фрезерованием.
Проектирование техпроцесса восстановления полуосипогрузчика Амкодор 134
Анализ существующего технологического процесса должен быть проведен с точки зрения обеспечения качества восстановленной полуоси. При этом следует выяснить правильно ли он составлен для выполнения требований чертежа и соблюдаются ли все требования технологического процесса.
Таблица 5.1 – Проектирование технологического процесса восстановления полуоси
Очистить деталь в моечной машине ОМ-15434 при температуре рабочей жидкости 85°С и рабочем давлении 10 МПа.
Править деталь гидравлическим прессом усилием в 8 10 кН.
Обезжирить деталь композицией ЭКОМЕТ-011НТ в ванне при температуре 25-35°С.
Напылить с припуском 05 мм используя установку плазменного напыления ОКС-22104 в среде аргона при частоте вращения детали 100 обмин и продольной подачей 04 ммин.
Приварить ленту из стали 40 толщиной 1 мм обеспечив 40-45 сварочных точек используя сварочный полуавтомат А-825М в среде углекислого газа при частоте вращения шпинделя 5 обмин при силе тока 180 А. Напряжение 18В.
Заплавить шлицыпри продольной подаче 75 ммоб проволокой 2ПП-ФН4 используя установку УД 609.02 при силе сварочного тока 500 А и напряжении 18 В.
Заплавить пазпри продольной подаче 75 ммоб с припуском 1 мм проволокой 2ПП-ФН4 используя установку УД 609.02 при силе сварочного тока 500 А и напряжении 18 В.
Фрезеровать шлицы с припуском 08 мм червячной однозаходной фрезой
Р6М5Ф3 на шлицефрезерном станке 5350А при подаче 0028 ммзуб и скорости резания 30 ммин.
Фрезеровать шпоночный паз с припуском 02 мм шпоночной фрезой Р6М5 на шпоночно-фрезерном станке Д691 при подаче 0028 ммзуб и скорости резания 20 ммин. Частота вращения фрезы 400 обмм.
Шлифовать поверхности под ступицу и под подшипники шлифовальным кругом 400х50х16 на круглошлифовальном станке 3М150 при подаче 8 ммоб.
Проверить вал на биение при помощи прибора индикаторного типа установив деталь в центрах токарного станка. Допуск торцевого биения не должен превышать 002 мм.
Проконтролировать диаметры посадочных мест под подшипники при помощи микрометра МК 75 МК 100 с ценой деления 001 мм. Величина допуска не должна превышать 001 мм. Шероховатость 125 040 мкм.
Проверить диаметр вала под ступицу штангенциркулем ШЦ-1-125-01.
Проконтролировать шлицы комплексным калибром.
Проконтролировать шпоночный паз плоским предельным калибром
1. Расчет технических режимов и норм времени
Операция 020.– Напыление(поверхности под подшипники)[7]
Основное время на нанесение покрытия:
гдеd – диаметр напыляемой поверхности мм ();
L – длина напыляемой поверхности мм ();
y – перебегметаллизатора мм ();
h – толщинанапыленного слоя мм ();
- плотность напыленного металла гсм3 ();
q – производительностьметаллизатора кгч ();
- коэффициент напыления ();
Операция 025. –Наплавочная(наварка ленты под ступицу)[7]
Скорость наплавки по винтовой линии:
где W- производительность наплавки по винтовой линии см2мин
S- шаг наплавки смоб ();
гдеh– толщина наносимого слоя проволокой мм (h=1);
где - коэффициент наплавки гАч ();
гдеd – диаметр детали мм (d=70);
Основное время наплавки:
где- площадь наплавляемой детали см2;
Операция 030. –Наплавочная(заваривание шлицев) [7]
Скорость подачи порошковой проволоки:
где I– сварочный ток А (I=500);
d – диаметр проволоки мм (d=2);
гдеS – величина продольной подачи ммоб(S=75);
- толщина слоя наплавки мм ();
где – длина зоны наплавкимм();
- ширина зоны наплавки мм ();
- толщина зоны наплавки мм ();
- диаметр электродной проволоки мм ();
- подача электродной проволоки мммин ();
- число зон наплавки ();
Операция 035. – Наплавочная (наплавка шпоночного паза)[7]
где – длина зоны наплавки мм ();
Операция 040. –Фрезерная(фрезерование шлицев)[48]
Определение скорости резания:
гдеТ – среднее значение периода стойкости фрезы мин (Т=80);
t – глубина резания мм (t=35);
S– подача ммзуб (S=0028);
D – диаметр фрезы мм (D=16).
Cv=12; q=025; y=03; u=0; p=0; m=026.
где Knv – коэффициент отражающий состояние поверхности заготовки (Knv=10);
Kuv– коэффициент учитывающий качество материала инструмента (Kuv=10);
Kmv – коэффициент учитывающий качество обрабатываемого материала.
где Kr – коэффициент характеризующий группу стали по обрабатываемости (Kr=10);
в – временное сопротивление материала сталь 40Х МПа (в=900 МПа);
nv – показатель степени (nv=09).
Определение частоты вращения фрезы:
Ряд частот вращения для станка 6Р11 будет:
Принимаем фактическую частоту вращения фрезы равную nф=250обмин.
Определение фактической скорости резания:
Определение основного машинного времени:
где h– глубина шлица мм (h=35);
Szв – вертикальная подача ммзуб (Szв=0010);
z – количество зубьев фрезы (z=2);
n – частота вращения фрезы обмин (n=250);
d – диаметр фрезы мм (d=16);
Szпр – продольная подача ммзуб (Szпр=0028).
Операция 045. –Фрезерная(фрезерование шпоночного паза)[48]
t – глубина резания мм (t=1);
S – подача ммзуб (S=0028);
Kuv – коэффициент учитывающий качество материала инструмента (Kuv=10);
в– временное сопротивление материала сталь 40Х МПа (в=900).
Принимаем фактическую частоту вращения фрезы равную nф=400 обмин.
Определение мощности резания:
где - сила резания кН ();
Необходимая мощность электродвигателя:
где - КПД станка ();
где - статическая мощность станка кВт ()
условие выполняется.
гдеh – глубина паза мм (h=35);
– продольная подача ммзуб (=0028).
Операция 050. –Шлифовальная(шлифование посадочных мест под подшипники и ступицу[48]
В – ширина шлифовального круга мм(В=16);
nз – частота вращения шлифовального круга обмин(nз=87);
Sпр – продольная подача ммоб (Sпр=8);
– коэффициент учитывающий пробный проход при шлифовании и замере диаметра;
где Vз=15 ммин – скорость вращения заготовки;
dз=85 мм – диаметр обрабатываемой заготовки.
Окончательная обработка:
2. Проектирование технологического процесса восстановления полуоси заднего моста погрузчикаАмкодор 134
Документация единичного технологического процесса восстановления полуоси (маршрутная и операционная карты)
Исходные данные необходимые для проектирования маршрута технологического процесса восстановления полуоси: ремонтный чертеж полуоси со всеми необходимыми видами разрезами и сечениями.
Для восстановления детали необходимо ее очистить промыть проверить состояние и определить пригодность для дальнейшего использования.
Маршрутный технологический процесс восстановления полуоси представлен в таблице 5.2.1.
Таблица 5.2.1 – Маршрутный технологический процесс
Моечная машина ОМ-15434
гидравлический пресс
Композиция ЭКОМЕТ-011НТ
Установка плазменного напыления ОКС-22104
Сварочный полуавтомат А-825М
Проволокой 2ПП-ФН4 установку УД 609.02
Фреза Р6М5Ф3 шлицефрезерный станок 5350А
Фрезой Р6М5 шпоночно-фрезерный станок
Шлифовальный круг 400х50х16круглошлифовальный станок 3М150
ШЦ-1-125-01 ГОСТ 166-80 кругломер «Телиронд» калибры микрометр МК 75 МК 100 ГОСТ 6507-90
Подробное описание технологического процесса(оборудование инструмент
и материалы) приведено в Приложении А.
Конструкторская разработка(Приспособление для фрезерования шпоночных пазов)
1. Технические расчеты [68]
2. Устройство и принцип работы
Жесткое закрепление предотвращение сдвигов и смещений деталей во время обработки играет важную роль как для обеспечения точности обработки так и для сохранения геометрии детали и её параметров.
Основные требования предъявляемые к зажимным устройствам:
)простота надежность жесткость и износостойкость;
)постоянная по величине сила закрепления и минимальное время закрепления-открепления заготовки или детали;
)отсутствие деформации заготовки или детали и ее смещения в процессе закрепления.
Зажимные устройства и приспособления разделяют на два типа:
)самотормозящие устройства: винтовые клиновые эксцентриковые и другие механизмы обеспечивающие жесткое замыкание независимо от вида привода. Упругие обжатия элементов таких устройств прямо пропорциональны приложенной силе;
)автоматизированные зажимные устройства: пневматические гидравлические и гневно-гидравлические механизмы прямого действия без промежуточных элементов. Если к зажимному элементу этих устройств (например к штоку) приложить возрастающую силу то перемещение элемента (штока) не произойдет до тех пор пока значение этой силы не превысит определенный уровень после чего шток сразу переместится на значительную величину.
При фрезеровании шпоночного паза на восстанавливаемый вал будут действовать силы резания стремящиеся сместить его с исходного положения. Во избежание этого необходимо произвести расчёт зажимной силы W:
где K=K0·K1·K2·K3·K4·K5·K6 – коэффициент запаса [13];
K0 K1 K2 K3 K4 K5 K6 – составляющие коэффициента запаса;
–составляющая силы резания действующая в осевом направленииН;
f – коэффициент трения (f=015) [13].
К=15· 14· 10· 12· 10·10·10=25.
Произведём расчёт усилия резания Рz [формула 4.13 8]:
гдеCp=682; y=072; u=1; q=086; v=0;
S – продольная подача ммзуб (S=0028);
D – диаметр фрезы мм (D=16);
В– ширина шпоночного паза мм (В=20);
n – показатель степени (n=03);
Определим значение составляющая силы резания действующая в осевом направлении [таблица 42 8]:
= 11·Рz=12·02=024 Н.
По формуле (30) произведём расчёт зажимной силы:
Для закрепления валов при фрезеровании шпоночного паза целесообразно использовать приспособление показанное на рисунке5.1.
Рисунок6.1 – Приспособление для фрезерования шпоночных пазов
-обрабатываемая деталь; 2-зажим; 3-резьбовое соединение (шпилька-гайка) для зажима; 4-плита; 5-станина
В данном случае используются винтовые зажимы они просты и надежны. К данному оборудованию а также к закрепленной в нем обрабатываемой детали предъявляются следующие требования:
Организация работы должна соответствовать мерам безопасности.
Исключается перекос половинок относительно стола.
Не допускается взаимная не перпендикулярность тисков и стола.
Обеспечение надежной фиксации обрабатываемой детали и устройства.
Настоящее оборудование также имеет характеристики:
Максимальное зажимное усилие устройства по паспорту –100 Н.
Вес зажимного устройства 5 кг.
Тип зажимного устройства – механическое стационарное.
Предельные размеры закрепляемой детали – диаметр D=45 75 мм длина L=150 450 мм.
Большинство дорожно-строительных предприятий из-за высокой стоимости и дефицита запасных частей широко применяют восстановленные детали.
В зависимости от потребности в запасных частях и технической оснащенности предприятия работы по восстановлению деталей могут выполняться различными способами как собственными силами так и в ремонтных организациях.
Выбор способа зависит от конструктивно - технологических особенностей детали условий ее работы величины износов характера дефектов и особенностей самих способов восстановления определяющих долговечность отремонтированных деталей и себестоимость ремонта.
Чтобы правильно осуществить выбор наиболее рационального способа восстановления детали необходимо всесторонне оценить свойства как самих покрытий так и применимость способа для конкретной детали.
В ходе выполнения курсовой работы был произведен анализ неисправностей полуоси заднего моста погрузчика Амкодор 134 и выбран оптимальный способ восстановления полуоси. Способ характерен экономичностью и высокой производительностью.
Восстановление одной детали составляет около 60 минут.
Производительность составляет 2000 штгод при работе в одну смену на одного рабочего.
Список использованных источников
Технология машиностроения: учеб.пособие М.Ф. Пашкевич [и др.]; под ред. М.Ф. Пашкевича. – Минск: Новое знание 2008. – 478 с.
Теория режимов резания:справочник под ред. Ю.В. Барановского – «Машиностроение» Москва 1972. – 363 с.
Курсовое проектирование по технологии машиностроения. Под ред. А.Ф. Горбацевича – Минск: «Вышэйшая школа» Минск 1975. – 288 с.
Станочные приспособления: справочник в двух томах под ред. Б.Н. Вардашкина и В.В. Данилевского. – Москва «Машиностроение» 1984. – 656 с.
Курсовое проектирование по технологии производства и ремонта автомобилей. Учебное пособие. А. Н. Унянин. – Ульяновск: УлГТУ 2004. – 72 с.
Расчет режимов резания при механической обработке металлов и сплавов: методическое пособие к курсовому и дипломному проектированию Э.Г. Бабенко – Хабаровск 1997. – 156 с.
Учебно-методическое пособие к курсовой работе по дисциплине «Технология производства и ремонта машин»Гарост М.М. Масловская Е. М. – Минск: БНТУ 2008. – 177 с.
Журнал "Автомобильная промышленность" 2005 год № 11
УДК 621.824.32. Д-р техн. наук С.М. Кадыров кандидаты техн. наук З.Э. Мусабеков и А.М. ХакимовТади.
Журнал«Формирование сплошного металлопокрытия при электроконтактной наплавке валов» (№09 2006год) Нафиков М.З.
Журнал «Определение размеров ролика для электроконтактной наплавки валов» (№02 2007год) Нафиков М.З. Загиров И.И. Сайфуллин Р.Н.
Журнал «Электроконтактная наплавка – эффективный способ восстановления валов» (№11 2007год) Нафиков М.З.
Журнал «Особенности формирования структуры металлопокрытий нанесенных электроконтактной наплавкой проволокой из углеродистых и легированных сталей» (№06 2008год) Нафиков М.З. Загиров И.И. Левин Э.Л. Сайфуллин Р.Н.
Журнал «О возможности восстановления изношенных валов электроконтактной приваркой стальных проволок с порошковым покрытием» (№05 2009год) Сайфуллин Р.Н. Нафиков М.З.
титульник +.docx
Белорусский национальный технический университет
Факультет транспортных коммуникаций
Кафедра: «Строительные и дорожные машины»
Пояснительная записка
по дисциплине «Технология производства и ремонта машин»
Тема: «Разработать технологический процесс восстановления
задней полуоси погрузчика Амкодор 134»
Исполнитель: студент гр. 115210
Руководитель: Гарост М.М.
-маршрутная карта-.doc
Министерство образования Республики Беларусь
Белорусский национальный технический университет
Руководитель М.М. Гарост
Консультант М.М. Гарост
ТЕХНОЛОГИЧЕСКОГО ПРОЦЕССА ВОССТАНОВЛЕНИЯ ПОЛУОСИ
ГОСТ 3.118-82 форма 1
Код наименование операции
Обозначение документации
Код наименование оборудования
РМ 005 Очистная ИОТ №5
Машина моечная ОМ-15434 2% раствор кальцинированной соды перчатки ГОСТ 124015-82 1-2
РМ 010 Правка ИОТ №10
Пресс гидравлический ПСГ-621 призмы индикатор часового типа.
РМ 015 Обезжиривание ИОТ №15
Ванна УЗ композиция ЭКОМЕТ-011НТ ванна ополаскивания ванна пассивации сушильная камера
РМ 020 Напыление ИОТ №20
Установка плазменного напыления ОКС-22104 порошковые стали ПК40Н2Д2-64 аргон
РМ 025 Наплавочная ИОТ №25
Стол сварщика ОКС-7523 полуавтомат сварочный А-825М баллон для СО2 сварочные клещи лента наплавочная сталь 40 ГОСТ 4543-71
Наименование детали сборочной единицы или материала
РМ 030 Наплавочная ИОТ №30
Установка наплавки порошковыми проволоками УД 609.02. горелка проволока 2ПП-ФН4 ГОСТ 26101-84
РМ 035 Наплавочная ИОТ №35
Установка наплавки порошковыми проволоками УД 609.02. горелка проволока 2ПП-ФН4
РМ 040 Фрезерная ИОТ №40
Шлицефрезерный станок 5350А фреза червячная сборная однозаходная Р6М5Ф3 ГОСТ 9324-80
РМ 045 Фрезерная ИОТ №45
Шпоночно-фрезерный станок Д691 фреза шпоночная Р6М5 ГОСТ 1940-78
РМ050 Шлифовальная ИОТ №50
Круглошлифовальный станок 3М150 плита магнитная круг ПП 400×50×16 ГОСТ 2424-83 штангенциркуль ШЦ-1-125-01 ГОСТ 166-80.
РМ 055 Контрольная ИОТ №55
Стол дефектовщика штангенциркуль ШЦ-1-125-01 ГОСТ 166-80 линейка стальная кругломер «Телиронд» комплексный калибр плоский
предельный калибр микрометр МК 75 МК 100 ГОСТ 6507-90
-операционная карта-.doc
Полуось заднего моста погрузчика Амкодор 134
Наименование операции
Оборудование устройство ЧПУ
Обозначение программы
Установка дуговой наплавки порошковыми проволоками УД 609.02.
Установить и закрепить заготовку в
станочное приспособление
Наплавить поверхность А
Очистить обработанные поверхности от брызг и шлака
Наплавить поверхность Б
Снять деталь уложить в тару
ГОСТ 3.118-82 форма 7а
Код наименование операции
Обозначение документа
Код наименование оборудования
Наплавить поверхности А и Б выдерживая размеры 5 и 6.
Рекомендуемые чертежи
- 22.07.2023
- 25.10.2022
- 20.03.2015
- 24.01.2020