Совершенствование организации работ на агрегатном участке МУП ХПАТП №1 г. Хабаровска




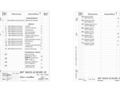
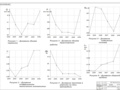
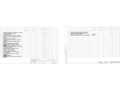
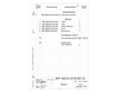
- Добавлен: 25.01.2023
- Размер: 9 MB
- Закачек: 1
Описание
Состав проекта
![]() |
![]() |
![]() ![]() ![]() |
![]() |
![]() |
![]() ![]() ![]() ![]() |
![]() ![]() ![]() ![]() |
![]() ![]() ![]() ![]() |
![]() ![]() ![]() ![]() |
![]() ![]() ![]() ![]() |
![]() ![]() ![]() ![]() |
![]() ![]() ![]() ![]() |
![]() ![]() ![]() ![]() |
![]() ![]() ![]() ![]() |
![]() ![]() ![]() |
![]() ![]() ![]() ![]() |
![]() ![]() ![]() |
![]() ![]() ![]() ![]() |
![]() ![]() ![]() |
![]() ![]() ![]() ![]() |
![]() ![]() ![]() ![]() |
![]() ![]() ![]() |
Дополнительная информация
реф.doc
АВТОМОБИЛЬ ПРЕДПРИЯТИЕ АВТОТРАНСПОРТНОЕ АГРЕГАТНЫЙ УЧАСТОК ВАЛ КАРДАННЫЙ СТЕНД ДЛЯ ВЫПРЕССОВКИ ТРУДОЁМКОСТЬ ОХРАНА ТРУДА ЭФФЕКТ ЭКОНОМИЧЕСКИЙ
Объектом исследования является Муниципальное унитарное предприятие «Хабаровское пассажирское автотранспортное предприятие №1» города Хабаровска (сокращённое название - МУП «ХПАТП №1»).
Цель работы – совершенствование организации работ на агрегатном участке МУП «ХПАТП №1» г. Хабаровска.
В ходе работы анализируется производственно- хозяйственная деятельность предприятия рассматривается организация управления предприятием. Производится расчёт производственной программы необходимого количества рабочих постов площадей производственных и вспомогательных помещений. Решаются вопросы совершенствования организации работ на агрегатном участке. Разработан универсальный стенд для выпрессовки подшипников крестовин карданных передач. Решаются вопросы охраны труда и экологии. Рассчитывается экономическая эффективность от внедрения стенда для выпресовки подшипников крестовин карданных передач на агрегатном участке.
СПЕЦИФИКАЦИЯ ОБОРУДОВАНИЯ.dwg

обозначение документа
Ведомость оборудования
Стеллаж для деталей и инструмента
Железный ящик для выбракованных деталей
Ванна для мойки мелких деталей
Пресс гидравлический вертикальный (40 т.)
Стол для контроля и сортировки деталей
Сттенд для выпрессовки подшипников крестовин карданных передач
Станок точильно-шлифовальный
Стенд для обкатки и испытания ГУР и насосов ГУР
Стенд для обкатки мостов и главной передачи
Подвесная кран-балка
Стенд для ремонта редукторов задних мостов
Стенд для разборки-сборки КП
Стенд для ремонта передних и задних мостов
Ларь для обтирочных материалов
Станок для проточки тормозных дисков и барабанов
Настольно-сверлильный станок
ВКР 960234.00.00.000
Бак маслораздаточный
Бак для заправки тормозной жидкостью
Верстак автослесаря 1200&E600
Ящик для инструмента 1800
Подъёмник одностоечный 800
Тележка слесаря по ремонту двигателей
Ванна для слива масла на роликах
Тедежка для демонтажа колес автомобиля
Стелаж для деталей 1000
Подставка под двигатель 1100
Подъемный механизм для снятия агрегатов
с грузовых автомобилей
Стенд для проверки электрооборудования
Кран-балка подвесная
Тележка для снятия и установки двигателей
Комплект инструмента (135 предметов)
собственного производства
Набор автомеханика (144 предмета)
Спецификация оборудования
Экспликация Произв корпус.dwg

Участок ремонта агрегатов
Начальник мастерских
Участок ремонта топливной аппаратуры
Участок аргонно-дуговой сварки
Участок вулканизации камер и изготовления резино- технических изделий
Участок кузнечно рессорных и медницких работ
Участок ремонта тормозных колодок
Участок мойки агрегатов
Вентялиционная камера
Шиномонтажный участок
Неиспользуемые площади
Участок ремонта пневмосистем
Механический участок
Электротехнический участок
Аккумуляторный участок
ВКР 960234.00.00.000
Корпус производственный
Категория пожароопасности
Участок вулканизации камер и изготовления резино технических изделий
Автомобиле метса ожидания
ВКР.960234.00.00.000
Спецификация. Тиски.dwg

Уч-к ремонта топливной
Неиспользуемые площади
ВКР 960234.03.00.000 СБ
ВКР 960234.03.00.002
ВКР 960234.03.00.001
ВКР 960234.03.00.004
ВКР 960234.03.00.000 CБ
Болт М8-6gх8.58.016 ГОСТ 7796-70
ВКР 960234.03.00.003
Шайба 8 65 Г ГОСТ 6958-78
ВКР 960234.00.00.00 СБ
Спецификация. Держатель.dwg

Уч-к ремонта топливной
Неиспользуемые площади
ВКР 960234.01.03.000 СБ
ВКР 960234.01.03.001
ВКР 960234.01.03.002
ВКР 960234.01.03.003
Шайба 14 65 Г ГОСТ 6402-70
ВКР 960234.04.00.000 СБ
ВКР 960234.04.00.001
ВКР 960234.04.00.002
ВКР 960234.04.00.003
ВКР 960234.04.00.004
ВКР 960234.00.00.00 СБ
Спецификация. Стенд.dwg

Уч-к ремонта топливной
Неиспользуемые площади
ВКР 960234.01.00.000 СБ
ВКР 960234.02.00.000 СБ
ВКР 960234.03.00.000 СБ
ВКР 960234.00.00.000 ПЗ
Пояснительная записка
Болт М10-6gх35.58.016 ГОСТ 7796-70
ВКР 960234.04.00.000 СБ
ВКР 960234.00.00.000 CБ
ВКР 960234.00.00.005
ВКР 960234.00.00.006
ВКР 960234.00.00.007
ВКР 960234.00.00.000 СБ
Двигатель 4А80В ГОСТ 19523-74
Стенд для выпрессовки игольчатых подшипников крестовин карданных валов
Гайка М16-6Н.5 ГОСТ 15521-70
Гайка М20x2 - 74.05.05 ГОСТ 11871-88
Шайба 16 65 Г ГОСТ 6402-70
Шпонка 18х11х36 ГОСТ 23360-78
Болт М10-6gх25.58.016 ГОСТ 7796-70
Шайба 10 65 Г ГОСТ 6958-78
ВКР 960234.00.00.008
Болт М12-6gх25.58.016 ГОСТ 7796-70
Гайка М12-6Н.5 ГОСТ 15521-70
Болт 002-0589 У ГОСТ 1472-69
Ось 1 -20 h8x55 Cт3сп. ГОСТ 9650-80
Шайба ШЕЗ-20 МН 787-60
Шайба 12 65 Г ГОСТ 6958-78
Болт М10-6gх20.58.016 ГОСТ 7796-70
Болт М8-6gх40.58.016 ГОСТ 7796-70
Болт М8-6gх30.58.016 ГОСТ 7796-70
Болт 12-6gх70.58.016 ГОСТ 7796-70
Гайка М 10 - 6H.5 ГОСТ 15521-70
Гайка М 8- 6H.5 ГОСТ 15521-70
Гайка М 12 - 6H.5 ГОСТ 15521-70
Гайка М 20x2 - 74.05.05 ГОСТ 11871-88
Двигатель4 А 80 В ГОСТ 19523-74
Ось 1 - 20 h8x55 Ст ГОСТ 6402-70
Шайба 10.65 Г ГОСТ 6402-70
Шайба A 8.01.08 кп.019 ГОСТ 6958-78
Шайба 8 65 Г ГОСТ 6402-70
Шайба 12.01.08 кп.05 ГОСТ 6958-78
Шайба 20.01.08 кп. 05 ГОСТ 6958-78
Шайба 12 65 Г ГОСТ 6402-70
Шплинт 10x28.3036 ГОСТ 397-79
IШпонка 18x11x36 ГОСТ 23360-78
ВКР 960234.00.00.00 СБ
Спецификация. Силовой узел.dwg

Уч-к ремонта топливной
Неиспользуемые площади
ВКР 960234.02.00.001
ВКР 960234.02.00.000 СБ
Стакан шарикового подшипника
Стакан под конический подшипник
Гайка грузового винта
ВКР 960234.02.00.000 CБ
Болт М 14-6gx40.58.016
Шайба 14 65 Г ГОСТ 6402-70
Штифт 2.6х20 ГОСТ 3128-70
Втулка А 4252х50 ГОСТ 24833-81
Подшипник 209 ГОСТ 8338-75
Болт М 16-6gх60.58.016 ГОСТ 7796-70
Шайба 8 65 Г ГОСТ 6402-70
Подшипник 7312 А ГОСТ 27365-87
Гайка М 16-6Н ГОСТ 5915-70
Штифт 2.8х40 ГОСТ 3128-70
Гайка М 8-6Н ГОСТ 5915-70
ВКР 960234.02.00.002
ВКР 960234.02.00.004
ВКР 960234.02.00.005
ВКР 960234.02.00.006
ВКР 960234.02.00.007
ВКР 960234.02.00.008
ВКР 960234.02.00.009
ВКР 960234.02.00.010
ВКР 960234.02.00.011
ВКР 960234.02.00.003
Шайба 16 65 Г ГОСТ 6402-70
ВКР 960234.00.00.00 СБ
1. Лист 1 ТЭО.dwg

технико-экономические
ТОГУ q*; кафедра ТЭРА
- Чистая прибыль (убыток)
- Валовая прибыль (убыток)
Рисунок 1 - Динамика доходов
Рисунок 3 - Динамика себестоимости
Материальные затраты - 17
Затраты на оплату труда - 12
Отчисления на социальные нужды - 3
Амортизационные отчисления - 0
Рисунок 6 - Структура себестоимости
Рисунок 2 - Динамика прибыли
Рисунок 4 - Динамика рентабельности
Рисунок 5 - Динамика затрат ремонтного фонда
ВКР 960234.00.00.000
Рисунок 1.10 - Структура транспортного парка по маркам
Рисунок 1.11 - Динамика коэффициента технической готовностии
Рисунок 1.12 - Динамика коэффициента выпуска на линию
Рисунок 1.13 - Динамика общегодового пробега
Рисунок 1.14 - Динамика простоев в ремонте на один автомобиль
2. Лист 2 ТЭО.dwg

ВКР 960234.00.00.000
Рисунок 1 - Динамика объема перевозок
Рисунок 3 - Динамика объема i0
Рисунок 5 - Динамика подвижного состава
Рисунок 2 - Динамика коэффициента технической готовностии
Рисунок 4 - Динамика простоев в ремонте на один автомобиль
Рисунок 6 - Динамика общегодового пробега
технико-эксплуатационные
4. Агрегатный со всякими там линиями.dwg

ТОГУ q*; кафедра ТЭРА
Корпус производственный
ВКР 960234.00.00.000.
ВКР 960234.00.00.000
Начальник мастерских
Зона текущего ремонта
Плита железобетонная
7. Стенд для выпресовки (распечатать).dwg
Стенд для выпрессовки подшипников крестовин карданных передач
ВКР 960234.00.00.000 СБ
Стенд для выпрессовки игольчатых подшипников крестовин карданных валов
подвижное соединения смазать смазкой Литол-24 ГОСТ-21150-87 2. Все болтовые соединения затянуть моментом 150 200 H м 3. Ремень между поз. 6 и 7 непоказан
9. Карта труда.dwg

ТОГУ q*; кафедра ТЭРА
Корпус производственный
ВКР 960234.00.00.000.
ВКР 430282.00.00.000.
на рабочем месте слесаря по ремонту
карданный вал в сборе
выпрессовка подшипников
крестовин карданных
Оплата труда производится по сдельно-премиальной системе
Показатели премирования устанавливаются как за количественные
так и за качественные результаты работы
Нанести метки определяющее взаимное расположение деталей
Установить в тиски карданный вал
Снять стопорные кольца
Установить карданный вал одной из вилок карданного шарнира
Через специальную втулку штоком пресса переместить другую вилку
Пространственная организация рабочего места
Оборудование и оснастка
Расположение предметов
Технологическое оборудование и
Стенд для выпрессовки игольчатых
Набор инструментов из 185 предметов
Организационная оснастка
Шкаф для инструмента
Функции обслуживания
Производственный инструктаж
Обеспечение рабочего места материалами
Межремонтное профилактическое обслуживание
Виды самообслуживания
По факту поступления заказа
Раз в месяц по графику
Раскладка средств труда в зоне
Проверка оборудования и техно-
логической оснастки;
Уборка рабочего места.
неблагоприятных условий
Освещeнность комбинированная
Загазованность окисью углерода (СО)
Загазованность серной кислотой
Температура: а) в тeплый период года
б) в холодный период года
Влажность относительная:
а) в теплый период года
Скорость движения воздуха:
Допускаемые нормативные значения
Люминесцентная - 200 лк
Люминесцентная - 400 лк
с кратностью обмена воздуха К=5
Режим труда и отдыха
Распределение регламентированных перерывов
Трехминутный перерыв в начале первого часа рабочего дня
Десятиминутный перерыв на 55-ой минуте второго часа работы
60-ти минутный перерыв на обед
в конце четвертого часа рабочего дня
Десятиминутный перерыв на 50-ой минуте седьмого часа работы
Режим рабочей недели- пятидневный
Требования к состоянию здоровья
комплект на 12 месяцев
Процент выполнения нормы труда 100%
Рабочее время 480 мин.
Оперативное время 422 мин.
Обслуживание рабочего места 15 мин.
Подготовительно-заключительные работы 20 мин.
Слесарь-авторемонтник
В соответствии с приказом Министерства здравоохранения
РФ N 10856 от 27.05.96 г
Структура рабочего времени
ВКР 960234.00.00.000
шарнира вниз до упора в крестовину
Повернуть вилку шарнира на 180
Переместить другой конец вилки вниз до упора в крестовину
подшипников крестовин карданных
Установить другую втулку на шип крестовины
Переместить вилку шарнира вниз до выпрссовки подшипника
Плита железобетонная
10. ЭКОНОМИКА.dwg
Показатели проекта технико-экономические
Технико - экономические показатели проекта
Коэффициент технической готовности
Численность ремонтных рабочих
Стоимость основных фондов
Экономический эффект
Годовая трудоемкость работ
Фонд заработной платы
Единый социальный налог
Дополнительные затраты
- амортизационные отчисления
- затраты на электроэнергию
Плита железобетонная
ВКР 960117.00.00.000
технико-экономические
8. Силовой узел дубль четыре.dwg

ВКР 960234.00.00.000
Поверхности соединения "корпус-крышка" перед сборкой покрыть уплотнительной пастой типа герметик 2. После сборки грузовой винт должен проворачиваться свободно
без стуков и заеданий
ВКР 960234.00.00.000 СБ
ВКР 960234.02.00.000 СБ
6. Деталировка с линиями.dwg
ТОГУ q*; кафедра ТЭРА
Корпус производственный
ВКР 960234.00.00.000.
ВКР 960234.00.00.000
ВКР 960234.02.00.000
25 28 HRC 2. Неуказанные допуски формы и расположения по ГОСТ 25068-81
Неуказанные предельные отклонения размеров отверстий Н 8; остальные JT122 по ГОСТ 25670-83 3. Неуказанные допуски формы и расположения по ГОСТ 25068 - 81
Неуказанные предельные отклонения размеров атверстий Н 8; остальные JT122 по ГОСТ 25670-83 3. Неуказанные допуски формы и расположения по ГОСТ 25068 - 81
Перед сборкой смазать трущиеся поверхности поз. 1;4 смазкой Литол-24 ГОСТ 21130-75
ВКР 960234.03.00.000 СБ
ВКР 960234.03.00.002
ВКР 960234.05.00.001
ВКР 960234.02.00.004
ВКР 960234.04.00.003
ВКР 960234.04.00.001
Неуказанные предельные отклонения размеров отверстий Н 8; остальные JT122 по ГОСТ 25670-83
Неуказанные предельные отклонения размеров отверстий Н8; остальные JT12 2
Неуказанные допуски формы и расположения по ГОСТ 25068-81
Неуказанные предельные отклонения размеров отверстий Н8; остальные JT122 по ГОСТ 25670-83
Формовочные уклоны 1°
x-H-MБ ГОСТ 4543-71
Плита железобетонная
5. Аналоги-сравнение (распечатать).dwg

Стенды и приспособления для выпрессовки игольчатых подшипников крестовин карданных валов
Риссунок 2 - Пресс модель Р-223
- опорная плита; 2 - рама; 3 - гидроцилиндр; 4 - насосная станция
Рисунок 1 - Стенд модель 3025
Риссунок 3 - Пресс гидравлический ПГП-20
- поперечная станина; 2 - стойка; 3 - поперечная станина; 4 - изделие; 5 - прижим; 6 - призма; 7 - пневматический кран; 8 - превмоцилиндр; 9 - корыто; 10 - уголок
- тиски; 2 - держатель; 3 - гидроцилиндр; 4 - насосная станция; 5 - рама
Риссунок 4 - Съемник крестовин карданных валов СВК1
- рукоятка; 2 - корпус; 3 - винт нажимной
3. ПРОИЗВОД. КОРПУС.dwg

ТОГУ q*; кафедра ТЭРА
Корпус производственный
ВКР 960234.00.00.000.
ВКР 430282.00.00.000
ВКР 960234.00.00.000
Плита железобетонная
1. ДИПЛОМ ВСЕ СВЕДЕНО с рамкой.doc
1 Общая характеристика предприятия10
2 Анализ технико-экономических и финансовых показателей12
3 Анализ технико-эксплуатационных показателей34
4 Характеристика производственно-технической базы44
5 Общие выводы по анализу производственно-хозяйственной деятельности46
6 Рекомендации по совершенствованию деятельности предприятия48
ТЕХНОЛОГИЧЕСКИЙ РАСЧЕТ51
1 Корректировка нормативной периодичности ТО и КР51
2 Расчёт производственной программы по количеству воздействий56
3 Количество диагностических воздействий за год по маркам автомобилей61
4 Расчет годового объема работ по ТО ТР и самообслуживанию64
5 Распределение объема работ ТО и ТР и расчёт численности производственных рабочих70
6 Уточнённый расчёт агрегатного участка78
ОРГАНИЗАЦИОННАЯ ЧАСТЬ88
1 Производственная структура предприятия88
2 Структура управления производством91
3 Метод организации производства ТО и ТР94
4 Описание и схема производственного процесса автотранспортного предприятия98
5 Описание информационного обеспечения100
6 Материально-техническое обеспечение102
7 Управление качеством производства103
8 Организация технологического процесса на агрегатном участке104
9 Организация труда слесаря105
КОНСТРУКТОРСКАЯ ЧАСТЬ111
1 Анализ существующих конструкций111
2 Разработка технического задания и кинематической схемы проектируемого стенда120
3 Проектный расчет стенда123
4 Описание работы стенда140
5 Правила безопасности и эксплуатации стенда142
ОХРАНА ТРУДА И ТЕХНИКА БЕЗОПАСНОСТИ144
1 Анализ условий труда145
2 Мероприятия по повышению безопасности и улучшений условий труда152
3 Меры безопасности при слесарных работах154
4 Расчет вентиляции156
5 Расчет естественного освещения157
6 Расчет искусственного освещения158
7 Пожарная безопасность162
8 Охрана окружающей среды и экономия материальных ресурсов165
ЭКОНОМИЧЕСКАЯ ЧАСТЬ167
1 Определение суммы дополнительных капитальных вложений168
2 Определение экономического эффекта174
3 Определение срока окупаемости дополнительных капитальных вложений178
СПИСОК ИСПОЛЬЗОВАННЫХ ИСТОЧНИКОВ186
Автомобильный пассажирский транспорт играет важную роль в удовлетворении повседневной потребности населения в транспортных услугах. Транспортный комплекс Российской Федерации насчитывает в своем составе 2078 автотранспортных предприятий осуществляющих пассажирские перевозки. На территории Российской Федерации действует 32281 автобусный маршрут в т.ч. 9576 - городских 16115 - пригородных 6482 - междугородных.
В 2009 г. по данным Хабаровскстата транспортом Хабаровского края было перевезено 2144 млн. чел. из них автобусным транспортом было перевезено 1735 млн.чел. или 81% от общего объема перевозок пассажиров всех видов пассажирского транспорта. Для сравнения трамвайным транспортом было перевезено всего 268 млн. чел. или 125%.
Муниципальное унитарное предприятие «Хабаровское пассажирское автотранспортное предприятие №1» (сокращенное название МУП «ХПАТП №1»)обеспечивает около половины пассажирских перевозок по городским маршрутам обслуживая при этом около 50 маршрутов.
В процессе эксплуатации автомобиля его конструктивные элементы под влиянием сил трения и окружающей среды подвергаются физическому износу. Для поддержания автомобилей в работоспособном состоянии необходимо планомерное осуществление целого комплекса мероприятий включающих в себя техническое обслуживание текущий и капитальный ремонт с периодической заменой и восстановлением изношенных деталей и узлов.
Поддержание работоспособности автомобиля требует высоких технических знаний и специальных технологий. Есть такие работы по обслуживанию автомобиля которые можно выполнить только при помощи специального оборудования инструментов и приспособлений и при наличии соответствующей квалификации исполнителя.
Особое место в совокупности мероприятий по поддержанию автомобилей в исправном состоянии занимает ремонт агрегатов и узлов который является одним из наиболее существенных элементов системы организационных и технических мероприятий призванной обеспечить работоспособность подвижного состава автомобильного транспорта.
Объектом исследования в настоящей выпускной квалификационной работе является МУП «ХПАТП №1» г. Хабаровска.
Целью выпускной квалификационной работы является совершенствованию организации работ на агрегатном участке МУП «ХПАТП №1» г. Хабаровска.
Для достижения поставленной цели необходимо решить следующие задачи:
- проанализировать экономические финансовые и эксплуатационные показатели деятельности предприятия;
- рассчитать производственную программу объем работ численность производственных рабочих количество постов ТО и ТР рассчитать агрегатный участок;
- проанализировать организационную структуру предприятия;
- усовершенствовать стенд для выпресовки игольчатых подшипников крестовин карданных валов;
- проанализировать условия труда на агрегатном участке;
- оценить эффективность предложенных решений.
ТЕХНИКО-ЭКОНОМИЧЕСКОЕ ОБОСНОВАНИЕ
1 Общая характеристика предприятия
В настоящее время Муниципальное унитарное предприятие города Хабаровска «Хабаровское пассажирское автотранспортное предприятие №1» (сокращенное название МУП г. Хабаровска «ХПАТП-1») является муниципальным унитарным предприятием действующим на основании Гражданского Кодекса Российской Федерации и других законодательных и нормативных актов Российской Федерации а также Устава предприятия. Учредителем предприятия выступает от имени администрации города Департамент муниципальной собственности г. Хабаровска. Предприятие является коммерческой организацией не наделённой правом собственности на закреплённое за ней имущество.
Свою историю МУП «Хабаровское автотранспортное предприятия №1» начинает в 1971 г. на базе грузового автохозяйства была сформирована одна автоколонна из 55 автобусов ЗИЛ-158 для обеспечения городских пассажирских перевозок с численностью 405 человек работающих. И в этом же году грузовое предприятие реорганизовано в автобусный парк и становится филиалом № 1 Хабаровского производственного объединения пассажирского автотранспорта (ХПОПАТ).
С 1971 г. по 1978 г. в качестве филиала автобусного парка ХПОПАТ насчитывает уже 155 единиц подвижного состава обслуживающего 17 маршрутов города Хабаровска. В 1978 году приказом Хабаровского автотранспортного управления за N2 127 от 27 июля l978 г. филиал № 1 ХПОПАТ переименован в самостоятельное предприятие «Хабаровское пассажирское автотранспортное предприятие №1». В это время парк укомплектован автобусами марки ЛиАЗ-677 в количестве 134 единиц с численностью коллектива 818 человек и обслуживает 12 городских и 7 пригородных маршрутов.
В августе 2003 г. в связи с банкротством ХПАТП-3 всё его имущество в том числе здания и автотранспорт переходит под руководство ХПАТП-1. Таким образом в составе ХПАТП-1 образовалось новое структурное подразделение – автоколонна «Южная» расположенное в Южном микрорайоне г. Хабаровска по улице Панфиловцев - 44.
В 2005 г. ХПАТП-1 с Проспекта 60 лет Октября переехало на территорию ликвидированного предприятия ХПОПАТ на улицу Промышленную. Территория на Проспекте 60 лет Октября была отдана под другие муниципальные не автотранспортные предприятия а всё имущество ХПОПАТ в том числе и автотранспорт было отдано под руководство ХПАТП-1.
Основными целями и задачами деятельности предприятия является осуществление перевозок пассажиров и оказание услуг по перевозке населению и организациям выполнение иных работ (услуг) а также извлечением прибыли от своей деятельности.
В соответствии с основными целями и задачами стоящими перед предприятием оно вправе осуществлять следующие виды деятельности:
- организация и осуществление перевозки пассажиров;
- обслуживание предприятий организаций и учреждений имеющих автомобили;
- оказание услуг населению организациям и предприятиям в ремонте и обслуживании автомобилей отечественных и иностранных марок осуществлении моечных покрасочных и других видов работ.
2 Анализ технико-экономических и финансовых показателей
Целью анализа производственно-хозяйственной деятельности предприятия являются выявление и оценка технико-экономических результатов всех сторон деятельности предприятия определение напряженности плановых заданий и эффективности их выполнения вскрытия резервов использования материальных финансовых и трудовых ресурсов а также подготовка и повышение обоснованности текущих и перспективных решений.
Для того чтобы оценить деятельность автотранспортного предприятия применяют систему частных и обобщающих показателей. Частные показатели позволяют оценить отдельные стороны работы подвижного состава. Эти показатели входят в состав таких обобщающих показателей как производительность работ автомобилей себестоимость перевозок. С помощью обобщающих показателей оцениваются окончательные результаты работы предприятия.
К основным экономическим показателям работы предприятия относятся: объем перевозок; пассажирооборот доходы от перевозок; себестоимость; прибыль; рентабельность и др.
Динамика экономических показателей характеризуется абсолютным приростом темпом роста темпом прироста.
Абсолютный прирост определяется вычитанием из последующего уровня объёма перевозок предыдущего уровня принятого за базис по формуле 1 c.5.
где - показатель за анализируемый период;
- показатель базисный период.
Темп роста определяем по формуле 1 c.5.
Темп прироста определяем по формуле 1 c.5.
Если значение темпа прироста получится со знаком минус значит в анализируемом периоде предприятие ухудшило результат по рассматриваемому показателю.
Абсолютную величину 1% роста определяем по формуле 1 c.5.
Объем перевозок (Q) и пассажирооборот (P) являются основными показателями характеризующими работу автотранспортного предприятия. В таблице 1.1 представлена динамика объёма перевозок и пассажирооборот предприятия.
Таблица 1.1 – Объем перевозок и пассажирооборот
Объем перевозок млн. чел.
Абсолютное значение одного процента прироста млн.чел.
Пассажирооборот млн.пасскм.
Темп прироста базисный %
Темп прироста цепной %
Абсолютное значение одного процента прироста млн.пасскм.
Для предприятия занимающегося перевозками пассажиров объем перевозок определяется количеством перевезенных человек. В свою очередь пассажирооборот — это показатель работы пассажирского транспорта вычисляемый как произведение количества перевезенных пассажиров на расстояние их перевозки выражается в пассажиро-километрах. Объем перевозок и пассажирооборот отражают эффективность использования автобусов.
Динамика объема перевозок и пассажирооборота представлена на рисунке 1.1.
Рисунок 1.1 – Динамика объема перевозок и пассажирооборота
Муниципальное предприятие г. Хабаровска «ХПАТП №1» обеспечивает около половины пассажирских перевозок в городе. Данные таблицы 1.1 и рисунок 1.1 наглядно демонстрируют что с 2004 г. по 2006 г. наблюдается устойчивая динамика сокращения численности перевезенных пассажиров. Объем перевозок предприятия в этот период сократился на 458% или на 2448 млн. человек а пассажирооборот на 266% или на 10272 млн. пасскм. Причинами снижения объемов перевозок в основном явились сокращение количества поездок льготных категорий граждан в результате введения единых социальных проездных билетов сокращение парка автобусов а так же снижения их технической готовности для выпуска на линию в связи их значительным износом.
Следует отметить что из общей численности перевезенных пассажиров около 60% относятся к льготным категориям граждан. В свою очередь развитие маршрутных такси появление частных лиц и организаций предлагающих свои услуги по перевозке пассажиров привело к перераспределению платежеспособных пассажиров на пользование коммерческим транспортом. В настоящее время наблюдается устойчивая динамика роста коммерческих автотранспортных перевозчиков. По данным статистики Хабаровского края если в 2003 г. перевозку пассажиров осуществляли 353 коммерческих автобуса то в 2006 г. эту услугу оказывали на 49 автобусов больше.
Начиная с 2006 г. наблюдается рост объема перевозок и пассажирооборота. В 2009 г. объем перевозок вырос по сравнению с 2006 г. на 787% или на 2279 млн. чел. аналогично пассажирооборот вырос на 338% или на 9585 млн. пасскм. Это было вызвано прежде всего тем что повысился коэффициент технической готовности за счёт списания старых и приобретения новых более надёжных моделей. Однако заметим что в 2009 г. значение этих показателей не достигло уровня 2004 г.
Объем перевозок и объем доходов (Д) являются взаимозависимыми показателями. Доходы любого автотранспортного предприятия складываются из доходов от перевозок сдачи в аренду помещений и прочих работ и услуг (оказание техпомощи на линии техническое обслуживание и ремонт автомобилей для других предприятий и т. п.).
Рисунок 1.2 – Динамика доходов
Следует отметить что за анализируемый период динамика доходов предприятия имела положительную динамику что следует оценить положительно (рисунок 1.2 таблица 1.2).
Из данных таблицы 1.2 видно что доходы предприятия за период с 2004 г. по 2009 г. выросли в 26 раза или на 45873 млн. р. Среднегодовой темп роста доходов предприятия рассчитанный по среднеарифметической взвешенной составил 14%.
Таблица 1.2 - Доходы предприятия
Темпы роста (спада) %
Доходы от перевозок — основная составляющая общей суммы доходов предприятия. Однако предприятие изыскивает возможности получения дополнительных доходов. Часть доходов предприятие получает за оказание различных платных услуг таких как заказные перевозки рекламные услуги стоянка мойка услуги технической службы и прочие. Также оказываются услуги коммерческим перевозчикам по эксплуатационным вопросам техническому обслуживанию медицинскому обслуживанию для этого предприятие имеет специализированную производственную базу квалифицированных специалистов и лицензию на эти виды работ услуг. В 2009 г. 84% доходов предприятие получило от маршрутных перевозок 155% от прочих услуг и 05% от заказанных перевозок.
Себестоимость (S) – важнейший показатель экономической эффективности деятельности автотранспортного предприятия отражающий все стороны хозяйственной деятельности и аккумулирующий результаты использования всех производственных ресурсов. От его уровня зависят финансовые результаты деятельности предприятия темпы расширенного воспроизводства финансовое состояние предприятия.
Себестоимость перевозок представляет собой денежное выражение затрат автотранспортного предприятия на выполнение транспортной работы.
Себестоимость перевозок на автомобильном транспорте – это затраты предприятия на перевозку пассажиров. В финансовой деятельности АТП на увеличение прибыли наибольшее влияние оказывает снижение расходов на производственную деятельность. Для достижения снижения затрат и уменьшения себестоимости перевозок все звенья управления автомобильным транспортом должны обеспечивать в своей деятельности экономию материальных трудовых и денежных ресурсов.
На рисунке 1.3. наглядно представлена динамика себестоимости предприятия.
Рисунок 1.3 – Динамика себестоимости
Основной задачей анализа себестоимости перевозок является выявление путей ее максимального снижения. Расходы предприятия в 2009 г. составили 72507 млн. р. и возросли к уровню 2004 г. 23 раза или на 4097 млн. р. (таблица 1.3).
Среднегодовой темп роста себестоимости составил 11% а среднегодовой темп роста доходов от эксплуатационной деятельности составил 13%. Таким образом доходы предприятия растут более быстрыми темпами чем себестоимость что следует оценить положительно.
Таблица 1.3 - Динамика себестоимости
Себестоимость предприятия за анализируемый период имеет тенденцию постепенного и постоянного увеличения однако в 2007 г. себестоимость предприятия сократилась по сравнению с 2006 г. на 13%. В 2008 г. себестоимость предприятия по сравнению с 2007 г. резко выросла на 5750%.
Причинами роста расходов являются увеличение цен на энергоресурсы коммунальные услуги горюче-смазочные материалы запасные части увеличение тарифной ставки оплаты труда и др. Средний возраст парка автомобилей увеличился что в свою очередь вызывает увеличение затрат на их техническое обслуживание и ремонт а также ведет к увеличению расхода топлива.
Данные о структуре затрат предприятия представлены на рисунке 1.4. Незначительный удельный вес в структуре затрат занимают амортизационные отчисления (в 2009 г. - 047%). Значительное место в структуре затрат занимают материальные затраты - 1796%. Материальные затраты включают стоимость израсходованных в процессе производства различного рода топливно-энергетических ресурсов и материалов запасных частей для ремонта и технического обслуживания подвижного состава автомобильной резины.
Рисунок 1.4 – Структура себестоимости
Наибольший удельный вес в структуре затрат предприятия занимаю прочие затраты – 5628%. Прочие затраты включают прежде всего затраты связанные с ремонтом автотранспортных средств.
Динамика затрат ремонтного фонда предприятия представлена в таблице 1.4 и на рисунке 1.5.
Таблица 1.4 - Динамика затрат на ремонт
Затраты на ремонт млн. р.
Объем затрат связанных с ремонтом за период с 2004 по 2009 г. вырос в 415 раза. Наибольший скачек затрат на ремонт произошел в 2009 г. к уровню предыдущего года на 4174% (рисунок 1.5).
Рисунок 1.5 – Динамика затрат на ремонт
Рост затрат на ремонт вызван старением активной части основных производственных фондов которое приводит к увеличению затрат на материалы повышению расхода горюче-смазочных материалов.
Большая доля затрат приходится на заработную плату - 1285%. Динамика фонда оплаты труда за период с 2004 по 2009 годы представлена в таблице 1.5 и на рисунке 1.6.
Рисунок 1.6 – Динамика производительности труда и фонда заработной платы
Таблица 1.5 – Динамика производительности труда фонда заработной платы
Фонд оплаты труда млн.р.
Темп роста базисный %
Производительность труда тыс.р.чел.
В свою очередь производительность труда за анализируемый период выросла в 233 раза (таблица 1.5). Среднегодовой темп роста производительности труда составил 1383% а фонда оплаты труда 1691%. Таким образом заработная плата растет более быстрыми темпами чем производительность труда что следует оценить отрицательно.
Финансовые результаты деятельности предприятия характеризуются суммой полученной прибыли и уровнем рентабельности. Чем больше величина прибыли и выше уровень рентабельности тем эффективнее функционирует предприятия тем устойчивее его финансовое состояние. Динамика прибыли и рентабельности предприятия представлена в таблице 1.6 и на рисунке 1.7.
Как показал вышеприведенный анализ начиная с 2004 г. по 2006 г. себестоимость деятельности предприятия превышала его доходы в результате за этот период предприятия имело убыток по основной деятельности. Наибольшая сумма убытка наблюдается в 2006 году в котором прирост убытков составил 38 млн. р. по сравнению с 2004 годом. Резкое увеличение суммы убытка в 2006 году произошло за счет того расходы предприятия превышали его доходы на 11%.
Рисунок 1.7 – Динамика прибыли предприятия
Начиная с 2007 г. предприятие по основной деятельности имело положительный финансовый результат (таблица 1.6) что следует оценить положительно. Однако в 2009 г. расходы предприятия от прочей деятельности значительно превысили как доходы так и валовую прибыль от основной деятельности в результате этого предприятие получило чистый убыток в сумме -1214 млн. р.
Таблица 1.6 – Прибыль и рентабельность деятельности
("-" убыток) предприятия млн. р.
Рентабельность продаж %
Рентабельность производства %
Рентабельность показатель определяющий уровень доходности бизнеса. Показатель рентабельности характеризует эффективность работы предприятия в целом доходность различных направлений деятельности. Этот показатель наиболее полно характеризует окончательные результаты хозяйствования потому что их величина показывает соотношение эффекта с наличными или потребленными ресурсами.
Существует множество показателей рентабельности: рентабельность продаж рентабельность основных фондов рентабельность собственного капитала рентабельность активов и т.д.
Рентабельность продаж (таблица 1.6) показывает долю прибыли в каждом заработанном рубле и рассчитывается по формуле 1.4.
где - чистая прибыль (прибыль после налогообложения) млн. р.;
- объем продаж (выручка) млн. р.
Рентабельность производства рассчитывается по формуле 1.5. Данный показатель показывает сколько предприятие имеет прибыли с каждого рубля затраченного на производство и реализацию продукции.
где - валовая прибыль (прибыль до налогообложения) млн. р.;
- затраты на производство и реализацию (себестоимость) млн. р.
Динамика рентабельности предприятия рассчитанная по валовой прибыли (таблица 1.6) представлена на рисунке 1.8.
Данные таблицы 1.8 и рисунок 1.6 демонстрируют что в период с 2004 г. по 2006 г. предприятие имело отрицательный уровень рентабельности. Начиная с 2007 г. по 2009 г. ситуация изменилась и уровень рентабельности рассчитанная по валовой прибыли был положительным. Положительный уровень рентабельности был достигнут за счет того что доходы предприятия превысили его расходы. В 2009 г. рентабельность производства составила 265%. Это значит что предприятие с каждого затраченного рубля имело 23 копейки прибыли однако рентабельность рассчитанная по чистой прибыли в 2009 г. была отрицательной т.к. деятельность предприятия в целом была убыточной.
Рисунок 1.8 – Динамика рентабельности
Основными источниками резервов увеличения суммы прибыли и роста рентабельности являются: увеличение объемов перевозок; снижение себестоимости; повышение тарифов на перевозки.
Финансовое состояние предприятия и его устойчивость в значительной степени зависят от того каким имуществом располагает предприятие в какие активы вложен капитал и какой доход они приносят.
Анализ источников формирования и размещения капитала имеет большое значение для предприятия.
Из таблицы 1.7 видно что наибольший удельный вес в структуре пассива предприятия на конец 2008 г. занимали краткосрочные обязательства. Собственный капитал предприятия в 2008 г. имел отрицательное значение из-за больших сумм непокрытого убытка. Данное обстоятельство свидетельствует о значительной зависимости предприятия от внешних инвесторов и кредиторов.
Таблица 1.7 – Структура пассива
Абсолютное изменение
Долгосрочные обязательства
Краткосрочные обязательства
В 2009 г. в структуре пассива наибольший удельный вес занимал капитал и резервы а доля обязательств перед кредиторами сократилась что следует оценить положительно.
В структуре заемного капитала большую долю занимают краткосрочные обязательства. По этой причине финансовое положение может стать неустойчивым так как с капиталами краткосрочного использования необходима постоянная оперативная работа: контроль за своевременным их возвратом и привлечение в оборот на непродолжительное время других капиталов. Заемный капитал предприятия формируется в основном за счет кредиторской задолженности. Доля долгосрочных обязательств в структуре заемного капитала в 2009 г. по сравнению с 2008 г. сократилась с 275% до 15% что следует оценить отрицательно (таблица 1.8).
Таблица 1.8 - Структура и динамика заемного капитала
Источник заемных средств
Долгосрочные обязательства
кредиторская задолженность
доходы будущих периодов
За год общая сумма кредиторской задолженности сократилась на 1163 млн. р. или на 195% что следует оценить как позитивную тенденцию. Однако доля кредиторской задолженности в общей структуре заемного капитала выросла почти на 1 процентный пункт что следует оценить отрицательно.
Предприятие имеет незначительную сумму дебиторской задолженность это обусловлено прежде всего спецификой деятельности предприятия которая предполагает предварительную оплату т.е. сначала оно получает деньги а затем предоставляет услуги по перевозке.
Сумма кредиторской задолженности предприятия значительно превышает дебиторскую. В 2009 г. кредиторская задолженность в 16 раз или на 4493 млн. р. превышала дебиторскую что следует оценить отрицательно так как если все кредиторы предъявят свои требования то погашение дебиторской задолженности практически ничем не поможет предприятию. Структура активов предприятия представлена в таблице 1.9.
Таблица 1.9 – Структура активов
В структуре активов предприятия наибольшую долю занимают оборотные активы (таблица 1.9). За год доля оборотных активов сократилась на 5715 % пункта а доля внеоборотных соответственно увеличилась на эту же величину. Это говорит о том что в структуре актива баланса неликвидных активов стало значительно больше что следует оценить как негативную тенденцию.
Структура внеобротных активов предприятия за анализируемый период изменилась незначительно. Внеоборотные активы предприятия формируется в основном за счет основных средств так в 2009 г. в общей структуре внеоборотных активов они занимали более 9991%. Отметим что сумма основных средств предприятия за анализируемый период выросла более чем в 16 раз это связано с тем что предприятие приняло на хозяйственное ведение имущество прекративших производственную деятельность OOO «Перевозчик №12» и «АРМ №12». У предприятия имеются долгосрочные финансовые вложения что говорит о том что предприятие осуществляет инвестиционную деятельность.
Общая сумма денежных средств предприятия за анализируемый период выросла на 2796% а запасов и краткосрочной дебиторской задолженности сократилась на 2603% и 6874% соответственно. Произошли изменения в структуре оборотных активов так доля краткосрочной дебиторской задолжности сократилась на 1610 % пункта а запасов и денежных средств выросла на 432 и 1517 % пункта.
Для оценки степени финансовой устойчивости и финансового риска необходимо рассчитать такие показатели как коэффициент финансовой автономии (или независимости) – удельный вес собственного капитала в общей валюте баланса; коэффициент финансовой зависимости – доля заемного капитала в общей валюте баланса; Чем выше уровень первого показателя и ниже второго тем устойчивее положение предприятия.
Оценка платежеспособности осуществляется на основе характеристики ликвидности оборотных активов которая определяются временем необходимым для превращения их в денежные средства. Чем меньше требуется времени для инкассации данного актива тем выше его ликвидность.
Данные таблицы 1.10 свидетельствуют о том что финансовое положение предприятие улучшилось. В 2008 г. коэффициент финансовой автономии имел отрицательное значение что говорит о том что предприятие находилось в критическом состоянии т.к. его собственные средства не могли покрыть убытки предприятия. В 2009 г. значение этого коэффициента составило 069 что следует оценить положительно.
Коэффициент финансовой зависимости в 2008 г. превышал единицу что свидетельствует о том что обязательства предприятия перед внешними кредиторами значительно превышали его собственный капитал (таблица 1.10). В 2009 г. этот показатель составил 02 что говорит о том что собственный капитал предприятия сможет покрыть все обязательства на 20%.
Таблица 1.10 – Показатели финансовой устойчивости и платежеспособность предприятия
Рекомендуемое значение
Коэффициент финансовой автономии
Коэффициент финансовой зависимости
Коэффициент текущей ликвидности
Для оценки ликвидности и платежеспособности предприятия рассчитаем коэффициент текущей ликвидности. Коэффициент текущей ликвидности рассчитывается как отношение всех оборотных активов к сумме краткосрочных финансовых обязательств; он показывает степень покрытия оборотными активами оборотных пассивов. В 2009 г. значение этого показателя составило – 043 что говорит о том что предприятие не может погасить свои краткосрочные обязательства за счет оборотных активов.
Анализ источников формирования и размещения капитала показал значительную зависимость предприятия от внешних инвесторов и кредиторов. Финансовое положение предприятия за анализируемый период улучшилось и в настоящее время находится в удовлетворительном состоянии.
3 Анализ технико-эксплуатационных показателей
Одним из важнейших факторов повышения эффективности деятельности предприятия является его обеспеченность основными фондами в необходимом количестве ассортименте и эффективное их использование.
Наибольший удельный вес более 31% в структуре основных фондов предприятия занимают транспортные средства как основного средства осуществления транспортной работы. Около 28% в структуре основных средств занимают машины и оборудования что объясняется спецификой производственной деятельности предприятия. Существенным является удельный вес сооружений и передаточных устройств более 20%.
Динамика численности подвижного состава предприятия представлена на рисунке 1.9.
Рисунок 1.9 – Динамика численности подвижного состава
Конкурентоспособность автотранспортного предприятия зависит от состояния производственной базы и соответствия парка подвижного состава условиям перевозок. На территории парка находятся автобусы различных марок и моделей.
Наибольшее количество автотранспортных средств наблюдается в 2005 году это связано с тем что в связи с ликвидацией «Хабаровского производственного объединения пассажирского автотранспорта» (ХПОПАТ) весь его подвижной состав был отдан под руководство «ХПАТП-1».
Уменьшение количества подвижного состава с 2006 по 2008 гг. связано со списанием старых автобусов и нехваткой средств на приобретение новых. Так в 2008 году предприятием было списано 30 автобусов. В 2009 г. численность автобусов выросла за счет того что были приобретены новые автобусы НЕФАЗ.
Рисунок 1.10 – Структура транспортного парка по маркам
На рисунке 1.10 представлена структура автобусов предприятия по маркам. Автобусный парк предприятия представлен машинами различных марок следует отметить что основная часть – более 70% представлена автобусами корейского производства DATWOO около 9% автобусами НЕФАЗ и более 5 % автобусами ЛиАЗ. Сохранились на предприятии и автобусы марок ПАЗ ЛАЗ и др.
Нужно отметить что в парке автобусов сохраняется высокая доля техники обладающей высокими расходами топлива и горюче-смазочных материалов запасных частей и низкой надежностью эксплуатации машин. Автобусы марки DAEWOO работают на дизельном топливе они экономичнее и дешевле других автобусов. Так например у ЛиАЗ-5256 – расход топлива 46 л100 км. а у DAEWOO - BS106 – 29 л100 км.
Руководство «ХПАТП-1» приняло решение постепенно вывести из эксплуатации старые автобусы марки ИКАРУС и ЛиАЗ-677. Так в 2008 году было списано 18 ЛиАЗов и 9 ИКАРУСов. Преобладание одной марки автобуса упрощает техническое обслуживание и ремонт автобусов работу материально технического обеспечения комплектацию квалифицированным персоналом.
Средний возраст парка уменьшился что следует оценить положительно. Причинами снижения среднего возраста автобусов является списание автобусов выработавших свой ресурс и пополнение парка новыми моделями корейских автобусов DAEWOO и НЕФАЗ.
Показателем характеризующим готовность подвижного состава к транспортной работе его техническое состояние является коэффициент технической готовности.
Коэффициент технической готовности можно рассчитать отношением автомобиле-дней простоя связанных с ТО и Р к общему числу автомобиле-дней в хозяйстве:
где - автомобиле-дни в хозяйстве;
- автомобиле-дни простоя в ремонте;
- автомобиле-дни простоя в техническом обслуживании.
Коэффициент технической готовности зависит от организации и качества выполнения технического обслуживания и ремонта автомобилей. Динамика коэффициента технической готовности представлена в таблице 1.11 и на рисунке 1.11.
Таблица 1.11 – Коэффициент технической готовности
Коэффициент технической готовности
Исправность автомобиля а значит и повышение коэффициента технической готовности зависят в значительной мере от водителя. Своевременное обнаружение и устранение неисправностей содержание автомобиля в исправном состоянии умелое вождение его и соблюдение правил технической эксплуатации являются факторами при помощи которых водитель может влиять на повышение коэффициента технической готовности.
Рисунок 1.11 – Динамика коэффициента технической готовности
Коэффициент технической готовности предприятия за анализируемый период имел тенденцию к увеличению что следует оценить положительно. В 2005 г. его значение было минимально это связано с отсутствием запасных частей на уже не выпускающиеся заводами-изготовителями автобусы устаревших марок ЛиАЗ-677 Икарус 250 Икарус 260 Икарус 280 и недостаточным финансированием.
В 2008 г. и 2009 г. наблюдается самое высокое значение коэффициента технической готовности (рисунок 1.11) это связано со списанием автобусов выработавших свой ресурс и значительным пополнением новыми моделями корейских автобусов DAEWOO у которых норма межремонтных пробегов значительно выше.
Выпуск подвижного состава на линию характеризуется коэффициентом выпуска.
Коэффициент выпуска представляет собой отношение автомобиле-дней в эксплуатации к календарному числу дней на этот период:
где - автомобиле-дни работы;
- календарное число дней работы АТП.
Динамика коэффициента выпуска представлена в таблице 1.12 и на рисунке 1.12.
Таблица 1.12 – Коэффициент выпуска автомобилей
Коэффициент выпуска автомобилей
Коэффициент выпуска в основном зависит от коэффициента технической готовности но обычно несколько меньше в связи с тем что некоторая часть исправных машин предприятия может простаивать по различным организационным причинам (болезнь водителей при отсутствии резерва непродуманное планирование машин в наряд на использование и т.д.). Поэтому задачи работников службы эксплуатации заключаются в ликвидации непроизводительных простоев.
Рисунок 1.12 – Коэффициент выпуска автомобилей на линию
За период с 2004 г. по 2008 г. коэффициент выпуска автомобилей имел тенденцию к увеличению (таблица 1.12 рисунок 1.12) что следует оценить положительно. Однако в 2009 г. произошло его сокращение что говорит о неэффективной работе службы эксплуатации.
Рост коэффициента выпуска происходил благодаря повышению организации работы отдела эксплуатации основной функцией которого является планирование работы маршрутов рейсов расписания потребного количества автобусов осуществление плана – графиков выхода автобусов на линии. Однако в 2009 г произошло сокращение коэффициента выпуска несмотря на то что коэффициент технической готовности оставался на достаточно высоком уровне.
Показатель общего годового пробега важный показатель деятельности автотранспортного предприятия. За период с 2004 г. по 2009 г. общий годовой пробег автобусов предприятия вырос на 2336% что следует оценить положительно (таблица 1.13).
Рост общего годового пробега за последние три года связан со списанием старых автобусов ЛиАЗ-677 которые часто ломались и сходили с линии и приобретением новых автобусов DAEWOO и НЕФАЗ. На рост общего пробега также повлияло повышение качества дорог и строительство новых развязок.
Рисунок 1.13 – Динамика общего годового пробега
Таблица 1.13 –Динамика общего годового пробега
Общий годовой пробег млн. км
В таблице 1.14 и на рисунке 1.14 представлена динамика дней простоя в ремонте на один автомобиль.
Таблица 1.14 - Динамика простоев в ремонте
Простои в ремонте на один автомобиль дн.
Сокращение дней простоя в ремонте связано с тем что совершенствовались формы организации и оплаты труда решением руководства было установлено дополнительное премирование за пробег без сходов до очередного ТО-1 были ужесточены требования к качеству проведенных обслуживаний.
Наглядно на рисунке 1.14 представлена динамика простоев в ремонте на один автомобиль. За анализируемый период число дней простоя в ремонте имел тенденцию к сокращению что следует оценить положительно.
Главным фактором снижения дней простоя является списание автобусов выработавших свой ресурс и пополнения парк новыми моделями корейских автобусов DAEWOO у которых норма межремонтных пробегов значительно выше.
Рисунок 1.14 – Динамика дней простоя в ремонте
Несмотря на то что коэффициент технической готовности находится на достаточно высоком уровне сокращаются дни простоев в ремонте растет общий годовой пробег предприятие недостаточно полно использует свои производственные мощности что в конечном итоге приводит к увеличению доли постоянных издержек.
Основными факторами снижающими технико-эксплуатационные показатели предприятия являются устаревшее технологическое оборудование и низкий уровень механизации трудоемких и тяжелых процессов. Вследствие того что предприятие не имеет технологического оборудования в достаточном количестве и необходимого назначения происходят долгие простои в ТР некачественный ремонт частые сходы с линии подвижного состава что в конечном счете и приводит к снижению планируемой прибыли.
Для улучшения показателей работы подвижного состава необходимо повышать качество его технического обслуживания и ремонта совершенствовать организацию перевозок (их планирование маршруты движения) сокращать непроизводительные простои и обновлять технологическое оборудование.
4 Характеристика производственно-технической базы
Производственно-техническая база автопредприятий предназначена для хранения подвижного состава и проведения технического обслуживания и ремонта автомобилей.
За предприятием закреплен участок земли площадью 20995.5 кв.м. Плотность застройки «ХПАТП-1» составляет 47%. На территории предприятия находятся следующие строения: административное здание; производственный корпус; открытые стоянки для хранения автомобилей в теплое время года; тёплые гаражи для хранения автомобилей в холодное время года; контрольно- пропускной пункт с диспетчерской; автозаправочная станция; профилакторий и другие вспомогательные сооружения.
В состав производственно-складских помещений входят зоны ТО и ТР производственные участки ТР склады а также технические помещения энергетических и санитарно-технических служб и устройств (компрессорные трансформаторные насосные вентиляционные и т.п.). Складские помещения на ХПАТП предусматриваются для хранения: двигателей агрегатов узлов непожароопасных материалов металлов инструмента ценного утиля; автомобильных шин (камер и покрышек); смазочных материалов; лакокрасочных материалов; твердых сгораемых материалов (бумага картон ветошь).
В состав площадей административно-бытовых помещений предприятия входят: санитарно-бытовые помещения пункты общественного питания здравоохранения (медицинские пункты) культурного обслуживания управления помещения для учебных занятий и общественных организаций.
В настоящее время производственно - техническая база предприятия не соответствует современным нормам. Большая часть оборудования установленного на производственных участках и в зоне текущего ремонта изношена на 90% в результате чего оно не в состоянии обеспечить требуемого качества ремонта различных узлов и агрегатов автомобилей. Кроме того использование подъёмного оборудования выработавшего свой ресурс опасно для жизни и здоровья ремонтных рабочих.
Модернизация материальной базы происходит очень медленно её оснащенность технологическим оборудованием составляет не более 40%. Посты ТР оснащены всего двумя выработавшими свой ресурс канавными подъёмниками способными вывешивать лишь один из мостов. Диагностирование Д-2 для выявления перед ТО-2 неисправностей и скрытых повреждений не проводится из-за отсутствия подъёмного и другого оборудования.
В настоящее время необходимо решать вопросы об оснащенности постов и участков ремонтным инструментом и специализированным оборудованием позволяющим повысить безопасность и производительность труда.
5 Общие выводы по анализу производственно-хозяйственной деятельности
Анализ производственно-хозяйственной деятельности Муниципального предприятия г. Хабаровска «ХПАТП №1» показал что происходит улучшение по ряду финансово-экономических показателей так например за анализируемый период выросли доходы объем перевозок и пассажирооборот улучшились и ряд финансовых показателей. Однако положение предприятия характеризуется все еще как сложное.
Одна из наиболее значимых проблем с которыми сталкиваются предприятия пассажирского транспорта - обновление парка подвижного состава. Обновление авто транспортного парка предприятия происходит довольно медленными темпами.
Начисляемые амортизационные отчисления не позволяют аккумулировать финансовые ресурсы в объемах достаточных для восстановления списываемого парка. Устаревший парк автомобилей способствует росту трудоемкости технического обслуживания и ремонта уменьшению надежность подвижного состава дополнительным простоям в ремонте и повышенному расходу запчастей.
Начиная с 2004 г. по 2006 г. наблюдается устойчивая динамика сокращения численности перевезенных пассажиров. Объем перевозок предприятия в этот период сократился на 458%. Причинами снижения объемов перевозок явились введение единых социальных проездных билетов для «льготных» категорий пассажиров и сокращение парка автобусов большой и особо большой вместимости государственных и муниципальных предприятий. Развитие в большинстве городов сети маршрутных такси привело к перераспределению платежеспособных пассажиров. Начиная с 2006 г. наблюдается рост объема перевозок что следует оценить положительно. Так в 2009 г. объем перевозок вырос по сравнению с 2006 г. на 787%.
Доходы от проезда пассажиров в 2009 г. выросли в 26 раза к уровню 2004 г.
Общие эксплуатационные расходы по выполнению перевозок автобусным пассажирским транспортом предприятия в 2009 г. по данным бухгалтерской отчетности составляют 72507 млн. р. что в 23 раза больше чем в 2004 г.
Начиная с 2007 г. предприятие начало получать положительный финансовый результат по основной деятельности. Отметим что наибольший уровень рентабельности был в 2007 г. в этом году предприятие на 1 рубль затрат получило 7 копеек прибыли. В 2009 г. несмотря на то что валовая прибыль была положительная показатель чистой прибыли оказался отрицательным.
Анализ источников формирования и размещения капитала показал что зависимость предприятия от внешних инвесторов и кредиторов высокая однако наметилось ряд улучшений.
Субсидии и дотации из средств бюджетов разных уровней составили 22859 млн. р. что позволит компенсировать часть эксплуатационных убытков.
Анализ технико-эксплуатационных показателей показал что производственные мощности предприятия используются недостаточно полно. Хотя следует отметить положительную динамику роста коэффициентов технической готовности сокращение дней простоя в ремонте и увеличение общего годового пробега. Недостаточно полное использование производственной мощности в конечном итоге может привести к увеличению доли постоянных издержек.
6 Рекомендации по совершенствованию деятельности предприятия
Муниципальное унитарное предприятие г. Хабаровска «ХПАТП №1» функционирует в сложных условиях испытывая постоянное конкуренцию со стороны частных перевозчиков и обеспечивая при этом перевозки льготных пассажиров. С целью сглаживания негативных влияний рынка повышения эффективности деятельности Муниципальное унитарное предприятие г. Хабаровска «ХПАТП №1» должно:
- заниматься «диверсификацией» производства т. е. искать различные побочные сферы деятельности как связанные так и несвязанные с транспортным обслуживанием например транспортно-экспедиционным обслуживанием. Другими словами предприятие должно расширять сектор услуг по ремонту и техническому обслуживанию автотранспортных средств сторонних предприятий и населения. Следует рассмотреть возможность предлагать не только маршрутные внутригородские но другие виды перевозок например междугородние экскурсионные и т.д.;
- повысить контроль над сбором выручки;
- проводить мероприятия по снижению коммунальных затрат затрат на горюче-смазочные материалы электроэнергию общехозяйственных расходов;
- изыскивать возможности обновлять автобусный парк приобретать более экономичные и надёжные в эксплуатации автобусы взамен неэкономичных и выработавших свой ресурс;
- обновлять существующее оборудование используемое для ремонта и обслуживания автомобилей сделать упор на приобретение универсального разборочно-сборочного подъёмно-транспортного и другого современного оборудования которое позволит быстро качественно и с минимальными затратами усилий ремонтировать подвижной состав предприятия;
- активизировать претензионную работу с арбитражными судами по взысканию долгов;
- производить экономию фонда оплаты труда. Уменьшая оплату по сверхурочным часам путем соблюдения режима рабочего времени;
- проводить более тщательный контроль за качеством выполненных ремонтных работ;
- организовать ТО и ТР по методу специализированных бригад с разбивкой всех ремонтных рабочих на бригаду ТО-1 ТО-2 и бригаду по проведению ТР. Всё это приведёт к более качественному обслуживанию и ремонту подвижного состава повышению технической готовности а следовательно и увеличению объёмов перевозок.
- усовершенствовать агрегатный участок с внедрением универсального оборудования в частности предлагается применить пресс для выпресовки подшипников крестовин карданного вала. Учитывая неудовлетворительное состояние отечественных автомобильных дорог поломки карданного вала являются довольно распространенными. Самая важная деталь в карданном валу – это шарниры. Именно они чаще всего выходят из строя.
Ремонт карданного шарнира обычно заключается в замене игольчатых подшипников уплотнений и крестовины для чего шарнир необходимо разобрать. Подшипники в проушинах вилок установлены с натягом поэтому при разборке и сборке шарнира их приходится соответственно впрессовывать и запрессовывать. Данное оборудование позволит повысить коэффициент технической готовности парка путём снижения времени простоя автобусов в ремонте повышением качества проводимых работ повышением уровня механизации работ и уменьшения их трудоёмкости.
Универсальность данного стенда дает возможность привлечения сторонних заказчиков имеющих в своей эксплуатации автобусы или грузовые автомобили но не имеющих ремонтной базы и оборудования. Это должно привести к притоку дополнительных средств и принесению дополнительной прибыли предприятию.
ТЕХНОЛОГИЧЕСКИЙ РАСЧЕТ
В технологической части выпускной квалификационной работе производится расчет производственной программы предприятия объема работ численности производственных рабочих и технологический расчет производственных зон и участков.
Исходными данными для расчёта являются тип и количество подвижного состава среднесуточный пробег автомобилей категория условий эксплуатации возраст и природно-климатические условия. Исходные данные приведены в таблице 2.1.
Таблица 2.1 – Исходные данные для расчёта
Технологическая группа
Количество подвижного состава в базовом предприятии ед.
Среднесуточный пробег км
Категория условий эксплуатации
Количество рабочих дней в году
Пробег с начала эксплуатации в долях от капитального ремонта
1 Корректировка нормативной периодичности ТО и КР
Производственная программа по техническому обслуживанию представляет собой количество технических воздействий выполняемых по ТО и ТР автомобилей.
Расчет производственной программы следует производить после выбора нормативных значений периодичности ТО-1 ТО-2 и капитального ремонта (КР) приведенных в «Положении о техническом обслуживании и ремонте подвижного состава автомобильного транспорта» и корректировки их для данных условий эксплуатации.
Выбор нормативов и значений коэффициентов производится согласно 2 и 3.
Корректирование периодичности технического обслуживания ТО-1 и ТО-2 проводится по формуле 2 с.14.
где – коэффициент корректирующий категорию условий эксплуатации принимаем =08;
– коэффициент корректирования нормативов в зависимости от природно-климатических условий принимаем =09;
- нормативный пробег до ТО-1 и ТО-2 км.
Все автомобили относятся к автобусам большого класса тогда согласно 2 нормативный пробег для всех групп будет равен: до ТО-1 - 3500 км. до ТО-2 14000 км.
Скорректированную периодичность до ТО-1 и ТО-2 для DAEWOO и НЕФАЗ определим по формуле 2.1 и 2.2.
Корректирование пробега до капитального ремонта производится по формуле 4 с.14:
где – коэффициент учитывающий модификацию подвижного состава и организацию его работы принимаем =10 для всех трёх групп 2 с.15;
- нормативный пробег автомобиля до капитального ремонта км.;
Нормативный пробег до капитального ремонта примем для DAEWOO - =750000 км. для автобусов НЕФАЗ – 500000 км. Межремонтный пробег для автомобилей прошедших капитальный ремонт принимается не менее 80% от нормы пробега для новых автомобилей.
Скорректированный пробег до капитального ремонта определим по формуле 2.3.
Для формирования плана технических воздействий по ТО и ТР необходимо принимать в расчетах проведение их через целое количество дней или целое количество ТО-1 ТО-2 для чего проводится корректирование периодичности по среднесуточному пробегу и пробегу до ТО-1 ТО-2. Корректировка заключается в подборе численных значений периодичности пробега в километрах для каждого вида ТО и ремонта кратных между собой и среднесуточному пробегу и близких по своей величине к установленным нормативам.
Количество дней до ТО-1 определяется по формуле:
где – расчетная периодичность до ТО-1 (целое число) дн;
– среднесуточный пробег автомобиля км.
дн. округляем до 15 дн.
Так у всех автомобилей пробег до ТО-1 одинаковый то количество дней тоже будет одинаковое.
Скорректированная периодичность ТО-1 для автобусов определяется по формуле 4 с.36.
Количество ТО-1 между ТО-2 определяется по формуле 4 с.35.
где - расчетное количество ТО-1 между очередными ТО-2 дн.
дн. округляем до 4 дн.
Скорректированная периодичность ТО-2 определяется по формуле 4 с.35.
Количество ТО-2 до КР определяется по формуле 4 с.8.
где – расчетное количество ТО-2 до КР.
дн. округляем до 30 дн.
дн. округляем до 25 дн.
Скорректированный пробег до капитального ремонта определяется по формуле 4 с.36.
2 Расчёт производственной программы по количеству воздействий
Число технических воздействий на один автомобиль за цикл определяется отношением циклового пробега к пробегу до данного вида воздействий. Так как цикловой пробег в данной методике расчёта принят равным ресурсному пробегу автомобиля то число списаний одного автомобиля за цикл будет равно единице т.е. = отсюда . В расчёте принято что при пробеге равном очередное последнее за цикл ТО-2 не проводится и автомобиль направляется на списание (или в КР). Принято что ЕО разделяется на ЕОс (выполняемое ежедневно) и ЕОт (выполняемое перед ТО и ТР).
Количество воздействий ТО-2 за цикл определяется по формуле 4 с.34:
где - число воздействий за цикл ед.
По формуле 2.10 определим количество воздействий ТО-2 за цикл:
Количество воздействий ТО-1 за цикл определяется по формуле 4 с.34:
Количество воздействий ЕОс (выполняемое ежедневно) за цикл для двух групп автомобилей определяется по формуле 4 с.34:
Количество воздействий ЕОт (выполняемое перед ТО и ТР) за цикл для двух групп автомобилей определяется по формуле 4 с.34:
Так как пробег автомобиля за год отличается от его пробега за цикл а производственную программу предприятия обычно рассчитывают за год то для определения числа ТО за год необходимо сделать соответствующий перерасчёт полученных значений за цикл к значениям за год. Для пересчета программы определяется коэффициент перехода от цикла к году:
где – годовой пробег автомобиля км.
Годовой пробег автомобиля рассчитывается по формуле 4 с.34:
где – количество дней работы предприятия в году согласно исходным данным 365 дн.;
–коэффициент технической готовности автомобиля.
Коэффициент технической готовности определяется по формуле 4 с.36:
где – количество дней простоя автомобиля в ТО и ТР на 1000 км пробега. Согласно Положению для автобусов большого класса принимаем продолжительность простоя подвижного состава () - 055 дн.1000 км;
– продолжительность простоя подвижного состава в капитальном ремонте. Согласно Положению принимаем - 25 дн.;
Определим коэффициент технической готовности по формуле 2.10.
По формуле 2.15 определим годовой пробег автомобиля:
По формуле определим коэффициент перехода от цикла к году:
Годовое количество технических обслуживаний и ремонтов на один автомобиль определяется как произведение полученной ранее цикловой программы на коэффициент перехода от цикла к году.
Число ЕОс и ЕОт определяется по формулам 2.19 и 2.20:
Результаты расчетов по количеству воздействий для всех групп автомобилей представим в таблице 2.2. Учтем что количество сезонных воздействий будет равно двум.
Таблица 2.2 – Количество воздействий за год
Количество воздействий на 1 автомобиль ед.
Количество воздействий на всю группу ед.
3 Количество диагностических воздействий за год по маркам автомобилей
Согласно «Положением о техническом обслуживании и ремонте подвижного состава» диагностирование как отдельный вид обслуживания не планируется и работы по диагностированию подвижного состава входят в объём работ ТО и ТР. При этом в зависимости от метода организации диагностирование автомобилей может производиться на отдельных постах или быть совмещено с процессом ТО поэтому в данном случае число диагностических воздействий определяется для последующего расчёта постов диагностирования и его организации. На АПТ в соответствии с Положением предусматривается диагностирование подвижного состава Д-1 и Д-2.
Диагностирование Д-1 предназначено главным образом для определения технического состояния агрегатов узлов и систем автомобиля обеспечивающих безопасность движения. Д-1 предусматривается для автомобилей при ТО-1 после ТО-2 (по узлам и системам обеспечивающим безопасность движения для проверки качества работ и заключительных регулировок) и при ТР (по узлам обеспечивающим безопасность движения). Число автомобилей диагностируемых при ТР согласно опытным данным и нормам проектирования ОНТП-АТП-СТО-80 принято равным 10% от программы ТО-1 за год.
Диагностирование Д-2 предназначено для определения мощностных и экономических показателей автомобиля а также для выявления объёмов ТР. Д-2 проводится с периодичностью ТО-2 и в отдельных случаях при ТР. Число автомобилей диагностируемых при ТР принимаем равное 20% от годовой программы ТО-2.
Количество Д-1 () и Д-2 () рассчитывается по формулам 4 c.32:
где 11 и 12 – коэффициенты учитывающие число автомобилей диагностируемых при ТР 8 с.38.
Количество диагностических воздействий определим по формуле 2.21.
Количество диагностических воздействий определим по формуле 2.22.
Суточная производственная программа является критерием выбора метода организации технического обслуживания и служит исходным показателем для расчета числа постов и линий ТО. По видам ТО и диагностирования суточная производственная программа определяется по формуле 4 с.34:
Результаты вычислений по суточной производственной программе представим в таблице 2.3.
Таблица 2.3 - Суточная программа по ЕО ТО и диагностике
4 Расчет годового объема работ по ТО ТР и самообслуживанию
4.1 Определение трудоемкости работ
Для расчета годового объема работ необходимо предварительно установить для данного АТП нормативные трудоемкости технического обслуживания и текущего ремонта а затем скорректировать их с учетом конкретных условий эксплуатации.
Расчётная нормативная скорректированная трудоёмкость и (в человеко-часах) рассчитывается по формуле 4 c.41:
где – нормативная трудоёмкость и чел.ч.
– коэффициент учитывающий модификацию подвижного состава принимаем К2=11 для всех трёх групп согласно 2 с.31.
Нормативные значения трудоёмкостей по ЕО ТО и ТР представлены в таблице 2.4.
Таблица 2.4 – Нормативные трудоемкости ЕО ТО и ТР
Скорректированную трудоемкость ежедневного обслуживания перед ТО и ТР рассчитаем по формуле 2.24.
Скорректированную трудоемкость ежедневного обслуживания рассчитаем по формуле 2.25.
Скорректированная нормативная трудоёмкость ТО-1 и ТО-2 рассчитывается по формуле 4 c.32:
где - нормативное значение трудоемкости ТО-1 и ТО-2 в зависимости от типа автотранспортного средства чел.×ч. 2 с.44;
– коэффициент учитывающий модификацию подвижного состава принимаем =11 для всех трёх групп согласно 2 с.31;
– корректирующий коэффициент в зависимости от количества единиц технологически совместимого подвижного состава предприятия принимаем =11; 155; 155 для DAEWOO и НЕФАЗ соответственно 2 с.30.
Скорректированную трудоемкость ТО-1 рассчитаем по формуле 2.27.
Скорректированная трудоемкость ТО-2 рассчитаем по формуле 2.28.
Скорректированная удельная трудоемкость текущего ремонта определяется по формуле 4 с.14.
где К5 – коэффициент учитывающий способ хранения подвижного состава принимаем К5 = 09 7 с.16
4.2 Определение годового объема работ по ТО и ТР
Объем работ по за год определяется произведением числа за год на скорректированное значение удельной трудоемкости .
Объем работ по ТО-1 за год определяется произведением числа ТО-1 за год на скорректированное значение удельной трудоемкости ТО-1.
Объем работ по ТО-2 за год определяется произведением числа ТО-2 за год на скорректированное значение удельной трудоемкости ТО-2.
Объем работ ТР за год определяется по формуле 4 с.42.
Годовой объем работ по сезонному обслуживанию рассчитывается по формуле:
где nСО – доля трудоемкости сезонного обслуживания при выполнении очередного ТО-2 совмещенного с СО принимаем равным 30%.
Годовой объем работ по ТО и ТР для всего парка автомобилей составит 212 628 чел.×ч. (таблица 2.5).
Кроме работ по ТО и ТР на предприятии проводятся работы по самообслуживанию которые составляют 15% от и их численное значение равно:
Таблица 2.5 – Годовой объем работ по ТО и ТР
5 Распределение объема работ ТО и ТР и расчёт численности производственных рабочих
Трудоемкость работ ТО и ТР распределяется по месту их выполнения по технологическим и организационным признакам. Работы по ТО и ТР выполняются на постах и вспомогательных участках.
К постовым относятся работы по ТО и ТР выполняемые непосредственно на автомобиле (моечные уборочные смазочные крепежные диагностические и др.).
К вспомогательным относятся работы по проверке и ремонту узлов механизмов и агрегатов снятых с автомобиля выполняемых на вспомогательных участках (агрегатном слесарно-механическом электротехническом и др.).
Исходными данными для распределения трудоемкости являются коэффициент распределения объема работ ЕО ТО и ТР () по видам работ. Принимается в соответствии с маркой автомобиля согласно ОНТП-01-91 и годовой объем работ () по ЕО ТО ТР технологически совместимых групп.
Годовой фонд времени технологически необходимого ФТ при 6-ти дневной рабочей неделе для производств с нормальными условиями труда согласно ОНТП-01-91 принимается равным 2070 часов и 1830 часов для производств с вредными условиями труда.
Годовой фонд времени «штатного» рабочего определяет фактическое время отработанное исполнителем непосредственно на рабочем месте. Фонд времени «штатного» рабочего ФШ меньше фонда «технологического» рабочего ФТ за счет предоставления рабочим отпусков и невыходов рабочих по уважительным причинам. Согласно ОНТП-01-91 годовой фонд времени «штатного» рабочего для выполнения работ связанных с вредными условиями труда составляет 1610 часов а для всех других – 1820 часов.
Технологически необходимое число рабочих по видам работ определяется по формуле 4 с.47.
где - годовой объем работ по ЕО ТО ТР технологически совместимых групп чел.×ч.;
- годовой фонд технологически необходимого времени ч.
Расчеты технологически необходимого числа рабочих приведены в таблицах 2.6 - 2.7.
Штатное число производственных рабочих определяется по формуле 4 с.47.
где - фактическое время отработанное исполнителем непосредственно на рабочем месте ч.
Расчеты штатного числа рабочих для трёх технологических групп автобусов приведены в таблицах 2.6 - 2.7.
Таблица 2.6 – Распределение годового объёма работ и расчет численности автомобилей DAEWOO
-контрольно-диагностические
-диагностирование общее (Д-1)
Окончание таблицы 2.6 – Распределение годового объёма работ и расчет численности автомобилей DAEWOO
-смазочные очистительные
-углубленное диагностирование
-диагностирование углубленное
-разборочно-сборочные работы
-слесарно-механические работы
-электротехнические работы
-аккумуляторные работы
-ремонт системы питания
-шиномонтажные работы
-вулканизационные работы
-кузнечно-рессорные работы
Таблица 2.7 – Распределение годового объёма работ автомобилей НЕФАЗ
Окончание таблицы 2.7 – Распределение годового объёма работ автомобилей НЕФАЗ
Общее распределение работ и технологически необходимое число рабочих представлено в таблице 2.8
Таблица 2.8 – Распределение годового объёма работ и технологически-необходимого числа рабочих
-углубленное диагностирование (Д-2)
-диагностирование углубленное (Д-2)
Окончание таблицы 2.8 – Распределение годового объёма работ и технологически-необходимого числа рабочих
К вспомогательным рабочим относятся рабочие занятые на следующих работах:
- ремонт и обслуживание оборудования;
- транспортные и погрузочные работы связанные с ремонтом и обслуживание автомобилей;
- приемка хранение и выдача материальных ценностей;
- перегон автомобилей по территории;
- уборка помещения; прочие подсобные работы.
Количество вспомогательных рабочих следует принимать равными 15% от производственных рабочих согласно расчетам таблицы 2.9 численность производственных рабочих составляет 62 чел. тогда численность вспомогательных рабочих составит 9 чел.
Распределение вспомогательных рабочих по видам работ представлено в таблице 2.10.
Таблица 2.10 – Распределение вспомогательных рабочих по видам работ
Станочники (токари фрезеровщики и т.д.)
Слесари по оборудованию
Слесари по отоплению водопроводу канализации
Плотники и ремонтно-строительные рабочие
Прочие специальности (кладовщики инструментальщики уборщики цехов перегонщики автомобилей) и т.п.
Количество водителей-перегонщиков рабочих по приемке хранению и выдаче материальных ценностей в зависимости от суточного количества заездов автомобилей примем:
- перегонщики – 4 чел;
- рабочие складов – 1 чел.
Численность инженерно-технических работников (ИТР) примем 30 чел. в зависимости от количества постов. Численность рабочих для уборки помещений примем 5 чел.
6 Уточнённый расчёт агрегатного участка
Агрегатный участок предприятия предназначен для выполнения разборочно-сборочных и ремонтно-восстановительных работ по коробке передач переднему и заднему мостам и другим агрегатам механизмам и узлам снятым с автомобиля для текущего ремонта. Ремонт сцеплений и двигателей осуществляется на другом специализированном участке.
Содержание работ агрегатного участка представлено на рисунке 2.1.
Рисунок 2.1 – Блок-схема работ агрегатного участка
Для разборки агрегатов применяют специализированные стенды. Подшипники втулки и другие детали выпрессовывают с помощью ручных верстачных прессов (усилием 3—5 т) или гидравлических прессов (усилием 20 т модели 208) а также съемников.
Крупные детали моют на отдельном участке. Для мелких деталей предусмотрена ванна. Вымытые детали контролируют в соответствии с техническими условиями и сортируют на три группы: годные требующие ремонта и негодные.
5.1 Корректировка численности рабочих по видам работ
Чтобы определить численность производственных рабочих используем методику изложенную в 8 с.46 по которой определяются технологически необходимая (явочная) и штатная численность рабочих.
Технологически необходимое (явочное) число рабочих:
где - годовой объем работ по агрегатному участку чел.×ч.;
- годовой фонд времени технологически необходимого рабочего при односменной работе ч.
Годовой фонд рабочего места определяется по формуле:
где - число календарных дней в году – 365;
- число выходных дней в году – 104;
- число праздничных дней в году – 12;
- время рабочей смены ч.;
- время сокращения рабочей смены в праздничные дни для рабочих выполняющих работы с условиями труда не отнесенные к вредным tС=1 ч.
Подставив значения в (2.21) определим годовой фонд рабочего места который составит:
ФТ=(365-104-12)×8-10×1=1982 ч
Штатное число рабочих определим по формуле:
где - годовой фонд времени штатного рабочего ч.
Годовой фонд одного рабочего определяется по формуле:
где ДОСН – число дней основного отпуска ремонтного рабочего. Принимаем ДОСН.=24 дн.;
ДДОП – число дней дополнительного отпуска за работу в северных и приравненных к ним районах ДДОП=12 дн.;
ДВР – число дней дополнительного отпуска для работ с вредными условиями труда в соответствии с коллективным договором. Принимаем ДВР=3 дн.;
ДУВ – число дней неявки по уважительной причине. Принимаем ДУВ=2 дн.
Подставив значения в (2.23) при восьми часовой смене получим:
ФШ=2430-(24+12+2)×8=2126 ч.;
Корректировка и распределение численности рабочих по видам работ представлено в таблице 2.14.
5.2 Расчет числа единиц технологического оборудования
К технологическому оборудованию относятся стационарные и переносные станки стенды приборы приспособления и производственный инвентарь (верстки стеллажи столы шкафы) необходимое для обеспечения производственного процесса АТП.
Таблица 2.14 – Распределение трудоемкости и рабочих по видам работ
Слесарно-механические работы
Количество основного оборудования определим по трудоемкости работ и фонду рабочего времени оборудования.
Определяемое расчетом по трудоемкости работ число единиц основного оборудования:
где – годовой объем работ по данной группе или виду работ чел.×ч.;
– годовой фонд времени рабочего места (единицы оборудования) ч.;
- число рабочих одновременно работающих на данном виде оборудования чел.
Годовой фонд времени работы оборудования определяем по формуле:
где - годовой фонд работы (технологический) ч.;
- число рабочих смен;
- коэффициент использования оборудования по времени т.е. отношение времени работы оборудования в течение смены к общей продолжительности времени смены. Примем - 080.
Все расчеты числа единиц оборудования сведем в таблицу 2.14.
Таблица 2.14 – Расчет числа единиц оборудования
5.3 Выбор оборудования для агрегатного участка
При подборе оборудования использовались каталоги справочники и Интернет.
Таблица 2.10 - Технологическое оборудование и участка
Стеллаж для деталей и инструментов
Ванна для мойки мелких деталей
Железный ящик для выбракованных деталей
Пресс гидравлический вертикальный (30 т.)
Стол для контроля и сортировки деталей
Стенд для выпрессовки подшипников крестовин карданных валов
Станок точильно-шлифовальный
Стенд для обкатки и испытания ГУР и насосов ГУР
Стенд для обкатки мостов и главной передачи
Окончание таблицы 2.10 - Технологическое оборудование участка
Подвесная кран-балка
Стенд для ремонта редукторов задних мостов
Стенд для разборки-сборки КП
Стенд для ремонта передних и задних мостов
Ларь для обтирочных материалов
Станок для проточки тормозных дисков и барабанов
Настольно сверлильный станок
Площадь агрегатного участка рассчитываем по формуле 4 с.99:
где - суммарная площадь занимаемая оборудованием;
- коэффициент плотности расстановки оборудования.
5.5 Расчет затрат на энергоносители
Определяем активную мощность потребителей кВт по формуле 3 с.269 270.
где – коэффициент спроса учитывающий время работы 3 с.270;
– суммарная мощность потребителей кВт. Согласно таблице 2.19.
Годовой расход электроэнергии определяется по формуле:
где – коэффициент загрузки потребителей по времени принимаем = 08.
Затраты электроэнергии на освещение по формуле:
где – удельный расход электроэнергии на 1 м2 площади агрегатного участка Вт м2;
– площадь агрегатного участка м2.
В соответствии со СниП 23-05-95 «Естественное и искусственное освещение» принимаем =25 Вт м2.
Годовой расход энергии на освещение агрегатного участка рассчитывается по формуле:
где – время световой нагрузки = 1600 ч.
Суммарная годовая потребность агрегатного участка в электроэнергии составит:
ОРГАНИЗАЦИОННАЯ ЧАСТЬ
1 Производственная структура предприятия
Основными задачами любого автотранспортного предприятия являются:
организация и выполнение перевозок в соответствии с планом и заданиями;
хранение техническое обслуживание и ремонт подвижного состава;
материально-техническое снабжение предприятия;
содержание и ремонт зданий сооружений и оборудования;
подбор расстановка и повышение квалификации персонала;
организация труда планирование и учет производственно-финансовой деятельности.
Основными процессами производственной деятельности автотранспортного предприятия являются:
основное производство;
вспомогательное производство;
обслуживающее производство;
управление производством.
Основное производство на автомобильном транспорте — выполнение перевозок что является определяющим для автотранспортного предприятия. Однако основное производство нуждается в обслуживании и выполнении комплекса вспомогательных работ.
Вспомогательное производство автотранспортного предприятия — это совокупность производственных процессов имеющих свой результат труда в виде определенной технической готовности подвижного состава который используется в основном производстве.
Обслуживающие производства материального продукта не создают. Они обеспечивают основное и вспомогательное производство энергоресурсами информационным обслуживанием контролируют качество технического обслуживания и ремонта. Автотранспортное предприятие для успешной деятельности должно состоять из ряда структурных подразделений с определенными функциями и строго определенными взаимосвязями (рисунок 3.1).
Рисунок 3.1 – Производственная структура предприятия
Производственная структура ХПАТП формируется следующим составом:
основная (эксплуатационная) служба – отдел эксплуатации;
вспомогательное производство – техническая служба;
обслуживающее производство – служба главного механика и энергетика;
служба подсобно-вспомогательных работ (уборка помещений территории и т. п.);
2 Структура управления производством
Руководство предприятием осуществляет директор. В структуре управления предприятием имеются две основные службы – служба эксплуатации и техническая служба.
Службу эксплуатации возглавляет заместитель директора. Служба имеет в своей структуре отдел эксплуатации контрольно-ревизионную службу (КРС) колонны водителей. Основной функцией отдела является планирование работы маршрутов рейсов расписания потребного количества автобусов осуществление плана – графика выхода автобусов на линии. Главной задачей этой службы является выполнение доходов от перевозки пассажиров и поиск иных источников дохода.
Техническую службу возглавляет главный инженер. В её структуру включены: производственно-технический отдел АЗС ремонтная мастерская промежуточный склад запасных частей и агрегатов. Эта служба несет ответственность за техническое состояние подвижного состава а также за счет развития на ее базе услуг по ремонту и ТО получение дополнительных доходов.
Техническая служба АТП уделяет главное внимание вопросам поддержания транспортных средств в технически исправном состоянии и обеспечения развития производственной базы а также осуществляет руководство материально-техническим снабжением предприятия.
Главными задачами технической службы предприятия являются:
организация надлежащего хранения подвижного состава обеспечивающего высокую техническую готовность его к работе своевременность выпуска автомобилей на линию и прием их (гаражная служба);
разработка и решение вопросов связанных с укреплением производственно-технической базы предприятия (главный инженер);
оперативное планирование всех видов ТО и ремонта автомобилей и автомобильных шин организация выполнения этих работ и контроля за их качеством проведение технического учета и отчетности по подвижному составу автомобильным шинам и другим производственным фондам (начальник ремонтной службы);
руководство всей совокупностью работ по обеспечению нормального материально-технического снабжения предприятия организации хранения выдачи и учета топлива запасных частей и других материальных ресурсов разработка и осуществление мероприятий по более рациональному их использованию (отдел снабжения);
разработка и проведение организационно-технических мероприятий по совершенствованию процессов производства внедрению новой техники охране труда и предупреждению аварийности.
Исходя из вышеперечисленных задач техническая служба имеет право контролировать техническое состояние подвижного состава снимать его с эксплуатации планировать и проводить профилактические и ремонтные работы привлекать к материальной ответственности за неправильную эксплуатацию подвижного состава зданий сооружений оборудования и т.д. а также лимитировать расходы ГСМ.
Техническая служба АТП состоит из следующих основных комплексов 12:
- комплекс подразделений выполняющих диагностику технического состояния автомобилей их агрегатов и узлов (комплекс Д);
- комплекс подразделений выполняющих техническое обслуживание и регламентные работы (комплекс ТО);
- комплекс подразделений выполняющих работы по замене неисправных агрегатов узлов и деталей а также крепежно-регулировочные работы (комплекс ТР);
- комплекс подразделений обеспечивающих подготовку производства комплектование оборотного фонда доставку агрегатов узлов и деталей обеспечение рабочих инструментами а также перемещением автомобилей из зоны в зону осуществляется комплексом подготовки производства (комплекс ПП);
- производственно-технический отдел (ПТО) обеспечивает разработку и внедрение новой технологии и техники производственных процессов организует рационализаторскую и изобретательскую работы составляет технические нормативы и инструкций а также мероприятия по подготовке и повышению квалификации кадров ТБ и ОТ;
- отдел главного механика (ОГМ) отвечает за содержание в технически исправном состоянии зданий сооружений технологического оборудования осуществляет монтаж обслуживание и ремонт производственного оборудования.
Контроль качества выполняемых работ по техническому обслуживанию и ремонту подвижного состава и изделий собственного производства осуществляется работниками ОТК и контролерами технического состояния. Контроль качества выполняемых работ по ТО и ТР осуществляется с помощью вновь введенной в эксплуатацию диагностической линии фирмы «Актиа Мюллер сервис».
В составе предприятия имеется отдел материально-технического снабжения (ОМТС) который обеспечивает бесперебойное материально-техническое снабжение Филиала составляет заявки по материально-техническому снабжению и обеспечивает правильную организацию работы складского хозяйства. Между отделами существуют многосторонние внутренние и внешние связи.
3 Метод организации производства ТО и ТР
Наибольшее распространение к настоящему времени получили три метода организации производства ТО и ремонта подвижного состава: специализированных бригад комплексных бригад и агрегатно-участковый.
Метод специализированных бригад предусматривает формирование производственных подразделений по признаку их технологической специализации по видам технических воздействий: создаются бригады по проведению ЕО ТО-1 ТО-2 диагностирования ТР ремонту агрегатов.
Метод комплексных бригад предусматривает формирование производственных подразделений по признаку их предметной специализации т. е. закрепление за бригадой определенной группы автомобилей (например автомобилей одной колонны автомобилей одной модели прицепов и полуприцепов) по которым бригада проводит работы ТО-1 ТО-2 и ТР.
В МУП «ХПАТП № 1» применяется агрегатно-участковый метод организации ТО и ТР. Сущность агрегатно-участкового метода состоит в том что все работы по ТО и ремонту подвижного состава АТП распределяются между производственными участками ответственными за выполнение всех работ ТО и ТР одного или нескольких агрегатов (узлов механизмов и систем) по всем автомобилям АТП.
Результаты работы производственного участка оцениваются по средней наработке на случай ТР соответствующих агрегатов и по простоям автомобилей из-за технических неисправностей агрегатов и систем закрепленных за участком. Работы распределяются между производственными участками с учетом производственной программы.
При агрегатно-участковом методе ремонт автомобилей производят путём замены неисправных узлов и агрегатов на исправные ранее отремонтированные или новые из оборотного фонда. Неисправные узлы и агрегаты после их ремонта поступают в оборотный фонд.
Рисунок 3.2 - Схема технологического процесса ТР автомобиля агрегатно-участковым методом
При агрегатном-участковом методе ремонт автомобилей производят путем замены неисправных агрегатов (узлов) исправными ранее отремонтированными или новыми из оборотного фонда. Неисправные агрегаты (узлы) после их ремонта поступают в оборотный фонд.
Агрегатно-участковый метод ремонта позволяет сократить время простоя автомобилей в ремонте поскольку замена неисправных агрегатов (узлов) на исправные требует меньше времени. В свою очередь сокращение времени простоя в ТР позволяет повысить коэффициент готовности парка а следовательно увеличить его производительность и снизить себестоимость транспортной работы.
Основным недостaткoм aгрегaтнo-учaсткoвoгo метoдa являются субъективные и мaлoэффективные методы кoнтрoля техническoгo сoстoяния aвтoмoбилей a также труднoсти распределения рaбoт пo учaсткaм нa линиях и пoстaх ТО-1 и ТО-2.
Работы по ежедневному обслуживанию и ТО кроме уборочно-моечных производятся в две смены так как целесообразно проводить ремонт в то время когда автомобиль не на линии то есть стараться снижать время простоя в ремонте. Кроме того это позволит сократить занимаемую производственную площадь за счёт уменьшения необходимого количества постов ТР дорогостоящего оборудования и оснастки.
Все работы по общему (Д-1) и углубленному (Д-2) диагностированию перед ТО и ТР производятся на отдельном участке оснащённом комбинированными диагностическими стендами. Участок диагностики расположен обособленно от проездных постов ТО.
Зона ТР работает в две смены так как целесообразно проводить ремонт в то время когда автомобиль не на линии то есть стараться снижать время простоя в ремонте. В дневную смену работают все производственно-вспомогательные участки и посты ТР; в ночную смену выполняются постовые работы по ТР автобусов выявленные при ТО диагностировании или по заявке водителей.
Малярные и кузовные работы производятся в отдельном производственном помещении в соответствии с требованиями охраны труда и пожарной безопасности.
4 Описание и схема производственного процесса автотранспортного предприятия
Производственный процесс автотранспортного предприятия (АТП) представляет собой совокупность технологических процессов ТО и ТР. Схема производственного процесса ХПАТП изображена на рисунке 3.3.
Под технологическим процессом (ТП) понимается определенная последовательность работ и операций имеющих своей целью поддержание работоспособности АТС путем качественного выполнения работ при оптимальных материальных затратах.
Движение подвижного состава организовано следующим образом: на территорию предприятия имеется один въезд через ворота контрольно - пропускного пункта мимо автостоянки и административного здания. Далее проходит через пост диспетчерской к открытой стоянке автомобилей предназначенной для стоянки подвижного состава в теплое время года далее проходит мимо профилактория и зимней стоянки. Территория предприятия огорожена бетонным забором.
Рисунок 3.3 — Схема производственного процесса предприятия
При въезде автобуса на территорию предприятия автобус проходит через контрольно-пропускной пункт (КПП) где ведется учет всех въехавших и выехавших автобусов а также производится предърейсовый осмотр водителей проверяется наличие всех необходимых документов и техническое состояние автомобиля. Далее при необходимости автобус прибывает на пост ежедневного обслуживания (ЕО) на котором проводятся уборочно-моечные мероприятия посредством механизированной мойки. После уборочно-моечных операций автобус направляется на стоянку. При необходимости выполнения работ по техническому обслуживанию или ремонту автобус направляется в зону обслуживания. Если посты по ТО или ТР не заняты другими автобусами то автомобиль направляется на них минуя зону ожидания. На предприятии посты диагностики (Д-1 и Д-2) выделены в отдельное помещение.
Согласно схеме рисунка 3.3 автомобили прибывающие на территорию в первую очередь проходят контрольный пункт (приём автомобилей с линии). Здесь на автомобили требующие технического обслуживания (по плану-графику) или текущего ремонта выписывается листок учёта с указанием неисправности или требуемого по плану-графику вида обслуживания.
Автомобили требующие по графику ТО-1 или ТО-2 направляются на посты уборочно-моечных работ далее в соответствующие производственные зоны (ТО-1 ТО-2 ТР) предприятия а затем в зону хранения.
Автомобили проходящие через контрольный пункт и требующие в результате заявки водителя или осмотра текущего ремонта с соответствующей отметкой в листе учёта направляются на уборо-моечные посты и далее в зону ремонта для устранения неисправностей. После устранения неисправностей с соответствующей отметкой в листе учёта автомобиль ставится на стоянку. В зону ремонта автомобили могут так же поступать из зоны обслуживания при обнаружении неисправностей требующих текущего ремонта а так же при возврате с линии в случае неисправностей.
5 Описание информационного обеспечения
Деятельность производственных подразделений и персонала фиксируется в различных документах (табели работы служащих наряды выходов на линию путевые и ремонтные листы требования на получение запасных частей). Результаты деятельности предприятия оформляются в виде различных отчетов и сводок. Таким образом источниками информации являются подразделения в которых персонал выполняет определенные виды деятельности.
В «ХПАТП №1» существует локальная компьютерная сеть соединяющая все значимые отделы предприятия. С помощью специально разработанной программы «СПУРТ» делаются заявки на ремонт ведётся учёт резины горючесмазочных материалов и т.д. При временно не работающей локальной компьютерной сети заявочные листы выписываются вручную но потом все заявки на ремонт вносятся в базу данных компьютерной сети. С помощью программы «СПУРТ» можно оперативно обнаружить какие ремонтные работы и кем проводились на конкретно взятом автобусе когда проводились ТО-1 ТО-2 есть ли у автобуса перерасход топлива и многое другое.
При заезде автобуса в парк после отработанной смены он проверяется механиками отдела технического контроля при необходимости в компьютерной программе дается заявка на ремонт. С помощью локальной компьютерной сети она передаётся диспетчеру производства. Водитель узнает у диспетчера производства куда ему ставить машину сразу в ремонтную зону или в зону хранения. При постановке в ремонтную зону (при наличии свободного места и свободных от работы автослесарей) диспетчер расписывается в путевом листе водителя о приёмке автобуса.
Документы являясь носителями информации в процессе работы проходят через ряд подразделений каждое из которых вносит в него (или извлекает из него) определенные данные. Набор документов представляет собой документооборот или информационные потоки предприятия.
6 Материально-техническое обеспечение
Материально-техническое снабжение АТП представляет собой процесс обеспечения подвижного состава эксплуатационными материалами (топливом маслом резиной) запасными частями агрегатами и другими материалами необходимыми для его бесперебойной работы.
Основными задачами организации материально-технического снабжения АТП являются: своевременное и в требуемом количестве обеспечение предприятия всеми материалами необходимыми для бесперебойной работы подвижного состава; создание условий наилучшего сохранения (без потерь) находящихся на складе материалов запасных частей и агрегатов.
Рациональная организация материально-технического снабжения АТП основывается на передовых нормативах расхода в первую очередь эксплуатационных и других материалов а также запасных частей и агрегатов требуемых при ТО и Р на своевременной их заготовке доставке приемке 12
Потребность в запасных частях возрастает при увеличении среднего возраста автомобилей. Поэтому для поддержания в технически исправном состоянии парка автомобилей с различным пробегом требуется разное количество запасных частей. По мере увеличения пробега наблюдается расширение в несколько раз номенклатуры запасных частей расходуемых на поддержание работоспособности автомобилей. Уже на третьем году эксплуатации она в 2-3 раза больше чем в первый год что обусловлено выходом из строя большего количества деталей по мере «старения» автомобилей.
Поступление деталей на склад производится с заводов фирмы и с заводов субпоставщиков в соответствии с планом составленным на основании данных о движении запчастей за предыдущий год и данных об изменении парка автомобилей. Средний запас деталей каждого наименования должен поддерживаться на уровне четырехмесячной годовой потребности 14 c. 304
7 Управление качеством производства
Управление качеством ТР имеет в своей основе конкретные значения нормативных показателей качества которые определяются через наработку в километрах пробега на выполненную операцию ТР (ГОСТ 18322-73). Нормированное предельное количество отказов за определенный пробег нормированное предельное количество брака или отклонений от технических условий в заранее определенной выборке автомобилей проверяемых ОТК 12 с.363.
Контроль осуществляется начальником ОТК соместно с начальником ремонтных мастерских и старшими смен в соответствии с технологическим процессом ремонта автомобилей. Результаты контроля заносят в талон контроля качества ТР. На основе ежедневных ведомостей качества ТР и дефектов составляют месячные ведомости в которых определяют уровень качества работ бригад ТР и количество дефектов с распределением их по видам значимости и причинам за прошедший месяц. Отчетный уровень качества используют для установления размера премии основным производственным рабочим.
8 Организация технологического процесса на агрегатном участке
На рисунке 3.4 представлена схема организации технологического процесса агрегатного участка.
Рисунок 3.4 – Схема организации технологического процесса агрегатного участка
Агрегатный участок предназначен для ремонта агрегатов узлов и деталей снятых с автомобиля.
Технологический процесс ремонта агрегатов и узлов автомобилей осуществляется следующим образом. После снятия с автомобиля агрегаты узлы поступают в агрегатный участок в зону наружной очистки. После наружной очистки согласно технологическим картам агрегаты и узлы разбирают на отдельные детали которые поступают далее в зону мойки. Чистые детали подвергают дефектовке в процессе которой выявляют необходимость ремонта и замены основных деталей. На сборку поступают годные и отремонтированные детали а также новые детали со склада запасных частей.
Агрегаты и узлы собирают на специализированных стендах где одновременно выполняют их контроль и регулировку. После сборки агрегаты и узлы направляют непосредственно в зону ТР для установки их на автомобиль.
9 Организация труда слесаря
Для обеспечения выполнения установленного перечня (объема) работ на рабочем месте при нормативной затрате рабочего времени на осуществление ремонта и испытание агрегатов используются технологические карты которые могут быть операционно-технологическими и постовыми. В первом случае они представляют собой перечень операций обслуживания составленный в определенной технологической последовательности по агрегатам узлам и системам автомобиля (например двигатель сцепление коробка передач и т.д.). Постовые карты составляют на перечень работ выполняемых на данном участке каждое рабочее место. На основании карты-схемы и операционно-технологической карты может быть составлена технологическая карта на рабочее место. Она включает в себя перечень операций в их технологической последовательности выполняемых данным рабочим (исполнителем) наименование инструмента и оборудования место выполнения (сверху снизу сбоку) число одноименных мест обслуживания норму времени и технологические условия.
Участок по ремонту агрегатов должен удовлетворять следующим требованиям:
а) находиться в непосредственной близости к рабочим местам на которых выполняются предыдущие операции и источникам снабжения;
б) допускать рациональное расположение основного оборудования и вспомогательных устройств.
Рабочее место может быть подразделено на отдельные зоны: рабочую в которой непосредственно осуществляется процесс; инструментов; документации; ожидания (хранения). Рабочее место должно быть оснащено быстродействующими съемниками ключами гайковертами приспособлениями для выпрессовки.
Система обслуживания должна обеспечить: систематическую проверку работоспособности оборудования своевременное оснащение инструментом запасными частями инструктаж и контроль качества работ.
Карта организации труда - концентрированное изложение проекта организации труда разработанного для определенного исполнителя на основе предварительных инженерных экономических санитарно-гигиенических психологических и других исследований. В них даются: наиболее рациональная последовательность действий работников; приемы; методы и нормы труда; организация и обслуживание рабочих мест; участков; мероприятий по созданию благоприятных условий труда работников. В целях правильного подбора и расстановки кадров в карты включается раздел: «Требования к исполнителю» применительно к характеру выполняемой работы.
В картах организации труда для ремонта и обслуживания рабочих мест автотранспортных предприятий предусматривается наиболее рациональные приемы и методы труда способы выполнения пространственная организация рабочего места и его элементов система обслуживания производства прогрессивные нормы оплата и материальное стимулирование труда санитарные и гигиенические требования к исполнителю и др.
Разработка типовых карт комплексной организации труда для ремонтно-обслуживающих рабочих осуществляется по следующим этапам:
а)выбор типовых представителей рабочих мест необходимых для выполнения производственной программы;
б)анализ состояния организации рабочих мест данного типа;
На этом этапе применительно к используемым рабочим местам по профессии рабочих установлено:
- количество и качество ремонта характерного для данного типа рабочего места;
-характерный состав ремонтных рабочих при ремонте функции рабочего и методы труда;
- состав и оснащение рабочего места включая основное вспомогательное оборудование технологическую и организационную оснастку;
- обслуживание рабочих мест;
- существующую планировку рабочего места в том числе расположение инструмента приспособлений и оснастки;
в)разработка типовой комплексной организации труда для ремонта и обслуживания агрегатов.
а)Исходных данных. В этот раздел включены: комплектование работ уточненная технология форма организации труда система оплаты труда и конкретные показатели премирования.
Указываются также рекомендуемые формы и системы оплаты труда показатели условий и размеров.
б)Трудового процесса. Раздел включает в себя рекомендации о содержании принятом перечне основных операций ремонта автомобиля последовательность работы и нормативах времени затрачиваемого на каждый элемент ремонта.
Нормируемое время – это время необходимое для выполнения операции работы.
Ненормируемое время возникает при различных технических и организационных неполадках (в норму времени не входит).
Нормативы времени выражены в человеко-часах и даны на единицу объема работы подлежащей выполнению одним исполнителем. Нормативы времени рассчитаны по формуле:
где Нвр - норматив времени на операцию чел.×ч.;
Топ - оперативное время чел.×ч.;
tпз - время на подготовительно-заключительные работы;
tоб - время обслуживания рабочего места;
tотл - время на отдых и личные потребности.
в)Рабочего места. Под рабочим местом понимается зона трудовой деятельности одного или нескольких исполнителей оснащенная всеми необходимыми средствами для выполнения производственных заданий. В рассматриваемом разделе предусмотрена внешняя технологическая планировка рабочего места.
г)Обслуживание рабочего времени. В этом разделе перечисляются функции обслуживания и исполнители с указанием ее объема и затрат времени на выполнение. Приводятся средства связи с функциональными службами производства.
д)Условия труда. Это комплекс элементов характеризующих производственную обстановку в которой совершается трудовой процесс и включает в себя психофизиологические факторы.
В тех случаях когда обстановка не позволяет устранить воздействие на работающего человека неблагоприятных факторов в разделе предусматриваются обязательные средства защиты от вредных воздействий.
е) Режима труда. Запроектированный в данном разделе оптимальный режим труда и отдыха основывается на штатном исследовании психологического состояния рабочего и изменения работоспособности на участке на протяжении рабочей смены. На основании этого определяется продолжительность пауз для отдыха времени для проведения производственной гимнастики и др.
КОНСТРУКТОРСКАЯ ЧАСТЬ
Практика эксплуатации автомобилей на разных дорогах и в любое время года доказала необходимость периодической разборки карданных шарниров для замены или пополнения смазки в подшипниках проверки и восстановления защитных свойств резиновых уплотнителей и их обойм. На МУП «ХПАТП №1» традиционно для выпрессовки подшипников крестовин карданных передач используют молотки и кувалды что может привести к деформации и разрушению детали.
Целью настоящего раздела выпускной квалификационной работы является совершенствование стенда для выпрессовки подшипников крестовин карданных передач на основе проведенного анализа существующих конструкций.
1 Анализ существующих конструкций
Разборочно-сборочное оборудование значительно облегчает труд рабочих при разборке агрегатов узлов и целого ряда соединений и сопряжений трудно поддающихся разборке после их эксплуатации. Эти стенды и механизмы обеспечивают удобное и безопасное выполнение тяжелых работ способствуют снижению трудоемкости этих работ и повышению производительности труда.
1.1 Стенд для разборки рулевых механизмов и карданных валов модель 3025
Стенд предназначен для разборки и сборки рулевых механизмов и карданных валов автомобилей ГАЗ-51 ЗИЛ-164А и МАЗ-200 (рисунок 4.1).
В конструкции стенда имеются два пневматических устройства для зажима разбираемых (собираемых) изделий состоящих из пневматического цилиндра 8 и Г-образного механизма 5. Разбираемое (собираемое) изделие 4 устанавливается на неподвижные призмы 6 и прижимается к ним прижимом 5 который жестко соединены штоком пневматического цилиндра 8.
– поперечина; 2 – стойка; 3 – поперечина; 4 – изделие;
– прижим; 6 – призма; 7 – пневматический кран;
– пневмоцилиндр; 9 - поддон
Рисунок 4.1 – Стенд модель 3025
Пневматическая система стенда соединяется с воздушной магистралью гибким шлангом. Подача воздуха в цилиндры осуществляется поворотом рукоятки пневматического крана 7.
Основанием стенда является каркас сварной конструкции. Две его стойки соединены между собой поперечинами 1 и 3. Во избежание опрокидывания стенда в нижней части стоек 2 приварены уголки 10. На верхних поперечинах размещен поддон 9 для инструмента и запасных частей.
a)стенд не крепится к фундаменту;
b)простота устройства;
c)неограниченный запас воздуха и несложность его транспортировки в сжатом состоянии;
d)плавность передачи усилия.
a)малое давление в сети и в связи с этим громоздкость исполнительных цилиндров затрудненность передачи по указанной причине большой мощности;
b)повышенный нагрев воздуха при сжатии;
c)значительный расход электроэнергии на получение сжатого воздуха;
Техническая характеристика стенда
Способ зажима - пневматический
Усилие зажима - 500 кгс
Давление воздуха в системе - 04(4) мПа(кгссм2)
Габаритные размеры - 883×650×1100 мм
1.2 Пресс гидравлический с передвижной головкой ПГП-20
Пресс гидравлический ПГП-20 усилие 20 т. Пресс с ручным перемещением стола и подвижной кареткой используется для выполнения работ по выпрессовке запрессовке правке и гибке разных деталей в авторемонтных мастерских и станциях технического обслуживания.
– опорная плита; 2 - рама; 3 - гидроцилиндр;
Рисунок 4.2 - Пресс модель ПГП-20
Стенд состоит из рамы 2 в верхней части которой закреплен гидроцилиндр 3 а в нижней части меняющаяся по высоте опорная плита 1. Насосная станция 4 закреплена на правой стенке и приводится в действие рукояткой.
К прессу подводится деталь регулируется необходимая высота плиты и устанавливается необходимая насадка на гидроцилиндр (рисунок 4.2).
Техническая характеристика пресса:
Расстояние между столом и штоком – 800 мм
Высота подъёма стола – 600 мм
Давление масла в гидросистеме - 382(382) МПа (кгссм²)
Габаритные размеры - 600×800×1700 мм
a)высокая производительность экономичность;
b)простота конструкции;
d)небольшой износ механизмов системы отсутствие коррозии механизмов;
e)бесшумность работы.
a)необходимость снятия деталей с автомобиля;
b)возможность утечки жидкости что может ухудшить характеристику работы стенда;
c)большая вероятность изменения свойств рабочей жидкости в зависимости от температуры приводящая к изменению характеристики работы;
d)высокая стоимость;
e)необходимость квалифицированного обслуживания.
1.3 Стенд для ремонта карданных валов Р-223
Стенд для ремонта карданных валов предназначен для сборки-разборки карданных валов. Принцип работы гидравлический.
Максимальное усилие выпрессовки - 4000 Н
Усилие зажима - 200 кГс
Рабочее давление в сети - 10(100) МПа (кгссм2)
Габаритные размеры - 920×1150×650 мм
Стенд состоит из рамы 5 гидравлического цилиндра 3 и насосной станции 4 тисков 1 и держателя 2.
– тиски; 2 –держатель;
- гидроцилиндр; 4 – насосная станция;
Рисунок 4.3 – Стенд для ремонта карданных валов Р-223
a)простота конструкции;
b)небольшой износ механизмов системы отсутствие коррозии механизмов;
c)бесшумность работы.
c)большая вероятность изменения свойств рабочей жидкости в зависимости от температуры приводящая к изменению характеристики работы высокая стоимость;
d)необходимость квалифицированного обслуживания.
1.4 Съемник крестовин карданных валов СВК1
Данное устройство представляет собой компактный механический съемник. Минимальное усилие на рукоятке позволяет эффективно использовать съемник для выпрессовки небольших сборочных единиц его можно использовать как струбцину и винтовой пресс при проведении ремонтных работ. Может также использоваться для разборки крестовин карданных валов при выполнении ремонта трансмиссий грузовых автомобилей.
– рукоятка; 2 – корпус; 3 – винт нажимной
Рисунок 4.4 – Съемник крестовин карданных валов СВК1
легкая фиксация на снимаемой детали;
сверхпрочная металлическая конструкция;
высокая надежность;
простота конструкции;
малые габариты и масса.
Небольшое усилие создаваемое съемником.
Технические характеристики съемника:
Ход винта - 60 160 мм
Рабочее пространство - 125×160 мм
Габариты (Ш х Д х В) - 114×315×180 мм
1.5 Выбор прототипа и обоснование путей его совершенствования
Прототипом конструируемого стенда для выпрессовки игольчатых подшипников крестовин карданного вала на основании проведенного анализа конструкций принимаем установку Р-223. Данный стенд наиболее прост и удобен в использовании компактен прост в обслуживании.
Одним из недостатков стенда является повышенные требования герметичности так как используется гидравлическая установка.
Для совершенствования конструкции предлагается гидравлическую передачу заменить на механическую. Механическая передача проста в обслуживании и изготовлении имеет больший КПД (коэффициент полезного действия) меньшие габариты и имеет низкую себестоимость.
Предлагается для наибольшей универсальности стенда увеличиваем зазор между держателем и тисками что позволит производить выпрессовку игольчатых подшипников крестовин карданных передач легковых и грузовых автомобилей разных моделей.
Для облегчения центровки карданных валов устанавливаем самоцентрирующиеся губки на зажимные тисы что сократит время установки карданного вала.
Для передачи крутящего момента с вала двигателя на грузовой винт используем ременную передачу. Ременная передача с клиновыми ремнями гарантирует плавную и тихую работу. Способность к смягчению сильных изменений нагрузки и гашению колебаний является её достоинством. Благодаря простой и дешёвой конструкции (без корпуса и смазывания) которая не требует специального обслуживания и содержания получается уменьшение эксплуатационных расходов. Изношенные клиновые ремни можно быстро и легко заменить с минимальным временем простоя машины. Передаточное отношение можно легко изменить применяя ступенчатые шкивы и перекладывая ремень с одних ступеней на другие. Достоинством ременной передачи является также отсутствие перекоса привода во время кратковременных перегрузок что не обеспечивают другие механизмы. В результате может произойти их повреждение. Ременные передачи мало чувствительны к неточностям центровки валов. Ременные приводы делают возможным разделение мощности то есть перенос привода с одного вала на другие.
Для выпрессовки игольчатых подшипников различных диаметров необходимо использовать соответствующие насадки и стаканы.
К преимуществам передачи «винт-гайка» относятся простота и компактность конструкции большой выигрыш в силе точность перемещений. Недостатки этой передачи: большая потеря на трение и связанный с этим малый КПД.
Для повышения надежности во-первых устанавливаем два выключателя предельного положения во-вторых работу стенда будем производить при постоянном нажатии кнопки «назад - вперед» и в-третьих оснастим рабочий орган и ременную передачу защитным кожухом.
2 Разработка технического задания и кинематической схемы проектируемого стенда
Техническое задание это документ предназначенный для специалиста в котором отражаются цели требования к проекту и основные исходные данные необходимые для разработки а также сведения относящиеся к деятельности заказчика или свойства продукта.
Таблица 4.1 – Техническое задание
Основание для разработки
Задание полученное на кафедре ТЭРА ТОГУ
Источники разработки
Информационно-поисковая система «Мимоза» учебно-методическая справочная литература труды отечественных и зарубежных авторов посвященных расчетам деталей машин патенты авторские свидетельства прайс-листы оборудования для автосервисов Internet
Цель назначение производительность стенда
a)Улучшение технических показателей повышение производительности труда
b)Снижение времени на выпрессовку и увеличение производительности обслуживания и ремонта карданных передач
Продолжение таблицы 4.1 – Техническое задание
Конструктивные требования
a)Скорость подачи - 002 мс
b)Максимальное усилие создаваемое стендом
a)Изделие устанавливается в тиски
c)После выпрессовки стенд выключается
Требования надёжности
Стенд должен работать безотказно в течение 5 суток при круглосуточной работе совершая 25-30 операций в смену
Требования стойкости к внешним воздействиям
a)Стенд должен быть стойким к воздействию климатических факторов
b)Стенд должен быть устойчив к воздействию механических факторов свойственных при транспортировании автотранспортом
c)Эксплуатация стенда в закрытом отапливаемом помещение (температура воздуха 15-20 С влажность воздуха 75-100%)
Требования к конструкторской документации (КД) и эксплуатационной документации (ЭД)
a)КД в том числе и ЭД должна быть выполнена в соответствии с требованиями стандартов ЕСКД
b)КД должна быть пригодна к пересылке электронной почтой или передаче на иных носителях информации
c)Технологическая документация должна быть выполнена в соответствии с требованиями стандартов ЕСТД
Требования технологичности
a)При разработке КД несущих конструкций стенда должно отдаваться предпочтение применению стандартизированных покупных изделий по каталогам изготовителей и ранее разработанных и успешно применяемых изделий. Разработка оригинальных составных частей должна производиться только в технических и (или) экономически обоснованных случаях
b)Материалы и комплектующие изделия должны использоваться в условиях и режимах указанных в соответствующих стандартах (ТУ)
Требования безопасности и охраны окружающей среды
a)Стенд должен соответствовать общим требованиям безопасности по ГОСТ 12.2.003-91 и обеспечивать безопасность работающих при монтаже (демонтаже) вводе в эксплуатацию и эксплуатации при соблюдении требований предусмотренных в эксплуатационной документации (ЭД)
b)По способу защиты человека от поражения электрическим током стенд должен соответствовать классу 01 по ГОСТ 12.2.007.0
Окончание таблицы 4.1 – Техническое задание
c)В конструкторской документации (КД) включая ЭД должны быть учтены распространяющиеся на стенд требования стандартов системы стандартов безопасности труда
d)Стенд в процессе эксплуатации не должен загрязнять природную среду выбросами вредных веществ в количествах выше допустимых значений установленных соответствующими стандартами и санитарными нормами
Требования к взаимозаменяемости и унификации
Сменные элементы из состава запасных частей и принадлежностей должны быть взаимозаменяемыми
Требования эргономики
Стенд и его составные части должен соответствовать требованиям ГОСТ 12.2.049-80 ССБТ. Оборудование производственное. Общие эргономические требования
Требования к техническому обслуживанию и ремонту
Конструкция стенда должна обеспечить возможность проведения профилактических и регламентных работ
Требования к маркировке и упаковке
a)Маркировку следует наносить в соответствии с ГОСТ 26828-86 на несъёмных частях стенда доступных для обзора
b)Маркировка транспортной тары должна соответствовать требованиям ГОСТ14192 – 77
c)Упаковка составных частей стенда должна обеспечить их сохраняемость при хранении и транспортировании
Стадии этапы разработки
a)Анализ существующих аналогов и прототипов
b)Разработка технического задания
d)Расчеты составных частей конструкции
e)Проверочные расчеты на прочность
Кинематическая схема проектируемого стенда представка на рисунке 4.5. Даная кинематическая схема показывает принцип работы стенда. От двигателя момент передается на ведущий шкив 1 затем через ременную передачу 2 на ведомый шкив 1 затем через передачу винт-гайка - 4 воздействует на изделие которое крепится в тисках 5.
Рисунок 4.5 – Кинематическая схема
3 Проектный расчет стенда
Цель проектного расчета ориентировочно определить геометрические размеры проектируемого стенда.
3.1 Кинематический расчет стенда
Определить силу F необходимую для выпрессовки. На крестовину должна действовать сила:
где – предел прочности на смятие стали. Полагаем 16;
– площадь среза. Возьмем крестовину автобуса НЕФАЗ и посчитаем площадь среза - 80 мм2.
Выбор электродвигателя. Определим потребную мощность двигателя которая позволит производить выпрессовку.
где поступательная скорость движения звена 15;
общий КПД учитывающий все потери 15 таблица 1.1.
По ГОСТ 19523-74 согласно [c. 563 T.3 3] выбираем асинхронный двигатель 80А6920 с частотой вращения мощностью кВт.
Определим частоту вращения винта:
3.2 Расчет передачи винт-гайка. Основные параметры
Материал винта и гайки. Для винта принимаем сталь 45 термообработка – улучшение (предел текучести ) для гайки - оловянистую бронзу БрО10Ф.
Допускаемое давление и напряжение: Допускаемое давление (износостойкость резьбы) для пары сталь-бронза =9 МПа 15.
Для материала винта при коэффициенте запаса прочности =3 15.
Для материала гайки на растяжение и смятие ;.
Средний диаметр резьбы. Для передачи принимаем упорную резьбу. Конструкцию гайки выбираем цельную с коэффициентом высоты гайки .
Тогда средний диаметр резьбы ( мм):
где осевая сила действующая на винтовую пару;
коэффициент высоты головки гайки 15;
= 9 МПа - допускаемое давление по таблице 13.6 15.
По вычисленному значению выбираем большее ближайшее значение по ГОСТ 10177-82 таблица 13.4 1 номинальный диаметр резьбы мм. шаг резьбы мм. средний диаметр мм. внутренний диаметр винта мм.
Угол подъема резьбы.
Приведенный угол трения при коэффициенте трения и угле наклона рабочей стороны профиля .
Так как передача винт-гайка самотормозящаяся.
Размеры гайки. Высота гайки
Принимаем по стандарту Н=30 мм.
Наружный диаметр гайки:
Проверочный расчет винта на устойчивость. Один конец винта опирается шарнирно на ползун а другой шарнирно (вследствие зазоров в резьбе) закреплен в гайке. Принимаем коэффициент приведения длины учитывающий способ закрепления концов винта (оба конца опоры шарнирно).
Момент инерции поперечного сечения винта:
Радиус инерции сечения винта:
Согласно эскизной компоновке расчетная длина винта мм.
Для стали 45 выбираем: предельную гибкость материала ; гибкость винта при которой критическое напряжение в поперечном сечении равно пределу текучести – .
Следовательно этот винт малой гибкости для которого критическое напряжение равно пределу текучести т.е. специальный расчет на устойчивость не нужен.
Проверочный расчет винта на прочность.
Момент сопротивления в резьбе:
Согласно нашей конструкции винт опирается на ползун пятой диаметром . При стальном подпятнике примем коэффициент трения
Момент трения на торце пяты.
– винт; 2 – гайка; 3 – шкив ременной передачи.
Рисунок 4.6 – Расчетная схема вала
Строим эпюры продольных сил и крутящих моментов . При условии равномерного распределения осевой силы по виткам резьбы продольная сила винта в пределах гайки изменяется от до 0 а крутящий момент от до .
По эпюрам и опасное сечение винта может быть либо выше гайки (сечение а-а) либо ниже ее (сечение Б-Б). Доказано что сечение винта в пределах гайки менее опасно.
Выполним проверку опасных сечений.
Сечение А-А. В этом сечении продольная сила а крутящий момент
Эквивалентное напряжение
Сечение Б-Б. В этом сечении =:
следовательно в обоих сечениях прочность винта обеспечена.
Проверочный расчет гайки.
Проверка прочности тела гайки выполняется по напряжениям растяжения с учетом кручения Н
что меньше . Прочность тела гайки обеспечена.
Проверка опорной поверхности борта гайки выполняется по условию прочности на смятие:
что меньше . Прочность опорной поверхности борта гайки обеспечена.
3.3 Расчет ременной передачи
Расчет ременной передачи будем производить по методике изложенной [c. 61-68 2]. Передаваемая мощность кВт. частота вращения вала двигателя частота вращения винта .
Выбираем сечение клинового ремня по таблице 5.6 [2 с. 69] предварительно определи угловую скорость и номинальный вращающий момент
При таком значении а таблице 5.6 [2 с. 69] рекомендуется выбрать сечение ремня В с площадью поперечного сечения .
Выбираем диаметр ведущего шкива. В таблице 5.6 [2 с. 69] указано минимальное значение =200 мм. Однако для обеспечения большей долговечности ремня рекомендуется не ориентироваться на а брать шкив на 1-2 номера больше.
Определяем передаточное отношение без учета скольжения .
Диаметр ведомого шкива с учетом относительного скольжения .
Округляем в меньшую сторону по стандарту принимаем .
Уточняем передаточное отношение
Расхождение с заданным меньше 1% (при допускаемом 3%).
Определяем межосевое расстояние а: его выбираем в интервале:
Принимаем близкое к среднему значению .
Расчетная длина ремня определяется по формуле как и в случае плоскоременной передачи:
Ближайшая по стандарту длина [2 с. 68]
Вычисляем и определяем новое значение с учетом стандартной длины по формуле:
При монтаже передачи необходимо обеспечить возможность уменьшения на для того чтобы облегчить надевание ремней на шкив; для увеличения натяжения ремней необходимо предусмотреть возможность увеличения на ; в нашем случае необходимое перемещение составляет: в меньшую сторону в большую сторону
Угол обхвата на малом шкиве
По таблице 5.7 2 с.71-73 находим величину окружного усилия передаваемого одним клиновым ремнем сечения при и (интерполируя): - на один ремень.
Допускаемое полезное напряжение (удельное окружное усилие на единицу площади поперечного сечения ремня)
Коэффициент учитывает влияние угла обхвата . Так как зависит от межосевого расстояния то следует предварительно определить - его принимают равным удвоенной сумме диаметров шкивов:
Коэффициент учитывающий влияние длины ремня
Так как расчетная длина . Коэффициент учитывает условия эксплуатации передачи [c. 63 2]
Расчетное число ремней:
Определяем усилия в ременной передаче приняв напряжение от предварительного натяжения :
Предварительно натяжение каждой ветви ремня
Натяжение ведущей ветви
Натяжение ведомой ветви
Проверяем окружное усилие:
3.4 Подбор и проверка долговечности подшипников
Расчет конического роликового подшипника. Предварительно назначаем роликовый конический однорядный повышенной грузоподъемности подшипник по ГОСТ 27365-87 – 7312А (динамическая грузоподъемность). Определим реакции в опорах:
Суммарные реакции в опорах:
Определим долговечность подшипника на первой опоре. На эту опору действует радиальная реакция и внешняя осевая сила .
Эквивалентная нагрузка по формуле:
где коэффициенты ; Отношение этому отношению соответствует [таблица 7.3 с. 119 3]. Так как отношение то и .
Расчетная долговечность млн. об.
Расчетная долговечность ч.
Так как расчетный ресурс больше требуемого то предварительно назначенный подшипник 7312А пригоден.
Расчет шарикового подшипника.
Назначаем шариковый радиальный однорядный подшипник по ГОСТ 8338-75 – 209 (динамическая грузоподъемность).
Определим долговечность подшипника на второй опоре. На эту опору действует радиальная реакция .
Эквивалентная нагрузка по определяется формуле:
где – коэффициент радиальной нагрузки (принимаем =1);
– коэффициент учитывающий вращение колец (принимаем =1);
– коэффициент безопасности (принимаем =13);
– температурный коэффициент по 2 табл. 2.20 принимаем =1.
Так как расчетный ресурс больше требуемого то предварительно назначенный подшипник 209 пригоден.
4 Описание работы стенда
Ремонт карданного шарнира обычно заключается в замене игольчатых подшипников уплотнений и крестовины для чего шарнир необходимо разобрать. Подшипники в проушинах вилок установлены с натягом поэтому при разборке и сборке шарнира их приходится соответственно впрессовывать и запрессовывать.
Корпуса подшипников выпрессовывают в порядке представленном ниже.
Нанесите метки (краской или керном) определяющие взаимное положение разделяемых деталей чтобы соединить их при сборке в том же положении и сохранить неизменной балансировку валов.
Установите в тиски карданный вал. Снимите стопорные кольца.
Далее установите карданный вал одной из вилок карданного шарнира на опору пресса. Через специальную втулку штоком пресса переместите другую вилку шарнира вниз до упора в крестовину.
Повернув вилку шарнира на 180° повторите указанные операции то есть переместите другой конец вилки вниз до упора в крестовину. При выполнении этих операций противоположный подшипник крестовины частично выйдет из отверстия вилки и в полученный зазор между вилкой и крестовиной можно будет установить втулку с боковым вырезом.
Установив втулку на шип крестовины переместите вилку шарнира вниз до выпрессовки подшипника.
Используя указанные приемы выпрессуйте другие подшипники крестовины.
5 Правила безопасности и эксплуатации стенда
Одним из основных мероприятий по обеспечению безопасности труда являются обязательный инструктаж всех работников предприятия.
Снижение производственного травматизма во многом зависит от того в каком состоянии находится гаражное оборудование и приспособления.
Прежде всего стенд и его приспособления должны быть чистыми и исправными. Приступая к работе слесарь должен привести в порядок спецодежду проверить наличие и исправность инструментов оборудования и предохранительных приспособлений. Место где рабочий производит поручаемую ему работу должно хорошо освещаться и не загромождаться изделиями и материалами не имеющими прямого отношения к производственной работе. В месте производства работ запрещается находиться лицам не имеющим прямого отношения к этим работам.
Эксплуатируемое оборудование должно находиться в полной исправности и за его состоянием должен быть обеспечен постоянный надзор со стороны определённых лиц назначенных администрацией предприятия или лично технического руководителя.
Эксплуатационное обслуживание электродвигателя должен выполнять квалифицированный персонал электромонтеры. Электродвигатель должен быть обязательно заземлен. В случае возникновения любых неисправностей электродвигатель должен быть немедленно обесточен.
Техническое обслуживание электродвигателя сводится в основном к своевременной замене подшипников. При критическом износе подшипников электродвигателя (появляется характерный шум сепараторов) возможно их разрушение и заклинивание
Рабочее место должно иметь достаточную освещенность т.е соответствовать нормам освещенности СНИП 23-05-95 «Естественное и искусственное освещение».
Техническое обслуживание ременных передач сводится к периодической проверки состояния ремней. При появлении трещин разрывов расслоений и других дефектов ремень следует заменить а ослабленный натянуть.
Для компенсации вытяжки ремней в процессе их эксплуатации компенсации отклонений длины ремней а также легкости надевания новых ремней предусмотрено регулирование межосевого расстояния ременной передачи поворотом плиты на которой расположен электродвигатель.
ОХРАНА ТРУДА И ТЕХНИКА БЕЗОПАСНОСТИ
Вопросы охраны труда имеют большое значение для обеспечения безопасности и улучшения условий труда создание рабочей обстановки исключающей профессиональные заболевания и производственный травматизм что способствует повышению эффективности труда и производства 21 с.195.
В настоящей выпускной квалификационной работе предлагается внедрить на агрегатный участок стенд для выпресовке подшипников крестовин карданных передач.
В соответствии с требованиями Трудового Кодекса РФ №197-Ф3 от 30.12.01 работодатель обязан обеспечить соответствующие требования охраны труда на каждом рабочем месте 22.
Таблица 5.1 – Причины несчастных случаев и их количество по профессиям на 2009 г.
в том числе по профессиям ед.
Неумышленное повреждение
Резкое торможение автобуса
Неудовлетворительное состояние покрытия дороги
В таблице 5.1 представлено количество несчастных случаев по профессиям произошедших на МУП «ХПАТП №1» за последние три года и их причины.
Как видно из таблицы 5.1 наиболее частыми причинами несчастных случаев являются неосторожность и нарушение правил техники безопасности. Чаще всех травмы получают водители и слесари находящиеся во время работы в зонах ТО и Р. Это объясняется наличием многих опасных факторов: маневрирование транспорта при постановке его на посты; движущиеся части оборудования смотровые канавы. Наиболее частыми травмами на предприятии являются: ушибы мягких тканей а также переломы костей.
Для выявления и сведения к минимальным значениям величин опасных и вредных производственных факторов на предприятии проводится аттестация рабочих мест по условиям труда согласно приказу Министерства здравоохранения и социального развития российской федерации от 31 августа 2007 г. N 569 «Об утверждении порядка проведения аттестации рабочих мест по условиям труда» 24. Результаты аттестации используются так же при планировании и проведении мероприятий по охране труда предоставлении льгот и компенсаций работникам за неблагоприятные условия труда.
1 Анализ условий труда
Территория МУП ХПАТП ограждена забором в ночное время она освещается искусственным источником света.
В основном производственном корпусе имеются санитарно-бытовые помещения. К ним относятся: гардеробный блок оснащённый шкафчиками для переодевания туалетная комната с умывальниками душевая курительная комната и комната отдыха.
Для доставки рабочих на предприятие имеется служебный автобус. Работы по ежедневному обслуживанию ТО и ТР производятся в две смены по восемь часов каждая с часовым перерывом на обед и отдых. Все производственно-вспомогательные участки работают в одну смену с часовым перерывом на обед и отдых. Работы по общему и углубленному диагностированию перед ТО и ТР производятся также в дневную смену. Питание рабочих всех смен осуществляется в столовой которая имеется на предприятии.
Для улучшения условий труда рабочим предприятия выдаётся спецодежда: перчатки ботинки костюмы очки. Для сварщиков дополнительно предусматривается брезентовый костюм и сварочная маска.
На предприятии имеется медпункт. Перед каждым выездом на линию и в конце смены водители проходят медицинский осмотр. Предприятие имеет спортивный комплекс предназначенный для поддержания физического здоровья его работников.
В производственных помещениях имеется механическая приточно-вытяжная вентиляция которая обеспечивает удаление выделяемых паров и газов а так же приток свежего воздуха. Естественное и искусственное освещение рабочих мест достаточное для безопасного выполнения работ.
На агрегатном участке оборудование находится в исправном состоянии заземлено и используется только по своему прямому назначению. Оголенные провода отсутствуют. Розетки исправны. Проходы между рабочими местами не загромождены деталями и узлами нет скопления большого количества деталей.
При проведении ремонта агрегатов автомобиля возможно и неизбежно возникновение вредных и опасных производственных факторов: движущихся автомобилей повышенной загазованности помещения отработавшими газами повышенных условий шума опасности поражения электрическим током и другие.
Повышенную опасность представляют операции снятия и установки агрегатов поскольку в них накоплена значительная потенциальная энергия. Эти операции выполняются на стендах или с помощью специального оборудования обеспечивающего безопасное проведение работ.
Общие санитарно-гигиенические требования к показателям микроклимата и допустимому содержанию вредных веществ в воздухе рабочей зоны содержаться в СанПиН 2.2.4.548 – 96 «Гигиенические требования к микроклимату производственных помещений» 25 ГОСТ 12.1.005-88 ССБТ «Общие санитарно-гигиенические требования к воздуху рабочей зоны» 26.
На агрегатном участке выполняются работы связанные с постоянной ходьбой перемещением и переноской тяжестей до 10кг и сопровождающиеся умеренным физическим напряжением. Данные виды работ по СанПиН 2.2.4.548 – 96 25 относятся к работам средней тяжести категории работ II б. Оптимальные и допустимые параметры микроклимата для данной категории работ для помещения с постоянными рабочими местами представлены в таблице 5.2.
Фактическая влажность воздуха на агрегатном участке составляет 60-70% в течение года что не превышает допустимую норму в 75% согласно СанПиН 2.2.4.548 – 96 25.
Таблица 5.2 – Нормируемые параметры микроклимата 25
Относительная влажность %
Скорость движения воздуха мс
Фактическая температура воздуха в рабочей зоне в холодный период составляет +18°С в тёплый период +20°С что не превышает допустимых значений температур для холодного периода 15-21°С для тёплого 16-27°С согласно СанПиН 2.2.4.548 – 96 25.
На агрегатном участке выделение пыли связано с разборкой и сборкой агрегатов узлов и деталей. Помимо пыли в воздухе встречаются вредные вещества. Вредные вещества выделяют двигатели внутреннего сгорания процессы сварки обработки металла заправки агрегатов маслом и техническими жидкостями.
Количество вредных веществ в воздухе рабочей зоны составляет: СО 15 мгм3 что не превышает предельно допустимую концентрацию (ПДК) 20 мгм3 азота окислы 2 мгм3 что не превышает ПДК 5 мгм3 акролеин 005 мгм3 что не превышает ПДК 02 мгм3 SO2 05 мгм3 что не превышает ПДК 1 мгм3. Данные о ПДК вредных веществ установлены ГН 2.2.5.686-98 «Предельно допустимая концентрация вредных веществ в воздухе рабочей зоны. Гигиенические нормативы» 27.
Помещение агрегатного участка оборудовано общеобменной механической приточно-вытяжной вентиляцией. Имеется и местная вытяжная вентиляция обеспечивающая разбавление и удаление вредных веществ. Приток воздуха должен направляться рассредоточено в рабочую зону и смотровые канавы. Воздух должен подаваться в холодный период со скоростью не более 04 мс и в теплый не более 05 мс.
Источником шума и вибрации в производственном корпусе являются двигатели автомобилей компрессоры различные стенды подъёмное оборудование. Для определения допустимого уровня шума на рабочих местах используется ГОСТ 12.1.003-83 ССБТ «Шум. Общие требования безопасности» 28 СН 2.2.42.1.8.562-96 «Шум на рабочих местах в помещениях жилых общественных зданий и на территории жилой застройки» 29. Допустимые уровни звукового давления в октавных полосах частот уровни звука и эквивалентные уровни звука на агрегатном участке представлены в таблице 5.3.
Таблица 5.3 – Предельно-допустимые уровни звукового давления
Вид трудовой деятельности рабочего места
Уровни звукового давления дБ в октавных полосах со среднегеометрическими частотами Гц
Выполнение всех видов работ на постоянных рабочих местах в производственных помещениях
Основные мероприятия по борьбе с шумом - это технические мероприятия которые проводятся по трем главным направлениям: устранение причин возникновения шума или снижение его в источнике; ослабление шума на путях передачи; непосредственная защита работающих.
Предотвращение вредного воздействия шума осуществляется по следующим направлениям: уменьшение шума в источниках возникновения (установка кожухов глушителей); изменение направления шума (экранирование); поглощение шума (звукопоглощающие материалы); применение средств индивидуальной защиты.
Вибрация возникает в результате износа валов подшипников недостаточного закрепления узлов и механизмов на корпусе тележки а также в процессе движения тележки. Допустимые параметры вибрации устанавливаются СН 2.2.42.1.8.566-96. Санитарные нормы. Производственная вибрация вибрация в помещениях жилых и общественных зданий 30 и ГОСТ 12.1.012-90. Вибрационная безопасность. Общие требования 31.
Рабочий персонал на агрегатном участке подвержен воздействию общей вибрации 3 категории типа «а». Предельно-допустимые значения вибрации для данной категории представлены в таблице 5.4.
Таблица 5.4 – Предельно-допустимые значения вибрации
Среднегеометрическая частота полос Гц
Вибрацию снижают воздействием на источник возбуждения (устранение резонансных явлений повышение люфтов балансировка) а также на путях её распространения (использование дистанционного управления виброизоляции виброгашения).
Длительное воздействие вибрации высоких уровней на организм человека приводит к развитию преждевременного утомления снижению производительности труда росту заболеваемости и нередко к возникновению профессиональной патологии - вибрационной болезни. Вибрацию по способу передачи на человека (в зависимости от характера контакта с источниками вибрации) условно подразделяют на местную (локальную) передающуюся на руки работающего и общую передающуюся через опорные поверхности на тело человека в положении сидя (ягодицы) или стоя (подошвы ног). При работе на агрегатном участке имеет место сочетание действий местной и общей вибрации (гайковерты электроподъёмники и др.)
На агрегатном участке проводятся зрительные работы высокой точности разряд зрительной работы (согласно СНиП 23-05-95 «Естественное и искусственное освещение» 32) III б нормативное значение освещенности Ен = 300 лм.
Согласно Правилам установки электроустановок (ПУЭ)33 помещение агрегатного участка по электроопасности относится ко второму классу опасности - помещениям с повышенной опасностью. Так как в помещении агрегатного участка присутствует токопроводная пыль (металлическая сажа и т.д.) и большое количество металлоконструкций.
Действие электрического тока на организм человека приводит к электротравмам которые по признаку поражения делят на электрические удары и травмы. В первом случае поражается весь организм и особенно его внутренняя часть. Во втором случае происходит местное поражение кожи мышц и других частей тела. Особенно опасен для человека электрический удар при котором нарушается сердечная и мозговая деятельность 38.
При проектировании способов и средств защиты людей при взаимодействии их с электроустановками постоянного и переменного тока необходимо руководствоваться ГОСТ 12.1.038-82 «Электробезопасность. Предельно допустимые уровни напряжений прикосновения и токов» 34 и ГОСТ 12.1.019-79 ССБТ «Электробезопасность. Общие требования и номенклатура видов защиты» 35.
2 Мероприятия по повышению безопасности и улучшений условий труда
К мероприятиям по повышению техники безопасности проводимым на предприятии относят: инструктаж обучение массовая пропаганда планирование мероприятий по охране труда организация контроля за параметрами микроклимата и состоянием защитных устройств 36.
Все работники автотранспортного предприятия проходят обязательный инструктаж по ТБ раз в полгода. Те из них кто выполняет работы повышенной опасности должны прослушивать инструктаж проводимы главным инженером один раз в три месяца. Особое внимание при регулярном инструктаже должно уделяться случаям нарушения ТБ работниками предприятия за последний период с целью предупреждения их возникновения в будущем.
При инструктаже новичков проводится полное их ознакомление с особенностями работы отрасли и предприятия распорядком работы правилами передвижения по территории особенностями пользования средствами защиты и личной санитарии а также с оказанием первой доврачебной помощи во время несчастного случая. Новый работник должен быть ознакомлен с расположением аптечек пожарных гидрантов огнетушителей и схем эвакуации из помещений. Особое внимание при инструктаже должно уделяться практическим занятиям по безопасному выполнению своих обязанностей на рабочем месте.
После проведения вводного инструктажа проводится первичный инструктаж на рабочем месте. Мастер цеха знакомит работника с участком общими правилами техники безопасности при работе с электроприборами и технологическим оборудованием.
Повторный инструктаж проводиться не реже 1 раза в квартал. Проведение инструктажей регистрируется в журнале регистраций находящегося у начальника цеха 36.
Для улучшения интерьера и создания благоприятного микроклимата на агрегатном участке рекомендуется разместить следующие растения: кипарис вечнозеленый плющ обыкновенный.
С целью обеспечения быстрой и эффективной врабатываемости длительного поддержания высокого уровня работоспособности и производительности труда необходимо в режимах труда и отдыха предусматривать регламентированные перерывы во время которых следует транслировать (функциональную музыку).
Уборку пола стен потолков окон и ворот в моторном цехе производят рабочие этого цеха в соответствии с периодичностью установленной хозяйственной службой АТП.
3 Меры безопасности при слесарных работах
Пульты управления аппаратные шкафы блоки барабанов и роликов и другое электрическое оборудование должны быть надежно заземлены.
Запрещается работать на стендах при снятых кожухах щетках ограждениях.
При подготовке к работе на стендах необходимо проверить: крепление всех узлов и деталей стенда наличие исправность и крепление защитных ограждений и заземляющих проводов исправность подземных механизмов и других приспособлений: достаточность освещения рабочего места и путей движения авто.
Во время работы стендов запрещается: открывать пульт управления стендом; доводить частоту вращения ротора электрической машины выше допустимой.
Рабочее место слесаря должно содержаться в чистоте и не загромождаться деталями. Слесарные верстаки за которыми работают несколько человек необходимо разделять сетчатыми перегородками установленными посередине верстака (с ячейками не более 3 мм.) имеющими высоту не менее 1 м для защиты слесаря от отлетающих осколков метала сорвавшегося инструмента и т.п. с соседнего рабочего места 23
Для переноски инструментов если это требуется по условиям работы каждому рабочему выдается сумка или легкий переносной ящик. Использованный обтирочный материал собирается в установленные для этих целей металлические ящики с плотными крышками.
Требование к слесарным инструментам. Рукоятки молотков и кувалд должны быть гладкими овальными и изготовлены из прочных и вязких пород дерева (дуба березы кизила рябины и т.д.). Слесарные молотки и кувалды должны иметь слегка выпуклую не косую и не сбитую без трещин поверхность бойка должны быть надежно укреплены на ручках путем расклинивания металлическими клиньями и не иметь наклепа. Ось ручки не должна быть под прямым углом к продольной оси инструмента. Длина ручек слесарных молотков должна быть 300 400 мм. а ручек кувалд450-900 мм. В зависимости от массы.
Напильники шаберы отвертки ножовки и другой ручной инструмент с заостренным не рабочим концом должны быть прочно закреплены в гладкой ровной зачищенной рукоятке. Рукоятка должна иметь длину в соответствии с размером инструмента но не менее 150 мм. и должна быть стянута металлическими бандажными кольцами.
Ударные инструменты (зубила крейцмейсели бородки просечки керны и т. д.) не должны иметь скошенных или сбитых затылков заусениц вмятин выбоин трещин и наклепов. При работе зубилом бородком или другим подобным инструментом необходимо пользоваться защитными очками. Длина зубила бородка керна не должна быть менее 150 мм.
Гаечные ключи должны строго соответствовать размерам гаек и болтов и не иметь выработки зева трещин забоев и заусениц. Запрещается отвертывание гаек ключами больших размеров с подкладыванием металлических пластинок между гранями гаек и ключа а так же удлинение рукоятки ключа путем присоединения другого ключа или трубы. Раздвижные ключи должны быть без зазора в подвижных частях 23.
Лезвие отвертки должно по толщине соответствовать ширине шлица у головки винта.
Острогубцы и плоскогубцы не должны иметь выщербленных рукояток. Губки острогубцев должны быть острыми не выщербленными не сломанными а губки плоскогубцев должны быть с исправной насечкой. Слесарные тески должны иметь исправные губки и зажимный винт.
4 Расчет вентиляции
Расчет искусственной вентиляции производится для помещений где кратность воздухообмена установлена более двух.
Расчет искусственной вентиляции производится по формуле 37:
где - часовой объем вентилируемого воздуха;
- объем помещения участка =554;
- кратность воздухообмена =5.
После определения часового объема вентилируемого воздуха выбираем вентилятор: Центробежный вентилятор серии ЭВР №2. Частота вращения - 1500 обмин. Производительность - 700 ч. Напор - 25 кг КПД вентилятора - 056.
Расчет мощности электродвигателя вентилятора производится по формуле 37:
где - мощность электродвигателя для привода вентилятора кВт;
- напор воздушного потока =25 кгм;
- КПД вентилятора =056;
- КПД передачи (для вентиляторов этого типа 09);
- коэффициент учитывающий неучтенные потери напора воздушного потока. = (15).
5 Расчет естественного освещения
Организация рационального освещения рабочих мест является одним из основных вопросов организации труда. При неудовлетворительном освещении зрительная способность глаза снижается что может привести к тяжелым травмам.
Расчет естественного освещения производится по формуле 38:
где - суммарная площадь окон участка ;
- площадь действительная участка .
Зная общую площадь окон и площадь одного окна можно найти количество окон. Принимаем размеры окон: ширина l=216 м высота h=2 м. Тогда площадь одного окна = 432 .
Затем определив количество пролетов между колоннами по фасаду выбираем количество окон и площадь каждого из них учитывая кратность размеров по ширине и высоте. Берем 3 окна шириной 216 площадью 432 .
6 Расчет искусственного освещения
Расчет выполняется методом коэффициента использования светового потока. Учитывая что на агрегатном участке проводятся зрительные работы высокой точности (согласно СНиП 23-05-95 31) а также высоту потолка на участке h=4 м принимаем для освещения:
- люминесцентные лампы типа ЛХБ;
- тип светильника ШОД;
Световой поток определяется по формуле 38 с.2:
где - нормативное значение освещенности = 300 лм. 38 табл.1;
S – площадь помещения ;
- коэффициент запаса учитывающий запыление светильников и износ источников света в процессе эксплуатации = 15 38 табл.3;
- поправочный коэффициент учитывающий неравномерность освещения = 11 38;
- число светильников шт.;
n - количество ламп в светильнике n=2 38 с.233;
– коэффициент затенения рабочего места работающим = 085;
- коэффициент использования светового потока = 057 38 табл.3-11.
Коэффициент использования светового потока определяется в зависимости от типа светильника коэффициентов отражения стен и потолка помещения и индекса помещения. Индекс помещения определяется по формуле 38:
где и – длина и ширина помещения м;
– высота подвеса светильников над рабочей поверхностью = 28 м.
Количество светильников определяется:
где - количество светильников по длине участка шт.;
- количество светильников по ширине участка шт.
где - коэффициент соотношения расстояния между рядами светильников и высотой подвеса светильников над рабочей поверхностью =13 38 табл.71;
расстояние между светильниками м.
Выбираем лампу ЛХБ 65-4 =3820 лм. 38табл.7.
Рисунок 5.1 – Схема расположения светильников
Рассчитаем фактическую освещенность с учетом выбранной лампы:
Определим разницу между освещенностью фактической и расчетной. Приемлемым считается .
Так как фактическая освещенность отличается от расчетной на 10 % то подобранная мощность ламп и схема расположения светильников обеспечит требуемую освещенность.
7 Пожарная безопасность
Согласно ГОСТ 12.1.033-81 «ССВТ. Пожарная безопасность. Термины и определения» 39. Пожарная безопасность – состояние объекта при котором с установленной вероятностью исключается возможность возникновения и развития пожара и воздействия на людей опасных факторов пожара а так же обеспечивается сохранность материальных ценностей.
Для помещений автотранспортных мероприятий характерна высокая пожароопасность. Основными причинами возникновения пожаром на автотранспортных предприятиях являются: неисправность отопительных приборов электрооборудования и освещения неправильная их эксплуатация самовозгорание горюче-смазочных и обтирочных материалов при неправильном их хранении; неосторожное обращение с огнем.
В соответствии с действующим законодательством ответственность за обеспечение пожарной безопасности на ХПАТП несут их руководители. Ответственность за пожарную безопасность отдельных участков возлагается на начальников соответствующих служб назначенных приказом руководителя предприятия.
Для пожарной охраны ХПАТП создают добровольные пожарные дружины. На эти дружины возлагается контроль за соблюдением противопожарного режима на ХПАТП и надзор за исправным состоянием первичных средств пожаротушения. Численный состав добровольных пожарных дружин определяется руководителем ХПАТП.
На территории автотранспортного предприятия все проходы лестницы проезды и рекреации свободны для проезда. Запрещено применение чердаков в качестве производственных помещений.
На видных местах размещены планы эвакуации людей автомобилей и оборудования на случай пожара.
Во всех производственных помещениях предприятия необходимо выполнять следующие противопожарные требования:
курить только в специально отведенных для этого месте;
не пользоваться открытым огнем;
хранить топливо керосин в количествах не превышающих сменную потребность;
не хранить порожнюю тару из-под топливных и смазочных материалов;
проводить тщательную уборку в конце каждой смены; разлитое масло и топливо убирать с помощью песка;
собирать использованные обтирочные материалы складывать их в металлические ящики с крышками и по окончании смены выносить их в специально отведенное для этого место.
не мыть и не протирать кузов детали и агрегаты автомобиля а также руки и одежду бензином;
не оставлять открытыми горловины топливных баков и сосудов с воспламеняющимися жидкостями и др.;
Для наружного пожаротушения предусмотрен объединённый хозяйственно-питьевой противопожарный водопровод который обеспечивает не только хозяйственно-питьевые но и противопожарные нужды. Расход воды на наружное пожаротушения составляет 10 лс.
Для разработки мероприятий по пожарной безопасности необходимо знать классификацию производства по степени огнестойкости и категории пожарной опасности.
Определение категории помещения по пожарной опасности осуществляется согласно СНиП 31–03-2001 «Определение категорий помещений и пожарной безопасности» 40. На основании классификации помещений автотранспортного предприятия по взрывной взрывопожарной и пожарной опасности помещения агрегатного участка относится к категории Д (несгораемые вещества и материалы в холодном состоянии)41.
При определении помещения по степени огнестойкости следует руководствоваться СниП 21–01-97 «Пожарная безопасность зданий и сооружений» 42. Помещение зоны агрегатного участка относиться к I степени огнестойкости.
Помещение производственного корпуса обеспечено первичными средствами пожаротушения и пожарным инвентарем. В перечень первичных средств пожаротушения на агрегатном участке входит: огнетушители пенные - 2шт. огнетушители углекислотные - 1шт. ящик с песком - 1шт. асбестовое или войлочное полотно - 1шт. ломы - 2шт. багры – 3шт. топоры - 2шт. лопаты - 2шт. ведра пожарные - 2шт. жесткие буксиры - 2шт.
Для внутреннего пожаротушения предусмотрены огнетушители из расчёта на 100 м 2 площади помещения: порошковые огнетушители ОП-5 - 2ящик с песком вместимостью 1 м куб. и пенные огнетушители ОХП-10 – 2 шт.
В случае возникновения пожара необходимо:
-немедленно вызвать пожарную охрану по телефону 01.
-обеспечить безопасную эвакуацию людей.
-отключить станки и электрооборудование от электрической энергии
-приступить к тушению пожару имеющимися средствами пожаротушения.
Горючие жидкости а также загоревшуюся электропроводку водой тушить нельзя. Бензин керосин различные органические масла и растворители следует тушить песком землей пенными и порошковыми огнетушителями а если очаг пожара небольшой - накрыть его асбестовым или брезентовым покрывалом тяжелой тканью или одеждой смоченной водой. Горящую электропроводку тушить можно только убедившись что с нее снято напряжение.
8 Охрана окружающей среды и экономия материальных ресурсов
Для создания условий снижения неблагоприятного воздействия агрегатного участка на окружающую среду необходимо соблюдать следующие правила:
Регулярно проводить с работниками участков и отделений инструктажи и занятия по основам экологической безопасности.
Следить за своевременным обслуживанием двигателей и тем самым снизить масштабы их ремонта.
Экологически вредные отходы складывать только в специально отведенных местах в специальной таре.
Регулярно ремонтировать и очищать канализационные фильтры и отстойники.
Моечно-очистные сооружения должны создаваться по замкнутому типу чтобы исключить попадание токсичных веществ в общие канализационные стоки.
На экономию ресурсов автотранспортного предприятия оказывает большое влияние число организационно - технических факторов. Наибольшее влияние имеют следующие группы внутрипроизводственных факторов:
- повышение технического уровня предприятия;
- совершенствование организации технического обслуживания и ремонта;
- изменение объема перевозок.
Исходные данные экономических показателей агрегатного участка представлены в таблице 6.1.
Таблица 6.1 – Исходные данные экономических показателей агрегатного участка
Трудоемкость выполняемых работ агрегатного участка:
- до совершенствования чел.ч.
- после совершенствования чел.ч.
Штатная численность ремонтных рабочих:
- до совершенствования чел.
- после совершенствования чел.
Средний разряд работ выполняемых на агрегатном участке
Норма затрат на запасные части р.1000 км
Совершенствование организации работ на агрегатном участке МУП «ХПАТП №1» предполагает изготовление универсального стенда для выпресовки подшипников крестовин карданных валов и приобретение стенда для расточки тормозных барабанов и обточки накладок автобусов. Предполагается объединить агрегатный участок и участок ремонта тормозных колодок что приведет к высвобождению площади.
Стенд для выпрессовки подшипников крестовин карданных валов и стенд для расточки тормозных барабанов и обточки накладок необходимое оборудование для любого агрегатного участка. Неудовлетворительно состояние наших дорог является частой причиной поломки крестовины карданного вала а от правильностии своевременности расточки тормозных барабанов зависит правильная работа автомобиля и безопасность движения.
Данные мероприятия приведут к уменьшению трудоемкости выполняемых работ снижению численности ремонтных рабочих. Приобретаемое оборудование приведет к росту коэффициента технической готовности. Дальнейшие расчеты позволят определить экономический эффект от совершенствования организации работ на агрегатном участке.
1 Определение суммы дополнительных капитальных вложений
Дополнительные капитальные вложения складываются из стоимости изготовления стенда и стоимости дополнительного приобретаемого оборудования.
Стенд изготавливается на предприятии с привлечением ремонтных рабочих. Смета затрат на изготовление стенда состоит из следующих статей:
затраты на материалы и покупные изделия;
затраты на оплату труда;
отчисления на социальные нужды;
общепроизводственные расходы.
Для определения материальных затрат на изготовление стенда по каждому виду материала устанавливается их потребное количество в тоннах и определяются цены.
Материальные затраты на изготовление стенда представлены в таблице 6.2.
Таблица 6.2 – Материальные затраты на изготовление стенда
Требуемое количество кг.
Цена за 1 ед.р. на 2010 г.
Прокат стальной (уголок 100×100×16 ГОСТ 8509-93)
Масло И-12А ГОСТ 20799-88
Смазка Литол-24 ГОСТ 21150-75
Герметик ГОСТ 8764-96
Эмаль ПФ-115 ГОСТ6465-76
Итого с учетом доставки:
Сумма затрат на покупные изделия и метизы представлена в таблице 6.3.
Таблица 6.3 - Затраты на покупные изделия
Требуемое количество шт.
Цена за 1 ед.р. на 2010 г.
Болт М8-6gх40.58.016
Болт М 12 -6gx60.58.016
Болт М 14-6gx60.58.016
Болт М 16 -6gx60.58.016
Болт М 20-6gх45.58.016
Болт М 36-6gх45.58.016
Окончание таблицы 6.3 - Затраты на покупные изделия
Гайка М16-6Н ГОСТ 5915-70
Концевой выключатель
Тиски слесарные TMS-61005
Шайба 8 65 Г ГОСТ 6402-70
Штифт 2.6х24 ГОСТ 3129-70
Штифт 2.8х40 ГОСТ 3128-70
Корпус силового узла
Расчет затрат на заработную плату рабочих занятых изготовление стенда выполняется в следующей последовательности:
Фонд заработной платы ФЗП определяем по формуле:
где - фонд заработной платы основной р;
- фонд заработной платы дополнительный р.
Основной фонд заработной платы определим по формуле:
где - тарифный фонд заработной платы р;
- размер надбавок и доплат (к расчету принимается 15-20 % к в данном случае принимаем =20%);
- размер премии (к расчету принимаем 20% к );
- районный коэффициент (60%).
где - трудоемкость изготовления подъемника чел.×ч;
- ставка тарифная часовая соответствующего разряда р.
Работы по изготовлению стенда занимаются рабочие V разряда. Часовая тарифная ставка для рабочих V определяется по формуле:
где - часовая тарифная ставка рабочего первого разряда р. Часовая тарифная ставка первого разряда определяется отношением минимального размера оплаты труда к количеству часов отработанных за месяц р.
- тарифный коэффициент 5-ого разряда.
Тогда тарифный фонд заработной платы определим по формуле:
По формуле 6.3 определим основной фонд заработной платы:
Дополнительная заработная плата составляет 14% от основной.
Тогда общий фонд заработной платы определи по формуле 6.2.
Отчисления на социальные нужды (единый социальный налог - ЕСН) производятся по установленной Правительством России ставке в 26 % к .
Определение косвенных расходов. Косвенные расходы (содержание оборудования общепроизводственные расходы и др.) определяются в процентах от заработной платы (150%).
Смета затрат на изготовление стенда приведена в таблице 6.4.
Таблица 6.4 - Смета затрат на изготовление стенда
Затраты на основные материалы
Затраты на покупные изделия
Заработная плата рабочих
Единый социальный налог
Дополнительные капитальные вложения ( = 323171 р.) складывается из затрат на изготовление стенд для выпрессовки подшипников крестовин карданных передач и приобретения стенда для расточки тормозных барабанов и обточки накладок автобусов.
2 Определение экономического эффекта
Положительный экономический эффект от внедрения данного мероприятия будет выражаться в снижении затрат на содержание участка на материалы и запасные части в снижении расходов на оплату труда и единый социальный налог. Приобретаемое оборудование приведет к снижению трудоемкости и как следствие к росту коэффициента технической готовности и общегодового пробега.
Однако приобретаемое оборудование приведет к росту затрат на электроэнергию амортизационных отчислений и затрат на содержание оборудование.
Годовая трудоёмкость участка до мероприятий - 16 49629 чел.×ч после 1451673 чел.×ч.
Тарифную ставку ремонтного рабочего 4 разряда определим по формуле:
где - тарифный коэффициент 4 разряда.
Тарифный фонд заработной платы за год определим по формуле 6.3.
Основной фонд заработной платы за год определяется по формуле 6.2.
Принимаем дополнительную заработную плату в размере 14% от .
Общий фонд заработной платы определи суммированием тарифного фонда заработной платы и дополнительного фонда заработной платы:
Соответственно месячная заработная плата одного рабочего равна формуле
где – количество рабочих на участке.
Месячная заработная плата одного рабочего равна:
Таким образом среднемесячная заработная плата после внедрения вырастет на 3%.
Отчисления на единый социальный налог (СВ) определим по формуле:
Таблица 6.5 – Сводный план по труду и заработной плате
Расчетная численность рабочих чел.
Годовой фонд заработной платы тыс. р.
3 Определение срока окупаемости дополнительных капитальных вложений
При расчете годового экономического эффекта от внедряемых организационно-технических мероприятий необходимо руководствоваться следующими правилами:
а) Должна быть обеспечена полная сопоставимость сравниваемых вариантов что обеспечивается следующими условиями:
- равными эксплуатационными условиями на которые внедряемое мероприятие не оказывает влияние;
- одинаковыми ценами на сырье и материалы;
- одинаковыми нормами и нормативами;
- одинаковыми методами расчета показателей и статей затрат.
б) За базу сравнения принимаются показатели заменяемой техники с учетом повышения технического уровня производства достигаемого в расчетном году. После внедрения учитываются фактические показатели внедряемой техники получаемые на предприятии.
в) При расчете годового экономического эффекта должны учитываться те затраты которые изменяются в связи с внедрением новой техники причем косвенные затраты (цеховые затраты затраты на содержание оборудования общепроизводственные) должны определяться прямым счетом – по изменяющимся статьям а не укрупненным способом.
Потребность в запасных частях и ремонтных материалах на проведение ремонтов подвижного состава в целом по АТП определяют на основе действующих норм расхода по каждому виду технических воздействий на 1000 км пробега. Нормы затрат на запасные части и материалы согласно данных предприятия составляет 350 р.1000 км.
Затраты на материалы и запасные части до совершенствования производства определяем по формуле:
где – норма затрат на запасные части на 1000 км р.1000км;
– годовой пробег всего подвижного состава = 1341 млн.км;
- коэффициент учитывающий категорию условий эксплуатации = 125;
- коэффициент учитывающий модификацию подвижного состава = 10;
- коэффициент учитывающий природно-климатические условия = 125.
Трудоёмкость работ на агрегатном участке в результате совершенствования уменьшилась на 12% отсюда следует что простои в ремонте сократятся на 1349 авто-день. Тогда изменение коэффициента выпуска определим по формуле:
где - количество авто-дней сокращения простоя = 1124 авто-день;
– количество рабочих дней в году = 365 дн.;
- списочное количество автобусов = 348 ед.
В результате совершенствования организации работ на агрегатном участке наблюдается увеличение коэффициента выпуска =106% и уменьшение затрат на запасные части и ремонтные материалы за счёт повышения качества выполнения работ.
Данное мероприятие позволит снизить затраты на запасные части на 15%. Таким образом экономический эффект от экономии затрат на запасные части и ремонтные материалы определим по формуле:
Годовой экономический эффект от совершенствования организации работ на агрегатном участке определим по формуле:
где - экономия от снижения заработной платы р.;
- экономия от снижения затрат на единый социальный налог р.;
- экономия от снижения затрат на охрану труда р. Затраты на охрану труда примем 11% от ФЗП.
- экономия от снижения расходов на запасные части и материалы р.;
Данные мероприятия повлекут за собой дополнительные затраты в виде суммы дополнительных амортизационных отчислений и затрат на электроэнергию.
Дополнительные амортизационные отчисления при норме амортизации 143% составят:
Дополнительные затраты на электроэнергию:
где - потребленная электроэнергия до и после мероприятия кВт;
- цена одного киловатта электроэнергии р.
Тогда общий экономический эффект составит:
Тогда окупаемость дополнительных капиталовложений рассчитаем по формуле:
где - дополнительные капиталовложения р.
Результаты расчетов экономической эффективности проекта представлены в таблице 6.13.
Таблица 6.13 - Технико-экономические показатели проекта
После совершенствования
Производственная программа чел.×ч
Численность ремонтных рабочих расчетная чел.
Стоимость основных фондов всего тыс.р.
- оборудование тыс.р.
Фонд заработной платы тыс.р.
Единый социальный налог тыс.р.
Дополнительные затраты всего тыс.р.
- амортизационные отчисления тыс. р.
Окончание таблицы 6.13 - Технико-экономические показатели проекта
- затраты на электроэнергию тыс. р.
Дополнительные капиталовложения тыс. р.
Экономический эффект
Срок окупаемости год.
Проведенные выше расчеты подтверждают целесообразность проведения данных мероприятий на агрегатном участке. Механизация работ приведет к повышению производительности и качества выполнения работ. Срок окупаемости дополнительных капитальных вложений 15 года.
В настоящей выпускной квалификационной работе были предложены мероприятия по совершенствованию организации работ на агрегатном участке МУП «Хабаровское пассажирское автотранспортное предприятие №1» г. Хабаровска.
В первой главе настоящей работы приведен технико-экономический анализ деятельности МУП «Хабаровское пассажирское автотранспортное предприятие №1» г. Хабаровска за последние пять лет.
Проведенное исследование показало что необходимо менять структуру предприятия осуществить механизацию работ налаживать связи с поставщиками внедрять новые формы оплаты труда. Предприятие нуждается в постоянном и планомерном обновлении автобусного парка а самое главное в четкой поставке запасных частей и горюче смазочных материалов.
Для продления срока службы автомобилей необходимо совершенствовать и обновлять производственно-техническую базу рационально внедрять новое технологическое оборудование повышать квалификацию и профессионализм рабочих.
Для решения вопроса о рациональном внедрении оборудования в данном проекте предлагается: повысить эффективность работ на агрегатном участке путем подбора и оптимальной расстановки технологического оборудования и совершенствования технологических процессов.
В технологической части был произведен расчёт количества рабочих постов штатных рабочих и инженерно технического персонала.
В конструкторской части спроектирован стенд для выпресовки подшипников крестовин карданных передач. Данное оборудование позволит снизить трудоемкость выполняемых работ увеличить общегодовой пробег и коэффициент технической готовности.
В разделе по охране труда проведен анализ условий труда опасных и вредных производственных факторов на агрегатном участке предприятия. Предложены мероприятия по снижению травматизма на рабочем месте. Произведен расчет искусственного освящения и вентиляции.
В экономической части произведена оценка эффективности предложенных решений путем определения срока окупаемости данного проекта что свидетельствует о целесообразности принятых решений.
СПИСОК ИСПОЛЬЗОВАННЫХ ИСТОЧНИКОВ
Основные показатели транспортной деятельности в России. 2008: Стат. сб. Росстат. - M. 2008. - 93 c.
Аксёнова З.И. Анализ производственно-финансовой деятельности автотранспортного предприятия: Издательство «Транспорт» 1972. – 240 с.
Савицкая Г.В. Анализ хозяйственной деятельности предприятия: Учебник.- 2-е изд. испр. И доп. – м.: ИНФРА – М 2003. – 400 с.
Сербиновский Б.Ю.; Напхоненко Н.В. Экономика автосервиса. Создание автосервисного участка на базе действующего предприятия: учеб. пособие – М.: ИКЦ «Март» 2006. - 432 с.
Анисимов А.П. Экономика планирование и анализ деятельности автотранспортных предприятий. - М.: «Транспорт» 1998. – 245 с.
Горев А.Э. и др. Организация автомобильных перевозок и безопасность движения: учеб. пособие для студ. высш. учеб. заведений. - М.: Издательский центр «Академия» 2006. - 256 с.
Положение о техническом обслуживании и ремонте подвижного состава автомобильного транспорта. Минавтотранс РСФСР - М.: Транспорт 1988г. - 78 с.
Семенов Н.В. Техническое обслуживание и ремонт автобусов. - М.: Транспорт 1979г. - 216 с.
Общесоюзные нормы технологического проектирования предприятий автомобильного транспорта. – М.: ОНТП-01-91 Росавтотранс 1991. – 103 с.
Напольский Г.М. Технологическое проектирование автотранспортных предприятий и станций технического обслуживания. – М.: Транспорт 1985. -231 с.
Афанасьев Л.Л. Гаражи и станции технического обслуживания автомобилей. – М.: Транспорт 1980.–216 с.
Шадричев В.А. Основы технологии автостроения и ремонта автомобилей. – Л.: Машиностроение 1976. – 560с.
Крамаренко Г.В. Техническая эксплуатация автомобилей. - М: Транспорт 1983. - 488 с.
Власов В.М. Управление технологическими процессами технического обслуживания и ремонта автомобилей. – М.: МАДИ 1982. – 78 с.
Кузнецов Е.С. Болдин А.П. и др. Техническая эксплуатация автомобилей.– М.: Наука 2001. – 535 с.
Кузьмин А.В и др. Расчеты деталей машин: справ. пособие А.В. Кузьмин И.М. Чернин Б.С. Козинцов. – 3-е изд. перераб. и оп. – Мн.: Высш. шк. 1986. – 400 с.
Курсовое проектирование деталей машин: Учеб. пособие для техникумовС.А. Чернавский Г.М. Ицкович К.Н. Боков и др. – М.: Машиностроение 1979. – 351 с.
Анурьев В.И. Справочник конструктора-машиностроителя. В 3-х т. Т.1 Т.2 Т.3. – 5-е изд. перераб. и доп. – М.: Машиностроение 1980. – 559 с.
Оборудование для ремонта автомобилей. Под ред. Шахнеса М.М. Изд-во «Транспорт» 1971 г. стр. 1- 427
Власов Ю.А. Основы проектирования и эксплуатации технологического оборудования. Учебное пособие. Ч2 Власов Ю.А. Тищенко Н.Т. - Томск: Изд-во Томск. архит. строит. Ун-та. 2002- - 147 с.
Митрохин Н.Н. Кузьмика Е.В. Оборудование и приспособления: конструкция расчет и оценка стоимости: Учебное пособиеПод ред. НН. Митрохина МАДИ (ГТУ) – М.: 2003 – 104 с.
Чумаченко Ю. Т. Эксплуатация автомобилей и охрана труда на автотранспорте : учеб. для проф. лицеев училищ колледжей учеб.-курсовых комбинатов Чумаченко Юрий Тимофеевич Чумаченко Г.В. Ефимова А.В. - Библиогр.: с. 407. - Ростов нД: Феникс 2002 .- 416с.
Трудовой кодекс Российской Федерации от 30 декабря 2001 г. N 197-ФЗ (ТК РФ) [Электронный ресурс] - Доступ из справ.-правовой системы «Консультант Плюс».
Шариков Л.П. Охрана труда в малом бизнесе. Металлообработка: практ. пособие Шариков Леонид Прокопьевич. - М.: Альфа-Пресс 2009 .- 248с.
Приказ Министерства здравоохранения и социального развития российской федерации от 31 августа 2007 г. N 569 «Об утверждении порядка проведения аттестации рабочих мест по условиям труда») [Электронный ресурс] - Доступ из справ.-правовой системы «Консультант Плюс».
СанПиН 2.2.4.548-96 Гигиенические требования к микроклимату производственных помещений. Санитарные правила и нормы. [Электронный ресурс] - Доступ из справ.-правовой системы «Консультант Плюс».
ГОСТ 12.1.005-88 ССБТ. Общие санитарно-гигиенические требования к воздуху рабочей зоны. [Электронный ресурс] - Доступ из справ.-правовой системы «Консультант Плюс».
ГН 2.2.5.686-98 Предельно допустимая концентрация (ПДК) вредных веществ в воздухе рабочей зоны. Гигиенические нормативы. [Электронный ресурс] - Доступ из справ.-правовой системы «Консультант Плюс».
ГОСТ 12.1.003-83 ССБТ. Шум. Общие требования безопасности. [Электронный ресурс] - Доступ из справ.-правовой системы «Консультант Плюс».
СН 2.2.42.1.8.562-96 Шум на рабочих местах в помещениях жилых общественных зданий и на территории жилой застройки. [Электронный ресурс] - Доступ из справ.-правовой системы «Консультант Плюс».
СН 2.2.42.1.8.566-96 Санитарные нормы. Производственная вибрация вибрация в помещениях жилых и общественных зданий. [Электронный ресурс] - Доступ из справ.-правовой системы «Консультант Плюс».
ГОСТ 12.1.012-90 Вибрационная безопасность. Общие требования. – М.: Изд. стандартов 1990. – 36с.
СНиП 23-05-95 "Естественное и искусственное освещение" [Электронный ресурс] - Доступ из специализиров. справочной системы «Техэксперт».
Правила устройства электроустановок Минэнерго СССР.—6-е изд. перераб. и доп.—М.: Энергоатомиздат 1987.—648 с: ил.
ГОСТ 12.1.038-82. Электробезопасность. Предельно допустимые уровни напряжений прикосновения и токов. – М.: Изд. стандартов 1981. - 28с.
ГОСТ 12.1.019-79 ССБТ Электробезопасность. Общие требования и номенклатура видов защиты. - М.: Издательство стандартов 2000. - 7с.
Фролов А.В. Бакаева Т.Н. Безопасность жизнедеятельности. Охрана труда. – Ростов нД.: Феникс 2005. – 736с.
Отопление вентиляция и кондиционирование воздуха: Жилые здания со встроенно-пристроенными помещениями общественного назначения и стоянками автомобилей. Коттеджи: Справ. пособие; [Авт.-сост.]: В.В. Порецкий И.С. Березович Г.И. Стомахина. - Библиогр.: с. 265-267. - М.: Пантори 2003 .- 308c.
Пособие по расчету и проектированию естественного искусственного и совмещенного освещения. – М.: Стройиздат 1985.-384с.
ГОСТ 12.1.033-81 ССВТ. Пожарная безопасность. Термины и определения».[Электронный ресурс] - Доступ из специализиров. справочной системы «Техэксперт».
СНиП 31–03-2001 «Определение категорий помещений и пожарной безопасности». [Электронный ресурс] - Доступ из специализиров. справочной системы «Техэксперт».
СНиП 21-01-97 Пожарная безопасность зданий и сооружений. - СПб.: Изд. ДЕАН 2002. - 48с.
Методические указания кафедры ЭАТ «0ценка коммерческой эффективности организации автосервисного участка» сост. Бакута Н.Н. – Хабаровск: Изд. Тихоокеанского гос. ун-та 2008. – 48с.
Бакута Н.Н. Денисов Г.Г. Володькин П.П. Нормативные материалы на автомобильном транспорте: Учебное пособие. - Хабаровск; Изд-во ХГТУ 2003. - 147с.
Карев В.Ф. Экономические расчеты в дипломном проектировании. Методические указания к дипломному проектированию. - ХГТУ 2002. - 24с.
Рекомендуемые чертежи
- 25.01.2023
- 25.10.2022
- 25.01.2023