Разработка техпроцесса изготовления крана



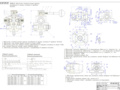

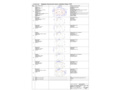
- Добавлен: 24.01.2023
- Размер: 1 MB
- Закачек: 0
Описание
Состав проекта
![]() |
![]() ![]() ![]() ![]() |
![]() |
![]() |
![]() ![]() ![]() ![]() |
![]() ![]() ![]() |
![]() |
![]() ![]() ![]() ![]() |
Дополнительная информация
Лист2.dwg

Название и содержание операции
Вертикально-сверлильная 1.Установить деталь. 2.Сверлить 4 отверстия 1 ø4
3.Снять деталь уложить в тару. 4.Контроль ОТК.
Вертикально-сверлильный станок 2М112
кондуктор МТ9644-471
глубиномер 17-1 МТ8157-4507.
Токарная с ЧПУ 1.Установить деталь в патрон. 2.Центровать и сверлить отверстие 6 ø10H14+0
3.Подрезать торец 7 в размер 12±0
4.Поворот патрона 5.Подрезать торец 3 в размер 50±0
6.Расточить отверстие 1 в размер ø31
с подрезкой поверхности 4. 7.Расточить фаску 14 в размер 2
х45°. 8.Нарезать резьбу 1 М33х1
-7Н на глубину 15+2. 9.Сверлить отверстие 2 ø18H9+0
3. 10.Расточить фаску 5 в размер 1х45°. 11.Поворот патрона. 12.Подрезать торец 9 в размер 29±0
13.Точить поверхность 10 в размер 3Н14+0
с обточкой поверхности 12 в размер ø32h12-0
14.Расточить отверстие 13 ø26H12+0
15.Поворот патрона. 16.Повторить переходы 5-11 для второй стороны корпуса. 17.Поворот патрона в исходное положение. 18.Снять деталь уложить в тару. 19.Контроль ОТК.
Токарно-револьверный станок с ЧПУ 1В340 Ф30
двухкулачковый гидравлический патрон МТ 9661-434
кулачки МТ 9664-440 резец 25х16х125 МТ2100-4041
2301-0030 ГОСТ 10903-77
резец 25х16х140 2103-0008 ГОСТ 18879-73
резец ø25х110 МТ2145-4007
резец ВК8 ø25х130 МТ2662-4005
сверло ø17 2301-0057 ГОСТ 10903-77
резец ВК8 ø25х110 МТ2145-4007
штангенциркуль ШЦI-125-0.1 ГОСТ 166-89
пробка резьбовая М33х1
калибр резьбовой М33х1
-7Нх15+2 МТ8229-4030-13
Вертикально-сверлильная 1.Установить деталь. 2.Зенкеровать 4 фаски 1 в размер 1х45° 3.Снять деталь
уложить в тару. 4.Контроль ОТК.
подставка МТ9648-713
штангенциркуль ШЦI-125-0.1 ГОСТ 166-89.
Резьбонарезная 1.Установить деталь. 2.Нарезать резьбу М6-7Н в 4 отверстиях 1 на глубину 12±0
Резьбонарезной и резьбофрезерный станок полуавтомат 2056
метчик М6-7Н 2620-1155 ГОСТ 3266-81
пробка резьбовая 8221-3030
калибр резьбовой М6-7Нх12min МТ8229-4026-09.
Вертикально-сверлильная 1.Установить деталь. 2.Сверлить 4 отверстия 1 ø6
кондуктор МТ9644-472
2300-0309 ГОСТ 10902-77
Вертикально-сверлильная 1.Установить деталь. 2.Зенкеровать 4 фаски 1 в размер 1
х45°. 3.Снять деталь
подставка МТ9648-714
Резьбонарезная 1.Установить деталь. 2.Нарезать резьбу М8-7Н в 4 отверстиях 1. 3.Снять деталь
метчик М8-7Н 2620-2529 ГОСТ 3266-81
пробка резьбовая М8-7Н 8221-3036.
Вертикально-сверлильная 1.Установить деталь. 2.Сверлить 2 отверстия 1 ø10H14+0
Вертикально-сверлильный станок 2Н118
Кондуктор МТ9644-472
втулка 6100-0141 ГОСТ 13598-85
Вертикально-сверлильная 1.Установить деталь. 2.Зенкеровать 3 отверстия ø18H14+0
по поверхностям 1 и 2 одновременно. 3.Снять деталь
Вертикально-сверлильный станок 2Н125
зенкер ø13xø18 МТ2331-4047
Зачистка 1.Зачистить заусенцы после механической обработки
Верстак Напильник 2820-0014 ГОСТ 1465-80
надфиль 2826-0034 ГОСТ 1513-77.
Промывка 1.Промыть детали согласно инструкции 25100.00020
Лист1.dwg

Обеспечить линейный размер пружины находящейся в сжатом состоянии в пределах 15±0
мм. 2. Обеспечить силу сжатия пружин клапана не менее 0
МПа 3. Обеспечить усилие при котором клапаны удерживаются в закрытом положении не более 9 МПа (сила
которой взрослый человек может надавить рукой). 4. обеспечить расстояние между кулачком и направляющей в пределах 0
Задача: Обеспечить линейный размер пружины находящейся в сжатом состоянии в пределах 15±0
Метод полной взаимозаменяемости:
Обеспечить соосность отверстий Б и В относительно общей оси А с допуском TБВ = ±0
2. Обеспечить плоскостность поверхности Г с допуском ТГ = -0
Выпуклость не допускается. 3. Обеспечить перпендикулярность оси Д относительно оси А с допуском ТД = ±0
4. Обеспечить твёрдость > 70HB. 5. Неуказанные литейные радиусы 3мм. 6. Обеспечить герметичность стенок при испытании сжатым воздухом под давлением 06 МПа в течении 30 с.
Метод неполной взаимозаменяемости:
Выпуклость не допускается
Обеспечить герметичность стенок при испытании сжатым воздухом под давлением 0
МПа в течении 30 с. 2. Неуказанные литейные радиусы 3мм.
уклоны до 3°. 3. Обеспечить плотное литьё - раковины и рыхлости не допускаются. 4. Старить.
записка.doc
Кафедра «Технология машиностроения»
«Разработать технологический процесс изготовления крана вспомогательного тормоза локомотива 172»
Определение типа производства и выбор вида его организации.
Разработка технологического процесса сборки узла.
1.Служебное назначение узла и принцип его работы.
2.Анализ чертежа технических требований на узел и технологичности его конструкции.
3.Выбор метода достижения требуемой точности узла.
4.Контроль точности сборки узла или его испытание.
5.Схема сборки узла.
6.Выбор вида и формы организации процесса сборки узла.
7.Выбор сборочного оборудования и технологической оснастки.
8.Нормирование сборочных операций.
9.Технологическая карта сборки узла.
10.Расчет числа рабочих мест и рабочих-сборщиков.
11.Построение циклограммы сборки.
12.Планировка сборочного места.
Разработка технологического процесса изготовления детали.
1.Служебное назначение детали.
2. Анализ чертежа технических требований на деталь и её технологичности.
3.Выбор вида заготовки и назначение припусков на обработку.
4.Выбор технологических баз и обоснование последовательности обработки поверхностей заготовки.
5.Выбор методов обработки поверхностей заготовки и определение количества переходов. Выбор режущего инструмента.
6.Разработка маршрутного технологического процесса. Выбор технологического оборудования и оснастки.
7.Определение припусков межпереходных размеров и их допусков. Определение размеров исходной заготовки.
8.Назначение режимов резания.
9.Нормирование технологической операции.
10.Контроль точности изготовленной детали.
11.Оформление технологической документации:
-маршрутной карты технологического процесса изготовления детали;
-операционной карты на одну операцию технологического процесса изготовления детали;
-технологической карты сборки.
Список использованной литературы.
Цель курсового проекта - разработать технологический процесс изготовления крана вспомогательного тормоза локомотива 172.
Задачи курсового проекта:
- определить тип производства и выбрать вид его организации
- разработать технологический процесс сборки крана вспомогательного тормоза локомотива 172
- разработать технологический процесс изготовления корпуса 172.001
Основной задачей курсового проекта является приобретение навыков применения теоретических знаний полученных в результате изучения различных дисциплин при разработке технологического процесса изготовления узла и детали используя необходимую справочную техническую литературу и руководящие материалы.
Необходимо решить задачу проектирования экономически эффективного технологического процесса изготовления сборочной единицы с использованием достижений науки техники и передового производственного опыта.
Определение типа производства.
Исходные данные для расчёта:
Общий выпуск по неизменным чертежам – 1000 штук;
Производственная программа – 500 штук в год.
Деталь будет выпускаться:
Такт выпуска при одноимённом режиме работы:
F = 2052 часов – годовой фонд времени
n – коэффициент учитывающий простои оборудования связанные с наладкой и обслуживанием;
N – количество деталей в партии:
Дневной выпуск изделий:
Число изделий в месяц:
Существует три типа производства: единичное серийное и массовое.
Под единичным производством машин их деталей или заготовок понимают изготовление их характеризуемое малым объёмом выпуска. При этом считают что выпуск таких машин деталей или заготовок не повторится по неизменяемым чертежам. Продукцией единичного производства являются машины не имеющие широкого применения (опытные образцы машин тяжёлые прессы крупные гидротурбины уникальные металлорежущие станки и т.п.).
Под серийным производством машин их деталей или заготовок понимают их периодическое изготовление повторяющимися партиями по неизменяемым чертежам в течение продолжительного промежутка календарного времени. Производство осуществляется партиями при этом возможна партия из одного изделия. В зависимости от объёма выпуска этот тип производства делят на мелко- средне- и крупносерийное. Примерами продукции серийного производства могут служить металлорежущие станки компрессоры судовые дизели и т.п. выпускаемые периодически повторяющимися партиями.
Под массовым производством машин деталей или заготовок понимается их непрерывное изготовление в больших объёмах по неизменяемым чертежам продолжительное время в течение которого на большинстве рабочих мест выполняется одна и та же операция. Для массового производства характерна узкая номенклатура и большой объём выпуска изделий. Продукцией массового производства являются трактора автомобили электродвигатели холодильники телевизоры и пр.
Используя исходные данные выбираем тип производства. Так как данное изделие (Кран вспомогательного тормоза локомотива 172) выпускается партиями не продолжительное время по неизменяемым чертежам учитывая массу и годовой выпуск по таблице [1] выберем тип производства мелкосерийный.
1Служебное назначение узла и принцип его работы.
Служебное назначение:
Кран вспомогательного тормоза локомотива 172 (далее кран) предназначен для ручного управления тормозами локомотива при рабочем давлении 06±01 МПа.
Ручка крана имеет три фиксированных положения: отпуск (О) перекрыша (П) торможение (Т).
В положении «Т» сжатый воздух из пневмомагистрали (ПМ) через входное отверстие G” в кронштейне поз.2 поступает под открытый тормозной клапан поз.24 и далее через центральное отверстие в корпусе поз.1 кронштейн поз.2 к тормозному цилиндру (ТЦ). Величина давления в ТЦ фиксируется по манометру и зависит от времени удержания рукоятки в этом положении.
По достижении необходимого давления в ТЦ ручка крана переводится в положение «П». В этом положении клапаны поз.24 (тормозной и отпускной) закрыты. Давление в ТЦ остаётся постоянным.
Для полного или частичного отпуска тормозов ручка устанавливается в положение «О» затем открывается отпускной клапан сообщающий ТЦ с АТ. Величина ступени отпуска зависит от времени удержания рукоятки в этом положении. Для прекращения отпуска ручку необходимо перевести в положение «П».
2Анализ чертежа технических требований на узел и технологичности его конструкции.
Кран состоит из корпуса поз.1 с двумя клапанами поз.24 отпускным и тормозным. Для управления клапанами поз.24 в корпусе устанавливается кулачок поз.3 с ручкой поз.8 которая жёстко соединена с кулачком поз.3 и имеет 3 фиксированных положения. Клапаны поз.24 удерживаются в закрытом положении пружинами поз.4 и поз.5. Корпус поз.1 крепится на кронштейне поз.2 в котором имеются резьбовые отверстия G” для подвода сжатого воздуха. В закрытом положении клапаны поз.24 удерживаются пружинами поз.45 которые останавливаются в заглушках поз.26. Одно резьбовое отверстие в кронштейне поз.2 закрывается заглушкой поз.18 с кольцом поз.15. крепление крана осуществляется посредством шпилек поз.19 и гаек поз.17.
Технические требования
а) обеспечить линейный размер пружины находящейся в сжатом состоянии в пределах 15±05мм.
б) обеспечить силу сжатия пружин клапана не менее 06МПа
в) обеспечить усилие при котором клапаны удерживаются в закрытом положении не более 9 МПа (сила которой взрослый человек может надавить рукой).
г) обеспечить расстояние между кулачком и направляющей в пределах 05±02мм.
Несоблюдение приведённых выше требований повлечёт за собой невозможность выполнения краном своего служебного назначения например: при несоблюдении технического требования - обеспечения усилия сжатия пружин возможен случай когда из-за малой его величины произойдёт самопроизвольное открытие отпускного клапана и в последствии невозможность набора необходимого давления в тормозном цилиндре.
Технологичность конструкции крана 172.000
Анализ чертежа корпуса 172.001 показал что он имеет симметричную геометрию в продольном сечении. Это сделано для того чтобы сократить время сборки узла используя одинаковые детали как в левой так и в правой части.
Диаметры расточки заглушки 172.005 и ступенчатого торца гнезда 172.011 рассчитаны и подобраны таким образом чтобы в состав узла - корпус 172.010 входили уже имеющиеся на производстве детали от ранее изготовленных приборов такие как пружины 150.203 и 483.031.
При закреплении деталей и узлов крана 172.000 используются стандартные изделия такие как винт М6х10 ГОСТ 1476-93 винт М6х12 ГОСТ 17475-80 винт ВМ3х6 ГОСТ 17473-80 гайка М8 ГОСТ 5915-70 гайка М12 ГОСТ 5915-70 шпилька М12х32 СТП 10-215-82.
Диаграмма зависимостей линейных размеров пружин от силы их сжатия
Из диаграммы видно что общее усилие создаваемое сжатыми пружинами (138 кгс) намного выше требуемого (6 кгс). В целях экономии целесообразней оставить только одну пружину – 483.031. Т.к. для её сжатия до размера 15±05мм. необходимо усилие 9±04кгс. что удовлетворяет требованиям предъявляемым к узлу.
В результате проведенного анализа технических требований на узел было выявлено одно из наиболее важных требований а именно: обеспечить линейный размер пружины находящейся в сжатом состоянии равный 15мм. с допуском ±05мм.
Для выполнения этого требования необходимо выявить все размеры деталей (в номиналах и допусках) влияющих на выполнение этого требования. Для этого необходимо выявить замыкающее звено и метод достижения точности РЦ.
Обеспечение точности создаваемого узла сводится к достижению требуемой точности замыкающих звеньев размерных цепей заложенных в его конструкцию и размерных цепей возникающих в процессе изготовления крана. Задачу обеспечения требуемой точности замыкающего звена решим одним из нижеследующих методов: полной и неполной взаимозаменяемости. Определим наиболее экономичный метод с учётом с предъявляемыми требованиями.
Размерная цепь А состоит из:
АΔ - замыкающее звено – длина пружины находящейся в сжатом состоянии при силе сжатия 11 МПа
A1 - размер между левым 22мм. и правым 13мм. торцом клапана 172.011
A2 - Высота седла 15мм. седла 172.009
A3 - Ширина бурта 22мм. седла 172.009
A4 - Глубина отверстия М33 в корпусе 172.001
A5 - Расстояние от торца М33 до торца 40мм. заглушки 172.005
A6 - Глубина отверстия 13 в заглушке 172.005
Размерная цепь А определяющая зазор показана в графической части лист 1.
а) Метод полной взаимозаменяемости.
Сущность метода заключается в том что требуемая точность замыкающего звена размерной цепи достигается во всех случаях её реализации путём включения в неё составляющих звеньев без выбора подбора или изменения их значений. Сборка изделий при использовании этого метода сводится к механическому соединению взаимозаменяемых деталей. При этом у 100% собираемых объектов автоматически обеспечивается требуемая точность замыкающих звеньев размерных цепей.
Определение номиналов полей допусков верхнего и нижнего предельных отклонений координат середины поля допуска размерной цепи А проходит по следующему алгоритму действий:
Уравнение номиналов.
n – число увеличивающих звеньев;
m – число уменьшающих звеньев.
из условия задачи следует что поле допуска замыкающего звена
а координата середины поля допуска замыкающего звена
Имея дело с плоской линейной размерной цепью и решая задачу методом полной взаимозаменяемости при назначении полей допусков на соответствующие звенья необходимо соблюдения условия:
Уравнения координат середин полей допусков.
Координату середины поля допуска шестого звена находим из уравнения:
Правильность назначения допусков проверим определив предельные отклонения замыкающего звена:
Сопоставление с условиями задачи показывает что допуски установлены правильно.
б) Метод неполной взаимозаменяемости.
Сущность метода заключается в том что требуемая точность замыкающего звена размерной цепи достигается с некоторым заранее обусловленным риском путём включения в неё составляющих звеньев без выбора подбора или изменение их значений.
Зададим значение коэффициента риска tАΔ считая что в данном случае Р=1% экономически оправдан. Такому риску tАΔ =257.
Полагая что условия изготовления деталей таковы что распределение отклонений составляющих звеньев будет близким к закону Гаусса принимаем
Найдём средний допуск на звенья при обоих методах:
Метод полной взаимозаменяемости
Метод неполной взаимозаменяемости
Для достижения требуемой точности замыкающего звена в одной размерной цепи выбираем метод не полной взаимозаменяемости. Данный метод позволяет расширить допуски на составляющие звенья что ведёт к понижению себестоимости и работоспособности по отношению к методам пригонки и регулирования.
Метод неполной взаимозаменяемости не гарантирует получения 100% изделий с отклонениями замыкающего звена в пределах заданного допуска с коэффициентом риска равным 1%. Однако дополнительные затраты труда и средств на исправление небольшого числа изделий размеры которых вышли за пределы допуска в большинстве случаев малы по сравнению с экономией труда и средств получаемых при изготовлении изделия размеры которого имеют более широкие допуски.
Экономический эффект получаемый от использования метода неполной взаимозаменяемости вместо метода полной взаимозаменяемости возрастает по мере повышения требований к точности замыкающего звена и увеличении числа составляющих звеньев в размерной цепи.
возможность выполнения технологических процессов изготовления деталей и особенно сборки машин рабочими невысокой квалификации.
4Контроль точности сборки узла или его испытание.
Контроль крана выполнить внешним осмотром с применением линейки штангенциркуля и весов. Выполнить внешний осмотр поверхностей трения сопрягаемых деталей после контрольной разборки. После контроля кран собрать и провести испытания на соответствие требованиям ТУ 24.05.10.126-97 на испытательном стенде. При разборке и сборке крана использовать средства измерения ОТК. Измерение величин давления сжатого воздуха провести по манометрам. При испытании рукоятка крана ставится в тормозное положение «Т». Время наполнения резервуара измеряют секундомером. Для испытания отпуска тормозов рукоятка крана ставится в отпускное положение. Время снижения давления в резервуаре измеряется секундомером. Затем рукоятка крана ставится в положение «П» последовательно после испытаний положений «Т» и «О». При этом не должно быть завышения давления после испытания в положении «Т» и снижения давления после испытания в положении «О». Измерения провести по истечении 30 секунд после перевода ручки крана в течение 30 секунд. Испытание провести в резервуаре V= 10л. 06 МПа обмыливанием мест соединений. Испытания крана при предельных значениях температур +45±3°С и -50±3 провести в климатической камере. После достижения в климатической камере предельного значения температуры кран выдержать в ней не менее чем в течении 2х часов. Подтверждение показателей надёжности допускается проводить сбором статистических данных по результатам эксплуатационных испытаний.
Схема пневматическая принципиальная стенда
-кран 1-2 УЗ ОСТ 24.290.16-86;
-резервуар V = 20 л.;
-резервуар V = 10 л.;
-манометр Кл.1 цд 01 кгссм2 предел 10 кгссм2 ГОСТ 2405-88;
-труба 15 ГОСТ 3262-75.
После установки крана на подвижной состав повторно проводят испытания на герметичность мест соединений.
6Выбор вида и формы организации процесса сборки узла.
На основании программы выпуска и габаритных размеров крана принимаем стационарную не поточную сборку с одним рабочим местом.
7Выбор сборочного оборудования и технологической оснастки.
Сборка крана 172 производится на верстаке. Перед сборкой необходимо продуть детали от остатков технической пыли. Для закрепления корпуса на верстаке используют тиски 7827-0325 ГОСТ 4045-75. Для сбора резьбовых соединений применяется пневмогайковёрт ИП 3112-У11 с наконечниками МТ 9694-686 и МТ 9694-685 отвёртки 7810-0941 3В ГОСТ 17199-88 и 7810-0964 3В ГОСТ 17199-88.
9Технологическая карта сборки узла.
Технологическая карта сборки узла приведена в приложении 3.
10Расчет числа рабочих мест и рабочих-сборщиков.
Сборка комплектов (172.020 Корпус 172.00 Клапан 172.040 Заглушка) - 12 мин.
Сборка подузлов (172.010 Корпус 172.070 Кронштейн 172.080 Кулачек 172.090 Ручка) - 345мин.
Сборка узла (Кран 172.000) - 40 мин.
при отсутствии совмещенных во времени операций при совмещении времени транспортирования кранов с оперативным временем и при стационарной сборке:
выбираем один рабочий-сборщик и одно рабочее место.
11Построение циклограммы сборки.
Ввиду того что работает один рабочий-сборщик в построении
циклограммы и планировке рабочих мест нет необходимости.
1Служебное назначение детали.
Корпус 172.001 предназначен для базирования деталей входящих в состав корпуса 172.010 и кулачка 172.080 а также для обеспечения герметичности всего узла.
Основными показателями качества корпуса являются:
соосность отверстий под сёдла относительно общей оси с установленным допуском плоскостность поверхности основания с установленным допуском перпендикулярность общей оси отверстий под сёдла относительно оси отверстия под кулачек с установленным допуском герметичность стенок при испытании сжатым воздухом под давлением 06 МПа в течении 30с..
2Анализ чертежа технических требований на деталь и её технологичности.
Корпус 172.001 представляет из себя простую корпусную деталь симметричную в поперечном сечении среднего класса точности небольших габаритов с двумя отверстиями в торцах для крепления клапанов одним сверху для крепления кулачка и тремя в основании для запрессовки ниппелей. Корпус изготавливается из алюминия марки АК7ч ГОСТ 1583-93 с твёрдостью > 70HB.
Из вышесказанного следует что при изготовлении корпуса будут
использоваться операции токарная вертикально-сверлильная резьбонарезная зачистка химическое окисление с последующим контролем исполненных размеров.
3Выбор вида заготовки и назначение припусков на обработку.
В производстве корпусные детали изготавливают в основном литьём но ввиду небольшого размера корпуса и непродолжительное время изготовления по неизменяемым чертежам можно также изготовить корпус штамповкой на ГКМ.
Расчеты получения заготовок ведут по формуле:
Объем детали Vдет = 67см3
Объем заготовки литьё Vзаг = 107см3
Объем заготовки из штамповки ГКМ Vзаг = 194см3
Ким1 = 67 107 = 035
Выбираем вариант 2 т.к. он экономически целесообразен.
Исходя из объёма выпуска и массы корпуса выбираем литьё по выплавляемым моделям.
4Выбор технологических баз и обоснование последовательности обработки поверхностей заготовки.
Для обработки корпусов и получения минимальных погрешностей нужно создать технологические базы для установки в токарных станках. Исходя из особенностей токарного станка и точного размещения заготовки на нем необходимо обработать торцы заготовки и выполнить центровочные отверстия. Выполнять будем на Токарно-револьверном станке с ЧПУ 1В340 Ф30 в двухкулачковом гидравлическом патроне МТ 9661-434 с кулачками МТ 9664-440. Так как кулачки сконструированы специально для закрепления корпуса 172.001 для обеспечения высокой точности обработки и установки заготовки в станке то так же являются и приспособлением.
Рассмотрим два варианта базирования:
a)базирование в двух сходящихся призмах и опорных пальцах.
Из чертежа видно что при установке технологическая база не совпадает с осью корпуса и призмы появляется погрешность базирования заготовки.
А2=Б=Б1+Б2+ Б3=тс(005)+ пр+заг=05+08+02=15
б)базирование в двухкулачковом гидравлическом патроне
МТ 9661-434 с кулачками МТ 9664-440.
Здесь за счет специальных кулачков обеспечивается более точное базирование корпуса.
А2=В=тс(005)+заг=05+02=07
Из вычислений можно оценить распределения припуска на поверхности отверстия под седло на 005 операции.
Распределение найдем из формулы:
вариант: А2=А1+А22=тс(005)+А22=05+15=2 мм
вариант: А1=А1+А12=тс(005)+А12=05+07=12 мм
Из расчета видим что второй вариант предпочтительнее поскольку имеет минимальный припуск на обработку.
5Выбор методов обработки поверхностей заготовки и определение количества переходов. Выбор режущего инструмента.
Последовательность обработки заготовки:
Вертикально-сверлильная
В связи с нашим производством выберем следующие станки:
Для выполнения токарной обработки выберем токарно-револьверный станок с ЧПУ 1В340 Ф30.
Для сверления на разных операциях вертикально-сверлильный станок 2М112 вертикально-сверлильный станок 2Н118 вертикально-сверлильный станок 2Н125.
Для резьбонарезной операции резьбофрезерный станок полуавтомат 2056.
6Разработка маршрутного технологического процесса. Выбор технологического оборудования и оснастки.
Разработка маршрутного технологического процесса и выбор технологического оборудования и оснастки приведены в приложении 3.
7Определение припусков межпереходных размеров и их допусков. Определение размеров исходной заготовки.
Рассчитаем припуски на поверхности нижнего торца корпуса.
Рассчитаем минимальный припуск:
Zmin = ((Rz + h)i-1 + (2Σi-1 + 2i))12
Где Rz – шероховатость поверхности возникающая на предшествующем переходе
h – глубина дефектного слоя
Σi-1 – суммарные отклонения расположения и формы поверхности
– погрешность установки заготовки на выполняемом переходе
Предварительное точение:
Zminпредв. = 2(700 +700+(200+250)2 + 1002)12 = 1628мкм
Окончательное точение:
Zminокон. = 2(500 +500+(100+150)2 + 502)12 = 1243мкм
Расчет общего минимального припуска:
Zminобщ = 1628 + 1243 = 2871мкм
Расчет максимального припуска для обработки поверхности
Zmax = Zmin + Tдет + Tзаг
где Тзаг – допуск на заготовку
Тдет – допуск на деталь
Zmax = 2871 + 50 + 400 = 3321 мкм
8Назначение режимов резания.
Расчет режима резания проведем на первую операцию первого перехода
Операция 005 токарная с ЧПУ.
Переход 1: Подрезать торец заготовки в размер 12±05
Глубина резания : t = 5 мм
Скорость резания V = Cv * Kv Tm * tx * Sy
где Cv – поправочный коэффициент
Т – стойкость инструмента
Kv – коэффициент учитывающий условия обработки
V = 332 * 07 18002 * 505*0304 = 102 ммин
Частота вращения шпинделя:
np = 1000 * V * Dфр = 1000 * 102 314 * 70 = 340 обмин
по паспорту станка получаем np = 350 обмин
Действительная скорость резания:
nд = * Dфр * np 1000 = 314 * 70 * 800 1000 = 106 ммин
9Нормирование технологической операции.
Машинное время на точение торца
Т0 = (L + l1 + l2) * i Cz * z * nд
где L – длина обработки
l1 – величина врезания
Т0 = (55 + 60 + 60) * 2 02 * 6 * 175 = 17мин
Определим оперативное время операции:
Топ = 17 + 21 = 38 мин
Штучное время на операцию:
Тшт = Топ * ( 1 + (Ко + Кп) 100)
Где Ко – доля времени на обслуживание рабочего времени 2 – 6%
Кп – доля времени на отдых и личные надобности 4 – 8%
Тшт = 38 * (1 + (4 + 5) 100) = 038мин
10Контроль точности изготовленной детали.
контроль размера торца при помощи штангенциркуля ШЦI-125-0.1 ГОСТ 166-89
Точность изготовления корпуса проверяют в определенной последовательности сначала определяют правильность формы поверхности затем их геометрические размеры и потом уж их положения.
Такая последовательность необходима для того чтобы можно было путем исключения погрешностей измерять с наибольшей точностью тот параметр который необходимо проверить.
Измерительными базами при проверке корпусов обычно являются поверхности его основания которые будучи его основными базами определяют положение всех остальных.
При контроле устанавливаем корпус основанием на контрольную плиту с упором в один торец.
Правильность геометрической формы проверяем в нескольких сечениях перпендикулярных к оси корпуса овальность и конусообразность отверстий а также других линейных размеров проверяем с помощью следующих измерительных инструментов и приспособлений:
штангенциркуль ШЦI-125-0.1 ГОСТ 166-89
пробка 10Н14+036 МТ8133-4106-03
пробка резьбовая М33х15-7Н 8221-3120
пробка 18Н9+0043 МТ8133-4161-05
пробка 26Н12+021 МТ8133-4170-05
пробка 495+026 МТ8133-4016
пробка 67+026 МТ8133-4017
пробка 12.5H12+018 МТ8133-4107 01
пробка 18Н14+043 МТ8133-4164
пробка резьбовая 8221-3030
пробка резьбовая М8-7Н 8221-3036
калибр 50±015 МТ8368-4078
калибр резьбовой М33х15-7Нх15+2 МТ8229-4030-13
калибр резьбовой М6-7Нх12min МТ8229-4026-09
калибр 25±02 МТ8368-4079
скоба 32h12-025 МТ8119-4055-05
высотомер 3Н14+025 МТ8151-4385-01
глубиномер 39Н14+062 МТ8151-4671
глубиномер 17-1 МТ8157-4507
глубиномер 25Н14+025 МТ8151-4671-02
глубиномер 7Н14+036 МТ8151-4563-10
втулка 6100-0141 ГОСТ 13598-85.
11Оформление технологической документации
маршрутной карты технологического процесса изготовления детали операционной карты на одну операцию технологического процесса изготовления детали технологической карты сборки приведены в приложении.
Справочник технолога-машиностроителя 1985 А.Г.Косилова Р.К.Мещеряков Тома № 1.
Справочник технолога-машиностроителя 1985 А.Г.Косилова Р.К.Мещеряков Тома № 2.
Технология машиностроения (специальная часть):
Учебник для машиностроительных специальностей вузов А.А.Гусев Е.Р.Ковальчук И.М.Колесов и др. – М.: Машиностроение1986. – 480 с.
Основы технологии машиностроения:
Учебник для машиностроительных вузовИ.М.Колесов – М.: Машиностроение 1997. – 592 с.
Методическое руководство по курсовому проектированиюН.Г.Латышев – М.: Мосстанкин 1982. – 52 с.
Взаимозаменяемость в машиностроении и приборостроенииА.И.Якушев – Москва – 1970.
Руководящие материалы по пневмооборудованию станков. Воздухораспределительная и контрольно-регулирующая аппаратура. – Москва – 1961.
Технологические процессы и операции в курсовых и дипломных проектах: Метод. указ.Сост. В.В.Плешаков Т.В.Никифоров В.К.Старков. – М.: МГТУ ”Станкин” 1999. – 43с.
Курс лекций по предмету Технология машиностроения.
Лист3.dwg

Обоснование выбора варианта базирования на операции 005
й Вариант: базирование в двухкулачковом гидравлическом патроне МТ 9661-434
с кулачками МТ 9664-440.
й Вариант: базирование в двух сходящихся призмах и опорных пальцах.
Токарная с ЧПУ - 0838
Токарно-револьверный станок с ЧПУ 1В340 Ф30
Обозначение инструмента
2301-0030 ГОСТ 10903-77
Определение распределения припуска
технологическая база
резец 25х16х140 2103-0008 ГОСТ 18879-73
резец ВК8 ø25х110 МТ2145-4007
резец ВК8 ø25х130 МТ2662-4005
зенкер ø13xø18 МТ2331-4047
Вертикально-сверлильная - 0837
Рекомендуемые чертежи
- 24.01.2023
- 24.01.2023