Разработка технологического процесса изготовления детали Корпус фрезы




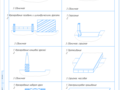
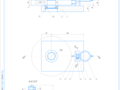
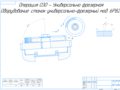
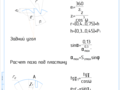
- Добавлен: 24.01.2023
- Размер: 6 MB
- Закачек: 1
Описание
Состав проекта
![]() |
![]() |
![]() |
![]() ![]() ![]() |
![]() ![]() ![]() ![]() |
![]() |
![]() ![]() ![]() |
![]() ![]() |
![]() ![]() ![]() |
![]() |
![]() |
![]() ![]() ![]() |
![]() ![]() ![]() |
![]() |
![]() ![]() ![]() ![]() |
![]() |
![]() |
![]() ![]() ![]() |
![]() ![]() ![]() |
![]() ![]() ![]() |
![]() |
![]() ![]() ![]() |
![]() ![]() ![]() |
![]() ![]() ![]() |
![]() ![]() ![]() |
![]() ![]() ![]() |
![]() |
![]() ![]() ![]() |
![]() ![]() ![]() |
![]() ![]() ![]() |
![]() |
![]() ![]() ![]() |
![]() |
![]() |
![]() ![]() ![]() |
![]() ![]() ![]() |
![]() ![]() ![]() |
![]() ![]() ![]() |
![]() ![]() ![]() |
![]() |
![]() |
![]() ![]() ![]() ![]() |
![]() ![]() ![]() |
![]() ![]() ![]() |
![]() ![]() ![]() |
![]() |
![]() ![]() ![]() |
![]() ![]() ![]() |
![]() ![]() ![]() |
![]() ![]() ![]() ![]() |
![]() ![]() ![]() |
![]() ![]() ![]() |
![]() ![]() ![]() |
![]() ![]() |
![]() ![]() ![]() |
![]() |
![]() |
![]() ![]() ![]() |
![]() |
![]() |
![]() ![]() ![]() ![]() |
![]() |
![]() |
![]() ![]() ![]() ![]() |
![]() ![]() ![]() ![]() |
![]() |
![]() ![]() ![]() ![]() |
![]() |
![]() ![]() ![]() ![]() |
![]() |
![]() |
![]() |
![]() ![]() ![]() |
![]() ![]() ![]() |
![]() |
![]() |
![]() |
![]() ![]() ![]() |
![]() |
![]() |
![]() ![]() ![]() ![]() |
![]() |
![]() |
![]() |
![]() ![]() ![]() |
![]() ![]() ![]() |
![]() |
![]() ![]() ![]() |
![]() ![]() ![]() |
![]() |
![]() |
![]() |
![]() ![]() ![]() |
![]() |
![]() |
![]() ![]() ![]() ![]() |
![]() |
![]() ![]() ![]() ![]() |
![]() |
![]() |
![]() ![]() ![]() |
![]() |
![]() |
![]() ![]() ![]() |
![]() |
![]() |
![]() ![]() ![]() ![]() |
![]() |
Дополнительная информация
маршрут2.DOC
Фреза двухсторонняя сборная
Код наименование операции
Обозначение документа
Код наименование оборудования
Наименование детали сб. единицы или материала
Универсально-фрезерная
Универсально-протяжной 6Р82
Верстак слесарный НЭ 1230
Плоскошлифовальный 3Б756
оэ 30.frw

о 060 1.DOC
Фреза двухсторонняя сборная
Код наименование операции
Обозначение документа
Код наименование оборудования
Внутришлифовальный 3А225
Установить закрепить заготовку снять после обработки
Патрон цанговый 8630-375 ГОСТ 24351-80
Шлифовать отверстие на базе торца
Круг шлифовальный 30 46-60СМ1-М3 ГОСТ16168-80; Калибр-пробка 8133-0918 Н8 ГОСТ 14810-89; 40
Контроль: исполнителю мастеру и ОТК 100%
0 – Внутришлифовальная
о 025 1.DOC
Фреза двухсторонняя сборная
Код наименование операции
Обозначение документа
Код наименование оборудования
Универсально-фрезерная
Универсально-фрезерный 6Р82
Установить закрепить заготовку снять после обработки
Универсальная делительная головка
Фрезеровать зубья на переферии
Оправка 6225-0148 ГОСТ 15067-75; Набор фрез одноугловых 90 80 z=30 ГОСТ 2287-76; Шаблон специальный
Контроль: исполнителю мастеру и ОТК 100%.
5 – Универсально-фрезерная
контроль2.DOC
Контролируемые параметры
Наименование средств ТО
Проверить габаритные размеры фрезы
Штангенциркуль ШЦ1-125-01 ГОСТ 166-89
Приспособление специальное
Технический контроль
маршрут3.DOC
Фреза двухсторонняя сборная
Код наименование операции
Обозначение документа
Код наименование оборудования
Наименование детали сб. единицы или материала
Внутришлифовальный 3А225
Универсально-заточная
Универсально-заточной 3А64Д
оэ 60.frw

относительно торцев проверять шаблоном.
о 035 1.DOC
Фреза двухсторонняя сборная
Код наименование операции
Обозначение документа
Код наименование оборудования
Универсально-фрезерный 6Р82
Напильник 2820-0027 ГОСТ 1465-80
Опилить фаску у шпоночного паза
Напильник 2820-0027 ГОСТ 1465-80; Надфиль полукруглый ГОСТ 1513-80
Контроль: исполнителю мастеру и ОТК 100%.
о 070 1.DOC
Фреза двухсторонняя сборная
Код наименование операции
Обозначение документа
Код наименование оборудования
Универсально-заточная
Универсально-заточной 3А64Д
Установить закрепить заготовку снять после обработки
Приспособление специальное
Заточить пластины по задней поверхности на переферии и торце
Оправка специальная; Круг алмазный АЧК 125×5×32 АС4-АСМ14-50-Б ГОСТ 9770-81; Угломер ГОСТ 5378-65
Контроль: исполнителю мастеру и ОТК 100%
0 – Универсально-заточная
оэ 25.frw

о 055 1.DOC
Фреза двухсторонняя сборная
Код наименование операции
Обозначение документа
Код наименование оборудования
Плоскошлифовальный 3Б756
Установить закрепить заготовку снять после обработки
Круг шлифовальный 24-36М1-М3 ГОСТ 161-81; Микрометр рычажный ГОСТ 4381-81
Контроль: исполнителю мастеру и ОТК 100%.
5 – Плоскошлифовальная
о 045 1.DOC
Фреза двухсторонняя сборная
Код наименование операции
Обозначение документа
Код наименование оборудования
Универсально-фрезерная
Универсально-фрезерный 6Р82
Установить закрепить заготовку снять после обработки
Универсальная делительная головка
Прорезать дно стружечных канавок на переферии
Оправка 6225-0148 ГОСТ 15067-75; Фреза специальная 90 z=60; Шаблон специальный; Радиусомер R15 ГОСТ4125-82
Контроль: исполнителю мастеру и ОТК 100%.
5 – Универсально-фрезерная
о 065 1.DOC
Фреза двухсторонняя сборная
Код наименование операции
Обозначение документа
Код наименование оборудования
Универсально-заточная
Универсально-заточной 3А64Д
Установить закрепить заготовку снять после обработки
Приспособление специальное
Заточить пластины по передней поверхности на переферии и торце
Оправка специальная; Круг алмазный АЧК 125×5×32 АС4-АСМ14-50-Б ГОСТ 9770-81; Угломер ГОСТ5378-65
Контроль: исполнителю мастеру и ОТК 100%
5 – Универсально-заточная
о 010 1.DOC
Фреза двухсторонняя сборная
Код наименование операции
Обозначение документа
Код наименование оборудования
Установить закрепить заготовку снять после обработки
Патрон 3-х кулачковый 7102-0072-1-2 ГОСТ 24351-80
Подрезать торец пов.
Резец подрезной 03129 ГОСТ20872-75 16×25×150
о 005 1.DOC
Фреза двухсторонняя сборная
Код наименование операции
Обозначение документа
Код наименование оборудования
Отрезной круглопильный па 8Г663-100
Установить закрепить заготовку снять после обработки
Станочное зажимное приспособление
Пила дисковая 250 мм z=72 ГОСТ2679-81; Штангенциркуль ШЦ1-125-01 ГОСТ166-89
Контроль: исполнителю мастеру и ОТК 100%.
о 030 1.DOC
Фреза двухсторонняя сборная
Код наименование операции
Обозначение документа
Код наименование оборудования
Универсально-фрезерная
Универсально-фрезерный 6Р82
Установить закрепить заготовку снять после обработки
Приспособление специальное
Фрезеровать зубья на торце
Оправка 6225-0148 ГОСТ 15067-75; Фреза одноугловая 90 z=36 ТУ2-035-526-76; Шаблон специальный
Контроль: исполнителю мастеру и ОТК 100%.
0 – Универсально-фрезерная
о 010 2.DOC
Фреза двухсторонняя сборная
Код наименование операции
Обозначение документа
Код наименование оборудования
Наименование детали сб. единицы или материала
Сверлить и зенкеровать отверстие
Сверло комбинированное; Штангенциркуль ШЦ1-125-01 ГОСТ 166-89
Резец проходной 03125-05 ТУ 35-892-82 16×25×150; Штангенциркуль ШЦ1-125-01 ГОСТ 166-89
Резец специальный Т15К6 ТУ 035-892-82 25×55×150; Штангенциркуль ШЦ1-125-01 ГОСТ 166-89; Радиусомер R2
Резец подрезной 03129 ГОСТ 20872-75 16×25×150; Плитка угловая α=450 ГОСТ 2875-82
контроль1.DOC
Фреза двухсторонняя сборная
Наименование операции
Наименование марка материала
Технический контроль
Наименование оборудования
Контролируемые параметры
Наименование средств ТО
Внешним осмотром проверить отсутствие заусенцев наличие фасок и маркировки
Проверить шероховатость обработанных пов.
Образцы шероховатости ГОСТ 9378-93
Проверить углы заточки пластин
Угломер универсальный ГОСТ 5378-85
Калибр-пробка 40 8133-0918 Н8 ГОСТ14810-69
Проверить размеры шпоночного паза
оэ 15-1.frw

о 020 1.DOC
Фреза двухсторонняя сборная
Код наименование операции
Обозначение документа
Код наименование оборудования
Универсально-фрезерная
Универсально-фрезерный 6Р82
Установить закрепить заготовку снять после обработки
Универсальная делительная головка
Фрезеровать паз под платину
Оправка 6225-0148 ГОСТ 15067-75; Фреза дисковая прорезная 100 z=80 ГОСТ 2679-73 Шаблоны специальные
Контроль: исполнителю мастеру и ОТК 100%.
0 – Универсально-фрезерная
маршрут1.DOC
Фреза двухсторонняя сборная
Код наименование операции
Обозначение документа
Код наименование оборудования
Отрезной круглопильный па 8Г663-100
Горизонтально-протяжная
Горизонтально-протяжной 7Б56
Универсально-фрезерная
Универсально-протяжной 6Р82
оэ 55.frw

ТИТ.DOC
на технологический процесс
механической обработки детали «Шестерня»
о 015 1.DOC
Фреза двухсторонняя сборная
Код наименование операции
Обозначение документа
Код наименование оборудования
Горизонтально-протяжная
Горизонтально-протяжной 7Б56
Установить закрепить заготовку снять после обработки
Станочное зажимное приспособление
Протянють шпоночный паз.
Протяжка специальная; Шаблон.
Контроль: исполнителю мастеру и ОТК 100%.
5 – Горизонтально-протяжная
оэ 45.frw

оэ 70.frw

о 050 1.DOC
Фреза двухсторонняя сборная
Код наименование операции
Обозначение документа
Код наименование оборудования
Универсально-фрезерная
Универсально-фрезерный 6Р82
Установить закрепить заготовку снять после обработки
Приспособление специальное
Прорезать дно стружечных канавок на торце
Оправка 6225-0148 ГОСТ 15067-75; Фреза специальная 90 z=36; Шаблон специальный; Радиусомер R1 ГОСТ4125-82
0 – Универсально-фрезерная
о 050 2.DOC
Фреза двухсторонняя сборная
Код наименование операции
Обозначение документа
Код наименование оборудования
Наименование детали сб. единицы или материала
Напильник 2820-0027 ГОСТ 1465-80 Надфиль полукруглый ГОСТ1513-80
Контроль: исполнителю мастеру и ОТК 100%.
0 – Универсально-фрезерная
оэ 20.frw

о 010 4.DOC
Фреза двухсторонняя сборная
Код наименование операции
Обозначение документа
Код наименование оборудования
Наименование детали сб. единицы или материала
Контроль: исполнителю мастеру и ОТК 100%.
о 010 3.DOC
Фреза двухсторонняя сборная
Код наименование операции
Обозначение документа
Код наименование оборудования
Наименование детали сб. единицы или материала
Расточить выточку поверхность
Резец расточной К01.4933 ГОСТ 18882-73 16×16×120; Шаблон специальный
Переустановить деталь закрепить снять после обработки
Патрон 3-х кулачковый 7102-0072-1-2 ГОСТ 24351-80
Резец подрезной 03129-05 ГОСТ 20872-75 16×25×150; Штангенциркуль ШЦ1-125-01 ГОСТ 166-89
Точить поверхности и
Резец специальный Т15К6 ТУ 035-892-82 25×65×150; Шаблон специальный; Радиусомер R2 ГОСТ4125-82
Резец подрезной 03129-05 ГОСТ 20872-75; Плитка угловая α=450 ГОСТ 2875-62
оэ 80.frw

торцев проверять шаблоном.
Радиальное биение режущих кромок зубьев
оэ 65.frw

оэ 10.frw

оэ 50.frw

записка 30 05 2004.doc
Проектируемый инструмент относится к группе режущих инструментов типа фреза. Данный тип инструмента является наиболее распространенным металлорежущим инструментом в машиностроении.
Разрабатываемый инструмент служит для обработки пазов редукционного корпуса железнодорожных ремонтных машин изготавливаемого из чугуна. Фреза двухсторонняя сборная правого резания обрабатывает пазы корпуса размером 70х15 миллиметров. Для увеличения продолжительности работы инструмента фреза оснащена твердосплавными пластинами марки ВК8 данный тип твердого сплава выбран в соответствии со справочными рекомендациями для данного типа обрабатываемого материала. Крепление твердосплавных пластин к корпусу фрезы осуществляется методом склеивания. Корпус фрезы является базовой деталью проектируемого инструмента с возможностью многократной смены твердосплавных пластин. Он изготавливается из конструкционной стали марки 45 с последующей термообработкой и точной подготовкой посадочных поверхностей под режущие твердосплавные пластины.
2 Определение типа производства
2.1 Разработку технологического процесса обработки детали «Корпус» начинаем с определения типа производства. Предварительно тип производства определяем по известному годовому объему и массе детали.
Масса детали равна 4.52 килограмма.
Объем выпуска деталей при типе производства 200 штук в год.
В соответствии с данными [1] ориентировочно принимаем мелко - серийный тип производства.
Таблица 1.1 – Ориентировочное определение типа производства
Объем выпуска деталей при типе производства шт.год
2.2 Окончательное определение типа производства осуществляется после разработки технологического процесса и расчета количества рабочих мест по ГОСТ3.1121-84 коэффициентом закрепления операций:
гдеО – число различных операций выполняемых в течении планового периода;
Р – число различных мест выполняющих различные операции.
По значению коэффициента закрепления операций видим что производство относится к мелкосерийному типу.
3 Анализ технологичности детали
3.1 По ГОСТ 14.205 – 83 технологичность конструкции – это совокупность свойств конструкции изделия определяющих ее приспособляемость к достижению оптимальных затрат при производстве эксплуатации и ремонте для заданных показателей качества объема выпуска и условий выполнения работ. К основным показателям качества изделия можно отнести безотказность функционирования долговечность точность сопряжений уровень шума безопасность коэффициент полезного действия удобство и простоту обслуживания степень механизации и т.д.
Технологическая характеристика детали определяется коэффициентом точности коэффициентом шероховатости поверхности коэффициентом использования металла.
3.2 Коэффициент точности обработки определяется по формуле:
где ITср – средний квалитет точности обработки изделия.
Средний квалитет точности обработки изделия определяется по формуле:
- общее количество принятых во внимание размеров детали.
3.3 Коэффициент шероховатости поверхности определяется по формуле:
где - среднее числовое значение параметра шероховатости поверхности по Ra для всех обрабатываемых поверхностей.
Среднее числовое значение параметра шероховатости поверхности определяется по формуле:
где - числовое значение параметра шероховатости поверхности;
- количество поверхностей имеющих соответствующую шероховатость;
- общее количество принятых во внимание поверхностей.
3.4 Коэффициент использования металла определяется после выбора заготовки определения ее массы и нормы расхода материала по формуле:
где - масса детали кг;
- норма расхода материала на деталь которая складывается из массы заготовки и потерь на отрезку угар заусенцы и т.д. кг.
3.5 Определяем средний квалитет точности и коэффициент точности обработки:
Определяем среднее числовое значение параметра шероховатости поверхности и коэффициент шероховатости поверхности:
Для большей наглядности технологическую характеристику детали «Корпус» приводят к табличной форме.
Таблица 1.2 – Технологическая характеристика детали «Корпус»
Квалитет шероховатости
Продолжение таблицы 1.2
Значение коэффициентов и близко к 1 что свидетельствует о низкой точности большинства поверхностей детали и большей их шероховатостью.
4 Расчет припусков на обработку
4.1 Припуски поковок определяются по ГОСТ 7505-89. По тем же стандартам производится назначение допусков на все размеры заготовки.
На наиболее точную поверхность детали припуск рассчитывается аналитически. В пояснительной записке выполняется расчет припусков на две поверхности вручную а на одну с использованием ЭВМ.
Исходная заготовка – Сталь 45 прокат. Габаритные размеры заготовки: диаметр 200 миллиметров ширина 30 миллиметров. В качестве заготовки используется круглый прокат обычной точности. Допуск на изготовление Tdз=2500.
4.2 Производим расчет припуска на внутреннюю поверхность детали «Корпус» диаметром 40Н11(+0027) миллиметров и шероховатостью 32 микрометра. Последовательность обработки отверстия по переходам: сверление растачивание и шлифование.
Расчет припуска производим по методике изложенной в [1].
Двусторонний минимальный припуск на обработку наружных поверхностей определяется по формуле (1.7):
– погрешность установки заготовки на выполняемом переходе мкм;
– суммарное отклонение расположения поверхности мкм;
– суммарное отклонение оси детали от прямолинейности мкм;
– отклонение оси детали от прямолинейности мкммм;
– погрешность центрирования заготовки мкм;
L – длина заготовки мм;
– допуск на диаметральный размер базы используемой при центрировании мкм.
Величина параметра качества поверхности проката составляет по [3]:
Для обычной точности проката величина удельной кривизны оси детали составляет 25 мкммм [2].
Суммарное отклонение оси детали от прямолинейности при обработке сортового проката круглого сечения составляет
Так как величина допуска на изготовление заготовки составляет Td3=2500 мкм погрешность центрирования заготовки
Тогда суммарное отклонение расположения поверхности
Значение параметров характеризующие точность и качество поверхности после обработки по переходам для поковки приведены в таблице (1.3)
Таблица 1.3 – Данные для расчета припуска
Остаточное отклонение расположения заготовки после обработки определяем по формуле
где Ку – коэффициент уточнения
Величина коэффициента уточнения после сверления Ку=006 для растачивания Ку=004.
Следовательно величина суммарного отклонения расположения поверхности на промежуточных переходах составит
Погрешность установки в трехкулачковом патроне мкм.
Погрешность установки после растачивания мкм.
4.3 Величина расчетных минимальных припусков равна:
Результаты расчета сводим в таблицу (1.4)
Определяется расчетный наибольший размер мм:
который является расчетным при обработки внутренних поверхностей. Он заносится в таблицу 1.8.2 в графу «Расчетный размер» и должен обеспечиваться шлифованием. Размер на предшествующем переходе определяется путем вычитания из наибольшего размера расчетного припуска на тонкое растачивание:
аналогично заполняются остальные ячейки таблицы
Эти размеры округляются до того же знака десятичной дроби с каким указан допуск на размер перехода и заносятся в графу dмах (Принятые размеры по переходам). Значения dmin получаем по формуле (1.11):
Подставив значения в формулу (1.11) получим:
Максимальные предельные значения припусков 2Zmax определяются как разность наименьших предельных размеров dmin на выполняемом и предшествующим переходах:
Минимальные предельные значения припусков 2Zmin определяются как разность наибольших предельных размеров dmax на выполняемом и предшествующим переходах:
Номинальный размер заготовки для внутренних поверхностей равен сумме наименьшего размера и половины поля допуска на заготовку и определяется по формуле (1.12):
Т. к. допуск расположен симметрично относительно номинального размера то на чертеже должно быть указано:
4.5 Проверка расчета проводится по формуле (1.13):
где и - соответственно полученные суммы предельных припусков;
и - допуск на изготовление заготовки и детали соответственно.
Подставляем полученные значения в формулу (1.13) и получаем:
5 Составление маршрута обработки детали
5.1 Исходя из того что выбранная нами заготовка – прокат 205х30 целесообразно на заготовительной операции применить отрезной – круглопильный полуавтомат ВГ663.
5.2Как было сказано выше всю токарную обработку целесообразно выполнять на одном станке с одним переустановом заготовки в трехкулачковом патроне. Для токарной операции выбираем токарно-винторезный станок 16К20.
5.3При протягивании шпоночного паза возможна одновременная обработка двух заготовок что снизит в два раза вспомогательное время. Для этой операции выбираем горизонтально – протяжной станок 7Б56.
5.4Фрезерование пазов под пластины производим при помощи универсальной делительной головки настроив ее на простое деление. Назначаем на эту операцию универсально – фрезерный станок 6Р82Ш.
5.5Снятие спинки зуба производим также в универсальной делительной головке на станке 6Р82Ш.
5.6Формирование торцовых зубьев невозможно без специального приспособления так как дно впадины зубьев находится под углом к горизонтальной плоскости. Конструирование и описание работы специального поворотного приспособления приведены в разделе 3. Приспособления закрепляются на столе станка с Т-образными пазами при помощи болтов. Выбираем для операции станок 6Р82Ш.
5.7После формирования окончательного профиля заготовки корпуса фрезы она подается на верстак слесарной операции где у нее зачищаются заусенцы опиливаются фаски шпоночного паза и набиваются пластинки ВК8 также заготовка клеймиться.
5.8После набивки пластин последние припаиваются в электропечи одновременно с этим корпус фрезы подвергается термообработке. После термообработки деталь подвергается для очистки пескоструйной обработке.
5.9При пайке припой иногда заполняет дно стружечных канавок поэтому необходимо прорезать дно канавок специальными фрезами при этом будет обеспечен необходимый радиус скруглений дна канавок. Обработка ведется аналогично снятию спинок зубьев на цилиндрической части и формированию торцовых зубьев. Используемый станок – 6Р82Ш.
5.10 Для шлифования посадочного отверстия необходимо предварительно обработать базу – отшлифовать посадочные торцы. Операцию проводим на плоскошлифовальном станке 3Б756 с вертикальным шпинделем и круглым столом.
5.11На базе торца шлифуем посадочное отверстие фрезы на внутришлифовальном станке 3А225 с закреплением заготовки в цанговом патроне.
5.12Заключительной частью процесса обработки резанием является заточка пластин по передней и задней поверхности на периферийных и торцовых зубьях. В отличие от базового технологического процесса по которому заточка происходила раздельно по торцовой и периферийной частям зубьев в проектируемом технологическом процессе благодаря использованию специального двухпозиционного приспособления возможна заточка передней или задней поверхности на периферийных и торцовых зубьях на одном станке в течение одной операции с одним переустановом заготовки в приспособлении. Используем два станка 3А64А.
5.13 Завершает техпроцесс контрольная операция в ходе выполнения которой контролируются все ответственные размеры и отклонения формы и расположения.
Для контроля радиального биения режущих кромок зубьев конструируем специальное приспособление.
6 Выбор оборудования
6.1 Станок токарный патронно – центровой с ЧПУ Модель 16К20Ф3.
Рисунок 1.1 - Станок токарный модель 16К20Ф3
Предназначен для токарной обработки деталей типа тел вращения в замкнутом полуавтоматическом цикле. Применяется в мелкосерийном и серийном производстве. Класс точности П по ГОСТ 8 – 82Е. Станки могут выпускаться с различными устройствами ЧПУ типа МС2101.05 – 02 2Р22 и электроника НЦ – 31 – 02 в исполнении для встраивания в гибкие производственные модули а также в специальном и специализированном исполнении по согласованию с заказчиком.
Наибольший диаметр заготовки устанавливаемой над станиной мм
Наибольшая длина заготовки устанавливаемая в центрах мм
Наибольший диаметр заготовки мм:
обрабатываемой над станиной не более
над суппортом не менее
Частота вращения шпинделя мин-1
Наибольший крутящий момент на шпинделе Н*м (кгс*м)
Минимальная рабочая скорость подачи мммин:
Максимальная рекомендуемая скорость рабочей подачи мммин:
Габарит станка без отдельно стоящего шкафа УЧПУ мм не более:
Габарит станка с отдельно стоящим шкафом УЧПУ мм не более:
без отдельно стоящего шкафа УЧПУ
с отдельно стоящим шкафом УЧПУ
6.2 Автомат отрезной круглопильный Модель 8Г663
Предназначен для разрезки дисковыми пилами черных металлов в заготовительных цехах машиностроительных и ремонтных предприятий.
Автомат оснащен механизированным устройством для складирования и поштучной выдачи круглых заготовок и труб а также автоматическим столом выгрузки.
Механизированное устройство позволяет одновременно укладывать на него от 5 до 18 заготовок в зависимости от их диаметра в диапазоне технической характеристики. Наибольшая длина укладываемого материала 6 м. наименьшая – 25 м.
Рисунок 1.2 - Автомат отрезной круглопильный Модель 8Г663
Применение механизированного устройства (стеллажа – накопителя) и автоматического стола для выгрузки заготовок длиной до 1500 мм позволяет полностью автоматизировать цикл разрезки заготовок повышает производительность автомата за счет сокращения вспомогательного времени на обслуживание станка.
В автомате применена новая более надежная конструкция механизмов зажима и подачи материала.
Широкий диапазон скоростей шпинделя и бесступенчатое регулирование рабочей подачи пильного диска позволяет подбирать оптимальные режимы резания
Адаптивный гидравлический привод рабочей подачи способствует получению наибольшей производительности разрезания материала и экономии режущего инструмента.
В гидроприводе автомата применена притирочная и модульная аппаратура с международными присоединительными размерами размещенная как и электрическая аппаратура в отдельных шкафах что облегчает ее обслуживание и увеличивает срок службы
Автомат оснащен шнековым транспортером для удаления стружки счетчиком числа резов.
Блокировка и защитные устройства обеспечивают безопасность работы.
Для разрезки профильных материалов (квадрат швеллер двутавр уголок) а также для патентной разрезки прутков малого диаметра (от 20 мм) необходимо производить переналадку.
Класс точности автомата Н по ГОСТ—82Е.
Габаритные размеры станка 2640х2400х1585 мм.
6.3 Станок внутришлифовальный универсальный особо высокой точности. Модель 3А225
Рисунок 1.3 - Станок внутришлифовальный. Модель 3А225
Станок предназначен для шлифования цилиндрических и конических глухих и сквозных отверстий; снабжен торцешлифовальным приспособлением позволяющим шлифовать наружный торец изделия за один установ со шлифовкой отверстия.
Выносное оборудование станка (электрошкаф насосная станция и бак эмульсии) соединено со станком готовой электропроводкой с штепсельными разъемами.
Область применения станка — машиностроительные заводы с серийным и мелкосерийным производством а также инструментальные и ремонтные цехи этих заводов.
Станина станка служит основой для установки и крепления основных узлов станка.
В верхней плоскости станины устанавливаются продольные стальные закаленные направляющие (V-образные и плоская) а также имеется ванна для сбора и слива охлаждающей жидкости. В передней нише станины располагается гидроаппаратура управления. Ниша закрыта крышкой на лицевой стороне которой расположены органы управления станком.
Стол совершает возвратно-поступательное движение от гидроцилиндра. Наладочное перемещение стола производится вручную от маховика ручного перемещения стола расположенного на передней стороне станины. Реверсирование стола при шлифовании и правке осуществляется упорами закрепленными на передней стороне и действующими на гидропанель реверса.
Станок универсальный загрузочных устройств не имеет в автоматическую линию не выстраивается. Процесс шлифования осуществляется с охлаждающей жидкостью вследствие чего вентиляция на станке не требуется.
Габариты станка: 2225х1775 мм.
Масса станка: 2100 кг.
6.4 Станок плоскошлифовальный с выдвижным круглым магнитным столом и вертикальным шпинделем. Модель 3Б756.
Рисунок 1.4 - Станок плоскошлифовальный. Модель 3Б756.
Предназначен для шлифования плоскостей различных деталей из чугуна стали и других ферромагнитных материалов торцом шлифовального круга. Конструкция и компоновка станка обеспечивают необходимые технологические качества и удобство обслуживания при эксплуатации.
На станке установлено измерительное устройство для проверки размеров деталей в процессе обработки.
Кинематическая схема имеет ручную дозированную и автоматическую подачи и ускоренное перемещение шлифовальной бабки.
С целью повышения ремонтоспособности в шлифовальной бабке применен пристроенный фланцевый электродвигатель.
Электромагнитный стол размагничивает шлифуемые детали непосредственно на станке. Кожух ограждения электромагнитного стола открытого типа обеспечивает свободный доступ к шлифовальной бабке столу и обрабатываемым деталям в зоне загрузки.
Роликовые опоры качения повышают плавность подачи шлифовальной бабки.
Система охлаждения обеспечивает отвод тепла из зоны шлифования и нормальный смыв шлама.
Высокая жесткость и виброустойчивость станка обеспечивают высокую точность и чистоту обрабатываемых изделий и сохраняют его первоначальную точность.
Класс точности станка П по ГОСТ 8—82.
Диаметр магнитного стола – 800 мм.
Габарит станка – 280±25х1635±25х3380±25 мм.
Масса станка – 9300 кг.
6.5 Консольно – фрезерный станок. Модель 6Р82Ш.
Станок предназначен для выполнения разнообразных работ цилиндрическими дисковыми фасонными торцовыми и пальцевыми фрезами в условиях единичного и серийного производства.
На станках можно обрабатывать вертикальные и горизонтальные плоскости пазы углы нарезать зубчатые колеса.
Технологические возможности станков могут быть расширены путем применения делительной головки и накладной фрезерной головки.
Станок обладает высокой жесткостью. Класс точности Н.
Габарит станка — 2305х1940х1680 мм.
Вес станка – 2900 кг.
Размеры рабочей поверхности стола – 1250х320 мм.
Рисунок 1.5 - Консольно – фрезерный станок. Модель 6Р82Ш.
6.6 Протяжной горизонтальный станок. Модель 7Б56.
Станок предназначен для обработки методом протягивания предварительно обработанных или черных сквозных отверстий различной геометрической формы и размеров.
При оснащении станка специальным приспособлением на нем можно обрабатывать и наружные поверхности.
Рисунок 1.6 - Протяжной горизонтальный станок. Модель 7Б56.
Класс точности станка Н. Станок отличается большой производительностью и высокой точностью обработки.
При оснащении автоматизированными приспособлениями для подачи и съема обрабатываемых деталей станок может работать в автоматическом цикле а также встраиваться в автоматические линии.
Наиболее эффективно использование станка в массовом и крупносерийном производстве. Однако простота переналадки позволяет успешно применять его в мелкосерийном и единичном производстве.
Повышенная жесткость и виброустойчивость конструкции станка позволяют работать во всем диапазоне рабочих скоростей и тяговых усилий сохраняя при этом высокий класс чистоты обработанной поверхности стойкость протяжки.
Привод станка гидравлический регулирование скорости рабочего и обратного ходов бесступенчатое.
Отвод и подвод протяжки к рабочему патрону а также процесс резания механизированы.
Для удобства обслуживания в станке предусмотрены механизм регулировки длины хода рабочих салазок централизованная принудительная смазка направляющих сигнализация о затуплении протяжки при помощи электроконтактного манометра фильтрация масла в гидросистеме.
Пусковая и предохранительная электроаппаратура размещена в отдельном электрошкафу что облегчает ее обслуживание и увеличивает срок службы.
Применение бесконтактных путевых переключателей слаботочной электроаппаратуры управления и электромагнитов постоянного тока обеспечивает высокую надежность работы электрооборудования.
По особому заказу за отдельную плату станок комплектуется поддерживающей призмой позволяющей компенсировать массу обрабатываемой детали и упростить процесс ее установки относительно оси протягивания и грузоподъемником для установки и снятия тяжелых обрабатываемых деталей и протяжек.
Габарит станка – 7200х2200х1700 мм.
7 Разработка операционного процесса обработки.
7.1 Отрезная операция. Используем отрезной – круглопильный па 8Г663. Заготовка – крут 205 мм разрезается на отдельные заготовки длиной l=30мм. В качестве режущего инструмента используем пилу дисковую 250 мм z=72.
Определим расчетные данные для установления режимов резания и технической нормы времени на элементы операции (далее расчетные данные). Ширина обработки В=5 мм; длина обработки L=1025 мм; глубина резания t=205 мм; число проходов i=1. Назначаем подачу S2=008 и частоту вращения шпинделя станка n=315мин-1 определяем скорость резания по формуле Vрез ммин
Основное время на операцию Т0 мин
где Sn – минутная подача мммин
где z – число зубьев инструмента
n – частота вращения шпинделя мин-1 .
Вспомогательное время на операцию Тв=05 мин.
7.2 Токарная операция. Используем токарно – винторезный станок 16К20Ф3.
а) подрезка торца. Режущий инструмент – резец подрезной 03129 ГОСТ 20872 – 75 16х25х100.
Расчетные данные: диаметр обработки D=205 мм длина обработки глубина резания t=25 мм; число проходов i=1 подача S=11 ммоб частота вращения шпинделя n=200 мин-1.
б) обработка отверстия. Режущий инструмент – специальный комбинированный осевой инструмент мерительный - штангельциркуль.
Расчетные данные: диаметр обработки D=40 мм длина обработки глубина резания t=20 мм; число проходов i=1 подача S=0105 ммоб частота вращения шпинделя n=530 мин-1.
в) обточка наружного диаметра. Режущий инструмент – резец проходной 03125 – 05 ТУ035 – 892 – 88 16х25х150 мерительный – штангельциркуль.
Расчетные данные: диаметр обработки D=200 мм длина обработки глубина резания t=20 мм; число проходов i=1 подача S=11 ммоб.
Для установления режимов резания рассчитаем максимально допустимую скорость резания Vрез ммин на данном переходе по формуле:
Т – среднее значение стойкости инструмента мин.
Кs – произведение коэффициентов учитывающих влияние материала заготовки состояния поверхности материала инструмента.
Рассчитаем максимально возможную частоту вращения шпинделя мин-1 по формуле:
Корректируя данное значение с паспортными данными станка назначаем ближайшую меньшую частоту n=200 мин-1 пересчитываем реальное значение скорости резания в соответствии с реальной частотой вращения шпинделя по формуле (1.17)
г) выточка на торце. Режущий инструмент – резец специальный Т15К6 25х55х150 мерительный – штангенциркуль.
Расчетные данные: диаметр обработки D=170 мм длина обработки глубина резания t=55 мм; подача S=11 ммоб скорость вращения шпинделя n=125 мин-1
д) нарезка фаски. Режущий инструмент – резец подрезной 03129 ГОСТ 20872 – 75 мерительный – плитка угловая α=45º ГОСТ 2875 – 82.
Расчетные данные: диаметр обработки D=43 мм длина обработки глубина резания t=212 мм; число проходов i=1 подача S=11 ммоб частота вращения шпинделя n=200 мин-1.
е) расточка выточки. Режущий инструмент – резец расточной К01.4933 ГОСТ 18882 – 73 мерительный – шаблон специальный.
Расчетные данные: диаметр обработки D=42 мм длина обработки L=9мм глубина резания t=1 мм число проходов i=1 подача S=11 ммоб частота вращения шпинделя n=200 мин-1.
ж) подрезка второго торца. Режущий инструмент – резец подрезной 03129 – 05 ГОСТ 20872 – 75 мерительный – штангенциркуль.
Расчетные данные: диаметр обработки D=200 мм длина обработки L=1205мм глубина резания t=25 мм число проходов i=1 подача S=11 ммоб частота вращения шпинделя n=200 мин-1.
з) проточка торцевых выточек. Режущий инструмент – резец специальный Т15К6 25х65х150 мерительный – радиусомер R2 ГОСТ 4125 – 82.
Расчетные данные: диаметр обработки D=170 мм длина обработки L=6мм глубина резания t=70 мм число проходов i=1 подача S=11 ммоб частота вращения шпинделя n=125 мин-1.
и) подрезка второй фаски – аналогичная п.п. д).
Общее основное время токарной операции Т0=154 мин вспомогательное 225 мин.
Протяжная операция. Режущий инструмент – протяжка специальная мерительный – шаблон специальный.
Расчетные данные: ширина резания В=10 мм длина обработки L=21мм глубина резания t=3 мм число проходов i=1 скорость резания 7 ммин.
Вспомогательное время на операции Тв=065 мин.
7.3 Фрезерная операция. Режущий инструмент – фреза дисковая прорезная 100 z=80 ГОСТ 2679-73 мерительный – шаблоны специальные.
Расчетные данные: ширина фрезерования В=4 мм длина обработки L=27мм глубина резания t=8 мм подача St=0025 число проходов i=36.
Рассчитаем максимально допустимую скорость резания ммин по формуле
Т – стойкость инструмента мин;
D – диаметр инструмента (фрезы);
z – количество зубьев фрезы.
Рассчитаем максимально возможную величины подачи по формуле (2.5)
Скорректируем полученное значение частоты по повороты станка и назначим ближайшую меньшую n=100 мин-1
Рассчитаем реальную скорость резания
Вспомогательное время на операции Тв=145 мин.
7.4 Фрезерование спинки зуба. Режущий инструмент – набор фрез угловых мерительный – шаблон специальный диаметр фрез 90 80 z=30 ТУ 2 – 035 – 76.
Расчетные данные: ширина фрезерования В=14 мм длина обработки L=27мм глубина резания t=5 мм подача St=009 число проходов i=36 частота вращения шпинделя n=80 мин-1.
Вспомогательное время на операции Тв=15 мин.
Фрезерование торцевых зубьев. Режущий инструмент – фреза угловая 90 z=36 ТУ 2 – 035 – 76 мерительный – шаблон специальный.
Расчетные данные: ширина фрезерования В=19 мм длина обработки L=13мм глубина резания t=3 мм подача St=01 число проходов i=36 частота вращения шпинделя n=80 мин-1.
Вспомогательное время на операции Тв=13 мин.
7.5 Слесарная операция. Инструмент: напильник 2820 – 0027 ГОСТ 1465 – 80 надфиль полукруглый ГОСТ 1513 – 80 молоток 7850 – 0102 Ц15хр ГОСТ 2310 – 77 клеймо специальное.
Вспомогательное время на операцию Тв=325 мин.
7.7 Шлифование торцев. Инструмент – круг шлифовальный 24–36М1–М3ГОСТ 14170 – 81 мерительный – микрометр рычажный ГОСТ 4381 – 81.
Расчетные данные: ширина шлифования В=10мм длина обработки L= 1855 мм число проходов i=1 скорость заготовки 15 мс круга 25 мс.
Вспомогательное время на операцию Тв=09 мин.
7.8 Шлифование отверстия. Инструмент – круг 70 46 – 60 СМ1 – М3 ГОСТ 16168 – 80 мерительный – калибр – пробка 8133 – 0918 М7 ГОСТ 14810 – 80 D=40.
Расчетные данные: диаметр отверстия D=40мм длина отверстия L=21 мм глубина резания t=002 мм подача продольная Sпрод.=22 мм число проходов i=1 скорость заготовки Vзаг.=25 мсек скорость круга Vкр=25 мсек.
где В – ширина круга мм.
7.9 Заточная операция. Заточка передних поверхностей. Инструмент – круг алмазный АЧК 125х5х32 АСЧ – АСМ 14 – 50 – 5 ГОСТ 9770 – 81 угломер ГОСТ 5378 – 65.
Расчетные данные: ширина обработки В=4мм длина обработки L=36 мм глубина резания t=001 мм подача продольная Sпрод.=25 мм число проходов i=36 подача поперечная Sпоп.=005 мм скорость круга Vкр=17 мсек.
7.10 Заточка пластин по задним поверхностям. Инструмент – круг алмазный АЧК 125х10х32 АСЧ – АСП14 – 50 –Б ГОСТ 9770 – 81 угломер ГОСТ 5378 – 65.
Расчетные данные: ширина шлифования В=55 мм длина шлифования L=30 мм глубина шлифования t=0008 мм число проходов i=36 продольная подача Sпрод=15 поперечная Sпоп=001 скорость круга = 22 мс.
Вспомогательное время на заточных операциях Тв=19 мин.
7.11 В ''Приложении Б'' представлены для сравнения расчет припусков на плоско – и внутришлифовальную операции а также расчет режимов резания для обточки наружного диаметра на токарной операции и фрезерования пазов под пластины.
Контроллер – проверяет все ответственные размеры наличие фасок клейма проверяет шероховатость поверхностей отклонения расположения и формы поверхностей.
Вспомогательное время Тв=86 мин.
Инструмент и средства контроля: образцы шероховатости ГОСТ 9378 – 93; угломер универсальный ГОСТ 5378 – 85; калибр - пробка 8133 – 0918 Н7 ГОСТ 14810 – 89 D=40; калибр специальный штангенциркуль ШЦ 1 – 125 – 01 ГОСТ 166 – 89шаблон специальный приспособления для контроля радиального биения кромок зубьев.
Проектирование инструмента
1 Выбор способа обработки заданной поверхности
1.1Поверхность для обработки которой необходимо спроектировать инструмент представляет собой широкий паз размерами 15х70 мм как показано на рисунке 2.1
Рисунок 2.1 – Обрабатываемая поверхность
Материал обрабатываемой поверхности – чугун.
Классификацию способов обработки ведем по типам производства в которых будет оправдано применение того или иного метода обработки.
1.2 Фрезерование паза торцевой фрезой в два или несколько проходов будет оправдывать себя в единичном производстве. При обработке одной или нескольких деталей не возникает необходимости проектирования специального инструмента поэтому обработку можно произвести на универсальном оборудовании стандартным режущим инструментом. При этом будет увеличиваться основное и вспомогательное время по сравнению с использованием специального режущего инструмента но в единичном производстве этой разницей можно пренебречь т. к. прибыль от изготовления и продаж нескольких деталей может оказаться ниже чем расходы на создание специального инструмента.
1.3 Последовательная обработка прорезными фрезами с последующим фрезерованием цилиндрической фрезой оправдает себя также только в единичном производстве. Данный способ предусматривает использование двух фрезерных станков что безусловно увеличит себестоимость обрабатываемой детали если применить его в серийном производстве. Этот способ можно использовать например при ремонте или изготовлении опытного оригинального изделия.
1.4 Фрезерование концевой фрезой в несколько проходов также оправдает себя только в единичном производстве. Этот метод мог бы оправдать себя в серийном производстве если бы паз имел криволинейное направление и для обработки требовалось использование специального копировально-фрезерного полуавтомата что нецелесообразно для обработки прямолинейного расположенного паза.
1.5 Строгание плоскости паза стандартным или специальным строгальным резцом может оправдать себя как в единичном так и в серийном производстве. Строгальный станок работает по замкнутому циклу поэтому производительность процесса строгания достаточно велика. Эффективность применения данного метода обуславливается еще тем что стандартный строгальный резец дешевле а специальный – проще в изготовлении чем другой стандартный или специальный инструмент например фреза или протяжка.
1.6 Электроискровое прошивание можно применить при обработке детали из труднообрабатываемого материала. При обработке заданной детали этот метод можно использовать в условиях единичного или мелкосерийного производства. Достоинства данного способа обработки: отсутствие надобности в специальных инструментах и абразивах; возможность полной механизации; возможность местной обработки крупногабаритных деталей без специальных крупных станков; возможность формоизменения заготовки с одновременным изменением технических свойств ее поверхности (повышение коррозионной стойкости; электропроводимости и пр.). Недостатки – большая величина времени обработки и энергоемкости.
1.7 Фрезерование набором фрез оправдает себя в среднем- и крупносерийном производстве. Набор фрез можно составить из нескольких стандартных инструментов. Процесс имеет достаточно большую производительность предусматривает использование универсально – фрезерного станка однако имеет недостаток – повышенную величину подготовительно - заключительного времени в сравнении с фрезерованием специальной фрезой.
1.8 В условиях крупно- и среднесерийного производства наиболее эффективно оправдает себя фрезерование специальной двухсторонней фрезой которое обеспечивает высокую производительность точность и качество обработки.
1.9 В условия массового и крупносерийного производства оправдает свое применение метод протягивания паза за один проход набором специальных наружных протяжек. Процесс протягивания характеризуется высокой производительностью вследствие снятия всего припуска за один проход а также возможностью одновременной обработки нескольких деталей высокой точностью и чистотой обработанной поверхности малой величиной основного времени. При непрерывной схеме протягивания когда детали движутся по относительно инструмента замкнутому контуру использование данного метода особенно эффективно.
Делая сравнительный анализ возможных способов обработки заданной поверхности приходим к выводу что наиболее целесообразным способом будет использование специальной двухсторонней фрезы для фрезерования в условиях среднесерийного производства крупногабаритной детали с заданными требованиями к точности и качеству обработанной поверхности.
Фрезу необходимо сделать сборной с припаянными к корпусу из стали 45 твердосплавными пластинами.
Марку твердого сплава выбираем в соответствии с обрабатываемым материалом и видом обработки. Для фрезерования паза в чугунной заготовке выбираем марку сплава ВК8 со следующими физико – механическими свойствами:
а) предел прочности при изгибе 1100 МПа;
б) предел прочности при сжатии 3300 МПа:
в) красностойкость 800 – 8500 С;
г) твердость 87 – 91 HRa.
2 Расчет конструктивных параметров фрезы двухсторонней сборной с пластинами ВК8
2.1 Наружный диаметр и ширину фрезы определяем исходя из размеров обрабатываемой поверхности.
B=Lпл.+5=20+5=25 мм.(2.1)
где Lпл – длина пластинки мм.
2.2 Диаметр посадочного отверстия D0мм определим исходя из размеров имеющейся оправки
2.3 Размеры шпоночного паза выбираем в соответствии с диаметром посадочного отверстия D0
Глубина паза t1=35мм.
Во избежание концентрации напряжений дно паза выполняем со скруглениями R=1 мм.
2.4 С обеих сторон посадочного отверстия делаем фаски 15х450
2.5 В середине отверстия для уменьшения длины точной посадочной поверхности делаем выточку глубиной 1 мм с оставлением точно обработанных поясков на длине
где L – длина посадочного отверстия мм.
2.6 Определим число зубьев zфрезы по формуле
где - коэффициент равномерности фрезерования;
- угол контакта фрезы с заготовкой град.
где t – глубина фрезерования мм.
2.7 Для улучшения равномерности фрезерования располагаем зубья под наклоном к оси фрезы с углом град.
где В – ширина фрезерования мм;
z – число зубьев фрезы шт.
2.8 Определим окружной шаг зубьев Рт мм по формуле
2.9 Определим профиль и размеры зубьев фрезы исходя из значения окружного шага.
Профиль зубьев – трапециидальный.
Угол тела зуба выбираем в пределах .
Угол стружечной канавки 0 определяем из выражения
где - угол соответствующий шагу зубьев при приведенном их количестве
Приведенной число зубьев есть то число зубьев которое имеет фреза радиусом Ri соответствующим радиусу кривизны эллипса в направлении его оси.
Окончательно угол тела зуба равен
Высота зуба Н мм определяем из выражения
Радиус закругления дна впадины R мм найдем из выражения
2.10 Задний угол выбирается по формуле
где - максимальная толщина среза мм
где Sz – подача на зуб при работе фрезы мм.
Передний угол γ0 выбирается в зависимости от свойств обрабатываемого материала. При обработке стали и чугуна б принимаем γ=50.
Для торцовых зубьев α=80 γ=80.
2.11 Проектируя фрезу с наклонными зубьями необходимо угол наклона паза под пластину и его смещение Е рассчитать так чтобы обеспечить получение заданного переднего угла без дополнительной заточки.
Радиальный передний угол γ1 определяем для точки А лежащей в середине ширины фрезы В2 так как в этом случае обеспечивается минимальное изменение переднего угла по ширине лезвия. Для этой точки
Для точки А смещение паза под пластину eмм
Для установки прорезной фрезы при фрезеровании паза смещение его на торцах Е мм определяется как
При округлении значений е Е1 Е2 до десятых долей получим следующие предельные отклонения величины переднего угла что приемлемо.
3 Прочностной и температурный расчет зубьев.
3.1 Расчет прочности режущей части инструмента производится по допускаемым напряжениям первого рода. Согласно этому методу по действующим нагрузкам определяется главные напряжения . Далее по теории предельных напряженных состояний определяются эквивалентные напряжения т.е. одноосные растягивающие напряжения равноопасные заданному сложному напряженному состоянию. Максимальное эквивалентное напряжение сопоставляется с допускаемым напряжением [6].
где - предел прочности инструментального материала при растяжении;
- коэффициент запаса хрупкой прочности.
В общем случае напряжения первого рода в режущей части определяются как сумма напряжений возникающих под действием сил резания и температурного поля.
Эквивалентное напряжение определяется по формуле
где - предел прочности материала при сжатии.
Главные напряжения вычисляются по формулам
где - радиальные тангенсальные и касательные напряжения.
При расчетах по формуле (2.20) имеем 1 при положительной величине и 2 при нулевой и отрицательной.
Для того чтобы определить можно ли эксплуатировать инструмент в течение срока службы Т при заданных условия обработки необходимо сравнить фактический коэффициент запаса прочности nB с коэффициентом запаса прочности n определяемым с учетом разброса прочностных характеристик инструментальных материалов изменчивости напряжений в опасных точках влияния температурного поля частоты и амплитуды колебаний сил резания.
Для определения данного коэффициента ученых М.П. Вадачкория предлагает формулу
где - характеристика безопасности
- коэффициент вариации параметра прочности
- коэффициент вариации параметра напряжения
предполагая что характеристика прочности и и параметр нагрузки подчиняются нормальному закону распределения.
Характеристика безопасности является функцией надежности которая в свою очередь является функцией срока службы.
При оценке работоспособности инструмента необходимо сравнить
и n рассчитанный по формуле (2.21). Если последний окажется больше чем фактический nB то выбранные условия резания для данного инструмента являются недопустимыми с заданной вероятностью безотказной работы и их следует корректировать.
3.2 Любой процесс резания характеризуется уравнением теплового баланса
Qд+Qтп+Qтз=Qс+Qдет+Qин+Qос(2.23)
где Qд – тепло деформации в зоне сдвига
Qтп – тепло трения по передней поверхности в пределах площадки контакта С1
Qтз – тепло трения по задней поверхности в пределах площадки контакта С2
Qс – тепло уходимое в стружку
Qдет – тепло уходимое в деталь
Qин– тепло уходимое в инструмент
Qос– тепло уходимое в окружающую среду.
Максимальная температура в зоне резания приходится примерно на середину площадки контакта передней поверхности инструмента со стружкой с1 к лезвию и основанию зуба температура зуба уменьшается.
Температурой резания называется средняя температура на поверхности контакта инструмента со стружкой и деталью ºС
где - средняя температура на передней поверхности ºС;
- средняя температура на задней поверхности ºС.
Так как у незатупленного инструмента площадка с2 довольно мала температурой резания ºС следует считать
где - средняя температура по передней поверхности ºС.
Выясним влияние угла наклона зубьев и скорости резания V на температуру резания.
На рисунке показаны два зуба. Первый – прямой работает с большей скоростью резания второй – наклонный работает с меньшей скоростью резания. Оба зуба снимают слои одинакового сечения.
F1=a1b1=a2b2=F2 при a1>a2 b1b2.
Таким образом на передней поверхности обоих зубьев действуют одинаковые по мощности готовые источники. При увеличении относительной длины движущегося теплового источника к его ширине средняя температура в пределах площадки с1 непрерывно уменьшается т.к. условия отвода тепла через тело инструмента до второго зуба более благоприятно потому что источник тепла более удален от вершины зуба что способствует понижению температуры.
Из вышеуказанного следует что температура резания тем меньше чем больше отношение ва и следовательно V.
Конструкторская часть
1 Конструирование станочного приспособления.
1.1 В ходе разработки технологического процесса изготовления проектируемой фрезы возникла необходимость на одном из переходов разместить заготовку под углом к горизонтальной плоскости для базирования наклонных стружечных канавок как показано на операционном эскизе. Мы реализовали это следующим образом.
1.2 Заготовка фрезы надевается на оправку делительного диска 2 и закрепляется на нем гайкой. Делительный диск расположен под требуемым углом к горизонтали. Нижняя шейка его помещена в упорный подшипник 6 который вставлен в отверстие в корпусе 1 приспособления и зафиксирован эксцентрическим кольцом 7. Пренебрегая погрешностью установки делительного диска в подшипник и подшипника в корпус делаем вывод что отклонение оси делительного диска от номинального расположения зависит в большей степени от точности отверстия в корпусе.
1.3 Кинематика деления заготовки на величину углового шага зубьев такова. Делительный диск связан через шпонку 11 с червячным колесом 4 которое вращается червяком 3 приводим в движение рукояткой 15 надетой на вал 5 на котором и помещается червяк связанный с валом шпонкой 12. Вал вращается в радиальных подшипниках 8 установленных в корпусе. Передаточное отношение червячной пары 1:36 поэтому при повороте рукоятки на 360º заготовка вместе с делительным диском повернется на 10º т.е. угловой шаг зубьев. Фиксация делительного диска происходит с помощью фиксатора 13 закрепленного в корпусе палец которого входит в одно из 36 – ти отверстий делительного диска. При повороте заготовки необходимо оттянуть фиксатор на себя и вращать рукоятку до того момента когда подпружиненный палец фиксатора не попадет в следующее отверстие делительного диска. Для базирования заготовки относительно одного из положений делительного диска и связанного с ним червячного колеса в теле последнего закреплен фиксатор 14 подпружиненный палец которого выступает из тела колеса на 57 мм под углом наклона под пластину обработанного на предыдущей операции и который является базой для формирования торцовых зубьев. При размещении заготовки на делительном диске торец фрезы нажмет на палец который утопится в теле червячного колеса. Для фиксации необходимо повернуть заготовку относительно колеса на несколько градусов пока над пальцем не появится паз тогда под действием пружины палец войдет в паз и заготовку останется зажать сверху гайкой.
В основании приспособления сделаны пазы для закрепления его на столе фрезерного станка.
Приспособление просто как в изготовлении так и в эксплуатации.
2 Конструирование контрольного приспособления.
2.1 Для контроля радиального биения режущих кромок зубьев фрезы предлагается следующее приспособление.
2.2 В корпусе 1 выполнен отверстие в которое помещен упорный подшипник 10 закрепленный в осевом направлении эксцентрическим кольцом 11. В подшипник вставлена оправка 2 на которую и надевается для контроля фреза.
2.3 Оценка биения производится при помощи стандартного индикатора 4 часового типа который закреплен лапкой в держателе 5 таким образом чтобы предельное положение конца рычага индикатора соответствующее нулю отсчета находилось на расстоянии 1001 мм от оси оправки и следовательно контролируемой фрезы. При вращении оправки с фрезой зуб вышедший за пределы допустимой величины биения нажмет на рычаг и индикатор покажет отклонение после чего пометив чем – либо зуб следует нажать на рычаг с тыльной стороны для возвращения его в номинальное положение.
2.4 Держатель 5 перемещается по закаленным и шлифованным направляющим 3 приваренным к корпусу в вертикальном направлении и может фиксироваться в двух положениях посредством шариковых фиксаторов для оценки биения у основания пластин и у вершин зубьев т.е. в двух горизонтальных плоскостях.
1 Анализ опасности поражения электрическим током
1.1 Анализ несчастных случаев на производстве показывает что число травм вызванных электрическим током сравнительно невелико и составляет от 05% до 30% общего числа несчастных случаев. Но при рассмотрении смертельных несчастных случаев оказывается что 20 – 40% их происходит в результате поражения электрическим током. Согласно статистическим данным 75 – 80 % смертельных поражений электрическим током наблюдается в электроустановках напряжением до 1000 В.
Тело человека является проводником электрического тока. Разные ткани человека оказывают току разное сопротивление: кожа кости жировая ткань – большое а мышечная ткань кровь и особенно спинной мозг – малое. Например при токе частотой 50Гц удельное электрическое сопротивление сухой кожи составляет 3*103 – 2*104Ом*м мышечной ткани 15 – 3 Ом*м крови 10 -2 Ом*м. Как видно из этих данных кожа по сравнению с другими тканями обладает очень большим сопротивлением. Поэтому сопротивление тела человека определяется главным образом сопротивлением кожи. Обычно при расчетах сопротивление тела человека принимается равным 1000 Ом.
В действительности это сопротивление – величина переменная нелинейно зависимая от многих факторов в том числе от состояния кожи параметров электрической цепи физиологических факторов и состояния окружающей среды (влажность температура и т.д.).
1.2 Состояние кожи очень сильно влияет на значение электрического сопротивления тела человека. Так повреждение рогового слоя в том числе порезы царапины ссадины и другие микротравмы могут сильно снизить сопротивление тела человека до значения близкого к значению внутреннего сопротивления (300 – 500 Ом) что безусловно увеличивает опасность поражения человека током. Такое же влияние оказывает и увлажнение кожи водой потом смазочно-охлаждающей жидкостью а также загрязнение кожи проводящей пылью и грязью.
Поскольку у одного и того же человека электрическое сопротивление кожи неодинаково на разных участках тела то на сопротивление в целом влияет и место приложения контактов а также их площадь.
Значение тока и длительность через его прохождение через тело человека непосредственно влияет на полное электрическое сопротивление: с ростом тока и времени его прохождения сопротивление падает поскольку при этом усиливается местный нагрев кожи что приводит к расширению ее сосудов а следовательно к усилению снабжения этого участка кровью и увеличению потовыделения.
1.3 Род и частота тока в значительной мере определяют степень поражения. Наиболее опасен переменный ток с частотой от 20 до 1000 Гц. Постоянный ток менее опасен.
Все мероприятия по защите людей от поражения электрическим током выполняются в соответствии с ''Правилами устройства электроустановок'' (ПУЭ) и ''Правилами техники безопасности при эксплуатации электроустановок потребителей.'' (ПТЭ и ПТБ).
Согласно правилам все электроустановки делятся на два класса: с напряжением до и выше 1000 В. В зависимости от класса к которому относится защищаемая проектируемая установка необходимо разрабатывать соответствующие защитные мероприятия и устройства.
1.4 Участок механической обработка является особо опасным помещением по степени опасности поражения электрическим током. На металлических кожухах станков в результате нарушения изоляции может неожиданно появиться напряжение. Опасность усиливается и тем что руки рабочих могут быть увлажнены смазочно-охлаждающей жидкостью в зоне обработки присутствует токопроводящая пыль. Кроме того очень часто на коже рук людей работающих с металлообработкой могут присутствовать порезы ссадины и другие повреждения. Все это в целом безусловно увеличивает опасность поражения электрическим током на проектируемом участке.
Для электробезопасности необходима защита от поражения электрическим током при прикосновении к частям станков не находящимся под напряжением но опасным в случае нарушения изоляции.
В общем случае защита от прикосновения к частям станков находящимся под напряжением сводится к их надежной изоляции применению защитных кожухов и ограждений помещению токоведущих частей в недоступные для прикосновения места защитной блокировке сигнализации опасности.
Защита от поражения при прикосновении к частям станков которые в случае пробоя изоляции оказываются под напряжением обычно достигается защитным заземлением занулением отключением.
Для предотвращения опасности поражения электрическим током на проектируемом участке будем использовать метод защитного заземления.
Защитное заземление – это преднамеренное соединение с землей металлических частей оборудования не находящихся под напряжением но которые могут оказаться под напряжением в результате нарушения изоляции токоведущих частей.
Назначение защитного заземления – устранение опасности поражения электрическим током при появлении напряжения на корпусе оборудования.
Заземляющим устройством называется совокупность заземлителя - металлических проводников находящимся в непосредственном соприкосновении с землей и заземляющих проводников соединяющих заземление части электроустановок с заземлителем.
По расположению заземлителей относительно заземляемых корпусов заземления делятся на выносные и контурные.
При выносном заземлении заземлители сосредоточены за пределами площадки с оборудованием. При контурном заземлении они располагаются по контуру вокруг заземляемого оборудования на расстоянии нескольких метров друг от друга и любая точка поверхности грунта внутри контура имеет значительный потенциал. Вследствие этого разность потенциалов между точками лежащими внутри контура снижена а максимальное значение коэффициентов напряжения прикосновения и шаги обуславливающих степень опасности не превышают допустимых. Ток проходящий через тело человека касающегося корпуса меньше чем при выносном заземлении имеющем большую величину напряжения прикосновения.
2 Расчет контурного защитного заземления
2.1 Из ПУЭ определяем нормированное сопротивления заземляющего устройства.
так как напряжение сети меньше 1000 В и мощность мигающего трансформатора более 100 кВ.
2.2 Выбираем конструкцию отдельных заземлителей – трубы длиной 3 м диаметром 100 мм и глубину их заложения 1 мм.
Вид грунта в котором необходимо установить заземлители песчано-глинистый. Удельное сопротивление грунта ρ=12*102 Ом*м повышающий коэффициент для третьей климатической зоны Кп=15. Тогда расчетное удельное сопротивление грунта
2.3 Определим сопротивление одиночного заземления с учетом выбранных геометрических размеров и найденного расчетного удельного сопротивления грунта по формуле
d – диаметр заземления м;
t – расчетная глубина м.
2.4 Определим ориентировочное число одиночных заземлений nпо формуле
2.5 Разместим одиночные заземлители на плане с расстоянием 4 – 5 метров друг от друга по контуру участка и по справочной таблице определим коэффициент использования одиночных заземлителей .
Уточним число одиночных заземлителей шт.
2.6 Для соединения между собой одиночных заземлителей используем стальную полосу шириной 100 мм толщиной 20 мм. Длина полосы соединения 15 заземлителей составит 90 м.
Сопротивление полосы определим по формуле
t – глубина залегания полосы м.
С учетом коэффициента использования полосы п= 07 ее сопротивление составит
2.7 Найдем сопротивление всего заземления Rз Ом
Пренебрегая малым сопротивлением заземляющих проводников принимаем сопротивление заземляющего устройства Rзу равным сопротивлению заземлителя
Сравнивая полученное значение Rзу=226 Ом с полученными для проектируемого участка сопротивлением заземляющего устройства (Rзу=4 Ом) видим что RзуRзудоп значит сопротивление рассчитано верно.
Таким образом заземляющее устройство для проектируемого участка механической обработки необходимо выполнить из 15 стальных труб диаметром 100 мм длиной 3 м. и глубиной залегания 1 м расположив их по контуру участка на расстоянии 4 – 5 м друг о друга и соединив стальной полосой шириной 100 мм и толщиной 20 мм.
Экономическое обоснование проектирования
1. Организация работы производственного участка по изготовлению изделия ''Фреза двухсторонняя сборная с пластинами ВК8
1.2 Определим такт производства по формуле мин
где - действительный годовой фонд времени работы оборудования r;
N – годовая программа выпуска деталей шт.
1.3 Штучно – калькуляционное время по каждой операции tшт-к мин вычисляем по формуле:
где - штучное время на операцию мин;
- подготовительно – заключительное время на операцию мин;
- оптимальная партия деталей шт.
1.4 Оптимальную партию деталей найдем из выражения:
где nраб – число рабочих дней в году.
Для расчета среднего значения величины штучно – калькуляционного времени воспользуемся таблицей.
Таблица 5.1 – Маршрутно-технологическая карта
Наименование операций
1.5 Определим коэффициент серийности Ксер по формуле
где - такт выпуска деталей мин;
- среднее штучно – калькуляционное время мин.
По полученному значению коэффициента серийности определяем тип производства – мелкосерийное. (Более 20 – мелкосерийное [33].)
1.6 Расчетное количество оборудования Срна участке определим по формуле (для каждой операции)
Принятое количество оборудования Спрполучаем округляя полученное значение Ср до целого числа в большую сторону.
1.7 Коэффициент загрузки оборудования на каждой операции Кз.о. определяем по формуле
Полученные расчетным путем показатели заносим в таблицу.
Таблица 5.2 – Расчет количества оборудования
Т.к. коэффициент загрузки оборудования мал производим дозагрузку оборудования по каждой операции до 95%. Для этого находим следующие показатели:
располагаемые станкочасы
трудоемкость заданной программы
количество станкочасов при Кз.о.=095
Расчет дозагрузки оборудования проводим с помощью таблицы.
Таблицы 5.3 – Дозагрузки оборудования
Спршт по заданной программе
Располагаемые станкочасы
Трудоемкость заданной программы
Количество станков при Кзо=095
Кол-во станкочасов при их дозагрузке гр.4-гр.3
Расчетное Ср при Кз.о.=095гр.4гр.2
Коэф. дозагруз. Обор.
1.8 Определим основную производственную площадь Sосн м2; исходя из выражения
где Sст – площадь занимаемая станками м2;
– количество метров отводимых на проходы и проезды для одного станка м2;
n – количество оборудования шт.
1.9 Для расчета площади занимаемой станками воспользуемся таблицей.
Таблица 5.4 – Определение площади станков
Суммируя полученные данные находим площадь всех станков Sст.=646м2.
Вспомогательную площадь принимаем в размере 30 м2.
Таким образом площадь участка Sуч. м2 находим по формуле
Принимаем площадь участка Sуч.=170 м2.
1.10 Определим стоимость производственной площади участка Сзд руб по формуле
где Сп – стоимость одного квадратного метра площади руб.
1.11 Стоимость оборудования определяем по данным следующей таблицы.
Таблица 5.5 – Расчет стоимости оборудования
Определяем сумму капитальных вложений К руб. по формуле
где Собор – стоимость оборудования руб.
1.12 Рассчитаем численность промышленно - производственного персонала.
Численность основных рабочих Rосн чел занятых выполнением технологического процесса определим по формуле
где Fд – действительный годовой фонд времени работы оборудования ч;
Спр – принятое количество оборудования на участке шт.;
Кз.о. – коэффициент загрузки оборудования %;
Fэф – годовой эффективный фонд времени работающего ч.
Для расчета последнего показателя составим таблицу.
Таблица 5.6 – Годовой фонд времени работающего
Показатели характеризующие бюджет времени
Планируемое время на год
Календарный фонд времени дни
Выходные и праздничные дни
Номинальный фонд времени дни
Планируемые невыходы в среднем на человека в год дни
- дополнительные отпуска и прочие плановые неявки
Среднее число явочных дней
Продолжительность рабочего дня ч
Сокращение рабочего дня по действующему законодательству в среднем на человека в день ч
Средняя продолжительность рабочего дня ч
Эффективный фонд времени работающего ч
1.13 Расчетное число основных рабочих Rосн округляем до целого и получаем принятое число основных рабочих Rосн=24 чел.
Коэффициент загрузки основных рабочих Кз.о.% по каждой операции определяем по формуле
Полученные данные заносим в таблицу.
Таблица 5.7 – Численность и загрузка основных рабочих
Профессии основных рабочих
1.14 Численность вспомогательных рабочих принимаем в размере % от численности основных рабочих.
Принимаем Rвсп=8 чел.
1.15 Численность инженерно – технических работников (ИТР) Rитр чел определяем в размере 10% от численности основных и вспомогательных рабочих Rитр=4 чел.
Полученные расчетным путем данные сводим в таблицу.
Таблица 5.8 – Численность промышленно – производственного персонала
Категории работающих
В том числе по сменам чел.
Вспомогательные рабочие
Средняя численность вспомогательных рабочих определяется в процентном отношении от численности основных рабочих. Размер процента зависит от типа производства. Для массового производства численность вспомогательных рабочих принимается в размере % для крупносерийного – 50% для средне- мелкосерийного и единичного - % от числа основных рабочих.
2. Расчет расценки на изделие и фонда заработной платы
2.1 Расценка на изделие по каждой операции q руб определяется по формуле
tшт-к – штучно – калькуляционное время на операции мин.
Для расчета расценки на изделие производства составляем таблицу.
Таблица 5.9 – Расчет расценки на изделие.
2.2 Определим фонд заработной платы (ФЗП) рабочих состоящий из прямого ФЗП дополнительной заработной платы и премий.
Прямой ФЗП основных рабочих определим по формуле руб.
где q – расценка на изделие руб.
N – годовая программа выпуска шт.
Фонд заработной платы основных рабочих с учетом дозагрузки оборудования 95% ФЗП руб определим по формуле руб.
где 095 – коэффициент загрузки оборудования;
Кз.о.ср – средний расчетный коэффициент загрузки оборудования.
Определим сумму дополнительной заработной платы (ДПЗ) в размере 25% и сумму премий (П) в размере 30% от прямого ФЗП.
ДПЗ'=025 ФЗП'пр.осн=025*4638=11595руб.;(5.18)
ДПЗ=025 ФЗПпр.осн=025*27538125= 6884531руб.;(5.19)
П'=025 ФЗП'пр.осн=03*4638=13914руб.;(5.20)
П=025 ФЗПпр.осн=03*27538125=8261437руб.(5.21)
2.3 Общий фонд заработной платы при среднем коэффициенте загрузки оборудования ФЗП'пр.осн руб. составит
ФЗП'об.осн= ФЗП'пр.осн+ДПЗ'+П'=4638+11595+13914=71889руб.(5.22)
С учетом дозагрузки оборудования до 95% общий ФЗП руб. составит
ФЗПоб.осн=ФЗПпр.осн+ДПЗ+П=27538125+6884531+8261437= 268409руб.(5.23)
Прямой фонд заработной платы вспомогательных рабочих ФЗПпр.всп руб. определим по формуле
ФЗПпр.всп=Rвсп*lr*Fэф=8*52*1860=77376 руб.(5.24)
где Rвсп – численность вспомогательных рабочих чел;
Fэф – эффективный фонд времени рабочего ч.
2.4 Определим сумму ДПЗ и сумму премий вспомогательных рабочих в размере 20% и 25% от прямого фонда заработной платы вспомогательных рабочих соответственно
ФЗПоб.всп=ФЗПпр.всп+ДПЗвсп+Пвсп=77376+154752+19344=112195 руб (5.25)
2.5 Аналогично определяем годовой фонд заработной платы ИТР руб
ФЗПпр.итр=Rитр*lr*Fэф=4*630*1860=46872руб.(5.26)
Сумму дополнительной заработной платы и сумму премий для ИТР определим в размере по 25% от суммы годового фонда заработной платы ИТР.
Питр=ДПЗитр=ФЗПпр.итр*025=46872*025=11718 руб.(5.27)
Общий фонд заработной платы ИТР ФЗПоб.итрруб. определим из выражения
ФЗПоб.итр=ФЗПпр.итр+2(ФЗПпр.итр*025)=46872+2(46872*025)=70308руб.(5.28)
Полученные данные сводим в таблицу.
Таблица 5.10 – Общий фонд заработной платы работающих руб.
Определим среднемесячную заработную плату основного рабочего ЗПосн руб. по формуле
Среднемесячная заработная плата производственного рабочего ЗПпр.р руб. по формуле
Рассчитаем среднемесячную заработную плату всех рабочих ЗПраб. руб. по формуле
3. Расчет себестоимости изделия.
3.1 Определим стоимость материала фрезы Смруб. по формуле
См=Qм*Цм-Q0*Ц0=452*17-390*358=7684-13962=62878руб.(5.32)
где Qм – масса заготовки кг;
Цм – стоимость одного килограмма материала руб.;
Q0 – масса отходов кг;
Ц0 – стоимость одного килограмма отходов руб.
Стоимость пластин Сп руб.
Сп=Цп*n=720*36=2592руб.(5.33)
где Цп – стоимость одной пластины руб.
n – количество пластин шт.
Калькуляцию по расходу себестоимости фрезы ведем при помощи таблицы.
Таблица 5.11 – Калькуляция по расчету себестоимости изделия
Сырье и материала за вычетом отходов
Покупные полуфабрикаты
Транспортно – заготовительные расходы
Основная заработная плата основных рабочих
Дополнительная заработная плата
Начисления на заработную плату
Отчисление на страхование от несчастных случаев и профессиональных заболеваний
Расходы на подготовку и освоение производства
Расходы на содержание и эксплуатацию оборудования
Общепроизводственные расходы
Общехозяйственные расходы
А. Производственная себестоимость
Коммерческие расходы
Б. Полная себестоимость
Оптовая цена (объем реализации)
Рыночная цена (выручка от реализации продукции)
Для расчета оптовой цены технико-экономических показателей и годового экономического эффекта от изготовления проектируемой фрезы необходимо произвести расчет себестоимости изделия по существующему т.е. базовому технологическому процессу.
4 Организация работы производственного участка по базовому варианту
4.1 Программа выпуска NБ=Nср=200 шт.
4.2 Такт выпуска =12045 мин формула (5.1)
Оптимальная партия деталей nопт.Б=nопт.ср=1формула (5.3)
Составим таблицу для расчета штучно – калькуляционного времени на каждую операцию и среднего штучно – калькуляционного времени.
Таблица 5.12 – Маршрутно-технологическая карта мин.
Продолжение таблица 5.12
Коэффициент серийности Ксер=8922 формула (5.4) – производство мелкосерийное.
5 Расчет себестоимости изделия
5.1 Стоимость материала заготовки за вычетом отходов - 2784 руб. смотри формулу (5.32).
Стоимость пластин – 252 руб. смотри формулу (5.33).
Калькуляцию полной себестоимости заносим в таблицу.
Таблица 5.19 – Калькуляция по расчету себестоимости изделия
Сырье и материалы за вычетом отходов
Покупные полуфабрикаты
Дополнительная заработная плата
Начисления на заработную плату (26%+43%)
Расходы на эксплуатацию и содержание оборудования
Технологическая себестоимость
Цеховая себестоимость
Общезаводские расходы
Производственная себестоимость
Внепроизводственные расходы
Полная себестоимость
Продолжение таблицы 5.19
5.2 Определим прибыль ПрБ руб по формуле
где rИБ – уровень рентабельности базового варианта %
СпБ – полная себестоимость базового варианта руб.
Определим оптовую цену изделия Оц руб. по формуле
ОЦ.Б.=Оц.пр=ОПБ+ПрБ=155110+38777=193887 руб.(5.38)
Определим прибыль проектную Прпр руб по формуле
Прпр=ОЦ.Б.-Сппр=193887-146484=47403 руб.(5.39)
Уровень рентабельности изделия в проектном варианте определяется выражением rи %
6 Расчет технико-экономических показателей изготовления проектируемой фрезы.
Рентабельность производства определим по формуле rпр %
где N – годовая программа выпуска шт;
К – сумма капитальных вложений руб.;
ОНС – оборотные нормируемые средства руб.
7 Срок окупаемости определим по формуле Ток лет
8 Фондоотдачу ОПФ λ руб. определим по формуле
Определим приведенные затраты Зпр руб. по формуле
где Ен – нормативный коэффициент экономической эффективности.
9 Рассчитаем годовой экономический эффект от изготовления проектируемой фрезы по проектному варианту технологического процесса Фэк руб. по формуле
Фэк=Зпр.Б-Зпр.пр=260558 руб.(5.45)
Производительность труда определим по формуле Д руб
10 Все рассчитанные данные в разделе показатели сводим в таблицу.
Таблица 5.20 – Технико-экономические показатели изготовления проектируемого инструмента.
Наименование показателя
Проектируемому варианту
Годовой выпуск продукции
Трудоемкость единицы изделия
Трудоемкость годового выпуска изделия
Себестоимость единицы изделия
Прибыль на единицу изделия
Прибыль на годовой объем продукции
Рентабельность изделия
Рентабельность производства
Среднесписочная численность промышленно - производственного персонала
- вспомогательных рабочих
Среднемесячная заработная плата
- основного рабочего
- производственного рабочего
Продолжение таблицы 5.20
Сумма капитальных вложений
- стоимость оборудования
- стоимость производственного здания
Годовой экономический эффект
ВВЕДЕНИЕОШИБКА! ЗАКЛАДКА НЕ ОПРЕДЕЛЕНА.
ТЕХНОЛОГИЧЕСКАЯ ЧАСТЬ2
1 Назначение детали2
Проектируемый инструмент относится к группе режущих инструментов типа фреза. Данный тип инструмента является наиболее распространенным металлорежущим инструментом в машиностроении.2
Разрабатываемый инструмент служит для обработки пазов редукционного корпуса железнодорожных ремонтных машин изготавливаемого из чугуна. Фреза двухсторонняя сборная правого резания обрабатывает пазы корпуса размером 70х15 миллиметров. Для увеличения продолжительности работы инструмента фреза оснащена твердосплавными пластинами марки ВК8 данный тип твердого сплава выбран в соответствии со справочными рекомендациями для данного типа обрабатываемого материала. Крепление твердосплавных пластин к корпусу фрезы осуществляется методом склеивания. Корпус фрезы является базовой деталью проектируемого инструмента с возможностью многократной смены твердосплавных пластин. Он изготавливается из конструкционной стали марки 45 с последующей термообработкой и точной подготовкой посадочных поверхностей под режущие твердосплавные пластины.2
2 Определение типа производства2
3 Анализ технологичности детали4
4 Расчет припусков на обработку7
5 Составление маршрута обработки детали11
6 Выбор оборудования13
7 Разработка операционного процесса обработки.23
ПРОЕКТИРОВАНИЕ ИНСТРУМЕНТА32
1 Выбор способа обработки заданной поверхности32
2 Расчет конструктивных параметров фрезы двухсторонней сборной с пластинами ВК835
3 Прочностной и температурный расчет зубьев.38
4 Клеесборный инструмент41
КОНСТРУКТОРСКАЯ ЧАСТЬ43
1 Конструирование станочного приспособления.43
2 Конструирование контрольного приспособления.44
1 Анализ опасности поражения электрическим током46
2 Расчет контурного защитного заземления49
ЭКОНОМИЧЕСКОЕ ОБОСНОВАНИЕ ПРОЕКТИРОВАНИЯ52
0000.CDW

план участка.cdw

эскиз 060.cdw

Оборудование: внатришлифовальный станок мод. 3А225
эскиз 030.cdw

Оборудование: станок универсально-фрезерный мод. 6Р82
ОЭ ток.cdw

Оборудование: Станок горизонтально-фрезерный с ЧПУ мод. ГФ-2175
схема контурного заземления.cdw

Заземляющие проводники
Соединение элементов заземляющего
устройства с корпусами оборудования и между
Сварные швы по ГОСТ 15164-78-У2-Ш3-
020.CDW

025.CDW

2.CDW

расчет конструктивных параметров фрезы.cdw

2.FRW

3.FRW

расчет хрупкой прочност.frw

Прочностные и температурные характеристики зубьев фрезы.doc
Расчет хрупкой прочности
Условие возможности эксплуатации фрезы
Тепловые явление в зоне резания
Уравнение теплового баланса
Влияние размеров срезаемого слоя на рост температуры
Тех-эк пок изг проек инструм.doc
Годовой выпуск продукции:
-в натуральном выражении
Количество оборудования
Коэффициент загрузки оборудования
Трудоемкость единицы изделия
Трудоемкость годового выпуска изделия
Себестоимость единицы изделий
Прибыль на единицу изделия
Прибыль на годовой объем продукции
Рентабельность изделия
Среднесписочная численность промышленно-производственного персонала
- вспомогательных рабочих
Среднемесячная заработная плата:
- основного рабочего
- производственного рабочего
Сумма капитальных вложений
-стоимость оборудования
- стоимость производственного здания
Годовой экономический эффект
Технико-экономические показатели изготовления проектируемого инструмента
клас спос обраб.cdw

заданной поверхности
Фрезерование торцевой фрезой
Фрезерование специальной фрезой
Фрезерование пазовыми и цилиндрическими фрезами
Фрезерование концевой фрезой
Фрезерование набором фрез
Электроискровое прошивание
корпус.cdw

Накопленная погрешность окружного шага зубьев - не более 0
Неуказанные предельные отклонения размеров отверстий H14
0000.FRW

Расчет конструктивных параметров фрезы двухсторонней сборной.doc
Максимальный диаметр
диаметр посадочного отверстия
Максимальное число зубьев
фреза 2сторон.cdw

Материал режущих пластин ВК8
твердость HRA не менее 87
Материал корпуса Сталь 45
твердость HRC 23-32.
Радиальное биение режущих кромок зубьев - не более 0
Неуказанные предельные отклонения размеров отверстий H14
Неуказанные предельные
Маркировать диаметр и число зубьев
Рекомендуемые чертежи
- 24.01.2023
- 01.07.2014