Разработка технологического процесса изготовления детали корпус




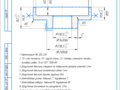
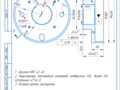
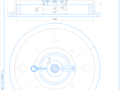
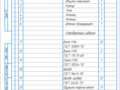
- Добавлен: 24.01.2023
- Размер: 4 MB
- Закачек: 2
Описание
Состав проекта
![]() |
![]() |
![]() ![]() ![]() ![]() |
![]() |
![]() ![]() ![]() ![]() |
![]() ![]() ![]() ![]() |
![]() ![]() ![]() ![]() |
![]() ![]() ![]() |
![]() ![]() ![]() ![]() |
![]() ![]() ![]() ![]() |
![]() |
![]() |
![]() ![]() ![]() |
![]() ![]() ![]() |
![]() ![]() ![]() |
![]() ![]() ![]() |
![]() ![]() ![]() |
![]() ![]() ![]() |
![]() ![]() ![]() |
![]() ![]() ![]() |
![]() |
![]() ![]() ![]() |
![]() ![]() ![]() |
![]() ![]() ![]() |
![]() |
![]() ![]() ![]() ![]() |
![]() ![]() ![]() ![]() |
![]() ![]() ![]() ![]() |
![]() ![]() ![]() ![]() |
![]() ![]() ![]() ![]() |
![]() ![]() ![]() ![]() |
![]() ![]() ![]() ![]() |
![]() ![]() ![]() ![]() |
![]() ![]() ![]() ![]() |
Дополнительная информация
Чертеж заготовки.cdw

С2- степень сложности паковки
виходной индекс 15 по ГОСТ 7505-89.
Допустимая величина смещения по поверхности разъема штампов 1
Допустимая величина остаточного облоя 1
Допустимая величина высоты заусенца 8мм.
Штампованые уклоны: внешние 2
Штампованые радиусы: внешние R5
Допустимые отклонения по изогнутости 1
Другие технические требования по ГОСТ 8479-70.
ПК 8.050.050.201.11.727.002
Вертикально-фрезерная с ЧПУ.cdw

Втулка HSK A63 МТ3х140
Втулка HSK A62 МТ3х120
Сверло 2301-3578 Р6М5
Сверло 2301-3602 Р6М5
Сверло 2301-3674 Р6М5
Сверло 2301-3672 Р6М5
Зенкер 2320-2599 Р6М5
Развертка 2363-3482 Р6М5
Развертка 2363-0652 Р6М5
Циковка 2350-0708 Р6М5
Фреза 2223-0147 Р6М5
Приспособление специальное
вертикально-фрезерную
Модель станка МА655ВС1
ПК 8.050.050.201.11.727.020
Токарная с ЧПУ.cdw

ТУ РБ 00223728.049-99
Резец S25Q-SSKCR Т5К10
Модель станка АТ-450ПН
ПК 8.050.050.201.11.727.010
Условные обозначения:
- ускоренное движение;
Круглошлифовальная.cdw

* - Размер для справок.
ПК 8.050.050.201.11.727.030
Пояснительная записка.docx
МОЛОДЕЖИ И СПОРТА УКРАИНЫ
ДОНЕЦКИЙ НАЦИОНАЛЬНЫЙ ТЕХНИЧЕСКИЙ УНИВЕРСИТЕТ
факультет инженерной механики и машиностроения
кафедра: «Технология машиностроения»
«Технология автоматизированного производства»
ПК 8.050.201.11.727.000 ПЗ
ст. гр. ТМ-11мЕрмоленко А.С.
консультантГолубов Н.В.
нормоконтролерБуленков Е.А.
Курсовой проект: 39 стр. 11 рис. 5 табл. 15 источников.
Объект исследования: технологический процесс специальное станочное приспособление для обработки пазов детали; специальное контрольное приспособление для измерения торцевого биения корпуса относительно оси детали.
Цель проекта: разработать технологический процесс изготовления детали обеспечивающий заданное качество изделия при минимальной себестоимости в заданных организационно-технологических условиях производства; спроектировать специальное станочное приспособление для обработки пазов шириной 30мм которое позволит получить необходимый размер в пределах установленного допуска; спроектировать специальное контрольное приспособление для измерения торцевого биения корпуса относительно оси детали которое позволит получить достоверный результат измерения в пределах установленного допуска.
В курсовом проекте произведен анализ технологичности конструкции детали произведены расчет усилия закрепления расчет параметров силового привода расчет деталей приспособления на прочность расчет погрешности установки заготовки в приспособление для механической обработки и в приспособление для контроля торцевого биения; выбран метод получения заготовки; спроектирован маршрутный и операционный технологический процессы механической обработки детали; сформулировано служебное назначение станочного и контрольного приспособления разработана их принципиальная схема; описаны принципы работы и конструкции приспособлений; выполнены чертеж заготовки детали карты наладки а также сборочный чертеж станочного и контрольного приспособлений.
АНАЛИЗ ТЕХНОЛОГИЧНОСТИ РЕЖУЩИЙ ИНСТРУМЕНТ ТЕХНОЛОГИЧНОСТЬ ЗАГОТОВКА ТЕХНОЛОГИЧЕСКИЙ ПРОЦЕСС ПРИСПОСОБЛЕНИЕ РЕЖИМЫ РЕЗАНИЯ УСИЛИЯ ЗАКРЕПЛЕНИЯ ПРИВОД.
1 Анализ технологичности конструкции детали. Выполнение чертежа детали . 5
2Определение типа производства 6
ТЕХНОЛОГИЧЕСКАЯ ЧАСТЬ 7
1 Выбор метода получения заготовки ..7
2Разработка маршрутного технологического процесса .8
3 Определение припусков на механическую обработку 11
4Определение размеров заготовки. Выполнение чертежа заготовки.. .13
5Анализ и выбор схем базирования заготовки 14
6 Обоснование и выбор технологического оборудования .17
7Обоснование и выбор технологической оснастки 19
8 Расчет режимов резания .20
9 Нормирование технологического процесса ..24
КОНСТРУКТОРСКАЯ ЧАСТЬ .27
1 Проектирование специального приспособления .27
1.1 Расчет усилия закрепления ..27
1.2 Расчет параметров привода .29
1.3Прочностной расчет элементов приспособления 30
1.4 Описание конструкции и принципа действия приспособления ..30
1.5Расчет приспособления на точность 32
2 Проектирование контрольного приспособления .32
2.1 Выбор схемы контроля 33
2.2 Описание работы приспособления 33
2.3 Расчет погрешности измерения .35
ПЕРЕЧЕНЬ ССЫЛОК ..37
Курсовой проект по технологии автоматизированного производства является самостоятельной работой студентов и его роль – систематизировать и укрепить знания полученные студентами при изучении специальных смежных дисциплин.
Основной целью курсового проекта является разработка технологического процесса обеспечивающего заданное качество изделия при минимальной себестоимости в заданных организационно-технологических условиях производства станочного приспособления и контрольного приспособления.
1Анализ технологичности конструкции детали. Выполнение чертежа детали.
Рассмотренная деталь “Корпус” типа диск. Максимальные габариты детали: длина детали 145мм диаметр 400мм. . На чертеже присутствуют все разрезы и сечения для понимания конструкции детали кроме сечения отверстия 1015.
На чертеже найдены ошибки и неточности. На разрезе с боку вместо основой линии должна быть осевая также в разрезе паза не указаны осевые линии. Устаревшая простановка шероховатости. Не правильный ГОСТ материала.
Для изготовления детали используется сталь 40Х ГОСТ 4543-78 – сталь конструкционная легированная. Химический состав: углерода 04% хрома до 1% остальное железо и вредные примеси (сера фосфор). Механические свойства: придел кратковременной прочности 1100МПа; придел текучести 900Мпа; относительное удлинение 12%; относительное сужение 40%; ударная вязкость (КСU): 750кДжм2; твердость НВ 200..220. Химический состав и механические свойства позволяют применять получение заготовки методом горячей объемной штамповки. Сталь этого класса обрабатывается удовлетворительно допустимо применять повышенные режимы резания.
Шероховатость поверхностей детали соответствует квалитету всех размеров. Удовлетворительная простановка размеров обеспечивает настройку станка по методу автоматического получения размеров.
Деталь подвергается ТО закалке НRC 42 45. При изготовлении детали применяется стандартное технологическое оснащение и режущий измерительный инструменты.
Удаление стружки из зоны резания обеспечено удовлетворительно. Имеется хороший доступ ко всем поверхностям измерительным инструментом.
В конструкции детали присутствуют не технологические элементы фрезерование закрытого паза вызывает затруднение при изготовлении необходимо сверлить отверстие а затем фрезеровать паз концевой фрезой. Конструкторской базой является ось детали. Технологическими базами являются торцы детали и внутренний и внешний диаметр. К левому торцу необходимо выполнить требования это допуск торцевого биения не более 005мм относительно к оси детали что является вполне выполнимо. Принцип совмещения баз выполняется измерительная база совпадает с технологической и конструкторской.
В общем виде деталь технологична не смотря на некоторые не точности ошибки и не технологические элементы.
2Определение типа производства.
Тип производства определяем согласно массе детали и годовой программе выпуска.
При массе детали и годовой программе выпуска изделий определяем что тип производства – крупносерийный.
Серийное производство является наиболее распространенным типом производства. На машиностроительных предприятиях серийного типа изготовляется достаточно большая номенклатура изделий хотя и более ограниченная чем в единичном производстве. Часть изделий являются родственными по конструктивно-технологическим признакам.
Другим признаком серийного производства является повторяемость выпуска изделий. Это позволяет организовать выпуск продукции более или менее ритмично.
Выпуск изделий в больших или относительно больших количествах позволяет проводить значительную унификацию выпускаемых изделий и технологических процессов; изготовлять стандартные или нормализованные детали входящие в конструктивные ряды большими партиями что уменьшает их себестоимость.
Относительно большие размеры программ выпуска однотипных изделий стабильность конструкции унификация деталей позволяют использовать для их изготовления наряду с универсальным специальное высокопроизводительное оборудование и специальную оснастку.
Поскольку в серийном производстве выпуск изделий повторяется экономически целесообразно разрабатывать технологические процессы обработки и сборки детально; представлять каждую операцию в виде переходов; устанавливать режимы обработки точные названия станков и специальной оснастки и технические нормы времени.
Организация труда в серийном производстве отличается высокой специализацией. За каждым рабочим местом закрепляется выполнение нескольких определенных деталей операций. Это позволяет рабочему хорошо освоить инструмент приспособления и весь процесс обработки.
Так как в серийном производстве применяется большое количество сложного оборудования и специальной оснастки наладка оборудования осуществляется специальными рабочими-наладчиками.
Особенности серийного производства обусловливают экономическую целесообразность выпуска продукции по циклически повторяющемуся графику. При этом возникают необходимые условия для установления строгого порядка чередования изделий в цехах на производственных участках и рабочих местах.
ТЕХНОЛОГИЧЕСКАЯ ЧАСТЬ
1Выбор метода получения заготовки
Существуют следующие способы получения заготовок: из проката методом пластической деформации литьем и сваркой.
Так как материал детали – легированная конструкционная сталь 40Х то отлить или сварить мы ее не сможем.
Так как максимальный диаметр заготовки – 400 мм а максимальный диаметр проката – 200 250 мм то данную деталь мы не сможем получить из проката.
Таким образом метод получения заготовки – метод пластической деформации а именно – штамповка в закрытых штампах на горячештамповочных автоматах.
Мп.р - расчетная масса поковки кг;
Мд – масса детали кг;
Кр - расчетный коэффициент установленный в соотношении с приложением [15].
Мп.р = 385·15 = 5775 (кг).
Определяем класс точности поковки.
Учитывая что поковку получаем на горячештамповочном автомате определяем класс точности – Т3 [15].
Определяем группу стали40Х ГОСТ 4543-78.
Средняя массовая доля углерода в стали 40Х составляет 04% и до 1% хрома. Группа стали М2 [15].
Определяем степень сложности.
где Мфиг - масса фигуры в которую вписано поковку кг.
где ρ – плотность стали 40Х гсм3 ρ =78 гсм3
V – объем фигуры в которую вписано поковку см3.
где Dфиг - диаметр фигуры см;
Lфиг – длина фигуры см.
Dфиг= Dдет *105= 40*105=42 (см).
Lфиг = Lдет *105=145*105= 152(см).
Так как полученное значение С=035 то принимаем степень сложности С2 [15].
Определяем конфигурацию поверхности разъединения штампа.
Принимаем поверхность разъема штампа П – плоская.
Определяем выходной индекс.
Для Мп.р. =5775 кг М2 С2Т3 выходной индекс – 15 [15].
Определение коэффициента использования материала:
2 Разработка маршрутного технологического процесса
В таблице 1 указаны точность и шероховатость обрабатываемых поверхностей на каждом переходе каждой операции.
Таблица 1 - Технологические переходы для обеспечения качества поверхностей
Точность поверхности (размер допускаемые отклонения точность формы точность относительного положения)
Шероховатость поверхности Ra мкм.
Точность выполнения перехода
Шероховатость обработанной поверхности Ra мкм.
Развертывание черновое
Развертывание чистовое
Рисунок 1 – Чертеж детали с нумерацией поверхностей
Маршрутный технологический процесс обработки детали типа диск:
5Заготовительная (штамповка на ГША)
0Токарная с ЧПУ (станок: токарный с ЧПУ; приспособление: механизированный клиновый трех кулачковый патрон; режущий инструмент: контурный резец расточной резец; измерительный инструмент: ШЦ слесарная линейка; базы: диаметр 210h8 упор в левый торец)
А. Установить и снять заготовку
Подрезать правый торец точить 400 последовательно по программе.
Расточить торец 140Н6380 по программе.
Расточить 380 фаску 2х45° 140Н6 последовательно по программе.
5Токарная с ЧПУ (станок: токарный с ЧПУ; приспособление: механизированный клиновый трех кулачковый патрон; режущий инструмент: два контурных резца расточной резец; измерительный инструмент: ШЦ слесарная линейка; базы: диаметр 380 упор в правый торец)
Подрезать левый торец торец 400210 последовательно по программе.
Точить 210h8 по программе.
Расточить фаску 2х45° 140Н6 последовательно по программе.
Подрезать левый торец точить фаску 2х45°210h8 галтель R3 фаску 2х45° последовательно по программе.
0 Вертикально-фрезерная с ЧПУ(станок: вертикально-фрезерный с ЧПУ; приспособление: специальное; режущий инструмент: сверло 10 сверло 15 сверло 30 сверло 28 зенкер 29 развертка черновая 296 развертка чистовая 30 концевая фреза 30; цековка 15; измерительный инструмент: калибр пробка ШЦ; базы: диаметр 140Н6 упор в левый торец)
Сверлить 4 отв. 10 на R125 последовательно по программе.
Сверлить 2 отв. 15 на R170 2 отв. 15 на R140 последовательно по программе.
Рассверлить 2 отверстия 30 на R170 последовательно по программе.
Фрезеровать 2 паза последовательно по программе.
Рассверлить 2 отверстия 29 на R140 последовательно по программе.
Зенкеровать 2 отв. 297 на R140 последовательно по программе.
Развернуть 2 отверстия 299 на R140 последовательно по программе.
Развернуть 2 отверстия 30 на R140 последовательно по программе.
Цековать 4 отв. 15на R125 последовательно по программе.
5 Термическая (закалка HRC 42 45 термопечь)
0 Внутришлифовальная (станок: внутришлифовальный; приспособление: мембранный патрон; режущий инструмент: шлифовальная головка (черновая); измерительный инструмент: калибр пробка; базы: 210h8 упор в левый торец)
Шлифовать 140Н6 предварительно на проход.
5 Круглошлифовальная (станок: круглошлифовальный; приспособление: оправка с тарельчатыми пружинами; режущий инструмент: шлифовальный круг; измерительный инструмент: калибр скоба; базы: 140Н6 упор в правый торец)
0 Внутришлифовальная (станок: внутришлифовальный; приспособление: мембранный патрон; режущий инструмент: шлифовальная головка (чистовая); измерительный инструмент: калибр пробка; базы: 210h8 упор в левый торец)
Шлифовать 140Н6 на проход.
5 Моечная (моечная машина)
Промыть деталь в 2х % растворе кальцинированной соды при t=80..90°С. Сушить деталь.
0 Технический контроль(поверочная плита)
3Определение припусков на механическую обработку
Таблица 2 - Припуски и операционные размеры для поверхностей 140Н6 210h8
Технологический переход
Элементы припуска мкм
Расчетный операц. р-р мм
Расчетный р-р припуска мм
Шлифование (чистов.)
Определение припуска на размеры 140Н6 210h8:
- шероховатость и глубина дифектов полученных на приведенной обработки;
- погрешность формы взаимного расположения поверхностей полученных на приведенной обработки;
- погрешность установки на текущей технологической операции.
Черновое шлифование:
Чистовое шлифование:
Качество поверхности достигаемая при штамповке:
Rz=320мкм; h=350мкм [4].
Отклонения расположения поверхности штамповки:
где Δсм.шт.=2000 – отклонение от концентричности мкм; [4]
Δкароб.=700 – коробление штампов мкм; [4]
Для последующих механических обработок ΔΣ определяется через коэффициент уточнения [4]:
Δчер.точ.= ΔΣзаг· kyчер.=2119·006=12714мкм;
Δчист.точ.= Δчер.· kyчист.=12714·004=508мкм;
Δшлиф.чер= Δчист.· kyшлиф. чер.=508·003=0152мкм;
Δшлиф. чист= Δшлиф.чер.· kyшлиф. чист.=0152·002=0003мкм.
Погрешность установки[4]:
учер.точ.=500 мкм; учист.точ.=80мкм; ушлиф.чер.=30мкм; ушлиф.чис=20мкм.
Операционные размеры для 140Н6:
Ачер.шл.=140-01-0063=139837мм;
Ачис.рас.=139837-016-016=139517мм;
Ачер.рас.=139517-045-04=138617мм;
Азаг.=138617-5694-24=130523мм.
Операционные размеры для 210h8:
Ачис.точ.=210+016+0185=210345мм;
Ачер.точ.=210345+045+046=211305мм;
Азаг.=211305+5694+13=218299мм.
4 Определение размеров заготовки
По исходному индексу и номинальным поверхностям детали назначаем припуски и допуски на размеры заготовки и сводим их в таблицу 3.
Таблица 3 - Припуски и допуски на изготовление заготовки.
Размер поверхности мм
Припуск на сторону мм
Дополнительный припуск мм
Общий припуск на размер мм
Размер заготовки с допуском
Дополнительный припуск на смещение по поверхности разъема штампа 05мм [15].
Дополнительный припуск на вогнутость и отклонение от плоскостности 05мм [15].
Величина радиусов скругления: внутренние R=5мм внешние R=5мм.
Величина штамповочных уклонов: внутренние1º внешние 2º.
Рисунок 2 – Эскиз заготовки
5 Анализ и выбор схем базирования заготовки
При механической обработке заготовок на станках базированием называется придание заготовки требуемого положения относительно элементов станка и приспособления которое определяет траекторию движения режущего инструмента при обработке. Схемы базирования детали в процессе обработки показаны на рисунках 3-7.
Рисунок 3 – Схема базирования и закрепления на операцию
Рисунок 4 – Схема базирования и закрепления на операцию
Рисунок 5 - Схема базирования и закрепления на операцию
0 Вертикально-фрезерную с ЧПУ
Рисунок 6 - Схема базирования и закрепления на операцию
5 Круглошлифовальная
Рисунок 7 - Схема базирования и закрепления на операции
0 040 Внутришлифовальные
6 Обоснование и выбор технологического оборудования
Оборудование выбираем по следующим критериям: метод обработки точность обработки шероховатость расположение и размеры обрабатываемой поверхности или габаритные размеры детали а также тип производства.
Для обработки наружных и внутренних цилиндрических а также торцовых поверхностей выбираю токарный станок с ЧПУ модели АТ-450ПН:
Класс точности по ГОСТ8-82 П
Наибольший диаметр устанавливаемого изделия мм:
- над суппортом 450
Наибольшая длина устанавливаемого изделия мм 600
Пределы рабочих продольных и поперечных
подач мммин. 1-10000
Ускоренное продольное и поперечное
перемещение мммин. 10000
Мощность приводов подач кВт:
Мощность привода главного движения кВт 37
Пределы частот вращения шпинделя обмин. 6-1400
Количество диапазонов чисел оборотов шпинделя 4
Количество инструментов 17
Габаритные размеры станка мм:
Для получения отверстий и пазов в детали выбираю вертикально-фрезерный станок с ЧПУ модели МА655ИС1:
Класс точности по ГОСТ8-82 Н
Размеры рабочей поверхности основного стола мм:
Расстояние от торца шпинделя до поверхности основного
Частота вращения электрошпинделя обмин:
- максимальная 18000
Мощность электрошпинделя кВт 195
Количество инструментов в магазине 12
Для окончательной обработки цилиндрической поверхности 210h8 принимаю круглошлифовальный станок модели 3М174:
Наибольшие размеры устанавливаемого изделия мм:
Наибольшие размеры шлифовального круга мм 750х80х305
Скорость резания мс 50
Диапазон скоростей перемещения стола ммин 005-50
Диапазон частот вращения обрабатываемой
диапазон автоматических подач шлифовального
Тонкая толчковая подача мм 0001
Наибольшая величина врезания мм 09
Угол поворота верхнего стола:
по часовой стрелке 2°
против часовой стрелки 5°
Наибольшая масса устанавливаемой детали кг 1000
(с отдельно расположенным оборудованием) мм 6710х3690х2135
Для окончательной обработки отверстия 140Н6 принимаю внутришлифовальный станок модели 3К228А:
Диаметр шлифуемого отверстия наибольший мм 400
Наибольшая длина шлифования при наибольшем
диаметре шлифуемого отверстия мм 320
Наибольшая рекомендуемая длина шлифования
при наименьшем диаметре отверстия мм 125
Наибольший наружный диаметр устанавливаемого
изделия без кожуха в кожухе мм 560 400
Наибольший угол шлифуемого конуса град. 60
Расстояние от оси шпинделя изделия до зеркала
Наибольшее расстояние от торца нового круга
торцешлифовального приспособления
до опорного торца шпинделя изделия мм 400
Мощность привода главного движения кВт 7.5
Суммарная мощность электродвигателей кВт 14.63
Габариты станка: длина-ширина-высота мм 3535х1460х1870
Общая площадь пола станка с выносным
Показатель точности обработки образца изделия:
постоянство диаметра в продольном сечении мкм 3
Шероховатость поверхности образца-изделия:
цилиндрической внутренней Ra мкм 0.08
плоской торцевой 0.32
7 Обоснование и выбор технологической оснастки
Для каждой операции была выбрана технологическая оснастка. Критерии выбора технологической оснастки габариты заготовки тип обработки и др. Технологическая оснастка на каждую операцию показана в таблице 4.
Таблица 4 - Ведомость технологической оснастки
Измерительный инструмент
Резец MTJNR2525M16 T5K10 ТУ РБ 00223728.049-99;
Резец S25Q-SSKCR T5K10 ГОСТ 26613-85.
Патрон токарный 3-х кулачковый клиновый механизированный 7102-0070У
ШЦ--500-01 ГОСТ 166-80;
Линейка слесарная ГОСТ 427-75.
Резец PDJNR2525M15 Т15К6 ТУ РБ 00223728.049-99;
Резец S25Q-SSKCR T15K6 ГОСТ 26613-85.
Патрон токарный 3-х кулачковый клиновый механизированный 7102-0080У
Вертикально-фрезерная с ЧПУ
Сверло 2301-3578 Р6М5 ГОСТ 10903-77;
Сверло 2301-3602 Р6М5 ГОСТ 10903-77;
Сверло 2301-3669 Р6М5 ГОСТ 10903-77;
Сверло 2301-3674 Р6М5 ГОСТ 10903-77;
Зенкер 2320-2599 Р6М5 ГОСТ 12489-71;
Развертка 2363-3482 Р6М5 ГОСТ 1672-80;
Развертка 2363-0652 Р6М5 ГОСТ 1672-80;
Фреза 2223-0147 Р6М5 ГОСТ 17026-71.
Цековка 2350-0708 ГОСТ 26258-87
Приспособление специальное;
Втулка HSK A 63 MT3
Втулка HSK A 63 MT1 X 110;
Втулка HSK A 63 MT2 x 120: 2.
Калібр пробка 8133-0922 Н7 ГОСТ 14810-69.
Головка AW 40х60 24А 25-Н СТ1 6К А 35мс ГОСТ 2447-82.
Патрон мембранный ГОСТ 16157-70.
Калибр пробка Н8 ГОСТ 21401-75.
Круг 23350х127х50 25А СМ2 24Н 6К 35мс ГОСТ2424-83.
Оправка с тарельчатыми пружинами.
МК 250-1 ГОСТ 6507-90
Головка AW 40х60 25А 24-Н С1 5К А 35мс ГОСТ 2447-82.
Калибр пробка Н6 ГОСТ 21401-75.
На токарную операцию с ЧПУ выбираем патрон токарный 3-х кулачковый клиновый механизированный так как необходимо на стадии обработки совместить ось патрона (шпинделя) и ось заготовки (совместить технологическую и конструкторскую базы). Механизированный привод позволит значительно сократить вспомогательное время на установку заготовки и обеспечит малую погрешность.
На вертикально-фрезерной операции с ЧПУ выбираем специальное приспособления которое будет базироваться по внутреннему отверстию и центрировать заготовку по оси.
На внутришлифовальные операции для закрепления заготовки выбираем мембранный патрон. Он обеспечивает точное центрирование заготовки с базовой поверхностью. Конструкция патронов при зажиме или раскреплении должна предусматривать сохранение упругой деформации под действием сил приложенных к зажимающей части. В противном случае при пережиме мембраны может возникнуть остаточная деформация вызывающая потерю точности центрирования. Погрешность обработки не превышает 001 -003мм.
На круглошлифовальную операцию для закрепления заготовки выбираем оправку с тарельчатыми пружинами. Приводится в действие пневматическим приводом к которому она присоединяется тягой. Оправка вставляется коническим хвостом в гнездо шпинделя. Гайка навертывается на головку шпинделя и используется для закрепления и удаления оправки из гнезда. Тарельчатые пружины центрируются на корпусе оправки и упираются в шайбу. При движении тяги справа налево деталь установленная своей ступицей в отверстии корпуса оправки нажимает грибовидной головкой на пружины которые сплющиваясь увеличиваются в диаметре настолько что деталь прочно закрепляется на оправке. При обратном движении тяги пружины под влиянием сил упругости принимают свою первоначальную форму и деталь может быть снята. Время затрачиваемое на установку и снятие детали составляет около 013 мин. при точности центрирования до 005 мм.
8 Расчет режимов резания
Рассчитываем режимы резания на один из переходов который наиболее нагруженный на операцию 010 токарную с ЧПУ и операцию 020 вертикально-фрезерную с ЧПУ. Для расчетов режимов резания используем литературу: [4].
Расчет режимов резания на операцию 010 токарную с ЧПУ
Данная операция состоит из трех переходов. Рассмотрим режимы резания на первый переход. Этот переход будет являться лимитирующим переходом для данной операции (так как силы возникающие при резании будут наибольшими по сравнению с остальными переходами).
При назначении элементов режимов резания учитывают характер обработки тип и размеры инструмента материал его режущей части материал и состояние заготовки тип и состояние оборудования.
Сравним полученную мощность с паспортной мощностью станка. Для токарного станка с ЧПУ модели АТ-450ПН мощность главного электродвигателя N = 37 кВт.
Инструмент: Резец MTJNR2525M16 T5K10 ТУ РБ 00223728.049-99;
Глубина резания: t=4мм;
где Сv y m х– коэффициенты и показатели степени [4] Сv=340
Т=30 мин [4] период стойкости инструмента.
Кv=Kmv·Kпv·Kиv=125·08·1=1
Коэффициент на обрабатываемый материал [4]:
Коэффициент на инструментальный материал [4]: Kuv=1
Коэффициент учитывающий глубину резания [4]: Kпv=08
в=570МПа – придел прочности стали 40Х.
где х; y; n – коэффициенты и показатели степени для
тангенциальной силы [4] Cp=300; х=1; y=075; n=-015.
Коэффициент учитывающий фактические условия обработки[4]:
где - поправочный коэффициент
учитывающий влияние качества обрабатываемого материала на
силовые зависимости;
Кφр=089 – поправочный коэффициент учитывающий геометрию
режущего инструмента главный угол в плане;
Кγр=1 – поправочный коэффициент учитывающий геометрию
режущего инструмента передний угол;
Кλр=1 – поправочный коэффициент учитывающий геометрию
режущего инструмента угол наклона лезвия;
Кrр=1 – поправочный коэффициент учитывающий геометрию
режущего инструмента радиус при вершине.
Частота вращения шпинделя [4]:
n=1000VD=1000·126314·400=1003обмин
Принимаем: 100обмин.
Мощность резания [4]:
Расчет режимов резания на операцию 020 вертикально-фрезерную с ЧПУ.
Данная операция состоит из восьми переходов. Рассмотрим режимы резания на четвертый переход. Этот переход будет являться лимитирующим переходом для данной операции (так как силы возникающие при резании будут наибольшими по сравнению с остальными переходами).
Сравним полученную мощность с паспортной мощностью станка. Для вертикально-фрезерного станка с ЧПУ модели МА655ВС1 мощность главного электродвигателя N = 195 кВт.
Инструмент: Фреза 2223-0147 Р6М5 ГОСТ 17026-71;
Глубина резания: t=30мм;
где Ср=465 q=045 u=01 p=01 y=05 m=033 х=05
[4] – коэффициенты и показатели степени.
Т=90 мин [4] период стойкости инструмента.
Кv=Kmv·Kпv·Kиv=128·1·065=083
Коэффициент на инструментальный материал [4]:
Коэффициент учитывающий глубину резания [4]:
в=570МПа – придел прочности стали 40Х
где Cp=682; х=086; y=072; u=1; q=086; w=0 [4] - коэффициенты и
показатели степени для окружной силы при фрезеровании.
Коэффициент учитывающий влияние качества обрабатываемого материала на силовые зависимости [4]:
где D – диаметр фрезы мм.
n=1000VD=1000·216314·30=2293обмин
Принимаем: 220обмин.
Режимы резания на все переходы операций технологического процесса показаны в таблице 5.
Таблица 5 – Режимы резания
Подрезать правый торец точить 400
Расточить торец 140H6 380
Расточить 380 фаску 2х45°
Подрезать левый торец
Расточить фаску 2х45° 140Н6
точить фаску 2х45° 210h8 галтель R3 фаску 2х45°
Сверлить 4 отв. 10 на R125
Сверлить 2 отв. 15 на R150
Рассверлить 2 отв. 30 R170
Рассверлить 2 отв. 29 R140
Зенкеровать 2 отв. 297 R140
Развернуть 2 отв. 299 R140
Развернуть 2 отв. 30Н7 R140
Цековать 4 отв. 15 на R125
9 Нормирование технологического процесса
Особенностью нормирования операций механической обработки деталей на станках с ЧПУ является то что основное время и время связанное с переходом составляют единую величину - время автоматической работы станка по программе составленной технологом-программистом которое складывается из основного времени автоматической работы станка и вспомогательного времени работы станка по программе т.е.:
где - длина пути проходимого инструментом или деталью в
направлении подачи при обработке -го технологического участка;
- минутная подача на данном участке;
- число технологических участков обработки;
- время на выполнение автоматических вспомогательных ходов;
- время технологических пауз.
Время вспомогательной ручной работы не перекрываемое временем автоматической работы станка:
где - вспомогательное время на установку и снятие детали;
- вспомогательное время связанное с выполнением операции;
- вспомогательное непрерывное время на контрольные
После расчета производят его корректировку в зависимости от серийности производства. Поправочный коэффициент:
где - число обрабатываемых деталей в партии запуска.
Подготовительно-заключительное время определяется так:
где - поправочные коэффициенты;
- число инструментов в наладке;
- число управляемых исходных режимов работы станка;
- число размеров набираемых переключателем на пультах
Время вспомогательной ручной работы не перекрываемое временем автоматической работы станка корректируем с учетом поправочного коэффициента – коэффициента серийности:
Тогда норма штучного времени равна:
Пронормируем операцию 010 токарную с ЧПУ.
где - длина подвода и отвода инструмента к зоне обработки;
=10000 мммин - ускоренное продольное и поперечное
перемещение (паспортные данные станка модели АТ-450ПН).
где Dn – диаметр поверхности по которой крепится деталь мм;
- число корректоров в программе;
- длина пленки – носителя программы.
где - поправочный коэффициент [7];
- показатели степени [7];
- диаметр или ширина измеряемой поверхности;
- длина измеряемой поверхности.
где - поправочные коэффициенты [7];
- число размеров набираемых переключателем на пультах станка.
Поправочный коэффициент:
где от оперативного времени.
КОНСТРУКТОРСКАЯ ЧАСТЬ
1Проектирование специального приспособления
Данное станочное приспособление проектируется для вертикально-фрезерной операции с ЧПУ а именно для обработки пазов. Данное приспособление должно обеспечить точность получаемых размеров. Деталь устанавливается на оправку с тарельчатыми пружинами по отверстию 140Н6 и левому торцу. Закрепляется заготовка с помощью деформации тарельчатых пружин усилие закрепления создает гидроцилиндром.
1.1Расчет усилия закрепления
При расчете режимов резания была найдена сила резания:
Пользуясь [4] определяем остальные составляющие силы резания. Для встречного фрезерования:
Значение коэффициента надежности К следует выбирать дифференцированно в зависимости от конкретных условий выполнения операции и способа закрепления заготовки. Его величину можно представить как произведение частных коэффициентов каждый из которых отражает влияние определенного фактора:
- гарантированный коэффициент запаса надежности закрепления;
- коэффициент учитывающий увеличение силы резания из-за случайных неровностей на заготовке (для чистовой обработки );
- коэффициент увеличение силы резания вследствие затупления инструмента (для материала инструмента Р6М5 - );
- коэффициент учитывающий увеличение силы резания при прерывном резании;
- коэффициент учитывающий непостоянство зажимного усилия (для гидропривода );
- коэффициент учитывающий удобство расположения рукояток при ручном закреплении заготовок (для механизированных приводов );
- коэффициент учитывающий неопределенность контакта заготовки с установочными элементами (для опорного элемента с большой площадью контакта ).
Тогда коэффициент надежности равен:
Рисунок 8 - Расчетная схема для определения усилий закрепления
Для схемы приведенной на рис. 8 описание действия сил может быть следующим. При фрезеровании со стороны инструмента на заготовку воздействуют вертикальная и горизонтальная составляющие силы резания а также составляющая силы резания .
Сила пытается сдвинуть заготовку в право этому препятствует сила закрепления Q. Сила создает крутящий момент с плечом l1 ей противодействует момент силы трения Fтр с плечом l2. Сила пытается провернуть заготовку относительно точки О и создает крутящий момент с плечом l4 ей противодействует момент сил трения Fтр' с плечом l3.
Для схемы приведенной на рис.8 уравнения равновесия заготовки под действием усилий резания будут иметь вид:
где – коэффициент трения =016;
К – коэффициент запаса прочности приспособления К=35.
Суммарное усилие закрепления определяется как геометрическая сумма :
1.2Расчет параметров привода
где – угол наклона тарельчатой пружины =12°.
где W0 – усилие создаваемое одной пружиной Н.
Принимаем nпр =11шт.
Фактическое усилие на приводе:
Параметры привода гидроцилиндра диаметр цилиндра:
где ρ – давление в гидросистеме ρ=10МПа;
Выразим из формулы для определения диаметра цилиндра усилие на приводе и пересчитаем его для стандартного значения диаметра:
1.3Прочностной расчет элементов приспособления
Рассчитаем диаметр тяги по допускаемым напряжениям растяжения. В качестве материала для тяги выбираем сталь 45 с термообработкой – закалка с последующим охлаждением в воде. Для стали 45:
Определение необходимого размера опасного сечения производим по зависимости:
Принимаем а резьбу на тяге М36.
1.4Описание конструкции и принципа действия приспособления
Описание конструкции приспособления:
В корпус 2 запрессовывается два фланца 4 и 5 которые крепятся болтами 7. На фланец 4 устанавливаются тарельчатые пружины 12 и нажимная втулка 1. На фланец 5 устанавливается гидроцилиндр 13 который передает усилие на нажимную втулку 1 через тягу 3 с помощью шайбы 10 и гайку 9. На корпус 2 по пазам устанавливается базирующие шпонки 6 с помощью винтов 8.
Описания принципа действия приспособления:
Заготовка устанавливается на тарельчатые пружины 12 и упирается торцом в фланец 4. Воздух подается в штоковую полость гидроцилиндра 13 перемещая тягу 3 в низ и создавая усилие на тарельчатых пружинах 12 через нажимную втулку 1 с помощью шайбы 10 и гайки 9. Тарельчатые пружины 12 деформируются и закрепляют заготовку центрируя ее. Производится обработка заготовки после чего воздух подается в поршневую полость гидроцилиндра 13 снимая усилие с тарельчатых пружин 12 они возвращаются в прежнее положение и заготовка раскрепляется.
Рисунок 9 – Станочное приспособление
1.5 Расчет приспособления на точность
Погрешность установки заготовки в приспособлении определяется по формуле:
где погрешность базирования;
погрешность закрепления;
погрешность приспособления.
Погрешность базирования и закрепления на оправке с тарельчатыми пружинами [4]:
Погрешность приспособления также равна нулю поскольку нет зазоров в приспособлении которые могут повлиять на точность получаемого размера:
Тогда погрешность установки равна:
Для обеспечения точности выполняемого размера должно выполняться следующее условие:
где TН14=520 мкм – допуск на выполняемый размер.
Проверим выполнение данного условия:
Таким образом условие выполняется а это значит что требуемый размер можно получить используя спроектированное приспособление.
2Проектирование контрольного приспособления
Данное контрольное приспособление проектируется для измерения торцевого биения левого торца корпуса относительно оси детали и оно не должно превышать 005 мм. Данное приспособление должно иметь как можно меньшую погрешность измерения.
2.1 Выбор схемы контроля
Метод контроля – с базированием контролируемой детали на оправке измерительного стола и измерительной головкой сбазированной по внутреннему отверстию детали. Схема контроля представлена на рисунке 10.
Рисунок 10 – Схема контроля торцевого биения
2.2Описание работы приспособления
Данное контрольное приспособление (рис. 10) предназначено для контроля торцевого биения детали корпус.
На корпус 4 измерительного приспособления устанавливается заготовка по внутренней цилиндрической поверхности 380Н14. В отверстие заготовки 140Н6 устанавливается оправка с гидропластмассом 1. Она имеет конус на который устанавливается кронштейн 5 который в свою очередь фиксируется гайкой 2 и контргайкой 3. Давление в гидропластмассе создается с помощью толкателя 8 через рукоятку 6 который давит на плунжер оправки и деформирует тонкостенную втулку закрепляя и центрирую оправку в заготовке. На одном конце кронштейна 5 запрессован противовес в виде рукоятки 7 с помощью которой и вращается кронштейн относительно оси заготовки. На другом конце кронштейна 5 в отверстии устанавливается индикатор часового типа 10 и крепится с помощью винта 9. Далее индикатор 10 настраивается на ноль после чего вращается кронштейн 5 и производится измерение торцевого биения детали корпус. После измерения торцевого биения с помощью рукоятки 6 через толкатель 8 снимают давление с гидропластмасса. Оправку с гидропластмассом 1 вынимают из отверстия заготовки заготовку снимают с корпуса 4. После чего устанавливают следующую заготовку и проводят последующие измерения.
Для измерения торцевого биения на другом расстоянии от оси детали на корпус оправки с гидропластмассой 1 устанавливается другой кронштейн 5 с другим расположением отверстия для установки индикатора часового типа 10.
Рисунок 11 – Контрольное приспособление
2.3Расчет погрешности измерения
Погрешность измерения вычисляется по следующей зависимости:
где - погрешность базирования ( так как погрешность установки в осевом направлении детали на оправку с гидропластмассой равна нулю);
- погрешность закрепления равна нулю так как деталь не закрепляется;
- погрешность приспособления равна нулю так как никакие элементы приспособления не влияют на точность измерения торцевого биения;
- погрешность измерительного прибора;
где - допускаемая погрешность прибора;
- цена деления прибора;
- погрешность передаточных устройств равно нулю так как измерение передается напрямую;
- погрешность детали-эталона по которому настраивается индикатор (так как индикатор настраивается на ноль без детали-эталона то эта погрешность равна нулю).
Таким образом погрешность измерения равна:
Для точности измерения должно выполняться условие:
где Т=50 мкм – торцевое биение детали корпус.
Проверяем выполнение данного условия:
Таким образом условие выполняется а это значит что требуемое торцевое биение детали корпус можно измерить используя спроектированное контрольное приспособление.
В результате выполнения курсового проекта был разработан технологический процесс изготовления детали корпус рассчитана заготовка выбран режущий и измерительный инструмент рассчитаны режимы резания и нормы времени а также было спроектировано специальное приспособление для обработки заготовки на вертикально-фрезерном станке с ЧПУ и разработан сборочный чертеж приспособления было спроектировано контрольное приспособление для измерения торцевого биения детали корпус разработан сборочный чертеж приспособления описаны принципы работы приспособлений. Сделаны выводы о пригодности приспособлений – станочное приспособление позволяет выдержать установленную точность размера; контрольное приспособление позволяет произвести измерения торцевого биения детали корпус в пределах допуска на измеряемое биение.
Методические указания к курсовому проекту по дисциплине «Технология автоматизированного производства» (для студентов специальности 7.090202 «Технология машиностроения» всех форм обучения) Сост. Голубов Н.В..
Анурьев В.И. Справочник конструктора-машиностроителя: В 3 т. Т. 1. – 8-е изд. перераб. и доп. Под ред. И.Н. Жестковой. – М.: Машиностроение 2001. – 920 с.
Руденко П.А. и др. Проектирование и производство заготовок в машиностроении: Учеб. ПособиеП.А.Руденко Ю.А.Харламов В.М.Плескач; Под общ. Ред. В.М. Плескача. – К.: Выща шк. – 1991.-247 с.
Справочник технолога-машиностроителя: В 2-х томах. Под ред. А.Г.Косиловой и Р.К.Мещеряковой. 4-е изд. Перераб. И доп. – М.: Машиностроение 1986. – 656 с.
Режимы резания металлов. Справочник Под ред. Ю.В.Барановского. Изд. 3-е перераб. и доп. – М.: Машиностроение 1972. – 408 с.
Сысоев В.И. Справочник молодого сверловщика. – М. Профтехиздат 1962. – 272 с.
Справочник нормировщика А.В. Ахумов Б.М.Генкин Н.Ю. Иванов и др.; Под общ. ред. А.В. Ахумова. – Л.: Машиностроение Ленингр. Отд-ние 1986. – 458 с.
Общемашиностроительные нормативы времени вспомогательного на обслуживание рабочего места и подготовительно-заключительного для нормирования станочных работ. Серийное производство. – М.: Машиностроение 1974. – 421 с.
Обработка металлов резанием: Справочник технолога А.А.Панов В.В.Аникин Н.Г.Бойм и др.; Под общ. ред. А.А. Панова. – М.: Машиностроение. 1988. – 736 с.
Горбацевич А.Ф. Шкред В.А. Курсовое проектирование по технологии машиностроения: [Учеб. пособие для машиностроит. спец. вузов]. – 4-е изд. перераб. и доп. – Мн.: Высш. Школа 1983. – 256 с.
Станочные приспособления: Справочник. В 2-х т.Ред. совет: Б.Н.Вардашкин (перед.) и др. – М.:Машиностроение 1984. – Т.1Под ред. Б.Н.Вардашкина А.А.Шатилова 1984. – 592 с.
Станочные приспособления: Справочник. В 2-х т.Ред. совет: Б.Н.Вардашкин (перед.) и др. – М.:Машиностроение 1984. – Т.2Под ред. Б.Н.Вардашкина А.А.Шатилова 1984. – 656 с.
Вереина В.И. Справочник токаря: учеб. пособие для нач. проф. образования Л.И.Вереина. – 2-е изд. стер. – М.: Издательский центр «Академия» 2006. – 448 с.
Черпаков Б.И. Металлорежущие станки: Учебник для нач. проф. образования Б.И.Черпаков Т.А. Альперович. – М.: Издательский центр «Академия» 2003. – 368 с.
ГОСТ 7505-89 – Поковки стальные штампованные.
Чертеж детали.cdw

Неуказанные отклонения размеров: отверстий Н14
Острые кромки притупить.
КОНТРОЛЬНОЕ ПРИСПОСОБЛЕНИЕ.cdw

Погрешность измерения - 11
Несоосность тонкостенной втулки и оси отверстия - не
Усилие на рукоятке - 150 Н.
Технические требования:
Трущиеся поверхности смазать смазкой ЛИТОЛ 25-4Н
Нерабочие поверхности приспособления покрыть эмалью серой
Маркировать шрифтом ПКС01.
Не создовать давление в гидропластмассе без заготовки.
Притереть плунжер с корпусом погрешностью
ПК 8.050.050.201.11.727.200
ОК010.docx
Наименование операции
Оборудование устройство ЧПУ
Обозначение программы
А.Установить и снять заготовку
Патрон 7102-0038 ГОСТ 24351-80
Точить поверхности 12 последовательно по программе 085
Резец MTJNR2525M16 T5K10 ТУ РБ 00223728.049-99
Расточить поверхность 3 по программе 119
Резец S25Q-SSKCR T5K10 ГОСТ 26613-85; ШЦ--500-01 ГОСТ 166-80
Расточить поверхности 456 последовательно по программе 15
Резец S25Q-SSKCR T5K10 ГОСТ 26613-85
Контролировать размеры ШЦ--500-01 ГОСТ 166-80; линейка слесарная ГОСТ 427-75
ОК020(1).doc
Фрезеровать 2 паза последовательно по программе. 06
Фреза 2223-0147 Р6М5 ГОСТ 17026-71; втулка HSK A 63 MT3 x 140
Рассверлить 2 отверстия 29 на R140 последовательно по программе. 028
Сверло 2301-3672 Р6М5 ГОСТ 10903-77; втулка HSK A 63 MT3 x 140
Зенкеровать 2 отв. 297 на R140 последовательно по программе. 023
Зенкер 2320-2599 Р6М5 ГОСТ 12489-71; втулка HSK A 63 MT3 x 140
Развернуть 2 отверстия 299 на R140 последовательно по программе. 026
Развертка 2363-3482 Р6М5 ГОСТ 1672-80; втулка HSK A 63 MT3 x 140
Развернуть 2 отверстия 30 на R140 последовательно по программе. 031
Развертка 2363-0652 Р6М5 ГОСТ 1672-80; калібр пробка 8133-0922 Н7 ГОСТ 14810-69; втулка HSK A 63 MT3 x 140
Цековать 4 отверстия 15 на R125 последовательно по программе 02
Циковка 2350-0708 Р6М5 ГОСТ 26258-87; втулка HSK A 63 MT2 x 120
ОК030.docx
Наименование операции
Оборудование устройство ЧПУ
Обозначение программы
А.Установить и снять заготовку
Патрон мембранный ГОСТ 16157-70 064
Шлифовать 140Н6 предварительно на проход.
Головка AW 40х60 24А 25-Н СТ1 6К А 35мс ГОСТ 2447-82; калибр пробка Н8 ГОСТ 21401-75 054 176
0 90 005 10 1680мммин 70 30
ОК015(1).doc
Точить поверхности 16378 последовательно по программе
Резец PDJNR2525M15 Т15К6 ТУ РБ 00223728.049-99 127
Контролировать внешний вид
ШЦ--500-01 ГОСТ 166-80; линейка слесарная ГОСТ 427-75
ОК035.docx
Наименование операции
Оборудование устройство ЧПУ
Обозначение программы
А.Установить и снять заготовку
Оправка с тарельчатыми пружинами 072
Шлифовать 210h8. 17 208
Круг 23350х127х50 25А СМ2 24Н 6К 35мс ГОСТ2424-83; МК 250-1 ГОСТ 6507-90
0 65 002 10 380мммин. 40 20
ОК015.docx
Наименование операции
Оборудование устройство ЧПУ
Обозначение программы
А.Установить и снять заготовку
Патрон 7102-0038 ГОСТ 24351-80
Точить поверхности 12 последовательно по программе 163
Резец MTJNR2525M16 T5K10 ТУ РБ 00223728.049-99
Точить поверхность 3 по программе 073
Расточить поверхности 45 последовательно по программе 095
Резец S25Q-SSKCR T15K6 ГОСТ 26613-85
ОК040.docx
Наименование операции
Оборудование устройство ЧПУ
Обозначение программы
А.Установить и снять заготовку
Патрон мембранный ГОСТ 16157-70 064
Шлифовать 140Н6 на проход. 067 176
Головка AW 40х60 25А 24-Н С1 5К А 35мс ГОСТ 2447-82; калибр пробка Н6 ГОСТ 21401-75
0 90 001 10 1350мммин 90 40
ОК020.docx
Наименование операции
Вертикально-фрезерная с ЧПУ
Оборудование устройство ЧПУ
Обозначение программы
А.Установить и снять заготовку
Приспособление специальное
Сверлить 4 отв. 10 на R125 последовательно по программе 048
Сверло 2301-3578 Р6М5 ГОСТ 10903-77; втулка HSK A 63 MT1 X 110
Сверлить 2 отв. 15 на R170 2 отв. 15 на R140 последовательно по программе. 071
Сверло 2301-3602 Р6М5 ГОСТ 10903-77; втулка HSK A 63 MT2 x 120
Рассверлить 2 отверстия 30 на R170 последовательно по программе. 028
Сверло 2301-3674 Р6М5 ГОСТ 10903-77; втулка HSK A 63 MT3x 140
Мкф1б 2.docx
Код наименование операции
Обозначение документа
Код наименование оборудования
Наименование детали сб. единицы или материала
Патрон токарный 3-х кулачковый клиновый механизированный 7102-0080У; резец MTJNR2525M16 T5K10
ТУ РБ 00223728.049-99; резец PDJNR2525M15 Т15К6 ТУ РБ 00223728.049-99; резец S25Q-SSKCR T15K6
ГОСТ 26613-85; ШЦ--350-005 ГОСТ 166-80; линейка слесарная ГОСТ 427-75
0 Вертикально-фрезерная с ЧПУ
Вертикально фрезерный станок с ЧПУ МА655ВС1 4 1 1 1 25 223 137
Сверлить 4 отв. 10 на R125 4 отв. 15 на R125 2 отв. 15 на R150 2 отв. 15 на рассверлить 2 отв.
на R150 2 отв. 28 на фрезеровать 2 паза; зенкеровать 2 отв. 29 на развернуть 2отв. 296
на R140 2 отв. 30 на R140 последовательно по программе
Приспособление специальное; втулка HSK A 63 MT3 втулка HSK A 63 MT1 X 110; втулка
HSK A 63 MT2 сверло 2301-3674 Р6М5 ГОСТ 10903-77; сверло 2301-3669 Р6М5 ГОСТ 10903-77; зенкер
20-2599 Р6М5 ГОСТ 12489-71; фреза 2223-0147 Р6М5 ГОСТ 17026-71; развертка 2363-3482 Р6М5 ГОСТ 1672-80; развертка
развертка 2363-0652 Р6М5 ГОСТ 1672-80; сверло 2301-3602 Р6М5 ГОСТ 10903-77; сверло 2301-3578 Р6М5
ГОСТ 10903-77; цековка 2350-0708 Р6М5 ГОСТ 26258-87; калібр пробка 8133-0922 Н7 ГОСТ 14810-69
МКф1.docx
Сталь 40Х ГОСТ 4543-71
Код наименование операции
Обозначение документа
Код наименование оборудования
Токарный станок с ЧПУ АТ-450ПН 4 1 1 1 25 173 1194
Подрезать правый торец; точить 400; расточить торец 140Н6380 380 фаску 2х45° 140Н6
Патрон токарный 3-х кулачковый клиновый механизированный 7102-0070У; резец MTJNR2525M16 T5K10
ТУ РБ 00223728.049-99; резец S25Q-SSKCR T5K10 ГОСТ 26613-85; ШЦ--500-01 ГОСТ 166-80;
линейка слесарная ГОСТ 427-75
Токарный станок с ЧПУ АТ-450ПН 4 1 1 1 25 195 134
Подрезать левый торец торец 400210; точить 210h8 2 фаски 2х45° галтель расточить 140Н6
фаску 2х45° последовательно по программе
МКф1б 3.docx
Код наименование операции
Обозначение документа
Код наименование оборудования
Наименование детали сб. единицы или материала
0 Внутришлифовальная
Внутришлифовальный станок 3К228А 5 1 1 1 25 95 47
Патрон ГОСТ 16157-70;головка AW 40х60 24А 25-Н СТ1 6К А 35мс ГОСТ 2447-82; калибр пробка Н8 ГОСТ 21401-75
Круглошлифовальный станок 3М174 5 1 1 1 25 89 51
Оправка с тарельчатыми пружинами; круг 23350х127х50 25А СМ2 24Н 6К 35мс ГОСТ2424-83; МК 250-1 ГОСТ 6507-90
Внутришлифовальный станок 3К228А 5 1 1 1 25 95 49
Патрон ГОСТ 16157-70; головка AW 40х60 25А 24-Н С1 5К А 35мс ГОСТ 2447-82; калибр пробка Н6 ГОСТ 21401-75
Промыть деталь в 2х % растворе кальцинированной соды при t=80..90°С. Сушить деталь.
0 Технический контроль
Плита поверочная 1-0-400х400 ГОСТ 10905-86
015-Токарно винторезная с ЧПУ.cdw

040-Внутришлифовальная.cdw

020-Вертикальнофрезерная с ЧПУ.cdw

035-Круглошлифовальная.cdw

030-Внутришлифовальная.cdw

010-Токарно винторезная с ЧПУ.cdw

ПРИСПОСОБЛЕНИЕ ЗАЖИМНОЕ.cdw

ТЕХНИЧЕСКИЕ ХАРАКТЕРИСТИКИ
Давление воздуха в сети Р=10 МПа
Усилие закрепления Q=247266 Н
Усилие на приводе W=82793 H
Длина хода поршня 12мм
ТЕХНИЧЕСКИЕ ТРЕБОВАНИЯ
После сборки приспособление испытать
Пневмосеть заполнить сжатым воздухом
давления в сети ниже отметки 10 МПа
Смазывать трущиеся поверхности смазкой
ЛИТОЛ-24 ГОСТ 21150-75
Маркировать: номер партии
товарный знак завода изготовителя
Неработающие поверхности приспособления окрасить эмалью
спецификация на контрольное приспособление.cdw

спецификация на зажимное приспособление.cdw

Рекомендуемые чертежи
- 24.01.2023
- 01.07.2014