Разработка технологического процесса детали Шестерня Z41




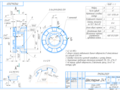
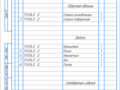
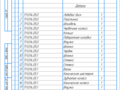
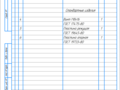
- Добавлен: 25.01.2023
- Размер: 2 MB
- Закачек: 1
Описание
Разработка технологического процесса детали Шестерня Z41
Состав проекта
![]() |
![]() |
![]() |
![]() ![]() ![]() |
![]() |
![]() ![]() |
![]() ![]() |
![]() ![]() |
![]() ![]() |
![]() ![]() |
![]() ![]() |
![]() ![]() |
![]() ![]() |
![]() ![]() |
![]() ![]() |
![]() ![]() |
![]() ![]() |
![]() ![]() |
![]() ![]() |
![]() ![]() |
![]() ![]() |
![]() ![]() |
![]() ![]() |
![]() ![]() ![]() |
![]() |
![]() ![]() ![]() ![]() |
![]() ![]() ![]() ![]() |
![]() ![]() ![]() ![]() |
![]() ![]() ![]() ![]() |
![]() ![]() ![]() |
![]() ![]() ![]() ![]() |
![]() ![]() ![]() ![]() |
![]() ![]() ![]() ![]() |
![]() ![]() ![]() ![]() |
![]() |
![]() ![]() ![]() ![]() |
![]() |
![]() |
![]() ![]() ![]() ![]() |
![]() ![]() ![]() ![]() |
![]() ![]() ![]() ![]() |
![]() |
![]() ![]() ![]() |
Дополнительная информация
Приложения.docx
( Комплект документации)
(Технические характеристики станков)
Режимы_резания_и_станки.docx
В ходе расчета режимов резания технологом назначаются подача s и глубина резания t в соответствии с указаниями в литературе.
Далее рассчитывается скорость резания сила резания и крутящий момент на шпинделе станка. Исходя из мощности резания назначается станок.
Операция 005 Токарная черновая.
Рассверливание поверхности 4 в размер спиральным сверлом.
а) Подача ммоб с. 277 таб.25 [2]
б) Глубина резания мм с. 276 [2]
в) Скорость резания
-эмпирические коэффициенты с. 279 таб.29 [2]
- поправочный коэффициент с. 261 [2]
- коэффициент учитывающий качество обрабатываемого материала
- показатель степени с. 262 таб.1 [2]
- коэффициент отражающий состояние поверхности заготовки с. 263 таб.5 [2]
- коэффициент учитывающий качество материала инструмента с. 263 таб.6 [2]
мин. - стойкость инструмента с. 280 таб.30 [2]
е) Частота вращения обрабатываемой детали обмин примем обмин.
Фактическая скорость резания ммин.
г) Крутящий момент с.277 [2]
- эмпирические коэффициенты с. 281 таб.32 [2]
- поправочный коэффициент с. 271 [2]
- поправочный коэффициент для стали и чугуна учитывающий влияние качества обрабатываемого материала на силовые зависимости с.264 таб.9 [2]
- показатель степени для быстрорежущей стали с.264 таб.9 [2]
ж) Мощность резания кВт
Точение поверхности 5 в размер 481 подрезным резцом с твердосплавной пластиной из материала Т15К6.
а) Подача ммоб с. 266 таб.11 [2]
б) Глубина резания мм с. 266 таб.11 [2]
Эмпирические коэффициенты
мин. - стойкость инструмента с. 268 [2]
г) Частота вращения обрабатываемой детали обмин принимаем из нормального ряда обмин тогда:
- эмпирические коэффициенты с. 274 таб.22 [2]
- поправочный коэффициент для стали учитывающий влияние качества обрабатываемого материала на силовые зависимости с.264 таб.9 [2]
- показатель степени для твердого сплава с.264 таб.9 [2]
- поправочные коэффициент учитывающие влияние геометрических параметров режущей части инструмента на составляющие силы резания при обработке стали и чугуна с.275 таб.23 [2]
е) Мощность резания кВт
Точение поверхности 2 в размер токарным прямым проходным резцом с твердосплавной пластиной из материала Т15К6.
Растачивание поверхности 1 в размер подрезным резцом с твердосплавной пластиной из материала Т15К6.
-поправочный коэффициент для внутренней обработки
Точение поверхности 3 в размер 40 подрезным резцом с твердосплавной пластиной из материала Т15К6.
б) Глубина резания мм с. 268 таб.11 [2]
Эмпирические коэффициенты:
Принимаем токарно-винторезный станок 16К20. Мощность главного привода кВт [Приложение В]
Операция 010 Токарная черновая.
Точение поверхности 6 в размер 47 подрезным резцом с твердосплавной пластиной из материала Т15К6.
Точение поверхности 4 в размер токарным прямым проходным резцом с твердосплавной пластиной из материала Т15К6.
Растачивание поверхности 5 в размер подрезным резцом с твердосплавной пластиной из материала Т15К6.
Точение поверхности 7 в размер подрезным резцом с твердосплавной пластиной из материала Т15К6.
Точение поверхности 8 (поверхность 3 получается автоматически) в размер специальным канавочным резцом с твердосплавной пластиной из материала Т15К6.
Точение поверхности 2 в размер специальным канавочным резцом с твердосплавной пластиной из материала Т15К6.
Операция 015 Токарная чистовая.
Растачивание поверхности 12 в размер токарным расточным резцом с твердосплавной пластиной из материала Т15К6.
а) Подача ммоб с. 268 таб.14 [2]
Точение поверхности 8 в размер 46 мм подрезным резцом с твердосплавной пластиной из материала Т15К6.
Точение поверхности 10 в размер токарным фасочным резцом с твердосплавной пластиной из материала Т15К6.
Растачивание поверхности 7 в размер токарным фасочным резцом с твердосплавной пластиной из материала Т15К6.
Точение поверхности 9 в размер 382 мм токарным подрезным резцом с твердосплавной пластиной из материала Т15К6.
Точение поверхности 11 3 в размер специальным канавочным резцом с твердосплавной пластиной из материала Т15К6.
Точение поверхности 2 1 в размер специальным канавочным резцом с твердосплавной пластиной из материала Т15К6.
Растачивание поверхности 6 в размер токарным фасочным резцом с твердосплавной пластиной из материала Т15К6.
Операция 020 Токарная чистовая.
Точение поверхности 3 в размер 45 мм подрезным резцом с твердосплавной пластиной из материала Т15К6.
Точение поверхности 1 в размер токарным прямым проходным резцом с твердосплавной пластиной из материала Т15К6.
Точение поверхности 4 в размер 37 мм токарным подрезным резцом с твердосплавной пластиной из материала Т15К6.
Операция 025 Сверлильная
Сверление поверхности 1 в размер спиральным сверлом.
- эмпирические коэффициенты с. 278 таб.28 [2]
е) Частота вращения инструмента обмин примем обмин.
Согласно получившейся мощности (N = 0177 кВт) выбираем вертикально-сверлильный станок 2М112 (Nст = 06 кВт). Технические характеристики станка указаны в прилож. В
Операция 030 Зубофрезерная
Нарезать зубья поверхность 1 пальцевой модульной фрезой.
а) Глубина нарезания t = 443 мм.
б) Выбираем подачу из предела (002 – 004) принимаем ммоб [2] с. 285 табл. 36;
Период стойкости фрезы Т = 80 мин [2] с. 290 табл.40.
Материал фрезы быстрорежущая сталь Р6М5.
Скорость резания при нарезании зубьев фрезами из быстрорежущей стали определяется эмпирической формулой [2] с. 282:
где Cv = 145 - коэффициент выбирается по [2] табл. 39; z = 6 – число зубьев фрезы; - поправочный коэффициент для стали учитывающий влияние качества обрабатываемого материала на силовые зависимости с. 282 [2]
- поправочный коэффициент с.261 таб.1 [2];
- поправочный коэффициент с.263 таб.5 [2];
- поправочный коэффициент с.263 таб.6 [2];
q=044; m=037; u = 01;p=013; x = 024 и y = 026 – показатели степени [2] с.287 табл. 39.
) Частота вращения фрезы:
обмин из нормального ряда принимаем n=2500 обмин тогда фактическая скорость резания равна:
где эмпирические коэффициенты [2] с. 291 табл. 41; коэффициент учитывающий качество обрабатываемого материала [2] с. 264 табл. 9;
) Крутящий момент на шпинделе
) Мощность резания (эффективная)
По значению фактической затрачиваемой мощности при процессе резанья выбираем широкоуниверсальный консольно-фрезерный станок СФ-676 (Nст = 3 кВт). Технические характеристики станка указаны в прилож. В.
Операция 035 Протяжная
Протягивание шлицев D-8 42H11 50H12 7D9 поверхности 1 на длину 292мм.
а) Подача(глубина резания) ммзуб – принимается по табл.54 стр. 300 [2] (ближайший больший к размерному перепаду между соседними режущими зубьями протяжки)
б) Периметр резания наибольшая суммарная длина лезвий всех одновременно режущих зубьев мм.
число зубьев в секции протяжки при профильной схеме резания;
мм – наибольшее число одновременно режущих зубьев; длина обрабатываемой поверхности мм; шаг режущих зубьев мм.
Согласно представленному ниже чертежу мм.
Исходя из требований к шероховатости по [2] стр. 299 табл.53 52 принимаем ммин.
где P=785 Н по [2] стр. 300 табл.54.
Так как требуемая мощность получается достаточно большой произведём перерасчёт скорости резания приняв мощность 8 кВт.
По значению силы резания принимаем горизонтально-протяжной станок 7А545 с максимальным тяговым усилием P=630 кН. Технические характеристики станка указаны в прилож. В
Операция 040 Фрезерная
Переход № 1. Фрезеровать поверхность № 1 длиной 12 мм шириной 6 мм.
Инструмент фреза специальная концевая угловая 12 мм ГОСТ 17025-71 с числом зубьев на глубину 12 мм.
а) Глубина резания мм;
б) Подача [2] с. 285 табл. 36;
в) Скорость резания ммин
где эмпирические коэффициенты [2] с. 287 таб. 39;
Принимаем концевую фрезу с коронками.
мин. - стойкость инструмента [2] с. 290 табл. 40;
поправочный коэффициент
где коэффициент учитывающий качество обрабатываемого материала [2] с. 261 табл. 1;
коэффициент учитывающий состояние поверхности заготовки [2] с. 263 табл. 5. ; коэффициент учитывающий материал инструмента [2] с. 263 табл. 6
г) Частота вращения фрезы:
е) Крутящий момент на шпинделе
з) Мощность резания (эффективная)
По значению фактической затрачиваемой мощности при процессе резанья выбираем вертикально-фрезерный станок с ЧПУ Haas TM-1 (Nст = 56 кВт). Технические характеристики станка указаны в прилож. В.
Операция 045 Фрезерная
Переход № 1. Фрезеровать поверхность № 1 длиной мм шириной 16 мм.
Инструмент фреза специальная концевая угловая 12 мм ГОСТ 17025-71 с числом зубьев на глубину 16 мм.
По значению фактической затрачиваемой мощности при процессе резанья (и для уменьшения времени обработки) выбираем вертикально-фрезерный станок с ЧПУ Haas TM-1 (Nст = 56 кВт). Технические характеристики станка указаны в прилож. В.
Операция 050 Шлифовальная
Переход № 1. Шлифовать начерно поверхность № 1 мм на длину 18 мм. Инструмент круг шлифовальный 125 мм ГОСТ 2424-83.
а) Продольная подача
ммин [2] с. 302 табл. 55;
б) Глубина шлифования мм;
в) Скорость заготовки выбираем из предела (8-30 ммин) принимаем ммин [2] с. 302 табл. 55;
г) Скорость круга выбираем из предела (30-35 мс) принимаем мс [2] с. 302 табл. 55.
Эффективная мощность
эмпирич. коэфф. [2] с. 303 таб. 56;
Переход № 2. Шлифовать начисто поверхность № 1 мм на длину 18 мм. Инструмент круг шлифовальный 125 мм ГОСТ 2424-83.
Согласно большей получившейся мощности (N = 298 кВт) выбираем станок кругло-шлифовальный 3Б12 (Nст = 30 кВт). Технические характеристики станка указаны в прилож. В.
Буквенно-цифирный индекс токарно-винторезного станка 16К20 обозначает следующее: цифра 1 - это токарный станок; цифра 6 – обозначает токарно-винторезный станок буква К – поколение станка цифра 20 – высота центров (220мм).
Технические характеристики станка 16К20
Диаметр обработки над станиной мм
Диаметр обработки над суппортом мм
Расстояние между центрам
Класс точности по ГОСТ 8-82
Размер внутреннего конуса в шпинделе
Конец шпинделя по ГОСТ 12593-72
Диаметр сквозного отверстия в шпинделе мм
Максимальная масса заготовки закрепленной в патроне кг
Максимальная масса детали закрепленной в центрах кг
Число ступеней вращения шпинделя шт.
Число ступеней частот обратного вращения шпинделя
Пределы частот прямого вращения шпинделя мин-1
Пределы частот обратного вращения шпинделя мин-1
Число ступеней рабочих подач - продольных
Число ступеней рабочих подач - поперечных
Пределы рабочих подач - продольных ммоб
Пределы рабочих подач - поперечных ммоб
Число нарезаемых метрических резьб
Число нарезаемых дюймовых резьб
Число нарезаемых модульных резьб
Число нарезаемых питчевых резьб
Число нарезаемых резьб - архимедовой спирали
Наибольший крутящий момент кНм
Наибольшее перемещение пиноли мм
Поперечное смещение корпуса мм
Наибольшее сечение резца мм
Мощность электродвигателя главного привода
Мощность электродвигателя привода быстрых перемещений суппорта кВт
Мощность насоса охлаждения кВт
Габаритные размеры станка (Д х Ш х В) мм
812 3 200 х 1 166 х 1 324
Сверлильный станок 2М112
Сверлильный станок 2М112 используется для получения отверстий диаметр которых не больше 12 мм а также нарезания резьбы значение которой не превышают М12 в меленьких деталях из дерева чугуна пластика цветных сплавов стали и т.д.
Наружный конус шпинделя по ГОСТ 9953-82
Вылет шпинделя от колонны
Расстояние от торца шпинделя до рабочей поверхности стола
Размеры рабочей поверхности стола
Количество Т-образных пазов
Расстояние между Т-образными пазами
Количество скоростей шпинделя
Частота оборотов шпинделя
Мощность главного привода
Широкоуниверсальный консольно-фрезерный станок СФ-676
Широкоуниверсальный консольно-фрезерный станок СФ-676 предназначен как для горизонтального фрезерования изделий цилиндрическми дисковыми фасонными и другими фрезами так и вертикального фрезерования торцевыми концевыми шпоночными и другими фрезами под различными углами в условиях единичного мелкосерийного и серийного производства. Со станком СФ-676 поставляются принадлежности необходимые для работы и обслуживания станка СФ-676: вертикальная шпиндельная головка хобот с серьгой патрон цанговый с цангами оправка и набор инструмента.
Технические характеристики:
Рабочая поверхность вертикального стола
Продольный ход стола
Вертикальный ход стола
Поперечный ход шпинделя
Расстояние от оси горизонтального шпинделя до рабочей поверхности съемного углового стола
Расстояние от торца вертикального шпинделя до рабочей поверхности съемного углового стола
Мощность главного двигателя
Габаритные размеры СФ-676
Горизонтально-протяжной станок 7А545
Горизонтально-протяжной станок цена 7А545 данное оборудование предназначено для обработки методом протягивания внутренних цилиндрических и фасонных поверхностей шлицевых и шпоночных пазов винтовых канавок внутренних зубьев и т. д. с целью получения заданных параметров точности шероховатости формы.
Наибольшая длина хода рабочих салазок мм
Наибольший наружный диаметр обрабатываемой детали мм
Наибольшая длина применяемой протяжки мм
Мощность электродвигателя главного привода кВт
Суммарная мощность электродвигателей кВт
Вертикально-фрезерный станок с ЧПУ Haas TM-1
Особенности конструкции
-Полностью литая чугунная станина
-Полностью закрытое герметичное защитное ограждение
-Серводвигатели перемещений по осям с прямой передачей момента
-Стальные закаленные подшипниковые блоки направляющих
-ШВП с двойным креплением и предварительно натянутой гайкой
-Система ручной смазки направляющих и ШВП
Макс. перемещение по оси X мм 762
Макс. перемещение по оси Y мм 305
Макс. перемещение по оси Z мм 406
Максимальное расстояние от стола до торца шпинделя мм 508
Минимальное расстояние от стола до торца шпинделя мм 102
Макс. нагрузка на стол (равном. распределенная) кг 454
Ширина Т-образных пазов мм 16
Расстояние между Т-образными пазами мм 1016
Размер конуса шпинделя 40
Максимальная частота вращения шпинделя обмин 4000
Макс. мощность шпинделя кВт 56
Макс. крутящий момент кН 45
Макс. осевое усилие кН 89
Макс. скорость холостых подач ммин 51
Макс. рабочие подачи по осям XYZ ммин 51
Точность позиционирования мм ±0010
Повторяемость мм ±0005
Объем бака СОЖ л 57 (опция)
Станок кругло-шлифовальный 3Б12
Предназначен для шлифования наружных и внутренних цилиндрических и конических поверхностей в условиях индивидуального и мелкосерийного производства.
Станок имеет поворотный стол. Это дает возможность шлифовать не только цилиндрические но и пологие конические поверхности.
Благодаря поворотной передней и поворотной шлифовальной бабке можно шлифовать крутые конические наружные и внутренние поверхности.
Шлифовальная бабка состоит из двух частей. Верхняя часть шлифовальной бабки может передвигаться относительно нижней (верхних салазок). Это дает возможность шлифовать периферией шлифовального круга торец детали закрепленной в патроне.
На станке 3Б12 можно шлифовать как в неподвижных центрах так и в патроне.
Наименование параметра
Наибольший диаметр обрабатываемого изделия мм
Наибольшая длина обрабатываемого изделия (РМЦ) мм
Наибольший диаметр шлифования мм
Наименьший диаметр шлифования мм
Рекомендуемый диаметр шлифования мм
Наибольшая длина шлифования мм
Диаметр шлифуемого отверстия мм
Расстояние от оси шпинделя передней бабки до зеркала стола - высота центров мм
Станина и столы станка
Наибольшее продольное перемещение стола мм
Наименьший ход стола между упорами мм
Ручное замедленное ускоренное перемещения стола за один оборот маховика мм
Скорость перемещения стола от гидросистемы ммин
Наибольший угол поворота верхнего стола по часовой стрелке град
Наибольший угол поворота верхнего стола против часовой стрелки град
Цена деления шкалы поворота верхнего стола град
Цена деления шкалы поворота верхнего стола (конусность) ммм
Наибольшее перемещение шлифовальной бабки от маховика мм
Перемещение шлифовальной бабки относительно верхних салазок мм
Перемещение шлифовальной бабки во время быстрого подвода мм
Поворот шлифовальной бабки град
Шлифовальный круг по ГОСТ 2424-67
Диаметр шлифовального круга - наибольший наименьший мс
Диаметр шлифовального круга - посадочный мс
Наибольшая высота устанавливаемого круга мм
Частота вращения шпинделя наружного шлифования обмин
Толчковая подача - периодическая подача с реверсированием стола мм
Цена деления лимба поперечной подачи мм
Цена деления лимба тонкой поперечной подачи мм
Величина поперечного перемещения шлифовальной бабки за один оборот маховика мм
Скорость быстрого установочного перемещения шлифовальной бабки мммин
Конец шлифовального шпинделя по ГОСТ 2323-67 (конусность 1:5 номинальный диаметр) мм
Приспособление для внутреннего шлифования
Наибольший диаметр заготовки устанавливаемой в патроне мм
Наибольшая длина шлифуемого отверстия мм
Диаметр внутришлифовальной головки мм
Число оборотов внутришлифовального шпинделя
Частота вращения изделия (бесступенчатое регулирование) обмин
Угол поворота в сторону шлифовального круга град
Угол поворота в сторону от шлифовального круга град
Конус шпинделя передней бабки по ГОСТ 2847-67
Величина отвода пиноли задней бабки от руки мм
Конус шпинделя пиноли задней бабки по ГОСТ 2847-67
Привод и электрооборудование станка
Количество электродвигателей на станке
Электродвигатель шпинделя шлифовальной бабки 2М кВт
Электродвигатель внутришлифовального шпинделя 7М кВт
Электродвигатель привода изделия 1М кВт
Электродвигатель насоса гидросистемы 3М кВт
Электродвигатель насоса системы смазки шпинделя 4М кВт
Электродвигатель насоса системы охлаждения 5М кВт
Электродвигатель магнитного сепаратора 6М кВт
Габаритные размеры и масса станка
Габаритные размеры станка (длина х ширина х высота) мм
Масса станка с электрооборудованием и охлаждением кг
Карты_эскизов_листы.cdw

Биениемер.cdw

Давление воздуха в системе
При замере радиального биения
поворот детали (автоматический)
Технические требования
Скорость вращения детали отрегулировать с помощью дросселей в
системе головки поворотной.
Настройку прибора производить по детали-эталону.
Деталь считается годной
измеряемых деталей не
биения зубчатого венца
Технология_НТТС.cdw

Допуск полного радиального биения поверхности В относительно
Боковые плоскости кулачков направить к центру детали.
Неуказанные предельные отклонения размеров: H14
На торцах зубьев поверхности Д выполнить фаску 1
Скоба.cdw

Твердость рабочей поверхности HRC 59 65.
Рабочая поверхность имеет хромовое износостойкое покрытие.
Покрытие нерабочих поверхностей - Хим.Фос.прм. ГОСТ 9.306-85.
Лист 2.cdw
Станок токарно-винторезный 16К20
Операция 010 токарная черновая
Операция 015 токарная чистовая
Станок токарно-винторезный 1
Операция 020 токарная чистовая
Станок токарно-винторезный
Операция 025 сверлильная
Станок вертикально-сверлильный 2М112
Операция 030 зубофрезерная
Широкоуниверсальный консольно-фрезерный станок СФ-676
Операция 035 протяжная
Станок горизонтально-протяжной 7А545
Операция 040 фрезерная
Вертикально-фрезерный станок с ЧПУ Haas TM-1
Операция 045 фрезерная
Операция 050 шлифовальная
Станок кругло-шлифовальный 3Б12
Коэффициент смещения
Неуказанные предельные отклонения размеров:
* - размер для справки.
Закрепление в делительной головке.
Сверлить через кондукторную плиту.
головка делительная.cdw

Заготовка.cdw

Внутренние уклоны 10
Неуказанные радиусы 3
Резец гост20874-75.cdw

пластин в гнезде державки.
Материал режущей пластины Т15К6 ГОСТ 3882-74.
Маркировать: материал режущей части резца
знак завода изготовителя.
Остальные технические требования по ГОСТ 19058-80.
Фреза_пальцевая_модульная.cdw

Спецификация прибора контроля.spw

Болт М10 х 40 ГОСТ 7798-70
Винт М6 х 16 ГОСТ 1491-80
Винт М8 х 35 ГОСТ 1491-80
Винт М4 х 8 ГОСТ P 50383-92
Шайба 8 Н ГОСТ 6402-70
Шайба 10 Н ГОСТ 6402-70
Скоба спецификация.cdw

Спецификация головки.spw

Циллиндрическая часть коробки
Спецификация резец.cdw

записка_типа.docx
РПЗ 34с. 4 рис. 3 табл. 10 источников 4 прил.
Разработка технологического процесса детали шестерня Z41.
Цель работы – сформировать новые и закрепить ранее полученные знания и навыки в области разработки технологических процессов механической обработки деталей с учетом современных тенденций в машиностроении.
В процессе работы был разработан технологический процесс технологическая документация включающая в себя чертеж заготовки и детали операционные наладки чертежи режущего и мерительного инструмента и чертеж станочного приспособления.
Результатом выполнения курсового проекта является комплект документов на технологический процесс изготовления шестерни Z41.
Данный комплект документов может быть использован на профильном машиностроительном предприятии для изготовления детали данного типа.
Технологическая часть6
1. Назначение детали6
2 Определение годового объема выпуска и типа производства8
3 Анализ технологичности конструкции детали9
4. Выбор способа получения заготовки10
5. Выбор технологических баз10
6. Разработка маршрута обработки заготовки11
7. Расчет операционных припусков и размеров.14
8. Расчет режимов резания.19
9. Расчет контрольно-измерительного инструмента24
9.1. Расчёт исполнительных размеров калибров-скоб24
Конструкторская часть26
1. Выбор станочного приспособления20
Технологическая часть
1. Назначение детали
Современные механизмы и машины трудно представить без зубчатых шестерёнок. В то же время до сих пор никто не знает кем и когда была изобретена шестерня. С появлением шестерни значительно сократился путь развития машинной цивилизации.
Наука о шестернях математическое и графическое обоснование профилей зубьев появились одновременно с развитием геометрии механики и кинематики в ХVII веке.
В современных машинах широко применяют зубчатые передачи. Различают силовые зубчатые передачи предназначенные для передачи крутящего момента с изменением частоты вращения валов и кинематические передачи служащие для передачи вращательного движения между валами при относительно небольших крутящих моментах.
Зубчатые передачи используемые в различных механизмах и машинах делят на цилиндрические конические червяковые смешанные и гиперболоидные (винтовые и гипоидные).
Наибольшее распространение получили цилиндрические конические и червяковые передачи (рис. 1).
Рис. 1. Виды зубчатых передач:
а – цилиндрическая; б – коническая; в – червячная;
– шестерня; 2 – зубчатое колесо; 3 – червяк; 4 – червячное колесо
Конструкция шестерёнок непосредственно связана с их служебным назначением. Служебное назначение не только определяет тип колеса.
Материал шестерёнок выбирают в зависимости от назначения и условий эксплуатации последних передаваемых ими нагрузок скоростей вращения и т.п. При выборе марки стали необходимо учитывать следующие требования: низкую стоимость материала хорошую обрабатываемость резанием минимальное коробление при закалке и три основных эксплуатационных показателя – высокую прочность долговечность работы и повышенную стойкость к износу.
Для большинства зубчатых передач комбайнов тракторов автомобилей и других сельскохозяйственных машин передающих большие нагрузки лимитирующими факторами являются: прочность зубьев – сопротивление на изгиб стойкость поверхности профиля зубьев против усталостного разрушения (питтинга) и изнашивание зубьев. Может лимитировать один из указанных факторов но тогда все три фактора имеют почти одинаковые значения.
Для производства зубчатых колес наиболее широко применяют следующие стали:
углеродистые – 40 50 45;
хромистые – 20Х 35Х 40Х 50Х;
хромоникелевые – 12ХН3А 12Х2Н4А 20ХН;
хромомарганцевые – 18ХГ 18ХГТ 25ХГТ 30ХГТ;
хромомолибденовые – 20ХМ 30ХМ.
Кроме того литые стальные колеса изготовляют из углеродистой стали 40Л 50Л а зубчатые колеса малонагруженных передач сельскохозяйственных машин из чугуна СЧ18. При малых нагрузках шестерни также могут изготовляться из текстолита капрона и других неметаллических материалов.
Легированные стали с содержанием хрома никеля молибдена марганца применяют для изготовления высоконагруженных шестерён. Наилучшие свойства в готовой шестерне получаются после цементации. Содержание углерода в цементируемых сталях обычно колеблется от 015 до 025 %. Стали с низким содержанием углерода дают максимальную вязкость зубьев а с высоким содержанием углерода – максимальную прочность сердцевины. Глубина цементованного слоя шестерён составляет 1 2 мм.
2 Определение годового объема выпуска и типа производства
Годовой объем выпуска деталей можно рассчитать используя формулу.
где m=1 – количество одноименных деталей в машине;
М=20000 – годовой объем выпуска машин;
γ – 5 10 количество запасных частей в процентах;
– 2 6 процент брака и технологических потерь включая детали используемые для настройки станка в процентах.
Тип производства определяется по годовому объему выпуска и массе детали по табл. 1 [5 стр7]
Масса детали 537 кг следовательно при годовом объёме выпуска 32100 детали тип производства будет являться среднесерийным.
Среднесерийное производство характерно тем что изделия выпускаются довольно крупными сериями ограниченной номенклатуры; серии повторяются с известной регулярностью. За рабочими местами закреплена более узкая номенклатура операций. Оборудование универсальное и специальное вид движения предметов труда - параллельно-последовательный. Заводы имеют развитую производственную структуру заготовительные цехи специализируются по технологическому принципу а в механосборочных цехах создаются предметно-замкнутые участки.
3 Анализ технологичности конструкции детали
Деталь состоит из стандартных и унифицированных конструкционных элементов: диаметральных и линейных размеров. Это способствует использованию стандартных режущих и мерительных инструментов.
Деталь имеет точность и шероховатость которые можно получить стандартным унифицированным инструментом при стандартном технологическом процессе.
Шероховатость базовых поверхностей удовлетворяет требованиям точности установки детали ее обработки и контролю.
На шестерне имеются канавки для свободного выхода режущего инструмента.
Все обрабатываемые поверхности имеют свободный подвод и отвод режущего инструмента.
В зубчатом зацеплении нечётное количество зубьев.
Коэффициент шероховатости поверхности детали:
где Бср – средняя шероховатость поверхности детали;
где n – число основных поверхностей детали соответствующей шероховатости;
Коэффициент шероховатости поверхности детали
Исходя из выше перечисленного деталь является технологичной.
4. Выбор способа получения заготовки
Наилучшим способом получения заготовки будет штамповка. При этом обеспечивается относительно высокая стабильность размеров.
Заготовку получаем из стали 40ХН. Предельные отклонения размеров поковки и припуски на механическую обработку а также предельные отклонения по массе выполняем по классу точности Т4. Внешние уклоны 7° внутренние 10°.
Определяем рациональность выбора заготовки исходя из экономии материала с помощью коэффициента использования материала (КИМ):
где Q1=238 кг – масса детали; Q2=428 кг – масса заготовки
КИМ равный 65.9% приемлем для заданного метода получения заготовки и типа производства.
5. Выбор технологических баз
Технологическая база - это поверхность сочетание поверхностей ось или точка принадлежащая заготовке и используемая для определения ее положения в процессе изготовления.
При разработке технологического процесса огромное значение имеет назначение технологических баз. От правильности их выбора зависят производительность обработки точность выполнения размеров конструкция приспособлений конструкция режущих и измерительных инструментов.
Операция 05 Токарная черновая.
Технологическая база – необработанная конусная поверхность с уклоном 10 и 92 и торец шестерни 82мм.
Операция 010 Токарная черновая.
Технологическая база – обработанная поверхность 88 и торец 88мм.
Операция 015 Токарная чистовая.
Технологическая база – обработанная поверхность колеса 88мм и торец 88мм.
Операция 020 Токарная чистовая.
Технологическая база – обработанная поверхность 84мм и торец 84мм.
Операция 025 Сверлильная.
Технологическая база – обработанная внутренняя поверхность отверстия 58мм торец шестерни 82мм и торец шестерни 86мм.
Операция 030 Зубофрезерная.
Технологическая база – обработанная поверхность шестерни 82мм и торец 82мм.
Операция 035 Протяжная.
Операция 040 Фрезерная.
Технологическая база – торец шестерни 86мм торец шестерни 75.2 мм и шлицевая оправка.
Операция 045 Фрезерная.
Операция 050 Шлифовальная.
6. Разработка маршрута обработки заготовки
Сверлить отверстие 40мм.
Подрезать торец в размер 48.1мм.
Точить начерно 88 мм на расстояние 21мм.
Расточить начерно 63мм.
Подрезать торец в размер 40мм.
Переустановить деталь.
Подрезать торец в размер 47мм.
Точить начерно 84 мм на расстояние 27мм.
Расточить начерно 56мм.
Подрезать торец в размер 39.2мм.
Точить начерно 60 мм.
Точить начерно 77.2 мм.
Расточить начисто отверстие 42мм.
Подрезать торец в размер 46мм.
Снять фаску на валу шестерни 82 мм.
Снять фаску в отверстии шестерни 42 мм.
Точить начисто 82 мм.
Расточить начисто 58мм.
Подрезать торец в размер 38.2мм.
Точить начисто 58 мм.
Точить начисто 75.2 мм.
Снять фаску в отверстии шестерни 58 мм.
Подрезать торец в размер 45мм.
Точить начисто 86 мм.
Расточить начисто 65мм.
Подрезать торец в размер 37мм.
Сверлить 2 отверстия 3мм.
Фрезеровать зубья колеса 86мм
Протянуть шлицы D-8 42H11 50H12 7D9
Фрезеровать кулачки 82мм.
Фрезеровать фаску на зубьях 86мм.
Шлифовать зубья эвольвентного зацепления 86мм.
7. Расчет операционных припусков и размеров.
Промежуточные припуски имеют очень важное значение в процессе разработки технологических операций механической обработки деталей. Правильное назначение промежуточных припусков на обработку заготовки обеспечивает экономию материальных и трудовых ресурсов качество выпускаемой продукции уменьшает себестоимость изделия.
Расчет припусков и определение размеров заготовки получаемых горячим деформированием (ГОСТ 7505-89).
Определение класса размерной точности поковки.
Применяем штамповочный молот и пламенный способ нагрева исходной заготовки.
Класс точности поковки – Т4.
Определение группы материала.
Определение группы материала производится в зависимости от процентного содержания углерода 035% 065% и легирующих элементов 2% 5%.
Сталь 40 ХН относится к группе М2.
Определение степени сложности поковки.
Определяется степень сложности поковки по соотношению массы (объема) поковки mп (Vп) к массе (объему) геометрической фигуры в которую вписывается форма поковки (шар цилиндр параллелепипед правильная призма).
Принимаем степень сложности поковки – С1.
Определение ориентировочной массы поковки.
Мп.р.=5.37·15=8.15 кг.
Определение исходного индекса поковки.
Исходный индекс определяется в зависимости от массы группы материала степени сложности и класса точности поковки.
Принимаем исходный индекс –12.
Определение дополнительного припуска на обработку.
Дополнительный припуск на смещение поверхностей штампов – 03 мм (для диаметральных размеров).
Дополнительный припуск на изогнутость и отклонение от плоскостности и прямолинейности – 03 мм (для линейных размеров).
Определение общего припуска.
Определение номинальных размеров заготовки.
Цилиндрические поверхности:
Lзаг=Lдет+Zoi+Zoj – охватываемые размеры
Lзаг=Lдет-Zoi-Zoj – охватывающие размеры
Lзаг=Lдет+Zoi-Zoj – прочие размеры
Номина-льный размер детали
Номи-нальные размеры заготовки
Диаметра-льные размеры
Для получения деталей более высокого качества необходимо при каждом технологическом переходе механической обработки заготовки предусматривать производственные погрешности характеризующие отклонения размеровгеометрические отклонения формы поверхности микронеровности отклонения расположения поверхностей. Все эти отклонения должны находиться в пределах поля допуска на размер поверхности заготовок.
Аналитический метод определения припусков базируется на анализе производственных погрешностей возникающих при конкретных условиях обработки заготовки
Минимальное и максимальное значения припусков по каждому технологическому переходу:
где – высота микронеровностей поверхности на предыдущем переходе
([1] стр. 185 табл. 10);
– пространственное отклонение в расположении обрабатываемой поверхности после предыдущего перехода ([3] стр. 68);
h – глубина дефектного слоя ([1] стр. 185 табл. 10);
– погрешность установки обрабатываемой заготовки на выполненном переходе ([1] стр. 41 табл. 12);
– допуски на размер заготовки соответственно на выполненном и предыдущем переходах ([3] стр. 68).
Расчет припусков расчетно-аналитическим способом.
Рассчитываемый размер: .
Число технологических переходов необходимых для достижения заданных параметров качества:
Черновое шлифование.
Чистовое шлифование.
Минимальный расчетный припуск:
Погрешность заготовки ;
Для чернового точения: при установке в трехкулачковый самоцентрирующийся патрон.
Для чистового точения:
Для чернового шлифования:
Общие минимальные и максимальные величины припусков:
Проверка правильности выполнения расчетов:
8. Расчет режимов резания. (продолжение в приложении А)
В ходе расчета режимов резания технологом назначаются подача s и глубина резания t в соответствии с указаниями в литературе.
Далее рассчитывается скорость резания сила резания и крутящий момент на шпинделе станка. Исходя из мощности резания назначается станок.
Операция 005 Токарная черновая.
Рассверливание поверхности 4 в размер спиральным сверлом.
а) Подача ммоб с. 277 таб.25 [2]
б) Глубина резания мм с. 276 [2]
в) Скорость резания
-эмпирические коэффициенты с. 279 таб.29 [2]
- поправочный коэффициент с. 261 [2]
- коэффициент учитывающий качество обрабатываемого материала
- показатель степени с. 262 таб.1 [2]
- коэффициент отражающий состояние поверхности заготовки с. 263 таб.5 [2]
- коэффициент учитывающий качество материала инструмента с. 263 таб.6 [2]
мин. - стойкость инструмента с. 280 таб.30 [2]
е) Частота вращения обрабатываемой детали обмин примем обмин.
Фактическая скорость резания ммин.
г) Крутящий момент с.277 [2]
- эмпирические коэффициенты с. 281 таб.32 [2]
- поправочный коэффициент с. 271 [2]
- поправочный коэффициент для стали и чугуна учитывающий влияние качества обрабатываемого материала на силовые зависимости с.264 таб.9 [2]
- показатель степени для быстрорежущей стали с.264 таб.9 [2]
ж) Мощность резания кВт
Точение поверхности 5 в размер 481 подрезным резцом с твердосплавной пластиной из материала Т15К6.
а) Подача ммоб с. 266 таб.11 [2]
б) Глубина резания мм с. 266 таб.11 [2]
Эмпирические коэффициенты
мин. - стойкость инструмента с. 268 [2]
г) Частота вращения обрабатываемой детали обмин принимаем из нормального ряда обмин тогда:
- эмпирические коэффициенты с. 274 таб.22 [2]
- поправочный коэффициент для стали учитывающий влияние качества обрабатываемого материала на силовые зависимости с.264 таб.9 [2]
- показатель степени для твердого сплава с.264 таб.9 [2]
- поправочные коэффициент учитывающие влияние геометрических параметров режущей части инструмента на составляющие силы резания при обработке стали и чугуна с.275 таб.23 [2]
е) Мощность резания кВт
Точение поверхности 2 в размер токарным прямым проходным резцом с твердосплавной пластиной из материала Т15К6.
9. Расчет контрольно-измерительного инструмента
9.1. Расчёт исполнительных размеров калибров-скоб
Определить предельные отклонения ES EI es ei а также исходные данные для расчета калибров:
Начертить схемы расположения полей допусков контролируемых отверстия и вала и используемых для контроля рабочих пробок и скоб;
Рассчитать предельные размеры Р- НП Р-ПР а также предельные размеры изношенных проходных калибров;
Построить эскизы калибров.
Предельные отклонения для отверстия: ES=+160 EI=0;
для вала: es=0 ei=-110
По приложению находим:
для пробки H=11 Z=22 Y=0;
для скобы H1=8Z1=16Y1=0;
Конструкторская часть
1. Выбор станочного приспособления
Делительные головки. Общие сведения
Делительные головки - это приспособление для широкоуниверсальных и консольно-фрезерных станков которое значительно расширяют их технологические возможности. Их используют при изготовлении различных инструментов (фрез разверток зенкеров метчиков) нормализованных деталей машин (головки болтов грани гаек корончатые гайки) при фрезеровании зубчатых колес звездочек прорезании пазов и шлицев на торцах (зубчатые муфты) и других деталей.
Делительные головки служат для закрепления и деления обрабатываемых деталей на равные части при фрезеровании квадратов шестигранников нарезания зубчатых колес звездочек и других подобных работ и для поворота обрабатываемых деталей на заданный угол. Универсальные делительные головки служат также и для сообщения вращения обрабатываемой детали при нарезании винтовых канавок на универсальных фрезерных станках.
Универсальные делительные головки УДГ-Д
Ранее нашей промышленностью выпускались универсальные делительные головки УДГ Н-100 УДГ Н-135 и УДГ Н-160 с высотой центров H = 100 H = 135 и H = 160 мм.
По стандарту ГОСТ 8615-69 за основной размер делительных головок принятнаибольший диаметр обрабатываемой заготовки D. По стандарту принят ряд из шести типоразмеров головок D = 160; 200; 250; 320; 400 и 500 мм. Наименование моделей УДГ-Д-160 УДГ-Д-200 УДГ-Д-250 УДГ-Д-400 УДГ-Д-500.
Передаточное отношение червячной парыэтих головок 1 : 40 (N=40) т. е. шпиндель головки поворачивается на полный оборот за 40 оборотов рукоятки.
Диапазон деленияокружности заготовки до 400 частей включая простые числа.
Универсальные делительные головки позволяют производить деления обрабатываемых деталей тремя методами: непосредственным простым и дифференциальным и используются для комплектации фрезерных станков отечественного и зарубежного производства.
Каждому размеру станка (по ширине стола) должен соответствовать определенный типоразмер делительной головки. Так к консольно-фрезерным станкам № 2 (с шириной стола 320 мм) рекомендуется делительная головка с наибольшим диаметром обрабатываемой заготовки D = 250 мм а к фрезерным станкам № 3 (с шириной стола 400 мм) - делительная головка УДГ-Д-320 и т. д.
В корпусе21головки расположена поворотная колодка6 закрепляемая в требуемом положении стяжками11и12затягиваемыми гайками. Колодка 6 может быть установлена так что ось шпинделя при одном из крайних положений располагается под углом 10° вниз от горизонтали а при другом — под углом 10° за вертикаль.
Шпонки8и10входят в паз стола станка и обеспечивают правильное положение головки на столе.
В колодке6расположен шпиндель3. Передним подшипником шпинделя служит коническое отверстие в колодке6 а задним — отверстие во втулке7 закрепленной в той же колодке6. На шпинделе жестко закреплено на шпонке червячное колесо4 находящееся в зацеплении с червяком9.
Шпиндель головки закрепляется в требуемом положении (стопорение шпинделя после выполнения деления) при помощи устройства состоящего из кольца5 связанного со шпинделем шпонкой втулки29 винта28с рукояткойГи сухарика30. При вращении винт28 перемещаясь вправо нажимает через сухарик30на стенку кольца5. В то же время втулка29перемещается влево и крючкообразным концом действует на другую стенку кольца5 что при затянутом винте28исключает возможность поворота шпинделя при фрезеровании.
Рабочий конец шпинделя имеет резьбу на которую навертывают патрон или другое зажимное приспособление и коническое гнездо для центра.
В коническое гнездо противоположного конца шпинделя вставляют валик необходимый при дифференциальном делении.
Червяк9находится в коробке24 наполненной маслом. Подшипником правого конца червячного валика25служат втулка17с цапфами31и32и втулка18 навинчиваемая на резьбовой конец валика25при помощи лысок27. Подшипником другого конца валика служит втулка23 запрессованная в левую стенку коробки24. Этот конец коробки поддерживается валиком20 эксцентричная шейка (правый конец) которого входит в отверстие цилиндрического ползунка22. Валик20при повороте рукоятки М позволяет выключать червяк из зацепления с червячным колесом что необходимо для деления лобовым диском1(метод непосредственного деления). Одно деление шкалы на лобовом диске соответствует повороту шпинделя на 1°. Угол поворота шпинделя отсчитывается по нониусу нанесенному на пластинке2. Точность отсчета 5'.
Для простого делениячервяк головки должен быть соединен с червячным колесом. Червяк (а следовательно и шпиндель головки) поворачивается рукояткойК закрепленной на валике13 через зубчатые колеса15и26. Отсчет производится по неподвижному двухстороннему делительному диску19 имеющему на одной стороне 2425 28 30 34 37 38 39 41 42 и 43 отверстия а на другой — 46 47 49 51 53 54 57 58 59 62 и 66 отверстий. В отверстия выбранного круга диска входит штифт фиксатораЛс использованием раздвижного сектора.
Если после установки заготовки в требуемое положение стержень фиксатора не входит в отверстие диска последний может быть повернут на небольшой угол. Для этого следует выключить защелкуЖи закрепить стопоромЕ(см. рис. 249).
Для дифференциального делениячервяк головки должен быть соединен с червячным колесом а защелкаЖделительного диска выключена. Необходимый поворот заготовки достигается вращением рукоятки головки причем требуемый угол поворота заготовки получается в результате вращения рукоятки относительно делительного диска и вращения самого делительного диска.
Делительный диск приводится во вращение следующим образом. На цилиндрическую частьакоробки33(рис. 232) привода головки устанавливается гитара (рис. 233) а в коническое отверстие заднего конца шпинделя вставляют валик для дифференциального деления называемый дальше для краткости шпиндельным валиком. На свободный конец шпиндельного валика устанавливается на шпонке зубчатое колесоz1.
Сменные зубчатые колесаz2иz3 промежуточное (паразитное) колесоz0устанавливают на гитаре а сменное колесоz4— на валике34привода (см. рис. 232) головки. Через конические зубчатые колеса16и14вращение валика34передается делительному диску19.
В других случаях вращение шпинделя головки передается делительному диску через две пары сменных зубчатых колес без промежуточного (паразитного) колеса или через одну пару сменных зубчатых колес соединенных одним промежуточным колесом или через одну пару и два промежуточных колеса (см. схемы табл. 15).
В ходе выполнения курсового проекта по дисциплине «Технология производства НТТС» был разработан технологический процесс на деталь «Шестерня Z41». Полученный опыт и навыки будут использованы при выполнении технологической части дипломного проекта.
Справочник технолога-машиностроителя. В 2-х т. Т.1Под ред. А.Г. Косиловой и Р.К. Мещерякова. – 4-е изд. перераб. и доп. – М.: Машиностроение 1985. 656 с. ил.
Справочник технолога-машиностроителя. В 2-х т. Т.2Под ред. А.Г. Косиловой и Р.К. Мещерякова. – 4-е изд. перераб. и доп. – М.: Машиностроение 1985. 656 с. ил.
Курсовое проектирование по предмету “Технология машиностроения” Добрыднев И.С. – М: Машиностроение 1985. 184 с. ил.
Шубин А. А. Сибилёв Н. П. Проектирование по дисциплине «Технология производства подъёмно-транспортных и строительно-дорожных машин»: методические указания. – М.: Издательство МГТУ им. Н. Э. Баумана 2012. – 56 с.
Физическое материаловедение: учебник для вузов. под общей ред. Б.А. Калина. – М.: МИФИ 2008.
Рекомендуемые чертежи
- 04.06.2017
- 24.01.2023