Разработка технологического процесса изготовления детали ''Вал-шестерня привода насоса''




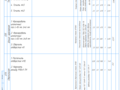
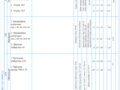
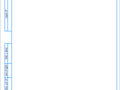

- Добавлен: 24.01.2023
- Размер: 6 MB
- Закачек: 0
Описание
Состав проекта
![]() |
![]() |
![]() ![]() ![]() |
![]() ![]() ![]() |
![]() ![]() ![]() |
![]() |
![]() |
![]() |
![]() |
![]() |
![]() |
![]() |
![]() |
![]() ![]() ![]() ![]() |
![]() |
![]() ![]() ![]() ![]() |
![]() ![]() ![]() ![]() |
![]() |
![]() ![]() ![]() ![]() |
![]() |
![]() |
![]() |
![]() ![]() ![]() ![]() |
![]() |
![]() ![]() ![]() ![]() |
![]() |
![]() |
![]() ![]() ![]() ![]() |
![]() |
![]() |
![]() |
![]() ![]() ![]() ![]() |
![]() |
![]() ![]() ![]() ![]() |
![]() ![]() ![]() ![]() |
![]() ![]() ![]() ![]() |
![]() ![]() ![]() ![]() |
![]() ![]() ![]() ![]() |
![]() ![]() ![]() ![]() |
![]() |
![]() ![]() ![]() |
![]() ![]() ![]() ![]() |
![]() |
![]() |
![]() ![]() ![]() |
![]() ![]() ![]() ![]() |
![]() |
![]() ![]() ![]() |
![]() ![]() ![]() |
![]() ![]() ![]() |
![]() ![]() ![]() |
![]() ![]() ![]() |
![]() ![]() ![]() |
![]() |
![]() |
![]() ![]() ![]() ![]() |
![]() |
![]() |
![]() |
![]() |
![]() ![]() ![]() ![]() |
![]() |
![]() |
![]() ![]() ![]() ![]() |
![]() |
![]() ![]() ![]() ![]() |
![]() |
![]() |
![]() |
![]() ![]() ![]() ![]() |
![]() |
![]() |
Дополнительная информация
Спецификация на фрезерное приспособление.docx
изготовления детали «Вал-шестерня привода насоса»
Винт М8х22 ГОСТ 17475-80
Гайка М16 ГОСТ 5915-70
Мaнжета 1-32х52-1 ГОСТ 8752-79
Штифт 10х24 ГОСТ 3128-70
Отзыв.docx
студентки группы ТМ-121
Вишняковой Елены Павловны
Выпускная квалификационная работа выполнена на тему «Разработка технологического процесса для изготовления детали «Вал-шестерня привода насоса» и содержит пояснительную записку чертежи графической части комплект технологической документации.
Расчетно-пояснительная записка содержит все разделы которые сопровождаются необходимыми расчетами описанием иллюстрациями. Текстовая и графическая части оформлены в соответствии с требованиями стандартов ЕСКД ЕСТД СТП.
Для вал-шестерни привода насоса разработан технологический процесс изготовления в условиях крупносерийного производства где использованы высокоэффективное оборудование и быстродействующее точное станочное приспособление.
На технологический процесс сформирован комплект технологической документации включающий в себя маршрутные и операционные карты а также карты эскизов. Графическая часть наглядно иллюстрирует текстовую часть работы.
При выполнении выпускной квалификационной работы студентка Вишнякова Е.П. проявила себя как сформировавшийся специалист способный самостоятельно ставить и решать технические задачи.
Пояснительная записка написана доходчивым технически грамотным языком с применением компьютерных информационных технологий.
Руководитель выпускной квалификационной работы
к.т.н. доцент Болдырев А. А.
Диплом.docx
листов графической части формата А1
ВАЛ-ШЕСТЕРНЯ ТЕХНОЛОГИЧНОСТЬ КОНСТРУКЦИИ РАЗМЕРНЫЙ АНАЛИЗ ТЕХНОЛОГИЧЕСКИЙ ПРОЦЕСС МЕХАНИЧЕСКАЯ ОБРАБОТКА ОПЕРАЦИИ РЕЖИМЫ РЕЗАНИЯ
Объектом проектирования является технологический процесс изготовления детали вал-шестерня привода насоса.
Целью выпускного квалификационного проектирования является разработка технологического процесса изготовления детали вал-шестерня привода насоса.
В выпускной квалификационной работе выполнен анализ конструкции детали проведен анализ базового технологического процесса изготовления детали вал-шестерня. Выполнен анализ вариантов получения заготовки в качестве заготовки выбран прокат. Разработан технологический маршрут обработки детали выполнен расчет припусков режимов резания и норм времени по операциям механической обработки.
Кроме того разработана управляющая программа для станка с ЧПУ оформлена сопроводительная документация выполнен расчет и проектирование участка цеха механической обработки.
Задание на выпускную квалификационную работу 2
Проектно-конструкторская часть8
1 Конструкторско-технологический анализ узла составной частью которого является «Вал-шестерня привода насоса»8
2 Разработка твердотельной модели детали «Вал-шестерня»9
Производственно-технологическая часть12
1 Оценка технологичности детали12
1.1 Установка типа производства16
2 Анализ базового технологического процесса19
3 Выбор мероприятий по оптимизации базового технологического процесса20
4 Выбор типа заготовки20
5 Назначение технологических баз и оценка точности базирования23
6 Разработка плана обработки и маршрута операций технологического процесса обработки детали «Вал-шестерня привода насоса»26
7 Выбор моделей оборудования28
8 Аналитический расчет технологических параметров31
8.1 Назначение припусков31
8.2 Расчет режимов резания для шпоночно-фрезерной операции37
9 Описание конструкции и расчет специальных средств технологического оснащения40
9.1 Силовой расчет приспособления.41
9.2 Расчет приспособления на точность получаемых размеров и точность базирования заготовки47
10 Автоматическое проектирование технологического процесса изготовления детали или средств технологического оснащения51
10.1 Использование САЕ систем для решения технологических задач51
10.2 Проектирование операционной технологии с разработкой управляющих программ и виртуальным моделированием обработки для станков с ЧПУ в САПР52
11 Технологическое проектирование производственного подразделения56
11.1 Расчет количества технологического оборудования и графика56
11.2 Определение производственной площади58
11.3 Расчет численности персонала61
11.4 Разработка технологической планировки64
12 Обоснование предложенных в работе технологических решений64
Научно-технический прогресс в машиностроении в значительной степени определяет развитие и совершенствование технологий применяемых в производстве по всей стране. Важнейшими условиями ускорения научно-технического прогресса являются рост производительности труда повышение эффективности производства и улучшение качества продукции.
Совершенствование технологических методов изготовления продукции является первостепенной задачей в области машиностроения. Качество деталей и машин надежность долговечность и экономичность эксплуатации зависят не только от совершенства конструкции но и от технологии производства. Применение современных высокопроизводительных методов обработки обеспечивающих высокое качество поверхностей деталей эффективное использование станков с ЧПУ разработка технологической документации и автоматизация расчетов при помощи компьютерных систем использование применение прогрессивных форм организации и экономики производственных процессов— все это направлено на решение главных задач: повышения эффективности производства и качества продукции.
Целью дипломного проекта является проектирование технологического процесса изготовления детали вал-шестерня привода насоса.
Задачи дипломного проекта:
- провести анализ конструкции детали с расчетом технологичности конструкции детали размерный анализ чертежа детали определение типа производства;
- разработать проектный вариант технологического процесса изготовления детали с расчетом припусков на обработку режимов резания и норм времени;
- спроектировать специальное станочное приспособление произвести силовой расчет приспособления и определить точность получаемых размеров;
- разработать управляющую программу для станков с ЧПУ.
Проектно-конструкторская часть
1 Конструкторско-технологический анализ узла составной частью которого является «Вал-шестерня привода насоса»
Деталь “Вал-шестерня привода насоса” является составной частью роторного насоса и служит для передачи вращательного движения на ротор.
В насосах роторного типа перемещение транспортируемой среды осуществляется путем последовательного заполнения рабочей камеры средой с последующим ее вытеснением происходящим за счет вращательного или вращательно-поступательного движения рабочего органа – ротора различающегося по конструкции в зависимости от вида роторного насоса. Несмотря на наличие вращающегося рабочего органа роторные насосы принципиально отличаются от большинства динамических насосов так как относятся к объемным насосам и имеют иной способ перемещения жидкости.
Вал-шестерня привода насоса является ответственной деталью. Прочность вала определяет механическую надежность машины в эксплуатации. Прямолинейность и прочность вала зависят не только от правильного расчета и выбора конструктивных размеров но и от технологических процессов обработки вала и сборки насаживаемых на него деталей.
Данный вал имеет форму ступенчатого цилиндра с зубчатыми колесами с посадкой деталей по системе отверстия. В целях снижения обработки следует стремиться к уменьшению числа ступеней. Вал имеет 2 ступени с повышенной точностью обработки по 6-му квалитету для посадки подшипников. Конструкция вала предусматривает два шпоночных паза под посадку зубчатых колес которые передают крутящий момент. Также на валу имеется два центровых отверстия с помощью которых вал надёжно фиксируется в приспособлении и обработка проходит с заданной точностью. Имеются также и шлицы выполненные по 5-му квалитету.
Данный вал-шестерня изготовлен из стали 40Х (свойства и химический состав представлены в таблице 1.1 и 1.2 [7]) и имеет ряд ответственных поверхностей к которым предъявляются жёсткие и высокие требования при изготовлении.
Таблица 1.1 – Химический состав стали 40Х ГОСТ 4543-71 %
Таблица 1.2 – Механические свойства стали 40Х ГОСТ 4543-71
2 Разработка твердотельной модели детали «Вал-шестерня»
Для создания твердотельной модели детали «вал-шестерня» используется программа для автоматизированного проектирования КОМПАС-3D V16.1 производства компании АСКОН. В качестве вспомогательного модуля используется дополнение «Валы и механические передачи 3D».
При создании твердотельной модели детали «вал-шестерня привода насоса» используется операция вращения по заданному эскизу. В качестве альтернативы допускается использовать операцию выдавливания по заданному эскизу – в данном случае эскизом будет окружность заданного диаметра указанная на чертеже детали. Таким же способом строится вся поверхность детали «вал-шестерня привода насоса». Дальнейшие операции – создание шестерни шпоночных и шлицевых соединений будут созданы при помощи дополнительной библиотеки «Валы и механические передачи 3D». Окно расчета и создания шлицевых соединений предоставлено на рисунке 1.1.
Рисунок 1.1 – Создание шлицевых соединений при помощи библиотеки стандартных изделий
Для автоматического создания шестерни для заданной детали используется меню «Менеджер библиотек - Валы и механические передачи 3D – Механические передачи – Шестерня коническая с прямым зубом» меню представлено на рисунке 1.2.
Дополнительная библиотека для программы Компас 3D может так же использоваться для создания стандартных разъемных элементов таких как шпоночный паз. Для создания шпоночного паза в программе для автоматизированного проектирования твердотельных моделей необходимо выбрать плоскость детали и ввести параметры шпоночного паза. Рассчитываемые параметры будут выбраны в соответствии и принятыми стандартами.
Рисунок 1.2 – Библиотека механических передач для расчета конической прямозубой шестерни
Твердотельная модель детали «вал-шестерня» с выполненными канавками и шпоночными пазами предоставлена в приложении А.
Производственно-технологическая часть
Технологичность конструкции детали имеет прямую связь с производительностью труда затратами времени на технологическую подготовку производства и изготовление изделия. Поэтому перед проектированием технологического процесса изготовления детали необходимо провести анализ технологичности ее конструкции. Цель такого анализа – выявление недостатков конструкции по сведениям содержащимся в чертежах и технических требованиях а также возможностей улучшения технологичности рассматриваемой конструкции.
1 Оценка технологичности детали
В процессе изготовления детали заготовка подвергается сложной обработке. Для обеспечения точности обработки и снижения стоимости обработки заготовка должна быть достаточно высокого качества. Деталь имеет сложную конфигурацию однако это оправдано конструктивным назначением. Деталь «вал-шестерня привода насоса» имеет достаточную жесткость при своих диаметрах и длине для использования обычных методов обработки что позволяет использовать обычные приспособления для ее установки и закрепления.
Относительно технологичности конструкции детали можно высказать следующие соображения. На основании имеющегося рабочего чертежа детали условий работы данной детали в конструкции а также с учетом того что конструкция детали достаточно хорошо отработана в условиях текущего производства нецелесообразно производить замену материала так как имеющийся полностью удовлетворяет требованиям по прочности свойствам и обрабатываемости.
Наружные поверхности детали могут быть использованы в качестве установочных или опорных баз при механической обработке.
Все прочие участки детали являются легкодоступными для обработки и следовательно позволяют производить их обработку точением фрезерованием сверлением шлифованием и т.п. Рабочие поверхности детали представлены на рисунке (2.1).
Рисунок 2.1 – Рабочие поверхности детали
Технические требования к детали содержат всю необходимую информацию касающеюся служебного назначения детали и сведения относящиеся непосредственно к чертежу. Это позволяет сделать вывод что технические условия к детали были основательно проработаны конструктором и соответствуют требованиям предъявляемым к детали.
Конструкция детали обеспечивает возможность применение типовых и стандартных технологических процессов её изготовления:
поверхность 1 выполнена в виде шлицевой части;
поверхность 2 является несущей поэтому жестких требований к ней не предъявляется;
поверхность 3 используется для внешнего контакта с внутренней поверхностью манжеты. Поэтому к ней предъявляются жесткие требования. Поверхность полируется до достижения шероховатости Ra 032 мкм;
поверхность 4 является несущей поэтому жестких требований к ней не предъявляется;
поверхность 5 также является несущей и предназначена для посадки подшипника. Поэтому к ней предъявляются жесткие требования. Поверхность шлифуется до достижения шероховатости Ra 125 мкм;
поверхность 6 Выполнена в виде канавки которая нужна для вывода шлифовального круга. Жестких требований к ней предъявлять нецелесообразно;
поверхность 7 является несущей и предъявлять жесткие требования к ней не нужно;
боковые стороны зубьев участвуют в работе и определяют как долговечность узла так и его шумность поэтому к боковым сторонам зубьев и их взаимному расположению предъявляют ряд требований как по точности расположения так и по качеству поверхности (Ra 25 мкм);
поверхность 9 является несущей и предъявлять жесткие требования к ней не нужно;
поверхность 10 Выполнена в виде канавки которая нужна для вывода шлифовального круга. Жестких требований к ней предъявлять нецелесообразно;
поверхность 11 является несущей и предназначена для посадки подшипника. Поэтому к ней предъявляются жесткие требования. Поверхность шлифуется до достижения шероховатости Ra 125 мкм;
поверхность 12 является несущей поэтому жестких требований к ней не предъявляется;
поверхность 13 используется для контакта с внутренней поверхностью манжеты. Поэтому к ней предъявляются жесткие требования. Поверхность полируется до достижения шероховатости Ra 032 мкм;
поверхность 14 является несущей поэтому жестких требований к ней не предъявляется;
поверхность 15 представлена в виде шпоночного паза который предназначен для передачи крутящего момента от вала-шестерни к ременному шкиву Rz 20 мкм;
поверхность 16 представлена канавкой которая служит для вывода резьбонарезного резца;
поверхность 17 выполнена в виде шпоночного паза для посадки стопорной шайбы Rz 40 мкм;
поверхность 18 представляет собой резьбу под гайку которая служит для поджатия шкива Ra 25 мкм.
Коэффициент унификации конструктивных элементов детали определяется по формуле (2.1) [10 c.34].
где Qу.э.- число унифицированных конструктивных элементов детали шт;
Qу.э.- общее число конструктивных элементов детали шт.
Деталь технологична так как значение показателя полученного коэффициента унификации больше 065 что по коэффициенту технологичности детали удовлетворяет требованиям [10 стр. 178 прил. 12].
Коэффициент использования материала определяется по формуле (2.2) [10 c.33].
где mд- масса детали кг;
mз- масса заготовки кг.
В крупносерийном и массовом производстве Км=085 09. Деталь технологична так как значение полученного показателя коэффициента использования материала удовлетворяет требованиям [10 стр. 178 прил. 12].
Коэффициент точности обработки определяется по формуле (2.3) [10 С.33].
где - средний квалитет точности.
Средний квалитет точности определяется по формуле (2.4)
Деталь нетехнологична так как значение показателя больше 08. По коэффициенту технологичности детали не удовлетворяет требованиям [10 стр. 178 прил. 12].
Исходя из произведенных расчетов можно сделать вывод что деталь технологична по коэффициенту унификации и по коэффициенту использования материала но не технологична по коэффициенту точности обработки.
1.1 Установка типа производства
Классификационной категорией производственного процесса является тип производства. Он определяется широтой номенклатуры регулярностью стабильностью и объёмом выпуска продукции.
Тип производства выбираем предварительно исходя из массы детали m = 46 кг и годовой программы выпуска деталей В = 9000
Крупносерийное производство предусматривает более широкое применение механизации и автоматизации производственных процессов. Коэффициент закрепления операций при крупносерийном производстве Кз.о = 1-10.
Крупносерийное производство характеризуется широкой номенклатурой изделий изготавливаемых или ремонтируемых периодически повторяющимися небольшими партиями и сравнительно небольшим объемом выпуска.
В этом случае для нового технологического процесса рассчитываем необходимое количество оборудования по операциям
Определяем количество станков по формуле (2.5)
где– годовая программа шт.;
– штучное или штучно-калькуляционное время;
– действительный фонд времени ч. =4029;
– нормативный коэффициент загрузки оборудования =085.
Фактический коэффициент загрузки рабочего места вычисляется по формуле.
Определяем фактический коэффициент загрузки рабочего места и количество операций выполняемых на рабочем месте.
где – принятое количество станков.
Количество операций выполняемых на рабочем месте определяется по формуле (2.7)
Рассчитанные значения для всех операций заносим в сводную таблицу 2.1
Таблица 2.1 –Расчетные данные для уточнения типа производства
Фрезерно-центровальная
Суммарное число операций =837.
Определим коэффициент закрепления операций по формуле
По ГОСТ 3.1121-84 коэффициенту закрепления операций соответствует крупносерийное производство ().
2 Анализ базового технологического процесса
Анализ заводского технологического процесса изготовления «Вал-шестерни привода насоса» позволяет выявить недостатки и преимущества присущие данному технологическому процессу.
Заводской технологический процесс разработан с учётом особенностей среднесерийного производства технических требований чертежа и с учётом принятой заготовки – проката.
В существующем техпроцессе предусмотрены все необходимые черновые и чистовые операции для получения детали согласно требованиям чертежа по точности размеров расположения поверхностей и по параметрам шероховатости а также все необходимые операции разметочные и слесарные что соответствует конкретно среднесерийному типу производства.
Оборудование для изготовления детали «вал-шестерня привода насоса» выбрано неверно с учётом вида производимых работ габаритов детали и требуемой точности из наличия станков существующего механического парка.
Отсутствие специального станочного приспособления для фрезерования шпоночных пазов детали влияет на точность обработки детали и увеличивает время подготовки станка.
Так же расположение станков на участке механической обработки не соответствует ходу технологического процесса обработки детали «вал-шестерня привода насоса» из-за чего значительная часть времени тратилась на транспортировку детали между этапами обработки.
В маршрутных картах не указан весь применяемый нормализованный режущий инструмент что объясняется спецификой данного предприятия.
3 Выбор мероприятий по оптимизации базового технологического процесса
В целях оптимизации базового технологического процесса изготовления детали «вал-шестерня привода насоса» будет разработана управляющая программа для станка с ЧПУ что позволит сократить время механической обработки детали и позволит оптимизировать затраты рабочего времени на наладку станочных приспособлений.
Для шпоночно-фрезерной операции будет спроектировано специальное станочное приспособление с использованием гидроцилиндра что позволит сократить время подготовки операции и повысит качество обрабатываемой детали.
Так же будет разработана сопроводительная документация оформленная по требованиям ЕСТД. К тому же будет произведен ряд улучшений касающихся взаимного расположения оборудования на участке механической обработки детали.
4 Выбор типа заготовки
Главным при выборе заготовки является обеспечение заданного качества готовой детали при ее минимальной себестоимости. Техпроцессы получения заготовок определяются технологическими свойствами материала конструктивными формами и размерами детали и программой выпуска.
Исходя из конфигурации и параметров обрабатываемой детали предлагается три варианта получения заготовки:
Экономическое обоснование заключается в сравнении себестоимости получения заготовок.
Стоимость заготовки из проката определяется по формуле
где М – затраты на материал заготовки руб.;
ΣСтех – технологическая себестоимость правки калибрования
Затраты на материал заготовки М руб. определяются по формуле
где - масса заготовки кг;
S - цена 1т материала заготовки руб. [3 c. 30];
- масса готовой детали кг;
- цена 1т отходов руб. [3 С. 32]
Определяем технологическая себестоимость Стех руб. по формуле (2.11)
где Сп.з. – приведённые затраты на рабочем месте руб.ч;
Тшт-к – штучно-калькуляционное время выполнения заготовительной
где Lрез – длина резания при резании проката на штучные заготовки мм;
Sм – минутная подача при разрезании мммин;
Sм=60 мммин; ;[4С.12];
i – коэффициент показывающий долю вспомогательного времени в
Заготовка получаемая ковкой вычисляется по формуле (2.13)
где - коэффициент зависящий от класса точности;; [3 С.33];
- коэффициент зависящий от группы сложности; ; [3С.35];
- коэффициент зависящий от массы; ; [3 c.25];
- коэффициент зависящий от марки материала; ; [3 С.33];
- коэффициент зависящий от объема производства;; [3 С.36].
Экономический эффект руб. вычисляют по формуле (2.14)
Выполненные расчеты подтверждают что экономически целесообразно в условиях крупносерийного производства применять в качестве заготовки для детали «вал-шестерня привода насоса» - прокат.
5 Назначение технологических баз и оценка точности базирования
Для каждой операции назначаются технологические базы выбранные с учетом используемого оборудования при обработке детали и принятого технологического процесса для изготовления вал-шестерни привода насоса.
Исходными данными для выбора баз является: чертеж детали со всеми необходимыми требованиями условия расположения и работы детали в машине. При выборе технологических баз целесообразно руководствоваться основными принципами. Воспользуемся принципом совмещения баз когда в качестве технологических баз принимают основные т.е. конструкторские базы используемые для определения положения детали в изделии.
Из ранее проанализированного заводского техпроцесса следует что для уменьшения погрешности обработки во многих операциях используются одни и те же базовые поверхности то есть соблюдается принцип постоянства баз что существенно снижает погрешность и увеличивает точность обработки.
Выбранные технологические базы представлены в таблице 2.2
Таблица 2.2 – Выбор технологических баз
Технологические базы
Фрезерно- центровальный станок 2Г942
Поверхности заготовки Ф70
Токарный станок 16К20
Токарный станок с ЧПУ 16К20Ф3
Фрезерный станок 6Р13Ф3
Фрезерный станок 5В312
0Токарно-винторезная
0Зубо-шевинговальная
Шлифовальный GearSpect SBO 340
5Кругло-шлифовальная
Кругло шлифовальный станок 3М151Ф2
Продолжение таблицы 2.2 – Выбор технологических баз
Вертикально-сверлильный станок 2Н150
Погрешность установки при базировании заготовки в самоцентрирующемся патроне зависит от величины возможного ее смещения в момент приложения силового замыкания. При черновой токарной обработке деталь устанавливается в самоцентрующийся трехкулачковый патрон; величины погрешности установки следует определить по формуле (2.15) [1 табл.19-24 Стр. 66]
где – величина возможного смещения заготовки в осевом направлении;
– величина возможного смещения заготовки в радиальном направлении.
Погрешность установки на последующих переходах при базировании заготовки в центрах принимается равной нулю.
6 Разработка плана обработки и маршрута операций технологического процесса обработки детали «Вал-шестерня привода насоса»
Технологический процесс изготовления детали «вал-шестерня привода насоса» разработан с учетом места каждой операции в маршрутной технологии. К моменту проектирования каждой операции известно какие поверхности и с какой точностью обрабатываются на предшествующих операциях какие поверхности и с какой точностью нужно обрабатывать на данной операции.
Проанализировав конструкцию детали на технологичность определив тип производства и выбрав вид получения заготовки разработаем маршрут механической обработки детали «вал-шестерня привода насоса».
Принятый технологический процесс обработки детали представлен в таблице 2.3
Таблица 2.3 – Принятый маршрутный технологический процесс
Фреза торцовая Т15К6 ГОСТ 6396-78; сверло центров. Р6М5 ГОСТ 14952-75
Резец проходной отогнутый Т15К6
Продолжение таблицы 2.3 – Принятый маршрутный технологический процесс
Резецпроходной отогнутый Т15К6
ГОСТ 18881-73 резец канавочный ГОСТ 20872-80
ГОСТ 18881-73 резец канавочный ГОСТ 20872-80 Резец резьбовой ГОСТ 18885-73
Шпоночная фреза Т15К6 ГОСТ 6396-78 Сверло спиральное ГОСТ 2034-80
Червячная фреза для шлицевых валов Р6М5 ГОСТ 8072-60
Червячная фреза ГОСТ 9324-80
Сверло спиральное ГОСТ 2034-80
Шлифовальный станок GearSpect SBO 340
Круг шлифовальный ГОСТ 2424-83
Круглошлифовальный станок 3М151Ф2
Круг плоский шлифовальный ГОСТ 2425-70 ПП600х60х305
Зенкер ГОСТ 12489-71 метчик ГОСТ 3266-81
7 Выбор моделей оборудования
Выбор типов и моделей оборудования рассматривается на различных стадиях технологической подготовки производства. Предварительный выбор оборудования производится при назначении метода обработки поверхностей обеспечивающего выполнение технических требований к обрабатываемым поверхностям. Выбор модели станка прежде всего определяется его возможностью обеспечить точность размеров и формы а также качество поверхности изготавливаемой детали.
Для изготовления и обработки детали «вал – шестерня привода насоса» применяется следующее оборудование.
Токарный станок с ЧПУ 16К20Ф3. Станок 16К20Ф3предназначен для токарной обработки в автоматическом режиме наружных и внутренних поверхностей деталей типа тел вращения со ступенчатым и криволинейным профилем различной сложности по заранее составленной управляющей программе. Обработка происходит в один или несколько проходов в замкнутом автоматическом цикле. Установка заготовок осуществляется в центрах. Станок 16К20Ф3 является наиболее распространенным и легкодоступным оборудованием для разных типов производств.
Технические характеристики станка представлены в таблицы 2.4.
Таблица 2.4 – Характеристики токарного станка с ЧПУ 16К20Ф3
Технические характеристики
Диаметр обработки над станиной
Диаметр обработки над суппортом
Диаметр цилиндрического отверстия в шпинделе
Наибольший поперечный ход суппорта
Наибольший продольный ход суппорта
Мощность электродвигателя главного движения
Габаритные размеры станка (Д х Ш х В) мм
Для шлифования зубьев детали «вал-шестерня привода насоса» выбран новый высокопроизводительный станок с ЧПУ GearSpect SBO 340 CNC Basic - высокопроизводительный станок современной конструкции с 7-ю управляемыми осями динамической балансировкой круга и мощной системой охлаждения для высокоскоростного шлифования. Зубошлифовальный станок с 7-ю управляемыми осями работает на принципе непрерывного шлифования методом обката при одновременной тангенциальной подаче заготовки. Скорость резания до 35 мсек. Привода шлифовального круга и заготовки управляются с помощью электроники включая позиционирование заготовки по отношению к шлифовальному кругу. Такой принцип значительно повышает рабочую точность станка и скорость шлифования.
Технические характеристики станка представлены в таблице 2.5.
Таблица 2.5 – Технические характеристики станка с ЧПУ GearSpect SBO 340 CNC Basic
Максимальный вес детали
Частота вращения шлифовального круга
Степень точности обработки зубчатых венцов по ГОСТ1643-81
8 Аналитический расчет технологических параметров
8.1 Назначение припусков
Разработка технологического процесса изготовления деталей машин всегда предусматривает расчет припусков и межоперационных размеров. Правильный расчет припусков на обработку детали позволяет повысить точность обработки качество исполнения детали и уменьшение количества бракованных деталей на производстве.
Технологический маршрут обработки поверхности 6511 состоит из обтачивания чернового и чистового и шлифования чернового и чистового. Рассчитаем припуски для заготовки чернового и чистового точения чернового и чистового шлифования.
Rz=150 мкм;[9 С.66];=250 мкм; [9 С.66];
=50 мкм; [9 С.67];=50 мкм; [9 С.67];
=30 мкм; [9 С.67];=30 мкм; [9 С.67];
=10 мкм; [9 С.67]; =20 мкм; [9 С.67];
Пространственное отклонение заготовки вала (мкм) вычисляется по формуле (2.16)
где - смещение оси заготовки в результате погрешности центрования мкм;
Используя справочную информацию находим [9 С.73].
Суммарное отклонение расположения заготовки детали при обработке проката в центрах мкм вычисляют по формуле (2.17)
где - удельная кривизна заготовок на 1 мм длины мкммм;
- длина смещаемой части заготовки мм.
Пространственное отклонение для чернового точения заготовки
Пространственное отклонение для чистового точения заготовки
Пространственное отклонение для шлифования
Минимальные значения припусков мкм вычисляются по формуле
Вычисляем наименьшие межоперационные размеры и размер заготовки:
- после чистового шлифования
- после чернового шлифования
- после чистового точения
- после чернового точения
Устанавливаем допуски на межоперационные размеры и размер заготовки:
- на чистовое шлифование мкм;
- на черновое шлифование мкм;
- на чистовое точение мкм;
- на черновое точение мкм;
Вычисляем наибольшие операционные размеры и размер заготовки:
- после чернового шлифования
Вычисляем предельные значения допусков:
- для чистового шлифования
- для чернового шлифования
- для чернового точения
Вычисляем общий припуск
Схематичное изображение припусков детали изображено на рисунке 2.2.
Рисунок 2.2 - Схема расположения припусков допусков и предельных
На все остальные обрабатываемые поверхности припуски назначаются по ГОСТ 2590-88. Значения всех припусков сводятся в таблицу 2.6.
Таблица 2.6 – Припуски и предельные отклонения на обрабатываемые поверхности вала
8.2 Расчет режимов резания для шпоночно-фрезерной операции
При назначении элементов режимов резания учитываем характер обработки тип и размеры инструмента материал его режущей части материал и состояние заготовки тип и состояние оборудования.
Обрабатываемый материал – сталь 40Х ГОСТ4543-71; в=980 МПа; станок вертикально - фрезерный 6Р13Ф3
Характеристика обрабатываемой поверхности:
Фрезеруется шпоночный паз – В = 8мм длиной – L = 50 мм.
Выбор режущего инструмента:
Фреза 2234-0135 ГОСТ6396-78 (диаметром 8 мм; L=73мм).
Скорость фрезы рассчитывается по формуле (2.40):
гдеСv – коэффициент учитывающий обрабатываемый материал;
D – диаметр фрезы в мм;
T – стойкость инструмента в мин;
T – глубина резания в мм;
Кv – общий поправочный коэффициент на скорость резания.
Определим коэффициент Кv по формуле (2.41) из [8 С.285]
где– коэффициент учитывающий обрабатываемый материал;
– коэффициент учитывающий состояние поверхности заготовки;
– коэффициент учитывающий материал инструмента.
Значение коэффициента Кмv рассчитаем по формуле (2.42)
гдеB – предел прочности B = 980 МПа;
KГ – коэффициент учитывающий группу стали KГ = 1;
nv – показатель степени nv = 1;
Тогда скорость вращения фрезы:
Определим частоту вращения фрезы по формуле (2.43):
гдеD – диаметр фрезы мм;
принимаем станка n = 650 мин-1 .
Уточним скорость резания по формуле (2.44):
Определим силу резания по формуле из [10 С.284]:
гдеСр – коэффициент учитывающий обрабатываемый материал;
Кмр – общий поправочный коэффициент на силу резания.
Определим мощность резания по формуле (2.45) из [10 с.284]:
гдеPz – сила резания в Н;
V – скорость резания в м мин.
Проверяем достаточность мощности привода станка по формуле (2.46).
У станка мод. 6Р13Ф3
гдеNДВ – мощность двигателя в кВт.;
NШП = 3 · 085 = 255 кВт.
Обработка возможна при условии что N ≤ NШП следовательно обработка возможна так как полученные значения удовлетворяют требованиям.
9 Описание конструкции и расчет специальных средств технологического оснащения
Использование специальных станочных приспособлений способствует повышению производительности и точности обработки облегчению условий труда сокращению количества рабочих сокращению вспомогательного времени затрачиваемого на подготовку к обработке данного типа деталей расширению технологических возможностей оборудования.
Специальное приспособление для фрезерования шпоночного паза детали «вал-шестерня привода насоса» предназначено для базирования и крепления заготовки вала на вертикально-фрезерном станке 6Р13Ф3.
Приспособление для фрезерования шпоночного паза детали «вал-шестерня привода насоса» работает следующим образом. Заготовку детали устанавливают на призму и закрепляют ее положение прихватами. Под давлением масла в полости цилиндра поршень сдвигается вправо чем давит на правый прихват. Таким образом прихват прижимает заготовку к призме что не позволяет ей сместиться во время фрезерования шпоночного паза детали «вал-шестерня привода насоса». Усилие крепления на правый прихват передается от поршня цилиндра через проушину и ось. Для разжима прихватов давление масла уменьшают при этом толкатель отходит назад и отжимает вал.
9.1 Силовой расчет приспособления.
Скорость фрезы рассчитывается по формуле (2.47):
Определяем коэффициент Кv по формуле (2.48) из [8 С.285]
Значение коэффициента Кмv рассчитаем по формуле (2.49)
Определим частоту вращения фрезы по формуле (2.50):
Уточним скорость резания по формуле (2.51):
Величины остальных составляющих силы резания найдем через окружную силу
Горизонтальная сила (подачи) .
Для закрепления заготовки используется зажимной механизм. В зажимных механизмах обычно применяются пневматические гидравлические и смешанные типы приводов.
Необходимую силу закрепления заготовки определяем по уравнению:
где: – необходимая сила крепления заготовки при учете силы резания создающая момент резания;
– необходимая сила закрепления заготовки при учете силы резания смещающая заготовку в направлении подачи.
Рисунок 2.3 – Схема зажимного механизма
Силу и определяем из условия статического равновесия заготовки находящейся под действием моментов от сил и .
Так как то с учетом коэффициента запаса
Полная сила крепления заготовки вычисляется по формуле (2.56):
Принимаем по табл. 3 [10 стр. 384] – коэффициенты трения в местах контакта заготовки с опорами и зажимным механизмом соответственно. Значение коэффициента обусловлено состоянием поверхности контакта заготовки во время фрезерования шпоночных отверстий.
Коэффициент запаса учитывающий нестабильность силовых воздействий на заготовку находим по формуле (2.57):
где: – гарантированный коэффициент запаса;
– коэффициент учитывающий вид технологической базы;
– коэффициент учитывающий увеличение сил резания вследствие затупления режущего инструмента;
– коэффициент учитывающий прерывистость резания;
– коэффициент характеризующий постоянство силы развиваемой зажимным механизмом;
– коэффициент характеризующий эргономику зажимного механизма;
– коэффициент характеризующий установку заготовки.
Так как в результате расчета то принимаем .
Из условия статического равновесия прихватов .
Сила цилиндра необходимая для закрепления заготовки равна тогда диаметр поршня цилиндра может быть рассчитан по формуле (2.58):
Решая это уравнение относительно получаем по формуле (2.59):
где: – рабочее давление масла принимаемое в расчетах равным 1 МПа;
Определяем диаметр поршня гидроцилиндра:
В качестве привода для специального фрезерного приспособления выбираем гидроцилиндр по ОСТ 2 Г22-3-86 с диаметром поршня 60 мм.
Т.к. действительная сила зажима превышает необходимую силу крепления заготовки то расчет выполнен верно.
9.2 Расчет приспособления на точность получаемых размеров и точность базирования заготовки
Сборка шпоночных соединений производится по методу полной взаимозаменяемости без дополнительной доработки шпонки или паза.
Точность паза определяется точностью размеров.
а) сечение шпоночного паза
Рисунок 2.4 – Сечение шпоночного паза
При работе на настроенном оборудовании точность размеров и зависит от точности настройки режущего инструмента и от точности выполнения приспособления.
Точность элементов приспособления в направлении размера рассчитываем по формуле (2.60):
где: – операционный допуск на размер ;
– коэффициент учитывающий отклонение рассеяния значений составляющих величин от закона нормального распределения ;
– коэффициент учитывающий уменьшение погрешности базирования при работе на настроенном оборудовании;
– коэффициент учитывающий долю погрешности обработки в суммарной погрешности метода вызываемой факторами не зависящими от приспособления.
Суммарная погрешность при фрезеровании паза состоит из погрешностей:
– погрешность установки;
– погрешность настройки;
– погрешность обработки возникающей в процессе изготовления детали;
– погрешность базирования в направлении операционного размера;
– погрешность закрепления;
–погрешность зависящая от точности изготовления установочного элемента (призмы);
– погрешность износа установочного элемента.
– экономическая точность обработки ;
При установке в призму нарушается принцип единства баз и по размеру появляется погрешность (2.61):
Величину рассчитываем по формуле (2.62):
где: – поправочный коэффициент учитывающий вид материала заготовки для стали .
– непостоянство силы зажима определяем используя формулу (2.63):
Учитывая что определяем погрешность по формуле (2.64):
Погрешность износа установочного элемента рассчитываем по формуле (2.65):
где: – средний износ установочного элемента при базовом числе установок . ;
– коэффициент учитывающий влияние материала заготовки ;
– коэффициент учитывающий вид оборудования ;
– коэффициент учитывающий условия обработки ;
– коэффициент учитывающий число установок заготовки отличающееся от принятого N .
Определяем погрешность:
Так как т.е. – спроектированное приспособление обеспечивает требуемую точность получения заданного размера.
10 Автоматическое проектирование технологического процесса изготовления детали или средств технологического оснащения
10.1 Использование САЕ систем для решения технологических задач
Построение маршрута технологического процесса производится путем ввода параметров обработки. На рисунке 2.5 представлен пример ввода параметров токарной обработки детали.
Таким же образом вводятся параметры других операций принятого технологического процесса обработки детали «вал-шестерня привода насоса».
Рисунок 2.5 - Ввод параметров токарной обработки детали
Таким же образом вводятся параметры для последующих этапов обработки включая механическую обработку на станке с ЧПУ.
Для создания проекта технологического перехода в системе ADEM необходимо контуры детали получающиеся в результате обработки нарастить припусками которые снимаются в процессе данного перехода.
В результате проектирования технологического перехода получаем маршрут обработки заданных поверхностей в рамках рассчитываемой операции - порядок выполнения команд и моделирования технологических объектов.
В итоге проделанной работы получаем полностью готовый технологический процесс. На все операции получен комплект технологической документации. Сформированный комплект технологической документации приведен в приложении В. ADEM позволяет быстро удобно и качественно проектировать технологические процессы и получать все регламентируемые ГОСТом технологические документы.
В результате применения систем автоматизированного проектирования сокращается время создания технологической документации при проектировании нового или модернизации технологического процесса.
10.2 Проектирование операционной технологии с разработкой управляющих программ и виртуальным моделированием обработки для станков с ЧПУ в САПР
Учебное оборудование: эмуляция станка «Siemens» программа SinuTrain Demo-Lathe 840d sl 4.7 SP3 HF1.
Создание новой программы для станка начинается с задания заготовки. Выбранная деталь изготавливается из заготовки типа «цилиндр» в связи с чем задаем ее параметры:
внешний диаметр ХА = 70 мм;
правый край заготовки ZA = 1 мм;
левый край ZI=–458 мм
глубина захвата заготовки кулачками ZB = –400 мм abs.
Параметры отвода инструмента XRA XRI ZRA и точки смены инструмента XT ZT а также скорости вращения при отводе S1 видны на рисунке 2.6.
Рисунок 2.6 - Параметры заготовки детали
Центруем деталь. Для этого кнопкой «Сверл.» вызываем диалог «Центр. сверление». Выбираем инструмент и его направление назначаем скорости подачи. Тип положение и направление обработки координаты перемещения сверла на рисунке 2.7.
Кнопкой «Обточ.» вызываем диалог «Обработка резанием» в появившемся окне задаем параметры резания детали. Так же можно выбрать графическое отображение контура детали. После введения всех параметров и выбора резца нажимаем кнопку «Перенести». Повторяем те же операции еще раз и задаем еще одну операцию резания детали. «Перенести».
Рисунок 2.7 - Центрование детали
Кнопкой «Перенести» актуализируем новые данные и возвращаемся в программу.
Далее создаем контур обработки детали. Для этого жмем «Обточ. контур» и вызываем меню «Новый контур». Вводя координаты точек получаем контур обрабатываемой детали на рисунке 2.8.
Рисунок 2.8 - Контур обрабатываемой детали
Для получившейся операции выбираем «Обраб. резанием». В появившемся окне выбираем параметры резания детали по контуру а также инструмент. Применяем изменения нажав кнопку «Перенести».
Таким же образом создаем еще один контур обработки детали. Называем его KONTUR2 открываем окно создания контура детали. После создания контура открываем окно обработки детали резанием по контуру (кнопка «Обраб. резанием») вводим параметры резания назначаем инструмент воспользовавшись встроенным каталогом резцов (список инструментов открывается по кнопке «Выбрать инструмент» - на рисунке 2.9). В случае отсутствия необходимого инструмента в каталоге есть возможность задать его вручную введя параметры инструмента в специальное поле ввода программы.
Таким же образом создаем операцию выточки детали. Выбираем кнопку «Обточ.» на панели справа выбираем «Выточка». Параметры выточки и инструмент задаются в появившемся окне аналогично операциям обработки резания.
Рисунок 2.9 - Выбор инструмента для обработки детали
После редактирования программы есть возможность запуска эмуляции обработки детали. Доступны несколько вариантов отображения модели в 3D а также масштабирование картинки и хронометража. Также возможно прослеживание траектории инструмента.
11 Технологическое проектирование производственного подразделения
11.1 Расчет количества технологического оборудования и графика
Количество оборудования по каждой операции определяется исходя из штучного времени обработки одного изделия приведенной годовой программы выпуска изделий и действительного годового фонда времени оборудования по формуле (2.66):
где Пр – расчетное число единиц оборудования;
Тшт – штучное время обработки одного изделия на
Nпр –годовая программа выпуска изделийNпр = 9000 шт.
- эффективный фонд времени работы станка для металлорежущих станков имеющих массу не более 10 т работающих в две смены из работы [7 табл. 2.1] имеем FД = 4060 часов а для металлорежущих станков массой от 10 до 100 т и работающих в две смены Fa = 3985 часов.
Проведем расчет оборудования на каждую операцию округляя число станков до требуемого количества учитывая желательную загрузку станков для крупносерийного типа производства (075-085).
Для токарной операции С ЧПУ на станке 16К20Ф3:
Принимаем один станок 16К20Ф3;
Таким же образом рассчитываем необходимое количество станков для других операций.
Рассчитаем коэффициент загрузки станков и результаты расчетов сведем в таблицу 2.7.
Коэффициент загрузки рассчитывается по формуле (2.67):
Кзаг = Пр Ппр (2.67)
где Ппр – число принятых станков.
При недостаточной загрузке оборудования оно будет догружено аналогичными операциями по обработке других деталей
Таблица 2.7 – Расчет потребности в технологическом оборудовании
Наименование оборудования
Количество оборудования шт.
Коэффициент загрузки
Фрезерно-центровальный
Продолжение таблицы 2.7 – Расчет потребности в технологическом оборудовании
Среднее значение нормативного коэффициента загрузки оборудования по участку цеха должно быть не менее 075. В нашем случае оборудование загружено достаточно.
11.2 Определение производственной площади
Производственная площадь участка занимаемая непосредственно оборудованием и рабочими местами определяется исходя из удельной площади приходящейся на один станок и числа основных станков.
Производственная площадь вычисляется по формуле (2.68):
где – удельная площадь на один средний станок м2стан.;
– удельная площадь на один крупный станок м2стан.;
– количество средних станков;
– количество крупных станков;
Производственная площадь участка вычисляется по формуле (2.69):
PПP = Σ [ ( Р1 +P2 ) CПР ] (2.69)
где Р1 = L B – удельная площадь на 1 станок;
Р2 = 6 м2 – дополнительная площадь на проходы проезды;
CПР – принятое количество станков.
PПP=Σ[(397175+6)+(2505119+6)+(2505119+6)+(37226+6)+ +(37226+6)+(1562045+6)+(2335155+6)+(1791725+6)+(49524+6)+(49524++6)+ (35623+6)] = 122595 м2
Вспомогательная площадь:
PBC = РСКЛ + PИРК + РКОНТР + PБЫТ (2.70)
где РСКЛ - площадь для складирования заготовок и готовых деталей (15% от PПP );
РИРК - площадь инструментально-раздаточной кладовой;
РКОНТР – площадь контрольного пункта
PБЫТ – площадь бытовых и конторских помещений.
РСКЛ = 015 122595 = 1839 м2
РИРК = 065 ΣCПР = 065 11 = 715 м2
Площадь контрольного пункта принимается 6 м2 на 1 контролёра:
PБЫТ = 122 CРАБ. Б. СМ = 122 8 = 976 м2
где CРАБ. Б. СМ = 8 число работающих в большую смену.
Общая площадь участка:
PY = 122595 + 1839 + 715 + 6 + 976 = 163895 м2
Объём здания участка при высоте h = 6 м:
V = PY h = 163895 6 = 98337 м3
В качестве межоперационного транспорта принимаем электротележку так как масса детали составляет всего 46 кг. Необходимое количество электротележек – 1 шт.
Цеховой склад материалов и заготовок предназначен для хранения запасов заготовок и другого материала. Площадь цехового склада вместе с заготовительным отделением составляет примерно 15 % от станочной площади:
S цех. скл. = 185 015 = 28 (м2).
Основываясь на произведённых расчётах и учитывая приведённые выше рекомендации можно выполнить планировку участка механического цеха по обработке детали «Вал-шестерня привода насоса».
11.3 Расчет численности персонала
Количество рабочих - станочников определяется расчетом по станкоемкости или по количеству станков принятому в проекте. Количество остальных рабочих определяется в процентном отношении к установленному числу рабочих-станочников (2.71)
где R - расчетное число рабочих-станочников данной профессии;
Ts - годовая станкоемкость работ для данного типа оборудования ч;
Fr - действительный годовой фонд времени рабочего ч;
км - коэффициент многостаночности т.е. количество станков на которых может одновременно работать один рабочий для универсальных токарных фрезерных и др. станков км =1 [9].
Средние значения коэффициентов загрузки оборудования Кзаг по цеху крупносерийного производства - 065 - 075.
По количеству станков число рабочих-станочников определяется по формуле (2.72):
где S - количество станков данного вида принятых в проекте;
FД - действительный годовой фонд времени работы оборудования;
Кзаг - коэффициент загрузки станков;
коэффициент многостаночности т. е. количество станков на которых может одновременно работать один рабочий для универсальных токарных фрезерных и др. станков =1;
Средние значения коэффициентов загрузки оборудования Кзаг по цеху крупносерийного производства принимают 065-075.
годовой эффективный фонд времени работы одного станка i-ой группы:
где Др - число рабочих дней в году;
mсм – число рабочих смен в сутки;
tсм – продолжительность рабочей смены;
k – плановые потери времени на ремонт % (2-8%);
n – количество наименований деталей обрабатываемых на i-ой группе оборудования.
Расчет требуемой численности рабочих оформлен в таблице 2.8.
Таблица 2.8 - Расчет требуемого числа основных рабочих
обслуживаемых станков
Количество рабочих чел
Оператор фрезерно-центровального станка
Оператор токарного станка
Продолжение таблицы 2.8 - Расчет требуемого числа основных рабочих
Оператор токарного станка с ЧПУ
Оператор фрезерного станка
Оператор зубофрезерного станка
Оператор токарно-винторезного станка
Оператор круглошлифовального станка
Оператор зубошевинговального станка
Общее число основных рабочих = 32 человека. Определение численности вспомогательных рабочих производится по нормам обслуживания. На основании этих норм составляется ведомость вспомогательных рабочих.
Rвсп = 32×3% = 096 = 1 чел.
11.4 Разработка технологической планировки
Станки на участке располагаем последовательно в соответствии с технологическими операциями. Последовательный переход детали со станка на станок образует технологическую линию движения детали.
Для проектируемого участка выбираем сетку колонн 18х12 м металлообрабатывающие станки устанавливаем в пролете в 2 ряда с поперечным проездом.
При разработке плана размещения станков следует координировать их расположение относительно колонн; этим достигается возможность точного определения места каждого станка независимо от положения других станков. При расстановке станков надо руководствоваться нормальными размерами промежутков (разрывов) между станками и поперечных направлениях и размерами расстояний от стен и колонн. Эти размеры должны гарантировать удобство выполнения работ на станках безопасность рабочих достаточную свободу движения людей и транспортных средств с грузом возможность выполнения ремонта. Разрывы между станками регламентируются правилами охраны труда и существующими нормативами которые учитывают удобство эксплуатации станков.
Характер оборудования оказывает существенное влияние на планировку. Все применяемые станки нормальной точности устанавливаем в общем помещении.
12 Обоснование предложенных в работе технологических решений
Базовый технологический процесс изготовления детали «вал-шестерня привода насоса» был разработан с четом особенностей среднесерийного производства. Степень автоматизации базового технологического процесса очень мала к тому же имелись погрешности в принятой технологической документации. Благодаря технологическим решениям представленным в данной выпускной квалификационной работе удалось увеличить степень автоматизации технологического процесса. Использование САПР позволяет автоматизировать разработку технологической документации своевременно вносить правки в чертежи деталей и приспособления что значительно сокращает рабочее время. Применение специального станочного приспособления для фрезерования шпоночных пазов детали «вал-шестерня привода насоса» позволяет увеличить степень точности изготовления детали уменьшить вспомогательное время на установку и наладку станков.
Перепланировка участка механической обработки детали «вал-шестерня привода насоса» позволяет сократить время на транспортировку детали между технологическими этапами обработки.
Качество изделия обеспечивается благодаря построению технологического процесса с постепенным переходом от черновых операций к отделочным в сочетании с различными методами термического воздействия. Оптимально подобранные схемы базирования заготовок снижают погрешность установки и повышают точность геометрических размеров и взаимного расположения поверхностей.
В выпускной квалификационной работе выполнен анализ конструкции детали включая анализ служебного назначения детали анализ технологичности конструкции. Проведен размерный анализ чертежа детали. Определен тип производства.
Разработан вариант технологического процесса изготовления детали в котором выполнены: анализ базового технологического процесса изготовления детали «вал-шестерня привода насоса» проведен анализ вариантов получения заготовки произведен расчет припусков режимов резания и норм времени.
Спроектировано специальное станочное приспособление для фрезерования шпоночных пазов что позволит повысить точность обработки и сократить рабочее время на подготовку к технологической операции.
Изменено расположение станков на участке механической обработки детали «вал-шестерня привода насоса».
В результате проведенного анализа базового технологического процесса изготовления вала-шестерни были спроектированы технологические операции такие как: фрезерно-центровальная предварительная токарная обработка чистовая токарная обработка на станке с ЧПУ обработка на станках фрезерной группы таких элементов как шпоночные пазы отверстие зубья шлицы.
В ходе работы были решены поставленные технологические задачи разработаны оптимальные условия обработки продумана эффективность в достижении лучшего результата с наименьшими производственными затратами.
Анурьев В.И. Справочник конструктора-машиностроителя. Справочник: в 3 т. В.И. Анурьев; под ред. И.Н. Жестковой. – 8-е изд. перераб и доп. – М.: Машиностроение 2001. – 2696 с.
Болдырев А.И. Основы технологии машиностроения: лабораторный практикум: учеб. пособие А.И. Болдырев А.А. Болдырев. – Воронеж: ФГБОУ ВПО «Воронежский государственный технический университет» 2011. – 181 с.
ГорбацевичА.Ф. Курсовое проектирование по технологии машиностроения: учеб. пособие А.Ф.Горбацевич В.А.Шкред.— Минск: Высш. шк. 1983— 126с.
КочергинИ.А. Конструирование и расчет металлорежущих станков и станочных комплектов. Курсовое проектирование: учеб. пособие для вузов И.А.Кочергин.— Минск: Высш. шк. 1991.— 382с.
Общемашиностроительные нормативы времени вспомогательного на обслуживание рабочего места и подготовительно-заключительного для технического нормирования станочных работ. Серийное производство.— 2-е изд.— Минск: Машиностроение 1974.— 421с.
Общемашиностроительные нормативы времени и режимов резания для нормирования работ выполняемых на универсальных и многоцелевых станках с числовым программным управлением. Часть1.— Минск: Экономика 1990.— 43с.
Справочник технолог-машиностроителя. В2т. Т.1 под ред. А.Г.Косиловой Р.К.Мещерякова.— Москва: Машиностроение1986.— 656с.
Справочник технолога-машиностроителя. В2т. Т.2 под ред. А.Г.Косиловой Р.К.Мещерякова.— Москва: Машиностроение1985.— 496с.
БабукВ.В Дипломное проектирование по технологии машиностроения: учеб. пособие В.В.Бабук.— Минск: Высш. шк.1979.—217с.
Основы проектирования цехов машиностроительных заводов: учебное пособие В.А Сай В.В Бородкин В.Б. Бочаров и др. – Воронеж: ГОУВПО «Воронежский государственный технический университет» 2010. – 176 с.
Норенков И.П. Автоматизированное проектирование: учеб. пособие И.П. Норенков. – М.: Изд-во МГТУ им. Н.Э. Баумана 2000. – 188 с. Ь
045 зубо-фрезерная_печать.frw

Нормальный исходный контур
Коэффициент смещения
Степень точности ГОСТ 1643-81
Средняя лина общей нормали
ГОСТ 3.1105-84 Форма 7
010 токарная.frw

075 сверлильная.frw

025 токарная с ЧПУ_печать.frw

060 зубо-шевинговальная.frw

Нормальный исходный контур
Коэффициент смещения
Степень точности ГОСТ 1643-81
Средняя длина общей нормали
ГОСТ 3.1105-84 Форма 7
040 Шлице-фрезерная.frw

005 фрезерно-центровальная.frw

030 токарная с ЧПУ.frw

065 кругло-шлифовальная.frw

070 токарная_печать.frw

035 фрезерная.frw

065 кругло-шлифовальная установ Б.frw

015 токарная.frw

050 токарная.frw

Маршрутная карта.doc
04110 Токарная с ЧПУИОТ №27
1148Токарный с ЧПУ 16К20Ф315292411156018297
5 4261 ФрезернаяИОТ №28
1611Вертикально-фрезерный 6Р13Ф318632411156018259
04151 ФрезернаяИОТ №27
Фрезерный станок 6Р13Ф318632411156029241
54153 ЗубофрезернаяИОТ №35
1572Зубофрезерный 5В312186324111560142142
04110 Токарно-винторезнаяИОТ №35
1111Токарно-винторезный 16К2017817411156024133
Согласно чертежу0604157 ЗубошевинговальнаяИОТ №28381574 GearSpect SBO 34012290411156014310654131 Кругло-шлифовальнаяИОТ №27381311 Кругло-шлифовальный с ЧПУ 3М151Ф218873411156010318070 4110 Токарно-винторезнаяИОТ №38381111Токарно-винторезный 16К2017817411156010320754121 Вертикально-сверлильнаяИОТ №27381213 Вертикально-сверлильный 2Н150173354111560105126080КонтрольнаяИОТ №27992145Стол ОТК
ИТК.cdw

резец канавочный ГОСТ 20872-80
Шпоночная фреза Т15К6 ГОСТ 6396-78
Сверло спиральное ГОСТ 2034-80
Шаблон для контроля паза
шероховатости. Калибр на расположение
технологическая карта
Разработка технологического процесса изготовления
детали "Вал-шестерня привода насоса
Токарный станок с ЧПУ 16К20Ф3
Патрон трехкулачковый ГОСТ 2675-80
Фрезерный станок 6Р13Ф3
Специальное станочное приспособление
Вертикально-сверлильный станок 2Н150
Зенкер ГОСТ 12489-71
Шаблоны резьбовые ГОСТ 519-77
ТЛ.doc
«Вал-шестерня привода насоса»
Комплект технологической документации
Разработка технологического процесса
изготовления детали «Вал-шестерня привода насоса»
ITK.cdw

резец канавочный ГОСТ 20872-80
Шпоночная фреза Т15К6 ГОСТ 6396-78
Сверло спиральное ГОСТ 2034-80
Шаблон для контроля паза
шероховатости. Калибр на расположение
технологическая карта
Разработка технологического процесса изготовления
детали "Вал-шестерня привода насоса
Токарный станок с ЧПУ 16К20Ф3
Патрон трехкулачковый ГОСТ 2675-80
Фрезерный станок 6Р13Ф3
Специальное станочное приспособление
Вертикально-сверлильный станок 2Н150
Зенкер ГОСТ 12489-71
Шаблоны резьбовые ГОСТ 519-77
Титульник_новый.docx
Федеральное государственное бюджетное образовательное учреждение высшего образования
«ВОРОНЕЖСКИЙ ГОСУДАРСТВЕННЫЙ ТЕХНИЧЕСКИЙ УНИВЕРСИТЕТ»
(ФГБОУ ВО «ВГТУ» ВГТУ)
Факультет заочного обучения
Кафедра технологии машиностроения
Направление подготовки специальность 15.03.05 "Конструкторско-технологическое обеспечение машиностроительных производств
Направленность «Технология машиностроения»
ВЫПУСКНАЯ КВАЛИФИКАЦИОННАЯ РАБОТА
Вишняковой Елены Павловны
(фамилия имя отчество студента)
Тема: «Разработка технологического процесса изготовления детали «Вал-шестерня привода насоса»
Состав выпускной квалификационной работы
Расчетно-пояснительная записка к выпускной квалификационной работе
Заведующий кафедрой
(наименование раздела подпись)
(наименование раздела подпись)
Студент Е.П.Вишнякова
(инициалы фамилия) (подпись)
Задание_новое.docx
Федеральное государственное бюджетное образовательное учреждение высшего образования
«ВОРОНЕЖСКИЙ ГОСУДАРСТВЕННЫЙ ТЕХНИЧЕСКИЙ УНИВЕРСИТЕТ»
(ФГБОУ ВО «ВГТУ» ВГТУ)
Факультет заочного обучения
Кафедра технологии машиностроения
Направление подготовки специальность 15.03.05 "Конструкторско-технологическое обеспечение машиностроительных производств
Направленность «Технология машиностроения»
НА ВЫПУСКНУЮ КВАЛИФИКАЦИОННУЮ РАБОТУ
Студенту Вишняковой Елене Павловне
(фамилия имя отчество)
Тема: «Разработка технологического процесса изготовления детали «Вал-шестерня привода насоса»
(по заданию какой организации выполняется работа)
(№ и дата приказа об утверждении темы)
Срок сдачи студентом выпускной квалификационной работы
Время работы в одну смену
Программа выпуска 9000 штук в год
Производство крупносерийное
Краткое содержание выпускной квалификационной работы
(перечень вопросов подлежащих разработке в выпускной квалификационной работе)
Проектно-конструкторская часть
Производственно-технологическая часть
Приложение А. Графическая часть
Приложение Б. Спецификации к графической части
Приложение В. Комплект технологической документации
Перечень графического материала (с точным указанием обязательных чертежей по разделам)
Рабочий чертеж детали
Сборочный чертеж станочного приспособления
Информационно-технологические карты
Консультанты (с указанием относящихся к ним разделов)
Задание принял к исполнению
Доклад.docx
(1 слайд – титульник)
Цель: Совершенствование базовой технологии изготовления детали “вал-шестерня привода насоса” и проектирование средств специального оснащения.
(2 слайд – рабочий чертеж)
«Вал шестерня привода насоса» представляет собой тело вращения и относится к деталям класса «Вал». По проведенному анализу деталь считается технологичной. Для ее обработки не требуются специальные режущие и мерительные инструменты.
(3 слайд - заготовка)
Для изготовления детали в качестве заготовки выбран наиболее оптимальный вариант – прокат т.к. заготовка из проката по себестоимости выгоднее чем кованая.
Для крупносерийного типа производства разработан технологический процесс обработки «Вала шестерни». Операции технологического процесса представлены на слайде.
Для принятого технологического процесса разработаны информационно-технологические карты. Пример для 3 операций представлен на слайде
(7 слайд - приспособление)
Для фрезерной операции спроектировано станочное приспособление с гидроприводом. При помощи специального станочного приспособления деталь закрепляется для фрезерования шпоночных пазов.
Поясню почему выбрала приспособление именно с гидроприводом.
Воздух сжимаем и при переменных нагрузках пневмопривод не обеспечит достаточной жёсткости закрепления.
Данный вид привода развивает меньшее усилие нежели гидропривод
Из-за мгновенного срабатывания пневмопривода прижим будет резко ударять по детали что отрицательно скажется и на заготовке и на зажимном механизме и на условиях труда рабочего. Соответственно в нашем приспособлении применим гидравлический привод.
Так же была разработана управляющая программа для токарного станка с ЧПУ. Симуляция программы и ее исходный код представлены на слайде.
(9 слайд - планировка)
В целях оптимизации была разработана планировка участка механической обработки. Это позволило сократить время на транспортировку заготовок между этапами технологического процесса.
Спасибо за внимание
Рецензия.docx
ФЕДЕРАЛЬНОЕ ГОСУДАРСТВЕННОЕ БЮДЖЕТНОЕ ОБРАЗОВАТЕЛЬНОЕ УЧРЕЖДЕНИЕ ВЫСШЕГО ОБРАЗОВАНИЯ «ВОРОНЕЖСКИЙ ГОСУДАРСТВЕННЫЙ ТЕХНИЧЕСКИЙ УНИВЕРСИТЕТ»
(ФГБОУ ВО «ВГТУ» ВГТУ)
Кафедра технология машиностроения
Направление 15.03.05 «Конструкторско-технологическое обеспечение машиностроительных производств»
(фамилия имя отчество)
на выпускную квалификационную работу
Тема выпускной квалификационной работы: «Разработка технологического процесса для изготовления детали «Вал-шестерня привода насоса»
На рецензию была представлена выпускная квалификационная работа
пояснительная записка 68 страниц
Общее заключение рецензента на выпускную квалификационную работу
Представленная работа Вишняковой Е.П. выполнена в полном соответствии с заданием в достаточной мере раскрывает сформулированную в задании тему и соответствует установленным требованиям к выпускным квалификационным работам (дипломным проектам).
Работа содержит графическую часть которая иллюстрирует особенности конструкции детали вид исходной заготовки основные операции разработанного технологического процесса необходимые технологические приспособления. Графическая часть выполнена в соответствии с требованиями ЕСКД и ЕСТД и свидетельствует о навыках и умении дипломника в разработке конструкторско- технологической документации. .
Расчетно-пояснительная записка содержит все необходимые компоненты для качественного раскрытия темы дипломного проекта: технологическую и конструкторскую части включающие анализ назначения и конструктивных особенностей детали определение типа и выбор формы организации производственного процесса анализ базового технологического процесса и постановку задач на проектирование выбор рациональной заготовки технологического оборудования маршрутного и операционного техпроцессов с базированием детали при выполнении технологических переходов расчет припусков режимов резания технического нормирования; расчеты по выбору технологической оснастки и контрольных приспособлений; методику и результаты проектирования производственного участка а также необходимые приложения. Все материалы изложены в соответствии с требованиями стандарта предприятия СТП ВГТУ. Замечания: погрешности в оформлении.
Оценка выпускной квалификационной работы
Учитывая все вышеизложенное считаю что выпускная квалификационная работа Вишняковой Е.П. заслуживает оценки «ХОРОШО» а сам дипломник присвоения ему квалификации бакалавра по направлению подготовки 15.03.05 «Конструкторско-технологическое обеспечение машиностроительных производств по профилю подготовки «Технология машиностроения».
(подпись инициалы фамилия студента)
Допускается к защите:
(подпись) (инициалы фамилия)
титул.docx
ФЕДЕРАЛЬНОЕ ГОСУДАРСТВЕННОЕ БЮДЖЕТНОЕ
ОБРАЗОВАТЕЛЬНОЕ УЧРЕЖДЕНИЕ ВЫСШЕГО ОБРАЗОВАНИЯ
«ВОРОНЕЖСКИЙ ГОСУДАРСТВЕННЫЙ ТЕХНИЧЕСКИЙ УНИВЕРСИТЕТ»
(ФГБОУ ВО «ВГТУ» ВГТУ)
Факультет заочного обучения
Кафедра Технология машиностроения .
Направление подготовки 15.03.05 "Конструкторско-технологическое обеспечение машиностроительных производств
Профиль подготовки «Технология машиностроения» .
ВЫПУСКНАЯ КВАЛИФИКАЦИОННАЯ РАБОТА
Тема: Разработка технологического процесса для изготовления детали
Подпись дата Инициалы фамилия
Зав. кафедрой И.Т. Коптев.
Руководитель Е.В.Смоленцев.
Студент группы ТМ-121 .
Логачев Сергей Владимирович .
(фамилия имя отчество)
на выпускную квалификационную работу
Тема выпускной квалификационной работы: Разработка технологического процесса для изготовления детали «Валик редуктора»
Содержание (разделы графические работы расчеты и проч.)
Графическая часть: 1) рабочий чертеж детали – 1 лист (А1); 2) чертеж заготовки с твердотельной моделью – 1 лист (А1); 3) сборочный чертеж станочного приспособления – 1 лист (А1); 4) планировка производственного участка (А1). Расчетно-пояснительная записка (А4): 1) производственно-технологическая часть; 2) проектно-конструкторская часть. Комплект карт технологического процесса.
План выполнения выпускной квалификационной работы
с « » 2017 г. по « » 2017 г.
Название элементов проектной работы
Подпись рук. консульт.
Проектно-конструкторская часть
Производственно-технологическая часть
Комплект карт технологического процесса
Руководитель выпускной квалификационной работы
Смоленцева Евгения Владиславовича
(подпись дата) (фамилия имя отчество)
Выпускная квалификационная работа закончен(а)
Пояснительная записка и все материалы просмотрены
Оценка руководителя Е.В. Смоленцев .
(подпись) (фамилия имя отчество)
Допустить студента Логачева С.В. .
к защите выпускной квалификационной работы в ГЭК
(протокол заседания кафедры № от « » 20__ г.)
Назначить защиту на « » 20__ г.
Заведующий кафедрой И.Т. Коптев .
(подпись) (инициалы фамилия)
Декан ФЗО М.Н. Подоприхин .
Чертеж фрезерного приспособления.cdw

изготовления детали "Вал-шестерня привода насоса
Заготовка с моделью.cdw

детали "Вал-шестерня привода насоса
твердотельной моделью
Сталь 40Х ГОСТ 4543-71
Твердость НВ 229 285
Предельные отклонения размеров по ГОСТ
Твердотельная модель.cdw

обработки детали "Вал-шестерня привода насоса
Твердотельная модель
детали "Вал-шестерня
Сталь 40Х ГОСТ 4543-71
Чертеж детали.cdw

Степень точности по ГОСТ 1643-72
Длинна общей нормали
Допуск на накопленную погрешность
шага по зубчатому колесу
Допуск на накопленную
погрешность К шагоов
Предельное отклонение
Допуск на погрешность направления зуба
Радиус кривизны эвольвенты
в начальной контактной точке
Обозначение чертежа сопряженного колеса
Сталь 40Х ГОСТ 4543-71
Разработка технологического процесса
обработки детали "Вал-шестерня привода насоса
Овальность и конусность поверхностей Г и Д не более 0
Неуказанные предельные отклонения размеров по ОСТ 2 Н31-2-72
Планировка участка.cdw

Разработка технологического процесса изготовления
детали "Вал-шестерня привода насоса
Рекомендуемые чертежи
- 04.06.2017
- 24.01.2023
- 24.01.2023