Разработка конструкции привода для конвейера (транспортера)




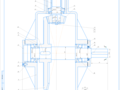
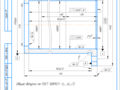
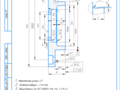
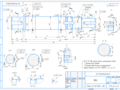
- Добавлен: 24.01.2023
- Размер: 3 MB
- Закачек: 0
Описание
Состав проекта
![]() |
![]() ![]() ![]() |
![]() ![]() ![]() |
![]() ![]() ![]() |
![]() ![]() ![]() |
![]() |
![]() |
![]() ![]() ![]() ![]() |
![]() |
![]() ![]() ![]() ![]() |
![]() ![]() ![]() ![]() |
![]() ![]() ![]() ![]() |
![]() ![]() ![]() ![]() |
![]() ![]() ![]() ![]() |
![]() |
![]() ![]() ![]() ![]() |
![]() ![]() ![]() |
![]() ![]() ![]() |
![]() ![]() ![]() |
![]() ![]() ![]() |
![]() ![]() ![]() |
![]() ![]() ![]() |
![]() ![]() ![]() |
![]() ![]() ![]() |
![]() ![]() ![]() |
![]() ![]() ![]() |
![]() ![]() ![]() |
![]() ![]() ![]() |
![]() |
![]() |
![]() |
![]() ![]() ![]() |
![]() ![]() ![]() |
![]() ![]() ![]() |
![]() ![]() ![]() |
![]() ![]() ![]() |
![]() ![]() ![]() |
Дополнительная информация
Спецификация_2(10.05).docx
КП.ПК.10.05.03.00.17
КП.ПК.10.05.03.00.18.
Прокладка регулировочная
КП.ПК.10.05.03.00.19.
КП.ПК.10.05.03.00.20
КП.ПК.10.05.03.00.21
КП.ПК.10.05.03.00.22
КП.ПК.10.05.03.00.23
КП.ПК.10.05.03.00.24
КП.ПК.10.05.03.00.25
Винт ГОСТ 11738 – 84
Гайка ГОСТ 5915 – 70
Манжета ГОСТ 8752 – 79
Подшипник ГОСТ27365–75
Шайба ГОСТ 6402 – 70
Шайба 42.21 ГОСТ11872-89
Шпонка ГОСТ 23360 – 78
Содержание.docx
1 Выбор электродвигателя
1.1 Общий КПД привода
1.2 Определение потребной мощности электродвигателя
1.3 Определение потребной частоты вращения электродвигателя
1.4 Выбор электродвигателя
2 Действительное передаточное число привода и окончательная разбивка его по ступеням
3 Определение частоты вращения валов привода
4 Определение мощностей передаваемых на валы
5 Определение крутящих моментов передаваемых на валы
Расчет конической передачи редуктора
2 Определение допускаемых контактных напряжений при расчете на выносливость
3 Определение допускаемых напряжений при действии максимальной нагрузки
4 Проектировочный расчет на контактную выносливость
5 Проверочный расчет на контактную выносливость
6 Проверочный расчет на контактную прочность при действии максимальной нагрузки
7 Определение допускаемых напряжений изгиба при расчете на выносливость
8 Определение допускаемых напряжений изгиба при расчете на прочность при изгибе максимальной нагрузки
9 Проверочный расчет на выносливость при изгибе
10 Проверочный расчет на прочность при изгибе максимальной нагрузки
11 Параметры зацепления прямозубой конической передачи
Расчет клиноременной передачи
Предварительный расчет валов. Выбор муфты
Конструктивные размеры шестерни колеса и шкива открытой передачи
Конструктивные размеры корпуса редуктора
Первый этап компоновки редуктора
Проверка долговечности подшипников
Второй этап компоновки редуктора
Проверка прочности шпоночных соединений
Уточненный расчет валов
Посадки деталей редуктора
Разработка конструкции литой плиты Литература
Введение.docx
Проект состоит из пояснительной записки спецификации и графической части.
Тематика курсового проекта – проектирование привода ленточного конвейера который состоит из двигателя открытой клиноременной передачи одноступенчатого редуктора и муфты соединяющей вал редуктора с приводным валом.
В курсовом проекте проводится энергетический и кинематический расчеты привода которые включают в себя подбор необходимого по мощности электродвигателя а также расчет мощности и крутящих моментов передаваемых валами привода.
Рассчитывается открытая клиноременная передача передающая крутящий момент от электродвигателя к валу редуктора.
Ведется проектирование редуктора которое состоит из расчета зубчатой передачи а также расчетов необходимых для изготовления редуктора заключительная часть которого состоит из эскизной компоновки.
Проводится подбор муфты для соединения вала редуктора с приводным валом.
Осуществляется выбор смазки зубчатой передачи редуктора а также подшипников качения редуктора.
В заключении составляется техническая документация на привод конвейера включающая в себя спецификацию и чертежи.
Раздел_8.docx
Cилы действующие в зацеплении:
Первый этап компановки дал:
Быстроходный вал испытывает нагрузку от ременной передачи:
Определяем реакции опор:
Рис. 5 Схема нагружения ведущего вала
Суммарные реакции опор:
Осевые составляющие радиальных реакций конических подшипников:
Осевые нагрузки подшипников ([1]с.121):
Рис.6 Схема нагружения подшипников
Рассмотрим подшипник 1 («левый»)
Так как то при расчете эквивалентной нагрузки осевые силы учитываем.
Эквивалентная нагрузка ([1]с.117):
где V=1 - коэффициент учитывающий вращение колец подшипника (вращается внутреннее кольцо) ([1]с.117)
Х= 04 - коэффициент радиальной нагрузки; ([1]с.119);
Y= 15 - коэффициент осевой нагрузки ([1]с.342-343);
45 Н - радиальная нагрузка;
42 Н - осевая нагрузка;
- коэффициент безопасности ([1]с.118);
-температурный коэффициент ([1]с.118);
Расчетная долговечность млн. об. ([1]с.117):
Расчетная долговечность ч. ([1]с.117):
Рассмотрим подшипник 2 («правый»)
Так как то при расчете эквивалентной нагрузки осевые силы не учитываем.
Х= 1- коэффициент радиальной нагрузки; ([1]с119);
Y= 0 - коэффициент осевой нагрузки ([1]с.342-343);
69 Н - радиальная нагрузка;
Найденная долговечность подшипников 7209А - приемлема.
Окружная сила 1777 Н;
Радиальная сила 157 Н;
= 656 мм 1484 мм 33102 мм.
Так как на тихоходном валу установлена муфта с торообразной оболочкой то нагрузку от муфты на вал не учитываем.
Рис. 7 Схема нагружения ведомого вала.
Изгибающие моменты относительно оси Х в сечениях 1 4 Н мм:
Изгибающие моменты относительно оси Y в сечениях 1 4 Н мм;
Суммарные изгибающие моменты в сечениях 1 4 Н мм;
Рис.8 Схема нагружения подшипников
Х= 04 - коэффициент радиальной нагрузки; ([1]с119);
Y=14 - коэффициент осевой нагрузки ([1]с.342-343);
68 Н - радиальная нагрузка;
65 Н - осевая нагрузка;
Так как e то при расчете эквивалентной нагрузки осевые силы не учитываем.
Так как то производить расчет долговечности подшипника по «второму» подшипнику не имеет смысла.
Найденная долговечность подшипников 7210А - приемлема.
Плита (10-05).cdw

КРЕПЛЕНИЯ ПЛИТЫ К ФУНДАМЕНТУ
Ось вала электродвигателя
Ось тихоходного вала редуктора
КП.ПК.10.05.04.00.00.
Литейные уклоны по ГОСТ 3212-80.
Необработанные места красить.
Отверстия М12 и М27 разметить по салазкам двигателя и
редуктору с проверкой соосности.
Общие допуски по ГОСТ 30893.1:
Шкив ведомый.cdw

Балансировать статически. Допустимый дисбаланс - 6 г
Общие допуски по ГОСТ 30893.1: Н14
Вал.cdw

Сталь 45 ГОСТ1050 - 88
* Размер для справок.
**Размер обеспечить инструментом.
Общие допуски по ГОСТ 30893.1: -t
Шестерня.cdw

Средний угол наклона зуба
Направление линии зуба
Коэффициент смещения
Угол делительного конуса
Межосевой угол передачи
Внешний окружной модуль
Внешнее конусное расстояние
Средний делительный диаметр
Обозначение чертежа сопря-
женного зубчатого колеса
КП.ПК.10.05.03.00.07
КП.ПК.10.05.03.00.23
Сталь 40Х ГОСТ 4543-71
*Размеры для справок.
Общие допуски по ГОСТ 30893.1: Н14
Крышка.cdw

Литейные радиусы - 2 мм max.
Общие допуски по ГОСТ 30893.1: Н14
Стакан.cdw

СБ (10-05).cdw

Объем масляной ванны - 1
КП.ПК.10.05.03.00.00.
Поверхности соединения "корпус - крышка" перед сборкой
покрыть уплотнительной пастой типа Герметик.
После сборки валы редуктора должны проворачиваться свободно
без стука и заедания.
Редуктор обкатать по 10-15 мин на всех режимах нагрузки.
!Титульный_КП.doc
УЧРЕЖДЕНИЕ ОБРАЗОВАНИЯ
«ГОМЕЛЬСКИЙ ГОСУДАРСТВЕННЫЙ ТЕХНИЧЕСКИЙ
УНИВЕРСИТЕТ ИМЕНИ П.О. СУХОГО»
Механико-технологический факультет
Кафедра: «Детали машин»
РАСЧЕТНО-ПОЯСНИТЕЛЬНАЯ ЗАПИСКА
по дисциплине: «Детали машин»
на тему: «Разработка конструкции привода для конвейера (транспортера)»
Исполнитель: студент гр. Л-31
Руководитель: преподаватель Столяров А.И.
Подписи членов комиссии
Раздел_10.docx
Шпонки призматические со скруглееными торцами. Размеры шпонок и пазов и длины шпонок по ГОСТ23360-78.
Материал шпонок - сталь45 нормализованная.
Напряжения смятия и условие прочности ([1]с.102);
Допускаемые напряжения смятия при стальной ступице: 100 120
при чугунной ступице: 50 70
Рассматриваем шпонку под шкивом:
Длина ступицы шкива: 45 мм.
Рассматриваем шпонку под шестерней:
b= 12 мм; h = 8 мм;
Длина ступицы шестерни: 40 мм.
Проверяем шпонку под зубчатым колесом:
b = 16 мм; h = 10 мм;
Длина ступицы зубчатого колеса 60 мм.
Условие прочности выполняется.
Проверяем шпонку под муфтой:
b = 12 мм; h = 8 мм;
Длина ступицы муфты 84 мм.
Раздел_7.docx
Выбираем способ смазывания:
-зацепление зубчатой пары - окунанием зубчатого колеса в масло;
-для подшипников - пластичный смазочный материал.
Раздельное смазывание принимаем потому что один из подшипников ведущего вала удален и это затрудняет попадание масляных брызг. Кроме того раздельная смазка предохраняет подшипники от попадания вместе с маслом частиц металла.
Камеры подшипников отделяем от внутренней полости корпуса мазеудерживающими кольцами.
Конструктивно оформляем по найденным выше размерам шестерню и колесо. Вычерчиваем их в зацеплении. Ступицу колеса выполняем симметричной относительно диска. Подшипники ведущего вала располагаем в стакане.
Намечаем для валов роликоподшипники конические однорядные cредней серии:
-для ведущего вала 7209A;
-для ведомого вала 7210A.
Таблица 6 – Характеристики подшипников.
Условное обозначение
Наносим габариты подшипников ведущего вала наметив предварительно внутреннюю стенку корпуса на расстоянии x= 10 мм от торца шестерни и отложив зазор между стенкой корпуса и торцом подшипника мм (для размещения мазеудерживающего кольца).
Определяем размер для подшипника 7209A.
Определяем размер для подшипника 7211A.
Размер от среднего диаметра шестерни до реакции подшипника 58 мм.
Размер между реакциями подшипников ведущего вала
Размещаем подшипники ведомого вала
Определяем замером размер А=107 мм.
Корпус редуктора выполним симметричным относительно оси ведущего вала и примем 107 мм.
Замером определяем расстояния:
Зазор между стенкой корпуса и крышки и зубьями колеса равный мм.
Намечаем положение шкива и замеряем расстояние от линии реакции ближнего к нему подшипника 102 мм.
Раздел_12.docx
Посадки назначаем в соответствии с указаниями данными в табл. 8.11.[1]:
-посадка зубчатого колеса и шестерни на вал -;
-подшипники на вал -;
-подшипники в корпус редуктора - ;
- посадка крышек подшипников в корпус редуктора -;
- посадка распорной втулки на вал -;
- шейку вала под подшипник выполняем с отклонением вала -;
- шейку вала под манжету выполняем с отклонением вала -
- шейку вала под муфту выполняем с отклонением вала -n6
- шейку вала под шкив открытой передачи выполняем с отклонением вала - n6
Раздел_2.docx
Пользуясь рекомендациями ([3].с.7-8) и ([3].табл.3;4) назначаем материал:
для шестерни - сталь 40Х термообработка - улучшение;
для колеса - сталь 40Х термообработка - нормализация.
Таблица 3 – Механические характеристики сталей
Предел прочности В МПа
Предел текучести Т МПа
Для обеспечения одинаковой долговечности зубьев шестерни 1 и колеса 2 прямозубых передач и ускорения их приработки должно выполняться условие ([3].ф.2.1)
2 Определение допускаемых контактных напряжений при расчете на выносливость
Допускаемые контактные напряжения МПа определяем раздельно для шестерни и колеса по формуле ([4]с.192)
где – предел контактной выносливости поверхностей зубьев соответствующий базовому числу циклов перемены напряжений МПа;
где – твердость рабочих поверхностей зубьев колеса по Бринелю;
– коэффициент безопасности; = 11;
– коэффициент долговечности учитывающий влияние срока службы и режима работы передачи
– базовое число циклов перемены напряжений соответствующее длительному пределу выносливости ([4]с.192)
– эквивалентное число циклов перемены напряжений определяемое в зависимости от характера нагружения передачи (циклограммы нагрузки); при ступенчатой циклограмме нагрузки
где – один из числа длительно действующих моментов учитываемых при расчете на выносливость Нм;
– максимальный момент учитываемый при расчете на выносливость Нм;
– частота вращения зубчатого колеса при действии момента обмин;
– продолжительность действия момента ч;
– число зацеплений зуба за один оборот равное числу колес зацепляющихся с рассчитываемым колесом;
– число часов работы передачи за расчетный срок службы
– срок службы привода;
– коэффициенты использования привода в течение года и суток.
За расчетное принимаем напряжение 4336 .
3 Определение допускаемых напряжений при действии максимальной нагрузки
Допускаемые напряжения изгиба МПа определяют раздельно для шестерни и колеса по формуле ([4]с.197)
где – предел текучести материала колеса при растяжении МПа (принимаем по таблице 3).
4 Проектировочный расчет на контактную выносливость
При расчете принимаем передачу прямозубой.
Определяем средний диаметр шестерни мм
где – вспомогательный коэффициент =770 (Нмм)13;
– вращающий момент на шестерне рассчитываемой пары
= 4 – передаточное число рассчитываемой пары;
– допускаемое контактное напряжение
- коэффициент ширины шестерни относительно среднего диаметра
- коэффициент учитывающий неравномерность распределения нагрузки по длине зуба ([3].с.27)
Окружная скорость шестерни мс ([3]с.12)
где – частота вращения вала шестерни обмин.
Так как V1= мс то передача действительно прямозубая.
Рабочая ширина венца шестерни ([3]с.12)
По ГОСТ 6636-69 принимаем = 34
Определяем углы делительных конусов:
Внешний диаметр вершин зубьев шестерни
Внешнее конусное расстояние:
Проверяем рекомендацию ([5].c.196).
Параметр = 04 выбран правильно.
Внешний окружной модуль:
По ГОСТ 9563-60 принимаем 35
Число зубьев шестерни и колеса:
Внешние диаметры вершин шестерни и колеса ([3].c.24):
Средние диаметры начальных конусов шестерни и колеса ([3].c.24).
Модуль в среднем нормальном сечении шестерни ([3].c.24)
Условное межосевое расстояние ([3].c.24):
Окружная скорость шестерни ([3].с.12)
5 Проверочный расчет на контактную выносливость
Для обеспечения контактной выносливости должно выполняться условие ([5]с.185)
где – коэффициент учитывающий форму сопряженных поверхностей зубьев
– основной угол наклона зубьев для прямозубых колес = ([3].c.23);
= – угол зацепления;
– коэффициент учитывающий механические свойства материалов сопряженных зубчатых колес([5]с.185); для стальных колес =275 Н05мм;
– коэффициент учитывающий суммарную длину контактных линий ([5]с.185);
для прямозубых передач;
где – коэффициент торцового перекрытия
- удельная расчетная окружная сила Нмм ([5]с.186);
= – коэффициент учитывающий распределение нагрузки между зубьями для косозубых передач. ([3]с.28);
= 1125 – коэффициент учитывающий неравномерность нагрузки по длине зуба; принимают в зависимости от параметра по графику ([3].с.27)
– коэффициент учитывающий динамическую нагрузку возникающую в зацеплении
535 – вращающий момент на шестерне
– удельная окружная динамическая сила Нмм ([5]с.185);
– коэффициент учитывающий влияние вида зубчатой передачи и модификации головок зубьев ([5]табл.9.9); при для прямозубых передач без модификации головки= 0006;
– коэффициент учитывающий влияние разности шагов в зацеплении зубьев шестерни и колеса; величину выбирают по таблице 9.9 [5]. = 73.
Для стальных зубчатых колес
Условие контактной выносливости соблюдается.
6 Проверочный расчет на контактную прочность при действии максимальной нагрузки
Расчет производят по формуле
где – расчетное напряжение создаваемое наибольшей нагрузкой из числа подводимых к передаче;
= 4047 – контактное напряжение при расчете на выносливость создаваемое исходной расчетной нагрузкой ;
– выбирают по каталогу электродвигателей;
= - предельное допускаемое напряжение
Условие прочности соблюдается.
7 Определение допускаемых напряжений изгиба при расчете на выносливость
Допускаемые напряжения изгиба МПа определяем раздельно для шестерни и колеса по формуле ([5].с.193)
где – предел выносливости зубьев при изгибе соответствующий базовому числу ([5].с.194) циклов перемены напряжений МПа;
– коэффициент безопасности
– коэффициент учитывающий нестабильность материала колеса и ответственность передачи; Принимаем =175;
– коэффициент учитывающий способ получения заготовки зубчатого колеса;
– коэффициент учитывающий переменность направления нагрузки на зуб при одностороннем приложении нагрузки =10;
– коэффициент долговечности
– базовое число циклов перемены напряжений ;
– эквивалентное число циклов перемены напряжений определяемое в зависимости от характера нагружения передачи;
– при ступенчатой циклограмме нагрузке
Определяем допускаемые напряжения изгиба для шестерни и колеса.
8 Определение допускаемых напряжений при расчете на прочность при изгибе максимальной нагрузкой
Допускаемые предельные напряжения МПа определяют раздельно для шестерни и колеса по формуле ([3].с.11)
где – предельные напряжения не вызывающие остаточных деформаций или хрупкого излома зуба МПа;
– коэффициент безопасности; принимаем =175;
– коэффициенты определяемые по графикам ([3].с.26) и ([3].с.27).
Допускаемые предельные напряжения
9 Проверочный расчет на выносливость при изгибе
Расчет выполняется для менее прочного зубчатого колеса т.е. для колеса у которого меньше отношение
где – допускаемое напряжение изгиба при расчете зубьев на выносливость
– коэффициент формы зуба определяемый по графикам ([5].с.184) в зависимости от эквивалентного числа зубьев колес которое определяется по формуле
где – число зубьев колеса;
– основной угол наклона зубьев косозубого колеса
Расчет ведем для колеса.
С заданной степенью вероятности усталостный излом зубьев предупреждается при выполнении условия
где – расчетное напряжение изгиба на переходной поверхности зуба МПа;
= – коэффициент учитывающий наклон зуба ([3].c.28);
– удельная расчетная окружная сила Нмм;
– вращающий момент на зубчатом колесе
– рабочая ширина зубчатого венца и диаметр начальной окружности колеса
– коэффициент учитывающий распределение нагрузки между зубьями;
– коэффициент учитывающий распределение нагрузки по длине зуба колеса; величину определяют по графику ([3].с.29); =125
- коэффициент учитывающий динамическую нагрузку возникающую в зацеплении
– удельная окружная динамическая сила Нмм
– коэффициент учитывающий влияние вида зубчатой передачи и модификации головки зуба;
=73 – принимается по таблице ([5].с.186).
Условие прочности выполняется
10 Проверочный расчет на прочность при изгибе максимальной нагрузкой
Расчет выполняют для менее прочного зубчатого колеса передачи.
С заданной степенью вероятности остаточные деформации или хрупкий излом зубьев предотвращается при выполнении условия
– напряжение изгиба при расчете на выносливость;
– выбирают по каталогу электродвигателей.
– предельное допускаемое напряжение
Условие прочности выполняется.
11. Параметры зацепления прямозубой конической передачи
где: - число зубьев плоского колеса;
Среднее конусное расстояние:
Наибольшая высота головки зуба:
Наибольшая высота ножки зуба:
Наибольшая высота зуба:
Внешний диаметр вершин:
Таблица 4 – Параметры зацепления конической передачи.
Наименование параметра
Внешний окружной модуль.
Средний окружной модуль.
Внешнее конусное расстояние
Среднее конусное расстояние
Ширина зубчатого венца
Внешний делительный диаметр
Средний делительный диаметр
Угол делительного конуса
Наибольшая высота головки зуба
Наибольшая высота ножки зуба
Наибольшая высота зуба
Внешний диаметр вершин
Раздел_4.docx
Расчет выполняем на кручение по пониженным допускаемым напряжениям.
Крутящие моменты в поперечных сечениях валов:
Диаметр выходного конца вала при допускаемом напряжении на кручение (для стали 45). ([1]с.94)
Диаметр под уплотнение:
Диаметр под резьбу: 42
Диаметр под подшипники:
Примем диаметр вала под шестерню 40 .
Рис.1 Эскиз ведущего вала
Диаметр выходного конца вала определяем при меньшем
Для соединения выходного вала редуктора с валом конвейера примем муфту упругую с торообразной оболочкой.
Муфта ГОСТ 20884-93.
Расчетный момент муфты:
где 279448 Н мм - крутящий момент на валу редуктора;
5 - коэффициент учитывающий условия эксплуатации ([1]с.272)
[T]= Н мм - допускаемое значение момента передаваемое муфтой.
Условие прочности выполняется.
Диаметр под зубчатым колесом принимаем 55
Диаметр вала под буртик колеса:
Рис.2 Эскиз ведомого вала
Рецензия_КП.doc
Соответствие курсового проекта заданию:
соответствует не соответствует
(нужное подчеркнуть)
Замечания по работе:
Выводы и оценка работы:
- уровень подготовленных материалов: высокий средний низкий
- отметка о допуске к защите: допущен не допущен
Подпись преподавателя
Раздел_9.docx
В развитие первой компоновки вычерчиваем валы с насаженными на них деталями размеры мазеудержиающих колец установочных гаек и шайб крышек и уплотнений шпонки и др.
Диаметры участков валов под зубчатые колеса подшипники и пр. Назначаем в соответствии с результатами предварительного расчета и с учетом технологических требований на обработку и сборку.
Взаимное расположение подшипников фиксируем распорной втулкой и установочной гайкой М 42 с предохранительной шайбой. Толщину стенки втулки назначаем
(01-015)d n1= (01-015)45 = 45 675 мм
Принимаем толщину стенки втулки равной 5 мм.
Мазеудержиающие кольца устанавливаем так чтобы они выходили за торец стакана или стенки корпуса на 1-2 мм.
Подшипники ведущего вала размещаем в стакане толщина стенки которого
где D-наружный диаметр подшипника.
Для фиксации наружных колец подшипников от осевых перемещений у стакана сделан упор величиной К = 5 мм.
У второго подшипника наружное кольцо фиксируем торцовым выступом крышки подшипника через распорное кольцо.
Для облегчения посадки на вал подшипника прилегающего к шестерне диаметр вала уменьшаем на 05-1 мм на длине несколько меньшей длины распорной втулки.
Очерчиваем всю внутреннюю стенку корпуса сохраняя величины зазоров принятых в первом этапе компоновки.
Для фиксации зубчатое колесо упирается с одной стороны в утолщение вала 63 мм а с другой стороны в распорное кольцо. Участок вала 55 мм делаем короче ступицы колеса чтобы распорное кольцо упиралось в торец колеса а не в буртик вала.
Переход вала от 55 мм к 50 мм смещаем на 2-3мм внутрь зубчатого колеса.
Наносим толщину стенки корпуса к= 9 мм и определяем размеры основных элементов корпуса.
Раздел_13.docx
Устанавливаем вязкость масла ([1] с. 164).
При скорости v = 113 рекомендуемая вязкость масла
Выбираем масло И - 40-А по ГОСТ 20799- 75.
Подшипники смазываем пластичной смазкой которую закладываем в подшипниковые камеры при сборке.
Сорт смазки - солидол синтетический марки С ГОСТ 4366-76 ([1]с.132).
Раздел_15.docx
Габариты плиты получаем путем обвода контуров присоединительных мест электродвигателя и редуктора (длина 923 мм ширина 448 мм).
Высота плиты является решающей для её жёсткости. На основе опыта разработки подобных конструкций рекомендуется:
Толщину стенки плиты определяем по таблице 3 [9] исходя из приведенного габарита отливки.
где приведенный габарит отливки;
Согласно рекомендации ([9] с.15) принимаем толщину стенки плиты .
Размеры платиков определяем по размерам опорных поверхностей присоединяемых деталей с припуском на неточность литья по всему контуру. Размер платиков под салазки электродвигателя . Размер платиков под редуктор . Высота платиков (без припуска на обработку). Эта высота должна обеспечивать возможность обработки на проход т.е. чтобы соседние черные поверхности вследствие неточности литья не мешали такой обработке. Резьбовые гнезда в платиках для крепления узлов М12 и М27 выполняем сквозными глубиной 2 25 диаметра болта что требует местного утолщения платика приливом с внутренней стороны плиты.
Опорную поверхность плиты выполняем в виде фланца по всему контуру с высокими пустотелыми бобышками. Ширину фланца примем 25 мм. Высокие бобышки способствуют увеличению жесткости плиты и более равномерному распределению нагрузок и деформаций от затяжки фундаментных болтов. Высоту бобышек примем 50 мм.
Диаметр (М20) и число фундаментных болтов (6) принимаем по таблице 2 ([9] с.13).
Для удобства установки плиты на фундаменте в торцовых стенках плиты делаем сквозные ниши (окно). В эти ниши заводят например концы ломиков и с их помощью передвигают плиту. В целях сокращения площади горизонтальных стенок в них выполняем окна. В нашем случае такой стенкой является верхняя стенка плиты а так же вертикальная стенка. В них выполняем четыре окна размерами и . Окна используем также при транспортировке плиты и для заливки жидкого раствора цемента (подливки) при закреплении плиты на фундаменте.
Для удобства удаления модели из формы поверхностям детали расположенным в направлении извлечения модели принимаем уклоны равные .
Вертикальную плиту для крепления электродвигателя усиливаем ребрами жесткости с двух сторон толщиной .
Литература.docx
М. Машиностроение. 1979-351с.
А.Е.Шейнблит. Курсовое проектирование деталей машин: Учебное пособие. Изд-е 2-е переработанное и дополненное . - Калининград: Янтарный сказ. 2002-454с.
В.И.Тростин. Методические указания по курсовому проектированию №980. Гомель ГПИ кафедра «Детали машин» 1988г
С.Н.Ничипорчик. Детали машин в примерах и задачах: Учебное пособие Мн. Выш. школа. 1981-432с.
А.В.Кузьмин. Курсовое проектирование деталей машин: Справочное пособие. Мн. Выш. школа 1982 - 2т.
П.Ф.Дунаев О.П.Леликов. Конструирование узлов и деталей машин: Учебное пособие для машиностроительных спец. ВУЗов. М. Высшая школа. 1985-416с.
С.А.Чернавский. Курсовое проектирование деталей машин. Учебное пособие для техн. М. Машиностроение. 1987-416с.
Полейчук В.Н. Методика расчета параметров зацепления закрытых цилиндрических и конических передач с нормализованными и улучшенными колесами: метод. Указания по курсовому проектированию по дисциплине «Детали машин» для студентов техн. специальностей днев. и заоч. форм обучения В.Н. Полейчук – Гомель : ГГТУ им. П.О.Сухого 2011 – 62с. (№188эл.)
Э.Я. Коновалов. Разработка чертежа общего вида механического привода : метод. указания к курсовому проектированию по дисциплинам «Детали машин» «Прикладная механика» и «Механика» для студентов всех специальностей днев. и заоч. форм обучения Э.Я. Коновалов В.Н. Полейчук В.М. Ткачев. – Гомель : ГГТУ им. П.О. Сухого 2010. – 50 с.
Раздел_6.docx
Толщина фланцев поясов корпуса и крышки:
-верхний пояс корпуса и пояс крышки:
Толщина ребер основания корпуса и крышки:
принимаем болты с резьбой М 27
- крепящих крышку к корпусу у подшипников:
принимаем болты с резьбой М20
- соединяющих крышку с корпусом:
принимаем болты с резьбой М14
Гнездо под подшипник
Раздел_5.docx
Так как у нас размеры шестерни не позволяют выделить ступицу то выделяем только длину посадочного участка (назовем ее )
Ступица: - диаметр наружный:
Рис.3 Эскиз конического колеса
Раздел_14.docx
Сборку производим в соответствии с чертежом общего вида редуктора начиная с узлов валов:
-в ведущий вал поз.22 устанавливаем шпонку поз.44 и напрессовываем шестерню поз.24 до упора в бурт вала и фиксируем концевой шайбой поз.39 со штифтом поз.47 и винтом поз.27. Затем насаживаем мазеудерживающее кольцо поз.15 и роликоподшипники поз.37 с распорной втулкой поз.17 предварительно нагретые в масле до температуры . Вал с подшипниками устанавливаем в стакан поз.16 и фиксируем концевой гайкой поз.34 с шайбой поз.42;
-в ведомый вал поз.26 устанавливаем шпонку поз.46 и напрессовываем зубчатое колесо поз.8 до упора в бурт вала затем надеваем распорное кольцо поз.14 и устанавливаем роликоподшипники поз.38 предварительно нагретые в масле.
Собранный быстроходный вал устанавливаем в крышку корпуса редуктора поз.4.
Собранный тихоходный вал укладываем в основание корпуса редуктора поз.9 и надеваем крышку корпуса поз.4 покрывая предварительно поверхность стыка крышки и корпуса уплотнительной пастой типа «Герметик». Для центровки устанавливаем крышку на корпус с помощью двух конических штифтов поз.48 затягиваем болты поз.28 и 29 крепящие крышку к корпусу. После этого в подшипниковые камеры закладываем пластичную смазку ставим крышки подшипников поз. 12 21 и 25 с комплектом металлических прокладок и регулируем тепловой зазор.
Перед постановкой сквозных крышек поз.21 и 25 в них запрессовываем манжеты поз.35 и 36. Проверяем проворачиванием валов отсутствие заклинивания подшипников (валы должны проворачиваться от руки) и закрепляем крышки болтами.
Далее на конец ведомого вала в шпоночную канавку закладываем шпонку поз.45 устанавливаем муфту и закрепляем ее торцовым креплением.
Затем ввертываем пробку поз.6 маслоспускного отверстия с прокладкой поз.7 и жезловый маслоуказатель поз.1. Заливаем в корпус масло через отверстие для отдушины поз.2. Устанавливаем отдушину в крышку корпуса с прокладкой поз.3.
Собранный редуктор обкатываем и подвергаем испытанию на стенде по программе устанавливаемой техническими условиями.
Раздел_11.docx
Принимаем что нормальные напряжения от изгиба изменяются по симметричному циклу а касательные от кручения - по отнулевому.
Уточненный расчет состоит в определении коэффициентов запаса прочности S для опасных сечений и сравнении их с допускаемыми значениями [S]= 25.
Расчет ведем для предположительно опасных сечений более нагруженного из валов т.е. ведомого.
Материал ведомого вала - сталь 20 термообработка - улучшение.
Предел выносливости при симметричном цикле изгиба
Предел выносливости при симметричном цикле касательных напряжений:
Рассмотрим сечение под муфтой. В этом сечении возникают только касательные напряжения. Концентрацию напряжений вызывает наличие шпоночной канавки.
- эффективный коэффициент концентрации нормальных напряжений ([1]с.98);
- эффективный коэффициент концентрации напряжений при кручении ([1]с. 98);
44 - масштабный фактор для нормальных напряжений ([1]с.99);
24 - масштабный фактор для напряжений кручения ([1]с.99);
– коэффициент зависящий от соотношения пределов выносливости при симметричном и отнулевом циклах изменения напряжений ([1]с.100);
- коэффициент характеризующий соотношение пределов выносливости при симметричном и отнулевом циклах изменения напряжений кручения ([1]с.100);
- коэффициент учитывающий влияние шероховатости поверхности ([1]с.100).
Амплитуда и среднее напряжение отнулевого цикла
при d =42 мм b = 12 мм 50 мм.
Коэффициент запаса прочности:
Рассмотрим сечение под подшипником. В этом сечении возникают только касательные напряжения. Концентрация напряжений обусловлена посадкой подшипника с гарантированным натягом.
Осевой момент сопротивления:
Полярный момент сопротивления:
Амплитуда и среднее напряжение цикла касательных напряжений
Коэффициент запаса прочности для сечения под подшипником:
Рассмотрим сечение под зубчатым колесом. Концентрацию напряжений вызывает наличие шпоночного паза
d= 55 мм b = 16 мм 6 мм;
Момент сопротивления кручению:
Момент сопротивления изгибу:
Амплитуда и среднее напряжение цикла касательных напряжений:
Амплитуда нормальных напряжений изгиба:
так как осевая нагрузка незначительная.
Коэффициент запаса прочности по нормальным напряжениям:
Коэффициент запаса прочности по касательным напряжениям:
Результирующий коэффициент запаса прочности для сечения под колесом:
Во всех случаях условие прочности выполняется: S > [S] = 25.
Раздел_1.docx
1 Выбор электродвигателя
1.1 Общий КПД привода ([3]c.4):
где м= 098 - КПД муфты ([3].с.32)
= 095 - КПД закрытой конической передачи ([3].с.32)
рп = 094 - КПД ременной передачи ([3].с.32)
пк1 =пк2 = пк3= 099 - КПД подшипников качения ([3].с.32)
1.2 Определение потребной мощности электродвигателя ([3]c.4):
1.3 Определение потребной частоты вращения электродвигателя ([3]c.5):
где = - передаточное число закрытой конической передачи ([3].с.6)
- передаточное число ременной передачи ([3].с.6)
1.4 Выбор электродвигателя
Выбираем электродвигатель типа АИР112MА8 ([8].с.49)
Таблица 1 – Технические данные электродвигателя.
Частота вращения номинальная.
2 Действительное передаточное число привода и окончательная разбивка его по ступеням ([3]c.6):
Принимаем передаточное число редуктора: = 4
Уточняем передаточное число ременной передачи:
3 Определение частоты вращения валов привода ([3]c.7):
4 Определение мощностей передаваемых на валы ([3]c.7):
5 Определение крутящих моментов передаваемых на валы ([3]c.7):
Таблица 2 – Энергетический и кинематический расчеты привода.
Спецификация_1(10.05).docx
КП.ПК.10.05.03.00.00.ПЗ.
Пояснительная записка
КП.ПК.10.05.03.01.00
КП.ПК.10.05.03.00.01
КП.ПК.10.05.03.00.02
КП.ПК.10.05.03.00.03
КП.ПК.10.05.03.00.04
КП.ПК.10.05.03.00.05
КП.ПК.10.05.03.00.06
КП.ПК.10.05.03.00.07
КП.ПК.10.05.03.00.08
КП.ПК.10.05.03.00.09
Прокладка регулировочная
КП.ПК.10.05.03.00.10
КП.ПК.10.05.03.00.11
КП.ПК.10.05.03.00.12
Кольцо мазеудерживающее
КП.ПК.10.05.03.00.13
КП.ПК.10.05.03.00.14
КП.ПК.10.05.03.00.15
Раздел_3.docx
P = 213 кВт - мощность на ведущем валу.
0 -частота вращения ведущего вала.
0 - частота вращения ведомого вала.
- передаточное отношение ременной передачи.
298 - крутящий момент на ведомом валу.
369 - крутящий момент на ведущем валу.
Из таблицы 8.12 [1] следует что мощность P = 213 кВт можно передать ремнями сечений А и Б. Целесообразно брать меньшие сечения так как при принятом диаметре меньшего шкива можно получить большие значения отношения а следовательно понизить напряжения изгиба и существенно увеличить долговечность ремней. Для определения оптимальных параметров передачи производим расчеты для всех этих сечений.
Принимаем диаметр меньшего шкива ([4]с.152) .
Определяем скорости ремня
Эти скорости не выходят из пределов рекомендуемых скоростей для рассматриваемых сечений.
Определяем диаметр ведомого шкива принимая коэффициент упругого скольжения .
По ГОСТ 1284 – 68 принимаем диаметр шкивов для сечений :
По стандартным значениям диаметров шкивов определяем действительные частоты вращения валов:
Уточняем передаточное число :
Из ГОСТ 1284 – 80 выписываем размеры сечений:
Принимаем межосевое расстояние 500 .
Определяем длину ремня ([4]с.144)
По таблице 8.2 [4] принимаем расчетную длину ближайшей к вычисленной:
Уточняем значение межосевого расстояния по стандартной длине ремня ([4]с.144).
Определяем число пробегов ремня
Определяем угол обхвата по формуле 8.2 [4]
Коэффициент угла обхвата:
Коэффициент скорости:
По таблице 8.10 [4] принимаем полезное напряжение:
Полезное напряжение при заданных условиях:
где - коэффициент динамичности ([4]табл.8.7)
Определяем нагрузку ремня:
Определяем число ремней:
Так как допускаемое число ремней то дальнейший расчет ведем по сечению Б.
Определяем силу давления ремней на вал ([4]ф.8.15):
Расчетная долговечность ([4]ф.8.16):
Максимальное напряжение ([4]ф.8.10):
Для клиновых ремней
Таблица 5 – Параметры клиноременной передачи.
Межосевое расстояние
Угол обхвата ведущего шкива
Частота пробегов ремня
Диаметр ведущего шкива
Диаметр ведомого шкива
Максимальное напряжение
Сила давления ремня на вал
Рекомендуемые чертежи
- 24.01.2023