Разработать маршрутно-операционный технологический процесс изготовления детали Шестерня, черт. ТМ6




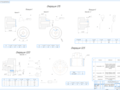
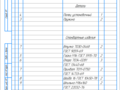
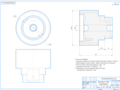
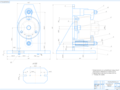
- Добавлен: 24.01.2023
- Размер: 13 MB
- Закачек: 1
Описание
Разработать маршрутно-операционный технологический процесс изготовления детали Шестерня, черт. ТМ6
Состав проекта
![]() |
![]() |
![]() ![]() ![]() |
![]() ![]() ![]() |
![]() |
![]() |
![]() ![]() ![]() ![]() |
![]() |
![]() |
![]() ![]() ![]() ![]() |
![]() |
![]() ![]() ![]() ![]() |
![]() |
![]() ![]() ![]() ![]() |
![]() |
![]() |
![]() |
![]() ![]() ![]() ![]() |
![]() ![]() ![]() ![]() |
Дополнительная информация
титульник и приложения.docx
БРЯНСКИЙ ГОСУДАРСТВЕННЫЙ ТЕХНИЧЕСКИЙ УНИВЕРСИТЕТ
Кафедра «Технология машиностроения»
По технологии машиностроения
Специальности 151001 – Технология машиностроения направления 151000- «Конструкторско-технологическое обеспечение машиностроительных производств»
На тему: Разработать маршрутно-операционный технологический процесс изготовления детали «Шестерня» черт. ТМ6
Студент Жукова В.С. Руководитель проекта
Группы В-11-КТО-1 доц.Круглов Е.И.
Брянск(Людиново) 2014.
Студенту Жуковой В.С. Группы В-11-КТО-1
Тема проекта: разработать технологический процесс и оснастку для изготовления детали «Шестерня» черт. ТМ6 для условий среднесерийного производства.
Содержание графической части проекта:
Руководитель проекта: доц. Круглов Е.И.
Штамповка 1645 l=155
Код наименование операции
Обозначение документа
Код наименование оборудования
1 01 1 005 Токарно-револьверная с ЧПУ
В340Ф30 Ток 4 1 1 1 1 22 738
1 01 2 010 Токарно-револьверная с ЧПУ
В340Ф30 Ток 4 1 1 1 1 22 15246
1 01 3 015 Многоцелевая
00VBF Фрез 4 1 1 1 1 35 12036
1 01 4 020 Многоцелевая
00VBF Фрез 4 1 1 1 1 35 7911
1 01 5 025 Зубофрезерная
А50Н Фрез 6 1 1 1 1 50 2535
Наименование детали сб. единицы или материала
1 01 6 030 Контрольная
Наименование операции
Токарно-револьверная с ЧПУ
Оборудование устройство ЧПУ
Обозначение программы
ПР. патрон трехкулачковый
Установить закрепить снять деталь
Подрезать торец выдерживая размер 066
РИ. Резец 20х12 2112-0033 ГОСТ 18871-73; СИ. Штангенциркуль ШЦ-I-250-005 ГОСТ166-89
Точить заготовку по контуру выдерживая размеры диаметр 96-087; диаметр 110-087; 112
РИ. Резец 20х12 2001-0009 Т30К4 ГОСТ 18879-73; СИ. Штангенциркуль ШЦ-I-250-005 ГОСТ166-89
Точить канавку выдерживая размеры диаметр 76-074; 04
РИ. Резец 16х20х3 2120-0002 т30К4 ГОСТ 18884-73; СИ. Штангенглубиномер ШГ-200-01 ГОСТ 162-90;
СИ. Штангенциркуль ШЦ-I-250-005 ГОСТ166-89
Подрезать торец выдерживая размер 150±05 049
Точить наружную цилиндрическую поверхность зубчатого венца однократно выдерживая размер 160-10 055
Точить торец ступицы начерно выдерживая размер 019
РИ. Резец 32х25 2102-1153 т30К4 ГОСТ 24996-81; СИ. Штангенциркуль ШЦ-I-250-005 ГОСТ166-89
Точить торцевую выточку выдерживая размеры диаметр 130+10; диаметр 72-074; 112
РИ. Резец 12х12х5 2120-0521 ГОСТ 18874-73; СИ Штангенглубиномер ШГ-200-01 ГОСТ 162-90;СИ. Штангенциркуль ШЦ-I-250-005
Точим торец ступицы начисто выдерживая размер 018
Расточить основное отверстие начерно выдерживая размер диаметр28+052 035
РИ. Резец 10х10 2142-0560 ГОСТ 10044-73; СИ. Штангенциркуль ШЦ-I-250-005 ГОСТ166-89
Расточить основное отверстие предварительно выдерживая размер диаметр 29+021 044
Расточить основное отверстие начисто выдерживая размер диаметр 296084 056
РИ. Резец 10х10 2142-0560 ГОСТ 10044-73; СИ. Нутромер НИ 18-50 ГОСТ 868-82
Расточить основное отверстие тонко выдерживая размер диаметр 30+0033 082
РИ. Резец 10х10 2142-0560 ГОСТ 10044-73; СИ. Калибр пробка D30 8133-0620 A ГОСТ 14807-69
Точить фаски 1х45по диаметру 160 036
РИ. Резец 12х12 2136-0707 ГОСТ 18875-73; СИ. Шаблон конус град
Точить фаску 1х45 по диаметрам 130 ;30 015
ПР. Приспособление специальное
Установить закрепить снять деталь.
Позиция I (шпиндельный узел вертикальный)
Фрезеровать сектор выдерживая размеры ;R45±031;60 град. 184
РИ. Фреза D45-z4 2220-0361 ВК8 ГОСТ 18372-73; СИ. Штангенциркуль ШЦ-I-250-005 ГОСТ166-89
Фрезеровать радиусную поверхность выдерживая размеры R35±031;32±031; 066
РИ. Фреза D70-z4 2220-0361 ВК8 ГОСТ 18372-73; СИ. Штангенциркуль ШЦ-I-250-005 ГОСТ166-89
Фрезеровать фаску 1х45 по диаметру 30 072
РИ. Фреза D125- z6 2252-0151 ГОСТ 7063-72; СИ. Шаблон конус град
Позиция II( повернуть шпиндельный узел на 90 град. по координате В)
Центровать отверстие выдерживая размеры диаметр 315+03; 01
РИ. Сверло D 315 2317-0166 ГОСТ 14952-75; СИ. Штангенциркуль ШЦ-I-250-005 ГОСТ166-89
Сверлить радиальное отверстие выдерживая размеры диаметром 10+036; 02
РИ. Сверло D 10 2301-0028 ГОСТ 10903-77; СИ. Штангенциркуль ШЦ-I-250-005 ГОСТ166-89
Центровать отверстие выдерживая размеры диаметр 315+03;55±031 01
Сверлить отверстие под резьбу выдерживая размеры диаметр 8 037
РИ. Сверло D8 2302-1136 ГОСТ 20696-75; СИ. Штангенциркуль ШЦ-I-250-005 ГОСТ166-89
Зенкеровать фаску 2х45 по диаметру 8 01
РИ. Зенковка D8 2353-0082 ГОСТ 14953-80; СИ. Шаблон конус град
Нарезать резьбу М10-Н7 выдерживая размер 03
РИ. Метчик М10х20 2621-2768.2 ГОСТ 3266-81; СИ. Пробка М10х20 8261-3048 7Н ГОСТ 177756-72
ПР. Оправка поводок при станке
Фрезеровать зубчатую поверхность выдерживая параметры m=50;z=30 169
РИ. Фреза D350-z10-B28 2262-0110 ГОСТ 9305-69; СИ. Головка изм 05 ИПГ-0-25 ГОСТ 6933-81;
СИ. Микрометр комбинированный; СИ. Нормалемер типа 1-2 ГОСТ 5378-88
Контролировать параметры детали по чертежу
текст проекта.docx
Исходные данные для проектирования детали9
Анализ технологичности конструкции детали10
Определение типа производства12
Технико-экономический анализ и обоснование выбора технологического процесса19
1 Выбор технологических баз20
2 Выбор маршрута обработки элементарной поверхности.21
3 Составление маршрута обработки заготовок в целом22
Разработка операции принятого варианта технологического процесса29
Выбор марки материала и конструкции режущих инструментов35
Определение припусков расчетно-аналитическим методом37
Расчет суммарной погрешности обработки42
Размерный анализ ТП и расчет технологических размерных цепей46
Определение режимов резания56
Расчет технических норм времени и трудоемкости обработки детали61
Расчет технологической себестоимости выполнения разработанной операции64
РАСЧЕТ ПРИСПОСОБЛЕНИЙ66
Обоснование необходимости разработки приспособлений66
Разработка конструкции приспособления67
1.Выбор конструкции установочных элементов и схемы зажимного устройства67
2.Расчет требуемой силы закрепления заготовки69
3.Расчет винтового зажимного механизма71
4.Расчет приспособления на точность72
5.Описание конструкции и работы приспособления74
Список используемой литературы76
Машиностроение поставляющее новую технику всем отраслям народного хозяйства определяет технический прогресс страны и оказывает решающее влияние на создание материальной базы нового общества.
Технология машиностроения - этот наука об изготовлении машин требуемого качества в установленном производственной программой количестве и в заданные сроки при наименьших затратах живого и овеществленного труда то есть при наименьшей себестоимости.
Технологическим процессом называют последовательное изменение формы размеров свойств материала ил полуфабриката в целях получения детали ил и изделия в соответствии с заданными техническими требованиями.
Технологический процесс разделяют на технологические операции- это составная часть технологического процесса выполняемая на одном рабочем месте она охватывает все действия рабочих и оборудования над объектом производства. Содержание операции может изменяться в широких пределах от работы на одном станке до работы выполняемой на автоматических линиях.
Число операции технологического процесса меняется в широких пределах от одной операции обработки деталей на токарном автомате до сотни (обработка сложных корпусных деталей).
Разрабатывать технологический процесс это значит установить порядок выполнения и содержания операции. Операция это основная часть технологического процесса. По операциям определяют трудоемкость процесса необходимые материалы необходимое количество рабочих.
При конструировании и построении машин необходимо наряду с расчетами кинематическими расчетами на прочность жесткость и износоустойчивость производить расчеты на точность.
Точность – основная характеристика деталей машин или приборов. Степень соответствия обработанной детали прототипу изображенному на чертеже. Абсолютно точно деталь изготовить невозможно так как при ее обработке возникают погрешности. На всех этапах технологического процесса изготовление машин неизбежно появляются погрешности. В результате добиться полного соответствия прототипу невозможно. Чем меньше отклонения от прототипа тем выше точность обработки. Точность изделия оказывает большое влияние на эксплуатационные характеристики изделия и прежде всего на долговечность и надежность.
С другой стороны повышение требований к изделию повышают трудоемкость ее изготовления так как приходиться в технологическом процессе вводить дополнительные операции. Так как точность обработки в производственных условиях зависит от многих факторов обработку на станках ведут не с достижимой а с так называемой экономической точностью. Под экономической точностью механической обработки понимают такую точность которая при минимальной себестоимости обработки достигается в нормальных производственных условиях предусматривающих работу на исправных станках с применением необходимых инструментов и приспособлений при нормальной затрате времени и нормальной квалификации рабочих соответствующей характеру работы. Под достижимой точностью понимают такую точность которую можно достичь при обработке в особых условиях необычных для этого производства высококвалифицированными рабочими при значительном увеличении затраты не считаясь с себестоимостью обработки.
Важно также отметить и то что сам процесс производства должен происходить при максимально безопасных условиях работы и при разработке технологического процесса технологу следует уделять на это внимание.
Характеристика узла машины и детали
Деталь представляет собой шестерню. Узел машины в который входит данная деталь может представлять собой редуктор либо этот шестерня непосредственно соединенная с каким-либо звеном машины и приводящая в движение вспомогательные агрегаты и узлы.
Деталь «Шестерня» относится представляет собой зубчатое колесо дискового типа со ступицей имеющей сложнопрофильные вырезы в виде выкружки радиусом 35 мм и в виде сектора с параметрами: наружный диаметр 96 мм внутренний радиус 45 мм угол сектора 60 град. Деталь предназначена для передачи крутящего момента от приводного механизма на исполнительный элемент. Величина передаваемого момента определяет параметр зубчатого венца – модуль равный 5. Число зубьев зубчатого венца и геометрические параметры конструктивных элементов на ступице (внутренний и наружный радиусы а так же угол сектора) определяют изменение скорости (частоты вращения) от привода к механизму. В наше случае число зубьев эвольвентного профиля по наружному венцу равно 30.
Для реализации требуемых эксплуатационных характеристик узла в конструкции детали предусмотрены следующие конструктивные элементы- выточка по торцу с формированием требуемых параметров качества опорного торца Ra 25 мкм внутренняя цилиндрическая поверхность основного отверстия диаметром 30 мм( точность 8 квалитет параметр среднего арифметического отклонения профиля от средней линии Ra 25 мкм) резьбовое отверстие М10 в торце выточки и радиальное отверстие диаметром 10 мм в ступице.
Исходные данные для проектирования детали
В результате анализа чертежа было определено что чертеж содержит все необходимые сведения о точности размеров качестве обрабатываемых поверхностей и взаимного расположения поверхностей а именно:
-допуск радиального биения цилиндрической поверхности 160 относительно базы А находящейся на поверхности отверстия 30Н8 30 мкм.
Для детали «Шестерня» основными поверхностями являются наружняя зубчатая эвольвентная поверхность с параметрами m=5 мм z=30 внутренняя цилиндрическая поверхности диаметром 30 мм а так же поверхность опорного торца диаметром 72 мм. Кроме этого необходимо получить вспомогательные конструктивные элементы: паз диаметром 76 мм осевое резьбовое отверстие и фигурные радиусные элементы на ступице.
С точки зрения механической обработки деталь имеет следующие элементы нетехнологичности: глухое резьбовое отверстие на торцевой части вала М10 фигурные радиусные вырезы на ступице и выточки по торцу. Кроме этого необходимо обеспечить высокие требования по точности внутренней цилиндрической поверхности.Наличие большого числа вспомогательных конструктивных элементов значительно повышает трудоемкость изготовления детали.
Деталь “Шестерня” позволяет вести обработку нескольких поверхностей за один установ или позицию(на многоцелевых станках и обрабатывающих центрах).
Конструкция депали обеспечивает свободный подвод и отвод инструмента и СОЖ в зону резания и из нее и отвод стружки на определенных стадиях обработки.
При механической обработке детали имеется возможность применения принципа постоянства и совмещения установочных баз.
Возможно применение высокотехнологичных методов обработки а именно обработка твердосплавными резцами.
Допуски на размеры точных поверхностей усложняют технологию производства.
С точки зрения технологичности деталь достаточно технологична ввиду своей симметрии и наличию разноуровневых наружних и внутренних поверхностей требующих обработки.
Остальные неуказанные предельные отклонения размеров по 14 квалитету точности.
Анализ технологичности конструкции детали
Качественная оценка технологичности детали
Данная деталь изготовлена из Стали 35 которая содержит углерода в пределах-032 04%;кремния – 017 037 % и магния -050 080 % процентов от общего объёма. Механические свойства стали:
Твердость НВ без термообработки ( не более ) 207 МПа; sт = 245 МПа; sв = 470 МПа.
Количественная оценка технологичности детали.
Коэффициент шероховатости где - средняя шероховатость поверхностей находящаяся по формуле
Коэффициент точности где - средняя точность поверхностей находящаяся по формуле
Определение типа производства
На данном этапе по базовому технологическому процессу либо по типовому технологическому процессу для данного класса деталей определяют коэффициент закрепления операций и в соответствии с этим делают вывод о типе производства.
Тип производства был задан в соответствии с заданием - мелкосерийный.
При выборе заготовки для заданной детали назначаем методы получения определенных конфигураций размеры допуски припуски на обработку и формируем технические условия на её изготовление. Процесс получения заготовки определяется техническими свойствами материала конструктивными формами и размерами детали и программой выпуска.
Учитывая форму и размеры детали «Шестерня» эксплуатационные условия работы марку материала (Сталь 35) а также тип производства среднесерийный возможно получение заготовки двумя способами — штамповка и круглый прокат.
При выборе вида заготовки учитываются не только эксплуатационные условия работы детали ее размеры и форму но и экономичность ее производства. Способ получения заготовки должен быть наиболее экономичным при заданном объеме выпуска деталей. Вид заготовки будет оказывать значительное влияние на характер технологического процесса трудоемкость и экономичность ее обработки.
Основным критерием выбора заготовки будет являться коэффициент использования материала.
Первый способ – горячая объёмная штамповка.
Горячая объёмная штамповка – это вид обработки материалов давлением при котором формообразование поковки из нагретой заготовки осуществляют с помощью специального инструмента – штампа. Течение металла ограничивается поверхностями плоскостей изготовленных в отдельных частях штампа так что в конечный момент штамповки они образуют единую замкнутую плоскость (ручей) по конфигурации поковки.
Штамповка имеет ряд преимуществ. Горячей объёмной штамповкой можно получать без напусков поковки сложной конфигурации которые другим способом изготовить без напусков нельзя при этом допуски на штамповочную поковку минимальны. В следствии этого значительно сокращается объём последующей механической обработки штамповочные поковки обрабатывают только в местах сопряжения с другими деталями и эта обработка может сводиться только к шлифованию.
Производительность штамповки значительно выше – составляет десятки и сотни штамповок в час.
Размеры заготовки «вал» полученной горячей штамповкой максимально приближены к размерам готовой детали вследствие чего за счёт сокращения механической обработки снижается стоимость готового изделия.
Второй способ – круглый прокат.
Стальной прокат широко используются в машиностроительной промышленности для изготовления различного рода деталей. Он может иметь стандартные диаметры: 12.0 20.0 28.0 30.0 42.0 45.0 50.0 65.0 немереной длины. Также прокат может иметь кратную длину и изготавливаться в нагартованном состоянии.
К недостаткам получения заготовки из проката относится:
· большой расход металла;
· большие припуски на механическую обработку (примерно 15 – 25 % от массы заготовки превращается в стружку) .
Горячая объёмная штамповка:
Массу заготовки найдем по формуле где-масса готовой детали - коэффициент весовой точности. Для этого случая
С- базовая стоимость 1 т заготовок рубт;
- коэффициент доплаты за термическую обработку и очистку заготовок рубт;
- масса заготовки кг;
- коэффициент учитывающий точностные характеристики заготовок;
– коэффициент учитывающий серийность выпуска заготовок;
- стоимость 1 т отходов(стружки)руб;
– коэффициент учитывающий инфляцию.
За базовую стоимость и стоимость отходов возьмем реальную цену взятую с завода БМЗ. Тогда:
Хоть цена на заготовку из проката ниже чем цена на заготовку выполненную ГОШ мы выберем заготовку полученную горячей объемной штамповкой в открытых штампах ( облойная ) т.к. у штамповки точность получаемых размеров выше припуск на механическую обработку меньше т.е. форма заготовки более приближена к форме детали значит затраты на обработку такой заготовки будут меньше количество отходов металла так же уменьшиться. Этим мы и компенсируем высокую стоимость начальной заготовки.
Горячей объемной штамповкой в открытых штампах характеризуется тем что после заполнения металлом полости ручья штампа избыток его вытесняется в специальную полость образуя при этом отход называемый облой. Облой обрезается особыми штампами. При штамповке в открытых штампах из заготовки малой точности получают поковки высокой точности за счет различного объема облоя. Технологический процесс изготовления поковок горячими штампами состоит из следующих основных операций.:
) Резка прутков на мерные заготовки
) Очистка от окалины
Штамповку целесообразно производить на прессе так как он позволяет получить более точные заготовки благодаря отсутствию ударных нагрузок уменьшается вероятность сдвига штампов (точнее верхнего штампа относительно нижнего фиксированного положения). Вертикальный штамп имеет в нижней точке выталкиватель заготовок (пресс) что позволяет уменьшать штамповочные уклоны до 3 5° а это позволяет уменьшить припуски на обработку. Кроме того производительность пресса выше чем молота в полтора-два раза за счет сокращения ударов в каждом ручье до одного.
1 Материал Сталь 35 ГОСТ 1050 - 88;
С- 032 04; S Mn- 050 080;
Подсчитаем суммарное количество легирующих элементов:
кол.лег.эл-ов=(017+037)2+(050+080)2 = 092 %
Средне количество легирующих элементов 092 %
Мп = mзаг× Кр=1425×15 =214 кг
Расчетный коэффициент Кр = 15
Деталь изготовлена в открытом штампе. Класс точности Т4.
Где Gп- масса(объем) поковки Gф – масса (объем) фигуры в которую вписывается поковка. При вычислении отношения GпGф принимают ту из геометрических фигур масса (объем) которой наименьший. При определении размеров описывающей поковку геометрической фигуры допускается исходить из увеличения в 105 раза габаритных линейных размеров детали определяющих положение ее обработанных поверхностей.
При С =084 сложность поковки соответствует классу С1.
7 Конфигурация поверхности разъема штампа - П ( плоская)
8 Исходный индекс 12.
Расчет припусков на механическую обработку.
1 Основные припуски:
Основные припуски на размеры (на одну сторону номинального размера поковки) назначены по таблицам ГОСТа и представлены в таблице 1 «Припуски на механическую обработку».
Таб.1 «Припуски на механическую обработку».
При назначении величины припуска на поверхность положение которой определяется двумя и более размерами поковки устанавливается наибольшее значение припуска для данной поверхности.
2 Дополнительные припуски:
- смещение поковки по поверхности разъема штампа 05 мм
- отклонение от плоскостности 05 мм
- штамповочный уклон : для наружной поверхности - не более 7° принимается 3°; для внутренней - не более 7° принимается 7°.
Размеры поковки после расчета (с учетом округления размеров поковки с точностью 05 мм) и предельные отклонения размеров представлены в таблице 2 «Размеры поковки и предельные отклонения размеров».
Предельные отклонения
Таб. 2 «Размеры поковки и предельные отклонения размеров»
Впадины и углубления в поковке когда их оси параллельны направлению движения одной из подвижных частей штампа а диаметр не менее 30 мм выполняют глубиной до 08 их отверстий.
Неуказанные предельные отклонения размеров принимаются равными 15 допуска соответствующего размера поковки с равными допускаемыми отклонениями.
Величина радиуса закругления внутренних углов - 7мм.
Допускаемые отклонения по изогнутости – 1 мм.
Технико-экономический анализ и обоснование выбора технологического процесса
Основным направлением сокращения затрат вспомогательного времени является автоматизация производственных процессов. Одним из главных направлений автоматизации является применение станков с ЧПУ. Эффективность применения этих станков выражается в повышенной точности и однородности размеров и формы обрабатываемых заготовок в повышении производительности обработки связанной с уменьшением доли вспомогательного времени в снижении себестоимости обработки связанной с повышением производительности в снижении требований к квалификации станочника. Сложные дорогостоящие в изготовлении и требующие трудоемкой наладки кулачки упоры кондукторы в системах ЧПУ не требуются что значительно удешевляет и ускоряет наладку.
Поэтому станки с ЧПУ являются принципиально новыми средствами автоматизации для мелкосерийного и серийного машиностроения сочетающими в себе производительность и точность станков-автоматов с гибкостью универсального оборудования.
Для современного этапа развития станков с ЧПУ характерно резкое расширение их функциональных возможностей повышение уровня автоматизации и все более широкое применение в системах управления мощных вычислительных средств (микро-ЭВМ и микропроцессорной техники). Появилась новая разновидность металлорежущего оборудования - многоцелевые станки.
В многоцелевых станках выражен новый подход к построению технологического процесса. Они обеспечивают различными видами инструмента комплексную обработку деталей без переустановок или при минимальном их числе.
Чтобы перейти от одной технологической операции к другой приходится каждый раз освобождать деталь снимать ее со станка и транспортировать на другой станок где вновь производить установку (базирование) настройку на исходные размеры и закрепление. Каждая переустановка обрабатываемой детали непременно вносит свои погрешности в ее окончательные размеры.
Таким образом большой выбор выполняемых на одном станке разнородных операций изменяет представление о традиционных технологических группах станков.
Учитывая приведенные выше доводы можно спроектировать технологический процесс следующим образом:
За две токарные операции проведем обточку заготовки с двух сторон. Операции будем выполнять на токарном станке с ЧПУ модели 1В340Ф30. Заготовку устанавливаем в трехкулачковый патрон. На первой операции базируем заготовку по наружной цилиндрической поверхности зубчатого венца и торцу. На этой операции выполним подрезку торца и обточку заготовки по контуру с формированием наружных
цилиндрических поверхностей и получением канавки.
На второй токарной операции заготовку установим по обработанной цилиндрической поверхности диаметром 96 мм и торцу. Получим торцы по зубчатому венцу и ступице обработаем наружную поверхность под нарезание зубьев. Для обеспечения требований по шероховатости (Ra=25 мкм) торец ступицы подрезаем за два перехода. Для достижения требуемой точности и качества внутренней цилиндрической поверхности выполняем растачивание за четыре перехода - черновое получистовое чистовое и тонкое растачивание. Обрабатываем фаски.
Для получения выкружек на торце ступицы и радиального отверстия применяем сверлильно-фрезерно-расточный станок с поворотной шпиндельной головкой модели 1000VBF. Заготовку устанавливаем в специальное приспособление с базированием по опорному торцу ступицы и внутренней цилиндрической поверхности основного отверстия. Закрепляем прихватами по торцу ступени диаметром 110 мм. Фрезерованием по контору получаем сектор по диаметру 96 мм. Радиусную поверхность по диаметру 110 мм получаем с радиальной подачей фрезой диаметром 70 мм. На второй позиции (поворот фрезерной головки на 90 град.) получаем радиальное отверстие диаметром 10 мм за два перехода - центрирование для предотвращения увода сверла и сверление
Осевое резьбовое отверстие получим на многоцелевой операции выполняемой на том же станке модели 1000VBF с установкой заготовки в то же приспособление дополнительно оснащенное упором по углу поворота. Отверстие получим за 4 прохода - центрирование сверление с получением отверстия под резьбу зенкерование заборной фаски и нарезание резьбы метчиком.
Наружную зубчатую поверхность получим на зубофрезерном станке модели 53А50 червячной фрезой. Заготовку устанавливаем на оправку с передачей крутящего момента через поводок.
1 Выбор технологических баз
Технологические базы – это поверхности детали которыми она ориентируется в пространстве на станке относительно режущего инструмента. При выборе технологической базы руководствуются следующими принципами:
Принцип постоянства баз требует на большинстве операций технологического процесса в качестве технологических баз использовать одни и те же поверхности. Это обеспечит точность взаимного положения поверхностей детали. Принцип совмещения баз требует при выборе схемы базирования в качестве технологической базы использовать измерительные базы детали. Это позволяет повысить точность размеров детали.
Основной конструктивной особенностью зубчатых колес дискового типа является обеспечение концентричности внутренней цилиндрической поверхности основного отверстия и делительной окружности зубчатого венца. Кроме этого необходимо обеспечить требуемую точность и допуски отклонения от взаимного положения отдельных конструктивных элементов относительно функциональных поверхностей.
Одним из технологических методов обеспечения данных технических требований является обработка с использованием принципа периодической смены баз при котором на каждой последующей операции механической обработки заготовка базируется на более точно обработанную поверхность.
При проектировании нашего технологического процесса выбираем следующие технологические базы:
Для обработки наружных цилиндрических поверхностей ступицы- наружная поверхность зубчатого венца и опорный торец ступицы.
Для обработки поверхности зубчатого венца основного отверстия и опорного торца ступицы за один установ что обеспечит требуемые параметры точности расположения и соответственно заданную долговечность изделия- наружную обработанную поверхность ступицы и торец.
Для получения зубчатого венца и остальных конструктивных элементов детали - внутреннюю цилиндрическую поверхность основного отверстия и торец.
2 Выбор маршрута обработки элементарной поверхности.
Разработку маршрутного технологического процесса обработки детали в целом начинают с определения маршрутов обработки ее элементарных поверхностей.
На данном этапе для каждой элементарной поверхности в зависимости от предъявляемых к ней требований по точности и качеству а так же параметров точности исходной заготовки выбирают оптимальный экономически обоснованный технологический маршрут механической обработки.
Для поверхности диаметром 30Н8мм Ra=25мкм:
- 2 растачивания 2 шлифования;
- 3 растачивания 1 шлифование;
- 4 растачивания ( черновое получистовое чистовое и тонкое).
С учетом среднесерийного типа производства и рекомендаций по повышению эффективности использования станков с ЧПУ за счет концентрации переходов на одной операции выбираем третий вариант.
Для торцевой поверхности диаметром 72 мм Ra= 25 мкм:
- 1 точение одно шлифование;
- 2 точения( черновое и чистовое на станках повышенной точности).
Выбираем вариант номер два.
Перед сверлением отверстий вводим дополнительный переход для предотвращения увода сверла – центрирование специализированными центровочными сверлами.
Наружную зубчатую поверхность с параметрами m=5:z=30 получаем зубофрезерованием червячной модульной фрезой на специализированном зубофрезерном оборудовании. Обработку ведем однократным фрезерованием.
Остальные поверхности обрабатываются однократно.
3 Составление маршрута обработки заготовок в целом
На данном этапе необходимо разработать общий план обработки заготовки по операциям выбрать модель оборудования вид и тип технологической оснастки а также вид режущего инструмента и материал режущей части инструмента.
Технологический процесс обработки детали представлен в таблице:
Наименование операции
Токарно-револьвентная с ЧПУ
Установить закрепить снять деталь(наружная «черная» цилиндрическая поверхность заготовки диаметром 160 и торец- трехкулачковый патрон)
Подрезать торец выдерживая размеры
Точить заготовку по контуру выдерживая размеры диаметр
-087; диаметр 110-087;
Точить канавку выдерживая размеры диаметр 76-074;
ΣТо=066+112+04= 226 мин
Тв=065+(3*06)=245 мин
Тшт.к=(226+245)*11+2210=738 мин
Установить закрепить снять деталь(наружная цилиндрическая поверхность заготовки диаметром 96 и торец- трехкулачковый патрон)
Подрезать торец выдерживая размер 150±05
Точить наружную цилиндрическую поверхность зубчатого венца однократно выдерживая размер 160-10
Точить торец ступицы начерно выдерживая размер
Точить торцевую выточку выдерживая размеры диаметр 130+10; диаметр 72-074;
Точим торец ступицы начисто выдерживая размер
Расточить основное отверстие начерно выдерживая размер диаметр28+052
Расточить основное отверстие предварительно выдерживая размер диаметр 29+021
Расточить основное отверстие начисто выдерживая размер диаметр 296084
Расточить основное отверстие тонко выдерживая размер диаметр 30+0033
Точить фаски 1х45по диаметру 160
Точить фаску 1х45 по диаметрам 130 ;30
ΣТо=049+055+019+112+018+035+044+056+082+036+015= 521 мин
Тв=065+(10*06)=665 мин
Тшт.к=(521+665)*11+2210=15246 мин
Установить закрепить снять деталь(внутренняя цилиндрическая поверхность диаметром 30 мм и торец ступицы- палец и опорные штыри)
Позиция I(шпиндельный узел вертикальный)
Фрезеровать сектор выдерживая размеры ;R45±031;60 град.
Фрезеровать радиусную поверхность выдерживая размеры R35±031;32±031;
Фрезеровать фаску 1х45 по диаметру 30
Позиция II(повернуть шпиндельный узел на 90 град по координате В)
Центровать отверстие выдерживая размеры диаметр 315+03;
Сверлить радиальное отверстие выдерживая размеры диаметром 10+036;
ΣТо=184+066+072+01+02=352 мин
Тв=114+(2*03)+(5*05)=424 мин
Тшт.к=(352+424)*11+3510=12036 мин
Установить закрепить снять деталь(внутренняя цилиндрическая поверхность диаметром 30 мм и торец ступицы по диаметру 110 мм и торец сектора - палец опорные штыри и упор)
Центровать отверстие выдерживая размеры диаметр 315+03;55±031
Сверлить отверстие под резьбу выдерживая размеры диаметр 8
Зенкеровать фаску 2х45 по диаметру 8
Нарезать резьбу М10-Н7 выдерживая размер
ΣТо=01+037+01+03=087 мин
Тв=114+(4*05)=314 мин
Тшт.к=(087+314)*11+3510=7911 мин
Установить закрепить снять деталь(внутренняя цилиндрическая поверхность диаметром 30 мм и торец - оправка поводок при станке)
Фрезеровать зубчатую поверхность выдерживая параметры m=50;z=30
Тшт.к=(169+16)*11+5010=2535 мин
Контролировать параметры детали по чертежу
Разработка операции принятого варианта технологического процесса
Станки с ЧПУ сочетают точность специализированных станков и имеют более высокую производительность.
Область применения станков с ЧПУ достаточно широка как по характеру технологических операций так и по типам производств для которых они предназначаются.
К основным условиям целесообразности можно отнести следующие:
необходимость построения процесса по принципу концентрации операций т.е. сосредоточения возможно большего числа однотипных видов обработки на одном рабочем месте;
необходимость уменьшения доли вспомогательного времени которое затрачивается в рассматриваемой операции на приеме связанные с изменением режимов резания переходом с обработки одной поверхности на другую сменой режущего инструмента и др.;
обработку отверстий сложной геометрической формы требующих применения нескольких последовательно работающих инструментов.
До появления многоцелевых станков металлорежущие станки создавали применительно к одному из традиционных методов обработки: токарная группа станков - для токарной обработки фрезерная - для фрезерной и т.д. Поэтому технологический процесс строился таким образом что определенные технологические операции выполнялись на станках определенной технологической группы.
Чтобы перейти от одной технологической операции к другой приходится каждый раз освобождать деталь снимать ее со станка и транспортировать на другой станок где вновь производить установку (базирование) настройку на исходные размеры и закрепление. Каждая переустановка обрабатываемой детали непременно вносит свои погрешности в ее окончательные размеры. Кроме того деталь совершает сложные перемещения по цеху долго пролеживает у станков различных технологических групп в ожидании обработки.
В связи с применением таких станков значительно сокращается основное и вспомогательное время обработки т.к. будет производиться комплексная обработка детали без переустановок или при минимальном их числе.
Станок токарно-револьверный с вертикальной головкой на крестовом суппорте 1В340Ф30
Станок токарно-револьверный с вертикальной инструментальной головкой на крестовом суппорте предназначен для токарной обработки деталей с прямолинейным ступенчатым и криволинейным профилем из прутка в автоматическом цикле и из штучных заготовок — в полуавтоматическом цикле в условиях серийного и мелкосерийного производств; на нем можно производить обточку расточку проточку канавок подрезку торцов сверление зенкерование развертывание нарезку резьб плашками и метчиками а также резцом по программе.
Восьмипозиционная револьверная головка па крестовом суппорте в сочетании с однокоординатным поперечным гидрофицированным суппортом обеспечивает высокие технологические возможности станка фиксируется с помощью зубчатых полумуфт и управляется гидравликой.
Продольное и поперечное перемещения осуществляются высокомоментными двигателями постоянного тока через шариковые винтовые пары. Станок оснащен оперативной системой управления типа «Электроника НЦ-31».
Станок изготавливается в двух исполнениях:
для обработки прутковых материалов диаметром до 40 мм
для обработки штучных заготовок диаметром до 200 мм.
Станок смонтирован на жесткой литой чугунной станине с закаленными призматическими направляющими. Крестовой суппорт с восьмипозиционной револьверной головкой обеспечивает высокие технологические возможности станка. Жесткость и точность положения инструмента обеспечивается зажимом револьвентной головки на высокоточные зубчатые полумуфты. Привод главного движения состоящий из двигателя постоянного тока и ременной передачи на шкив шпинделя одновременно служащий цилиндром зажима позволяет вести высокоэффективную обработку на современных режимах. Применение в приводах подачи высокомоментальных двигателей постоянного тока и шариковых винтовых пар в комплекте с фотоимпульсными датчиками обратной связи обеспечивает высокую точность обработки. Для выгрузки из рабочей зоны готовых деталей из пруткового материала установлено разгрузочное устройство. Для поддержания прутка длинной более 1000 мм предусмотрена защитная труба с двумя стойками. Станок комплектуется транспортером для уборки стружки.
Технические характеристики станка 1В340Ф30
Наибольший диаметр заготовки устанавливаемой мм:
Наибольший диаметр обрабатываемой заготовки мм:
Расстояние от торца шпинделя до револьверной головки мм
Наибольшее поперечное перемещение револьверной головки мм
Частота вращения шпинделя обмин
Пределы подач револьверного суппорта мммин:
Для станка с поворотным патроном:
Высота зажимаемой детали мм
Расстояние от оси поворота до торца детали мм
Угол поворота детали за один рабочий ход град
Мощность электродвигателя кВт
Габаритные размеры мм:
Станок многоцелевой сверлильно-фрезерно-расточной СЧПУ 1000VBF.
Станок многоцелевой сверлильно-фрезерно-расточный с автоматической сменой инструмента (АСИ) и числовым программным управлением (ЧПУ) повышенной точности 1000VBF предназначен для комплексной обработки деталей сложной формы. Выполняет операции сверления зенкерования развертывания отверстий нарезания резьбы метчиками и фрезами а также получистое и чистое прямолинейное и контурное фрезерование деталей чистовое растачивание отверстий.
Область применения станка многоцелевого сверлильно-фрезерно-расточного с ЧПУ 1000VBF: обработка газотурбинных лопаток пресс-форм и штампов изготовление моделей и другие универсальные задачи.
- 5-осевая обработка
- Возможность оснащения различными инструментальными магазинами
- Возможность оснащения щупами для измерения детали и инструмента
- Обработка с пяти сторон без переустановки
Основные технические характеристики cтанка многоцелевого сверлильно-фрезерно-расточного с ЧПУ 1000VBF:
Размер рабочей поверхности стола мм
Количество Т-образных пазов стола
Ширина направляющего паза мм
Наибольшее расстояние от торца шпинделя до стола мм
Расстояние между Т-образными пазами стола мм
Наибольшая масса обрабатываемой детали кг
Пределы частот вращения шпинделя обмин
Номинальный крутящий момент на шпинделе Нм
Наибольшие перемещения по осям мм
- продольное перемещение колонны (Х)
- поперечное перемещение стола (Y)
- вертикальное перемещение поворотной головки (Z)
Угол поворота шпиндельной бабки (ось В) град.
Точность позиционирования по осям X Y Z ммин
Наибольшее усилие подачи по координатам Н
Диапазон рабочих подач по координатам мммин
Скорость быстрого перемещения по координатам ммин
Точность позиционирования по оси В град.
Номинальная частота вращения по оси В обмин
Номинальный крутящий момент поворота шпиндельной бабки (ось В) Нм
Инструментальный магазин
Емкость инструментального магазина
Время смены инструмента сек.
Наибольший диаметр инструмента устанавливаемого в магазине мм
Наибольшая длина инструмента устанавливаемого в шпинделе станка мм
Наибольшая масса оправки устанавливаемой в магазине кг
Характеристика электрооборудования
Номинальная мощность привода главного движения кВт
Диапазон частот вращения привода главного движения обмин
Суммарная мощность установленных на станке электродвигателей кВт
SIEMENS SINUMERIK 840D
Прочие характеристики
Габаритные размеры мм
Общая площадь станка в плане кв.м. не более (с учетом открытых дверей шкафа)
Перемещение по осям cтанка многоцелевого сверлильно-фрезерно-расточного с ЧПУ 1000VBF:
Ось Х - продольное перемещение колонны
Ось Y - поперечное перемещение стола
Ось Z - вертикальное перемещение поворотной головки
Ось B - поворот шпиндельной бабки
Выбор марки материала и конструкции режущих инструментов
При обработке Втулка на станках с ЧПУ применяют резцы с механическим креплением многогранных твердосплавных пластин. Припайка твердосплавных пластин к державке часто вызывает трещины пластин. Трещины возникают в результате дополнительных напряжений возникающих вследствие неравномерного охлаждения пластин и различного линейного расширения твердого сплава и материала державки инструмента. Температурный коэффициент линейного расширения у твердых сплавов примерно в 2 раза меньше чем у углеродистой стали. Это обстоятельство приводит к трещинам пластин и способствует их интенсивному выкрашиванию и разрушению во время работы. Наряду с образованием трещин в пластинах дополнительные напряжения вызывают отслаивание пластин что также снижает качество инструмента. К недостаткам напайных резцов относится и то что для завивания стальной стружки в спираль малого радиуса и излома ее на мелкие части необходимо либо делать на передней поверхности специальные лунки и уступы либо применять специальные стружколоматели.
Ввиду этих недостатков напайных резцов мы применяем резцы с механическим креплением многогранных твердосплавных пластин. Компактность надежность в работе удобство в обслуживании простота конструкции долговечность державок и простота их восстановления в случае повреждения или разрушения пластины удовлетворительный отвод стружки экономия в расходах на инструмент делает эти резцы применимыми для широкого внедрения. Чтобы повысить режимы резания т.е. поднять производительность применяем твердосплавные неперетачиваемые пластины с покрытием. Для чернового фрезерования и точения стали (детали Корпус) применяем твердый сплав Т5К10 а для чистовой обработки - Т15К6. Осевой и резьборезный инструмент изготавливаем из быстрорежущей стали марки Р6М5.
Форма пластины и радиус при вершине.
Взгляните сверху на инструмент- пластина имеет определенную форму и радиус при вершине. Форма пластин может быть различной в зависимости от угла при вершине находящегося в пределах от 35 до 100 град вплоть до круглых пластин. Между этими крайними случаями расположены пластины квадратной треугольной и ромбической формы с углами при вершине 55 60 и 80 град. Такое разнообразие позволяет выполнить обработку от грубой черновой до тонкой профильной с возможностью обработки труднодоступных мест.
Пластины с большими углами при вершине наряду с высокой прочностью вершины позволяют вовлекать в работу большую часть режущей кромки что может привести к возникновению вибраций и увеличению потребляемой мощности. С увеличением возможностей пластины по обработке деталей сложной формы происходит ослабление ее вершины. Необходима выбирать наиболее оптимальное решение для каждой конкретной операции.
Большое значение при выборе инструмента для точения имеет радиус при вершине поскольку его величина влияет на прочность режущей кромки и на шероховатость обрабатываемой поверхности. Существует ряд значений радиусов который начинается от минимального значения 02 мм до максимального радиуса 24 мм хотя для некоторых размеров и форм пластин используется не весь диапазон существующих радиусов.
При черновом точении радиус при вершине следует выбирать как можно больше для обеспечения максимальной прочности вершины при этом его использование не должно вызывать вибраций. На выбор радиуса также влияет величина подачи и наоборот. Чем больше радиус при вершине тем прочнее режущая кромка что позволяет вести обработку с большими подачами. Малый радиус при вершине предполагает ослабленную режущую кромку но способную выполнять более качественную обработку.
Определение припусков расчетно-аналитическим методом
Поверхность для расчета припусков: диаметр 30+0039
Припуск – слой материала удаляемый с поверхности заготовки в целях достижения заданных свойств обрабатываемой поверхности детали. Припуск на обработку поверхностей детали может быть назначен по справочным таблицам или на основе расчетно-аналитического метода. Расчетным значением припуска является минимальный припуск на обработку достаточный для устранения на выполняемом переходе погрешностей обработки и дефектов поверхностей полученных на предшествующем переходе и компенсации погрешностей возникающих на выполняемом переходе.
Минимальный припуск при обработке наружных и внутренних цилиндрических поверхностей (двусторонний припуск):
где Rz h - суммарные отклонения расположения поверхности (отклонение от параллельности перпендикулярности соосности) на предшествующем переходе; - погрешность установки заготовки на выполняемом переходе.
Отклонение расположения необходимо учитывать у заготовок (под первый технологический переход); после черновой и получистовой обработки лезвийным инструментом (под последующий технологический переход); после термической обработки. В связи с закономерным уменьшением величины при обработке поверхности за несколько переходов на стадиях чистовой и отделочной обработки ею пренебрегают.
Величину отклонений кованной заготовки при обработке в патроне определяют по формуле:
где - общее отклонение оси от прямолинейности; =;
здесь - удельная кривизна в мкм на 1 мм длины.
– смещение половинок штампа или плоскости пунсона и матрицы (для свободной ковки) по оси заготовки в результате погрешности ковки:
Черновое обтачивание. Величину остаточных пространственных отклонений определяют по уравнению:
где Кy - коэффициент уточнения.
Определим минимальные значения припусков по приведенной выше формуле.
Предварительно определив заносим минимальные значения припусков в таблицу и определяем расчетные размеры для этого прибавляем 2Zmin последнего перехода к наименьшему предельному размеру детали по чертежу и получаем расчетный размер предыдущего перехода.
Определяем наибольшие размеры для каждого технологического перехода путем прибавления к минимальному размеру допуска на переход.
Предельные значения припусков 2Zmax определяем как разность наибольших предельных размеров а 2Zmin как разность наименьших предельных размеров предшествующего и выполняемого переходов.
На основе расчета промежуточных припусков определяем предельные размеры заготовки и межоперационные размеры по всем технологическим переходам. Промежуточные расчетные размеры устанавливаем в порядке обратном ходу технологического процесса обработки этой поверхности т.е. от размера готовой детали к размеру заготовки путем последовательного прибавления (для наружных поверхностей) к исходному размеру готовой детали промежуточных припусков или путем последовательного вычитания (для внутренних поверхностей) от исходного размера готовой детали промежуточных припусков. Наименьшие (наибольшие) предельные размеры по всем технологическим переходам определяем округляя их увеличением (уменьшением) расчетных размеров. Округление производим до того знака десятичной дроби с каким дан допуск на размер для каждого перехода.
Предельные значения припусков Zmax определяем как разность наибольших (наименьших) предельных размеров и Zmin как разность наименьших (наибольших) предельных размеров предшествующего и выполняемого (выполняемого и предшествующего) переходов.
Общие припуски и определяем как сумму промежуточных припусков на обработку:
Правильность расчетов определяем по уравнениям:
где - допуски на заготовку; - допуски на деталь.
Выбираем составляющие минимального припуска для заготовки [9 стр 186]:
заготовка (штамповка)
шероховатость поверхности по десяти точкам Rz =250 мкм
глубина дефектного слоя h = 250 мкм
кривизна заготовки ΔΣ = 283 мкм
черновое точение (IT14)
шероховатость поверхности по десяти точкам Rz =50 мкм
глубина дефектного слоя h = 50 мкм
кривизна заготовки ΔΣ = 17 мкм
предварительное точение (IT12)
шероховатость поверхности по десяти точкам Rz =25 мкм
глубина дефектного слоя h = 25 мкм
кривизна заготовки ΔΣ = 1 мкм
чистовое точение (IT10)
шероховатость поверхности по десяти точкам Rz =20 мкм
глубина дефектного слоя h = 20 мкм
тонкое точение (IT8)
шероховатость поверхности по десяти точкам Rz =10 мкм
глубина дефектного слоя h = 10 мкм
кривизна заготовки ΔΣ = 0 мм
Погрешность установки заготовки на операциях [9 стр 42]:
на токарной операции = 02 мм.
Определяем расчетные значения минимального припуска:
Для чернового точения 2Z min = 1694 мм
Для чистового точения 2Z min = 0234 мм
Для тонкого точения 2Z min = 0102 мм
Определяем расчетное значение минимальных диаметров:
Для тонкого точения dmini-1 = dmini + 2Zmini = 29.957 мм
Для чистового точения dmini-1 = dmini + 2Zmini = 29855 мм
Для чернового точения dmini-1 = dmini + 2Zmini = 29621 мм
Для заготовки dmini-1 = dmini + 2Zmini =27927 мм
Определяем максимальные значения межоперационных размеров:
Для тонкого точения d max = d min + Td = 299 мм
Для чистового точения d max = d min + Td = 2961 мм
Для чернового точения d max = d min + Td = 2901 мм
Для заготовки d max = d min + Td = 264 мм
Технологический маршрут обработки элементарной поверхности
Расч. припуск 2Z min
Тонкое точение (IT8)
Расчет суммарной погрешности обработки
Суммарную погрешность будем определять на размер диаметр 30+0039
В общем случае наиболее значимыми погрешностями возникающими в процессе механической обработки являются:
- погрешности вызываемые упругими деформациями технологической системы под влиянием силы резаниямкм;
- погрешности возникающие из-за неточной настройки станкамкм;
- погрешности вызываемые размерным износом режущего инструментамкм;
- погрешность обработки вызываемая температурными деформациями технологической системымкм.
- погрешности возникающие вследствие геометрических неточностей станкамкм.
При обработке на станке ЧПУ дополнительно возникают погрешности позиционирования элементов системы и отработки программ управления.
Расчет точности (определение суммарной погрешности обработки) целесообразен в основном для операций чистовой стадии обработки т.е. при 6 11 квалитете точности.
Тогда суммарная погрешность обработки для диаметральных размеров:
где- погрешности установки заготовки;
- износ инструмента;
- упругие деформации;
- погрешности формы детали (например кривизна) с предыдущей операции.
После определения суммарной погрешности проверяется возможность обработки без брака для чего полученные значения сравнивают с допуском по чертежу.
В случае невозможности достижения требуемой точности - необходимо предложить конкретные мероприятия по снижению первичных погрешностей.
Исходные данные для расчетов:
Материал обрабатываемой заготовки- сталь
Предел прочности обрабатываемого материала – sb=470МПа
Материал режущей части инструмента- твердый сплав
Обрабатываемый диаметр 30 мм
Длина обработки 122 мм
Таблица с режимами для обработки
Определяем величину погрешности Δи (на радиус) вызванную размерным износом инструмента:
где L-длина пути резания при обработке партии N деталей определяемая как:
Дополнительный путь резания Lo=500 м соответствует начальному износу вершины резца в период приработки.
Для сплава Т30К4 относительный износ = 3 мкмкм
Определим колебание отжатий системы Δу вследствие изменения силы Ру из-за непостоянных глубин резания и податливости системы при обработке.
где -наибольшая податливость системы мкмкН
- наибольшее и наименьшее значение составляющей силы резания совпадающей с направлением выдерживаемого размера кН.
Для станка 1В340Ф30 повышенной точности наибольшее допустимое перемещение продольного суппорта под нагрузкой 55 кН составляет соответственно 350 и 220 мкм. При обработке заготовки устанавливаемой в патрон консольно минимальную податливость системы не определяют. Максимальная податливость будет возможна при положении резца в конце обработки. Исходя из этого можно принять =.
При обработке расточным резцом с большим вылетом определяем максимальную податливость державки резца:
Тогда максимальная податливость технологической системы:=63636+43004=10664 мкмкН.
Наибольшее и наименьшее нормальные составляющие усилия резания определяются согласно формулам:
Где постоянная Ср= 0243; показатели степени х = 09; у=06; n=-03; поправочный коэффициент Кр=Кмр*Кφр*Кγр*Кλр*Кгр=1.
На предшествующей операции загатовка обработана с допуском по 10 квалитетут.е. возможно колебание припуска н велечину *(IT10+IT) что для диаметра 30 мм составит (0033+0084)2=00585 мм а колебоние глубины резания составит:
t max=Zmin +00585=02585 мм
Py max=243*0258509*008506*157-03*1=0036 кН
Py min=243*0258509*008506*157-03*1=0029кН
Колебание обрабатываемого размера вследствие упругих деформаций:
Определим погрешность вызванную геометрическими неточностями станка ΣΔст:
Где С- допустимое отклонение от параллельности оси шпинделя направляющим станины в плоскости выдерживаемого размера L; l- длинна обрабатываемой поверхности.
Для токарных станков с ЧПУ повышенной точности при наибольшем диаметре обрабатываемой поверхности до 320 мм С=12 мкм на длине L= 300 мм. При длине обработкиl=122 мм:
В предположении что настройка резца на выполняемый размер производится с учетом дискретного перемещения инструмента шаговым двигателем то примем метод регулирования положения вершины резца с контролем положения резца с помощью стрелочного индикатора с ценой деления 0005 мм определим погрешность настройки в соответствии с формулой:
Где Δр- погрешность регулирования резца;
Δизм-погрешность измерения детали;
Кр=173 и Ки=10-коэффициенты учитывающее отклонения величин Δр и от нормального закона.
Для заданных условий обработки Δр=5 мкм и Δизм=10 мкм при измерении IT8 мм. Тогда погрешность настройки Δн=999 мкм
Определим температурные деформации технологической системы приняв их равными 15% от суммы остальных погрешностей:
ΣΔт=015(Δи+Δу+ΣΔст+Δн)=015*(5556+999+488+075)=3176 мкм
Определим суммарную погрешность обработки:
ΔΣ=323 мкм что не превышает заданную величину допуска поэтому возможна обработка без брака.
Размерный анализ ТП и расчет технологических размерных цепей
Размерная цепь – это замкнутый контур образованный тремя или более размерами непосредственно участвующими в решении задачи обеспечения точности замыкающего звена.
Технологические размеры цепи рассчитываются чаще всего методом полной взаимозаменяемости.
В размерной цепи замыкающим звеном является технологические требования на обеспечение работоспособности узла. Чаще всего замыкающим звеном в технологической размерной цепи является то которое получается как результат выполнения всех остальных.
Размерно-точностной анализ имеет целью: выявление схемы взаимосвязей между размерами заготовки готовой детали технологическими операционными размерами и припусками на обработку; выявление и расчет технологических размерных цепей; оценку точности принятого варианта технологического процесса изготовления детали.
Схематическое представление технологического процесса обработки детали:
Составляем размерные цепи и строим их.
Найдено 17 цепей. Точность обеспечена во всех цепях.
-я цепь: А10[217]S5[217]
Исходное уравнение: А10=S5
Замыкающее звено: A10min=1495 A10 max=1505
Неизвестное звено: S5
Расчетное уравнение: S5=A10
Так как искомое звено имеет 7 квалитет то допуск TS5=004
Окончательное уточнение с учетом вида расположения поля допуска(js):
S5min= 14998 S5max=15002
Допуск замыкающего звена: ТА10=+004=004=1(точность зам. звена обеспечена)
-я цепь: Z1min[12]S5[217]S1[117]
Исходное уравнение: +Z1min=-S5max+S1min
Замыкающее звено: Z1min=2
Уменьшающее звено: S5max=15002
Неизвестное звено: S1min
Расчетное уравнение: +S1min=+S5max+Z1min
Результат расчета неизвестного: S1min=15202
Так как искомое звено имеет 10 квалитет то допуск TS1=016
S1min= 15202 S1max=15218
Перерасчет припуска: Z1=-S5+S1
Найденный припуск: Z1min=2 Z2max=216
Допуск замыкающего звена: ТZ1=+004+016=02
-я цепь: Z7min[1718]В1[118]S1[117]
Исходное уравнение: +Z7min=+В1 min -S1 max
Замыкающее звено: Z7min=3
Уменьшающее звено: S1max=15218
Неизвестное звено: В1min
Расчетное уравнение: +В1min=+S1max+Z7min
Результат расчета неизвестного: В1min=15518
Так как искомое звено имеет 16 квалитет то допуск TВ1=25
В1min= 15518 В1max=15768
Перерасчет припуска: Z7=-S1+В1
Найденный припуск: Z1min=3 Z2max=55
Допуск замыкающего звена: ТZ7=+25+016=266
-я цепь: А1[25]S8[517]S5[217]
Исходное уравнение: +A1min=+S5 min –S8 max
Замыкающее звено: A1min=19958
Увеличивающее звено: S5 min=14998
Неизвестное звено: S8 max
Расчетное уравнение: -S8max=-S5min+A1min
Результат расчета неизвестного: S8max=130022
Так как искомое звено имеет 7 квалитет то допуск TS8=004
S8min= 129982 S8max=130022
Допуск замыкающего звена: ТA1=+004+004=008=0084
-я цепь: А2[26]S6[617]S5[217]
Исходное уравнение: +A2min=+S5 min –S6 max
Замыкающее звено: A2min=2474
Неизвестное звено: S6 max
Расчетное уравнение: -S6max=-S5min+A2min
Результат расчета неизвестного: S6max=12524
Так как искомое звено имеет 10 квалитет то допуск TS6=016
S6min= 12508 S6max=12524
Допуск замыкающего звена: ТA2=+016+004=02=052
-я цепь: А4[1217]S1[117]S4[112]
Исходное уравнение: +A4min=+S1 min –S4 max
Замыкающее звено: A4min=3469
Увеличивающее звено: S1 min=15202
Неизвестное звено: S4 max
Расчетное уравнение: -S4max=-S1min+A4min
Результат расчета неизвестного: S4max=11733
Так как искомое звено имеет 9 квалитет то допуск TS4=0087
S4min= 117243 S4max=11733
Допуск замыкающего звена: ТA4=+0087+016=0247=062
-я цепь: А5[1617]S8[517]S10[516]
Исходное уравнение: +A5min=+S8 min –S10 max
Замыкающее звено: A5min=782
Увеличивающее звено: S8 min=129982
Неизвестное звено: S10 max
Расчетное уравнение: -S10max=-S8min+A5min
Результат расчета неизвестного: S10max=122162
Так как искомое звено имеет 11 квалитет то допуск TS10=022
S10min= 121942 S10max=122162
Допуск замыкающего звена: ТA5=+022+004=026=036
-я цепь: А6[1516] S10[516]S11[515]
Исходное уравнение: +A6min=+S10 min –S11 max
Замыкающее звено: A6min=1478
Увеличивающее звено: S10 min=121942
Неизвестное звено: S11 max
Расчетное уравнение: -S11max=-S10min+A6min
Результат расчета неизвестного: S11max=107162
Так как искомое звено имеет 11 квалитет то допуск TS11=022
S11min= 106942 S11max=107162
Допуск замыкающего звена: ТA6=+022+022=044=044
-я цепь: А7[67] S13[712]S4[112] S1[117]S6[617]
Исходное уравнение: +A7min=+S4 min –S13 max+S6 min –S1 max
Замыкающее звено: A7min=2974
Увеличивающее звено: S4 min=117243
Уменьшающее звено: S1 max=15218
Увеличивающее звено: S6 min=12508
Неизвестное звено: S13 max
Расчетное уравнение: -S13max=-S4min+A7min+ S1 max- S6 min
Результат расчета неизвестного: S13max=60403
Так как искомое звено имеет 9 квалитет то допуск TS13=0074
S13min= 60329 S13max=60403
Допуск замыкающего звена: ТA7=+0074+0087+016+016=0481=052
-я цепь: А8[68] S12[812]S4[112] S1[117]S6[617]
Исходное уравнение: +A8min=+S4 min –S12 max+S6 min –S1 max
Замыкающее звено: A8min=3469
Неизвестное звено: S12 max
Расчетное уравнение: -S12max=-S4min+A8min+ S1 max- S6 min
Результат расчета неизвестного: S12max=55453
Так как искомое звено имеет 9 квалитет то допуск TS12=0074
S12min= 55379 S12max=55453
Допуск замыкающего звена: ТA8=+0074+0087+016+016=0481=062
-я цепь: Z3min[45]S8[517]S7[417]
Исходное уравнение: +Z3min=-S8max+S7min
Замыкающее звено: Z3min=05
Уменьшающее звено: S8 max=130022
Неизвестное звено: S7min
Расчетное уравнение: +S7min =+S8max+Z3min
Результат расчета неизвестного: S7min=130522
Так как искомое звено имеет 14 квалитет то допуск TS7=10
S7min= 130522 S7max=131522
Перерасчет припуска:Z3=-S8+S7
Найденный припуск: Z3min=05 Z3max=15
Допуск замыкающего звена: ТZ3=+004+1=104
-я цепь: Z5min[1213]S2[113]S4[112]
Исходное уравнение: +Z5min=-S4max+S2min
Замыкающее звено: Z5min=05
Уменьшающее звено: S4 max=11733
Неизвестное звено: S2min
Расчетное уравнение: +S2min =+S4max+Z5min
Результат расчета неизвестного: S2min=11783
Так как искомое звено имеет 14 квалитет то допуск TS2=087
S2min= 11783 S2max=1187
Перерасчет припуска:Z5=-S4+S2
Найденный припуск: Z3min=05 Z3max=137
Допуск замыкающего звена: ТZ5=+087+0087=0957
-я цепь: Z6min[1314]B2[1418]B1[118]S2[113]
Исходное уравнение: +Z6min=-B2max+B1min-S2max
Замыкающее звено: Z6min=15
Увеличивающее звено:B1min=15518
Уменьшающее звено: S2 max=1187
Неизвестное звено: B2max
Расчетное уравнение: -B2max=+Z6min-B1min+S2max
Результат расчета неизвестного: B2max =3498
Так как искомое звено имеет 16 квалитет то допуск TB2=16
B2min= 3338 B2max=3498
Перерасчет припуска:Z6=-B2+B1-S2
Найденный припуск: Z6min=15 Z6max=647
Допуск замыкающего звена: ТZ6=+16+087+25=497
-я цепь: A3[912]S4[112]S3[19]
Исходное уравнение: +Amin=-S3max+S4min
Замыкающее звено: A3min=2974
Увеличивающее звено: S4min =117243
Неизвестное звено: S3 max
Расчетное уравнение: -S3max = +A3min-S4min
Результат расчета неизвестного: S3max=87503
Так как искомое звено имеет 11 квалитет то допуск TS3=022
S3min= 87283 S3max=87503
Допуск замыкающего звена: ТA3=+022+0087=0307=052
-я цепь: А9[911] S9[511]S8[517] S1[117]S3[19]
Исходное уравнение: +A9min=+S9 min –S18max+S1 min –S3 max
Замыкающее звено: A9min=782
Уменьшающее звено: S8max = 130022
Увеличивающее звено: S1 min =15202
Уменьшающее звено: S3max=87503
Неизвестное звено: S9 min
Расчетное уравнение: +S9min=+A9min+S8max-S1min+S3max
Результат расчета неизвестного: S9min=73325
Так как искомое звено имеет 9 квалитет то допуск TS9=0074
S9min= 73325 S9max=73399
Допуск замыкающего звена: ТA9=+0074+022+004+005=0384=039
-я цепь: Z2min[34]S7[417]S1[117]B4[13]
Исходное уравнение: +Z2min=-S7max+S1min-B4max
Замыкающее звено: Z2min=15
Увеличивающее звено:S1min= 15202
Уменьшающее звено: S7 max=131522
Неизвестное звено: B4max
Расчетное уравнение: -B4max=+Z2min-S1min+S7max
Результат расчета неизвестного: B4max =18998
Так как искомое звено имеет 16 квалитет то допуск TB4=11
B4min= 17898 B4max=18998
Перерасчет припуска:Z2=-B4+S1-S7
Найденный припуск: Z2min=15 Z2max=376
Допуск замыкающего звена: ТZ2=+11+016+10=226
-я цепь: Z4min[910]B3[1014]B2[1418]B1[118]S3[19]
Исходное уравнение: +Z4min=-B3max-B2max+B1min-S3max
Замыкающее звено: Z4min=25
Уменьшающее звено: B2 max=3498
Увеличивающее звено:B1min= 15518
Уменьшающее звено: S3 max=87503
Неизвестное звено: B3max
Расчетное уравнение: -B3max=+Z4min-B1min+S3max+B2max
Результат расчета неизвестного: B3max =302
Так как искомое звено имеет 16 квалитет то допуск TB3=16
Перерасчет припуска:Z4=-B3-B2+B1-S3
Найденный припуск: Z4min=25 Z4max=842
Допуск замыкающего звена: ТZ4=+16+022+16+25=592
Полученные размеры указываем на операционных эскизах.
Определение режимов резания
Обрабатываемый диаметр 80 мм
Длинна обработки 28 мм
Выбираем глубину резания в зависимости от стадии обработки поверхности(при получении канавки глубина резания равна ширине канавки) t=3мм[9стр.266].Выбираем рабочую подачу в зависимости от глубины резания и достигаемой шероховатости поверхности S=024ммоб [9стр.267]. Рассчитаем скорость резания по зависимости [9стр.265]:
где Cvmnxy-коэффициенты учитывающее вид обработки [9стр.265]:
Т-значение стойкости инструмента для одноинструментальной обработки принимаем Т=45 мин.
Kv- коэффициент учитывающий конкретные условия обработки:
Kv=Kmv*Kpv*Kiv*Kfl*Kflv*Kr где
Kmv- коэффициент учитывающий влияние материала заготовки определяется по формуле [9стр.261]:
Kpv-коэффициент учитывающий состояние обрабатываемой поверхности равен 08.
Kiv- коэффициент учитывающий материал инструмента равен 085.
Kfl- коэффициент учитывающий влияние главного угла в плане равен 08.
Kflv- коэффициент учитывающий влияние вспомогательного угла в плане равен 08.
Kr-коэффициент учитывающий влияние радиуса при вершине инструмента равен 094.
Kv=16*08*085*08*08*094=065454
Фактическая скорость резания V=87 ммин.
Частота вращения шпинделя рассчитывается по формуле станка расчетное значение n корректируем в соответствии с рядом частот вращения шпинделя n=350 обмин.
Определяем основное время обработки То:
Расточить основное отверстие тонко выдерживая размер диаметр 30+0039
Длинна обработки 122 мм
Выбираем глубину резания в зависимости от стадии обработки поверхности t=02мм[9стр.266].Выбираем рабочую подачу в зависимости от глубины резания и достигаемой шероховатости поверхности S=0085ммоб [9стр.267]. Рассчитаем скорость резания по зависимости [9стр.265]:
Фактическая скорость резания V=157 ммин.
Частота вращения шпинделя рассчитывается по формуле станка расчетное значение n корректируем в соответствии с рядом частот вращения шпинделя n=1750 обмин.
Сверлить отверстие под резьбу выдерживая размеры диаметр 8+03655±31
Материал режущей части инструмента- быстрорежущая сталь
Диаметр сверления 8 мм
Длинна сверления 35 мм
Глубину резания для сверления отверстия в сплошном металле определяем как половина требуемого диаметра t=4мм.
Рабочую подачу выбираем в зависимости от обрабатываемого материала s=01 ммоб.
Расчитаваем скорость резания
где Cvmnqy-коэффициенты учитывающее вид обработки [9стр.278]:
Т-значение стойкости инструмента для обработки сверлами из быстрорежущей стали принимаем Т=28 мин.
Kiv- коэффициент учитывающий материал инструмента равен 1.
Klv- коэффициент учитывающий глубину сверления равен 085.
Фактическая скорость резания V=23 ммин.
Частота вращения шпинделя рассчитывается по формуле станка расчетное значение n корректируем в соответствии с рядом частот вращения шпинделя n=950 обмин.
Режимы резания на остальные переходы механической обработки определяем аналогично и указываем в бланках технологической документации.
Расчет технических норм времени и трудоемкости обработки детали
Определим нормы времени на Многоцелевую операцию 015.
В серийном производстве определяется норма штучно-калькуляционного времени:
Тп. з. - подготовительно-заключительное время мин;
n - количество деталей в партии запуска (в нашем случае 300 см вариант задания) шт;
Тшт. - норма штучного времени мин.
Тшт. =То+Тус+Тзо+Туп+ Тизм+Тоб. ст
То - основное время мин;
Т ус - время на установкуснятие детали мин;
Туп - время на приемы управления мин;
Т зо - время на закрепление и открепление детали;
Т об. ст - общее время на обслуживание рабочего места и отдыха
Тоб. ст. =Топ* (nоб. ст. 100%) где Топ - оперативное время.
nоб. ст. - затраты времени на обслуживание рабочего места %;
Время работы станка по программе управления (время цикла обработки) tп. у. равно неполному оперативному времени работы станка: tп. у. =tо+tм. в. =tоп. н.
Элементы штучного времени определяются так же как и для случаев обработки на станке с ручным управлением.
Определяем основное время по переходам:
Основное время на всю операцию:
Определяем вспомогательное время:
Так как способы установки и закрепления заготовок при обработке на станках с ЧПУ принципиально не отличаются от способов применяемых на станках с ручным управлением то tв. у. определяют по имеющимся нормативам для станков с ручным управлением (для приспособления открытого типа с винтовыми зажимными механизмами):
tв. у. = 114 мин [9 с.54]
Машинное вспомогательное время tм. в. включает комплекс приемов связанных с позиционированием (для операции 015 обработка ведется за две позиции- время поворота шпиндельного узла станка 03 мин) ускоренным перемещением рабочих органов станка подводом инструмента вдоль оси в зону обработки и последующим отводом автоматической сменой режущего инструмента из инструментального магазина (в операции 015 используется 5 инструментов - время смены инструмента 05 мин):
Определяем время обслуживания рабочего места и время на личные надобности:
В состав по организационному обслуживанию рабочего места включены: осмотр нагрев системы ЧПУ и гидросистемы опробование оборудования получение инструмента от мастера в течение смены смазывание и очистка станка в течение смены предъявление контролеру ОТК пробной детали уборка станка и рабочего места по окончанию работы.
К техническому обслуживанию рабочего места относятся: смена затупившегося инструмента коррекция инструмента на заданные размеры регулирование и подналадка станка в течение смены удаление стружки из зоны резания в процессе работы.
На обслуживание рабочего места и личные надобности отводится от 8 до 25% от оперативного времени tоп.
Штучно-калькуляционное время определяется:
Тшт.к. =Тшт+Тп. з. n мин
Тп. з. - подготовительно-заключительное время на партию мин;
n - размер партии деталей запускаемых в производство шт;
Подготовительно-заключительное время Тп. з. при обработке на станках с ЧПУ состоит из затрат времени (приемов) Тп. з.1 из затрат Тп. з.2 учитывающих дополнительные работы и времени Тп. з.3 на пробную обработку детали.
Тп. з. =Тп. з.1+Тп. з.2+Тп. з.3 [9 с.604]
В соответствии с руководящим материалом Оргстанкинпрома принята единая норма для всех станков с ЧПУ:
Тп. з.2=15 мин [1 табл.12 с.607]
Тп. з.3=8 мин [1 табл.15 с.617]
Тп. з. =12+15+8=35 мин
Нормы времени на другие операции определяем аналогично и заносим в соответствующие графы операционных карт технологической документации.
Расчет технологической себестоимости выполнения разработанной операции
Используя результаты расчета штучно - калькуляционного времени Тшт.к. на токарную операцию с ЧПУ рассчитываем технологическую себестоимость выполнения операции Соп. по зависимости:
Cоп = Зо + Зв. р + Ао + Ат. о + Pо + И + Ло + Пл + Пр. Cоп = 2686 руб
Заработная плата станочника с учетом всех видов доплат и начислений
Зо=Кц1Но. чtшт. кКм60 руб
Амортизационные отчисления от стоимости оборудования
Амортизационные отчисления от стоимости технологического оснащения приходящиеся на одну деталь при расчетном сроке службы оснастки 2 года определяются как
Ат. о=Кц2 Фт. о (2Nг) руб
Затраты на ремонт и обслуживание оборудования
Затраты на режущий инструмент отнесенные к 1 детали
Затраты на технологическую электроэнергию
Л=Кц 5ЦэNэз. оtшт. к60 руб
Затраты на содержание и амортизацию производственных площадей
Пл=Кц6НпПуКс. уtшт. к (60 Fд) руб
Исходные данные к расчёту
Штучно-калькуляционное время tшт. к мин
Количество станков обслуживаемых в смену:
РАСЧЕТ ПРИСПОСОБЛЕНИЙ
Обоснование необходимости разработки приспособлений
Интенсификация производства в машиностроении неразрывно связана с техническим перевооружением и модернизацией производства на базе применения новейших достижений науки и техники. Техническое перевооружение подготовка производства новых видов продукции машиностроения и модернизация средств производства неизбежно включают процессы проектирования средств технологического оснащения и их изготовления.
В общем объёме средств технологического оснащения примерно 50 % составляют станочные приспособления. Применение станочных приспособлений позволяет:
)надежно базировать и закреплять обрабатываемую деталь с сохранением её жесткости в процессе обработки;
)стабильно обеспечивать высокое качество обрабатываемых деталей при минимальной зависимости качества от квалификации рабочего;
)повысить производительность и облегчить условия труда рабочего в результате механизации приспособлений;
)расширить технологические возможности используемого оборудования.
Для эффективного использования станков и станочных приспособлений предъявляется ряд требований.
Для обеспечения высокой точности обработки заготовок приспособления должны быть выполнены с высокой точностью. Погрешности базирования и закрепления должны быть сведены к минимуму. Конструкция приспособления не должна быть наиболее податливым звеном системы станок-приспособление-инструмент - деталь чтобы использовать полную мощность станка на черновых операциях и обеспечивать высокую точность на чистовых операциях. Приспособление должно обеспечивать хорошую инструментальную доступность т.е. возможность подхода инструмента к как можно большему количеству поверхностей заготовки. Приспособления должны обеспечивать сокращение времени зажима-разжима заготовки. Для сокращения времени переналадки станков приспособления должны обеспечивать возможность их быстрой смены или переналадки.
Анализ разработанного проектного варианта технологического процесса механической обработки детали «Шестерня» указывает на необходимость проектирования станочного приспособления для операции 015 Многоцелевой. Обработка детали на указанной операции производиться на Многоцелевом станке модели 1000BVF.
Станочное приспособление должно обеспечивать рациональную схему базирования детали надежное ее закрепление. Кроме тог конструкция приспособления должна обеспечивать базирование и крепление его на столе станка.
В условиях среднесерийного производства широкое распространение получила система неразборных специальных приспособлений (НСП). Приспособления представляют собой необратимые конструкции не предназначенные для разборки. НСП применяются на участках производства при длительном нахождении изделия в производстве обеспечивающей эксплуатацию приспособления до физического износа. В конструкции максимально используются стандартные детали узлы и заготовки различного назначения.
Разработка конструкции приспособления
1.Выбор конструкции установочных элементов и схемы зажимного устройства
Обработка детали на данной операции производиться в приспособлении с поворотом стала станка.
Для полной ориентации в пространстве заготовку достаточно лишить пяти степеней свободы так как угловое положение заготовки не влияет на точность получения размеров на донной операции.
Заготовку устанавливаем на опоры по плоской поверхности торца(при этом заготовка лишается трех степеней свободы) и внутренней цилиндрической поверхности на короткий палец( при этом заготовка лишается двух степеней свободы).
Такая установка позволяет упростить конструкцию станочного приспособления выдерживать принцип постоянства баз и обеспечивать доступ режущего инструмента к различным поверхностям заготовки.
В качестве зажимного устройства дл условий среднесерийного производства применяем винтовой механизм. Он состоит из поворотного прихвата и гайки навинчиваемой на шпильку. Применение зажимного устройства с ручным приводом ( усилие Q создается на плече рабочим при закреплении детали) обусловлено в первую очередь тем что это упрощает удешевляет конструкцию приспособления по сравнению с использованием гидравлических и пневматических зажимных механизмов.
При закреплении детали в приспособлении должны соблюдаться основные правила:
Не должно нарушаться положение заготовки достигнутое при базировании
Закрепление должно быть надежным
Возникающее при закреплении смятие поверхности заготовки так же деформация должны быть минимально и находиться в допустимых пределах
При выборе направления зажимной силы необходимо руководствоваться следующими соображениями:
Сила должна быть направлена перпендикулярно поверхности установочных элементов
При базировании по нескольким базам сила зажима должна быть направлена на тот установочный элемент с которым заготовка имеет наибольшую площадь контакта
Таким образом согласно схеме установки сила закрепления должна предотвращать поворот заготовки под действием сил резания наибольшая из которых будет достигнута на переходе:
2.Расчет требуемой силы закрепления заготовки
Зажимные механизмы(ЗМ) станочных приспособлений предназначены для надежного закрепления предупреждающего вибрации и смещение заготовки относительно опор приспособления при обработке.
При конструировании нового станочного приспособления (СП) силу закрепления Рз находят из условия равновесия заготовки под действием сил резания тяжести трения; реакции в опорах и собственно силы закрепления. Полученное значение силы закрепления проверим из условия точности выполнения операции.
При расчетах силы закрепления следует учитывать упругую характеристику ЗМ. Самотормозящий (винтовой) ЗМ имеет линейную зависимость между приложенной силой и упругим перемещением (типI).
Формула для вычисления силы закрепления Рз заготовки:
где К-коэффициент запаса; М-момент резания Н; f1f2- коэффициенты трения с опорами и зажимным механизмом.
Сила резания определяется по формуле:
где tSzBzDn- элементы режим резания и параметры инструментов определенные ранее; Ср=30;х=086;u=1;q=086;y=072;w=0- коэффициенты дл определении силы резания; при расчете режимов резания был определен Кмр=Кр=0б68.
Таким образом М=8998 Н*мм.
Коэффициенты трения: с опорпми f1=016; с зажимным механизмом f2=02.
Коэффициент запаса К вводят в формулу для обеспечения надежногот закрепления заготовки:
К=К0*К1*К2*К3*К4*К5*К6
где К0-гарантированный коэффициент запаса равный 15;
К1- коэффициент учитывающий увеличение сил резания из-за случайных неровностей на обрабатываемых поверхностях заготовок при черновой обработке равен 12;
К2- коэффициент учитывающий увеличение сил резания вследствии затупления инструмента равен 13;
К3- коэффициент учитывающий увеличение сил резания при прерывистом резании при сверлении равен 12;
К4- коэффициент характеризующий постоянство силы развиваемой ЗМ для ЗМ с механическим приводом равен 13;
К5- коэффициент характеризующий эргономику немеханизированного ЗМ равен 10;
К6- коэффициент учитываемый только при наличии моментов стремящихся повернуть заготовку установленную плоской поверхностью равен 10.
К=15*12*13*12*13*1*1=365
R1=70мм R2=68мм- расстояние от оси до опор и др точки приложения силы закрепления.
Рз=(365*8998)(016*70+02*68)=436524 Н.
3.Расчет винтового зажимного механизма
Закрепление заготовки в проектируемом приспособлении осуществляется при помощи гайки передающей усилие закрепления через быстросъемный прихват.
Сила Рз для надежного закрепления заготовки определена выше и равна 436524 Н.
Выбираем стандартную шестигранную гайку с буртиком Dц=18 мм и метрической резьбой М12 с шагом Р=175 мм.
Материал и твердость гайки: Сталь 45 HRCэ=35-40.
Вычислим момент М который нужно приложить к винту для создания силы закрепления Р3:
М=Рз(01d2+033Dцf1)=436524*(01*10863+033*18*016)=8890684 Нмм.
4.Расчет приспособления на точность
Расчет приспособления на точность производим для проверки услвия при котором ожидаемое расчетное значение допуска Т должно быть меньше заданного [T] т.е. должно выполняться условие Т≤[T].
Анализ операционных размеров показывает что наиболее точный выдерживаемый линейный размер 45±031.
Расчетное значение допуска определяем по формуле Т=+ где
- погрешность установки мм;
- точность получения размеров по паспортным данным станка 005 мм.
Погрешность рассчитываем по формуле
где - погрешность базирования детали мм;
- погрешность закрепления детали мм;
- погрешность положения заготовки мм;
Погрешность базирования рассматриваемого размера определяем по формуле:
где ITD=0033 мм ITd=0016 мм- допуски на сопрягаемые размеры базирующего отверстия и установочного пальца;
=EI-es=0+0007=0007 мм- минимальный зазор между сопрягаемыми поверхностями;
=0517- вероятностный коэффициент.
Погрешность закрепления =0 т.к. силы закреплении перпендикулярны рассматриваемому размеру.
Погрешность положении заготовки определяем по формуле
где -погрешность вызываемая неточностью изготовления и сборки установочных элементов приспособления;
- погрешность вызываемая износом установочных элементов;
- погрешность установки приспособления на столе станка.
Принимаем =0025 мм; =002 мм.
Погрешность определяем по формуле:
N=1000- число устанавливаемых заготовок;
П1=094- критерий износостойкости;
Q=0- нагрузка на рассматриваемую опору;
L=9 мм- длина скольжения заготовки по пальцу;
=3 мин- машинное время обработки в приспособлении;
=112- коэффициент учитывающий условия обработки;
m=2248 m2=1212- экспериментальные коэффициенты.
Тогда ==0065 мм следовательно Т=о065+005=0115 мм
Условие Т≤[T] соблюдается следовательно приспособление обеспечивает точность получения рассматриваемых размеров и имеется запас точности равный 062-0115=0505 мм.
5.Описание конструкции и работы приспособления
Приспособление для обработки детали «Шестерня» состоит из корпуса с установочными элементами- пальцем и опорами.
Зажимной механизм приспособления состоит из стандартного прихвата установленного в специальную направляющую втулку и шпильки.
Базирование приспособления на столе станка производиться по двум круглым шпонкам диаметром 16 мм соответствующим присоединительным размерам стола станка.
Для установки детали в приспособление необходимо установить деталь на палец повернуть прихваты во втулке после чего затянуть прижимные гайки. Для снятия детали после обработки необходимо выполнить выше описанные действия в обратном порядке.
Конструкция приспособления проста унифицирована. Изготовление специальных деталей применяемых в приспособлении не требует применения дорогостоящих конструкционных материалов.
Курсовая работа является важной составляющей процесса подготовки квалифицированных кадров специалистов производства. В процессе курсового проектирования были закреплены углублены и обобщены знания полученные на лекционных и практических занятиях что поможет решить комплексную задачу по базовой специальности.
Эффективность применения станков с ЧПУ выражается в повышенной точности и однородности размеров и формы обрабатываемых заготовок в повышении производительности обработки. Станки с ЧПУ являются принципиально новыми средствами автоматизации для мелкосерийного и серийного машиностроения сочетающими в себе производительность и точность станков-автоматов с гибкостью универсального оборудования.
Список используемой литературы
Курсовое проектирование по технологии машиностроения Под ред. А.Ф. Горбацевича. - Минск: Высш. шк. 1983. - 256 с.
А.Ф. Чистопьян Е.Н. Фролов. Проектирование и производство заготовок. Разработка чертежа и технологии изготовления отливок и поковок: Метод. указания. - Брянск: БИТМ 1991. - 24 с.
Технологичность деталей машин: Методические указания. - Брянск: БИТМ 1990. - 7 с.
Станочное оборудование автоматизированного производства Под ред.В. В. Бушуева. - М.: Издательство “СТАНКИН” 1993. Т.1. - 582 с.
Общемашиностроительные нормативы режимов резания. - М: Машиностроение 1991. Т.1. - 635 с.
Общемашиностроительные нормативы режимов резания. - М: Машиностроение 1991. Т.2. - 302 с.
Общемашиностроительные нормативы времени вспомогательного на обслуживание рабочего места и подготовительно-заключительного для технического нормирования станочных работ. Серийное производство. - М: Машиностроение 1974. - 422 с.
Справочник технолога-машиностроителя Под ред. А.Г. Косиловой Р.К. Мещерякова. - М.: Машиностроение 1985. Т.1. - 656 с.
Справочник технолога-машиностроителя Под ред. А.Г. Косиловой Р.К. Мещерякова. - М.: Машиностроение 1985. Т.2. - 496 с.
Общемашиностроительные нормативы режимов резания. - М: НИИМАШ 1983. - 174 с.
В.С. Корсаков Основы конструирования приспособлений - М.: Машиностроение 1983. - 277 с.
Оснастка для станков с ЧПУ: Справочник - М.: Машиностроение 1983. - 203 с.
Ю.И. Кузнецов А.Р. Маслов А.Н. Байков Оснастка для станков с ЧПУ: Справочник. - 2-е изд. перераб. и доп. - М.: Машиностроение 1990. - 512с.
В.Б. Ильицкий Проектирование технологической оснастки: Учеб. пособие. - Брянск: БИТМ 1993. - 100 с.
эскиз 2.cdw

получение радиальной
поверхности ирадиального
отверстия наповерхности
Получения отверстия с резьбой
на торце зубчатого колеса
Получение зубчатого венца
Контроль размеров детали
ТМ.2014.В11КТО1.44.С.К.
Технологическая обработка
2.cdw

Неуказанные предельные отклонения размеров принимаются равными 1
соответствующего размера поковки с равными допускаемыми отклонениями.
Величина радиуса закругления внутренних углов - 7мм.
Допускаемые отклонения по изогнутости 1 мм.
Штамповочный уклон: для наружной поверхности 3град.;
для внутренней поверхности 7 град
ТМ.2014.В11КТО1.44.С.К.
Сталь 35 ГОСТ 1050-88
приспособа.cdw

относительно повершности не более 0
Перепад высот опор (поз.6) не более 0
* Размеры для справок.
ТМ.2014.В11КТО1.44.С.К.
Спецификация.spw

Шестерня (ТМ6) _ ТМ.2014.В11КТО1.44.С.К..cdw

эскиз.cdw

Рекомендуемые чертежи
Свободное скачивание на сегодня
Другие проекты
- 20.08.2014