Расчетная работа - Проектирование узла выходного вала редуктора




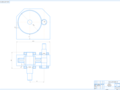
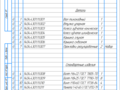
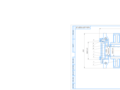
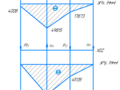
- Добавлен: 24.01.2023
- Размер: 699 KB
- Закачек: 0
Описание
Расчетная работа - Проектирование узла выходного вала редуктора
Состав проекта
![]() |
![]() |
![]() |
![]() ![]() ![]() ![]() |
![]() ![]() ![]() ![]() |
![]() ![]() ![]() ![]() |
![]() ![]() ![]() |
![]() |
![]() ![]() ![]() |
![]() |
![]() |
![]() ![]() ![]() |
Дополнительная информация
3.cdw

Сборочный чертеж.cdw

Спецификация.spw

Колесо зубчатое коническое
Колесо зубчатое цилиндрическое
Прокладки регулировачные
Манжета 1-40-60-3 ГОСТ 8752-79
Подшипник 208 ГОСТ 8328-75
Шайба 6 65Г ГОСТ 6402-70
Шайба 8 65Г ГОСТ 6402-70
Шайба 7019-0625 ГОСТ 14734-69
РГР.doc
Редуктор состоит из корпуса (литого чугуна или стального сварного). В корпусе редуктора размещены зубчатые или червячные передачи неподвижно закрепленные на валах. Валы опираются на подшипники размещенные в гнездах корпуса; в основном используют подшипники качения.
Тип редуктора определяется составом передач порядком их размещения в направлении от быстроходного вала к тихоходному и положением осей зубчатых коле в пространстве.
Назначение редуктора - понижение угловой скорости и повышение вращающего момента ведомого вала по сравнению с валом ведущим. Принцип действия зубчатой передачи основан на зацеплении пары зубчатых колес. Достоинством зубчатых передач является: высокий КПД постоянство передаточного отношения и широкий диапазон мощностей.
В данном проекте произведен расчет механического привода состоящего из закрытой цилиндрической прямозубой передачи.
Задание на расчетно-графическую работу
Рассчитать и спроектировать привод с одноступенчатым редуктором по заданной схеме.
Твых = 67 Н×м - вращающий момент на выходном валу;
nвых = 205 обмин - частота вращения выходного вала;
Lh = 15000 ч - время работы редуктора;
Z3 = 22 - число зубьев шестерни открытой передачи;
режим нагрузки – 1; прямозубая передача.
РАСЧЕТ СИЛОВЫХ И КИНЕМАТИЧЕСКИХ ПАРАМЕТРОВ ПРИВОДА
1 Выбор электродвигателя определение основных кинематических и энергетических параметров редуктора
Определение КПД привода. Общий КПД привода определяем по формуле:
где h - общий КПД привода;
hп– КПД подшипников качения;
hм – КПД упругой компенсирующей муфты;
hз – КПД зубчатой передачи.
hоп - КПД открытой зубчатой передачи
Численные значения КПД определяем по таблице [1 табл. 1.1] :
hп = 099; hм = 098; hз = 097; hоп = 095
Подставив численные значения в формулу (1.1) получим:
2 Определение требуемой мощности привода
Требуемая мощность привода определяется по формуле:
где Р - требуемая мощность привода кВт;
Твых - вращающий момент на выходном валу Н×м
nвых – частота вращения выходного вала обмин.
Подставив численные значения в формулу (1.2) получим:
3 Определение требуемой мощности электродвигателя
Требуемая мощность на валу электродвигателя определяется по формуле:
где Рвых – выходная мощность электродвигателя кВт;
Р – номинальная мощность на ведомом валу привода кВт;
h - общий КПД привода формула (1.1).
Подставив численные значения в формулу (1.3) получим:
По таблице [1 табл. 1.3]определяем мощность двигателя Рном=22 кВт.
4 Определение частоты вращения вала электродвигателя
Требуемая частота вращения вала определяется по формуле:
где nэд - требуемая частота вращения вала обмин;
Подставив численные значения в формулу (1.4) получим:
По таблице определяем частоту вращения вала nном=950 обмин.
5 Выбор электродвигателя
Согласно рассчитанным данным выбираем по каталогу [1 табл.1.4]двигатель марки 4АМ100L6У3 асинхронная частота вращения 950 обмин.
Диаметр выходного вала: d1 = 28 мм
6 Определение передаточного числа редуктора
Общее передаточное число привода определяем по формуле:
где uр - общее передаточное число привода;
nном - частота вращения вала электродвигателя обмин;
nвых - частота вращения выходного вала обмин.
Подставив численные значения в формулу (1.5) получим:
7 Определение крутящих моментов на валах редуктора
На конце быстроходного выла:
РАСЧЕТЫ ЗУБЧАТЫХ ПЕРЕДАЧ
1 Выбор материала зубчатых колес
При выборе материала зубчатых колес следует учитывать назначение проектируемой передачи условия эксплуатации требования к габаритным размерам и возможную технологию изготовления колёс. Основным материалом для изготовления зубчатых колёс является сталь. Необходимую твердость в сочетании с другими механическими характеристиками (а следовательно желаемые габариты и массу передачи) можно получить за счет назначения соответствующей термической или химико-термической обработки стали.
В условиях индивидуального и мелкосерийного производства в мало- и средненагруженных передачах а также в передачах с большими габаритами колес (когда термическая обработка их затруднена) обычно применяют стали с твердостью не более 350 НВ которая обеспечивается нормализацией или термоулучшением материала. При этом возможно чистовое нарезание зубьев непосредственно после термообработки с высокой точностью изготовления а при работе передачи обеспечивается хорошая прирабатываемость зубьев без хрупкого разрушения их при динамических нагрузках.
Для равномерного изнашивания зубьев и лучшей их прирабатываемости твёрдость шестерни НВ1 рекомендуют назначать больше твёрдости НВ2 колеса не менее чем на (10 15) НВ.
По таблице [1 табл. 2.1] для колеса и шестерни выбираем материал - сталь 45 вид термообработки – улучшение.
Твердость поверхности колеса - 235 262 НВ шестерни – 269 302 НВ.
2 Определение допускаемых напряжений
Допускаемое контактное напряжение рассчитывают для каждого зубчатого колеса передачи по формуле:
где [sН12] - допускаемое контактное напряжение МПа;
SН12 – коэффициент безопасности;
ZN12 – коэффициент долговечности.
Предел выносливости sНlim12 назначаем по эмпирическим зависимостям в зависимости от вида термообработки (в данном случае улучшение):
где - среднее значение твердости материала.
Подставив численные значения в формулу (2.2) получим:
Коэффициент безопасности назначаем в зависимости от вида термообработки (в данной работе – улучшение) и принимаем SН12 = 11.
Коэффициент долговечности ZN12 определяем по формуле:
где NHG12 – базовое число циклов;
NНЕ12 – эквивалентное число циклов до разрушения при расчетном контактном напряжении Эквивалентное число циклов определяем по формуле:
где mН – коэффициент эквивалентности;
NН12 – циклическая долговечность.
Коэффициент эквивалентности определяем в зависимости от режима работы и вида термообработке по таблице [1 табл. 2.3]: mН = 05.
Циклическую долговечность определяем по формуле:
где с – число зацеплений зуба за один оборот (для проектируемого редуктора с = 1);
n12 – частота вращения того зубчатого колеса по материалу которого определяют допускаемые напряжения обмин;
t – время работы передачи (ресурс) ч; t = Lh .
Подставив численные значения в формулу (2.5) получим:
Полученные данные подставляем в формулу (2.4):
Базовое число циклов NHG перемены напряжений рассчитывают по следующим эмпирическим зависимостям:
Подставив численные значения в формулу (2.6) получим:
Полученные данные подставляем в формулу (2.3) и определяем коэффициент долговечности ZN12:
По вычисленным данным определяем допускаемое контактное напряжение по формуле (2.1):
Из двух значений рассчитанного допускаемого контактного напряжения в дальнейшем рассчитываем из соотношения:
Допускаемые напряжения изгиба [sF]12 вычисляются по формуле:
SF – коэффициент безопасности [стр.27];
YА – коэффициент учитывающий влияние двустороннего приложения нагрузки [стр.27];
YN – коэффициент долговечности [стр.27].
Коэффициент безопасности принимаем SF = 175 при односторонней нагрузке YА = 1.
Коэффициент долговечности YN определяем по формуле (при НВ ≤ 350):
где NFG – базовое число циклов;
NFE – эквивалентное число циклов.
Для всех сталей рекомендуют принимать NFG = 4×106 [1 стр.25].
При переменных режимах нагрузки NFE определяют по формуле:
Коэффициент эквивалентности принимаем по таблице mF = 03.
Подставив численные значения в формулу (2.9) получим:
По полученным данным определяем коэффициент долговечности YN по формуле (2.8):
Предел выносливости sFlim12 назначаем по эмпирическим зависимостям в зависимости от вида термообработки:
По полученным данным определяем допускаемые напряжения изгиба по формуле (2.7):
3 Проектный расчет закрытой зубчатой передачи
При проектном расчете прежде всего определяют межосевое расстояние аw мм. Для косозубой передачи расчет производят по следующей формуле:
где u – передаточное число;
Т2 - вращающий момент на колесе передачи Н×мм;
КНb - коэффициент неравномерности нагрузки по длине контакта;
Епр – приведенный модуль упругости МПа;
[sН] - допускаемое контактное напряжение МПа формула 2.1;
yba – относительная ширина колес.
Так как в данной работе передача внешнего зацепления то в формуле (2.11) принимаем знак +.
Коэффициент неравномерности нагрузки по длине контакта КНb выбирают в соответствии с расположением зубчатых колес передачи относительно опор твердостью рабочих поверхностей зубьев и относительной шириной колес по графику[1 стр.29]: КНb = 106.
Приведенный модуль упругости принимаем Епр = 21 × 105 МПа [1 стр.30]
В соответствии со схемой расположения колес относительно опор и выбранной твердостью поверхностей зубьев назначаем относительную ширину колес по таблице[1 2.4]: yba = 03.
Подставив численные значения в формулу (2.11) получим:
Вычисленное межосевое расстояние округляем в большую сторону до стандартного значения: аw = 95 мм.
4 Геометрический расчет закрытой передачи
Модуль зацепления определяем из соотношения (при НВ ≤ 350):
Полученное значение модуля округляем до стандартного значения по ряду модулей: mn = 15 .
Суммарное число зубьев шестерни и колеса определяют по формуле (для прямозубых колес):
Число зубьев шестерни определяем из соотношения:
где u – передаточное число передачи.
Знак “+” – для внешнего зацепления.
Число зубьев колеса передачи определяем:
Фактическое значение передаточного числа передачи определяем по формуле:
Допускаемое отклонение от заданного передаточного числа должно составлять ≤ 4 % :
Фактическое межосевое расстояние определяем по формуле:
где aWФ – фактическое межосевое расстояние мм;
mn – модуль формула (2.13).
Подставив численные значения в формулу (2.18) получим:
Рабочая ширина зубчатого венца колеса:
Тогда ширина зубчатого венца колеса:
Ширина зуба шестерни составит:
Делительные диаметры рассчитываем по следующим формулам:
Подставив численные значения в формулу (2.21)получим:
Начальный диаметр шестерни рассчитываем по формуле:
где awф - фактическое межосевое расстояние мм
uф – фактическое значение передаточного числа.
Начальный диаметр колеса передачи рассчитываем по формуле:
Диаметры вершин зубьев колес:
Диаметры впадин зубьев колес:
Угол aW зацепления передачи принимают равным углу a профиля исходного контура: aW = a = 20° [1 стр.33]
5 Проверочный расчет закрытой передачи
Проверка контактной выносливости рабочих поверхностей зубьев колес. Расчетом должна быть проверена справедливость соблюдения неравенства:
Т1 – вращающий момент на шестерне Н × мм;
КНb - коэффициент неравномерности распределения нагрузки по длине контакта[1 стр.29];
КНV – коэффициент внутренней динамической нагрузки;
uФ – фактическое передаточное число;
dW – начальный диаметр колеса мм;
bW – рабочая ширина зубчатого венца колеса мм;
Епр – приведенный модуль упругости;
aW – угол зацепления град.
Величину вращающего момента Т1 на шестерне определяем по формуле:
где h - КПД передачи он учитывает потери мощности в зубчатой пердаче; обычно принимается h = 097.
Коэффициент неравномерности нагрузки по длине контакта КНb выбирают в соответствии с расположением колес относительно опор и твердостью рабочих поверхностей зубьев колес по графику КНb = 106.
Для определения коэффициента внутренней динамической нагрузки КНV необходимо рассчитать окружную скорость в зацеплении V мс:
В зависимости от значения V по таблице[2.6] назначаем степень точности передачи – 9. Затем определяем коэффициент внутренней динамической нагрузки по таблице [1 табл. 2.7]: КНV = 112 КFV =133.
Подставив численные значения в формулу (2.26) получим:
Допускаемое контактное напряжение т. е. неравенство (2.26) соблюдается: sН [sН].
Проверка прочности зубьев по напряжениям изгиба
Проверяют справедливость соотношения расчетных напряжений изгиба sF и допускаемых напряжений [sF ]:
где Ft – окружное усилие в зацеплении колес Н;
КFb - коэффициент неравномерности распределения нагрузки по длине контакта;
КFV – коэффициент внутренней динамической нагрузки;
mn – модуль зацепления;
bWуточн. – уточненное значение рабочей ширины венца;
YF12 – коэффициент формы зуба[1 табл. 2.9].
Окружное усилие в зацеплении колес Ft определяем по формуле:
Коэффициент неравномерности нагрузки по длине контакта КFb выбирается в соответствии с расположением колес относительно опор и твердостью рабочих поверхностей зубьев колес по графику: КFb = 113. [1 стр.29]
В зависимости от значения окружной скорости V по таблице назначаем степень точности передачи – 9. Затем определяем коэффициент внутренней динамической нагрузки КFV = 133 [1 стр.35].
Коэффициент формы зуба YF для прямозубых колес назначается по табл. 2.9 в зависимости от фактического числа зубьев:
Подставив численные значения в формулу (2.29) найдем значения расчетных напряжений изгиба sF:
Допускаемые напряжения изгиба: [sF]1 = 293.66 МПа [sF]2 = 255.6 МПа неравенство (2.29) соблюдается.
ПРОЕКТНЫЙ РАСЧЁТ ОТКРЫТОЙ КОНИЧЕСКОЙ ПРЯМОЗУБОЙ ПЕРЕДАЧИ
Для проектировочного расчёта открытых передач по напряжениям изгиба определяют модуль зацепления из соотношения:
где - число зубьев шестерни открытой передачи; z3 = 22;
Твых – вращающий момент на выходном валу
- коэффиеиент ширины зубчатого венца колеса относительного модуля;
- коэффициент неравномерности распределения нагрузки по длине линии контакта = 1.13 [1 рис 2.3];
- допускное напряжение изгиба.
- коэффициент формы зуба = 407 [1 табл. 2.9];
Подставив численные значения в формулу (3.1) получим:
Принимаем из ряда стандартных модулей m=3 мм [1 стр. 43];
1 Основные геометрические параметры зубчатого колеса
Делительный диаметр в среднем сечении зуба шестерни определяется по формуле:
Ширина зубчатого венца:
По принятому передаточному числу uотк= 45 [5 стр. 27]; находим угол при вершине делительного конуса:
Среднее конусное расстояние:
Внешнее конусное расстояние:
Модуль зацепления на внешнем торце:
Внешний делительный диаметр шестерни:
Внешний диаметр вершин зубьев:
2 Проверка зубьев колеса на выносливость по напряжениям изгиба
где окружное усилие в зацеплении Н ; (3.11)
коэффициент расчётной нагрузки
K.F = KFb KFV (3.12)
KFb = 1 + 1.5 (KHb 1)=1+1.5×(1.14-1)=1.21
определяют по табл. 2.7 с понижением точности на одну степень против фактической =113
Подставим численные значения в формулу (3.12):
KF=KFb×KFV=1.21×1.13=1.3673
коэффициент формы зуба (по табл. 2.9) YF3=407
Подставим численные значения в формулу (3.10):
sF3=14767 МПа [sF3] = 293.66МПа – неравенство (3.10) соблюдается Условия прочности выполняются.
ПРОЕКТНЫЙ РАСЧЕТ ВАЛОВ И ОПОРНЫХ КОНСТРУКЦИЙ
1 Выбор материала валов
В проектируемом редукторе для вала выберем термически обработанную сталь – 45 вид термообработки – улучшение. Твердость поверхности вала – 269 302 НВ.
Тогда [sF3] = 293.66 МПа – допускаемое напряжение изгиба.
2 Определение геометрических параметров ступеней валов
Редукторный вал представляет собой ступенчатое цилиндрическое тело количество и размеры ступеней которого зависят от количества и размеров установленных на вал деталей.
Диаметры различных участков вала редуктора определяют по формулам:
Диаметр d1 концевого участка вала:
где Т – крутящий момент Н × м;
[t]К – допускаемое напряжение на кручение Нмм2.
Расчет валов редуктора выполняют только по напряжениям кручения то есть при этом не учитывают напряжений изгиба концентрации напряжений и переменность напряжений во времени. Для компенсации этого значения допускаемых напряжений на кручение выбирают заниженными в пределах для тихоходного вала [t]К = 15Нмм2 для быстроходного вала [t]К = 10Нмм2.
Подставляя численные значения в формулу(4.1) получим:
Полученное значение по ряду нормальных линейных размеров округляем до d1 = 30 мм.
Длину ступени вала определяем по формуле:
Диаметр d2 под уплотнение крышки с отверстием и подшипник:
где t – высота буртика выбираем в зависимости от диаметра ступени вала d1 по таблице [1 стр.51] t = 3.5 мм.
Полученное значение округляем до ближайшего стандартного диаметра внутреннего кольца подшипника d2 = 40 мм
Диаметр d3 под колесо:
где r – радиус скругления мм [1 стр.51]
Радиус скругления выбираем в зависимости от диаметра ступени d2: r = 25мм.
Полученное значение округляем по ряду нормальных линейных размеров:
Длина ступени вала l3 определяется графически на эскизной компоновке.
Диаметр под подшипник d4 = d2 =40мм.
Длина ступени вала l4 равна ширине подшипника В.
Наружный диаметр буртика d5 вычисляется по формуле:
где f – величина фаски ступицы[1 стр.51] мм .
Величину фаски ступицы выбираем в зависимости от диаметра ступени d3: f = 16 мм .
Длину l5 определяем графически.
Рисунок 1 – Эскиз тихоходного вала
Диаметры ступеней вала – шестерни определяем по формулам:
Диаметр d1 выходного конца вала соединенного с двигателем через муфту находим по формуле:
где d1дв – диаметр выходного конца вала ротора двигателя мм.
Диаметр выходного конца вала ротора двигателя [1 табл. 1.4]
Полученное значение по ряду нормальных линейных размеров округляем до d1 = 24 мм.
Длину ступени вала определяем по формуле (4.2):
Диаметр d2 под уплотнение крышки с отверстием и подшипник находим по формуле:
Высоту буртика выбираем в зависимости от диаметра ступени d1: t=3мм по [1 стр.51]
Полученное значение по ряду нормальных линейных размеров округляем до d2 = 30 мм.
Диаметр d3 под шестерню находим по формуле:
Радиус скругления выбираем в зависимости от диаметра ступени d2: r=2мм по [1 стр.51]
Диаметр под подшипник d4 = d2 = 35мм.
Рисунок 2 - Эскиз быстроходного вала
5 Предварительный выбор подшипников
Определение типа серии и схемы установки подшипников. Для опор валов цилиндрических прямозубых и косозубых колес редукторов и коробок передач применяют чаще всего шариковые радиальные подшипники.
Из всех стандартных подшипников качения однорядные радиальные шарикоподшипники являются одними из наиболее дешевых имеют наименьшие потери на трение и обладают наибольшей быстроходностью. Кроме того эти подшипники хотя и не являются самоустанавливающимися допускают небольшие (иногда до 05°) перекосы колец и следовательно менее чувствительны к несоосности посадочных мест. Эти существенные достоинства однорядных радиальных шарикоподшипников обеспечили им широкое распространение и наибольшее число конструктивных разновидностей .
Предварительно выбираем для вала шариковые радиальные однорядные подшипники легкой серии схема установки - враспор. Для вала – шестерни шариковые радиальные однорядные подшипники с защитными шайбами легкой серии схема установки - враспор.
Определение основных параметров подшипников. По каталогу в зависимости от диаметра d внутреннего кольца подшипника равного диаметру второй d2 и четвертой d4 ступеней вала определяем основные параметры подшипников легкой серии :
- для тихоходного вала: Подшипник 208 ГОСТ 8338-75.
Параметры: d = 40мм; D = 80 мм; В = 18 мм; r = 2 ;Сr = 320 кН С0r = 178 кН.
- для быстроходного вала: Подшипник 206 ГОСТ 8338-75.
Параметры: d = 30мм; D = 62 мм; В = 16 мм; r = 15; Сr = 195 кН С0r = 10 кН.
6 Конструирование крышек подшипников
Рисунок 3 - Крышка подшипника на тихоходном валу
Стенка крышки при диаметре внешнего кольца подшипника D = 80 по = 6 мм
Канавка для выхода шлифовального круга b = 5 при диаметре внешнего кольца подшипника D = 80 мм
Диаметр болтов крепления при диаметре внешнего кольца подшипника D = 80 по d = 8 мм
Диаметр крышки = + = 80 +
Толщина фланца крышки принимается равной толщине стенке крышки = 5 мм
Длина пояска сопряжения l b = 5 мм
Толщина прокладки 2 мм
Толщина фланца под болт = = = 72 мм
7 Конструирование подшипниковых фланцев
Рисунок 4 - Эскиз фланца подшипников.
Диаметры приливов в которых располагаются подшипники определяются по формуле
Фланец подшипника на тихоходном валу:
= + 2..3 = 114 + 2..3 = 116 117 = 115 мм;
Минимальная ширина фланца редуктора мм.
ПРОВЕРОЧНЫЙ РАСЧЕТ ВАЛОВ НА ВЫНОСЛИВОСТЬ
1 Определение сил действующих на валу
2 Определение размеров вала колеса
2.1 Подшипники легкой серии для тихоходного вала
Характеристики подшипника: d = 40мм; D = 80 мм; В = 18 мм; r = 2 ;Сr = 320 кН С0r = 178 кН.
Покомпановке вала определяем необходимые для размера линейные размеры:
3 Выбор расчетной схемы вала определение опорных реакций построение эпюр изгибающих и крутящих моментов.
Строим схематично вал в плоскости YOZ и находим реакции опор в этой плоскости.
Проверка правильности расчётов:
Схематично строим вал в плоскости XOZ и находим реакции опор в этой плоскости.
Определение суммарных изгибающих моментов:
Построение эпюр изгибающих и крутящих моментов
4 Определение коэффициента запаса усталостной прочности
При расчете коэффициента запаса усталостной прочности принимают что напряжения изгиба изменяются по симметричному циклу а напряжения кручения – по нулевому. Выбор от нулевого цикла для напряжения кручения основан на том что большинство валов передает переменное по значению но постоянные по направлению вращающие моменты [1].
Определяем амплитуду симметричного цикла нормальных напряжений при изгибе вала в опасных сечениях:
и амплитуду от нулевого цикла касательных напряжений при кручении вала:
где Mоп - результирующий изгибающий момент в рассматриваемом опасном сечении(М2) Н × мм;
Т – крутящий момент на валу Н×мм [1].
Моменты сопротивления изгибу и кручению нетто – сечения вала:
Подставляем численные значения в формулы (5.13) (5.14):
При совместном действии изгиба и кручения запас усталостной прочности определяют по формуле:
где Ss - запас сопротивления усталости только по изгибу;
St - запас сопротивления усталости только по кручению;
В зависимости от марки стали 45 принимаем следующие характеристики:
где s-1 - предел выносливости материала вала при симметричном цикле нагружения принимаем s-1=410
кF - масштабный фактор принимаем кF=1.15
ys - коэффициент учитывающий влияние постоянной составляющей цикла напряжения на сопротивление усталости принимается в зависимости от материала для легированных сталей коэффициент равен 0.15[1 стр.62];
sm – среднее напряжение цикла для симметричного цикла равен 0.
Подставляя численные значения в формулу (5.18) получим:
Коэффициент запаса сопротивления усталости вычисляется по формуле:
гдеt-1 - предел выносливости материала вала при симметричном цикле нагружения[4 стр.165];
yt=01- коэффициент учитывающий влияние постоянной составляющей цикла напряжения на сопротивление усталости для легированных сталей;
Подставляя в формулу (5.19) получим:
Подставляем численное значение в формулу (5.17):
Условие прочности выполняется.
ПРОВЕРКА ПРАВИЛЬНОСТИ ПОДБОРА ПОДШИПНИКОВ
1 Проверочный расчет подшипников
Расчеты производим по более нагруженной опоре в несколько этапов.
Выбираем схему установки подшипников «враспор». Выписываем значения базовых динамической Cr и статической Cor радиальных грузоподъемностей:
Определяем осевые силы:
Для подшипников шариковых радиальных в зависимости отсоотношения FaCor находим значения Х Y.
Вычисляем эквивалентную динамическую радиальную нагрузку по формуле:
где Кб - коэффициент безопасности учитывающий характер нагрузки при умеренных толчках Кб=13 15
КТ - температурный коэффициент для температуры подшипникового узла t≤100 КТ=1
V – коэффициент вращения. Принимаю V=1
Подставляем численное значение в формулу (6.3)
Выбираем из них максимальное значение. PE=3894Н
Определяем требуемую динамическую грузоподъемность подшипника:
где n - частота вращения вала;
L10h - требуемая долговечность;
P=3 для шариковых подшипников;
Подставляем численное значение в формулу (74):
Сr > Cтр – условие выполняется.
Проверяем на долговечность.
Условие долговечности выполняется.
КОНСТРУИРОВАНИЕ ЭЛЕМЕНТОВ РЕДУКТОРА
1 Общие рекомендации
Размеры корпуса определяются числом и размерами размещенных в них деталей их относительным расположением и величиной зазора между ними. Для удобства сборки корпус выполняют разъёмным.
Плоскость разъёма проходит через оси валов для удобства обработки располагается параллельно оси обработки. Верхняя часть крышки служащая технологической базой для обработки плоскости разъёма также выполняется параллельно оси валов.
2 Конструктивное оформление внутреннего контура редуктора
Определение зазоров между вращающимися деталями:
Рисунок 5 - Компоновка редуктора.
Толщина стенки корпуса:
Толщина стенки крышки редуктора:
Размеры конструктивных элементов:
Рисунок 6 - Сечение корпуса.
3 Фиксирующее крепление крышки к корпусу
Для крепления используются винты с цилиндрической головкой и шестигранным углублением под ключ.
Диаметр фланцевых винтов крепления крышки корпуса к корпусу определяется по формуле:
Принимаем d = 10 мм.
Минимальная ширина фланца редуктора определяется из условия свободного размещения головки винта крепления крышки редуктора и толщины стенки редуктора.
Координата размещения оси болта:
Рисунок 7 - Крепление фланцевым болтом.
Необходимая точность фиксирования достигается штифтами. Используются два конических штифта с внутренней резьбой которые устанавливаются по срезам углов крышки.
Длина штифтов = 40 мм.
Рисунок 8 - Фиксирование крышки редуктора штифтом.
4 Конструктивное оформление опорной части корпуса
Опорная поверхность выполнена в виде четырех расположенных в местах установки болтов платиков. Такое расположение позволяет снизить расход металла и уменьшает время обработки опорной поверхности корпуса снижает нагрузки на резьбовые детали.
Рисунок 9 - Опорная поверхность.
Диаметр фундаментных болтов определяется по формуле
5 Конструктивное оформление крышки люка
Для заливки масла в редуктор и контроля правильности зацепления делают люк. Чтобы удобнее было заливать масло и наблюдать за зубчатыми колесами размеры люка должны быть максимально возможными. Люк закрывается стальной крышкой из листов толщиной
При среднесерийном производстве крышку выполняют штампованной. Для того чтобы внутрь корпуса извне не засасывалась пыль под крышку ставят уплотняющую прокладку. Материал прокладки - технический картон толщиной мм. Крышка крепится к корпусу винтами.
Крышка совмещена с отдушиной. Во внутренней штампованной крышке пробиты 4 отверстия диаметром мм. Наружная крышка - плоская. Вдоль её длинной стороны выдавлены гребня через которые внутренняя полость редуктора соединена с внешней средой.
Пространство между внутренней и внешней крышками заполнено фильтром из тонкой медной проволоки.
Длина крышки L = 95 мм.
Рисунок 10 - Крышка-отдушина.
Проушина для подъема и транспортировки выполняется в виде ребра с отверстием диаметр которого D = = = 16 мм и шириной S = = = 16 мм.
Рисунок 11 - Проушина.
6 Конструирование колеса
Так как в техническом задании на курсовое проектирование отсутствуют указания о серийности производства редукторов зубчатое колесо можно задать отдавая предпочтение индивидуальному и мелкосерийному производству.
Рисунок 12 – Эскиз зубчатого колеса.
Длину lст посадочного отверстия колеса принимаю равной ширине b2 зубчатого венца колеса :
В одноступенчатых редукторах колеса делают со ступицей симметрично выступающей в обе стороны от диска колеса.
Диаметр dст ступицы назначают в зависимости от материала колеса: для стали dст = (15 155) d;
dст=(1.5 155)×50=(75 775) мм
Ширину S торцов зубчатого венца принимают S = 22 m + 005 b2
где m модуль зацепления мм.
b2 – ширина зубчатого венца колеса.
S=2.2×15+0.05×285=475 мм
На торцах зубчатого венца выполняют фаски: при твердости рабочих поверхностей зубьев менее 350 НВ f45.
7 Коническое зубчатое колесо
Размер ступицы колеса определяют так же как при расчете цилиндрического зубчатого колеса:
Длину lст : lст = (1 12)d = (1 12)*30=(30 36)мм. Принимаю: 45 мм.
Диаметр dст: dст = (15 155) d= (15 155)×30 = (45 465)мм.
Рисунок 13 – Эскиз шестерни.
При любой форме колес внешние углы зубьев притупляют фаской
f05mе= 05× 3 = 15 мм.
Ширину зубчатого венца принимают равной: S = 25mе+2 = 25×3+2 = 95мм
Торец зубчатого венца шириной b=07S = 07× 95 = 665 мм - используют для установки заготовки колеса в приспособлении при нарезании зубьев на станке. Для уменьшения объема точной механической обработки выполняют выточки глубиной 1 2 мм.
ПРОВЕРОЧНЫЙ РАСЧЁТ ШПОНОЧНЫХ СОЕДИНЕНИЙ
Для расчётного вала применяем призматические шпонки по ГОСТу 23360-78.
1 Проверочный расчёт шпонок вала шестерни
На вал шестерни устанавливаем одну шпонку под диаметр
По таблице[5 табл. 24.29]определяем параметры шпонки:
Длина шпонкивычисляется по формуле:
где - геометрический размер быстроходного вала.
По ряду приведённому в таблице [5 табл. 24.29] принимаем длину шпонки .
Рабочая длина шпонкивычисляется по формуле:
Определим напряжение смятия на участке где расположена шпонка:
Согласно расчётам принимаем шпонку ГОСТ 23360 - 78
2 Проверочный расчёт шпонок вала колеса
Обычно на вал колеса устанавливают две шпонки соответствующего размера под шпонку.
Длина шпонкивычисляется по формуле (8.1):
где - геометрический размер тихоходного вала
Рабочая длина шпонкивычисляется по формуле (8.2):
Определим напряжение смятия на участке где расположена шпонка по формуле (8.3):
) d3=50 мм b=16мм h=10мм f=04 06 t1=6мм t2=43мм l=45..180мм.
где - геометрический размер тихоходного вала.
СМАЗКА ЗУБЧАТОЙ ПЕРЕДАЧИ
Для уменьшения потерь мощности на трение и снижения интенсивности износа трущихся поверхностей а также для предохранения их от “заедания” “задиров” коррозии и лучшего отвода теплоты трущиеся поверхности деталей должны иметь надежную смазку.
В редукторе применяем картерную систему смазки.
Для того чтобы выбрать необходимую марку масла нужно вычислить окружную скорость:
В зависимости от контактного напряжения и окружной скорости колёс по таблице [4] принимаем масло ИГА - 32.
Уплотнительные устройства применяют для предохранения от вытекания смазки из подшипниковых узлов а так же для предотвращения попадания пыли и влаги извне. В проектируемом редукторе в качестве уплотнительных устройств используем манжетные уплотнения.
Объем масла ИГА-32 требуемый для заливки в редуктор составляет 16 литра из соотношения 04 08л на 1 КВт передаваемой мощности.
Манжеты выбираем резиновые армированные по ГОСТ 8752-79 под диаметр для тихоходного вала.
Со следующими характеристиками:[5 табл. 24.26].
Манжеты выбираем резиновые армированные по ГОСТ 8752-79 под диаметр для быстроходного вала. Со следующими характеристиками:[5 табл. 24.26].
Перед сборкой внутреннюю область полости редуктора тщательно очистить и покрыть маслостойкой краской.
Сборку производить в соответствии со сборочным чертежом редуктора начиная с узлов валов:
-на ведущий вал насадить подшипники предварительно нагретые в масле до 80-100 С;
- в ведомый вал заложить шпонку и напрессовать зубчатое колесо до упора в бурт вала; затем надеть дистанционное кольцо и установить подшипники предварительно нагретые в масле;
Собранные валы уложить в основание корпуса редукторами надеть крышку корпуса покрыв предварительно поверхности стыка крышки и корпуса спиртовым лаком. Затянуть болты крепящие крышку к корпусу.
Установить сквозную и глухую крышки подшипников с комплектом прокладок для регулировки.
Проверить проворачиванием валов отсутствие заклинивания подшипников (валы должны проворачиваться от руки) и закрепить крышки болтами.
Далее на конец ведомого вала в шпоночную канавку заложить шпонку.
Залить в корпус масло.
Собранный редуктор обкатать и подвергнуть испытанию на стенде по программе устанавливаемой техническими условиями.
Эскизы стандартных деталей
Болт с шестигранной головкой класса точности B (ГОСТ 7790-70)
Винт с цилиндрической головкой класса точности B (ГОСТ 11738-84)
Манжеты резиновые армированные для валов (ГОСТ 8752-79)
Подшипники шариковые радиальные однорядные (ГОСТ 8328-75)
Шайба пружинная (ГОСТ 6402-70)
Шпонки призматические (ГОСТ 23360-78)
Шайба концевая (ГОСТ 14734-69)
СПИСОК ИСПОЛЬЗОВАННОЙ ЛИТЕРАТУРЫ
Расчет и конструирование одноступенчатого зубчатого редуктора: Учеб. пособие М. Ш. Мигранов С.М. Минигалеев О. Ф. Ноготков А. А. Сидоренко Л. Ш. Шустер – М.: Изд-во МАИ 2008. – 125 с.
Расчет зубчатых передач. Методические указания к выполнению курсового проектирования по дисциплине «Прикладная механика». 4-е изд. испр. и доп. Уфимск. гос. авиац. техн. ун-т; Сост.: А.А.Сидоренко Р.Г.Ахматвалиев Х.Ш.Газизов. – Уфа 2006. – 35 с.
Курсовое проектирование деталей машин: Учеб. пособие. 2-е изд. перераб. и доп. Шейнблит А.Е.- Калининград: Янтар. сказ 2004. – 454с.
Детали машин: Учебник для машиностроительных специальностей вузов 12-е изд. Испр. М.Н. Иванов В.А. Финогенов. – М.:Высш. Шк. 2008. – 408с.
Детали машин. Курсовое проектирование: Учеб. пособие для машиностроит. спец. ср. проф. образов. - 5-е изд. Дунаев II. Ф. Леликов О. П. М.: Высш. шк. 2004.- 560с.
Детали машин. Курсовое проектирование: Учеб. пособие для машиностроит. спец. техникумов. Дунаев II. Ф. Леликов О. П. М.: Высш. шк. 1984.- 336с.
моя эпюра.frw

Содержание.doc
Расчет силовых и кинематических параметров привода 6
1 Выбор электродвигателя определение основных кинематических и энергетических параметров редуктора .. 6
2 Определение требуемой мощности привода .. 6
3 Определение требуемой мощности электродвигателя .. 6
4 Определение частоты вращения вала электродвигателя .. 7
5 Выбор электродвигателя . 7
6 Определение передаточного числа редуктора 7
7 Определение крутящих моментов на валах редуктора .8
Расчеты зубчатых передач. . ..9
1 Выбор материала зубчатых колес .. .9
2 Определение допускаемых напряжений .. ..9
3 Проектный расчет закрытой зубчатой передачи .14
4 Геометрический расчет закрытой передачи. 14
5 Проверочный расчет закрытой передачи 17
Проектный расчёт открытой конической прямозубой передачи . 20
1 Основные геометрические параметры зубчатого колеса 20
2 Проверка зубьев колеса на выносливость по напряжениям изгиба 21
Проектный расчет валов и опорных конструкций . 23
1 Выбор материала валов 23
2 Определение геометрических параметров ступеней валов . 23
4 Быстроходный вал 25
5 Предварительный выбор подшипников 26
6 Конструирование крышек подшипников 27
7 Конструирование подшипниковых фланцев 28
Проверочный расчет валов на выносливость 29
1 Определение сил действующих на валу 29
2 Определение размеров вала колеса 29
3 Выбор расчетной схемы вала определение опорных реакций построение эпюр изгибающих и крутящих моментов 29
4 Определение коэффициента запаса усталостной прочности ..33
Проверка правильности подбора подшипников 36
Конструирование элементов редуктора.. . ..38
1 Общие рекомендации 38
2 Конструктивное оформление внутреннего контура редуктора .. 38
3 Фиксирующее крепление крышки к корпусу 39
4 Конструктивное оформление опорной части корпуса 41
5 Конструктивное оформление крышки люка 41
6 Конструирование колеса 42
7 Коническое зубчатое колесо 43
Проверочный расчёт шпоночных соединений ..45
1 Проверочный расчёт шпонок вала шестерни 45
2 Проверочный расчёт шпонок вала колеса . 45
Смазка зубчатой передачи . ..47
Сборка редуктора.. . .48
Список использованной литературы . ..52
Рекомендуемые чертежи
- 24.01.2023
Свободное скачивание на сегодня
Другие проекты
- 24.10.2015